Master Sourcing CNC Milling Machine Bits: Unlock Precision
Introduction: Navigating the Global Market for cnc milling machine bits
In the rapidly evolving world of manufacturing, CNC milling machine bits are not just tools; they are critical components that drive precision, efficiency, and productivity across various industries. For B2B buyers in regions such as Africa, South America, the Middle East, and Europe, understanding the intricacies of these milling bits is vital. Selecting the right bit can mean the difference between a successful machining operation and costly production delays.
This comprehensive guide aims to demystify the complexities of CNC milling machine bits by covering a wide range of topics essential for informed sourcing decisions. From an exploration of various bit types—including flat end mills, ball-nose end mills, and roughing end mills—to an analysis of materials and coatings, this resource provides actionable insights tailored to the unique needs of international buyers. Additionally, we delve into manufacturing quality control standards, supplier selection criteria, and cost structures, ensuring that you are well-equipped to navigate the global market.
By leveraging this guide, B2B buyers will gain the knowledge necessary to optimize their procurement strategies, enhance operational efficiency, and ultimately support sustainable growth in a competitive landscape. With a focus on practical answers to common questions, this resource empowers manufacturers from Brazil to Kenya to make strategic decisions that elevate their machining capabilities and drive business success.
Understanding cnc milling machine bits Types and Variations
Type Name | Key Distinguishing Features | Primary B2B Applications | Brief Pros & Cons for Buyers |
---|---|---|---|
Flat (Square) End Mill | Flat tip; 2–4 flutes; sharp edges for material removal | Slotting, face milling, profiling, general part production | Versatile and precise; may leave sharp corners susceptible to chipping |
Ball-Nose End Mill | Rounded tip; varying diameters; 2+ flutes | 3D contouring, mold & die, finishing curved surfaces | Ideal for smooth curves; not suited for sharp corners |
Roughing End Mill | Serrated/fluted edges; aggressive geometry | Bulk material removal, pre-finishing, heavy-duty cuts | Increases throughput, reduces vibration; leaves coarse finish |
Tapered End Mill | Angled sides; variable taper degree | Mold making, die cutting, deep cavities with angles | Enables deep, angled cuts; less flexible for flat work |
Shell End Mill | Large cutting diameter; replaceable inserts | High-volume face milling, large surface finishing | Efficient for wide areas; initial investment higher |
Flat (Square) End Mill
Flat end mills are the backbone of CNC machining, characterized by their sharp corners and flat cutting faces. They are widely used for general milling tasks, including slotting and profiling, across various materials like metals, plastics, and composites. B2B buyers should consider the mill’s compatibility with their machine’s spindle horsepower and opt for solid carbide or coated variants to enhance tool longevity, especially in high-wear applications.
Ball-Nose End Mill
Ball-nose end mills feature a rounded tip, making them ideal for intricate 3D contouring and finishing curved surfaces. Their design minimizes tool marks, facilitating the creation of complex shapes required in industries such as automotive and aerospace. When purchasing, buyers should evaluate the required tip radii and shank compatibility, along with selecting heat-resistant coatings to extend tool life in demanding environments.
Roughing End Mill
Roughing end mills are designed with serrated flutes that allow for rapid material removal, making them essential for the roughing phase of machining. Their aggressive geometry not only increases throughput but also reduces mechanical stress on both the tooling and workpiece. Buyers should consider production volume needs and select robust materials, such as carbide or cobalt, to optimize cost efficiency and minimize downtime.
Tapered End Mill
Tapered end mills have angled sides, providing versatility for creating deep cavities and angled surfaces, particularly in mold and die manufacturing. Their unique profile allows them to access complex geometries that standard end mills cannot. B2B buyers should assess the specific taper degree required for their applications and consider the tool’s rigidity and compatibility with their machining setup to ensure effective performance.
Shell End Mill
Shell end mills are characterized by their large cutting diameter and replaceable inserts, making them suitable for high-volume face milling and large surface finishing tasks. They offer efficiency in machining wide areas but come with a higher initial investment compared to other types. Buyers should weigh the long-term benefits of reduced tool change times and increased productivity against the upfront costs when considering shell end mills for their operations.
