The Ultimate Guide to Protective Plastic Coating (2025)
Introduction: Navigating the Global Market for protective plastic coating
In an increasingly interconnected world, sourcing effective protective plastic coatings has become essential for businesses aiming to safeguard their products against environmental challenges. Whether you’re in the automotive, electronics, or consumer goods sector, the right coating can significantly enhance product durability and performance. This guide provides a comprehensive exploration of protective plastic coatings, covering various types, applications, and critical considerations for international B2B buyers.
From understanding the advantages of UV-resistant coatings to exploring eco-friendly options, we delve into the diverse landscape of protective coatings available in today’s global market. Additionally, we offer insights into the supplier vetting process, enabling you to choose reliable partners that align with your business needs, whether you’re based in Africa, South America, the Middle East, or Europe.
Navigating the complexities of cost structures and market trends, this guide equips you with the knowledge necessary for informed purchasing decisions. By addressing key challenges such as quality assurance and compliance with regional regulations, we aim to empower your business to thrive in competitive environments. With actionable insights and expert analysis, this resource serves as your roadmap to successfully sourcing protective plastic coatings that meet your unique operational requirements.
Understanding protective plastic coating Types and Variations
Type Name | Key Distinguishing Features | Primary B2B Applications | Brief Pros & Cons for Buyers |
---|---|---|---|
Hard Coatings | High hardness (greater than 9H), transparent, UV resistant | Electronics, automotive, optics | Pros: Excellent abrasion resistance; Cons: Higher cost compared to softer coatings. |
Strippable Coatings | Rubber-like, transparent, easy to remove, odor-free | Tool protection, glass breakage containment | Pros: Cost-effective; easy application/removal; Cons: May require frequent reapplication. |
Nano Coatings | Extremely thin, hydrophobic, high durability | Automotive, aerospace, consumer products | Pros: Superior protection; enhances aesthetics; Cons: Requires specialized application techniques. |
Thermal Plastic Coatings | Flexible, shock-absorbent, good corrosion resistance | Wood protection, tool coatings | Pros: Excellent for shipping protection; Cons: Limited to specific applications. |
Laminating Coatings | Provides a thin, protective layer, often used for documents and ID cards | Packaging, signage, document protection | Pros: Cost-effective; enhances appearance; Cons: Limited protection against heavy abrasion. |
What Are the Characteristics of Hard Coatings?
Hard coatings are designed to provide exceptional durability and protection for plastic components. With a hardness rating exceeding 9H, these coatings are ideal for applications in electronics, automotive parts, and optics where resistance to scratches and abrasion is critical. B2B buyers should consider the specific environmental conditions their products will face, as hard coatings also offer excellent UV resistance, preventing yellowing and degradation over time. However, the initial investment may be higher compared to softer coatings.
How Do Strippable Coatings Benefit B2B Buyers?
Strippable coatings are a versatile option for protecting tools and other equipment during shipping and storage. Their rubber-like texture allows them to absorb shocks and prevent scratches, while being easy to remove without leaving residue. This feature is particularly advantageous for companies that frequently ship delicate items, such as glass or precision tools. While they are cost-effective and provide decent protection, buyers should be mindful of the need for reapplication over time, especially in high-use environments.
What Makes Nano Coatings Unique for B2B Applications?
Nano coatings represent a cutting-edge solution for B2B buyers looking for high-performance protection. These coatings are exceptionally thin and can create a hydrophobic barrier, making surfaces easier to clean and maintain. They are often used in automotive and aerospace sectors to enhance the durability and aesthetic appeal of products. However, the application process may require specialized equipment and expertise, which can increase overall costs. Buyers should evaluate the long-term benefits against the initial investment.
Why Choose Thermal Plastic Coatings?
Thermal plastic coatings are particularly suited for applications requiring flexibility and shock resistance. These coatings are commonly used for protecting wooden items and tools, offering excellent abrasion resistance during storage and transport. Their application process can be straightforward, but buyers should consider the specific temperature ranges and conditions under which these coatings will perform best. While they are effective for many uses, their protective qualities may not be suitable for more demanding industrial applications.
How Do Laminating Coatings Enhance Product Value?
Laminating coatings provide a thin protective layer that is widely used for documents, packaging, and signage. They not only enhance the visual appeal of products but also offer a degree of protection against wear and moisture. For businesses focused on branding and presentation, laminating coatings can be a cost-effective solution. However, they may not provide the same level of protection against heavy-duty abrasion as other coating types, so buyers should assess their specific needs carefully.
Key Industrial Applications of protective plastic coating
Industry/Sector | Specific Application of Protective Plastic Coating | Value/Benefit for the Business | Key Sourcing Considerations for this Application |
---|---|---|---|
Automotive | Coating for car interiors and exteriors | Enhances durability and aesthetic appeal | UV resistance, temperature stability, and color retention |
Electronics | Insulation for electronic components | Protects against moisture and electrical shorts | Compliance with safety standards and thermal conductivity |
Manufacturing & Fabrication | Protective coating for tools and machinery | Reduces wear and prolongs lifespan of equipment | Application method (spray, dip, etc.) and thickness |
Aerospace | Coating for aircraft components | Increases resistance to corrosion and wear | Weight considerations and certification requirements |
Construction | Coating for building materials and fixtures | Improves lifespan and reduces maintenance costs | Environmental impact and adhesion properties |
How is Protective Plastic Coating Utilized in the Automotive Industry?
In the automotive sector, protective plastic coatings are extensively used on both interior and exterior components, including dashboards, door panels, and body parts. These coatings provide a barrier against scratches, UV damage, and chemicals, enhancing the overall durability and aesthetic appeal of vehicles. For international buyers, particularly in regions like Africa and South America, sourcing coatings that can withstand extreme temperatures and humidity is crucial. Additionally, compliance with automotive industry standards ensures that the coatings meet safety and performance expectations.
