Unlock Efficiency: The Ultimate Epicyclic Gear Guide (2025)
Introduction: Navigating the Global Market for epicyclic gear
As global industries increasingly rely on sophisticated mechanical systems, the demand for high-performance components such as epicyclic gears continues to rise. International B2B buyers face a critical challenge in sourcing these essential components, which are pivotal for applications ranging from automotive transmissions to industrial machinery. This comprehensive guide will illuminate the complexities of the epicyclic gear market, exploring various types, applications, and the intricacies of supplier vetting.
In this guide, we delve into the different configurations of epicyclic gears, such as the star, planetary, and solar arrangements, and their respective advantages. Understanding these variations is crucial for selecting the right gear for specific operational needs. Additionally, we will cover cost considerations, best practices for evaluating suppliers, and key factors that influence pricing, helping buyers from regions like Africa, South America, the Middle East, and Europe (including Turkey and Nigeria) make informed purchasing decisions.
By navigating this guide, international B2B buyers will gain valuable insights that empower them to select the most suitable epicyclic gear solutions tailored to their operational requirements. This knowledge not only facilitates effective sourcing strategies but also enhances the overall efficiency and reliability of their mechanical systems.
Understanding epicyclic gear Types and Variations
Type Name | Key Distinguishing Features | Primary B2B Applications | Brief Pros & Cons for Buyers |
---|---|---|---|
Star Configuration | Fixed planet carrier; sun and annulus rotate | Automotive, aerospace | Pros: High torque output, compact design. Cons: Limited gear ratios. |
Planetary | Fixed annulus; sun gear and planet carrier rotate | Robotics, industrial machinery | Pros: Versatile speed ratios, efficient. Cons: Complexity in design and assembly. |
Solar | Fixed sun gear; annulus and planet carrier rotate | Heavy machinery, marine applications | Pros: Simple design, lower manufacturing costs. Cons: Limited torque handling capabilities. |
Compound | Multiple stages of planetary gears for higher ratios | Construction, mining equipment | Pros: Extremely high gear ratios, efficient space usage. Cons: Increased weight and complexity. |
Reverted | Gear arrangement allows for reversed output directions | Electrical drives, conveyor systems | Pros: Flexibility in design, can reverse output. Cons: More wear on components due to complexity. |
What are the Characteristics of Star Configuration Epicyclic Gears?
The star configuration features a fixed planet carrier, allowing the sun and annulus gears to rotate around it. This arrangement is commonly found in automotive and aerospace applications where high torque output is essential. Buyers should consider the star configuration for applications requiring compact designs, though they should be aware of the limited gear ratios it offers.
How Does the Planetary Type of Epicyclic Gear Work?
In the planetary configuration, the annulus gear is fixed while the sun gear and planet carrier rotate. This setup provides versatile speed ratios and is widely used in robotics and industrial machinery. B2B buyers should look for planetary gear systems when efficiency and adaptability are priorities, but they must also consider the complexities involved in design and assembly.
What are the Benefits of Solar Configuration Epicyclic Gears?
The solar configuration has the sun gear fixed, allowing the annulus and planet carrier to rotate. This design is prevalent in heavy machinery and marine applications due to its simplicity and lower manufacturing costs. Buyers should weigh the advantages of ease of use against the limitations in torque handling capabilities when considering this type.
Why Choose Compound Epicyclic Gears for High Gear Ratios?
Compound epicyclic gears consist of multiple stages of planetary gears, enabling extremely high gear ratios in a compact space. They are ideal for construction and mining equipment, where efficiency and power are paramount. While they offer significant advantages in terms of performance, buyers need to be mindful of the increased weight and complexity associated with these systems.
What Makes Reverted Epicyclic Gears Unique?
Reverted epicyclic gears feature an arrangement that allows for reversed output directions, making them suitable for electrical drives and conveyor systems. This flexibility in design is a key advantage for B2B buyers looking for versatile solutions. However, the complexity may lead to increased wear on components, which should be factored into purchasing decisions.
Key Industrial Applications of epicyclic gear
Industry/Sector | Specific Application of epicyclic gear | Value/Benefit for the Business | Key Sourcing Considerations for this Application |
---|---|---|---|
Automotive | Automatic transmissions in vehicles | Enhanced torque efficiency and compact design | Quality certifications, compatibility with vehicle models |
Renewable Energy | Wind turbine gearboxes | Improved energy conversion efficiency | Durability under harsh conditions, maintenance support |
Robotics | Robotic arms and automated machinery | Precision control and space-saving design | Customization options, supplier reliability |
Mining and Construction | Heavy machinery gear systems | High load capacity and reliability | Material specifications, performance under extreme loads |
Aerospace | Aircraft landing gear systems | Lightweight design with high torque transmission | Compliance with aerospace standards, testing certifications |
How is Epicyclic Gear Used in the Automotive Industry?
In the automotive sector, epicyclic gears are primarily utilized in automatic transmissions. This application allows for seamless gear shifting and optimal torque distribution, which is essential for enhancing vehicle performance. For international buyers, particularly in regions like Africa and South America, the demand for fuel-efficient vehicles makes this technology critical. Buyers should consider compatibility with specific vehicle models and ensure that suppliers can provide quality certifications to meet safety and performance standards.
What Role Does Epicyclic Gear Play in Renewable Energy?
