Improve Efficiency: The Complete Guide to Check Valves (2025)
Introduction: Navigating the Global Market for check valves
In an increasingly interconnected world, international B2B buyers face the challenge of sourcing reliable check valves that meet specific operational needs while ensuring compliance with diverse regional standards. Check valves play a crucial role in preventing backflow and maintaining system integrity across various applications, from water supply to industrial processes. This comprehensive guide aims to equip buyers with the knowledge needed to navigate the global market effectively, focusing on essential aspects such as types of check valves, their applications, supplier vetting, and cost considerations.
Understanding the nuances of check valve selection is vital for businesses in Africa, South America, the Middle East, and Europe, where varying environmental conditions and regulatory requirements can significantly impact purchasing decisions. By delving into the different types of check valves—such as inline, swing, and dual check valves—and their specific applications, buyers can make informed choices tailored to their unique operational contexts.
Moreover, this guide emphasizes the importance of supplier vetting to ensure product quality and reliability, which is paramount for avoiding costly operational disruptions. With detailed insights and actionable strategies, this resource empowers international B2B buyers to streamline their procurement processes, mitigate risks, and ultimately enhance their operational efficiency.
Understanding check valves Types and Variations
Type Name | Key Distinguishing Features | Primary B2B Applications | Brief Pros & Cons for Buyers |
---|---|---|---|
Swing Check Valve | Uses a hinged disc that swings open and closed | Water supply systems, sewage treatment | Pros: Simple design, low pressure drop. Cons: Can be affected by turbulence. |
Spring-Loaded Check Valve | Features a spring mechanism to assist closing | Industrial fluid systems, HVAC | Pros: Quick response to flow changes. Cons: More complex, higher maintenance. |
Ball Check Valve | Utilizes a ball that seals against the seat | Oil and gas pipelines, chemical processing | Pros: Excellent sealing capability. Cons: Requires higher cracking pressure. |
Diaphragm Check Valve | Employs a flexible diaphragm to control flow | Food and beverage processing, pharmaceutical systems | Pros: Good for low-pressure applications. Cons: Limited flow rates. |
Dual Plate Check Valve | Consists of two plates that open and close | Fire protection systems, water distribution networks | Pros: Compact design, low head loss. Cons: More expensive than traditional types. |
What Are the Characteristics of Swing Check Valves?
Swing check valves are characterized by their simple design, featuring a disc that swings open to allow flow and closes under back pressure. They are commonly used in water supply systems and sewage treatment plants due to their low pressure drop and reliability. When purchasing, consider the valve’s size and material compatibility with the fluids in your system, as well as the potential impact of turbulence on performance.
How Do Spring-Loaded Check Valves Function in B2B Applications?
Spring-loaded check valves utilize a spring mechanism that assists in closing the valve quickly when backflow is detected. This feature makes them ideal for industrial fluid systems and HVAC applications where rapid response to flow changes is crucial. Buyers should evaluate the spring’s durability and the valve’s ability to handle varying pressure conditions, as these factors can affect long-term performance and maintenance requirements.
What Advantages Do Ball Check Valves Offer for Industrial Use?
Ball check valves are distinguished by their use of a ball that seals against a seat to prevent backflow. They are widely used in oil and gas pipelines and chemical processing due to their excellent sealing capabilities. When considering a ball check valve, buyers should assess the required cracking pressure and ensure that the valve’s materials are suitable for the specific fluids being transported, as this can significantly impact efficiency and safety.
What Are the Benefits of Diaphragm Check Valves in Sensitive Industries?
Diaphragm check valves feature a flexible diaphragm that controls fluid flow and is particularly effective in low-pressure applications. They are commonly used in the food and beverage industry as well as pharmaceutical systems where contamination risks must be minimized. B2B buyers should focus on the valve’s material compatibility with the media and ensure that it meets industry-specific hygiene standards to avoid compliance issues.
How Do Dual Plate Check Valves Enhance System Efficiency?
Dual plate check valves consist of two plates that open and close in response to flow changes, providing a compact design that reduces head loss. They are frequently used in fire protection systems and water distribution networks. When purchasing dual plate check valves, buyers should consider the installation space available and the valve’s ability to handle the specific flow rates required for their applications, as well as any budget constraints.
Key Industrial Applications of check valves
Industry/Sector | Specific Application of Check Valves | Value/Benefit for the Business | Key Sourcing Considerations for this Application |
---|---|---|---|
Water Treatment | Backflow prevention in potable water systems | Ensures safe drinking water and compliance with regulations | Material compatibility, pressure ratings, and certifications |
Oil & Gas | Flow control in pipeline systems | Prevents contamination and protects infrastructure | Temperature resistance, sealing materials, and maintenance needs |
Chemical Processing | Preventing backflow in chemical transfer systems | Protects equipment and reduces contamination risks | Chemical compatibility, pressure ratings, and design specifics |
Agriculture | Irrigation systems and hydroponics | Maintains system efficiency and prevents water wastage | Flow rate requirements, material durability, and installation orientation |
HVAC Systems | Preventing backflow in heating and cooling systems | Enhances system efficiency and reduces maintenance costs | Size, pressure ratings, and temperature tolerance |
How Are Check Valves Used in Water Treatment Systems?
In water treatment facilities, check valves are critical for backflow prevention in potable water systems. They ensure that contaminants do not enter clean water supplies, thereby safeguarding public health. International buyers, particularly from regions like Africa and the Middle East, should focus on sourcing valves that meet local regulatory standards for potable water. Material compatibility with various water conditions and pressure ratings are essential considerations to ensure reliable performance and compliance.
