Discover Seton ID Products: The Ultimate Sourcing Guide (2025)
Introduction: Navigating the Global Market for seton id products
Navigating the global market for Seton ID products can be a daunting task for international B2B buyers, especially when it comes to ensuring compliance and safety across diverse regulatory environments. As companies strive to maintain workplace efficiency and safety, sourcing high-quality identification products such as nameplates, labels, and safety signs becomes essential. This guide offers a comprehensive overview of Seton ID products, covering their various types, applications, and the best practices for supplier vetting.
With a focus on actionable insights, this resource empowers B2B buyers from Africa, South America, the Middle East, and Europe, including countries like Vietnam and Egypt, to make informed purchasing decisions. By understanding the nuances of product compliance, cost considerations, and supplier reliability, buyers can enhance their operational safety and efficiency.
Furthermore, this guide delves into the importance of proper labeling and identification in mitigating workplace hazards and improving compliance with safety regulations. Whether you are looking to streamline your procurement process or enhance your workplace safety protocols, the information presented here is tailored to support your strategic goals in the global market for Seton ID products.
How Can You Effectively Source Seton ID Products?
The key to effective sourcing lies in understanding your specific needs and aligning them with the offerings of reputable suppliers.
What Are the Different Types of Seton ID Products Available?
Explore the various categories of Seton ID products, including nameplates, labels, and safety signs, to find the best fit for your organization.
How Do Compliance Standards Affect Your Purchasing Decisions?
Knowing the compliance standards relevant to your industry can significantly influence your selection process, ensuring that your purchases meet legal requirements.
What Should You Consider When Vetting Suppliers for Seton ID Products?
Supplier vetting is crucial for establishing long-term partnerships that support your safety and identification needs, particularly in a global marketplace.
By leveraging the insights in this guide, you will be well-equipped to navigate the complexities of sourcing Seton ID products, ultimately contributing to a safer and more efficient work environment.
Understanding seton id products Types and Variations
Type Name | Key Distinguishing Features | Primary B2B Applications | Brief Pros & Cons for Buyers |
---|---|---|---|
Equipment Nameplates | Durable materials (aluminum, brass, stainless steel) | Manufacturing, construction, healthcare | Pros: Customizable; enhances safety compliance. Cons: May require installation expertise. |
Control Panel Nameplates | Identifies switches and buttons; often color-coded | Industrial control systems | Pros: Improves operational safety; enhances user experience. Cons: Limited to specific applications. |
Data Center Nameplates | Designed for high-density environments; durable | IT and data management | Pros: Essential for organization; resistant to wear. Cons: Higher cost for specialized materials. |
Safety Labels & Decals | Various materials and adhesive options; OSHA compliant | General workplace safety | Pros: Quick installation; effective communication tool. Cons: May fade over time if not UV resistant. |
Lockout/Tagout Products | Color-coded and standardized for safety compliance | Maintenance and repair sectors | Pros: Critical for safety; helps prevent accidents. Cons: Requires training for proper use. |
What Are the Key Characteristics of Equipment Nameplates?
Equipment nameplates are essential for identifying machinery and equipment within various industries. Made from durable materials like aluminum, brass, and stainless steel, these nameplates can be customized with specific information such as manufacturer details, model numbers, and serial numbers. B2B buyers should consider factors such as environmental conditions and the need for durability when purchasing. Properly affixed nameplates not only improve safety compliance but also enhance operational efficiency by reducing misidentification.
How Do Control Panel Nameplates Enhance Safety?
Control panel nameplates are designed to clearly identify switches, buttons, and controls within industrial environments. Often color-coded for easy recognition, these nameplates improve safety by reducing the risk of operator error. Businesses in sectors such as manufacturing and energy management should prioritize these products to ensure compliance with safety regulations. When selecting control panel nameplates, buyers should consider customization options and the specific needs of their operational environment.
What Are the Benefits of Data Center Nameplates?
Data center nameplates serve a crucial role in high-density environments by identifying servers, racks, and other critical equipment. Made from durable materials, these nameplates are designed to withstand harsh conditions, ensuring they remain legible over time. B2B buyers in the IT sector should focus on the durability and customization options available, as well as the ease of installation. Proper labeling in data centers enhances organization and efficiency, ultimately leading to better management of resources.
Why Are Safety Labels & Decals Important for Businesses?
Safety labels and decals are versatile tools for communicating important safety information in the workplace. Available in various materials and adhesive options, these products must often comply with OSHA regulations. B2B buyers should evaluate the longevity of the labels, especially in environments with exposure to harsh conditions. While they offer quick installation and effective communication, buyers should be aware that some labels may fade over time, necessitating periodic replacement.
How Do Lockout/Tagout Products Contribute to Workplace Safety?
Lockout/tagout products are vital for ensuring safety during maintenance and repair activities. These products are often color-coded and standardized to prevent accidental machine start-up, making them critical for compliance with safety regulations. B2B buyers in maintenance-heavy industries should invest in high-quality lockout/tagout solutions and consider the training required for proper usage. While these products significantly enhance workplace safety, the need for training can be seen as a drawback for some organizations.
