Discover Cost-Saving Benefits of Polyethene Tubing (2025)
Introduction: Navigating the Global Market for polyethene tubing
Navigating the complexities of sourcing polyethylene tubing can be a significant challenge for international B2B buyers. With various types and applications ranging from potable water systems to industrial gas lines, understanding the nuances of polyethylene tubing is crucial for making informed purchasing decisions. This guide provides a comprehensive overview of polyethylene tubing, detailing the different types, their specific applications, and the critical factors to consider when vetting suppliers.
For buyers in regions like Africa, South America, the Middle East, and Europe—such as Egypt and the UK—this resource is tailored to address your unique market dynamics. You’ll learn how to effectively assess supplier reliability, evaluate cost structures, and recognize compliance with international standards. Moreover, insights into regional supply chains and logistics will empower you to streamline procurement processes and mitigate risks associated with sourcing.
By equipping you with actionable knowledge and strategic insights, this guide aims to enhance your purchasing strategies, ensuring you select the most suitable polyethylene tubing solutions for your operational needs. Whether you are looking to optimize costs, enhance product quality, or ensure compliance with regulations, this comprehensive resource is designed to help you navigate the global market with confidence.
Understanding polyethene tubing Types and Variations
Type Name | Key Distinguishing Features | Primary B2B Applications | Brief Pros & Cons for Buyers |
---|---|---|---|
Low-Density Polyethylene (LDPE) | Flexible, lightweight, and resistant to impact and moisture | Packaging, tubing for liquids | Pros: Cost-effective, good for low-pressure applications. Cons: Less durable than HDPE. |
High-Density Polyethylene (HDPE) | Higher tensile strength, chemical resistance, and UV stability | Water supply, gas distribution | Pros: Long-lasting, suitable for high-pressure systems. Cons: More expensive than LDPE. |
Linear Low-Density Polyethylene (LLDPE) | Enhanced flexibility and puncture resistance compared to LDPE | Food and beverage, agricultural use | Pros: Excellent for high-stress applications. Cons: Limited temperature resistance. |
Polyethylene Tubing for Medical Use | FDA approved, non-toxic, and sterilizable | Medical devices, laboratory use | Pros: High safety standards, versatile. Cons: More expensive due to regulatory compliance. |
EVA-Lined Polyethylene Tubing | Combines flexibility with enhanced chemical resistance | Industrial applications, food processing | Pros: Excellent for harsh chemicals, maintains integrity. Cons: Can be pricier than standard tubing. |
What Are the Characteristics of Low-Density Polyethylene (LDPE) Tubing?
Low-Density Polyethylene (LDPE) tubing is characterized by its flexibility and lightweight properties, making it an ideal choice for applications requiring bending and shaping. It is resistant to moisture, which is beneficial for packaging and tubing in liquid transfer systems. When considering B2B purchases, buyers should note that while LDPE is cost-effective, its lower durability compared to HDPE may limit its use in high-pressure situations.
Why Choose High-Density Polyethylene (HDPE) Tubing?
High-Density Polyethylene (HDPE) tubing is known for its superior tensile strength and chemical resistance, making it suitable for demanding applications such as water supply and gas distribution. Its UV stability allows for outdoor installations without degradation over time. B2B buyers should weigh the long-term investment against the higher upfront costs, as HDPE offers a more robust solution for high-pressure systems.
What Are the Advantages of Linear Low-Density Polyethylene (LLDPE) Tubing?
Linear Low-Density Polyethylene (LLDPE) tubing offers enhanced flexibility and puncture resistance, which is crucial in applications such as food and beverage processing and agricultural use. Its environmental stress crack resistance (ESCR) makes it a reliable choice for high-stress environments. Buyers should consider LLDPE for projects requiring both flexibility and durability, although they should be aware of its limitations regarding temperature resistance.
How Does Medical-Grade Polyethylene Tubing Differ?
Medical-grade polyethylene tubing is specifically designed to meet FDA regulations, ensuring non-toxicity and sterility for medical applications. This tubing is essential for devices that require high safety standards, such as in laboratories and medical devices. While it provides versatility and safety, buyers should prepare for higher costs associated with compliance and quality assurance.
What Makes EVA-Lined Polyethylene Tubing Ideal for Harsh Environments?
EVA-lined polyethylene tubing combines flexibility with enhanced chemical resistance, making it suitable for industrial applications and food processing. This tubing maintains its integrity even in harsh chemical environments, which is vital for many B2B operations. Buyers should consider the cost-benefit ratio, as while EVA-lined tubing may be pricier, its durability and performance in challenging conditions can justify the investment.
Key Industrial Applications of polyethene tubing
Industry/Sector | Specific Application of Polyethene Tubing | Value/Benefit for the Business | Key Sourcing Considerations for this Application |
---|---|---|---|
Agriculture | Irrigation Systems | Efficient water delivery and crop yield improvement | UV resistance, flexibility, and size options |
Oil and Gas | Natural Gas Distribution | Safe and reliable transportation of gas | Compliance with safety standards and pressure ratings |
Food and Beverage | Beverage Dispensing Systems | Hygiene and safety in food transfer | FDA approval, odorless and tasteless materials |
Construction | Water Supply Lines | Durable and long-lasting infrastructure | Resistance to chemicals and environmental factors |
Hydroponics | Nutrient Delivery Systems | Enhanced growth rates and resource efficiency | Compatibility with various nutrient solutions |
How is Polyethene Tubing Used in Agriculture?
In the agricultural sector, polyethene tubing is extensively employed in irrigation systems. It facilitates efficient water delivery directly to the root zones of crops, which is crucial for maximizing yields, especially in regions with scarce water resources. The tubing’s UV resistance and flexibility make it suitable for various terrains and climates, particularly in Africa and South America where irrigation is vital for food production. Buyers should consider the tubing’s durability and resistance to environmental factors when sourcing.
What Role Does Polyethene Tubing Play in Oil and Gas?
