Master CNC Plastic Machine Sourcing: Top Strategies for B2B
Introduction: Navigating the Global Market for cnc plastic machine
In the rapidly evolving landscape of global manufacturing, CNC plastic machines have emerged as essential tools for businesses seeking precision, efficiency, and flexibility in production. These advanced machines leverage computer numerical control technology to produce intricate plastic components that serve various industries, from automotive and electronics to medical devices and consumer goods. For international B2B buyers, particularly those in Africa, South America, the Middle East, and Europe, understanding the dynamics of sourcing CNC plastic machines is crucial for maintaining competitiveness and driving innovation.
This comprehensive guide offers valuable insights into the world of CNC plastic machining. It explores the various types of CNC machines available, detailing their specific applications and advantages. Additionally, the guide delves into material selection and its impact on product performance, alongside best practices for manufacturing and quality control. Buyers will also find essential information on supplier qualification, cost structures, and the latest market trends affecting CNC plastic machining.
By providing actionable strategies and a thorough understanding of sourcing options, this guide empowers procurement teams to make informed decisions that optimize their supply chain. Whether you are looking to expand production capabilities, enhance product quality, or reduce costs, mastering the nuances of CNC plastic machines will position your business for success in the global marketplace.
Understanding cnc plastic machine Types and Variations
Type Name | Key Distinguishing Features | Primary B2B Applications | Brief Pros & Cons for Buyers |
---|---|---|---|
CNC Plastic Milling | Utilizes rotating cutting tools for precision work | Aerospace, automotive, consumer goods | Pros: High precision, versatile; Cons: Requires skilled operators. |
CNC Plastic Turning | Rotates the workpiece while a stationary tool cuts | Cylindrical parts, fittings, connectors | Pros: Efficient for round parts; Cons: Limited to circular geometries. |
CNC Plastic Router | High-speed spindle for cutting softer materials | Signage, furniture, custom parts | Pros: Cost-effective for large jobs; Cons: Less rigid than milling machines. |
CNC Plastic Laser Cutting | Uses lasers for high-precision cuts | Electronics, medical devices, signage | Pros: Clean cuts, minimal waste; Cons: Slower than traditional methods. |
CNC Plastic 3D Printing | Builds parts layer by layer from digital models | Prototyping, complex geometries | Pros: Flexible designs, quick iterations; Cons: Material limitations. |
CNC Plastic Milling
CNC plastic milling employs rotating cutting tools to create intricate shapes and features from plastic materials. This method is particularly suitable for industries requiring high precision, such as aerospace and automotive. Buyers should consider the supplier’s capability to maintain tight tolerances and the availability of skilled operators to ensure optimal results. The versatility of CNC milling makes it an excellent choice for both prototyping and production runs.
CNC Plastic Turning
CNC plastic turning is ideal for producing cylindrical components, with the workpiece rotating against a stationary cutting tool. This technique is commonly used for manufacturing parts like fittings and connectors in sectors such as oil & gas and automotive. B2B buyers should evaluate the supplier’s ability to handle secondary operations, as additional features may be needed beyond simple turning. While efficient for high-volume production, the geometry limitations may restrict design options.
