The Ultimate Guide to Polyurethane Roller (2025)
Introduction: Navigating the Global Market for polyurethane roller
In the ever-evolving landscape of industrial manufacturing, sourcing high-quality polyurethane rollers can pose significant challenges for international B2B buyers. With applications ranging from material handling to specialized machinery, the demand for durable and efficient rollers is on the rise. This comprehensive guide aims to equip buyers, especially those from Africa, South America, the Middle East, and Europe, with essential insights into the various types of polyurethane rollers available, their applications, and critical factors to consider when making a purchasing decision.
Throughout this guide, we will explore the diverse types of polyurethane rollers, including their unique properties that enhance performance in different industrial environments. We will also delve into the key applications of these rollers across multiple sectors, highlighting their versatility and effectiveness in improving operational efficiency. Furthermore, the guide will provide actionable strategies for vetting suppliers, understanding pricing structures, and ensuring quality assurance, enabling buyers to make informed choices tailored to their specific needs.
By addressing the complexities involved in sourcing polyurethane rollers, this guide empowers international B2B buyers to navigate the global market with confidence. Whether you are in South Africa seeking reliable suppliers or in Europe looking for innovative roller solutions, our goal is to help you streamline your procurement process and enhance your operational capabilities.
Understanding polyurethane roller Types and Variations
Type Name | Key Distinguishing Features | Primary B2B Applications | Brief Pros & Cons for Buyers |
---|---|---|---|
Standard Polyurethane Roller | Versatile design, good load capacity, high durability | Material handling, conveyor systems | Pros: Cost-effective, widely available. Cons: Limited customization options. |
Heavy-Duty Polyurethane Roller | High load capacity, reinforced core, abrasion-resistant | Industrial machinery, heavy equipment | Pros: Exceptional durability, supports heavy loads. Cons: Higher upfront cost. |
Polyurethane Coated Roller | Steel core with polyurethane coating for floor protection | Warehousing, logistics | Pros: Protects flooring, reduces noise. Cons: May wear faster on rough surfaces. |
Custom Polyurethane Roller | Tailored specifications for unique applications | Specialized machinery, custom equipment | Pros: Perfect fit for specific needs. Cons: Longer lead times and potentially higher costs. |
Temperature-Resistant Roller | Designed to withstand extreme temperatures | Food processing, chemical industries | Pros: Maintains performance in extreme conditions. Cons: Limited availability and higher price. |
What Are the Characteristics of Standard Polyurethane Rollers?
Standard polyurethane rollers are characterized by their versatility and robust design, making them suitable for a variety of applications. They typically feature a durable polyurethane coating over a steel core, which allows for good load capacities while protecting surfaces from damage. These rollers are ideal for material handling and conveyor systems, providing a cost-effective solution for many businesses. When considering a purchase, buyers should evaluate the roller’s load rating and compatibility with existing equipment.
How Do Heavy-Duty Polyurethane Rollers Differ?
Heavy-duty polyurethane rollers are designed for high-load applications and are reinforced to handle significant weight without compromising performance. Their abrasion-resistant properties make them ideal for use in industrial machinery and heavy equipment. Businesses looking for reliability in challenging environments will find these rollers advantageous. However, buyers should be prepared for a higher initial investment due to the advanced materials and construction methods used.
Why Choose Polyurethane Coated Rollers?
Polyurethane coated rollers offer a unique combination of durability and floor protection. The steel core is coated with a layer of polyurethane, which not only provides strength but also minimizes floor damage and noise during operation. These rollers are commonly used in warehousing and logistics settings. Buyers should consider the surface conditions of their operational environment, as these rollers may wear more quickly on rough surfaces.
What Are the Benefits of Custom Polyurethane Rollers?
Custom polyurethane rollers are tailored to meet specific operational requirements, making them ideal for specialized machinery and unique applications. These rollers can be designed with varying dimensions, load capacities, and materials to suit particular needs. While they provide a perfect fit, buyers should be aware that custom solutions often come with longer lead times and potentially higher costs. Assessing the urgency of need versus the benefits of customization is crucial for B2B buyers.
When to Use Temperature-Resistant Rollers?
Temperature-resistant polyurethane rollers are engineered to withstand extreme heat or cold, making them essential in food processing and chemical industries. Their ability to maintain performance under challenging conditions makes them a valuable asset in operations where temperature fluctuations are common. However, availability may be limited, and prices can be higher than standard rollers. Buyers should ensure that their chosen rollers meet the specific temperature requirements of their applications.