What Role Does Protective Plastic Coating Play in Electronics?
Protective plastic coatings are vital for insulating electronic components, safeguarding them from moisture and dust, which can lead to electrical shorts and failures. This is particularly important in regions with high humidity, such as parts of the Middle East and Southeast Asia. Buyers should consider sourcing coatings that meet international safety standards and provide excellent thermal conductivity to ensure optimal performance of electronic devices. Additionally, coatings that are resistant to solvents and chemicals are essential for protecting sensitive components during manufacturing and usage.
How is Protective Plastic Coating Beneficial in Manufacturing & Fabrication?
In manufacturing, protective plastic coatings are applied to tools and machinery to reduce wear and extend their lifespan. These coatings can absorb shocks and prevent damage from abrasives, which is particularly beneficial in industries that rely on heavy machinery. For international buyers in Europe and South America, it is essential to consider the application method (spray, dip, etc.) and the required thickness of the coating, as these factors can significantly impact performance and cost-effectiveness. Moreover, coatings that provide easy removal options can enhance operational efficiency.
Why is Protective Plastic Coating Important in Aerospace?
In the aerospace industry, protective plastic coatings are applied to various components to enhance their resistance to corrosion and wear, which is crucial for maintaining safety and performance standards. These coatings help to minimize maintenance costs and extend the lifespan of aircraft parts. Buyers from regions with stringent aviation regulations, such as Europe, should ensure that the coatings they source meet specific weight and certification requirements. Additionally, coatings that can withstand extreme temperatures and pressures are essential for aerospace applications.
How Does Protective Plastic Coating Enhance Construction Materials?
Protective plastic coatings are increasingly used in the construction industry to protect building materials and fixtures from environmental damage. These coatings improve the lifespan of surfaces exposed to harsh weather conditions, reducing maintenance costs over time. For international buyers in regions like Africa and the Middle East, sourcing coatings with strong adhesion properties and environmental compliance is critical. Furthermore, buyers should evaluate the long-term performance of coatings, especially in terms of durability against UV exposure and moisture, to ensure the integrity of construction projects.
3 Common User Pain Points for ‘protective plastic coating’ & Their Solutions
Scenario 1: Insufficient Protection Against Environmental Factors
The Problem: B2B buyers often face challenges when protective plastic coatings fail to provide adequate resistance to environmental factors such as UV exposure, chemicals, or extreme temperatures. For instance, a manufacturer in the Middle East may find that the coatings on their products begin to degrade under intense sunlight, leading to product failures and increased warranty claims. This not only affects their bottom line but also tarnishes their reputation with clients.
The Solution: To combat this issue, it is crucial to select a protective plastic coating that offers high UV resistance and thermal stability. When sourcing coatings, buyers should look for products like Brewer Science’s ProTEK® PSR-R, which boasts greater than 9H pencil hardness and high solvent resistance. Additionally, conducting thorough testing on sample batches under simulated environmental conditions can help ensure that the chosen coating meets durability requirements. Establishing a partnership with reputable suppliers who provide data sheets and performance testing can also aid in making informed decisions about long-lasting coatings.
Scenario 2: Difficulty in Application and Removal of Coatings
The Problem: Another common challenge for B2B buyers arises during the application and removal of protective coatings. Many products require meticulous application techniques to avoid issues like uneven coverage or bubbles, which can compromise the protective layer. Moreover, when it comes time to remove these coatings, especially in industries such as optics or electronics, improper removal can lead to damage of sensitive components, resulting in costly repairs or replacements.
The Solution: To alleviate these concerns, buyers should prioritize selecting coatings that are designed for ease of application and removal. For instance, Type 4 Protective Plastic Strippable Coating offers a user-friendly application process and is designed to be easily removed without damaging the underlying surface. Suppliers should provide clear guidelines and training materials for proper application techniques, including environmental considerations (temperature and humidity) that could affect the process. Additionally, investing in training for staff on the best practices for both application and removal can help minimize errors and enhance efficiency.
Scenario 3: Rising Costs Due to Frequent Reapplication
The Problem: Frequent reapplication of protective coatings can significantly increase operational costs for businesses, particularly for those in sectors like manufacturing or construction. For example, a company in South America might find that their protective coatings wear out quickly due to heavy abrasion, leading to repeated expenses that hinder profitability and operational efficiency.
The Solution: To address rising reapplication costs, B2B buyers should focus on investing in high-performance coatings that offer superior durability and longevity. Exploring advanced options such as nano-coatings, which provide exceptional abrasion resistance and chemical durability, can yield significant savings over time. Furthermore, buyers should conduct a cost-benefit analysis comparing the lifecycle costs of different coatings, taking into account not only the upfront costs but also the projected lifespan and maintenance needs. Engaging with suppliers who offer warranties or performance guarantees can also provide peace of mind and reduce long-term expenses associated with frequent coating applications.
Strategic Material Selection Guide for protective plastic coating
What are the Key Properties of Common Materials Used in Protective Plastic Coatings?
When selecting protective plastic coatings, understanding the properties of different materials is crucial for ensuring optimal performance in various applications. Here, we analyze four common materials used in protective plastic coatings: Polyurethane, Epoxy, Polyvinyl Chloride (PVC), and Thermoplastic Rubber. Each material presents unique characteristics that influence its suitability for specific applications.
How Does Polyurethane Perform as a Protective Plastic Coating?
