Master Plugging Electrical: Your Complete Guide to Efficiency (2025)
Introduction: Navigating the Global Market for plugging electrical
Navigating the complexities of sourcing plugging electrical solutions can pose significant challenges for international B2B buyers, particularly in regions like Africa, South America, the Middle East, and Europe. Understanding the intricacies of plugging—ranging from types and applications to the nuances of supplier vetting and cost implications—is essential for informed decision-making. This guide offers a comprehensive overview that addresses these key aspects, ensuring that businesses can effectively evaluate their options when integrating plugging mechanisms into their operations.
The guide delves into the different types of plugging methods available for both DC and AC motors, highlighting their respective applications in various industries such as manufacturing, construction, and transportation. Buyers will gain insights into how to assess suppliers based on reliability, performance, and compliance with regional standards. Additionally, we will explore cost considerations, including initial investment versus long-term operational efficiency, to help buyers make financially sound choices.
By equipping international B2B buyers with actionable insights and a structured approach to sourcing plugging electrical solutions, this guide aims to simplify the purchasing process. It empowers businesses to navigate the global market confidently, ensuring that they are well-prepared to meet their operational needs while optimizing performance and minimizing risks.
Understanding plugging electrical Types and Variations
Type Name | Key Distinguishing Features | Primary B2B Applications | Brief Pros & Cons for Buyers |
---|---|---|---|
DC Motor Plugging | Reverses armature voltage to create reverse current. | Elevators, cranes, presses | Pros: Fast stopping time; effective for quick reversals. Cons: High mechanical shock; can damage equipment. |
AC Induction Plugging | Interchanges supply leads to reverse stator voltage. | Manufacturing machinery, conveyors | Pros: Strong braking effect; suitable for high inertia loads. Cons: Induces heat; requires robust motor starters. |
Dynamic Braking | Uses resistors to dissipate energy as heat during braking. | Electric vehicles, industrial fans | Pros: Less mechanical stress; more energy-efficient than plugging. Cons: Slower stop; may require additional components. |
Regenerative Braking | Captures energy and feeds it back into the system. | Electric trains, hybrid vehicles | Pros: Energy-efficient; reduces operational costs. Cons: Complex systems; may not be suitable for all applications. |
Anti-Plugging Control | Prevents sudden reversals to protect equipment. | Automated systems, robotics | Pros: Reduces wear and tear; enhances equipment longevity. Cons: Slower response time; may limit operational flexibility. |
What are the Characteristics of DC Motor Plugging?
DC motor plugging involves reversing the polarity of the armature voltage to create a reverse current, effectively stopping the motor quickly. This method is particularly effective in applications requiring rapid stopping, such as elevators and cranes. However, buyers should consider the potential for high mechanical shock loads, which can lead to equipment damage if not properly managed. Additionally, the high current generated during plugging necessitates circuit resistance to prevent damage, which may require additional investment in components.
How Does AC Induction Plugging Work?
In AC induction plugging, the stator voltage is reversed by interchanging two supply leads. This results in the rotor spinning faster than the stator’s magnetic field, creating a strong braking effect. This method is suitable for high-inertia loads commonly found in manufacturing machinery and conveyors. While it offers effective stopping power, buyers must be aware of the heat generated during the process, which may necessitate enhanced cooling solutions and robust motor starters to handle the increased demands.
What are the Advantages of Dynamic Braking?
Dynamic braking utilizes resistors to dissipate energy as heat, providing a less abrupt stop compared to plugging methods. This technique is often employed in electric vehicles and industrial fans, where a smoother deceleration is preferred. Buyers benefit from reduced mechanical stress on components, leading to longer equipment life. However, the trade-off is a slower stopping time, which may not be suitable for all applications, particularly those requiring immediate stops.
Why Choose Regenerative Braking?
Regenerative braking captures kinetic energy during braking and feeds it back into the power supply, making it highly energy-efficient. This method is commonly used in electric trains and hybrid vehicles, where operational costs can be significantly reduced. However, the complexity of regenerative systems can be a barrier for some buyers, as they require specialized components and expertise for installation and maintenance.
What is Anti-Plugging Control and Its Benefits?
Anti-plugging control is designed to prevent sudden reversals of motor direction, protecting equipment from excessive wear and tear. This control method is particularly useful in automated systems and robotics, where maintaining equipment longevity is crucial. While it enhances reliability, the trade-off is a slower response time, which might limit operational flexibility in certain applications. Buyers must weigh these factors when considering the implementation of anti-plugging systems in their operations.
Key Industrial Applications of plugging electrical
Industry/Sector | Specific Application of plugging electrical | Value/Benefit for the Business | Key Sourcing Considerations for this Application |
---|---|---|---|
Manufacturing | Quick deceleration of conveyor systems | Enhances operational efficiency and safety | Ensure compatibility with existing motor systems and load types |
Construction | Braking in cranes and hoists | Provides rapid stopping capabilities for safety | Focus on high-quality components to withstand heavy loads |
Transportation | Emergency braking in electric vehicles | Increases safety during critical situations | Consider regulations and standards for automotive applications |
Mining | Control of drilling equipment | Allows for precise stopping and reversing actions | Assess environmental conditions and required certifications |
Material Handling | Stopping and reversing in automated guided vehicles (AGVs) | Improves workflow and productivity | Evaluate battery and power supply requirements for efficiency |
How is Plugging Electrical Used in Manufacturing for Conveyor Systems?