Key Industrial Applications of polyurethane roller
Industry/Sector | Specific Application of polyurethane roller | Value/Benefit for the Business | Key Sourcing Considerations for this Application |
---|---|---|---|
Manufacturing | Conveyor Systems | Enhanced load capacity and reduced floor damage | Durability, load capacity, and compatibility with existing systems |
Food Processing | Food Packaging Equipment | Hygiene compliance and minimal contamination risk | Food-grade materials, ease of cleaning, and temperature resistance |
Automotive | Assembly Line Machinery | Improved efficiency and reduced wear on components | Precision specifications and resistance to chemicals |
Logistics and Warehousing | Material Handling Equipment | Increased mobility and operational efficiency | Weight capacity, surface compatibility, and ease of installation |
Textile Industry | Textile Processing Machines | Smooth operation and reduced noise levels | Material resilience, abrasion resistance, and customization options |
How Are Polyurethane Rollers Used in Manufacturing Conveyor Systems?
In manufacturing, polyurethane rollers are integral to conveyor systems, facilitating the movement of materials and products across production lines. These rollers are designed to support heavy loads while minimizing floor damage, which is crucial in high-capacity environments. Buyers should consider the durability of the polyurethane material and the roller’s load capacity to ensure compatibility with their specific manufacturing processes, particularly in regions like South Africa and Brazil where industrial operations may vary in scale.
What Role Do Polyurethane Rollers Play in Food Processing Equipment?
In the food processing sector, polyurethane rollers are utilized in packaging equipment to ensure hygiene and efficiency. These rollers help in the smooth transfer of food products while preventing contamination, which is vital for compliance with health regulations. International buyers need to prioritize sourcing food-grade polyurethane that is easy to clean and can withstand temperature variations, especially in warmer climates found in parts of Africa and South America.
How Do Polyurethane Rollers Improve Automotive Assembly Lines?
Polyurethane rollers are pivotal in automotive assembly lines, where they support various machinery and ensure the seamless movement of components. Their durability and ability to reduce wear on machinery enhance operational efficiency, which can lead to lower maintenance costs. Automotive manufacturers in Europe and the Middle East should focus on precise specifications to match the unique requirements of their assembly processes, taking into account the roller’s resistance to automotive fluids.
Why Are Polyurethane Rollers Important in Logistics and Warehousing?
In logistics and warehousing, polyurethane rollers are used in material handling equipment such as pallet jacks and carts. They provide increased mobility and operational efficiency, allowing for the smooth transport of goods. Buyers in these sectors should consider the weight capacity and surface compatibility of the rollers to ensure they meet the demands of their specific applications, particularly in regions with varying infrastructure challenges.
How Are Polyurethane Rollers Beneficial in the Textile Industry?
In the textile industry, polyurethane rollers are employed in processing machines to facilitate the movement of fabrics. They are designed to operate quietly and smoothly, minimizing noise and vibration during production. Buyers in the textile sector should look for rollers that offer high abrasion resistance and customization options to meet the specific needs of their operations, especially in areas where textile manufacturing is a key economic driver.
3 Common User Pain Points for ‘polyurethane roller’ & Their Solutions
Scenario 1: Difficulty in Finding Durable Polyurethane Rollers for Heavy Loads
The Problem: Many B2B buyers, particularly in manufacturing and logistics sectors, face the challenge of sourcing polyurethane rollers that can withstand heavy loads without compromising performance. In regions like South Africa and the Middle East, where industrial equipment must endure harsh conditions, the risk of roller failure can lead to costly downtimes and safety hazards. Buyers often struggle with limited supplier options and the lack of clear specifications regarding load capacities, leading to frustration and potential losses.
The Solution: To overcome this issue, buyers should prioritize sourcing from reputable manufacturers who provide comprehensive technical specifications, including load ratings and material properties. When evaluating suppliers, consider those that offer a detailed breakdown of their polyurethane roller’s capabilities, including the type of steel core and the density of the polyurethane used. Additionally, buyers should inquire about the testing standards the rollers have undergone, ensuring they meet industry benchmarks. Collaborating with suppliers to customize roller dimensions and hardness can also enhance durability for specific applications. Establishing a close relationship with suppliers who understand regional challenges can further streamline sourcing processes.
Scenario 2: Short Lifespan of Polyurethane Rollers in Harsh Environments
The Problem: Buyers in industries such as construction and mining often find that polyurethane rollers wear out quickly when exposed to abrasive materials and extreme temperatures. For example, in regions of South America where heavy machinery operates in rugged terrains, the rollers may degrade faster than expected, resulting in frequent replacements and increased operational costs. This not only affects productivity but also strains maintenance budgets.
The Solution: To address this pain point, buyers should look for polyurethane rollers specifically designed for high abrasion resistance and temperature tolerance. It is essential to choose rollers that incorporate advanced formulations of polyurethane, which can enhance their resilience. Additionally, consider rollers with protective coatings that can minimize wear and tear from harsh environmental factors. Implementing a proactive maintenance schedule, which includes regular inspections and lubrication of the roller bearings, can significantly extend the lifespan of the rollers. Buyers should also explore suppliers who offer warranties or service agreements that ensure long-term support and durability of their products.
