Your Ultimate Guide to Sourcing Inexpensive Cnc Milling
Introduction: Navigating the Global Market for inexpensive cnc milling machine
In the ever-evolving landscape of manufacturing, the demand for cost-effective solutions is paramount. Inexpensive CNC milling machines have emerged as a game-changer, enabling businesses across diverse sectors to enhance production efficiency without compromising on quality. For international B2B buyers, particularly those in Africa, South America, the Middle East, and Europe, understanding the nuances of sourcing these machines is crucial.
This comprehensive guide is designed to empower you with actionable insights into the global market for inexpensive CNC milling machines. We will explore various types of milling machines, delve into the materials commonly processed, and scrutinize the manufacturing and quality control standards that ensure reliability. Additionally, we will identify reputable suppliers and provide a detailed analysis of cost factors that can influence your purchasing decisions.
With a focus on the unique challenges and opportunities in regions like Italy and Kenya, this guide aims to equip you with the knowledge needed to make informed sourcing decisions. By understanding the market dynamics and leveraging best practices, you can enhance your procurement strategy and drive your business forward. Whether you’re a seasoned buyer or new to the CNC milling landscape, this resource will serve as your essential toolkit for navigating the complexities of sourcing inexpensive CNC milling machines.
Understanding inexpensive cnc milling machine Types and Variations
Type Name | Key Distinguishing Features | Primary B2B Applications | Brief Pros & Cons for Buyers |
---|---|---|---|
Benchtop CNC Milling Machines | Compact size, often portable, suitable for small workshops | Prototyping, small batch production | Pros: Affordable, space-saving; Cons: Limited capacity and power. |
Vertical CNC Milling Machines | Vertical spindle orientation, versatile tooling options | Aerospace, automotive, and mold making | Pros: High precision and flexibility; Cons: Requires more floor space. |
Horizontal CNC Milling Machines | Horizontal spindle orientation, ideal for heavy materials | Heavy machining, large-scale production | Pros: Efficient for bulk processing; Cons: Higher initial investment. |
CNC Router Machines | Designed for softer materials, often includes a vacuum table | Woodworking, plastics, and signage | Pros: Great for detailed work; Cons: Limited to non-metal materials. |
Mini CNC Milling Machines | Smaller footprint, often entry-level machines | Hobbyist projects, educational use | Pros: Very affordable, user-friendly; Cons: Limited functionality for complex tasks. |
Benchtop CNC Milling Machines
Benchtop CNC milling machines are compact and often portable, making them ideal for small workshops and limited spaces. They typically offer sufficient precision for prototyping and small batch production. When considering a purchase, B2B buyers should assess the machine’s weight capacity and the types of materials it can handle. These machines are particularly suitable for startups and small manufacturers looking to minimize initial costs while still achieving decent machining capabilities.
Vertical CNC Milling Machines
Vertical CNC milling machines are characterized by their vertical spindle orientation, which allows for versatile tooling options and is widely used in industries like aerospace and automotive. They provide high precision and flexibility, making them suitable for complex parts. Buyers should consider the machine’s rigidity, tooling options, and software compatibility. While they require more floor space, their capabilities can lead to increased productivity and reduced cycle times for larger operations.
Horizontal CNC Milling Machines
Horizontal CNC milling machines feature a horizontal spindle orientation, making them ideal for heavy materials and large-scale production. They are particularly efficient for bulk processing and can handle more demanding tasks than their vertical counterparts. B2B buyers must evaluate the machine’s power, tool change capabilities, and coolant systems. Although the initial investment may be higher, the operational efficiency gained can justify the cost for larger manufacturers.
CNC Router Machines
CNC router machines are designed primarily for softer materials such as wood, plastics, and composites. They often come equipped with a vacuum table for material hold-down, making them excellent for detailed work in woodworking, signage, and prototyping. When purchasing, buyers should assess the machine’s software compatibility and maximum cutting area. While they excel in non-metal applications, their limitations in handling harder materials should be considered for manufacturers looking for versatility.
Mini CNC Milling Machines
Mini CNC milling machines are characterized by their small footprint and user-friendly operation, making them perfect for hobbyist projects and educational purposes. They are very affordable, providing an entry point for businesses looking to explore CNC machining without significant investment. However, buyers should note that their functionality is limited for complex tasks and larger materials. This type of machine is best suited for small-scale operations or as a supplementary tool in a larger manufacturing setup.