Epicyclic gears are integral to wind turbine gearboxes, where they facilitate the conversion of wind energy into electrical energy. Their compact design allows for efficient power transmission, which is crucial in maximizing energy output. For buyers in the Middle East, where renewable energy projects are expanding, sourcing durable epicyclic gear systems that can withstand extreme weather conditions is vital. Buyers should prioritize suppliers who offer robust maintenance support and have experience in the renewable energy sector.
How is Epicyclic Gear Beneficial in Robotics?
In the robotics industry, epicyclic gears are employed in robotic arms and automated machinery to achieve precise motion control while saving space. This is particularly important for industries that require high levels of automation, such as manufacturing. International buyers, especially from Europe, should look for suppliers that can provide customization options to tailor gear systems to specific robotic applications. Reliability and supplier reputation are also key factors in sourcing decisions.
Why are Epicyclic Gears Important in Mining and Construction?
Heavy machinery in mining and construction often relies on epicyclic gears for their ability to handle high loads while maintaining reliability. These gear systems are essential for equipment like excavators and bulldozers, which require robust performance under extreme conditions. Buyers from regions like Nigeria should focus on sourcing materials that meet rigorous performance standards and ensure that the gear systems can endure harsh operational environments.
How Does Epicyclic Gear Contribute to Aerospace Applications?
In the aerospace industry, epicyclic gears are used in aircraft landing gear systems, providing a lightweight yet strong solution for torque transmission. This is critical for ensuring safety and performance in flight operations. European buyers in the aerospace sector need to ensure compliance with stringent aerospace standards and seek suppliers that can provide thorough testing certifications. The focus should be on sourcing high-quality, reliable gear systems that meet the specific demands of the aerospace industry.
3 Common User Pain Points for ‘epicyclic gear’ & Their Solutions
Scenario 1: Difficulty in Calculating Gear Ratios Accurately
The Problem:
B2B buyers often struggle with calculating the correct gear ratios when integrating epicyclic gears into their machinery. This can lead to inefficiencies, such as overloading the gears or failing to achieve the desired speed or torque. Particularly in industries like automotive and manufacturing, where precise performance metrics are critical, incorrect ratios can result in costly downtime and repairs. Buyers may feel overwhelmed by the complexity of the calculations involved and unsure of how to approach the specification of these systems.
The Solution:
To overcome this challenge, buyers should invest time in understanding the fundamental principles of gear ratio calculations specific to epicyclic gear systems. Utilizing software tools that can model gear interactions can simplify the process. Additionally, consulting with experienced engineers or suppliers who specialize in planetary gear systems can provide insights into best practices for calculating ratios. It’s advisable to create a checklist of parameters to consider, including the number of teeth on each gear, the desired output speed, and load requirements. By collaborating with technical experts during the design phase, buyers can ensure that they achieve the correct ratios and enhance operational efficiency.
Scenario 2: Managing Heat Generation and Lubrication Issues
The Problem:
Another significant issue for B2B buyers is the management of heat generation and lubrication in epicyclic gear systems. High friction and inadequate lubrication can lead to overheating, which adversely affects the lifespan and performance of the gears. This scenario is particularly relevant for buyers in industries such as mining and heavy machinery, where equipment operates under extreme conditions. The buyer may feel pressured to maintain productivity while navigating these mechanical challenges, leading to decisions that could compromise equipment integrity.
The Solution:
To effectively manage heat generation, buyers should prioritize selecting high-quality lubricants that are specifically designed for epicyclic gears. Implementing a regular maintenance schedule that includes checking lubrication levels and inspecting for signs of wear can mitigate these risks. Additionally, considering the installation of temperature monitoring systems can provide real-time data on gear performance, allowing for timely interventions. Buyers should also evaluate the gear design for heat dissipation features and consider opting for gear materials that can withstand higher temperatures. By adopting a proactive maintenance approach and utilizing advanced lubricants, buyers can significantly enhance the reliability and longevity of their epicyclic gear systems.
Scenario 3: Sourcing Reliable and Cost-Effective Suppliers
The Problem:
B2B buyers often face challenges in sourcing reliable suppliers for epicyclic gears, particularly in regions like Africa and South America, where supply chains can be less stable. The pressure to find cost-effective solutions without compromising quality can lead to frustration and uncertainty. Inadequate supplier support can result in delays, subpar products, and ultimately, financial losses. Buyers may feel isolated in their procurement efforts, unsure of how to identify trustworthy suppliers.
The Solution:
To tackle this sourcing challenge, buyers should leverage industry networks and platforms that facilitate connections with reputable suppliers of epicyclic gears. Conducting thorough due diligence, including reviewing supplier certifications, past performance, and customer testimonials, is essential. Engaging with industry associations can also provide insights into reliable suppliers and market trends. Additionally, buyers should consider establishing long-term partnerships with suppliers who can offer technical support and after-sales service. By diversifying their supplier base and fostering relationships with multiple vendors, buyers can mitigate risks associated with supply chain disruptions while ensuring they have access to high-quality products at competitive prices.
Strategic Material Selection Guide for epicyclic gear
What Are the Key Materials for Epicyclic Gears?
When selecting materials for epicyclic gears, international B2B buyers must consider various factors that influence performance, durability, and application suitability. The following analysis covers four common materials used in the manufacturing of epicyclic gears: steel, aluminum, brass, and polymer composites. Each material presents unique properties, advantages, and disadvantages that can significantly impact the performance of gear systems.
How Does Steel Perform in Epicyclic Gear Applications?
Steel is the most widely used material for epicyclic gears due to its exceptional strength and durability. Key properties include high tensile strength, good wear resistance, and the ability to withstand high temperatures and pressures.
