Your Ultimate Guide to Sourcing Cnc Tool Cutter Grinding
Introduction: Navigating the Global Market for cnc tool cutter grinding machine
In today’s competitive manufacturing landscape, the CNC tool cutter grinding machine stands out as a critical asset for businesses aiming to enhance precision, efficiency, and productivity. These advanced machines are essential for producing high-quality cutting tools, which are fundamental to various industries, including automotive, aerospace, and metalworking. As international B2B buyers from Africa, South America, the Middle East, and Europe seek to optimize their supply chains, understanding the nuances of CNC tool cutter grinding machines becomes paramount.
This comprehensive guide is designed to empower buyers by offering in-depth insights into the global market for CNC tool cutter grinding machines. It covers a wide array of topics, including the different types of machines available, the materials they process, and the manufacturing and quality control standards that ensure reliability and performance. Additionally, we delve into supplier evaluations, cost considerations, and current market trends, providing a holistic view of the landscape.
By equipping yourself with the knowledge contained in this guide, you will be better positioned to make informed sourcing decisions. Whether you are a procurement manager in a manufacturing firm or an entrepreneur looking to invest in cutting-edge technology, understanding the intricacies of CNC tool cutter grinding machines will enable you to enhance your operations and drive business growth. Engage with this resource to navigate the complexities of the market confidently and secure the best solutions tailored to your specific needs.
Understanding cnc tool cutter grinding machine Types and Variations
Type Name | Key Distinguishing Features | Primary B2B Applications | Brief Pros & Cons for Buyers |
---|---|---|---|
Universal Tool Grinder | Versatile for various tool shapes and sizes | Aerospace, automotive, and general manufacturing | Pros: Highly versatile; Cons: Can be complex to operate. |
CNC Tool Cutter Grinder | Automated precision grinding | High-volume production environments | Pros: High accuracy; Cons: Initial cost can be high. |
Surface Grinder | Flat surface finishing, often with magnetic tables | Mold making, die manufacturing | Pros: Excellent surface finish; Cons: Limited to flat tools. |
Multi-Axis CNC Grinder | Capable of grinding complex geometries | Medical devices, precision engineering | Pros: Handles intricate designs; Cons: Requires skilled operators. |
Tool and Cutter Grinding Machine | Specialized for sharpening cutting tools | Tool manufacturing and maintenance | Pros: Essential for tool longevity; Cons: Limited to specific tools. |
Universal Tool Grinder
The Universal Tool Grinder is designed to accommodate a wide range of tool shapes and sizes, making it an ideal choice for businesses that require versatility in their grinding operations. This type of machine is commonly utilized in sectors such as aerospace and automotive manufacturing, where different tool specifications are needed frequently. When purchasing, buyers should consider the machine’s adaptability to various tool types and its ease of operation, as some models may have a steeper learning curve.
CNC Tool Cutter Grinder
The CNC Tool Cutter Grinder is an advanced machine that automates the grinding process, providing high precision and efficiency. It is particularly suited for high-volume production environments, where consistent quality and speed are paramount. B2B buyers should weigh the initial investment against long-term savings from reduced labor costs and increased output. Additionally, understanding the software and programming capabilities is essential, as this can significantly impact the machine’s usability.
Surface Grinder
Surface Grinders are specialized for achieving flat surfaces and often feature magnetic tables for tool placement. They are widely used in mold making and die manufacturing, where precision surface finishing is critical. Buyers should evaluate the machine’s capacity to handle various sizes of workpieces and its ability to produce the desired surface finish. While they excel in flat tool grinding, buyers should note that they may not be suitable for all tool shapes.
Multi-Axis CNC Grinder
Multi-Axis CNC Grinders are designed for grinding complex geometries and are crucial in industries like medical device manufacturing and precision engineering. These machines can handle intricate designs that require multiple angles and orientations. When considering a purchase, B2B buyers should assess the machine’s capability to meet specific design requirements and the skill level of operators needed to run such advanced equipment. The investment can yield significant returns through enhanced product quality and innovation.
Tool and Cutter Grinding Machine
Tool and Cutter Grinding Machines are specifically engineered for sharpening cutting tools, making them indispensable in tool manufacturing and maintenance. These machines ensure that tools maintain their effectiveness, which is crucial for operational efficiency. Buyers should focus on the machine’s compatibility with the types of tools they commonly use and its grinding capabilities. While essential for tool longevity, these machines may be limited in their versatility compared to other types, which is an important consideration for businesses looking to optimize their production processes.
