Enhance Quality: The Ultimate Welding Table Guide (2025)
Introduction: Navigating the Global Market for welding table
Navigating the global market for welding tables poses unique challenges for international B2B buyers, especially those in Africa, South America, the Middle East, and Europe. With a myriad of options available, sourcing the right welding table can be daunting. Buyers must consider factors such as durability, functionality, and compliance with local regulations. This guide aims to streamline your purchasing process by providing a detailed exploration of the various types of welding tables, their specific applications across different industries, and essential tips for supplier vetting.
Our comprehensive resource delves into the intricacies of welding tables, from portable options for fieldwork to heavy-duty models for industrial use. By understanding these categories and their applications, B2B buyers can make informed decisions that align with their operational needs. Additionally, this guide emphasizes the importance of evaluating potential suppliers, ensuring they meet quality standards and offer competitive pricing.
What sets this guide apart is its focus on empowering you—international B2B buyers—by equipping you with actionable insights that enhance your procurement strategies. By addressing critical questions about cost, quality, and supplier reliability, we aim to facilitate smoother transactions and foster successful partnerships. Whether you’re in the manufacturing sector or involved in construction, this guide will serve as your go-to resource for navigating the global market for welding tables effectively.
Understanding Search Intent for ‘welding table’
When users search for **”welding table”**, Google’s results indicate a strong **informational intent**. This means users are primarily looking to learn and understand the topic. They want definitions, explanations, and foundational knowledge about ‘welding table’.
Our analysis of the search engine results page (SERP) reveals several key features that shape this article:
* **Presence of Video Content:** No.
* **Shopping Ad Integration:** No.
* **’People Also Ask’ Questions:** We found 0 relevant user questions, which we have directly addressed in our FAQ and other sections to resolve common user queries.
This data-driven approach ensures our content directly matches what users are looking for, providing a more professional and helpful resource.
Understanding welding table Types and Variations
Type Name | Key Distinguishing Features | Primary B2B Applications | Brief Pros & Cons for Buyers |
---|---|---|---|
Fixed Welding Table | Sturdy construction, non-adjustable height | Heavy fabrication, assembly work | Pros: Durable, stable; Cons: Limited flexibility in height adjustment. |
Adjustable Welding Table | Height and angle adjustments available | Custom fabrication, diverse projects | Pros: Versatile, ergonomic; Cons: Generally higher cost. |
Portable Welding Table | Lightweight, easy to transport | On-site projects, maintenance work | Pros: Mobility, convenience; Cons: May lack stability for heavy tasks. |
Modular Welding Table | Interchangeable components, customizable layout | Complex assembly lines, specialized tasks | Pros: Highly adaptable; Cons: Can be expensive to set up. |
CNC Welding Table | Integrated computer controls for precision | Automated welding, mass production | Pros: High accuracy, efficiency; Cons: Requires training and software investment. |
What Are the Characteristics of Fixed Welding Tables?
Fixed welding tables are designed for stability and durability, making them ideal for heavy-duty applications. These tables typically have a non-adjustable height and are constructed from robust materials like steel, ensuring they can withstand the rigors of welding operations. B2B buyers should consider the fixed nature of these tables, as they are best suited for environments where the height and position do not need frequent adjustments. Their reliability makes them a staple in industries focused on heavy fabrication and assembly work.
How Do Adjustable Welding Tables Enhance Versatility?
Adjustable welding tables offer the flexibility of height and angle adjustments, catering to a wide range of welding tasks. This adaptability is crucial for B2B buyers involved in custom fabrication, where varying project requirements necessitate different working heights. The ergonomic design can help reduce worker fatigue, enhancing productivity. However, buyers should weigh the benefits of versatility against the generally higher costs associated with these tables, especially if their operations require frequent adjustments.
Why Choose Portable Welding Tables for On-Site Work?
Portable welding tables are lightweight and designed for mobility, making them ideal for on-site welding projects and maintenance work. B2B buyers in sectors such as construction and repair will find these tables advantageous due to their ease of transport. While they provide convenience, it is important to note that they may lack the stability required for heavy-duty tasks. Buyers should assess their specific needs to determine if the trade-off between mobility and stability aligns with their operational requirements.
What Are the Benefits of Modular Welding Tables?
Modular welding tables feature interchangeable components that allow for a customizable layout, making them suitable for complex assembly lines and specialized tasks. B2B buyers can benefit from these tables as they can be adjusted to fit various project specifications. However, the initial investment can be higher due to the need for multiple components. Businesses should evaluate their production processes and the potential return on investment when considering modular welding tables.
How Do CNC Welding Tables Improve Efficiency and Precision?
CNC (Computer Numerical Control) welding tables integrate advanced technology to provide high precision and efficiency in automated welding applications. These tables are particularly beneficial for mass production environments where consistency and accuracy are critical. B2B buyers should consider the upfront costs associated with CNC technology, including training and software investments, but the long-term gains in productivity and reduced error rates can justify the expense. Businesses focused on high-volume production will find CNC welding tables to be a valuable asset.
Related Video: What are Transformer Models and how do they work?
Key Industrial Applications of welding table
Industry/Sector | Specific Application of Welding Table | Value/Benefit for the Business | Key Sourcing Considerations for this Application |
---|---|---|---|
Manufacturing | Fabrication of metal components | Increases precision and efficiency in production | Consider load capacity, adjustability, and material quality |
Automotive | Assembly of vehicle frames and parts | Reduces assembly time and enhances structural integrity | Look for modular designs and compatibility with tools |
Construction | Structural steel fabrication | Provides a stable work surface for large components | Ensure surface area and height can accommodate large pieces |
Aerospace | Production of aircraft components | Meets strict safety and quality standards | Verify compliance with industry certifications and standards |
Shipbuilding | Welding of hulls and large structures | Improves workflow and minimizes rework | Assess durability and resistance to environmental factors |
How is a Welding Table Used in Manufacturing?
