Discover Cost-Effective Bracket Metal Solutions (2025)
Introduction: Navigating the Global Market for bracket metal
In the ever-evolving landscape of international trade, sourcing high-quality bracket metal poses unique challenges for B2B buyers, particularly in emerging markets across Africa, South America, the Middle East, and Europe. Whether you are looking for heavy-duty steel brackets for industrial applications or lightweight aluminum options for consumer products, understanding the diverse types of bracket metal and their specific applications is crucial. This guide offers a comprehensive overview of the global market for bracket metal, focusing on various types, applications, and material specifications that meet industry standards.
Navigating this complex market requires more than just identifying the right product; it involves meticulous supplier vetting, an understanding of cost implications, and knowledge of regional regulations that could impact procurement. For businesses in regions like Mexico and Thailand, where local suppliers may have varying levels of quality and service, this guide is designed to empower you with the insights needed for informed purchasing decisions. By addressing key considerations such as sourcing strategies, material properties, and potential suppliers, this resource will help you streamline your procurement process and enhance your competitive advantage in the global marketplace.
As you delve deeper into the guide, you’ll find actionable insights tailored to your unique needs, ensuring that you can confidently navigate the intricacies of sourcing bracket metal in today’s dynamic environment.
Understanding bracket metal Types and Variations
Type Name | Key Distinguishing Features | Primary B2B Applications | Brief Pros & Cons for Buyers |
---|---|---|---|
Stainless Steel Brackets | Corrosion-resistant, high strength, polished finish | Construction, industrial shelving | Pros: Durable, aesthetic appeal; Cons: Higher cost compared to other metals. |
Galvanized Steel Brackets | Coated with zinc for rust prevention, cost-effective | Outdoor applications, heavy-duty support | Pros: Affordable, good weather resistance; Cons: Limited aesthetic options. |
Aluminum Brackets | Lightweight, resistant to corrosion, easy to fabricate | Aerospace, automotive, and lightweight structures | Pros: Easy to transport, good strength-to-weight ratio; Cons: Less load-bearing capacity than steel. |
Wrought Iron Brackets | Heavy-duty, decorative options available, high tensile strength | Architectural applications, furniture | Pros: Strong, decorative; Cons: Heavier, can be more expensive. |
Plastic Brackets | Lightweight, non-corrosive, budget-friendly | Temporary structures, low-load applications | Pros: Cost-effective, easy to install; Cons: Not suitable for high-load applications. |
What Are the Characteristics and Suitability of Stainless Steel Brackets?
Stainless steel brackets are renowned for their corrosion resistance and strength, making them ideal for a variety of applications, especially in environments exposed to moisture or chemicals. They are often used in construction and industrial shelving due to their ability to support significant weight while maintaining structural integrity. When purchasing stainless steel brackets, B2B buyers should consider factors like load capacity, finish options, and pricing, as they tend to be more expensive than other materials.
How Do Galvanized Steel Brackets Compare in Cost-Effectiveness and Applications?
Galvanized steel brackets are coated with zinc, providing excellent protection against rust and making them suitable for outdoor use and heavy-duty applications. They are frequently utilized in construction projects that require a robust and cost-effective solution. Buyers should evaluate the specific needs of their projects, such as load requirements and exposure to elements, when selecting galvanized steel brackets, as they offer a good balance between affordability and durability.
Why Choose Aluminum Brackets for Lightweight Structures?
Aluminum brackets are favored for their lightweight nature and corrosion resistance, which makes them ideal for applications in the aerospace and automotive industries. Their ease of fabrication allows for custom designs, catering to specific project needs. B2B buyers should assess the strength-to-weight ratio and the specific load requirements of their applications, as aluminum may not support as much weight as steel but offers significant advantages in transport and installation.
What Advantages Do Wrought Iron Brackets Offer for Architectural Applications?
Wrought iron brackets are known for their heavy-duty capabilities and decorative potential, making them a popular choice for architectural designs and furniture. They provide excellent tensile strength, which is beneficial for load-bearing applications. Buyers should consider the weight of wrought iron brackets and their aesthetic appeal when making purchasing decisions, as they can be more expensive and heavier than other options, but offer a unique design element.
In What Scenarios Are Plastic Brackets a Viable Choice?
Plastic brackets are lightweight, non-corrosive, and budget-friendly, making them suitable for temporary structures and low-load applications. They are often used in settings where heavy-duty support is not required. B2B buyers should consider the intended use and load requirements when opting for plastic brackets, as they are not designed for high-load situations but can be an economical choice for specific applications.
Key Industrial Applications of bracket metal
Industry/Sector | Specific Application of bracket metal | Value/Benefit for the Business | Key Sourcing Considerations for this Application |
---|---|---|---|
Construction & Building | Structural support for beams and shelves | Enhances stability and load distribution | Material grade, corrosion resistance, and load capacity |
Automotive Manufacturing | Mounting brackets for vehicle components | Improves assembly efficiency and safety | Compliance with industry standards and custom sizes |
Electronics & Telecommunications | Brackets for mounting servers and equipment | Maximizes space efficiency and equipment accessibility | Precision in dimensions and material durability |
Renewable Energy | Support structures for solar panels | Increases energy generation efficiency | Weather resistance and compatibility with local codes |
Furniture Design & Retail | Decorative and functional shelf brackets | Enhances aesthetic appeal while providing support | Design versatility and finish options |
How is Bracket Metal Used in the Construction & Building Industry?
In the construction and building sector, bracket metal serves as critical structural support for beams, shelves, and various installations. It ensures stability and load distribution, addressing the need for robust frameworks in both residential and commercial projects. For international buyers, especially from regions like Africa and South America, sourcing high-quality materials that meet local building codes is essential. Consideration should be given to the corrosion resistance of the metal, particularly in humid or coastal environments, to ensure longevity and safety.
What Role Does Bracket Metal Play in Automotive Manufacturing?
