Maximize Efficiency: The Complete Robotic Palletizing Guide (2025)
Introduction: Navigating the Global Market for robotic palletizing
In today’s fast-paced global market, sourcing effective robotic palletizing solutions can be a daunting challenge for B2B buyers, especially those in regions like Africa, South America, the Middle East, and Europe. As businesses seek to enhance operational efficiency and reduce labor costs, the need for advanced automation technologies has never been more critical. This guide serves as a comprehensive resource for international buyers, delving into various types of robotic palletizers, their applications across different industries, and practical insights for supplier vetting and cost considerations.
With a focus on empowering decision-makers, this guide outlines the key factors to consider when investing in robotic palletizing systems. From understanding the differences between standard and custom solutions to evaluating the return on investment (ROI) based on throughput rates and maintenance needs, our insights are designed to help you make informed purchasing decisions. We will explore the latest technologies, including collaborative robots and high-speed systems, as well as the importance of ongoing support and training for seamless integration into existing operations.
By addressing the unique challenges faced by businesses in diverse markets, this guide equips B2B buyers with the knowledge and tools needed to navigate the global landscape of robotic palletizing. Whether you’re looking to streamline your packaging line or enhance workplace safety, the insights provided here will help you identify the best solutions tailored to your specific needs.
Understanding robotic palletizing Types and Variations
Type Name | Key Distinguishing Features | Primary B2B Applications | Brief Pros & Cons for Buyers |
---|---|---|---|
High-Performance Robotic Palletizer | Offers full automation, high throughput (20-80 units/min) | Large-scale manufacturing, food and beverage | Pros: High efficiency; Cons: Higher initial investment. |
Semi-Automatic Robotic Palletizer | Economical entry-level option; manual pallet placement | Small to medium-sized operations | Pros: Cost-effective; Cons: Limited automation. |
Custom Robotic Palletizing System | Tailored solutions for specific needs; flexible configurations | Diverse industries with unique needs | Pros: Versatile; Cons: Potentially longer lead times. |
Hybrid Robotic Palletizer | Combines speed of conventional systems with robotic flexibility | Food processing, consumer goods | Pros: High adaptability; Cons: Complexity in setup. |
Collaborative Robotic Palletizer | Safe, easy-to-integrate robots designed for human collaboration | Small businesses, flexible environments | Pros: User-friendly; Cons: Lower throughput compared to full automation. |
What Are the Characteristics of High-Performance Robotic Palletizers?
High-performance robotic palletizers are designed for maximum efficiency, capable of handling between 20 to 80 units per minute. They are fully automated systems that integrate advanced technology to streamline the palletizing process. These systems are ideal for large-scale manufacturing operations, particularly in industries like food and beverage, where speed and reliability are critical. When considering this option, B2B buyers should evaluate their production volume and the potential return on investment, as the initial cost is higher compared to other types.
How Do Semi-Automatic Robotic Palletizers Work?
Semi-automatic robotic palletizers represent a cost-effective solution for businesses looking to automate their palletizing processes without a significant financial outlay. These systems require manual pallet placement but automate the stacking process, making them suitable for small to medium-sized operations. Buyers should consider their budget constraints and the level of automation they seek, as this type of palletizer may not meet the needs of larger operations demanding higher throughput.
Why Choose a Custom Robotic Palletizing System?
Custom robotic palletizing systems are tailored to meet the unique requirements of various industries. These systems can handle atypical products or accommodate specific automation needs, making them versatile and adaptable. B2B buyers should assess their specific operational challenges and product types when considering this option, as the flexibility can lead to improved efficiency but may involve longer lead times and higher costs.
What Are the Benefits of Hybrid Robotic Palletizers?
Hybrid robotic palletizers combine the speed of traditional systems with the flexibility of robotic technology, making them suitable for industries like food processing and consumer goods. They can efficiently handle different product types, ensuring optimal pallet loads. Buyers should consider the complexity of setup and potential maintenance challenges, as these systems may require more sophisticated training and support.
How Do Collaborative Robotic Palletizers Enhance Operations?
Collaborative robotic palletizers are designed to work alongside human operators, making them an excellent choice for small businesses or environments requiring flexibility. These systems are user-friendly and can be integrated with existing workflows without extensive modifications. However, buyers should keep in mind that while they are easier to implement, these systems generally offer lower throughput compared to fully automated solutions, which may impact productivity in high-demand settings.
Key Industrial Applications of robotic palletizing
Industry/Sector | Specific Application of Robotic Palletizing | Value/Benefit for the Business | Key Sourcing Considerations for this Application |
---|---|---|---|
Food and Beverage | Palletizing bags of flour, sugar, or beverage cases | Increases throughput and consistency, reduces labor costs | Ensure compliance with food safety standards; consider flexibility for different bag sizes and weights. |
Consumer Goods | Automated palletizing of retail product cases | Enhances efficiency in high-volume environments, reduces manual handling injuries | Look for solutions that can handle various SKUs and integrate with existing packaging lines. |
Pharmaceuticals | Palletizing cartons of medications or medical supplies | Improves accuracy and traceability, minimizes contamination risks | Focus on systems that offer robust safety features and can handle sensitive materials. |
Building Materials | Palletizing bags of cement, tiles, or lumber | Reduces manual labor, improves safety, and increases storage efficiency | Consider equipment that can adapt to heavy and bulky items while ensuring stability during stacking. |
E-commerce and Logistics | Palletizing mixed SKU pallets for order fulfillment | Streamlines operations, enhances order accuracy, and speeds up delivery times | Seek flexible solutions that can adapt to varying order sizes and integrate with automated picking systems. |
How is Robotic Palletizing Applied in the Food and Beverage Sector?
In the food and beverage industry, robotic palletizing is commonly used for stacking bags of flour, sugar, or cases of beverages onto pallets. This application addresses the challenges of high-volume production while ensuring consistent stacking patterns and reducing the risk of injuries associated with manual handling. International buyers should prioritize systems that comply with food safety regulations and can accommodate various bag sizes and weights to maintain operational flexibility.