In the manufacturing sector, welding tables are crucial for the fabrication of metal components. These tables provide a stable and adjustable platform that enhances precision during the welding process. By allowing for the secure positioning of materials, they help reduce errors and minimize waste, which is vital in a competitive market. International buyers should prioritize tables that offer high load capacities and robust construction to withstand the demands of heavy-duty applications.
What Role Does a Welding Table Play in the Automotive Industry?
In the automotive industry, welding tables facilitate the assembly of vehicle frames and parts. These tables allow for better alignment and fitting of components, significantly reducing assembly time and improving overall structural integrity. For buyers in regions like Europe and South America, sourcing tables that are modular and compatible with various tools can enhance operational efficiency and adaptability in production lines.
How Do Welding Tables Benefit the Construction Sector?
Welding tables are essential in the construction sector, particularly for structural steel fabrication. They provide a stable surface for working on large components, which is crucial for ensuring accuracy and safety. Buyers should consider the size and height of the welding tables to accommodate various steel pieces and ensure they meet the specific demands of large-scale projects, especially in the Middle East where construction activity is booming.
Why are Welding Tables Important in Aerospace Manufacturing?
In aerospace manufacturing, welding tables are used for the production of aircraft components where adherence to safety and quality standards is paramount. These tables not only support complex assemblies but also ensure that welding processes are executed with precision. International buyers must verify that the welding tables comply with industry certifications, as this can significantly impact product safety and performance.
What Applications Do Welding Tables Have in Shipbuilding?
In shipbuilding, welding tables are utilized for the welding of hulls and other large structures. These tables enhance workflow by providing a solid base for welding tasks, which helps to minimize rework and improve efficiency. Buyers in Africa and Europe should assess the durability of the welding tables and their resistance to environmental factors such as corrosion, which is critical in maritime applications.
Related Video: frame welding fixture – (weld jig / welding table) – 4300 (english)
3 Common User Pain Points for ‘welding table’ & Their Solutions
Scenario 1: Inconsistent Work Surface Levels
The Problem: Many B2B buyers encounter the challenge of inconsistent surface levels when using welding tables. This issue can arise due to variations in table height or the presence of warping over time. Such inconsistencies not only lead to inaccurate welds but also pose safety risks to workers, as they might have to adjust their positions frequently, resulting in fatigue and potential injuries.
The Solution: To mitigate these problems, it is crucial to invest in high-quality, adjustable welding tables that feature leveling feet. This allows for precise adjustments even on uneven floors commonly found in industrial settings. When sourcing welding tables, buyers should look for features such as a robust frame construction and a flat, machined surface. Additionally, establishing a regular maintenance routine to check for warping can prolong the life of the table and ensure a consistent working environment. Investing in a table with a warranty can also provide peace of mind, knowing that any manufacturing defects can be addressed promptly.
Scenario 2: Limited Versatility in Welding Applications
The Problem: A common pain point for B2B buyers is the lack of versatility in welding tables, which restricts their use for various types of welding projects. For instance, tables designed solely for MIG welding may not provide the necessary features for TIG welding, leading to inefficiencies and the need for multiple sets of equipment. This limitation can result in increased operational costs and wasted time as teams transition between different tasks.
The Solution: Buyers should prioritize multi-functional welding tables that can accommodate diverse welding processes. Look for tables that offer adjustable work surfaces or modular attachments, such as clamps and fixtures, to secure different materials. When evaluating options, consider tables with integrated features like built-in fume extraction systems and tool storage, which enhance productivity and safety. Furthermore, collaborating with suppliers who can customize tables based on specific operational needs can provide a significant advantage, allowing businesses to streamline their processes and reduce the need for additional equipment.
Scenario 3: Difficulty in Ensuring Safety and Compliance Standards
The Problem: Safety is a paramount concern in welding operations, and many B2B buyers face challenges in ensuring their welding tables meet industry safety standards. In regions such as Africa and the Middle East, where regulations may vary widely, navigating compliance can be daunting. Non-compliance not only risks legal ramifications but can also lead to severe accidents, impacting worker safety and company reputation.
The Solution: To address this issue, it is essential for buyers to thoroughly research and understand the safety standards applicable in their regions. When sourcing welding tables, look for those certified by recognized industry standards, such as ISO or CE certifications. Additionally, incorporating safety features like anti-static surfaces, proper grounding, and fire-resistant materials can significantly enhance workplace safety. Regular training sessions for staff on the proper usage of welding tables and compliance protocols can further ensure adherence to safety standards. Building relationships with local suppliers who understand the regional regulations can also help streamline the compliance process, ensuring that all equipment used is up to standard and safe for daily operations.
Strategic Material Selection Guide for welding table
When selecting materials for welding tables, international B2B buyers must consider various factors, including the material’s properties, suitability for specific applications, and compliance with regional standards. Below is a detailed analysis of four common materials used in welding tables: steel, aluminum, cast iron, and composite materials.
What Are the Key Properties of Steel for Welding Tables?
Steel is the most widely used material for welding tables due to its excellent strength and durability. Key properties include high-temperature resistance, making it suitable for various welding processes. Steel can withstand significant pressure and is resistant to deformation under heavy loads. However, it is prone to corrosion if not properly treated or maintained.
Pros & Cons of Steel Welding Tables:
Steel tables offer exceptional durability and can be manufactured to meet specific dimensions and load capacities. They are often more cost-effective than other materials, making them a popular choice. On the downside, they can be heavy and require additional handling equipment. Corrosion resistance can be a concern, especially in humid or corrosive environments, necessitating protective coatings.
How Does Aluminum Compare as a Material for Welding Tables?