What Role Do Check Valves Play in Oil & Gas Industries?
In the oil and gas sector, check valves are employed to control the flow in pipeline systems, preventing backflow that could lead to contamination or damage to infrastructure. This application is vital in maintaining the integrity of the system and ensuring operational safety. For B2B buyers in South America and Europe, sourcing valves made from materials that can withstand harsh environmental conditions and high pressures is crucial. Additionally, understanding the specific sealing materials is important to prevent leaks and ensure longevity.
How Are Check Valves Essential in Chemical Processing?
Check valves in chemical processing plants serve to prevent backflow during the transfer of hazardous materials. This is essential for protecting equipment and minimizing contamination risks. Buyers in this sector, especially in regions with stringent safety regulations, should prioritize sourcing valves that are compatible with the specific chemicals being processed. Key considerations include pressure ratings and sealing materials, as these factors will influence the valve’s performance and safety in high-risk environments.
In What Ways Do Check Valves Benefit Agricultural Applications?
In agriculture, check valves are utilized in irrigation systems and hydroponics to maintain water flow and prevent wastage. They ensure that water flows in the desired direction, contributing to efficient water use in farming practices. International buyers from Africa and South America should consider the specific flow rate requirements and durability of materials when sourcing these valves. Proper installation orientation is also crucial to maximize efficiency and prevent system failures.
How Do Check Valves Improve HVAC Systems?
Check valves are vital in HVAC systems to prevent backflow, ensuring that heating and cooling processes operate efficiently. They help maintain system pressure and reduce maintenance costs associated with system failures. B2B buyers in Europe and the Middle East should focus on sourcing check valves that meet size specifications and pressure ratings suitable for their systems. Additionally, temperature tolerance is a key factor to consider, as HVAC systems often operate under varying conditions.
3 Common User Pain Points for ‘check valves’ & Their Solutions
Scenario 1: Backflow Leading to Contamination Risks
The Problem:
One of the most pressing challenges for B2B buyers dealing with check valves is the risk of backflow, which can lead to contamination of clean water supplies or other critical fluids. In industries such as food and beverage, pharmaceuticals, or water treatment, even a small backflow event can compromise the integrity of the entire system. For instance, a manufacturing facility might find that the check valve installed is not suitable for the specific fluid type or pressure conditions, resulting in backflow and potential contamination. This not only disrupts production but also poses serious health and regulatory compliance issues.
The Solution:
To mitigate this risk, buyers should prioritize sourcing check valves designed specifically for their application. This involves understanding the fluid characteristics—such as viscosity, temperature, and chemical compatibility—and selecting a valve material that can withstand these conditions. For example, a stainless steel check valve may be ideal for high-pressure applications, while PVC check valves are more suitable for lower pressure and non-corrosive fluids.
Additionally, ensuring that the check valve has an appropriate cracking pressure is crucial. Buyers should consult with manufacturers to verify that the valve’s specifications align with the operational pressures of their systems. Regular maintenance and inspections are also essential; implementing a routine check can help identify wear and tear before it leads to catastrophic failure.
Scenario 2: Installation Errors Leading to Operational Failures
The Problem:
Improper installation of check valves is another common pain point that can lead to significant operational failures. Many B2B buyers, especially those in construction or facilities management, may encounter situations where the check valve is installed in the wrong orientation. This can prevent fluid flow, causing pressure build-up and ultimately leading to equipment failure or leaks. For example, a construction site may experience delays and additional costs if a check valve is installed backward, resulting in downtime and frustration.
The Solution:
To avoid installation errors, it is crucial for buyers to ensure that their procurement process includes detailed installation guidelines. When sourcing check valves, look for models that come with clear markings indicating the correct flow direction, as well as comprehensive installation manuals. Additionally, investing in training for installation personnel can drastically reduce errors. Buyers should consider partnering with suppliers who offer installation services or technical support, as this can provide peace of mind and ensure that the check valves function correctly from the outset.
Moreover, utilizing technology such as flow direction indicators can enhance installation accuracy. Before finalizing the installation, conducting pressure tests can help confirm that the valve is functioning as intended, allowing for immediate corrections if issues arise.
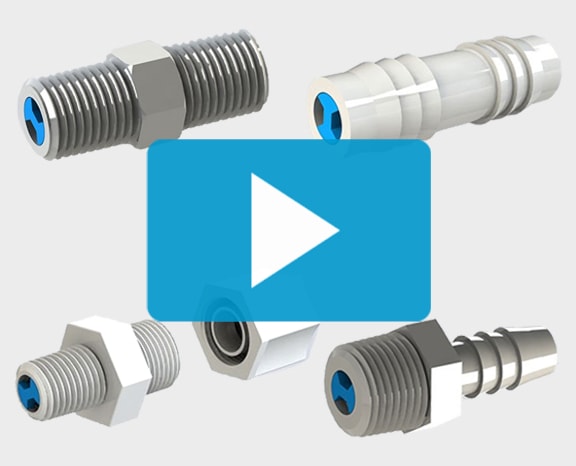
A stock image related to check valves.
Scenario 3: Inadequate Valve Selection Leading to System Inefficiencies
The Problem:
Another significant challenge for B2B buyers is selecting the wrong type of check valve for their specific application. Each type of check valve—be it swing, ball, or diaphragm—has distinct advantages and disadvantages based on the operational environment. For instance, a swing check valve may be unsuitable for applications with low flow rates, leading to inefficiencies and increased operational costs. Buyers often find themselves facing unexpected downtime and repair costs when the selected check valve fails to perform as needed.