What are the Benefits of Robotic Palletizing for Consumer Goods?
Robotic palletizing in consumer goods focuses on automating the stacking of retail product cases, which enhances efficiency in high-demand environments. This automation minimizes manual labor, reducing the risk of workplace injuries and improving overall safety. Buyers from diverse regions should consider solutions that can easily handle multiple SKUs and seamlessly integrate into existing packaging lines to maximize productivity.
How Does Robotic Palletizing Improve Pharmaceutical Operations?
In the pharmaceutical sector, robotic palletizing is vital for stacking cartons of medications and medical supplies. This application significantly improves accuracy and traceability while minimizing contamination risks during the palletizing process. For international buyers, it is essential to focus on systems that feature advanced safety mechanisms and can handle sensitive products, ensuring compliance with strict industry regulations.
What Role Does Robotic Palletizing Play in Building Materials?
Robotic palletizing is increasingly utilized in the building materials sector for stacking heavy items such as bags of cement, tiles, or lumber. This application helps reduce manual labor and enhances worker safety while optimizing storage efficiency. Buyers should look for equipment capable of adapting to the weight and bulkiness of these materials while ensuring stability during the stacking process.
How is Robotic Palletizing Transforming E-commerce and Logistics?
In e-commerce and logistics, robotic palletizing is essential for creating mixed SKU pallets for order fulfillment. This automation streamlines operations, enhances order accuracy, and accelerates delivery times, which are critical in today’s fast-paced market. Buyers should seek flexible robotic solutions that can adapt to varying order sizes and integrate smoothly with automated picking systems to maintain a competitive edge.
3 Common User Pain Points for ‘robotic palletizing’ & Their Solutions
Scenario 1: Struggling with High Labor Costs in Manual Palletizing
The Problem: Many businesses, particularly in developing regions like Africa and South America, rely heavily on manual palletizing due to budget constraints or lack of understanding of automation technologies. This can lead to skyrocketing labor costs, employee fatigue, and potential safety hazards. Moreover, as demand grows, the inability to scale operations quickly becomes a significant challenge, hindering competitiveness and profitability.
The Solution: To address this issue, businesses should consider investing in entry-level robotic palletizers, such as the RPL-1000 Series. These systems are designed to be economical and straightforward, allowing for manual pallet placement while automating the stacking process. By conducting a thorough cost-benefit analysis, businesses can determine the return on investment (ROI) of transitioning from manual to robotic solutions. Additionally, engaging with suppliers who provide training and ongoing support can ease the transition and ensure that staff are comfortable operating the new technology. This combination of a manageable initial investment and the potential for significant labor savings can lead to improved productivity and reduced operational costs.
Scenario 2: Difficulty Managing Diverse Product SKUs
The Problem: Companies that handle a wide variety of products, such as those in the food and beverage or consumer goods sectors, often face challenges with managing multiple SKUs during the palletizing process. This complexity can lead to increased errors, slower operations, and difficulties in maintaining consistent quality standards. Buyers in markets like the Middle East and Europe may find that their current systems are not adaptable enough to handle diverse products efficiently.
The Solution: To mitigate this issue, businesses should look for robotic palletizing systems that offer flexibility in handling multiple SKUs. The RPM Series, for instance, is specifically designed for mixed case palletizing, allowing for the assembly of pallets from various sizes and weights automatically. Buyers should prioritize suppliers who provide customizable solutions and can simulate the palletizing process using their specific products. This ensures that the robotic system is tailored to meet their unique needs. Additionally, investing in a 3D vision system can enhance the robot’s ability to identify and manipulate different products accurately, leading to improved efficiency and reduced error rates.
Scenario 3: Concerns Over Safety and Equipment Reliability
The Problem: Safety concerns are paramount in any manufacturing environment, and robotic palletizing systems are no exception. Businesses in Europe and the Middle East may be particularly sensitive to compliance with safety regulations and ensuring employee well-being. Concerns about equipment reliability, maintenance costs, and the potential for downtime can deter companies from adopting robotic solutions.
The Solution: It’s essential for buyers to choose robotic palletizing systems that are designed with safety and reliability in mind. Models that come equipped with safety features, such as light curtains, emergency-stop buttons, and collision guard software, significantly reduce the risk of accidents. Buyers should also inquire about the maintenance requirements of potential systems; for instance, many modern robotic palletizers, like those from reputable manufacturers such as FANUC, are designed for low maintenance and high reliability. Establishing a partnership with suppliers who offer comprehensive lifecycle management and 24/7 technical support can further alleviate concerns about equipment downtime. By investing in robust, safe technology and ensuring that proper training is provided to operators, businesses can create a safer work environment while maximizing productivity.
Strategic Material Selection Guide for robotic palletizing
When selecting materials for robotic palletizing systems, international B2B buyers must consider various factors that influence performance, durability, and cost. Below, we analyze four common materials used in robotic palletizing applications, focusing on their properties, pros and cons, and specific considerations for buyers from regions such as Africa, South America, the Middle East, and Europe.
What Are the Key Properties of Steel in Robotic Palletizing?
Steel is a widely used material in robotic palletizing systems due to its strength and durability. It boasts high tensile strength, making it suitable for heavy loads and high-pressure environments. Steel also has excellent wear resistance, which is critical in high-throughput applications.
Pros: The primary advantage of steel is its durability and ability to withstand harsh conditions, including temperature fluctuations and mechanical stress. It is also relatively low-cost compared to other materials, making it an economical choice for many businesses.
Cons: However, steel is prone to corrosion if not properly treated, which can lead to maintenance challenges. Additionally, its weight can be a drawback in applications where mobility is essential.
Impact on Application: Steel is particularly effective in environments where heavy loads are common, such as in food and beverage, automotive, and chemical industries.
Considerations for Buyers: Buyers should ensure compliance with international standards such as ASTM for steel grades. Corrosion-resistant coatings may be necessary in humid regions, particularly in parts of Africa and South America.
How Does Aluminum Compare for Robotic Palletizing Solutions?