In manufacturing, plugging electrical is essential for quick deceleration of conveyor systems. This technique allows for rapid stopping and can prevent accidents in high-speed environments. International buyers from regions like Africa and South America should consider the specific voltage and power ratings of their motors to ensure compatibility with plugging systems. Additionally, sourcing durable components that can withstand the high mechanical stresses associated with frequent stopping is crucial for maintaining operational efficiency.
What Role Does Plugging Electrical Play in Construction Equipment like Cranes?
In the construction sector, plugging electrical is utilized in cranes and hoists to provide rapid braking capabilities. This application is vital for ensuring the safety of personnel and equipment during lifting operations. Buyers should prioritize sourcing high-quality, robust motor starters that can handle the intense inrush currents associated with sudden stops. Evaluating suppliers for industry certifications can help ensure compliance with safety standards prevalent in Europe and the Middle East.
How Does Plugging Electrical Enhance Safety in Electric Vehicles?
Plugging electrical serves a critical function in the transportation industry, particularly in emergency braking systems for electric vehicles. By allowing for immediate stopping, it increases safety in potentially hazardous driving situations. B2B buyers in this sector must consider local regulations and standards when sourcing components, ensuring that they meet stringent safety requirements. Collaborating with suppliers who have experience in automotive applications can provide valuable insights into best practices.
In What Ways is Plugging Electrical Applied in Mining Operations?
In mining, plugging electrical is crucial for controlling drilling equipment, enabling precise stopping and reversing actions. This capability is vital for operational safety and efficiency, as it allows miners to manage equipment effectively in challenging environments. Buyers should assess the environmental conditions of their operations and ensure that sourced components are rated for durability in harsh conditions, including dust and moisture. Understanding local regulations and certifications can also facilitate smoother procurement processes.
How Does Plugging Electrical Improve Workflow in Material Handling Systems?
For material handling operations, plugging electrical is employed in automated guided vehicles (AGVs) to stop and reverse movements efficiently. This application enhances workflow and productivity by allowing for quick adjustments in transport routes. International buyers should evaluate the battery and power supply requirements of their AGVs to ensure optimal performance. Partnering with suppliers who offer comprehensive support and customization options can further enhance operational capabilities.
3 Common User Pain Points for ‘plugging electrical’ & Their Solutions
Scenario 1: Frequent Equipment Failures Due to Abrupt Stops
The Problem: Many B2B buyers, particularly in manufacturing and construction sectors across Africa and South America, face the challenge of equipment failures due to the harsh impacts of plugging electrical. The rapid stopping and potential reversal of motors can induce significant mechanical shock loads, leading to wear and tear on both the motors and connected machinery. This not only results in costly repairs and replacements but also leads to production downtime, negatively affecting operational efficiency.
The Solution: To mitigate the risks associated with plugging, buyers should consider investing in advanced motor control systems that incorporate zero-speed switches and overload protection. These systems can help in monitoring the motor’s speed and automatically disconnecting power to prevent abrupt stops. Additionally, proper sizing of motor starters is crucial; increasing the horsepower rating can help accommodate the sudden reversals without damaging the motor. Implementing regular maintenance schedules to inspect wear components will also extend the lifespan of the machinery and ensure consistent performance.
Scenario 2: High Energy Costs from Inefficient Braking
The Problem: In regions like the Middle East and Europe, where energy costs can be significant, many B2B buyers struggle with the inefficiencies of plugging electrical as a braking method. The process generates excess heat and consumes more energy than necessary, leading to inflated operational costs. This inefficiency is particularly concerning for businesses that rely on high-volume production, where every kilowatt-hour counts.
The Solution: To combat this issue, buyers should evaluate alternative braking methods, such as regenerative braking, which not only stops the motor effectively but also recovers energy for reuse in the system. When sourcing equipment, look for motors and drives that support regenerative capabilities. Additionally, investing in smart energy management systems can help monitor energy consumption patterns and identify areas for improvement, thereby optimizing operational efficiency and reducing overall costs.
Scenario 3: Challenges in Motor Direction Control
The Problem: B2B buyers in sectors such as logistics and material handling may encounter difficulties in controlling motor direction using plugging, especially when precise stopping or reversing is required. The abrupt nature of plugging can lead to issues such as misalignment of loads or unintended motor reversals, which can compromise safety and efficiency.
The Solution: Implementing a more sophisticated control strategy can alleviate these challenges. Utilize variable frequency drives (VFDs) that allow for smoother acceleration and deceleration, thereby reducing the likelihood of abrupt stops. Additionally, integrating anti-plugging features into the control circuit, such as using normally closed zero-speed switches, can provide an extra layer of safety by preventing the motor from being energized in the reverse direction until it has completely stopped. Training personnel on the proper operation of these systems can further enhance safety and operational reliability, ensuring that motor direction control is both precise and efficient.
Strategic Material Selection Guide for plugging electrical
What Materials Are Commonly Used for Plugging Electrical Applications?
When selecting materials for plugging electrical applications, it is essential to consider their properties, advantages, disadvantages, and suitability for specific environments. Below, we analyze four common materials: copper, aluminum, stainless steel, and thermoplastics.
How Does Copper Perform in Plugging Electrical Applications?
Copper is widely recognized for its excellent electrical conductivity and is often the go-to material for electrical connections. Key properties include a high melting point of around 1,984°F (1,085°C) and good resistance to corrosion, particularly in non-oxidizing environments.
Pros: Copper’s high conductivity ensures minimal energy loss, making it ideal for high-performance applications. It is also relatively easy to manufacture and can be easily formed into various shapes.
Cons: However, copper is susceptible to corrosion in certain environments, especially when exposed to moisture or acidic conditions. Additionally, it is more expensive than some alternatives, which may be a consideration for budget-conscious buyers.