Related Video: Inexpensive but Impressive Amateur CNC Milling Machine: Unpacking and Reviewing Two Trees TTC450 Pro
Key Industrial Applications of inexpensive cnc milling machine
Industry/Sector | Specific Application of Inexpensive CNC Milling Machine | Value/Benefit for the Business | Key Sourcing Considerations for this Application |
---|---|---|---|
Manufacturing | Precision Part Production | High accuracy and reduced waste | Look for machines with reliable precision specs |
Automotive | Prototype Development | Faster time-to-market for new designs | Ensure compatibility with automotive materials |
Aerospace | Component Machining | Lightweight, high-strength components | Focus on machines that can handle complex geometries |
Electronics | Custom Enclosures and Mounts | Improved product aesthetics and functionality | Verify the ability to mill intricate designs |
Construction | Tooling and Fixture Creation | Enhanced efficiency in assembly processes | Assess machine durability and ease of maintenance |
Manufacturing
In the manufacturing sector, inexpensive CNC milling machines are utilized for precision part production. These machines allow companies to produce high-accuracy components while minimizing material waste. For international buyers, particularly from regions like Africa and South America, sourcing machines that meet specific precision standards is crucial. They should also consider after-sales support and availability of replacement parts to ensure continuous operation.
Automotive
In the automotive industry, CNC milling machines play a vital role in prototype development. By enabling rapid prototyping, these machines help manufacturers bring new designs to market faster, which is essential in the highly competitive automotive sector. Buyers from the Middle East and Europe should prioritize machines that can handle various materials, including metals and plastics, and ensure that the equipment complies with local automotive industry standards.
Aerospace
The aerospace sector demands high-quality component machining to produce lightweight and high-strength parts. Inexpensive CNC milling machines can meet these stringent requirements, making them ideal for small to mid-sized aerospace manufacturers. Buyers, especially from Europe, should focus on machines capable of intricate geometries and those with certifications that align with aerospace standards, ensuring compliance and reliability in their production processes.
Electronics
In the electronics industry, inexpensive CNC milling machines are employed to create custom enclosures and mounts for various devices. This application enhances both the aesthetics and functionality of electronic products. B2B buyers, particularly from Africa and South America, should assess the machine’s ability to mill intricate designs and prioritize suppliers who offer advanced software integration to streamline the design process.
Construction
In the construction sector, CNC milling machines are essential for tooling and fixture creation. These tools significantly enhance efficiency during assembly processes by providing precise and repeatable components. Buyers from the Middle East and Europe should consider the durability of the machines and their maintenance requirements, as these factors will impact long-term operational costs and productivity in demanding construction environments.
Related Video: DIY CNC Milling Machine – The Complete How to Build Video
Strategic Material Selection Guide for inexpensive cnc milling machine
When selecting materials for inexpensive CNC milling machines, it is crucial to consider the properties, advantages, and limitations of each material. Here, we analyze four common materials used in CNC milling applications, focusing on their relevance to international B2B buyers from regions such as Africa, South America, the Middle East, and Europe.
Aluminum Alloys
Key Properties: Aluminum alloys are lightweight, have good corrosion resistance, and can withstand moderate temperatures. They typically possess a tensile strength ranging from 70 to 700 MPa, making them suitable for various applications.
Pros & Cons: The main advantage of aluminum alloys is their excellent machinability, which reduces manufacturing complexity and costs. However, they may not be as durable as steel in high-stress applications, and their performance can degrade at elevated temperatures.
Impact on Application: Aluminum is compatible with a wide range of media, making it suitable for both structural and aesthetic components. It is commonly used in the automotive and aerospace industries.
Considerations for International Buyers: Buyers should ensure compliance with international standards like ASTM and DIN when sourcing aluminum alloys. Additionally, the availability of specific alloy grades may vary by region, affecting procurement strategies.
Steel Alloys
Key Properties: Steel alloys are known for their high strength and durability, with tensile strengths often exceeding 1000 MPa. They exhibit excellent wear resistance and can handle high-pressure applications.
Pros & Cons: The primary advantage of steel is its robustness, making it ideal for heavy-duty applications. However, steel is heavier than aluminum, which can increase shipping costs. Moreover, the machining process is more complex and may require specialized tools.
Impact on Application: Steel is widely used in applications requiring high strength and durability, such as machinery components and structural elements.