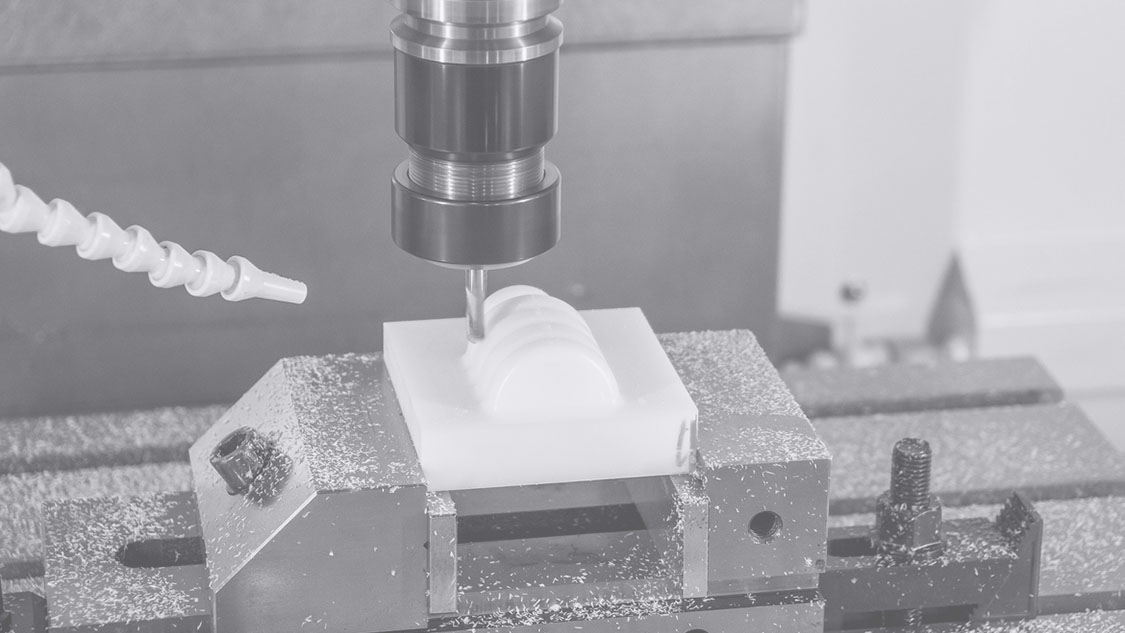
Illustrative Image (Source: Google Search)
CNC Plastic Router
CNC plastic routers utilize high-speed spindles optimized for softer materials, making them a cost-effective solution for large-scale cutting tasks. This method is frequently used in the signage and furniture industries, where rapid production is essential. Buyers should assess the rigidity of the equipment and the supplier’s experience with the specific plastics used in their projects. While routers excel in speed, they may not achieve the same precision as milling machines.
CNC Plastic Laser Cutting
CNC plastic laser cutting offers exceptional precision by using focused laser beams to cut through materials. This method is particularly beneficial for industries like electronics and medical devices, where clean cuts and minimal waste are crucial. Buyers should consider the speed of production and the intricacy of designs when selecting a supplier. While laser cutting can be slower than traditional machining methods, its accuracy and finish quality can justify the trade-off.
CNC Plastic 3D Printing
CNC plastic 3D printing represents a transformative approach to manufacturing, allowing for the creation of complex geometries layer by layer. This technology is ideal for prototyping and applications where design flexibility is paramount. B2B buyers should be aware of material limitations and the potential for slower production speeds compared to traditional methods. However, the ability to rapidly iterate designs and produce customized components makes 3D printing an attractive option for innovative companies.
Related Video: CS 198-126: Lecture 12 – Diffusion Models
Key Industrial Applications of cnc plastic machine
Industry/Sector | Specific Application of cnc plastic machine | Value/Benefit for the Business | Key Sourcing Considerations for this Application |
---|---|---|---|
Automotive | Production of interior trim and components | Lightweight parts improve fuel efficiency and design flexibility | Supplier capabilities in high-volume production and quality control standards |
Medical Devices | Manufacturing custom housings for devices | Enhanced patient safety through precise and reliable components | Compliance with medical standards and rapid prototyping capabilities |
Consumer Electronics | Creation of enclosures and parts for gadgets | Aesthetic appeal and functional design in competitive markets | Material compatibility and supplier experience in high-tech applications |
Packaging | Development of custom containers and packaging | Increased product shelf life and branding opportunities | Sustainability practices and cost-effectiveness of materials |
Aerospace | Fabrication of complex components for aircraft | Reduces weight and enhances performance in aviation | Rigorous testing certifications and precision machining capabilities |
Automotive Industry
In the automotive sector, CNC plastic machines are employed to manufacture lightweight interior trim and components, such as dashboards and door panels. These parts are crucial for improving vehicle fuel efficiency and allowing for innovative designs. International buyers must ensure their suppliers can handle high-volume production while maintaining stringent quality control standards to meet safety regulations and customer expectations.
Medical Devices
CNC plastic machining is pivotal in the medical device industry for producing custom housings and components that require high precision. These parts must adhere to strict regulatory standards to ensure patient safety. Buyers should prioritize suppliers with experience in medical manufacturing, as well as rapid prototyping capabilities to facilitate timely product development and compliance with medical standards.