Pros: Steel gears offer excellent load-bearing capacity, making them suitable for heavy-duty applications. They can also be heat-treated to enhance hardness and wear resistance, which extends their lifespan.
Cons: The primary drawback of steel is its weight, which can be a disadvantage in applications where reducing weight is crucial. Additionally, steel is prone to corrosion if not properly treated or coated, which may lead to increased maintenance costs.
Impact on Application: Steel gears are compatible with a wide range of media, including oils and greases, making them versatile for various industrial applications. However, buyers should ensure compliance with standards such as ASTM A36 or DIN 1.0503.
What Are the Benefits of Using Aluminum in Epicyclic Gears?
Aluminum is increasingly being used in epicyclic gear applications due to its lightweight nature and good corrosion resistance.
Pros: The key advantage of aluminum is its low density, which helps reduce the overall weight of the gear system. This is particularly beneficial in automotive and aerospace applications where weight savings can lead to improved fuel efficiency.
Cons: While aluminum has good strength-to-weight ratios, it is generally not as strong as steel and may not be suitable for high-load applications. Additionally, aluminum gears can be more expensive to manufacture due to the complexities involved in machining and finishing.
Impact on Application: Aluminum gears are often used in environments where corrosion resistance is critical, such as in marine applications. Compliance with standards like ASTM B211 is essential for international buyers to ensure quality.
Why Choose Brass for Epicyclic Gear Manufacturing?
Brass is another material option for epicyclic gears, particularly in applications requiring good machinability and corrosion resistance.
Pros: Brass gears are known for their excellent wear resistance and self-lubricating properties, which can reduce friction and prolong gear life. They are also relatively easy to machine, making them suitable for complex designs.
Cons: The main limitation of brass is its lower strength compared to steel, which may restrict its use in high-load applications. Additionally, brass can be more expensive than steel, impacting overall production costs.
Impact on Application: Brass is compatible with various lubricants and can withstand exposure to moisture, making it suitable for applications in humid environments. Buyers should consider compliance with standards like ASTM C36000.
What Role Do Polymer Composites Play in Epicyclic Gears?
Polymer composites are gaining traction as a lightweight alternative for epicyclic gears, especially in applications where noise reduction is a priority.
Pros: These materials offer excellent noise-dampening properties and are resistant to corrosion and chemical exposure. Their lightweight nature also contributes to energy efficiency in moving parts.
Cons: However, polymer composites generally have lower load-bearing capacities compared to metals, which can limit their use in high-stress applications. Additionally, they may have higher manufacturing costs due to specialized processing techniques.
Impact on Application: Polymer gears are often used in consumer products and automotive applications where noise reduction is essential. Compliance with international standards for polymers, such as ISO 1043, is crucial for ensuring product quality.
Summary Table of Material Selection for Epicyclic Gears
Material | Typical Use Case for Epicyclic Gear | Key Advantage | Key Disadvantage/Limitation | Relative Cost (Low/Med/High) |
---|---|---|---|---|
Steel | Heavy-duty industrial applications | Excellent strength and durability | Heavy and prone to corrosion | Medium |
Aluminum | Automotive and aerospace applications | Lightweight and corrosion-resistant | Lower strength than steel | High |
Brass | Humid environment applications | Good machinability and wear resistance | Lower strength compared to steel | Medium |
Polymer Composites | Consumer products and automotive | Noise reduction and chemical resistance | Limited load-bearing capacity | High |
In conclusion, selecting the right material for epicyclic gears involves balancing performance requirements with cost considerations. International buyers should evaluate their specific application needs and ensure compliance with relevant standards to make informed purchasing decisions.
In-depth Look: Manufacturing Processes and Quality Assurance for epicyclic gear
What Are the Typical Manufacturing Processes for Epicyclic Gears?
The manufacturing of epicyclic gears is a complex process that requires precision and attention to detail. Understanding the main stages of manufacturing and the techniques involved is essential for international B2B buyers, especially those sourcing from regions like Africa, South America, the Middle East, and Europe.
Which Stages Are Involved in Manufacturing Epicyclic Gears?
-
Material Preparation
– The first step involves selecting high-quality materials, typically alloy steels or specialized materials such as aluminum alloys for lightweight applications. The choice of material directly impacts the gear’s performance, durability, and resistance to wear.
– Materials are then cut to size and prepared for further processing. This may involve heat treatment to enhance hardness and strength, which is critical for the longevity of the gears under heavy loads. -
Forming Processes
– Machining: This includes processes like turning, milling, and grinding. Precision machining is vital for ensuring that the gear teeth are accurately formed to allow for smooth meshing with other gears.
– Hobbing: A specialized machining process used to create the gear teeth profiles. Hobbing is particularly efficient for producing large quantities of gears with high accuracy.
– Shaping and Broaching: These methods may also be employed for creating internal gear teeth or complex profiles that cannot be produced through hobbing. -
Assembly
– Once the individual components (sun gear, planet gears, and ring gear) are manufactured, they are assembled into the final epicyclic gear unit. This assembly often requires precise alignment to ensure optimal performance.
– The assembly process may include the installation of bearings and other supportive structures that help in the smooth operation of the gear system. -
Finishing
– After assembly, the gears undergo finishing processes, which may include surface treatments like shot peening or nitriding. These treatments enhance fatigue resistance and improve surface hardness, which is essential for high-performance applications.
– Final inspections are also conducted during this stage to ensure that the gears meet all required specifications and standards.
How Is Quality Assurance Implemented in the Manufacturing of Epicyclic Gears?
