5 Key Benefits of Using a Compressor in Industry (2025)
Introduction: Navigating the Global Market for compressor in industry
In today’s global marketplace, sourcing the right air compressor for industrial applications presents a unique set of challenges for international B2B buyers. The complexities of selecting an appropriate compressor—whether for automotive assembly in Mexico, food processing in Colombia, or manufacturing in Europe—can be daunting. With the vast array of types, configurations, and suppliers, making an informed purchasing decision is crucial for optimizing operational efficiency and cost-effectiveness. This guide aims to demystify the world of compressors in industry, exploring various types such as rotary screw, reciprocating, and centrifugal compressors, alongside their specific applications across sectors like pharmaceuticals, agriculture, and energy.
Buyers will gain insight into essential factors to consider, including energy efficiency, pressure requirements, and the benefits of stationary versus portable units. Additionally, this guide provides actionable strategies for vetting suppliers, assessing total cost of ownership, and understanding maintenance needs. By equipping B2B buyers from Africa, South America, the Middle East, and Europe with comprehensive knowledge and practical tools, we empower them to make strategic decisions that enhance productivity and drive growth in their respective markets. Whether you are looking to streamline your operations or reduce long-term costs, this guide will serve as a valuable resource in navigating the global market for industrial compressors.
Understanding compressor in industry Types and Variations
Type Name | Key Distinguishing Features | Primary B2B Applications | Brief Pros & Cons for Buyers |
---|---|---|---|
Rotary Screw Compressors | Continuous operation, higher efficiency, low maintenance | Automotive, manufacturing, HVAC | Pros: High reliability, energy-efficient; Cons: Higher initial cost, requires space for installation. |
Reciprocating Compressors | Uses pistons to compress air, suitable for small to medium applications | Construction, automotive repair, woodworking | Pros: Versatile, lower initial cost; Cons: Noisy, less efficient for continuous operations. |
Centrifugal Compressors | Utilizes high-speed rotating impellers, ideal for large volumes | Oil & gas, chemical processing | Pros: High flow rates, efficient for large applications; Cons: Complex design, higher maintenance costs. |
Scroll Compressors | Compact design, uses spiral scrolls for compression | Food processing, medical equipment | Pros: Quiet operation, low vibration; Cons: Limited capacity for larger applications. |
Portable Compressors | Designed for mobility, smaller tank sizes | Construction sites, outdoor events | Pros: Easy to transport, versatile; Cons: Limited air supply, may not meet high-demand applications. |
What are Rotary Screw Compressors and When Should You Use Them?
Rotary screw compressors are designed for continuous operation, making them suitable for industries requiring a constant supply of compressed air. They are commonly used in automotive, manufacturing, and HVAC applications due to their high efficiency and low maintenance requirements. When purchasing, consider the initial investment, as they tend to be pricier than other types, but their long-term energy savings and reliability can justify the cost.
How Do Reciprocating Compressors Work and What Are Their Benefits?
Reciprocating compressors operate using pistons to compress air and are ideal for small to medium-sized applications like construction and woodworking. They are versatile and generally have a lower upfront cost, making them attractive for businesses with budget constraints. However, buyers should be aware of their noisiness and reduced efficiency during extended operations, which may impact workplace comfort.
What Makes Centrifugal Compressors Suitable for Large-Scale Operations?
Centrifugal compressors utilize high-speed rotating impellers to compress air, making them ideal for large-scale applications such as oil and gas or chemical processing. They offer high flow rates and efficiency, which can significantly enhance production processes. However, potential buyers should consider their complex design and higher maintenance costs, which may require specialized knowledge for upkeep.
Why Choose Scroll Compressors for Specific Applications?
Scroll compressors are compact and utilize spiral scrolls for air compression, making them suitable for applications in food processing and medical equipment where noise and vibration must be minimized. Their quiet operation is a significant advantage, but their limited capacity can restrict use in larger applications. Buyers should evaluate their specific needs to determine if a scroll compressor meets their operational demands.
What Are the Advantages of Portable Compressors?
Portable compressors are designed for mobility, making them an excellent choice for construction sites and outdoor events. They are easy to transport and versatile, allowing for a range of applications. However, buyers should be cautious of their limited air supply, as they may not meet the demands of high-output operations. Assessing the required air volume and pressure is crucial before investing in a portable unit.
Key Industrial Applications of compressor in industry
Industry/Sector | Specific Application of compressor in industry | Value/Benefit for the Business | Key Sourcing Considerations for this Application |
---|---|---|---|
Automotive | Powering pneumatic tools for assembly lines | Increases efficiency and reduces labor costs | Evaluate CFM and PSI requirements; consider rotary screw models for continuous operation. |
Food and Beverage | Ingredient portioning and packaging | Enhances accuracy and speeds up production | Look for compressors with clean air certification; ensure compliance with food safety regulations. |
Pharmaceutical | Pneumatic conveying of powders and granules | Streamlines production and minimizes contamination | Focus on energy efficiency and reliability; consider compact designs for limited space. |
Manufacturing | Operating machinery in assembly processes | Improves productivity and reduces downtime | Assess the total air demand; consider dual-stage compressors for higher pressure needs. |
HVAC | Temperature and humidity control | Enhances comfort and energy efficiency | Ensure compatibility with existing systems; prioritize low noise levels for residential areas. |
How Are Compressors Used in the Automotive Industry?
In the automotive sector, compressors are essential for powering pneumatic tools used in assembly lines. These tools, such as impact wrenches and spray guns, require a reliable supply of compressed air to operate efficiently. By streamlining assembly processes, businesses can significantly reduce labor costs and production time. Buyers should consider the required CFM and PSI specifications to ensure optimal performance. Rotary screw compressors are often preferred for their continuous airflow capabilities, making them ideal for high-demand environments.