Aluminum is another popular choice, known for its lightweight and corrosion-resistant properties. It is easier to manipulate than steel, which can enhance the flexibility of robotic systems.
Pros: The lightweight nature of aluminum allows for faster operation and less energy consumption. Its resistance to corrosion makes it ideal for industries that require cleanliness, such as pharmaceuticals and food processing.
Cons: On the downside, aluminum is generally more expensive than steel and may not be suitable for very heavy loads due to its lower tensile strength.
Impact on Application: Aluminum is best suited for applications where weight savings are crucial, such as in high-speed packaging lines.
Considerations for Buyers: Buyers in Europe and the Middle East may prefer aluminum due to its aesthetic appeal and lightweight benefits. Compliance with JIS standards is essential for ensuring quality.
What Role Does Plastic Play in Robotic Palletizing?
Plastic, particularly high-density polyethylene (HDPE) and polypropylene, is increasingly used in robotic palletizing systems, especially for lightweight products.
Pros: Plastics are resistant to chemicals and moisture, making them suitable for various applications. They are also lightweight, which can enhance system speed and efficiency.
Cons: The main drawback is that plastics can be less durable than metals, especially under high temperatures or heavy loads. They may also be subject to wear and tear over time.
Impact on Application: Plastic materials are ideal for industries that handle lightweight goods, such as consumer products and electronics.
Considerations for Buyers: Buyers should check for compliance with local regulations regarding plastic materials, especially in regions with stringent environmental laws.
Why Is Composite Material Gaining Popularity in Robotic Palletizing?
Composite materials, which combine plastic with other materials like glass or carbon fibers, are gaining traction in robotic palletizing due to their unique properties.
Pros: Composites are lightweight yet strong, offering a good balance between durability and weight. They are also resistant to corrosion and can be tailored for specific applications.
Cons: The primary limitation is the higher cost associated with composite materials. Additionally, manufacturing complexity can lead to longer lead times.
Impact on Application: Composites are suitable for specialized applications where weight and strength are critical, such as in aerospace or advanced manufacturing sectors.
Considerations for Buyers: Buyers should evaluate the cost-benefit ratio of composites versus traditional materials. Compliance with industry standards is crucial for ensuring performance.
Summary Table of Material Selection for Robotic Palletizing
Material | Typical Use Case for Robotic Palletizing | Key Advantage | Key Disadvantage/Limitation | Relative Cost (Low/Med/High) |
---|---|---|---|---|
Steel | Heavy-duty applications in food and beverage | High durability and strength | Prone to corrosion | Medium |
Aluminum | High-speed packaging lines for lightweight goods | Lightweight and corrosion-resistant | Higher cost and lower strength | High |
Plastic | Consumer products and electronics | Resistant to moisture and chemicals | Less durable under heavy loads | Low |
Composite | Specialized applications in aerospace | Lightweight with high strength | Higher cost and manufacturing complexity | High |
This comprehensive analysis provides B2B buyers with actionable insights into material selection for robotic palletizing systems, ensuring informed decisions tailored to their specific operational needs and regional considerations.
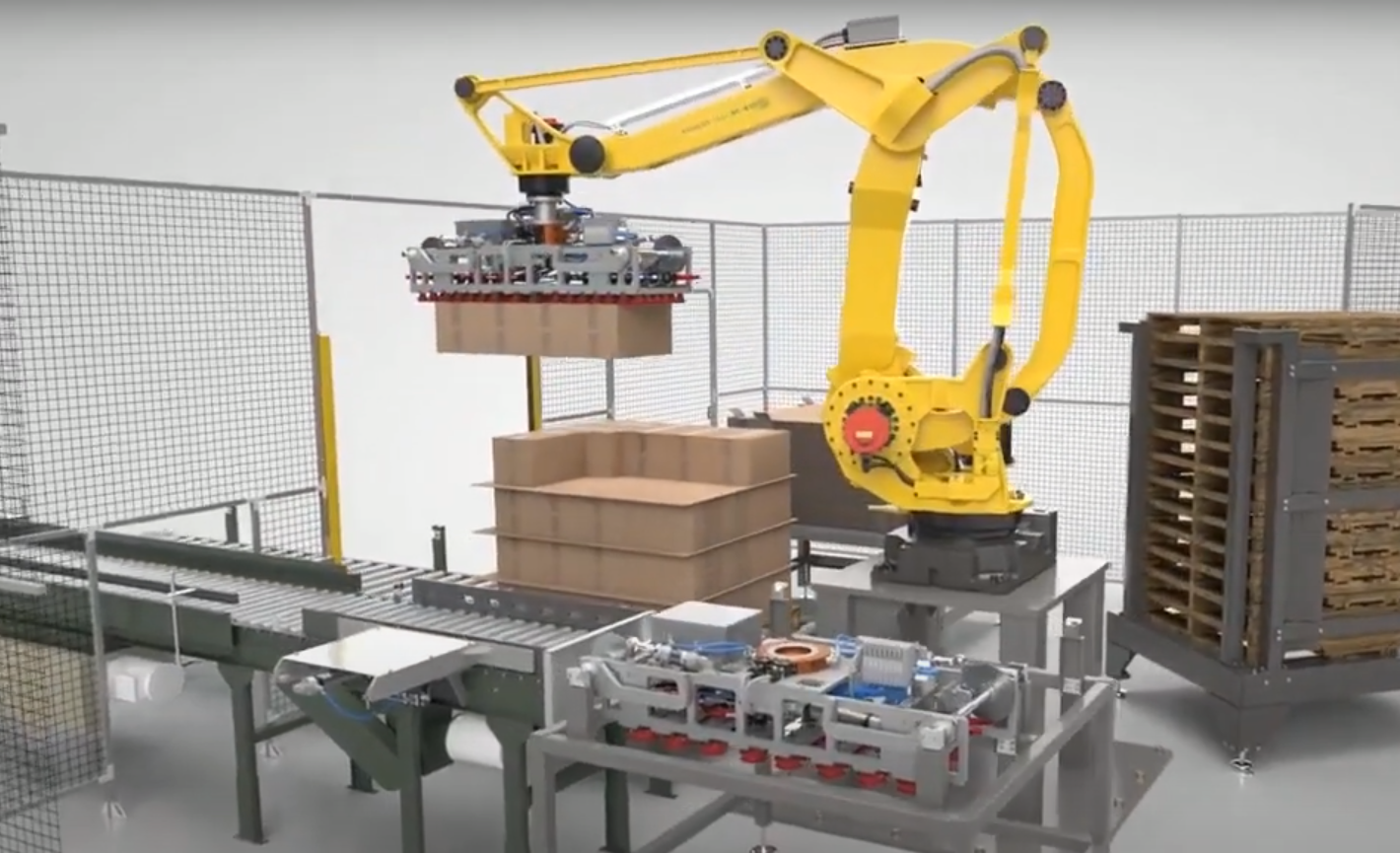
A stock image related to robotic palletizing.