Considerations for International Buyers: Buyers should be aware of the varying grades of steel and their respective standards (e.g., JIS, ASTM). Additionally, the cost of steel can fluctuate based on global market conditions, which may impact budgeting.
Plastics (e.g., Nylon, Polycarbonate)
Key Properties: Plastics like nylon and polycarbonate are lightweight and offer good chemical resistance. They can operate under moderate temperatures, with tensile strengths ranging from 50 to 150 MPa.
Pros & Cons: Plastics are cost-effective and easy to machine, which can significantly lower production costs. However, they may not be suitable for high-stress applications due to lower strength and durability compared to metals.
Impact on Application: Plastics are ideal for applications requiring insulation or chemical resistance, such as housings and non-structural components.
Considerations for International Buyers: Buyers should ensure that the selected plastics meet relevant safety and environmental standards. Additionally, sourcing may be affected by regional availability and import regulations.
Composites (e.g., Carbon Fiber Reinforced Polymers)
Key Properties: Composites are known for their high strength-to-weight ratio and excellent fatigue resistance. They can withstand a range of temperatures and offer good corrosion resistance.
Pros & Cons: The main advantage of composites is their lightweight nature combined with high strength, making them suitable for advanced applications. However, they can be more expensive and complex to manufacture compared to metals and plastics.
Impact on Application: Composites are often used in high-performance applications such as aerospace and automotive components, where weight savings are critical.
Considerations for International Buyers: Buyers should be aware of the specific manufacturing processes required for composites and ensure compliance with international standards. The availability of composite materials may vary, impacting sourcing strategies.
Summary Table
Material | Typical Use Case for inexpensive cnc milling machine | Key Advantage | Key Disadvantage/Limitation | Relative Cost (Low/Med/High) |
---|---|---|---|---|
Aluminum Alloys | Automotive and aerospace components | Excellent machinability | Less durable than steel | Low |
Steel Alloys | Heavy-duty machinery components | High strength and durability | Heavier and more complex to machine | Medium |
Plastics (e.g., Nylon) | Housings and non-structural components | Cost-effective and easy to machine | Lower strength and durability | Low |
Composites (e.g., Carbon Fiber) | Aerospace and automotive high-performance components | High strength-to-weight ratio | More expensive and complex to manufacture | High |
This guide provides actionable insights for B2B buyers to make informed decisions when selecting materials for inexpensive CNC milling machines, taking into account regional considerations and compliance with international standards.
In-depth Look: Manufacturing Processes and Quality Assurance for inexpensive cnc milling machine
Manufacturing Processes for Inexpensive CNC Milling Machines
The manufacturing of inexpensive CNC milling machines involves several critical stages that ensure both functionality and cost-effectiveness. Understanding these processes is essential for international B2B buyers looking to make informed purchasing decisions.
Material Preparation
The first stage in the manufacturing process is material preparation, which typically involves selecting the right metals and alloys. Common materials include aluminum, steel, and cast iron, chosen for their machinability and durability.
- Material Sourcing: Suppliers often source materials locally to reduce costs. Buyers should inquire about the origin of materials to ensure compliance with international standards and regulations.
- Cutting and Shaping: Raw materials are cut into manageable sizes using saws or plasma cutters. This initial shaping is crucial for minimizing waste and optimizing material use.
Forming
The forming stage includes various techniques that shape the material into the components required for the CNC milling machine.
- Machining Processes: Techniques such as turning, drilling, and milling are employed. For inexpensive models, automated processes may be utilized to enhance efficiency while maintaining quality.
- CNC Programming: The components are programmed for CNC machining, which ensures precision and repeatability. Buyers should confirm that suppliers use modern software to facilitate accurate machining.
Assembly
Assembly is a pivotal stage where all components come together.
- Component Integration: Key parts, including the spindle, axis, and control systems, are assembled. This step often involves both manual and automated processes to ensure accuracy.
- Alignment and Calibration: Proper alignment is essential for machine performance. Buyers should verify that suppliers perform rigorous calibration procedures before shipping.
Finishing
The finishing process enhances the machine’s appearance and performance.
- Surface Treatment: Techniques such as anodizing or powder coating are used to protect the machine from wear and corrosion.
- Quality Checks: Final inspections are crucial at this stage to ensure that all components meet the specified tolerances and quality standards.
