Improve Efficiency: The Complete Bucket Elevator Guide (2025)
Introduction: Navigating the Global Market for bucket elevator
In today’s fast-paced global market, sourcing a reliable bucket elevator can pose significant challenges for B2B buyers, particularly in regions like Africa, South America, the Middle East, and Europe. Whether you’re dealing with heavy materials like iron ore or delicate products such as grains, selecting the right equipment is crucial to ensure operational efficiency and minimize product damage. This guide offers an in-depth exploration of bucket elevators, covering various types, applications, and essential factors to consider when making a purchase.
International buyers will benefit from our comprehensive insights into the different models available, including centrifugal and continuous discharge elevators, which are tailored to meet specific material handling needs. We delve into the critical aspects of supplier vetting, helping you assess the reliability and reputation of manufacturers to ensure you are investing in quality equipment. Additionally, we provide a breakdown of cost factors, enabling you to make informed budgetary decisions.
By addressing the unique challenges faced by B2B buyers in diverse markets, this guide empowers you to navigate the complexities of sourcing bucket elevators effectively. With a focus on actionable insights and strategic considerations, we aim to equip you with the knowledge necessary to enhance your material handling processes and drive your business success.
Understanding bucket elevator Types and Variations
Type Name | Key Distinguishing Features | Primary B2B Applications | Brief Pros & Cons for Buyers |
---|---|---|---|
Centrifugal Bucket | Uses centrifugal force for discharge; operates at higher speeds. | Mining, agriculture, cement production | Pros: High output, efficient for non-fragile materials. Cons: Can damage delicate products. |
Continuous Bucket | Operates at lower speeds to minimize product breakage; versatile. | Food processing, chemicals, minerals | Pros: Gentle handling, suitable for fragile materials. Cons: Lower capacity compared to centrifugal types. |
Belt Bucket | Utilizes a belt system for material transport; flexible design. | Heavy-duty applications, construction | Pros: Robust and reliable, adaptable to various materials. Cons: May require more maintenance over time. |
Chain Bucket | Features a chain mechanism for heavy and abrasive materials. | Mining, steel production, power generation | Pros: Handles harsh materials, high durability. Cons: Heavier and can be more expensive. |
Custom Bucket | Tailored designs for specific applications and materials. | Specialized industries, unique requirements | Pros: Optimized for specific needs, high efficiency. Cons: Longer lead times and potential higher costs. |
What Are Centrifugal Bucket Elevators and When to Use Them?
Centrifugal bucket elevators are designed to discharge materials using centrifugal force, making them suitable for applications requiring higher speed and output. They are commonly utilized in industries like mining and agriculture, where materials are less fragile. When considering this type, buyers should evaluate the product’s susceptibility to damage, as the force used during discharge can be detrimental to delicate items.
How Do Continuous Bucket Elevators Differ in Operation?
Continuous bucket elevators operate at lower speeds, which helps minimize product breakage. This feature makes them ideal for handling fragile materials, particularly in food processing and chemical industries. Buyers should consider the type of materials being handled and the desired throughput, as continuous systems may offer lower capacity compared to centrifugal types but excel in preserving product integrity.
What Are the Advantages of Belt Bucket Elevators?
Belt bucket elevators employ a belt system for transporting materials, offering flexibility in design and application. They are robust and reliable, making them suitable for heavy-duty applications in construction and bulk material handling. Buyers should assess the specific material characteristics and operational conditions, as belt elevators may require regular maintenance to ensure optimal performance.
Why Choose Chain Bucket Elevators for Heavy Materials?
Chain bucket elevators are specifically designed to handle heavy and abrasive materials, such as those found in mining and steel production. Their durable construction ensures longevity in harsh environments, making them a solid investment for companies dealing with challenging materials. Buyers should weigh the initial costs against the long-term benefits of durability and performance when considering this option.
How Can Custom Bucket Elevators Meet Unique Needs?
Custom bucket elevators provide tailored solutions for specialized applications, allowing businesses to optimize their material handling processes. These elevators can be designed to meet specific requirements, such as handling unique materials or fitting into constrained spaces. While they may come with longer lead times and potentially higher costs, the efficiency gains and suitability for niche markets often justify the investment for B2B buyers looking for a competitive edge.
Key Industrial Applications of bucket elevator
Industry/Sector | Specific Application of Bucket Elevator | Value/Benefit for the Business | Key Sourcing Considerations for this Application |
---|---|---|---|
Agriculture | Transporting grains and seeds from storage silos | Efficient vertical transport reduces labor costs | Material compatibility, capacity needs, and discharge mechanism |
Mining and Minerals | Elevating heavy minerals like iron ore and potash | High durability and reliability for harsh environments | Customization options for material type and lifting height |
Cement Production | Conveying cement and additives to processing units | Enhances production flow and minimizes downtime | Temperature tolerance and corrosion resistance of materials used |
Food Processing | Elevating bulk food products like beans and grains | Ensures gentle handling to maintain product integrity | Compliance with sanitation standards and easy maintenance access |
Power Generation | Moving fly ash and other by-products for disposal | Reduces environmental impact and improves efficiency | Consideration of material abrasiveness and discharge type |
How are Bucket Elevators Used in Agriculture?
In the agriculture sector, bucket elevators are primarily used for transporting grains and seeds from storage silos to processing areas. These systems ensure efficient vertical transport, which not only saves time but also reduces labor costs. For international buyers, especially from regions like Africa and South America, it’s crucial to consider the compatibility of the bucket elevator with local grain types and the specific capacity requirements to ensure optimal operational efficiency.
What Role Do Bucket Elevators Play in Mining and Minerals?
In mining, bucket elevators are essential for elevating heavy minerals such as iron ore and potash. Their robust construction and ability to handle high volumes make them ideal for this demanding environment. Buyers from the Middle East and Europe should focus on customization options that cater to the specific material characteristics, including particle size and weight, as well as the necessary lifting height to meet their operational needs.
How are Bucket Elevators Beneficial in Cement Production?
Cement production facilities utilize bucket elevators to convey cement and various additives to processing units. This application enhances production flow and minimizes downtime, which is critical for maintaining high output levels. For B2B buyers in regions like Turkey and Egypt, sourcing equipment that can withstand extreme temperatures and resist corrosion is vital to ensure longevity and reliability in their operations.