In the oil and gas industry, polyethene tubing is used for the safe and reliable distribution of natural gas. Its lightweight nature and resistance to corrosion make it an ideal choice for underground installations, minimizing the risk of leaks and ensuring compliance with safety regulations. For international buyers, especially from the Middle East, understanding the applicable safety standards and pressure ratings is essential when sourcing polyethene tubing for gas distribution.
How is Polyethene Tubing Essential in Food and Beverage?
Polyethene tubing is critical in the food and beverage industry, particularly for beverage dispensing systems. Its FDA-approved, odorless, and tasteless properties ensure that the integrity of the products is maintained during transfer. This is particularly important for businesses in Europe that prioritize hygiene and safety standards. When sourcing, buyers should verify the tubing’s certifications and material specifications to ensure compliance with local regulations.
Why is Polyethene Tubing Used in Construction?
In construction, polyethene tubing is widely utilized for water supply lines due to its durability and long-lasting nature. It can withstand harsh environmental conditions and is resistant to various chemicals, making it suitable for diverse applications. For B2B buyers in Europe and Africa, sourcing polyethene tubing requires attention to the tubing’s resistance to environmental factors and its compatibility with other construction materials to ensure a reliable water supply infrastructure.
How Does Polyethene Tubing Benefit Hydroponics?
In hydroponics, polyethene tubing is essential for nutrient delivery systems, allowing for efficient water and nutrient distribution to plants. This method enhances growth rates and optimizes resource use, making it an attractive option for agricultural businesses looking to innovate. Buyers from South America and Africa should focus on sourcing tubing that is compatible with different nutrient solutions and has a proven track record in hydroponic applications, ensuring optimal plant health and productivity.
3 Common User Pain Points for ‘polyethene tubing’ & Their Solutions
Scenario 1: Inconsistent Quality of Polyethylene Tubing
The Problem:
International B2B buyers often encounter challenges with the quality of polyethylene tubing, particularly when sourcing from different suppliers across regions like Africa, South America, and the Middle East. Variability in manufacturing standards can lead to tubing that does not meet the required specifications, resulting in leaks, premature wear, and costly downtime in operations. Buyers may feel frustrated as they attempt to balance cost and quality, leading to doubts about the integrity of their supply chain.
The Solution:
To mitigate quality issues, buyers should establish a robust supplier evaluation process. This includes requesting certifications such as ISO 9001 for quality management systems and compliance with relevant local standards. Engage in regular audits of supplier facilities, focusing on their production processes and quality control measures. Additionally, consider sourcing polyethylene tubing from suppliers with a strong reputation and positive customer feedback. Implementing a sampling strategy, where a small batch is tested for performance before full-scale orders, can also ensure that the product meets your quality standards.
Scenario 2: Challenges with Sizing and Compatibility
The Problem:
Another common pain point for B2B buyers is the confusion surrounding the sizing and compatibility of polyethylene tubing with existing systems. Incorrect sizing can lead to installation issues, resulting in leaks or inefficiencies in fluid transfer. This problem is particularly prevalent in industries such as agriculture and construction, where precise measurements are critical. Buyers may find themselves stuck with incompatible products, leading to delays and increased costs.
The Solution:
Buyers should invest time in understanding the specific requirements of their applications, including pressure ratings, temperature tolerances, and the types of fluids being transported. Utilizing tools such as online calculators can help determine the correct tubing diameter and wall thickness. It’s advisable to create a detailed specification sheet that outlines these requirements when sourcing polyethylene tubing. Collaborate with suppliers who offer customization options, ensuring that the product is tailored to fit seamlessly with your existing systems. Additionally, engaging in dialogue with suppliers can provide insights into the best practices for installation and maintenance.
Scenario 3: Environmental and Regulatory Compliance
The Problem:
With increasing environmental regulations and a growing emphasis on sustainability, B2B buyers are often faced with the challenge of ensuring that their polyethylene tubing complies with local and international standards. This is particularly critical in industries like food and beverage, where the tubing must meet stringent health and safety regulations. Buyers may experience anxiety over the risk of non-compliance, which could lead to penalties and damage to their reputation.
The Solution:
To navigate environmental and regulatory compliance, B2B buyers should prioritize sourcing polyethylene tubing that is certified for specific applications, such as FDA-approved materials for food and beverage use. Familiarize yourself with the regulations applicable to your industry, and maintain an updated list of compliance requirements. When evaluating suppliers, inquire about their adherence to standards such as RoHS and REACH, which address hazardous substances. Consider developing a partnership with suppliers who proactively provide documentation and support regarding compliance. This not only streamlines the procurement process but also enhances your organization’s credibility in the market.
Strategic Material Selection Guide for polyethene tubing
What Are the Key Properties of Different Polyethylene Tubing Materials?
When selecting polyethylene tubing for international B2B applications, understanding the specific properties of different materials is crucial. The most common types of polyethylene tubing include Low-Density Polyethylene (LDPE), High-Density Polyethylene (HDPE), Linear Low-Density Polyethylene (LLDPE), and Cross-Linked Polyethylene (PEX). Each material offers unique characteristics that can significantly impact performance, durability, and suitability for various applications.
Low-Density Polyethylene (LDPE)
Key Properties: LDPE is known for its flexibility and low-density structure, which allows it to withstand low-temperature applications. It typically has a temperature rating of -50°C to 60°C and offers moderate pressure resistance.
Pros & Cons: The primary advantage of LDPE is its excellent flexibility and ease of processing, making it suitable for applications requiring bending and shaping. However, its lower tensile strength compared to HDPE can limit its use in high-pressure applications. Additionally, LDPE is less resistant to environmental stress cracking.
Impact on Application: LDPE is ideal for applications involving non-potable water, air, and gas transfer. However, it is not recommended for high-pressure systems due to its lower durability.
Considerations for International Buyers: Buyers should ensure compliance with local standards such as ASTM D1248 or DIN 73378. LDPE is widely accepted in various regions, including Europe and Africa, but may face scrutiny in food-grade applications.
High-Density Polyethylene (HDPE)
Key Properties: HDPE boasts a higher density, providing superior strength and impact resistance. It can typically handle temperatures up to 80°C and is highly resistant to chemicals and corrosion.
