Discover the Best Types of Aluminium Materials for Cost Savings (2025)
Introduction: Navigating the Global Market for types of aluminium materials
Navigating the global market for various types of aluminum materials can be daunting for international B2B buyers, especially when sourcing specific alloys that meet unique project requirements. The challenge lies not only in understanding the diverse grades of aluminum—such as 1100, 3003, and 6061—but also in discerning their applications across industries. This comprehensive guide delves into the different types of aluminum materials, providing insights into their properties, applications, and the critical factors to consider when selecting a supplier.
In this guide, buyers will explore the nuances of aluminum grades, their specific uses, and the advantages they offer in various industrial settings. From lightweight aluminum tubing and durable aluminum coils to specialized alloys designed for high-temperature applications, understanding these materials is essential for making informed purchasing decisions. Additionally, we will cover best practices for vetting suppliers, assessing costs, and ensuring compliance with regional standards, particularly for buyers from Africa, South America, the Middle East, and Europe, including countries like Nigeria and Indonesia.
Armed with this knowledge, international B2B buyers can confidently navigate the complexities of the aluminum market, optimizing their procurement strategies while ensuring they select the best materials for their projects. This guide is designed to empower you to make strategic decisions that enhance efficiency, reduce costs, and drive success in your operations.
Understanding types of aluminium materials Types and Variations
Type Name | Key Distinguishing Features | Primary B2B Applications | Brief Pros & Cons for Buyers |
---|---|---|---|
Aluminum 1100 | Purest form with excellent ductility and corrosion resistance | Food processing, chemical equipment | Pros: High workability, good thermal conductivity. Cons: Lower strength than other alloys. |
Aluminum 3003 | Manganese alloy that offers good weldability and moderate strength | Cooking utensils, storage tanks | Pros: Economical, versatile for many applications. Cons: Less corrosion resistance than 6061. |
Aluminum 6061 | Known as the “workhorse” aluminum; offers excellent corrosion resistance and strength | Structural components, automotive parts | Pros: High strength-to-weight ratio, good machinability. Cons: Higher cost than 1100 and 3003. |
Aluminum Coil | Rolled aluminum sheets coiled for ease of transport and use | Construction, signage, packaging | Pros: Flexible for various applications, easy to handle. Cons: Requires specific processing equipment. |
Aluminized Steel | Steel coated with aluminum for enhanced corrosion resistance | Automotive, appliances, industrial applications | Pros: Combines strength of steel with aluminum’s corrosion resistance. Cons: Can be more expensive than standard steel. |
What are the characteristics and suitability of Aluminum 1100 for B2B buyers?
Aluminum 1100 is recognized for its high purity (99% minimum) and excellent workability, making it suitable for industries requiring intricate shaping and forming processes. It boasts superior corrosion resistance and thermal conductivity, making it ideal for food processing and chemical storage applications. B2B buyers should consider its lower strength compared to other alloys, which may limit its use in structural applications. However, its affordability and versatility make it a popular choice for manufacturers across various sectors.
Why is Aluminum 3003 a popular choice among B2B buyers?
Aluminum 3003 is an alloy primarily composed of aluminum with manganese, providing a balanced mix of strength and workability. It is widely used in cooking utensils and storage tanks due to its good weldability and moderate strength. B2B buyers appreciate its cost-effectiveness, especially for general-purpose applications. However, it is important to note that while it is economical, it does not offer the same corrosion resistance as higher-grade alloys like 6061, which could be a consideration for long-term applications.
How does Aluminum 6061 stand out for industrial applications?
Aluminum 6061 is often referred to as the “workhorse” of aluminum alloys due to its excellent mechanical properties and versatility. It offers superior corrosion resistance and strength, making it a preferred choice for structural applications, including automotive and aerospace components. B2B buyers should weigh its higher cost against its long-term durability and performance benefits. Its good machinability also allows for complex shapes, enhancing its appeal for custom manufacturing projects.
What are the advantages of using Aluminum Coil in construction?
Aluminum Coil is produced by flattening aluminum sheets into rolls, facilitating easy transport and processing. This form is especially advantageous for construction, signage, and packaging applications where flexibility and ease of handling are paramount. B2B buyers can benefit from its adaptability to various manufacturing processes. However, it is crucial to ensure that the necessary processing equipment is available, as handling coils may require specialized machinery.
Why choose Aluminized Steel for industrial applications?
Aluminized Steel combines the strength of traditional steel with the corrosion-resistant properties of aluminum. This dual advantage makes it suitable for a wide range of applications, including automotive parts and appliances. B2B buyers may find this material particularly appealing for projects where durability and resistance to harsh environments are critical. Nonetheless, the cost of aluminized steel can be higher than standard steel, necessitating careful consideration of budget constraints versus performance needs.
Key Industrial Applications of types of aluminium materials
Industry/Sector | Specific Application of types of aluminium materials | Value/Benefit for the Business | Key Sourcing Considerations for this Application |
---|---|---|---|
Aerospace | Lightweight structural components made from 6061 aluminum | Enhanced fuel efficiency and reduced operational costs | Certification standards, weight specifications, and alloy properties |
Automotive | Engine parts and body panels manufactured from 3003 aluminum | Improved performance and corrosion resistance | Supplier reliability, alloy strength, and processing capabilities |
Construction | Facades and roofing systems using aluminum coils | Durability and aesthetic appeal | Material thickness, finish options, and weather resistance |
Packaging | Food and beverage containers made from 1100 aluminum | Excellent barrier properties and lightweight design | Compliance with food safety regulations and recyclability |
Electrical | Electrical conduits and busbars using aluminum tubing | High conductivity and low weight | Electrical conductivity standards and thermal management features |
How is Aluminum Used in the Aerospace Industry?
In the aerospace sector, aluminum alloys such as 6061 are extensively used for crafting lightweight structural components. These materials play a crucial role in enhancing fuel efficiency, which is a significant cost-saving factor for airlines. Buyers must consider certification standards and specific weight requirements when sourcing aluminum, ensuring that the materials meet rigorous safety and performance benchmarks.
What Role Does Aluminum Play in the Automotive Sector?
Aluminum, particularly the 3003 alloy, is widely utilized in the automotive industry for manufacturing engine parts and body panels. Its lightweight nature contributes to better vehicle performance and fuel efficiency, while its corrosion resistance ensures longevity. For international B2B buyers, key considerations include the reliability of suppliers, the specific strength of the alloy, and the processing capabilities of the manufacturer to meet design specifications.