Consumer Electronics
In the consumer electronics sector, CNC plastic machines are utilized to create enclosures and intricate parts for gadgets, enhancing both functionality and aesthetic appeal. With the rapid pace of innovation, companies need suppliers that can provide materials compatible with high-tech applications while delivering high-quality finishes. Buyers should assess the supplier’s experience in the electronics domain to ensure competitive edge and product reliability.
Packaging
The packaging industry leverages CNC plastic machining to develop custom containers and packaging solutions that enhance product shelf life and branding. By using advanced machining techniques, companies can create unique designs that stand out in the market. Buyers should consider suppliers that prioritize sustainability in their practices and materials, as this is increasingly important to consumers and regulatory bodies alike.
Aerospace
CNC plastic machines play a critical role in the aerospace industry, where they are used to fabricate complex components that contribute to aircraft performance. These lightweight parts help reduce overall weight, which is essential for fuel efficiency and safety. Buyers must ensure their suppliers possess rigorous testing certifications and advanced precision machining capabilities to meet the high standards demanded in the aerospace sector.
Related Video: My Secrets for CNC Machining PLASTIC
Strategic Material Selection Guide for cnc plastic machine
When selecting materials for CNC plastic machining, it’s essential to consider the specific properties and applications of each material. This guide analyzes four common plastics used in CNC machining, focusing on their key properties, advantages, disadvantages, and considerations for international B2B buyers.
Acrylonitrile Butadiene Styrene (ABS)
Key Properties: ABS is known for its excellent impact resistance and toughness. It can withstand temperatures up to 80°C (176°F) and has good chemical resistance against acids and alkalis.
Pros & Cons: The durability of ABS makes it suitable for a wide range of applications, including automotive parts and consumer goods. However, it can be more challenging to machine than other plastics due to its tendency to warp during the cooling process, which may lead to higher manufacturing complexity.
Impact on Application: ABS is often used in applications requiring strength and rigidity, such as housings and structural components. Its compatibility with various media makes it versatile for different industrial uses.
Considerations for International Buyers: Buyers should ensure compliance with regional standards such as ASTM D3965 for ABS. Additionally, sourcing from suppliers familiar with local regulations can help mitigate risks associated with material quality and performance.
Polycarbonate (PC)
Key Properties: Polycarbonate is renowned for its high impact resistance and optical clarity. It can withstand temperatures ranging from -40°C to 120°C (-40°F to 248°F) and has excellent UV resistance.
Pros & Cons: The key advantage of polycarbonate is its ability to absorb significant impacts without breaking, making it ideal for safety applications. However, it can be more expensive than other plastics and may require specialized machining tools due to its toughness.
Impact on Application: Commonly used in safety glasses, automotive components, and electronic housings, polycarbonate’s clarity and strength make it suitable for applications where visibility and durability are critical.
Considerations for International Buyers: Buyers should be aware of the specific grades of polycarbonate that meet local safety standards. Compliance with standards like DIN EN 12150 for glass-like applications may also be necessary.
Nylon (Polyamide)
Key Properties: Nylon exhibits excellent wear resistance and low friction properties, making it ideal for mechanical applications. It can operate effectively at temperatures up to 120°C (248°F) and has good chemical resistance to oils and fuels.
Pros & Cons: The durability and self-lubricating properties of nylon make it suitable for gears and bearings. However, it is hygroscopic, meaning it absorbs moisture, which can affect dimensional stability and performance.
Impact on Application: Nylon’s versatility allows it to be used in various applications, including automotive parts, industrial machinery, and consumer products. Its compatibility with oils and fuels makes it ideal for automotive applications.
Considerations for International Buyers: Buyers should consider the moisture content and environmental conditions of their specific regions, as these factors can impact nylon’s performance. Compliance with standards such as ASTM D4066 can also be essential.
Polyethylene (PE)
Key Properties: Polyethylene is characterized by its low-density structure and excellent chemical resistance. It can withstand temperatures up to 80°C (176°F) and is highly resistant to moisture and various chemicals.
Pros & Cons: The lightweight nature of polyethylene makes it cost-effective for large-scale applications. However, its lower strength compared to other plastics can be a limitation in high-stress environments.
Impact on Application: PE is widely used in packaging, containers, and various consumer goods due to its flexibility and resistance to impact. Its chemical resistance makes it suitable for applications involving corrosive substances.