Quality assurance is critical to ensuring that epicyclic gears meet both international standards and specific customer requirements. Effective QA processes help mitigate risks and enhance product reliability.
What Are the Relevant International Standards for Quality Assurance?
-
ISO 9001 Certification
– This internationally recognized standard outlines the criteria for a quality management system (QMS). Manufacturers of epicyclic gears should ideally be ISO 9001 certified, which indicates their commitment to quality and continual improvement. -
Industry-Specific Standards
– Depending on the application, additional certifications may apply. For example, gears used in automotive applications may need to comply with specific automotive industry standards, while those used in oil and gas may require API certifications.
– CE marking is also essential for products sold within the European market, indicating compliance with health, safety, and environmental protection standards.
What Are the Key Quality Control Checkpoints in Gear Manufacturing?
-
Incoming Quality Control (IQC)
– This phase involves inspecting raw materials and components upon receipt. It ensures that only materials that meet specified standards proceed to the next stages of manufacturing. -
In-Process Quality Control (IPQC)
– Throughout the manufacturing process, various checkpoints are established to monitor quality. This includes measuring critical dimensions, checking gear tooth profiles, and conducting hardness tests.
– Regular audits during this stage can help catch defects early and reduce waste. -
Final Quality Control (FQC)
– After the finishing processes, a comprehensive inspection is conducted. This may include dynamic testing of the gear assembly under load conditions to assess performance and reliability.
– Non-destructive testing methods, such as ultrasonic or magnetic particle testing, may also be employed to detect internal flaws.
How Can B2B Buyers Verify Supplier Quality Control Processes?
For international B2B buyers, especially those operating in regions like Africa, South America, and the Middle East, ensuring supplier quality is paramount. Here are actionable steps to verify QC processes:
-
Conduct Supplier Audits
– Regular audits of suppliers’ manufacturing facilities can provide insights into their quality control practices. Buyers should assess the supplier’s adherence to international standards and their internal QA processes. -
Request Quality Assurance Reports
– Buyers should ask for detailed quality assurance reports that document the results of inspections and tests conducted throughout the manufacturing process. This transparency is critical in building trust. -
Engage Third-Party Inspectors
– Utilizing third-party inspection services can provide an unbiased assessment of the supplier’s quality control measures. These inspectors can verify compliance with specified standards and identify potential issues before shipment.
What Are the Quality Control Nuances for International B2B Buyers?
Navigating the complexities of quality control in international trade involves understanding regional standards and practices. For buyers in Africa, South America, and Europe, here are key considerations:
-
Cultural Differences in Quality Expectations
Different regions may have varying expectations regarding quality. Understanding these nuances can help in setting realistic quality standards and negotiating contracts. -
Logistical Challenges
International logistics can complicate quality assurance. Buyers should consider how transport conditions may affect product integrity and establish protocols for quality checks upon delivery. -
Legal and Regulatory Compliance
Compliance with local laws and regulations is crucial. Buyers should ensure that their suppliers are not only meeting international standards but also adhering to regional laws regarding product safety and quality.
In conclusion, the manufacturing processes and quality assurance for epicyclic gears are critical factors for B2B buyers to consider. By understanding these processes and implementing thorough verification measures, buyers can ensure they source high-quality products that meet their operational needs.
Practical Sourcing Guide: A Step-by-Step Checklist for ‘epicyclic gear’
This guide provides a structured approach for B2B buyers seeking to procure epicyclic gears. By following these steps, you can ensure that your sourcing process is efficient, cost-effective, and aligned with your technical requirements.
Step 1: Define Your Technical Specifications
Before initiating the procurement process, it is essential to clearly outline your technical requirements. This includes specifications such as gear ratios, torque capacity, and physical dimensions.
– Consider the application: Understand the specific use-case for the epicyclic gear, whether it’s for automotive, industrial machinery, or robotics.
– Document performance requirements: Specify factors like efficiency, operational speed (RPM), and environmental conditions.
Step 2: Research Potential Suppliers
Conduct thorough research to identify reputable suppliers that specialize in epicyclic gears. Utilize industry directories, trade shows, and online platforms to compile a list of potential candidates.
– Look for industry experience: Choose suppliers with a proven track record in manufacturing epicyclic gears.
– Check geographical considerations: Evaluate suppliers from regions like Europe, Africa, and the Middle East, as they may offer localized support and logistics advantages.
Step 3: Evaluate Supplier Certifications
Before proceeding, verify that your shortlisted suppliers possess relevant certifications. This ensures that they adhere to industry standards and quality control measures.
– ISO certifications: Look for ISO 9001 or other applicable quality management standards.
– Industry-specific certifications: Depending on your sector, check for certifications related to automotive or aerospace standards, if applicable.
Step 4: Request Detailed Quotations
Once you have identified potential suppliers, request detailed quotations that include pricing, lead times, and terms of delivery. This step is critical for comparing offers effectively.
– Breakdown of costs: Ensure that the quotation includes all costs, such as shipping, customs duties, and taxes.
– Lead time expectations: Confirm estimated delivery times to align with your project timelines.
Step 5: Assess Quality Control Processes
Investigate the quality control measures implemented by suppliers. Understanding their production processes can help mitigate risks associated with defective products.
– On-site inspections: If possible, arrange for site visits to evaluate manufacturing facilities.
– Quality assurance protocols: Inquire about their testing methods and warranty policies to ensure reliability.
Step 6: Negotiate Terms and Conditions
Before finalizing any contracts, engage in negotiations to secure favorable terms. This could include pricing, payment terms, and after-sales support.