Scenario 3: Compatibility Issues with Existing Equipment
The Problem: Another common challenge faced by B2B buyers is the compatibility of polyurethane rollers with existing machinery. Many companies, especially in the Middle East and Europe, utilize a variety of equipment types, leading to confusion about which roller specifications will work with their systems. Misalignment can result in operational inefficiencies and additional costs incurred from retrofitting or modifying equipment.
The Solution: To mitigate compatibility issues, buyers should conduct a thorough assessment of their existing machinery and its specifications before sourcing polyurethane rollers. This includes measuring shaft sizes, roller diameters, and mounting configurations. Engaging with suppliers who provide detailed compatibility charts or technical support can streamline this process. Furthermore, buyers should consider suppliers that offer a range of customization options, allowing them to tailor the roller to fit their specific machinery needs. Conducting a trial run with a small batch of rollers can also be beneficial, providing insight into performance and fit before committing to a larger order. By ensuring that the selected rollers are compatible with existing equipment, buyers can enhance operational efficiency and reduce potential downtime.
Strategic Material Selection Guide for polyurethane roller
What Are the Key Materials Used in Polyurethane Rollers?
When selecting polyurethane rollers for various applications, understanding the materials that comprise these rollers is crucial for optimizing performance and ensuring compatibility with specific operational environments. Here, we analyze several common materials used in the production of polyurethane rollers, focusing on their properties, advantages, disadvantages, and implications for international B2B buyers.
How Does Polyurethane Affect Roller Performance?
Polyurethane is a widely used material for roller coatings due to its excellent mechanical properties. It offers high abrasion resistance, making it suitable for applications involving heavy loads and continuous movement. Polyurethane can withstand a temperature range from -30°F to 200°F (-34°C to 93°C) and provides good chemical resistance against oils, greases, and solvents. However, it may not perform well in extreme temperatures or in the presence of certain harsh chemicals, which could lead to degradation over time.
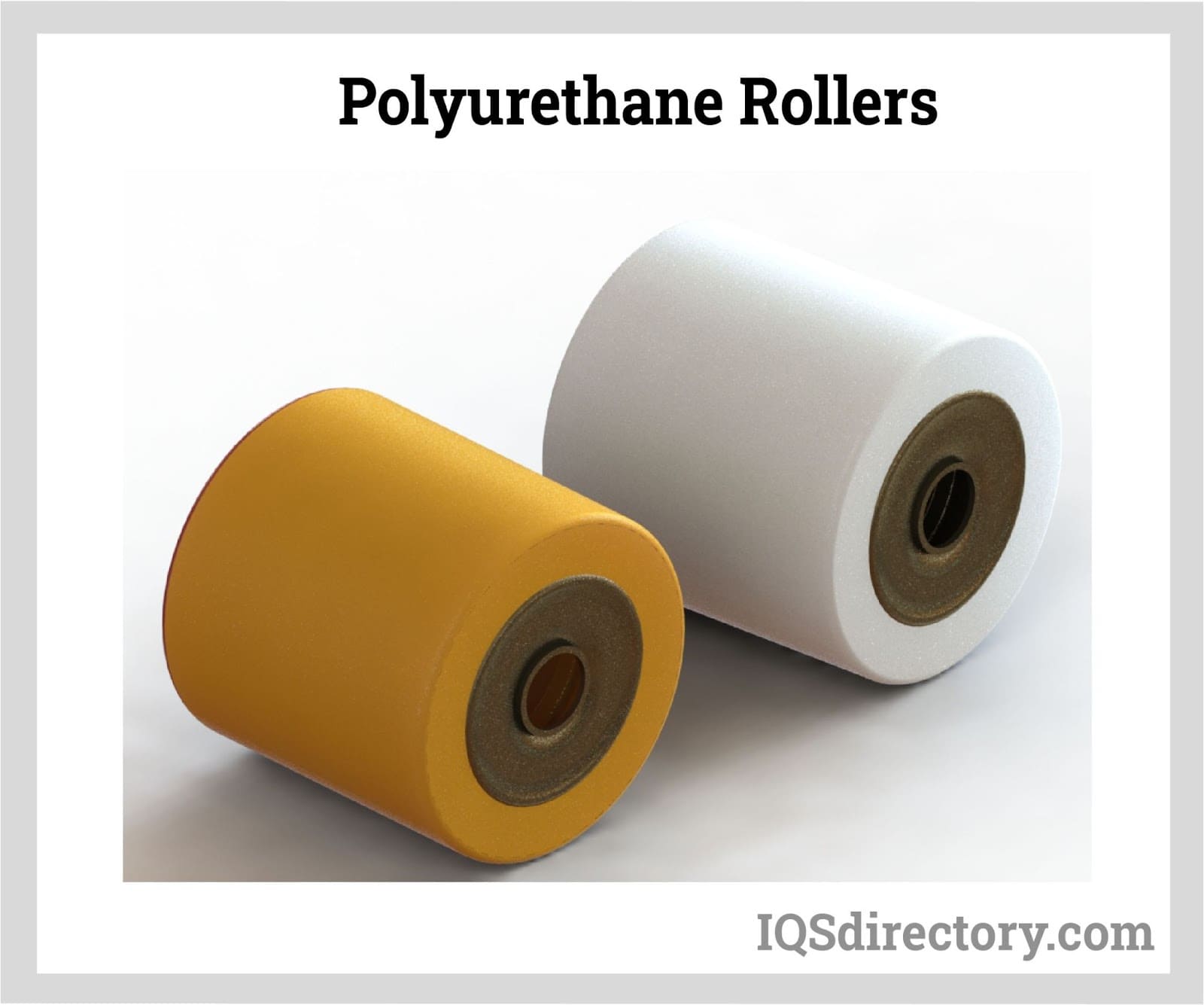
A stock image related to polyurethane roller.