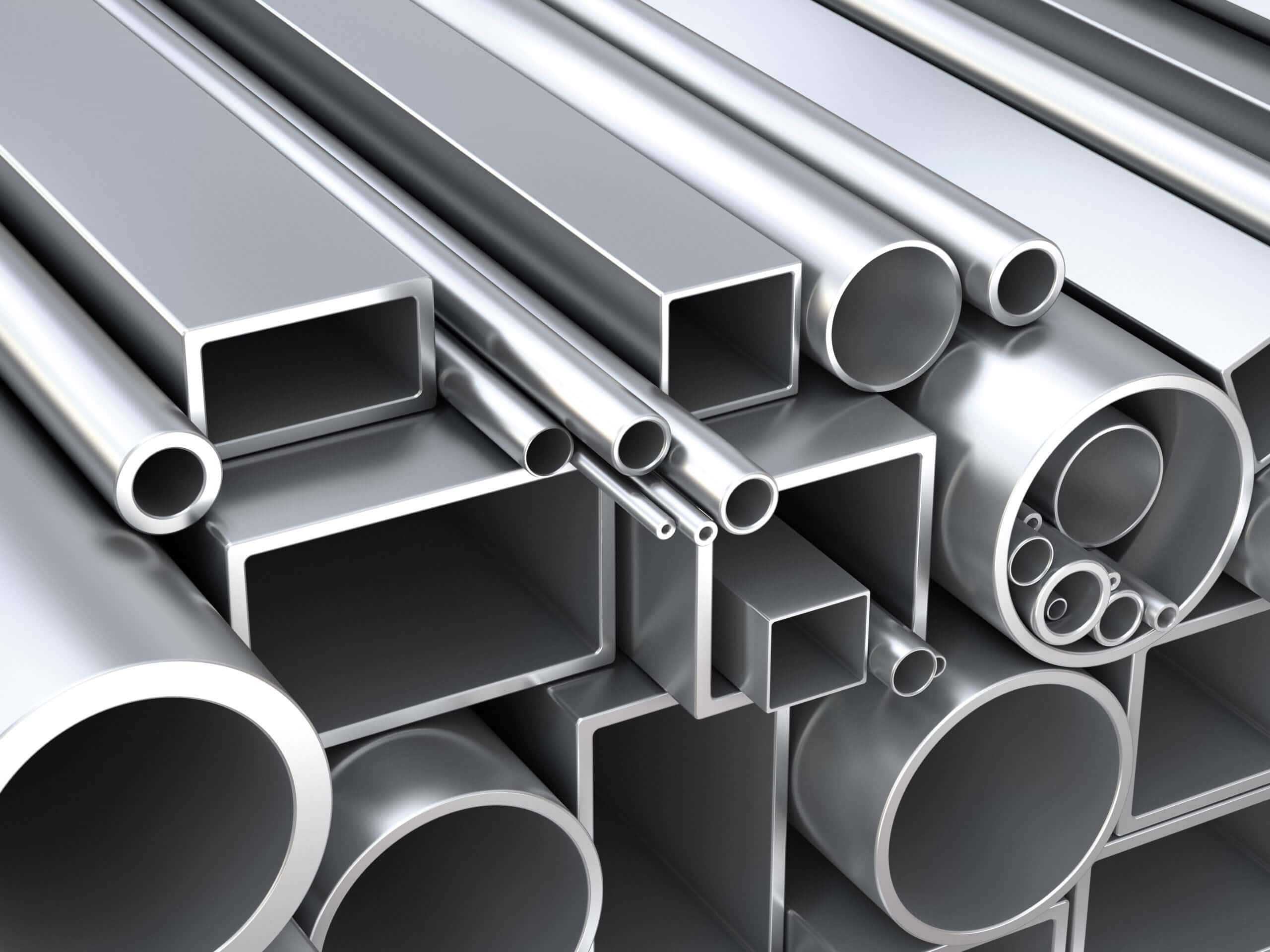
A stock image related to types of aluminium materials.
Why is Aluminum Important in Construction?
In construction, aluminum coils are often used for facades and roofing systems due to their durability and aesthetic appeal. These materials can withstand harsh weather conditions while providing a modern look to buildings. Buyers should focus on material thickness, finish options, and weather resistance when sourcing aluminum for construction projects, ensuring that they select products that meet local building codes and standards.
How is Aluminum Used in Packaging?
Aluminum, especially in the form of 1100 alloy, is commonly used for food and beverage containers due to its excellent barrier properties and lightweight design. This not only helps in preserving the contents but also reduces shipping costs. When sourcing aluminum for packaging applications, international buyers need to ensure compliance with food safety regulations and consider the recyclability of materials to align with sustainability goals.
What are the Applications of Aluminum in Electrical Industries?
In the electrical sector, aluminum tubing is used for conduits and busbars, providing high conductivity and low weight advantages. This is particularly beneficial in reducing energy losses and improving overall system efficiency. Buyers must pay attention to electrical conductivity standards and thermal management features when sourcing aluminum for electrical applications, ensuring that the materials can handle the specific load and environmental conditions they will face.
3 Common User Pain Points for ‘types of aluminium materials’ & Their Solutions
Scenario 1: Navigating Corrosion Resistance for Industrial Applications
The Problem: One of the most significant challenges faced by B2B buyers in sectors such as construction, automotive, and manufacturing is selecting the right aluminum grade that offers adequate corrosion resistance. For instance, a buyer sourcing materials for outdoor structures may mistakenly choose a lower-grade aluminum, like 3003, which lacks the necessary protection against environmental elements. This can lead to premature failure of components, increased maintenance costs, and potential safety hazards.
The Solution: To address this issue, buyers should prioritize understanding the specific environmental conditions their aluminum products will face. For outdoor applications, opting for aluminum alloys from the 5000 series, such as 5052 or 5083, is advisable due to their superior corrosion resistance and durability. Buyers can enhance their sourcing process by consulting with suppliers about the expected environmental exposure and requesting specific corrosion resistance data. Additionally, implementing a detailed specifications document that outlines the required properties of aluminum can ensure that the materials meet the necessary standards for longevity and reliability.