Key Industrial Applications of seton id products
Industry/Sector | Specific Application of Seton ID Products | Value/Benefit for the Business | Key Sourcing Considerations for this Application |
---|---|---|---|
Manufacturing | Equipment Nameplates | Enhances safety and compliance by clearly identifying machinery. | Material durability, customization options, compliance standards. |
Construction | Safety Signs and Labels | Communicates hazards and safety protocols effectively. | Regulatory compliance, visibility, weather resistance. |
Healthcare | Asset Tags for Medical Equipment | Ensures proper tracking and maintenance of critical equipment. | RFID/barcode options, material resistance to cleaning agents. |
Warehousing | Inventory and Inspection Tags | Streamlines asset management and reduces loss. | Ease of application, durability under varying conditions. |
Transportation & Logistics | Traffic Safety Equipment and Parking Controls | Improves safety and organization in high-traffic areas. | Compliance with local regulations, visibility, and durability. |
How are Seton ID Products Used in Manufacturing?
In the manufacturing sector, Seton ID products such as equipment nameplates play a crucial role in workplace safety and operational efficiency. These nameplates provide essential information about machinery, including manufacturer details and operational guidelines, ensuring compliance with safety regulations. International buyers must consider the durability of materials, as equipment often operates in harsh environments. Customization options are also vital to meet specific branding and regulatory requirements, especially in regions like Africa and South America where local compliance standards may vary.
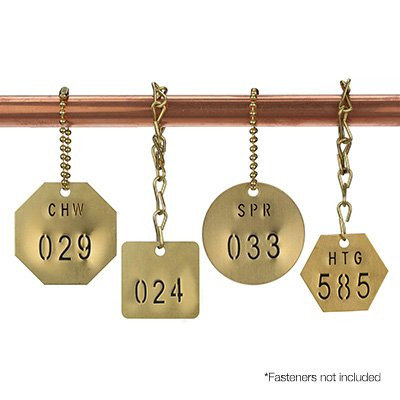
A stock image related to seton id products.
What Role do Seton ID Products Play in Construction Safety?
Seton ID products are indispensable in the construction industry, particularly through the use of safety signs and labels. These products communicate potential hazards and safety protocols, helping to mitigate risks on construction sites. For B2B buyers, sourcing products that comply with local regulations is essential to avoid legal issues. Additionally, the visibility and weather resistance of these signs are critical, as they need to withstand outdoor conditions common in regions such as the Middle East and Europe.
How are Seton ID Products Beneficial in Healthcare Settings?
In healthcare, asset tags are vital for tracking medical equipment, ensuring that all devices are maintained and available when needed. Seton’s asset tags can be customized with RFID or barcode options, which facilitate efficient inventory management and compliance with safety standards. Buyers in this sector should prioritize materials that resist cleaning agents and harsh sanitizers, as healthcare environments require stringent hygiene protocols. This is particularly relevant for international buyers in diverse markets, such as Egypt and South America, where healthcare regulations may differ.
Why are Seton ID Products Important for Warehousing Operations?
For warehousing, inventory and inspection tags from Seton are essential tools for efficient asset management. These tags help businesses track inventory levels, monitor equipment conditions, and reduce losses, ultimately enhancing operational efficiency. Buyers should consider the ease of application and the durability of these tags, as they must withstand various environmental conditions typical in warehouses. This is especially important for international buyers who may face different logistical challenges in regions like Africa and South America.
How Do Seton ID Products Enhance Safety in Transportation & Logistics?
In the transportation and logistics sectors, Seton’s traffic safety equipment and parking controls are crucial for maintaining order and safety in high-traffic areas. These products help manage pedestrian and vehicle flow, reducing the risk of accidents. When sourcing these products, businesses should ensure compliance with local traffic regulations and focus on visibility and durability, particularly in regions with diverse weather patterns, such as Europe and the Middle East. Proper sourcing can significantly enhance safety and efficiency, leading to better operational outcomes.
3 Common User Pain Points for ‘seton id products’ & Their Solutions
Scenario 1: Navigating Compliance Challenges with Seton ID Products
The Problem:
International B2B buyers often grapple with the complexities of compliance regulations that vary across regions. For example, a manufacturing company in Egypt may struggle to ensure their workplace safety signage meets both local regulations and international standards like OSHA or ANSI. Failure to comply can lead to fines, increased liability, and even workplace accidents, which can be devastating for business operations and employee safety.
The Solution:
To address compliance challenges effectively, buyers should first familiarize themselves with the specific regulations that apply in their region. Seton ID products are designed to meet various compliance standards, so sourcing products that clearly state their adherence to OSHA or ANSI can simplify this process. Utilize Seton’s Resource Center for guides tailored to compliance requirements in your industry. Moreover, when ordering, consider consulting with Seton’s OSHA-trained specialists, who can provide insights into the specific products required for your business. This ensures that you are not only meeting compliance but also fostering a safe work environment.
Scenario 2: Ensuring Durability in Harsh Environments
The Problem:
B2B buyers often face the issue of product durability when selecting identification products for harsh environments, such as those found in the construction or manufacturing sectors. For instance, a company in South America may require nameplates that can withstand extreme temperatures, humidity, or exposure to chemicals. Many standard products may fade, corrode, or break down, leading to costly replacements and potential safety hazards.
The Solution:
To combat durability issues, it’s essential to select Seton ID products specifically designed for harsh conditions. For example, buyers should opt for nameplates made from materials such as stainless steel or high-grade plastics that are resistant to corrosion and environmental stressors. In addition, review product specifications for durability ratings and ensure they are suitable for your specific use case. Engaging with Seton’s customer service team can also help identify the most appropriate materials and coatings for your needs. By proactively selecting durable products, businesses can minimize replacement costs and maintain safety standards.
