The Ultimate Guide to Us Electrical Plug (2025)
Introduction: Navigating the Global Market for us electrical plug
Navigating the global market for US electrical plugs presents unique challenges for international B2B buyers. Understanding the intricacies of sourcing the correct plug types—especially when dealing with equipment that requires type A or type B plugs—can significantly impact operational efficiency and safety. This guide delves into essential aspects such as the different plug types, voltage specifications, and the necessity of travel adapters, which are crucial for businesses looking to import US appliances or equipment.
International buyers from regions like Africa, South America, the Middle East, and Europe, including Germany and Thailand, will find this comprehensive resource invaluable. It not only outlines the specific applications and compatibility of US electrical plugs but also provides actionable insights into supplier vetting processes, cost considerations, and compliance with local regulations. By equipping buyers with the knowledge to make informed purchasing decisions, this guide aims to streamline the procurement process and mitigate risks associated with electrical compatibility.
In an increasingly interconnected world, ensuring that your equipment functions seamlessly across borders is critical. This guide empowers you to navigate the complexities of the US electrical plug market with confidence, ensuring that your business remains competitive and compliant in various international landscapes.
Understanding us electrical plug Types and Variations
Type Name | Key Distinguishing Features | Primary B2B Applications | Brief Pros & Cons for Buyers |
---|---|---|---|
Type A | Two flat parallel pins | Small appliances, chargers | Pros: Widely used, low cost. Cons: No grounding, less safe for high-power devices. |
Type B | Two flat parallel pins and one round pin | Heavy-duty appliances, computers | Pros: Grounded design enhances safety. Cons: Slightly bulkier, may not fit in all outlets. |
Type C | Two round pins | International devices, light appliances | Pros: Common in Europe, versatile. Cons: Requires adapter for US use, no grounding. |
Type D | Three round pins | Industrial equipment, larger devices | Pros: High safety with grounding. Cons: Not common in the US, requires adapters. |
Universal | Multiple plug types in one | Travel, diverse electronics | Pros: Flexibility across regions. Cons: May not support high wattage, can be bulky. |
What Are the Characteristics of Type A Plugs?
Type A plugs feature two flat parallel pins and are primarily used for low-power devices such as chargers and small appliances. They are prevalent in the United States, making them a go-to choice for B2B buyers sourcing products for the American market. When purchasing, consider the absence of grounding, which may pose risks when used with high-power equipment. This plug type is cost-effective and widely available, but its lack of safety features makes it less suitable for industrial applications.
How Do Type B Plugs Enhance Safety?
Type B plugs include two flat parallel pins and a grounding pin, making them ideal for high-power and heavy-duty appliances like computers and machinery. The grounding feature significantly reduces the risk of electrical shock, which is crucial for businesses that rely on safe operations. Buyers should ensure compatibility with their equipment and consider the slightly larger size when integrating these plugs into existing systems. While they are more secure than Type A plugs, they may not be compatible with all sockets, necessitating the use of adapters in some cases.
Why Are Type C Plugs Commonly Used in International Markets?
Type C plugs, characterized by their two round pins, are prevalent in many countries outside the US, particularly in Europe. They are often found in lightweight appliances and are a preferred choice for B2B transactions involving international devices. Buyers should be aware that while Type C plugs are versatile, they require a travel adapter for use in the US, which can add to overall costs. Their lack of grounding is another consideration for safety-conscious businesses.
What Are the Applications of Type D Plugs in Industry?
Type D plugs, featuring three round pins, are primarily used in industrial settings for larger equipment that demands a higher safety standard. Their grounded design provides additional protection, making them suitable for heavy-duty applications. B2B buyers should evaluate the availability of Type D sockets in their operational regions since they are not common in the US. The need for adapters may complicate logistics, but the safety benefits can outweigh these challenges.
How Do Universal Adapters Benefit International Buyers?
Universal adapters accommodate multiple plug types, making them ideal for international travel and diverse electronics. They are particularly useful for B2B buyers who engage in global trade and need to ensure compatibility across various regions. While these adapters offer flexibility, businesses should consider their power ratings, as some may not support high wattage devices. Additionally, their bulkiness can be a drawback for compact setups, but the convenience they provide can be invaluable for frequent travelers or multinational companies.
Key Industrial Applications of us electrical plug
Industry/Sector | Specific Application of US Electrical Plug | Value/Benefit for the Business | Key Sourcing Considerations for this Application |
---|---|---|---|
Manufacturing | Machinery and Equipment Power Supply | Ensures reliable operation of equipment | Verify compatibility with voltage and frequency standards. |
Hospitality | Guest Room Electrical Outlets | Enhances guest experience with accessible power | Consider local regulations for safety and accessibility. |
Information Technology | Server and Data Center Power Supply | Supports continuous operation of critical systems | Ensure redundancy and compliance with electrical standards. |
Construction | Temporary Power for Tools and Equipment | Facilitates efficient project execution | Check for ruggedness and suitability for outdoor use. |
Healthcare | Medical Equipment Power Supply | Vital for patient care and operational efficiency | Source equipment that meets safety and regulatory standards. |
How is the US Electrical Plug Used in Manufacturing?
In the manufacturing sector, the US electrical plug is critical for powering machinery and equipment. It ensures that devices operate consistently at the standard voltage of 120V and frequency of 60Hz, which is essential for production efficiency. International buyers must ensure that any machinery sourced is compatible with these specifications, as mismatched voltage can lead to equipment damage or failure. Additionally, it’s crucial to assess the durability of plugs and sockets used in high-demand environments.
What Role Does the US Electrical Plug Play in the Hospitality Industry?
In the hospitality sector, US electrical plugs are essential for guest room outlets, allowing visitors to charge devices easily. This convenience enhances the overall guest experience, which is vital for customer satisfaction and repeat business. When sourcing, buyers should consider the placement of outlets for accessibility and compliance with local safety regulations. Additionally, ensuring that the plugs accommodate various device types can further improve guest services.