In automotive manufacturing, bracket metal is used for mounting essential components such as engines, exhaust systems, and electronic modules. The use of high-strength materials in these brackets improves assembly efficiency and enhances vehicle safety. Buyers from the Middle East and Europe should prioritize compliance with industry standards, as well as the availability of custom sizes, to meet the specific demands of their production lines. The ability to withstand vibrations and temperature variations is also crucial in this sector.
Why is Bracket Metal Important in Electronics & Telecommunications?
In the electronics and telecommunications industries, bracket metal is vital for mounting servers, routers, and other equipment. These brackets maximize space efficiency and ensure easy accessibility for maintenance and upgrades. For international buyers, particularly from Europe and South America, precision in dimensions is critical to accommodate various equipment types. Additionally, durability against environmental factors, such as dust and moisture, should be a key consideration when sourcing these components.
How Does Bracket Metal Support Renewable Energy Initiatives?
Bracket metal is increasingly utilized in renewable energy applications, particularly for supporting solar panels. The right brackets enhance energy generation efficiency by ensuring optimal panel positioning and stability against wind and weather conditions. Buyers in regions like Africa, where solar energy is a growing market, should focus on sourcing weather-resistant materials that comply with local regulations. This ensures that installations are not only efficient but also safe and durable.
What are the Applications of Bracket Metal in Furniture Design & Retail?
In furniture design and retail, bracket metal is used for both decorative and functional purposes, such as supporting shelves and creating unique display fixtures. This dual functionality enhances the aesthetic appeal while providing necessary support for various products. Buyers from diverse markets, including Europe and South America, should consider design versatility and finish options when sourcing these brackets to align with consumer preferences and trends in interior design.
3 Common User Pain Points for ‘bracket metal’ & Their Solutions
Scenario 1: Inconsistent Quality of Metal Brackets
The Problem:
B2B buyers often face challenges with the inconsistent quality of metal brackets from various suppliers. This inconsistency can result in the use of substandard materials that fail to meet structural requirements, leading to project delays, increased costs, and potential safety hazards. Buyers in Africa and South America, in particular, may encounter difficulties in sourcing reliable suppliers due to varying manufacturing standards across regions.
The Solution:
To mitigate these risks, buyers should prioritize sourcing from reputable manufacturers who adhere to international quality standards such as ISO 9001. When evaluating suppliers, request certifications and samples to assess the durability and load-bearing capabilities of their products. Additionally, consider engaging suppliers who offer a product warranty or guarantee, as this demonstrates their confidence in the quality of their brackets. By establishing long-term relationships with reliable suppliers, buyers can ensure a consistent supply of high-quality metal brackets that meet their specific project needs.
Scenario 2: Difficulty in Finding the Right Specifications for Metal Brackets
The Problem:
Many B2B buyers struggle to identify the right specifications for metal brackets needed for their projects. This can include selecting the appropriate size, material, and load capacity, which can vary significantly based on the application. For instance, a construction company in the Middle East might require heavy-duty brackets for mounting solar panels, while a European buyer may need lightweight options for interior shelving. Miscalculating these requirements can lead to project inefficiencies and additional costs.
The Solution:
To overcome this challenge, buyers should conduct thorough research on the specific application requirements for their projects. Consulting with engineers or technical experts can provide insights into the appropriate specifications for metal brackets. Buyers should also leverage resources such as product datasheets and load capacity charts offered by manufacturers. Additionally, utilizing online tools or calculators can help determine the necessary bracket specifications based on load requirements and environmental conditions. This proactive approach will ensure that buyers select the right metal brackets for their applications, optimizing both performance and safety.
Scenario 3: Limited Availability of Custom Metal Brackets
The Problem:
International buyers often find it challenging to procure custom metal brackets tailored to their specific needs. This is particularly true in regions like Africa and South America, where suppliers may not offer customization options or have long lead times for custom orders. As a result, buyers may have to settle for generic solutions that do not fit their precise requirements, potentially compromising the integrity of their projects.
The Solution:
To address this pain point, buyers should seek out suppliers who specialize in custom metal fabrication and have a proven track record of delivering tailored solutions. When approaching suppliers, clearly articulate the specific requirements, including dimensions, load capacities, and materials needed. It may also be beneficial to collaborate with manufacturers who utilize advanced technologies such as CNC machining or laser cutting, as these capabilities can enable faster production of custom brackets. Establishing a partnership with a flexible supplier that can accommodate custom orders will not only enhance project outcomes but also foster innovation and efficiency in product design.
Strategic Material Selection Guide for bracket metal
What Are the Key Properties of Common Bracket Metal Materials?
When selecting materials for bracket metal, it’s essential to consider the unique properties of each option. Here, we analyze four common materials: steel, aluminum, stainless steel, and wrought iron. Each material has distinct characteristics that influence performance, durability, and suitability for specific applications.
How Does Steel Perform as a Bracket Metal?
Steel is a widely used material for brackets due to its high strength and load-bearing capabilities. It can withstand significant pressure and is often used in heavy-duty applications. Steel brackets are typically cost-effective, making them a popular choice for many industries.
Pros:
– High tensile strength and load capacity.
– Cost-effective compared to other metals.
– Versatile for various applications.
Cons:
– Prone to corrosion if not treated.
– Heavier than alternatives like aluminum.
– Requires more complex manufacturing processes.
For international buyers, particularly in regions with high humidity or coastal environments, ensuring proper corrosion resistance through galvanization or powder coating is crucial. Compliance with standards like ASTM A36 for structural steel can also be a determining factor.
What Are the Advantages of Using Aluminum for Brackets?
Aluminum is known for its lightweight properties and excellent corrosion resistance, making it suitable for applications where weight is a concern. It is also non-magnetic and has good thermal conductivity.
Pros:
– Lightweight and easy to handle.
– Excellent corrosion resistance.
– Good thermal and electrical conductivity.
Cons:
– Lower strength compared to steel.
– More expensive than steel.
– May require specialized manufacturing techniques.
For buyers in regions like Africa and South America, where weight can impact shipping costs, aluminum brackets can offer significant logistical advantages. However, it’s essential to consider local standards for aluminum alloys, such as JIS H 4040 in Japan or EN 573 in Europe.