Scenario 3: Streamlining Asset Tracking with Seton ID Products
The Problem:
Efficient asset tracking is a significant concern for many international B2B buyers, particularly those operating in large facilities or warehouses. A company in the Middle East may struggle to keep track of valuable equipment, leading to inefficiencies, misplaced tools, and increased operational costs. Without effective labeling and identification systems, monitoring inventory becomes an overwhelming task.
The Solution:
To streamline asset tracking, buyers should implement Seton’s comprehensive range of asset tagging solutions, which include RFID tags, barcode labels, and customizable nameplates. Start by conducting an inventory audit to determine the specific tagging needs of your assets. Then, leverage Seton’s asset tag buyer’s guide to select the most suitable products for your operational context. Additionally, consider integrating a digital asset management system that works in tandem with the physical tags. This integration can provide real-time tracking and updates on asset locations and conditions. By utilizing effective identification solutions, businesses can enhance efficiency, reduce loss, and improve overall asset management practices.
Strategic Material Selection Guide for seton id products
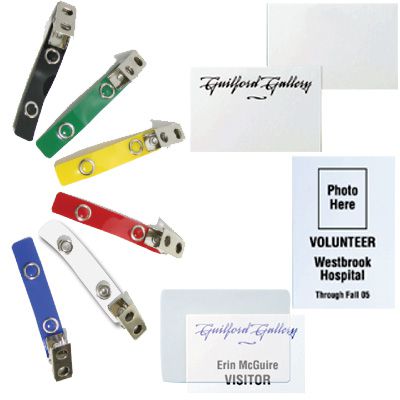
A stock image related to seton id products.
When selecting materials for Seton ID products, it’s crucial to consider the specific requirements of your application, including environmental conditions, compliance standards, and budget constraints. Below, we analyze four common materials used in Seton ID products, focusing on their properties, advantages, disadvantages, and considerations for international buyers.
What are the Key Properties of Aluminum for Seton ID Products?
Aluminum is a lightweight metal known for its excellent corrosion resistance and good thermal conductivity. It typically has a temperature rating up to 150°C (302°F) and can withstand moderate pressure levels. Its natural oxide layer provides a barrier against corrosion, making it suitable for various environments.
Pros: Aluminum is durable, lightweight, and cost-effective. It can be easily machined and customized, allowing for intricate designs and engravings.
Cons: While aluminum is resistant to corrosion, it may not perform well in highly acidic or alkaline environments. Additionally, it can be more expensive than plastic options.
Impact on Application: Aluminum is ideal for outdoor applications where exposure to moisture and UV light is common. It is compatible with various media, including water and oils, but may not be suitable for aggressive chemicals.
Considerations for International Buyers: Buyers from regions like Africa and the Middle East should ensure compliance with local environmental regulations and standards, such as ASTM and DIN. The lightweight nature of aluminum also reduces shipping costs, making it a favorable option for international procurement.
How Does Stainless Steel Compare for Seton ID Products?
Stainless steel is renowned for its exceptional strength and corrosion resistance, making it a popular choice for industrial applications. It can withstand high temperatures (up to 800°C or 1472°F) and is highly resistant to rust and other forms of corrosion.
Pros: Its durability and aesthetic appeal make stainless steel suitable for high-end applications. It is also easy to clean, which is essential in industries like healthcare and food processing.
Cons: The cost of stainless steel is generally higher than other materials, and it can be more challenging to machine. Additionally, it may not be suitable for environments with extreme chemical exposure.
Impact on Application: Stainless steel is ideal for environments that require high hygiene standards, such as hospitals and food processing plants. It is compatible with a wide range of media, including corrosive substances.
Considerations for International Buyers: Compliance with international standards such as JIS and ASTM is crucial, especially in regulated industries. Buyers in Europe may prefer stainless steel due to its perceived quality and durability.
What Advantages Does Plastic Offer for Seton ID Products?
Plastic is a versatile material used in various Seton ID products, offering a range of properties depending on the type of plastic used (e.g., PVC, polycarbonate). It typically has a temperature rating of up to 80°C (176°F) and is resistant to many chemicals.
Pros: Plastic is lightweight, cost-effective, and easy to manufacture. It can be produced in various colors and finishes, making it suitable for branding and aesthetic purposes.
Cons: Plastic may not be as durable as metal options and can degrade under UV exposure unless treated. Its temperature and pressure ratings are lower, limiting its use in high-stress environments.
Impact on Application: Plastic is suitable for indoor applications and environments where chemical exposure is minimal. It is often used for labeling and signage in warehouses and offices.
Considerations for International Buyers: Buyers should check for compliance with local safety standards and regulations. In regions like South America, where cost is a significant factor, plastic may be the preferred choice for budget-conscious buyers.
How Does Brass Perform in Seton ID Products?
Brass is an alloy of copper and zinc, known for its attractive appearance and good machinability. It has a temperature rating similar to that of aluminum, typically around 150°C (302°F), and offers moderate corrosion resistance.
Pros: Brass is aesthetically pleasing and can be easily engraved or stamped, making it suitable for decorative applications. It is also relatively resistant to corrosion in non-harsh environments.
Cons: Brass can tarnish over time and may require maintenance to maintain its appearance. It is also more expensive than plastic and aluminum.
Impact on Application: Brass is often used for nameplates and decorative labels in environments where appearance matters, such as hotels and upscale retail spaces.