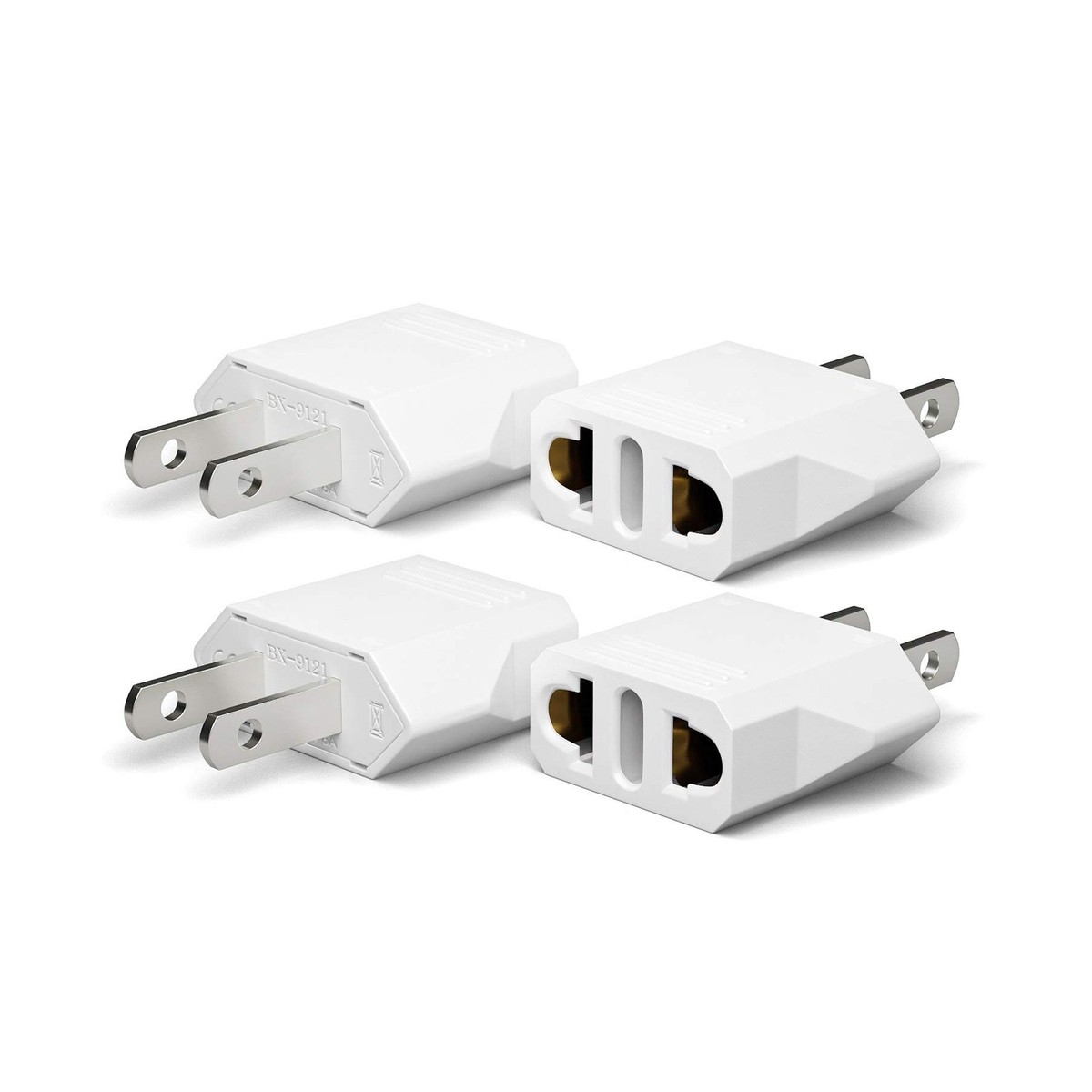
A stock image related to us electrical plug.
Why is the US Electrical Plug Important for Information Technology?
For the information technology sector, the US electrical plug is vital for powering servers and data centers. These facilities require a stable power supply to maintain continuous operations and prevent downtime. International B2B buyers should prioritize sourcing equipment that adheres to electrical standards and offers redundancy options, such as backup power solutions. Understanding the specific power requirements of IT equipment can also help in selecting the right plugs and sockets.
How Does the US Electrical Plug Facilitate Construction Projects?
In construction, the US electrical plug is often used for providing temporary power to tools and equipment at job sites. This flexibility allows for efficient project execution, as workers can operate various power tools without delays. Buyers in this sector should consider sourcing rugged and weather-resistant plugs and sockets that can withstand outdoor conditions. Furthermore, compliance with safety standards is critical to ensure worker safety during operations.
What is the Significance of the US Electrical Plug in Healthcare?
In the healthcare industry, the US electrical plug is indispensable for powering medical equipment, which is crucial for patient care. The reliability of electrical supply directly impacts operational efficiency in hospitals and clinics. Buyers must source equipment that meets stringent safety and regulatory standards to ensure patient safety. Additionally, understanding the specific power requirements of medical devices is essential for selecting the appropriate plugs and sockets.
3 Common User Pain Points for ‘us electrical plug’ & Their Solutions
Scenario 1: Difficulty in Sourcing the Right Adapters for US Electrical Plugs
The Problem:
Many international B2B buyers face the challenge of sourcing the appropriate travel adapters for US electrical plugs, particularly when dealing with multiple clients across different regions. For example, a company in Africa might need to send equipment to the US, but the electrical specifications differ, leading to confusion about which adapters are needed. This can result in delays in project timelines, increased costs, and ultimately, dissatisfaction among clients who rely on timely service delivery.
The Solution:
To mitigate this issue, businesses should conduct thorough research on the specific plug types used in the United States—Type A and Type B. B2B buyers should establish relationships with reputable suppliers who can provide high-quality adapters tailored for US sockets. When sourcing, consider investing in universal travel adapters that accommodate multiple plug types, as this not only streamlines operations but also prepares for future projects in different regions. Additionally, having a checklist of the electrical specifications required for each project can simplify the process and ensure compliance with local regulations.
Scenario 2: Voltage Compatibility Issues with Electrical Appliances
The Problem:
Another common pain point arises when international buyers attempt to use appliances designed for different voltage systems. For instance, a company in South America may wish to utilize equipment rated at 220V in the US, where the standard is 120V. This mismatch can lead to equipment malfunction or damage, resulting in costly repairs and downtime.
