Discover Benefits of Closed Cell Polyurethane Foam (2025)
Introduction: Navigating the Global Market for closed cell polyurethane foam
Navigating the global market for closed cell polyurethane foam presents unique challenges, particularly for international B2B buyers in regions such as Africa, South America, the Middle East, and Europe. Sourcing high-quality closed cell polyurethane foam can be daunting due to the vast array of options available, from polyethylene to polystyrene variants, each with specific properties that cater to diverse applications. This guide aims to demystify the complexities of this versatile material, providing insights into the various types, applications, and performance characteristics of closed cell foams.
Throughout this comprehensive resource, we will explore the practical applications of closed cell polyurethane foam in industries ranging from automotive to healthcare, and offer guidance on supplier vetting to ensure quality and reliability. Additionally, we will address critical cost considerations, helping you to make informed purchasing decisions that align with your budget and project requirements.
By leveraging this guide, B2B buyers from Italy to Kenya will gain actionable insights into selecting the right foam solutions for their specific needs, ultimately enhancing their operational efficiency and product offerings. Whether you’re seeking materials for packaging, insulation, or specialized applications, this guide serves as your essential companion in navigating the global market for closed cell polyurethane foam.
Understanding closed cell polyurethane foam Types and Variations
Type Name | Key Distinguishing Features | Primary B2B Applications | Brief Pros & Cons for Buyers |
---|---|---|---|
Polyethylene Foam | Sturdy, water-resistant, good shock absorption | Packaging, sports, healthcare | Pros: Cost-effective, versatile. Cons: Limited temperature tolerance. |
Cross Linked Polyethylene Foam | Mold and mildew resistant, high durability | Industrial applications, flotation devices | Pros: Excellent chemical resistance. Cons: Higher cost compared to standard polyethylene. |
Polystyrene Foam | Rigid structure, available in various densities | Packaging, insulation, construction | Pros: High compressive strength. Cons: Less flexible than other foams. |
Neoprene Rubber Foam | Resistant to mold and bacteria, available in sheets and rolls | Flooring, insulation, athletic equipment packaging | Pros: Durable and sanitary. Cons: Heavier than other foam types. |
Polyurethane Foam Core | Rigid, flame-retardant, high strength-to-weight ratio | Composite structures, prototypes, packaging for RAM | Pros: Excellent structural integrity. Cons: More expensive than basic foams. |
What are the Characteristics of Polyethylene Foam?
Polyethylene foam is known for its sturdiness and water-resistant properties, making it an ideal choice for a wide range of applications, including packaging, healthcare, and sports equipment. This foam type offers good shock absorption and buoyancy, which is crucial for protecting sensitive items during transport. Buyers should consider its cost-effectiveness and versatility, although they should also note its limited tolerance to extreme temperatures, which may restrict its use in certain environments.
How Does Cross Linked Polyethylene Foam Stand Out?
Cross linked polyethylene foam is distinguished by its enhanced durability and resistance to mold and mildew. This foam is particularly suitable for industrial applications and flotation devices due to its robust structure and chemical resistance. When purchasing, B2B buyers should weigh the foam’s higher cost against its long-term benefits, such as reduced maintenance and replacement needs, especially in demanding environments.
What Makes Polystyrene Foam a Preferred Choice?
Polystyrene foam is characterized by its rigid structure and availability in various densities, which allows for tailored solutions to meet specific project requirements. It is commonly used in packaging, insulation, and construction applications. Buyers appreciate its high compressive strength, but should be aware that its rigidity may limit flexibility, making it less suitable for applications requiring bending or shaping.
Why Choose Neoprene Rubber Foam for Your Projects?
Neoprene rubber foam is highly regarded for its resistance to mold, mildew, and bacteria, making it a favored option for applications in clean environments such as hospitals and gyms. Available in both sheets and rolls, this foam is ideal for flooring and insulation. While it offers durability and sanitary benefits, buyers should consider its weight, which may influence shipping costs and ease of installation.
What are the Benefits of Polyurethane Foam Core?
Polyurethane foam core is a rigid, flame-retardant material known for its high strength-to-weight ratio, making it suitable for composite structures and prototypes. Its closed-cell design prevents water absorption, ensuring longevity in various applications, including packaging for radioactive materials. Buyers should factor in the higher cost of polyurethane foam core, but the investment is often justified by its superior performance and structural integrity in demanding applications.
Key Industrial Applications of closed cell polyurethane foam
Industry/Sector | Specific Application of closed cell polyurethane foam | Value/Benefit for the Business | Key Sourcing Considerations for this Application |
---|---|---|---|
Automotive | Sound insulation in vehicles | Reduces noise levels, enhancing passenger comfort and vehicle quality | Ensure compliance with regional automotive standards; consider weight and density requirements |
Construction | Insulation for walls and roofs | Improves energy efficiency, reducing heating and cooling costs | Verify thermal resistance properties; check for moisture resistance in humid climates |
Healthcare | Medical device packaging | Protects sensitive equipment during transport, ensuring safety and reliability | Look for FDA compliance; consider customization for specific device dimensions |
Marine and Recreational | Flotation devices and boat insulation | Enhances safety by providing buoyancy and thermal insulation | Assess buoyancy ratings; ensure resistance to water and UV damage |
Packaging | Protective packaging for fragile items | Minimizes damage during shipping, reducing costs associated with returns | Evaluate shock absorption properties; consider customization for specific product shapes |
How is Closed Cell Polyurethane Foam Used in the Automotive Industry?
In the automotive sector, closed cell polyurethane foam serves as an effective sound insulation material. Its dense structure significantly dampens noise levels, enhancing passenger comfort and overall vehicle quality. For international buyers, especially from regions like Africa and the Middle East, sourcing foam that meets local automotive standards is critical. Buyers should also consider the weight and density of the foam, as these factors directly influence vehicle performance and fuel efficiency.
What Role Does Closed Cell Polyurethane Foam Play in Construction?
Closed cell polyurethane foam is widely utilized for insulation in walls and roofs within the construction industry. Its superior thermal resistance contributes to energy efficiency by minimizing heat transfer, thereby reducing heating and cooling costs. For buyers in Europe, particularly in Italy where energy regulations are stringent, it is essential to verify the thermal resistance properties of the foam. Additionally, buyers should assess moisture resistance to ensure long-term performance, especially in humid climates.
How is Closed Cell Polyurethane Foam Beneficial in Healthcare Applications?