In-depth Look: Manufacturing Processes and Quality Assurance for robotic palletizing
What Are the Key Stages in the Manufacturing Process for Robotic Palletizing?
The manufacturing process for robotic palletizing systems involves several critical stages that ensure the final product meets high-quality standards and operational efficiency. Understanding these stages is essential for B2B buyers looking to invest in robotic solutions.
1. Material Preparation: What Goes into Building a Robotic Palletizer?
Material preparation is the first step in the manufacturing process. This involves selecting high-quality components that can withstand the rigors of continuous operation. Common materials used include steel for structural components, durable plastics for end-effectors, and advanced sensors for operational precision. Suppliers often source these materials from certified vendors to ensure compliance with international standards.
2. Forming: How Are Components Shaped and Crafted?
The forming stage includes processes like cutting, bending, and machining. Advanced technologies such as CNC (Computer Numerical Control) machining are frequently employed to achieve precise dimensions and tolerances. This stage is critical for creating components like the robotic arm, base, and other structural elements that must fit together seamlessly.
3. Assembly: How Are Robotic Palletizers Built?
Assembly is where the various components come together. This process typically involves both manual and automated methods. Skilled technicians often perform the initial assembly, while robotic systems may be employed for repetitive tasks. The assembly line is designed to facilitate efficient workflow and minimize downtime, ensuring that each robotic palletizer is built to specifications.
4. Finishing: What Quality Controls Are in Place?
In the finishing stage, the robotic palletizers undergo surface treatment and painting to enhance durability and aesthetics. This stage also includes quality checks to ensure that all components are functioning correctly. Manufacturers may use automated testing systems to simulate operational scenarios, verifying that the palletizer can handle the expected load and speed.
What Quality Assurance Standards Should B2B Buyers Look For?
Quality assurance (QA) is paramount in the manufacturing of robotic palletizers. Buyers should be familiar with both international and industry-specific standards to ensure they are sourcing reliable equipment.
Which International Standards Are Relevant for Robotic Palletizing?
ISO 9001 is a widely recognized international standard that outlines the requirements for a quality management system (QMS). Manufacturers that adhere to ISO 9001 demonstrate their commitment to consistent quality and customer satisfaction. Other relevant standards include CE marking for products sold in Europe, which indicates compliance with health, safety, and environmental protection standards.
What Are the Key Quality Control Checkpoints in the Manufacturing Process?
Quality control (QC) checkpoints are critical to maintaining product integrity. Common checkpoints include:
-
Incoming Quality Control (IQC): This stage involves inspecting raw materials and components as they arrive at the manufacturing facility. Suppliers should provide certificates of compliance to validate material quality.
-
In-Process Quality Control (IPQC): This involves monitoring the manufacturing processes. Regular inspections and testing during assembly help identify issues early, reducing rework and waste.
-
Final Quality Control (FQC): Before shipment, each robotic palletizer undergoes thorough testing to ensure it meets design specifications. This may include functional tests, load tests, and safety checks.
How Can B2B Buyers Verify Supplier Quality Control Practices?
Verifying a supplier’s quality control practices is crucial for B2B buyers, especially when dealing with international suppliers. Here are several methods:
What Audits and Reports Should Buyers Request?
Buyers should request access to quality management system documentation, including internal audit reports, corrective action reports, and process validation records. Conducting on-site audits can provide deeper insights into the supplier’s QA processes and overall operational environment.
How Can Third-Party Inspections Enhance Quality Assurance?
Engaging third-party inspection services can offer an unbiased assessment of the supplier’s capabilities. These inspections can occur at various stages of the manufacturing process and can help verify compliance with industry standards. Buyers should consider using accredited inspectors familiar with robotic systems.
What Are the Unique Quality Control Considerations for International B2B Buyers?
For buyers from Africa, South America, the Middle East, and Europe, unique challenges may arise when sourcing robotic palletizers.
How Do Regional Standards Impact Quality Assurance?
Different regions may have specific compliance requirements that manufacturers must meet. For instance, while CE marking is essential for products sold in Europe, buyers in Africa and South America may need to consider local certifications that ensure safety and performance standards are met.
What Cultural and Logistical Factors Should Buyers Consider?
Cultural differences can impact communication and expectations regarding quality assurance. Buyers should establish clear quality metrics and expectations at the outset of the supplier relationship. Additionally, logistical considerations, such as transportation and import regulations, can affect delivery timelines and product condition upon arrival.
Conclusion: Ensuring Quality in Robotic Palletizing Systems
Investing in robotic palletizing systems requires a thorough understanding of both the manufacturing processes and quality assurance practices. By familiarizing themselves with these aspects, B2B buyers can make informed decisions, ensuring that their investment leads to improved efficiency, safety, and productivity in their operations. Engaging with suppliers who demonstrate robust QA practices and compliance with international standards will ultimately contribute to long-term success in their automation journey.
Practical Sourcing Guide: A Step-by-Step Checklist for ‘robotic palletizing’
To assist international B2B buyers in navigating the procurement of robotic palletizing systems, this guide outlines essential steps to ensure a successful sourcing process. Robotic palletizers can significantly enhance operational efficiency and safety, making informed purchasing decisions critical.