What is the Importance of Bucket Elevators in Food Processing?
In food processing, bucket elevators are used to transport bulk food products such as beans and grains. The design of these elevators ensures gentle handling, which is crucial for maintaining the integrity of fragile food items. Buyers, especially those from Europe, must consider compliance with stringent sanitation standards and ensure that the elevators provide easy access for maintenance to prevent contamination and uphold food safety.
How Do Bucket Elevators Assist in Power Generation?
In the power generation sector, bucket elevators are employed to move fly ash and other by-products for proper disposal or recycling. This application helps reduce the environmental impact of power plants and improves overall efficiency. B2B buyers should prioritize sourcing elevators that can handle abrasive materials and select the appropriate discharge type to optimize their waste management processes.
3 Common User Pain Points for ‘bucket elevator’ & Their Solutions
Scenario 1: Minimizing Product Damage During Transport
The Problem: In industries such as food processing and agriculture, the integrity of bulk materials is paramount. A common pain point for B2B buyers is the risk of product damage during the transportation process. For instance, when using centrifugal bucket elevators, fragile materials like edible beans or powdered substances can suffer from degradation due to high-speed discharges. This not only impacts product quality but also leads to financial losses and reduced customer satisfaction.
The Solution: To mitigate product damage, consider specifying continuous bucket elevators designed for gentle handling. These elevators operate at lower speeds, significantly reducing the impact forces that can break or degrade fragile materials. When sourcing a bucket elevator, assess the material characteristics, such as bulk density and particle size distribution. It’s essential to work closely with suppliers who can customize the equipment based on the specific needs of your operation. Investing in models with features like adjustable speeds and specialized bucket designs can further enhance material protection, ensuring a smoother transport process and maintaining product quality.
Scenario 2: Addressing Equipment Downtime and Maintenance Challenges
The Problem: Frequent breakdowns and maintenance challenges can significantly disrupt operations, especially in high-demand environments such as mining or cement production. B2B buyers often struggle with unplanned downtime caused by equipment failures, which can arise from inadequate maintenance access or outdated technology in bucket elevators. This not only leads to increased operational costs but also hampers productivity.
The Solution: To tackle maintenance challenges, prioritize bucket elevators that are designed with easy access points for inspections and repairs. Models with removable covers and access doors can simplify maintenance tasks, allowing for quicker checks and interventions. Additionally, consider investing in equipment that features advanced monitoring systems, such as belt alignment sensors and temperature sensors, to proactively identify issues before they escalate. Collaborate with suppliers who offer comprehensive service plans, including training for your maintenance team on best practices. This proactive approach will help minimize downtime and optimize the operational efficiency of your material handling systems.
Scenario 3: Customizing Elevators for Diverse Material Handling Needs
The Problem: International B2B buyers often face challenges when dealing with a diverse range of materials that require different handling capabilities. For example, a company may need to transport both abrasive materials like iron ore and delicate products like seeds. Using a one-size-fits-all bucket elevator can lead to inefficiencies and increased wear on the equipment, resulting in higher costs and potential operational issues.
The Solution: To address this, focus on sourcing customizable bucket elevators that can be tailored to handle various materials effectively. Collaborate with manufacturers who provide options for different configurations, such as centrifugal versus continuous discharge systems, and belt versus chain designs. Before making a purchase, conduct a thorough analysis of the materials you need to transport, including their physical properties and the specific requirements of your production process. This will help you select a bucket elevator that is versatile enough to adapt to multiple material types while maintaining efficiency. Engaging with suppliers who understand the nuances of your industry can lead to optimized solutions that enhance performance across diverse applications.
Strategic Material Selection Guide for bucket elevator
What Are the Key Properties of Common Materials Used in Bucket Elevators?
When selecting materials for bucket elevators, it is crucial to consider their properties, as these directly influence performance, durability, and suitability for specific applications. Here, we analyze four common materials used in bucket elevator construction: carbon steel, stainless steel, plastic, and aluminum.
Carbon Steel: A Cost-Effective Choice for Heavy-Duty Applications
Key Properties: Carbon steel is known for its high tensile strength and durability, making it suitable for heavy-duty applications. It can withstand high temperatures and pressures, with a typical temperature rating up to 400°F (204°C). However, it is prone to corrosion if not properly treated.
Pros & Cons: The primary advantage of carbon steel is its cost-effectiveness and strength, making it ideal for bulk materials like sand and gravel. However, its susceptibility to rust and corrosion can lead to increased maintenance costs and reduced lifespan, particularly in humid or corrosive environments.
Impact on Application: Carbon steel is well-suited for handling abrasive materials, but it may not be ideal for food-grade applications without proper coatings. Buyers should consider the specific environmental conditions of their operations, especially in regions with high humidity.
Considerations for International Buyers: Compliance with standards such as ASTM A36 is essential. Buyers from Africa and South America should also consider local corrosion challenges and seek protective coatings to enhance longevity.
Stainless Steel: The Go-To Material for Hygiene and Corrosion Resistance
Key Properties: Stainless steel boasts exceptional corrosion resistance and can withstand temperatures exceeding 800°F (427°C). It is also non-reactive, making it suitable for food and pharmaceutical applications.
Pros & Cons: The primary advantage of stainless steel is its durability and hygiene, making it ideal for sensitive materials like grains and pharmaceuticals. However, it comes at a higher cost compared to carbon steel and may require specialized welding techniques.
Impact on Application: Stainless steel is particularly beneficial in food processing and chemical industries, where contamination must be avoided. Its smooth surface also facilitates easy cleaning.
Considerations for International Buyers: Compliance with standards such as FDA and USDA is crucial for food applications. Buyers in the Middle East and Europe should also ensure adherence to local regulations regarding food safety and hygiene.
Plastic: A Lightweight Option for Specific Applications
Key Properties: Plastic materials, such as polyethylene and polypropylene, are lightweight and resistant to corrosion. They can handle temperatures up to 200°F (93°C) and are generally non-conductive.
Pros & Cons: The main advantage of plastic is its resistance to corrosion and lightweight nature, making installation easier. However, it may not be suitable for heavy loads or high-temperature applications, limiting its use to lighter materials like grains or pellets.
