Unlock Cost Savings: The Ultimate Polyethylene Tank Guide (2025)
Introduction: Navigating the Global Market for polyethylene tank
Navigating the complexities of sourcing polyethylene tanks can be a significant challenge for international B2B buyers, especially when considering the diverse requirements of various industries. Whether you are in agriculture, water treatment, or chemical storage, understanding the different types of polyethylene tanks available—such as vertical, conical, and double-wall tanks—is crucial for making informed purchasing decisions. This guide offers a comprehensive overview of the polyethylene tank market, highlighting essential aspects such as applications, supplier vetting processes, pricing strategies, and regulatory compliance.
By addressing these critical factors, we aim to empower buyers from regions including Africa, South America, the Middle East, and Europe—countries like Argentina and Italy—by providing actionable insights that facilitate effective procurement. With over 15,500 types of tanks available globally, including options tailored for specific gravity and chemical compatibility, knowing what to look for can streamline your sourcing process.
This guide is designed to equip you with the knowledge needed to confidently select the right polyethylene tank for your operational needs, ensuring optimal performance and compliance with industry standards. By leveraging this information, you can enhance your supply chain efficiency, reduce costs, and ultimately drive your business success in the competitive global market.
Understanding polyethylene tank Types and Variations
Type Name | Key Distinguishing Features | Primary B2B Applications | Brief Pros & Cons for Buyers |
---|---|---|---|
Vertical Storage Tanks | Tall, cylindrical design for bulk storage | Water, chemicals, and agricultural use | Pros: Efficient space utilization, easy access to contents. Cons: Limited drainage options. |
Double Wall Tanks | Features an outer wall for secondary containment | Chemical storage, hazardous materials | Pros: Enhanced safety, reduced risk of leaks. Cons: Higher initial cost. |
Conical Bottom Tanks | Cone-shaped bottom for complete drainage | Waste collection, agricultural runoff | Pros: Efficient drainage, ideal for viscous materials. Cons: May require more space. |
Rectangular Tanks | Flat sides, often stackable for space efficiency | RVs, marine applications, food service | Pros: Versatile, space-saving design. Cons: Limited capacity compared to cylindrical tanks. |
Chemical Injection Tanks | Designed specifically for chemical dosing and mixing | Water treatment, industrial processes | Pros: Customizable for specific chemicals, precise control. Cons: Requires careful maintenance. |
What Are Vertical Storage Tanks and Their Key Applications?
Vertical storage tanks are designed for bulk storage, featuring a tall and cylindrical shape that maximizes vertical space. These tanks are commonly used in various industries, including water treatment, agriculture, and chemical storage. When considering a vertical tank, buyers should assess the tank’s capacity and the materials it can safely store. Additionally, the ease of access to the tank’s contents can impact operational efficiency, making this a crucial factor for B2B buyers.
How Do Double Wall Tanks Enhance Safety in Chemical Storage?
Double wall tanks are engineered with an outer wall that provides an additional layer of containment, making them ideal for storing hazardous materials. This design significantly reduces the risk of leaks and environmental contamination, which is critical for industries dealing with chemicals. Buyers should evaluate the tank’s certifications and the materials used in construction, as these factors influence safety and compliance with regulations. While the initial investment may be higher, the long-term benefits in safety and reduced liability are substantial.
Why Choose Conical Bottom Tanks for Efficient Drainage?
Conical bottom tanks are characterized by their cone-shaped bases, which facilitate complete drainage of liquids. This design is particularly beneficial for applications involving waste collection and agricultural runoff, where residue removal is essential. B2B buyers should consider the tank’s size and the type of materials it will handle. While conical tanks offer excellent drainage capabilities, they may require more space compared to traditional tanks, which is a crucial consideration for operational logistics.
What Are the Advantages of Rectangular Tanks in Various Industries?
Rectangular tanks are known for their flat sides, which allow for stacking and efficient use of space. These tanks are versatile and find applications in RVs, marine environments, and food service industries. When purchasing rectangular tanks, buyers should focus on the dimensions and how they fit within existing infrastructure. Although they may have a lower capacity compared to cylindrical tanks, their design can be advantageous for companies with space constraints.
How Do Chemical Injection Tanks Support Industrial Processes?
Chemical injection tanks are specifically designed for the accurate dosing and mixing of chemicals in processes such as water treatment and various industrial applications. These tanks can be customized to meet the specific needs of different chemicals, allowing for precise control over chemical concentrations. B2B buyers should prioritize tanks that come with robust safety features and consider ongoing maintenance requirements to ensure operational efficiency. While they can be more complex than standard tanks, the benefits of enhanced dosing accuracy can justify the investment.
Key Industrial Applications of polyethylene tank
Industry/Sector | Specific Application of Polyethylene Tank | Value/Benefit for the Business | Key Sourcing Considerations for this Application |
---|---|---|---|
Agriculture | Fertilizer and Pesticide Storage | Safe and efficient storage of chemicals, reducing spills and contamination risks. | Ensure compliance with local regulations on chemical storage; consider tank size based on operational needs. |
Water Treatment | Water Storage and Distribution | Reliable storage solution for potable water, enhancing supply chain integrity. | Look for NSF/ANSI certification for potable water; assess tank durability against local climate conditions. |
Chemical Processing | Chemical Storage Tanks | Secure containment of hazardous materials, minimizing environmental impact. | Evaluate the tank’s chemical compatibility and secondary containment features. |
Oil and Gas | Waste Oil Collection Tanks | Efficient and safe collection of used oils, facilitating recycling and compliance. | Check for certifications regarding hazardous waste; consider tank mobility for various site requirements. |
Aquaculture | Fish Farming and Aquaponics Tanks | Optimal water management and quality control, promoting healthy aquatic life. | Assess tank size and shape for specific aquatic species; consider options for water aeration and filtration. |
How Are Polyethylene Tanks Used in Agriculture?
In the agriculture sector, polyethylene tanks are essential for storing fertilizers and pesticides. These tanks provide a safe and efficient solution for managing agricultural chemicals, significantly reducing the risk of spills and environmental contamination. For international buyers, particularly in regions like Africa and South America, it’s crucial to ensure that tanks meet local regulations regarding chemical storage. Additionally, the size of the tank should align with the scale of agricultural operations to optimize logistics and reduce costs.
