Your Ultimate Guide to Sourcing Best Cnc Machine For Small
Introduction: Navigating the Global Market for best cnc machine for small business
In an increasingly competitive global market, small businesses must leverage technology to optimize operations and enhance productivity. Computer Numerical Control (CNC) machines stand out as transformative tools, allowing businesses to automate complex manufacturing processes with precision and efficiency. For international B2B buyers, particularly those operating in regions such as Africa, South America, the Middle East, and Europe, selecting the best CNC machine is crucial for meeting diverse production needs while maintaining cost-effectiveness.
This comprehensive guide will navigate you through the essential factors to consider when sourcing CNC machines for small businesses. It covers various types of CNC machines, the range of materials they can process, manufacturing and quality control considerations, and insights on suppliers and pricing. By addressing frequently asked questions, this guide aims to empower buyers with the knowledge necessary to make informed decisions.
Understanding the intricate landscape of CNC technology is essential for small businesses looking to enhance their manufacturing capabilities. Whether you are focused on producing custom furniture, intricate designs, or specialized components, this guide will equip you with actionable insights and strategies to harness the full potential of CNC machining. As you explore your options, you’ll be better positioned to invest wisely and ultimately drive success in your business endeavors.
Understanding best cnc machine for small business Types and Variations
Type Name | Key Distinguishing Features | Primary B2B Applications | Brief Pros & Cons for Buyers |
---|---|---|---|
CNC Router | High-speed cutting and engraving, ideal for wood and soft materials | Furniture making, signage, custom decor | Pros: Versatile, easy to use; Cons: Limited to softer materials. |
CNC Milling Machine | Precision machining for metals and hard materials | Aerospace, automotive, metal fabrication | Pros: High precision; Cons: Higher initial investment. |
CNC Plasma Cutter | Uses plasma to cut through metal, suitable for thick materials | Metal art, industrial fabrication | Pros: Fast cutting of thick materials; Cons: Requires ventilation and safety precautions. |
CNC Laser Cutter | Uses laser technology for cutting and engraving | Jewelry making, intricate designs, prototypes | Pros: Extremely precise; Cons: Limited to thin materials and can be expensive. |
CNC Mill/Turn Center | Combines milling and turning in one machine | Complex parts for machinery, automotive parts | Pros: Versatile for complex machining; Cons: Larger footprint and cost. |
CNC Router
CNC routers are known for their ability to cut and engrave a variety of materials, particularly wood and plastics. They are often used in applications like furniture making, signage production, and custom decor. B2B buyers should consider the machine’s speed, work area, and compatibility with different software. While CNC routers are user-friendly and versatile, they are best suited for softer materials, which may limit their application in industries requiring metal fabrication.
CNC Milling Machine
CNC milling machines are designed for precision machining of metals and harder materials. They are widely utilized in sectors such as aerospace, automotive, and metal fabrication. Buyers should evaluate the machine’s accuracy, spindle speed, and tooling options. Although CNC milling machines offer high precision, they typically require a larger upfront investment and may need more extensive training for operation compared to routers.
CNC Plasma Cutter
CNC plasma cutters utilize high-velocity plasma to cut through metals, making them ideal for thick materials. They find applications in metal art and industrial fabrication. When considering a plasma cutter, buyers should assess the cutting thickness capabilities, software compatibility, and safety measures. While plasma cutters are efficient for heavy-duty tasks, they necessitate proper ventilation and safety precautions, which can add complexity to their operation.
CNC Laser Cutter
CNC laser cutters employ laser technology for cutting and engraving, providing exceptional precision. They are commonly used in jewelry making, intricate design work, and prototyping. B2B buyers should focus on the machine’s wattage, cutting speed, and material compatibility. Although laser cutters offer high accuracy, they are generally limited to thinner materials and can represent a significant investment, especially for high-powered models.
CNC Mill/Turn Center
CNC mill/turn centers combine milling and turning capabilities, allowing for the production of complex parts in one setup. They are particularly valuable in manufacturing machinery and automotive components. Buyers should consider the machine’s versatility, tooling options, and footprint. While these machines offer significant advantages for complex machining tasks, they typically require a larger investment and more space, which may not be feasible for all small businesses.