Why Choose Stainless Steel for Bracket Applications?
Stainless steel is renowned for its corrosion resistance and aesthetic appeal, making it ideal for applications exposed to moisture or where appearance matters, such as in architectural designs.
Pros:
– Exceptional corrosion resistance.
– Attractive finish, suitable for visible applications.
– High strength-to-weight ratio.
Cons:
– Higher cost than regular steel.
– More challenging to machine and fabricate.
– Potential for galling when fastened.
International buyers should be aware of the various grades of stainless steel, such as 304 and 316, which offer different levels of corrosion resistance. Compliance with standards like ASTM A240 is also important for ensuring quality.
What Are the Specific Benefits of Wrought Iron as a Bracket Material?
Wrought iron is known for its malleability and ductility, allowing for intricate designs and shapes. It is often used in decorative applications, such as railings and gates.
Pros:
– Highly malleable and can be shaped easily.
– Excellent durability and resistance to wear.
– Aesthetic appeal for decorative applications.
Cons:
– Heavier than aluminum and some steels.
– More expensive due to labor-intensive manufacturing.
– Prone to rust if not properly coated.
For buyers in the Middle East and Europe, wrought iron brackets are often favored for their traditional aesthetic. Compliance with local standards for wrought iron products can vary, so it’s crucial to verify specifications.
Summary Table of Bracket Metal Materials
Material | Typical Use Case for bracket metal | Key Advantage | Key Disadvantage/Limitation | Relative Cost (Low/Med/High) |
---|---|---|---|---|
Steel | Heavy-duty structural applications | High tensile strength | Prone to corrosion | Low |
Aluminum | Lightweight structures and frameworks | Excellent corrosion resistance | Lower strength than steel | Med |
Stainless Steel | Architectural and marine applications | Exceptional corrosion resistance | Higher cost | High |
Wrought Iron | Decorative railings and gates | Highly malleable for designs | Heavier and more expensive | Med |
This guide provides a comprehensive overview of material selection for bracket metals, enabling international B2B buyers to make informed decisions based on their specific needs and regional considerations.
In-depth Look: Manufacturing Processes and Quality Assurance for bracket metal
What Are the Main Stages of Manufacturing Bracket Metal?
Manufacturing bracket metal involves several critical stages that ensure the final product meets industry standards and customer specifications. Understanding these stages can help B2B buyers make informed purchasing decisions.
Material Preparation: How Are Raw Materials Processed?
The manufacturing process begins with the careful selection and preparation of raw materials. Common materials used for bracket metal include stainless steel, aluminum, and galvanized steel.
- Material Selection: The choice of material depends on the intended application, such as load-bearing capacity and environmental resistance.
- Cutting and Sizing: Raw metal sheets are cut into specific sizes using methods such as laser cutting or shearing. Precision at this stage is crucial to minimize waste and ensure compatibility with design specifications.
How Is Bracket Metal Formed?
After material preparation, the next step involves forming the bracket into the desired shape. This stage employs various techniques to achieve the necessary geometries.
- Die Stamping: This cold forming process uses a series of dies to cut and shape metal sheets into brackets. The pressure applied during this process alters the metal’s geometry, allowing for complex shapes to be produced efficiently.
- Bending and Punching: For brackets that require angles or holes, bending and punching techniques are employed. These processes can enhance the functionality of the brackets, allowing for easier installation and better load distribution.
What Assembly Techniques Are Commonly Used for Bracket Metal?
Once the individual components are formed, assembly techniques come into play to create the final product.
- Welding: In many cases, brackets are assembled using welding techniques. This provides a strong bond, ensuring durability under stress.
- Fastening: For some designs, mechanical fasteners such as bolts or screws may be used. This method allows for easy disassembly and reconfiguration, which can be beneficial for modular applications.
How Does Finishing Impact the Quality of Bracket Metal?
The finishing process is essential for both aesthetic and functional purposes.
- Surface Treatment: Techniques such as powder coating, anodizing, or galvanizing can enhance corrosion resistance and improve the visual appeal of the brackets.
- Quality Inspection: Post-finishing, brackets undergo a thorough inspection to ensure that they meet dimensional tolerances and surface finish requirements.
What Quality Assurance Standards Are Relevant for Bracket Metal?
Quality assurance is a critical component of the manufacturing process, especially for international B2B transactions. B2B buyers should be aware of the relevant standards and practices that ensure product quality.
What International Standards Should B2B Buyers Know About?
- ISO 9001: This is a widely recognized standard for quality management systems. Suppliers certified under ISO 9001 demonstrate a commitment to quality processes and continuous improvement.
- CE Marking: For products sold within the European Economic Area, CE marking indicates compliance with health, safety, and environmental protection standards.
What Are the Key Quality Control Checkpoints in Manufacturing?
Quality control (QC) is integrated throughout the manufacturing process, with specific checkpoints established at various stages.
- Incoming Quality Control (IQC): Materials are inspected upon arrival to ensure they meet specified standards before processing begins.
- In-Process Quality Control (IPQC): Continuous monitoring occurs during the manufacturing process, including dimensional checks and visual inspections.
- Final Quality Control (FQC): Before shipment, finished products undergo a final inspection to verify compliance with all specifications.
What Common Testing Methods Are Used to Ensure Quality?
Various testing methods are employed to validate the quality and functionality of bracket metal.
- Tensile Testing: This test evaluates the strength and ductility of the metal, ensuring that it can withstand the required loads.
- Corrosion Resistance Testing: Especially important for brackets used in outdoor or harsh environments, this testing assesses the material’s ability to resist corrosion over time.
- Dimensional Inspection: Using tools such as calipers and gauges, manufacturers check that the brackets conform to specified dimensions.
How Can B2B Buyers Verify Supplier Quality Control Practices?
For international buyers, verifying a supplier’s quality control practices is essential for ensuring product reliability.
- Supplier Audits: Conducting regular audits of suppliers can provide insights into their manufacturing processes and quality management systems.