Considerations for International Buyers: Buyers should ensure that the polyethylene grades they select meet local environmental regulations. Standards such as ISO 1183 for density and ISO 1628 for viscosity can be relevant in ensuring quality.
Summary Table
Material | Typical Use Case for cnc plastic machine | Key Advantage | Key Disadvantage/Limitation | Relative Cost (Low/Med/High) |
---|---|---|---|---|
ABS | Automotive parts, consumer goods | Excellent impact resistance | Tends to warp during machining | Medium |
Polycarbonate | Safety glasses, electronic housings | High impact resistance and clarity | More expensive and requires specialized tools | High |
Nylon | Gears, bearings, industrial machinery | Low friction and wear resistance | Hygroscopic, affecting dimensional stability | Medium |
Polyethylene | Packaging, containers | Lightweight and cost-effective | Lower strength in high-stress applications | Low |
This guide provides a comprehensive overview of material selection for CNC plastic machining, enabling international B2B buyers to make informed decisions tailored to their specific needs and regional requirements.
In-depth Look: Manufacturing Processes and Quality Assurance for cnc plastic machine
The manufacturing processes and quality assurance protocols for CNC plastic machines are crucial for ensuring that products meet the high standards required in various industries. For international B2B buyers, particularly those from Africa, South America, the Middle East, and Europe, understanding these processes and quality checks can significantly influence purchasing decisions and supplier relationships.
Manufacturing Processes for CNC Plastic Machines
The manufacturing of CNC plastic machines typically involves several key stages, including material preparation, forming, assembly, and finishing. Each stage employs specific techniques to ensure precision and quality.
1. Material Preparation
The initial phase involves selecting the appropriate plastic material based on the application requirements. Common materials include:
- Acrylic (PMMA): Known for its clarity and UV resistance.
- Polycarbonate (PC): Offers high impact resistance.
- Nylon (PA): Provides excellent wear resistance and strength.
Once the material is selected, it undergoes processes such as cutting and milling to create manageable sizes for subsequent operations. This preparation is critical as it sets the foundation for the accuracy and integrity of the final product.
2. Forming
CNC machining is the primary technique used in forming components from prepared plastic sheets or blocks. The process involves:
- CNC Milling: Employing rotating multi-point cutting tools to shape the material with high precision. This method is favored for creating complex geometries.
- CNC Turning: Used for cylindrical components, where the workpiece rotates against a stationary cutting tool.
- CNC Routing: Ideal for larger sheets of softer plastics, where high-speed spindles are utilized.
These techniques allow for high accuracy and repeatability, essential for producing parts that meet strict specifications.
3. Assembly
Once the individual components are machined, they may require assembly. This stage can involve:
- Adhesive Bonding: Using specialized adhesives to join different plastic parts.
- Mechanical Fastening: Employing screws, bolts, or clips for secure connections.
- Welding: Utilizing techniques like ultrasonic or laser welding for thermoplastics.
The assembly process must ensure that the final product is structurally sound and functions as intended.
4. Finishing
Finishing processes enhance the aesthetic and functional properties of the machined parts. Common finishing techniques include:
- Sanding and Polishing: To achieve a smooth surface finish.
- Coating: Applying paints or protective coatings for added durability.
- Printing: Adding labels or logos using digital printing technologies.
These finishing touches not only improve the product’s appearance but also its performance in various applications.
Quality Assurance in CNC Plastic Machine Manufacturing
Quality assurance is paramount in CNC plastic machine manufacturing. It ensures that products are consistently produced to meet international standards and customer expectations.
Relevant International Standards
B2B buyers should be aware of various international standards that govern manufacturing quality. Some of the key certifications include:
- ISO 9001: A globally recognized standard that outlines criteria for a quality management system (QMS).
- CE Marking: Indicates compliance with European health, safety, and environmental protection standards.
- API Certification: Relevant for products used in the oil and gas industry, ensuring they meet specific performance standards.
These certifications provide assurance that suppliers adhere to rigorous quality practices.
Quality Control Checkpoints
Quality control (QC) involves several checkpoints throughout the manufacturing process, including:
- Incoming Quality Control (IQC): Inspects raw materials upon arrival to ensure they meet specified standards.
- In-Process Quality Control (IPQC): Monitors production processes to detect and correct issues in real-time.
- Final Quality Control (FQC): Conducts thorough inspections of the finished products to verify compliance with specifications.