Related Video: Top 5 Best CNC Machines for Small Business With Offline Controller/Router Bits Review in 2024
Key Industrial Applications of best cnc machine for small business
Industry/Sector | Specific Application of best cnc machine for small business | Value/Benefit for the Business | Key Sourcing Considerations for this Application |
---|---|---|---|
Woodworking | Custom furniture production, including tables and chairs | High precision and repeatability in designs | Ensure compatibility with various wood types and thicknesses; consider dust collection features. |
Metal Fabrication | Creation of metal components, such as brackets and fixtures | Enhanced accuracy and reduced material waste | Assess motor power for metal cutting; verify machine tolerance for high-stress applications. |
Signage | Production of custom signs and plaques | Ability to create intricate designs and personalization | Look for software that supports 2D and 3D designs; consider size for large signs. |
Prototyping | Rapid prototyping for product development | Fast turnaround for design iterations and testing | Evaluate the machine’s software compatibility for CAD/CAM; ensure it can handle multiple materials. |
Jewelry Making | Crafting intricate jewelry pieces | Precision in small, detailed work | Focus on machine size and detail capabilities; consider ease of use for beginners. |
Woodworking
CNC machines have revolutionized the woodworking industry by enabling small businesses to produce custom furniture with high precision and repeatability. By automating the cutting and shaping processes, these machines allow artisans to create complex designs that would be time-consuming and labor-intensive to achieve manually. For international buyers, particularly in regions like Africa and South America, sourcing machines with compatibility for various wood types is essential. Additionally, features such as effective dust collection systems are crucial to maintaining a clean workspace, which can improve efficiency and product quality.
Metal Fabrication
In the metal fabrication sector, CNC machines are employed to create components such as brackets, fixtures, and even custom parts for machinery. The high accuracy of CNC machining significantly reduces material waste, which is a critical consideration for small businesses aiming to maximize profitability. Buyers from the Middle East and Europe should prioritize sourcing machines with adequate motor power to handle metal cutting tasks. Furthermore, understanding machine tolerance for high-stress applications is vital to ensure longevity and reliability in production.
Signage
CNC machines are widely used in the signage industry to produce custom signs and plaques. The ability to create intricate designs and personalized messages makes CNC technology invaluable for businesses looking to differentiate themselves in a competitive market. For buyers in Europe and Africa, it is essential to select machines with software that supports both 2D and 3D designs. Additionally, the machine’s size should be considered, especially for larger signage projects, to ensure that it can accommodate various dimensions without compromising on quality.
Prototyping
Rapid prototyping is another key application of CNC machines, particularly for businesses involved in product development. These machines allow for quick iterations of designs, enabling companies to test and refine their products before mass production. This capability is particularly beneficial for small businesses in South America, where market responsiveness can determine success. Buyers should evaluate the machine’s software compatibility with CAD/CAM systems to streamline the design-to-production process. Furthermore, versatility in handling multiple materials can enhance prototyping capabilities.
Jewelry Making
In the jewelry-making industry, CNC machines facilitate the crafting of intricate pieces that require a high level of detail. The precision offered by CNC technology allows artisans to produce unique designs that meet customer specifications, thus enhancing brand value. For international buyers, particularly in regions like Europe, focusing on machine size and detail capabilities is crucial, especially when working with small components. Additionally, ease of use is a significant consideration for those new to CNC technology, as it can minimize the learning curve and accelerate production.
Related Video: Best CNC Router Machine for Beginners in 2024 | Top 5 | Cut/Engraving
Strategic Material Selection Guide for best cnc machine for small business
When selecting a CNC machine for a small business, the choice of materials is crucial for achieving optimal performance and efficiency. Below, we analyze four common materials that are frequently used in CNC machining, focusing on their properties, advantages, disadvantages, and considerations for international B2B buyers.
Wood
Key Properties:
Wood is a natural material known for its lightweight and ease of machining. It has good tensile strength and can be easily shaped and finished. However, its properties can vary significantly depending on the species and moisture content.
Pros & Cons:
The primary advantage of wood is its availability and low cost. It is also relatively easy to work with, making it suitable for a variety of applications, from furniture to decorative items. On the downside, wood can warp or split under pressure and is susceptible to moisture damage and pests, which may affect durability.