What Role Do Compressors Play in the Food and Beverage Sector?
In the food and beverage industry, compressors are vital for precise ingredient portioning and packaging. Compressed air systems enhance accuracy in measuring ingredients, thereby minimizing human error and waste. Additionally, they speed up production processes, ensuring that products reach the market faster. B2B buyers should prioritize compressors that meet food safety standards, including clean air certifications. Moreover, understanding the specific pressure and volume requirements for packaging machinery is crucial for selecting the right compressor.
How Are Compressors Utilized in the Pharmaceutical Industry?
Pharmaceutical manufacturers rely on compressors for pneumatic conveying systems that transport powders and granules throughout the production process. This application is crucial for maintaining product integrity and minimizing contamination risks. Compressors help streamline operations, resulting in increased productivity and reduced waste. Buyers in this sector should focus on energy-efficient models that offer reliability and compact designs, as space is often limited in pharmaceutical facilities. Compliance with strict regulatory standards is also a key consideration.
What Are the Applications of Compressors in Manufacturing?
In the broader manufacturing sector, compressors are used to operate various machinery, including assembly line equipment and tools. They enhance productivity by providing a consistent power source, which reduces downtime and improves operational efficiency. When sourcing compressors, manufacturers should assess their total air demand to select an appropriately sized unit. Dual-stage compressors may be necessary for applications requiring higher pressure, ensuring that production processes run smoothly and without interruption.
How Do Compressors Enhance HVAC Systems?
Compressors play a critical role in HVAC systems by helping regulate temperature and humidity levels in commercial and residential buildings. This function is essential for creating comfortable living and working environments while also improving energy efficiency. B2B buyers should ensure that the compressors they choose are compatible with existing HVAC systems and prioritize low noise levels, especially in urban areas. Additionally, understanding the specific cooling requirements of the building can aid in selecting the most effective compressor solution.
3 Common User Pain Points for ‘compressor in industry’ & Their Solutions
Scenario 1: Inefficient Energy Consumption in Compressed Air Systems
The Problem: B2B buyers often face the challenge of high operational costs due to inefficient energy consumption in their compressed air systems. In industries such as manufacturing and food processing, where air compressors are essential, excessive energy use can lead to skyrocketing utility bills. Additionally, older models may not meet modern efficiency standards, resulting in wasted resources and increased environmental impact. This inefficiency can be particularly burdensome for businesses in Africa and South America, where energy costs can be significantly higher and reliability can be a concern.
The Solution: To combat this issue, B2B buyers should invest in energy-efficient compressor models that utilize advanced technologies such as variable speed drives (VSD). These compressors adjust their motor speed to match air demand, significantly reducing energy consumption. Additionally, conducting an energy audit can help identify leaks in the air distribution system, which can waste up to 30% of compressed air. Buyers should engage with suppliers who offer comprehensive maintenance packages that include leak detection and repair services. Regular maintenance can ensure that the system operates at peak efficiency, ultimately leading to substantial cost savings.
Scenario 2: Inconsistent Air Pressure Affecting Production Quality
The Problem: Many manufacturers encounter problems with inconsistent air pressure, which can negatively impact product quality and operational efficiency. Fluctuating pressure levels can lead to malfunctioning pneumatic tools, resulting in defects in products, increased waste, and delayed production schedules. This issue is particularly critical in industries such as automotive and pharmaceuticals, where precision is paramount. Buyers may find themselves stuck between the need for reliable performance and the challenge of sourcing the right equipment to meet their specific pressure requirements.
The Solution: To ensure consistent air pressure, B2B buyers should evaluate the compressor’s capacity in relation to their operational needs. Understanding the required CFM (cubic feet per minute) and PSI (pounds per square inch) is crucial. Buyers should consider investing in two-stage compressors, which provide better efficiency and stable pressure output compared to single-stage models. Additionally, implementing a pressure regulator can help maintain consistent pressure levels throughout the production process. Partnering with experienced manufacturers who can provide tailored solutions based on specific industry needs will further enhance reliability.
Scenario 3: Maintenance Challenges Leading to Downtime
The Problem: Downtime due to compressor failures can be a significant pain point for industrial buyers, especially in sectors that rely heavily on continuous operation, such as energy and automotive manufacturing. Unexpected breakdowns can lead to production halts, resulting in lost revenue and missed deadlines. This issue is compounded in regions where access to quick repair services may be limited, such as in some parts of Africa and the Middle East, making proactive maintenance even more critical.
The Solution: To mitigate maintenance challenges, B2B buyers should implement a predictive maintenance program. This involves utilizing IoT sensors and monitoring tools that can provide real-time data on compressor performance, allowing for early detection of potential issues. Buyers should also establish a regular maintenance schedule with qualified technicians who can perform routine checks and necessary repairs. Investing in compressors with extended warranties and service agreements can also provide peace of mind, ensuring that support is readily available when needed. Additionally, training staff on basic troubleshooting can empower teams to address minor issues before they escalate, further reducing downtime risks.
Strategic Material Selection Guide for compressor in industry
What Are the Common Materials Used in Compressors for Industrial Applications?
When selecting materials for compressors, it is essential to consider their properties and suitability for specific applications. Below, we analyze four common materials used in the construction of compressors, focusing on their key properties, advantages, disadvantages, and considerations for international B2B buyers.
How Does Aluminum Perform in Compressor Manufacturing?
Key Properties:
Aluminum is lightweight and exhibits excellent corrosion resistance, making it suitable for various environments. It can withstand moderate temperatures and pressures, typically rated up to 150 psi.
Pros & Cons:
The primary advantage of aluminum is its low weight, which facilitates easier installation and maintenance. However, it is less durable than steel and can be more expensive to manufacture due to its specific processing requirements.