Quality Assurance Standards
Quality assurance (QA) plays a vital role in the production of CNC milling machines, especially for international buyers who require consistency and reliability.
International Standards
Compliance with international standards, such as ISO 9001, is essential for ensuring quality management systems. This certification demonstrates a supplier’s commitment to quality and customer satisfaction.
- CE Marking: For buyers in Europe, CE marking indicates that the product meets EU safety, health, and environmental protection standards.
- API Standards: For those in industries like oil and gas, adhering to API (American Petroleum Institute) standards can be crucial.
Quality Control Checkpoints
Quality control (QC) checkpoints are integrated throughout the manufacturing process to detect and correct defects early.
- Incoming Quality Control (IQC): Inspects raw materials upon arrival to ensure they meet specified standards.
- In-Process Quality Control (IPQC): Monitors the manufacturing process in real-time to catch any deviations from quality standards.
- Final Quality Control (FQC): Conducts a thorough examination of the finished product before it is shipped to ensure it meets all specifications.
Common Testing Methods
Testing methods are essential to validate the machine’s performance and durability.
- Functional Testing: Ensures that the CNC milling machine operates as intended under various loads and conditions.
- Dimensional Testing: Uses tools such as calipers and gauges to verify that all components meet design specifications.
- Durability Testing: Simulates long-term usage to assess the machine’s longevity and reliability.
Verifying Supplier Quality Control
For B2B buyers, especially those in Africa, South America, the Middle East, and Europe, verifying a supplier’s quality control processes is crucial.
- Supplier Audits: Conducting audits allows buyers to assess the manufacturing processes and QC measures in place. This can be done through on-site visits or third-party inspections.
- Quality Reports: Requesting detailed quality reports from suppliers can provide insights into their QC processes and any corrective actions taken.
- Third-Party Inspections: Engaging third-party inspection services can provide an unbiased assessment of the machine’s quality before shipment.
QC and Certification Nuances for International Buyers
International buyers must navigate various certification requirements that can differ significantly by region.
- Regional Compliance: In Europe, compliance with CE standards is critical, while in the Middle East, local regulations may vary. Buyers should ensure suppliers are knowledgeable about regional requirements.
- Documentation: Buyers should insist on comprehensive documentation, including test results and certifications, to facilitate customs clearance and compliance in their respective countries.
Conclusion
Understanding the manufacturing processes and quality assurance protocols for inexpensive CNC milling machines is essential for international B2B buyers. By focusing on material preparation, forming, assembly, and finishing stages, along with stringent QC measures, buyers can ensure they select reliable suppliers that meet their operational needs. Engaging in thorough verification practices will further enhance confidence in the procurement process, ultimately leading to more successful business outcomes.
Related Video: SMART Quality Control for Manufacturing
Comprehensive Cost and Pricing Analysis for inexpensive cnc milling machine Sourcing
Understanding the cost and pricing landscape of inexpensive CNC milling machines is crucial for international B2B buyers. This analysis will break down the various components influencing costs, factors affecting pricing, and provide actionable insights for efficient sourcing.
Cost Components
-
Materials: The type and quality of materials used in manufacturing CNC milling machines significantly impact the overall cost. Steel and aluminum are commonly used, but the choice between standard and high-grade materials can affect durability and machine performance. Buyers should prioritize suppliers that offer a balance between cost and material quality.
-
Labor: Labor costs vary by region and can significantly influence the pricing of CNC machines. Regions with lower labor costs may offer cheaper machines, but this could compromise on the skill level of workers. It’s essential to assess the supplier’s workforce and their expertise in CNC manufacturing.
-
Manufacturing Overhead: This includes costs related to factory operations, utilities, and equipment maintenance. Efficient manufacturing processes can reduce overhead, translating to lower prices for buyers. Investigate suppliers that employ lean manufacturing principles or automation to optimize costs.
-
Tooling: Tooling costs are often overlooked but can be substantial, especially if custom tools are required for specific machine specifications. Buyers should consider the tooling setup as part of their total cost when evaluating offers from suppliers.
-
Quality Control (QC): Rigorous QC processes ensure that machines meet required standards. While this adds to the cost, it ultimately protects the buyer’s investment by reducing the risk of defects. Evaluate suppliers based on their QC certifications and practices.