Impact on Application:
Wood is ideal for applications requiring aesthetic appeal, such as custom furniture or decorative pieces. However, it may not be suitable for high-stress applications where structural integrity is paramount.
International Considerations:
Buyers in Africa, South America, the Middle East, and Europe should consider local wood regulations, such as the Convention on International Trade in Endangered Species (CITES), which may affect the sourcing of certain wood types. Compliance with local standards for treated wood is also essential to avoid pest infestations.
Aluminum
Key Properties:
Aluminum is lightweight, corrosion-resistant, and has excellent thermal and electrical conductivity. It can withstand moderate temperatures and pressures, making it suitable for various applications.
Pros & Cons:
The main advantage of aluminum is its strength-to-weight ratio, which makes it ideal for components requiring durability without added weight. However, machining aluminum can be more complex and may require specialized tools, increasing manufacturing costs.
Impact on Application:
Aluminum is commonly used in aerospace, automotive, and consumer electronics applications where lightweight and strong components are necessary. Its corrosion resistance makes it suitable for outdoor applications.
International Considerations:
B2B buyers should ensure compliance with international standards such as ASTM for aluminum alloys. Additionally, understanding the local market for aluminum sourcing and potential tariffs is crucial for cost management.
Plastics
Key Properties:
Plastics, such as acrylic, polycarbonate, and nylon, are versatile materials with varying properties. They can be lightweight, impact-resistant, and available in numerous colors and finishes.
Pros & Cons:
Plastics offer a high degree of customization and are generally easier to machine compared to metals. They are also resistant to corrosion and chemicals. However, some plastics may not withstand high temperatures and can be prone to scratching or wear over time.
Impact on Application:
Plastics are ideal for applications requiring lightweight components, such as housings for electronic devices or prototypes. Their versatility allows for creative designs but may limit their use in high-strength applications.
International Considerations:
Buyers should be aware of local regulations regarding plastic use and recycling, especially in Europe, where strict environmental standards apply. Compliance with standards like ISO for plastic materials can also influence sourcing decisions.
Steel
Key Properties:
Steel is known for its high strength, durability, and resistance to wear and deformation. It can withstand high temperatures and pressures, making it suitable for heavy-duty applications.
Pros & Cons:
The primary advantage of steel is its robustness, making it ideal for structural components and machinery. However, steel is heavier and can be more expensive to machine, requiring specialized tools and techniques.
Impact on Application:
Steel is widely used in construction, automotive, and manufacturing applications where strength and durability are critical. It is less suitable for applications requiring lightweight components.
International Considerations:
B2B buyers must consider compliance with international standards such as ASTM and EN for steel grades. Additionally, understanding local sourcing options and potential trade regulations can impact cost and availability.
Summary Table
Material | Typical Use Case for best cnc machine for small business | Key Advantage | Key Disadvantage/Limitation | Relative Cost (Low/Med/High) |
---|---|---|---|---|
Wood | Custom furniture, decorative items | Low cost, easy to work with | Susceptible to warping, moisture damage | Low |
Aluminum | Aerospace, automotive components | Strength-to-weight ratio | More complex machining | Medium |
Plastics | Electronic housings, prototypes | High customization, lightweight | Limited high-temperature resistance | Medium |
Steel | Heavy-duty machinery, structural components | High strength and durability | Heavier, more expensive to machine | High |
This strategic material selection guide aims to equip international B2B buyers with the necessary insights to make informed decisions regarding CNC machines for their small businesses. Understanding the properties, advantages, and limitations of each material will help optimize production processes and meet specific application requirements.
In-depth Look: Manufacturing Processes and Quality Assurance for best cnc machine for small business
Manufacturing Processes for CNC Machines
When evaluating CNC machines for small businesses, understanding the manufacturing processes involved is crucial. The production of CNC machines typically involves several key stages, each with its specific techniques and requirements.
1. Material Preparation
The first stage in the manufacturing process involves selecting and preparing the materials used in the construction of the CNC machine. Common materials include:
- Aluminum: Lightweight and durable, often used for structural components.
- Steel: Provides strength and stability, particularly in the frame.
- Plastics: Used in non-load bearing components and for insulation.
Material preparation includes cutting raw materials to size, deburring edges, and ensuring that surfaces are clean and free of contaminants. This step is vital for ensuring the integrity of the machine and preventing defects during later stages.