Impact on Application: In applications involving high electrical loads, such as motors and generators, copper’s performance is unmatched. However, it is crucial to ensure compatibility with the specific media and environmental conditions.
Considerations for International Buyers: Compliance with international standards such as ASTM and IEC is vital. Buyers in regions like Africa and South America should be aware of local corrosion risks and choose copper alloys that can withstand specific environmental challenges.
What Role Does Aluminum Play in Plugging Electrical Applications?
Aluminum is another popular choice due to its lightweight and cost-effective nature. It has a melting point of approximately 1,221°F (660.3°C) and offers decent conductivity, though not as high as copper.
Pros: The primary advantage of aluminum is its lower cost and lighter weight, making it easier to handle and install. It also exhibits good resistance to corrosion, especially when anodized.
Cons: The downside is its lower electrical conductivity, which can lead to higher energy losses in some applications. Additionally, aluminum can be more challenging to work with due to its tendency to oxidize, which can affect electrical connections.
Impact on Application: Aluminum is suitable for applications where weight is a critical factor, such as in transportation or aerospace. However, its lower conductivity may limit its use in high-load scenarios.
Considerations for International Buyers: Buyers should ensure compliance with local standards and consider the potential for oxidation in humid environments, particularly in the Middle East and Africa.
Why Choose Stainless Steel for Plugging Electrical Applications?
Stainless steel is renowned for its durability and corrosion resistance, making it an excellent choice for harsh environments. With a melting point of around 2,500°F (1,370°C), it can withstand high temperatures.
Pros: Its strength and resistance to corrosion make stainless steel ideal for applications exposed to moisture or chemicals. It is also highly durable, which can reduce maintenance costs over time.
Cons: The primary drawback is its higher cost compared to other materials like aluminum and copper. Additionally, stainless steel has lower electrical conductivity, which may not be suitable for all applications.
Impact on Application: Stainless steel is often used in marine or industrial applications where exposure to corrosive elements is a concern. However, its lower conductivity may necessitate larger components to achieve the same performance as copper or aluminum.
Considerations for International Buyers: Ensure compliance with standards such as ASTM and ISO. Buyers in Europe may prefer stainless steel for its durability, especially in coastal areas.
How Do Thermoplastics Compare in Plugging Electrical Applications?
Thermoplastics are increasingly being used in electrical applications due to their insulating properties and resistance to chemicals. Common types include PVC and nylon, which can withstand temperatures up to 200°F (93°C).
Pros: Thermoplastics are lightweight, cost-effective, and provide excellent electrical insulation. They are also resistant to many chemicals, making them suitable for various environments.
Cons: However, thermoplastics have lower mechanical strength compared to metals and may not withstand high temperatures or heavy loads. They can also degrade over time when exposed to UV light.
Impact on Application: Thermoplastics are ideal for applications requiring insulation or protection from environmental factors. However, they may not be suitable for high-load applications where mechanical strength is critical.
Considerations for International Buyers: Buyers should consider local temperature and chemical exposure conditions when selecting thermoplastics. Compliance with standards such as JIS and DIN is also essential.
Summary Table of Material Selection for Plugging Electrical
Material | Typical Use Case for plugging electrical | Key Advantage | Key Disadvantage/Limitation | Relative Cost (Low/Med/High) |
---|---|---|---|---|
Copper | High-performance electrical connections | Excellent conductivity | Susceptible to corrosion | High |
Aluminum | Lightweight applications | Cost-effective and lightweight | Lower conductivity | Medium |
Stainless Steel | Harsh environment applications | Durability and corrosion resistance | Higher cost and lower conductivity | High |
Thermoplastics | Insulation and protection | Lightweight and excellent insulation | Lower mechanical strength | Low |
This strategic material selection guide provides essential insights for international B2B buyers looking to make informed decisions about materials for plugging electrical applications. By understanding the properties, advantages, and limitations of each material, buyers can better align their choices with specific application requirements and regional considerations.
In-depth Look: Manufacturing Processes and Quality Assurance for plugging electrical
What Are the Key Stages in the Manufacturing Process for Plugging Electrical Components?
Manufacturing electrical components for plugging systems involves several critical stages that ensure both functionality and durability. Each stage requires specific techniques and materials to meet industry standards and fulfill the operational demands of various applications.
1. Material Preparation: What Materials Are Used for Plugging Electrical Components?
The first step in manufacturing plugging electrical components is material selection. Common materials include:
- Copper: Used for electrical contacts due to its excellent conductivity.
- Insulating Plastics: Such as thermoplastics and thermosetting plastics, which provide electrical insulation and mechanical strength.
- Steel: Often used for structural components and housing due to its strength and durability.
These materials undergo extensive quality checks to confirm they meet the required specifications. This includes verifying conductivity, tensile strength, and temperature resistance.
2. Forming: How Are Electrical Components Shaped and Molded?
The forming stage involves shaping the raw materials into desired forms through various methods:
- Injection Molding: This technique is commonly used for producing plastic housings and insulating components. It allows for high precision and repeatability.
- Stamping: Metal parts are produced by stamping sheets of metal into specific shapes. This method is efficient for high-volume production.
- Machining: For components requiring tight tolerances, machining processes such as turning, milling, or drilling are employed.
Each forming method is selected based on the component’s design, volume requirements, and material properties.
3. Assembly: How Are Different Components Integrated?
Once individual parts are formed, they are assembled into a complete unit. The assembly process may include:
- Soldering: Used for connecting electrical contacts securely.
- Mechanical Fastening: Screws, rivets, or clips may be employed to hold components together.