Impact on Application:
Aluminum is particularly compatible with air and non-corrosive gases. Its lightweight nature allows for portable compressor designs, making it ideal for industries requiring mobility, such as construction and automotive repair.
Considerations for International Buyers:
Buyers from regions like Africa and South America should ensure compliance with local standards and regulations regarding aluminum use. Familiarity with ASTM standards can facilitate smoother procurement processes.
What Role Does Cast Iron Play in Compressor Design?
Key Properties:
Cast iron is known for its high strength and durability, capable of withstanding high temperatures and pressures, often rated above 200 psi.
Pros & Cons:
The significant advantage of cast iron is its robustness, which leads to a longer lifespan and reduced maintenance costs. However, it is heavier and more susceptible to corrosion if not properly coated or maintained.
Impact on Application:
Cast iron is well-suited for heavy-duty applications, such as manufacturing and energy production, where high durability is essential. Its ability to handle high pressures makes it ideal for stationary compressors.
Considerations for International Buyers:
Buyers in Europe and the Middle East should be aware of the various grades of cast iron and their compliance with industry standards such as DIN and JIS. Proper documentation of material specifications is crucial for quality assurance.
How Does Stainless Steel Enhance Compressor Performance?
Key Properties:
Stainless steel offers excellent corrosion resistance and can handle high temperatures and pressures, typically rated up to 300 psi.
Pros & Cons:
The key advantage of stainless steel is its durability and resistance to rust, making it suitable for harsh environments. However, it is more expensive than other materials, which can impact overall project budgets.
Impact on Application:
Stainless steel is ideal for compressors used in the food and beverage and pharmaceutical industries, where hygiene and material compatibility are paramount. Its non-reactive nature ensures that it does not contaminate the compressed air.
Considerations for International Buyers:
B2B buyers should verify compliance with international standards such as ASTM for stainless steel grades. Understanding the specific requirements for food-grade materials is essential for industries operating in regulated environments.
What Benefits Does Plastic Bring to Compressor Applications?
Key Properties:
Plastics, such as polycarbonate and nylon, are lightweight and can be molded into complex shapes, offering flexibility in design. They can withstand moderate pressures and are often rated up to 150 psi.
Pros & Cons:
The primary advantage of plastic is its resistance to corrosion and chemical reactions, making it suitable for various gases. However, plastics may not endure high temperatures or pressures as effectively as metals, limiting their application scope.
Impact on Application:
Plastic components are often used in smaller, portable compressors or in applications where weight is a concern. They are suitable for low-pressure applications, such as pneumatic tools in light manufacturing.
Considerations for International Buyers:
Buyers from regions with diverse climates, such as Africa and South America, should consider the temperature tolerance of plastic materials. Compliance with local safety standards is also crucial for ensuring product reliability.
Summary Table of Material Selection for Compressors
Material | Typical Use Case for compressor in industry | Key Advantage | Key Disadvantage/Limitation | Relative Cost (Low/Med/High) |
---|---|---|---|---|
Aluminum | Portable compressors in construction | Lightweight and corrosion-resistant | Less durable than steel | Medium |
Cast Iron | Heavy-duty stationary compressors | High strength and durability | Heavier and prone to corrosion | Medium |
Stainless Steel | Food and beverage industry compressors | Excellent corrosion resistance | Higher cost | High |
Plastic | Small, portable compressors | Corrosion-resistant and flexible | Limited pressure and temperature tolerance | Low |
This guide provides essential insights into material selection for compressors, helping international B2B buyers make informed decisions tailored to their specific industry needs.
In-depth Look: Manufacturing Processes and Quality Assurance for compressor in industry
What Are the Main Stages of Manufacturing Air Compressors?
The manufacturing process of air compressors involves several critical stages that ensure quality and performance. Understanding these stages can help B2B buyers evaluate potential suppliers effectively.
Material Preparation: What Raw Materials Are Used in Compressor Manufacturing?
The first stage in the manufacturing of air compressors is material preparation. Key materials include:
- Metals: High-grade steel and aluminum are commonly used for the compressor housing and components due to their strength and durability.
- Plastics: Various plastic components may be utilized, particularly in non-structural applications like housing for electronic controls.
- Seals and Gaskets: Rubber or synthetic materials are critical for ensuring airtight seals to prevent air leaks.
These materials must meet specific industry standards to ensure reliability and longevity. Buyers should inquire about the source of materials and any certifications that guarantee quality.
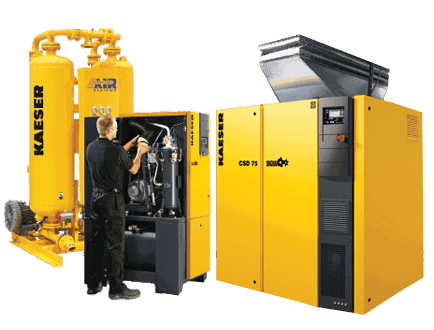
A stock image related to compressor in industry.
Forming: How Are Compressor Parts Shaped?
The forming process involves shaping the raw materials into the necessary components. Common techniques include:
- Casting: Used for complex shapes, casting allows for high precision in creating components like compressor housings.
- Machining: After casting, components often undergo machining to achieve precise dimensions. This includes processes like milling and turning.
- Stamping: For sheet metal parts, stamping is commonly used to create components like brackets and frames.
These techniques ensure that parts fit together correctly, which is vital for the efficient operation of the compressor.
Assembly: What Does the Assembly Process Entail?
The assembly stage is crucial, as it brings together all manufactured components. Key steps include:
- Pre-Assembly Inspection: Before assembly, each part undergoes an inspection to ensure it meets quality standards.