Implementing these checkpoints helps minimize defects and enhance product reliability.
Common Testing Methods
To ensure quality, various testing methods may be employed, such as:
- Dimensional Inspection: Using tools like calipers and gauges to measure component dimensions against specifications.
- Material Testing: Assessing physical properties, such as tensile strength and impact resistance.
- Functional Testing: Verifying that the product performs its intended function under expected conditions.
These tests provide crucial insights into product quality and performance.
Verifying Supplier Quality Control
For international B2B buyers, verifying a supplier’s quality control measures is essential for ensuring product reliability. Here are actionable steps to consider:
- Conduct Supplier Audits: Regular audits can assess the effectiveness of a supplier’s quality management system and manufacturing processes.
- Request Quality Reports: Suppliers should provide documentation of their quality control processes, including results from testing and inspections.
- Engage Third-Party Inspectors: Employing independent inspectors can provide an unbiased evaluation of the manufacturing processes and product quality.
Quality Control Nuances for International Buyers
International buyers must navigate several nuances when it comes to quality control:
- Cultural Differences: Understanding the cultural context of suppliers in different regions can influence communication and expectations regarding quality.
- Regulatory Compliance: Buyers should be aware of local regulations that may affect product standards and certification requirements.
- Supply Chain Reliability: Evaluating the entire supply chain, including logistics and transportation, is critical for maintaining quality throughout the product lifecycle.
By emphasizing these quality assurance practices and manufacturing processes, B2B buyers can make informed decisions when sourcing CNC plastic machines, ensuring that they partner with reliable suppliers that meet their standards for quality and performance.
Related Video: Plastic bottle manufacturing process – explained by UpSkul
Comprehensive Cost and Pricing Analysis for cnc plastic machine Sourcing
Understanding the cost structure and pricing dynamics for sourcing CNC plastic machines is essential for international B2B buyers. This analysis delves into the key components that affect pricing, the factors influencing costs, and actionable insights for buyers, particularly in Africa, South America, the Middle East, and Europe.
Cost Components in CNC Plastic Machine Sourcing
-
Materials: The choice of plastic material significantly influences costs. Common materials like ABS, PVC, and polycarbonate vary in price, durability, and machinability. Buyers should consider not only the initial material costs but also their performance characteristics and availability in their region.
-
Labor: Labor costs can vary widely depending on the supplier’s location. Regions with lower labor costs may offer competitive pricing, but this must be balanced with the expertise and experience of the workforce. Skilled labor is crucial for maintaining quality in CNC machining processes.
-
Manufacturing Overhead: This includes operational costs such as utilities, facility maintenance, and administrative expenses. Understanding a supplier’s overhead can help buyers gauge their pricing structure and identify potential areas for negotiation.
-
Tooling: Tooling costs are a significant upfront investment in CNC machining. Depending on the complexity of the part designs, buyers may need to invest in custom tooling, which can add to the initial cost. Long-term production runs can help amortize these costs over time.
-
Quality Control (QC): Implementing robust QC measures ensures that products meet specifications and quality standards. The costs associated with quality control should be factored into the total price, as they can prevent expensive rework or rejects later in the supply chain.
-
Logistics: Shipping and handling costs can be substantial, especially for international shipments. Factors such as distance, shipping method, and customs duties can all impact the final price. Buyers should explore different logistics options to optimize costs.
-
Supplier Margin: The profit margin that suppliers build into their pricing can vary based on their business model, market demand, and competition. Understanding the typical margins in the industry can help buyers negotiate more effectively.
Price Influencers
Several key factors influence the pricing of CNC plastic machines:
-
Volume/MOQ: Minimum Order Quantities (MOQs) and order volumes can significantly affect pricing. Larger orders often yield lower per-unit costs, so consolidating purchases can lead to better pricing.
-
Specifications/Customization: Custom designs and specifications can increase costs due to the additional labor and tooling required. Standardized parts generally cost less, so buyers should assess whether customization is necessary.
-
Material Selection: Different plastic materials come with varying costs. Selecting materials that balance performance and cost can lead to more efficient spending.
-
Quality and Certifications: Higher-quality materials and certified manufacturing processes often come with a premium price. Buyers should evaluate the necessity of certifications like ISO or industry-specific standards based on their end-use applications.