Polyurethane is known for its excellent durability and flexibility. It can withstand a wide range of temperatures and pressures, making it suitable for applications in both industrial and consumer products. Polyurethane coatings exhibit high abrasion resistance and can be formulated to be UV-stable, which is particularly beneficial in regions with intense sunlight, such as parts of Africa and South America.
Pros:
– Exceptional abrasion and impact resistance.
– Versatile formulations available for different environmental conditions.
– Good adhesion to various substrates.
Cons:
– Higher cost compared to other materials.
– Can be sensitive to moisture during application, which may complicate manufacturing.
Impact on Application: Polyurethane is compatible with various media, including oils and solvents, making it ideal for automotive and industrial applications.
Considerations for International Buyers: Compliance with standards such as ASTM D4060 for abrasion resistance is essential. Buyers should also consider local regulations regarding VOC emissions, particularly in Europe.
What Advantages Does Epoxy Offer for Protective Coatings?
Epoxy coatings are renowned for their strong adhesion and chemical resistance, making them a popular choice for protective coatings in harsh environments. They can withstand high temperatures and are often used in industrial applications where chemical exposure is a concern.
Pros:
– Superior chemical and corrosion resistance.
– Excellent adhesion properties.
– Long-lasting durability.
Cons:
– Longer curing times can affect production schedules.
– Less flexible than polyurethane, which may lead to cracking under stress.
Impact on Application: Epoxy is suitable for applications exposed to harsh chemicals, such as in the oil and gas industry, making it a preferred choice in regions with significant industrial activity.
Considerations for International Buyers: Ensure compliance with relevant standards like ASTM D3359 for adhesion and ASTM D638 for tensile strength. Awareness of local regulations regarding hazardous materials is also critical.
How Does Polyvinyl Chloride (PVC) Compare in Protective Coating Applications?
PVC coatings are widely used due to their cost-effectiveness and versatility. They provide good resistance to moisture and are often used in applications requiring water resistance.
Pros:
– Economical and widely available.
– Good moisture resistance.
– Easy to apply and can be formulated for various applications.
Cons:
– Limited temperature resistance compared to polyurethane and epoxy.
– Can be less durable in high-abrasion environments.
Impact on Application: PVC is commonly used in consumer products, including coatings for electrical components and plumbing fixtures, especially in humid environments.
Considerations for International Buyers: Buyers should verify compliance with standards such as ASTM D2247 for moisture resistance. Understanding local market preferences and regulations regarding plastic materials is also essential.
What Role Does Thermoplastic Rubber Play in Protective Coatings?
Thermoplastic rubber (TPR) coatings are known for their flexibility and shock absorption properties. They are particularly effective in applications requiring impact resistance and are often used for tools and equipment.
Pros:
– Excellent flexibility and shock absorption.
– Good weather resistance.
– Can be easily removed and reapplied.
Cons:
– Generally lower chemical resistance compared to epoxy and polyurethane.
– May not be suitable for high-temperature applications.
Impact on Application: TPR is ideal for protective coatings on tools and equipment that may experience drops or impacts, making it a good choice for construction and manufacturing industries.
Considerations for International Buyers: Buyers should assess compliance with relevant standards like ASTM D412 for tensile properties. Understanding the local demand for flexible coatings can influence purchasing decisions.
Summary Table of Protective Plastic Coating Materials
Material | Typical Use Case for Protective Plastic Coating | Key Advantage | Key Disadvantage/Limitation | Relative Cost (Low/Med/High) |
---|---|---|---|---|
Polyurethane | Automotive and industrial applications | Exceptional abrasion resistance | Higher cost compared to alternatives | High |
Epoxy | Industrial coatings in harsh environments | Superior chemical resistance | Longer curing times | Medium |
Polyvinyl Chloride (PVC) | Consumer products and plumbing fixtures | Economical and moisture resistant | Limited temperature resistance | Low |
Thermoplastic Rubber | Tools and equipment requiring impact resistance | Excellent flexibility and shock absorption | Lower chemical resistance | Medium |
This guide provides a comprehensive overview of the materials available for protective plastic coatings, helping international B2B buyers make informed decisions tailored to their specific needs and regional considerations.
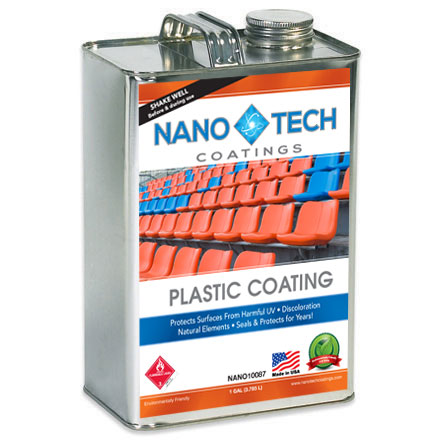
A stock image related to protective plastic coating.
In-depth Look: Manufacturing Processes and Quality Assurance for protective plastic coating
What Are the Main Stages of Manufacturing Protective Plastic Coatings?
The manufacturing process of protective plastic coatings is multi-faceted and involves several critical stages. Understanding these stages is essential for B2B buyers looking to ensure product quality and supplier reliability.
-
Material Preparation
– The first step involves sourcing high-quality raw materials, including polymers and additives. These materials must meet specific industry standards and performance requirements. Suppliers should provide Material Safety Data Sheets (MSDS) to confirm compliance with regulations.
– Proper storage and handling of materials are crucial to prevent contamination, which can affect the final product’s performance. Buyers should inquire about the supplier’s material sourcing and storage practices. -
Forming Techniques
– Various techniques are used to apply protective coatings, including dip coating, spray coating, and electrostatic coating. Each method has its own advantages depending on the application and desired properties of the final product.