- Component Assembly: Skilled technicians assemble the components using specialized tools. This may include attaching the motor, compressor head, and control systems.
- Final Assembly: Once individual components are joined, the final assembly process includes installing the tank and connecting all systems.
Attention to detail during assembly can greatly affect the compressor’s performance and longevity.
Finishing: What Are the Final Touches in Compressor Manufacturing?
The finishing stage enhances the compressor’s durability and aesthetics. Key processes include:
- Surface Treatment: Components may undergo treatments such as anodizing or powder coating to improve corrosion resistance.
- Painting: Aesthetic finishes are often applied to meet branding or customer preferences.
- Quality Testing: Before leaving the factory, compressors are tested for functionality, pressure, and efficiency.
Finishing processes not only contribute to the visual appeal but also to the operational effectiveness of the compressors.
How Is Quality Assurance Implemented in Compressor Manufacturing?
Quality assurance (QA) is integral to compressor manufacturing, ensuring products meet international standards and customer expectations.
What International Standards Are Relevant for Compressor Quality Assurance?
B2B buyers should be aware of several international standards that govern compressor manufacturing:
- ISO 9001: This standard outlines requirements for a quality management system (QMS), focusing on consistent quality and customer satisfaction.
- CE Marking: In Europe, compressors must comply with specific directives to ensure safety and performance, evidenced by CE marking.
- API Standards: For certain industrial applications, compliance with American Petroleum Institute (API) standards may be required, particularly in oil and gas sectors.
Understanding these standards can help buyers assess the credibility of suppliers.
What Are the Key Quality Control Checkpoints During Manufacturing?
Quality control (QC) checkpoints are essential at various stages of the manufacturing process:
- Incoming Quality Control (IQC): This involves inspecting raw materials upon receipt to ensure they meet specifications.
- In-Process Quality Control (IPQC): During assembly, ongoing inspections help identify defects early, allowing for corrections before final assembly.
- Final Quality Control (FQC): After assembly, compressors undergo rigorous testing to verify they meet performance and safety standards.
By understanding these checkpoints, B2B buyers can inquire about the QC practices of their potential suppliers.
What Common Testing Methods Are Used in Compressor Quality Assurance?
Testing methods play a vital role in ensuring compressors function as intended. Common methods include:
- Pressure Testing: Ensures the compressor can handle specified pressure levels without leaking.
- Performance Testing: Measures airflow and efficiency to confirm the compressor meets operational specifications.
- Noise Level Testing: Assesses sound levels to ensure compliance with regulations and customer expectations.
These tests provide tangible evidence of a compressor’s reliability and performance.
How Can B2B Buyers Verify Supplier Quality Control?
To mitigate risks associated with supplier quality, B2B buyers can take several steps:
What Audit Practices Should Buyers Consider?
- Supplier Audits: Conduct regular audits of suppliers to assess their manufacturing processes and QA practices.
- Certification Verification: Check for ISO and other relevant certifications to ensure compliance with quality standards.
How Can Third-Party Inspections Enhance Quality Assurance?
Engaging third-party inspection services can provide an unbiased evaluation of the supplier’s quality control processes. These services can conduct:
- Pre-shipment Inspections: Ensure products meet specifications before shipment.
- Random Sampling: Test a selection of compressors for compliance with quality standards.
Using third-party services can provide peace of mind and help in making informed purchasing decisions.
What Are the Unique QC Considerations for International B2B Buyers?
B2B buyers from Africa, South America, the Middle East, and Europe face unique challenges regarding quality assurance.
How Do Regulatory Differences Affect Quality Standards?
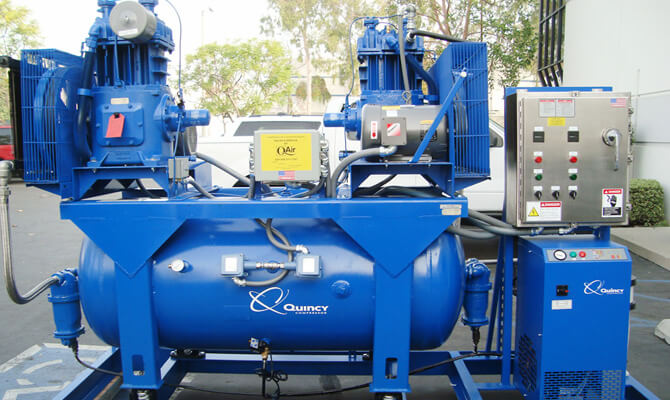
A stock image related to compressor in industry.
Different regions may have varying regulations and standards. For example, compressors sold in the European Union must meet CE marking requirements, while those in the U.S. may need to comply with specific ANSI standards. Buyers should familiarize themselves with local regulations to ensure compliance.
What Cultural and Logistical Factors Should Buyers Be Aware Of?
Understanding cultural differences and logistical challenges can impact supplier relationships. Buyers should consider:
- Communication: Ensure clear communication regarding quality expectations.
- Logistics: Assess shipping and handling practices, as these can affect product integrity during transit.
By addressing these nuances, buyers can foster stronger relationships with suppliers and ensure quality products that meet their operational needs.
In summary, a thorough understanding of the manufacturing processes and quality assurance practices is crucial for B2B buyers in the compressor industry. By focusing on these areas, buyers can make informed decisions that enhance their operational efficiency and product quality.
Practical Sourcing Guide: A Step-by-Step Checklist for ‘compressor in industry’
Introduction
This sourcing guide provides a practical step-by-step checklist for international B2B buyers aiming to procure compressors for industrial applications. Understanding the complexities of selecting the right compressor is essential to ensure efficiency, cost-effectiveness, and compatibility with your operational needs. This guide will help streamline your decision-making process, ensuring you make informed choices that align with your business objectives.