2. Forming
Once materials are prepared, the forming stage begins. This involves various techniques to shape the materials into components:
- CNC Machining: This is often utilized to create intricate shapes and features with high precision. It involves using other CNC machines to mill, turn, or drill parts.
- Laser Cutting: Employed for cutting sheet metals or plastics with precision, allowing for complex designs.
- Bending and Welding: Used for assembling larger components, especially for frames and housing.
Forming techniques must align with the design specifications and tolerances established in the CAD models, ensuring compatibility and performance of the final product.
3. Assembly
After individual components are formed, they are assembled into the final machine. This stage includes:
- Sub-Assembly: Components are often pre-assembled into smaller units (like motors or spindles) before being integrated into the main frame.
- Alignment and Calibration: Ensuring that all parts fit together correctly and are aligned according to specifications is critical. This step often involves adjusting the machine’s mechanical parts to ensure optimal performance.
- Integration of Electronics: This includes installing control systems, wiring, and software interfaces, which are essential for the machine’s operation.
Proper assembly techniques are essential to achieve the required precision and reliability in the final CNC machine.
4. Finishing
The finishing stage focuses on enhancing the appearance and functionality of the CNC machine. This may involve:
- Surface Treatment: Processes like anodizing or powder coating are applied to protect against corrosion and wear, particularly for metal parts.
- Quality Checks: Visual inspections and tests are performed to ensure that components meet quality standards before the machine is packaged for shipment.
Finishing not only impacts aesthetics but also plays a vital role in the machine’s durability and performance.
Quality Assurance (QA) in CNC Machine Manufacturing
Quality assurance is a critical component in the manufacturing of CNC machines, ensuring that each unit meets international standards and customer expectations. Various frameworks and checkpoints are employed throughout the production process.
International Standards
Many manufacturers adhere to internationally recognized standards to ensure product quality and safety:
- ISO 9001: This standard focuses on quality management systems and is applicable across various industries. Manufacturers must demonstrate their ability to consistently provide products that meet customer and regulatory requirements.
- CE Marking: In Europe, CE marking indicates conformity with health, safety, and environmental protection standards for products sold within the European Economic Area (EEA).
For B2B buyers, understanding these certifications can provide assurance of a supplier’s commitment to quality.
Quality Checkpoints
Quality control in CNC machine manufacturing typically involves several checkpoints:
- Incoming Quality Control (IQC): Raw materials are inspected upon arrival to ensure they meet specified standards.
- In-Process Quality Control (IPQC): Continuous monitoring during the manufacturing process helps identify and rectify defects in real-time.
- Final Quality Control (FQC): The final product undergoes comprehensive testing and inspections to verify that it meets all design specifications and quality standards.
These checkpoints are crucial for ensuring that defects are caught early, minimizing waste and rework.
Common Testing Methods
Testing methods vary but generally include:
- Dimensional Inspection: Using tools like calipers and gauges to ensure all components meet dimensional specifications.
- Functional Testing: Assessing the machine’s operational capabilities under load conditions to confirm performance.
- Durability Testing: Simulating extended use to evaluate the machine’s lifespan and reliability.
Implementing robust testing protocols ensures that each CNC machine operates as intended, providing value to end-users.
Verifying Supplier Quality Control
For international B2B buyers, particularly from regions such as Africa, South America, the Middle East, and Europe, verifying a supplier’s quality control measures is essential. Here are strategies to ensure supplier credibility:
-
Supplier Audits: Conducting on-site audits can provide insights into the manufacturing processes, quality control practices, and compliance with international standards.
-
Quality Reports: Requesting detailed quality reports can help assess the supplier’s historical performance and adherence to quality standards.
-
Third-Party Inspections: Engaging third-party inspection agencies can provide an unbiased assessment of the machine’s quality before shipment.
-
Certifications Verification: Always verify that the supplier’s certifications (like ISO and CE) are valid and up to date. This can often be done through the certifying bodies.
Conclusion
Understanding the manufacturing processes and quality assurance practices of CNC machines is vital for B2B buyers looking to invest in these technologies. By focusing on material preparation, forming, assembly, and finishing, alongside robust quality control measures, buyers can ensure they select machines that meet their operational needs and maintain high standards of performance. Furthermore, verifying supplier quality through audits, reports, and third-party inspections can safeguard investments, especially in diverse international markets.