Related Video: Beginners Guide to CNC Bits – Including Speeds and Feeds
Key Industrial Applications of cnc milling machine bits
Industry/Sector | Specific Application of cnc milling machine bits | Value/Benefit for the Business | Key Sourcing Considerations for this Application |
---|---|---|---|
Automotive | Precision component manufacturing | High accuracy and repeatability in part production | Compatibility with CNC machines; material selection |
Aerospace | Mold and die creation for complex parts | Enhanced performance in high-stress environments | Coating options; supplier certifications; lead times |
Electronics | PCB prototyping and enclosures | Improved design flexibility and reduced time-to-market | Precision tolerances; material compatibility |
Construction Machinery | Heavy-duty part fabrication | Increased durability and operational efficiency | Tool life expectancy; cost-effectiveness of materials |
Medical Devices | Custom tooling for implants and instruments | Strict adherence to quality standards and precision | Regulatory compliance; specialized coatings |
Automotive Industry
In the automotive sector, CNC milling machine bits are essential for the manufacturing of precision components such as engine parts, transmission housings, and chassis components. The use of high-quality milling bits ensures that parts meet stringent tolerances, which is critical for performance and safety. International buyers must consider the compatibility of bits with their CNC machines and the specific materials being machined, such as aluminum or steel, to enhance productivity and reduce waste.
Aerospace Sector
The aerospace industry relies heavily on CNC milling for mold and die creation, enabling the production of complex components that withstand high stress and temperatures. High-performance milling bits, especially those with specialized coatings, are crucial for achieving the durability required in aerospace applications. Buyers should prioritize suppliers who can provide certified tooling solutions and consider lead times for critical components, as delays can significantly impact production schedules.
Electronics Industry
In electronics, CNC milling machine bits are used for the prototyping of printed circuit boards (PCBs) and the fabrication of enclosures. The precision and flexibility offered by these bits allow manufacturers to iterate designs rapidly, reducing time-to-market for new products. Buyers in this sector should focus on sourcing bits that can achieve tight tolerances and are compatible with various materials, including plastics and copper, to ensure high-quality outputs.
Construction Machinery
CNC milling is vital in the construction machinery industry for fabricating heavy-duty parts such as frames and gears. The robustness of milling bits directly affects the durability and efficiency of the final products. B2B buyers should evaluate the tool life and material costs when sourcing, as longer-lasting bits can reduce downtime and overall production costs, enhancing the business’s bottom line.
Medical Devices
The medical device industry demands extremely precise custom tooling for implants and surgical instruments, where even minor deviations can lead to significant issues. CNC milling machine bits play a critical role in this process, ensuring high-quality finishes and adherence to strict regulatory standards. Buyers must ensure that their suppliers comply with relevant medical manufacturing regulations and offer specialized coatings that enhance tool performance in biocompatible materials.
Related Video: Project ‘Poo Zoo’ uses animal dung to save at-risk species | REUTERS
Strategic Material Selection Guide for cnc milling machine bits
When selecting CNC milling machine bits, the choice of material is critical to achieving optimal performance and cost-effectiveness. Below is an analysis of four common materials used for milling bits, tailored for international B2B buyers, particularly from Africa, South America, the Middle East, and Europe.
Carbide
Key Properties:
Carbide is known for its exceptional hardness and wear resistance, making it suitable for high-speed machining. It can withstand high temperatures without losing its edge, which is crucial for maintaining performance in demanding applications.
Pros & Cons:
Carbide bits are durable and maintain sharpness longer than other materials, resulting in fewer tool changes and reduced downtime. However, they are more expensive than other options, which may impact budget considerations for smaller manufacturers.
Impact on Application:
Carbide is highly effective for machining hard materials like stainless steel and titanium, making it ideal for industries such as aerospace and automotive. Its performance in high-stress environments enhances productivity.
Considerations for International Buyers:
Buyers should ensure compliance with international standards such as ASTM and DIN. The higher initial investment in carbide bits can be justified by their longer lifespan and lower total cost of ownership.
High-Speed Steel (HSS)
Key Properties:
HSS is characterized by its ability to withstand high temperatures and maintain hardness. While not as hard as carbide, it offers good toughness and is less brittle, making it suitable for various applications.
Pros & Cons:
HSS bits are generally more affordable than carbide options, making them attractive for budget-conscious buyers. However, they tend to wear out faster, especially when used on harder materials, leading to more frequent replacements.
Impact on Application:
HSS is versatile and can be used for machining softer metals, plastics, and wood. It is particularly well-suited for general-purpose milling tasks in lower-stress environments.
Considerations for International Buyers:
Buyers should evaluate the trade-offs between cost and performance. HSS bits may be preferable in regions where softer materials are predominant, but compliance with local manufacturing standards remains essential.