Step 1: Define Your Technical Specifications
Identifying your technical requirements is the first step in sourcing the right compressor. Consider the operating pressure (psi) and airflow requirements (CFM) specific to your industry. Understanding these specifications will help you narrow down your options and ensure the compressor meets your production needs.
- Operating Pressure: Determine the maximum pressure needed for your applications to choose between single-stage or two-stage compressors.
- Airflow Requirements: Calculate the total CFM needed by adding the specifications of all tools that will operate simultaneously, plus a 30% buffer for future needs.
Step 2: Assess Your Application Needs
Different industries utilize compressors for various applications, so understanding your specific needs is crucial. Whether it’s powering pneumatic tools, cooling equipment, or conveying materials, the application will influence the type of compressor you should consider.
- Industry-Specific Uses: Identify the primary functions the compressor will serve within your operations, such as automotive assembly or food processing.
- Mobility Requirements: Decide if you need a stationary compressor with larger capacity or a portable unit for flexibility in operations.
Step 3: Evaluate Energy Efficiency Options
Energy costs can significantly impact your operational budget. Look for compressors that offer energy-efficient features, which can lead to substantial savings over time. Efficient models reduce energy consumption without compromising performance.
- Variable Speed Drives (VSD): Consider compressors with VSDs, which adjust motor speed based on demand, thus saving energy.
- Rated Efficiency: Check for energy efficiency ratings and certifications that indicate the compressor’s performance in real-world conditions.
Step 4: Research and Verify Supplier Credentials
Finding a reliable supplier is vital for a successful procurement process. Conduct thorough research to ensure the supplier has a solid reputation in the industry.
- Supplier Certifications: Verify if the supplier holds relevant certifications, such as ISO standards, which reflect quality and reliability.
- Customer References: Request references from other businesses in your region or industry to gauge their satisfaction with the supplier’s products and services.
Step 5: Request Quotes and Compare Options
Once you have identified potential suppliers, request detailed quotes. This step allows you to compare pricing, features, warranty options, and after-sales support.
- Detailed Quotations: Ensure that quotes include all costs, such as installation, maintenance, and spare parts.
- Warranty Terms: Look for comprehensive warranty options that protect your investment and ensure peace of mind.
Step 6: Plan for Maintenance and Support
Consider the long-term maintenance and support required for the compressor you select. A good maintenance plan is essential for prolonging the life of your equipment and minimizing downtime.
- Service Agreements: Investigate if the supplier offers service contracts that include routine maintenance and emergency support.
- Availability of Spare Parts: Confirm the supplier’s ability to provide spare parts promptly to avoid operational interruptions.
Step 7: Make Your Decision and Implement
After evaluating all the factors, make your purchasing decision. Ensure that your team is trained on the new compressor’s operation and maintenance to maximize its efficiency.
- Training Programs: Check if the supplier offers training sessions for your staff on optimal usage and maintenance practices.
- Integration Planning: Develop a plan for integrating the new compressor into your existing systems to ensure a smooth transition.
By following this checklist, you can effectively navigate the sourcing process for industrial compressors, ensuring that your investment aligns with your operational goals while meeting industry standards.
Comprehensive Cost and Pricing Analysis for compressor in industry Sourcing
What Are the Key Cost Components in Sourcing Industrial Compressors?
When evaluating the cost structure for industrial compressors, several key components must be considered. The primary cost elements include:
-
Materials: The type and quality of materials used in the compressor significantly influence the overall cost. High-grade metals and components often lead to higher prices but can enhance durability and performance.
-
Labor: Labor costs can vary based on the region and complexity of the manufacturing process. Skilled labor in regions with higher wage standards can increase production costs.
-
Manufacturing Overhead: This includes indirect costs associated with production, such as utilities, rent, and equipment maintenance. Efficient manufacturing processes can help minimize these overheads.
-
Tooling: Initial tooling costs are crucial, especially for custom or specialized compressors. Investing in high-quality tooling can improve production efficiency and reduce long-term costs.
-
Quality Control (QC): Comprehensive QC processes ensure that the compressors meet specific standards and certifications. While this may add to costs, it is essential for ensuring product reliability and compliance with international standards.
-
Logistics: Transportation and warehousing costs are significant, particularly for international shipments. The choice of shipping method and distance can greatly influence the final price.
-
Margin: Suppliers typically add a profit margin to cover their costs and achieve profitability. This can vary based on market conditions and competition.
What Influences Pricing for Industrial Compressors?
Understanding the factors that influence the pricing of industrial compressors is vital for international buyers:
-
Volume and Minimum Order Quantity (MOQ): Bulk purchases often lead to discounts. Suppliers may offer lower per-unit prices for larger orders, making it advantageous for buyers to consolidate their purchasing.
-
Specifications and Customization: Custom compressors tailored to specific operational needs can significantly affect pricing. Unique specifications may require additional materials or engineering, thus increasing costs.
-
Materials and Quality Certifications: Higher-quality materials and certifications (e.g., ISO, CE) typically command higher prices. Buyers should assess whether the added cost aligns with their operational needs and regulatory requirements.
-
Supplier Factors: The reputation and reliability of suppliers can affect pricing. Established suppliers may charge more due to their proven track record, while newer entrants might offer competitive pricing to gain market share.
-
Incoterms: The choice of Incoterms influences total costs. For instance, “CIF” (Cost, Insurance, and Freight) includes shipping and insurance, which can vary based on the destination and risk factors involved.
How Can International Buyers Negotiate for Better Pricing?
Negotiation strategies are crucial for international B2B buyers, particularly from diverse regions such as Africa, South America, the Middle East, and Europe:
-
Research Market Prices: Understanding the average prices for compressors in your region can provide a solid foundation for negotiation. Utilize online marketplaces and industry reports to gather data.