What Role Do Polyethylene Tanks Play in Water Treatment?
Water treatment facilities utilize polyethylene tanks for the safe storage and distribution of potable water. These tanks are designed to maintain water quality, ensuring that it meets health standards. For buyers in the Middle East and Europe, sourcing tanks with NSF/ANSI certification is vital to guarantee the safety of drinking water. Moreover, understanding the durability of the tank against local climate conditions can prevent premature wear and prolong service life.
How Are Polyethylene Tanks Utilized in Chemical Processing?
In chemical processing, polyethylene tanks serve as storage solutions for hazardous materials. They are engineered to provide secure containment, which minimizes the risk of leaks and environmental damage. Buyers should prioritize tanks that offer secondary containment features and compatibility with specific chemicals being stored. This is particularly important for international buyers in regions with strict environmental regulations, ensuring compliance and safety in operations.
Why Are Polyethylene Tanks Important for Oil and Gas Industries?
The oil and gas sector employs polyethylene tanks for waste oil collection, facilitating the recycling of used oils while adhering to environmental regulations. These tanks are designed to handle hazardous materials safely, which is critical for compliance with local laws. International buyers should verify the tank’s certifications related to hazardous waste and consider the mobility of the tanks, especially for operations that may require relocation.
What Benefits Do Polyethylene Tanks Provide in Aquaculture?
In aquaculture, polyethylene tanks are used for fish farming and aquaponics, enabling optimal water management and quality control. These tanks support the health of aquatic life by maintaining stable environmental conditions. Buyers should assess the size and shape of the tanks based on the specific species being cultivated, and consider additional features such as aeration and filtration systems. This is particularly relevant for buyers in regions like South America and Africa, where aquaculture is a growing industry.
3 Common User Pain Points for ‘polyethylene tank’ & Their Solutions
Scenario 1: Insufficient Tank Capacity for Growing Operations
The Problem: Many businesses, especially in sectors like agriculture or chemical processing, find themselves constrained by inadequate tank capacity. As their operations expand or as demand fluctuates, existing polyethylene tanks may no longer meet their storage requirements. This can lead to overflows, inefficient operations, or even operational shutdowns, resulting in lost revenue and customer dissatisfaction. Additionally, purchasing new tanks can be a complicated process, often involving significant lead times and logistical challenges.
The Solution: To address capacity challenges, B2B buyers should conduct a thorough analysis of their current and projected storage needs. It’s essential to engage with suppliers who offer a wide range of polyethylene tank sizes, including large-capacity options like 15,000-gallon tanks for industrial applications. When sourcing, consider suppliers that provide customizable solutions to match specific operational requirements, such as double-walled tanks for enhanced safety and compliance. To streamline logistics, establish a relationship with a supplier that offers quick shipping options, ideally within 8-10 weeks, to minimize downtime during transitions. Additionally, implementing inventory management software can help forecast future needs and optimize ordering schedules.
Scenario 2: Chemical Compatibility Concerns with Polyethylene Tanks
The Problem: A significant concern for many B2B buyers is ensuring that polyethylene tanks are compatible with the chemicals they intend to store. Chemical reactions can compromise tank integrity, leading to leaks and environmental hazards. Buyers in industries such as pharmaceuticals or food processing must ensure that their storage solutions adhere to strict regulations and quality standards, which can often be a daunting task.
The Solution: To mitigate compatibility issues, buyers should proactively consult with manufacturers who specialize in chemical storage solutions. It’s crucial to verify that the polyethylene used is suitable for the specific chemicals involved, particularly when dealing with aggressive substances. Suppliers like Poly Processing offer extensive resources that outline material compatibility for their tanks, which can serve as a valuable guide. Additionally, investing in high-density cross-linked polyethylene (XLPE) tanks can enhance durability and reliability, as they are engineered to withstand a broader range of chemicals. Regular training for staff on safe handling and storage practices can further reduce risks associated with chemical compatibility.
Scenario 3: Maintenance and Longevity of Polyethylene Tanks
The Problem: Many companies struggle with the maintenance and longevity of their polyethylene tanks. Over time, exposure to environmental factors such as UV light, temperature fluctuations, and chemical exposure can lead to degradation and failure. This not only results in costly replacements but can also create safety hazards and compliance issues with environmental regulations, especially in regions like Africa and South America where regulations may be evolving.
The Solution: To enhance the lifespan of polyethylene tanks, B2B buyers should focus on regular maintenance practices and the selection of high-quality products. When purchasing, look for tanks that come with manufacturer warranties, typically ranging from 3 to 5 years, as this can indicate quality and durability. Establishing a routine inspection schedule to check for signs of wear, such as cracks or discoloration, can help catch potential issues early. Additionally, consider investing in UV-resistant coatings or covers to protect tanks from sunlight exposure, especially in regions with high UV levels. Collaborating with suppliers who offer maintenance support or training can further empower teams to proactively manage tank care, ultimately extending their operational life and reducing long-term costs.
Strategic Material Selection Guide for polyethylene tank
What Are the Key Properties of Common Materials Used in Polyethylene Tanks?
When selecting materials for polyethylene tanks, it is essential to consider their properties, performance under various conditions, and suitability for specific applications. Below are analyses of several common materials used in the manufacturing of polyethylene tanks.
High-Density Polyethylene (HDPE)
Key Properties: HDPE is known for its high strength-to-density ratio, excellent impact resistance, and good chemical resistance. It typically has a temperature rating of up to 120°C (248°F) and can withstand moderate pressure.
Pros & Cons: The durability of HDPE makes it a popular choice for various liquid storage applications. It is relatively cost-effective and easy to manufacture, which reduces overall production costs. However, HDPE can be susceptible to UV degradation if not treated, limiting its outdoor applications unless properly coated.
Impact on Application: HDPE tanks are suitable for storing a wide range of chemicals and liquids, including water, agricultural products, and some industrial chemicals. However, it may not be compatible with certain solvents or high-temperature materials.
Considerations for International Buyers: Buyers in regions such as Africa and South America should ensure that HDPE tanks comply with local regulations and standards, such as ASTM or ISO certifications. In Europe, adherence to EU regulations regarding chemical storage is crucial.