-
Logistics: Shipping costs and logistics management are critical, particularly for international buyers. Factors such as distance, shipping mode, and customs duties can add significant expenses. Buyers should seek suppliers with efficient logistics solutions to minimize these costs.
-
Margin: Suppliers will include a profit margin in their pricing, which can vary widely. Understanding the typical margins in the CNC milling machine market can help buyers identify reasonable pricing and negotiate better deals.
Price Influencers
-
Volume/MOQ: The minimum order quantity (MOQ) and volume of purchase can significantly influence pricing. Larger orders often lead to discounts, so pooling orders with other buyers or negotiating for bulk pricing can enhance cost efficiency.
-
Specifications/Customization: Custom machines or specific configurations may carry higher costs. Buyers should clearly define their requirements and assess whether the benefits of customization justify the additional expense.
-
Materials: As mentioned, the choice of materials affects both price and quality. Opting for standard materials can reduce costs, but buyers must balance this with performance needs.
-
Quality/Certifications: Machines that meet international quality standards or possess relevant certifications may command higher prices. Buyers in regions with strict regulations should ensure compliance to avoid future costs.
-
Supplier Factors: Supplier reputation, experience, and geographical location can influence costs. Established suppliers may charge more due to their reliability, but they often deliver better quality and service.
-
Incoterms: Understanding the Incoterms used in the contract can clarify who bears shipping costs and risks. This knowledge helps buyers negotiate terms that are more favorable and reduce unexpected expenses.
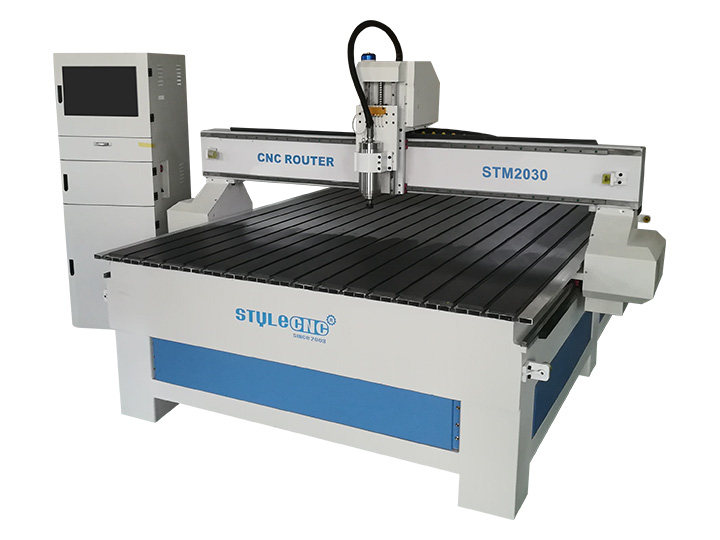
Illustrative Image (Source: Google Search)
Buyer Tips
-
Negotiation: Always negotiate pricing, especially for larger orders. Suppliers may have flexibility in their pricing structures, particularly if they are keen on securing a deal.
-
Cost-Efficiency: Evaluate total costs, including shipping, customs, and potential tariffs. Sometimes a slightly higher upfront price can lead to lower total costs if the machine is more durable or efficient.
-
Total Cost of Ownership (TCO): Consider the TCO, which includes maintenance, operational costs, and potential downtime. Investing in a slightly more expensive, higher-quality machine can be more cost-effective in the long run.
-
Regional Considerations: Buyers from Africa, South America, the Middle East, and Europe should be mindful of regional market conditions and trade agreements that may influence pricing.
Disclaimer
Prices mentioned in this analysis are indicative and can vary based on market conditions, supplier negotiations, and specific buyer requirements. Always conduct thorough due diligence before making purchasing decisions.
Spotlight on Potential inexpensive cnc milling machine Manufacturers and Suppliers
This section looks at several manufacturers active in the ‘inexpensive cnc milling machine’ market. This is a representative sample for illustrative purposes; B2B buyers must conduct extensive due diligence before any transaction. Information is synthesized from public sources and general industry knowledge.
Essential Technical Properties and Trade Terminology for inexpensive cnc milling machine
When considering an inexpensive CNC milling machine, understanding its essential technical properties and the relevant trade terminology is crucial for making informed purchasing decisions. This knowledge not only aids in evaluating machine capabilities but also enhances communication with suppliers and manufacturers.