Cobalt Steel
Key Properties:
Cobalt steel is an alloy that combines the toughness of HSS with improved heat resistance. This material can withstand higher temperatures than standard HSS, making it a reliable choice for tough machining tasks.
Pros & Cons:
Cobalt bits offer a good balance between cost and performance, providing longer tool life than standard HSS. However, they are still less durable than carbide, which may limit their use in high-volume production settings.
Impact on Application:
Cobalt steel is particularly effective for machining tough materials like stainless steel and high-temperature alloys, making it suitable for industries such as oil and gas.
Considerations for International Buyers:
Buyers should assess the availability and compliance of cobalt bits with international standards. The cost-effectiveness of cobalt tools can be appealing, but understanding local market conditions is crucial for optimal sourcing.
Coated Tools (TiN, TiAlN)
Key Properties:
Coatings such as titanium nitride (TiN) and aluminum titanium nitride (TiAlN) enhance the hardness and reduce friction of the base material. These coatings improve tool life and performance, especially in high-speed applications.
Pros & Cons:
Coated tools can significantly extend the life of the milling bits and improve cutting performance. However, the additional cost of coatings can be a consideration for budget-limited projects.
Impact on Application:
Coated bits are effective across a wide range of materials, including aluminum, steel, and composites. They are particularly beneficial in high-speed machining applications where heat generation is a concern.
Considerations for International Buyers:
It is essential to verify the quality of coatings and their compliance with relevant standards. Buyers should also consider the specific applications for which they are purchasing coated bits to ensure they meet performance expectations.
Summary Table
Material | Typical Use Case for cnc milling machine bits | Key Advantage | Key Disadvantage/Limitation | Relative Cost (Low/Med/High) |
---|---|---|---|---|
Carbide | Machining hard materials like stainless steel | Exceptional hardness and durability | Higher initial investment | High |
High-Speed Steel | General-purpose milling of softer metals | Cost-effective | Wears out faster than carbide | Low |
Cobalt Steel | Machining tough materials like high-temp alloys | Good balance of toughness and heat resistance | Less durable than carbide | Medium |
Coated Tools | High-speed machining across various materials | Extended tool life and performance | Additional cost for coatings | Medium to High |
This analysis provides a comprehensive overview of materials used in CNC milling machine bits, equipping international B2B buyers with the insights needed to make informed procurement decisions.
In-depth Look: Manufacturing Processes and Quality Assurance for cnc milling machine bits
CNC milling machine bits are critical components in various manufacturing processes, and understanding their manufacturing and quality assurance is vital for B2B buyers looking to optimize their procurement strategies. This section delves into the typical manufacturing processes and quality control measures employed in the production of these bits, providing actionable insights for international buyers, particularly those from Africa, South America, the Middle East, and Europe.
Manufacturing Processes for CNC Milling Machine Bits
The manufacturing process of CNC milling machine bits consists of several key stages: material preparation, forming, assembly, and finishing. Each stage incorporates specific techniques aimed at ensuring the quality and precision of the final product.
1. Material Preparation
The first step involves selecting high-quality raw materials, typically high-speed steel (HSS) or carbide, which are chosen based on the intended application and performance requirements.
- Material Selection: HSS is often used for general-purpose applications, while carbide is preferred for high-performance tasks due to its hardness and wear resistance.
- Material Treatment: Initial treatments, such as heat treatment or surface hardening, may be applied to enhance material properties before further processing.
2. Forming
The forming stage includes several techniques to shape the milling bits.
- CNC Machining: Computer Numerical Control (CNC) machining is used to achieve precise dimensions and geometries. CNC lathes and mills cut the raw material into the desired shape, creating flutes, cutting edges, and shank configurations.
- Grinding: After initial shaping, grinding processes refine the edges and surfaces. This step is crucial for achieving the fine tolerances required in milling applications.
- Coating Application: Bits may receive coatings such as titanium nitride (TiN) or aluminum titanium nitride (AlTiN) to improve wear resistance and reduce friction during operation.
3. Assembly
While most milling bits are single-piece constructions, some specialized tools may require assembly of multiple components.
- Insert Tools: For shell end mills or similar tools, replaceable inserts may be assembled to the main body. This allows for easy replacement of worn cutting edges without discarding the entire tool.
- Quality Checks: During assembly, manufacturers may perform preliminary inspections to ensure that all components fit together correctly and meet design specifications.
4. Finishing
The finishing stage is essential for enhancing the performance characteristics of milling bits.