Cross-Linked Polyethylene (XLPE)
Key Properties: XLPE offers superior chemical resistance, temperature tolerance (up to 80°C or 176°F), and excellent structural integrity. It is less permeable than standard polyethylene, making it ideal for hazardous materials.
Pros & Cons: The primary advantage of XLPE is its durability and resistance to environmental stress cracking. However, it is more expensive to manufacture than HDPE, which can increase the overall cost of the tank.
Impact on Application: XLPE is particularly effective for storing aggressive chemicals and high-purity liquids, making it suitable for industrial applications. Its higher strength allows for thinner tank walls without compromising safety.
Considerations for International Buyers: Buyers should verify that XLPE tanks meet specific industry standards, such as NSF/ANSI/CAN 61 for potable water storage. Compliance with local regulations in the Middle East and Europe is also necessary to ensure safety and environmental protection.
Polypropylene (PP)
Key Properties: Polypropylene has a melting point of around 160°C (320°F) and is known for its excellent resistance to chemical solvents, bases, and acids. It also has a lower density compared to HDPE.
Pros & Cons: The lightweight nature of polypropylene makes it easier to handle and transport. However, it is generally less impact-resistant than HDPE and may not be suitable for high-stress environments.
Impact on Application: Polypropylene tanks are ideal for storing aggressive chemicals, such as acids and alkalis, making them suitable for the chemical and pharmaceutical industries. However, they may not be suitable for long-term outdoor use without UV protection.
Considerations for International Buyers: Buyers in regions like Italy should ensure that polypropylene tanks comply with food safety regulations if used for food storage. Understanding local chemical compatibility standards is also essential.
Polyvinyl Chloride (PVC)
Key Properties: PVC is known for its excellent chemical resistance and can handle temperatures up to 60°C (140°F). It is also highly resistant to corrosion.
Pros & Cons: The affordability and ease of installation of PVC tanks make them attractive for many applications. However, PVC can become brittle over time, especially when exposed to UV light, which can limit its lifespan.
Impact on Application: PVC tanks are commonly used for water storage and certain chemical applications. They are not suitable for high-temperature liquids or long-term outdoor storage without protective measures.
Considerations for International Buyers: Buyers from South America should be aware of the specific regulations regarding PVC use in chemical storage. Compliance with local standards, such as DIN or JIS, is crucial for ensuring safety and reliability.
Summary Table of Material Selection for Polyethylene Tanks
Material | Typical Use Case for polyethylene tank | Key Advantage | Key Disadvantage/Limitation | Relative Cost (Low/Med/High) |
---|---|---|---|---|
High-Density Polyethylene (HDPE) | Water and agricultural liquid storage | Cost-effective and durable | UV degradation potential | Low |
Cross-Linked Polyethylene (XLPE) | Hazardous chemical storage | Superior chemical resistance | Higher manufacturing cost | High |
Polypropylene (PP) | Chemical and pharmaceutical applications | Lightweight and chemical-resistant | Less impact-resistant | Medium |
Polyvinyl Chloride (PVC) | Water storage and some chemicals | Affordable and easy to install | Brittleness over time | Low |
This strategic material selection guide provides international B2B buyers with essential insights into the various materials available for polyethylene tanks, enabling informed purchasing decisions tailored to specific applications and regulatory environments.
In-depth Look: Manufacturing Processes and Quality Assurance for polyethylene tank
What Are the Key Stages in the Manufacturing Process of Polyethylene Tanks?
The manufacturing of polyethylene tanks is a multi-stage process that ensures the final product meets industry standards for durability and safety. Here’s an in-depth look at the key stages involved:
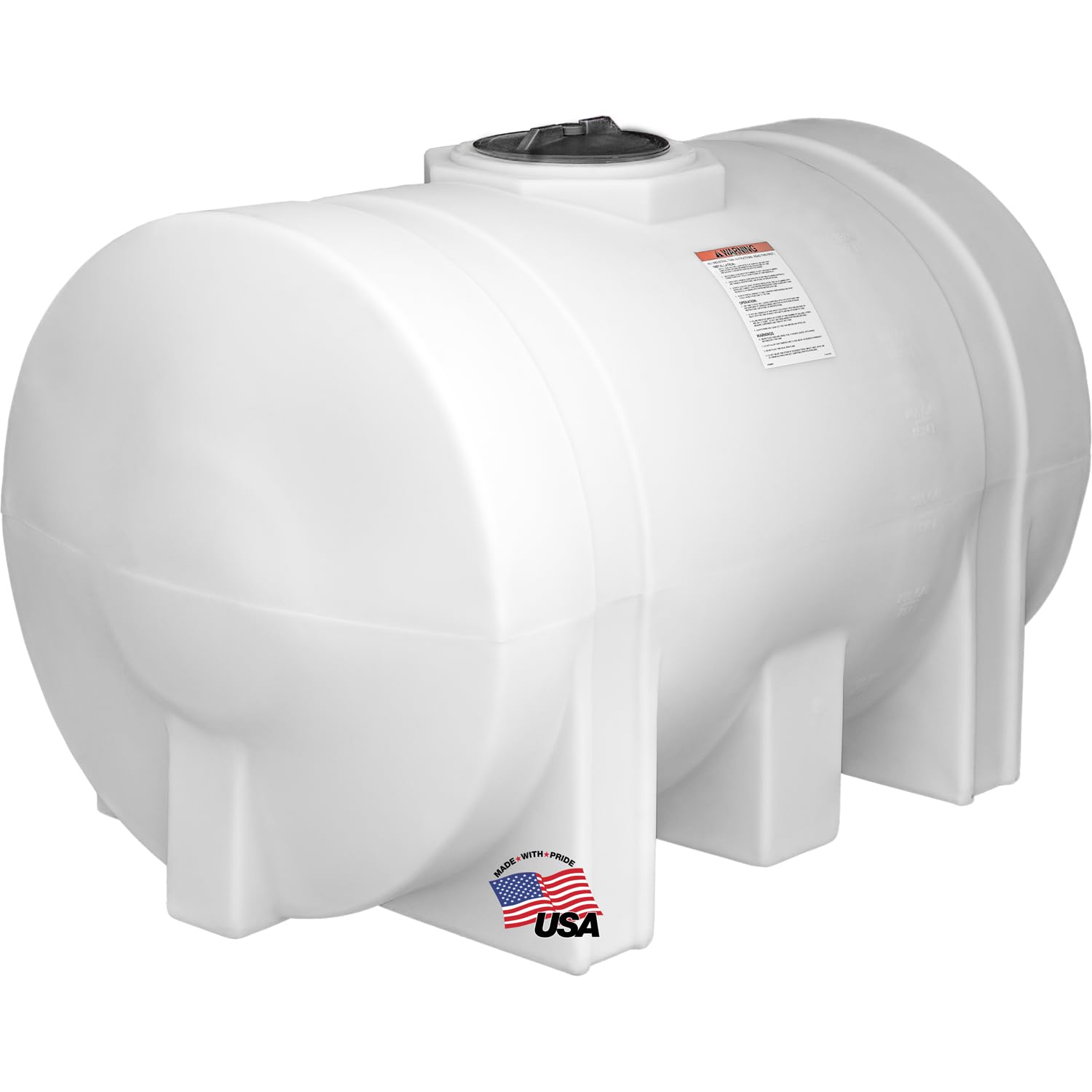
A stock image related to polyethylene tank.