-
Leverage Volume Discounts: If possible, consolidate orders or collaborate with other companies to achieve higher purchase volumes, thereby securing better pricing.
-
Focus on Total Cost of Ownership (TCO): Emphasize the long-term savings associated with quality compressors, such as reduced maintenance and energy costs. Suppliers may be more willing to negotiate on upfront prices if TCO is highlighted.
-
Be Aware of Pricing Nuances: Each market has unique pricing dynamics. Factors such as local demand, currency fluctuations, and geopolitical stability can affect pricing. Understanding these nuances can enhance negotiation tactics.
-
Consider Payment Terms: Flexible payment options can be a negotiating point. Offering upfront payment might lead to discounts, while extended payment terms may be more favorable for cash flow.
What Should International Buyers Keep in Mind Regarding Pricing?
It is important for buyers to approach compressor sourcing with a clear understanding of potential price variations. Prices can fluctuate based on market conditions, supplier relationships, and global economic factors. Thus, always request a detailed quotation that breaks down costs to ensure transparency.
While indicative prices can serve as a benchmark, they should not be relied upon solely. Buyers should be prepared for adjustments based on real-time market dynamics and specific project requirements. By engaging in thorough research and strategic negotiation, international buyers can secure favorable pricing while ensuring they meet their operational demands effectively.
Alternatives Analysis: Comparing compressor in industry With Other Solutions
Understanding the Alternatives to Compressors in Industry
As industries evolve, so do the technologies that support them. While compressors have been a staple in industrial applications for providing compressed air for various processes, alternative solutions are becoming increasingly viable. These alternatives can help businesses optimize operations, reduce costs, and improve efficiency. In this analysis, we will compare air compressors with two notable alternatives: pneumatic systems powered by fans and hydraulic systems.
Comparison Table of Industrial Solutions
Comparison Aspect | Compressor In Industry | Pneumatic Systems (Fans) | Hydraulic Systems |
---|---|---|---|
Performance | High pressure and volume output; continuous operation | Moderate pressure; best for light-duty applications | High pressure; suitable for heavy-duty tasks |
Cost | Higher initial investment; long-term savings possible | Lower initial cost; can incur high operating costs | Moderate to high initial cost; variable operating costs |
Ease of Implementation | Requires installation and setup; often complex | Simple to install; minimal training required | Requires skilled personnel for setup; more complex |
Maintenance | Regular maintenance needed; can be costly | Low maintenance; less frequent service required | High maintenance; requires specialized knowledge |
Best Use Case | Suitable for manufacturing, automotive, and HVAC industries | Ideal for light applications like cooling and ventilation | Best for heavy machinery and applications requiring high force |
Detailed Breakdown of Alternatives
What Are the Advantages and Disadvantages of Pneumatic Systems?
Pneumatic systems powered by fans use air flow to accomplish tasks like cooling and light material transport. They are simpler to implement compared to compressors, making them attractive for businesses with limited resources. The lower initial cost and minimal maintenance required are significant advantages. However, their performance is limited to lower pressures and volumes, making them less suitable for heavy-duty industrial tasks. In industries where high precision and power are necessary, pneumatic systems may not provide adequate performance.
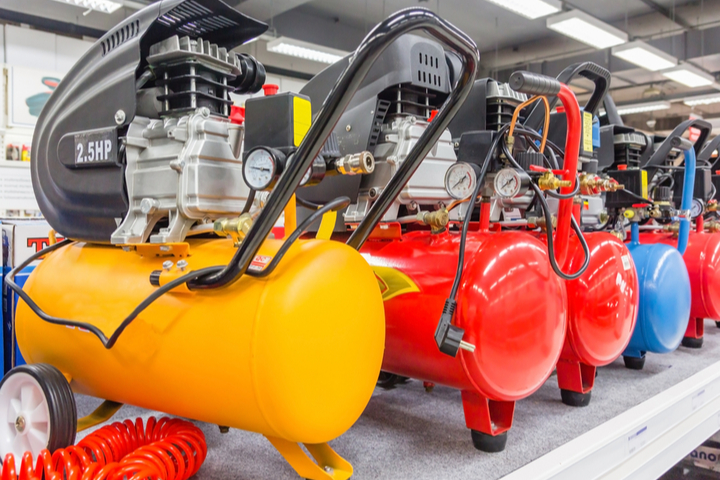
A stock image related to compressor in industry.
How Do Hydraulic Systems Compare in Industrial Applications?
Hydraulic systems utilize fluid pressure to generate force, making them ideal for heavy machinery and applications requiring high torque. They can operate at much higher pressures than pneumatic systems, which allows for more powerful and efficient operation in demanding environments. However, hydraulic systems can be costly to implement and maintain, requiring skilled technicians for setup and service. Their maintenance can also be intensive due to the complexity of fluid dynamics and potential leaks. This makes them more suitable for industries like construction and manufacturing, where heavy lifting is essential.
Conclusion: How Should B2B Buyers Choose the Right Solution?
When selecting between compressors and their alternatives, B2B buyers should carefully assess their operational needs and constraints. Consider factors such as the required pressure and volume, initial investment versus long-term costs, and the complexity of installation and maintenance. For industries focused on high-volume air delivery, compressors remain the best choice. However, for lighter applications or scenarios where initial costs need to be minimized, pneumatic systems may suffice. Conversely, hydraulic systems are optimal for heavy-duty tasks requiring significant force but come with higher costs and maintenance requirements. By aligning their choice with specific operational goals, B2B buyers can enhance efficiency and productivity in their industrial processes.
Essential Technical Properties and Trade Terminology for compressor in industry
What Are the Essential Technical Properties of Compressors in Industry?