- Surface Finishing: Processes such as polishing and additional grinding may be conducted to improve surface quality and reduce tool marks.
- Final Coating: A second layer of coating may be applied post-grinding to ensure optimal performance, particularly in high-temperature applications.
Quality Assurance Measures
Quality assurance (QA) is a critical aspect of the manufacturing process for CNC milling machine bits. Implementing robust QA protocols helps ensure that the final product meets international standards and customer expectations.
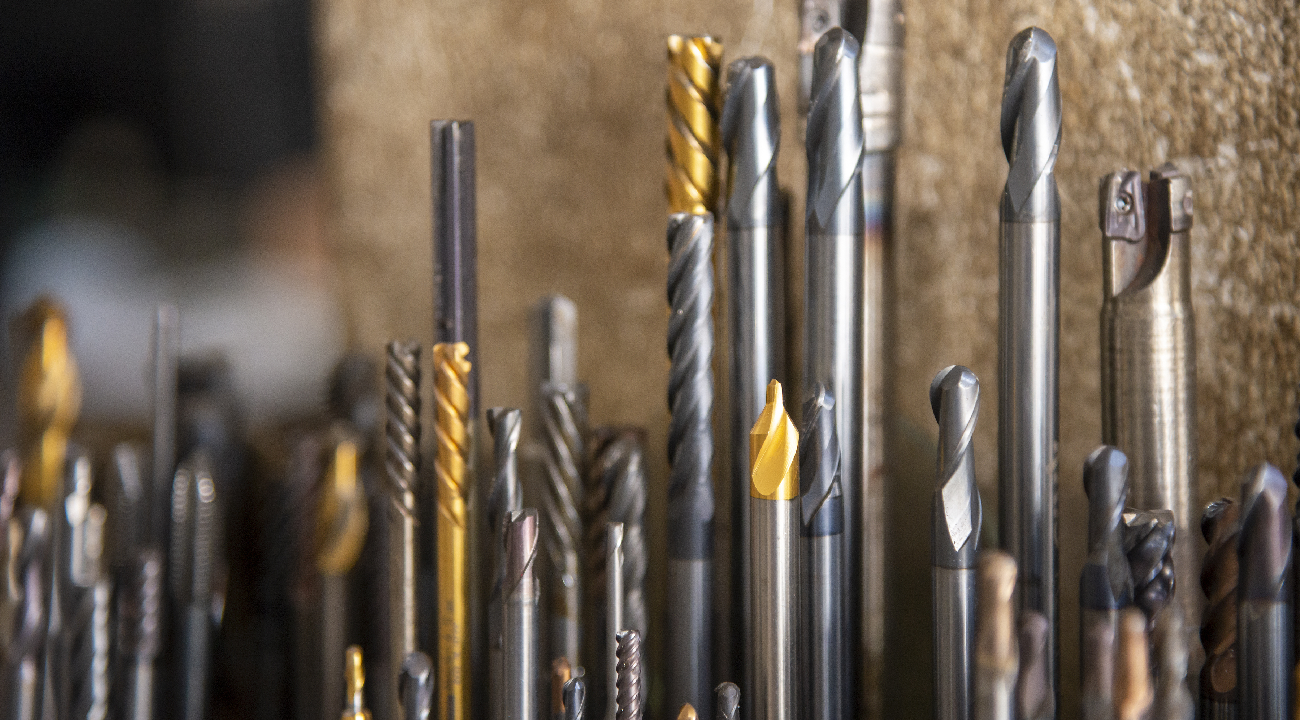
Illustrative Image (Source: Google Search)
Relevant International Standards
B2B buyers should be aware of the various international and industry-specific standards that govern the quality of CNC milling bits:
- ISO 9001: This standard outlines the requirements for a quality management system and is essential for ensuring consistent product quality.
- CE Marking: Products sold in the European Economic Area must meet specific safety, health, and environmental protection standards.
- API Standards: For bits used in oil and gas applications, adherence to American Petroleum Institute (API) standards may be necessary to ensure performance and safety.
QC Checkpoints
Quality control checkpoints are strategically placed throughout the manufacturing process:
- Incoming Quality Control (IQC): Raw materials are inspected upon arrival to verify their compliance with specified standards.
- In-Process Quality Control (IPQC): During manufacturing, regular checks are conducted to monitor the process and ensure that specifications are met.
- Final Quality Control (FQC): The finished products undergo comprehensive testing to validate their performance, including dimensional checks and functionality tests.