Scenario 2: Ensuring Proper Fabrication and Machining of Aluminum Alloys
The Problem: Many international B2B buyers encounter difficulties when machining or fabricating aluminum materials, especially when they are unfamiliar with the specific alloy properties. For instance, a buyer might procure 6061 aluminum, expecting it to be as easy to machine as 1100 aluminum, only to find that its toughness and higher tensile strength complicate fabrication processes. This often results in increased costs and project delays due to tool wear or incorrect machining techniques.
The Solution: To mitigate these challenges, buyers should invest time in understanding the machining characteristics of different aluminum grades. For alloys like 6061, it is crucial to select the right tools and techniques that cater to its unique properties. Utilizing tools with sharper cutting edges and proper coolant application can significantly enhance machining efficiency. Furthermore, buyers can collaborate with experienced machinists or consult technical guides that provide specific recommendations on feed rates, speeds, and tooling for various aluminum grades. This proactive approach can streamline fabrication processes and reduce operational costs.
Scenario 3: Managing Supply Chain Issues for Aluminum Material Procurement
The Problem: International buyers often face supply chain disruptions, especially when sourcing aluminum materials from different geographical regions. For example, a buyer in South America may experience delays in receiving shipments of aluminum coils due to logistical challenges or trade restrictions, leading to project standstills and financial penalties for late deliveries.
The Solution: To counteract these supply chain challenges, buyers should establish strong relationships with multiple suppliers across different regions. Diversifying the supplier base not only mitigates the risk of delays but also enables buyers to compare pricing and quality. Implementing just-in-time (JIT) inventory strategies can also ensure that materials are procured as needed, reducing storage costs and waste. Additionally, utilizing technology such as supply chain management software can enhance visibility and tracking of orders, allowing buyers to anticipate and respond to potential disruptions proactively. By adopting these strategies, B2B buyers can ensure a more resilient and efficient procurement process for aluminum materials.
Strategic Material Selection Guide for types of aluminium materials
What Are the Key Properties of Common Aluminum Materials?
When selecting aluminum materials for B2B applications, understanding the properties of various aluminum grades is crucial. Here, we analyze three common types of aluminum materials: 1100, 3003, and 6061. Each has distinct characteristics that influence their performance in different applications.
What Are the Key Properties of Aluminum 1100?
Aluminum 1100 is known for its excellent workability and high corrosion resistance. With a minimum purity of 99%, it is soft and ductile, making it easy to shape and form. However, it has a lower strength compared to other alloys and is not suitable for high-temperature applications.
Pros & Cons:
– Pros: High thermal conductivity, excellent corrosion resistance, and great for forming processes.
– Cons: Limited strength and not ideal for structural applications or high-temperature environments.
Impact on Application:
Aluminum 1100 is compatible with food processing, chemical storage, and electrical transmission due to its non-toxic nature and corrosion resistance. However, it may not withstand harsh conditions or heavy loads.
Considerations for International Buyers:
When sourcing Aluminum 1100, buyers in Africa, South America, the Middle East, and Europe should ensure compliance with local standards such as ASTM and DIN. The material’s lower cost makes it appealing for budget-sensitive projects.
How Does Aluminum 3003 Compare in Terms of Performance?
Aluminum 3003 is an alloy that contains manganese, enhancing its strength while maintaining excellent workability. It is widely used in applications requiring moderate strength and good corrosion resistance, making it a versatile choice.
Pros & Cons:
– Pros: Economical, readily weldable, and suitable for various applications including cooking utensils and storage tanks.
– Cons: Lower corrosion resistance compared to 6061 and not suitable for high-stress applications.
Impact on Application:
This alloy is ideal for environments where moderate strength and corrosion resistance are necessary. It performs well in manufacturing food containers and chemical equipment.
Considerations for International Buyers:
Buyers should be aware of the alloy’s limitations in corrosion resistance and ensure that it meets the specific requirements of their applications. Familiarity with local standards is also essential.
Why Is Aluminum 6061 Considered the Workhorse Alloy?
Aluminum 6061 is often referred to as the “workhorse” of aluminum alloys due to its excellent mechanical properties and versatility. It offers superior corrosion resistance and can be easily welded, making it suitable for a wide range of applications.
Pros & Cons:
– Pros: High strength, excellent corrosion resistance, and good machinability.
– Cons: Higher cost compared to 1100 and 3003, which may be a consideration for budget-conscious buyers.
Impact on Application:
6061 is ideal for structural applications, automotive parts, and marine environments due to its strength and resistance to corrosion. It is particularly effective in humid conditions.
Considerations for International Buyers:
International buyers should consider the higher cost of 6061 but weigh it against its durability and performance benefits. Compliance with international standards such as ASTM and JIS is essential for ensuring quality and reliability.
Summary Table of Aluminum Materials
Material | Typical Use Case for types of aluminium materials | Key Advantage | Key Disadvantage/Limitation | Relative Cost (Low/Med/High) |
---|---|---|---|---|
Aluminum 1100 | Food processing, chemical storage | Excellent corrosion resistance | Limited strength | Low |
Aluminum 3003 | Cooking utensils, storage tanks | Economical and readily weldable | Lower corrosion resistance | Medium |
Aluminum 6061 | Structural applications, automotive parts | High strength and good machinability | Higher cost compared to others | High |
This comprehensive analysis provides international B2B buyers with the insights needed to make informed decisions when selecting aluminum materials for their specific applications.
In-depth Look: Manufacturing Processes and Quality Assurance for types of aluminium materials
What Are the Main Stages in the Manufacturing Process of Aluminum Materials?
The manufacturing process for aluminum materials typically consists of several key stages: material preparation, forming, assembly, and finishing. Understanding these stages is essential for B2B buyers looking to ensure quality and reliability in their supply chains.
Material Preparation: How Is Raw Aluminum Processed?
The first step in aluminum manufacturing involves sourcing raw aluminum, often in the form of ingots or scrap. The material is then cleaned and prepared for further processing. This preparation may include melting, where the aluminum is heated to its melting point (around 660°C) and purified to remove any impurities.