Key Technical Properties
-
Material Grade
The material grade of the CNC milling machine components, such as the frame, bed, and spindle, directly impacts durability and performance. Common materials include cast iron, aluminum, and steel. Higher-grade materials usually offer better stability and longevity, which is vital for businesses in high-demand environments. Selecting machines made from robust materials can minimize maintenance costs and downtime. -
Tolerance
Tolerance refers to the permissible limit of variation in a physical dimension. For CNC milling machines, tighter tolerances indicate a machine’s ability to produce precise parts. Typical tolerances range from ±0.01 mm to ±0.1 mm. For B2B buyers, understanding the required tolerances for their specific applications ensures that the chosen machine can meet production quality standards, ultimately affecting product reliability. -
Spindle Speed
Spindle speed, measured in revolutions per minute (RPM), is crucial for determining the types of materials a CNC milling machine can effectively process. Higher spindle speeds allow for faster machining but can also generate more heat, affecting tool life and material finish. Buyers should assess the spindle speed in relation to the materials they plan to work with, ensuring compatibility with their production needs. -
Feed Rate
The feed rate indicates how quickly the machine’s cutting tool moves through the material. It is usually expressed in millimeters per minute (mm/min). A higher feed rate can lead to increased production efficiency, but it must be balanced against tool wear and the quality of the finished product. Buyers should consider their production volume and material characteristics to select a machine that optimally matches their operational requirements. -
Axis Configuration
CNC milling machines can have various axis configurations, typically 3, 4, or 5 axes. A 3-axis machine is sufficient for basic milling tasks, while 5-axis machines offer greater flexibility for complex geometries. For international buyers, understanding the axis configuration is essential for determining the machine’s suitability for specific applications, especially in industries like aerospace and automotive.
Common Trade Terminology
-
OEM (Original Equipment Manufacturer)
An OEM is a company that produces parts or equipment that may be marketed by another manufacturer. In the context of CNC milling machines, buyers often deal with OEMs to ensure they receive high-quality machines and parts. Understanding OEM relationships helps buyers assess the reliability and reputation of their suppliers. -
MOQ (Minimum Order Quantity)
MOQ refers to the smallest quantity of a product that a supplier is willing to sell. This term is significant for B2B buyers as it affects budgeting and inventory management. Understanding MOQ can help businesses negotiate better terms with suppliers, especially when sourcing machines or components in bulk. -
RFQ (Request for Quotation)
An RFQ is a document that a buyer sends to suppliers to request pricing and terms for specific products or services. For international buyers, crafting a clear RFQ can facilitate better responses from suppliers, ensuring they receive competitive pricing and terms tailored to their needs. -
Incoterms (International Commercial Terms)
Incoterms are a set of predefined commercial terms published by the International Chamber of Commerce that define the responsibilities of buyers and sellers in international transactions. Familiarity with Incoterms helps buyers understand shipping costs, risk transfer, and delivery obligations, which are critical for planning and budgeting in international procurement. -
Lead Time
Lead time is the duration between placing an order and receiving the product. In the context of CNC milling machines, understanding lead times is essential for project planning and operational efficiency. Buyers should evaluate lead times when selecting suppliers to avoid delays in production schedules.
By grasping these technical properties and trade terms, international B2B buyers can make more informed decisions regarding inexpensive CNC milling machines, ultimately enhancing their procurement strategies and operational effectiveness.
Navigating Market Dynamics, Sourcing Trends, and Sustainability in the inexpensive cnc milling machine Sector
Market Overview & Key Trends
The global market for inexpensive CNC milling machines is witnessing significant growth, driven by the increasing demand for precision manufacturing across various industries, including automotive, aerospace, and electronics. B2B buyers from Africa, South America, the Middle East, and Europe are particularly influenced by the need for cost-effective solutions that do not compromise on quality. Key trends shaping this market include the rise of automation and the adoption of Industry 4.0 technologies, which are streamlining production processes and enhancing operational efficiency.
International buyers are increasingly seeking suppliers that can provide not only machines but also comprehensive support services, such as installation, training, and maintenance. The shift towards e-commerce platforms for sourcing machinery is also notable, as it allows buyers to compare products and prices more easily, enhancing transparency. Additionally, the integration of IoT in CNC machines is gaining traction, enabling real-time monitoring and predictive maintenance, which can significantly reduce downtime and improve productivity.