-
Supplier Factors: The supplier’s reputation, location, and production capabilities can all affect pricing. Engaging with suppliers who have proven track records can lead to better pricing and reliability.
-
Incoterms: Understanding Incoterms is crucial as they define the responsibilities of buyers and sellers in international shipping. Different terms can affect the overall cost structure, including shipping and insurance.
Buyer Tips for Cost-Efficiency
-
Negotiate Pricing: Leverage volume and long-term partnerships to negotiate better pricing. Suppliers are often willing to provide discounts for repeat business or bulk orders.
-
Consider Total Cost of Ownership (TCO): Look beyond the initial purchase price. Evaluate maintenance, operational costs, and the expected lifespan of the machine to determine the TCO.
-
Explore Local Suppliers: Whenever possible, consider sourcing from local or regional suppliers to reduce logistics costs and lead times. This can also enhance communication and collaboration.
-
Be Aware of Pricing Nuances: International buyers should be aware of currency fluctuations, import tariffs, and local market conditions that may impact costs. Staying informed can help in making better purchasing decisions.
Disclaimer: Prices for CNC plastic machines can vary widely based on the aforementioned factors. This analysis provides indicative insights, and actual costs should be confirmed with suppliers during the procurement process.
Spotlight on Potential cnc plastic machine Manufacturers and Suppliers
This section looks at several manufacturers active in the ‘cnc plastic machine’ market. This is a representative sample for illustrative purposes; B2B buyers must conduct extensive due diligence before any transaction. Information is synthesized from public sources and general industry knowledge.
Essential Technical Properties and Trade Terminology for cnc plastic machine
In the realm of CNC plastic machining, understanding the essential technical properties and trade terminology is crucial for B2B buyers. This knowledge not only aids in making informed purchasing decisions but also enhances communication with suppliers. Below are critical specifications and common jargon that every international buyer should be familiar with.

Illustrative Image (Source: Google Search)
Key Technical Properties
-
Material Grade
Material grade refers to the specific formulation of plastic used in CNC machining, such as ABS, polycarbonate, or nylon. Each type has unique properties, including strength, flexibility, and thermal resistance. For B2B buyers, selecting the right material grade is vital for ensuring that the final product meets performance requirements and regulatory standards in their respective markets. -
Tolerance
Tolerance defines the acceptable deviation from specified dimensions in a machined part. In CNC plastic machining, tolerances can range from ±0.01 mm to ±0.5 mm, depending on the complexity of the component. High tolerance levels are critical for applications requiring precision, such as medical devices or automotive parts. Understanding tolerance specifications helps buyers ensure compatibility and functionality in their assemblies. -
Surface Finish
The surface finish of a CNC machined part affects both aesthetics and functionality. Common finishes include rough, medium, and polished. A smoother finish can enhance the part’s appearance and reduce friction in moving components. Buyers should consider the required surface finish to achieve the desired performance and visual appeal for their products. -
Dimensional Stability
Dimensional stability refers to a material’s ability to maintain its shape and size under varying environmental conditions, such as temperature and humidity. For B2B buyers, choosing materials with high dimensional stability is essential to prevent warping or distortion during and after the manufacturing process, which can lead to costly rework or product failures. -
Impact Resistance
Impact resistance is the ability of a plastic material to withstand sudden forces or shocks without breaking. This property is particularly important for products used in high-stress environments, such as automotive components or protective housings. Buyers should assess impact resistance to ensure durability and longevity in their applications.
Common Trade Terminology
-
OEM (Original Equipment Manufacturer)
An OEM is a company that produces parts or equipment that may be marketed by another manufacturer. In the context of CNC plastic machining, understanding OEM relationships helps buyers identify reliable suppliers capable of delivering components that meet their specifications. -
MOQ (Minimum Order Quantity)
MOQ refers to the minimum number of units a supplier is willing to produce or sell in a single order. For B2B buyers, knowing the MOQ is essential for budgeting and inventory planning, as it can significantly impact cost per unit and overall procurement strategy. -
RFQ (Request for Quotation)
An RFQ is a formal document that buyers send to suppliers to request pricing, delivery timelines, and terms for specific products or services. This process is crucial for comparing offers and selecting the best supplier based on price and capability.