– Flexibility in terms: Discuss options for bulk discounts or payment plans that suit your cash flow requirements.
– After-sales service: Ensure that the supplier offers robust support, including installation assistance and spare parts availability.
Step 7: Establish a Clear Communication Channel
Effective communication is key to a successful procurement process. Establish a direct line of contact with your supplier to facilitate smooth exchanges of information.
– Designate points of contact: Assign dedicated representatives from both sides for efficient communication.
– Regular updates: Schedule periodic check-ins to monitor progress and address any issues promptly.
By following this checklist, you can streamline your sourcing process for epicyclic gears, ensuring that you select the best supplier to meet your technical and operational needs.
Comprehensive Cost and Pricing Analysis for epicyclic gear Sourcing
What Are the Key Cost Components in Epicyclic Gear Sourcing?
When sourcing epicyclic gears, understanding the cost structure is vital for B2B buyers to make informed decisions. The primary cost components include:
-
Materials: The choice of materials significantly impacts the cost. Common materials include steel, aluminum, and composite materials, each with varying costs based on market fluctuations and availability. High-quality materials that meet stringent specifications generally incur higher costs but enhance durability and performance.
-
Labor: Labor costs vary by region and the complexity of manufacturing processes. Regions with lower labor costs may offer competitive pricing, but this could be offset by variations in quality and expertise. Skilled labor is often required for precision machining and assembly in epicyclic gear production.
-
Manufacturing Overhead: This includes costs related to factory operations, such as utilities, equipment maintenance, and indirect labor. Efficient manufacturing processes can help reduce overhead, but buyers should consider these costs when evaluating supplier quotes.
-
Tooling: Custom tooling is often necessary for specific gear designs, which can add to initial costs. However, once established, tooling can lead to cost savings on subsequent orders, especially for high-volume production runs.
-
Quality Control (QC): Implementing stringent QC measures ensures that the gears meet required specifications and certifications. While this may increase upfront costs, it mitigates risks associated with product failure and warranty claims.
-
Logistics: Transportation costs can vary widely depending on the shipping method, distance, and Incoterms negotiated. Understanding the logistics involved is crucial, especially for international buyers who may face tariffs and customs fees.
-
Margin: Suppliers typically include a profit margin in their pricing, which can vary based on market demand, competition, and the supplier’s positioning. Negotiating effectively can help buyers secure better margins.
How Do Pricing Influencers Affect Epicyclic Gear Costs?
Several factors influence the pricing of epicyclic gears, including:
-
Volume/MOQ (Minimum Order Quantity): Bulk purchasing often leads to lower per-unit costs. Suppliers may offer discounts for larger orders, making it essential for buyers to assess their needs and potential for future orders.
-
Specifications and Customization: Custom designs or specifications may lead to increased costs due to the additional engineering and manufacturing processes involved. Buyers should weigh the benefits of customization against potential price increases.
-
Material Selection: The choice of materials not only affects the initial cost but also the long-term performance and maintenance costs of the gears. Opting for premium materials can provide better durability and efficiency, ultimately lowering the Total Cost of Ownership (TCO).
-
Quality and Certifications: Higher quality standards and certifications (such as ISO) often come at a premium. However, investing in certified products can reduce risks and enhance operational reliability.
-
Supplier Factors: The reputation, reliability, and geographical location of suppliers can significantly impact costs. Suppliers located in regions with advanced manufacturing capabilities may command higher prices, but their products may also offer superior quality.
-
Incoterms: The terms of delivery can affect the overall cost. Buyers should be familiar with Incoterms to understand their responsibilities regarding shipping and customs, which can influence total expenses.
What Are the Best Buyer Tips for Cost-Efficient Epicyclic Gear Sourcing?
B2B buyers looking to optimize their sourcing strategy for epicyclic gears should consider the following actionable insights:
-
Negotiate Effectively: Don’t hesitate to negotiate with suppliers. Presenting clear requirements and demonstrating potential for future orders can lead to better pricing arrangements.
-
Focus on Total Cost of Ownership: Consider not just the purchase price but also the long-term costs associated with maintenance, downtime, and energy efficiency. Investing in higher-quality gears can yield savings over time.
-
Understand Pricing Nuances for International Markets: Buyers from Africa, South America, the Middle East, and Europe should be aware of local market conditions, currency fluctuations, and import tariffs that can affect pricing. Engaging local experts can provide valuable insights.
-
Evaluate Multiple Suppliers: Gathering quotes from various suppliers allows for comparison and better understanding of market pricing. It also provides leverage during negotiations.
-
Plan for Long-term Relationships: Building strong relationships with suppliers can lead to better pricing, priority service, and access to new products. Consider suppliers who are willing to collaborate on future projects.
Disclaimer on Indicative Prices
Prices for epicyclic gears can vary widely based on the factors discussed above. The figures provided in this analysis are indicative and should be verified with suppliers for current pricing tailored to specific requirements.
Alternatives Analysis: Comparing epicyclic gear With Other Solutions
Exploring Alternatives to Epicyclic Gears for B2B Buyers
In the realm of mechanical engineering, selecting the right gear system is crucial for optimizing performance, cost, and maintenance. While epicyclic gears, also known as planetary gears, offer unique advantages in compact design and efficiency, other alternatives may better suit specific applications. This analysis will compare epicyclic gears with two viable alternatives: Spur Gears and Helical Gears.