Related Video: CNC Tool & Cutter grinding machine – Double Spindle W4+
Key Industrial Applications of cnc tool cutter grinding machine
Industry/Sector | Specific Application of cnc tool cutter grinding machine | Value/Benefit for the Business | Key Sourcing Considerations for this Application |
---|---|---|---|
Aerospace | Precision grinding of turbine blades and components | Enhances performance and safety of aircraft systems | Look for machines with high precision and reliability |
Automotive | Manufacturing cutting tools for engine components | Improves production efficiency and tool lifespan | Consider supplier support and maintenance services |
Metalworking | Production of custom cutting tools and dies | Allows for tailored solutions to meet specific needs | Evaluate machine adaptability to different materials |
Medical Devices | Grinding surgical instruments and implants | Ensures high standards of hygiene and precision | Assess compliance with international quality standards |
Electronics | Fabrication of PCB drilling tools | Increases accuracy in electronic component production | Verify technology compatibility with existing systems |
Aerospace Industry
In the aerospace sector, CNC tool cutter grinding machines are critical for producing precision grinding of turbine blades and other components. These machines ensure that parts meet stringent safety and performance standards, which is vital in an industry where failure can have catastrophic consequences. International buyers should prioritize sourcing machines that offer high precision and reliability, as well as those that can handle the specialized materials often used in aerospace applications.
Automotive Industry
The automotive industry relies heavily on CNC tool cutter grinding machines for the manufacturing of cutting tools used in engine components. These machines help improve production efficiency and extend the lifespan of tools, which ultimately leads to reduced operational costs. Buyers in this sector should consider suppliers that provide robust after-sales support and maintenance services to ensure minimal downtime and consistent production quality.
Metalworking Industry
In metalworking, CNC tool cutter grinding machines are used to produce custom cutting tools and dies tailored to specific project requirements. This capability allows manufacturers to create highly specialized tools that enhance their production processes. B2B buyers should evaluate the adaptability of the machines to work with various materials and the ease of programming for different tool designs, ensuring that their investment can meet evolving production demands.
Medical Devices Industry
For the medical devices sector, CNC tool cutter grinding machines are essential for grinding surgical instruments and implants with high precision. The need for stringent hygiene and precision standards makes these machines invaluable. International buyers must assess the machines for compliance with international quality standards, as well as the ability to produce instruments that meet regulatory requirements across different markets.
Electronics Industry
In the electronics industry, CNC tool cutter grinding machines are utilized for the fabrication of PCB drilling tools. The accuracy of these tools directly impacts the efficiency of electronic component production. Buyers should verify that the machines are compatible with existing systems and technologies, ensuring seamless integration into their manufacturing processes. Additionally, considering the rapid advancements in electronics, the ability to adapt to new designs and specifications is crucial for maintaining a competitive edge.
Strategic Material Selection Guide for cnc tool cutter grinding machine
When selecting materials for CNC tool cutter grinding machines, it is essential to consider various factors that impact performance, durability, and cost. Below is an analysis of four common materials used in this context, focusing on their properties, advantages, disadvantages, and implications for international B2B buyers.
High-Speed Steel (HSS)
Key Properties: High-speed steel is known for its excellent hardness and wear resistance, capable of withstanding high temperatures without losing its temper. It typically has a temperature rating of around 600°C and can endure significant pressure during machining.
Pros & Cons: HSS tools are relatively easy to manufacture and can be sharpened multiple times, extending their lifespan. However, they are generally more expensive than carbon steel and may not perform as well in high-speed applications compared to carbide tools.
Impact on Application: HSS is compatible with a variety of media, making it suitable for general-purpose machining. However, its performance may degrade when used with abrasive materials.
Considerations for International Buyers: Buyers should ensure compliance with local standards such as ASTM A681 or DIN 1.3343. In regions like Europe and the Middle East, HSS is widely accepted, but buyers in Africa and South America should verify availability and local supplier capabilities.
Carbide
Key Properties: Carbide tools are extremely hard and provide excellent wear resistance, withstanding temperatures up to 1000°C. They maintain their cutting edge longer than HSS, making them suitable for high-speed applications.
Pros & Cons: The primary advantage of carbide is its durability and performance in high-speed machining, which reduces cycle times. However, carbide is more brittle than HSS, making it susceptible to chipping and breaking under certain conditions. Additionally, the manufacturing process is more complex and costly.
Impact on Application: Carbide is ideal for machining hard materials and is often used in industries requiring precision, such as aerospace and automotive. Its compatibility with various media enhances its application scope.
Considerations for International Buyers: Buyers should be aware of the need for compliance with standards like ASTM B648 and DIN 4972. In regions such as Europe, carbide tools are preferred for their efficiency, while buyers in Africa may need to consider import costs and availability.
Cobalt Alloys
Key Properties: Cobalt alloys exhibit high temperature and corrosion resistance, making them suitable for extreme environments. They can perform well at temperatures exceeding 1000°C and are resistant to oxidation.
Pros & Cons: The primary advantage of cobalt alloys is their ability to maintain hardness and strength under extreme conditions. However, they are significantly more expensive than both HSS and carbide, and their manufacturing process is complex.
Impact on Application: These materials are particularly effective in applications involving high-speed machining of tough materials. Their corrosion resistance makes them ideal for industries like oil and gas.