- Wiring: Internal wiring is connected to ensure proper electrical functionality.
Quality control during assembly is crucial; components must fit precisely to avoid operational failures.
4. Finishing: What Surface Treatments Are Applied?
Finishing processes enhance the durability and appearance of electrical components. Common finishing techniques include:
- Plating: Electroplating with nickel or gold can improve conductivity and corrosion resistance.
- Coating: Application of protective coatings can prevent wear and tear from environmental factors.
- Polishing: This step enhances the aesthetic appeal and ensures smooth surfaces for electrical connections.
These finishing processes are essential to extend the lifespan of the components, especially in demanding applications.
What Quality Assurance Standards Are Relevant for Plugging Electrical Components?
Quality assurance is paramount in the manufacturing of plugging electrical components to ensure safety, reliability, and compliance with international standards. Understanding these standards helps B2B buyers assess suppliers effectively.
1. International Standards: Which Certifications Should Buyers Look For?
The most relevant international quality management standards include:
- ISO 9001: This standard focuses on quality management systems and is applicable to any organization. It ensures that manufacturers consistently meet customer and regulatory requirements.
- IEC 60947: Specific to low-voltage switchgear and controlgear, this standard covers safety and performance for electrical devices.
In addition to ISO standards, buyers should look for industry-specific certifications such as:
- CE Marking: Indicates compliance with EU safety, health, and environmental protection legislation.
- API Standards: Relevant for components used in the oil and gas industry, ensuring reliability under extreme conditions.
2. What Are the Key Quality Control Checkpoints in Manufacturing?
Quality control (QC) is integrated into every stage of the manufacturing process. Common QC checkpoints include:
- Incoming Quality Control (IQC): Inspection of raw materials upon arrival to ensure they meet specified standards.
- In-Process Quality Control (IPQC): Ongoing checks during the manufacturing process to monitor consistency and identify defects early.
- Final Quality Control (FQC): Comprehensive inspection of the finished product before shipment, including performance testing and visual inspections.
Each checkpoint plays a vital role in maintaining quality throughout production.
How Can B2B Buyers Verify Supplier Quality Control Processes?
For international B2B buyers, particularly those from Africa, South America, the Middle East, and Europe, ensuring supplier quality is crucial. Here are some strategies to effectively verify QC processes:
1. Conduct Supplier Audits: What Should Be Included in an Audit?
Regular audits of suppliers can help assess their manufacturing and QC processes. Key areas to evaluate include:
- Documentation: Review quality management system documentation, including process flows and quality manuals.
- Compliance Records: Check for records of compliance with relevant standards and previous audit findings.
- Production Capabilities: Inspect the manufacturing facilities to evaluate equipment and adherence to safety and quality standards.
2. Request Quality Reports: What Information Should Buyers Seek?
Buyers should request detailed quality reports from suppliers, which may include:
- Test Results: Documentation of performance tests conducted on components.
- Non-Conformance Reports: Records of any defects found during manufacturing and corrective actions taken.
- Certificates of Compliance: Proof of adherence to international standards and regulations.
These documents provide insights into the supplier’s commitment to quality.
3. Utilize Third-Party Inspections: How Can Independent Verification Help?
Engaging third-party inspection services can provide an unbiased assessment of a supplier’s quality control measures. These services can perform:
- Random Inspections: Verify product quality during or after production.
- Certification Verification: Ensure that suppliers hold valid certifications and comply with industry standards.
Independent inspections offer an additional layer of security for buyers, especially when dealing with international suppliers.
Conclusion: Why Is Quality Assurance Critical for Plugging Electrical Components?
In summary, the manufacturing processes and quality assurance for plugging electrical components are integral to ensuring reliability and safety. By understanding the stages of manufacturing, relevant standards, and effective verification methods, international B2B buyers can make informed decisions. This knowledge not only helps in selecting reliable suppliers but also ensures that the products meet the necessary operational demands across various industries.
Practical Sourcing Guide: A Step-by-Step Checklist for ‘plugging electrical’
In this practical sourcing guide, we provide a step-by-step checklist designed for B2B buyers interested in procuring plugging electrical solutions. This guide aims to streamline your procurement process, ensuring that you select the most suitable products and suppliers for your specific operational needs.
Step 1: Define Your Technical Specifications
Before starting your sourcing process, clearly outline your technical requirements. This includes the type of motor (DC or AC), voltage specifications, and the desired braking characteristics. Having a detailed specification will help you communicate effectively with suppliers and ensure that the products meet your operational needs.
- Motor Type: Specify whether you need solutions for DC or AC induction motors.
- Voltage Requirements: Identify the voltage levels that are compatible with your existing systems.
Step 2: Research Market Trends and Innovations
Understanding the current trends in plugging technology can provide insights into which products are most effective and efficient. Research innovations such as advanced braking methods or energy-efficient solutions that may enhance your operations.
- Efficiency Improvements: Look for suppliers offering new technologies that minimize energy loss during plugging.
- Safety Features: Investigate products that include enhanced safety mechanisms to reduce risks associated with abrupt stops.
Step 3: Evaluate Potential Suppliers
Thoroughly vet potential suppliers to ensure they meet your quality and reliability standards. Request documentation such as company profiles, case studies, and references from other clients in similar industries.
- Company Reputation: Research online reviews and industry ratings to gauge supplier reliability.
- Experience: Prefer suppliers with a proven track record in your specific industry or application.
Step 4: Verify Supplier Certifications and Compliance
Ensure that your selected suppliers hold relevant certifications and comply with international standards. This is crucial for ensuring product quality and safety, particularly in regions with stringent regulations.
