Unlock Efficiency: The Complete Toggle and Latch Guide (2025)
Introduction: Navigating the Global Market for toggle and latch
Navigating the global market for toggle and latch products poses unique challenges for international B2B buyers, especially in regions like Africa, South America, the Middle East, and Europe. The complexity of sourcing high-quality toggle clamps and latches—critical components in manufacturing, construction, and various industrial applications—demands thorough understanding and strategic decision-making. This guide delves into the diverse types of toggle and latch systems available, their specific applications, and the intricacies of supplier vetting to ensure reliability and quality.
With a focus on cost considerations and market trends, this comprehensive resource aims to empower buyers to make informed purchasing decisions. By exploring factors such as clamping strength, material specifications, and compatibility with existing systems, businesses can enhance operational efficiency and product integrity. Additionally, the guide provides insights into regional suppliers, facilitating connections that align with local compliance and logistical needs.
International B2B buyers will find value in understanding the nuances of the toggle and latch market, equipping them to navigate procurement processes confidently. Whether you are a manufacturer in Nigeria seeking durable latches or a construction firm in Spain looking for reliable toggle clamps, this guide serves as an essential tool to streamline sourcing and enhance competitiveness in the global marketplace.
Understanding toggle and latch Types and Variations
Type Name | Key Distinguishing Features | Primary B2B Applications | Brief Pros & Cons for Buyers |
---|---|---|---|
Quick-Release Toggle Clamp | Fast action release mechanism, adjustable clamping | Manufacturing, woodworking, assembly lines | Pros: Speedy operation, versatile. Cons: May wear out faster with heavy use. |
Latch-Action Toggle Clamp | Secure hold with a latch mechanism, high clamping force | Heavy machinery, automotive, construction | Pros: High strength, reliable. Cons: More complex installation. |
Spring Claw Toggle Latch | Lightweight, curved spring for tension | Packaging, light-duty fastening | Pros: Simple design, cost-effective. Cons: Limited load capacity. |
U-Bolt Toggle Clamp | Adjustable U-bolt for secure attachment | Metal fabrication, heavy-duty applications | Pros: Customizable fit, robust. Cons: Requires precise alignment. |
Vertical Toggle Clamp | Vertical clamping action, space-efficient design | CNC machining, woodworking | Pros: Space-saving, effective for vertical surfaces. Cons: Limited to vertical applications. |
What Are the Characteristics of Quick-Release Toggle Clamps?
Quick-release toggle clamps are designed for efficiency, allowing users to quickly secure and release workpieces. Their adjustable clamping strength makes them suitable for various applications in manufacturing and woodworking. When purchasing, buyers should consider the clamping force required for their specific tasks, as these clamps can vary significantly in holding capacity. Additionally, their longevity can be a concern in high-frequency use scenarios, so selecting a durable model is essential.
How Do Latch-Action Toggle Clamps Differ from Other Types?
Latch-action toggle clamps provide a secure hold through a locking mechanism, making them ideal for applications that require high clamping force, such as in heavy machinery and automotive assembly. These clamps are known for their reliability and strength. Buyers should evaluate the installation complexity and the necessary adjustments for optimal performance. While they offer excellent strength, the intricate installation may require additional tools or expertise.
In Which Situations Should Spring Claw Toggle Latches Be Used?
Spring claw toggle latches are typically used for lightweight applications, such as packaging or securing lids. Their simple design and cost-effectiveness make them attractive for businesses seeking basic fastening solutions. However, their limited load capacity means they are not suitable for heavy-duty applications. B2B buyers should assess the weight and stress requirements of their projects when considering these latches.
What Advantages Do U-Bolt Toggle Clamps Offer in Heavy-Duty Applications?
U-bolt toggle clamps are particularly valuable in heavy-duty applications due to their adjustable design, allowing for a secure fit on various materials. They are commonly used in metal fabrication where robust fastening is essential. Buyers should focus on the compatibility of the clamp with their specific projects, as precise alignment is crucial for effective use. While they provide a strong hold, their adjustment may require additional time during setup.
Why Are Vertical Toggle Clamps Ideal for Space-Constrained Environments?
Vertical toggle clamps are designed to operate in tight spaces, making them ideal for CNC machining and woodworking where vertical surfaces are common. Their design allows for efficient use of space without compromising on clamping strength. When purchasing vertical clamps, buyers should consider the vertical load they will handle and ensure compatibility with their machinery or workspace. Despite their advantages, their application is limited to vertical operations, which may not suit all projects.
Key Industrial Applications of toggle and latch
Industry/Sector | Specific Application of toggle and latch | Value/Benefit for the Business | Key Sourcing Considerations for this Application |
---|---|---|---|
Manufacturing | Assembly line equipment | Enhances production speed and efficiency | Look for durable materials and appropriate clamping force. |
Transportation | Cargo securing systems | Ensures safety and stability of transported goods | Consider weight capacity and weather resistance. |
Construction | Temporary structures and scaffolding | Provides reliable support and stability | Evaluate load ratings and ease of installation. |
Automotive | Vehicle body assembly | Improves assembly precision and reduces labor costs | Focus on compatibility with vehicle specifications. |
Electronics | Enclosure fastening for electronic devices | Protects sensitive components and improves durability | Check for size compatibility and environmental ratings. |
How is Toggle and Latch Used in Manufacturing?
In the manufacturing sector, toggle and latch mechanisms are essential for assembly line equipment. They facilitate quick and secure fastening of components, allowing for rapid changes in production setups. This adaptability enhances production speed and efficiency, critical in competitive markets. International buyers must prioritize sourcing durable materials that can withstand the rigors of high-speed operations, as well as appropriate clamping force to handle varying component sizes.
What Role Do Toggle and Latch Play in Transportation?
In the transportation industry, toggle and latch systems are integral to cargo securing solutions. They provide a reliable method for fastening loads, ensuring safety and stability during transit. This is particularly crucial for international shipping, where goods are subjected to various conditions. Buyers should consider the weight capacity of the latches and their resistance to environmental factors, such as moisture and temperature fluctuations, to ensure cargo integrity.
How Are Toggle and Latch Utilized in Construction?