The Solution:
Buyers should carefully review the voltage ratings of their appliances before shipping them to the US. For dual voltage appliances (typically marked with an input range of 100-240V), only a plug adapter is needed, allowing them to operate safely on a 120V system. If the appliances are single voltage and not compatible, a voltage converter must be procured. It is crucial to choose converters with appropriate wattage ratings to ensure they can handle the power requirements of the appliances. Keeping a detailed inventory of equipment along with their voltage specifications can also streamline this process and prevent future issues.
Scenario 3: Misunderstanding Electrical Safety Standards
The Problem:
Electrical safety standards can vary significantly between countries, leading to serious compliance issues for B2B buyers. For example, a business from Europe may not be aware that certain types of adapters are not suited for appliances requiring earth connections, which could pose a safety risk. This lack of understanding can lead to accidents, equipment damage, and regulatory fines.
The Solution:
It is essential for international buyers to familiarize themselves with US electrical safety standards before purchasing or using adapters and plugs. Consulting resources such as the National Electrical Code (NEC) or working with local compliance experts can provide clarity on necessary safety requirements. Additionally, ensuring that all adapters used comply with UL (Underwriters Laboratories) safety standards can help mitigate risks. B2B buyers should also invest in training for their staff to recognize and adhere to these standards, thus fostering a culture of safety and compliance in their operations.
Strategic Material Selection Guide for us electrical plug
When selecting materials for US electrical plugs, it is essential to consider various factors that influence performance, durability, and compliance with international standards. Below, we analyze four common materials used in the manufacturing of US electrical plugs, focusing on their properties, advantages, disadvantages, and specific considerations for international B2B buyers.
What Are the Key Properties of Polycarbonate in US Electrical Plugs?
Polycarbonate is a popular choice for the casing of electrical plugs due to its excellent impact resistance and thermal stability. It can withstand temperatures ranging from -40°C to 120°C, making it suitable for various environments. Additionally, polycarbonate has good electrical insulating properties, which is critical for safety in electrical applications.
Pros & Cons: Polycarbonate is known for its durability and lightweight nature, which makes it easier to handle during manufacturing. However, it can be more expensive than other plastics, potentially increasing production costs. Its manufacturing complexity is moderate, as it requires specific molding techniques.
Impact on Application: Polycarbonate plugs are compatible with a wide range of electrical devices, ensuring safety and performance. They are particularly effective in environments where mechanical stress and temperature fluctuations are common.
Considerations for International Buyers: Buyers from regions like Europe and the Middle East should ensure that polycarbonate plugs comply with relevant standards such as IEC 60884-1. Additionally, they should consider the environmental regulations regarding plastic use in their respective countries.
How Does PVC Contribute to the Performance of US Electrical Plugs?
Polyvinyl Chloride (PVC) is frequently used for insulation in electrical plugs due to its excellent electrical properties and resistance to moisture and chemicals. PVC can operate effectively in temperatures ranging from -10°C to 70°C.
Pros & Cons: The primary advantage of PVC is its low cost and ease of manufacturing, making it a cost-effective option for mass production. However, PVC is less durable than materials like polycarbonate and may degrade over time when exposed to UV light or extreme temperatures.
Impact on Application: PVC insulation is suitable for indoor applications but may not be ideal for outdoor use where exposure to sunlight and extreme weather conditions is a concern.
Considerations for International Buyers: Buyers in Africa and South America should be aware of local regulations regarding the use of PVC, particularly concerning environmental concerns and recycling. Compliance with standards such as ASTM D256 and ASTM D638 is also crucial.
Why Is Thermoplastic Elastomer (TPE) Preferred for Flexible Plugs?
Thermoplastic Elastomer (TPE) is often selected for flexible components of electrical plugs due to its rubber-like properties. TPE can endure temperature variations from -40°C to 90°C and offers excellent flexibility and resilience.
Pros & Cons: TPE provides superior flexibility and is more resistant to wear and tear compared to traditional plastics. However, it can be more expensive and complex to manufacture, which may not be suitable for all production scales.
Impact on Application: TPE is particularly beneficial in applications requiring frequent plugging and unplugging, as it can withstand repeated mechanical stress without losing its shape.
Considerations for International Buyers: Buyers from regions with stringent safety regulations, such as Germany, should ensure that TPE materials meet relevant standards like DIN EN 60529 for ingress protection.
What Are the Benefits of Using Copper in Electrical Contacts?
Copper is the standard material for electrical contacts within plugs due to its excellent electrical conductivity and corrosion resistance. It can handle high current loads, making it ideal for various electrical applications.
Pros & Cons: The primary advantage of copper is its superior conductivity, which ensures efficient power transfer. However, copper is susceptible to oxidation, which can affect performance over time. Additionally, it is more expensive than alternatives like aluminum.
Impact on Application: Copper contacts are essential for high-performance applications where reliability and efficiency are critical. They are commonly used in plugs designed for heavy-duty electrical devices.
Considerations for International Buyers: Buyers should ensure that copper components comply with international standards such as JIS C 8303 for electrical connectors. Understanding the local market’s preferences for copper quality is also essential.
Summary of Material Selection for US Electrical Plugs
Material | Typical Use Case for US Electrical Plug | Key Advantage | Key Disadvantage/Limitation | Relative Cost (Low/Med/High) |
---|---|---|---|---|
Polycarbonate | Casing for plugs | Excellent impact resistance | Higher cost than other plastics | High |
PVC | Insulation for indoor plugs | Low cost and easy to manufacture | Less durable, UV degradation | Low |
Thermoplastic Elastomer | Flexible components | Superior flexibility | Higher manufacturing complexity | Medium |
Copper | Electrical contacts | Excellent conductivity | Susceptible to oxidation | High |
This guide provides a comprehensive overview of material selection for US electrical plugs, enabling international B2B buyers to make informed decisions based on performance, cost, and compliance with local regulations.
In-depth Look: Manufacturing Processes and Quality Assurance for us electrical plug
What Are the Key Manufacturing Processes for US Electrical Plugs?
The manufacturing of US electrical plugs involves several critical stages that ensure the final product meets safety and performance standards. Understanding these stages can help B2B buyers assess potential suppliers and ensure they are sourcing high-quality products.
How Are Materials Prepared for Electrical Plug Manufacturing?
The first stage in the manufacturing process is material preparation. US electrical plugs are typically made from high-grade thermoplastics and conductive metals, such as copper or brass. The selection of materials is crucial, as they must meet specific electrical and thermal properties to ensure safety and durability.