Comparison Table: Epicyclic Gear vs. Alternatives
Comparison Aspect | Epicyclic Gear | Spur Gears | Helical Gears |
---|---|---|---|
Performance | High torque and speed ratios; compact | Moderate torque; good for simple tasks | High load capacity; smoother operation |
Cost | Higher initial cost due to complexity | Lower cost; easy to manufacture | Moderate cost; requires precision machining |
Ease of Implementation | More complex installation; requires skilled labor | Simple installation; widely used | Moderate; needs alignment adjustments |
Maintenance | Low maintenance; robust design | Moderate; wear can occur quickly | Low maintenance; quieter but requires alignment |
Best Use Case | Automotive and robotics; space-constrained applications | Basic machinery; low-speed applications | High-speed applications; where noise reduction is essential |
Detailed Breakdown of Alternatives
What Are Spur Gears and When Should You Use Them?
Spur gears are the simplest type of gear, featuring straight teeth aligned parallel to the gear axis. They excel in applications requiring straightforward torque transmission and are cost-effective due to their simple design and ease of manufacturing. However, spur gears can produce significant noise at high speeds and are limited in the torque they can handle compared to epicyclic gears. They are best suited for applications where space is not a constraint and where noise and vibration are not critical factors.
Understanding Helical Gears: Advantages and Limitations
Helical gears, with teeth cut at an angle, provide smoother engagement than spur gears, resulting in quieter operation and higher load capacity. They are particularly effective in high-speed applications such as automotive transmissions and industrial machinery. However, their more complex design leads to higher manufacturing costs and requires precise alignment during installation. While they offer excellent performance, the need for careful installation and maintenance can be a drawback in certain environments.
How to Choose the Right Gear Solution for Your Needs
When selecting a gear system, B2B buyers should assess their specific operational requirements, including torque needs, available space, and budget constraints. Epicyclic gears are ideal for applications requiring high efficiency and compactness, such as in modern automotive and robotic systems. On the other hand, spur gears may be preferable for simpler, cost-sensitive applications, while helical gears can be the best choice for high-speed and high-load scenarios. By understanding the distinct advantages and limitations of each option, buyers can make informed decisions that align with their operational goals.
Essential Technical Properties and Trade Terminology for epicyclic gear
What are the Essential Technical Properties of Epicyclic Gears?
When evaluating epicyclic gears for B2B applications, understanding their technical properties is vital for ensuring compatibility with specific machinery and operational requirements. Here are some key specifications to consider:
1. Material Grade: Why Does It Matter?
The material used in manufacturing epicyclic gears significantly impacts durability and performance. Common materials include steel alloys, which offer high strength and wear resistance. For applications requiring lower weight, aluminum alloys may be considered. Choosing the right material ensures the gear can withstand operational stresses, reducing maintenance costs and prolonging service life.
2. Gear Ratio: How is it Calculated?
Gear ratio is a crucial specification that defines the relationship between the input and output speeds of the gear system. In epicyclic gear arrangements, the ratio can vary widely depending on the configuration (e.g., sun gear fixed, ring gear fixed). Understanding gear ratios helps buyers predict performance outcomes, such as acceleration and torque distribution, ensuring that the selected gear meets the application’s specific requirements.
3. Tolerance Levels: What Should You Know?
Tolerance refers to the allowable deviation in the dimensions of the gear components. High-precision gears often require tighter tolerances to ensure smooth operation and efficient power transmission. Selecting gears with the appropriate tolerance levels is essential for minimizing backlash and preventing premature wear, thus enhancing the overall reliability of the machinery.
4. Load Capacity: How is it Defined?
Load capacity indicates the maximum load a gear can handle without failure. This property is often expressed in terms of torque (Nm) and is critical for determining whether a particular epicyclic gear can meet the demands of heavy machinery applications. Buyers should assess the load capacity in relation to their specific usage scenarios to avoid gear failure and ensure operational efficiency.
5. Efficiency Rating: Why is it Important?
Efficiency ratings for epicyclic gears reflect how effectively they transmit power without excessive energy loss due to friction. High-efficiency gears contribute to lower operational costs and improved performance in applications such as automotive transmissions and industrial machinery. Buyers should prioritize gears with high efficiency ratings to optimize system performance and reduce energy consumption.
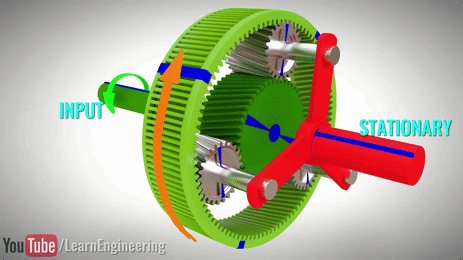
A stock image related to epicyclic gear.
6. Noise and Vibration Levels: What Should You Consider?
Epicyclic gears can generate noise and vibrations during operation, which can affect the comfort and performance of the machinery. Buyers should inquire about the expected noise and vibration levels of the gear system to ensure compliance with industry standards and customer expectations. Selecting gears designed for quiet operation can enhance product quality and customer satisfaction.
What are Common Trade Terminology and Jargon Related to Epicyclic Gears?
Familiarity with industry terminology is crucial for effective communication and negotiation in the B2B marketplace. Here are some essential terms related to epicyclic gears:
1. OEM (Original Equipment Manufacturer): What Does It Mean?
An OEM refers to a company that produces parts or equipment that may be marketed by another manufacturer. In the context of epicyclic gears, OEMs often supply specialized components to machinery manufacturers. Understanding the OEM landscape can help buyers identify reliable suppliers and assess product quality.