The Solution:
To overcome this issue, buyers must engage in thorough market research and analysis before making a purchase. Understanding the specific application requirements, such as flow rate, pressure, and the type of media, is critical in selecting the appropriate valve type. Buyers should utilize resources from manufacturers that provide comparative analyses of different check valve types to inform their decision-making.
Furthermore, collaborating with industry experts or engineers during the selection process can lead to more informed choices. Considerations such as the valve’s response time, sealing mechanisms, and maintenance needs should all play a role in the selection process. Buyers should also keep an eye on product reviews and case studies that highlight performance in similar applications, ensuring that they choose a check valve that will enhance system efficiency and reliability.
Strategic Material Selection Guide for check valves
What Are the Key Properties of Common Check Valve Materials?
When selecting check valves, the choice of material significantly influences performance, durability, and compatibility with various media. Here, we analyze four common materials used in check valves: brass, stainless steel, PVC, and bronze. Each material has unique properties that cater to different applications and environments.
How Does Brass Perform in Check Valve Applications?
Brass is a popular choice for check valves due to its excellent corrosion resistance and good mechanical properties. It typically has a temperature rating of up to 200°F (93°C) and can withstand pressures of around 150 PSI.
Pros: Brass check valves are durable and resistant to rust, making them suitable for potable water applications. They are also relatively easy to manufacture and install.
Cons: However, brass can be more expensive than other materials and may not be suitable for high-temperature applications beyond its rating. Additionally, it can be susceptible to dezincification in certain corrosive environments.
Impact on Application: Brass check valves are ideal for water supply and gas applications. International buyers should consider compliance with local standards like ASTM for quality assurance.
What Are the Advantages of Stainless Steel in Check Valves?
Stainless steel check valves offer exceptional strength and corrosion resistance, making them suitable for harsh environments. They can handle temperatures up to 250°F (121°C) and pressures exceeding 300 PSI.
Pros: Their durability and resistance to a wide range of chemicals make stainless steel a preferred choice for industrial applications, including chemical processing and food and beverage industries.
Cons: The primary drawback is the higher cost compared to other materials. Stainless steel also requires more complex manufacturing processes, which can lead to longer lead times.
Impact on Application: Buyers from regions with stringent regulatory requirements, such as Europe, often prefer stainless steel for compliance with health and safety standards.
Why Choose PVC for Check Valve Applications?
PVC check valves are lightweight and cost-effective, with a typical temperature rating of up to 140°F (60°C) and a pressure rating of around 150 PSI.
Pros: They are resistant to corrosion and chemical attack, making them suitable for non-potable water applications and irrigation systems. Their low cost and ease of installation make them attractive for budget-conscious projects.
Cons: PVC is not suitable for high-temperature applications and may become brittle over time when exposed to UV light.
Impact on Application: International buyers should ensure that PVC products meet local standards for water quality and safety, particularly in agricultural applications in regions like South America and Africa.
What Role Does Bronze Play in Check Valve Design?
Bronze check valves are known for their strength and corrosion resistance, particularly in marine environments. They can handle temperatures up to 200°F (93°C) and pressures around 150 PSI.
Pros: Bronze is highly durable and resistant to seawater corrosion, making it ideal for marine applications. It also has good machinability and can be easily fabricated.
Cons: The main disadvantage is the cost, which is typically higher than brass and PVC. Bronze can also be heavy, which may complicate installation.
Impact on Application: Buyers in the Middle East, where marine applications are prevalent, should consider bronze check valves for their durability in harsh conditions.
Summary Table of Check Valve Materials
Material | Typical Use Case for check valves | Key Advantage | Key Disadvantage/Limitation | Relative Cost (Low/Med/High) |
---|---|---|---|---|
Brass | Potable water and gas applications | Good corrosion resistance | Susceptible to dezincification | Medium |
Stainless Steel | Industrial and chemical processing | Exceptional strength and durability | Higher cost and complex manufacturing | High |
PVC | Irrigation and non-potable water | Lightweight and cost-effective | Not suitable for high temperatures | Low |
Bronze | Marine applications | Highly durable and corrosion-resistant | Higher cost and heavier weight | High |
This strategic material selection guide provides international B2B buyers with crucial insights into the properties, advantages, and limitations of different check valve materials, aiding in informed purchasing decisions tailored to specific applications and regional standards.
In-depth Look: Manufacturing Processes and Quality Assurance for check valves
What Are the Key Stages in the Manufacturing Process of Check Valves?
The manufacturing process of check valves consists of several critical stages that ensure the final product meets both performance and safety standards. Understanding these stages is vital for B2B buyers looking to source high-quality check valves.
-
Material Preparation
– The first step involves selecting the appropriate materials, which can include stainless steel, brass, PVC, or bronze, depending on the application. Each material has unique properties that influence the valve’s performance, such as resistance to corrosion and temperature stability.
– After selection, materials undergo inspection to ensure they meet specified standards, including chemical composition and mechanical properties. -
Forming Techniques
– Various forming techniques are employed to shape the valve components. Common methods include casting, forging, and machining.