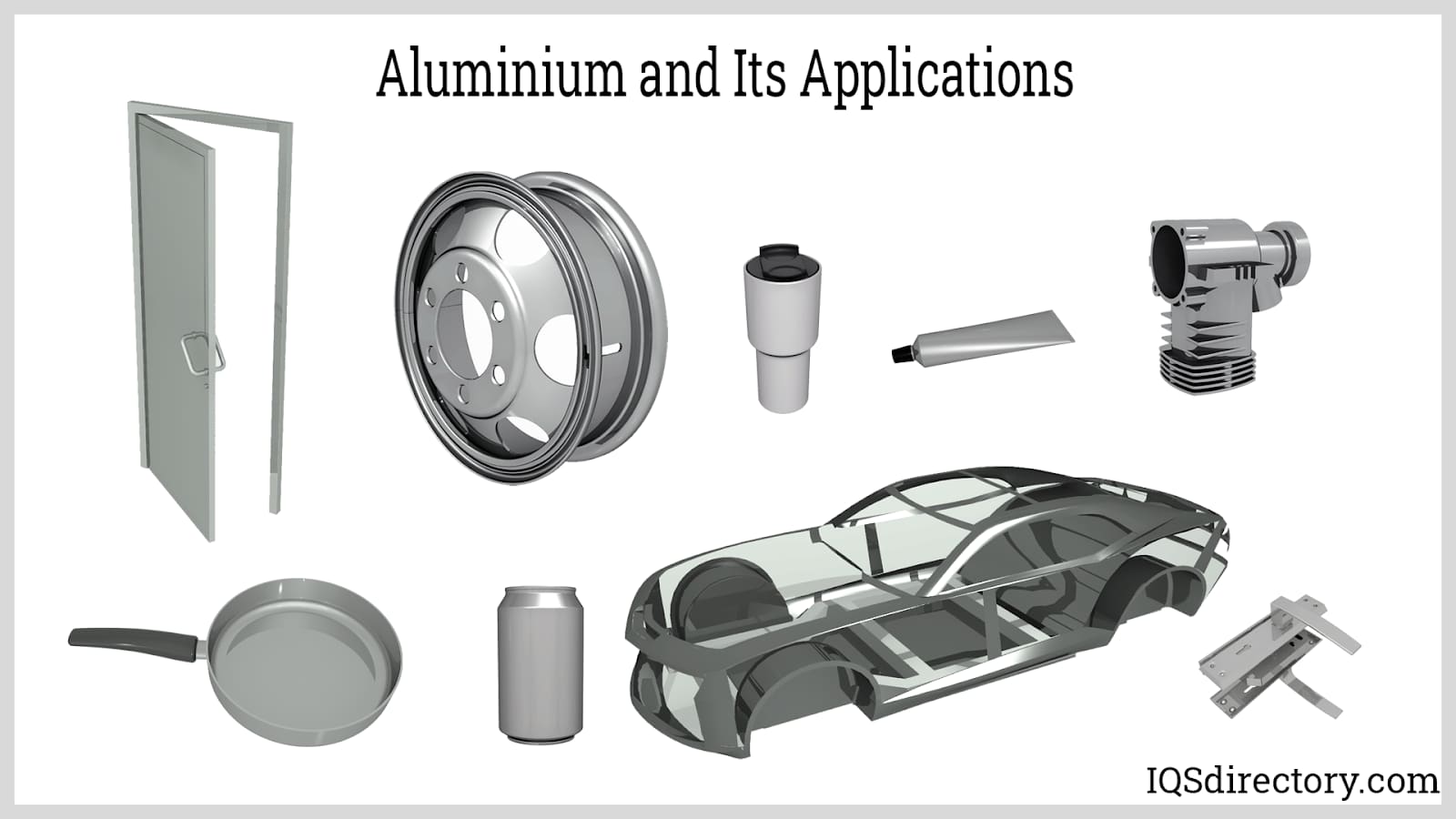
A stock image related to types of aluminium materials.
For international buyers, especially those in Africa and South America, verifying the source of raw materials is crucial. Ensuring that suppliers adhere to environmental and ethical sourcing standards can mitigate risks related to compliance and corporate social responsibility.
Forming: What Techniques Are Used to Shape Aluminum?
Once the aluminum is prepared, it undergoes various forming techniques, including extrusion, rolling, and forging.
- Extrusion involves forcing molten aluminum through a die to create specific shapes, such as tubing or profiles, and is particularly effective for producing long sections of material.
- Rolling flattens aluminum into sheets or coils, which are then used in diverse applications, from packaging to construction.
- Forging shapes the aluminum under pressure, enhancing its strength, making it ideal for components that require durability.
Each technique has its own set of operational parameters, which should be documented and reviewed to ensure compliance with international standards.
How Is Assembly Performed in Aluminum Manufacturing?
In the assembly stage, different aluminum components are joined together using various methods such as welding, riveting, or adhesive bonding.
- Welding is commonly used for structural applications, while riveting is often preferred in aerospace and automotive industries.
- Adhesive bonding is gaining traction due to its ability to create strong, lightweight assemblies without the need for mechanical fasteners.
B2B buyers should inquire about the specific assembly techniques used by suppliers, as this can affect the overall integrity and performance of the final product.
What Finishing Processes Enhance the Quality of Aluminum Products?
Finishing processes, including anodizing, painting, and powder coating, are crucial for enhancing the aesthetic appeal and functional properties of aluminum materials.
- Anodizing increases corrosion resistance and can add a decorative finish.
- Painting provides a protective layer and can enhance UV resistance.
- Powder coating offers a durable finish that is more environmentally friendly than traditional liquid paints.
Buyers should assess the finishing capabilities of potential suppliers to ensure that the products meet both functional and aesthetic requirements.
What Quality Control Measures Are Essential in Aluminum Manufacturing?
Quality assurance is pivotal in aluminum manufacturing, especially for international B2B buyers who need to ensure that products meet specific industry standards.
Which International Standards Are Relevant for Aluminum Quality Control?
Aluminum manufacturers often adhere to international standards such as ISO 9001, which outlines criteria for an effective quality management system. Compliance with these standards helps ensure that products are consistently produced to meet customer and regulatory requirements.
Other relevant standards may include:
- CE Marking: Indicates compliance with European health, safety, and environmental protection standards.
- API Standards: Relevant for aluminum used in oil and gas applications.
Understanding these standards is critical for buyers, particularly in regions like Europe and the Middle East, where compliance can significantly impact market access.
What Are the Key QC Checkpoints in the Manufacturing Process?
Quality control checkpoints are integrated throughout the manufacturing process:
- Incoming Quality Control (IQC): Ensures raw materials meet specified requirements before production begins.
- In-Process Quality Control (IPQC): Monitors production processes to detect defects early.
- Final Quality Control (FQC): Conducts thorough inspections and testing of finished products before they are shipped.