Related Video: Top 10 Small Machines for Manufacturing Businesses || The Ultimate List
Comprehensive Cost and Pricing Analysis for best cnc machine for small business Sourcing
CNC machines represent a significant investment for small businesses, particularly in regions such as Africa, South America, the Middle East, and Europe. Understanding the comprehensive cost structure and pricing analysis is essential for making informed purchasing decisions. This analysis will explore the various cost components, price influencers, and provide actionable tips for international B2B buyers.
Cost Components of CNC Machines
-
Materials: The primary materials involved in the manufacturing of CNC machines include metals (aluminum, steel), plastics, and electronic components. The quality and sourcing of these materials can heavily influence the final price. Buyers should consider the material grade and its impact on machine durability and performance.
-
Labor: Labor costs can vary greatly depending on the region of manufacture. In countries with higher labor costs, such as those in Europe, the manufacturing expenses may increase. Conversely, sourcing from regions with lower labor costs could present savings but may affect quality and lead times.
-
Manufacturing Overhead: This includes the costs associated with running a manufacturing facility, such as utilities, rent, and equipment maintenance. Overhead is typically factored into the final pricing, and understanding this can help buyers gauge whether a supplier’s prices are reasonable.
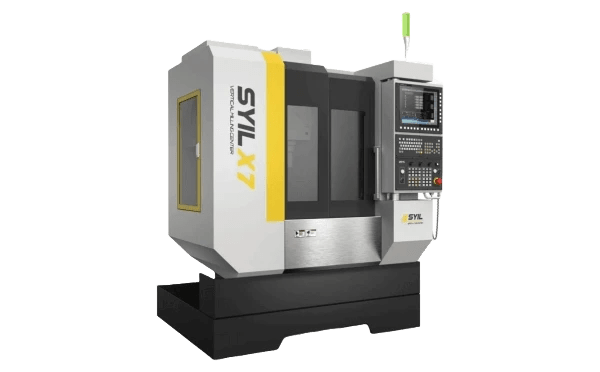
Illustrative Image (Source: Google Search)
-
Tooling: Specialized tools are necessary for CNC machining, and these can be a significant cost factor. Buyers should inquire whether the quoted price includes necessary tooling or if it will incur additional charges.
-
Quality Control (QC): Ensuring that the CNC machines meet international standards and certifications often involves additional QC processes. This can add to the overall cost but is crucial for maintaining product quality and reliability.
-
Logistics: The cost of shipping and handling can vary significantly based on the destination and the Incoterms used. Buyers should be aware of these costs as they can add a substantial amount to the total purchase price.
-
Margin: Suppliers will typically apply a margin to cover their costs and ensure profitability. Understanding the typical margins in your region can help buyers negotiate better prices.
Price Influencers
Several factors can influence the pricing of CNC machines:
-
Volume/MOQ: Purchasing in bulk can often lead to reduced unit prices. Buyers should consider their production needs and potential for future orders when negotiating pricing.
-
Specifications/Customization: Custom specifications can lead to higher costs. Buyers should clearly define their requirements to avoid unnecessary expenses.
-
Materials: The choice of materials not only impacts the performance but also the price. High-quality materials may lead to higher upfront costs but can provide long-term savings through durability and reduced maintenance.
-
Quality/Certifications: Machines with higher certifications or those that meet specific quality standards may come at a premium. However, investing in quality can lead to greater operational efficiency and lower Total Cost of Ownership (TCO).
-
Supplier Factors: The reputation and reliability of suppliers can greatly affect pricing. Established suppliers may charge more due to their proven track record, while new entrants might offer lower prices to gain market share.
-
Incoterms: Understanding shipping terms is crucial for international buyers. Incoterms dictate who is responsible for costs and risks at various stages of the shipping process, affecting the overall price.
Buyer Tips
-
Negotiation: Always negotiate prices, especially when ordering in bulk. Suppliers are often willing to provide discounts for larger orders.
-
Cost-Efficiency: Focus on the Total Cost of Ownership rather than just the upfront price. Consider maintenance costs, energy consumption, and potential downtime.