- Quality Reports: Requesting detailed QC reports, including results from various tests and inspections, can help assess a supplier’s commitment to quality.
- Third-Party Inspections: Engaging third-party inspection services can offer an unbiased evaluation of a supplier’s products and processes.
What Are the Quality Control Nuances for International B2B Buyers?
B2B buyers from regions such as Africa, South America, the Middle East, and Europe should be aware of specific nuances in quality control.
- Regulatory Compliance: Different regions may have varying regulatory requirements that affect product quality and safety. Understanding these requirements is crucial for compliance.
- Cultural Differences: Approaches to quality assurance may differ across cultures. Establishing clear communication and expectations can help bridge these gaps.
- Supply Chain Transparency: Buyers should seek suppliers who provide transparency in their supply chains, including details on sourcing materials and manufacturing practices.
Conclusion
Understanding the manufacturing processes and quality assurance measures for bracket metal is essential for international B2B buyers. By focusing on the main stages of manufacturing, relevant quality standards, and verification methods, buyers can make informed decisions that align with their business needs and compliance requirements. Investing time in supplier evaluations and quality assessments can lead to long-term partnerships that enhance operational efficiency and product reliability.
Practical Sourcing Guide: A Step-by-Step Checklist for ‘bracket metal’
This guide is designed to assist international B2B buyers in sourcing metal brackets effectively. The procurement of bracket metal requires careful consideration of specifications, supplier capabilities, and market dynamics. By following this checklist, buyers can ensure they make informed decisions that meet their operational needs.
Step 1: Define Your Technical Specifications
Before reaching out to suppliers, it’s essential to clearly outline your technical requirements. This includes the type of metal (e.g., stainless steel, aluminum), dimensions, load-bearing capacity, and any specific finishes or coatings.
– Why it matters: Clear specifications help suppliers provide accurate quotes and reduce the risk of receiving incorrect products.
– What to look for: Consider the application of the brackets—whether for structural support, decorative purposes, or specialized uses.
Step 2: Research Market Trends and Pricing
Understanding current market trends and pricing for metal brackets is crucial. Research historical price data and compare costs across different regions, particularly in Africa, South America, the Middle East, and Europe.
– Why it matters: This insight helps in negotiating better prices and identifying potential suppliers who offer competitive rates.
– What to look for: Pay attention to fluctuations in metal prices due to global supply chain issues or local demand spikes.
Step 3: Evaluate Potential Suppliers
Thoroughly vet potential suppliers before making commitments. Request company profiles, case studies, and references from other buyers in similar industries or regions.
– Why it matters: Supplier reliability and quality assurance are critical to ensuring that your projects run smoothly.
– What to look for: Check for certifications (e.g., ISO standards), production capabilities, and past performance with similar products.
Step 4: Request Samples for Testing
Once you have shortlisted suppliers, request samples of the metal brackets. Testing these samples for quality and durability is an important step in the selection process.
– Why it matters: Hands-on testing allows you to assess the fit and function of the brackets in real-world applications.
– What to look for: Evaluate the material quality, finish, and structural integrity under load.
Step 5: Assess Supplier Communication and Support
Effective communication is crucial for a successful partnership. Evaluate how responsive and informative potential suppliers are during the inquiry phase.
– Why it matters: Strong communication can ease the ordering process and help resolve issues promptly.
– What to look for: Consider their willingness to provide technical support and their responsiveness to inquiries.
Step 6: Verify Compliance with Local Regulations
Ensure that the metal brackets meet any local industry standards or regulations applicable in your region. This is particularly important in industries like construction, where safety is paramount.
– Why it matters: Compliance reduces legal risks and enhances safety standards in your operations.
– What to look for: Request documentation proving compliance with relevant standards and certifications.
Step 7: Finalize Terms and Conditions
Before placing an order, clearly outline the terms and conditions of the purchase, including payment terms, delivery schedules, and warranty provisions.
– Why it matters: This clarity helps prevent misunderstandings and protects both parties in the transaction.
– What to look for: Ensure that terms are fair and that they align with your operational timelines and budget constraints.
By following these steps, B2B buyers can navigate the complexities of sourcing metal brackets effectively, ensuring they select the right products and suppliers for their specific needs.
Comprehensive Cost and Pricing Analysis for bracket metal Sourcing
What Are the Key Cost Components in Bracket Metal Sourcing?
When sourcing bracket metal, understanding the cost structure is essential for making informed purchasing decisions. The primary components include:
-
Materials: The type of metal used (e.g., stainless steel, aluminum, galvanized steel) significantly affects cost. Higher-grade materials often command a premium due to their durability and corrosion resistance.
-
Labor: Labor costs are influenced by regional wage rates and the complexity of manufacturing processes. Countries with lower labor costs may provide competitive pricing, but it’s crucial to ensure quality standards.
-
Manufacturing Overhead: This encompasses costs associated with equipment, utilities, and facility maintenance. Efficient manufacturing processes can help reduce overhead, translating to lower prices for buyers.
-
Tooling: Custom tooling can be a significant upfront cost, especially for specialized designs. However, these costs can be amortized over larger production runs, making bulk purchases more cost-effective.
-
Quality Control (QC): Implementing stringent QC measures ensures product reliability but adds to the cost. Buyers should evaluate the balance between acceptable quality levels and associated costs.
-
Logistics: Shipping and handling fees can vary widely based on distance, mode of transport, and packaging requirements. International buyers should be aware of potential tariffs and customs duties that can further inflate costs.
-
Margin: The supplier’s profit margin can vary depending on competition and demand. Understanding the market landscape can help buyers negotiate better pricing.
How Do Price Influencers Affect Bracket Metal Costs?
Several factors can influence the pricing of bracket metal:
-
Volume/MOQ: Suppliers often provide discounts for larger orders. Understanding the minimum order quantity (MOQ) can help buyers optimize costs.
-
Specifications and Customization: Custom designs typically incur additional costs due to unique tooling and production processes. Buyers should weigh the necessity of customization against potential price increases.
-
Material Quality and Certifications: Premium materials or those with specific certifications (e.g., ISO, ASTM) may come at a higher cost. Buyers should assess the value of these certifications based on their application needs.