Pros & Cons: The key advantage of HDPE is its durability and long lifespan, making it suitable for high-pressure applications. However, its rigidity can be a disadvantage in applications requiring flexibility. Additionally, HDPE can be more expensive than LDPE.
Impact on Application: HDPE is often used in potable water systems, gas distribution, and industrial applications due to its chemical resistance and strength. It is particularly suitable for harsh environments.
Considerations for International Buyers: Compliance with standards like ASTM D3035 and ISO 4427 is essential. HDPE is favored in Europe and the Middle East, where stringent regulations on potable water systems exist.
Linear Low-Density Polyethylene (LLDPE)
Key Properties: LLDPE combines the properties of LDPE and HDPE, offering enhanced flexibility and tensile strength. It has a temperature range of -60°C to 80°C and excellent puncture resistance.
Pros & Cons: LLDPE’s flexibility and strength make it suitable for a wide range of applications. However, it may not be as readily available as LDPE or HDPE, potentially complicating sourcing for international buyers.
Impact on Application: LLDPE is ideal for applications involving food and beverage transfer, as it is FDA-approved for such uses. Its resistance to environmental stress cracking makes it suitable for various industrial applications.
Considerations for International Buyers: Buyers should verify compliance with FDA regulations for food-grade applications. LLDPE is increasingly popular in South America and Africa, where food safety standards are evolving.
Cross-Linked Polyethylene (PEX)
Key Properties: PEX is a flexible tubing material known for its high resistance to temperature and pressure, with a typical operating temperature of up to 95°C. It is also resistant to chemical degradation.
Pros & Cons: The flexibility of PEX allows for easy installation and fewer fittings, reducing potential leak points. However, its higher cost and the need for specialized fittings can be a limitation for some buyers.
Impact on Application: PEX is commonly used in plumbing and heating systems, particularly in residential applications. Its resistance to freezing makes it suitable for colder climates.
Considerations for International Buyers: Compliance with standards such as ASTM F876 is crucial. PEX is gaining acceptance in Europe and North America but may face regulatory challenges in some African and South American markets.
Summary Table of Polyethylene Tubing Materials
Material | Typical Use Case for Polyethylene Tubing | Key Advantage | Key Disadvantage/Limitation | Relative Cost (Low/Med/High) |
---|---|---|---|---|
Low-Density Polyethylene (LDPE) | Non-potable water, air, gas transfer | Excellent flexibility | Lower tensile strength | Low |
High-Density Polyethylene (HDPE) | Potable water systems, gas distribution | Superior strength and durability | Less flexible | Medium |
Linear Low-Density Polyethylene (LLDPE) | Food and beverage transfer | Enhanced flexibility and strength | Limited availability | Medium |
Cross-Linked Polyethylene (PEX) | Plumbing and heating systems | High temperature and pressure resistance | Higher cost and specialized fittings | High |
This strategic material selection guide serves as a valuable resource for international B2B buyers, helping them make informed decisions based on the specific requirements of their applications.
In-depth Look: Manufacturing Processes and Quality Assurance for polyethene tubing
What Are the Main Stages of Polyethylene Tubing Manufacturing?
The manufacturing of polyethylene tubing involves several key stages that ensure the final product meets industry standards and customer specifications. Understanding these processes is crucial for B2B buyers seeking reliable suppliers.
1. Material Preparation
The first stage in the manufacturing process is the preparation of polyethylene resin. Manufacturers typically use either Low-Density Polyethylene (LDPE) or High-Density Polyethylene (HDPE) depending on the desired characteristics of the tubing. The resin is sourced from reputable suppliers to ensure quality. It is then mixed with additives that can enhance properties like UV resistance, color, and flexibility. This mixture is then pelletized for easier handling.
2. Forming
In the forming stage, the prepared resin pellets are fed into an extruder. The extruder melts the pellets and forces the molten polyethylene through a die, shaping it into a continuous tube. The diameter and wall thickness can be adjusted by changing the die size and the extrusion speed. This process can be tailored to meet specific customer requirements, such as custom lengths and diameters.
3. Cooling and Finishing
Once extruded, the tubing is cooled using water baths or air cooling systems. This solidifies the shape and ensures dimensional accuracy. After cooling, the tubing undergoes a finishing process, which may include cutting to specified lengths, printing for branding, or additional treatments to enhance performance characteristics. This step is crucial for ensuring that the product is ready for its intended application, whether it be for fluid transfer, gas supply, or agricultural use.
4. Quality Control Checks
Quality control (QC) is integrated throughout the manufacturing process to ensure that the polyethylene tubing meets both international and industry-specific standards. This includes inspections at various checkpoints: Incoming Quality Control (IQC) for raw materials, In-Process Quality Control (IPQC) during manufacturing, and Final Quality Control (FQC) before shipment.
How Is Quality Assurance Managed in Polyethylene Tubing Production?
Quality assurance is a fundamental aspect of polyethylene tubing production, as it directly impacts product performance and safety. B2B buyers should be aware of the relevant international standards and specific QC practices employed by manufacturers.
International and Industry-Specific Standards
Manufacturers often adhere to international standards such as ISO 9001, which outlines requirements for a quality management system. Additionally, industry-specific standards may include:
- CE Marking: Indicates compliance with European health, safety, and environmental protection standards.
- API Standards: Relevant for manufacturers producing tubing for the oil and gas sector, ensuring products can withstand high pressures and harsh environments.
These standards help ensure that the products are safe and reliable for use in various applications.
What QC Checkpoints Are Commonly Used?
Quality control involves several critical checkpoints during the manufacturing process:
- Incoming Quality Control (IQC): Raw materials are inspected for quality before production begins. This includes testing for material consistency and verifying supplier certifications.
- In-Process Quality Control (IPQC): Continuous monitoring during the extrusion process helps identify any deviations from quality standards. This includes checks for wall thickness, diameter, and physical properties.
- Final Quality Control (FQC): The finished product undergoes rigorous testing, which may include pressure tests, burst tests, and flexibility assessments. Documentation of these tests is essential for B2B buyers.