Considerations for International Buyers: Compliance with local regulations regarding metal use is essential. Buyers in Europe may favor brass for its aesthetic qualities, while those in Africa might consider the cost implications.
Summary Table of Material Selection for Seton ID Products
Material | Typical Use Case for Seton ID Products | Key Advantage | Key Disadvantage/Limitation | Relative Cost (Low/Med/High) |
---|---|---|---|---|
Aluminum | Outdoor signage and labels | Lightweight and corrosion-resistant | Limited chemical resistance | Medium |
Stainless Steel | Industrial and healthcare applications | High strength and durability | Higher cost and machining difficulty | High |
Plastic | Indoor labeling and signage | Cost-effective and versatile | Lower durability and UV sensitivity | Low |
Brass | Decorative nameplates and labels | Aesthetic appeal and machinability | Tarnishing and maintenance required | Medium to High |
This strategic material selection guide provides international B2B buyers with insights into the various materials used in Seton ID products, helping them make informed purchasing decisions based on their specific needs and regional considerations.
In-depth Look: Manufacturing Processes and Quality Assurance for seton id products
What Are the Main Stages in the Manufacturing Process of Seton ID Products?
The manufacturing process for Seton ID products involves several critical stages, ensuring that each product meets high standards of quality and compliance. The main stages include:
-
Material Preparation: The first step involves sourcing high-quality raw materials such as aluminum, brass, stainless steel, and various plastics. Suppliers must adhere to international standards for material quality. This stage may include processes like cutting and shaping the raw materials into appropriate sizes for further processing.
-
Forming: After preparation, materials undergo forming processes which may include stamping, engraving, or printing. Advanced technology, such as laser cutting and digital printing, is often employed to ensure precision and clarity in the final product. This stage is crucial for ensuring that the identification products can withstand environmental challenges and maintain legibility over time.
-
Assembly: Depending on the product, the assembly stage may involve affixing labels, tags, or nameplates to equipment or packaging. This stage can also include the integration of additional features like QR codes or barcodes for tracking and inventory purposes. Attention to detail during assembly is essential to ensure that all components are securely attached and function as intended.
-
Finishing: The final stage involves applying protective coatings or treatments to enhance durability and resistance to harsh conditions. This may include anodizing metal products or applying weather-resistant finishes to labels. The finishing process is vital for products that will be exposed to outdoor conditions or extreme environments.
How Is Quality Assurance Implemented in Seton ID Product Manufacturing?
Quality assurance (QA) is integral to the manufacturing of Seton ID products, ensuring compliance with international standards and industry-specific regulations. Here are the key aspects of the QA process:
-
Adherence to International Standards: Seton ID products often comply with ISO 9001, which emphasizes a quality management system that improves customer satisfaction and operational efficiency. Additionally, products may need to meet industry-specific certifications such as CE marking for European markets or API standards for the oil and gas industry.
-
Quality Control Checkpoints: The quality control process involves several checkpoints throughout the manufacturing process:
– Incoming Quality Control (IQC): Raw materials are inspected upon arrival to ensure they meet specified standards.
– In-Process Quality Control (IPQC): Ongoing inspections occur during manufacturing to identify any deviations from quality standards.
– Final Quality Control (FQC): Finished products undergo rigorous testing and inspection to verify that they meet all specifications before shipment. -
Common Testing Methods: Various testing methods are employed, including:
– Visual Inspections: Checking for defects in appearance, such as scratches or misprints.
– Dimensional Testing: Using calipers and gauges to ensure that products meet specified dimensions.
– Environmental Testing: Assessing the durability of products under various conditions, such as temperature extremes or exposure to chemicals.
How Can B2B Buyers Verify Supplier Quality Control?
For B2B buyers, especially those in Africa, South America, the Middle East, and Europe, verifying a supplier’s quality control processes is essential for ensuring that the products meet their needs. Here are some actionable steps:
-
Conduct Supplier Audits: Request on-site audits of the manufacturing facility to assess the quality control processes firsthand. During these audits, buyers can evaluate the entire production line, from material sourcing to final quality checks.
-
Review Quality Control Reports: Ask suppliers for detailed quality control reports, including results from IQC, IPQC, and FQC. These reports should outline any issues encountered during production and the measures taken to rectify them.
-
Engage Third-Party Inspection Services: Consider hiring independent third-party inspection services to conduct assessments of the manufacturing processes and final products. This adds an extra layer of assurance regarding compliance and quality.
What Are the Quality Control and Certification Nuances for International Buyers?
When sourcing Seton ID products, international buyers should be aware of specific nuances related to quality control and certification:
-
Understanding Regional Standards: Different regions may have distinct quality and safety standards. For example, products sold in Europe must comply with CE marking requirements, while those in the U.S. may need to meet OSHA regulations. Familiarizing oneself with these regulations is crucial.
-
Documentation Requirements: Buyers should ensure that suppliers provide all necessary documentation, including certificates of compliance, test reports, and warranties. This documentation is often required for customs clearance and regulatory compliance in the buyer’s home country.
-
Language and Communication Barriers: When dealing with suppliers from different regions, communication can pose challenges. It’s advisable to have bilingual representatives or use translation services to ensure clarity in specifications and requirements.
-
Cultural Sensitivity: Understanding cultural differences in business practices can facilitate smoother negotiations and partnerships. Being aware of local customs and practices can enhance collaboration and foster better relationships with suppliers.