1. Material Preparation
The first stage in manufacturing polyethylene tanks involves sourcing high-density polyethylene (HDPE) or cross-linked polyethylene (XLPE) materials. These materials are chosen for their strength, chemical resistance, and durability. Suppliers should verify that the materials meet relevant international standards, such as ASTM or ISO specifications.
- Sourcing and Quality Control: Ensure that suppliers conduct incoming quality control (IQC) to assess raw materials before use. Buyers should ask for material certification to confirm compliance with industry standards.
2. Forming the Tank
The forming process can vary depending on the specific design and application of the tank. Common techniques include:
-
Rotational Molding: This method involves placing powdered polyethylene in a mold, which is then heated and rotated. As the powder melts, it coats the inside of the mold, creating a seamless tank. This process is ideal for larger tanks and ensures uniform wall thickness.
-
Blow Molding: Used for smaller, hollow tanks, this technique involves inflating a heated plastic tube until it conforms to the shape of the mold. This method is efficient for high-volume production.
-
Injection Molding: Although less common for large tanks, this technique is used for smaller components or accessories associated with tanks.
3. Assembly
Once the tank components are formed, they are assembled, if necessary. For tanks requiring additional features such as fittings or valves, this stage involves:
-
Welding and Joining: Components may be welded using hot air or extrusion welding techniques to ensure a secure and leak-proof joint. Buyers should inquire about the welding standards used by suppliers.
-
Quality Checks During Assembly: In-process quality control (IPQC) is crucial at this stage. Regular inspections should be conducted to ensure that all components meet design specifications and quality standards.
4. Finishing
The finishing stage includes surface treatments and final inspections to ensure the tanks are ready for shipment. This may involve:
-
Surface Cleaning: Removing any contaminants that could affect the tank’s performance or appearance.
-
UV Stabilization: Applying additives to improve resistance to UV degradation, especially important for tanks that will be used outdoors.
-
Final Quality Control (FQC): Conducting final inspections to ensure that the tanks meet all specifications and standards before shipping.
What Quality Assurance Practices Should B2B Buyers Expect?
Quality assurance is crucial in ensuring that polyethylene tanks are safe, reliable, and compliant with relevant standards. Here are some key practices that B2B buyers should look for:
1. Compliance with International Standards
Manufacturers should adhere to recognized international standards such as:
-
ISO 9001: This standard focuses on quality management systems and continuous improvement. Buyers should request certification to ensure that the manufacturer has implemented a quality management system.
-
CE Marking: For products sold in the European market, CE marking indicates compliance with health, safety, and environmental protection standards.
-
API Standards: Particularly relevant for tanks used in the oil and gas industry, API standards ensure that tanks meet specific performance and safety criteria.
2. Key Quality Control Checkpoints
Quality control checkpoints throughout the manufacturing process include:
-
Incoming Quality Control (IQC): Verification of raw materials upon arrival.
-
In-Process Quality Control (IPQC): Regular checks during the manufacturing process to ensure adherence to specifications.
-
Final Quality Control (FQC): Comprehensive testing and inspection of the finished product.
3. Common Testing Methods for Polyethylene Tanks
Testing methods to ensure quality and safety include:
-
Hydrostatic Testing: Assessing the tank’s ability to hold liquid without leaks.
-
Impact Resistance Testing: Evaluating the tank’s durability under stress.
-
Chemical Compatibility Testing: Ensuring the tank material is suitable for the intended liquid storage.
How Can B2B Buyers Verify Supplier Quality Control?
To ensure that suppliers meet quality standards, B2B buyers can take several steps:
1. Conduct Supplier Audits
Regular audits of suppliers can provide insights into their manufacturing processes and quality control measures. Buyers should develop a checklist based on industry standards and best practices.
2. Request Quality Assurance Reports
Buyers should request detailed quality assurance reports, including inspection results, testing data, and compliance certifications. These documents should be available upon request and provide transparency regarding the manufacturer’s quality practices.
3. Utilize Third-Party Inspections
Engaging third-party inspection services can provide an independent assessment of the manufacturing process and final products. This can be particularly valuable for international buyers who may not have the resources to conduct on-site audits.
What Are the Quality Control Nuances for International B2B Buyers?
When sourcing polyethylene tanks internationally, buyers from regions such as Africa, South America, the Middle East, and Europe should be aware of specific nuances:
-
Cultural Differences: Understanding local manufacturing practices and quality expectations can aid in effective communication and collaboration.
-
Regulatory Compliance: Each region may have different regulations regarding product safety and environmental impact. Buyers should familiarize themselves with local standards and ensure suppliers comply.
-
Shipping and Logistics Considerations: Quality assurance should extend to the shipping process. Buyers should verify that tanks are packaged securely to prevent damage during transit and that suppliers provide adequate shipping documentation.
By understanding the manufacturing processes and quality assurance practices, international B2B buyers can make informed decisions when sourcing polyethylene tanks, ensuring they select suppliers that meet their specific needs and standards.
Practical Sourcing Guide: A Step-by-Step Checklist for ‘polyethylene tank’
In the international B2B landscape, sourcing polyethylene tanks requires a strategic approach to ensure that your investment meets both operational needs and regulatory standards. This practical guide outlines essential steps to help buyers from Africa, South America, the Middle East, and Europe navigate the procurement process effectively.