In healthcare, closed cell polyurethane foam is primarily used for packaging medical devices. Its cushioning properties protect sensitive equipment during transport, ensuring that items arrive safely and reliably. For international buyers, particularly in South America, it is vital to source foam that complies with FDA regulations. Customization may also be necessary to accommodate the specific dimensions of medical devices, making it essential to work with suppliers who offer tailored solutions.
What Advantages Does Closed Cell Polyurethane Foam Offer in Marine and Recreational Applications?
In the marine and recreational sectors, closed cell polyurethane foam is essential for flotation devices and boat insulation. Its buoyancy enhances safety on the water, while its thermal insulation properties keep users warm in cold conditions. Buyers, especially from coastal regions in Africa or Europe, should assess the buoyancy ratings of the foam and ensure its resistance to water and UV damage, which are critical for prolonged use in harsh marine environments.
How Does Closed Cell Polyurethane Foam Enhance Packaging Solutions?
Closed cell polyurethane foam is also used extensively in protective packaging for fragile items. Its shock absorption capabilities minimize damage during shipping, significantly reducing costs associated with returns and replacements. For B2B buyers in South America and the Middle East, evaluating the shock absorption properties of the foam is crucial. Additionally, customization options should be considered to fit the specific shapes and sizes of the products being packaged, ensuring optimal protection.
3 Common User Pain Points for ‘closed cell polyurethane foam’ & Their Solutions
Scenario 1: Difficulty in Sourcing the Right Density of Closed Cell Polyurethane Foam
The Problem: Many B2B buyers struggle to find closed cell polyurethane foam with the correct density for their specific applications. For instance, a manufacturer in the automotive sector might require a foam that not only provides insulation but also has a high strength-to-weight ratio to maintain vehicle efficiency. In regions like Africa and South America, where access to diverse suppliers may be limited, this challenge becomes even more pronounced. The wrong density can lead to product failure, increased costs, and ultimately dissatisfied customers.
The Solution: To address this issue, buyers should engage in thorough market research to identify suppliers that offer a variety of densities and grades of closed cell polyurethane foam. When sourcing, it’s crucial to request samples and conduct physical tests to ensure the material meets the desired specifications for compressive strength and thermal insulation. Additionally, buyers should clearly communicate their requirements to suppliers, including the intended application, environmental conditions, and any regulatory standards that must be met. This proactive approach will help ensure the selection of the right foam density, thereby improving product performance and reducing the risk of returns or complaints.
Scenario 2: Concerns About Water Resistance and Durability
The Problem: Another common pain point for B2B buyers is ensuring that the closed cell polyurethane foam they choose is truly water-resistant and durable. For example, construction firms in the Middle East, where humidity and temperature fluctuations can be extreme, need materials that will not degrade over time. Inadequate water resistance can lead to mold growth and structural issues, compromising both safety and quality.
The Solution: To mitigate this risk, buyers should prioritize sourcing closed cell polyurethane foam that is explicitly labeled as water-resistant and durable. When evaluating products, buyers should check for certifications such as ASTM or ISO standards that validate the foam’s performance against water absorption and resistance to mold and mildew. Furthermore, discussing the foam’s intended application with the supplier can lead to recommendations for surface treatments or coatings that enhance durability. Conducting field tests in similar environmental conditions can also provide insights into long-term performance, ensuring the chosen foam will withstand the rigors of its application.
Scenario 3: Misalignment Between Foam Specifications and Application Needs
The Problem: B2B buyers often face challenges when the specifications of closed cell polyurethane foam do not align with their application needs. For example, a company in Europe might order foam designed for insulation but receive a product that lacks the necessary fire-retardant properties required for compliance with local safety regulations. This misalignment can result in project delays, increased costs, and potential legal repercussions.
The Solution: To avoid such miscommunications, buyers must be diligent in specifying their needs during the ordering process. This includes providing detailed information about the foam’s intended use, required certifications, and environmental conditions. Establishing a checklist of critical properties—such as flame retardance, thermal conductivity, and load-bearing capacity—can serve as a guide during discussions with suppliers. Additionally, it may be beneficial to create a partnership with a supplier who understands the specific industry requirements and can provide ongoing support and guidance. Regularly reviewing and updating specifications based on evolving project needs will also help maintain alignment and ensure that the right materials are always sourced for each application.
Strategic Material Selection Guide for closed cell polyurethane foam
What Are the Key Properties of Common Closed Cell Polyurethane Foam Materials?
When selecting closed cell polyurethane foam for various applications, understanding the specific properties of different materials is crucial. Below, we analyze four common materials used in closed cell polyurethane foam, focusing on their key properties, advantages and disadvantages, application impacts, and considerations for international B2B buyers.
1. Polyethylene Foam
Key Properties:
Polyethylene foam is lightweight and offers excellent buoyancy, sound dampening, and shock absorption. It is resistant to moisture, chemicals, and UV radiation, making it suitable for outdoor applications.
Pros & Cons:
The main advantage of polyethylene foam is its versatility and cost-effectiveness, particularly for packaging and insulation. However, it may not withstand high temperatures as well as other materials, limiting its use in heat-sensitive applications.
Impact on Application:
This foam is ideal for applications that require cushioning and protection, such as packaging fragile items or insulation in construction. Its compatibility with various media makes it a preferred choice for many industries.
Considerations for International Buyers:
Buyers from regions like Africa and South America should ensure compliance with local environmental regulations, as polyethylene foam can be less biodegradable. Familiarity with standards such as ASTM and ISO can help in selecting the right product.
2. Cross-Linked Polyethylene Foam
Key Properties:
Cross-linked polyethylene (XLPE) foam features a dense structure that enhances its durability and resistance to moisture and chemicals. It can handle higher temperatures compared to standard polyethylene.
Pros & Cons:
XLPE foam is highly resilient, making it suitable for demanding applications such as automotive and marine uses. However, its manufacturing process can be more complex, leading to higher costs.
Impact on Application:
Due to its robustness, XLPE is often used in applications requiring thermal insulation and impact resistance. It is particularly effective in environments where exposure to water and harsh chemicals is common.
Considerations for International Buyers:
International buyers should verify that the XLPE foam meets relevant industry standards, such as DIN for construction applications. Additionally, understanding the local market for pricing can help in budgeting.
3. Neoprene Rubber Foam
Key Properties:
Neoprene foam offers excellent resistance to temperature fluctuations, water, and chemicals. It has a high tensile strength and can be manufactured in various densities.