– Casting allows for complex shapes and is often used for large valves. Forging enhances material strength through deformation and is preferred for high-pressure applications. Machining, such as CNC (Computer Numerical Control) machining, is used for precision parts, ensuring tight tolerances. -
Assembly Process
– The assembly of check valves requires meticulous attention to detail. Components such as the body, disc, and seals are brought together, often with the aid of automation for efficiency and consistency.
– Proper alignment and fitting are crucial to prevent leaks and ensure the valve operates effectively. This stage may also include the installation of springs in spring-loaded check valves. -
Finishing Operations
– Finishing treatments enhance durability and aesthetics. Common techniques include polishing, coating, and surface treatment to improve corrosion resistance.
– Each valve may undergo pressure testing to ensure it can withstand operational conditions before moving to the quality assurance phase.
How Is Quality Assurance Implemented in Check Valve Manufacturing?
Quality assurance (QA) is a fundamental aspect of check valve manufacturing, ensuring that products meet international standards and customer expectations.
-
International Standards and Certifications
– B2B buyers should look for manufacturers that comply with international standards, such as ISO 9001, which outlines criteria for a quality management system. This certification indicates a commitment to quality and continuous improvement.
– Industry-specific certifications, such as CE marking for compliance with European safety standards or API (American Petroleum Institute) certifications for valves used in the oil and gas industry, are also essential. These certifications help guarantee product reliability and safety. -
Key Quality Control Checkpoints
– The quality control process is typically divided into several checkpoints:- Incoming Quality Control (IQC): Inspects raw materials and components upon arrival to ensure they meet specified standards.
- In-Process Quality Control (IPQC): Conducts checks during the manufacturing process to identify and rectify issues in real-time. This may involve dimensional checks and functional tests.
- Final Quality Control (FQC): A thorough examination of the finished product, including pressure testing, leakage testing, and functional testing, to ensure the valve meets operational specifications.
-
Common Testing Methods for Check Valves
– Hydraulic Testing: Measures the valve’s ability to withstand pressure without leaking.
– Functional Testing: Ensures the valve opens and closes correctly under specified conditions.
– Material Testing: Assesses the mechanical properties of materials used, such as tensile strength and ductility.
How Can B2B Buyers Verify Supplier Quality Control Processes?
B2B buyers, especially those from diverse regions like Africa, South America, the Middle East, and Europe, must take proactive steps to verify the quality control processes of potential suppliers.
-
Supplier Audits
– Conducting audits is one of the most effective ways to assess a supplier’s quality assurance practices. This can include on-site visits to observe manufacturing processes, quality control measures, and adherence to safety standards. -
Review of Quality Reports
– Requesting detailed quality reports and documentation can provide insights into the supplier’s QC processes. Look for records of previous audits, testing results, and compliance with international standards. -
Engaging Third-Party Inspection Services
– Utilizing third-party inspection services can further validate the quality of the check valves. These independent entities can provide unbiased assessments of the manufacturing and quality assurance processes, offering additional peace of mind.
What Are the Quality Control and Certification Nuances for International B2B Buyers?
Navigating quality control and certification can be complex for international buyers, particularly those sourcing from different continents.
-
Understanding Regional Standards
– Different regions have distinct standards and regulations. For instance, European buyers often prioritize CE marking, while buyers in the Middle East may focus on compliance with local regulations. Familiarizing yourself with these nuances is essential for successful procurement. -
Language and Communication Barriers
– Language differences can hinder effective communication regarding quality specifications. Establishing clear channels of communication and possibly employing local representatives can help bridge these gaps. -
Cultural Differences in Quality Expectations
– Quality perceptions can vary significantly between regions. Buyers should clarify their expectations upfront and engage in discussions about quality benchmarks to ensure alignment with suppliers.
Conclusion
Understanding the manufacturing processes and quality assurance measures for check valves is crucial for B2B buyers in international markets. By focusing on material selection, forming techniques, assembly, and finishing processes, as well as robust quality control measures, buyers can make informed decisions that align with their operational needs. Verifying suppliers through audits, quality reports, and third-party inspections can further mitigate risks and ensure that the check valves sourced meet the highest standards of quality and reliability.
Practical Sourcing Guide: A Step-by-Step Checklist for ‘check valves’
In the competitive landscape of international B2B procurement, especially in sectors reliant on fluid control systems, sourcing check valves effectively is paramount. This practical sourcing guide aims to provide a clear checklist for buyers, ensuring that you make informed decisions tailored to your specific operational needs.
Step 1: Define Your Technical Specifications
Identifying precise technical specifications is crucial for ensuring compatibility and performance. Consider factors such as:
– Material Requirements: Determine whether you need brass, stainless steel, or PVC based on the media type and operating conditions.
– Pressure and Temperature Ratings: Ensure the check valves can withstand your system’s maximum pressure and temperature to prevent failures.
Step 2: Identify Your Application Needs
Understanding the specific application of the check valve helps narrow down your choices. Different applications may require:
– Type of Check Valve: For example, inline check valves are suitable for most applications, while swing check valves may be needed for larger pipelines.
– Fluid Compatibility: Ensure the valve can handle the specific fluids (e.g., potable water, chemicals, or sewage) without risking contamination or damage.
Step 3: Evaluate Potential Suppliers
Thorough supplier evaluation is key to ensuring reliability and quality. Look for:
– Company Background: Research their experience in the industry and specific expertise in check valves.
– Customer Reviews: Seek out testimonials or case studies, particularly from companies in similar regions (like Egypt or Brazil) to gauge supplier performance.