B2B buyers should seek suppliers who provide detailed QC documentation, including inspection reports and testing results, to facilitate transparency and build trust.
What Testing Methods Are Commonly Used for Aluminum Quality Assurance?
Several testing methods are employed to validate the quality of aluminum materials:
- Mechanical Testing: Includes tensile strength tests, hardness tests, and impact tests to evaluate the physical properties of the aluminum.
- Chemical Analysis: Confirms the composition of the aluminum to ensure it meets specified grades and standards.
- Non-Destructive Testing (NDT): Techniques such as ultrasonic and radiographic testing identify internal defects without damaging the material.
Buyers should request information about the testing methods used by suppliers to ensure they align with industry standards and requirements.
How Can B2B Buyers Verify Supplier Quality Control Practices?
To ensure reliable quality control, B2B buyers can take several steps:
- Conduct Audits: Regular audits of suppliers can help verify compliance with quality standards and manufacturing processes.
- Request Reports: Suppliers should provide documentation of their quality control measures, including inspection and testing reports.
- Engage Third-Party Inspectors: Utilizing independent inspection services can provide an unbiased assessment of a supplier’s quality practices.
For buyers from regions like Africa and South America, where supply chain risks may be higher, these practices are essential for ensuring product quality and reliability.
What Are the QC and Certification Nuances for International B2B Buyers?
When sourcing aluminum materials, international B2B buyers must be aware of the nuances in quality control and certification processes that vary by region.
- Regional Compliance: Different markets may have distinct regulatory requirements, such as EU regulations for buyers in Europe or local standards in Africa and South America.
- Supplier Certifications: Certifications from recognized bodies can serve as a benchmark for supplier credibility, but buyers should verify the legitimacy and relevance of these certifications.
Understanding these nuances can significantly influence purchasing decisions and long-term supplier relationships, ensuring that buyers receive high-quality aluminum materials tailored to their specific needs.
Practical Sourcing Guide: A Step-by-Step Checklist for ‘types of aluminium materials’
In the fast-paced world of international B2B procurement, sourcing the right types of aluminum materials is crucial for ensuring product quality and operational efficiency. This guide provides a step-by-step checklist to help buyers navigate the complexities of aluminum sourcing, particularly for businesses operating in Africa, South America, the Middle East, and Europe.
Step 1: Define Your Technical Specifications
Before initiating the sourcing process, it’s essential to clearly outline your technical requirements. Identify the specific aluminum grade (such as 1100, 3003, or 6061) based on the application, whether it’s for structural components, packaging, or industrial uses. Consider the mechanical properties, corrosion resistance, and thermal conductivity needed for your project to ensure you select the right material.
Step 2: Research Available Aluminum Grades and Their Applications
Understanding the various grades of aluminum and their respective applications is vital. The 1000 series, for instance, offers excellent corrosion resistance, making it suitable for food processing, while the 6061 grade is ideal for high-stress applications due to its strength and weldability. Familiarize yourself with these characteristics to make informed decisions that align with your project needs.
Step 3: Evaluate Potential Suppliers
Before committing to a supplier, it’s crucial to conduct thorough evaluations. Request company profiles, case studies, and references from businesses in similar industries or regions. Verify their production capabilities and whether they can meet your specific technical requirements. Look for suppliers with a solid reputation and proven track record in aluminum supply.
Step 4: Verify Supplier Certifications and Compliance
Ensure that your selected suppliers have the necessary certifications and comply with international quality standards. Check for ISO certifications, which indicate that the supplier adheres to rigorous quality management practices. This is particularly important when sourcing materials for industries that require strict compliance, such as aerospace or food processing.
Step 5: Request Samples and Conduct Quality Testing
Before placing a bulk order, request samples of the aluminum materials to assess their quality. Conduct tests to verify that the samples meet your specifications, including checks for strength, corrosion resistance, and thermal conductivity. This step helps mitigate risks associated with material defects that could impact your final products.
Step 6: Negotiate Terms and Pricing
Once you’ve selected a supplier, engage in negotiations regarding pricing, delivery schedules, and payment terms. Understanding the market rates for various aluminum grades can empower you during negotiations, ensuring you secure competitive pricing while maintaining quality. Consider factors such as shipping costs and lead times that may affect your overall procurement budget.
Step 7: Establish a Communication Plan
Effective communication with your supplier is crucial for successful sourcing. Establish a clear communication plan that includes regular updates on order status, potential delays, and any changes in specifications. A proactive approach ensures that both parties remain aligned throughout the sourcing process, leading to better outcomes and reduced misunderstandings.
By following this checklist, international B2B buyers can effectively navigate the complexities of sourcing aluminum materials, ensuring they obtain the right products for their specific needs while fostering strong supplier relationships.
Comprehensive Cost and Pricing Analysis for types of aluminium materials Sourcing
What Are the Key Cost Components in Sourcing Aluminum Materials?
When sourcing aluminum materials, understanding the cost structure is crucial for making informed purchasing decisions. The total cost typically comprises several components:
-
Material Costs: This is the primary expense and varies significantly based on the aluminum grade (e.g., 1100, 3003, 6061) and current market prices. Pure aluminum generally costs more than alloys but offers distinct advantages in certain applications.
-
Labor: Labor costs include wages for workers involved in manufacturing and processing the aluminum. Regions with lower labor costs, such as parts of Africa and South America, can offer competitive pricing, but quality may vary.
-
Manufacturing Overhead: This encompasses the indirect costs associated with production, including utilities, rent, and equipment maintenance. Efficient manufacturing processes can help reduce these costs.
-
Tooling: The cost of tooling is essential for custom orders. Specialized dies and molds can increase the initial investment but may lead to cost savings in large production runs.
-
Quality Control (QC): Ensuring the aluminum meets specified standards involves additional costs. Certifications and testing can enhance the material’s value but add to the overall price.
-
Logistics: Transportation and storage costs can vary greatly, especially for international shipments. Incoterms (International Commercial Terms) play a vital role in determining who bears these costs.
-
Margin: Suppliers typically add a margin to cover their costs and profit, which can vary based on market conditions and competition.
How Do Price Influencers Affect Aluminum Material Sourcing?
Several factors influence the pricing of aluminum materials that buyers must consider:
-
Volume/MOQ (Minimum Order Quantity): Larger orders often qualify for bulk discounts. Buyers should assess their needs carefully to balance inventory costs with potential savings.