What Testing Methods Are Utilized for Polyethylene Tubing?
B2B buyers should understand the various testing methods that manufacturers use to ensure product quality and compliance with standards:
- Burst Pressure Testing: Measures the maximum pressure the tubing can withstand before failure.
- Tensile Testing: Assesses the strength and elasticity of the tubing material.
- Chemical Resistance Testing: Ensures that the tubing can withstand exposure to various chemicals without degrading.
- Environmental Stress Crack Resistance (ESCR) Testing: Evaluates the tubing’s durability under environmental stress, which is particularly relevant for applications in harsh conditions.
How Can B2B Buyers Verify Supplier Quality Control?
To ensure that suppliers maintain high-quality standards, B2B buyers can implement several strategies:
- Supplier Audits: Conducting on-site audits can provide insights into a manufacturer’s processes and adherence to quality standards.
- Reviewing Quality Reports: Requesting detailed quality reports that document testing methods, results, and compliance with international standards can help verify supplier claims.
- Third-Party Inspections: Engaging independent inspection agencies can provide unbiased assessments of product quality and manufacturing practices.
What Are the QC and Certification Nuances for International Buyers?
B2B buyers from Africa, South America, the Middle East, and Europe must navigate various certification and quality nuances when sourcing polyethylene tubing:
- Regulatory Compliance: Different regions may have unique regulations governing the use of polyethylene tubing, especially for food-grade applications. Buyers should ensure that the supplier’s products meet local regulatory requirements.
- Cultural and Market Differences: Understanding regional market expectations and cultural nuances can help in selecting suppliers that align with specific needs. For example, European buyers may prioritize eco-friendly certifications, while buyers in Africa may focus on cost-effectiveness.
- Documentation and Traceability: Ensure that suppliers provide clear documentation for all materials used, including certificates of compliance and material safety data sheets (MSDS). This is particularly important for industries with stringent regulatory requirements.
By comprehensively understanding the manufacturing processes and quality assurance measures, international B2B buyers can make informed decisions when sourcing polyethylene tubing, ensuring they receive reliable products that meet their specific needs.
Practical Sourcing Guide: A Step-by-Step Checklist for ‘polyethene tubing’
To assist B2B buyers in sourcing polyethylene tubing effectively, this guide outlines critical steps to ensure a smooth procurement process. By following these actionable steps, buyers can make informed decisions, leading to successful partnerships and quality product acquisition.
Step 1: Define Your Technical Specifications
Understanding the specific requirements of your project is crucial. Start by determining the type of polyethylene tubing needed, such as low-density polyethylene (LDPE) or high-density polyethylene (HDPE), and the intended application—be it for potable water, gas transfer, or food and beverage use. This clarity helps streamline the sourcing process and ensures compatibility with your operational needs.
Step 2: Research and Identify Reliable Suppliers
Conduct thorough research to identify potential suppliers that specialize in polyethylene tubing. Look for manufacturers with a proven track record in your industry and region. Utilize online directories, trade shows, and industry forums to gather a list of candidates. Check their reputation through reviews and testimonials, ensuring they have experience with the specific type of tubing you require.
Step 3: Evaluate Supplier Certifications and Compliance
Before making a commitment, it’s essential to verify that your selected suppliers meet relevant industry standards and certifications. Check for compliance with regulations such as FDA approval for food-grade tubing or ISO certifications for quality management. This step protects your business from potential legal issues and ensures that the products meet safety and quality standards.
Step 4: Request Samples for Quality Assessment
Once you have shortlisted suppliers, request samples of the polyethylene tubing to evaluate their quality firsthand. Assess the material’s flexibility, strength, and resistance to environmental factors pertinent to your application. This practical evaluation allows you to make an informed decision based on the actual performance of the products.
Step 5: Compare Pricing and Terms of Sale
Gather quotes from multiple suppliers and compare them not only on price but also on terms of sale, including payment options, minimum order quantities, and delivery timelines. Consider the total cost of ownership, including shipping and potential customs fees for international orders. This comprehensive comparison ensures you get the best value without compromising on quality.
Step 6: Establish Communication and Support Channels
Effective communication is vital in any business relationship. Ensure that your chosen supplier offers reliable support, including customer service and technical assistance. Establish clear communication channels for inquiries and support during the procurement and post-purchase phases. A supplier with strong support can significantly enhance your operational efficiency.
Step 7: Finalize Contracts and Place Orders
After selecting the supplier that best meets your needs, finalize the contracts with clear terms and conditions. Ensure all aspects, such as delivery schedules, payment terms, and warranties, are documented. Placing the order should be straightforward, but having everything in writing protects both parties and sets clear expectations moving forward.
By following this structured sourcing guide, B2B buyers can confidently navigate the procurement of polyethylene tubing, ensuring they make informed choices that align with their operational requirements and business goals.
Comprehensive Cost and Pricing Analysis for polyethene tubing Sourcing
What Are the Key Cost Components in Polyethylene Tubing Sourcing?
When sourcing polyethylene tubing, international B2B buyers must understand the multifaceted cost structure involved. The main components include:
-
Materials: The primary material, typically low-density polyethylene (LDPE) or high-density polyethylene (HDPE), significantly impacts pricing. Prices can fluctuate based on market demand, crude oil prices, and the specific grade of polyethylene required.
-
Labor: Labor costs vary by region and can influence the overall pricing. Countries with higher wage standards may incur increased manufacturing costs, which can be passed on to the buyer.
-
Manufacturing Overhead: This includes costs associated with running production facilities, including utilities, maintenance, and factory management. Efficient manufacturing processes can help minimize these costs.
-
Tooling: Tooling costs pertain to the initial investment in machinery and molds necessary for production. Custom tooling can raise costs, especially for unique specifications or lower volume orders.
-
Quality Control (QC): Ensuring product quality through rigorous testing and compliance with industry standards is essential. The costs associated with QC can vary based on the certifications required, such as FDA approval for food-grade applications.
-
Logistics: Transportation and shipping costs are crucial in international trade. Factors such as shipping distance, mode of transport (air vs. sea), and local tariffs can add significant costs.