-
Incoterms (International Commercial Terms)
Incoterms are a set of predefined international trade terms that clarify the responsibilities of buyers and sellers in shipping goods. Understanding these terms helps B2B buyers navigate logistics and shipping costs effectively, ensuring that they are aware of who bears the risk and costs during transportation. -
Lead Time
Lead time is the amount of time from placing an order to its delivery. For international buyers, understanding lead times is essential for planning production schedules and managing supply chain efficiency. Longer lead times can impact market responsiveness and inventory levels.
By familiarizing themselves with these technical properties and trade terms, B2B buyers can enhance their procurement strategies and foster stronger partnerships with suppliers in the CNC plastic machining industry.
Navigating Market Dynamics, Sourcing Trends, and Sustainability in the cnc plastic machine Sector
In the rapidly evolving landscape of CNC plastic machining, international B2B buyers are increasingly influenced by several global drivers and emerging trends. The demand for precision-engineered plastic components across various industries—such as automotive, electronics, and healthcare—continues to grow. Key market dynamics include the rise of automation and Industry 4.0 technologies, enabling manufacturers to achieve higher production efficiencies and flexibility. As a result, buyers from regions like Africa, South America, the Middle East, and Europe should focus on suppliers who leverage advanced CNC technologies and can offer scalable solutions tailored to their specific needs.
Moreover, the increasing emphasis on customization is reshaping sourcing strategies. B2B buyers are seeking suppliers that can adapt quickly to design changes and offer rapid prototyping capabilities. This trend is particularly relevant in competitive markets where time-to-market is crucial. Additionally, the integration of smart manufacturing practices, including IoT-enabled machines and predictive maintenance, is enhancing operational reliability and reducing downtime. For buyers, partnering with technologically advanced suppliers can lead to significant cost savings and improved product quality.
Sustainability & Ethical Sourcing in B2B
Sustainability is becoming a central theme in the sourcing of CNC plastic machining services. The environmental impact of plastic production is a growing concern, prompting buyers to consider suppliers with sustainable practices. This includes the use of recycled materials, biodegradable plastics, and processes that minimize waste and energy consumption.
Ethical supply chains are crucial for maintaining brand reputation and meeting regulatory requirements. Buyers should prioritize suppliers that have transparent sourcing practices and adhere to international standards for environmental management, such as ISO 14001. Furthermore, certifications such as the Global Recycled Standard (GRS) and the Forest Stewardship Council (FSC) can serve as benchmarks for evaluating the sustainability of materials used in CNC plastic machining. By aligning with suppliers committed to ethical practices, businesses can enhance their corporate social responsibility profiles and appeal to environmentally conscious consumers.
Brief Evolution/History
The evolution of CNC plastic machining has been significantly influenced by advancements in technology and materials. Initially reliant on manual processes, the sector has transitioned to automated CNC systems, dramatically increasing precision and production speed. The introduction of computer-aided design (CAD) software allowed for more complex geometries and designs, making CNC plastic machining a preferred choice for manufacturers looking for efficiency and quality.
As the industry progressed, innovations in materials science led to the development of high-performance plastics that are not only lightweight but also durable and resistant to various environmental factors. This evolution has positioned CNC plastic machining as a vital component in modern manufacturing, catering to diverse applications across multiple sectors, thus enhancing its importance in the B2B landscape.
Overall, understanding these dynamics and trends is essential for international B2B buyers seeking to make informed sourcing decisions in the CNC plastic machine sector.
Related Video: What Is International Trade?
Frequently Asked Questions (FAQs) for B2B Buyers of cnc plastic machine
-
How can I effectively vet suppliers of CNC plastic machines?
When vetting suppliers, consider their industry experience, technological capabilities, and customer reviews. Request references from previous clients to gauge reliability. It’s also essential to verify their certifications, such as ISO 9001, which indicates adherence to quality management standards. For international buyers, engage in video calls to assess their operational setup and ensure they can meet your specific requirements. Additionally, visiting the supplier’s facility, if feasible, can provide valuable insights into their production capabilities and quality control processes. -
What customization options should I expect when sourcing CNC plastic machines?
Many suppliers offer customization in terms of machine specifications, such as size, speed, and control software. Discuss your specific applications and the types of plastic materials you plan to process, as this may influence machine design. It’s crucial to communicate your production volume and tolerances, as this will help suppliers recommend the most suitable configurations. Request prototypes or sample runs to evaluate if the customized features meet your operational needs before making a significant investment. -
What are the typical minimum order quantities (MOQ) and lead times for CNC plastic machines?