– Dip Coating: This involves immersing the substrate into a liquid coating material. It’s particularly effective for achieving uniform coverage on complex shapes.
– Spray Coating: This method is ideal for applying thin layers of coating and is often used for large surfaces.
– Electrostatic Coating: Utilizes charged particles to achieve a high-quality finish, minimizing waste and ensuring even coverage. -
Assembly and Curing
– After application, the coatings undergo a curing process, which can involve heat, UV light, or chemical reactions. This step is vital for achieving the desired hardness and chemical resistance.
– Different types of coatings, such as UV-cure or thermosetting, require specific curing conditions, impacting the final product’s performance. Buyers should assess the curing technology used by suppliers to ensure it aligns with their needs. -
Finishing Touches
– Finishing processes may include sanding, polishing, or applying additional layers of coating. This stage enhances aesthetic qualities and overall durability.
– Quality control measures should be in place to ensure that the finished product meets specifications before it is shipped.
How Is Quality Assurance Implemented in Protective Plastic Coating Manufacturing?
Quality assurance (QA) is a critical aspect of the manufacturing process that ensures products meet both regulatory and customer standards. For international B2B buyers, understanding QA processes can provide confidence in supplier capabilities.
-
International Standards and Compliance
– Compliance with international standards such as ISO 9001 is crucial for establishing a quality management system. This standard focuses on continuous improvement, customer satisfaction, and operational efficiency.
– Industry-specific standards may also apply, such as CE marking for products sold in Europe or API standards for oil and gas applications. Buyers should verify that their suppliers adhere to relevant certifications. -
Quality Control Checkpoints
– Incoming Quality Control (IQC): This stage involves inspecting raw materials before they enter the production line. Ensuring that materials meet specified criteria helps prevent defects.
– In-Process Quality Control (IPQC): Continuous monitoring during the manufacturing process helps identify issues early. This may include regular inspections and tests at various stages of production.
– Final Quality Control (FQC): A thorough examination of the finished product is essential. This may involve visual inspections, adhesion tests, and performance assessments to ensure that the product meets all specifications before shipment. -
Common Testing Methods for Protective Coatings
– Testing methods include pencil hardness tests, solvent resistance tests, and adhesion tests. These assessments help verify the durability and performance of coatings under various conditions.
– Buyers should ask suppliers for test reports and certifications to ensure transparency and reliability.
How Can B2B Buyers Verify Supplier Quality Control Practices?
For international buyers, particularly from regions like Africa, South America, the Middle East, and Europe, ensuring supplier quality control is paramount. Here are several actionable steps:
-
Conduct Supplier Audits
– Regular audits of suppliers can provide insights into their manufacturing processes and quality control measures. Buyers should establish audit schedules and criteria to assess compliance with international standards.
– Audits can also reveal potential areas for improvement and help build stronger relationships with suppliers. -
Request Documentation and Reports
– Suppliers should provide documentation, including quality management system certifications, inspection reports, and test results. These documents serve as proof of compliance with quality standards.
– Buyers can also request historical data on product performance to assess reliability over time. -
Third-Party Inspections
– Engaging third-party inspection agencies can add an additional layer of confidence. These organizations can conduct independent assessments of manufacturing practices and product quality.
– This approach is particularly beneficial for buyers in regions where regulatory compliance may vary.
What Are the Quality Control Nuances for International B2B Buyers?
Understanding the nuances of quality control for international B2B transactions is essential for mitigating risks and ensuring product quality.
-
Cultural and Regulatory Differences
– Buyers must be aware of cultural differences that may affect communication and expectations regarding quality. Establishing clear guidelines and expectations upfront can help bridge these gaps.
– Regulatory compliance may vary significantly between regions. Buyers should familiarize themselves with local regulations that affect product acceptance in their respective markets. -
Customization and Adaptability
– Customization of coatings for specific applications may require additional quality control measures. Buyers should collaborate with suppliers to develop tailored solutions that meet unique performance requirements.
– Flexibility in adapting to changes in specifications or production processes is vital for maintaining quality standards. -
Building Long-term Relationships
– Establishing long-term partnerships with reliable suppliers can enhance quality control outcomes. Ongoing collaboration fosters trust and allows for continuous improvement in processes and products.
– Buyers should prioritize suppliers with a proven track record of quality and reliability, especially when sourcing from regions with varying standards.
By understanding these manufacturing processes and quality assurance practices, B2B buyers can make informed decisions when sourcing protective plastic coatings, ensuring that they receive high-quality products that meet their specific needs.
Practical Sourcing Guide: A Step-by-Step Checklist for ‘protective plastic coating’
In the world of industrial applications, selecting the right protective plastic coating is crucial for ensuring durability and performance. This guide provides a step-by-step checklist to assist B2B buyers in making informed procurement decisions, particularly for those operating in diverse regions such as Africa, South America, the Middle East, and Europe.
Step 1: Define Your Technical Specifications
Understanding your specific needs is the foundation of successful sourcing. Identify the physical and chemical properties required for your application, such as hardness, flexibility, UV resistance, and compatibility with the substrates you intend to coat. This clarity will help narrow down suppliers that can meet your precise requirements.
Step 2: Research Supplier Options
Conduct thorough research to compile a list of potential suppliers. Utilize online marketplaces, industry directories, and trade associations to identify reputable manufacturers. Pay attention to their experience in your specific industry and their track record with similar products.
Step 3: Evaluate Supplier Certifications
Before engaging with suppliers, ensure they possess relevant certifications. Look for ISO certifications, compliance with environmental regulations, and industry-specific quality standards. These certifications not only reflect the supplier’s commitment to quality but also reduce risks associated with product performance and regulatory compliance.