Impact on Application: Plastic bucket elevators are ideal for handling non-abrasive materials and are commonly used in agricultural settings. However, their lower durability compared to metal options may lead to more frequent replacements.
Considerations for International Buyers: Buyers should consider the specific material grades and compliance with environmental regulations. In Europe, for instance, adherence to REACH regulations may be necessary.
Aluminum: A Lightweight and Corrosion-Resistant Alternative
Key Properties: Aluminum is lightweight and offers good corrosion resistance, with a temperature rating of around 400°F (204°C). It is also non-magnetic, making it suitable for applications requiring non-reactive materials.
Pros & Cons: The key advantage of aluminum is its lightweight nature, which reduces energy consumption during operation. However, it is generally less durable than steel and may not be suitable for heavy-duty applications.
Impact on Application: Aluminum is often used in applications where weight savings are crucial, such as in mobile or temporary installations. However, it may not be suitable for handling heavy or abrasive materials.
Considerations for International Buyers: Compliance with standards such as ASTM B221 is important. Buyers from regions with high temperatures, like parts of Africa, should assess the material’s performance under local conditions.
Summary Table of Material Selection for Bucket Elevators
Material | Typical Use Case for bucket elevator | Key Advantage | Key Disadvantage/Limitation | Relative Cost (Low/Med/High) |
---|---|---|---|---|
Carbon Steel | Heavy-duty applications (sand, gravel) | Cost-effective and strong | Prone to corrosion | Low |
Stainless Steel | Food and pharmaceutical industries | Corrosion-resistant and hygienic | Higher cost and specialized welding | High |
Plastic | Agricultural settings (grains, pellets) | Lightweight and corrosion-resistant | Limited to lighter loads | Medium |
Aluminum | Mobile or temporary installations | Lightweight and non-reactive | Less durable for heavy applications | Medium |
This detailed analysis provides international B2B buyers with actionable insights into material selection for bucket elevators, ensuring informed decisions that align with their operational needs and regional conditions.
In-depth Look: Manufacturing Processes and Quality Assurance for bucket elevator
What Are the Key Stages in the Manufacturing Process of Bucket Elevators?
The manufacturing process of bucket elevators typically involves several critical stages: material preparation, forming, assembly, and finishing. Each stage is essential for ensuring the reliability and efficiency of the final product.
Material Preparation
The first step in manufacturing a bucket elevator is material selection and preparation. High-quality raw materials such as steel, stainless steel, and specialized alloys are chosen based on the intended application and environmental conditions. The materials are then cut, shaped, and pre-treated to enhance their durability and resistance to corrosion and abrasion. This stage is crucial, as the longevity of the bucket elevator is directly linked to the quality of materials used.
Forming Techniques
Once the materials are prepared, they undergo various forming techniques, including welding, bending, and machining. Advanced technologies like laser cutting and CNC machining are often employed to ensure precision. For example, the head and boot sections of the bucket elevator are typically fabricated using heavy-duty steel to withstand the stresses of continuous operation. Additionally, forming techniques may vary depending on the type of bucket elevator being produced (e.g., centrifugal or continuous discharge models).
Assembly Processes
After the components are formed, the next stage is assembly. This involves integrating various parts, such as buckets, belts, and drive systems, into a cohesive unit. Manufacturers often utilize jigs and fixtures to maintain accuracy during assembly. Moreover, assembly lines may incorporate automated systems for repetitive tasks, enhancing efficiency. Quality checks are integrated into this stage to ensure that each component fits correctly and functions as intended.
Finishing Touches
The final stage in manufacturing is finishing, which includes surface treatment and coating. This process protects the bucket elevator from environmental factors and wear over time. Techniques such as powder coating, galvanization, or painting are common. Additionally, manufacturers may conduct final inspections to ensure that the product meets aesthetic and functional standards before shipping.
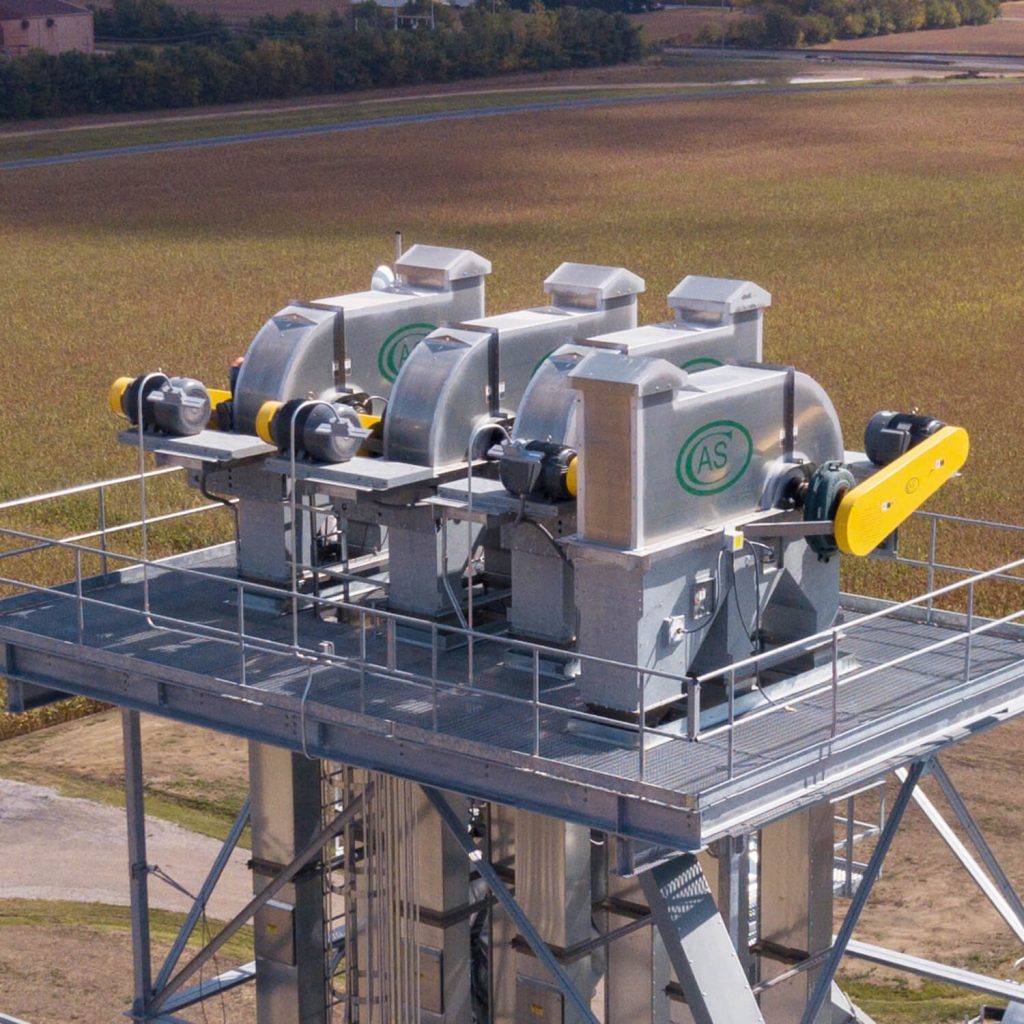
A stock image related to bucket elevator.