When considering a compressor for industrial applications, understanding its technical properties is critical for making informed purchasing decisions. Here are some of the key specifications that B2B buyers should prioritize:
1. Operating Pressure (PSI)
Operating pressure, measured in pounds per square inch (PSI), indicates the maximum pressure the compressor can achieve. Different applications require varying PSI levels; for instance, automotive or manufacturing operations may demand higher pressures. Understanding your operational needs can help you select a compressor that enhances efficiency and productivity.
2. Cubic Feet per Minute (CFM)
CFM measures the volume of air a compressor can deliver per minute. This specification is crucial for determining whether a compressor can meet the demands of your tools and processes. It’s advisable to calculate the total CFM required by all tools in use and add a buffer (typically 30%) to ensure adequate supply during peak operations.
3. Tank Size (Gallons)
The size of the receiver tank is essential for the compressor’s performance, as it determines how much compressed air can be stored for immediate use. Smaller tanks are suitable for applications requiring short bursts of air, while larger tanks are necessary for extended operations. Selecting the right tank size can lead to better performance and reduced downtime.
4. Motor Power (HP)
Motor power, typically measured in horsepower (HP), indicates the strength of the compressor’s motor. A higher HP rating often correlates with greater efficiency and the ability to handle more demanding applications. Buyers should evaluate their specific requirements to ensure they choose a compressor with adequate motor power for their needs.
5. Energy Efficiency Rating
Energy efficiency is becoming increasingly important in industrial settings, not just for cost savings but also for sustainability initiatives. Compressors with high energy efficiency ratings can significantly reduce operational costs over time. Look for models that offer variable speed drives or energy-efficient technologies.
What Are Common Trade Terms Related to Industrial Compressors?
Familiarity with industry jargon can facilitate smoother negotiations and better understanding of contractual obligations. Here are some essential trade terms to know:
1. Original Equipment Manufacturer (OEM)
An OEM refers to a company that produces parts or equipment that may be marketed by another manufacturer. In the context of compressors, understanding whether you are dealing with an OEM or a third-party supplier can impact warranty, support, and product quality.
2. Minimum Order Quantity (MOQ)
MOQ is the smallest quantity of a product that a supplier is willing to sell. This term is particularly relevant for bulk purchases of compressors or parts. Knowing the MOQ helps buyers plan their procurement strategy and budget accordingly.
3. Request for Quotation (RFQ)
An RFQ is a document sent to suppliers requesting pricing information for specific products or services. It’s a crucial step in the buying process, allowing buyers to compare costs and terms from different suppliers. A well-structured RFQ can lead to more favorable pricing and terms.
4. Incoterms
International Commercial Terms (Incoterms) define the responsibilities of buyers and sellers in international transactions. Understanding these terms is vital for B2B buyers, especially when importing compressors from different regions. They specify aspects like shipping, insurance, and risk transfer, which can significantly impact total cost and delivery timelines.
5. Warranty Period
The warranty period is the duration for which the manufacturer guarantees the performance of the compressor. Understanding the warranty terms can help buyers assess the long-term reliability of their investment and plan for potential service needs.
By grasping these technical specifications and trade terms, international B2B buyers can make more informed decisions, optimize their procurement strategies, and enhance operational efficiency in their respective industries.
Navigating Market Dynamics and Sourcing Trends in the compressor in industry Sector
What Are the Current Market Dynamics and Key Trends in the Compressor Industry?
The global compressor market is witnessing significant growth, driven by the increasing demand across various sectors, including automotive, food and beverage, pharmaceuticals, and manufacturing. With the rise of automation and the need for efficient production processes, air compressors are becoming essential tools for improving productivity and precision. For international B2B buyers from regions like Africa, South America, the Middle East, and Europe, understanding these dynamics is crucial.
Emerging technologies, such as IoT-enabled compressors, are enhancing operational efficiency by allowing real-time monitoring and predictive maintenance. Additionally, the trend towards energy-efficient models is reshaping the market, as companies seek to reduce operational costs and comply with stringent environmental regulations. Buyers should focus on suppliers that offer advanced features, such as variable speed drives, which can significantly lower energy consumption while maintaining performance.
Furthermore, the market is becoming increasingly competitive, with manufacturers focusing on customization and flexibility in their offerings. For B2B buyers, this means greater choice and the ability to tailor solutions to specific operational needs. Understanding local market conditions, such as supply chain challenges and regulatory requirements, will be pivotal in making informed sourcing decisions.
How Is Sustainability and Ethical Sourcing Impacting the Compressor Industry?
Sustainability is no longer a secondary consideration in the compressor industry; it has become a primary focus for many manufacturers and buyers alike. The environmental impact of compressor operations, particularly in terms of energy consumption and emissions, is prompting companies to seek eco-friendly solutions. This shift is evident in the growing demand for compressors that comply with energy efficiency standards and utilize environmentally friendly refrigerants.
Ethical sourcing is also gaining traction, as buyers increasingly prioritize suppliers who demonstrate commitment to sustainability and social responsibility. This includes ensuring fair labor practices and minimizing environmental harm throughout the supply chain. Certifications such as ISO 14001 (Environmental Management) and ISO 50001 (Energy Management) are becoming essential indicators of a supplier’s commitment to sustainability.
For B2B buyers, investing in sustainable and ethically sourced compressors not only aligns with corporate social responsibility goals but also enhances brand reputation in an increasingly eco-conscious market. By choosing suppliers with recognized ‘green’ certifications, businesses can contribute to a more sustainable future while enjoying the long-term cost savings associated with energy-efficient technologies.
How Has the Compressor Industry Evolved Over Time?
The compressor industry has undergone a remarkable evolution since its inception. Initially, air compressors were simple, mechanical devices designed for basic tasks. Over the decades, technological advancements have transformed these machines into sophisticated systems capable of meeting the diverse needs of various industries.