-
Supplier Factors: The supplier’s reputation, reliability, and production capabilities play a critical role in pricing. Established suppliers may charge higher prices but offer better quality assurance and service.
-
Incoterms: The agreed terms of shipping (e.g., FOB, CIF) can significantly impact overall costs. Understanding these terms is crucial for managing logistics expenses effectively.
What Tips Can Help Buyers Achieve Cost-Efficiency in Bracket Metal Sourcing?
For international B2B buyers, particularly those from Africa, South America, the Middle East, and Europe, several strategies can enhance cost-efficiency:
-
Negotiate Effectively: Establishing a strong relationship with suppliers can lead to better pricing. Don’t hesitate to negotiate terms, especially for long-term contracts or bulk purchases.
-
Consider Total Cost of Ownership (TCO): Look beyond the purchase price. Evaluate factors such as maintenance, longevity, and potential failure costs to gain a clearer picture of overall expenses.
-
Pricing Nuances for International Transactions: Be aware of currency fluctuations and international shipping costs. Engaging in forward contracts or bulk shipping can mitigate some of these risks.
-
Research Local Regulations: Understanding import duties and compliance requirements in the buyer’s country can prevent unexpected costs.
-
Explore Multiple Suppliers: Conduct market research to identify various suppliers. This not only aids in finding competitive pricing but also diversifies risk in the supply chain.
Conclusion
While sourcing bracket metal involves various cost components and price influencers, applying strategic purchasing practices can lead to significant savings. By leveraging negotiation tactics and understanding the full scope of costs, international buyers can make informed decisions that align with their business objectives. Always consider indicative pricing as a guideline, as actual costs can vary based on the dynamic market conditions.
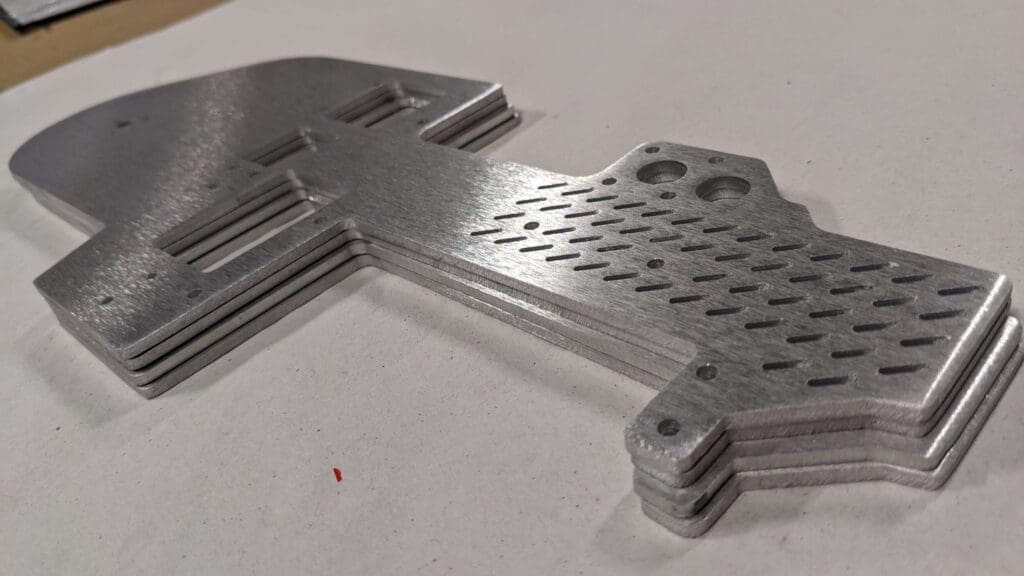
A stock image related to bracket metal.
Alternatives Analysis: Comparing bracket metal With Other Solutions
Exploring Alternatives: How Does Bracket Metal Compare to Other Solutions?
In the world of construction and manufacturing, choosing the right support systems is crucial for ensuring stability, efficiency, and cost-effectiveness. Bracket metal is a popular choice due to its strength and versatility; however, there are several alternative solutions available that can also meet specific project needs. This section will compare bracket metal against two viable alternatives: wooden brackets and plastic brackets.
Comparison Table of Bracket Metal and Alternatives
Comparison Aspect | Bracket Metal | Wooden Brackets | Plastic Brackets |
---|---|---|---|
Performance | High load-bearing capacity | Moderate load capacity | Low load capacity |
Cost | Moderate to High | Low to Moderate | Low |
Ease of Implementation | Requires tools for installation | Easy to install with basic tools | Very easy to install, often with adhesive |
Maintenance | Low (rust-resistant options available) | Moderate (can rot or warp) | Low (durable, but can become brittle) |
Best Use Case | Heavy-duty applications, industrial use | Aesthetic applications, light-duty support | Lightweight assemblies, temporary structures |
Detailed Breakdown of Alternatives
What are the Pros and Cons of Wooden Brackets?
Wooden brackets are a traditional alternative that can provide aesthetic appeal and are often used in residential applications. They are generally less expensive than metal brackets, making them a cost-effective solution for projects with budget constraints. However, wooden brackets have a moderate load capacity and can suffer from issues such as warping or rotting over time, especially in humid conditions. They are best used in settings where appearance is a priority and the load requirements are not too demanding.
How Do Plastic Brackets Stack Up Against Bracket Metal?
Plastic brackets are another alternative, often utilized in lightweight applications and temporary structures. They are easy to install, sometimes requiring no tools at all, and are generally resistant to corrosion and moisture. However, plastic brackets typically have a lower load-bearing capacity compared to both metal and wooden options, making them unsuitable for heavy-duty applications. They are ideal for scenarios where ease of installation and low cost are prioritized over structural integrity.