How Is Quality Assurance Implemented in Bucket Elevator Manufacturing?
Quality assurance (QA) is a vital component of the manufacturing process for bucket elevators. It ensures that products not only meet customer expectations but also comply with international standards.
What International Standards Govern Bucket Elevator Manufacturing?
Bucket elevator manufacturers often adhere to several international standards, including ISO 9001, which focuses on quality management systems. Compliance with ISO standards demonstrates a commitment to quality and continuous improvement. Additionally, industry-specific certifications like CE (Conformité Européenne) and API (American Petroleum Institute) are crucial for manufacturers targeting markets in Europe and the Middle East, respectively. These certifications ensure that the products meet safety, health, and environmental protection requirements.
What Are the QC Checkpoints Throughout the Manufacturing Process?
Quality control (QC) checkpoints are integrated into various stages of the manufacturing process to catch defects early. Common QC checkpoints include:
- Incoming Quality Control (IQC): This involves inspecting raw materials upon delivery to ensure they meet specified standards.
- In-Process Quality Control (IPQC): Continuous monitoring occurs during the manufacturing process to identify defects or deviations from specifications.
- Final Quality Control (FQC): After assembly, a thorough inspection is conducted to verify that the bucket elevator meets all design and functional requirements before shipment.
What Testing Methods Are Commonly Used for Bucket Elevators?
Testing methods for bucket elevators include functional tests, load tests, and safety tests. Functional tests ensure that all components operate correctly under normal and extreme conditions. Load tests are particularly important for assessing the elevator’s performance under maximum capacity, while safety tests check for compliance with safety regulations.
How Can B2B Buyers Verify Supplier Quality Control?
For international B2B buyers, especially from regions like Africa, South America, the Middle East, and Europe, verifying supplier quality control is essential. Here are some actionable steps:
- Conduct Audits: Regular audits of suppliers can provide insights into their manufacturing processes and quality assurance practices. Buyers should inquire about the frequency and scope of these audits.
- Request Quality Reports: Suppliers should be able to provide detailed quality reports, including information on material certifications, inspection results, and compliance with international standards.
- Engage Third-party Inspection Services: Utilizing third-party inspection services can provide an unbiased assessment of the supplier’s quality control processes. These inspections can be scheduled at various stages of the manufacturing process.
What Are the Quality Control Nuances for International B2B Buyers?
When dealing with international suppliers, B2B buyers must navigate specific nuances related to quality control:
- Understanding Local Standards: Different regions may have varying standards for manufacturing and quality assurance. Buyers should familiarize themselves with the local regulations in the supplier’s country.
- Cultural Differences: Cultural attitudes towards quality and craftsmanship can vary significantly. Establishing clear communication and expectations upfront can mitigate misunderstandings.
- Documentation and Traceability: Ensuring that suppliers provide complete documentation for all materials and processes is crucial for accountability. Buyers should request traceability documentation to verify the origin and quality of materials used.
By understanding the manufacturing processes and quality assurance protocols of bucket elevators, B2B buyers can make informed decisions that align with their operational needs and standards. This comprehensive approach not only enhances the reliability of their material handling systems but also contributes to overall operational efficiency.
Practical Sourcing Guide: A Step-by-Step Checklist for ‘bucket elevator’
Introduction
When sourcing a bucket elevator, particularly for industries in Africa, South America, the Middle East, and Europe, it is essential to approach the procurement process systematically. This guide provides a step-by-step checklist designed to help international B2B buyers navigate the complexities of selecting the right bucket elevator for their specific needs. By following these steps, you can ensure that your investment meets operational requirements and maximizes efficiency.
Step 1: Define Your Technical Specifications
Clearly outline the technical specifications of the bucket elevator you need. This includes the type of material to be handled, capacity, discharge method, and the required height for elevation. Defining these parameters upfront helps streamline the selection process and ensures compatibility with your operational environment.
– Material Characteristics: Consider bulk density, particle size, and any potential corrosive properties.
– Capacity Requirements: Determine the volume of material that needs to be transported per hour.
Step 2: Research and Compare Different Elevator Types
Understanding the various types of bucket elevators available is critical. Common types include centrifugal and continuous bucket elevators, each suited for different applications. Centrifugal elevators are ideal for high-speed operations, while continuous elevators minimize product degradation.
– Evaluate Pros and Cons: Identify which type aligns with your specific material handling needs.
– Consider Speed and Efficiency: Look for models that optimize output without compromising material integrity.
Step 3: Evaluate Potential Suppliers
Before committing to a supplier, conduct thorough evaluations. Request company profiles, case studies, and references from other businesses in similar industries or regions. Supplier reliability is crucial for ongoing support and service.
– Check Certifications: Ensure that the supplier meets international quality and safety standards.
– Request Samples or Demonstrations: Whenever possible, ask for product demonstrations or samples to assess quality firsthand.
Step 4: Inquire About Customization Options
Customization can significantly enhance the functionality of your bucket elevator. Inquire if the supplier offers tailored solutions that fit your specific operational needs, such as special materials or design modifications.
– Discuss Design Flexibility: A supplier that can adapt designs based on your material characteristics is valuable.