Considerations for International Buyers: Compliance with ASTM F75 and JIS G4404 is crucial for buyers. In the Middle East and Europe, cobalt alloys are often required for specialized applications, while buyers in South America may face challenges in sourcing these materials due to higher costs.
Ceramic
Key Properties: Ceramic materials are known for their exceptional hardness and wear resistance, withstanding temperatures up to 1200°C. They are chemically inert and resistant to oxidation and corrosion.
Pros & Cons: Ceramics provide excellent performance in high-speed applications and are ideal for machining hard materials. However, they are brittle and can fracture under shock or impact, limiting their use in certain applications.
Impact on Application: Ceramics excel in high-speed cutting of hard metals and are often used in the aerospace and automotive industries. Their compatibility with abrasive materials makes them a preferred choice in specific applications.
Considerations for International Buyers: Buyers should ensure compliance with standards such as ISO 13006. In Europe, ceramics are increasingly popular, while buyers in Africa and South America may need to consider the availability and cost implications.
Summary Table
Material | Typical Use Case for cnc tool cutter grinding machine | Key Advantage | Key Disadvantage/Limitation | Relative Cost (Low/Med/High) |
---|---|---|---|---|
High-Speed Steel | General-purpose machining | Easy to sharpen and manufacture | Less effective at high speeds | Medium |
Carbide | High-speed machining of hard materials | Excellent wear resistance | Brittle and costly | High |
Cobalt Alloys | Extreme environment applications | High temperature and corrosion resistance | Expensive and complex manufacturing | High |
Ceramic | High-speed cutting of hard metals | Exceptional hardness | Brittle, prone to fracture | High |
This analysis provides actionable insights for international B2B buyers, enabling them to make informed decisions regarding material selection for CNC tool cutter grinding machines.
In-depth Look: Manufacturing Processes and Quality Assurance for cnc tool cutter grinding machine
Manufacturing a CNC tool cutter grinding machine involves several critical stages, each requiring precision and adherence to quality assurance standards. This section provides an overview of the manufacturing processes, key techniques involved, and the quality control measures that international B2B buyers should consider when evaluating suppliers.
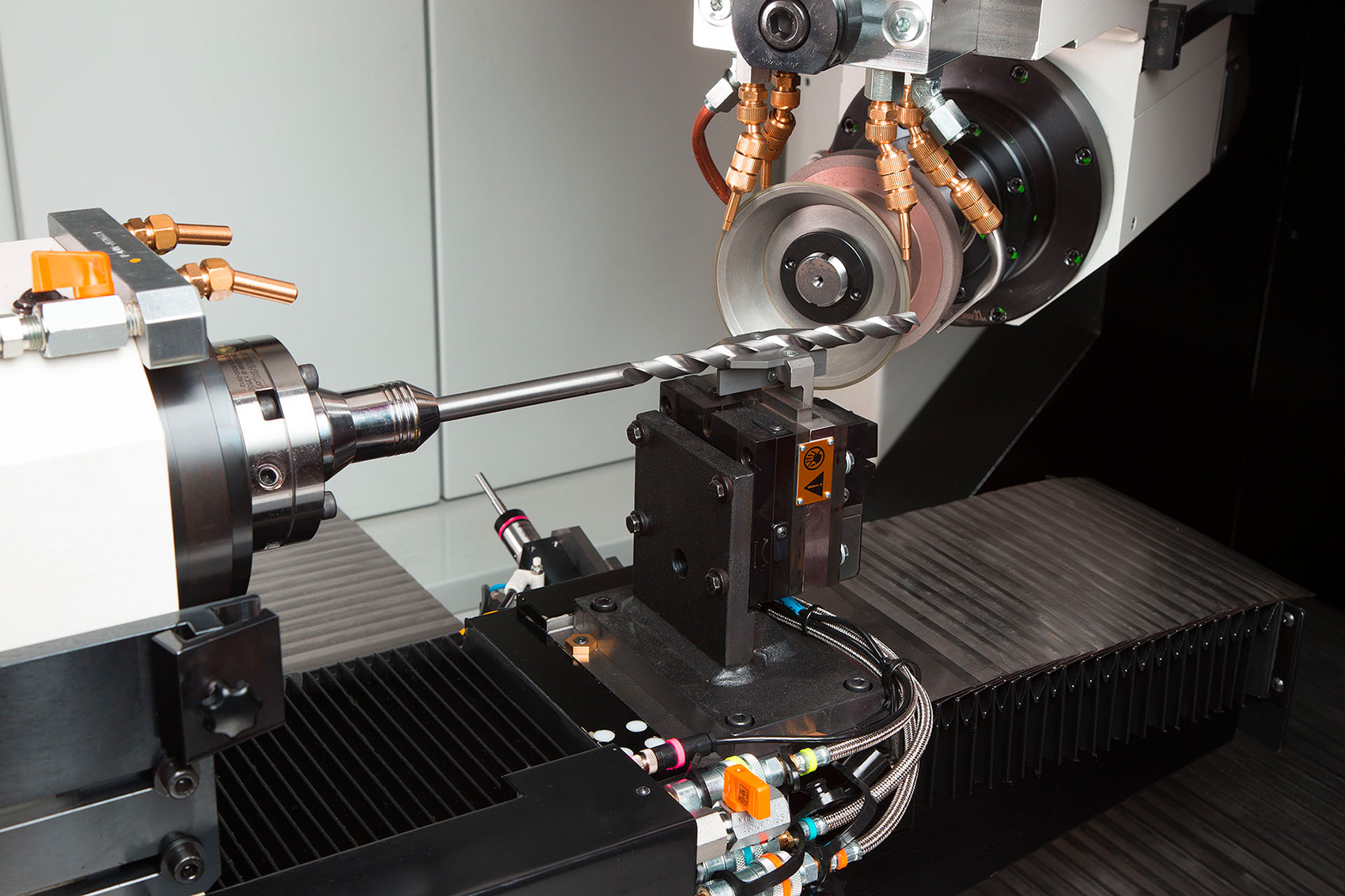
Illustrative Image (Source: Google Search)
Manufacturing Processes
The manufacturing of CNC tool cutter grinding machines generally comprises four main stages: Material Preparation, Forming, Assembly, and Finishing.