Regional dynamics also play a crucial role. For instance, buyers in Europe and the Middle East are often looking for suppliers with established reputations and certifications, while those in Africa and South America may prioritize affordability and flexibility in payment options. Understanding these nuances is essential for making informed purchasing decisions in this competitive landscape.
Sustainability & Ethical Sourcing in B2B
Sustainability has become a critical consideration for B2B buyers in the inexpensive CNC milling machine sector. The environmental impact of manufacturing processes, including energy consumption and waste generation, is prompting companies to seek out machines that are designed for efficiency and lower emissions. Ethical sourcing is equally important, as buyers are increasingly aware of the social implications of their supply chains.
When evaluating suppliers, look for certifications such as ISO 14001 for environmental management systems or energy-efficient labels. These certifications indicate a commitment to sustainability and can enhance a company’s reputation in the marketplace. Moreover, utilizing sustainable materials and components in CNC machines, such as recyclable metals and eco-friendly lubricants, can further minimize environmental impact.
Buyers should also consider the entire lifecycle of the machines they purchase. This includes not only the sourcing of materials but also the potential for recycling or repurposing machines at the end of their operational life. Engaging with suppliers who prioritize sustainability can create a positive brand image and align with the growing consumer demand for environmentally responsible practices.
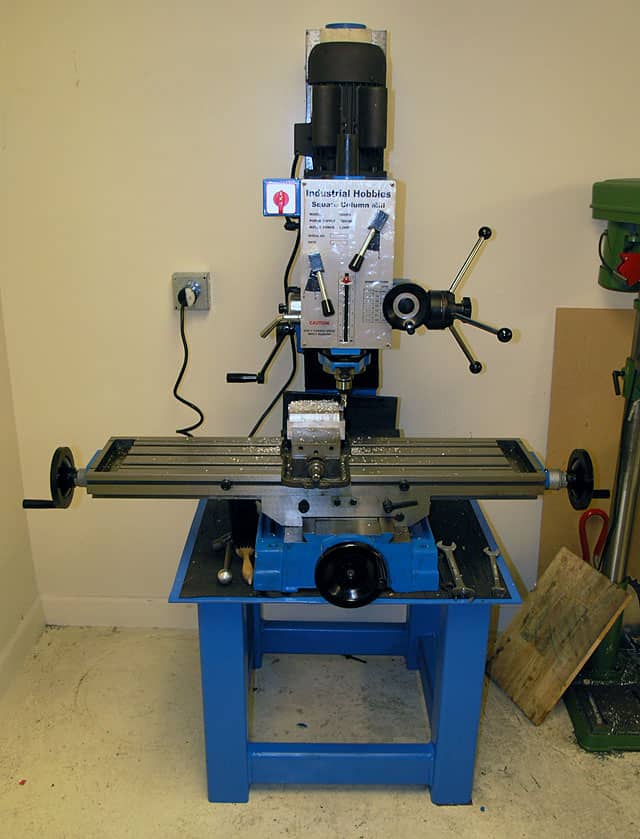
Illustrative Image (Source: Google Search)
Brief Evolution/History
The evolution of CNC milling machines has transformed from manual machining processes to highly sophisticated automated systems over the past few decades. Initially, CNC technology was primarily accessible to large manufacturers, but advancements in technology have led to the development of more affordable options suitable for small and medium-sized enterprises.
The introduction of computer-aided design (CAD) and computer-aided manufacturing (CAM) software has further revolutionized the sector, allowing for greater precision and efficiency. As global markets expand, the demand for inexpensive CNC milling machines continues to rise, driven by the need for quality manufacturing solutions across diverse industries. Understanding this evolution helps buyers appreciate the technological advancements that enhance productivity and reduce costs in today’s manufacturing landscape.
Related Video: Best CNC under $1000 – 4040 Pro Max Review
Frequently Asked Questions (FAQs) for B2B Buyers of inexpensive cnc milling machine
-
How can I effectively vet suppliers for inexpensive CNC milling machines?
When vetting suppliers, prioritize those with proven track records and credible references. Check for certifications such as ISO 9001, which indicates quality management standards. Utilize platforms like Alibaba or Global Sources to read reviews and ratings. Engage in direct communication to assess their responsiveness and willingness to provide detailed product specifications. Consider requesting samples or visiting their facilities to ensure they meet your quality standards. -
Are customization options available for inexpensive CNC milling machines?