Pros & Cons:
The main advantage of neoprene foam is its durability and versatility in applications ranging from insulation to protective gear. However, it can be more expensive than other foam types, which may affect budget-conscious projects.
Impact on Application:
Neoprene is commonly used in applications requiring high resilience, such as in the automotive and aerospace industries. Its ability to resist mold and mildew makes it suitable for healthcare environments.
Considerations for International Buyers:
Buyers should ensure compliance with health and safety standards, especially in the healthcare sector. Additionally, understanding the local supply chain can help in sourcing neoprene foam efficiently.
4. Polypropylene Foam
Key Properties:
Polypropylene foam is known for its high rigidity and strength-to-weight ratio. It is resistant to moisture and chemicals, making it suitable for various industrial applications.
Pros & Cons:
The primary advantage of polypropylene foam is its superior strength, making it ideal for heavy-duty packaging and structural applications. However, it can be less flexible than other foam types, which may limit its use in certain scenarios.
Impact on Application:
This foam is particularly effective in applications requiring strong, lightweight materials, such as in automotive parts and protective packaging. Its compatibility with various media enhances its utility across industries.
Considerations for International Buyers:
International buyers should consider the specific regulations regarding the use of polypropylene in their respective markets. Familiarity with compliance standards like JIS can facilitate smoother procurement processes.
Summary Table of Closed Cell Polyurethane Foam Materials
Material | Typical Use Case for closed cell polyurethane foam | Key Advantage | Key Disadvantage/Limitation | Relative Cost (Low/Med/High) |
---|---|---|---|---|
Polyethylene Foam | Packaging, insulation | Versatile and cost-effective | Limited temperature resistance | Low |
Cross-Linked Polyethylene Foam | Automotive, marine applications | High durability and moisture resistance | Higher manufacturing complexity | Medium |
Neoprene Rubber Foam | Insulation, protective gear | Excellent resilience | Higher cost compared to alternatives | High |
Polypropylene Foam | Heavy-duty packaging, structural applications | Superior strength and rigidity | Less flexibility | Medium |
This guide provides a comprehensive overview of closed cell polyurethane foam materials, enabling international B2B buyers to make informed decisions based on their specific application needs and regional considerations.
In-depth Look: Manufacturing Processes and Quality Assurance for closed cell polyurethane foam
What Are the Main Stages of Manufacturing Closed Cell Polyurethane Foam?
The manufacturing process for closed cell polyurethane foam involves several key stages, each critical to ensuring the final product meets specific performance and quality standards. Understanding these stages can help B2B buyers assess potential suppliers more effectively.
1. Material Preparation
The first step in manufacturing closed cell polyurethane foam is the preparation of raw materials. This typically includes polyols and isocyanates, which are the primary components of polyurethane. Other additives may include flame retardants, colorants, and blowing agents.
- Key Techniques: Suppliers often use specialized mixers to ensure that the components are combined evenly. The quality of the raw materials is vital; therefore, suppliers should conduct Incoming Quality Control (IQC) checks to verify that materials meet specified standards.
2. Forming the Foam
Once the materials are prepared, the next stage is forming the foam. This involves mixing the prepared components at controlled temperatures and pressures to initiate a chemical reaction that produces foam.
- Key Techniques: The process can vary based on the desired properties of the foam. For example, continuous pouring, batch processing, or block molding techniques can be employed. The choice of method can affect the density and structural integrity of the final product.
3. Assembly and Curing
After forming, the foam is allowed to cure. This stage is critical as it determines the foam’s final properties, including its strength and resilience.
- Key Techniques: Curing can be enhanced through controlled temperature and humidity conditions. Some manufacturers may also use additives to accelerate curing times. It’s essential for suppliers to maintain consistency during this phase to achieve uniform quality across batches.
4. Finishing Processes
The final stage involves finishing the foam, which may include cutting, shaping, or laminating. This is where the foam is tailored to specific applications, such as insulation, packaging, or cushioning.
- Key Techniques: CNC machining is commonly used for precision cutting and shaping, ensuring that the foam meets exact specifications. Additionally, surface treatments may be applied to enhance properties such as adhesion or resistance to chemicals.
What International Standards Should B2B Buyers Be Aware Of?
Quality assurance in closed cell polyurethane foam manufacturing is governed by various international standards. Understanding these can help buyers ensure they are selecting reliable suppliers.
ISO 9001: What Does It Mean for Quality Management?
ISO 9001 is a widely recognized standard for quality management systems (QMS). Manufacturers certified under this standard demonstrate their commitment to consistent quality and customer satisfaction.
- Relevance for Buyers: When assessing suppliers, buyers should request proof of ISO 9001 certification. This indicates that the manufacturer has implemented processes for continuous improvement and adheres to best practices in quality management.
CE Marking and Other Industry-Specific Certifications
For products sold within the European Union, CE marking signifies compliance with health, safety, and environmental protection standards. Other industry-specific certifications, such as API (American Petroleum Institute) for products used in the oil and gas sector, may also apply.
- Relevance for Buyers: B2B buyers should verify that suppliers possess the necessary certifications relevant to their industry. This not only ensures compliance but also enhances product credibility in the marketplace.
How Do Quality Control Checkpoints Ensure Product Integrity?
Quality control checkpoints are crucial in the manufacturing process of closed cell polyurethane foam. These checkpoints help ensure that the foam meets specified performance characteristics and safety standards.
1. Incoming Quality Control (IQC)
IQC involves testing raw materials upon arrival at the manufacturing facility. This step ensures that only materials that meet the required specifications are used in the production process.
2. In-Process Quality Control (IPQC)
During the manufacturing process, IPQC checks are performed to monitor the production environment and conditions. This helps identify any deviations from the established manufacturing protocols.
3. Final Quality Control (FQC)
FQC is conducted once the product is finished. This includes testing for physical properties such as density, compressive strength, and resistance to water absorption.
What Common Testing Methods Are Used in Quality Assurance?
To verify the quality of closed cell polyurethane foam, various testing methods are employed:
- Physical Testing: This includes measuring density, tensile strength, and compressive strength.
- Water Absorption Tests: Essential for applications where moisture resistance is critical.
- Flammability Testing: For compliance with safety standards, especially in industries like automotive and construction.
How Can B2B Buyers Verify Supplier Quality Control?