-
Pricing Nuances: International buyers should be aware of currency fluctuations and import duties that may affect the final cost of CNC machines.
-
Due Diligence: Research suppliers and request references to ensure they can deliver quality products that meet your requirements.
-
Long-Term Relationships: Building a relationship with suppliers can lead to better pricing and terms in future transactions.
Disclaimer
Prices for CNC machines can vary widely based on the aforementioned factors. It’s advisable for buyers to conduct thorough research and obtain multiple quotes to ensure they are receiving competitive pricing.
Spotlight on Potential best cnc machine for small business Manufacturers and Suppliers
This section looks at several manufacturers active in the ‘best cnc machine for small business’ market. This is a representative sample for illustrative purposes; B2B buyers must conduct extensive due diligence before any transaction. Information is synthesized from public sources and general industry knowledge.
Essential Technical Properties and Trade Terminology for best cnc machine for small business
When selecting a CNC machine for a small business, understanding key technical properties and industry terminology is crucial for making informed decisions. Here’s a comprehensive guide to essential specifications and common jargon that will enhance your purchasing strategy.
Key Technical Properties
-
Material Compatibility
– Definition: Refers to the range of materials a CNC machine can effectively process, including wood, metal, plastic, and composites.
– Importance: Ensures the machine aligns with your business’s specific production needs. For instance, a machine designed for wood may not perform well with metal, potentially leading to increased costs and wasted time. -
Tolerance
– Definition: The permissible limit of variation in a physical dimension, typically measured in millimeters or inches.
– Importance: High precision is essential in manufacturing. Machines with tighter tolerances produce parts that fit better and function correctly, which is particularly important in industries such as automotive and aerospace. -
Motor Power
– Definition: The strength of the motors that drive the CNC machine’s movements, usually measured in watts or horsepower.
– Importance: The required motor power depends on the materials being cut and the complexity of the tasks. Insufficient power can lead to slower operation and inadequate cutting performance, affecting overall productivity. -
Cooling System
– Definition: A system designed to dissipate heat generated during operation, often involving fans or liquid cooling.
– Importance: Prevents overheating, which can compromise the machine’s performance and longevity. A reliable cooling system is essential for maintaining consistent production quality and reducing downtime. -
Work Area Dimensions
– Definition: The maximum size of the material that can be processed in a single operation, typically expressed as length x width x height.
– Importance: Ensures that the machine can handle your projects without requiring frequent repositioning of materials, thereby increasing efficiency.
Common Trade Terminology
-
OEM (Original Equipment Manufacturer)
– Definition: A company that produces parts or equipment that may be marketed by another manufacturer.
– Significance: Understanding OEM relationships is vital for sourcing high-quality components and ensuring compatibility with your CNC machine. -
MOQ (Minimum Order Quantity)
– Definition: The smallest number of units a supplier is willing to sell.
– Significance: Helps in budgeting and inventory management. Knowing the MOQ can prevent over-purchasing and ensure you have enough materials for production without incurring excess costs. -
RFQ (Request for Quotation)
– Definition: A document sent to suppliers requesting a price quote for specific goods or services.
– Significance: Essential for comparing costs and negotiating terms with suppliers. A well-structured RFQ can lead to better pricing and service agreements. -
Incoterms (International Commercial Terms)
– Definition: A set of predefined commercial terms published by the International Chamber of Commerce (ICC) that clarify the responsibilities of buyers and sellers in international transactions.
– Significance: Understanding Incoterms is crucial for managing shipping costs and responsibilities, ensuring that both parties are clear on who handles various aspects of transportation. -
CAM (Computer-Aided Manufacturing)
– Definition: Software used to control machine tools in the manufacturing process.
– Significance: Critical for translating CAD designs into machine instructions. Familiarity with CAM software can enhance operational efficiency and precision.
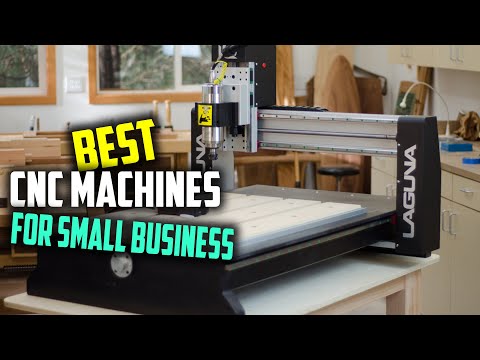
Illustrative Image (Source: Google Search)
By comprehensively understanding these properties and terms, international B2B buyers can make more informed decisions when investing in CNC machines for their small businesses. This knowledge not only aids in selecting the right equipment but also helps in establishing effective supplier relationships and optimizing production processes.