Step 1: Define Your Technical Specifications
Understanding your operational needs is paramount. Consider factors like the types of products being palletized (e.g., bags, cases, or bundles), desired throughput rates, and space constraints in your facility. This clarity will help you communicate effectively with potential suppliers and ensure the equipment matches your specific requirements.
Step 2: Assess Your Budget and Financing Options
Establish a clear budget that encompasses not only the initial purchase price but also installation, training, and ongoing maintenance costs. Look for suppliers offering flexible financing options, such as leasing programs, which can make high-quality systems more accessible without a hefty upfront investment.
- Consider Total Cost of Ownership: Evaluate long-term savings from reduced labor costs and increased efficiency against initial costs.
- Explore Financing Solutions: Options like SmartLease can help manage cash flow while acquiring advanced technology.
Step 3: Evaluate Potential Suppliers
Before making a commitment, vet suppliers thoroughly. Request company profiles, case studies, and references from businesses in similar industries or regions. This step helps you understand their track record and reliability.
- Check Industry Experience: Look for suppliers with a proven history in your industry to ensure they understand your unique challenges.
- Review Customer Testimonials: Positive feedback can give insights into the supplier’s customer service and support capabilities.
Step 4: Request Customization Capabilities
Not all operations are the same, and a one-size-fits-all solution may not suffice. Inquire about the supplier’s ability to customize their robotic palletizing solutions to fit your specific production line and product handling needs.
- Discuss Flexibility: Ensure that the system can adapt to different product types and sizes, as well as changes in production volume.
- Explore Modular Designs: A modular system can allow for future upgrades and expansions as your business grows.
Step 5: Examine Safety Features and Compliance
Safety should be a top priority when selecting robotic equipment. Verify that the robotic palletizers meet international safety standards and include features like emergency stop buttons, safety fences, and collision detection systems.
- Request Safety Certifications: Ensure compliance with relevant regulations in your region (e.g., CE marking in Europe).
- Review Maintenance Requirements: Low-maintenance systems can reduce downtime and operational costs.
Step 6: Understand Support and Training Services
Post-purchase support is crucial for maximizing your investment. Evaluate the supplier’s customer service, availability of technical support, and training programs for your operators.
- Check Support Availability: Ensure 24/7 support is available for troubleshooting and maintenance.
- Inquire About Training: Comprehensive training for your team can lead to smoother implementation and operation.
Step 7: Compare Warranty and Service Agreements
Lastly, analyze the warranty and service agreements offered by different suppliers. A robust warranty can provide peace of mind and protect your investment against unforeseen issues.
- Look for Comprehensive Coverage: A longer warranty period often indicates supplier confidence in their product.
- Evaluate Service Level Agreements (SLAs): Ensure that SLAs outline response times and service commitments that align with your operational needs.
By following these steps, B2B buyers can make informed decisions that not only improve their operational efficiency but also enhance overall productivity in their facilities.
Comprehensive Cost and Pricing Analysis for robotic palletizing Sourcing
What are the Key Cost Components in Robotic Palletizing?
When considering the sourcing of robotic palletizing solutions, it’s crucial to understand the cost structure involved. The primary components include:
-
Materials: The choice of materials for robotic arms and components significantly affects pricing. High-quality materials, such as aluminum and advanced polymers, enhance durability but may increase upfront costs.
-
Labor: While robotic systems reduce the need for manual labor, skilled labor is required for programming and maintenance. Training costs for operators should also be factored in.
-
Manufacturing Overhead: This includes expenses related to production facilities, utilities, and equipment maintenance. Efficient manufacturing processes can help keep these costs down.
-
Tooling: Custom tooling for specific applications can add to the initial investment. Standardized tools may reduce costs but can limit flexibility.
-
Quality Control (QC): Rigorous QC processes ensure reliability and safety, particularly important in industries with stringent regulations. This may involve additional labor and testing materials.
-
Logistics: Transportation costs can vary widely depending on the supplier’s location and the shipping terms agreed upon. Import duties and tariffs may also apply, especially for international buyers.
-
Margin: Supplier profit margins can fluctuate based on demand, competition, and market conditions. Understanding the supplier’s pricing strategy is essential for negotiation.
How Do Price Influencers Impact Robotic Palletizing Costs?
Several factors can influence the pricing of robotic palletizing systems:
-
Volume/MOQ (Minimum Order Quantity): Higher order volumes often lead to lower per-unit costs due to economies of scale. Negotiating for bulk purchases can yield significant savings.
-
Specifications and Customization: Custom-designed solutions tailored to specific operational needs typically carry a higher price tag. Standard models are generally more cost-effective.
-
Materials and Quality Certifications: Premium materials and certifications (e.g., ISO, CE) ensure compliance with safety and quality standards, which can increase costs but also provide value in the long run.
-
Supplier Factors: The reputation, reliability, and location of the supplier can significantly affect pricing. Established suppliers may charge more but often provide better support and warranty services.
-
Incoterms: Understanding shipping terms (e.g., FOB, CIF) is crucial for managing total landed costs. Buyers must consider who bears the risk and cost during transit.
What Buyer Tips Can Optimize Cost-Efficiency in Robotic Palletizing?
International B2B buyers can adopt several strategies to enhance cost-efficiency when sourcing robotic palletizing systems:
-
Negotiate Wisely: Leverage volume commitments to negotiate better terms. Suppliers may be open to discounts for larger orders or longer-term contracts.
-
Consider Total Cost of Ownership (TCO): Evaluate not just the initial purchase price but also ongoing operational costs, including maintenance, energy consumption, and potential downtime. A higher upfront investment in reliable equipment can result in lower TCO over time.
-
Research Local and Regional Suppliers: Engage with suppliers who understand local market conditions and can provide tailored solutions. This can reduce shipping costs and lead to faster support.
-
Understand Pricing Nuances for International Transactions: Be aware of currency fluctuations, import duties, and other potential hidden costs that may arise when sourcing from different regions, particularly from Africa, South America, the Middle East, and Europe.