For international B2B buyers, verifying the quality control practices of potential suppliers is essential. Here are some actionable steps:
Conduct Supplier Audits
Regular audits of suppliers can provide insights into their manufacturing processes and quality control measures. Buyers should prepare a checklist based on relevant standards and best practices.
Request Quality Control Reports
Buyers should request documentation that outlines the supplier’s quality control processes, including IQC, IPQC, and FQC reports. This documentation should detail the results of tests performed and any corrective actions taken.
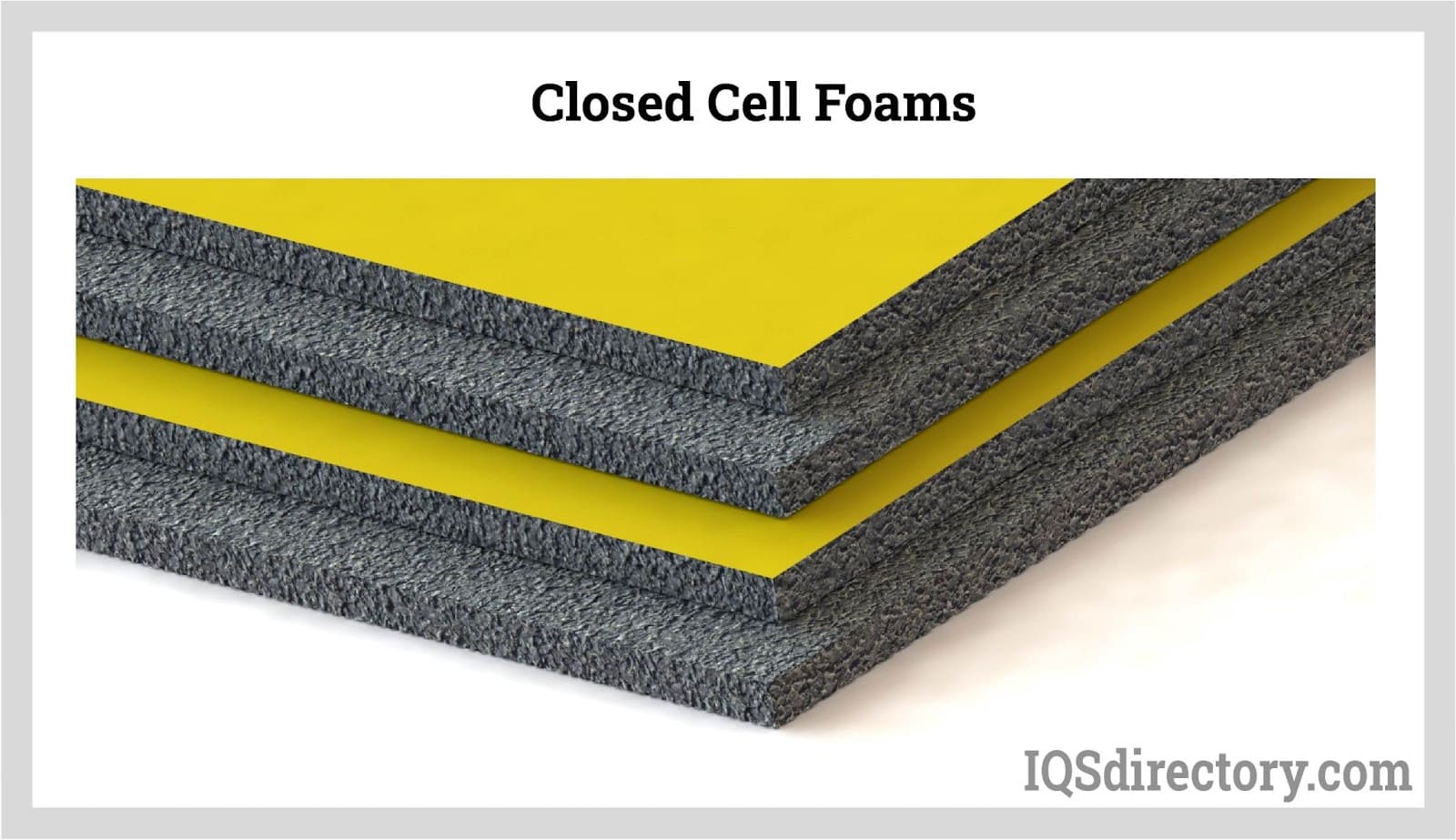
A stock image related to closed cell polyurethane foam.
Engage Third-Party Inspectors
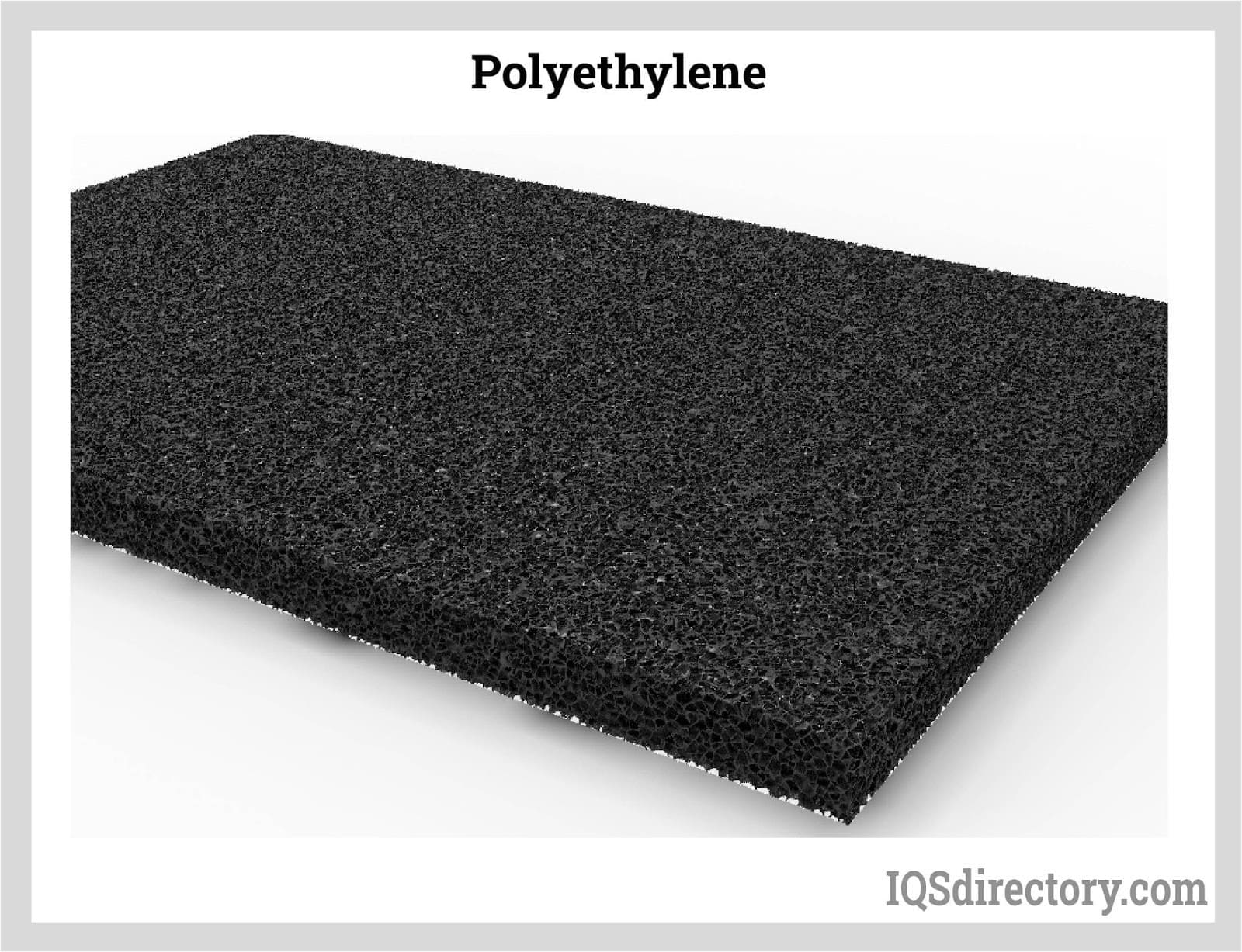
A stock image related to closed cell polyurethane foam.