In construction, toggle and latch mechanisms are commonly used for securing temporary structures and scaffolding. They provide a reliable means of fastening that enhances the stability of these structures, reducing the risk of accidents. For buyers in this sector, evaluating load ratings and ease of installation is vital. These factors can significantly impact project timelines and overall safety standards on site.
How Do Toggle and Latch Improve Automotive Assembly?
Within the automotive industry, toggle and latch mechanisms are used extensively in vehicle body assembly. They enhance assembly precision, which is crucial for meeting safety regulations and quality standards. Additionally, they can reduce labor costs by allowing for faster assembly processes. Buyers should focus on sourcing latches that are compatible with specific vehicle designs and materials to ensure a seamless integration into existing manufacturing processes.
What is the Importance of Toggle and Latch in Electronics?
In the electronics sector, toggle and latch systems are essential for fastening enclosures that protect sensitive components. They ensure that devices are securely closed, enhancing durability and user safety. For international buyers, it is important to check for size compatibility and environmental ratings, as electronic devices often need to withstand various operating conditions. Selecting the right toggle and latch can significantly extend the lifespan of electronic products, making it a critical decision for manufacturers.
3 Common User Pain Points for ‘toggle and latch’ & Their Solutions
Scenario 1: Difficulty in Ensuring Consistent Clamping Pressure
The Problem:
B2B buyers often face challenges with toggle clamps that fail to maintain consistent clamping pressure, especially in high-stakes applications like manufacturing or assembly lines. This inconsistency can lead to defective products, increased rework, and potential safety hazards. Buyers may also struggle with products that do not fit their specific application needs, resulting in wasted time and resources.
The Solution:
To address this issue, buyers should prioritize sourcing toggle and latch systems that offer adjustable clamping pressure. Look for products that feature a quick-release mechanism and adjustable arms, which allow for fine-tuning the clamping force. When selecting toggle clamps, request detailed specifications regarding their holding capacity and clamping strength, ensuring they align with your application requirements. Additionally, consider investing in heavy-duty clamps for demanding environments, as these typically provide more stable and reliable performance. Regular maintenance, such as lubrication and inspection for wear, will also help sustain optimal clamping pressure over time.
Scenario 2: Challenges with Material Compatibility in Toggle and Latch Systems
The Problem:
Another common pain point for B2B buyers is the mismatch between toggle and latch materials and the environments in which they are used. For instance, in industries such as food processing or pharmaceuticals, equipment must withstand exposure to harsh chemicals or moisture. Buyers often find that standard metal clamps corrode or degrade quickly, resulting in costly replacements and downtime.
The Solution:
To mitigate material compatibility issues, buyers should opt for toggle and latch systems made from corrosion-resistant materials, such as stainless steel or specialized polymers. When sourcing these products, it’s critical to communicate your environmental conditions to suppliers, ensuring they recommend the most suitable materials. Buyers can also request samples or conduct tests in their specific environments to evaluate performance before making bulk purchases. Additionally, exploring coating options, such as zinc plating or powder coating, can enhance the longevity of toggle and latch systems in challenging conditions.
Scenario 3: Complex Installation and Adjustability Issues
The Problem:
Many B2B buyers encounter difficulties during the installation of toggle and latch mechanisms, particularly when there is a lack of clear guidelines or when products are not designed for easy integration into existing systems. Complicated installation processes can lead to delays in production and increased labor costs, which are particularly burdensome for small and medium-sized enterprises.
The Solution:
To simplify installation and adjustability, buyers should look for toggle and latch systems that come with comprehensive installation guides and customer support. It’s advisable to choose products with modular designs that allow for easy customization and adjustments post-installation. When contacting suppliers, inquire about training sessions or technical support that can assist your team during the installation phase. Additionally, consider investing in toggle and latch systems that offer user-friendly features, such as tool-free adjustments and clear marking for optimal positioning, to streamline the setup process. This proactive approach can significantly reduce installation time and enhance overall productivity.
Strategic Material Selection Guide for toggle and latch
When selecting materials for toggle and latch mechanisms, B2B buyers must consider various factors that influence performance, cost, and suitability for specific applications. The choice of material directly impacts durability, manufacturing complexity, and compliance with international standards. Below, we analyze four common materials used in toggle and latch systems, providing insights tailored for international buyers, particularly from Africa, South America, the Middle East, and Europe.
What Are the Key Properties of Steel in Toggle and Latch Applications?
Key Properties:
Steel is renowned for its strength and versatility. It typically offers high tensile strength, excellent durability, and good resistance to deformation under load. Depending on the alloy composition, steel can also exhibit varying degrees of corrosion resistance.
Pros & Cons:
The primary advantage of steel is its high load-bearing capacity, making it suitable for heavy-duty applications. However, it can be prone to rust if not properly treated or coated, which may limit its use in humid or corrosive environments. Additionally, the manufacturing process for steel components can be complex, impacting lead times and costs.
Impact on Application:
Steel toggle and latch systems are ideal for applications requiring robust locking mechanisms, such as in industrial machinery or outdoor equipment. However, buyers must ensure that the steel is treated for corrosion resistance if used in environments with moisture or chemicals.
Considerations for International Buyers:
Buyers should verify compliance with relevant standards such as ASTM A36 for structural steel. In regions with high humidity, like parts of Africa and South America, selecting stainless steel or coated options is advisable.
How Does Aluminum Compare for Toggle and Latch Systems?
Key Properties:
Aluminum is lightweight and has good corrosion resistance, particularly when anodized. It also offers moderate strength, making it suitable for applications where weight savings are critical.
Pros & Cons:
The main advantage of aluminum is its lightweight nature, which can reduce overall product weight, enhancing portability. However, it has lower tensile strength compared to steel, which may limit its use in high-stress applications. Additionally, aluminum can be more expensive than some steel options.
Impact on Application:
Aluminum toggle and latch mechanisms are often used in aerospace, automotive, and portable equipment applications where weight is a concern. They are also suitable for marine environments due to their corrosion resistance.
Considerations for International Buyers:
Buyers should consider the specific grades of aluminum, such as 6061 or 7075, which comply with international standards like DIN EN 573. In Europe, buyers should also be aware of REACH regulations regarding material safety.