Pros: High durability, excellent load-bearing capacity, and good resistance to wear and tear.
Cons: Limited performance in extreme temperatures and potential chemical sensitivity.
Impact on Application: Polyurethane rollers are ideal for manufacturing, material handling, and packaging industries, where they can handle various media without significant wear.
Considerations for International Buyers: Compliance with local standards such as ASTM or DIN is essential. Buyers in regions like Africa and South America should ensure that the material meets local environmental regulations.
What Are the Benefits of Steel Cores in Polyurethane Rollers?
Steel cores are often used in conjunction with polyurethane coatings to enhance the strength and load-bearing capacity of rollers. The steel core provides structural integrity, allowing the roller to support heavier loads without deformation. Steel can withstand high pressures and impacts, making it suitable for heavy-duty applications.
Pros: Exceptional strength, high load capacity, and resistance to deformation.
Cons: Heavier than other materials, which can affect mobility; potential for corrosion if not properly treated.
Impact on Application: Steel-cored polyurethane rollers are commonly used in heavy machinery and industrial applications where high load-bearing capabilities are required.
Considerations for International Buyers: Buyers should consider corrosion resistance treatments, especially in humid or coastal regions. Compliance with international standards for safety and performance is also critical.
How Do Rubber Rollers Compare in Terms of Performance?
Rubber rollers are another alternative, often used in applications requiring high elasticity and shock absorption. They can provide excellent grip and traction, which is beneficial in conveyor systems and printing applications. Rubber is also resistant to wear and can handle moderate temperatures.
Pros: High elasticity, good shock absorption, and excellent grip.
Cons: Lower load capacity compared to polyurethane and steel; may degrade faster under UV exposure.
Impact on Application: Ideal for applications where traction is critical, such as in printing or packaging.
Considerations for International Buyers: Buyers should ensure that the rubber used meets local regulations regarding chemical safety and environmental impact.
What Role Does PVC Play in Polyurethane Roller Manufacturing?
Polyvinyl chloride (PVC) is sometimes used as a base material for roller cores. While not as strong as steel, PVC is lightweight and resistant to various chemicals. It is often used in applications where weight reduction is a priority.
Pros: Lightweight, good chemical resistance, and cost-effective.
Cons: Lower strength compared to steel and polyurethane; may not withstand high temperatures.
Impact on Application: Suitable for lighter-duty applications or environments where chemical exposure is a concern.
Considerations for International Buyers: Buyers should verify the chemical compatibility of PVC with the intended media. Compliance with local standards for PVC use is also essential.
Summary Table of Material Options for Polyurethane Rollers
Material | Typical Use Case for Polyurethane Roller | Key Advantage | Key Disadvantage/Limitation | Relative Cost (Low/Med/High) |
---|---|---|---|---|
Polyurethane | Material handling, packaging | High durability and abrasion resistance | Limited performance in extreme temperatures | Medium |
Steel Core | Heavy machinery, industrial applications | Exceptional strength and load capacity | Heavier, potential for corrosion | High |
Rubber | Printing, conveyor systems | High elasticity and shock absorption | Lower load capacity, UV sensitivity | Medium |
PVC | Light-duty applications | Lightweight and cost-effective | Lower strength and temperature tolerance | Low |
This guide provides a comprehensive overview of the materials used in polyurethane rollers, enabling international B2B buyers to make informed decisions based on their specific needs and compliance requirements.
In-depth Look: Manufacturing Processes and Quality Assurance for polyurethane roller
What Are the Main Stages in the Manufacturing Process of Polyurethane Rollers?