Step 4: Verify Supplier Certifications
It’s essential to ensure that your suppliers comply with industry standards and regulations. Check for:
– Quality Certifications: Look for ISO 9001 or equivalent certifications that indicate adherence to quality management systems.
– Product Certifications: Confirm that the check valves meet specific industry standards, such as API or ASTM, especially for critical applications.
Step 5: Request Samples for Testing
Before placing a bulk order, requesting samples is vital to validate performance. Consider:
– Testing Conditions: Evaluate the samples under the same pressure and temperature conditions they will face in your operations.
– Installation Fit: Ensure the dimensions and connection types are compatible with your existing systems.
Step 6: Negotiate Terms and Pricing
Once you’ve shortlisted suppliers, it’s time to discuss terms. Focus on:
– Volume Discounts: Inquire about pricing breaks for larger orders, which can significantly reduce costs.
– Lead Times: Clarify delivery schedules to align with your project timelines, especially if operating in regions with potential supply chain challenges.
Step 7: Establish a Relationship for Future Needs
Building a long-term relationship with suppliers can lead to better service and pricing. Consider:
– Communication: Foster open lines of communication to address any issues or changes in specifications promptly.
– Feedback Loop: Provide feedback on product performance, which can help suppliers improve their offerings and strengthen your partnership.
By following this step-by-step checklist, international B2B buyers can streamline their procurement process for check valves, ensuring that they select the right products from reliable suppliers while optimizing costs and performance.
Comprehensive Cost and Pricing Analysis for check valves Sourcing
What Are the Key Cost Components for Check Valves in B2B Sourcing?
When evaluating the cost structure for sourcing check valves, several components must be considered. The primary costs typically include:
-
Materials: The choice of materials significantly impacts pricing. Common materials include brass, stainless steel, PVC, and nickel-plated bronze. Prices can vary widely based on material quality and market demand.
-
Labor: Labor costs encompass wages for workers involved in manufacturing, assembly, and quality control. Regions with lower labor costs may offer more competitive pricing.
-
Manufacturing Overhead: This includes the indirect costs associated with production, such as utilities, equipment depreciation, and facility maintenance. Efficient manufacturing processes can help keep these costs down.
-
Tooling: Custom tooling for specific valve designs can be a significant upfront investment. Buyers should weigh the long-term benefits against initial costs, especially if a high volume of valves is required.
-
Quality Control (QC): Ensuring that check valves meet industry standards and certifications incurs additional costs. Investing in rigorous QC processes can prevent costly returns and reputational damage.
-
Logistics: Shipping and handling costs can vary based on location and delivery method. Incoterms will influence these costs, as they dictate who is responsible for shipping and import duties.
-
Margin: Suppliers typically add a markup to cover their costs and profit margin. Understanding the supplier’s pricing strategy can aid in negotiations.
How Do Price Influencers Affect Check Valve Costs?
Several factors can influence the pricing of check valves, particularly for international B2B buyers:
-
Volume/MOQ (Minimum Order Quantity): Larger orders often lead to lower per-unit costs. Buyers should assess their needs and negotiate for bulk pricing if feasible.
-
Specifications and Customization: Custom valves designed for specific applications can significantly increase costs. Buyers should determine whether standard options can meet their needs to avoid unnecessary expenses.
-
Material Quality and Certifications: Higher-quality materials and valves that comply with international standards often come at a premium. Buyers should evaluate the importance of certifications based on their application requirements.
-
Supplier Factors: The reputation and reliability of the supplier can affect pricing. Established suppliers with a history of quality may charge more but offer assurance in terms of product performance and support.
-
Incoterms: Understanding the implications of different Incoterms is crucial for budgeting. Terms like FOB (Free On Board) and CIF (Cost, Insurance, Freight) can significantly alter total costs based on shipping responsibilities.
What Are Effective Buyer Tips for Negotiating Check Valve Prices?
International B2B buyers, particularly those from regions like Africa, South America, the Middle East, and Europe, should consider the following strategies for effective negotiation:
-
Total Cost of Ownership (TCO): Beyond the initial purchase price, consider the long-term costs associated with maintenance, replacement, and operational efficiency. A higher upfront cost may be justified by lower operational costs.
-
Engage in Negotiations: Be prepared to negotiate pricing, especially for large orders. Suppliers may offer discounts or better terms for bulk purchases or long-term contracts.
-
Explore Multiple Suppliers: Obtaining quotes from several suppliers can provide leverage in negotiations and help identify the most competitive pricing.
-
Stay Informed on Market Trends: Understanding market conditions, including material prices and labor costs, can enhance negotiation efforts. Buyers should keep abreast of fluctuations that could impact pricing.
-
Evaluate Payment Terms: Favorable payment terms can enhance cash flow. Buyers should negotiate terms that allow for better liquidity while maintaining good relationships with suppliers.
Disclaimer on Indicative Prices for Check Valves
Prices for check valves can vary widely based on the factors discussed. The prices mentioned in this analysis are indicative and subject to change based on market conditions, supplier pricing strategies, and regional economic factors. Buyers are encouraged to conduct thorough market research and engage directly with suppliers for the most accurate and current pricing information.
Alternatives Analysis: Comparing check valves With Other Solutions
Understanding Alternatives to Check Valves
In various industrial applications, ensuring the unidirectional flow of liquids and gases is critical. While check valves are a popular solution for preventing backflow, several alternatives exist that can serve similar functions. This section explores how check valves compare to two viable alternatives: diaphragm valves and solenoid valves. Each option has unique characteristics that may better suit specific applications based on performance, cost, and ease of implementation.