- ISO Certifications: Look for suppliers with ISO 9001 or similar certifications, indicating a commitment to quality management.
- Regional Compliance: Verify that products comply with local regulations, especially if you’re sourcing from different continents.
Step 5: Request Samples and Conduct Testing
Before making a bulk purchase, request samples to evaluate the product’s performance in your operational context. Conduct thorough testing to ensure the plugging solutions work as intended under your specific conditions.
- Performance Evaluation: Test the samples for efficiency, braking speed, and heat generation during operation.
- Compatibility Checks: Ensure that the products integrate seamlessly with your existing systems.
Step 6: Negotiate Terms and Conditions
Once you have selected a supplier, negotiate favorable terms that align with your budget and operational needs. Discuss pricing, delivery timelines, and after-sales support to ensure a smooth procurement process.
- Pricing Structure: Inquire about volume discounts or long-term agreements that may reduce costs.
- Support Services: Ensure the supplier provides adequate technical support and warranty terms.
Step 7: Establish a Long-Term Relationship
After the initial procurement, focus on building a long-term relationship with your supplier. Regular communication and feedback can lead to better service and potential innovations that could benefit your operations in the future.
- Feedback Mechanism: Establish a process for providing feedback on product performance and service.
- Collaboration Opportunities: Explore potential collaborations for future projects or custom solutions tailored to your needs.
By following this checklist, you can ensure a comprehensive and effective sourcing process for plugging electrical solutions, enhancing your operational efficiency and safety.
Comprehensive Cost and Pricing Analysis for plugging electrical Sourcing
What Are the Key Cost Components of Plugging Electrical Sourcing?
When sourcing plugging electrical components, understanding the cost structure is crucial for international B2B buyers. The primary cost components include:
-
Materials: The choice of materials significantly affects the overall cost. High-quality conductors, insulation, and components for plugs and connectors can lead to higher prices. It’s essential to balance quality with cost, particularly when considering the operational environment.
-
Labor: Labor costs vary widely by region. In regions like Africa and South America, labor may be less expensive compared to Europe or the Middle East. However, local expertise in manufacturing and assembly can also influence costs.
-
Manufacturing Overhead: This includes expenses related to factory operations, such as utilities, equipment maintenance, and administrative costs. Efficient manufacturing processes can minimize overhead, impacting the overall price.
-
Tooling: Investment in specialized tooling for production can be significant. For custom or specialized products, tooling costs need to be factored into the pricing model, as they can be substantial upfront expenses.
-
Quality Control (QC): Rigorous quality control measures are vital for ensuring product reliability, particularly in applications that utilize plugging as a braking method. Implementing QC can increase costs but is essential for maintaining high standards.
-
Logistics: Transportation and handling costs can vary based on the distance from the manufacturer to the buyer. Incoterms play a critical role in determining who is responsible for these costs and risks.
-
Margin: Supplier margins can differ based on market competition, demand, and supplier reputation. Buyers should be aware of typical margins in their specific industry to negotiate effectively.
How Do Price Influencers Impact Plugging Electrical Sourcing?
Several factors influence the pricing of plugging electrical components:
-
Volume/MOQ (Minimum Order Quantity): Larger orders often result in lower per-unit prices due to economies of scale. Understanding a supplier’s MOQ can help negotiate better pricing.
-
Specifications and Customization: Custom specifications can lead to increased costs. Buyers should clearly define their requirements and be prepared to discuss how customization impacts pricing.
-
Materials: The quality and type of materials used can drastically alter the price. Buyers should evaluate whether premium materials justify their cost based on the application.
-
Quality and Certifications: Products that meet international safety and quality standards may come at a premium. Buyers in regions with stringent regulations should prioritize certified products, even if they are more expensive.
-
Supplier Factors: The supplier’s reputation, reliability, and location can affect pricing. Established suppliers may charge more but offer better service and quality assurance.
-
Incoterms: Understanding Incoterms is essential for determining costs associated with shipping, insurance, and customs duties. This knowledge can help buyers avoid unexpected expenses.
What Are the Best Buyer Tips for Sourcing Plugging Electrical Components?
To achieve cost efficiency and effective sourcing of plugging electrical components, international B2B buyers should consider the following tips:
-
Negotiate Wisely: Leverage volume purchases and long-term contracts to negotiate better terms. Building a strong relationship with suppliers can also lead to more favorable pricing.
-
Focus on Total Cost of Ownership (TCO): Consider not just the initial purchase price but also installation, maintenance, and operational costs over the product’s lifecycle. This approach can lead to more informed purchasing decisions.
-
Understand Pricing Nuances in Different Regions: Buyers from Africa, South America, the Middle East, and Europe should be aware of regional pricing structures and demand fluctuations. Local market conditions can significantly impact costs.
-
Be Cautious of Indicative Prices: Prices can vary widely based on the factors discussed above. It’s crucial to request detailed quotes and understand what is included in the pricing.
By keeping these insights in mind, international B2B buyers can make more informed decisions when sourcing plugging electrical components, ensuring they achieve the best value for their investments.
Alternatives Analysis: Comparing plugging electrical With Other Solutions
Introduction: What Alternatives Exist to Plugging Electrical?
When considering motor control and braking solutions, plugging electrical stands out for its rapid stopping capability. However, it is essential for international B2B buyers to explore alternative methods that may offer enhanced efficiency, reduced wear, or cost-effectiveness depending on their specific applications. This section compares plugging electrical with regenerative braking and dynamic braking, providing insights to help buyers make informed decisions.