-
Specifications and Customization: Custom specifications can increase costs due to additional processing and tooling requirements. Buyers should weigh the necessity of customization against the potential for increased expenses.
-
Material Quality and Certifications: Higher-quality materials that meet specific certifications (like ISO or ASTM) may command higher prices but can also enhance product reliability and marketability.
-
Supplier Factors: The reputation and reliability of the supplier can significantly impact pricing. Established suppliers may charge more but often provide better quality assurance and customer service.
-
Incoterms: Understanding the terms of delivery can affect total costs. Options such as FOB (Free on Board) or CIF (Cost, Insurance, and Freight) dictate who is responsible for shipping costs and risks.
What Negotiation Strategies Can Buyers Use to Enhance Cost Efficiency?
B2B buyers from Africa, South America, the Middle East, and Europe can employ several strategies to improve cost efficiency:
-
Leverage Relationships: Building strong relationships with suppliers can lead to better pricing and terms. Regular communication and feedback can foster trust and collaboration.
-
Negotiate Payment Terms: Flexible payment options, such as extended payment terms, can alleviate cash flow issues. Buyers should negotiate these terms upfront to avoid surprises later.
-
Total Cost of Ownership (TCO): Rather than focusing solely on the purchase price, consider the total cost of ownership, which includes maintenance, operational costs, and potential resale value. This broader perspective can lead to more cost-effective purchasing decisions.
-
Market Research: Staying informed about market trends and price fluctuations can provide leverage during negotiations. Buyers should monitor aluminum prices and supply chain developments to make timely decisions.
Are There Any Pricing Nuances for International B2B Buyers?
International buyers should be aware of specific pricing nuances when sourcing aluminum materials:
-
Currency Fluctuations: Exchange rates can impact costs significantly. Buyers should consider pricing in their local currency to mitigate risks associated with currency fluctuations.
-
Import Duties and Tariffs: Understanding the import regulations of the destination country is crucial. Duties and tariffs can add substantial costs to imported aluminum materials.
-
Cultural Considerations: Different regions may have varying expectations regarding negotiation styles and business practices. Being culturally aware can facilitate smoother transactions and better relationships.
Disclaimer on Indicative Prices
Prices for aluminum materials can fluctuate based on market demand, supplier availability, and geopolitical factors. It is advisable for buyers to seek multiple quotes and conduct thorough due diligence to ensure they are getting competitive pricing tailored to their specific needs.
Alternatives Analysis: Comparing types of aluminium materials With Other Solutions
Understanding Alternative Materials to Types of Aluminium
In the quest for suitable materials, international B2B buyers must often assess the performance and cost-effectiveness of aluminium against other viable alternatives. This analysis will focus on comparing aluminium materials with two notable alternatives: stainless steel and copper. Each material has unique properties, applications, and economic implications, making it essential for buyers to understand their relative advantages and disadvantages.
Comparison Aspect | Types Of Aluminium Materials | Stainless Steel | Copper |
---|---|---|---|
Performance | Lightweight, corrosion-resistant, good thermal conductivity | Strong, corrosion-resistant, but heavier | Excellent thermal and electrical conductivity, but less corrosion-resistant |
Cost | Generally lower-cost, varies by grade | Typically higher due to alloying elements | Moderate, can be expensive depending on purity |
Ease of Implementation | Easy to fabricate and weld, versatile | Requires specialized welding techniques | Easy to work with but can be challenging to solder |
Maintenance | Low maintenance, resistant to rust | Requires periodic cleaning to prevent tarnishing | Regular maintenance needed to prevent oxidation |
Best Use Case | Aerospace, automotive, construction | Kitchen equipment, structural applications | Electrical wiring, plumbing, heat exchangers |
What Are the Advantages and Disadvantages of Stainless Steel Compared to Aluminium?
Stainless steel is renowned for its strength and durability. It is often used in applications that require resistance to extreme conditions, including high temperatures and corrosive environments. Its composition allows it to withstand wear and tear, making it a preferred choice in the food and beverage industry, as well as in construction. However, its heavier weight can be a drawback in applications where weight savings are critical. Additionally, the higher cost of stainless steel compared to aluminium may deter budget-conscious buyers.
How Does Copper Stack Up Against Aluminium in Terms of Applications?
Copper is well-known for its excellent electrical and thermal conductivity, making it indispensable in electrical wiring and heat exchangers. Its malleability allows for easy shaping and forming. However, copper’s susceptibility to corrosion, particularly in moist environments, can limit its lifespan without proper treatment. Additionally, while copper can be cost-effective, high-purity copper can be quite expensive, making it less suitable for large-scale applications where budget is a concern.
Conclusion: Choosing the Right Material for Your B2B Needs
When selecting between aluminium and its alternatives, international B2B buyers must consider their specific application requirements, budget constraints, and long-term maintenance implications. Aluminium is often the go-to choice for projects requiring lightweight materials with good corrosion resistance at a lower cost. However, for applications demanding exceptional strength or conductivity, stainless steel and copper may be more appropriate despite their higher costs or maintenance needs. Conducting a thorough analysis based on these factors will empower buyers to make informed decisions that align with their operational goals.
Essential Technical Properties and Trade Terminology for types of aluminium materials
What Are the Key Technical Properties of Aluminium Materials for B2B Buyers?
When considering aluminium materials for procurement, understanding their technical properties is crucial for making informed purchasing decisions. Here are some of the essential specifications to keep in mind:
-
Material Grade
Aluminium is categorized into various grades based on its composition and properties. For example, the 1100 series is known for its excellent workability, while the 6061 series offers superior strength and corrosion resistance. Selecting the appropriate grade is vital as it directly affects the performance of the product in its intended application. -
Tensile Strength
This property measures how much force a material can withstand while being stretched or pulled before breaking. For B2B buyers, tensile strength is a critical consideration, especially for applications requiring durability and reliability, such as structural components in construction or automotive parts. -
Corrosion Resistance
Aluminium naturally forms a protective oxide layer, making it inherently resistant to corrosion. However, different alloys can offer varying levels of resistance. Buyers should assess the environmental conditions where the material will be used—such as exposure to saltwater or industrial chemicals—to ensure long-lasting performance. -
Thermal Conductivity
This property indicates how well a material can conduct heat. Aluminium is known for its high thermal conductivity, which is particularly advantageous in applications like heat exchangers and cooking utensils. Understanding this property helps buyers select materials that can efficiently manage heat transfer in their specific applications. -
Workability
This refers to how easily a material can be shaped and formed. Some aluminium alloys, such as 1100, are highly malleable, making them suitable for intricate designs. For B2B buyers, assessing workability can lead to cost savings in manufacturing and quicker production timelines. -
Weight-to-Strength Ratio
Aluminium is prized for its lightweight nature while maintaining a high strength-to-weight ratio. This characteristic is particularly important in industries like aerospace and automotive, where reducing weight can lead to improved fuel efficiency and performance.