What Are the Benefits of Using Plastic for Toggle and Latch Mechanisms?
Key Properties:
Plastics, especially engineering-grade thermoplastics, offer good chemical resistance and are lightweight. They can be engineered to provide specific properties, such as flexibility or rigidity.
Pros & Cons:
The key advantage of plastic is its resistance to corrosion and chemicals, making it suitable for various environments. However, plastics generally have lower mechanical strength compared to metals, which may limit their use in high-load applications. Additionally, the manufacturing process can vary in complexity depending on the type of plastic used.
Impact on Application:
Plastic toggle and latch systems are ideal for applications in the food and pharmaceutical industries, where corrosion resistance and cleanliness are paramount. They are also used in consumer products where weight and cost are significant factors.
Considerations for International Buyers:
Buyers should ensure that the selected plastics meet relevant food safety standards, such as FDA compliance in the U.S. and EU regulations for food contact materials.
How Does Stainless Steel Enhance Toggle and Latch Performance?
Key Properties:
Stainless steel combines the strength of steel with excellent corrosion resistance, making it suitable for a wide range of applications. It typically has a high tensile strength and is available in various grades, each offering different properties.
Pros & Cons:
The main advantage of stainless steel is its durability and resistance to corrosion, making it suitable for both indoor and outdoor applications. However, it is generally more expensive than carbon steel and can be more challenging to machine.
Impact on Application:
Stainless steel toggle and latch systems are widely used in marine, automotive, and food processing applications, where exposure to moisture and corrosive substances is common.
Considerations for International Buyers:
Buyers should look for compliance with international standards such as ASTM A240 for stainless steel. In regions with strict environmental regulations, such as Europe, ensuring that the stainless steel is sourced from compliant suppliers is crucial.
Summary Table of Material Selection for Toggle and Latch
Material | Typical Use Case for toggle and latch | Key Advantage | Key Disadvantage/Limitation | Relative Cost (Low/Med/High) |
---|---|---|---|---|
Steel | Heavy-duty machinery, outdoor equipment | High load-bearing capacity | Prone to rust without treatment | Medium |
Aluminum | Aerospace, automotive, portable equipment | Lightweight and corrosion-resistant | Lower tensile strength than steel | High |
Plastic | Food and pharmaceutical industries | Corrosion and chemical resistance | Lower mechanical strength | Low |
Stainless Steel | Marine, automotive, food processing | Excellent durability and corrosion resistance | Higher cost and machining complexity | High |
This strategic material selection guide provides B2B buyers with crucial insights into the properties, advantages, and limitations of various materials used in toggle and latch systems. By understanding these factors, buyers can make informed decisions that align with their specific application needs and compliance requirements.
In-depth Look: Manufacturing Processes and Quality Assurance for toggle and latch
What Are the Key Stages in the Manufacturing Process of Toggle and Latch Products?
The manufacturing of toggle and latch mechanisms involves several critical stages that ensure the final products meet the required quality and performance standards. Here are the primary stages involved:
-
Material Preparation: This initial stage involves selecting the right materials, typically high-strength steel or stainless steel for durability and corrosion resistance. The materials are cut and prepared to specific dimensions based on design specifications. This phase may include processes like shearing, sawing, or laser cutting.
-
Forming: The prepared materials are then formed into the desired shapes using various techniques. Common methods include stamping, bending, and forging. For toggle clamps, the clamping arms and bases are shaped to provide the necessary holding capacity and functionality. Precision in this stage is critical to ensure that all components fit together correctly.
-
Assembly: Once the components are formed, they are assembled. This may involve welding, riveting, or using screws and bolts to secure the parts. The assembly process must be performed with care to maintain the integrity of the toggle and latch mechanisms, ensuring they operate smoothly and safely.
-
Finishing: The final manufacturing stage includes surface treatments to enhance durability and aesthetics. Common finishing techniques include powder coating, anodizing, or plating (e.g., zinc or chrome plating). These processes not only improve the appearance but also increase resistance to wear and corrosion, which is especially important for products used in harsh environments.
What Quality Assurance Measures Are Essential for Toggle and Latch Manufacturing?
Quality assurance (QA) is a crucial component of the manufacturing process, ensuring that products meet international standards and customer expectations. Here are key elements of quality assurance for toggle and latch products:
-
International Standards Compliance: Many manufacturers adhere to ISO 9001, which specifies requirements for a quality management system (QMS). This standard helps ensure consistent quality and continuous improvement. Additionally, compliance with industry-specific certifications, such as CE marking for products sold in Europe or API standards for applications in the oil and gas sector, is essential for global market acceptance.
-
Quality Control Checkpoints: Implementing systematic checkpoints throughout the manufacturing process is vital. This includes:
– Incoming Quality Control (IQC): Evaluating raw materials upon receipt to ensure they meet specified standards.
– In-Process Quality Control (IPQC): Monitoring production processes to identify and rectify defects early.
– Final Quality Control (FQC): Conducting thorough inspections of finished products to ensure they meet all specifications before shipping. -
Testing Methods: Various testing methods are employed to verify the performance and safety of toggle and latch products. Common tests include:
– Functional Testing: Ensures the mechanism operates as intended under specified loads.
– Durability Testing: Assesses the product’s ability to withstand repeated use over time.
– Corrosion Resistance Testing: Evaluates how well the product resists environmental factors that could cause degradation.
How Can B2B Buyers Verify Supplier Quality Control Practices?
For international B2B buyers, particularly those from Africa, South America, the Middle East, and Europe, verifying the quality control practices of suppliers is critical. Here are some actionable steps:
-
Supplier Audits: Conducting on-site audits can provide insights into a supplier’s manufacturing processes and quality control measures. During the audit, buyers should assess compliance with relevant standards, observe production practices, and review documentation.
-
Quality Control Reports: Requesting detailed quality control reports can help buyers understand a supplier’s QA processes. These reports should outline testing results, defect rates, and any corrective actions taken.
-
Third-Party Inspections: Engaging third-party inspection agencies can provide an unbiased evaluation of a supplier’s products. These inspections can occur at various stages of production, ensuring adherence to quality standards before shipment.