Minimum order quantities can vary widely based on the supplier and machine specifications. Generally, MOQs can range from one unit for standard machines to several for highly customized options. Lead times typically range from 4 to 12 weeks, depending on the complexity of the machine and the supplier’s production schedule. To avoid delays, plan your orders well in advance and discuss timelines during the negotiation phase to ensure they align with your project schedules. -
What payment terms should I negotiate with international suppliers?
Payment terms can vary significantly, with options including upfront payment, partial payment upon order confirmation, and balance before shipment. Consider using secure payment methods such as letters of credit or escrow services to mitigate risks. Be aware of currency fluctuations and potential transaction fees when dealing with international suppliers. Establish clear terms regarding payment milestones and conditions for any penalties or refunds to protect your investment. -
How can I ensure quality assurance and certifications when sourcing CNC plastic machines?
Request documentation of the supplier’s quality management system, including certifications like ISO 9001 or ISO 13485 for medical applications. Discuss their quality control processes and ask for specific metrics they track to ensure product consistency. Consider implementing a third-party inspection service to conduct audits or quality checks before shipment. Establish clear acceptance criteria and warranty terms to safeguard against defects in materials or workmanship. -
What logistics considerations should I keep in mind when importing CNC plastic machines?
Logistics can be complex, especially when importing machinery. Understand the shipping methods available—air freight is faster but more expensive, while sea freight is cost-effective for heavy machinery. Ensure that the supplier provides all necessary shipping documentation, including a commercial invoice, packing list, and certificate of origin. Familiarize yourself with customs regulations in your country and consider working with a freight forwarder to navigate the import process smoothly. -
How should I handle disputes with international suppliers?
To mitigate disputes, establish clear contractual agreements that detail terms of sale, delivery schedules, and quality expectations. If disagreements arise, start with open communication to resolve the issue amicably. If necessary, refer to the terms outlined in your contract regarding dispute resolution processes, such as mediation or arbitration. It’s advisable to document all communications and agreements to provide a clear record should legal action become necessary. -
What are the common challenges faced when sourcing CNC plastic machines internationally?
Common challenges include language barriers, cultural differences, and varying standards of quality and service. Additionally, international shipping delays and customs clearance issues can impact timelines. To address these challenges, invest time in building a strong relationship with your supplier, employing clear communication strategies, and understanding the local market dynamics. Conducting thorough market research and having contingency plans can also help mitigate risks associated with international sourcing.
Important Disclaimer & Terms of Use
⚠️ Important Disclaimer
The information provided in this guide, including content regarding manufacturers, technical specifications, and market analysis, is for informational and educational purposes only. It does not constitute professional procurement advice, financial advice, or legal advice.
While we have made every effort to ensure the accuracy and timeliness of the information, we are not responsible for any errors, omissions, or outdated information. Market conditions, company details, and technical standards are subject to change.
B2B buyers must conduct their own independent and thorough due diligence before making any purchasing decisions. This includes contacting suppliers directly, verifying certifications, requesting samples, and seeking professional consultation. The risk of relying on any information in this guide is borne solely by the reader.
Strategic Sourcing Conclusion and Outlook for cnc plastic machine
In conclusion, strategic sourcing for CNC plastic machines is essential for international B2B buyers seeking to enhance their manufacturing capabilities. Key takeaways include understanding the diverse types of CNC machining processes and their applications, recognizing the importance of material selection, and ensuring robust supplier qualification and partnership models. By leveraging these insights, businesses can optimize production, reduce costs, and maintain a competitive edge in their respective markets.
As the global landscape continues to evolve, particularly in regions such as Africa, South America, the Middle East, and Europe, the ability to adapt and innovate will be paramount. Buyers are encouraged to actively engage with suppliers, explore emerging technologies, and stay informed about market trends to make data-driven decisions.
Looking ahead, the demand for precision-engineered plastic components will only increase, making it crucial for businesses to prioritize strategic sourcing as a pathway to growth and resilience. Embrace the opportunities that lie ahead, and take proactive steps to forge partnerships that will drive success in the dynamic world of CNC plastic machining.