Conclusion
In summary, the manufacturing processes and quality assurance protocols for Seton ID products are designed to ensure high standards of safety, compliance, and performance. By understanding these processes and actively verifying supplier quality control measures, B2B buyers can make informed purchasing decisions that contribute to a safer and more efficient workplace. This diligence not only enhances operational efficiency but also fosters long-term partnerships with reliable suppliers across the globe.
Practical Sourcing Guide: A Step-by-Step Checklist for ‘seton id products’
In today’s global marketplace, sourcing high-quality Seton ID products is essential for enhancing workplace safety and efficiency. This step-by-step checklist will guide international B2B buyers, particularly from Africa, South America, the Middle East, and Europe, through the procurement process, ensuring they make informed decisions.
Step 1: Identify Your Specific Needs
Before initiating the sourcing process, clearly define your requirements for Seton ID products. Consider what types of identification solutions you need, such as nameplates, labels, or safety signs. Understanding your specific needs helps in narrowing down suppliers who can meet those criteria.
- Types of Products: Determine whether you need customized solutions or standard products.
- Volume Requirements: Assess the quantity needed for your operations to facilitate bulk purchasing.
Step 2: Research Suppliers and Manufacturers
Conduct thorough research to find reputable suppliers of Seton ID products. Utilize online resources, trade directories, and industry forums to compile a list of potential vendors.
- Reputation Matters: Look for suppliers with positive reviews and a proven track record in your industry.
- Product Range: Ensure the supplier offers a comprehensive range of ID products that align with your requirements.
Step 3: Evaluate Supplier Certifications and Compliance
Verify that potential suppliers hold necessary certifications and comply with industry standards. This step is crucial for ensuring the quality and safety of the products you are sourcing.
- Certifications to Look For: Check for ISO certifications, OSHA compliance, and any relevant local safety standards.
- Product Testing: Inquire about their product testing processes to confirm durability and safety.
Step 4: Request Samples and Product Specifications
Before finalizing any orders, request samples of the products you are interested in. This allows you to assess quality firsthand and ensure that the items meet your specifications.
- Quality Assessment: Examine the samples for durability, material quality, and clarity of labeling.
- Customization Options: Discuss customization possibilities for nameplates or labels to ensure they fit your branding needs.
Step 5: Compare Pricing and Terms
Once you have shortlisted suppliers, compare pricing and terms of service. While cost is a significant factor, also consider the total value offered by each supplier.
- Bulk Discounts: Inquire about volume discounts or loyalty programs that could reduce overall costs.
- Payment Terms: Assess the payment terms and delivery timelines to ensure they align with your budget and project timelines.
Step 6: Review Customer Support and Service
Evaluate the level of customer support each supplier provides. Strong customer service can be invaluable, especially when dealing with complex orders or customization needs.
- Response Times: Test their responsiveness by asking questions about products or services.
- After-Sales Support: Inquire about their policies on returns, warranties, and technical support.
Step 7: Finalize Your Purchase Order
After conducting due diligence and gathering all necessary information, proceed to finalize your purchase order. Ensure that all specifications, pricing, and delivery terms are clearly outlined in the contract.
- Document Everything: Keep records of communications and agreements for future reference.
- Set Clear Expectations: Confirm delivery timelines and follow up on the order status regularly to avoid delays.
By following this practical sourcing guide, international B2B buyers can efficiently navigate the procurement process for Seton ID products, ensuring they enhance safety and compliance in their workplaces.
Comprehensive Cost and Pricing Analysis for seton id products Sourcing
What Are the Key Cost Components in Seton ID Products Sourcing?
When sourcing Seton ID products, understanding the cost structure is essential for making informed purchasing decisions. The main components influencing the overall cost include:
-
Materials: The choice of materials significantly impacts the pricing of ID products. For instance, aluminum and stainless steel are more expensive than plastic but offer greater durability and longevity, which may reduce replacement costs over time.
-
Labor: Labor costs vary by region and can affect the final pricing of products. In regions with higher labor costs, such as Europe, you might see a premium on products compared to those sourced from countries with lower labor expenses.
-
Manufacturing Overhead: This includes costs related to facilities, utilities, and administrative expenses associated with production. Efficient manufacturing processes can help reduce these overhead costs, allowing suppliers to offer more competitive pricing.
-
Tooling: Custom tooling is often required for specific products, particularly those that are customized. This upfront investment can lead to higher initial costs but can be amortized over larger production runs.
-
Quality Control (QC): Rigorous quality control processes ensure product reliability and compliance with safety standards. While adding to costs, effective QC can prevent costly recalls and enhance customer satisfaction.
-
Logistics: Shipping and handling costs must be considered, especially for international buyers. Factors like distance, shipping method, and customs duties can significantly influence total costs.
-
Margin: Suppliers typically add a margin to cover their costs and ensure profitability. Understanding the margin expectations of different suppliers can aid in negotiations.
What Influences Pricing for Seton ID Products?
Several factors influence the pricing of Seton ID products, particularly for international B2B buyers:
-
Volume and Minimum Order Quantity (MOQ): Higher order volumes generally lead to lower per-unit costs due to economies of scale. It’s advisable to inquire about MOQs and consider aggregating orders with other businesses to meet these thresholds.
-
Specifications and Customization: Customized products, such as unique labeling or branding, typically incur additional costs. Be clear about your specifications upfront to avoid unexpected expenses later.