-
Certifications and Documentation: Buyers should verify that suppliers possess relevant certifications (e.g., ISO 9001, CE) and maintain proper documentation of their QA processes. This can include quality manuals, inspection records, and compliance certificates.
What Are the Unique Quality Control Nuances for International Buyers?
International buyers face specific challenges when ensuring product quality. Here are some nuances to consider:
-
Cultural and Regulatory Differences: Understanding the local manufacturing culture and regulations in regions like Africa or South America is essential. Buyers should familiarize themselves with local standards and how they compare to international ones.
-
Language Barriers: Effective communication is crucial for quality control. Buyers may encounter language barriers that can complicate the transfer of quality standards and specifications. Utilizing bilingual staff or translators can help bridge this gap.
-
Logistical Challenges: The global supply chain can introduce logistical complexities that impact product quality. Buyers should consider how shipping methods, storage conditions, and handling can affect the integrity of toggle and latch products during transit.
-
Long-Term Partnerships: Building long-term relationships with suppliers can enhance quality assurance. Frequent communication, feedback, and collaboration on quality initiatives can lead to improved manufacturing practices and product quality over time.
Conclusion
Understanding the manufacturing processes and quality assurance measures for toggle and latch products is essential for international B2B buyers. By focusing on material preparation, forming, assembly, and finishing, alongside robust quality control practices, buyers can ensure they select reliable suppliers who deliver high-quality products. Utilizing audits, reports, and third-party inspections further empowers buyers to make informed purchasing decisions in the global marketplace.
Practical Sourcing Guide: A Step-by-Step Checklist for ‘toggle and latch’
In today’s global market, sourcing toggle and latch components requires a systematic approach to ensure quality, compliance, and value for money. This checklist is designed to guide international B2B buyers, particularly those from Africa, South America, the Middle East, and Europe, through the essential steps in procuring these crucial fastening devices.
Step 1: Define Your Technical Specifications
Establishing clear technical specifications is the foundation of successful procurement. Consider the specific requirements of your application, such as load capacity, material type (e.g., stainless steel for corrosion resistance), and size dimensions. This clarity will not only streamline communication with suppliers but also help in evaluating their product offerings against your needs.
Step 2: Research Market Trends and Standards
Understanding the latest market trends and industry standards is critical. Stay informed about innovations in toggle and latch technology, such as quick-release mechanisms or enhanced durability features. Familiarize yourself with relevant certifications and compliance standards (like ISO or CE) that may apply to your industry to ensure that the products meet safety and quality benchmarks.
Step 3: Evaluate Potential Suppliers
Before committing, it’s crucial to vet suppliers thoroughly. Look for suppliers with a strong reputation in the market, and request company profiles, case studies, and references from buyers in similar industries or regions. This due diligence will help you assess their reliability and quality of service, which is particularly important when sourcing from regions with varying manufacturing standards.
Step 4: Request Samples for Testing
Never overlook the importance of testing samples before making bulk purchases. Request samples of the toggle and latch products to evaluate their functionality, durability, and overall quality. This step is essential to confirm that the products will meet your operational requirements and can withstand the conditions they will face in use.
Step 5: Negotiate Pricing and Terms