-
Margin: Suppliers typically add a margin to cover risks and ensure profitability. Understanding the supplier’s margin expectations can aid in negotiation.
How Do Price Influencers Affect Polyethylene Tubing Costs?
Several factors can influence the pricing of polyethylene tubing:
-
Volume/MOQ (Minimum Order Quantity): Larger orders often qualify for bulk discounts, significantly lowering the cost per unit. Buyers should assess their needs to determine optimal order sizes.
-
Specifications and Customization: Custom dimensions, colors, or materials can increase costs. Providing detailed specifications upfront can help suppliers offer accurate quotes.
-
Material Quality and Certifications: High-quality materials or those that meet stringent certifications (like ISO or FDA) may come at a premium. Buyers should weigh the benefits of quality against the costs.
-
Supplier Factors: The supplier’s reputation, reliability, and production capabilities can impact pricing. Established suppliers may charge more due to their proven track record.
-
Incoterms: Understanding the chosen Incoterm (e.g., FOB, CIF) is essential as it delineates responsibility for shipping costs and risks. This can affect the total landed cost of the product.
What Are Effective Buyer Tips for Negotiating Prices?
International B2B buyers, particularly from regions such as Africa, South America, the Middle East, and Europe, should consider the following strategies:
-
Negotiate Terms: Always negotiate payment terms, delivery schedules, and pricing. Flexibility on both sides can lead to better deals.
-
Focus on Cost-Efficiency: Evaluate the total cost of ownership (TCO), which includes not just purchase price but also costs related to maintenance, operational efficiency, and potential waste.
-
Understand Pricing Nuances: Different regions may have varying pricing structures due to local economic conditions, tariffs, and market demand. Researching these nuances can provide leverage in negotiations.
-
Build Relationships: Establishing strong relationships with suppliers can lead to better pricing and terms over time. Trust and loyalty often translate into financial benefits.
-
Request for Quotes (RFQs): Sending RFQs to multiple suppliers can provide a benchmark for pricing and help identify competitive offers.
Disclaimer on Indicative Prices
Prices for polyethylene tubing can vary widely based on specifications, market conditions, and supplier factors. It is advisable for buyers to conduct thorough market research and obtain multiple quotes to ensure they are getting the best deal tailored to their specific needs.
Alternatives Analysis: Comparing polyethene tubing With Other Solutions
Understanding Alternative Solutions to Polyethylene Tubing
When considering the best solutions for fluid transfer and gas distribution, it’s essential to analyze alternatives to polyethylene tubing. While polyethylene (PE) tubing is well-regarded for its flexibility, durability, and resistance to corrosion, other options may offer specific advantages depending on the application. This section will compare polyethylene tubing against two viable alternatives: PVC tubing and rubber hoses, providing international B2B buyers with actionable insights.
Comparison of Polyethylene Tubing with Alternative Solutions
Comparison Aspect | Polyethylene Tubing | PVC Tubing | Rubber Hoses |
---|---|---|---|
Performance | High flexibility, corrosion-resistant, FDA-approved for food use | Good chemical resistance, less flexible than PE | Excellent flexibility and temperature resistance |
Cost | Moderate cost, competitive pricing for bulk orders | Generally lower cost than PE | Higher cost due to material and manufacturing |
Ease of Implementation | Simple installation with various fittings available | Easy to cut and join, but requires solvent for connections | Requires specific fittings and may need clamps |
Maintenance | Low maintenance; UV resistant options available | Low maintenance, but can become brittle over time | Moderate maintenance; check for wear and tear regularly |
Best Use Case | Fluid transfer in agricultural, industrial, and food applications | Ideal for drainage, waste, and vent piping | High-pressure applications and areas requiring flexibility |
Detailed Breakdown of Alternatives
What are the Benefits and Drawbacks of PVC Tubing?
PVC (Polyvinyl Chloride) tubing is a popular alternative due to its affordability and good chemical resistance. It is commonly used in applications such as drainage and venting systems. PVC tubing is easier to install because it can be cut to length and joined with solvent adhesives. However, it is less flexible than polyethylene and can become brittle over time, particularly when exposed to UV light or extreme temperatures. This brittleness can lead to cracks and leaks, potentially increasing maintenance costs in the long run.
How Does Rubber Hose Compare to Polyethylene Tubing?
Rubber hoses are known for their excellent flexibility and temperature resistance, making them suitable for high-pressure applications in industries such as automotive and manufacturing. They can handle a wide range of temperatures and pressures, making them versatile in various environments. However, rubber hoses tend to be more expensive due to the material and production processes involved. Additionally, they require more maintenance, as users need to regularly inspect for wear, especially in high-stress applications.
How Can B2B Buyers Choose the Right Solution?
Selecting the right tubing solution hinges on your specific application requirements. Buyers should consider factors such as the type of fluids being transported, environmental conditions, budget constraints, and installation capabilities. For applications requiring high flexibility and resistance to UV exposure, polyethylene tubing may be the best option. Conversely, for cost-sensitive projects where chemical resistance is paramount, PVC could be more suitable. Rubber hoses excel in high-pressure environments but come at a premium and require regular maintenance.