Navigating Market Dynamics, Sourcing Trends, and Sustainability in the best cnc machine for small business Sector
Market Overview & Key Trends
The CNC machine market for small businesses is experiencing robust growth driven by technological advancements and increased demand for precision manufacturing across various industries. Global drivers include the rise of automation in production processes, the push for customization, and the need for efficient resource management. In regions like Africa and South America, a growing manufacturing sector and increased foreign investments are propelling the demand for CNC machines. Meanwhile, the Middle East is leveraging CNC technology to diversify economies away from oil dependence, while Europe is focusing on high-quality, precision engineering.
Current trends indicate a shift towards more compact and versatile CNC machines that cater to small business needs. Emerging technologies such as cloud computing and IoT are being integrated into CNC operations, allowing for real-time monitoring and data analytics, which enhance productivity and minimize downtime. Furthermore, the rise of open-source CNC software is enabling small manufacturers to customize their operations without incurring significant costs, making it easier for international buyers to source machinery that fits their unique production requirements. Buyers should also be aware of regional trade agreements that may affect sourcing costs and availability, particularly in light of geopolitical dynamics.
Sustainability & Ethical Sourcing in B2B
As environmental awareness grows, sustainability has become a crucial factor for B2B buyers in the CNC machine sector. The production of CNC machines can have significant environmental impacts, from resource extraction to manufacturing processes. International buyers must prioritize sourcing from manufacturers who adopt sustainable practices, such as using recycled materials and reducing waste in production.
Ethical supply chains are increasingly important, particularly in regions where labor practices may be scrutinized. Buyers should seek manufacturers that comply with international labor standards and demonstrate a commitment to ethical sourcing. Certifications such as ISO 14001 (Environmental Management) and ISO 45001 (Occupational Health and Safety) can serve as indicators of a company’s commitment to sustainability.
Moreover, the use of “green” materials, such as eco-friendly lubricants and energy-efficient components, is gaining traction. Buyers can also explore CNC machines that incorporate energy-saving technologies, reducing both operational costs and carbon footprints. By aligning purchasing decisions with sustainability goals, international buyers can enhance their brand reputation and appeal to environmentally-conscious consumers.
Brief Evolution/History
The evolution of CNC technology dates back to the 1950s when the first numerically controlled machines were developed. Originally designed for large-scale manufacturing, CNC machines have evolved significantly, becoming more accessible and user-friendly for small businesses. The introduction of CAD/CAM software in the 1980s marked a turning point, allowing for greater design flexibility and precision in machining.
In recent years, advancements in technology have led to the miniaturization of CNC machines, making them suitable for smaller workshops. The rise of desktop CNC routers and affordable 3D printing technologies has democratized access to CNC machining, enabling small business owners to innovate and compete in global markets. Today, CNC machines are integral to various sectors, from woodworking and metal fabrication to prototyping and custom manufacturing, reflecting the dynamic needs of modern businesses.
Related Video: Entry-Level Excellence: Beginner-Friendly Genmitsu PROVerXL 4030 V2 CNC Router Machine Review
Frequently Asked Questions (FAQs) for B2B Buyers of best cnc machine for small business
-
How do I vet suppliers for CNC machines internationally?
When vetting suppliers for CNC machines, consider their industry reputation, customer reviews, and certifications. Start by checking if they are ISO certified, which ensures compliance with international quality standards. Engage with past clients to understand their experiences. Additionally, request detailed product specifications and inquire about after-sales support. Tools such as Alibaba or ThomasNet can help in finding reputable suppliers, but always conduct due diligence by verifying business licenses and requesting samples if possible. -
Can I customize the CNC machine to fit my specific needs?