The manufacturing of polyurethane rollers involves several critical stages that ensure the final product meets the required specifications for performance and durability. Understanding these stages can help international B2B buyers assess potential suppliers effectively.
1. Material Preparation: What Raw Materials Are Used?
The process begins with the selection and preparation of raw materials. Polyurethane is synthesized from a reaction between isocyanates and polyols, which can be tailored to achieve specific hardness and flexibility. Other additives may include colorants, fillers, and stabilizers, which enhance properties like UV resistance and wear. The quality of these raw materials is pivotal; therefore, suppliers should provide certificates of analysis (COA) to verify material quality.
2. Forming: How Are Polyurethane Rollers Shaped?
The forming stage involves various techniques, with the two most common being:
-
Injection Molding: This is the most widely used technique for creating polyurethane rollers. In this process, the polyurethane material is heated until it melts and is then injected into a mold where it cools and solidifies into the desired shape. This method allows for high precision and mass production.
-
Compression Molding: Suitable for larger rollers, this method involves placing the raw polyurethane material into a heated mold, where pressure is applied to shape the material. This technique is often used for custom or low-volume production runs.
Both techniques require careful control of temperature and pressure to ensure uniformity and eliminate defects.
3. Assembly: How Are Rollers Constructed?
After forming, the next step is assembly, which may include integrating additional components such as bearings or steel cores. The assembly process should adhere to specific guidelines to ensure that the components fit correctly and function optimally. For example, ensuring that the bearings are properly seated is crucial for the roller’s performance.
4. Finishing: What Final Touches Are Added?
Finishing processes may include surface treatments to enhance durability and aesthetics. Common finishing techniques include:
- Coating: Applying a protective layer to enhance wear resistance and reduce friction.
- Trimming: Removing any excess material or imperfections to achieve the desired dimensions.
- Polishing: This step is often used to provide a smooth finish that minimizes wear on surfaces the rollers will contact.
What Quality Assurance Measures Are Important for Polyurethane Rollers?
Quality assurance is vital in manufacturing polyurethane rollers, ensuring that products meet international standards and customer specifications. Here are key quality assurance measures that B2B buyers should consider.
International Standards: What Certifications Should You Look For?
International standards such as ISO 9001 are crucial for ensuring consistent quality management systems. This certification demonstrates that a manufacturer has effective quality management processes in place. Additionally, specific industry certifications such as CE marking (for compliance with European safety standards) and API standards (for products used in the oil and gas industry) can be critical depending on the application of the rollers.
Quality Control Checkpoints: What Are the Critical Control Points?
Quality control (QC) checkpoints are essential throughout the manufacturing process:
-
Incoming Quality Control (IQC): This initial checkpoint involves inspecting raw materials before they enter production to ensure they meet required specifications.
-
In-Process Quality Control (IPQC): This ongoing assessment occurs during production. It may include monitoring temperature and pressure in molding processes or checking dimensions of rollers at various stages.
-
Final Quality Control (FQC): At this stage, completed products undergo rigorous testing to ensure they meet all specifications. Common tests include:
-
Load Testing: To assess the roller’s performance under actual load conditions.
- Durability Testing: Evaluating how the roller withstands wear over time.
- Visual Inspection: Checking for surface defects or inconsistencies.
How Can B2B Buyers Verify Supplier Quality Control?
For international B2B buyers, particularly those in Africa, South America, the Middle East, and Europe, verifying a supplier’s quality control processes is essential. Here are actionable strategies to ensure compliance and quality:
1. Conduct Supplier Audits: What to Look For?
Regular supplier audits can provide insights into the quality management systems of a manufacturer. During these audits, buyers should assess:
- Compliance with international standards.
- Evidence of effective quality control processes.
- Facilities and equipment used for manufacturing.
2. Request Quality Reports: What Documentation Is Needed?
Buyers should request detailed quality reports that document the outcomes of IQC, IPQC, and FQC processes. These reports should include data on defect rates, test results, and corrective actions taken for non-conformities.
3. Utilize Third-Party Inspections: How Can You Ensure Objectivity?
Engaging third-party inspection services can provide an unbiased assessment of the supplier’s quality control practices. These services can conduct random inspections, verify compliance with standards, and provide certification that can enhance buyer confidence.
What Unique Quality Control Nuances Should International Buyers Be Aware Of?
International buyers should be aware of specific nuances related to quality control that may vary by region. For instance, regulatory standards can differ significantly between Africa, South America, the Middle East, and Europe. Understanding these regional differences can help buyers navigate compliance requirements more effectively.
In regions with less stringent regulations, buyers should prioritize finding suppliers who voluntarily adhere to international standards. This commitment can often indicate a higher level of quality assurance and reliability.