Common Testing Methods
Several testing methods are employed to assess the quality of CNC milling bits:
- Dimensional Inspection: Tools are measured against design specifications using calipers and gauges to ensure accurate dimensions.
- Hardness Testing: Techniques such as Rockwell or Vickers hardness tests evaluate the material’s hardness, ensuring it meets performance requirements.
- Cutting Tests: Practical tests may be conducted to assess the milling bit’s performance under operational conditions, verifying its effectiveness in real-world applications.
Verifying Supplier Quality Control
For international B2B buyers, verifying a supplier’s quality control measures is crucial for mitigating risks associated with procurement. Here are several strategies:
- Supplier Audits: Conducting on-site audits of potential suppliers helps assess their manufacturing processes, quality control systems, and adherence to international standards.
- Quality Reports: Requesting detailed quality reports, including data on past production runs and quality issues, can provide insights into a supplier’s reliability.
- Third-Party Inspections: Engaging independent inspection agencies to evaluate products before shipment ensures compliance with specified standards and reduces the risk of receiving subpar goods.
QC and Certification Nuances for International Buyers
When sourcing CNC milling bits from different regions, B2B buyers must navigate various certification requirements and quality nuances:
- Regional Standards: Different countries may have specific standards or certifications that must be met. Familiarizing oneself with these can streamline the procurement process.
- Cultural Considerations: Understanding cultural attitudes toward quality and compliance can influence supplier relationships and negotiations, particularly in regions like Africa and South America where standards may vary significantly.
By comprehensively understanding the manufacturing processes and quality assurance measures for CNC milling machine bits, B2B buyers can make informed decisions that enhance productivity, reduce downtime, and ensure the longevity of their tools. This knowledge is essential for navigating the complexities of international sourcing, particularly for buyers from Africa, South America, the Middle East, and Europe.
Related Video: SMART Quality Control for Manufacturing
Comprehensive Cost and Pricing Analysis for cnc milling machine bits Sourcing
Understanding the cost structure and pricing dynamics of CNC milling machine bits is crucial for international B2B buyers. This analysis provides insights into the various components that contribute to the overall cost, price influencers, and strategic tips for effective procurement.
Cost Components
-
Materials: The primary cost driver is the raw materials used to manufacture milling bits. Common materials include high-speed steel (HSS) and carbide, with carbide typically being more expensive due to its superior performance and durability. The choice of material significantly impacts both the price and the longevity of the bits.
-
Labor: Labor costs encompass the wages of skilled workers involved in the manufacturing process. In regions like Africa and South America, labor costs may vary widely, influencing the overall pricing of milling bits. Countries with lower labor costs might provide a competitive edge in pricing.
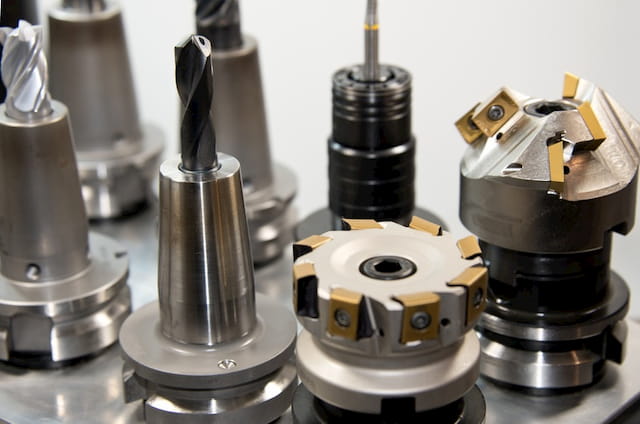
Illustrative Image (Source: Google Search)
-
Manufacturing Overhead: This includes indirect costs such as utilities, rent, and equipment maintenance. Efficient production processes can help minimize these costs, allowing suppliers to offer more competitive pricing.
-
Tooling: The initial investment in tooling and equipment is another significant cost component. High-quality tooling can enhance production efficiency but may require a higher upfront investment, which could be reflected in the price of the final product.
-
Quality Control (QC): Maintaining high standards of quality assurance adds to the cost structure. Suppliers that implement rigorous QC processes may charge a premium, but this can lead to enhanced reliability and performance of the milling bits.
-
Logistics: Transportation and shipping costs are crucial, especially for international buyers. Factors such as distance, shipping method, and local customs regulations can significantly influence the final price.
-
Margin: Suppliers typically incorporate a profit margin into their pricing. This margin can vary based on market competition, supplier reputation, and the perceived value of the product.