-
Request Multiple Quotes: Engage with several suppliers to compare not only prices but also value-added services such as installation, training, and after-sales support.
Disclaimer on Indicative Prices
Prices for robotic palletizing systems can vary widely based on the factors discussed above. While entry-level models may start around $100,000, customized solutions can exceed $175,000 or more, depending on specifications and configurations. Therefore, it is advisable to consult directly with suppliers for the most accurate and up-to-date pricing based on specific requirements.
Alternatives Analysis: Comparing robotic palletizing With Other Solutions
Introduction to Alternatives in Palletizing Solutions
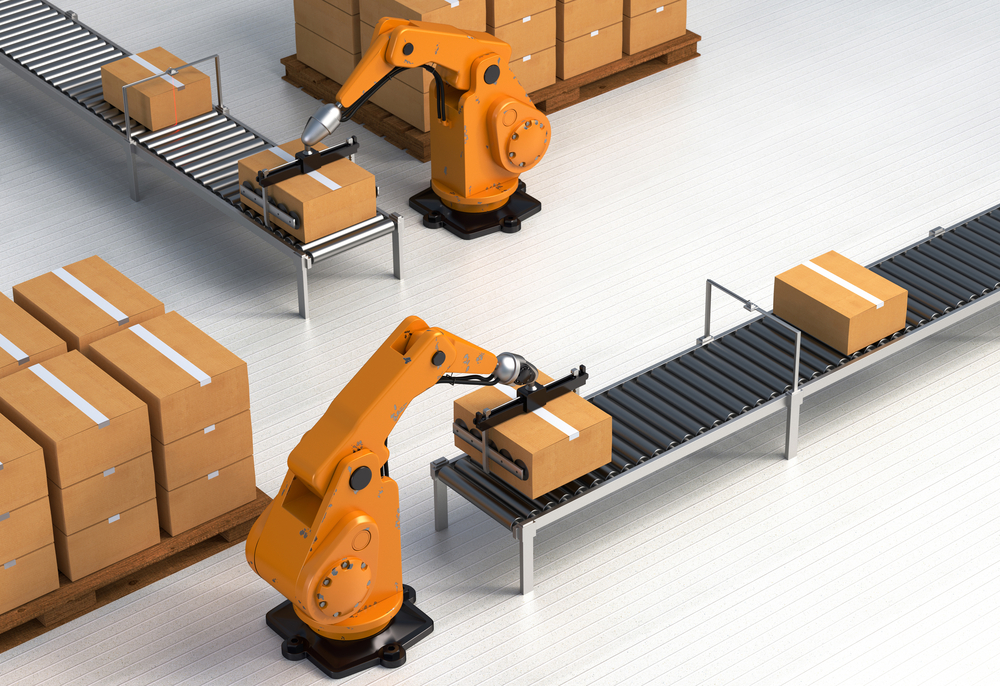
A stock image related to robotic palletizing.
In the quest for efficiency and productivity, businesses in Africa, South America, the Middle East, and Europe are increasingly exploring various palletizing solutions. Robotic palletizing has gained significant traction due to its automation capabilities, but it’s essential to consider alternative solutions that may better fit specific operational needs or budget constraints. This section provides a comparative analysis of robotic palletizing against two viable alternatives: manual palletizing and semi-automatic palletizing systems.
Comparison Table of Palletizing Solutions
Comparison Aspect | Robotic Palletizing | Manual Palletizing | Semi-Automatic Palletizing |
---|---|---|---|
Performance | High throughput (20-80 units/minute) | Low throughput; highly variable | Moderate throughput (up to 40 units/minute) |
Cost | $100,000 – $500,000+ | Low initial cost, but high labor costs | Moderate initial cost ($30,000 – $100,000) |
Ease of Implementation | Requires integration and training | Quick to implement but labor-intensive | Easier to set up than robotic systems |
Maintenance | Low maintenance; fewer moving parts | High maintenance due to labor turnover | Moderate maintenance; depends on automation level |
Best Use Case | High-volume, repetitive tasks | Low volume, flexible production needs | Moderate volume with some automation |
Pros and Cons of Manual Palletizing
Manual palletizing involves human labor to stack products onto pallets.
Pros:
– Cost-Effective: The initial investment is low, making it accessible for small businesses.
– Flexibility: Easily adaptable to different products and configurations without needing specialized equipment.
Cons:
– Labor-Intensive: Requires significant manpower, which can lead to higher ongoing costs and challenges with labor availability, especially in regions with workforce shortages.
– Variable Performance: Productivity can fluctuate based on the skill and speed of workers, leading to inefficiencies.
Pros and Cons of Semi-Automatic Palletizing Systems
Semi-automatic palletizing systems bridge the gap between manual and fully automated solutions.
Pros:
– Moderate Automation: Reduces the manual effort needed for palletizing while still allowing for some human oversight.
– Lower Initial Investment: More affordable than robotic systems, making it suitable for mid-sized operations looking to enhance efficiency.
Cons:
– Limited Throughput: Generally, these systems do not match the speed and efficiency of fully automated robotic solutions, which could be a drawback for high-volume operations.
– Training Required: Workers still need training to operate and maintain semi-automatic systems, adding to the implementation time.
Conclusion: Choosing the Right Palletizing Solution for Your Business
When selecting a palletizing solution, B2B buyers must consider their unique operational requirements, including budget constraints, throughput needs, and workforce capabilities. Robotic palletizing offers high efficiency and low maintenance, making it ideal for high-volume operations, while manual palletizing provides flexibility at a lower upfront cost. Semi-automatic systems serve as a middle ground, offering improved efficiency without the full investment of automation. Ultimately, the right choice will depend on the specific needs and goals of your business, ensuring that you achieve optimal productivity and cost-effectiveness.
Essential Technical Properties and Trade Terminology for robotic palletizing
What Are the Key Technical Properties of Robotic Palletizing Systems?
Understanding the essential technical properties of robotic palletizing systems is crucial for B2B buyers looking to optimize their packaging lines. Here are some critical specifications to consider:
-
Payload Capacity
– Definition: This refers to the maximum weight that the robotic palletizer can handle, typically measured in kilograms or pounds.