Conclusion: Ensuring Quality in Polyurethane Rollers
The manufacturing processes and quality assurance measures for polyurethane rollers are intricate yet essential to ensuring a reliable product. By understanding the key stages of manufacturing and the importance of robust quality control measures, international B2B buyers can make informed decisions when selecting suppliers. This knowledge not only facilitates better partnerships but also enhances the quality and performance of the rollers used in various applications across industries.
Practical Sourcing Guide: A Step-by-Step Checklist for ‘polyurethane roller’
Introduction
This sourcing guide is designed to assist B2B buyers in effectively procuring polyurethane rollers, crucial components used across various industries for material handling and machinery applications. By following this step-by-step checklist, buyers can ensure they make informed decisions, optimize their supply chain, and secure high-quality products that meet their operational needs.
Step 1: Define Your Technical Specifications
Before diving into the sourcing process, it’s essential to clearly outline your technical requirements. Determine the diameter, length, load capacity, and material properties of the polyurethane roller needed for your specific application.
- Consider operational conditions: Identify factors like temperature, environment, and load types to ensure the chosen roller can withstand these conditions.
- Check compatibility: Ensure the roller specifications align with existing machinery or equipment to avoid costly modifications.
Step 2: Research Potential Suppliers
Begin your search by identifying suppliers who specialize in polyurethane rollers. Use online directories, trade shows, and industry recommendations to compile a list of potential vendors.
- Focus on experience: Look for suppliers with a proven track record in manufacturing polyurethane products relevant to your industry.
- Evaluate geographic considerations: Suppliers in your region may offer logistical advantages, including reduced shipping times and costs.
Step 3: Evaluate Supplier Certifications and Standards
It’s crucial to verify that your suppliers adhere to industry standards and certifications, which can be an indicator of product quality and reliability.
- Seek ISO certifications: Suppliers with ISO 9001 certification demonstrate their commitment to quality management systems.
- Review product compliance: Ensure the polyurethane rollers meet applicable safety and environmental regulations in your target markets.
Step 4: Request Samples for Testing
Before finalizing any orders, request samples of the polyurethane rollers to assess their quality and performance. Testing samples can help prevent potential issues down the line.
- Conduct performance tests: Evaluate the rollers under actual working conditions to ensure they meet your specifications.
- Assess durability: Look for signs of wear and tear during testing to gauge the longevity of the material.
Step 5: Inquire About Customization Options
Depending on your application, you may require customized polyurethane rollers. Discuss any specific needs with potential suppliers to see how they can accommodate your requirements.
- Discuss modifications: Customization can include dimensions, color, or specific features that enhance the roller’s functionality.
- Understand the cost implications: Custom solutions may incur additional costs, so ensure you have a clear understanding of pricing before proceeding.
Step 6: Compare Pricing and Terms
Once you have narrowed down your options, compare pricing structures and payment terms from different suppliers to ensure you receive the best value.
- Consider total cost of ownership: Look beyond initial pricing; factor in shipping, potential tariffs, and maintenance costs.
- Negotiate terms: Don’t hesitate to negotiate payment and delivery terms that align with your budget and operational timelines.
Step 7: Finalize the Order and Establish Communication Channels
After selecting a supplier, finalize your order while ensuring clear communication channels are established for ongoing support and inquiries.
- Confirm delivery schedules: Establish timelines for order fulfillment and delivery to manage your production schedules effectively.
- Set up a feedback loop: Maintain regular communication with your supplier to address any issues and foster a strong business relationship.
By following this structured sourcing guide, B2B buyers can make informed decisions when procuring polyurethane rollers, ensuring they select the right products for their operational needs while maximizing value and efficiency.
Comprehensive Cost and Pricing Analysis for polyurethane roller Sourcing
What Are the Key Cost Components in Polyurethane Roller Manufacturing?
When sourcing polyurethane rollers, understanding the cost structure is crucial. Key components influencing the overall cost include:
-
Materials: The primary raw material, polyurethane, can vary significantly in price based on quality and supplier. Higher-grade materials offer better performance and durability but come at a premium.
-
Labor: Labor costs depend on the location of the manufacturing facility. For example, labor is generally more affordable in regions like South America compared to Europe. Additionally, skilled labor for specialized processes, such as molding and finishing, may incur higher costs.
-
Manufacturing Overhead: This encompasses utilities, facility maintenance, and equipment depreciation. Overhead can vary by region; manufacturers in areas with high energy costs may pass these expenses onto buyers.
-
Tooling: The initial setup for production requires tooling, which can be a significant one-time expense. Custom designs or specific dimensions might necessitate specialized tools, further increasing costs.
-
Quality Control (QC): Ensuring product quality is vital, especially for applications demanding high performance. Robust QC processes add to manufacturing costs but can prevent costly defects and returns.