Aluminum is gaining popularity for welding tables, especially in industries where weight is a critical factor. It has a lower density than steel, making it easier to transport and manipulate. Aluminum also has good corrosion resistance, which is advantageous in outdoor or humid environments.
Pros & Cons of Aluminum Welding Tables:
The primary advantage of aluminum is its lightweight nature, which enhances mobility and ease of use. Additionally, aluminum’s natural corrosion resistance reduces maintenance needs. However, aluminum is generally less durable than steel and can deform under high-temperature conditions. The cost of aluminum is typically higher than that of steel, which may be a consideration for budget-conscious buyers.
What Are the Benefits of Using Cast Iron for Welding Tables?
Cast iron is another traditional material used for welding tables, known for its excellent vibration-damping properties. This makes it particularly suitable for precision welding tasks. Cast iron can withstand high temperatures and is resistant to warping, providing a stable working surface.
Pros & Cons of Cast Iron Welding Tables:
The key advantage of cast iron is its stability and ability to absorb vibrations, which is crucial for high-precision welding applications. However, it is brittle and can crack under impact, limiting its use in some environments. Cast iron tables are also relatively heavy, which can complicate transportation and setup. The cost is generally moderate, but the manufacturing process can be complex.
What Role Do Composite Materials Play in Welding Tables?
Composite materials, which often combine metals with polymers or other materials, are emerging as a versatile option for welding tables. These materials can be engineered for specific properties, such as enhanced corrosion resistance or reduced weight.
Pros & Cons of Composite Welding Tables:
The main advantage of composite materials is their customizable properties, allowing for tailored solutions to meet specific application needs. They can be lighter than traditional materials and offer good resistance to chemicals and corrosion. However, the manufacturing process can be more complex and expensive, and the long-term durability compared to metals may be a concern in heavy-duty applications.
Summary Table of Material Selection for Welding Tables
Material | Typical Use Case for welding table | Key Advantage | Key Disadvantage/Limitation | Relative Cost (Low/Med/High) |
---|---|---|---|---|
Steel | General-purpose welding and fabrication | High durability and strength | Prone to corrosion without treatment | Medium |
Aluminum | Lightweight applications and mobile setups | Lightweight and corrosion-resistant | Less durable under high temperatures | High |
Cast Iron | Precision welding and heavy-duty tasks | Excellent vibration damping | Brittle and heavy | Medium |
Composite | Specialized applications with unique needs | Customizable properties | Potentially higher manufacturing cost | High |
In conclusion, the selection of material for welding tables should be guided by specific application requirements, budget constraints, and environmental considerations. By understanding the properties, advantages, and limitations of each material, international B2B buyers can make informed decisions that align with their operational needs.
In-depth Look: Manufacturing Processes and Quality Assurance for welding table
What Are the Main Stages in the Manufacturing Process of Welding Tables?
The manufacturing process of welding tables encompasses several critical stages, ensuring that the final product meets the stringent demands of the industry. The primary stages include material preparation, forming, assembly, and finishing.
1. Material Preparation
The first step in manufacturing a welding table is the selection and preparation of raw materials. Typically, high-quality steel, such as carbon steel or stainless steel, is used for its strength and durability. This stage involves cutting the raw materials into specified dimensions using techniques such as laser cutting or plasma cutting. Additionally, surface treatment may be applied to prevent corrosion, which is especially important for buyers in humid regions.
2. Forming the Table Components
In this stage, the prepared materials are shaped into the various components of the welding table. Techniques such as bending, welding, and machining are employed. CNC (Computer Numerical Control) machines are often utilized for precision, ensuring that every component fits together seamlessly. It is crucial for B2B buyers to inquire about the level of automation in this process, as advanced machinery can enhance efficiency and consistency.
3. Assembly of Components
Once the individual components are formed, they are assembled into the final structure. This may involve welding parts together or using bolts and screws for modular designs. Buyers should pay attention to the assembly methods, as proper joining techniques contribute significantly to the table’s strength and longevity. It is advisable for buyers to verify that the assembly process adheres to best practices, such as those outlined in ISO standards.
4. Finishing Touches
The final stage involves surface finishing treatments that enhance the table’s aesthetics and durability. Common methods include powder coating, galvanizing, or painting. These finishes not only provide a pleasing appearance but also protect against wear and tear. Buyers should look for suppliers that offer customizable finishes to match their specific operational environments.
How is Quality Assurance Implemented in Welding Table Manufacturing?
Quality assurance (QA) is a critical part of the manufacturing process, particularly in industries requiring high precision and safety standards. For welding tables, several international and industry-specific standards guide quality assurance practices.
1. What Are the Relevant International Standards?
International standards such as ISO 9001 play a vital role in ensuring consistent quality in manufacturing processes. ISO 9001 outlines requirements for a quality management system (QMS) that can enhance customer satisfaction and operational efficiency. Additionally, industry-specific certifications like CE marking (for compliance with European safety standards) and API (American Petroleum Institute) standards are crucial for buyers in sectors such as oil and gas.
2. What Are the Key Quality Control Checkpoints?
Quality control (QC) involves multiple checkpoints throughout the manufacturing process:
-
Incoming Quality Control (IQC): This initial stage checks the quality of raw materials upon arrival. Ensuring that materials meet specified standards can prevent issues later in the production process.
-
In-Process Quality Control (IPQC): Conducted during manufacturing, this checkpoint monitors processes and components to ensure they adhere to quality standards. Techniques such as visual inspections and measurements are commonly employed.
-
Final Quality Control (FQC): Once the welding table is assembled, FQC involves a thorough inspection of the finished product. This may include functional testing, dimensional checks, and surface inspections to ensure that the product meets all specifications.
How Can B2B Buyers Verify Supplier Quality Control Practices?