Once you have selected potential suppliers, initiate negotiations on pricing and terms. Be transparent about your budget constraints and seek volume discounts, especially if you plan to order in bulk. Also, clarify payment terms, delivery schedules, and any warranties or return policies to protect your investment.
Step 6: Verify Shipping and Logistics Capabilities
Understanding the supplier’s shipping and logistics capabilities is vital for timely delivery. Inquire about their shipping methods, lead times, and experience with international shipping regulations, especially if you are importing to regions with specific customs requirements. Efficient logistics will ensure that you receive your toggle and latch components without unnecessary delays.
Step 7: Establish a Long-Term Relationship
Building a strong relationship with your suppliers can lead to better pricing, priority service, and access to new products. Maintain open lines of communication and provide feedback on their products and services. A collaborative approach can foster innovation and mutual growth, benefiting both parties in the long run.
By following this checklist, B2B buyers can navigate the complexities of sourcing toggle and latch components more effectively, ensuring they secure high-quality products that meet their specific needs while fostering beneficial supplier relationships.
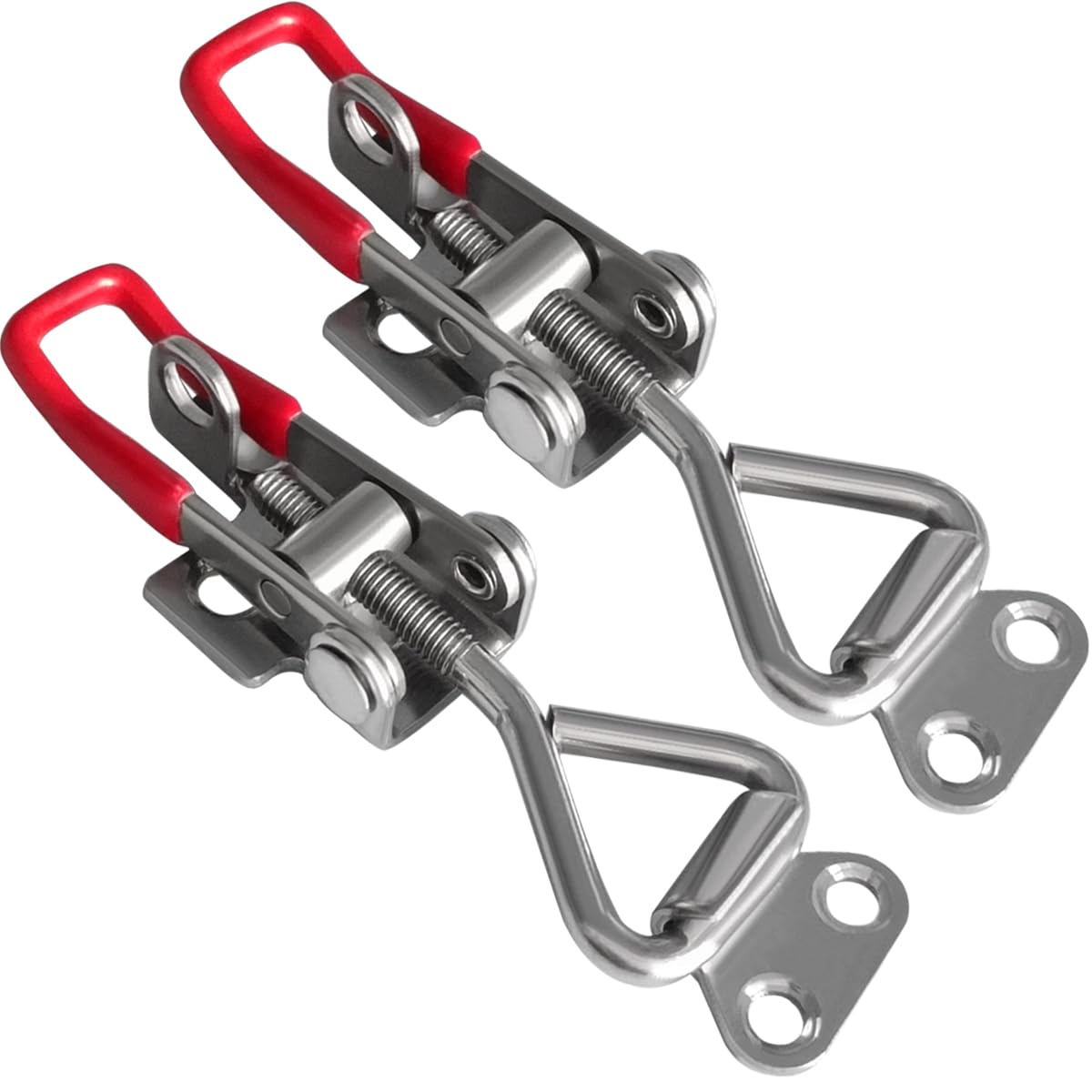
A stock image related to toggle and latch.
Comprehensive Cost and Pricing Analysis for toggle and latch Sourcing
What Are the Key Cost Components in Toggle and Latch Manufacturing?
Understanding the cost structure of toggle and latch manufacturing is crucial for B2B buyers. The primary components include:
-
Materials: The choice of materials significantly impacts costs. Stainless steel, for example, is often preferred for its durability but comes at a higher price compared to lower-grade metals or plastics. Pricing can vary based on market fluctuations and regional availability.
-
Labor: Labor costs can differ based on the geographical location of the manufacturer. For instance, labor in countries with lower wage standards may result in reduced production costs, making it an attractive option for buyers looking to optimize expenses.
-
Manufacturing Overhead: This includes indirect costs such as utilities, rent, and administrative expenses. Understanding the overhead costs associated with your supplier can help gauge their pricing strategy.
-
Tooling and Setup Costs: Custom tooling can be a significant upfront investment, especially for specialized toggle and latch designs. Buyers should inquire about tooling costs and how they affect the overall pricing for smaller order quantities.
-
Quality Control (QC): Stringent quality control processes ensure the reliability of products, but they also add to the overall cost. Certifications and testing can increase expenses, particularly if compliance with international standards is required.
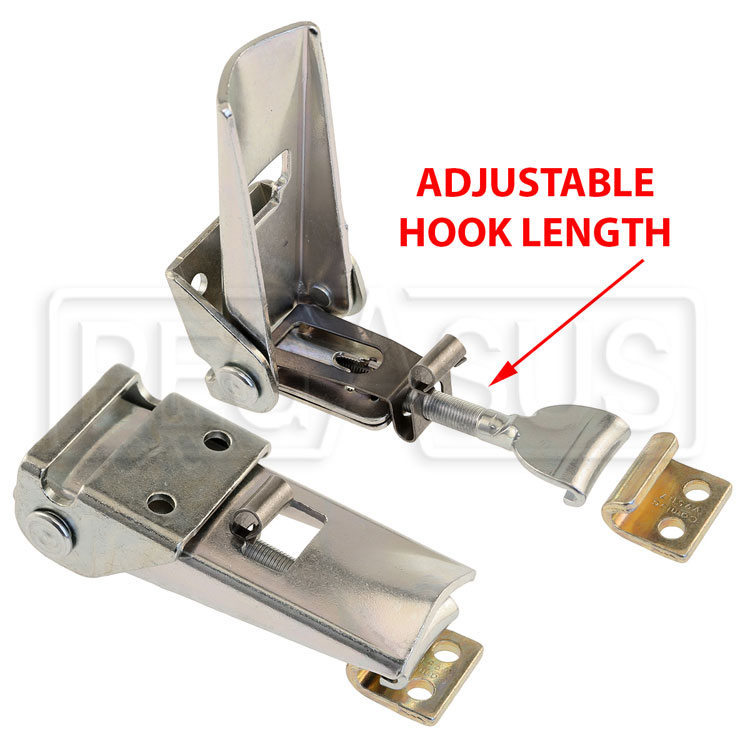
A stock image related to toggle and latch.
-
Logistics: Shipping and handling costs can vary widely based on the distance, mode of transport, and any customs duties applicable. International buyers should consider these factors when evaluating total costs.
-
Margin: Suppliers typically add a markup to cover their costs and profit margins. Understanding the typical margins in the industry can aid buyers in negotiating better prices.
How Do Price Influencers Affect Toggle and Latch Pricing?
Several factors influence pricing in the toggle and latch market:
-
Volume and Minimum Order Quantity (MOQ): Bulk orders often qualify for discounts, which can significantly reduce the per-unit cost. Buyers should evaluate their needs and consider negotiating MOQs to benefit from lower prices.
-
Specifications and Customization: Customized products usually carry a premium price due to additional design and manufacturing efforts. Buyers should weigh the need for customization against the potential cost increases.
-
Material Choices: As noted earlier, the material used affects price. Buyers should consider the balance between cost and performance when selecting materials for their toggle and latch needs.
-
Quality and Certifications: Products that meet specific industry standards or certifications may command higher prices. Buyers should assess whether these certifications are necessary for their applications.