The introduction of rotary screw compressors in the mid-20th century marked a significant milestone, allowing for continuous operation and higher efficiency. As industries expanded and automation became prevalent, the demand for more powerful and versatile compressors grew. Today, innovations such as digital controls, IoT integration, and energy-efficient designs dominate the landscape, ensuring that compressors not only meet the functional requirements but also align with sustainability goals.
For international B2B buyers, understanding this evolution provides insight into the capabilities and reliability of modern compressors, enabling them to make informed purchasing decisions that cater to their specific operational needs.
Frequently Asked Questions (FAQs) for B2B Buyers of compressor in industry
-
How do I solve issues with air compressor inefficiency?
To address air compressor inefficiency, first assess your system’s airflow and pressure requirements. Identify if the compressor is oversized or undersized, as this can lead to energy waste. Regular maintenance is crucial; check for leaks in the piping and ensure filters are clean. Upgrading to energy-efficient models or implementing variable speed drives can also enhance performance. Lastly, consider conducting an air audit to pinpoint specific areas for improvement and align your compressor’s capabilities with operational demands. -
What is the best type of compressor for industrial applications?
The best type of compressor for industrial applications largely depends on your specific needs. Rotary screw compressors are ideal for large-scale operations due to their continuous airflow and efficiency. For smaller applications, reciprocating compressors may suffice. If your operations require high pressure, consider two-stage compressors. Evaluate factors like required CFM, operating pressure, and whether you need a portable or stationary unit to make an informed choice. -
What factors should I consider when sourcing compressors internationally?
When sourcing compressors internationally, consider the supplier’s reputation, compliance with international standards, and their ability to meet your specific needs. Evaluate their manufacturing capabilities and certifications to ensure product quality. Additionally, assess logistics and shipping costs, lead times, and potential customs duties. Establish clear communication regarding payment terms, after-sales support, and warranty conditions to mitigate risks and ensure a smooth procurement process. -
How can I effectively vet suppliers for compressors?
To effectively vet suppliers for compressors, start by researching their track record and customer reviews. Request references from previous clients to gauge their reliability and service quality. Verify certifications and compliance with industry standards. Conduct site visits if possible or utilize third-party inspection services to assess manufacturing practices. Additionally, evaluate their responsiveness to inquiries and ability to provide technical support, which are crucial for long-term partnerships. -
What are typical payment terms for international compressor purchases?
Payment terms for international compressor purchases can vary widely. Common terms include payment in advance, letters of credit, or net 30-60 days after shipment. Negotiate terms that suit both parties, considering factors like order size and supplier trustworthiness. Some suppliers may offer discounts for upfront payments or bulk orders. Ensure clarity in terms regarding currency exchange rates and potential transaction fees to avoid surprises during payment. -
How can I customize a compressor to meet my specific industrial needs?
Customizing a compressor involves discussing your specific requirements with the manufacturer. Consider factors such as desired pressure levels, airflow capacity, and any unique operational needs. Many suppliers offer customization options, including tank size, motor type, and control systems. Be prepared to provide detailed specifications and, if necessary, collaborate on design modifications. Ensure that any changes comply with safety and regulatory standards for your industry. -
What are the minimum order quantities (MOQ) for compressors?
Minimum order quantities (MOQ) for compressors can differ significantly based on the supplier and the specific model. Some manufacturers may allow smaller orders, especially for standard models, while customized or specialized compressors may have higher MOQs due to production costs. Always clarify MOQ during negotiations, and consider grouping orders with other companies or future needs to meet supplier requirements without overcommitting. -
How can I ensure quality assurance (QA) for my compressor purchase?
To ensure quality assurance (QA) for your compressor purchase, request detailed specifications and quality control processes from the supplier. Verify if the manufacturer follows international quality standards, such as ISO certifications. Consider requesting product samples or conducting pre-shipment inspections to confirm compliance with your requirements. Establish a clear return policy and warranty terms to safeguard against defects or performance issues post-purchase. Regular maintenance and servicing will also help maintain quality over time.
Important Disclaimer & Terms of Use
⚠️ Important Disclaimer
The information provided in this guide, including content regarding manufacturers, technical specifications, and market analysis, is for informational and educational purposes only. It does not constitute professional procurement advice, financial advice, or legal advice.
While we have made every effort to ensure the accuracy and timeliness of the information, we are not responsible for any errors, omissions, or outdated information. Market conditions, company details, and technical standards are subject to change.
B2B buyers must conduct their own independent and thorough due diligence before making any purchasing decisions. This includes contacting suppliers directly, verifying certifications, requesting samples, and seeking professional consultation. The risk of relying on any information in this guide is borne solely by the reader.
Strategic Sourcing Conclusion and Outlook for compressor in industry
In today’s competitive industrial landscape, strategic sourcing of air compressors is paramount for optimizing operational efficiency and reducing costs. By understanding the specific requirements of your industry—be it automotive, pharmaceutical, or food and beverage—B2B buyers can make informed decisions that align with their production needs. Emphasizing the importance of factors such as operating pressure, CFM requirements, and energy efficiency can lead to significant long-term savings and enhanced productivity.
Investing in the right type of compressor, whether it be a rotary screw for high-demand environments or a portable model for flexibility, can streamline processes and improve output quality. As industries across Africa, South America, the Middle East, and Europe continue to evolve, the demand for efficient, reliable compressed air solutions will only grow.
International B2B buyers are encouraged to assess their current and future needs meticulously and engage with reputable suppliers who understand the nuances of their specific markets. By prioritizing strategic sourcing now, businesses can position themselves for success in an increasingly dynamic global economy. Embrace the power of compressed air and secure your competitive advantage today.