Price Influencers
-
Volume/MOQ: Bulk purchases often lead to discounts. Buyers should negotiate minimum order quantities (MOQs) to leverage better pricing, especially when sourcing from international suppliers.
-
Specifications/Customization: Custom bits designed for specific applications may incur additional costs. Buyers should weigh the benefits of customization against standard options to determine the best value.
-
Quality/Certifications: Products with industry certifications or superior quality assurance may come at a premium. However, investing in higher-quality bits can reduce the total cost of ownership by minimizing downtime and increasing productivity.
-
Supplier Factors: The supplier’s reputation, reliability, and service capabilities can affect pricing. Established suppliers may charge more due to their proven track record, but they often provide better support and consistent quality.
-
Incoterms: Understanding international shipping terms (Incoterms) is vital. These terms define the responsibilities of buyers and sellers, influencing logistics costs and risks associated with shipping.
Buyer Tips
-
Negotiation: Engage in active negotiations to secure favorable terms. Discuss volume discounts and payment terms to optimize procurement costs.
-
Cost Efficiency: Conduct a thorough analysis of the total cost of ownership (TCO), which includes purchase price, maintenance, and operational costs over the bit’s lifespan. This approach helps in evaluating the long-term value of different options.
-
Pricing Nuances: Be aware of regional pricing variations. For instance, sourcing from suppliers in emerging markets may offer cost advantages but could come with quality trade-offs. Thoroughly vet suppliers to ensure they meet your operational standards.
-
Disclaimer for Indicative Prices: Prices for CNC milling machine bits can fluctuate based on market conditions, material availability, and supplier pricing strategies. Always seek updated quotes and consider multiple suppliers to ensure competitive pricing.
By understanding these cost components and pricing influencers, international B2B buyers can make informed decisions that enhance their procurement strategies for CNC milling machine bits.
Essential Technical Properties and Trade Terminology for cnc milling machine bits
When sourcing CNC milling machine bits, understanding the essential technical properties and trade terminology is crucial for making informed procurement decisions. This knowledge not only enhances operational efficiency but also minimizes risks associated with incorrect specifications or misunderstandings in contracts.
Key Technical Properties
-
Material Grade
– The material from which a milling bit is made significantly affects its performance, durability, and suitability for various applications. Common materials include High-Speed Steel (HSS) for general use and Carbide for demanding applications requiring precision. B2B buyers should prioritize material grade based on the specific needs of their machining tasks, considering factors like wear resistance and thermal stability. -
Flute Count
– The number of flutes on a milling bit influences its cutting efficiency and chip removal capability. Generally, bits with fewer flutes (1-2) are used for rapid material removal, while those with more flutes (3-6) provide finer finishes. Understanding flute count allows buyers to select the appropriate bit for their machining operations, ensuring optimal performance and efficiency. -
Diameter and Length
– The diameter of the milling bit affects the depth and width of the cut, while the length determines reach and stability during machining. Buyers must match these specifications to their specific machinery and operational requirements to achieve desired outcomes without compromising tool integrity. -
Tolerance
– Tolerance refers to the allowable deviation from a specified dimension. High tolerance levels are critical in precision engineering, as they ensure components fit together correctly without excessive play. B2B buyers should assess tolerance requirements based on the end-use of the machined parts to ensure compatibility and functionality.
- Coating
– Coatings such as Titanium Nitride (TiN) or Aluminum Titanium Nitride (AlTiN) enhance tool life by reducing friction and wear. These coatings are particularly beneficial in high-speed applications or when machining abrasive materials. Buyers should consider the coating type to maximize the lifespan and efficiency of their milling bits.
Common Trade Terminology
-
OEM (Original Equipment Manufacturer)
– Refers to companies that produce parts or equipment that may be marketed by another manufacturer. Understanding OEM specifications is vital for ensuring compatibility and quality in milling bits, especially when sourcing from international suppliers. -
MOQ (Minimum Order Quantity)
– The smallest quantity of a product that a supplier is willing to sell. This term is essential for budget planning and inventory management, as it impacts the overall cost structure of purchasing milling bits. -
RFQ (Request for Quotation)
– A formal process where buyers solicit price quotes from suppliers. An RFQ allows B2B buyers to compare costs, terms, and capabilities of different suppliers, ensuring they make informed purchasing decisions. -
Incoterms (International Commercial Terms)
– A set of predefined international trade terms used in sales contracts to clarify the responsibilities of buyers and sellers regarding shipping, insurance, and tariffs. Familiarity with Incoterms helps buyers understand their obligations and risks during the procurement process. -
Lead Time
– The time taken from placing an order to receiving the product. Understanding lead times is crucial for project planning, as delays can impact manufacturing schedules and delivery commitments.