Step 4: Request Samples for Testing
Once you have shortlisted potential suppliers, request samples of their protective plastic coatings. Testing these samples in your specific application environment will provide insights into their performance characteristics. Evaluate factors such as adhesion, durability, and ease of application to ensure they meet your operational standards.
Step 5: Assess Production Capabilities
Understanding a supplier’s production capabilities is essential for ensuring they can meet your volume and lead-time requirements. Inquire about their manufacturing processes, technology, and flexibility to adapt to changing order sizes. Suppliers with advanced production methods can often provide better consistency and faster turnaround times.
Step 6: Negotiate Terms and Pricing
Once you are satisfied with a supplier’s product quality and production capabilities, initiate discussions on pricing and contract terms. Consider not only the cost of the coating but also shipping, lead times, and payment terms. Ensure that you are clear about any warranties or guarantees they offer, as these can significantly impact your overall cost of ownership.
Step 7: Establish a Communication Plan
Finally, develop a communication plan with your selected supplier. Clear communication channels are essential for addressing any issues that may arise during the procurement process. Establish regular check-ins and updates to ensure that both parties are aligned on expectations, timelines, and any changes in requirements.
By following this checklist, B2B buyers can effectively navigate the complexities of sourcing protective plastic coatings, ensuring that they select the right materials for their applications while minimizing risks and maximizing value.
Comprehensive Cost and Pricing Analysis for protective plastic coating Sourcing
What Are the Key Cost Components in Protective Plastic Coating?
When sourcing protective plastic coatings, understanding the cost structure is crucial for B2B buyers. The primary cost components include:
-
Materials: The type of resin or polymer used significantly influences the price. High-quality materials that offer superior protection against abrasion, chemicals, and UV exposure tend to cost more. Buyers should evaluate the performance characteristics of materials, such as hardness and transparency, to justify the cost.
-
Labor: Skilled labor is necessary for the application of coatings, particularly when precision is required. Labor costs can vary based on the region, with higher wages in developed markets impacting overall pricing.
-
Manufacturing Overhead: This includes costs related to facility maintenance, utilities, and equipment depreciation. Efficient manufacturing processes can help reduce overhead costs, which is beneficial for buyers.
-
Tooling: Custom tooling for specific coating applications can represent a significant investment. Buyers should consider whether their order volume justifies the tooling costs, especially for unique specifications.
-
Quality Control (QC): Rigorous QC processes ensure that coatings meet required standards and specifications. This may involve additional testing and certification, which can raise costs but is essential for maintaining product integrity.
-
Logistics: Transportation costs can vary greatly depending on the supplier’s location and the shipping method used. International buyers must factor in customs duties and potential delays in logistics planning.
-
Margin: Suppliers typically add a profit margin that can vary based on competition, market demand, and the uniqueness of the product. Understanding this can help buyers gauge fair pricing.
How Do Price Influencers Affect Protective Plastic Coating Costs?
Several factors can influence the pricing of protective plastic coatings:
-
Volume and Minimum Order Quantity (MOQ): Bulk orders often lead to lower per-unit costs. Buyers should negotiate MOQ terms to maximize cost efficiency.
-
Specifications and Customization: Customized coatings designed for specific applications usually come with a premium. Buyers should evaluate whether the additional features justify the price increase.
-
Material Quality and Certifications: Coatings that meet international standards or certifications (e.g., ISO) often command higher prices. Buyers must assess the value of such certifications against their requirements.
-
Supplier Factors: The reputation and reliability of suppliers can impact pricing. Established suppliers may charge more but offer greater assurance of quality and service.
-
Incoterms: Understanding Incoterms is essential for international transactions. Terms like FOB (Free on Board) and CIF (Cost, Insurance, and Freight) can affect the overall cost structure and risk distribution.
What Are the Best Buyer Tips for Cost-Efficiency in Protective Plastic Coating Sourcing?
For international B2B buyers, particularly from Africa, South America, the Middle East, and Europe, the following strategies can enhance cost-efficiency:
-
Negotiate Effectively: Leverage bulk purchasing power and build long-term relationships with suppliers to negotiate better terms. Consider discussing flexible payment terms or discounts for early payment.
-
Evaluate Total Cost of Ownership (TCO): Beyond the initial purchase price, consider the TCO, which includes maintenance, durability, and potential replacement costs. Investing in higher-quality coatings may reduce long-term expenses.
-
Stay Informed on Pricing Nuances: Be aware of regional market trends and economic factors that may influence pricing. Fluctuations in material costs due to supply chain disruptions can affect your sourcing strategy.
-
Consider Local Suppliers: Sourcing from local suppliers can reduce logistics costs and lead times. Assess the quality of local offerings against international suppliers to make informed decisions.
Disclaimer on Pricing
Prices for protective plastic coatings can vary significantly based on the factors mentioned above. It is advisable to obtain quotes from multiple suppliers and conduct thorough market research before making procurement decisions.
Alternatives Analysis: Comparing protective plastic coating With Other Solutions
Understanding the Importance of Alternatives in Protective Coatings
When considering protective solutions for various applications, international B2B buyers must evaluate multiple options to determine which best meets their specific needs. Protective plastic coatings serve as one solution, but other methods exist that may offer unique advantages depending on the context of use, material compatibility, and cost considerations. This section delves into a comparative analysis of protective plastic coating alongside two viable alternatives: lamination and hard coatings.