For international B2B buyers, particularly those from Africa, South America, the Middle East, and Europe, verifying a supplier’s quality control practices is essential. Here are several actionable strategies:
1. Conduct Supplier Audits
One of the most effective ways to assess a supplier’s quality assurance practices is to perform on-site audits. During an audit, buyers can review the manufacturing processes, inspect raw materials, and evaluate QC procedures firsthand. This transparency helps establish trust and ensures that suppliers adhere to required standards.
2. Request Quality Assurance Reports
Buyers should request detailed reports documenting the supplier’s quality assurance processes. These reports should outline IQC, IPQC, and FQC practices, as well as any certifications obtained. Analyzing these documents can provide insights into the supplier’s commitment to quality and consistency.
3. Utilize Third-Party Inspections
Engaging third-party inspection services can further enhance the verification process. Independent inspectors can conduct quality assessments at various stages of production, offering an unbiased evaluation of the supplier’s practices. This is particularly beneficial for buyers who may not have the resources to conduct comprehensive audits themselves.
What QC/Cert Nuances Should Buyers Consider in International Transactions?
When engaging in international transactions, B2B buyers should be mindful of specific nuances related to quality control and certification. Understanding regional regulations, such as those in the EU or specific requirements in African or Middle Eastern markets, is crucial. For instance, the CE marking is mandatory for products sold in the EU, while some African countries may have their own certification requirements that must be met.
Additionally, buyers should ensure that suppliers can provide documentation that proves compliance with both international and local standards. This documentation can include test reports, certificates of conformity, and manufacturing process details.
Conclusion
In summary, understanding the manufacturing processes and quality assurance protocols for welding tables is essential for international B2B buyers. By focusing on the main stages of production, relevant quality standards, and effective verification methods, buyers can make informed decisions that enhance their procurement strategies. Engaging with suppliers who prioritize quality and compliance will ultimately lead to better operational efficiency and product reliability.
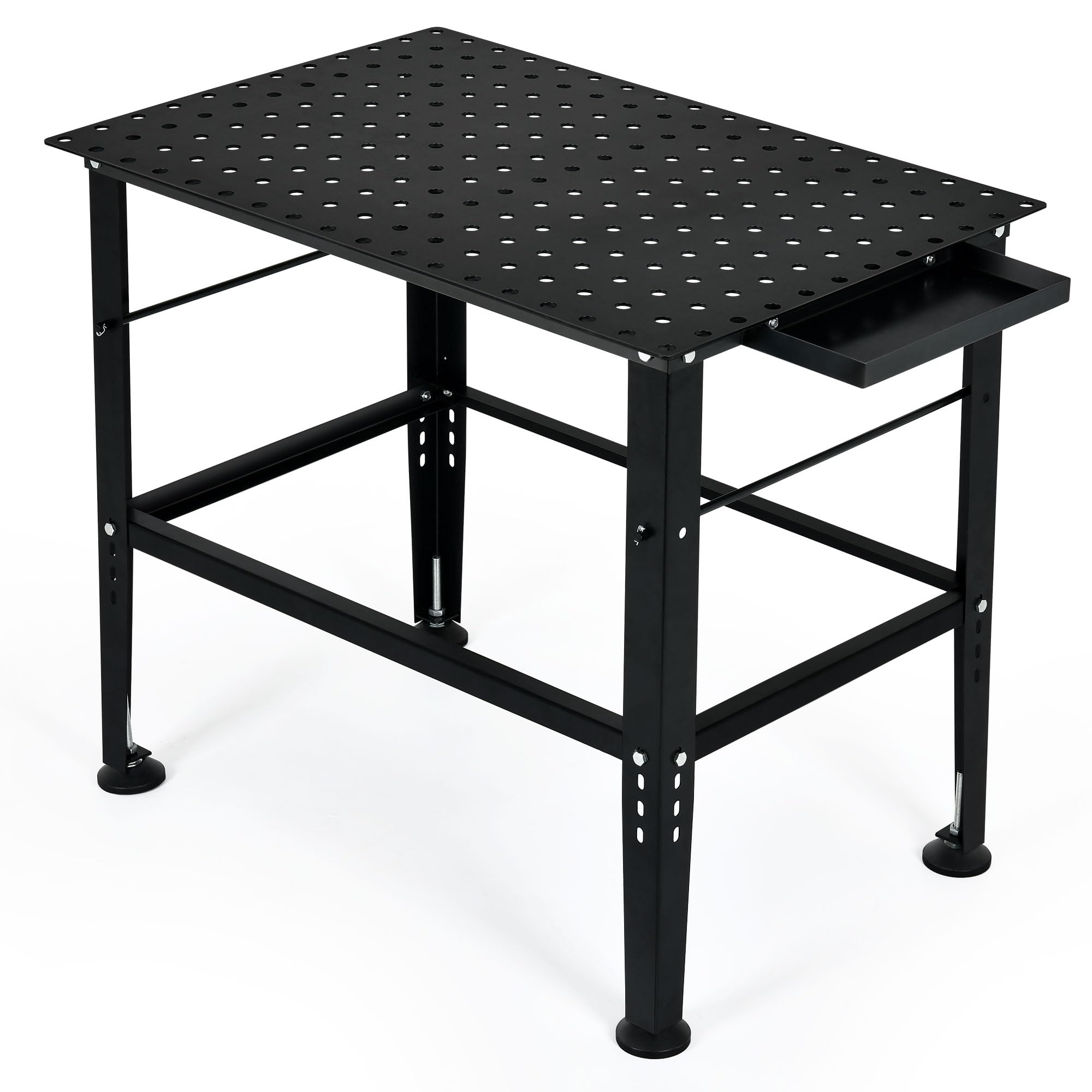
A stock image related to welding table.