Step 1: Define Your Technical Specifications
Clearly outlining your technical requirements is the first step in sourcing polyethylene tanks. Consider factors such as tank size, shape, capacity, and intended use (e.g., chemical storage, water containment). This clarity will guide your supplier selection and ensure the tanks meet your operational demands.
- Capacity Requirements: Determine the volume of liquid you need to store.
- Material Specifications: Identify whether standard polyethylene is sufficient or if specialized materials (like cross-linked polyethylene) are necessary for chemical compatibility.
Step 2: Research Potential Suppliers
Conduct thorough research to identify potential suppliers specializing in polyethylene tanks. Look for companies with a strong market presence and positive reviews from international clients.
- Supplier Reputation: Check online reviews and testimonials.
- Industry Experience: Prioritize suppliers who have a proven track record in your industry.
Step 3: Evaluate Supplier Certifications and Compliance
Before making a commitment, verify that suppliers possess necessary certifications and compliance with international standards. This is crucial for ensuring product quality and safety.
- Quality Standards: Look for certifications such as ISO 9001 or NSF/ANSI certifications relevant to your industry.
- Regulatory Compliance: Ensure that the tanks meet local regulations regarding material safety and environmental impact.
Step 4: Request Detailed Quotations
Once you have shortlisted suppliers, request detailed quotations that include pricing, lead times, and terms of service. This step is essential for comparing offers and understanding the total cost of ownership.
- Breakdown of Costs: Ensure quotations include shipping, handling, and any additional fees.
- Lead Times: Confirm estimated delivery times to align with your project timelines.
Step 5: Assess Customization Options
Depending on your application, you may need customized solutions. Discuss with potential suppliers about available customization options for tank design, such as additional fittings or specific dimensions.
- Design Flexibility: Inquire about the supplier’s ability to accommodate unique specifications.
- Previous Custom Projects: Ask for examples of past customizations they have successfully completed.
Step 6: Conduct a Site Visit or Virtual Audit
If feasible, arrange a site visit or virtual audit of the supplier’s manufacturing facility. This will provide insight into their production capabilities, quality control processes, and overall operational standards.
- Production Capacity: Assess whether the supplier can meet your volume requirements.
- Quality Control Processes: Understand how they ensure product quality throughout manufacturing.
Step 7: Finalize Terms and Place the Order
After selecting the supplier, finalize the terms of the agreement. This includes payment terms, warranty conditions, and after-sales support. Clear agreements help prevent misunderstandings and ensure a smooth procurement process.
- Payment Structures: Decide between upfront payments, milestones, or post-delivery payments.
- Warranty and Support: Understand warranty coverage and what support is available post-purchase.
By following this checklist, B2B buyers can streamline their sourcing process for polyethylene tanks, ensuring they select the right products from reputable suppliers that meet their specific needs.
Comprehensive Cost and Pricing Analysis for polyethylene tank Sourcing
What Are the Key Cost Components in Sourcing Polyethylene Tanks?
When sourcing polyethylene tanks, understanding the cost structure is crucial for B2B buyers. The primary cost components include:
-
Materials: The type of polyethylene used significantly impacts pricing. High-density polyethylene (HDPE) and cross-linked polyethylene (XLPE) are common choices. HDPE offers durability at a lower price, while XLPE, known for its strength, may come at a premium.
-
Labor: Labor costs can vary based on the geographical location of the manufacturer. Regions with lower labor costs can offer competitive pricing but may also affect lead times and quality.
-
Manufacturing Overhead: This includes costs associated with factory operations, utilities, and maintenance of machinery. Efficient production techniques can help reduce these overhead costs.
-
Tooling: Customization requires specialized tools, impacting the initial investment. For standard tanks, this cost is lower, while custom designs will necessitate a larger financial commitment.
-
Quality Control (QC): Ensuring that tanks meet safety and performance standards incurs additional costs. Certifications such as NSF/ANSI can further elevate the price but are essential for compliance, especially in regulated industries.
-
Logistics: Shipping costs can vary widely based on distance, shipping method, and volume. International buyers must consider customs duties and taxes, which can significantly affect the total cost.
-
Margin: Suppliers typically apply a profit margin on top of their costs. Understanding the average margin in your target market can help in negotiations.
How Do Price Influencers Affect the Cost of Polyethylene Tanks?
Several factors influence the pricing of polyethylene tanks:
-
Volume and Minimum Order Quantity (MOQ): Bulk orders often lead to discounts. Understanding the MOQ from suppliers can help you negotiate better pricing.
-
Specifications and Customization: Tanks with specialized features or larger sizes generally cost more. Be clear on your specifications to avoid unexpected costs.
-
Materials and Quality Certifications: Higher-quality materials or those with specific certifications (like FDA approval) will increase the price. Evaluate if these certifications are necessary for your application.
-
Supplier Factors: The supplier’s reputation, reliability, and history can influence pricing. Established suppliers may charge more due to perceived quality but could offer better service and reliability.
-
Incoterms: The agreed terms of delivery (e.g., FOB, CIF) significantly affect logistics costs. Understanding these terms can help you assess the total landed cost of tanks.
What Are Some Effective Buyer Tips for Negotiating Polyethylene Tank Prices?
For international B2B buyers, especially those from Africa, South America, the Middle East, and Europe, the following tips can enhance your sourcing strategy:
-
Negotiate Based on Volume: Leverage potential bulk orders to negotiate better pricing or terms. Suppliers may offer discounts for larger orders or long-term contracts.
-
Consider Total Cost of Ownership (TCO): Evaluate not just the purchase price but also the long-term costs, including maintenance, shipping, and potential disposal costs. A lower initial price may lead to higher overall expenses.
-
Understand Pricing Nuances: Prices can fluctuate based on market demand, raw material costs, and geopolitical factors. Stay informed on market trends to negotiate more effectively.
-
Request Samples: Before committing to a large order, request samples to verify quality. This can help ensure you are investing in a product that meets your needs.
-
Explore Local Suppliers: For buyers in regions like Africa and South America, sourcing locally can reduce shipping costs and lead times. It also may enhance communication and support.