Comparison Table of Protective Solutions
Comparison Aspect | Protective Plastic Coating | Lamination | Hard Coatings |
---|---|---|---|
Performance | Excellent abrasion resistance and flexibility | Good protection against moisture and scratches | Superior hardness and durability |
Cost | Moderate, varies by application | Generally lower initial cost | Higher initial investment |
Ease of Implementation | Requires specialized application techniques | Simple application process | Requires advanced equipment and expertise |
Maintenance | Minimal, durable over time | May require periodic replacement | Low maintenance, long-lasting |
Best Use Case | Ideal for tools, automotive parts | Suitable for packaging and electronics | Best for optical components and industrial machinery |
Analyzing Lamination as an Alternative to Protective Plastic Coating
Lamination involves applying a thin layer of protective material over a substrate, typically using heat and pressure. This method provides an effective barrier against moisture, dust, and scratches. The primary advantage of lamination is its cost-effectiveness, making it an attractive option for many B2B buyers, especially in industries like packaging and electronics. However, lamination may not offer the same level of flexibility or durability as protective plastic coatings, particularly in high-abrasion environments.
Exploring Hard Coatings as Another Alternative
Hard coatings are typically applied using advanced techniques such as vacuum deposition or sputtering. They provide exceptional durability and scratch resistance, often exceeding that of traditional protective plastic coatings. Hard coatings are particularly beneficial for applications requiring high-performance optics or industrial machinery. However, the initial investment and complexity of the application process can be a barrier for some buyers, especially those in regions where specialized equipment is less accessible.
Conclusion: How to Choose the Right Protective Solution
Selecting the appropriate protective coating solution requires a thorough analysis of the specific application, budget constraints, and performance requirements. B2B buyers should consider not only the cost but also the long-term benefits each option can provide. For instance, while protective plastic coatings offer excellent flexibility and abrasion resistance, alternatives like lamination may be more suitable for cost-sensitive projects, whereas hard coatings may be necessary for high-performance applications. By carefully evaluating these factors, buyers can make informed decisions that align with their operational goals and budgetary constraints.
Essential Technical Properties and Trade Terminology for protective plastic coating
What Are the Key Technical Properties of Protective Plastic Coatings?
When considering protective plastic coatings, international B2B buyers should focus on essential technical properties that impact performance and suitability for various applications. Here are some critical specifications:
-
Material Grade
The material grade refers to the specific formulation of the coating, which can influence its durability and application method. Different grades are designed for varying performance levels, such as UV resistance, chemical resistance, and hardness. Understanding the material grade is crucial for ensuring the coating meets the requirements of the intended application, especially in industries like automotive and electronics. -
Pencil Hardness
Pencil hardness is a measure of the coating’s resistance to scratches and abrasions. This is typically measured on a scale from 1H (softest) to 9H (hardest), with higher numbers indicating greater durability. For B2B buyers, selecting a coating with the appropriate pencil hardness is vital to ensure the longevity of the coated products, particularly in high-wear environments. -
Solvent Resistance
Solvent resistance indicates how well a coating can withstand exposure to various solvents and chemicals without degrading. This property is essential for applications in industries such as food processing, pharmaceuticals, and automotive manufacturing, where contact with chemicals is common. Buyers should assess solvent resistance to avoid premature failure of the coating, which could lead to increased costs and downtime. -
UV Stability
UV stability refers to the coating’s ability to resist degradation when exposed to ultraviolet light. Coatings with high UV stability maintain their appearance and protective qualities over time, making them ideal for outdoor applications. Buyers should prioritize UV stability to ensure that their products remain functional and visually appealing, particularly in markets with high sun exposure. -
Gloss Level
The gloss level of a coating affects its aesthetic appeal and can also influence its protective capabilities. High-gloss coatings typically offer better protection against moisture and contaminants. Buyers should consider the desired finish of the final product and select a coating that aligns with both aesthetic and functional requirements.
What Are Common Trade Terms in Protective Plastic Coating?
Understanding industry jargon is crucial for effective communication and negotiation in the B2B marketplace. Here are some common terms associated with protective plastic coatings:
-
OEM (Original Equipment Manufacturer)
OEM refers to companies that produce parts or equipment that may be marketed by another manufacturer. In the context of protective coatings, OEMs often require specific coatings for their products. Understanding OEM requirements helps buyers ensure compatibility and compliance with industry standards. -
MOQ (Minimum Order Quantity)
MOQ denotes the smallest quantity of a product that a supplier is willing to sell. For buyers in international markets, knowing the MOQ is essential for budgeting and planning inventory. It can significantly affect purchasing decisions, particularly for smaller businesses or startups. -
RFQ (Request for Quotation)
An RFQ is a formal request to suppliers to provide pricing for specific products or services. Buyers should prepare detailed RFQs that outline their technical specifications and requirements to receive accurate and competitive quotes from potential suppliers. -
Incoterms (International Commercial Terms)
Incoterms are a set of international rules that define the responsibilities of buyers and sellers in international transactions. These terms clarify who is responsible for shipping, insurance, and tariffs, which can significantly impact the total cost of acquisition for protective coatings. Familiarity with Incoterms helps buyers negotiate better terms and avoid unexpected costs. -
Strippable Coating
A strippable coating is designed to be easily removed after its protective function has been fulfilled. This property is particularly valuable in applications where temporary protection is needed during shipping or storage. Buyers should assess whether a strippable coating is suitable for their specific use case to enhance efficiency and reduce waste.
By understanding these technical properties and trade terms, B2B buyers can make informed decisions when selecting protective plastic coatings, ensuring they meet both operational needs and budget constraints.
Navigating Market Dynamics and Sourcing Trends in the protective plastic coating Sector
What Are the Current Market Dynamics and Key Trends in the Protective Plastic Coating Sector?
The protective plastic coating market is experiencing significant growth, driven by advancements in technology and increasing demand across various industries. Key global drivers include the rising need for durable and corrosion-resistant materials in automotive, electronics, and consumer goods. International B2B buyers, particularly from regions like Africa, South America, the Middle East, and Europe, are increasingly seeking coatings that offer superior protection against abrasion, chemicals, and UV exposure.