Related Video: AUTOMATED WELDING & PRODUCTION SYSTEMS | PEMA welding automation
Practical Sourcing Guide: A Step-by-Step Checklist for ‘welding table’
When sourcing a welding table for your business, it’s essential to have a strategic approach that ensures quality, cost-effectiveness, and compatibility with your operational needs. This checklist will guide you through the key steps necessary to make an informed purchase, particularly relevant for international B2B buyers from Africa, South America, the Middle East, and Europe.
Step 1: Define Your Technical Specifications
Before you begin sourcing, clearly outline the technical specifications required for your welding table. Consider factors such as size, weight capacity, material (steel, aluminum, etc.), and adjustability options. Understanding these specifications will help you narrow down your options and ensure that the table meets your operational demands.
Step 2: Research Market Trends and Pricing
Investigate current market trends in welding tables to understand average pricing and features available. This can involve browsing industry publications, attending trade shows, or consulting online marketplaces. Being informed about market dynamics will empower you to negotiate better deals and recognize value when you see it.
Step 3: Identify Potential Suppliers
Compile a list of potential suppliers that specialize in welding tables. Utilize online directories, trade associations, and recommendations from industry peers. Prioritize suppliers that have a substantial presence in your target regions, as they are more likely to understand local regulations and market conditions.
Step 4: ✅ Verify Supplier Certifications
Ensure that the suppliers you are considering possess the necessary certifications and compliance documents. Look for ISO certifications, CE markings, or other relevant industry standards that indicate quality and safety. This verification not only protects your investment but also mitigates risks associated with substandard products.
Step 5: Evaluate Supplier Experience and Reputation
Research the experience and reputation of each supplier. Look for customer reviews, testimonials, and case studies that highlight their performance in similar projects. A supplier with a solid track record in your industry will likely provide better service and support.
Step 6: Request Samples and Specifications
Once you have shortlisted potential suppliers, request samples or detailed specifications of their welding tables. Examine the materials, craftsmanship, and features of the samples to ensure they align with your needs. This hands-on evaluation is crucial for making an informed decision.
Step 7: Negotiate Terms and Conditions
Finally, negotiate the terms and conditions of your purchase, including pricing, payment terms, delivery timelines, and warranty conditions. Be clear about your expectations, and don’t hesitate to seek discounts for bulk orders or long-term partnerships. Establishing favorable terms can lead to significant savings and a more fruitful supplier relationship.
By following these steps, you will be well-equipped to source a welding table that not only meets your operational needs but also aligns with your budget and quality standards.
Comprehensive Cost and Pricing Analysis for welding table Sourcing
What Are the Key Cost Components in Sourcing Welding Tables?
When sourcing welding tables for international B2B transactions, understanding the intricate cost structure is essential. The primary components include:
-
Materials: The choice of material greatly affects the cost. Common materials like steel, aluminum, or specialty alloys can vary in price based on market conditions. High-quality materials may incur a higher upfront cost but can lead to longevity and lower maintenance expenses.
-
Labor: Labor costs can fluctuate based on geographical location and the complexity of manufacturing processes. Countries with lower labor costs may offer competitive pricing; however, the skill level and experience of the workforce should not be overlooked, as this directly impacts product quality.
-
Manufacturing Overhead: This includes costs associated with factory operations, utilities, and administrative expenses. Efficient manufacturing processes can reduce overhead, thereby lowering overall costs.
-
Tooling: Initial tooling costs are crucial, especially for custom designs. Investing in high-quality tooling can enhance production efficiency and reduce long-term costs, but it can inflate initial sourcing expenses.
-
Quality Control (QC): Ensuring product quality may involve rigorous QC processes, which can add to the cost. However, investing in quality assurance can prevent costly defects and returns, proving beneficial in the long run.
-
Logistics: Shipping and handling costs can vary significantly based on distance, shipping method, and the volume of the order. International buyers must consider these costs in their total budget.
-
Margin: Supplier margins can vary, influenced by their operational efficiency and market positioning. Understanding the supplier’s cost structure can provide insights into their pricing strategy.
How Do Price Influencers Affect Welding Table Costs?
Several factors can influence the pricing of welding tables for international buyers:
-
Volume and Minimum Order Quantity (MOQ): Purchasing in bulk often leads to discounts. Understanding the MOQ is vital for negotiating better pricing, especially for larger projects.
-
Specifications and Customization: Custom designs can significantly increase costs. Buyers should weigh the benefits of tailored solutions against standard options to determine the best value.
-
Materials and Quality Certifications: Higher-grade materials and certifications (e.g., ISO, CE) can lead to increased costs, but they also assure quality and compliance with international standards.
-
Supplier Factors: The supplier’s reputation, location, and production capabilities can greatly impact pricing. Established suppliers with a track record of reliability may command higher prices but often provide better service and quality assurance.
-
Incoterms: Understanding Incoterms (International Commercial Terms) is crucial for cost management. They define responsibilities regarding shipping, insurance, and tariffs, impacting the final price.
What Are the Best Strategies for Negotiating Welding Table Prices?
For international B2B buyers, negotiating effectively can yield significant cost savings:
-
Research and Comparison: Conduct thorough market research to understand average pricing and identify competitive suppliers. Having benchmark data can strengthen your negotiation position.
-
Total Cost of Ownership (TCO): Evaluate the TCO, which includes purchase price, maintenance, and operational costs over the product’s lifespan. Presenting a TCO analysis can justify higher upfront costs if long-term savings are evident.
-
Flexibility in Specifications: Being open to alternative specifications can lead to cost reductions. Suppliers may offer lower prices for standard models or materials.
-
Leverage Relationships: Building strong relationships with suppliers can lead to better pricing and terms. Regular communication and loyalty can result in preferential treatment and discounts.
-
Understand Pricing Nuances for Different Regions: Pricing can vary based on geographical factors. Buyers from Africa, South America, the Middle East, and Europe should be aware of local economic conditions, import tariffs, and currency fluctuations that might affect costs.