-
Material Selection: The choice of materials can significantly affect pricing. High-performance materials may come at a premium but can offer long-term savings through durability.
-
Quality Certifications: Products that meet specific safety and compliance certifications, such as OSHA or ANSI, may cost more initially but can reduce liability and enhance workplace safety.
-
Supplier Factors: Supplier reputation, reliability, and customer service can impact pricing. Established suppliers like Seton may offer premium prices due to their reputation for quality and service.
-
Incoterms: Understanding Incoterms is crucial for international transactions. These terms define the responsibilities of buyers and sellers concerning shipping, insurance, and tariffs, which can affect overall costs.
What Tips Can Help International Buyers Optimize Costs?
For international B2B buyers, particularly those in Africa, South America, the Middle East, and Europe, here are some actionable tips to optimize sourcing costs:
-
Negotiate Pricing: Don’t hesitate to negotiate prices, especially for larger orders. Suppliers may offer discounts or better terms based on your purchasing volume.
-
Consider Total Cost of Ownership (TCO): Evaluate the long-term costs associated with a product, including maintenance, durability, and replacement frequency. A higher upfront cost may lead to lower TCO if the product lasts longer.
-
Understand Pricing Nuances: Be aware that pricing can vary significantly based on region and market conditions. Conduct market research to identify competitive pricing and ensure you’re not overpaying.
-
Plan for Logistics Costs: Factor in shipping costs and potential delays. Understanding your logistics options and costs can help you make better purchasing decisions and avoid surprises.
-
Leverage Online Resources: Utilize online resources and product catalogs to compare prices and specifications. Seton’s resource center offers valuable insights and guides that can aid in the decision-making process.
Disclaimer
Prices for Seton ID products can vary widely based on the factors discussed above. It is advisable for buyers to request quotes and conduct thorough research to ensure they receive the best value for their investments.
Alternatives Analysis: Comparing seton id products With Other Solutions
When evaluating workplace safety and identification solutions, businesses often seek alternatives to established products like Seton ID products. Understanding the strengths and weaknesses of various options can help international B2B buyers make informed decisions that align with their specific operational needs and compliance requirements.
Comparison Table of Seton ID Products and Alternatives
Comparison Aspect | Seton ID Products | Alternative 1: RFID Tags | Alternative 2: Custom Engraved Plates |
---|---|---|---|
Performance | High durability and compliance | Excellent for tracking and data | Good for static identification |
Cost | Moderate cost per unit | Higher initial investment | Generally lower cost per unit |
Ease of Implementation | Straightforward installation | Requires integration with systems | Simple to install |
Maintenance | Minimal maintenance required | Requires regular system updates | Low maintenance, durable |
Best Use Case | Comprehensive safety and identification | Asset tracking in dynamic environments | Permanent identification in fixed locations |
What Are the Benefits and Drawbacks of RFID Tags as an Alternative?
RFID (Radio Frequency Identification) tags offer significant advantages, particularly in environments where real-time tracking and data management are crucial. They can automate inventory management, enhancing efficiency in warehouses and manufacturing settings. However, the initial investment for RFID systems can be high, as they require specialized readers and software integration. Additionally, regular updates and maintenance of the system are necessary to ensure optimal performance, which might not be feasible for all companies, especially small and medium enterprises.
How Do Custom Engraved Plates Compare?
Custom engraved plates provide a cost-effective solution for permanent identification needs, such as labeling machinery or equipment. They can be made from various materials, ensuring durability and resistance to environmental factors. The installation process is straightforward, making them accessible for a wide range of users. However, their static nature means they are less suitable for environments where asset tracking is needed, as they do not provide real-time updates or tracking capabilities. They are best used in settings where long-term identification is required without frequent changes.
Conclusion: How Can International B2B Buyers Choose the Right Solution?
For international B2B buyers from regions like Africa, South America, the Middle East, and Europe, selecting the right identification solution hinges on understanding specific operational needs. If your business requires robust compliance and safety measures, Seton ID products may be the best fit. Alternatively, for dynamic tracking environments, RFID tags can offer substantial efficiency gains, albeit at a higher initial cost. If the focus is on long-lasting and low-cost identification, custom engraved plates could be the ideal choice. Ultimately, a thorough assessment of performance, cost, ease of implementation, and maintenance requirements will guide buyers in making the most suitable decision for their unique business context.
Essential Technical Properties and Trade Terminology for seton id products
What Are the Essential Technical Properties of Seton ID Products?
When evaluating Seton ID products, understanding their technical properties is crucial for making informed purchasing decisions. Here are some key specifications:
-
Material Grade
– Definition: The type of material used in manufacturing, such as aluminum, brass, stainless steel, or plastic.
– Importance: Different materials offer varying durability, corrosion resistance, and weight. For example, stainless steel is ideal for outdoor applications due to its resistance to rust, while plastic may be more suitable for indoor use where cost is a concern. -
Tolerance
– Definition: The allowable deviation from a specified dimension in the manufacturing process.
– Importance: Tighter tolerances ensure that components fit together correctly, which is critical for safety and functionality. In environments where precision is vital, such as manufacturing or healthcare, selecting products with the appropriate tolerance can prevent operational disruptions. -
Durability Rating
– Definition: A measure of how well a product withstands wear and tear, often tested against environmental conditions.
– Importance: A high durability rating indicates that the product can endure harsh conditions, such as extreme temperatures or exposure to chemicals. For B2B buyers in industries like construction or manufacturing, this ensures longevity and reduces replacement costs. -
Customization Options
– Definition: The ability to alter design features, such as size, color, or text, to meet specific needs.