-
Logistics: Shipping costs can vary widely based on the destination and the chosen Incoterms. Import duties and tariffs also play a significant role in the total cost, particularly for buyers in Africa and South America.
-
Margin: Suppliers typically add a profit margin to cover their costs and risks. This can range from 10% to 30%, depending on market competition and demand.
How Do Pricing Influencers Affect Polyurethane Roller Costs?
Several factors can impact the pricing of polyurethane rollers:
-
Volume/MOQ (Minimum Order Quantity): Purchasing in bulk usually results in lower unit prices. Suppliers often offer discounts for larger orders, making it essential for buyers to negotiate their MOQ.
-
Specifications and Customization: Custom rollers tailored to specific applications will generally incur higher costs due to unique tooling and material requirements. Buyers should clearly define their specifications to receive accurate pricing.
-
Materials and Quality Certifications: The choice of materials and any required certifications (e.g., ISO, ASTM) can influence pricing. Premium materials and certified products typically come at a higher price point but can offer enhanced performance and compliance.
-
Supplier Factors: The supplier’s reputation, manufacturing capabilities, and location can affect pricing. Established suppliers may charge more for their expertise and reliability, while new entrants might offer lower prices to gain market share.
-
Incoterms: The terms of shipping (e.g., FOB, CIF) dictate who is responsible for various logistics costs and risks. Understanding these terms can help buyers negotiate better deals and predict total costs more accurately.
What Buyer Tips Can Enhance Cost-Efficiency for Polyurethane Rollers?
International buyers can leverage several strategies to optimize their sourcing of polyurethane rollers:
-
Negotiate Prices: Engaging in negotiations can yield significant savings. Be prepared to discuss volume discounts, long-term contracts, and payment terms to find a mutually beneficial agreement.
-
Consider Total Cost of Ownership (TCO): Rather than focusing solely on the purchase price, assess the TCO, which includes maintenance, longevity, and potential downtime costs. Investing in higher-quality rollers may reduce overall expenses in the long run.
-
Research Local and International Suppliers: Diversifying supplier options can provide leverage in negotiations. Compare local manufacturers with international ones to identify the best combination of price, quality, and service.
-
Stay Informed About Market Trends: Awareness of global market conditions, such as fluctuations in raw material prices or changes in shipping regulations, can help in making informed purchasing decisions.
-
Understand Pricing Nuances for Your Region: Each market has its peculiarities. For instance, buyers in Africa and South America may face different import duties or logistical challenges compared to those in Europe. Tailoring your strategy to these factors can enhance cost-effectiveness.
Disclaimer for Indicative Prices
Prices for polyurethane rollers can vary widely based on the factors discussed above. The information provided here serves as a general guideline and may not reflect specific offers. Always consult suppliers for the most accurate and up-to-date pricing tailored to your needs.
Alternatives Analysis: Comparing polyurethane roller With Other Solutions
Understanding the Importance of Alternatives in Material Handling Solutions
When it comes to selecting the right materials for industrial applications, understanding the alternatives available is crucial for B2B buyers. Polyurethane rollers are widely recognized for their durability and performance, but other solutions also exist that may fit specific operational needs. This section compares polyurethane rollers with two viable alternatives—rubber rollers and steel rollers—providing insights into their respective advantages and disadvantages.
Comparison Table of Polyurethane Roller and Alternatives
Comparison Aspect | Polyurethane Roller | Rubber Roller | Steel Roller |
---|---|---|---|
Performance | High load capacity, excellent abrasion resistance | Good grip, moderate load capacity | Very high load capacity, durable |
Cost | Moderate | Low to moderate | High |
Ease of Implementation | Easy to integrate into existing systems | Simple installation, but requires alignment | Requires specialized equipment for installation |
Maintenance | Low maintenance, resistant to wear | Moderate maintenance, prone to degradation | Low maintenance, but may rust if not coated |
Best Use Case | Material handling in warehouses, automotive applications | Light to medium-duty applications, conveyor systems | Heavy-duty applications, manufacturing industries |
Detailed Breakdown of Alternatives
What Are the Pros and Cons of Rubber Rollers?