Conclusion on Welding Table Pricing
While the costs associated with sourcing welding tables can be complex, a comprehensive understanding of the cost components and price influencers allows international B2B buyers to make more informed purchasing decisions. By leveraging negotiation strategies and being aware of regional pricing nuances, buyers can optimize their sourcing processes and achieve better value for their investments.
Disclaimer: The pricing discussed is indicative and can vary based on market conditions and specific supplier agreements. Always conduct detailed inquiries and obtain quotes tailored to your specific needs.
Alternatives Analysis: Comparing welding table With Other Solutions
Understanding Alternative Solutions to Welding Tables
When considering welding operations, businesses often evaluate various tools and solutions that can enhance efficiency and quality. While welding tables are a popular choice due to their versatility and stability, there are alternative methods and technologies that can also serve the needs of manufacturers and fabricators. This section explores the comparative aspects of welding tables against other viable solutions, specifically portable welding fixtures and CNC plasma cutting machines.
Comparison Table
Comparison Aspect | Welding Table | Portable Welding Fixture | CNC Plasma Cutting Machine |
---|---|---|---|
Performance | High precision and stability | Moderate precision; portable | High speed and precision |
Cost | Moderate initial investment | Lower initial cost | Higher investment, but faster ROI |
Ease of Implementation | Simple setup and use | Quick to deploy, but less stable | Requires skilled operation |
Maintenance | Low maintenance needs | Moderate; depends on usage | Higher maintenance costs |
Best Use Case | Fixed, multi-task welding | On-site projects, repairs | High-volume, automated cutting |
What are the Advantages and Disadvantages of Portable Welding Fixtures?
Portable welding fixtures are designed to enhance the flexibility of welding operations, allowing for on-site work or adjustments. Their primary advantage is cost-effectiveness, making them accessible for smaller operations or projects requiring mobility. However, they often lack the stability and precision of a dedicated welding table, which can lead to inconsistent weld quality if not carefully managed. Best suited for small-scale projects or repairs, portable fixtures can be an excellent option when budget constraints are a priority.
How Does CNC Plasma Cutting Compare to Welding Tables?
CNC plasma cutting machines provide a different approach to metal processing, focusing on cutting rather than joining. They excel in high-speed operations and can produce intricate designs with remarkable precision. While the initial investment is generally higher than that of welding tables, the potential for faster returns through increased productivity can justify the cost. However, these machines require skilled operators and have a steeper learning curve, which may not be ideal for all businesses. CNC plasma cutting is particularly advantageous for high-volume production environments where speed and accuracy are paramount.
Conclusion: How Can B2B Buyers Choose the Right Welding Solution?
For international B2B buyers, the decision between a welding table and its alternatives should be guided by specific operational needs, budget constraints, and the nature of projects undertaken. If precision and stability are critical, a welding table may be the best choice. Conversely, if mobility and cost are more significant concerns, portable welding fixtures could be ideal. For businesses focusing on high-volume production and intricate designs, investing in CNC plasma cutting machines may yield the best long-term benefits. By carefully assessing these aspects, buyers can make informed decisions that align with their operational goals and market demands.
Essential Technical Properties and Trade Terminology for welding table
What Are the Key Technical Properties of a Welding Table?
When sourcing a welding table, understanding its technical specifications is crucial for ensuring it meets your operational needs. Here are some essential properties that international B2B buyers should consider:
1. Material Grade: Why Is It Important?
The material grade of a welding table often dictates its durability and load-bearing capacity. Common materials include steel, aluminum, and cast iron. For instance, high-strength steel (like S235 or S275) is preferred for heavy-duty applications due to its excellent weldability and strength. Selecting the right material is vital to enhance the table’s longevity and performance, particularly in industries that require frequent and intensive welding tasks.
2. Tolerance: How Does It Affect Precision?
Tolerance refers to the permissible limit of variation in dimensions and weight. In welding applications, maintaining strict tolerances ensures that the components fit together accurately, reducing the likelihood of defects. A welding table with tighter tolerances is essential for precision work, especially in sectors like automotive and aerospace, where exact specifications are crucial.
3. Load Capacity: What Should You Know?
Load capacity indicates the maximum weight the welding table can safely support. This property is particularly important for B2B buyers who anticipate heavy usage. Tables designed for industrial purposes typically have a load capacity ranging from 500 kg to over 2000 kg. Understanding the load requirements of your specific applications will help you choose a table that enhances productivity without risking safety.
4. Surface Finish: Why Does It Matter?
The surface finish of a welding table can influence both its performance and maintenance. A smooth, non-porous surface is easier to clean and maintain, while a rough surface can improve the grip for fixtures. Additionally, certain finishes can enhance corrosion resistance, which is crucial for tables used in humid or outdoor environments. Buyers should consider the environmental conditions where the table will be used to select an appropriate finish.
5. Adjustability: What Benefits Does It Offer?
Adjustable welding tables allow users to modify the height and angle according to specific tasks, which can significantly boost ergonomic efficiency. This adaptability is especially beneficial in diverse work environments, enabling operators to work comfortably and with greater precision. For international buyers, investing in adjustable features can translate to improved productivity and reduced fatigue among workers.
What Common Trade Terms Should You Know When Purchasing a Welding Table?
In addition to understanding technical specifications, familiarity with industry terminology can streamline the purchasing process.
1. OEM (Original Equipment Manufacturer): What Does It Signify?
OEM refers to companies that produce parts or equipment that are marketed by another manufacturer. When purchasing a welding table, knowing whether a supplier is an OEM can help assess the quality and reliability of the product. It often indicates that the manufacturer adheres to industry standards and quality controls.