Disclaimer on Indicative Prices
Prices for polyethylene tanks can vary significantly based on the factors mentioned above. The information provided serves as a guideline; always consult with suppliers for the most accurate and current pricing tailored to your specific requirements.
Alternatives Analysis: Comparing polyethylene tank With Other Solutions
When selecting storage solutions for liquids, particularly in B2B contexts, it’s crucial to evaluate various alternatives to polyethylene tanks. Polyethylene tanks are popular due to their durability and cost-effectiveness, but understanding other options can lead to better decision-making based on specific operational needs.
Comparison Aspect | Polyethylene Tank | Fiberglass Tank | Stainless Steel Tank |
---|---|---|---|
Performance | Good resistance to chemicals; lightweight | Excellent chemical resistance; strong | High durability; can withstand extreme temperatures |
Cost | Generally low cost; affordable for bulk purchases | Moderate cost; more expensive than polyethylene | High initial investment; cost-effective over time |
Ease of Implementation | Easy to install and transport; minimal site prep | Requires specialized installation; heavier | Requires skilled labor for installation; heavy |
Maintenance | Low maintenance; resistant to corrosion | Moderate maintenance; can require repairs | Low maintenance; corrosion-resistant with proper care |
Best Use Case | Agricultural, water storage, and waste | Chemical storage, water treatment | Food and beverage, pharmaceuticals |
What are the Advantages and Disadvantages of Fiberglass Tanks?
Fiberglass tanks are known for their excellent chemical resistance and strength. They can handle a wide range of corrosive substances, making them ideal for chemical storage applications. However, they tend to be heavier and may require specialized installation, which can increase initial costs. While the durability of fiberglass tanks is commendable, they can also be more prone to cracking under certain conditions compared to polyethylene options. For buyers in sectors such as the chemical industry or water treatment, the investment in fiberglass may be justified by the longer lifespan and superior resistance to chemical reactions.
Why Consider Stainless Steel Tanks for Liquid Storage?
Stainless steel tanks offer unparalleled durability and strength, making them suitable for extreme conditions, including high temperatures and pressures. They are particularly advantageous in the food and beverage industry, where hygiene and safety are paramount. However, the initial investment for stainless steel tanks is significantly higher than that of polyethylene and fiberglass tanks. While they require minimal maintenance, proper care is essential to prevent corrosion. Buyers looking for long-term solutions with high durability should consider stainless steel tanks, especially if they require compliance with strict health regulations.
How to Choose the Right Storage Solution for Your Needs?
When evaluating the best storage solution for your needs, consider several factors, including the type of liquids you intend to store, the environment in which the tank will be placed, and your budget constraints. Polyethylene tanks are an excellent choice for cost-conscious buyers needing reliable performance for agricultural or water storage. On the other hand, if your operations involve corrosive chemicals, fiberglass tanks may be worth the additional investment. For industries requiring stringent hygiene standards, stainless steel tanks might be the optimal choice despite their higher costs.
Ultimately, the right solution will align with your operational requirements, budget, and long-term storage goals. By assessing the strengths and weaknesses of each option, B2B buyers can make informed decisions that enhance efficiency and safety in their operations.
Essential Technical Properties and Trade Terminology for polyethylene tank
What Are the Key Technical Properties of Polyethylene Tanks?
When considering polyethylene tanks for your business needs, understanding their technical properties is crucial. Here are some essential specifications that can significantly impact your purchasing decisions:
1. Material Grade: What Type of Polyethylene Should You Choose?
Polyethylene tanks are typically made from high-density polyethylene (HDPE) or cross-linked polyethylene (XLPE). HDPE is known for its durability and resistance to chemicals, making it suitable for a variety of applications, including water storage and chemical containment. XLPE offers enhanced structural integrity and can withstand higher temperatures and pressures. Selecting the appropriate material grade is vital for ensuring that the tank meets your specific requirements, particularly in terms of chemical compatibility and environmental conditions.
2. Capacity: How Much Storage Do You Need?
Polyethylene tanks come in various capacities, ranging from small tanks for residential use to large industrial tanks that hold thousands of gallons. When evaluating capacity, consider your operational needs, as well as any regulatory requirements in your region. For example, in agriculture or manufacturing, understanding the volume of liquids you need to store can help you choose the right tank, avoiding unnecessary costs associated with overcapacity or undercapacity.
3. Tolerance: Why Is Precision Important?
Tolerance refers to the allowable variation in dimensions and capacity of the tank. High tolerance specifications ensure that the tank fits properly within your existing infrastructure and functions effectively. For instance, if a tank is slightly larger or smaller than specified, it may not integrate well with existing systems, leading to leaks or operational inefficiencies. Ensuring accurate tolerances is essential for maximizing the tank’s lifespan and performance.
4. Wall Thickness: How Does It Affect Durability?
The wall thickness of polyethylene tanks can vary significantly, impacting their strength and resistance to impact and environmental stressors. Thicker walls generally provide greater durability and resistance to punctures and deformation, making them suitable for more demanding applications. When selecting a tank, consider the environmental factors it will face, such as UV exposure or temperature fluctuations, to choose a suitable wall thickness that offers long-term reliability.
5. Chemical Resistance: What Liquids Can the Tank Hold?
Polyethylene’s chemical resistance is a critical property, particularly if you plan to store hazardous or corrosive materials. Different grades of polyethylene exhibit varying levels of resistance to chemicals like acids, bases, and solvents. It is imperative to consult chemical compatibility charts to ensure that the tank material will withstand the specific liquids you intend to store, thus preventing leaks and ensuring safety.
What Trade Terminology Should You Understand When Purchasing Polyethylene Tanks?
Familiarizing yourself with industry terminology can streamline your purchasing process and ensure clarity in communications with suppliers. Here are some common terms to know:
1. OEM (Original Equipment Manufacturer)
OEM refers to a company that produces parts or equipment that may be marketed by another manufacturer. Understanding OEM relationships can help you identify the quality and reliability of the tanks you are considering, as reputable OEMs often provide warranties and support.
2. MOQ (Minimum Order Quantity)
MOQ denotes the smallest number of units a supplier is willing to sell. Knowing the MOQ can help you assess whether a supplier aligns with your budget and inventory needs. If your operational requirements fluctuate, negotiating MOQs can be beneficial.