2. MOQ (Minimum Order Quantity): Why is it Relevant?
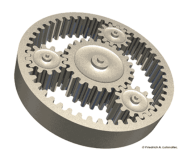
A stock image related to epicyclic gear.
MOQ is the smallest quantity of a product that a supplier is willing to sell. For epicyclic gears, this can impact purchasing decisions, especially for smaller companies or those testing new applications. Knowing the MOQ helps buyers plan their budgets and inventory needs effectively.
3. RFQ (Request for Quotation): How is it Used?
An RFQ is a document sent to suppliers to request pricing information for specific products. For B2B buyers of epicyclic gears, submitting RFQs can facilitate competitive pricing and help identify the best suppliers. Crafting a detailed RFQ ensures that all necessary specifications and requirements are communicated effectively.
4. Incoterms: What are They?
Incoterms (International Commercial Terms) are a set of predefined commercial terms used in international trade. They define the responsibilities of buyers and sellers regarding shipping, insurance, and tariffs. Understanding Incoterms is essential for B2B buyers to negotiate contracts effectively and manage logistics for importing epicyclic gears.
5. Lead Time: Why is it Important?
Lead time refers to the time taken from placing an order until it is delivered. For businesses relying on epicyclic gears for production, understanding lead times is crucial for planning and maintaining operational efficiency. Buyers should consider suppliers with shorter lead times to minimize delays in production.
By grasping these essential properties and terminology, international B2B buyers can make informed purchasing decisions, streamline their procurement processes, and enhance their operational efficiencies in utilizing epicyclic gears.
Navigating Market Dynamics and Sourcing Trends in the epicyclic gear Sector
What Are the Current Market Dynamics and Key Trends in the Epicyclic Gear Sector?
The global epicyclic gear market is experiencing significant growth driven by advancements in automation and the increasing demand for compact and efficient mechanical systems. Industries such as automotive, aerospace, and industrial machinery are the primary consumers of epicyclic gears due to their ability to deliver high torque in limited space, which is crucial for modern applications. Additionally, the growing trend of miniaturization in technology has amplified the need for compact gear solutions, leading to a rise in the adoption of epicyclic gear systems across various sectors.
Emerging technologies such as Industry 4.0 and the Internet of Things (IoT) are reshaping sourcing trends in the epicyclic gear market. B2B buyers from Africa, South America, the Middle East, and Europe are increasingly seeking suppliers who leverage smart manufacturing processes, allowing for real-time monitoring and optimization of production. This shift not only improves efficiency but also enhances supply chain transparency, which is vital for international buyers looking to mitigate risks associated with sourcing.
Moreover, sustainability is becoming a pivotal factor in purchasing decisions. As companies prioritize environmental responsibility, there is a growing trend towards sourcing from manufacturers that adhere to sustainable practices. This encompasses everything from using recyclable materials to implementing energy-efficient manufacturing processes. B2B buyers are encouraged to evaluate potential suppliers based on their commitment to sustainability and their capacity to provide environmentally friendly products.
How Is Sustainability and Ethical Sourcing Affecting the Epicyclic Gear Market?
Sustainability and ethical sourcing are increasingly influencing the purchasing decisions of international B2B buyers in the epicyclic gear sector. The environmental impact of manufacturing processes, particularly in industries that heavily rely on mechanical components, has led to a heightened awareness among buyers regarding the sourcing of materials and production practices. Companies are now more focused on ensuring that their suppliers adopt eco-friendly practices that minimize waste and reduce carbon footprints.
The importance of ethical supply chains cannot be overstated. Buyers are seeking partners who maintain high standards of labor practices and environmental stewardship. Certifications such as ISO 14001 (Environmental Management) and ISO 45001 (Occupational Health and Safety) are becoming essential indicators of a supplier’s commitment to sustainability. Moreover, the use of ‘green’ materials in the production of epicyclic gears, such as recycled metals and environmentally friendly lubricants, is gaining traction, offering buyers more options that align with their corporate social responsibility (CSR) goals.
In addition, the emphasis on transparency within supply chains is driving buyers to demand more information about the origins of materials used in epicyclic gears. By prioritizing suppliers who can provide traceability and demonstrate ethical sourcing practices, B2B buyers can mitigate risks and enhance their brand reputation in a marketplace that increasingly values sustainability.
What Is the Historical Context of the Epicyclic Gear Industry?
The evolution of epicyclic gears dates back to the early 19th century, where they were primarily utilized in clock mechanisms and early industrial machinery. However, the real breakthrough for epicyclic gear systems came with the advent of the automotive industry in the early 20th century. Their ability to provide high gear ratios in compact designs made them ideal for automatic transmissions, revolutionizing vehicle design and performance.
Over the decades, advancements in materials and manufacturing technologies have further enhanced the efficiency and reliability of epicyclic gears. Today, these systems are not only integral to automotive applications but are also widely used in aerospace, robotics, and renewable energy sectors, showcasing their versatility and adaptability in meeting the needs of modern mechanical systems. Understanding this historical context allows B2B buyers to appreciate the technological advancements that have shaped the current landscape of the epicyclic gear market, providing valuable insights into future trends and innovations.
Frequently Asked Questions (FAQs) for B2B Buyers of epicyclic gear
-
How do I choose the right epicyclic gear for my application?
Selecting the appropriate epicyclic gear involves assessing your specific requirements, including torque, speed, size constraints, and operational environment. Evaluate the gear ratio needed, as epicyclic gears can provide high ratios in compact designs. Additionally, consider the type of input and output shafts you need, as well as any space limitations. Collaborate with suppliers to understand their offerings and request samples to test under your operational conditions. -
What are the key advantages of using epicyclic gears in machinery?