Comparison Table of Braking Solutions
Comparison Aspect | Plugging Electrical | Regenerative Braking | Dynamic Braking |
---|---|---|---|
Performance | Fast stop, high shock load | Converts energy back to supply | Moderate stop, less shock |
Cost | Low initial cost, high maintenance | Higher upfront cost, lower long-term costs | Moderate cost, variable maintenance |
Ease of Implementation | Requires specialized controls | Complex integration needed | Simple setup, less complexity |
Maintenance | High due to wear and tear | Low, fewer components degrade | Moderate, depends on usage |
Best Use Case | Heavy machinery needing rapid stops | Electric vehicles, energy recovery | General industrial applications |
Detailed Breakdown of Alternatives
What Are the Advantages and Disadvantages of Regenerative Braking?
Regenerative braking captures the kinetic energy of a motor when it decelerates and converts it back into electrical energy, which can be reused. This solution is particularly advantageous in applications such as electric vehicles and public transport systems. The primary benefits include energy savings and reduced operational costs over time. However, the initial investment can be high due to the complexity of installation and the need for advanced control systems. Additionally, regenerative braking may not be suitable for all applications, particularly those requiring immediate stopping power.
How Does Dynamic Braking Compare to Plugging Electrical?
Dynamic braking uses a resistor to dissipate the energy produced during braking, creating a controlled deceleration. This method is easier to implement than regenerative braking and is effective in many industrial applications where rapid stops are not as critical. Dynamic braking offers a balance between performance and maintenance, providing moderate stopping power without the harsh shock loads associated with plugging electrical. However, it does not recover energy like regenerative braking, making it less efficient in energy management scenarios.
Conclusion: Choosing the Right Braking Solution for Your Needs
When selecting a braking solution, international B2B buyers must consider the specific demands of their operations. Plugging electrical offers rapid stopping capabilities but comes with high maintenance costs and potential mechanical shocks. On the other hand, regenerative braking is ideal for energy-efficient applications, while dynamic braking offers a more straightforward implementation with moderate performance. Evaluating these factors in light of your operational requirements will help you choose the most effective braking method for your business needs.
Essential Technical Properties and Trade Terminology for plugging electrical
What Are the Key Technical Properties of Plugging Electrical Systems?
Understanding the essential technical properties of plugging electrical systems is crucial for international B2B buyers, particularly those involved in industries such as manufacturing, construction, and automation. Here are some critical specifications that impact performance and reliability:
1. Motor Type Compatibility
Plugging can be utilized in both DC and AC induction motors. For buyers, it’s essential to know the compatibility of the plugging system with the motor type being used. This impacts performance and efficiency; for instance, DC motors require polarity reversal, while AC motors need supply lead interchanges. Ensuring the right motor type can prevent potential damage and inefficiencies.
2. Slip Ratio
The slip ratio (s) in AC induction motors, defined as the difference between the speed of the stator’s rotating magnetic field and the rotor speed, plays a significant role in the effectiveness of plugging. A slip greater than one indicates a strong braking effect. Buyers should consider this property when assessing motor performance during plugging operations, as it influences the torque generated and the motor’s operational efficiency.
3. Inrush Current Rating
When a motor is energized, it experiences an inrush current that can be significantly higher than its normal operating current. This is crucial for B2B buyers to consider when selecting motor starters and protective devices. Inadequate ratings may lead to equipment failure or safety hazards. Therefore, understanding the inrush current can help in specifying components that can withstand such surges.
4. Thermal Resistance
Plugging generates substantial heat due to the abrupt stopping action, making thermal resistance a vital property. Buyers must evaluate the thermal management systems in place, such as cooling fans or heat sinks, to prevent overheating and ensure longevity. This is particularly important in high-frequency applications where frequent stopping and starting occur.
5. Mechanical Shock Tolerance
The abrupt stop caused by plugging can induce mechanical shock loads, which can be detrimental to both the motor and connected equipment. Buyers should assess the mechanical shock tolerance of components and systems to minimize wear and tear, especially in applications like cranes and presses where high inertia loads are common.
6. Control Circuit Design
The design of control circuits, including zero-speed switches and reversing starters, is essential for effective plugging operation. Buyers should ensure that their systems are equipped with appropriate controls to facilitate smooth transitions between directions and prevent unintended damage to equipment.
What Are Common Trade Terms Associated with Plugging Electrical?
Familiarity with industry jargon is vital for effective communication and negotiation in international trade. Here are some key terms that B2B buyers should understand:
1. OEM (Original Equipment Manufacturer)
OEM refers to companies that produce parts or equipment that may be marketed by another manufacturer. Understanding OEM relationships can help buyers identify reliable sources for components and ensure compatibility with existing systems.
2. MOQ (Minimum Order Quantity)
MOQ is the smallest quantity of a product that a supplier is willing to sell. For international buyers, being aware of MOQ can assist in budgeting and inventory management, especially when dealing with suppliers from different regions.
3. RFQ (Request for Quotation)
An RFQ is a document that buyers send to suppliers to request pricing and terms for specific products or services. Crafting a detailed RFQ can lead to better pricing and terms, enabling buyers to make informed purchasing decisions.
4. Incoterms (International Commercial Terms)
Incoterms are a set of international rules that define the responsibilities of buyers and sellers in shipping. Understanding these terms is crucial for managing shipping costs, risks, and responsibilities in international transactions.
5. Zero-Speed Switch
A zero-speed switch is a safety device that ensures the motor stops before the plugging action occurs. This term is essential for buyers looking to implement safety measures in their operations to prevent accidents and equipment damage.