– Explore Additional Features: Consider options like removable covers for maintenance, dust-tight designs, or advanced monitoring systems.
Step 5: Assess Total Cost of Ownership
While the initial purchase price is important, evaluating the total cost of ownership (TCO) is essential. This includes installation, maintenance, and operational costs over the elevator’s lifespan.
– Factor in Installation Costs: Ensure you understand whether installation is included or if additional fees will apply.
– Consider Long-Term Maintenance Needs: Choose suppliers that offer comprehensive service packages or warranties.
Step 6: Verify After-Sales Support and Service
Strong after-sales support is vital for minimizing downtime and ensuring the longevity of your equipment. Confirm what kind of support the supplier provides post-purchase, including maintenance services and spare parts availability.
– Evaluate Response Times: Ask about average response times for service calls or equipment issues.
– Look for Training Opportunities: Suppliers that offer training for your staff can help maximize the efficiency of the elevator.
Step 7: Finalize Your Decision and Place the Order
After thorough evaluation and comparison, finalize your choice based on the gathered information. Ensure all terms are clearly outlined in the contract, including delivery timelines and payment terms.
– Review the Contract: Check for warranties, service agreements, and any clauses that may affect your purchase.
– Establish Communication Channels: Maintain open lines of communication with the supplier for any future inquiries or issues.
By following this checklist, you can make informed decisions that enhance your material handling operations and drive business success.
Comprehensive Cost and Pricing Analysis for bucket elevator Sourcing
What Are the Key Cost Components in Bucket Elevator Sourcing?
When sourcing bucket elevators, understanding the various cost components is crucial for B2B buyers. The primary cost elements include:
-
Materials: The type of materials used significantly affects the overall cost. For instance, elevators designed for heavy-duty applications often utilize high-strength steel, which can be more expensive than standard materials. Additionally, the choice between belt and chain systems can also impact material costs.
-
Labor: Labor costs encompass both manufacturing and installation. Skilled labor is required for assembly and installation, especially in custom applications where specific adaptations are needed.
-
Manufacturing Overhead: This includes indirect costs associated with production, such as factory utilities, equipment depreciation, and administrative expenses. These costs vary based on the manufacturer’s efficiency and location.
-
Tooling: Custom tooling may be necessary for specialized bucket designs or configurations, which can add to the initial investment. The complexity of the tooling required is often proportional to the customization level of the bucket elevator.
-
Quality Control (QC): Implementing rigorous QC processes ensures the reliability and longevity of the equipment. However, this comes at a cost, which should be factored into the overall pricing structure.
-
Logistics: Shipping and handling costs can vary significantly based on the origin of the equipment and the destination. For international buyers, understanding the logistics involved, including customs duties and transportation fees, is essential.
-
Margin: Suppliers will typically add a margin to cover their operational costs and profit. This margin can vary widely depending on the supplier’s market position and reputation.
How Do Price Influencers Affect Bucket Elevator Costs?
Several factors can influence the pricing of bucket elevators, which are vital for international buyers to consider:
-
Volume and Minimum Order Quantity (MOQ): Bulk orders often lead to discounted pricing. Understanding the MOQ policies of suppliers can help buyers negotiate better deals, especially when sourcing for large projects.
-
Specifications and Customization: Tailoring bucket elevators to specific operational needs can increase costs. Buyers should weigh the benefits of customization against the potential for higher prices.
-
Material Quality and Certifications: Elevators built with higher-quality materials and those that meet specific industry certifications (like ISO or CE) typically come at a premium. Buyers should ensure that the quality justifies the cost, especially in industries with stringent safety and operational standards.
-
Supplier Factors: The supplier’s location, reputation, and relationship with the buyer can influence pricing. Established suppliers may offer better service and reliability but at a higher cost.
-
Incoterms: The agreed terms of trade (Incoterms) can significantly affect total costs. Understanding whether costs include shipping, insurance, and duties is essential for accurate budgeting.
What Tips Can International Buyers Use to Optimize Costs?
To ensure cost-effectiveness in sourcing bucket elevators, international buyers should consider the following strategies:
-
Negotiation: Engage in discussions with suppliers to explore price flexibility. Highlighting potential bulk orders or long-term partnerships may yield favorable pricing.
-
Total Cost of Ownership (TCO): Assess not just the purchase price but the total cost of ownership, which includes maintenance, operation, and potential downtime. A more expensive bucket elevator might offer lower TCO due to enhanced durability and efficiency.
-
Research and Compare Suppliers: Conduct thorough research on various suppliers, considering their reputation, product range, and support services. Comparing quotes from multiple suppliers can provide leverage during negotiations.
-
Understand Pricing Nuances: Different regions may have varying pricing structures due to factors like labor costs, material availability, and market demand. Familiarizing oneself with these nuances can aid in making informed purchasing decisions.
-
Stay Updated on Market Trends: Keeping abreast of industry trends, such as technological advancements and shifts in material costs, can help buyers anticipate price changes and make timely purchases.
Disclaimer on Indicative Prices
Prices for bucket elevators can vary widely based on the above factors, and this analysis is intended to provide a general overview rather than specific pricing. Buyers should request detailed quotes from suppliers to obtain accurate cost estimates tailored to their unique requirements.
Alternatives Analysis: Comparing bucket elevator With Other Solutions
Exploring Alternatives to Bucket Elevators: What Are Your Options?
When considering bulk material handling solutions, it’s essential to explore various alternatives to bucket elevators. While bucket elevators are widely recognized for their efficiency in vertical conveying, other technologies might better suit specific operational needs, especially for international B2B buyers in regions such as Africa, South America, the Middle East, and Europe. This section will compare bucket elevators with two viable alternatives: Conveyor Belts and Drag Conveyors.
Comparison Table of Material Handling Solutions
Comparison Aspect | Bucket Elevator | Conveyor Belt | Drag Conveyor |
---|---|---|---|
Performance | High capacity and efficient vertical lift | Versatile, suitable for horizontal and inclined transport | Excellent for heavy, abrasive materials |
Cost | Moderate initial investment, low operating costs | Lower initial costs but higher maintenance | Higher initial investment, long-term savings |
Ease of Implementation | Requires precise engineering for installation | Generally easier to install and modify | More complex installation, requires custom design |
Maintenance | Regular checks needed for wear and tear | Lower maintenance but periodic inspections required | Requires regular maintenance, particularly for chains |
Best Use Case | Ideal for bulk materials needing vertical lift | Suitable for a variety of materials and distances | Best for heavy, bulk materials in a confined space |
What Are the Pros and Cons of Conveyor Belts?