2. MOQ (Minimum Order Quantity): Why Is It Relevant?
MOQ is the smallest quantity of a product that a supplier is willing to sell. Understanding the MOQ is critical for budgeting and inventory management. For businesses in Africa or South America, where startup costs may be a concern, negotiating lower MOQs can be beneficial.
3. RFQ (Request for Quotation): How Can It Help You?
An RFQ is a document that a buyer sends to suppliers to request pricing and other details for specific products. Crafting a well-defined RFQ can help ensure that you receive accurate and comparable quotes, facilitating better decision-making when sourcing welding tables.
4. Incoterms: What Should You Understand?
Incoterms (International Commercial Terms) are standard trade definitions that clarify the responsibilities of buyers and sellers in international transactions. Understanding these terms helps mitigate risks associated with shipping, insurance, and customs duties. Familiarity with Incoterms is crucial for businesses in the Middle East and Europe, where cross-border trade is prevalent.
5. Lead Time: Why Is It Critical?
Lead time refers to the duration between placing an order and receiving the product. Knowing the lead time is essential for planning and inventory management. It can vary significantly based on the supplier’s location and production capabilities, impacting project timelines.
By understanding these essential properties and trade terms, B2B buyers can make informed decisions when sourcing welding tables, ensuring that their investments align with operational needs and industry standards.
Navigating Market Dynamics and Sourcing Trends in the welding table Sector
What Are the Current Market Dynamics and Key Trends Influencing the Welding Table Sector?
The welding table market is witnessing dynamic shifts driven by technological advancements, increased automation, and a growing emphasis on precision in manufacturing. Global demand for customized solutions is rising, particularly in countries across Africa, South America, the Middle East, and Europe. Buyers are increasingly looking for versatile and adaptable welding tables that can accommodate various applications, from heavy industrial use to lighter fabrication.
Emerging trends include the integration of Industry 4.0 technologies, which facilitate smart manufacturing and improve operational efficiency. Digital tools like CAD/CAM software are becoming essential for designing and modifying welding tables to meet specific project requirements. Additionally, the rise of e-commerce platforms is transforming sourcing processes, allowing international B2B buyers to access a broader range of suppliers and products with ease. This shift is particularly relevant for buyers in regions like South America and Africa, where traditional sourcing channels may be limited.
The market is also influenced by the ongoing push for higher productivity and cost-efficiency. Buyers should be prepared to evaluate suppliers based on their ability to deliver high-quality products that can withstand rigorous use while offering competitive pricing. Understanding regional market dynamics, including local manufacturing capabilities and import regulations, is crucial for successful sourcing.
How Is Sustainability Shaping the Welding Table Sector and Influencing Ethical Sourcing?
Sustainability has become a key consideration for international B2B buyers in the welding table sector. The environmental impact of manufacturing processes and materials is under heightened scrutiny, prompting companies to adopt greener practices. Buyers are increasingly favoring suppliers that demonstrate a commitment to sustainability through responsible sourcing of materials and energy-efficient production methods.
Ethical supply chains are gaining importance as businesses recognize the need for transparency and accountability in their sourcing practices. Certifications such as ISO 14001 for environmental management and other green certifications are becoming essential for suppliers looking to gain a competitive edge. Buyers should prioritize suppliers who can provide evidence of their adherence to these standards, ensuring that the welding tables they procure are produced with minimal environmental impact.
Furthermore, the use of recycled materials in the construction of welding tables is becoming a viable option. This not only reduces waste but also appeals to buyers who are looking to enhance their corporate social responsibility (CSR) initiatives. As sustainability continues to be a focal point, B2B buyers in Africa, South America, the Middle East, and Europe should actively seek partnerships with suppliers committed to ethical and sustainable practices.
How Has the Welding Table Sector Evolved Over Time?
The evolution of the welding table sector can be traced back to the industrial revolution, where the need for robust and versatile work surfaces became apparent. Initially, welding tables were simple, utilitarian designs made from basic materials. However, as technology advanced, so did the complexity and functionality of welding tables.
The introduction of adjustable features, modular designs, and the incorporation of advanced materials has transformed welding tables into specialized tools that enhance productivity and precision. The shift towards automation and digitalization in manufacturing processes has further emphasized the need for high-quality, adaptable welding tables that can easily integrate with modern technologies.
As the global market continues to evolve, understanding this historical context can help international B2B buyers make informed decisions about the types of welding tables that best suit their operational needs, while also considering the latest trends and innovations in the sector.
Related Video: Is global trade transforming? | Counting the Cost
Frequently Asked Questions (FAQs) for B2B Buyers of welding table
-
How do I choose the right welding table for my business needs?
Selecting the ideal welding table involves assessing your specific welding applications, workspace size, and weight capacity requirements. Consider tables with adjustable heights for ergonomic benefits and those made from durable materials like steel for longevity. Additionally, evaluate features such as integrated clamping systems or modular designs that allow for customization based on your projects. It’s also wise to consult with suppliers about the table’s specifications and how they align with your production processes. -
What are the key features to look for in a high-quality welding table?
A high-quality welding table should have a robust construction with a flat, stable surface to ensure precision. Features such as T-slot or grid patterns allow for easy clamping and adjustments. Additionally, consider tables that offer portability, adjustable heights, and built-in tool storage. Look for tables with a high weight capacity suitable for your heaviest workpieces, as well as those that come with a warranty for added peace of mind. -
What are the common minimum order quantities (MOQ) for welding tables?
MOQs for welding tables can vary significantly based on the supplier and the type of table. Typically, manufacturers may set an MOQ ranging from 5 to 20 units, particularly for custom designs. When sourcing internationally, it is beneficial to negotiate MOQs directly with suppliers, especially if you are interested in a pilot order. Establishing a solid relationship with a supplier can also lead to more flexible terms in future orders. -
What payment terms should I expect when purchasing welding tables internationally?