Emerging trends in sourcing include the adoption of innovative application methods such as UV curing and dip coating, which enhance efficiency and reduce environmental impact. Additionally, the trend toward customization is gaining traction, as businesses aim to meet specific performance requirements for diverse applications. For instance, products like the ProTEK® PSR-R UV-cure coatings offer primerless application and high solvent resistance, making them attractive to buyers looking for high-performance solutions.
Another notable trend is the integration of digital technologies in the sourcing process. Buyers are leveraging e-commerce platforms and digital marketplaces to streamline procurement, allowing for easier access to suppliers worldwide. This shift is particularly beneficial for B2B buyers in developing regions who may face logistical challenges.
How Is Sustainability and Ethical Sourcing Influencing the Protective Plastic Coating Industry?
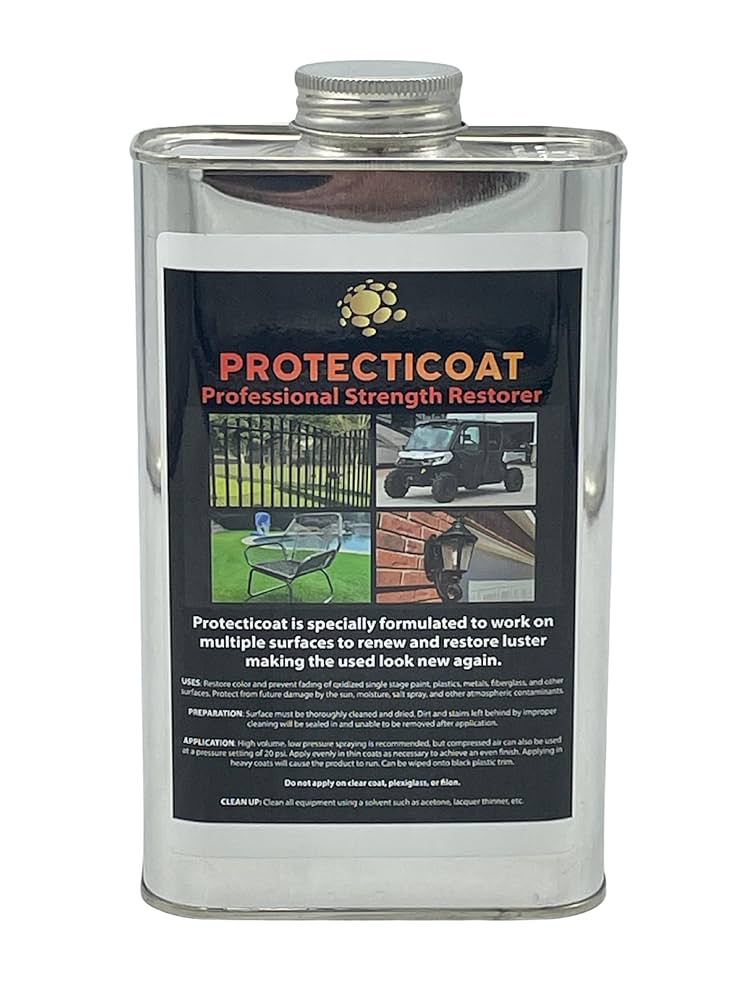
A stock image related to protective plastic coating.
Sustainability has become a critical consideration for international B2B buyers in the protective plastic coating sector. As environmental concerns escalate, companies are increasingly prioritizing eco-friendly materials and manufacturing processes. The use of ‘green’ certifications and materials not only enhances a company’s reputation but also aligns with global sustainability goals.
Ethical sourcing plays a pivotal role in this context. Buyers are encouraged to evaluate their suppliers based on their environmental impact, labor practices, and adherence to ethical standards. Coatings that are free from harmful solvents and made from renewable resources are gaining popularity. For instance, coatings that exhibit low volatile organic compound (VOC) emissions are particularly attractive to buyers in regions with stringent environmental regulations.
Furthermore, businesses that demonstrate commitment to sustainability can differentiate themselves in a competitive market. By selecting suppliers who prioritize eco-friendly practices, buyers can contribute to a more sustainable supply chain, ultimately driving positive change within their industries.
What Is the Evolution of Protective Plastic Coatings in the B2B Landscape?
The evolution of protective plastic coatings dates back several decades, with initial applications primarily focused on enhancing the durability of consumer products. Over time, technological advancements have significantly broadened the scope of applications, leading to the development of specialized coatings for industrial and commercial use.
In the early 2000s, the industry saw a shift towards high-performance coatings that provide enhanced resistance to chemicals, UV light, and abrasion. Innovations such as UV-cured coatings and advanced polymer formulations have emerged, enabling manufacturers to meet the increasing demands for durability and aesthetic appeal.
Today, the protective plastic coating sector continues to evolve, driven by the need for customization, sustainability, and advanced performance. This ongoing transformation presents B2B buyers with a wealth of opportunities to leverage cutting-edge solutions that can enhance the longevity and functionality of their products. As the market matures, staying informed about these trends is essential for making strategic sourcing decisions that align with both business goals and sustainability initiatives.
Frequently Asked Questions (FAQs) for B2B Buyers of protective plastic coating
-
How do I select the right protective plastic coating for my application?
Selecting the right protective plastic coating involves assessing the specific requirements of your application. Consider factors such as the environmental conditions (UV exposure, chemicals, temperature), the type of substrate (plastic, metal, etc.), and the intended use (indoor vs. outdoor). Look for coatings that offer features like high hardness, solvent resistance, and non-yellowing properties. Engaging with suppliers who provide samples for testing can also help you make an informed decision. -
What is the best protective plastic coating for UV protection?