Many suppliers offer customization options to meet specific operational needs. Before placing an order, communicate your requirements clearly, including dimensions, materials, and features. Some suppliers may have limitations on customization for lower-priced models, so be prepared to negotiate or adjust your expectations. Request a prototype or detailed design mock-up to ensure the final product aligns with your specifications. -
What should I know about minimum order quantities (MOQ) and lead times?
MOQs can vary significantly among suppliers, especially for inexpensive CNC milling machines. Some may require orders of several units to achieve cost efficiency, while others may accommodate smaller orders. Lead times are also crucial; they can range from a few weeks to several months depending on the supplier’s production capacity and your location. Always confirm these details upfront to avoid delays in your supply chain. -
How do I ensure quality assurance and certifications when sourcing CNC machines?
Request documentation that verifies compliance with international quality standards. This may include quality assurance (QA) reports and any relevant certifications. Ask for details on the supplier’s quality control processes, such as inspections during manufacturing and testing protocols. Establish a clear agreement on quality expectations and consider third-party inspection services to verify the machines before shipment. -
What are the logistics considerations when importing CNC milling machines?
Logistics can be complex when importing machinery. Evaluate shipping methods (air vs. sea) based on cost, speed, and urgency. Ensure that the supplier can handle export documentation and customs clearance. Additionally, consider the machine’s size and weight for transport. Partner with a reputable freight forwarder who understands the import regulations of your country to streamline the process. -
How can I resolve disputes with suppliers effectively?
Establish clear communication channels and document all agreements in writing to minimize misunderstandings. In the event of a dispute, try to resolve issues amicably through negotiation. If necessary, refer to the terms outlined in your purchase agreement regarding dispute resolution mechanisms, such as mediation or arbitration. Familiarize yourself with international trade laws that may apply to your transaction for better leverage in disputes. -
What payment methods are most secure when sourcing internationally?
Secure payment methods are essential for international transactions. Options such as letters of credit (LC) offer protection for both buyer and supplier, ensuring payment is only made upon fulfillment of contract terms. Consider using escrow services for added security, where funds are held by a third party until satisfactory delivery is confirmed. Be wary of suppliers demanding full upfront payments, especially if they lack a solid reputation. -
Are there any additional costs I should anticipate beyond the purchase price?
Yes, anticipate several additional costs when sourcing inexpensive CNC milling machines. These may include shipping fees, customs duties, insurance, and potential taxes upon importation. Additionally, factor in costs for installation, training, and maintenance, which can be significant for machinery. It’s advisable to request a full breakdown of potential costs from suppliers and consult with a logistics expert to avoid unexpected expenses.
Important Disclaimer & Terms of Use
⚠️ Important Disclaimer
The information provided in this guide, including content regarding manufacturers, technical specifications, and market analysis, is for informational and educational purposes only. It does not constitute professional procurement advice, financial advice, or legal advice.
While we have made every effort to ensure the accuracy and timeliness of the information, we are not responsible for any errors, omissions, or outdated information. Market conditions, company details, and technical standards are subject to change.
B2B buyers must conduct their own independent and thorough due diligence before making any purchasing decisions. This includes contacting suppliers directly, verifying certifications, requesting samples, and seeking professional consultation. The risk of relying on any information in this guide is borne solely by the reader.
Strategic Sourcing Conclusion and Outlook for inexpensive cnc milling machine
In conclusion, the strategic sourcing of inexpensive CNC milling machines presents a significant opportunity for international B2B buyers, particularly from emerging markets in Africa, South America, the Middle East, and Europe. By prioritizing cost-efficiency, quality assurance, and supplier reliability, businesses can enhance their production capabilities without compromising on performance.
Key takeaways emphasize the importance of conducting thorough market research and leveraging local partnerships to navigate supply chains effectively. Establishing a clear set of criteria for evaluating suppliers, including after-sales support and technological advancements, can lead to more informed purchasing decisions.
Looking ahead, the demand for affordable yet high-quality CNC milling machines is set to rise as industries increasingly adopt automation and precision engineering. Buyers should remain proactive in exploring innovative sourcing strategies, such as group purchasing or direct imports, to maximize their investment.
By embracing these approaches, companies can not only secure competitive pricing but also foster long-term relationships with manufacturers that align with their growth ambitions. Engage with suppliers today to position your business for success in this evolving landscape.