Epicyclic gears offer several benefits, including compact design, high efficiency, and versatile torque distribution. They can achieve higher gear ratios within limited space, making them ideal for applications in automotive transmissions and robotics. Additionally, their design minimizes backlash and enhances load distribution, resulting in quieter operation and reduced wear over time. This makes them a reliable choice for demanding industrial applications. -
What should I consider when vetting suppliers for epicyclic gears?
When vetting suppliers, prioritize their experience and reputation in the industry. Check for certifications like ISO 9001, which ensures quality management systems. Request references and case studies from previous clients to gauge their reliability and service quality. Evaluate their capacity for customization and responsiveness to inquiries, as these factors are crucial for building a successful long-term partnership. -
What are the minimum order quantities (MOQs) for epicyclic gears?
MOQs for epicyclic gears can vary significantly among suppliers based on their production capabilities and the specific gear types. Typically, MOQs can range from 50 to several hundred units. If you require a smaller quantity, discuss potential options for prototypes or small-batch orders with the supplier. Many manufacturers are open to negotiation, especially if you express interest in long-term collaboration.
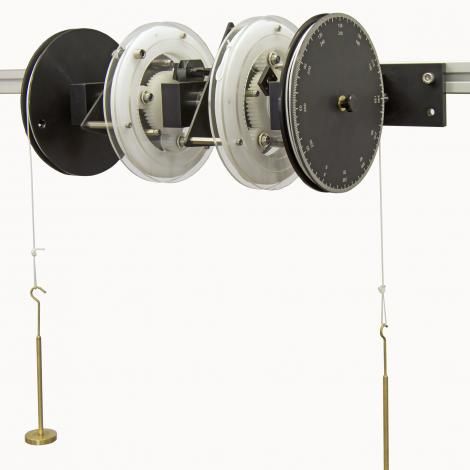
A stock image related to epicyclic gear.
-
How do I ensure quality assurance when sourcing epicyclic gears?
To ensure quality, request detailed specifications and manufacturing processes from your supplier. Implement a quality control plan that includes inspections at various production stages. Consider third-party inspections or certifications to validate the quality of the gears. Establish clear communication regarding your quality expectations and arrange for samples to be tested in your application before placing a larger order. -
What payment terms should I expect when purchasing epicyclic gears internationally?
Payment terms can vary by supplier and region but typically include options like upfront deposits (often 30-50%) followed by the balance upon delivery or after inspection. Some suppliers may offer credit terms for established customers. Ensure you understand the terms before finalizing the order, and consider using secure payment methods like letters of credit or escrow services for large transactions to mitigate risks. -
How can I manage logistics and shipping for my epicyclic gear orders?
Effective logistics management starts with selecting a supplier that has experience in international shipping. Discuss delivery timelines and shipping methods (air, sea, or land) based on your urgency and budget. Work with freight forwarders to optimize shipping routes and costs, and ensure all necessary customs documentation is in order to prevent delays. Tracking shipments can help you stay informed about the status of your order. -
What customization options are available for epicyclic gears?
Customization options for epicyclic gears typically include variations in gear ratios, materials, and coatings. Depending on the supplier’s capabilities, you may also request specific dimensions or features tailored to your application. Discuss your requirements in detail with potential suppliers to understand their design flexibility and lead times for custom orders. This collaborative approach can lead to innovative solutions that enhance your machinery’s performance.
Important Disclaimer & Terms of Use
⚠️ Important Disclaimer
The information provided in this guide, including content regarding manufacturers, technical specifications, and market analysis, is for informational and educational purposes only. It does not constitute professional procurement advice, financial advice, or legal advice.
While we have made every effort to ensure the accuracy and timeliness of the information, we are not responsible for any errors, omissions, or outdated information. Market conditions, company details, and technical standards are subject to change.
B2B buyers must conduct their own independent and thorough due diligence before making any purchasing decisions. This includes contacting suppliers directly, verifying certifications, requesting samples, and seeking professional consultation. The risk of relying on any information in this guide is borne solely by the reader.
Strategic Sourcing Conclusion and Outlook for epicyclic gear
What Are the Key Takeaways for Strategic Sourcing of Epicyclic Gears?
In conclusion, strategic sourcing of epicyclic gears offers significant advantages for international B2B buyers, particularly in regions such as Africa, South America, the Middle East, and Europe. Understanding the unique design features and operational efficiencies of epicyclic gear systems can lead to reduced costs and enhanced performance in various applications, from automotive to industrial machinery. Buyers should prioritize suppliers that provide comprehensive solutions, including customizable gear configurations and robust after-sales support.
How Can B2B Buyers Leverage Strategic Sourcing for Competitive Advantage?
By engaging in strategic sourcing, businesses can tap into a global supply chain that emphasizes quality and innovation. This approach not only facilitates access to advanced technologies but also fosters partnerships with suppliers who are committed to sustainability and ethical practices. As market demands evolve, the ability to source high-performance epicyclic gear systems will empower companies to remain competitive and responsive to changing needs.
What Does the Future Hold for Epicyclic Gear Sourcing?
Looking ahead, B2B buyers are encouraged to stay informed about technological advancements and market trends that influence the epicyclic gear landscape. Investing in relationships with reliable suppliers can yield long-term benefits, ensuring that businesses are well-positioned to adapt to future challenges and opportunities. As you consider your sourcing strategies, prioritize collaboration and innovation to drive growth and efficiency in your operations.