For buyers, particularly those in Africa, South America, the Middle East, and Europe, using third-party inspection services can provide an unbiased assessment of the supplier’s quality control processes.
What Are the Quality Control Nuances for International B2B Buyers?
When sourcing closed cell polyurethane foam, international buyers must consider regional regulations and standards.
-
Regional Compliance: Different regions may have specific requirements, such as environmental regulations in the EU or fire safety standards in the Middle East. Buyers should be familiar with these local requirements to ensure compliance.
-
Cultural Considerations: Understanding the business practices and expectations in different regions can aid in establishing effective communication and partnerships with suppliers.
In conclusion, a thorough understanding of the manufacturing processes, quality assurance standards, and verification methods for closed cell polyurethane foam can empower B2B buyers to make informed decisions. Prioritizing quality and compliance not only reduces risks but also enhances the overall value of their procurement strategies.
Practical Sourcing Guide: A Step-by-Step Checklist for ‘closed cell polyurethane foam’
To successfully procure closed cell polyurethane foam, international B2B buyers must navigate a series of strategic steps to ensure they select the right product and supplier. This checklist provides actionable insights tailored to the specific needs of buyers from regions such as Africa, South America, the Middle East, and Europe.
Step 1: Define Your Technical Specifications
Establishing clear technical specifications is crucial for sourcing closed cell polyurethane foam that meets your project requirements. Consider factors such as density, thickness, flame retardancy, and water absorption characteristics. Specific applications, such as automotive or construction, may require unique properties, so detail these in your specifications to guide supplier discussions.
Step 2: Identify Your Application Needs
Understanding the intended application of the foam is vital. Closed cell polyurethane foam is versatile, used in areas ranging from packaging to insulation and even flotation devices. Clarifying your specific needs will help you select the right type of foam and ensure it meets performance expectations.
Step 3: Evaluate Potential Suppliers
Before committing, vet potential suppliers thoroughly. Request company profiles, case studies, and references from buyers in similar industries or regions. Ensure they have experience with closed cell polyurethane foam and can provide evidence of quality and reliability, such as industry certifications or standards compliance.
- Check for Certifications: Look for ISO certifications or other relevant industry standards that indicate quality assurance.
Step 4: Assess Material Properties
Investigate the material properties of the closed cell polyurethane foam offered by suppliers. Key attributes to consider include compressive strength, thermal conductivity, and resistance to chemicals and moisture. Understanding these properties helps ensure the foam will perform adequately in your specific application.
Step 5: Request Samples for Testing
Always request samples before finalizing your order. Testing samples allows you to evaluate the foam’s performance in real-world conditions relevant to your application. Check for characteristics like durability, flexibility, and moisture resistance during your testing phase.
Step 6: Review Pricing and Payment Terms
Once you’ve narrowed down your options, review pricing structures and payment terms. Understand what factors influence the cost, such as material density, custom sizes, or additional services like CNC machining. Negotiate terms that align with your budget while considering quality as a priority.
Step 7: Establish Logistics and Delivery Terms
Finally, clarify logistics and delivery terms with your chosen supplier. Discuss shipping methods, lead times, and any potential customs issues, especially if sourcing from international suppliers. Ensure that the supplier can meet your delivery timeline to avoid project delays.
By following this checklist, B2B buyers can streamline the procurement process for closed cell polyurethane foam, ensuring they make informed decisions that support their business needs.
Comprehensive Cost and Pricing Analysis for closed cell polyurethane foam Sourcing
What Are the Key Cost Components for Closed Cell Polyurethane Foam?
When sourcing closed cell polyurethane foam, understanding the cost structure is essential for making informed purchasing decisions. The main cost components include:
-
Materials: The primary raw materials for closed cell polyurethane foam, such as isocyanates and polyols, significantly impact pricing. Variations in these materials can lead to price fluctuations based on market demand and availability.
-
Labor: Labor costs encompass the wages paid to workers involved in manufacturing, cutting, and finishing the foam. This cost can vary by region, with labor rates generally higher in Europe compared to regions in Africa and South America.
-
Manufacturing Overhead: This includes expenses related to utilities, facility maintenance, and equipment depreciation. Efficient manufacturing processes can help reduce overhead costs, which in turn can lower the final price of the foam.
-
Tooling: Custom tooling for specific foam shapes or sizes can incur additional costs. For international buyers, understanding the tooling requirements can be crucial, as these costs can vary significantly between suppliers.
-
Quality Control (QC): Implementing rigorous QC processes ensures product consistency and compliance with safety standards. The costs associated with QC can influence overall pricing, especially for high-quality or specialized foam products.