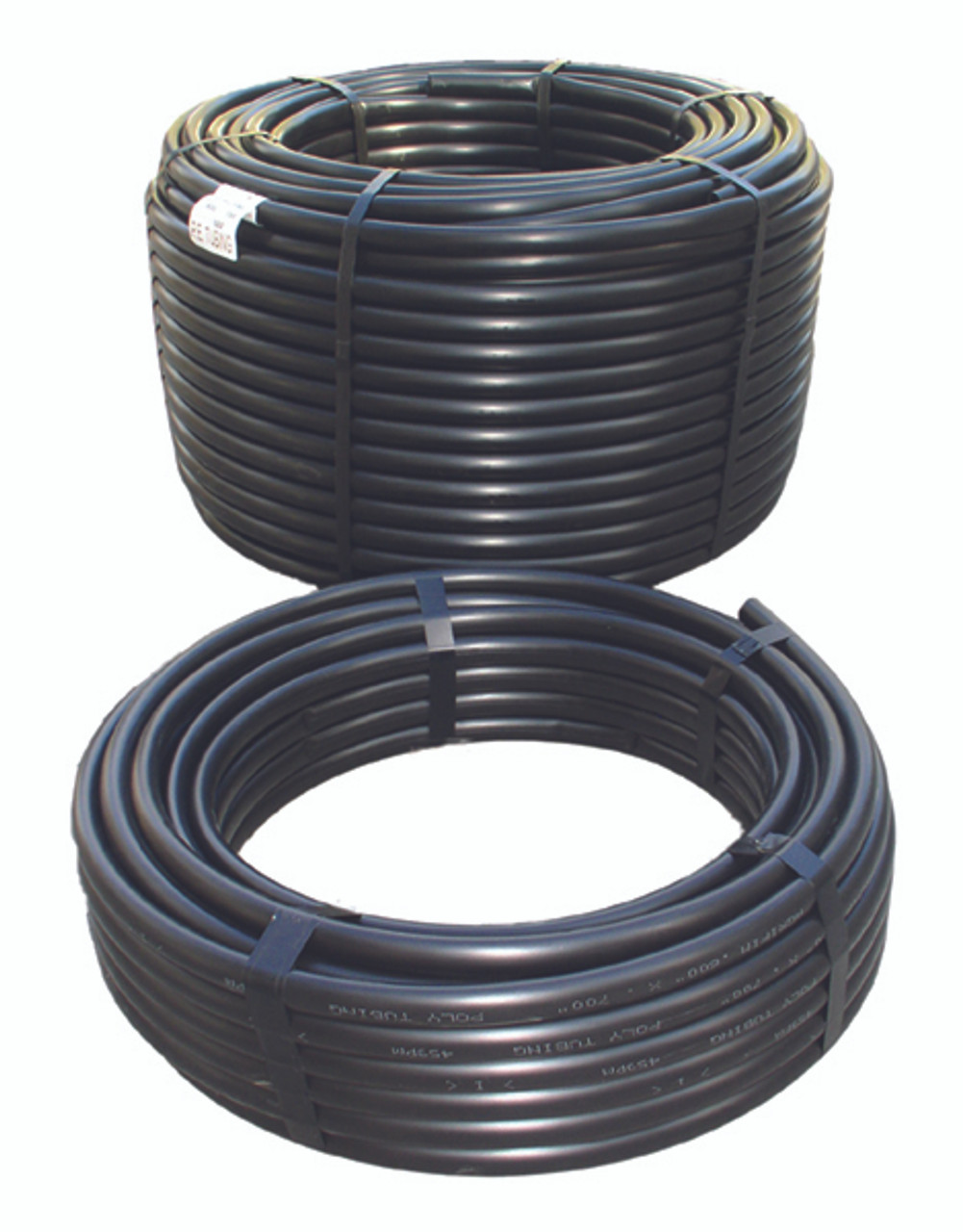
A stock image related to polyethene tubing.
In conclusion, understanding the strengths and weaknesses of polyethylene tubing compared to its alternatives enables B2B buyers to make informed decisions tailored to their operational needs.
Essential Technical Properties and Trade Terminology for polyethene tubing
What Are the Key Technical Properties of Polyethylene Tubing?
Understanding the technical properties of polyethylene tubing is essential for international B2B buyers, especially those sourcing from regions such as Africa, South America, the Middle East, and Europe. Here are some critical specifications to consider:
1. Material Grade: What Types of Polyethylene Are Available?
Polyethylene tubing is categorized mainly into Low-Density Polyethylene (LDPE) and High-Density Polyethylene (HDPE). LDPE is known for its flexibility and impact resistance, making it suitable for applications requiring bending. HDPE, on the other hand, offers higher tensile strength and is more resistant to chemicals, making it ideal for transporting hazardous materials. Selecting the right material grade is crucial for ensuring the tubing meets the operational demands of specific applications.
2. Tolerance: Why Is It Important?
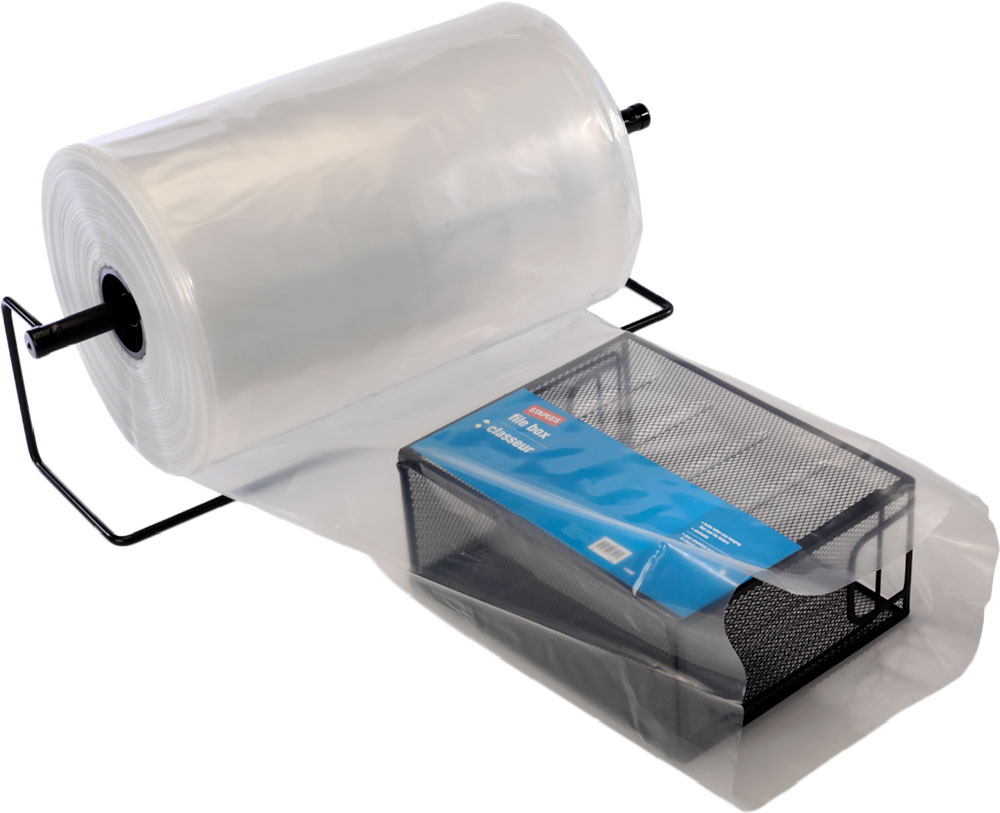
A stock image related to polyethene tubing.