For UV protection, coatings that are specifically formulated for high UV stability are ideal. Products like UV-cure hard coatings, such as Brewer Science’s ProTEK® PSR-R, provide superior resistance to UV degradation while maintaining transparency and gloss. These coatings help prevent yellowing and hazing, making them suitable for applications in outdoor settings. Always verify the UV resistance ratings and conduct real-world testing to ensure compatibility with your materials. -
What customization options are available for protective plastic coatings?
Many suppliers offer customization options, allowing you to tailor the coating’s properties to meet your specific needs. Customization can include variations in color, thickness, finish (matte or gloss), and performance characteristics (e.g., enhanced abrasion resistance or additional chemical resistance). Discuss your requirements with potential suppliers and request samples to evaluate how well the customized coatings meet your expectations. -
What are the minimum order quantities (MOQs) for protective plastic coatings?
Minimum order quantities can vary significantly depending on the supplier and the type of coating. Typically, MOQs range from a few liters for smaller custom formulations to several hundred liters for standard products. It’s advisable to communicate directly with suppliers to understand their MOQ policies, especially for international orders, as logistics and shipping considerations may also influence these requirements. -
What payment terms should I expect when sourcing protective plastic coatings internationally?
Payment terms for international transactions can vary widely among suppliers. Common practices include upfront payments, letters of credit, and payment upon delivery. It’s essential to discuss and negotiate payment terms upfront to avoid misunderstandings. Consider using secure payment methods and ensure that the terms are clearly outlined in the purchase agreement, particularly when dealing with suppliers from different regions. -
How can I ensure quality assurance for protective plastic coatings?
To ensure quality assurance, request certification documents and product specifications from suppliers. Look for coatings that meet international standards, such as ISO certifications. Additionally, consider suppliers who offer third-party testing or quality control processes. Conducting your own tests on samples before placing larger orders can also help confirm that the coatings perform as expected in your specific applications.
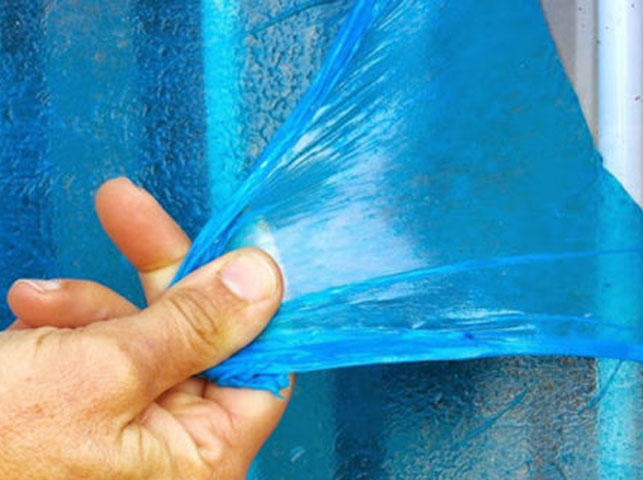
A stock image related to protective plastic coating.
-
What logistics considerations should I be aware of when importing protective plastic coatings?
Logistics considerations include shipping methods, customs regulations, and potential import duties. Ensure that your supplier is familiar with international shipping requirements and can provide necessary documentation for customs clearance. Discuss logistics options, such as freight forwarding and insurance, to mitigate risks during transport. Additionally, consider the lead times for production and shipping to align with your project timelines. -
How do I vet suppliers for protective plastic coatings effectively?
Effective supplier vetting involves researching their reputation, quality of products, and customer service. Check for reviews, testimonials, and case studies from other B2B buyers. Request references and inquire about their experience with international shipping and compliance with safety regulations. Conducting site visits or virtual tours of the manufacturing facility can also provide insights into their operational capabilities and quality control measures.
Important Disclaimer & Terms of Use
⚠️ Important Disclaimer
The information provided in this guide, including content regarding manufacturers, technical specifications, and market analysis, is for informational and educational purposes only. It does not constitute professional procurement advice, financial advice, or legal advice.
While we have made every effort to ensure the accuracy and timeliness of the information, we are not responsible for any errors, omissions, or outdated information. Market conditions, company details, and technical standards are subject to change.
B2B buyers must conduct their own independent and thorough due diligence before making any purchasing decisions. This includes contacting suppliers directly, verifying certifications, requesting samples, and seeking professional consultation. The risk of relying on any information in this guide is borne solely by the reader.
Strategic Sourcing Conclusion and Outlook for protective plastic coating
In the evolving landscape of protective plastic coatings, strategic sourcing emerges as a critical factor for international B2B buyers. By understanding the diverse applications and benefits of various protective coatings, businesses can enhance their operational efficiency and product longevity. Key insights reveal that investing in high-quality coatings, such as UV-cured options and flexible strippable varieties, can significantly reduce maintenance costs and improve product performance across industries.
Why Is Strategic Sourcing Essential for Protective Plastic Coatings?
Strategic sourcing not only ensures the acquisition of superior materials but also fosters strong supplier relationships, enabling access to innovations and competitive pricing. For companies in Africa, South America, the Middle East, and Europe, leveraging local suppliers can streamline logistics and reduce lead times, ultimately enhancing market responsiveness.
Looking ahead, the demand for advanced protective coatings is poised to grow, driven by increasing environmental standards and a focus on sustainability. International B2B buyers should prioritize suppliers who demonstrate a commitment to eco-friendly practices and technological advancements. Embrace this opportunity to secure your supply chain and elevate your product offerings—your proactive approach today will pave the way for success in tomorrow’s market.