-
Logistics: Shipping costs, including freight and handling fees, are critical, particularly for international shipments. Factors such as distance, shipping method, and local tariffs can significantly affect logistics costs.
-
Margin: Suppliers will add a profit margin to cover their risks and operational expenses. This margin can vary widely based on the supplier’s market position, brand reputation, and service offerings.
How Do Volume and Customization Impact Pricing for Closed Cell Polyurethane Foam?
Pricing for closed cell polyurethane foam can be heavily influenced by order volume and customization requirements:
-
Volume/MOQ: Larger orders often qualify for bulk pricing, which can reduce the cost per unit significantly. Buyers should consider their anticipated needs and negotiate minimum order quantities (MOQ) to achieve better rates.
-
Specifications and Customization: Custom specifications, such as density, thickness, and specific chemical properties, may lead to higher prices. Buyers should clearly define their requirements to avoid unexpected costs and delays.
What Factors Influence Pricing in the Sourcing of Closed Cell Polyurethane Foam?
Several external factors can influence pricing dynamics in the sourcing of closed cell polyurethane foam:
-
Material Quality and Certifications: Higher quality materials and certifications (e.g., flame retardancy, environmental compliance) can increase costs. Buyers should weigh the benefits of these certifications against their budget constraints.
-
Supplier Reputation and Reliability: Well-established suppliers may charge higher prices due to their perceived quality and reliability. However, partnering with reputable suppliers can lead to better service and lower risks in the long term.
-
Incoterms: Understanding Incoterms is crucial for international buyers. The chosen Incoterm can affect costs related to shipping, insurance, and customs duties, which can significantly alter the total cost of ownership.
What Are the Best Negotiation and Cost-Efficiency Tips for International Buyers?
For international B2B buyers, particularly from regions like Africa, South America, the Middle East, and Europe, here are actionable tips for negotiating better prices:
-
Research Market Prices: Before negotiations, conduct thorough market research to understand the standard pricing for closed cell polyurethane foam. This knowledge empowers buyers during discussions.
-
Leverage Total Cost of Ownership (TCO): When assessing suppliers, consider the TCO, which includes all costs associated with the procurement process, such as maintenance, logistics, and potential future customizations.
-
Build Long-Term Relationships: Establishing strong relationships with suppliers can lead to more favorable pricing and better service. Regular communication and feedback can foster trust and collaboration.
-
Request Samples: Before placing large orders, request samples to evaluate the quality and ensure it meets specifications. This practice can help avoid costly mistakes.
Disclaimer on Indicative Prices
Prices for closed cell polyurethane foam can vary significantly based on numerous factors, including market conditions, supplier pricing strategies, and specific buyer requirements. Always consult directly with suppliers for the most accurate and up-to-date pricing information tailored to your specific needs.
Alternatives Analysis: Comparing closed cell polyurethane foam With Other Solutions
Exploring Alternatives to Closed Cell Polyurethane Foam
When considering materials for insulation, packaging, or cushioning, closed cell polyurethane foam often stands out due to its unique properties. However, various alternatives exist that may better suit specific applications or budget constraints. This analysis will compare closed cell polyurethane foam with two viable alternatives: Cross-Linked Polyethylene Foam and Polystyrene Foam. Each option has its distinct advantages and disadvantages, making it essential for B2B buyers to understand these differences to make informed decisions.
Comparison Table
Comparison Aspect | Closed Cell Polyurethane Foam | Cross-Linked Polyethylene Foam | Polystyrene Foam |
---|---|---|---|
Performance | High strength-to-weight ratio, excellent thermal insulation, resistant to water and chemicals | Good shock absorption, water-resistant, mold-resistant | Lightweight, rigid, excellent for packaging but less insulating |
Cost | Moderate to high, depending on density and customization | Moderate, often slightly lower than polyurethane | Generally low-cost, widely available |
Ease of Implementation | Requires specialized tools for cutting and shaping | Easily shaped with standard tools | Simple to cut and shape, minimal tooling required |
Maintenance | Low maintenance, resistant to mold and chemicals | Low maintenance, easy to clean | Moderate maintenance, can be damaged by moisture |
Best Use Case | Aerospace, automotive, and construction applications requiring fire resistance | Medical packaging, sports equipment, and flotation devices | Packaging, insulation, and construction applications where rigidity is needed |
Detailed Breakdown of Alternatives
What are the advantages and disadvantages of Cross-Linked Polyethylene Foam?
Cross-linked polyethylene foam is known for its good shock absorption and excellent resistance to water and mold. This makes it a suitable choice for applications in medical packaging and sports equipment. Additionally, it can be easily shaped using standard woodworking tools, facilitating quick implementation. However, while it offers good insulation properties, it may not match the thermal performance of closed cell polyurethane foam, particularly in high-temperature applications. Cost-wise, it typically falls in the moderate range, making it a cost-effective choice for many industries.
How does Polystyrene Foam compare to closed cell polyurethane foam?
Polystyrene foam is lightweight and rigid, making it a popular choice for packaging and insulation. Its affordability is a significant advantage, especially for B2B buyers operating within tight budgets. However, it lacks the thermal insulation properties of closed cell polyurethane foam and is more susceptible to moisture damage. While it is easy to cut and shape, the rigidity of polystyrene limits its application in scenarios requiring more flexibility or cushioning. This foam is best used in applications where weight savings and cost efficiency are prioritized over insulation performance.
Conclusion: How to Choose the Right Foam Solution for Your Needs
Selecting the right foam solution requires careful consideration of various factors, including performance requirements, budget, and application specifics. Closed cell polyurethane foam excels in applications demanding high strength, fire resistance, and superior insulation. In contrast, cross-linked polyethylene foam may be preferable for environments requiring moisture resistance and shock absorption. Polystyrene foam offers an economical choice for packaging and insulation where flexibility and thermal properties are less critical. By evaluating the specific needs of your project against the strengths and weaknesses of each alternative, B2B buyers from regions like Africa, South America, the Middle East, and Europe can make informed decisions that align with their operational goals.
Essential Technical Properties and Trade Terminology for closed cell polyurethane foam
What Are the Key Technical Properties of Closed Cell Polyurethane Foam?
Closed cell polyurethane foam is widely recognized for its durability, versatility, and insulation properties. For B2B buyers, understanding its technical specifications is crucial for selecting the right foam for specific applications. Here are some essential properties:
-
Density
– Definition: Density refers to the mass of foam per unit volume, typically expressed in pounds per cubic foot (PCF).