Material Preparation
The first step in the manufacturing process is the selection and preparation of raw materials. Typically, high-grade steel or hardened alloys are used for their durability and ability to maintain sharpness.
- Material Inspection: Before use, materials undergo rigorous inspection to ensure they meet specified standards. Buyers should ensure suppliers provide material certificates indicating compliance with international standards such as ASTM or ISO.
- Cutting and Shaping: Raw materials are cut into the required dimensions using high-precision cutting tools. This step may involve laser cutting or water jet cutting for intricate designs.
Forming
In this stage, the components of the CNC tool cutter grinding machine are shaped and formed.
- CNC Machining: Computer Numerical Control (CNC) machining is crucial in this phase, as it allows for high precision in shaping parts. This technique enhances repeatability and accuracy in producing complex geometries.
- Heat Treatment: Components may undergo heat treatment to enhance their hardness and wear resistance. This step is essential for the longevity of the machine’s components.
Assembly
Once the individual components are prepared, the assembly process begins.
- Sub-assembly: Parts are often assembled into sub-units. This modular approach allows for easier handling and quality checks at various stages.
- Final Assembly: The final assembly is carried out with meticulous attention to detail, ensuring that all components fit perfectly and function as intended. Buyers should inquire about the assembly process to understand how quality is maintained during this phase.
Finishing
The finishing stage involves the final touches that ensure the machine operates at optimal performance levels.
- Surface Treatment: This may include grinding, polishing, or coating to enhance surface properties and aesthetics. Buyers should consider the type of finish required for their specific applications.
- Calibration and Testing: After assembly, machines undergo calibration to ensure precision. This step is critical, as it affects the machine’s performance. Buyers should request documentation of calibration processes used.
Quality Assurance
Quality assurance in manufacturing CNC tool cutter grinding machines is paramount, particularly for international buyers. Recognizing and understanding relevant quality standards is essential for evaluating suppliers.
International Standards
- ISO 9001: This is the most recognized quality management standard globally. Suppliers should be ISO 9001 certified, indicating their commitment to maintaining quality in their processes.
- CE Marking: For buyers in Europe, checking for CE marking is crucial, as it indicates that the product meets EU safety, health, and environmental protection standards.
Industry-Specific Standards
Certain industries may require compliance with additional standards:
- API (American Petroleum Institute): For machines used in oil and gas applications, API standards ensure that products meet the necessary operational safety and reliability criteria.
- ANSI (American National Standards Institute): This is relevant for machinery used in specific applications, ensuring compliance with American safety and performance standards.
Quality Control Checkpoints
To ensure quality throughout the manufacturing process, several checkpoints are implemented:
- Incoming Quality Control (IQC): This involves inspecting raw materials upon arrival to confirm they meet specifications.
- In-Process Quality Control (IPQC): During production, regular checks are conducted to monitor processes and identify any deviations from quality standards.
- Final Quality Control (FQC): This is the last checkpoint before the product is shipped. Comprehensive testing and inspections are carried out to ensure the finished product meets all required specifications.
Common Testing Methods
Several testing methods are employed to ensure the quality of CNC tool cutter grinding machines:
- Dimensional Inspection: This involves measuring components to ensure they meet specified tolerances.
- Functional Testing: Machines are tested under operational conditions to verify performance.
- Non-Destructive Testing (NDT): Techniques such as ultrasonic testing or magnetic particle inspection are used to detect internal defects without damaging the components.
Verifying Supplier Quality Control
B2B buyers should adopt a proactive approach to verify the quality control measures of their suppliers:
- Supplier Audits: Conducting audits of suppliers’ facilities can provide insights into their quality management practices. Buyers should request access to audit reports or consider third-party audits for an unbiased assessment.