Conclusion: How to Choose the Right Solution for Your Needs
When selecting between bracket metal and its alternatives, B2B buyers should consider the specific requirements of their projects. For heavy-duty industrial applications, bracket metal remains the superior choice due to its strength and durability. If aesthetics and cost are primary concerns, wooden brackets may be suitable for lighter applications. For temporary setups or less demanding environments, plastic brackets offer a practical and easy-to-use solution. Ultimately, understanding the performance, cost, maintenance, and best use cases of each option will guide buyers in making the most informed decision for their unique project needs.
Essential Technical Properties and Trade Terminology for bracket metal
What Are the Key Technical Properties of Bracket Metal?
Understanding the technical specifications of bracket metal is essential for B2B buyers, especially when making informed purchasing decisions. Here are some critical properties to consider:
1. Material Grade
The material grade of bracket metal, such as stainless steel, aluminum, or galvanized steel, directly impacts its strength, corrosion resistance, and suitability for specific applications. For instance, stainless steel is preferred for outdoor applications due to its resistance to rust and weathering, while aluminum offers lightweight options for easy handling.
2. Thickness
The thickness of the metal bracket is crucial for determining its load-bearing capacity. Common thicknesses range from 1/8 inch to 1/4 inch. Thicker brackets can support heavier loads and are typically used in structural applications. Buyers must evaluate the anticipated load to select the appropriate thickness.
3. Tolerance
Tolerance refers to the allowable variation in dimensions, which is critical for ensuring that brackets fit correctly in their intended applications. Tight tolerances are essential in precision applications, such as robotics or machinery, where even minor deviations can lead to malfunctions or safety issues.
4. Finish
The surface finish of bracket metal affects both aesthetic appeal and functionality. Common finishes include powder coating, anodizing, or galvanization. A well-applied finish not only enhances appearance but also improves corrosion resistance, making it vital for outdoor and industrial applications.
5. Load Capacity
Load capacity indicates the maximum weight a bracket can support without failure. This specification is often tested according to industry standards and should be matched against the intended use case. Understanding load capacity helps prevent structural failures and ensures safety.
6. Mounting Configuration
The design of mounting holes and brackets determines how and where the metal can be installed. Features such as pre-drilled holes, slots, or brackets with multiple mounting options increase versatility and ease of installation, which can significantly reduce labor costs.
What Are Common Trade Terms Used in Bracket Metal Procurement?
Familiarity with industry terminology is vital for effective communication and negotiation. Here are some essential terms:
1. OEM (Original Equipment Manufacturer)
An OEM produces components that are used in the manufacturing of another company’s products. For B2B buyers, understanding OEM relationships can help ensure that the components meet specific quality and compatibility standards.
2. MOQ (Minimum Order Quantity)
MOQ refers to the smallest quantity of a product that a supplier is willing to sell. Knowing the MOQ is crucial for budget planning and inventory management, especially for businesses that may require smaller quantities for specific projects.
3. RFQ (Request for Quotation)
An RFQ is a document that solicits price proposals from suppliers. It outlines the specifications, quantities, and delivery timelines for the products needed. Issuing an RFQ is an effective way to compare pricing and services from different suppliers, ensuring the best deal.
4. Incoterms (International Commercial Terms)
Incoterms are standardized trade terms that define the responsibilities of buyers and sellers in international transactions. Understanding these terms helps clarify issues such as shipping costs, risk transfer, and delivery obligations, which can significantly impact the total cost of procurement.
5. Lead Time
Lead time refers to the time taken from placing an order to receiving the product. This metric is crucial for project management and planning, as longer lead times can affect project timelines and operational efficiency.
6. Certification Standards
Certification standards, such as ISO or ASTM, indicate that the products meet specific quality and safety requirements. Familiarity with these standards can help buyers ensure that they are purchasing high-quality products that comply with local regulations.
By understanding these technical properties and trade terms, international B2B buyers can make informed decisions and establish strong supplier relationships, ultimately leading to better project outcomes and reduced costs.
Navigating Market Dynamics and Sourcing Trends in the bracket metal Sector
What Are the Key Trends Shaping the Bracket Metal Market?
The global bracket metal market is witnessing significant growth, driven by the increasing demand for structural support across various industries, including construction, automotive, and aerospace. Key trends include the integration of advanced manufacturing technologies such as automation and robotics, which enhance production efficiency and reduce costs. Additionally, the rise of e-commerce platforms is reshaping how B2B buyers source materials, making it easier for international buyers, particularly from Africa, South America, the Middle East, and Europe, to access a broader range of products.
Emerging trends also highlight the demand for customized solutions. International B2B buyers are increasingly looking for manufacturers that can provide tailored bracket metal solutions to meet specific project requirements. This customization trend is supported by advancements in 3D printing and CNC machining, allowing for rapid prototyping and production of complex designs. Furthermore, the push towards lightweight materials in industries like automotive and aerospace is driving innovation in bracket designs, with manufacturers exploring materials such as aluminum and high-strength alloys.
The market dynamics are also influenced by geopolitical factors and economic conditions. Buyers should be aware of potential supply chain disruptions due to trade policies or regional conflicts. Establishing strong relationships with multiple suppliers can mitigate risks and ensure a steady supply of materials.
How Does Sustainability Impact the Sourcing of Bracket Metal?
Sustainability is increasingly becoming a core consideration for B2B buyers in the bracket metal sector. The environmental impact of metal production, including greenhouse gas emissions and resource depletion, is prompting companies to seek more sustainable sourcing options. Buyers are encouraged to prioritize suppliers that demonstrate a commitment to sustainability through the use of recycled materials and eco-friendly production processes.
Moreover, ethical sourcing practices are gaining traction, with international buyers increasingly scrutinizing their supply chains for transparency and fairness. This includes ensuring that materials are sourced from suppliers who adhere to labor rights and environmental regulations. Certifications such as ISO 14001 for environmental management and Fair Trade can serve as indicators of a supplier’s commitment to ethical practices.
Investing in ‘green’ materials, such as recycled metals or those certified by recognized environmental organizations, not only aligns with corporate social responsibility goals but can also enhance brand reputation. As consumers and businesses alike become more environmentally conscious, choosing sustainable bracket metal solutions can provide a competitive edge in the marketplace.
What Is the Historical Context of Bracket Metal Development?