– Importance: Higher density foams often provide better structural support and durability. For example, a density of 6 PCF is common for rigid applications, making it suitable for use in packaging and insulation. -
Compressive Strength
– Definition: This measures the foam’s ability to withstand axial loads without collapsing, often quantified in psi (pounds per square inch).
– Importance: A higher compressive strength indicates that the foam can endure greater loads, which is essential for applications like automotive parts or structural components where weight and durability are critical. -
Thermal Conductivity
– Definition: This property indicates how well the foam insulates against heat transfer, measured in BTUin/ft²°Fh.
– Importance*: Lower thermal conductivity values signify better insulation properties, making closed cell polyurethane foam ideal for energy-efficient buildings and refrigeration applications. -
Water Absorption
– Definition: This indicates the amount of water the foam can absorb over time, typically measured in pounds per square foot.
– Importance: Closed cell foams are designed to be water-resistant, making them suitable for marine applications or environments with high moisture levels. A low water absorption rate (e.g., 0.17 lbs/ft²) ensures longevity in challenging conditions. -
Flame Retardancy
– Definition: This property refers to the foam’s ability to resist ignition and slow the spread of fire.
– Importance: Flame-retardant foams are essential for applications in industries such as aerospace and construction, where safety regulations require materials to meet specific fire resistance standards.
What Are Common Trade Terms Related to Closed Cell Polyurethane Foam?
Understanding trade terminology is essential for effective communication in the B2B sector. Here are some common terms that buyers should know:
-
OEM (Original Equipment Manufacturer)
– Definition: A company that produces parts or equipment that may be marketed by another manufacturer.
– Relevance: Understanding OEM specifications is vital for buyers looking to source foam for specific equipment or machinery, ensuring compatibility and performance. -
MOQ (Minimum Order Quantity)
– Definition: The smallest quantity of a product that a supplier is willing to sell.
– Relevance: Knowing the MOQ helps buyers plan their purchasing strategy, ensuring they meet supplier requirements without overcommitting to inventory. -
RFQ (Request for Quotation)
– Definition: A document sent to suppliers to request pricing information for specific products or services.
– Relevance: An RFQ is essential for comparing costs and negotiating better terms, allowing buyers to make informed financial decisions. -
Incoterms (International Commercial Terms)
– Definition: A set of internationally recognized rules that define the responsibilities of buyers and sellers in international transactions.
– Relevance: Familiarity with Incoterms is crucial for understanding shipping responsibilities, costs, and risks, especially for international buyers from regions like Africa and South America. -
CFC-Free
– Definition: Refers to products that do not contain chlorofluorocarbons, which are harmful to the ozone layer.
– Relevance: For environmentally conscious buyers, sourcing CFC-free closed cell polyurethane foam ensures compliance with environmental regulations and supports sustainability initiatives.
By grasping these technical properties and trade terms, international B2B buyers can make informed decisions when sourcing closed cell polyurethane foam, ensuring they select products that meet their specific application needs and comply with regulatory standards.
Navigating Market Dynamics and Sourcing Trends in the closed cell polyurethane foam Sector
What are the Current Market Dynamics and Key Trends in Closed Cell Polyurethane Foam?
Closed cell polyurethane foam is witnessing robust growth across various sectors due to its unique properties such as water resistance, durability, and excellent insulation capabilities. The global demand for this material is driven by industries including automotive, construction, packaging, and healthcare. In regions like Africa, South America, the Middle East, and Europe, the rapid urbanization and infrastructural developments are significantly boosting the demand for insulation and protective materials.
Emerging B2B technologies, such as advanced manufacturing processes and automation, are reshaping sourcing strategies. For instance, companies are increasingly leveraging digital platforms for procurement, enabling them to source materials more efficiently and cost-effectively. Furthermore, the rise of just-in-time (JIT) inventory systems is allowing businesses to minimize storage costs while ensuring timely availability of closed cell foam products.
Another notable trend is the increasing focus on customization. Buyers are looking for suppliers who can provide tailored solutions, such as specific densities or dimensions that meet unique project requirements. This is particularly relevant in regions with diverse climate conditions, such as the Middle East, where thermal insulation is crucial.
How is Sustainability and Ethical Sourcing Impacting the Closed Cell Polyurethane Foam Market?
Sustainability has become a central theme in the sourcing of closed cell polyurethane foam. As global awareness about environmental impacts increases, B2B buyers are actively seeking materials that align with eco-friendly practices. Closed cell polyurethane foam can be produced using water-blown technologies, which significantly reduce the emission of volatile organic compounds (VOCs), making it a more sustainable option.
Ethical sourcing is also gaining traction. Buyers are increasingly demanding transparency in the supply chain, pushing manufacturers to adopt ethical practices. Certifications such as ISO 14001 for environmental management and Greenguard for low chemical emissions are becoming essential for suppliers aiming to attract discerning international buyers.
In regions like Europe, where regulatory frameworks are stringent, compliance with sustainability standards is not just beneficial but mandatory. B2B buyers from Africa and South America are also encouraged to evaluate suppliers based on their environmental and social governance (ESG) practices to ensure long-term partnerships that are both profitable and responsible.
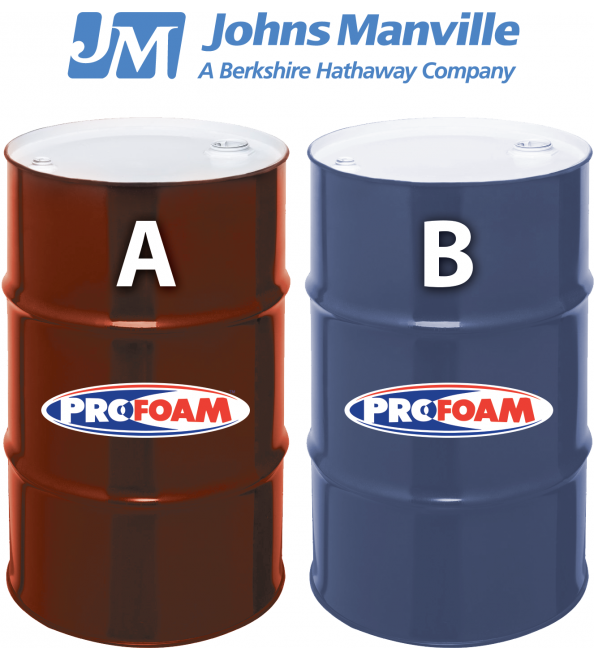
A stock image related to closed cell polyurethane foam.