- Material Selection: Manufacturers often source materials that comply with UL (Underwriters Laboratories) and IEC (International Electrotechnical Commission) standards. Buyers should inquire about the certifications of materials used.
- Testing Raw Materials: Before production begins, raw materials undergo rigorous testing to check for impurities and consistency. This ensures that the final product will perform reliably under various conditions.
What Are the Main Forming Techniques Used in Electrical Plug Production?
Once materials are prepared, the next step involves forming the components of the plug. This includes molding and stamping processes that shape the plastic housing and metal contacts.
- Injection Molding: This is a common technique used to create the plastic casing of the plugs. Manufacturers inject molten plastic into molds, which are then cooled to form the desired shape. This process allows for high precision and the ability to produce complex designs.
- Metal Stamping: The metal prongs of the plugs are usually produced through stamping. Sheets of metal are cut and shaped using dies, ensuring uniformity and strength.
How Is the Assembly of Electrical Plugs Conducted?
After forming, the next phase is assembly, where the various components are put together.
- Automated Assembly Lines: Many manufacturers use automated systems to assemble plugs, which enhances efficiency and consistency. Robots may be employed to insert metal contacts into the plastic housing, reducing human error.
- Manual Assembly: In some cases, skilled workers are involved in assembly, particularly for quality-sensitive tasks. This dual approach allows manufacturers to maintain high standards.
What Finishing Processes Are Involved in Electrical Plug Manufacturing?
Finishing processes enhance the aesthetic and functional qualities of the plugs.
- Surface Treatments: Plugs may undergo surface treatments such as plating or coating to improve corrosion resistance and conductivity of the metal parts. This is particularly important for plugs that will be used in humid environments.
- Final Inspection: After assembly and finishing, plugs go through a final inspection to ensure they meet all specifications and safety standards before packaging.
What Quality Assurance Standards Are Relevant for US Electrical Plugs?
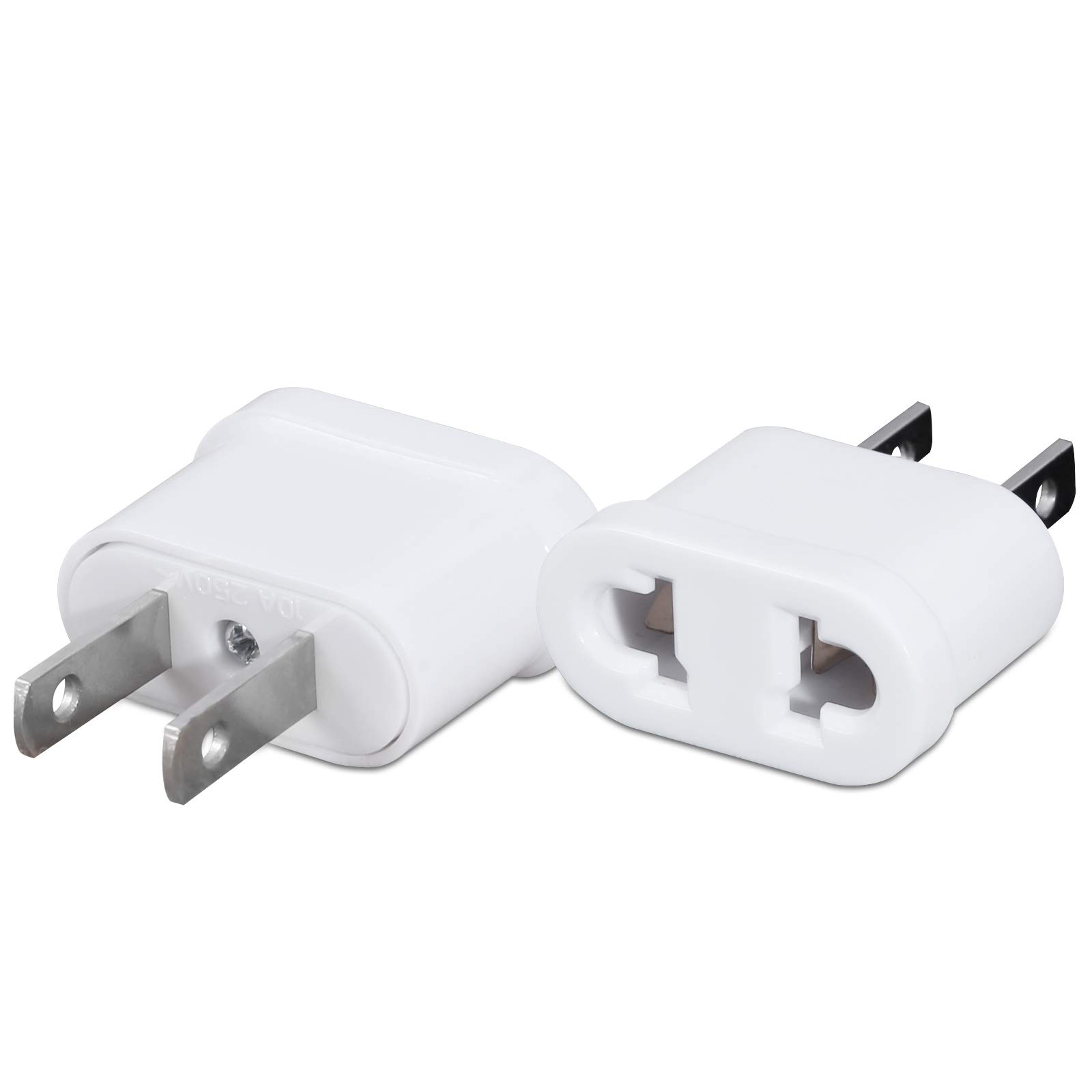
A stock image related to us electrical plug.
Quality assurance (QA) is a critical aspect of manufacturing US electrical plugs. Adhering to international and industry-specific standards ensures that products are safe for consumer use.
Which International Standards Should B2B Buyers Be Aware Of?
For international buyers, understanding the key QA standards can help in evaluating suppliers.
- ISO 9001: This is a widely recognized standard for quality management systems (QMS). Manufacturers adhering to ISO 9001 demonstrate their commitment to quality control processes.