- Quality Reports: Suppliers should provide regular quality reports detailing inspection results, testing outcomes, and any corrective actions taken.
- Third-Party Inspections: Engaging independent inspection services can help verify that products meet the specified quality standards before shipment.
QC and Certification Nuances for International Buyers
When sourcing from international suppliers, particularly in regions like Africa, South America, the Middle East, and Europe, buyers should be aware of specific nuances:
- Regulatory Compliance: Different regions may have varying regulations and standards. Buyers should ensure that suppliers comply with local laws and international standards relevant to their market.
- Cultural Considerations: Understanding cultural differences in business practices can aid in building strong relationships with suppliers, which is crucial for effective quality management.
- Supply Chain Transparency: Buyers should seek suppliers who demonstrate transparency in their supply chain processes, as this can significantly impact the quality of the final product.
In conclusion, understanding the manufacturing processes and quality assurance measures for CNC tool cutter grinding machines is vital for B2B buyers. By focusing on these elements, buyers can make informed decisions, ensuring they partner with reliable suppliers who meet international standards and deliver high-quality products.
Related Video: SMART Quality Control for Manufacturing
Comprehensive Cost and Pricing Analysis for cnc tool cutter grinding machine Sourcing
Understanding the Cost Structure of CNC Tool Cutter Grinding Machines
When sourcing CNC tool cutter grinding machines, international B2B buyers must grasp the intricate cost structure involved. The primary components include:
-
Materials: The choice of materials significantly impacts the overall cost. High-grade steel and advanced composites may increase initial expenses but enhance durability and performance.
-
Labor: Labor costs vary by region. In countries with higher wages, such as many in Europe, labor can constitute a larger portion of the total cost. Conversely, in regions like South America or parts of Africa, labor might be less expensive, but skill levels can vary.
-
Manufacturing Overhead: This encompasses indirect costs associated with production, such as utilities, rent, and administrative expenses. Efficient factories with optimized processes can reduce these costs, which can be passed on to buyers.
-
Tooling: Custom tooling for specific grinding applications can add to costs, especially if the buyer requires unique specifications. Standardized tooling may reduce costs, but it could limit flexibility.
-
Quality Control (QC): Implementing rigorous QC measures ensures product reliability but can increase costs. Buyers should balance the importance of QC with their budget constraints.
-
Logistics: Transportation and handling costs are critical, especially for international shipments. Factors such as distance, mode of transport, and insurance can all influence this component.
-
Margin: Supplier profit margins vary widely. Understanding the market landscape can help buyers negotiate better terms.
Price Influencers in CNC Tool Cutter Grinding Machines
Several factors can influence the pricing of CNC tool cutter grinding machines:
-
Volume/MOQ: Larger orders often qualify for bulk pricing discounts. Buyers should consider their long-term needs and potential for future orders to negotiate better rates.
-
Specifications/Customization: Custom machines tailored to specific applications can be significantly more expensive than standard models. Buyers need to assess whether customization is necessary for their operations.
-
Materials: The quality of materials used directly affects both performance and price. Buyers should inquire about the materials to ensure they align with their operational needs.
-
Quality Certifications: Machines that meet international quality standards (e.g., ISO, CE) may come at a premium. However, these certifications can enhance reliability and safety, potentially reducing total costs in the long run.
-
Supplier Factors: The supplier’s reputation, production capabilities, and financial stability can impact pricing. Established suppliers may charge more but offer better service and reliability.
-
Incoterms: Understanding the Incoterms (International Commercial Terms) governing the shipment can affect pricing. Terms like FOB (Free on Board) or CIF (Cost, Insurance, and Freight) dictate who is responsible for shipping costs, insurance, and risks, impacting the final price.
Buyer Tips for Cost-Efficient Sourcing
To maximize value while sourcing CNC tool cutter grinding machines, international B2B buyers should consider the following:
-
Negotiate Terms: Always negotiate pricing, payment terms, and delivery schedules. Suppliers may be flexible, especially with larger orders.
-
Evaluate Total Cost of Ownership (TCO): Beyond the initial purchase price, consider maintenance, operational costs, and potential downtime. A machine that is slightly more expensive upfront may offer greater savings over time.
-
Pricing Nuances: Be aware of regional pricing trends. For example, suppliers in Africa may have different pricing structures than those in Europe or South America, influenced by local market conditions and demand.
-
Research and Compare: Obtain quotes from multiple suppliers to ensure competitive pricing. Comparing specifications, quality, and support services will help make informed decisions.
-
Consider Local Regulations: Be mindful of import duties, taxes, and compliance costs that may apply when bringing machines into your region, as these can significantly affect the overall expenditure.
Disclaimer
The prices mentioned in this analysis are indicative and subject to change based on market conditions, supplier negotiations, and other variables. Buyers are encouraged to conduct thorough market research and engage with suppliers to obtain accurate pricing information tailored to their specific needs.