Conveyor belts offer a flexible solution for transporting materials horizontally or at various inclines. Their versatility allows them to handle a wide range of materials, from lightweight grains to heavy aggregates. The initial setup cost is often lower than that of bucket elevators, making them an attractive option for companies looking to minimize upfront expenses. However, they may require more frequent maintenance and monitoring to ensure optimal performance, especially in high-load scenarios.
How Do Drag Conveyors Compare to Bucket Elevators?
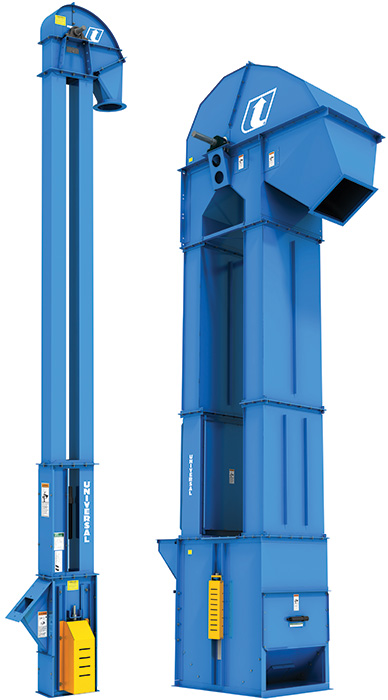
A stock image related to bucket elevator.
Drag conveyors are particularly suited for heavy and abrasive materials, such as mining products and bulk aggregates. They operate at lower speeds, which minimizes material degradation and allows for gentle handling. While drag conveyors often involve a higher initial investment, they can lead to significant long-term savings due to their durability and lower operational costs. However, their installation can be more complex, requiring custom design and engineering to fit specific operational layouts.
Conclusion: Which Bulk Material Handling Solution Is Right for You?
Choosing the right bulk material handling solution ultimately depends on your specific operational requirements, budget, and the types of materials you handle. Bucket elevators are excellent for high-capacity vertical lifting, while conveyor belts provide flexibility for various transport needs. Drag conveyors excel in handling heavy, abrasive materials but may require a more significant investment upfront. By carefully evaluating these alternatives, international B2B buyers can make informed decisions that align with their strategic goals and operational efficiencies.
Essential Technical Properties and Trade Terminology for bucket elevator
What Are the Key Technical Properties of a Bucket Elevator?
When selecting a bucket elevator, understanding its technical specifications is crucial for ensuring optimal performance and compatibility with your material handling needs. Here are several critical properties to consider:
1. Material Grade
The material grade of the bucket elevator’s construction affects its durability and resistance to wear. Common materials include carbon steel, stainless steel, and specialized alloys. For instance, stainless steel is ideal for food-grade applications due to its corrosion resistance. Choosing the right material grade is essential for enhancing the longevity of the equipment and minimizing maintenance costs.
2. Bucket Design and Capacity
Buckets come in various designs—such as standard, deep, or shallow—and are selected based on the type of material being handled. The capacity of the buckets, often measured in liters or kilograms, directly influences the overall throughput of the elevator. Understanding bucket design and capacity is vital for aligning the elevator’s performance with your operational requirements.
3. Discharge Type: Centrifugal vs. Continuous
Bucket elevators can feature either centrifugal or continuous discharge mechanisms. Centrifugal discharge elevators operate at higher speeds and are suitable for free-flowing materials, while continuous discharge elevators are designed for fragile materials that require gentler handling. Knowing the right discharge type is essential for avoiding product damage and ensuring efficient material transfer.
4. Height and Lift
The lift height of a bucket elevator is a key specification that determines how high materials can be transported. This is often linked to the elevator’s horsepower and configuration. For international buyers, especially those dealing with varying building regulations, understanding the height capabilities helps in planning installations and ensuring compliance with local standards.
5. Power and Speed Ratings
Power ratings, typically expressed in horsepower (HP), indicate the motor’s capability to handle the load. Speed ratings, measured in feet per minute (FPM), determine how quickly materials are moved. Both specifications are crucial for optimizing efficiency and energy consumption, which can significantly impact operational costs.
6. Tolerance Levels
Tolerance levels refer to the allowable deviations in manufacturing dimensions. Higher tolerance levels can lead to better operational efficiency and reduced wear and tear on components. For B2B buyers, understanding these tolerances is important for ensuring compatibility with existing systems and maintaining operational reliability.
What Are Common Trade Terminologies Related to Bucket Elevators?
Familiarity with industry jargon can greatly enhance communication and negotiation with suppliers and manufacturers. Here are some essential terms to know:
1. OEM (Original Equipment Manufacturer)
An OEM refers to a company that produces parts and equipment that may be marketed by another manufacturer. In the context of bucket elevators, selecting an OEM ensures that you receive quality components that meet industry standards.
2. MOQ (Minimum Order Quantity)
MOQ represents the smallest quantity of a product that a supplier is willing to sell. Understanding MOQs is important for budgeting and inventory management, especially for international buyers who may face different shipping and storage constraints.
3. RFQ (Request for Quotation)
An RFQ is a formal process where a buyer requests pricing information from suppliers. It is crucial for securing competitive quotes and understanding the full cost of procurement, including shipping and duties.
4. Incoterms (International Commercial Terms)
Incoterms are a set of predefined commercial terms published by the International Chamber of Commerce (ICC) that define the responsibilities of buyers and sellers in international transactions. Familiarity with these terms helps ensure clarity in shipping arrangements and risk management.
5. Lead Time
Lead time refers to the amount of time from the placement of an order to its delivery. Understanding lead times is vital for project planning and inventory control, especially in industries with tight production schedules.
6. Customization
Customization in the context of bucket elevators involves tailoring the equipment to meet specific operational requirements, such as size, capacity, and material handling features. Knowing how to negotiate customization options can lead to more efficient and effective material handling solutions.
By grasping these essential technical properties and trade terminologies, international B2B buyers can make informed decisions when sourcing bucket elevators, ultimately leading to improved operational efficiency and cost savings.