- CE Marking: For buyers in Europe, CE marking indicates compliance with health, safety, and environmental protection standards. It is essential for ensuring that products can be sold in the European market.
- UL Certification: This is particularly relevant for US markets, as UL certifies that electrical products meet specific safety standards.
What Are the Key QC Checkpoints in Electrical Plug Manufacturing?
Throughout the manufacturing process, several quality control (QC) checkpoints are critical for ensuring product reliability.
- Incoming Quality Control (IQC): This initial inspection phase involves checking raw materials upon arrival at the manufacturing facility. This step is crucial for preventing defective materials from entering production.
- In-Process Quality Control (IPQC): During production, IPQC involves monitoring processes to identify any deviations from standards. This may include checking dimensions, weights, and electrical properties of the components.
- Final Quality Control (FQC): Before products are packaged, they undergo a final inspection to ensure they meet all specifications and are free from defects.
How Can B2B Buyers Verify Supplier Quality Control?
To ensure that suppliers maintain high-quality standards, B2B buyers should take proactive steps in verifying their QC processes.
What Auditing Methods Can Be Used to Assess Supplier Quality?
- Supplier Audits: Conducting regular audits of suppliers can help buyers assess their quality systems and adherence to international standards. This includes reviewing documentation, observing production processes, and inspecting finished products.
- Quality Reports: Requesting detailed QC reports from suppliers can provide insights into their processes and any corrective actions taken in case of deviations.
- Third-Party Inspections: Engaging third-party inspection agencies can provide an unbiased assessment of supplier quality. These agencies can conduct random inspections and provide certifications based on their findings.
What Are the QC and Certification Nuances for International B2B Buyers?
B2B buyers from diverse regions, such as Africa, South America, the Middle East, and Europe, must be aware of specific nuances in QC and certification.
- Regional Compliance: Different regions may have varying compliance requirements. For instance, the Middle East may require compliance with the Gulf Standards Organization (GSO), while European buyers look for CE marking.
- Understanding Local Regulations: Buyers should familiarize themselves with local regulations regarding electrical products. In some cases, additional testing may be required to meet national standards.
- Cultural Considerations: Building trust with suppliers from different cultures can enhance collaboration. Understanding local business practices and communication styles is vital for successful partnerships.
By considering these manufacturing processes and quality assurance measures, B2B buyers can make informed decisions when sourcing US electrical plugs, ensuring they receive reliable and compliant products for their markets.
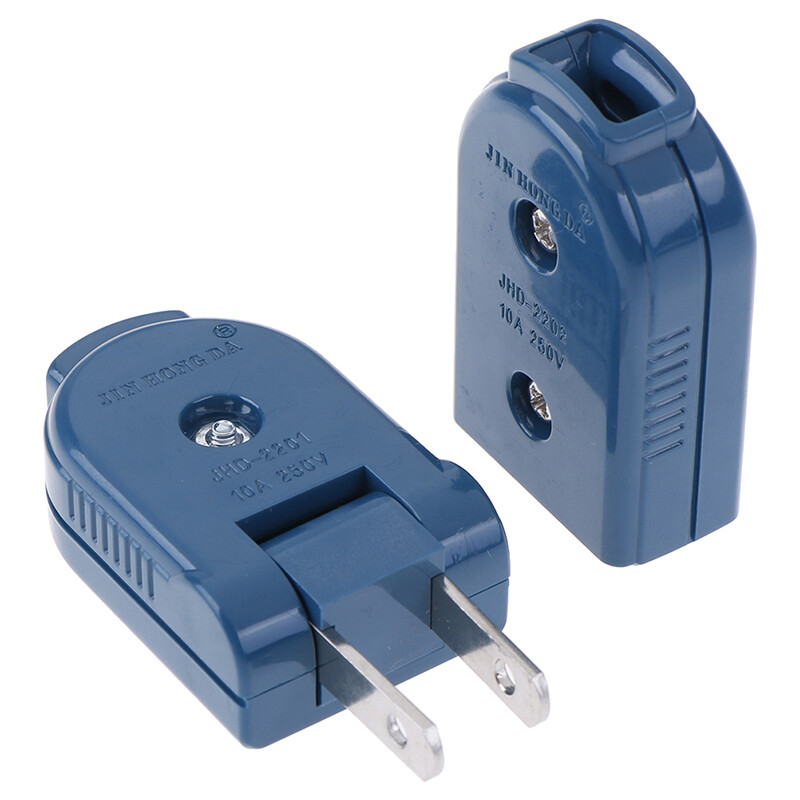
A stock image related to us electrical plug.
Practical Sourcing Guide: A Step-by-Step Checklist for ‘us electrical plug’
In the global marketplace, sourcing electrical plugs that meet US standards is crucial for international B2B buyers. This guide provides a practical checklist to ensure you procure the correct US electrical plugs effectively, considering the unique requirements of your region and the specific standards applicable in the United States.
Step 1: Define Your Technical Specifications
Establishing clear technical specifications is the first step in sourcing US electrical plugs. You need to identify whether you require Type A or Type B plugs, based on your target market’s needs. Consider the voltage requirements (120V) and frequency (60Hz) of the devices you plan to use, as these factors influence compatibility.
Step 2: Research Regulatory Compliance
Understanding regulatory requirements in the US is essential for ensuring your products are market-ready. Check for certifications such as UL (Underwriters Laboratories) or ETL (Electrical Testing Laboratories), which indicate that the plugs meet safety standards. Compliance not only facilitates smoother entry into the market but also builds trust with your customers.
Step 3: Evaluate Potential Suppliers
Before committing to a supplier, conducting thorough evaluations is crucial. Review company profiles, ask for case studies, and seek references from businesses in similar sectors or regions. This vetting process helps you gauge the reliability and reputation of potential suppliers, ensuring you choose partners that can meet your quality and delivery expectations.
Step 4: Request Samples for Testing
Once you have shortlisted suppliers, request samples of the US electrical plugs. Testing these samples for quality, durability, and compatibility with your devices is essential. Ensure that they can withstand local conditions and adhere to safety standards. This step will help you avoid costly mistakes down the line.