6. Power Contacts
Power contacts are components within a motor starter that connect and disconnect the motor from the power supply. Knowledge of power contacts can help buyers select appropriate starters that can handle the specific demands of plugging operations.
By understanding these technical properties and trade terms, international B2B buyers can make more informed decisions, ensuring efficient and reliable plugging electrical systems in their operations.
Navigating Market Dynamics and Sourcing Trends in the plugging electrical Sector
What Are the Current Market Dynamics and Key Trends in the Plugging Electrical Sector?
The plugging electrical sector is experiencing significant shifts driven by advancements in technology and increasing demand for efficient motor control solutions. Globally, the rise of automation in industries such as manufacturing, construction, and logistics is a key driver. As businesses seek to optimize productivity, the need for systems that can quickly and efficiently stop machinery—like plugging methods—becomes crucial. In regions like Africa and South America, where industries are rapidly modernizing, there is a growing interest in technologies that enhance operational efficiency and reduce downtime.
Emerging trends include the adoption of smart motor control systems that integrate IoT technologies, enabling real-time monitoring and predictive maintenance. This shift not only enhances operational efficiency but also reduces costs associated with unplanned downtime. Additionally, the demand for energy-efficient solutions is prompting manufacturers to innovate in the realm of plugging methods, seeking to minimize energy waste and heat generation during operation. For international B2B buyers, understanding these trends is essential for making informed sourcing decisions that align with their operational needs.
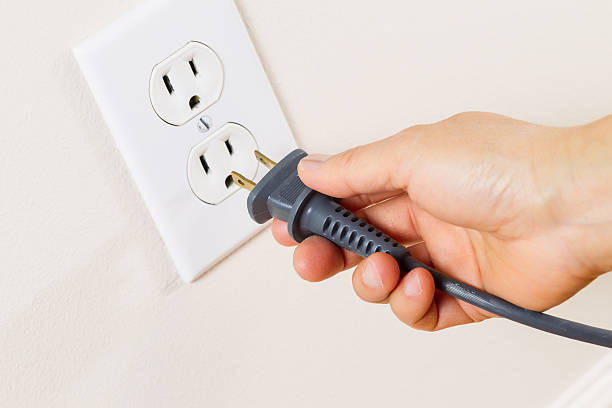
A stock image related to plugging electrical.
How Can Sustainability and Ethical Sourcing Impact the Plugging Electrical Sector?
Sustainability and ethical sourcing are becoming increasingly important in the plugging electrical sector, as businesses and consumers alike prioritize environmental responsibility. The production and disposal of electrical components can have significant environmental impacts, including electronic waste and energy consumption during manufacturing. B2B buyers should consider suppliers that demonstrate a commitment to sustainability through eco-friendly practices, such as using recyclable materials and reducing carbon footprints in their manufacturing processes.
Moreover, ethical sourcing is critical in ensuring that materials are obtained from suppliers who adhere to fair labor practices and environmental regulations. Certifications such as ISO 14001 for environmental management and the Responsible Business Alliance (RBA) Code of Conduct can provide assurance to buyers about the sustainability and ethical standards of their suppliers. Implementing these practices not only aligns with corporate social responsibility goals but can also enhance brand reputation and customer loyalty, particularly in markets that value sustainability.
What Is the Evolution of Plugging Technology in the Electrical Sector?
The evolution of plugging technology in the electrical sector can be traced back to the early 20th century when electric motors became widespread in industrial applications. Initially, the focus was on simple methods of controlling motor speed and direction. However, as technology advanced, more sophisticated techniques emerged, including dynamic braking and regenerative braking, alongside plugging.
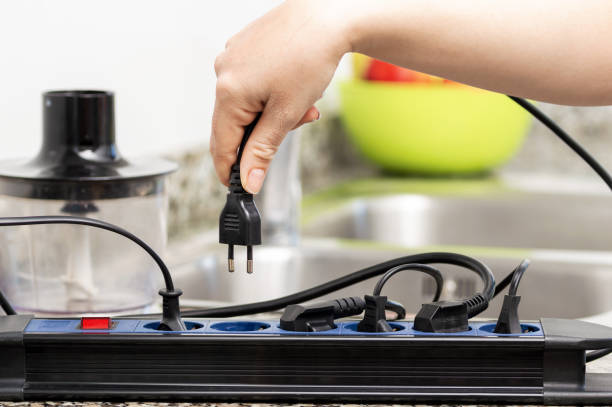
A stock image related to plugging electrical.
Plugging, or reverse current braking, gained popularity due to its ability to provide rapid stopping capabilities, essential for applications like elevators and cranes. Over the decades, the technology has evolved to incorporate electronic controls and automation, enhancing its efficiency and reliability. This evolution reflects a broader trend in industrial automation, where the integration of advanced technologies continues to shape the landscape of motor control solutions, making it vital for B2B buyers to stay abreast of these developments to leverage the best solutions for their operational needs.
Frequently Asked Questions (FAQs) for B2B Buyers of plugging electrical
-
How do I solve the problem of selecting the right plugging electrical system for my application?
To select the right plugging electrical system, begin by evaluating your specific application requirements. Consider factors such as the type of motor (DC or AC), the load it will drive, the frequency of stopping and starting, and the necessary stopping time. It’s also crucial to assess the environment in which the motor operates, including temperature and humidity. Collaborate with suppliers to understand their product offerings and seek expert advice to ensure that the selected system meets your operational needs while minimizing wear and tear on your equipment. -
What is the best electrical plugging solution for heavy machinery operations?