-
Supplier Factors: The reputation and reliability of the supplier can also influence pricing. Established suppliers might offer higher prices due to their track record of quality and service, while newer suppliers may provide lower prices to build their customer base.
-
Incoterms: Understanding Incoterms is vital for international transactions. These terms define the responsibilities of buyers and sellers regarding shipping, insurance, and tariffs, which can affect the total landed cost.
What Are Effective Buyer Tips for Cost Efficiency in Toggle and Latch Sourcing?
-
Negotiate Wisely: Engage suppliers in discussions about pricing and be prepared to negotiate terms. Highlighting your potential for repeat business can strengthen your negotiating position.
-
Consider Total Cost of Ownership (TCO): Evaluate not just the purchase price but also the longevity, maintenance, and potential failure costs of toggle and latch products. Investing in higher-quality items may yield savings in the long run.
-
Research Pricing Nuances for International Sourcing: Prices can vary significantly across regions due to local market conditions and economic factors. Buyers in Africa, South America, the Middle East, and Europe should conduct thorough market research to identify competitive pricing.
-
Leverage Volume Discounts: If feasible, consolidate orders to take advantage of volume discounts. This strategy can lead to substantial savings, especially for larger projects.
-
Stay Informed About Market Trends: Keeping abreast of changes in material costs, labor rates, and global supply chain dynamics can help buyers make informed purchasing decisions.
Disclaimer on Indicative Prices
All prices mentioned in this analysis are indicative and may vary based on supplier, region, and market conditions. It is advisable for buyers to conduct their own research and obtain quotes from multiple suppliers to ensure competitive pricing.
Alternatives Analysis: Comparing toggle and latch With Other Solutions
Introduction to Alternatives for Toggle and Latch Mechanisms
In the realm of fastening solutions, toggle and latch mechanisms are prevalent for their robust performance and ease of use. However, international B2B buyers should also explore viable alternatives that may better suit their specific applications, particularly in diverse markets across Africa, South America, the Middle East, and Europe. Understanding the comparative advantages and drawbacks of various fastening methods is crucial for making informed purchasing decisions.
Comparison Table of Toggle and Latch with Alternatives
Comparison Aspect | Toggle and Latch | Pneumatic Clamps | Magnetic Locks |
---|---|---|---|
Performance | High clamping force, reliable | Fast operation, consistent | Quick access, secure locking |
Cost | Moderate, varies by strength | Higher initial investment | Low to moderate |
Ease of Implementation | Simple mechanical installation | Requires air supply setup | Easy installation, minimal parts |
Maintenance | Low maintenance, durable | Requires regular checks | Minimal maintenance |
Best Use Case | Heavy-duty applications | High-speed production | Security-sensitive environments |
Detailed Breakdown of Alternatives
Pneumatic Clamps: Are They Right for Your Application?
Pneumatic clamps utilize compressed air to provide rapid clamping action, making them ideal for high-speed production environments. Their performance is unmatched in terms of speed and consistency; however, they come with a higher initial cost due to the need for an air supply system. Maintenance is also a consideration, as regular checks are necessary to ensure optimal performance and prevent air leaks. For B2B buyers focused on efficiency and speed in manufacturing, pneumatic clamps can be a worthwhile investment.
Magnetic Locks: What Advantages Do They Offer?
Magnetic locks are gaining traction in applications requiring quick access and secure locking mechanisms. They are relatively easy to install, as they typically consist of fewer parts compared to toggle and latch systems. The cost is generally low to moderate, making them accessible for various budgets. However, magnetic locks may not provide the same level of clamping force as toggle and latch systems, making them less suitable for heavy-duty applications. For businesses prioritizing security in environments like warehouses or sensitive areas, magnetic locks can be an excellent alternative.
Conclusion: How Should B2B Buyers Choose the Right Solution?
Selecting the appropriate fastening solution hinges on understanding the specific requirements of your application. Toggle and latch mechanisms are excellent for heavy-duty tasks due to their high clamping strength and durability. However, alternatives like pneumatic clamps and magnetic locks can offer distinct advantages in speed, ease of use, and security. B2B buyers should assess factors such as performance needs, budget constraints, and maintenance capabilities to determine the best solution for their operational context. Engaging with suppliers and seeking demonstrations can further aid in making an informed choice that aligns with business goals.
Essential Technical Properties and Trade Terminology for toggle and latch
What Are the Key Technical Properties of Toggle and Latch Systems?
When considering toggle and latch systems for your projects, understanding their technical specifications is crucial. Here are some essential properties to keep in mind:
1. Material Grade
The material used in toggle and latch systems significantly affects their durability and performance. Common materials include stainless steel, aluminum, and plastic. For instance, stainless steel offers high corrosion resistance, making it ideal for outdoor applications. Buyers should assess the material grade to ensure it meets the specific environmental conditions of their operations.
2. Clamping Strength
Clamping strength indicates the maximum load a toggle clamp can securely hold. This is often measured in pounds or kilograms. Understanding this specification helps B2B buyers select clamps that can handle their specific workload, ensuring safety and efficiency in their operations. It’s advisable to choose clamps with a clamping strength that exceeds the anticipated load for added safety.
3. Throat Depth
Throat depth refers to the distance between the pivot point and the clamping face. This dimension is crucial for determining how deep a clamp can reach into a workpiece. Buyers should consider throat depth when selecting clamps for specific applications, as it affects the clamp’s ability to secure various materials effectively.
4. Jaw Width
Jaw width impacts the surface area that the clamp can grip. A wider jaw can distribute pressure more evenly and hold larger or irregularly shaped objects. This specification is particularly relevant in manufacturing and assembly operations where a secure grip is essential to prevent workpiece movement.
5. Quick Release Mechanism
A quick-release feature allows for faster operation, enabling users to secure and release workpieces efficiently. This property is especially beneficial in high-volume production environments where time savings can lead to increased productivity. Buyers should assess whether a quick-release mechanism is necessary based on their operational needs.
6. Safety Features
Many toggle and latch systems incorporate safety features such as locking mechanisms or safety catches. These features prevent accidental release and enhance user safety. Understanding the available safety options is vital for B2B buyers, especially in industries where safety is paramount.