Step 5: Negotiate Terms and Conditions
Engage in negotiations regarding pricing, payment terms, and delivery schedules. It’s important to clarify the minimum order quantities, lead times, and any potential penalties for delays. Establishing clear terms helps mitigate risks and ensures that both parties have aligned expectations, which is especially important in B2B transactions.
Step 6: Plan for Logistics and Distribution
Consider the logistics of transporting the plugs from the supplier to your location. Evaluate shipping options, customs regulations, and potential tariffs that may affect your overall cost. Developing a logistics plan ensures that you can deliver products efficiently to your customers, which is vital for maintaining a competitive edge.
Step 7: Monitor Supplier Performance
After placing orders, continuously monitor your supplier’s performance regarding product quality and delivery timelines. Establish feedback mechanisms to address any issues promptly. Regular communication helps build a strong partnership and ensures that your sourcing strategy remains effective over time.
By following these steps, international B2B buyers can confidently navigate the complexities of sourcing US electrical plugs, ensuring they meet both technical specifications and market regulations. This strategic approach ultimately leads to better product offerings and enhanced customer satisfaction.
Comprehensive Cost and Pricing Analysis for us electrical plug Sourcing
What Are the Key Cost Components for Sourcing US Electrical Plugs?
Understanding the cost structure of US electrical plug sourcing is crucial for international B2B buyers. The main cost components include:
-
Materials: The choice of raw materials significantly influences costs. Common materials for electrical plugs include thermoplastics for the casing and copper for the pins. Buyers should consider the quality of materials, as higher-grade materials may incur additional costs but lead to better durability and safety.
-
Labor: Labor costs vary by region. For instance, manufacturing in countries with higher wage standards can increase the overall price. However, countries with lower labor costs may offer cheaper options, albeit with potential trade-offs in quality and compliance with safety standards.
-
Manufacturing Overhead: This includes expenses related to factory operations, utilities, and administrative costs. Efficient manufacturing processes can help reduce these overheads, impacting the final price.
-
Tooling: Custom tooling for specific designs or features can be a significant upfront cost. Buyers should assess whether the tooling costs can be amortized over larger order volumes to make the pricing more favorable.
-
Quality Control (QC): Ensuring compliance with international standards, such as UL or CE certifications, is essential. The costs associated with QC processes should be factored into the overall pricing as they safeguard against potential liability issues.
-
Logistics: Shipping costs, including freight, insurance, and customs duties, can vary significantly depending on the origin and destination. Choosing the right shipping method and Incoterms (e.g., FOB, CIF) can help manage these costs.
-
Margin: Suppliers will typically include a profit margin in their pricing. Understanding industry standards for margins can assist buyers in negotiating better deals.
How Do Price Influencers Affect the Cost of US Electrical Plugs?
Several factors can influence the pricing of electrical plugs, particularly for international buyers:
-
Volume and Minimum Order Quantity (MOQ): Larger orders often result in lower per-unit costs. Buyers should negotiate MOQs that suit their needs while also seeking volume discounts.
-
Specifications and Customization: Custom designs or features will generally increase costs. It’s important for buyers to clearly define their requirements to avoid unexpected charges during production.
-
Material Quality and Certifications: Higher-quality materials and additional certifications can increase costs but often lead to a superior product that meets safety and regulatory standards.
-
Supplier Factors: The supplier’s reputation, production capabilities, and location can all influence pricing. Conducting thorough due diligence on potential suppliers is essential.
-
Incoterms: The choice of Incoterms can significantly affect logistics costs. Understanding the implications of terms like FOB (Free on Board) versus CIF (Cost, Insurance, and Freight) can lead to more favorable pricing.
What Are Some Buyer Tips for Cost-Efficient Sourcing?
For B2B buyers from Africa, South America, the Middle East, and Europe, here are actionable tips to optimize sourcing costs:
-
Negotiate Wisely: Building a relationship with suppliers can open the door for better pricing. Leverage your purchasing power and be prepared to discuss long-term contracts to secure favorable terms.
-
Focus on Total Cost of Ownership (TCO): While the initial purchase price is important, consider the TCO, which includes maintenance, energy efficiency, and longevity. A slightly higher upfront cost may lead to lower overall expenses.
-
Be Aware of Pricing Nuances: Different regions may have varying price sensitivities based on local demand and supply conditions. Researching these nuances can provide leverage in negotiations.
-
Consider Local Sourcing: Depending on the market, local suppliers may offer competitive pricing due to reduced shipping costs and faster turnaround times. This can also enhance supply chain resilience.
-
Stay Informed on Market Trends: Keeping abreast of trends in electrical components can help buyers anticipate price fluctuations and adjust their sourcing strategies accordingly.
Disclaimer on Indicative Prices
Prices for US electrical plugs can fluctuate based on market conditions, material costs, and supplier changes. Buyers are encouraged to conduct thorough market research and obtain multiple quotations to ensure they are making informed purchasing decisions.
Alternatives Analysis: Comparing us electrical plug With Other Solutions
Exploring Alternative Solutions to the US Electrical Plug
When considering the use of electrical plugs and sockets, particularly for international B2B transactions, it is essential to evaluate various alternatives to the US electrical plug. This analysis will compare the traditional US electrical plug with several viable alternatives, focusing on their performance, cost, ease of implementation, maintenance, and best use cases. This information is crucial for businesses looking to optimize their electrical infrastructure, especially when expanding operations across different regions.
Comparison Aspect | Us Electrical Plug | Universal Plug Adapter | IEC 60320 Connector |
---|---|---|---|
Performance | 120V, 60Hz | Varies (dual voltage) | Varies (dual voltage) |
Cost | Moderate | Low to Moderate | Moderate to High |
Ease of Implementation | Simple | Very Simple | Complex |
Maintenance | Low | Low | Moderate |
Best Use Case | Domestic US appliances | International travel | Fixed installations |
What are the Advantages and Disadvantages of Using a Universal Plug Adapter?
Universal Plug Adapter
Universal plug adapters are designed to accommodate multiple plug types, allowing devices from various countries to be connected to local sockets. This flexibility makes them ideal for travelers and businesses that frequently operate in different regions. The primary advantage is their cost-effectiveness and ease of use, as they typically require minimal setup. However, they do not convert voltage, meaning devices must be compatible with the local supply. This can pose a risk if users are unaware of their devices’ voltage requirements.
How Does the IEC 60320 Connector Compare?