By grasping these essential technical properties and trade terms, international B2B buyers can navigate the complexities of sourcing CNC milling machine bits more effectively, ensuring they make strategic decisions that enhance productivity and reduce costs.
Navigating Market Dynamics, Sourcing Trends, and Sustainability in the cnc milling machine bits Sector
Market Overview & Key Trends
The CNC milling machine bits market is experiencing dynamic growth driven by several global factors. The rise of automation and Industry 4.0 has led to increased demand for precision machining tools, particularly in sectors such as automotive, aerospace, and medical devices. B2B buyers from Africa, South America, the Middle East, and Europe are increasingly focused on sourcing high-quality milling bits that enhance productivity and reduce operational costs. Emerging technologies, including advanced materials and coatings, are revolutionizing bit performance, enabling longer tool life and improved cutting speeds.
Key trends influencing the market include the shift toward customized solutions and smart manufacturing. Buyers are looking for suppliers that offer tailored milling bits that meet specific project requirements, such as unique geometries or specialized coatings. Additionally, the integration of IoT technologies in machining processes allows for real-time monitoring and predictive maintenance, reducing downtime and enhancing efficiency.
Moreover, the market is witnessing a surge in e-commerce platforms that facilitate easier access to global suppliers. For international buyers, understanding the nuances of local regulations, certifications, and standards compliance is crucial for making informed procurement decisions. As competition intensifies, companies that prioritize quality, reliability, and service differentiation will stand out in the crowded marketplace.
Sustainability & Ethical Sourcing in B2B
Sustainability has become a pivotal consideration for B2B buyers in the CNC milling machine bits sector. The environmental impact of manufacturing processes, including waste generation and energy consumption, is under scrutiny. Buyers are increasingly seeking suppliers that demonstrate a commitment to sustainable practices, such as using eco-friendly materials and minimizing carbon footprints.
Ethical sourcing is equally important, especially for international buyers navigating complex supply chains. Implementing transparent supply chain practices ensures compliance with labor laws and environmental regulations. Buyers should look for suppliers with green certifications, such as ISO 14001, that signify adherence to environmental management standards. Additionally, sourcing bits made from recycled materials or those that can be easily recycled at the end of their life cycle supports a circular economy.
Investing in sustainable milling bits not only aligns with corporate social responsibility goals but can also enhance brand reputation and customer loyalty. As sustainability becomes a competitive differentiator, B2B buyers should prioritize partnerships with suppliers who share these values and demonstrate tangible efforts toward sustainability.
Brief Evolution/History
The evolution of CNC milling machine bits can be traced back to the early days of machining when manual tools dominated the industry. With the advent of computer numerical control (CNC) technology in the mid-20th century, machining processes became more precise and efficient. Initially, milling bits were predominantly made from high-speed steel (HSS), but the introduction of carbide and other advanced materials revolutionized the sector. These materials offered superior hardness, wear resistance, and thermal stability, enabling manufacturers to produce complex geometries with high accuracy.
Over time, the development of specialized coatings further enhanced the performance of milling bits, allowing them to withstand demanding machining environments. As globalization expanded, international trade opened new markets, leading to increased competition and innovation. Today, the CNC milling bits market is characterized by a diverse range of products, catering to the evolving needs of industries worldwide, particularly in emerging economies like those in Africa and South America.
Related Video: International Trade Explained
Frequently Asked Questions (FAQs) for B2B Buyers of cnc milling machine bits
-
What should I consider when vetting suppliers for CNC milling machine bits?
When vetting suppliers, prioritize their experience in the industry and reputation for quality. Check for certifications such as ISO 9001, which ensure adherence to international quality standards. Request samples to evaluate the performance and durability of the milling bits. Also, consider their ability to provide custom solutions tailored to your specific machining needs, as well as their responsiveness to inquiries and support services. Finally, review their customer feedback and case studies to gauge satisfaction levels among previous clients. -
Can I customize milling machine bits to suit specific applications?