What Are Common Trade Terms Used in Toggle and Latch Transactions?
Familiarity with industry jargon can streamline communication and negotiations. Here are several critical terms that B2B buyers should know:
1. OEM (Original Equipment Manufacturer)
An OEM refers to a company that produces components that are used in another company’s end product. Understanding OEM relationships is essential for buyers looking to source parts that integrate seamlessly into their systems.
2. MOQ (Minimum Order Quantity)
MOQ signifies the smallest quantity a supplier is willing to sell. This term is crucial for buyers, especially smaller businesses, as it directly affects inventory management and cash flow. Knowing the MOQ helps in planning purchases and avoiding overstock.
3. RFQ (Request for Quotation)
An RFQ is a document that a buyer sends to potential suppliers to request pricing and terms for specific products. This process helps buyers compare offers and negotiate better deals. It’s essential for ensuring that all relevant specifications are included to avoid miscommunication.
4. Incoterms (International Commercial Terms)
Incoterms define the responsibilities of buyers and sellers in international transactions, particularly regarding shipping and delivery. Familiarity with these terms helps buyers understand their obligations and potential liabilities, ensuring smoother transactions.
5. Lead Time
Lead time refers to the time taken from placing an order to receiving the goods. It is a critical factor in supply chain management and can affect project timelines. Understanding lead times allows buyers to plan their production schedules accordingly.
6. Certification Standards
Certification standards indicate that a product meets specific safety or quality requirements. Common certifications include ISO and ANSI. Buyers should verify that the toggle and latch systems they are considering meet relevant certification standards, ensuring reliability and compliance with industry regulations.
In conclusion, being informed about the technical properties and trade terminology related to toggle and latch systems is vital for effective purchasing decisions. By understanding these aspects, international B2B buyers can optimize their sourcing strategies and enhance operational efficiency.
Navigating Market Dynamics and Sourcing Trends in the toggle and latch Sector
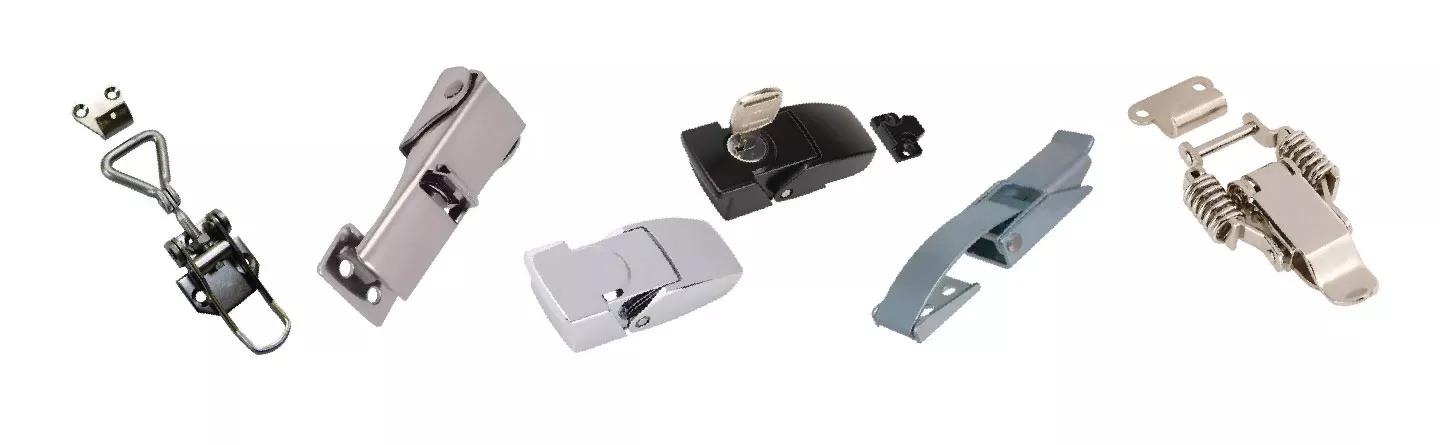
A stock image related to toggle and latch.
What Are the Key Market Dynamics and Trends in the Toggle and Latch Sector?
The toggle and latch market is witnessing significant growth driven by various global factors. Increasing demand for automation in manufacturing processes, particularly in sectors such as automotive and electronics, is pushing the need for efficient fastening solutions. Moreover, the rise in construction activities across Africa, South America, and the Middle East is leading to a greater requirement for reliable toggle and latch systems in building structures and equipment.
Current sourcing trends indicate a shift towards digital procurement platforms, which enhance transparency and efficiency in the supply chain. International B2B buyers are increasingly leveraging e-commerce platforms and digital marketplaces to access a broader range of suppliers and products, allowing for competitive pricing and improved logistics. Additionally, the advent of Industry 4.0 technologies is enhancing the production capabilities of toggle and latch manufacturers, enabling them to offer customized solutions that meet specific buyer needs.
Emerging markets, particularly in Africa and South America, are becoming focal points for toggle and latch suppliers due to rising industrialization and urbanization. Buyers from these regions should consider engaging with local suppliers to reduce lead times and shipping costs, while also exploring partnerships with manufacturers who have a strong presence in their respective markets. Understanding regional regulations and certifications is crucial for navigating these dynamics effectively.
How Is Sustainability Influencing Sourcing Decisions in the Toggle and Latch Sector?
Sustainability is becoming a pivotal consideration for B2B buyers in the toggle and latch sector. Environmental impacts of manufacturing processes, such as waste generation and energy consumption, are increasingly under scrutiny. Buyers are encouraged to prioritize suppliers that implement eco-friendly practices, such as using recycled materials and minimizing carbon footprints.
The importance of ethical supply chains cannot be overstated. Buyers should seek manufacturers who are committed to fair labor practices and responsible sourcing. Certifications such as ISO 14001 (Environmental Management) and FSC (Forest Stewardship Council) can serve as indicators of a supplier’s commitment to sustainability. Furthermore, the use of ‘green’ materials, such as biodegradable plastics or sustainably sourced metals, is gaining traction in product offerings.