Essential Technical Properties and Trade Terminology for cnc tool cutter grinding machine
When evaluating CNC tool cutter grinding machines, understanding their technical properties and trade terminology is crucial for informed purchasing decisions. This section outlines essential specifications and common industry terms that can significantly impact B2B transactions.
Essential Technical Properties
-
Material Grade
The material grade of the machine’s components, particularly the spindle and frame, determines its durability and performance. High-grade materials, such as cast iron or high-strength steel, enhance stability and reduce vibration, leading to improved precision in grinding. For B2B buyers, investing in machines with superior material grade can result in lower maintenance costs and longer machine life. -
Tolerance Levels
Tolerance refers to the allowable deviation from a specified dimension in the grinding process. Machines are typically rated by their ability to maintain tight tolerances, often within micrometers. For manufacturers, achieving precise tolerances is vital for producing high-quality tools that meet stringent industry standards, ultimately affecting product reliability and customer satisfaction. -
Spindle Speed
Spindle speed, measured in revolutions per minute (RPM), is a critical factor in determining the efficiency and effectiveness of the grinding process. Higher spindle speeds can lead to faster material removal rates but may also generate more heat. B2B buyers should assess their production needs and select machines that balance speed with the quality of the finished product. -
Grinding Wheel Size and Type
The size and type of grinding wheel used influence the machine’s versatility and the range of materials it can handle. Common types include vitrified, resin-bonded, and diamond wheels, each suited for different applications. Understanding the wheel specifications allows buyers to select machines that align with their specific grinding requirements, enhancing operational efficiency. -
Control System
The control system of a CNC tool cutter grinding machine dictates how operators interact with the equipment. Advanced systems, such as those featuring touch screens and user-friendly interfaces, facilitate easier programming and operation. For international B2B buyers, investing in machines with robust control systems can lead to reduced training time and increased productivity. -
Cooling Systems
Effective cooling systems are essential in preventing overheating during the grinding process. Machines equipped with advanced cooling mechanisms can maintain optimal operating temperatures, thereby extending tool life and ensuring consistent performance. B2B buyers should prioritize machines that offer efficient cooling solutions to enhance their production capabilities.
Common Trade Terminology
-
OEM (Original Equipment Manufacturer)
An OEM refers to a company that produces parts and equipment that may be marketed by another manufacturer. Understanding OEM relationships is crucial for buyers seeking high-quality components or machines, as OEMs often provide superior products backed by warranties and support. -
MOQ (Minimum Order Quantity)
MOQ is the smallest quantity of a product that a supplier is willing to sell. For international buyers, knowing the MOQ helps in planning inventory and managing cash flow effectively. It is essential to negotiate favorable MOQs to align with production needs without overcommitting resources. -
RFQ (Request for Quotation)
An RFQ is a document that buyers send to suppliers to request pricing for specific products or services. A well-structured RFQ can lead to competitive bids, allowing buyers to compare offers and make informed decisions. Including detailed specifications in the RFQ is critical for receiving accurate quotes.
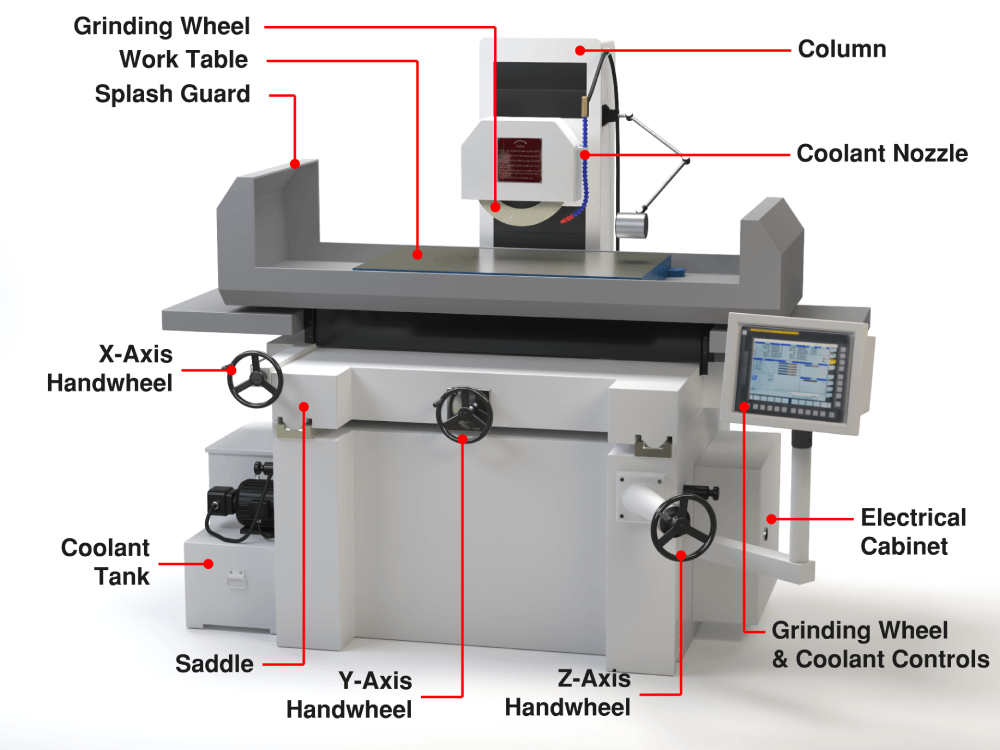
Illustrative Image (Source: Google Search)
-
Incoterms (International Commercial Terms)
Incoterms are a set of predefined international trade terms that clarify the responsibilities of buyers and sellers in shipping agreements. Familiarity with Incoterms helps B2B buyers understand their obligations regarding shipping, insurance, and risk transfer, facilitating smoother international transactions. -
Lead Time
Lead time refers to the time between placing an order and receiving the goods. Understanding lead times is essential for inventory management and production planning. Buyers should communicate with suppliers to establish realistic lead times, ensuring that their operations run smoothly without delays. -
Warranty
A warranty is a guarantee provided by the manufacturer regarding the condition and performance of the machine. Knowing the warranty terms is crucial for B2B buyers, as it protects their investment and ensures support in case of defects or malfunctions. Buyers should seek warranties that offer comprehensive coverage and clear service terms.