Yes, many suppliers offer customization options for CNC milling machine bits. Customization may include altering the geometry, coating, or material composition to fit specific machining tasks or materials. When discussing customization, clearly outline your requirements, including size, shape, and intended application. Ensure the supplier has the capability to produce tailored bits and inquire about any additional costs or lead times associated with custom orders. -
What are the typical minimum order quantities (MOQs) and lead times for CNC milling bits?
MOQs for CNC milling machine bits can vary significantly based on the supplier and the complexity of the order. Common MOQs range from 10 to 100 pieces, particularly for standard items. For custom bits, MOQs may be higher. Lead times also depend on factors such as the supplier’s production capacity and whether the bits are in stock. Generally, expect lead times of 2 to 6 weeks for standard orders and potentially longer for custom products. Always confirm these details upfront to avoid delays. -
What payment options are available when sourcing CNC milling bits internationally?
Payment options for international orders may include wire transfers, letters of credit, PayPal, or escrow services. It’s crucial to establish a secure payment method that protects both parties. Discuss payment terms with your supplier, including deposits, payment schedules, and any applicable credit options. Be mindful of currency fluctuations and consider negotiating terms that mitigate risks associated with international transactions. -
How can I ensure the quality of CNC milling bits before making a purchase?
To ensure quality, request detailed specifications and certifications from the supplier, such as ISO compliance or other relevant industry standards. Ask for samples to conduct in-house testing, evaluating factors like durability, cutting efficiency, and finish quality. Additionally, inquire about their quality control processes, including inspections and testing methodologies. Establishing a trial order can also help assess performance before committing to larger purchases. -
What logistics considerations should I keep in mind when importing CNC milling bits?
When importing milling bits, consider shipping methods, costs, and delivery times. Evaluate whether the supplier offers direct shipping to your location or if you need to manage logistics independently. Familiarize yourself with import duties, taxes, and regulations in your country to avoid unexpected expenses. It’s advisable to work with a reliable freight forwarder who can assist with customs clearance and ensure timely delivery. -
How should I handle disputes with suppliers regarding CNC milling bits?
To effectively handle disputes, maintain clear and open communication with your supplier. Document all agreements, specifications, and communications to establish a record in case issues arise. If a dispute occurs, address it promptly by discussing the problem directly with the supplier and seeking an amicable resolution. If necessary, refer to your contract for dispute resolution procedures, which may include mediation or arbitration. Building a strong relationship with suppliers can often prevent disputes from escalating. -
What certifications or quality assurance measures should I look for in CNC milling bits?
Look for certifications such as ISO 9001, which indicate that the supplier adheres to rigorous quality management standards. Additionally, check if the bits comply with any industry-specific standards relevant to your application, such as ASTM or DIN. Inquire about the supplier’s quality assurance processes, including inspections, testing protocols, and material traceability. Suppliers that prioritize quality assurance are more likely to provide reliable products that meet your operational needs.
Important Disclaimer & Terms of Use
⚠️ Important Disclaimer
The information provided in this guide, including content regarding manufacturers, technical specifications, and market analysis, is for informational and educational purposes only. It does not constitute professional procurement advice, financial advice, or legal advice.
While we have made every effort to ensure the accuracy and timeliness of the information, we are not responsible for any errors, omissions, or outdated information. Market conditions, company details, and technical standards are subject to change.
B2B buyers must conduct their own independent and thorough due diligence before making any purchasing decisions. This includes contacting suppliers directly, verifying certifications, requesting samples, and seeking professional consultation. The risk of relying on any information in this guide is borne solely by the reader.
Strategic Sourcing Conclusion and Outlook for cnc milling machine bits
In navigating the complex landscape of CNC milling machine bits, international B2B buyers must prioritize strategic sourcing as a key driver of operational success. Understanding the diverse types of milling bits—such as flat end mills, ball-nose end mills, and roughing end mills—enables buyers to make informed decisions that enhance productivity and machining accuracy. Selecting the right materials and coatings not only prolongs tool life but also optimizes performance across various applications.
Buyers should leverage market intelligence to identify reliable suppliers, ensuring compliance with regional standards while negotiating favorable pricing structures. Investing time in understanding the total cost of ownership and the specific requirements of their operations can mitigate risks associated with procurement errors, such as costly downtimes and compromised quality.
Looking ahead, the demand for advanced machining solutions will continue to rise across Africa, South America, the Middle East, and Europe. By embracing innovative sourcing strategies and staying informed about industry trends, B2B buyers can position themselves for long-term growth and competitiveness. Take action today—evaluate your sourcing strategies, engage with trusted suppliers, and optimize your milling operations for a successful tomorrow.