What Are Common Trade Terms Related to Aluminium Materials?
Familiarity with industry terminology can enhance communication and streamline transactions. Here are some commonly used terms that B2B buyers should know:
-
OEM (Original Equipment Manufacturer)
This term refers to companies that produce parts and equipment that may be marketed by another manufacturer. Understanding OEM relationships can help buyers identify reliable suppliers who meet specific quality standards and requirements. -
MOQ (Minimum Order Quantity)
MOQ is the smallest quantity of a product that a supplier is willing to sell. Knowing the MOQ is essential for B2B buyers to gauge whether a supplier can meet their needs without overcommitting resources. -
RFQ (Request for Quotation)
An RFQ is a document sent to suppliers to solicit price quotes for specified products or services. This process helps buyers compare costs and make informed purchasing decisions based on competitive pricing. -
Incoterms (International Commercial Terms)
These are a set of predefined commercial terms published by the International Chamber of Commerce (ICC) that define the responsibilities of sellers and buyers in international transactions. Understanding Incoterms is crucial for managing logistics and ensuring compliance with international shipping regulations. -
Fabrication
This term encompasses the processes involved in constructing products from raw materials. For B2B buyers, knowing about fabrication capabilities can help them choose suppliers who can deliver tailored solutions to their specific needs. -
Alloying Elements
These are metals added to aluminium to enhance its properties. Common alloying elements include copper, magnesium, and zinc. Understanding the role of these elements can assist buyers in selecting the right aluminium grade for their applications, ensuring optimal performance and cost-effectiveness.
By comprehensively understanding these technical properties and trade terminologies, international B2B buyers can better navigate the complexities of aluminium procurement, leading to successful purchasing outcomes.
Navigating Market Dynamics and Sourcing Trends in the types of aluminium materials Sector
What Are the Key Market Dynamics and Trends in the Aluminium Materials Sector?
The aluminium materials sector is experiencing significant growth due to increasing global demand across various industries such as construction, automotive, and aerospace. Key drivers include the lightweight nature of aluminium, which enhances fuel efficiency in vehicles and reduces transportation costs. Additionally, the rise of electric vehicles (EVs) is pushing for more lightweight materials, fostering innovation in aluminium alloys, particularly the 6000 and 7000 series, which offer improved strength and corrosion resistance.
Emerging B2B technology trends are also reshaping the sourcing landscape. Digital platforms for procurement are becoming prevalent, allowing international buyers to compare prices, assess supplier reliability, and streamline logistics. Blockchain technology is gaining traction for ensuring transparency in supply chains, critical for managing international transactions. For buyers from Africa, South America, the Middle East, and Europe, understanding these technologies can optimize sourcing strategies and reduce lead times.
In terms of market dynamics, the competitive landscape is evolving with increased participation from emerging markets. Countries in Africa and South America are ramping up aluminium production, driven by local demand and export opportunities. For instance, Nigeria is developing its aluminium sector to cater to both domestic and international markets. Buyers should be aware of regional suppliers that can offer competitive pricing and shorter delivery times, thus enhancing their supply chain resilience.
How Can International B2B Buyers Ensure Sustainability and Ethical Sourcing of Aluminium Materials?
Sustainability is becoming a crucial consideration in the aluminium materials sector, as the environmental impact of mining and refining processes is significant. The aluminium industry is taking steps towards reducing its carbon footprint by investing in more efficient manufacturing technologies and recycling processes. For international B2B buyers, sourcing recycled aluminium can significantly mitigate environmental impact, as recycled aluminium uses 95% less energy compared to primary production.
The importance of ethical supply chains cannot be overstated, especially for buyers in regions where sourcing practices may not always align with global sustainability standards. Certifications such as ISO 14001 for environmental management and the Aluminium Stewardship Initiative (ASI) certification ensure that suppliers adhere to responsible production practices. Buyers should prioritize suppliers that possess these certifications, as they reflect a commitment to sustainable practices and ethical sourcing.
Moreover, engaging with suppliers who utilize ‘green’ materials or have invested in renewable energy sources for their operations can enhance a company’s sustainability profile. As consumers increasingly demand eco-friendly products, aligning procurement strategies with sustainability goals can not only improve brand reputation but also drive long-term business success.
What Is the Historical Context of Aluminium Materials in B2B Sourcing?
The use of aluminium dates back to the early 19th century, but its commercial viability was established with the Hall-Héroult process in 1886, which enabled large-scale production. Initially, aluminium was seen as a luxury material, but advancements in extraction and refining techniques have made it more accessible and cost-effective.
Historically, aluminium’s lightweight and corrosion-resistant properties made it a favored choice in industries such as aviation and transportation. The post-World War II era witnessed a surge in aluminium applications, as it became integral to the automotive and construction sectors. In recent years, the focus has shifted towards enhancing the material properties through the development of various aluminium alloys, which cater to specific industry needs.
Understanding this historical evolution is essential for international B2B buyers, as it highlights the material’s adaptability and growing importance in modern manufacturing. With the ongoing advancements in technology and increasing emphasis on sustainability, aluminium continues to be a pivotal material in global trade.
Frequently Asked Questions (FAQs) for B2B Buyers of types of aluminium materials
-
How do I solve challenges in sourcing the right aluminum materials for my project?
To effectively address sourcing challenges, start by defining your project requirements, including specifications such as grade, thickness, and intended application. Research suppliers with a proven track record in your region, focusing on those with certifications and quality assurance processes. Utilize platforms that connect buyers and suppliers, and consider attending trade shows to establish direct relationships. Always request samples to evaluate material quality before committing to larger orders. -
What is the best aluminum grade for high-corrosion environments?