Navigating Market Dynamics and Sourcing Trends in the bucket elevator Sector
What Are the Current Market Dynamics and Key Trends in the Bucket Elevator Sector?
The bucket elevator market is experiencing significant growth, driven by a surge in demand for efficient material handling solutions across various industries, including agriculture, mining, and construction. Key factors propelling this growth include an increasing need for automation and the adoption of advanced technologies. As international B2B buyers from regions such as Africa, South America, the Middle East, and Europe (notably Turkey and Egypt) seek to enhance operational efficiency, the demand for custom and heavy-duty bucket elevators is rising.
Emerging trends in the sector include the integration of IoT technologies for real-time monitoring and predictive maintenance, which can significantly reduce downtime and maintenance costs. Additionally, sustainability is becoming a focal point, with buyers increasingly prioritizing equipment that utilizes energy-efficient designs and materials. The market is also witnessing a shift towards modular and flexible designs that can be tailored to specific material handling requirements, enabling businesses to adapt quickly to changing operational needs.
International buyers must stay informed about local regulations and industry standards that affect equipment specifications and safety requirements. Understanding these dynamics is crucial for making informed purchasing decisions, ensuring compliance, and optimizing supply chain efficiency.
How Can Sustainability and Ethical Sourcing Impact Your Bucket Elevator Purchases?
As global awareness of environmental issues increases, sustainability and ethical sourcing have become essential considerations for B2B buyers in the bucket elevator sector. The environmental impact of manufacturing and operating bucket elevators can be substantial, particularly regarding energy consumption and waste generation. Buyers from Africa, South America, the Middle East, and Europe are increasingly looking for suppliers who prioritize eco-friendly practices, such as using recyclable materials and minimizing energy use in their manufacturing processes.
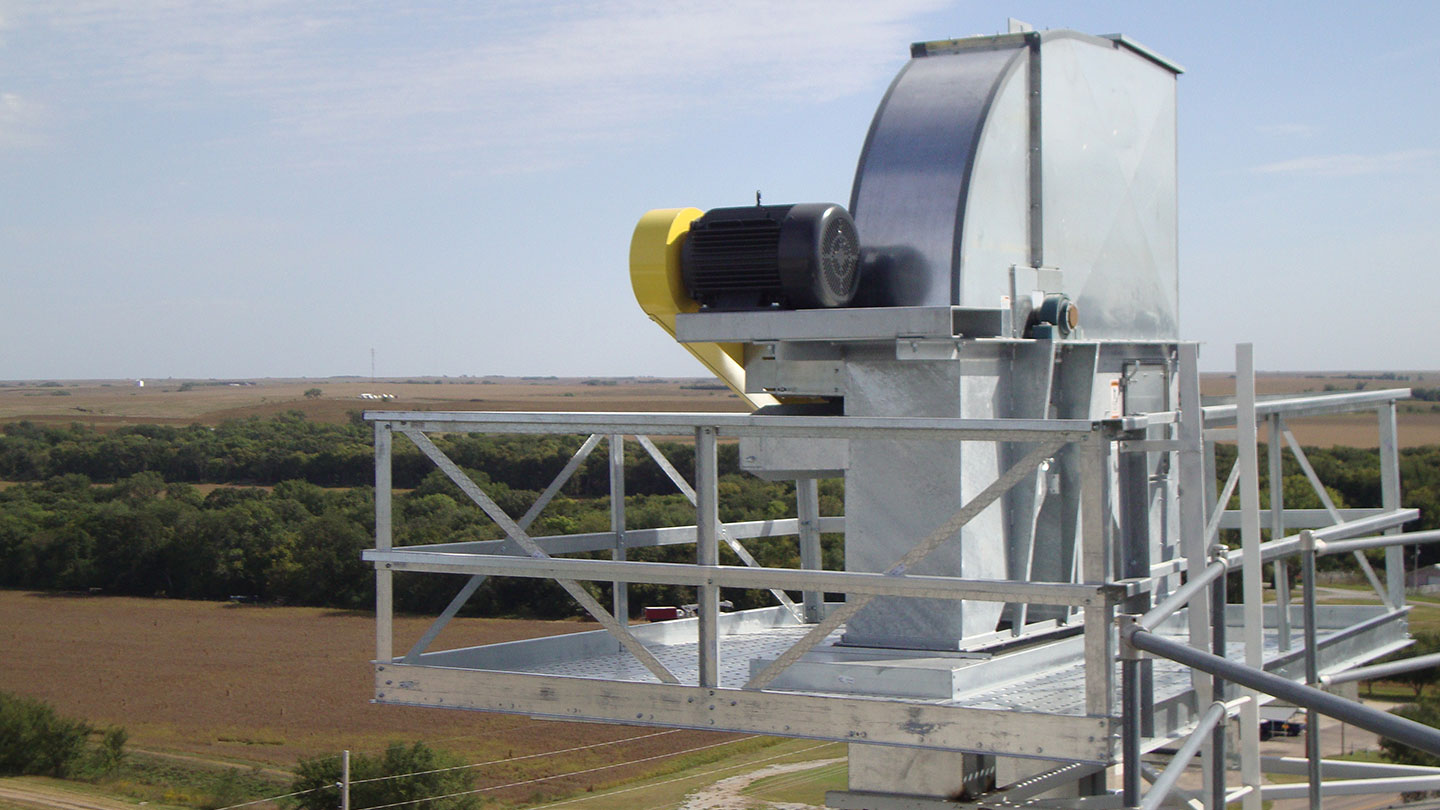
A stock image related to bucket elevator.
Ethical supply chains are also gaining importance. Buyers should look for suppliers who adhere to fair labor practices and transparency in their sourcing processes. Certifications such as ISO 14001 for environmental management and ISO 9001 for quality management can provide assurance of a supplier’s commitment to sustainability.
Investing in bucket elevators that are designed with sustainability in mind not only benefits the environment but also enhances a company’s reputation and aligns with the values of increasingly eco-conscious consumers. This shift towards ‘green’ certifications and materials is not merely a trend; it is a critical component of long-term business strategy.
What Is the Brief Evolution and History of Bucket Elevators in B2B Markets?