– B2B Importance: Knowing the payload capacity is vital for ensuring that the robotic system can manage your specific product types, whether bags, cases, or bundles, without compromising performance. -
Speed and Throughput
– Definition: This metric indicates how many units the robotic palletizer can process per minute (units/min).
– B2B Importance: Speed affects overall productivity. A higher throughput means faster order fulfillment, which is essential in competitive markets. Buyers should match the robot’s speed with their operational needs to avoid bottlenecks. -
Precision and Tolerance
– Definition: Precision refers to the accuracy with which the robot can place items, often specified in millimeters or inches, while tolerance indicates the allowable deviation from a target position.
– B2B Importance: Precision ensures that products are stacked correctly, reducing the risk of load instability during transportation. This is particularly important for high-value or fragile items. -
Footprint and Layout Flexibility
– Definition: The footprint is the physical space the robotic system occupies, while layout flexibility refers to how easily the system can be integrated into existing workflows.
– B2B Importance: A compact design maximizes floor space, especially in facilities with limited room. Layout flexibility allows businesses to adapt as they scale operations or change product lines. -
Durability and Material Grade
– Definition: This refers to the quality of materials used in the construction of the robotic palletizer, impacting its lifespan and maintenance needs.
– B2B Importance: Investing in high-grade materials can reduce long-term operational costs and downtime, ensuring reliable performance even in demanding environments.
What Common Trade Terms Should B2B Buyers Know?
Familiarity with industry terminology can significantly enhance communication and negotiation processes. Here are some key terms associated with robotic palletizing:
-
OEM (Original Equipment Manufacturer)
– Definition: A company that produces parts or equipment that may be marketed by another manufacturer.
– Importance: Understanding OEM relationships helps buyers identify reliable suppliers and assess the quality of components in robotic systems. -
MOQ (Minimum Order Quantity)
– Definition: The smallest quantity of a product that a supplier is willing to sell.
– Importance: Knowing the MOQ can help in budgeting and inventory planning, especially for businesses looking to scale operations without excess stock. -
RFQ (Request for Quotation)
– Definition: A standard business process where buyers invite suppliers to submit price quotes for specific products or services.
– Importance: Submitting RFQs allows buyers to compare different suppliers’ offerings and negotiate better terms, ensuring cost-effectiveness in procurement. -
Incoterms (International Commercial Terms)
– Definition: A series of predefined commercial terms published by the International Chamber of Commerce (ICC) that clarify the responsibilities of buyers and sellers in international transactions.
– Importance: Familiarity with Incoterms helps in understanding shipping costs, insurance responsibilities, and risk management in cross-border purchases. -
Lead Time
– Definition: The time taken from placing an order to the delivery of the product.
– Importance: Knowing the lead time is essential for planning and meeting production schedules, particularly for companies that rely on just-in-time inventory systems.
By understanding these technical properties and trade terminology, international B2B buyers can make informed decisions, facilitating smoother transactions and enhancing operational efficiency in their robotic palletizing solutions.
Navigating Market Dynamics and Sourcing Trends in the robotic palletizing Sector
What Are the Key Market Trends Driving Robotic Palletizing?
The global robotic palletizing market is witnessing significant growth, driven by the increasing demand for automation across various industries. Factors such as labor shortages, the need for enhanced productivity, and the desire for improved workplace safety are propelling businesses toward adopting robotic palletizing solutions. In regions like Africa, South America, the Middle East, and Europe, manufacturers are increasingly looking for flexible, scalable solutions that can accommodate diverse product types and packaging formats.
Emerging technologies such as collaborative robots (cobots) and advanced AI-driven systems are reshaping the landscape, enabling companies to integrate robotic solutions seamlessly into existing workflows. The shift towards Industry 4.0 is another key trend, with smart, connected machines that facilitate data sharing and analytics, thereby enhancing operational efficiency. International B2B buyers should consider suppliers that offer customizable solutions tailored to specific operational needs, including the ability to handle multiple SKUs and varying speeds.
Moreover, the demand for quick-ship and cost-effective robotic systems is on the rise, allowing companies to implement automation without lengthy lead times or significant upfront investments. This trend is particularly relevant for buyers in emerging markets, where budget constraints often dictate purchasing decisions.
How Is Sustainability Influencing Robotic Palletizing Sourcing Decisions?
As global awareness of environmental issues rises, sustainability is becoming a crucial consideration for international B2B buyers in the robotic palletizing sector. Companies are increasingly prioritizing sustainable practices and ethical sourcing in their supply chains. This includes assessing the environmental impact of robotic systems, such as energy consumption and waste generation during manufacturing and operation.
The use of eco-friendly materials and ‘green’ certifications is gaining traction, as businesses look to align their operations with corporate social responsibility (CSR) objectives. Suppliers that offer energy-efficient robotic systems not only reduce operational costs but also contribute to lower carbon footprints, making them attractive to environmentally-conscious buyers.
Additionally, the importance of transparency in the supply chain cannot be overstated. Buyers are encouraged to partner with manufacturers that provide clear information about their sourcing practices and materials used in robotic systems. This approach not only enhances brand reputation but also meets the growing consumer demand for ethical products. As sustainability becomes a defining factor in purchasing decisions, companies should seek out suppliers that demonstrate a commitment to environmental stewardship and ethical sourcing.
How Has Robotic Palletizing Evolved Over the Years?
The evolution of robotic palletizing can be traced back to the early 1980s when the first industrial robots were introduced in manufacturing environments. Initially, these systems were primarily used for heavy lifting and repetitive tasks. However, as technology advanced, so did the capabilities of robotic palletizers.
The introduction of advanced sensors, AI, and machine learning has transformed robotic palletizers from simple machines into intelligent systems capable of adapting to various products and environments. Today, robotic palletizers can handle complex tasks such as mixed case palletizing and product tracking, significantly enhancing efficiency and reducing labor costs.