IEC 60320 Connector
The IEC 60320 connector is commonly used in appliances that require a more secure and standardized connection, such as computers and servers. Its design allows for a robust connection that can handle higher power loads, making it suitable for commercial applications. While it offers better performance in terms of stability and safety, its complexity in installation can be a barrier for some businesses. Additionally, the initial cost of IEC connectors and compatible sockets can be higher than that of standard plugs, which may deter smaller enterprises.
Conclusion: Which Solution is Right for Your Business Needs?
Choosing the right electrical connection solution depends on your specific business needs and operational contexts. The US electrical plug is sufficient for domestic applications, while universal plug adapters offer flexibility for international travel. For businesses focused on fixed installations, especially in data centers or industrial environments, the IEC 60320 connector may provide the best performance and reliability. Assessing factors like the nature of your electrical appliances, frequency of international operations, and installation complexity will guide you in selecting the most suitable alternative for your organization.
Essential Technical Properties and Trade Terminology for us electrical plug
What Are the Key Technical Properties of US Electrical Plugs?
When purchasing US electrical plugs, understanding their technical properties is essential for ensuring compatibility and safety. Here are critical specifications to consider:
1. Voltage Rating
The standard voltage for US electrical plugs is 120V with a frequency of 60Hz. This specification is crucial because appliances designed for different voltage levels may not function correctly and can be damaged if plugged into the wrong voltage. For B2B buyers, verifying the voltage compatibility of products is vital to avoid costly returns or equipment failure.
2. Current Rating
US plugs typically have a current rating of 15A or 20A. This rating indicates the maximum current the plug can handle without overheating. Understanding the current rating is crucial when selecting plugs for high-power devices, as exceeding this limit can result in electrical fires or equipment damage. B2B buyers should ensure that the plugs can support the operational demands of their electrical devices.
3. Material Composition
Most US electrical plugs are made from polycarbonate or thermoplastic materials. These materials provide durability and heat resistance, which are essential for safe electrical operation. For manufacturers and suppliers, the choice of material can affect the plug’s longevity and safety standards. Buyers should look for plugs that meet relevant safety certifications, such as UL or CE.
4. Pin Configuration
US electrical plugs come in two types: Type A (two flat parallel pins) and Type B (two flat pins and a grounding pin). Understanding the pin configuration is crucial for ensuring compatibility with outlets. B2B buyers must check the plug type required for their devices and whether additional adapters are necessary for international use.
5. Grounding Method
Type B plugs include a grounding pin, which enhances electrical safety by preventing shocks. This grounding method is particularly important for devices that require grounding for safe operation. Buyers should assess whether their equipment necessitates grounding and choose plugs accordingly.
6. Tolerance and Fit
The tolerance of the pins and the fit in the socket are critical for ensuring a secure connection. Loose connections can lead to arcing and potential fires. Buyers should ensure that the plugs they select fit snugly into the intended sockets and maintain good electrical contact.
What Are Common Trade Terms Associated with US Electrical Plugs?
Understanding trade terminology is essential for successful B2B transactions. Here are some common terms you may encounter:
1. OEM (Original Equipment Manufacturer)
An OEM refers to a company that produces parts or equipment that may be marketed by another manufacturer. In the context of electrical plugs, an OEM might supply components that are integrated into finished products. This term is crucial for buyers looking to source specific components for their manufacturing processes.
2. MOQ (Minimum Order Quantity)
MOQ indicates the smallest number of units a supplier is willing to sell. This term is important for B2B buyers as it helps determine the minimum investment required for a purchase. Understanding MOQ can assist buyers in budgeting and inventory planning.
3. RFQ (Request for Quotation)
An RFQ is a document that a buyer submits to suppliers requesting pricing and other terms for specific products. For buyers, issuing an RFQ is a strategic way to gather information from multiple suppliers and negotiate better deals on US electrical plugs.
4. Incoterms (International Commercial Terms)
Incoterms are a set of predefined international trade terms that clarify the responsibilities of buyers and sellers in international transactions. Understanding these terms helps B2B buyers navigate shipping logistics and clarify who is responsible for costs and risks at different stages of the delivery process.
5. Certification Standards
Certification standards, such as UL (Underwriters Laboratories) or CE (Conformité Européenne), indicate that a product meets specific safety and performance criteria. For international buyers, ensuring that plugs have the appropriate certifications is critical for compliance and safety in their markets.
6. Lead Time
Lead time refers to the amount of time it takes from placing an order to receiving the products. For B2B buyers, understanding lead times is essential for inventory management and project planning, especially when sourcing products from international suppliers.
By familiarizing yourself with these technical properties and trade terms, you can make informed purchasing decisions regarding US electrical plugs, ensuring safety and compatibility for your operations.
Navigating Market Dynamics and Sourcing Trends in the us electrical plug Sector
What Are the Key Market Dynamics and Trends in the US Electrical Plug Sector?
The US electrical plug market is undergoing significant transformation, driven by a mix of technological advancements and evolving buyer needs. International B2B buyers from regions like Africa, South America, the Middle East, and Europe should be aware of key trends shaping the industry. The demand for smart electrical solutions, such as IoT-enabled plugs and energy-efficient designs, is rising. These innovations are not only enhancing user convenience but also aligning with global sustainability goals.
Additionally, the push for standardization in electrical components is gaining momentum. This is particularly relevant for buyers looking to source products that comply with international standards. The US market predominantly utilizes Type A and Type B plugs, operating at a standard voltage of 120V and frequency of 60Hz. Understanding these specifications is crucial for international buyers to ensure compatibility with their electrical systems.
Another noteworthy trend is the growing emphasis on e-commerce platforms for sourcing electrical components. B2B buyers can leverage online marketplaces to compare products, read reviews, and access a broader range of suppliers. This shift towards digital sourcing is essential for buyers aiming to streamline procurement processes while ensuring quality and cost-effectiveness.
How Can International Buyers Ensure Sustainability and Ethical Sourcing in the US Electrical Plug Market?
Sustainability and ethical sourcing are becoming increasingly important for B2B buyers in the US electrical plug sector. The environmental impact of manufacturing electrical components cannot be overlooked. Buyers should prioritize suppliers that adhere to sustainable practices, such as minimizing waste and utilizing renewable energy sources in production.