Comparison Table of Check Valves and Alternatives
Comparison Aspect | Check Valves | Diaphragm Valves | Solenoid Valves |
---|---|---|---|
Performance | Excellent at preventing backflow | Good for flow control and isolation | Fast actuation, but may not prevent backflow effectively |
Cost | Generally low to moderate cost | Moderate cost, depends on size and material | Moderate to high cost, depending on complexity |
Ease of Implementation | Simple installation with clear flow direction | Requires careful alignment; can be complex | Requires electrical connections, can complicate installation |
Maintenance | Low maintenance, but requires periodic checks | Moderate maintenance; diaphragm replacement may be needed | Low maintenance but requires electrical system checks |
Best Use Case | Water supply, sewage, and HVAC systems | Chemical processing, food and beverage applications | Automation in industrial processes, where fast actuation is needed |
What Are the Advantages and Disadvantages of Diaphragm Valves?
Diaphragm Valves are designed for flow regulation and isolation, featuring a flexible diaphragm that moves to open or close the valve.
Pros:
– Versatile Applications: They are suitable for various industries, including pharmaceuticals and food processing, where contamination prevention is critical.
– Effective Isolation: Diaphragm valves provide excellent sealing capabilities, making them ideal for applications requiring tight shutoff.
Cons:
– Higher Maintenance: The diaphragm may require periodic replacement, adding to maintenance efforts.
– Installation Complexity: Proper alignment and installation are crucial, which can complicate the setup process.
How Do Solenoid Valves Function Compared to Check Valves?
Solenoid Valves utilize an electromagnetic coil to control the flow of liquids or gases. They can open or close rapidly, making them suitable for automated systems.
Pros:
– Rapid Response: Solenoid valves can switch on and off quickly, making them ideal for applications requiring immediate flow control.
– Automation Friendly: They can be easily integrated into automated systems for precise control.
Cons:
– Electrical Dependence: Their reliance on electrical systems can complicate installation and maintenance.
– Limited Backflow Prevention: Unlike check valves, solenoid valves may not provide sufficient backflow prevention, which could lead to potential contamination issues.
How Can B2B Buyers Choose the Right Solution?
When selecting between check valves, diaphragm valves, and solenoid valves, B2B buyers should consider their specific operational needs. For applications requiring robust backflow prevention, check valves are typically the best choice. If fluid control and isolation are paramount, diaphragm valves offer versatility, especially in sensitive environments. For automated processes where rapid actuation is essential, solenoid valves may be the most effective option. Ultimately, understanding the unique requirements of your system will guide you in making an informed decision that aligns with your operational goals and budget constraints.
Essential Technical Properties and Trade Terminology for check valves
When evaluating check valves for your business needs, understanding their essential technical properties and the associated trade terminology is crucial for making informed purchasing decisions. Below are key specifications and terms that are frequently encountered in the check valve industry.
What Are the Critical Technical Properties of Check Valves?
1. Material Grade
The material of a check valve significantly impacts its durability and suitability for specific applications. Common materials include stainless steel, brass, PVC, and bronze. Each material has unique characteristics such as corrosion resistance, temperature tolerance, and pressure ratings. For instance, stainless steel check valves are ideal for high-pressure applications and environments where corrosion resistance is paramount.
2. Cracking Pressure
Cracking pressure refers to the minimum pressure differential required to open the check valve. It is essential for ensuring that the valve operates effectively within your system. Understanding the cracking pressure helps in selecting the right valve that aligns with your operational pressure requirements, thereby preventing backflow and ensuring system efficiency.
3. Maximum Working Pressure (MWP)
This specification indicates the highest pressure a check valve can withstand during operation without failure. For B2B buyers, selecting a valve with an appropriate MWP is critical to avoid leaks and potential damage to the system. It’s important to consider the operational conditions to ensure that the valve can handle the expected pressure loads.
4. Temperature Rating
Temperature ratings define the maximum and minimum temperatures at which a check valve can operate. This is particularly important for industries dealing with hot fluids or gases. Buyers must ensure that the temperature ratings of the check valves are compatible with their specific applications to avoid premature failure.
5. Connection Type
Check valves come with various connection types such as threaded, flanged, or push-fit. The connection type affects installation ease and compatibility with existing piping systems. Understanding the connection requirements is crucial for ensuring a seamless integration of the valve into your operations.
What Are Common Trade Terms in the Check Valve Industry?
1. OEM (Original Equipment Manufacturer)
An OEM is a company that produces parts or equipment that may be marketed by another manufacturer. In the check valve industry, knowing whether a supplier is an OEM can impact the quality and reliability of the valves you purchase.
2. MOQ (Minimum Order Quantity)
MOQ refers to the smallest amount of a product that a supplier is willing to sell. Understanding the MOQ is important for B2B buyers to manage inventory costs effectively and ensure that they are making a worthwhile purchase.
3. RFQ (Request for Quotation)
An RFQ is a document sent to suppliers to solicit price quotes for specific products. When dealing with check valves, issuing an RFQ allows buyers to compare prices, terms, and specifications from multiple suppliers, enabling informed decision-making.
4. Incoterms (International Commercial Terms)
Incoterms are a set of predefined international rules that clarify the responsibilities of buyers and sellers in global trade. Understanding Incoterms is vital for international B2B transactions involving check valves, as they define who pays for shipping, insurance, and customs duties.