The evolution of bracket metal can be traced back to the early days of construction and manufacturing, where simple metal supports were used to provide stability and strength to structures. Over time, advancements in metallurgy and manufacturing techniques led to the development of more specialized and robust designs.
The industrial revolution marked a significant turning point, as mass production techniques enabled the widespread use of bracket metal in various applications. With the advent of modern technology, bracket designs have become more intricate and tailored to meet specific engineering requirements, reflecting the ongoing innovation in this sector.
Today, the bracket metal market continues to evolve, driven by technological advancements and changing consumer preferences, making it essential for international B2B buyers to stay informed about the latest developments and trends.
Frequently Asked Questions (FAQs) for B2B Buyers of bracket metal
-
How do I choose the right metal bracket for my project?
Selecting the appropriate metal bracket involves considering several factors: the weight and type of load it will bear, the material compatibility, and the environment in which it will be used. For heavy-duty applications, opt for galvanized steel or stainless steel brackets that offer durability and corrosion resistance. Additionally, evaluate the dimensions and design of the bracket to ensure it fits your specific requirements. Consulting with suppliers about their product specifications and load ratings can provide further guidance. -
What are the key advantages of using metal brackets in construction?
Metal brackets offer numerous advantages, including enhanced strength, durability, and resistance to environmental factors like moisture and temperature fluctuations. They provide reliable support for various structures, including shelves, furniture, and frameworks. Metal brackets are also easy to install and can be customized to meet specific project needs, making them a versatile choice for both residential and commercial applications. -
What should I consider when vetting international suppliers for metal brackets?
When vetting international suppliers, prioritize their reputation, experience, and compliance with quality standards. Request samples to assess product quality and ensure they meet your specifications. Additionally, check for certifications such as ISO 9001, which indicate a commitment to quality management. It’s also beneficial to read customer reviews and testimonials to gauge reliability and service levels. Establishing clear communication channels can help facilitate smoother transactions. -
What are typical minimum order quantities (MOQs) for metal brackets?
Minimum order quantities for metal brackets can vary significantly based on the supplier and the specific type of bracket. Generally, MOQs range from 100 to 500 pieces for standard designs, while customized brackets may require higher quantities to justify production costs. Discussing your project needs with suppliers can help you negotiate MOQs that align with your purchasing capabilities. -
What payment terms should I expect when sourcing metal brackets internationally?
Payment terms for international transactions often include options such as letter of credit, advance payment, or net terms (e.g., net 30, net 60). It’s essential to clarify these terms with your supplier upfront to avoid misunderstandings. Ensure that you understand any additional fees that may apply, such as currency conversion or transaction fees, and consider using secure payment methods to protect your investment.
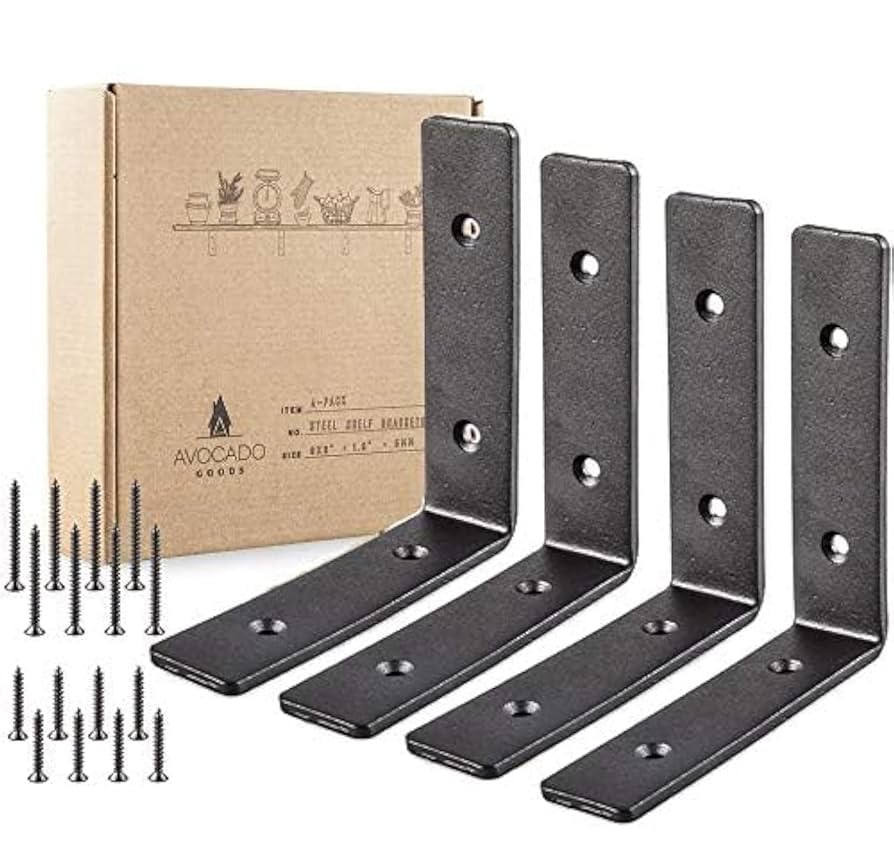
A stock image related to bracket metal.
-
How can I ensure quality assurance (QA) for my metal bracket orders?
To ensure quality assurance, establish clear specifications and standards before placing an order. Request documentation from your supplier, such as certificates of compliance and test reports. Consider conducting inspections either in-person or through third-party services, particularly for large orders. Establishing a robust communication line with your supplier can also help resolve any quality issues that may arise during production. -
What logistics considerations should I keep in mind when importing metal brackets?
When importing metal brackets, consider factors such as shipping methods, lead times, and customs regulations in your country. Choose a reliable freight forwarder familiar with the specifics of your product and destination. Additionally, ensure that your supplier provides accurate documentation to facilitate smooth customs clearance. Planning for potential delays and understanding import duties can help you manage costs effectively. -
Can I customize metal brackets to fit my specific needs?