Furthermore, ethical supply chains are essential for fostering transparency and accountability. Buyers should look for manufacturers that comply with international labor standards and demonstrate a commitment to fair trade practices. Certifications such as ISO 14001 for environmental management and Fair Trade certifications can serve as indicators of a supplier’s dedication to sustainability.
In terms of materials, opting for ‘green’ certifications can enhance a company’s reputation while contributing to environmental conservation. Many manufacturers are now producing electrical plugs using recyclable or biodegradable materials, which not only reduce environmental footprints but also cater to the growing consumer demand for eco-friendly products.
What Is the Brief Evolution of the US Electrical Plug Sector?
The US electrical plug sector has evolved significantly since the introduction of standardized electrical systems in the early 20th century. The establishment of Type A and Type B plugs has provided a reliable framework for electrical connectivity across the nation. Initially designed for safety and efficiency, these plug types have adapted over time to meet the increasing demand for higher power loads and user-friendly designs.
In recent decades, technological advancements have propelled the sector towards innovation. The emergence of smart plugs and energy-efficient designs reflects a shift in consumer preferences towards convenience and sustainability. This evolution not only highlights the adaptability of the electrical plug market but also underscores the importance of staying informed about emerging trends for international B2B buyers looking to make informed sourcing decisions.
Frequently Asked Questions (FAQs) for B2B Buyers of us electrical plug
-
How do I solve compatibility issues with US electrical plugs in my region?
To address compatibility issues with US electrical plugs, first, identify the type of plug used in your country. The US utilizes Type A and Type B plugs. If your devices do not fit, you will need a travel adapter or a universal power adapter that accommodates multiple plug types. Additionally, ensure that your devices are compatible with the US voltage (120V) and frequency (60Hz). For devices not rated for dual voltage, a voltage converter will be necessary to prevent damage. -
What is the best power plug adapter for US electrical plugs?
The best power plug adapter for US electrical plugs depends on your specific needs. A universal travel adapter is highly recommended as it can accommodate various plug types, making it versatile for international travel. Ensure it supports Type A and Type B plugs specifically. Additionally, look for adapters with built-in surge protection and USB ports for charging multiple devices simultaneously, which is ideal for business travelers. -
How can I ensure the quality of US electrical plugs when sourcing from suppliers?
To ensure the quality of US electrical plugs, conduct thorough supplier vetting by checking for certifications such as UL (Underwriters Laboratories) and CE (Conformité Européenne). Request product samples to assess their quality and performance. Additionally, consider suppliers with a solid reputation and positive reviews from previous clients. Establishing a quality assurance process, including inspections during production and before shipment, can further enhance confidence in the products you source. -
What are the minimum order quantities (MOQ) for US electrical plugs from suppliers?
The minimum order quantity (MOQ) for US electrical plugs varies by supplier and can range from as few as 100 units to several thousand. When negotiating with suppliers, clarify the MOQ and assess whether it aligns with your purchasing needs. If you are a smaller buyer, look for suppliers willing to offer lower MOQs or consider joining a consortium with other buyers to meet higher order requirements. -
What payment terms should I consider when purchasing US electrical plugs?
When purchasing US electrical plugs, consider payment terms that offer protection and flexibility. Common payment methods include wire transfers, letters of credit, and PayPal. Aim for terms that allow for partial payments upfront with the remainder due upon delivery or after inspection. Establishing clear payment timelines can prevent misunderstandings and ensure a smoother transaction process. -
How can I manage logistics for importing US electrical plugs to my country?
Managing logistics for importing US electrical plugs involves coordinating with reliable freight forwarders who understand international trade regulations. Determine whether to use air or sea freight based on your urgency and budget. Ensure all necessary import documentation, such as customs declarations and import permits, is prepared in advance. Collaborate closely with your suppliers to confirm shipping timelines and track the shipment to mitigate delays. -
What customization options are available for US electrical plugs?
Many manufacturers offer customization options for US electrical plugs, including branding, color variations, and specific features like built-in surge protection or USB ports. When discussing customization, provide clear specifications and quantities required. Be aware that customized products may have higher MOQs and longer lead times, so factor this into your planning. -
What quality assurance processes should I implement when sourcing US electrical plugs?
Implementing a robust quality assurance process involves several steps: first, define quality standards that align with industry regulations. Conduct initial supplier audits to assess their manufacturing capabilities. During production, schedule regular inspections and testing of samples to ensure compliance with safety standards. Finally, perform a final inspection before shipment to verify that the products meet your specifications and quality benchmarks.
Important Disclaimer & Terms of Use
⚠️ Important Disclaimer
The information provided in this guide, including content regarding manufacturers, technical specifications, and market analysis, is for informational and educational purposes only. It does not constitute professional procurement advice, financial advice, or legal advice.
While we have made every effort to ensure the accuracy and timeliness of the information, we are not responsible for any errors, omissions, or outdated information. Market conditions, company details, and technical standards are subject to change.
B2B buyers must conduct their own independent and thorough due diligence before making any purchasing decisions. This includes contacting suppliers directly, verifying certifications, requesting samples, and seeking professional consultation. The risk of relying on any information in this guide is borne solely by the reader.
Strategic Sourcing Conclusion and Outlook for us electrical plug
The strategic sourcing of US electrical plugs is essential for international buyers looking to penetrate the American market or provide products that meet US standards. With the prevalent use of Type A and Type B plugs and a standard voltage of 120V at 60Hz, understanding these specifications is crucial for avoiding compatibility issues. Businesses must prioritize sourcing high-quality, compliant products to ensure safety and reliability for their customers.
Investing in strategic sourcing not only mitigates risks associated with voltage discrepancies but also enhances supply chain efficiency. By fostering relationships with reputable suppliers, buyers can secure a steady flow of necessary components while adapting to the evolving demands of the market. This is particularly important for stakeholders from Africa, South America, the Middle East, and Europe, who must navigate diverse regulatory landscapes.
Looking ahead, the increasing globalization of the electrical goods market presents a significant opportunity for growth. International buyers are encouraged to leverage the knowledge gained from this guide, ensuring they are well-equipped to make informed purchasing decisions. Embrace the potential of strategic sourcing to thrive in the competitive landscape of electrical plugs, and connect with suppliers who can meet your needs today.