– Importance: Customization allows businesses to tailor products to their branding or operational requirements. For instance, a company may want its logo on safety signage to enhance brand visibility while ensuring compliance with safety standards. -
Compliance Standards
– Definition: Adherence to regulations set by organizations like OSHA (Occupational Safety and Health Administration) or ANSI (American National Standards Institute).
– Importance: Compliance ensures that products meet safety and quality benchmarks, which is essential for legal protection and employee safety. B2B buyers must verify that the products they purchase conform to relevant standards in their regions.
What Are the Common Trade Terminology Terms for Seton ID Products?
Understanding industry jargon is vital for effective communication and negotiation in B2B transactions. Here are some common terms:
-
OEM (Original Equipment Manufacturer)
– Definition: A company that produces parts or equipment that may be marketed by another manufacturer.
– Importance: Recognizing OEMs helps buyers identify reliable sources for high-quality products that can be integrated into their operations. -
MOQ (Minimum Order Quantity)
– Definition: The smallest quantity of a product that a supplier is willing to sell.
– Importance: Knowing the MOQ is essential for budget planning and inventory management. Buyers must assess whether they can meet these minimums without overcommitting resources. -
RFQ (Request for Quotation)
– Definition: A document issued by a buyer to solicit price quotations from suppliers for specific products or services.
– Importance: An RFQ allows buyers to compare pricing, terms, and conditions from multiple suppliers, facilitating better decision-making and cost management. -
Incoterms (International Commercial Terms)
– Definition: A series of predefined commercial terms published by the International Chamber of Commerce, defining the responsibilities of buyers and sellers in international transactions.
– Importance: Familiarity with Incoterms helps buyers understand shipping costs, risks, and responsibilities, ensuring clarity in cross-border transactions. -
Lead Time
– Definition: The amount of time it takes from placing an order to receiving the product.
– Importance: Understanding lead times is crucial for inventory planning and meeting operational deadlines. Buyers should consider lead times when assessing suppliers to avoid delays in production or service delivery.
By grasping these technical properties and trade terminologies, international B2B buyers can make informed decisions regarding Seton ID products that align with their operational needs and compliance requirements.
Navigating Market Dynamics and Sourcing Trends in the seton id products Sector
What Are the Current Market Dynamics and Key Trends for Seton ID Products?
The Seton ID products sector is experiencing dynamic shifts driven by globalization, technological advancements, and heightened safety regulations. International B2B buyers, particularly from Africa, South America, the Middle East, and Europe, must navigate a landscape characterized by increasing demand for workplace safety solutions and compliance with local and international safety standards. In regions like Egypt and Vietnam, businesses are prioritizing investments in safety signage, asset tagging, and identification products to enhance workplace safety and operational efficiency.
Emerging trends indicate a growing reliance on digital solutions, such as RFID and IoT technologies, for asset tracking and management. These technologies not only streamline operations but also provide real-time data that can inform decision-making processes. Additionally, the rise of e-commerce platforms has transformed sourcing strategies, enabling buyers to access a broader range of suppliers and products with ease. This shift is particularly beneficial for buyers in developing regions, as it opens up global markets and competitive pricing.
Moreover, the emphasis on compliance with regulations such as OSHA in the U.S. and local equivalents in other regions has prompted businesses to seek out suppliers that can provide compliant products. The focus on innovative solutions, such as custom products tailored to specific operational needs, is also on the rise, reflecting a market that values flexibility and responsiveness to unique challenges.
How Is Sustainability Influencing Sourcing Practices for Seton ID Products?
Sustainability has become a cornerstone of B2B sourcing practices in the Seton ID products sector. The environmental impact of manufacturing processes and materials is increasingly under scrutiny from both regulators and consumers. International buyers are now more aware of the importance of ethical supply chains and are actively seeking suppliers that prioritize sustainable practices. This includes the use of eco-friendly materials, reduction of waste in production, and adherence to environmental certifications.
Buyers should consider products that feature ‘green’ certifications, such as LEED or ISO 14001, as these can provide assurances regarding the environmental responsibility of the manufacturing processes. For example, many Seton ID products can be sourced using recyclable materials or produced through processes that minimize carbon footprints. Additionally, transparency in sourcing and manufacturing practices is crucial; suppliers that can demonstrate their commitment to sustainability are more likely to build trust and foster long-term partnerships.
Furthermore, ethical sourcing not only benefits the environment but also enhances brand reputation. Companies that prioritize sustainability can differentiate themselves in competitive markets, appealing to a growing segment of eco-conscious consumers and businesses. As such, B2B buyers in Africa, South America, the Middle East, and Europe should incorporate sustainability as a key criterion in their sourcing strategies.
What Is the Historical Context of Seton ID Products?
Seton has established itself as a leader in the identification and safety products sector since its inception in 1956. Originally focused on workplace safety solutions, the company has evolved alongside changing market demands and technological advancements. Over the decades, Seton has expanded its product offerings to include a comprehensive range of safety signs, labels, tags, and custom solutions that cater to various industries, including manufacturing, healthcare, and education.
This evolution reflects broader trends in workplace safety and compliance, as organizations increasingly recognize the importance of maintaining safe environments for their employees. The company’s commitment to innovation and customer service has allowed it to adapt to the needs of a diverse global market, positioning Seton as a trusted partner for international B2B buyers seeking reliable identification products. As safety regulations continue to evolve, Seton remains at the forefront of providing solutions that not only meet compliance requirements but also enhance operational efficiency.