5. Lead Time
Lead time refers to the period between placing an order and receiving the product. In the check valve industry, knowing the lead time is essential for planning and ensuring that your projects remain on schedule.
6. Backpressure
Backpressure is the pressure exerted in the opposite direction of the normal flow. For check valves, understanding backpressure is essential as it can influence the valve’s functionality and the overall system performance.
Understanding these technical properties and trade terms equips international B2B buyers with the knowledge to make strategic purchasing decisions regarding check valves. This knowledge is particularly beneficial for buyers from regions such as Africa, South America, the Middle East, and Europe, where market dynamics can vary significantly.
Navigating Market Dynamics and Sourcing Trends in the check valves Sector
What Are the Current Market Dynamics in the Check Valves Sector?
The check valves market is witnessing robust growth driven by increased industrialization and urbanization across the globe. Key sectors such as water management, oil and gas, and chemical processing are pushing the demand for reliable backflow prevention solutions. International B2B buyers, particularly from regions like Africa, South America, the Middle East, and Europe, should note that advancements in technology, such as smart valve systems and IoT integration, are becoming prevalent. These innovations enhance system efficiency and offer real-time monitoring capabilities, making them attractive for buyers looking to optimize operational performance.
Moreover, the market is experiencing a shift towards more localized sourcing due to geopolitical uncertainties and supply chain disruptions. B2B buyers should consider engaging with suppliers who offer flexible delivery options and can quickly adapt to changing market conditions. Additionally, the focus on regulatory compliance is intensifying, with manufacturers increasingly meeting international standards to ensure product reliability and safety. This evolution presents an opportunity for buyers to secure high-quality check valves that align with their operational requirements.
How Can Sustainability Impact Your Sourcing Decisions for Check Valves?
Sustainability is becoming a critical factor for international B2B buyers in the check valves sector. The environmental impact of manufacturing processes and materials used in valve production is under scrutiny, and companies that prioritize sustainability are gaining a competitive edge. Buyers should seek suppliers who demonstrate a commitment to ethical sourcing and offer products made from recyclable or eco-friendly materials.
Certifications such as ISO 14001 (Environmental Management) and Green Seal can serve as indicators of a supplier’s dedication to sustainable practices. Furthermore, the use of biodegradable or less harmful seal materials, such as EPDM or Viton, can significantly reduce the environmental footprint of check valves. By choosing suppliers who adhere to these standards, buyers can not only contribute to sustainability goals but also enhance their brand reputation in increasingly eco-conscious markets.
How Has the Check Valves Industry Evolved Over Time?
The evolution of the check valves industry is marked by significant technological advancements and shifts in material science. Initially, check valves were primarily made from traditional materials like cast iron and brass, but the introduction of high-performance plastics and composite materials has expanded application possibilities. These modern materials offer enhanced durability and corrosion resistance, making them suitable for a wider range of fluids and environments.
Historically, the primary function of check valves was to prevent backflow, but as industries evolved, so did the complexity of valve designs. Innovations such as spring-loaded and diaphragm check valves have emerged, providing greater efficiency and reliability in various applications. Today, the focus on smart technology integration, including digital monitoring and automated control, marks a new chapter in the check valves sector, catering to the evolving needs of B2B buyers looking for advanced solutions.
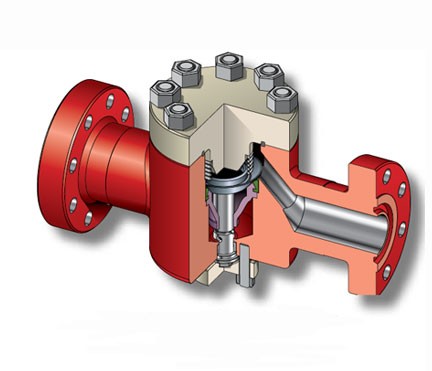
A stock image related to check valves.
In conclusion, international B2B buyers from regions such as Africa, South America, the Middle East, and Europe must stay informed about market dynamics, prioritize sustainability in sourcing decisions, and recognize the historical advancements that continue to shape the check valves sector.
Frequently Asked Questions (FAQs) for B2B Buyers of check valves
-
How do I solve issues with backflow in my system?
To prevent backflow, the installation of a check valve is essential. Check valves allow fluid to flow in only one direction, effectively blocking any reverse flow. Ensure you choose a valve with the appropriate cracking pressure for your system’s requirements. Regular maintenance and inspections can also help identify potential issues before they escalate. If backflow persists, consider consulting with a valve specialist to assess the system’s design and recommend more robust solutions, such as installing dual check valves or backflow preventers. -
What is the best check valve for high-pressure applications?
For high-pressure applications, a stainless steel or brass check valve is typically the best choice due to their superior strength and durability. Stainless steel valves can withstand higher temperatures and pressures, making them ideal for demanding environments. When selecting a valve, pay attention to its maximum pressure rating and ensure it meets or exceeds your system’s operational requirements. Additionally, consider the valve’s sealing mechanism, as a robust seal will prevent leaks under high-pressure conditions. -
How can I effectively vet suppliers for check valves?
To vet suppliers, start by assessing their industry reputation through reviews and testimonials from previous clients. Request certifications and compliance documents to ensure they meet international standards, especially for safety and quality. Evaluate their production capabilities and lead times, as well as their willingness to provide samples for testing. Engaging in direct communication can also reveal their responsiveness and customer service quality, which are crucial for a successful long-term partnership. -
What are the customization options available for check valves?