3. RFQ (Request for Quotation)
An RFQ is a formal document sent to suppliers to request pricing and terms for specific products. This is an essential step in the procurement process, allowing you to compare options and negotiate better deals based on your needs.
4. Incoterms (International Commercial Terms)
Incoterms are a set of rules that define the responsibilities of buyers and sellers in international trade. Familiarity with these terms can help you understand shipping costs, insurance, and risk management, ensuring that you are fully aware of your obligations and liabilities.
5. Secondary Containment
Secondary containment refers to a secondary barrier designed to prevent leaks or spills from a primary storage tank. Understanding this concept is crucial for compliance with environmental regulations and for ensuring safe storage practices, especially when dealing with hazardous materials.
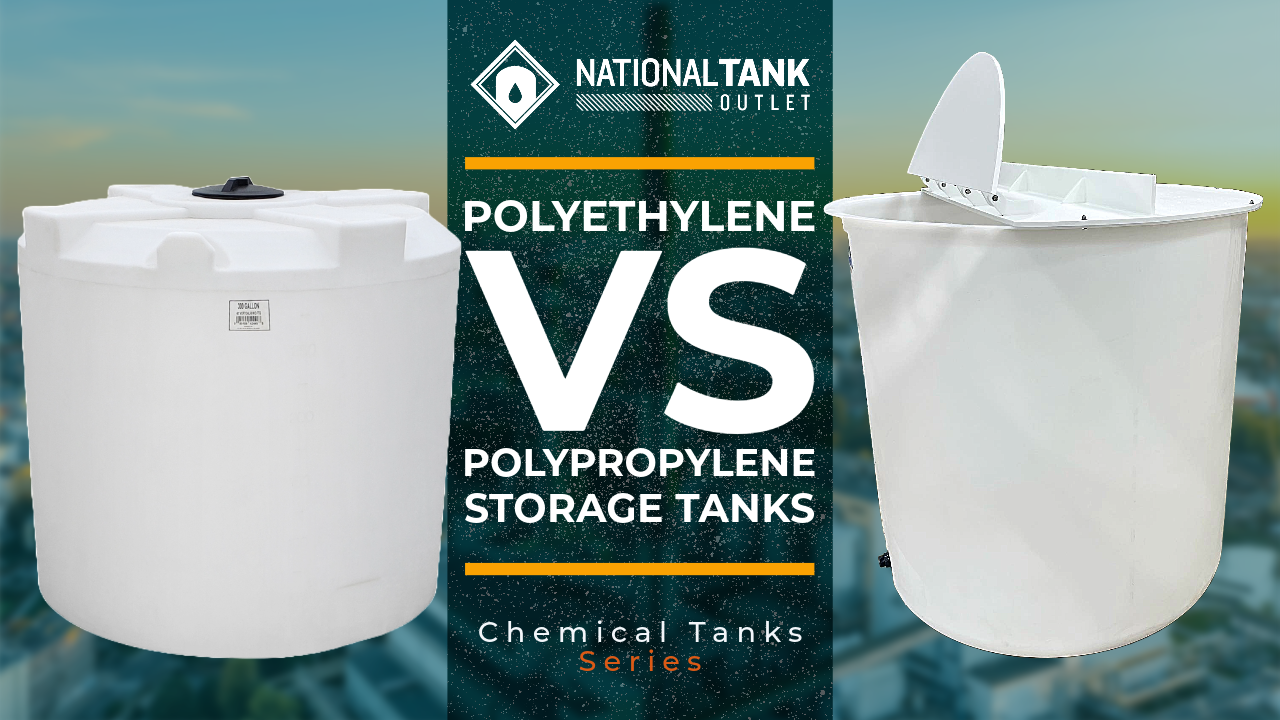
A stock image related to polyethylene tank.
By grasping these essential technical properties and trade terminologies, international B2B buyers can make informed decisions when purchasing polyethylene tanks, ensuring they meet operational requirements while navigating the complexities of global trade effectively.
Navigating Market Dynamics and Sourcing Trends in the polyethylene tank Sector
What Are the Current Market Dynamics and Key Trends in the Polyethylene Tank Sector?
The polyethylene tank sector is witnessing dynamic shifts driven by global demand for sustainable storage solutions and advancements in manufacturing technologies. In regions like Africa, South America, the Middle East, and Europe, key trends include the increasing adoption of high-density polyethylene (HDPE) tanks due to their durability and resistance to corrosion. The rising need for water storage solutions in arid regions, particularly in Africa and the Middle East, is propelling market growth. Additionally, the agricultural sector’s demand for bulk liquid storage, especially in South America, is fostering innovation in tank designs.
Emerging technologies such as rotational molding and 3D printing are enhancing manufacturing capabilities, allowing for more customized solutions tailored to specific industry needs. Furthermore, international buyers are increasingly prioritizing suppliers who offer transparency in their sourcing processes, ensuring compliance with global standards. The market is also seeing a shift towards double-wall tanks that provide secondary containment, addressing environmental concerns and regulatory requirements.
How Can International B2B Buyers Ensure Sustainable and Ethical Sourcing of Polyethylene Tanks?
Sustainability is becoming a cornerstone of procurement strategies for international B2B buyers. The environmental impact of polyethylene tanks, particularly in terms of plastic waste, is prompting buyers to seek suppliers committed to ethical sourcing and sustainability. This includes the use of recycled materials in tank production and adherence to eco-friendly manufacturing processes.
Buyers should look for suppliers who hold certifications such as ISO 14001 for environmental management or NSF/ANSI/CAN 61 for safe drinking water system components. These certifications not only validate the supplier’s commitment to sustainability but also ensure that the products meet stringent quality and safety standards. Furthermore, engaging with manufacturers that implement sustainable practices in their supply chains can enhance brand reputation and reduce overall environmental footprints.
What Is the Historical Context of Polyethylene Tanks in B2B Markets?
The evolution of polyethylene tanks dates back to the mid-20th century when the development of synthetic polymers revolutionized storage solutions. Initially used for agricultural and industrial applications, polyethylene tanks gained popularity due to their lightweight, corrosion-resistant, and cost-effective nature compared to traditional materials like steel and concrete. Over the decades, advancements in manufacturing techniques, such as blow molding and rotational molding, have allowed for a wider variety of tank shapes and sizes, catering to diverse industries including water treatment, agriculture, and chemical storage.