Moreover, the rise of collaborative robots has changed the dynamics, allowing for safer and more flexible interactions between human workers and robotic systems. This evolution has made robotic palletizing more accessible for businesses of all sizes, enabling them to improve productivity and streamline operations. As the technology continues to develop, international B2B buyers can expect even greater innovations that will further enhance the capabilities and applications of robotic palletizing solutions.
Frequently Asked Questions (FAQs) for B2B Buyers of robotic palletizing
-
How do I solve challenges in manual palletizing?
Manual palletizing can lead to inefficiencies and workplace injuries. To address these challenges, consider investing in robotic palletizing systems, which automate the stacking process, reduce labor costs, and enhance worker safety. Look for solutions that can accommodate various product types and sizes, and ensure they are easy to operate. Partnering with a reputable supplier who offers ongoing support and maintenance can further streamline this transition and ensure a quick return on investment. -
What is the best robotic palletizer for small to medium-sized businesses?
For small to medium-sized businesses, entry-level robotic palletizers like the RPL-1000 Series offer a cost-effective solution. These systems provide semi-automatic operations, allowing for manual pallet placement while still improving throughput. Ensure the chosen model can handle your specific product types and has the flexibility to scale as your business grows. Consulting with suppliers who can customize solutions based on your operational needs will also yield significant advantages. -
How can I ensure the quality of robotic palletizing equipment?
To ensure quality, source robotic palletizers from established manufacturers with a proven track record. Look for equipment that complies with international safety standards and has undergone rigorous testing, such as Factory Acceptance Tests (FAT). Request client testimonials and case studies to understand the supplier’s reliability and support service. Additionally, inquire about the availability of spare parts and maintenance packages to maintain optimal performance over time. -
What customization options are available for robotic palletizing systems?
Most suppliers offer a range of customization options to meet specific operational needs. These can include adjustments to speed, end-of-arm tooling for different product types, and integration with existing systems like conveyors and wrappers. Discuss your unique requirements with potential vendors to explore tailored solutions that maximize efficiency and accommodate your production layout. Customization can significantly enhance the performance and adaptability of your robotic palletizing solution. -
What are the minimum order quantities (MOQs) for robotic palletizers?
Minimum order quantities for robotic palletizers can vary significantly between suppliers. Some manufacturers may offer standard models with no MOQ, while custom solutions often require larger orders to justify the investment. It is advisable to discuss your project specifics with suppliers to determine their policies and explore options for smaller-scale purchases or leasing agreements, which can help mitigate upfront costs. -
What payment terms can I expect when purchasing robotic palletizers?
Payment terms vary by supplier and can be negotiated based on your company’s purchasing power and relationship with the vendor. Common terms include upfront payments, staggered payments during production, or financing options like leasing. Be sure to clarify any warranties, maintenance, and support packages included in the price, as these can significantly impact the total cost of ownership over time.
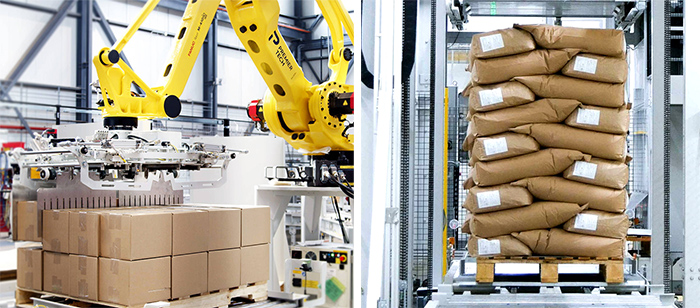
A stock image related to robotic palletizing.
-
How do I vet suppliers for robotic palletizing solutions?
When vetting suppliers, consider their industry experience, reputation, and customer service track record. Request references and case studies from businesses similar to yours to assess the supplier’s capabilities. Additionally, verify that the supplier adheres to international quality standards and has a robust support system for installation and ongoing maintenance. A thorough evaluation will help ensure that you partner with a reliable supplier who can meet your specific needs. -
What logistical considerations should I keep in mind when sourcing robotic palletizers internationally?
When sourcing robotic palletizers from international suppliers, consider shipping costs, import duties, and lead times. Ensure that the supplier provides detailed shipping and handling information, including the ability to track shipments. Additionally, confirm that the equipment complies with local regulations and standards in your country. Engaging a logistics partner familiar with international trade can help streamline the process and mitigate potential delays or issues during transportation.
Important Disclaimer & Terms of Use
⚠️ Important Disclaimer
The information provided in this guide, including content regarding manufacturers, technical specifications, and market analysis, is for informational and educational purposes only. It does not constitute professional procurement advice, financial advice, or legal advice.
While we have made every effort to ensure the accuracy and timeliness of the information, we are not responsible for any errors, omissions, or outdated information. Market conditions, company details, and technical standards are subject to change.
B2B buyers must conduct their own independent and thorough due diligence before making any purchasing decisions. This includes contacting suppliers directly, verifying certifications, requesting samples, and seeking professional consultation. The risk of relying on any information in this guide is borne solely by the reader.
Strategic Sourcing Conclusion and Outlook for robotic palletizing
In the evolving landscape of logistics and manufacturing, robotic palletizing emerges as a critical solution for businesses aiming to enhance efficiency and reduce operational costs. Key takeaways for international B2B buyers include the importance of investing in customizable robotic systems that cater to diverse product types and varying production speeds. Understanding the different models—from entry-level semi-automatic options to high-performance automated solutions—allows companies to select the right technology that aligns with their operational needs and budget constraints.
Strategic sourcing is essential in this context, as it not only involves selecting the right equipment but also establishing partnerships with reliable suppliers who can offer ongoing support and maintenance. Buyers from Africa, South America, the Middle East, and Europe should prioritize vendors that provide comprehensive lifecycle management services and robust technical support to ensure seamless integration into existing operations.
Looking ahead, the demand for robotic palletizing solutions will continue to grow as businesses seek to optimize their supply chains and enhance workplace safety. To capitalize on this trend, international buyers are encouraged to explore innovative robotic solutions that can scale with their operations. Engaging with experienced suppliers now will position your business for success in an increasingly automated future.