The evolution of bucket elevators dates back to the late 19th century when they were first used in grain handling. Initially powered by steam engines, these elevators have undergone significant transformations with advancements in technology. By the mid-20th century, electric motors became the standard, allowing for more efficient operation and increased capacity.
Today, bucket elevators are engineered for specific applications, utilizing advanced materials and designs that enhance durability and performance. The introduction of automation and smart technology has further revolutionized the industry, allowing for real-time monitoring and improved operational efficiency. As the market continues to evolve, international B2B buyers must consider the historical context of bucket elevators to understand the innovations that shape their purchasing decisions today.
Frequently Asked Questions (FAQs) for B2B Buyers of bucket elevator
-
How do I choose the right bucket elevator for my specific material handling needs?
Choosing the right bucket elevator involves assessing the characteristics of the material you intend to handle, such as bulk density, particle size, and temperature. Evaluate whether your material is fragile, abrasive, or requires gentle handling. Consider the desired capacity and height for vertical transport. Consult with manufacturers to ensure that the selected model—whether centrifugal or continuous discharge—fits your operational requirements. Additionally, factor in maintenance needs and space constraints in your facility to optimize efficiency and minimize downtime. -
What is the best bucket elevator for handling fragile materials?
For fragile materials, a continuous bucket elevator is typically the best choice. This type of elevator operates at lower speeds, reducing the impact on delicate products and minimizing breakage. Models with features like weather-tight construction and dust-tight design are ideal for sensitive materials. It’s crucial to consult with suppliers about the specific requirements of your materials, as they can recommend models with specialized buckets and belts that ensure gentle handling and efficient transport. -
What are the common payment terms for international B2B buyers purchasing bucket elevators?
Payment terms for international purchases can vary significantly by supplier and region. Common terms include letters of credit, advance payments, and net 30 or net 60 days after delivery. It’s essential to clarify these terms upfront to avoid any misunderstandings. Many suppliers also offer financing options or installment payments for larger orders. Always negotiate terms that align with your cash flow and project timelines while ensuring the supplier’s reliability and reputation. -
How can I vet suppliers of bucket elevators for international trade?
Vetting suppliers is crucial to ensure quality and reliability. Start by checking their industry experience, customer reviews, and references from previous clients. Request certifications relevant to your industry, such as ISO or CE compliance, which indicate adherence to quality standards. Conduct site visits if possible, or arrange virtual tours to see their manufacturing processes. Additionally, engage in discussions about their after-sales support, warranty terms, and service capabilities to gauge their commitment to customer satisfaction. -
What is the minimum order quantity (MOQ) for bucket elevators?
The MOQ for bucket elevators can vary widely depending on the manufacturer and the customization required. Some suppliers may offer a single unit for specialized needs, while others may require a minimum of five to ten units for standard models to justify production costs. It’s advisable to discuss your specific requirements with potential suppliers, as many are willing to negotiate MOQs based on your business needs and future order potential. -
How do I ensure quality assurance when purchasing bucket elevators internationally?
Quality assurance can be ensured by establishing clear specifications and standards with your supplier before production. Request documentation such as quality control processes, inspection reports, and compliance certificates. Consider arranging third-party inspections during manufacturing or before shipment. Additionally, inquire about warranty policies and after-sales support, as these can indicate the supplier’s commitment to quality and customer satisfaction. -
What logistics considerations should I take into account when importing bucket elevators?
When importing bucket elevators, consider logistics factors such as shipping methods, customs regulations, and lead times. Choose between sea freight for cost-effectiveness or air freight for speed, depending on your urgency and budget. Ensure compliance with local import regulations and tariffs in your country. Collaborate with a reliable freight forwarder to manage shipping logistics, including insurance and tracking, to minimize delays and ensure safe delivery. -
How can I customize my bucket elevator to meet specific operational requirements?
Customization options for bucket elevators typically include modifications in size, material, discharge method, and design features such as bucket shape and belt type. Discuss your operational needs with manufacturers to explore available options, such as weather-tight designs for dusty environments or specialized coatings for corrosive materials. Many suppliers offer tailored solutions that can optimize performance and efficiency for your specific application, so be proactive in communicating your requirements.
Important Disclaimer & Terms of Use
⚠️ Important Disclaimer
The information provided in this guide, including content regarding manufacturers, technical specifications, and market analysis, is for informational and educational purposes only. It does not constitute professional procurement advice, financial advice, or legal advice.
While we have made every effort to ensure the accuracy and timeliness of the information, we are not responsible for any errors, omissions, or outdated information. Market conditions, company details, and technical standards are subject to change.
B2B buyers must conduct their own independent and thorough due diligence before making any purchasing decisions. This includes contacting suppliers directly, verifying certifications, requesting samples, and seeking professional consultation. The risk of relying on any information in this guide is borne solely by the reader.
Strategic Sourcing Conclusion and Outlook for bucket elevator
What Are the Key Takeaways for Strategic Sourcing of Bucket Elevators?
In summary, strategic sourcing of bucket elevators is pivotal for international B2B buyers aiming to optimize their material handling processes. Understanding the various models—such as centrifugal and continuous discharge systems—enables businesses to select equipment tailored to their specific material characteristics and operational needs. Emphasizing quality and reliability in sourcing can lead to reduced downtime and enhanced productivity, which is essential in competitive markets across Africa, South America, the Middle East, and Europe.
Why Is Strategic Sourcing Important for Your Business?
Investing in high-quality bucket elevators from reputable manufacturers not only enhances operational efficiency but also minimizes product damage during handling. This aspect is particularly crucial for industries dealing with fragile materials, such as food processing or pharmaceuticals, where maintaining product integrity is paramount. By prioritizing strategic sourcing, businesses can ensure compliance with industry standards and achieve long-term cost savings.
How Can You Prepare for Future Trends in Bucket Elevator Technology?
Looking ahead, the integration of advanced technologies—such as IoT sensors for real-time monitoring and predictive maintenance—will revolutionize bucket elevator operations. International B2B buyers should stay informed about these innovations and consider suppliers who offer adaptable solutions that can evolve with market demands. Now is the time to engage with trusted suppliers and explore customized options that align with your unique operational goals. Embrace the future of material handling and secure your competitive advantage today.