As the global emphasis on sustainability grew in the 21st century, the industry adapted by introducing more environmentally friendly options, including tanks made from recycled materials. This historical context highlights the ongoing innovation within the sector and underscores the importance of sustainability and ethical sourcing in the purchasing decisions of modern B2B buyers.
Frequently Asked Questions (FAQs) for B2B Buyers of polyethylene tank
-
How do I choose the right polyethylene tank for my application?
Choosing the right polyethylene tank involves assessing your specific needs, including the type of liquid to be stored, required capacity, and environmental conditions. Consider whether you need features like a double wall for secondary containment or specific gravity ratings for chemical storage. Additionally, evaluate tank shapes (vertical, horizontal, or conical) based on your available space and installation requirements. Reviewing manufacturer specifications and consulting with suppliers can further refine your selection. -
What are the key benefits of using polyethylene tanks in industrial applications?
Polyethylene tanks offer numerous advantages, including excellent chemical resistance, lightweight construction, and ease of installation. They are also highly durable, resistant to corrosion, and can be manufactured in a variety of shapes and sizes to suit diverse applications. Their seamless construction reduces the risk of leaks, making them ideal for storing hazardous materials. Furthermore, their cost-effectiveness and low maintenance requirements make them a preferred choice for many industries. -
What customization options are available for polyethylene tanks?
Most manufacturers provide customization options for polyethylene tanks, allowing you to tailor features such as size, shape, color, and fittings. Additionally, you can request specific gravity ratings, wall thickness, and integrated secondary containment features. When discussing your requirements with suppliers, be clear about your application needs to ensure the tank meets industry standards and regulations. Customization may also affect lead times and pricing, so factor these into your planning. -
What is the minimum order quantity (MOQ) for polyethylene tanks?
The minimum order quantity for polyethylene tanks can vary significantly by supplier and the type of tank. Smaller tanks may have lower MOQs, while larger or custom tanks may require a higher volume to justify production costs. When sourcing from international suppliers, inquire about MOQs upfront to avoid potential delays in procurement. Some suppliers may also offer flexible options for startups or smaller businesses, so it’s worth negotiating based on your specific needs. -
How do I verify the credibility of a polyethylene tank supplier?
To verify a polyethylene tank supplier’s credibility, start by checking their industry certifications, customer reviews, and case studies. Look for suppliers with ISO certifications or compliance with relevant safety standards (e.g., NSF/ANSI). Engage in direct communication, asking about their manufacturing processes, quality assurance measures, and after-sales support. Participating in trade shows or industry events can also provide opportunities to meet suppliers face-to-face and gauge their reliability. -
What payment terms should I expect when sourcing polyethylene tanks internationally?
Payment terms for international transactions can vary widely depending on the supplier and your negotiation. Common options include upfront payments, letters of credit, or staggered payments based on shipment milestones. Ensure that you understand the terms regarding currency exchange, payment methods, and any applicable tariffs or taxes. Clear communication about payment expectations can prevent misunderstandings and facilitate smoother transactions. -
How can I ensure the quality of polyethylene tanks during shipping?
To ensure the quality of polyethylene tanks during shipping, verify that your supplier uses appropriate packaging methods to protect against damage. This includes using cushioning materials and securing tanks to prevent movement. Request inspection reports or certifications for quality assurance before shipment. Additionally, consider working with logistics partners experienced in handling specialized equipment, and establish clear communication channels to address any issues that may arise during transit. -
What are the logistics considerations for importing polyethylene tanks?
When importing polyethylene tanks, several logistics considerations come into play, including shipping methods, customs clearance, and delivery timelines. Choose a shipping method that balances cost and speed, considering options like sea freight for large orders. Familiarize yourself with import regulations in your country, including potential duties and taxes. Collaborate with a freight forwarder to streamline the process, ensuring that all documentation is prepared correctly to avoid delays at customs.
Important Disclaimer & Terms of Use
⚠️ Important Disclaimer
The information provided in this guide, including content regarding manufacturers, technical specifications, and market analysis, is for informational and educational purposes only. It does not constitute professional procurement advice, financial advice, or legal advice.
While we have made every effort to ensure the accuracy and timeliness of the information, we are not responsible for any errors, omissions, or outdated information. Market conditions, company details, and technical standards are subject to change.
B2B buyers must conduct their own independent and thorough due diligence before making any purchasing decisions. This includes contacting suppliers directly, verifying certifications, requesting samples, and seeking professional consultation. The risk of relying on any information in this guide is borne solely by the reader.
Strategic Sourcing Conclusion and Outlook for polyethylene tank
What Are the Key Takeaways for B2B Buyers in Strategic Sourcing of Polyethylene Tanks?
Strategic sourcing of polyethylene tanks presents an invaluable opportunity for international B2B buyers, particularly in regions like Africa, South America, the Middle East, and Europe. By focusing on supplier reliability, product quality, and competitive pricing, businesses can secure tanks that meet diverse storage needs, from agricultural applications to industrial uses. Engaging with manufacturers that offer warranties and certifications ensures that you are investing in durable and compliant products, reducing long-term operational risks.
How Can Buyers Prepare for Future Procurement of Polyethylene Tanks?
As we look ahead, the demand for polyethylene tanks is expected to grow, driven by increasing industrialization and environmental regulations. Buyers should stay informed about innovations in tank design, such as double-wall systems for enhanced safety and sustainability. Building strong relationships with suppliers will be crucial for accessing the latest technologies and favorable pricing structures.
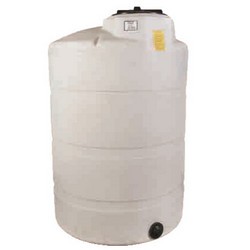
A stock image related to polyethylene tank.
What Actions Should International Buyers Take Now?
International B2B buyers are encouraged to evaluate their current sourcing strategies and consider diversifying their supplier base to mitigate risks. By prioritizing strategic partnerships with manufacturers who have a proven track record, businesses can not only secure quality products but also gain insights into market trends and advancements. The time to act is now—embrace strategic sourcing to ensure you are well-equipped for future challenges in the polyethylene tank market.