Frequently Asked Questions (FAQs) for B2B Buyers of seton id products
-
How do I solve compliance issues with Seton ID products?
To address compliance issues when sourcing Seton ID products, start by understanding the specific regulations applicable in your region, such as OSHA in the U.S. or local health and safety laws in Africa, South America, the Middle East, and Europe. Review the compliance certifications of the products you are considering, ensuring they meet your local standards. Consulting with Seton’s customer service team, which includes OSHA-trained specialists, can provide tailored advice to ensure your selections align with legal requirements. -
What is the best way to customize Seton ID products for my business needs?
The best way to customize Seton ID products is to leverage their online customization tools, which allow you to choose materials, sizes, colors, and add text or logos. Consider your specific requirements, such as durability for outdoor use or compliance with specific industry standards. Engaging directly with Seton’s customer service can also yield insights into recommended customizations that enhance both safety and brand visibility, ensuring that the final product meets your operational needs. -
What are the minimum order quantities (MOQ) for Seton ID products?
Minimum order quantities for Seton ID products can vary based on the type of product and customization options. Generally, standard products have lower MOQs, while custom items may require larger quantities to ensure cost-effectiveness. It’s advisable to check directly with Seton or their authorized distributors for specific MOQs related to the products you are interested in, especially if you’re considering bulk purchases for larger projects. -
What payment terms can I expect when purchasing Seton ID products internationally?
Payment terms for international purchases of Seton ID products typically include options such as credit card payments, wire transfers, and sometimes letters of credit for larger transactions. The exact terms can vary based on the order size and the buyer’s credit history. It’s essential to clarify payment options during the quotation process, ensuring that you understand any potential fees associated with currency exchange or international transactions. -
How can I ensure quality assurance when sourcing Seton ID products?
To ensure quality assurance when sourcing Seton ID products, request product samples to evaluate material quality and durability before placing a larger order. Additionally, inquire about Seton’s quality control processes, including certifications and adherence to industry standards. Engaging with other customers or seeking testimonials can provide insights into the reliability of their products, helping you make informed purchasing decisions. -
What logistics considerations should I keep in mind when importing Seton ID products?
When importing Seton ID products, consider shipping methods, lead times, and customs regulations specific to your country. Work with a logistics provider familiar with international shipping to navigate potential tariffs, import duties, and documentation requirements. Establishing clear communication with Seton regarding delivery timelines and shipping options will also help mitigate delays and ensure a smooth import process. -
How do I vet suppliers for Seton ID products to ensure reliability?
To vet suppliers of Seton ID products, research their reputation through customer reviews, industry certifications, and years of experience in the market. Request references from previous clients and assess their responsiveness to inquiries. Additionally, verify their compliance with international trade regulations and consider visiting their facilities if possible. Establishing a strong relationship with a reputable supplier can lead to better service and product reliability. -
What are the benefits of using Seton ID products for workplace safety?
Using Seton ID products significantly enhances workplace safety by providing clear identification and communication of hazards, equipment, and safety protocols. Their products are designed to meet compliance standards, reducing liability risks. Moreover, effective labeling and signage help in streamlining operations and improving employee awareness, which can lead to fewer accidents and injuries, ultimately fostering a safer and more productive work environment.
Important Disclaimer & Terms of Use
⚠️ Important Disclaimer
The information provided in this guide, including content regarding manufacturers, technical specifications, and market analysis, is for informational and educational purposes only. It does not constitute professional procurement advice, financial advice, or legal advice.
While we have made every effort to ensure the accuracy and timeliness of the information, we are not responsible for any errors, omissions, or outdated information. Market conditions, company details, and technical standards are subject to change.
B2B buyers must conduct their own independent and thorough due diligence before making any purchasing decisions. This includes contacting suppliers directly, verifying certifications, requesting samples, and seeking professional consultation. The risk of relying on any information in this guide is borne solely by the reader.
Strategic Sourcing Conclusion and Outlook for seton id products
What Are the Key Takeaways for Strategic Sourcing of Seton ID Products?
In summary, strategic sourcing of Seton ID products offers substantial benefits for businesses aiming to enhance workplace safety and compliance. By investing in high-quality identification solutions such as nameplates, safety signs, and asset tags, companies can improve operational efficiency while ensuring adherence to industry regulations. The diverse range of products available allows for customization to meet specific needs across various sectors, including manufacturing, healthcare, and construction.
How Can International B2B Buyers Leverage Seton Products for Competitive Advantage?
For international B2B buyers in regions like Africa, South America, the Middle East, and Europe, the emphasis on quality and compliance cannot be overstated. Prioritizing strategic sourcing from reputable suppliers such as Seton not only enhances workplace safety but also fortifies the brand’s reputation. By leveraging the expertise of Seton’s OSHA-trained specialists and utilizing their resource center, buyers can make informed decisions that align with local regulations and international standards.
What Does the Future Hold for Seton ID Products?
Looking ahead, the demand for innovative safety solutions will continue to rise as businesses increasingly recognize the importance of a safe working environment. By proactively sourcing Seton ID products, companies can stay ahead of regulatory changes and industry trends. Engage with Seton today to explore tailored solutions that will not only meet your compliance needs but also drive your business toward greater safety and efficiency.