For heavy machinery operations, dynamic braking or regenerative braking might be more suitable due to their lower mechanical stress compared to plugging. However, if rapid stopping is essential, select a robust plugging system specifically designed for high-inertia loads. Ensure that the system incorporates features like heavy-duty motor starters and thermal overload protection to handle the increased demands. Consult with manufacturers experienced in your industry to identify solutions that balance performance with reliability. -
How can I ensure the quality of plugging electrical systems when sourcing from international suppliers?
To ensure quality, conduct thorough supplier vetting before making a purchase. Check for certifications (like ISO 9001) that indicate compliance with quality management standards. Request product samples and conduct performance tests to evaluate reliability. Additionally, consider visiting the supplier’s facility if possible or utilizing third-party inspection services to verify quality. Establish clear quality assurance protocols and warranty terms in your contracts to protect your interests. -
What are the typical minimum order quantities (MOQs) for plugging electrical components?
Minimum order quantities for plugging electrical components can vary significantly based on the supplier and the specific components required. Typically, MOQs can range from a few units to several hundred. Discuss your needs directly with suppliers, as many are willing to negotiate MOQs, especially for first-time buyers or for bulk orders. Understanding the MOQ will help you plan your inventory and budget accordingly. -
What payment terms should I negotiate when purchasing plugging electrical systems from international suppliers?
Payment terms can greatly affect your cash flow and overall project budget. Common terms include a deposit upon order confirmation (often 30-50%) and the balance upon delivery or before shipment. Depending on your relationship with the supplier, you may negotiate more favorable terms, such as extended payment periods or letter of credit arrangements. Always ensure that payment terms are clearly outlined in the contract to avoid misunderstandings. -
How can logistics impact the sourcing of plugging electrical systems from different regions?
Logistics plays a critical role in sourcing plugging electrical systems, especially when dealing with international suppliers. Factors such as shipping times, customs clearance, and local regulations can affect delivery schedules and costs. Research potential shipping routes and consider using freight forwarders experienced in handling electrical components to streamline the process. Additionally, factor in lead times for production and delivery when planning your procurement timeline.
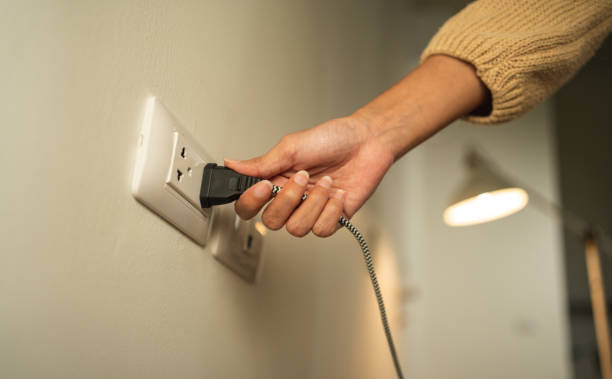
A stock image related to plugging electrical.
-
What customization options are available for plugging electrical systems to fit specific operational needs?
Many manufacturers offer customization options for plugging electrical systems, allowing you to tailor components to your specific operational requirements. Customizations may include adjustments to voltage ratings, torque specifications, and control interfaces. Discuss your unique needs with suppliers to explore available options. Custom solutions can enhance performance and efficiency, but be aware that they may also impact lead times and costs. -
What are the best practices for maintaining plugging electrical systems to ensure longevity?
To ensure the longevity of plugging electrical systems, implement a regular maintenance schedule that includes inspections, cleaning, and testing of all components. Monitor operating conditions to prevent overheating and excessive wear. Ensure that all connections are secure and that any dust or debris is cleared from the system. Training your operational staff on proper usage and maintenance procedures can also significantly reduce the risk of damage and prolong the system’s operational life.
Important Disclaimer & Terms of Use
⚠️ Important Disclaimer
The information provided in this guide, including content regarding manufacturers, technical specifications, and market analysis, is for informational and educational purposes only. It does not constitute professional procurement advice, financial advice, or legal advice.
While we have made every effort to ensure the accuracy and timeliness of the information, we are not responsible for any errors, omissions, or outdated information. Market conditions, company details, and technical standards are subject to change.
B2B buyers must conduct their own independent and thorough due diligence before making any purchasing decisions. This includes contacting suppliers directly, verifying certifications, requesting samples, and seeking professional consultation. The risk of relying on any information in this guide is borne solely by the reader.
Strategic Sourcing Conclusion and Outlook for plugging electrical
What Are the Key Takeaways for B2B Buyers in Plugging Electrical?
In the realm of plugging electrical applications, understanding the nuances of braking methods such as plugging is crucial for optimizing motor performance and longevity. While plugging offers rapid stopping capabilities, it can impose significant mechanical stress and generate excess heat, which may lead to equipment failure if not managed properly. B2B buyers should prioritize sourcing components that are robust enough to withstand the rigors of plugging, particularly when dealing with high-inertia loads.
How Can Strategic Sourcing Enhance Your Operations?
Effective strategic sourcing is vital in ensuring that your operations remain efficient and cost-effective. By engaging with reputable suppliers who specialize in high-quality electrical components, you can mitigate risks associated with plugging applications. Additionally, consider investing in advanced motor control solutions that incorporate anti-plugging features to enhance operational reliability.
What’s Next for International B2B Buyers?
As the global market evolves, particularly in regions like Africa, South America, the Middle East, and Europe, staying ahead of technological advancements will be key. Embrace innovative solutions that improve energy efficiency and reduce downtime. Take action now by evaluating your current supplier relationships and exploring new partnerships that align with your strategic goals. This proactive approach will not only enhance your operational capabilities but also position your business for long-term success in the competitive landscape of plugging electrical applications.