Tolerance refers to the allowable deviation from a specified dimension. In the case of polyethylene tubing, maintaining a tight tolerance is vital for ensuring compatibility with fittings and connectors. A high tolerance level minimizes the risk of leaks and ensures efficient fluid transfer. For B2B buyers, understanding tolerance specifications can prevent costly mistakes in assembly and installation.
3. Pressure Rating: How Does It Affect Application?
Pressure rating indicates the maximum pressure the tubing can handle without bursting. This is critical for applications involving gas and liquid transport. Tubing with a higher pressure rating is essential for industrial uses, such as oil and gas pipelines. Buyers must assess the pressure requirements of their specific applications to select appropriately rated polyethylene tubing.
4. Chemical Resistance: What Should You Consider?
Chemical resistance is the ability of polyethylene tubing to withstand corrosive substances without degrading. This property is particularly significant for buyers in industries like agriculture and pharmaceuticals, where exposure to chemicals is common. Knowing the chemical compatibility of the tubing with the intended materials can prevent premature failure and ensure long-term reliability.
5. UV Resistance: Why Is It Necessary for Outdoor Applications?
For applications exposed to sunlight, UV resistance is an essential property of polyethylene tubing. UV degradation can weaken the tubing over time, leading to failure. Buyers should look for polyethylene tubing that incorporates UV stabilizers if the application is outdoors, ensuring durability and longevity.
What Are Common Trade Terms Associated with Polyethylene Tubing?
Familiarity with trade terminology helps streamline communication and negotiations in the B2B space. Here are some essential terms to know:
1. OEM (Original Equipment Manufacturer): What Does It Mean?
OEM refers to companies that produce parts or equipment that may be marketed by another manufacturer. In the context of polyethylene tubing, knowing whether a supplier is an OEM can help buyers understand product quality and reliability. OEM products often adhere to higher standards and specifications.
2. MOQ (Minimum Order Quantity): Why Is It Relevant?
MOQ is the minimum number of units a supplier is willing to sell. For international buyers, understanding the MOQ is crucial for budgeting and planning inventory. It can also affect shipping costs and lead times, making it an important consideration in procurement strategies.
3. RFQ (Request for Quotation): How Does It Work?
An RFQ is a document that a buyer sends to suppliers asking for pricing on specific products. In the polyethylene tubing market, issuing an RFQ can help buyers compare prices, terms, and product specifications from multiple suppliers, ensuring they make informed purchasing decisions.
4. Incoterms: What Are They and Why Are They Important?
Incoterms (International Commercial Terms) define the responsibilities of buyers and sellers in international transactions. They clarify who is responsible for shipping, insurance, and tariffs, which is particularly important for B2B buyers involved in cross-border procurement of polyethylene tubing. Familiarity with Incoterms can help avoid disputes and ensure smooth transactions.
5. ASTM Standards: What Do They Indicate?
ASTM (American Society for Testing and Materials) standards provide guidelines for the quality and performance of materials, including polyethylene tubing. Understanding these standards is essential for buyers to ensure that the products they procure meet industry requirements and safety regulations.
By grasping these essential technical properties and trade terminologies, international B2B buyers can make informed decisions, ensuring they select the right polyethylene tubing for their specific needs.
Navigating Market Dynamics and Sourcing Trends in the polyethene tubing Sector
What Are the Current Market Dynamics and Key Trends in the Polyethene Tubing Sector?
The global polyethylene tubing market is experiencing robust growth driven by various factors, including increasing demand for flexible packaging, advancements in manufacturing technology, and the rising need for efficient fluid transfer solutions across multiple industries. In regions such as Africa, South America, the Middle East, and Europe, the growing agricultural sector significantly influences the demand for polyethylene tubing, especially in irrigation and hydroponics applications. Additionally, the construction and plumbing sectors are also contributing to this growth, fueled by urbanization and infrastructure development projects.
Emerging technologies, such as smart manufacturing and automation, are reshaping the sourcing landscape for B2B buyers. Companies are increasingly adopting digital platforms for procurement, which enhances transparency and improves supply chain efficiency. Furthermore, the trend towards customization in polyethylene tubing—tailoring products to meet specific industry needs—offers buyers the opportunity to optimize their operations and reduce waste.
Another noteworthy trend is the shift towards lightweight and high-performance materials, such as linear low-density polyethylene (LLDPE), which provides superior flexibility and strength compared to traditional options. International buyers must stay informed about these trends to make strategic purchasing decisions that align with market demands.
How Does Sustainability Impact Sourcing Trends in the Polyethene Tubing Sector?
Sustainability has become a critical consideration for B2B buyers in the polyethylene tubing sector. With increasing scrutiny on environmental impacts, companies are prioritizing ethical sourcing and sustainable practices. The production of polyethylene tubing often involves significant energy consumption and the release of greenhouse gases, prompting the need for greener alternatives.
Buyers are encouraged to seek suppliers that utilize recycled materials or implement eco-friendly manufacturing processes. Certifications such as ISO 14001 (Environmental Management) and the use of bio-based polyethylene can indicate a supplier’s commitment to sustainability. Additionally, many manufacturers are now offering products that are free from harmful substances, such as phthalates and BPA, catering to the growing demand for safe and environmentally responsible materials.
Investing in sustainable sourcing not only enhances a company’s brand image but also contributes to long-term cost savings through improved resource efficiency. B2B buyers should engage with suppliers that demonstrate transparency in their supply chains and offer ‘green’ certifications to ensure compliance with both local and international environmental regulations.