By familiarizing themselves with these technical properties and trade terms, international B2B buyers can make more informed decisions, streamline their procurement processes, and ultimately enhance their operational efficiency.
Navigating Market Dynamics, Sourcing Trends, and Sustainability in the cnc tool cutter grinding machine Sector
Market Overview & Key Trends
The CNC tool cutter grinding machine sector is experiencing a transformative phase, driven by several global factors. Increased automation and the adoption of Industry 4.0 technologies are reshaping production processes, enhancing efficiency, and reducing operational costs. For international B2B buyers, particularly in regions such as Africa, South America, the Middle East, and Europe, understanding these dynamics is crucial. Buyers should pay attention to the rise of smart manufacturing solutions, which integrate IoT (Internet of Things) capabilities into CNC machines, allowing for real-time monitoring and predictive maintenance.
Emerging trends also highlight the shift towards customization and flexibility in manufacturing. Companies are increasingly investing in machines that can handle various materials and geometries, catering to niche markets and specific client demands. As a result, B2B buyers should consider sourcing CNC machines that offer modular designs or adaptable features, enabling them to meet evolving market needs without significant capital expenditure.
Furthermore, the market is witnessing a growing demand for high-precision tools that enhance productivity in sectors like aerospace, automotive, and healthcare. Buyers should focus on suppliers that prioritize innovation and quality assurance, as these attributes can significantly impact their operational success. Lastly, geopolitical factors and trade agreements will continue to influence sourcing strategies, making it essential for buyers to stay informed about the regulatory landscape affecting international trade.
Sustainability & Ethical Sourcing in B2B
Sustainability is becoming a paramount consideration in the CNC tool cutter grinding machine sector, driven by environmental regulations and consumer demand for responsible sourcing. The production and disposal of manufacturing equipment can have significant environmental impacts, including energy consumption and waste generation. International B2B buyers must prioritize suppliers that demonstrate a commitment to sustainable practices, such as using energy-efficient machinery and minimizing waste throughout the production process.
Moreover, ethical supply chains are increasingly important, particularly for buyers in Africa and South America, where social responsibility can enhance brand reputation and customer loyalty. Buyers should seek out suppliers with transparent sourcing practices and certifications that verify compliance with environmental standards. Certifications such as ISO 14001 (Environmental Management) or ISO 50001 (Energy Management) can serve as indicators of a supplier’s commitment to sustainability.
Additionally, the use of “green” materials and processes, including recyclable components and eco-friendly lubricants, can significantly reduce the environmental footprint of CNC operations. Buyers should engage with manufacturers who prioritize these sustainable options, ensuring that their sourcing decisions align with broader corporate social responsibility goals.
Brief Evolution/History
The CNC tool cutter grinding machine has evolved significantly since its inception in the mid-20th century. Originally, these machines were primarily mechanical and required extensive manual intervention. However, the integration of computer numerical control technology revolutionized the industry, allowing for higher precision and automation in machining processes. Over the past few decades, advancements in materials, software, and automation have led to machines that are not only more efficient but also capable of performing complex tasks that were previously unattainable.
As industries increasingly emphasize precision and customization, the CNC tool cutter grinding machine continues to adapt, incorporating features such as multi-axis capabilities and enhanced user interfaces. This evolution reflects the sector’s responsiveness to market demands, making it vital for international B2B buyers to remain engaged with technological advancements to maintain a competitive edge in their respective markets.
Related Video: STUDER S11 CNC Grinding Machine Configurations and Options
Frequently Asked Questions (FAQs) for B2B Buyers of cnc tool cutter grinding machine
-
What factors should I consider when vetting suppliers of CNC tool cutter grinding machines?