Many manufacturers offer customization options to tailor CNC machines to your business requirements. Before proceeding, communicate your specific application needs, such as material types and production volume. Inquire about the machine’s capabilities, compatibility with different software, and any additional features you may need. A well-defined customization plan can improve productivity and efficiency, but be sure to clarify any additional costs and lead times associated with these modifications. -
What are typical minimum order quantities (MOQ) and lead times for CNC machines?
MOQs for CNC machines can vary significantly based on the supplier and machine type. Generally, established manufacturers may have a MOQ of one unit for standard models, while custom machines could require higher quantities. Lead times typically range from 4 to 12 weeks, depending on machine complexity and customization. It’s advisable to confirm these details upfront and factor in potential delays due to shipping or customs, especially when sourcing internationally. -
What payment methods are recommended for international CNC machine purchases?
Opt for secure payment methods such as letters of credit or escrow services to protect your investment when dealing with international suppliers. These methods ensure that funds are only released upon meeting specific conditions outlined in your contract. Additionally, consider using PayPal or bank transfers for smaller transactions, as they provide buyer protection. Always clarify payment terms in advance, including deposits, installment payments, and final payment conditions to avoid misunderstandings. -
How can I ensure quality assurance and certifications for the CNC machines I purchase?
Request comprehensive quality assurance documentation from your supplier, including ISO certifications and compliance with local regulations. Ask for a Certificate of Conformity to ensure the machine meets specified standards. Additionally, consider establishing a quality control process that includes pre-shipment inspections or third-party audits. Familiarize yourself with international standards relevant to your industry to ensure that the machines you receive are compliant and of high quality. -
What logistics considerations should I keep in mind when importing CNC machines?
Logistics for importing CNC machines involve understanding shipping methods, customs regulations, and potential tariffs. Choose a reliable freight forwarder experienced in handling machinery to navigate these complexities. Ensure you have the necessary import licenses and understand your country’s customs clearance processes. Additionally, consider insurance for your shipment to protect against loss or damage during transit, and plan for local transportation from the port to your facility. -
How can I handle disputes with international suppliers effectively?
To manage disputes, establish clear terms and conditions in your purchase agreement, including specifics on product quality, delivery timelines, and dispute resolution processes. Consider including a mediation or arbitration clause to address conflicts without resorting to litigation, which can be costly and time-consuming. Maintain open communication with your supplier to resolve issues amicably. If a dispute arises, document all communications and agreements to support your position. -
What are the key factors to consider regarding after-sales support for CNC machines?
After-sales support is crucial for the longevity and efficiency of your CNC machine. Inquire about warranty terms, technical support availability, and whether the supplier provides training for your staff. Assess the availability of spare parts and how quickly they can be delivered if needed. Additionally, consider suppliers who offer maintenance services or support contracts, as this can significantly reduce downtime and enhance your operational efficiency in the long run.
Important Disclaimer & Terms of Use
⚠️ Important Disclaimer
The information provided in this guide, including content regarding manufacturers, technical specifications, and market analysis, is for informational and educational purposes only. It does not constitute professional procurement advice, financial advice, or legal advice.
While we have made every effort to ensure the accuracy and timeliness of the information, we are not responsible for any errors, omissions, or outdated information. Market conditions, company details, and technical standards are subject to change.
B2B buyers must conduct their own independent and thorough due diligence before making any purchasing decisions. This includes contacting suppliers directly, verifying certifications, requesting samples, and seeking professional consultation. The risk of relying on any information in this guide is borne solely by the reader.
Strategic Sourcing Conclusion and Outlook for best cnc machine for small business
In summary, selecting the best CNC machine for your small business is a strategic decision that can significantly enhance productivity and precision in your manufacturing processes. Key considerations include machine capability, pricing, and software compatibility, all of which directly impact your operational efficiency and cost-effectiveness.
For international B2B buyers, particularly in regions like Africa, South America, the Middle East, and Europe, understanding local market dynamics and sourcing options is crucial. Strategic sourcing not only allows you to find quality machines that meet your unique production needs but also helps in establishing long-term supplier relationships that can foster innovation and adaptability in a rapidly evolving marketplace.
As you move forward, consider the scalability of your CNC investments and the potential for integrating advanced technologies. Engaging with local suppliers and leveraging trade partnerships can provide significant advantages in terms of support and service. Embrace the opportunities that CNC technology offers to elevate your business, and take the first step towards transforming your production capabilities today.