What is the Brief Evolution and History of Closed Cell Polyurethane Foam in B2B Markets?
The evolution of closed cell polyurethane foam dates back to the mid-20th century when it was first developed as a lightweight and durable material suitable for various applications. Initially utilized in the aerospace and automotive industries, its unique properties quickly found favor in sectors such as construction, marine, and healthcare.
Over the decades, advancements in foam technology, including the introduction of cross-linked structures, have enhanced its mechanical properties and thermal insulation capabilities. Today, closed cell polyurethane foam is recognized not only for its functional benefits but also for its potential in promoting sustainability within the manufacturing process.
As the market continues to evolve, international B2B buyers are encouraged to stay informed about technological advancements and emerging trends, ensuring they make strategic sourcing decisions that align with their business objectives.
Frequently Asked Questions (FAQs) for B2B Buyers of closed cell polyurethane foam
-
How do I select the right closed cell polyurethane foam for my application?
Selecting the appropriate closed cell polyurethane foam depends on several factors, including the intended use, environmental conditions, and specific properties required. Consider the foam’s density, water resistance, thermal insulation, and chemical resistance. For instance, if you need foam for packaging sensitive equipment, choose a foam with high shock absorption and cushioning properties. Conducting a thorough analysis of your project’s requirements and consulting with suppliers can help ensure you make an informed decision. -
What are the advantages of using closed cell polyurethane foam over other materials?
Closed cell polyurethane foam offers numerous advantages, including superior water resistance, thermal insulation, and durability. Its closed cell structure prevents moisture absorption, making it ideal for applications in wet or humid environments. Additionally, it has excellent compressive strength and is resistant to chemicals and solvents, which enhances its longevity in industrial settings. These properties make it a preferred choice for sectors such as automotive, aerospace, and construction. -
How can I verify the quality of closed cell polyurethane foam before purchasing?
To verify the quality of closed cell polyurethane foam, request samples from potential suppliers and conduct tests for density, compressive strength, and water absorption. Review certifications like ISO 9001 or ASTM standards to ensure compliance with industry norms. Additionally, inquire about the supplier’s manufacturing processes, quality control measures, and any third-party testing they may utilize to guarantee product consistency. -
What are the common customization options available for closed cell polyurethane foam?
Many manufacturers offer customization options for closed cell polyurethane foam, such as varying thickness, density, and shapes. You can also request specific dimensions and colors to meet your project needs. Some suppliers provide CNC machining services for precise cuts and shapes. Discussing your requirements with the supplier can help them tailor their offerings to your specifications, ensuring optimal performance for your application. -
What is the typical minimum order quantity (MOQ) for closed cell polyurethane foam?
The minimum order quantity (MOQ) for closed cell polyurethane foam can vary significantly among suppliers, typically ranging from 100 square feet to several thousand. Smaller quantities may be available but might incur higher costs. It’s essential to communicate your needs with potential suppliers to negotiate favorable terms, especially if you’re a small business or a startup. -
What payment terms should I expect when sourcing closed cell polyurethane foam internationally?
Payment terms for international orders of closed cell polyurethane foam can vary widely depending on the supplier and the buyer’s creditworthiness. Common arrangements include upfront payments, 30-day net terms, or letters of credit. Ensure you clarify payment methods and conditions before finalizing the order to avoid misunderstandings. Establishing a good relationship with your supplier can also help negotiate more favorable terms. -
How do I handle logistics and shipping for closed cell polyurethane foam?
When arranging logistics for international shipments of closed cell polyurethane foam, consider factors such as packaging requirements, lead times, and customs regulations. Ensure that the foam is packaged adequately to prevent damage during transit, as some foams may require custom packaging solutions. Work with a freight forwarder experienced in handling foam products to streamline the shipping process and ensure compliance with international trade regulations. -
What are the best practices for supplier vetting when sourcing closed cell polyurethane foam?
Vetting suppliers for closed cell polyurethane foam involves assessing their reputation, quality certifications, and financial stability. Start by reviewing customer testimonials and case studies to gauge their reliability. Request references and check for any complaints with trade organizations. It’s also beneficial to visit the supplier’s manufacturing facility, if possible, to observe their processes and quality control measures firsthand. This thorough vetting can help mitigate risks and ensure you partner with a reputable supplier.
Important Disclaimer & Terms of Use
⚠️ Important Disclaimer
The information provided in this guide, including content regarding manufacturers, technical specifications, and market analysis, is for informational and educational purposes only. It does not constitute professional procurement advice, financial advice, or legal advice.
While we have made every effort to ensure the accuracy and timeliness of the information, we are not responsible for any errors, omissions, or outdated information. Market conditions, company details, and technical standards are subject to change.
B2B buyers must conduct their own independent and thorough due diligence before making any purchasing decisions. This includes contacting suppliers directly, verifying certifications, requesting samples, and seeking professional consultation. The risk of relying on any information in this guide is borne solely by the reader.
Strategic Sourcing Conclusion and Outlook for closed cell polyurethane foam
In today’s competitive landscape, the strategic sourcing of closed cell polyurethane foam presents significant opportunities for international B2B buyers. As industries across Africa, South America, the Middle East, and Europe increasingly recognize the versatility and durability of this material, understanding its applications—from packaging to insulation—becomes crucial. The unique properties of closed cell foam, such as water resistance, flame retardancy, and high strength-to-weight ratio, make it an invaluable asset in various sectors including automotive, construction, and healthcare.
How Can Strategic Sourcing Enhance Your Procurement Process?
By leveraging strategic sourcing, businesses can optimize their supply chain, reduce costs, and improve product quality. Engaging with reliable suppliers who understand local market dynamics and can provide tailored solutions ensures that you receive the best value for your investment. This approach not only enhances operational efficiency but also fosters long-term partnerships that can drive innovation.
What Does the Future Hold for Closed Cell Polyurethane Foam?
Looking ahead, the demand for closed cell polyurethane foam is expected to grow, driven by advancements in technology and sustainability initiatives. For B2B buyers in regions like Italy and Kenya, now is the time to explore strategic partnerships that can position your business for success in this evolving market. Embrace the potential of closed cell foam solutions to enhance your product offerings and meet the diverse needs of your customers. Take action today to secure your competitive edge in the marketplace.