Payment terms for international purchases often include options like T/T (telegraphic transfer), L/C (letter of credit), or PayPal for smaller transactions. Common practices involve a 30% deposit upfront, with the remaining balance due prior to shipment. Ensure that the payment terms are clearly outlined in the contract to avoid any misunderstandings. Additionally, consider the implications of currency exchange rates and transaction fees that may affect the overall cost. -
How can I assess the quality assurance (QA) processes of a welding table supplier?
To evaluate a supplier’s QA processes, request detailed information about their quality control measures during production. Inquire about certifications such as ISO 9001 that indicate adherence to international standards. Ask for documentation related to testing procedures, inspection reports, and warranty policies. Engaging with previous clients or seeking third-party reviews can also provide insight into a supplier’s reliability and product quality.
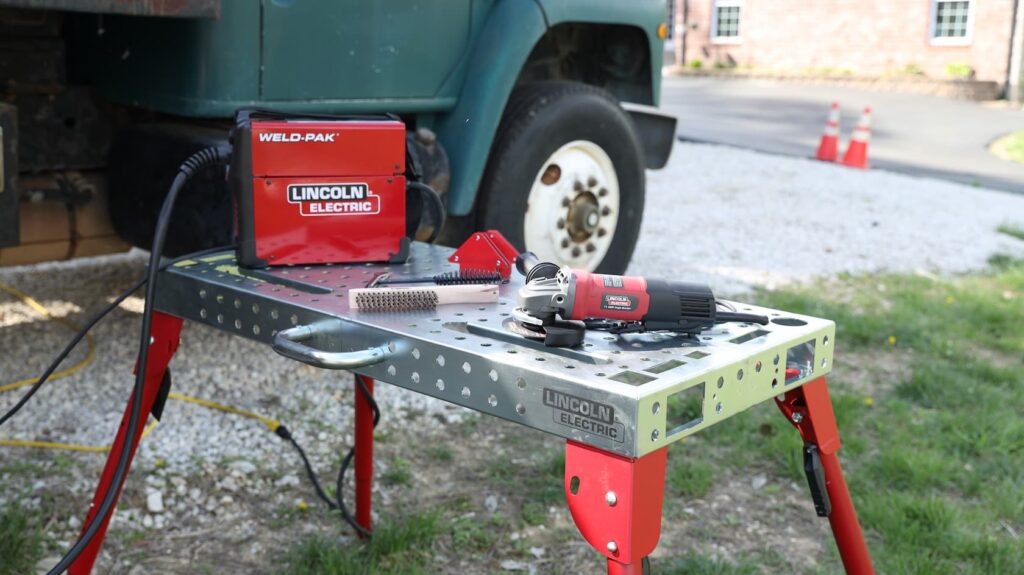
A stock image related to welding table.
-
What logistics considerations should I keep in mind when importing welding tables?
Logistics play a crucial role in international sourcing. Assess shipping methods, lead times, and costs associated with transporting welding tables from the supplier’s location to your facility. Familiarize yourself with customs regulations and import duties applicable in your country. It may also be beneficial to partner with a freight forwarder who can streamline the shipping process and manage any complexities related to customs clearance. -
What customization options are typically available for welding tables?
Many manufacturers offer various customization options, including size, surface material, and additional features like integrated measuring systems or electrical outlets. You can also request specific color finishes or branding options to align with your company’s aesthetic. When discussing customization, provide your supplier with detailed specifications and consider the implications on pricing and lead times for tailored solutions. -
How can I verify the credibility of a welding table supplier before making a purchase?
Verifying a supplier’s credibility involves conducting thorough research. Check their business registration details, certifications, and years of operation. Engage with references or read reviews from other international buyers. Utilize platforms such as Alibaba or Global Sources, which often provide ratings and feedback on suppliers. Additionally, consider requesting samples before committing to a large order, allowing you to assess the product quality firsthand.
Important Disclaimer & Terms of Use
⚠️ Important Disclaimer
The information provided in this guide, including content regarding manufacturers, technical specifications, and market analysis, is for informational and educational purposes only. It does not constitute professional procurement advice, financial advice, or legal advice.
While we have made every effort to ensure the accuracy and timeliness of the information, we are not responsible for any errors, omissions, or outdated information. Market conditions, company details, and technical standards are subject to change.
B2B buyers must conduct their own independent and thorough due diligence before making any purchasing decisions. This includes contacting suppliers directly, verifying certifications, requesting samples, and seeking professional consultation. The risk of relying on any information in this guide is borne solely by the reader.
Strategic Sourcing Conclusion and Outlook for welding table
How Can Strategic Sourcing Enhance Your Welding Table Procurement?
In the ever-evolving landscape of international B2B procurement, strategic sourcing stands out as a critical driver of efficiency and cost-effectiveness, especially when acquiring welding tables. By focusing on supplier relationships, quality assessments, and market analysis, buyers from Africa, South America, the Middle East, and Europe can optimize their purchasing decisions. Key takeaways include the importance of understanding local regulations, assessing supplier reliability, and leveraging negotiation tactics to secure the best terms.
Moreover, embracing digital tools and platforms can streamline the sourcing process, allowing businesses to make data-driven decisions. As global supply chains become more interconnected, maintaining flexibility and adaptability will be paramount.
What Steps Should B2B Buyers Take for Future Welding Table Investments?
Looking ahead, it is crucial for B2B buyers to stay informed about market trends and technological advancements in welding table manufacturing. Engaging in continuous learning and networking will provide insights into emerging suppliers and innovative products.
Now is the time to take proactive steps in refining your sourcing strategy. Invest in building strong partnerships with reputable manufacturers and distributors that align with your operational needs. This approach will not only enhance your procurement process but also fortify your competitive advantage in the marketplace. Embrace the future of welding table sourcing and position your business for sustained success.