For applications in high-corrosion environments, aluminum grade 6061 is often recommended due to its superior corrosion resistance compared to other grades. This alloy is particularly effective for structural applications and marine environments, making it ideal for components exposed to moisture or chemicals. Always consult with your supplier to ensure the selected grade aligns with your specific environmental conditions and mechanical requirements. -
How can I verify the quality of aluminum materials before purchasing?
To verify quality, request certificates of compliance from your supplier, which should detail the material’s properties and compliance with industry standards. Additionally, ask for third-party testing results that confirm the mechanical and chemical properties of the aluminum. Conducting your own quality checks through independent labs can also provide peace of mind. Establishing clear communication with your supplier about quality expectations is crucial. -
What are the minimum order quantities (MOQs) for aluminum materials in international trade?
Minimum order quantities for aluminum materials can vary significantly based on the supplier and the specific alloy grade. Generally, MOQs can range from a few hundred kilograms to several tons. When sourcing internationally, it’s essential to clarify MOQs with your supplier early in discussions. Some suppliers may offer flexibility for first-time buyers or smaller businesses, so negotiate terms that suit your needs. -
What payment terms should I expect when sourcing aluminum from international suppliers?
Payment terms can vary widely but typically include options such as upfront payment, letters of credit, or payment upon delivery. It is advisable to negotiate terms that mitigate risk, such as partial payments upfront and the balance upon delivery. Additionally, ensure that the payment methods you choose are secure and provide recourse in case of disputes. Understanding the currency exchange implications is also crucial when dealing with international transactions. -
How do I choose the right supplier for aluminum materials?
Selecting the right supplier involves evaluating their experience, reputation, and product quality. Look for suppliers with industry certifications and positive reviews from previous clients. Establish communication to gauge their responsiveness and willingness to accommodate your specific needs. Visiting their facilities or requesting virtual tours can provide insights into their operations and quality control practices. Building a relationship with your supplier can also lead to better service and terms. -
What logistics considerations should I keep in mind when importing aluminum materials?
Logistics for importing aluminum should encompass shipping methods, customs regulations, and lead times. Choose a reliable freight forwarder familiar with your destination’s import requirements. Ensure you understand tariff classifications and potential duties that may apply. Additionally, factor in the lead time for manufacturing, shipping, and customs clearance to avoid delays. Maintaining clear communication with your supplier about shipping timelines is essential for planning. -
Can I customize aluminum materials to fit specific project requirements?
Yes, many suppliers offer customization options for aluminum materials, including cuts, shapes, and alloy grades tailored to your project specifications. Discuss your requirements in detail with potential suppliers to determine their capabilities in customization. Be prepared to provide drawings or samples to convey your needs effectively. Keep in mind that customized orders may have different lead times and minimum order quantities compared to standard products.
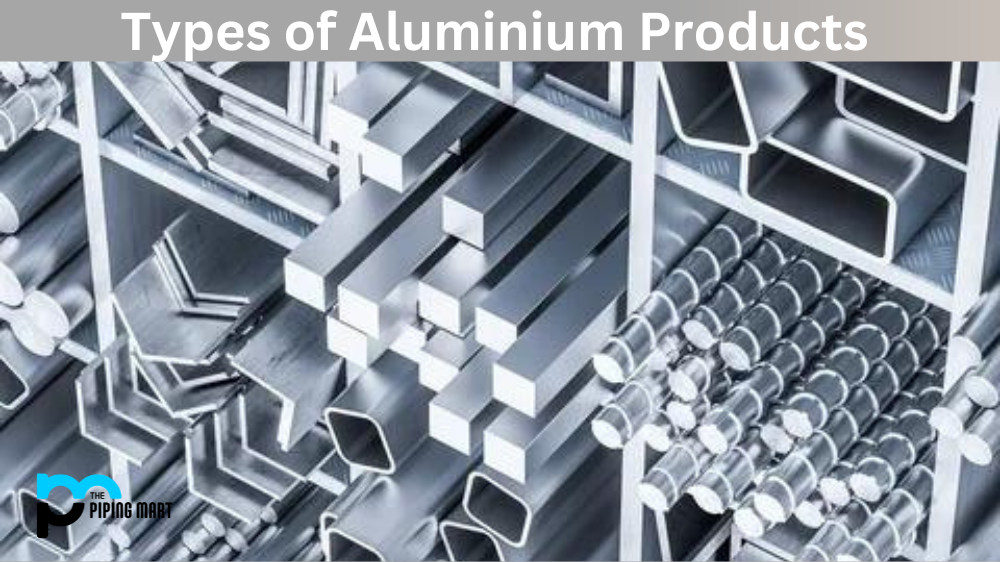
A stock image related to types of aluminium materials.
Important Disclaimer & Terms of Use
⚠️ Important Disclaimer
The information provided in this guide, including content regarding manufacturers, technical specifications, and market analysis, is for informational and educational purposes only. It does not constitute professional procurement advice, financial advice, or legal advice.
While we have made every effort to ensure the accuracy and timeliness of the information, we are not responsible for any errors, omissions, or outdated information. Market conditions, company details, and technical standards are subject to change.
B2B buyers must conduct their own independent and thorough due diligence before making any purchasing decisions. This includes contacting suppliers directly, verifying certifications, requesting samples, and seeking professional consultation. The risk of relying on any information in this guide is borne solely by the reader.
Strategic Sourcing Conclusion and Outlook for types of aluminium materials
In navigating the diverse landscape of aluminum materials, international B2B buyers must prioritize strategic sourcing to harness the advantages of various aluminum grades. Understanding the unique properties of alloys such as 1100, 3003, and 6061 is essential for selecting the right material for specific applications. For instance, while 1100 aluminum offers excellent workability for food processing, 6061 is preferred in demanding structural applications due to its enhanced strength and corrosion resistance.
How Can Strategic Sourcing Enhance Your Supply Chain?
Strategic sourcing not only ensures access to high-quality materials but also fosters long-term relationships with reliable suppliers, particularly crucial in regions like Africa, South America, the Middle East, and Europe. By leveraging local and global supply chains, buyers can mitigate risks related to price volatility and material shortages.
What’s Next for International B2B Buyers in Aluminum Sourcing?
As industries evolve, the demand for sustainable and high-performance materials will only increase. Buyers are encouraged to stay informed about market trends and innovations in aluminum production to make proactive sourcing decisions. Embrace the opportunity to collaborate with suppliers who prioritize sustainability and quality, ensuring your operations are not only efficient but also environmentally responsible. By doing so, you position your business for success in the competitive global market.