When vetting suppliers, prioritize their industry experience, reputation, and client testimonials. Check for certifications such as ISO 9001, which indicate quality management standards. Investigate their production capabilities, including technology used and workforce expertise. Additionally, assess their after-sales support and service offerings, as ongoing support is crucial for machine maintenance and operation. -
Can I customize CNC tool cutter grinding machines to meet specific needs?
Yes, many suppliers offer customization options based on your operational requirements. When discussing customization, be clear about the specifications you need, such as size, speed, and tooling options. Ensure that the supplier has experience with similar custom projects and can provide examples or case studies. This can help avoid miscommunication and ensure that the final product meets your exact specifications. -
What is the typical minimum order quantity (MOQ) and lead time for CNC tool cutter grinding machines?
The MOQ can vary significantly based on the supplier and the complexity of the machine. Generally, for standard models, the MOQ may range from one to five units. Lead times also depend on customization; expect anywhere from 4 to 12 weeks for production and delivery. Always clarify these details upfront and consider potential delays due to shipping or customs, especially when importing to regions like Africa or South America. -
What payment terms are commonly accepted for international purchases of CNC machines?
Common payment methods include bank transfers, letters of credit, and escrow services. Many suppliers require a deposit (usually 30-50%) upfront, with the balance due upon completion or delivery. It’s crucial to negotiate terms that protect both parties, especially when dealing with new suppliers. Additionally, consider the implications of currency exchange rates and international transaction fees. -
How can I ensure the quality of the CNC tool cutter grinding machines I purchase?
Request detailed product specifications, including material quality and performance metrics. Suppliers should provide quality assurance documentation, including inspection reports and certification details. If possible, arrange for a factory visit or request a video demonstration of the machine in operation. Post-purchase, establish a clear protocol for regular maintenance and inspections to sustain performance over time. -
What certifications should I look for when sourcing CNC tool cutter grinding machines?
Key certifications include ISO 9001 for quality management and CE marking, which indicates compliance with EU safety and environmental standards. Additionally, look for industry-specific certifications relevant to your region or sector. These certifications help ensure that the machines meet international safety and performance standards, reducing the risk of operational issues after purchase. -
What logistical considerations should I keep in mind when importing CNC machines?
Understand the shipping methods and costs associated with transporting heavy machinery. Consider using a freight forwarder who specializes in industrial equipment to navigate customs and ensure compliance with local regulations. Additionally, factor in insurance for the shipment to mitigate risks during transit. Be prepared for potential delays at ports, especially in regions with high shipping traffic or less efficient customs processes. -
How should I handle disputes with suppliers regarding CNC machine orders?
First, clearly outline all terms and conditions in your purchase agreement, including delivery timelines, quality expectations, and warranties. If a dispute arises, maintain open communication with the supplier to seek a resolution. Involve a neutral third party if necessary. Always keep records of all communications and agreements, as these can be crucial in resolving disputes effectively and may help avoid future issues.
Important Disclaimer & Terms of Use
⚠️ Important Disclaimer
The information provided in this guide, including content regarding manufacturers, technical specifications, and market analysis, is for informational and educational purposes only. It does not constitute professional procurement advice, financial advice, or legal advice.
While we have made every effort to ensure the accuracy and timeliness of the information, we are not responsible for any errors, omissions, or outdated information. Market conditions, company details, and technical standards are subject to change.
B2B buyers must conduct their own independent and thorough due diligence before making any purchasing decisions. This includes contacting suppliers directly, verifying certifications, requesting samples, and seeking professional consultation. The risk of relying on any information in this guide is borne solely by the reader.
Strategic Sourcing Conclusion and Outlook for cnc tool cutter grinding machine
In the evolving landscape of CNC tool cutter grinding machines, strategic sourcing has emerged as a pivotal approach for international B2B buyers. By leveraging strategic partnerships with manufacturers and suppliers, companies can enhance their operational efficiency, reduce costs, and ensure access to cutting-edge technology. Buyers from Africa, South America, the Middle East, and Europe should prioritize sourcing from regions that offer not only competitive pricing but also robust support services and innovation.
Key Takeaways for B2B Buyers:
– Diversification of Suppliers: Establishing a diverse supplier network mitigates risks associated with supply chain disruptions.
– Investment in Technology: Opt for suppliers who invest in the latest grinding technologies to improve precision and productivity.
– Quality Assurance: Implement stringent quality control measures to ensure that sourced machines meet industry standards and performance expectations.
As the market continues to grow, international buyers are encouraged to actively engage with manufacturers that align with their strategic goals. By fostering collaborative relationships and remaining adaptable to market changes, businesses can position themselves for sustained growth and competitive advantage. The future of CNC tool cutter grinding machines is bright, and now is the time to act—evaluate your sourcing strategies today to secure a stronger foothold in this dynamic sector.