For international buyers, particularly those in Europe and the Middle East, aligning sourcing strategies with sustainability goals not only enhances brand reputation but can also lead to cost savings in the long run through improved efficiencies and reduced waste.
What Is the Brief Evolution of the Toggle and Latch Sector?
The toggle and latch sector has evolved significantly over the past few decades. Initially developed for simple mechanical applications, these fastening devices have undergone substantial advancements in design and materials. With the introduction of modern manufacturing techniques and the incorporation of new materials such as stainless steel and advanced polymers, toggle and latch products are now more durable and versatile than ever.
This evolution has been driven by the demand for higher performance in diverse applications, from heavy-duty industrial uses to delicate consumer products. As industries continue to innovate, the toggle and latch sector is expected to further adapt, offering enhanced functionality and sustainability to meet the needs of international B2B buyers across various regions.
By staying informed about these market dynamics and trends, buyers can make more strategic sourcing decisions that align with their operational goals and sustainability objectives.
Frequently Asked Questions (FAQs) for B2B Buyers of toggle and latch
-
How do I choose the right toggle and latch for my application?
Choosing the right toggle and latch involves assessing your specific needs, including the weight and size of the items being secured. Consider the clamping strength required; toggle clamps can range from light-duty (under 100 lbs) to heavy-duty (over 1,000 lbs). Additionally, evaluate the material—stainless steel offers corrosion resistance for outdoor use, while carbon steel may be suitable for indoor applications. Always review the specifications and consult with suppliers to ensure compatibility with your equipment. -
What is the best type of latch for securing containers in international shipping?
For securing containers during international shipping, a heavy-duty latch, such as a latch-action toggle clamp, is ideal. These latches provide robust security and can withstand the rigors of transport. Look for features like quick-release mechanisms for efficiency and materials that resist corrosion, such as stainless steel. Ensure that the latch is compliant with international shipping regulations to avoid issues during transit. -
How can I verify the credibility of a toggle and latch supplier?
Verifying a supplier’s credibility involves multiple steps. Start by checking their business registration and certifications relevant to your region. Look for customer reviews and testimonials to gauge their reliability. Request product samples to assess quality firsthand. Additionally, inquire about their manufacturing processes and quality assurance practices. Networking with other businesses in your industry can provide valuable insights about trustworthy suppliers. -
What are the typical minimum order quantities (MOQs) for toggle and latch products?
Minimum order quantities (MOQs) can vary significantly based on the supplier and the type of toggle and latch. Generally, MOQs can range from as low as 50 units for standard products to several hundred for customized or specialized items. Discuss your needs directly with suppliers to negotiate favorable terms, especially if you are a new buyer. Some suppliers may offer flexible MOQs for initial orders to build long-term relationships. -
What payment terms should I expect when sourcing toggle and latch internationally?
Payment terms can vary widely among international suppliers, but common practices include payment in advance, net 30, or payment upon delivery. For larger orders, suppliers may accept a partial payment upfront, followed by the balance upon delivery. Ensure to clarify these terms before placing an order and consider using secure payment methods such as letters of credit or escrow services to mitigate risks associated with international transactions. -
How do I ensure quality assurance for toggle and latch products?
To ensure quality assurance, establish clear specifications and standards with your supplier before production begins. Request documentation of quality control processes, including testing and inspection protocols. Consider performing third-party inspections or audits during production or before shipment. This proactive approach helps identify potential issues early and ensures that the products meet your requirements upon arrival. -
What logistics considerations should I keep in mind when importing toggle and latch products?
When importing toggle and latch products, consider factors such as shipping methods, lead times, and customs regulations. Choose a reliable freight forwarder who understands the requirements of your destination country. Calculate shipping costs, including duties and taxes, to avoid surprises. Additionally, ensure all necessary documentation is in order, such as invoices, packing lists, and certificates of origin, to facilitate smooth customs clearance. -
Can toggle and latch products be customized to fit specific applications?
Yes, many suppliers offer customization options for toggle and latch products. Customization can include adjustments in size, material, finish, and even functionality to meet specific application needs. When discussing customization, provide detailed specifications and any relevant drawings. Be prepared for potential lead times and minimum order quantities that may apply for custom products, as these factors can vary by supplier.
Important Disclaimer & Terms of Use
⚠️ Important Disclaimer
The information provided in this guide, including content regarding manufacturers, technical specifications, and market analysis, is for informational and educational purposes only. It does not constitute professional procurement advice, financial advice, or legal advice.
While we have made every effort to ensure the accuracy and timeliness of the information, we are not responsible for any errors, omissions, or outdated information. Market conditions, company details, and technical standards are subject to change.
B2B buyers must conduct their own independent and thorough due diligence before making any purchasing decisions. This includes contacting suppliers directly, verifying certifications, requesting samples, and seeking professional consultation. The risk of relying on any information in this guide is borne solely by the reader.
Strategic Sourcing Conclusion and Outlook for toggle and latch
In the realm of toggle and latch sourcing, strategic considerations are paramount for international B2B buyers. As outlined, the diverse applications and technical specifications of these components require a thorough understanding of both market dynamics and product capabilities. The emphasis on sourcing high-quality materials, such as stainless steel for durability, and the importance of understanding clamping strength and design variations cannot be overstated.
How Can Strategic Sourcing Enhance Your Competitive Edge?
Strategic sourcing not only minimizes costs but also maximizes operational efficiency. By partnering with reputable suppliers who offer scalable solutions, businesses can ensure consistent product quality while also benefiting from bulk pricing. This is especially relevant for buyers in regions like Africa, South America, the Middle East, and Europe, where market conditions and supply chain reliability can vary significantly.
What’s Next for International B2B Buyers in Toggle and Latch Procurement?
Looking ahead, it is crucial for buyers to stay informed about evolving industry trends and emerging technologies that could influence toggle and latch applications. Engaging with suppliers who are forward-thinking and adaptive to change will provide a distinct advantage in the marketplace. As you navigate your sourcing strategy, consider reaching out to industry experts and leveraging networking opportunities to enhance your procurement process. Your proactive approach today will set the foundation for sustained success in the dynamic landscape of toggle and latch components.