What Is the Historical Context Behind Polyethene Tubing?
The evolution of polyethylene tubing dates back to the mid-20th century when polyethylene was first synthesized. Initially, it found applications primarily in packaging and insulation. Over the decades, the material’s versatility and cost-effectiveness led to its widespread adoption across various sectors, including agriculture, construction, and healthcare.
The introduction of advanced manufacturing techniques in the late 20th century further enhanced the quality and performance of polyethylene tubing, allowing for innovations such as reinforced and multi-layered tubing. Today, polyethylene tubing is recognized for its flexibility, durability, and resistance to corrosion, making it a preferred choice for fluid transfer applications in numerous industries.
Understanding this historical context enables international B2B buyers to appreciate the material’s evolution and the technological advancements that have shaped its current applications, ultimately guiding more informed sourcing decisions.
Frequently Asked Questions (FAQs) for B2B Buyers of polyethene tubing
-
How do I choose the right polyethylene tubing for my application?
Choosing the right polyethylene tubing involves assessing the specific requirements of your application. Consider factors such as the type of fluid or gas being transported, temperature range, and pressure conditions. For instance, if you’re working with food and beverage applications, opt for FDA-approved food-grade polyethylene. Additionally, evaluate the tubing’s flexibility, chemical resistance, and whether you need features like UV stabilization or color coding for identification. -
What is the best type of polyethylene tubing for agricultural use?
For agricultural applications, low-density polyethylene (LDPE) tubing is often preferred due to its flexibility and resistance to environmental stress. It is suitable for irrigation systems and can handle various chemicals used in farming. Linear low-density polyethylene (LLDPE) is also a great option for its enhanced tensile strength and puncture resistance, making it ideal for more demanding applications. -
What are the key quality assurance measures to consider when sourcing polyethylene tubing?
When sourcing polyethylene tubing, ensure that your suppliers adhere to recognized quality assurance standards such as ISO 9001. Look for certifications that demonstrate compliance with industry regulations, including FDA approval for food-grade applications. Additionally, request samples to evaluate the material’s properties, and inquire about the supplier’s testing processes for durability, flexibility, and resistance to chemicals. -
How can I verify the reliability of a polyethylene tubing supplier?
To verify a polyethylene tubing supplier’s reliability, conduct thorough research on their business history and reputation. Look for client testimonials and case studies that showcase their experience in your industry. Additionally, check if they have relevant certifications and affiliations with trade organizations. Engaging in direct communication about your needs and their capabilities can also provide insights into their responsiveness and customer service. -
What customization options are typically available for polyethylene tubing?
Most suppliers offer various customization options for polyethylene tubing, including size, color, and thickness. Some suppliers can also provide tubing with specific additives for UV protection or anti-static properties. If you have unique application requirements, discuss them with your supplier to explore tailor-made solutions that meet your needs, such as custom lengths or specialized fittings. -
What minimum order quantities (MOQ) should I expect when purchasing polyethylene tubing?
Minimum order quantities for polyethylene tubing can vary widely among suppliers. Typically, MOQs range from 100 meters to several kilometers, depending on the product type and the supplier’s production capabilities. If you are a smaller business or testing a new application, consider negotiating with suppliers for smaller quantities or asking about trial orders to ensure the product meets your requirements before committing to larger purchases. -
What payment terms should I negotiate when sourcing polyethylene tubing internationally?
When sourcing internationally, standard payment terms include options like Letter of Credit (LC), advance payment, or net 30/60 days after delivery. It’s crucial to negotiate terms that align with your cash flow needs while ensuring the supplier’s confidence in your order. Consider using escrow services for large orders to protect both parties. Always confirm the currency of payment and whether there are any additional fees related to currency exchange or international transactions. -
What logistics considerations should I keep in mind when importing polyethylene tubing?
Logistics is critical when importing polyethylene tubing, particularly regarding shipping methods and timelines. Evaluate options such as air freight for faster delivery or sea freight for cost-effectiveness. Be aware of customs regulations in your country, as they can impact delivery times and costs. Additionally, consider the supplier’s ability to provide documentation for customs clearance, such as invoices, packing lists, and certificates of origin, to streamline the import process.
Important Disclaimer & Terms of Use
⚠️ Important Disclaimer
The information provided in this guide, including content regarding manufacturers, technical specifications, and market analysis, is for informational and educational purposes only. It does not constitute professional procurement advice, financial advice, or legal advice.
While we have made every effort to ensure the accuracy and timeliness of the information, we are not responsible for any errors, omissions, or outdated information. Market conditions, company details, and technical standards are subject to change.
B2B buyers must conduct their own independent and thorough due diligence before making any purchasing decisions. This includes contacting suppliers directly, verifying certifications, requesting samples, and seeking professional consultation. The risk of relying on any information in this guide is borne solely by the reader.
Strategic Sourcing Conclusion and Outlook for polyethene tubing
What Are the Key Takeaways for B2B Buyers in Polyethylene Tubing?
In conclusion, strategic sourcing of polyethylene tubing is essential for international B2B buyers looking to optimize their supply chain. The versatility of polyethylene tubing across various applications—from potable water systems to gas transportation—offers significant advantages, including durability, flexibility, and resistance to corrosion. Buyers should prioritize suppliers who provide a range of options, such as LLDPE and EVA-lined tubing, to meet specific industry needs.
How Can B2B Buyers Enhance Their Sourcing Strategies?
Investing time in understanding the unique demands of your regional market—whether in Africa, South America, the Middle East, or Europe—can lead to better supplier relationships and improved procurement outcomes. Consider leveraging local suppliers to reduce lead times and transportation costs, while also ensuring compliance with regional regulations.
What Is the Future Outlook for Polyethylene Tubing Procurement?
Looking ahead, the demand for polyethylene tubing is expected to rise due to growing sectors such as agriculture, water management, and renewable energy. As sustainability becomes a focal point, sourcing eco-friendly options will not only enhance your brand image but also align with global environmental standards. Engage with suppliers now to secure favorable terms and stay ahead of the competition in this dynamic market.