Many manufacturers offer customization options for check valves, including materials, sizes, and connection types. Depending on your specific application, you may require valves that can handle unique fluid types or environmental conditions. Discuss your needs with potential suppliers to explore available modifications, such as special coatings or seals. Custom valves may have minimum order quantities (MOQs), so be prepared to discuss your project scale and budget during negotiations. -
What are common minimum order quantities (MOQs) for check valves?
MOQs for check valves can vary significantly based on the supplier and the type of valve. Generally, for standard models, MOQs may range from 50 to 100 units, while custom valves could require larger orders. When negotiating with suppliers, inquire about their flexibility on MOQs, especially if your project demands fewer units. Some suppliers may offer bulk pricing discounts or allow for combined orders to meet MOQ requirements. -
What payment terms should I expect when sourcing check valves internationally?
Payment terms for international B2B transactions can vary widely among suppliers. Common options include advance payment, letters of credit, or payment upon delivery. It’s crucial to clarify these terms upfront and consider using secure payment methods to mitigate risks. Additionally, discuss potential payment plans for larger orders, as some suppliers may offer installment options. Always ensure that the payment terms align with your cash flow needs and project timelines.
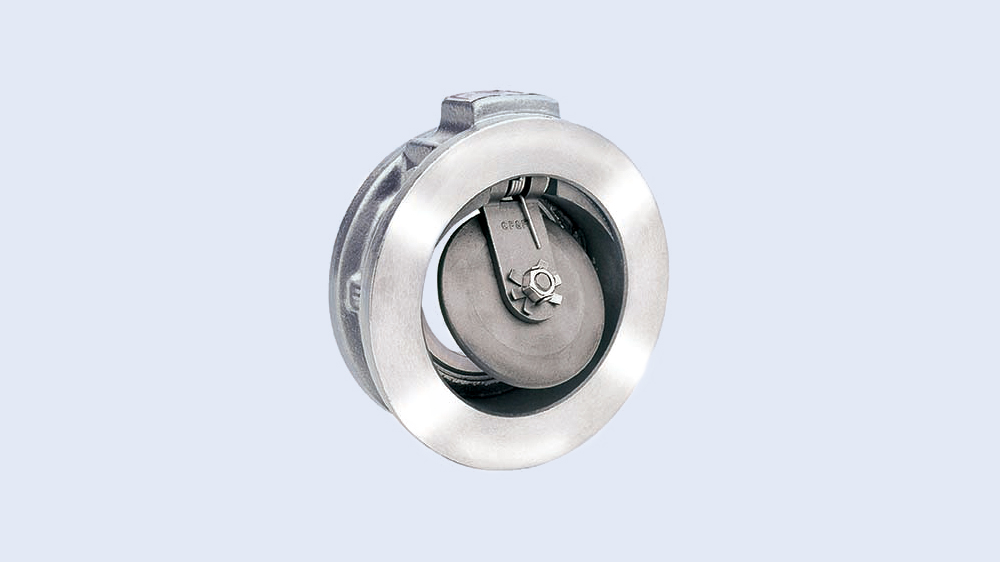
A stock image related to check valves.
-
How can I ensure quality assurance for check valves?
To ensure quality assurance, request detailed documentation from suppliers, including product specifications and compliance certifications. Many manufacturers adhere to international quality standards such as ISO 9001. Consider asking for samples before placing a large order to verify the valve’s performance in your specific application. Regular inspections during production and upon delivery can also help maintain quality control, ensuring that the valves meet your operational requirements. -
What logistics considerations should I keep in mind when sourcing check valves?
When sourcing check valves internationally, consider shipping methods, customs regulations, and lead times. Choose a logistics partner experienced in handling industrial components to ensure timely and safe delivery. Be aware of any tariffs or import duties that may apply to your order, as these can affect overall costs. Establish clear communication with your supplier regarding shipping schedules and tracking to avoid delays and ensure smooth logistics operations.
Important Disclaimer & Terms of Use
⚠️ Important Disclaimer
The information provided in this guide, including content regarding manufacturers, technical specifications, and market analysis, is for informational and educational purposes only. It does not constitute professional procurement advice, financial advice, or legal advice.
While we have made every effort to ensure the accuracy and timeliness of the information, we are not responsible for any errors, omissions, or outdated information. Market conditions, company details, and technical standards are subject to change.
B2B buyers must conduct their own independent and thorough due diligence before making any purchasing decisions. This includes contacting suppliers directly, verifying certifications, requesting samples, and seeking professional consultation. The risk of relying on any information in this guide is borne solely by the reader.
Strategic Sourcing Conclusion and Outlook for check valves
In conclusion, strategic sourcing of check valves is essential for optimizing operational efficiency and ensuring compliance with industry standards across various applications. By understanding the diverse types of check valves, including inline spring-loaded, swing, and diaphragm valves, international B2B buyers can make informed decisions tailored to their specific needs. Emphasizing the importance of material selection—ranging from brass to stainless steel—enables businesses to mitigate risks associated with backflow and system contamination, ultimately reducing maintenance costs and enhancing system reliability.
For buyers in regions such as Africa, South America, the Middle East, and Europe, leveraging local suppliers while considering global sourcing strategies can lead to cost savings and improved supply chain resilience. As industries continue to evolve, staying informed about technological advancements and regulatory changes will further empower decision-making processes.
Take proactive steps today by evaluating your current check valve suppliers and exploring new partnerships that align with your strategic goals. The future of your operations depends on the quality and reliability of your valve systems—make the smart choice for your business’s success.