Yes, many suppliers offer customization options for metal brackets, including size, shape, and finish. When discussing customization, provide detailed specifications, including load requirements and design preferences. Some manufacturers may require a minimum order quantity for customized products, so be prepared for potential cost implications. Collaborating closely with your supplier can ensure that the final product meets your exact needs and enhances your project’s success.
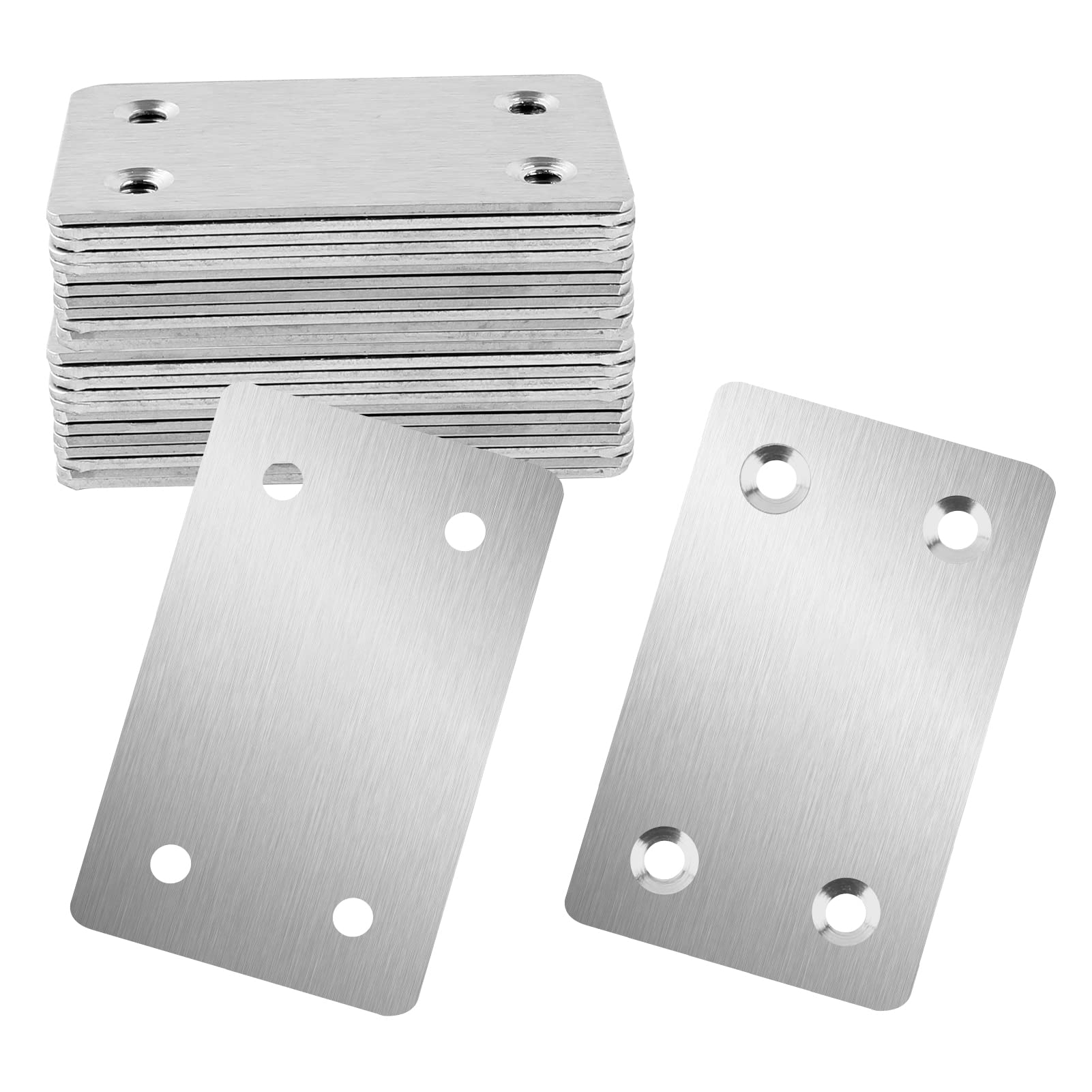
A stock image related to bracket metal.
Important Disclaimer & Terms of Use
⚠️ Important Disclaimer
The information provided in this guide, including content regarding manufacturers, technical specifications, and market analysis, is for informational and educational purposes only. It does not constitute professional procurement advice, financial advice, or legal advice.
While we have made every effort to ensure the accuracy and timeliness of the information, we are not responsible for any errors, omissions, or outdated information. Market conditions, company details, and technical standards are subject to change.
B2B buyers must conduct their own independent and thorough due diligence before making any purchasing decisions. This includes contacting suppliers directly, verifying certifications, requesting samples, and seeking professional consultation. The risk of relying on any information in this guide is borne solely by the reader.
Strategic Sourcing Conclusion and Outlook for bracket metal
In navigating the complexities of sourcing bracket metal, international B2B buyers must prioritize strategic partnerships and a thorough understanding of market dynamics. The diverse range of materials available—from stainless steel to aluminum—highlights the importance of selecting the right type of bracket for specific applications, ensuring both durability and cost-effectiveness. Establishing relationships with reliable suppliers can lead to better pricing, consistent quality, and timely deliveries, which are crucial for maintaining competitive advantage.
How Can Strategic Sourcing Enhance Your Supply Chain?
Strategic sourcing not only mitigates risks associated with fluctuating metal prices but also fosters innovation through collaboration with manufacturers. Buyers should leverage data analytics to anticipate trends and optimize inventory management, ultimately driving operational efficiency. Understanding regional regulations and standards can further enhance compliance and reduce potential disruptions in the supply chain.
What’s Next for International B2B Buyers?
As the global market for bracket metal continues to evolve, staying ahead requires agility and a proactive approach. Engage with local suppliers in Africa, South America, the Middle East, and Europe to tap into emerging markets and foster sustainable practices. By prioritizing strategic sourcing today, you position your business for growth and resilience in the future. Embrace these insights, and take the next step towards refining your sourcing strategy for bracket metal.