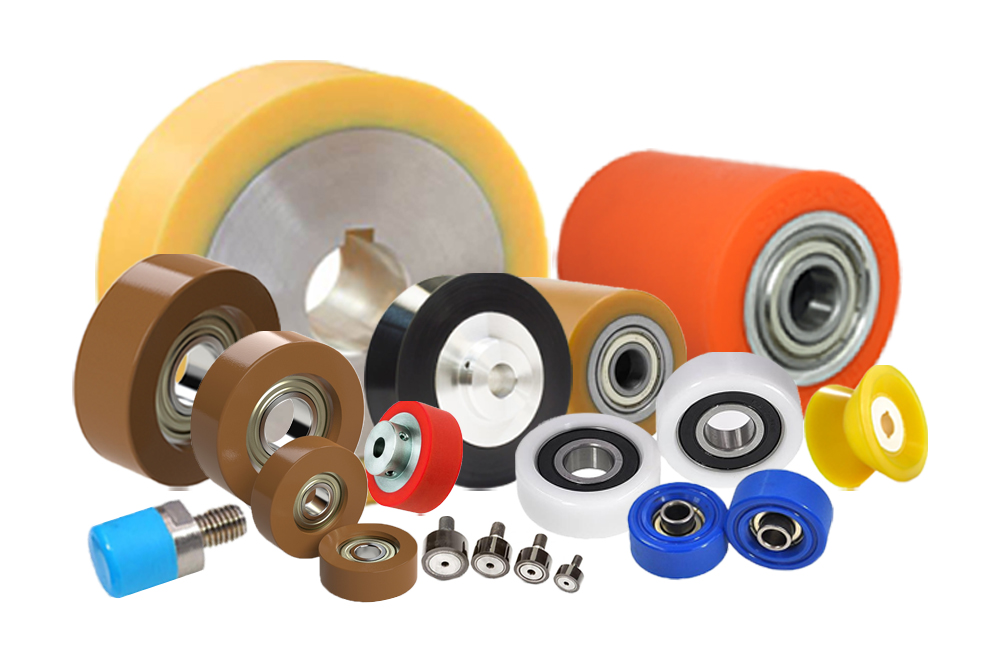
A stock image related to polyurethane roller.
Rubber rollers are a cost-effective alternative that offers good traction and cushioning. Their main advantage is their ability to conform to uneven surfaces, which can be beneficial in specific applications. However, rubber has a lower load capacity compared to polyurethane and can degrade over time, especially in harsh environments. This makes them suitable for light to medium-duty applications but less ideal for heavy-duty uses where durability and high performance are critical.
How Do Steel Rollers Compare?
Steel rollers are known for their exceptional strength and durability, making them suitable for heavy-duty applications in manufacturing environments. They can handle very high loads and are resistant to deformation. However, they are generally more expensive than both polyurethane and rubber rollers, and their installation may require specialized equipment and expertise. Additionally, steel rollers can rust if not properly coated, leading to maintenance concerns. They are best used in scenarios where load capacity is paramount and where environmental conditions are controlled.
Conclusion: How to Choose the Right Roller Solution for Your Business
Choosing the right roller solution depends on various factors, including the specific operational demands of your business, budget constraints, and environmental conditions. Polyurethane rollers offer a balanced solution with high performance and low maintenance, making them ideal for various applications. However, if cost is a primary concern and the application is light-duty, rubber rollers may be the better choice. For industries that require handling heavy loads, steel rollers can provide the necessary durability despite their higher cost. Assess your unique needs carefully to select the most effective roller solution for your operations.
Essential Technical Properties and Trade Terminology for polyurethane roller
What Are the Key Technical Properties of Polyurethane Rollers?
When selecting polyurethane rollers, it’s crucial for B2B buyers to understand their essential technical properties. Below are some critical specifications that can impact performance and suitability for various applications.
1. Material Grade
Polyurethane rollers are typically made from different grades of polyurethane, which can affect their durability, flexibility, and load-bearing capacity. Higher-grade materials offer better resistance to abrasion, chemicals, and temperature fluctuations. For B2B buyers, selecting the right material grade is essential to ensure that the rollers will perform effectively in their specific operational environments, such as manufacturing or material handling.
2. Shore Hardness
Shore hardness indicates the hardness of the polyurethane material on a scale from 0 to 100. A higher Shore A rating means a harder roller, while a lower rating indicates a softer material. Buyers should consider the hardness based on their application needs; softer rollers provide better grip and shock absorption, while harder rollers are suited for heavy loads and high-speed applications.
3. Load Capacity
The load capacity of a polyurethane roller refers to the maximum weight it can support without failing. It’s crucial for B2B buyers to verify the load ratings provided by manufacturers to ensure compatibility with their equipment and operational requirements. Inadequate load capacity can lead to equipment failure and increased maintenance costs.
4. Tolerance
Tolerance refers to the allowable deviation from specified dimensions. For polyurethane rollers, this can affect their fit and performance in machinery. Tight tolerances are essential in precision applications where alignment is critical. Buyers should consult with manufacturers to determine the acceptable tolerance levels for their specific needs.
5. Temperature Resistance
Polyurethane rollers can be engineered to withstand various temperature ranges. Understanding the temperature resistance is vital for applications that involve extreme heat or cold, as it can affect the roller’s performance and lifespan. B2B buyers should ensure that the rollers they select can operate effectively in the environmental conditions of their facilities.
What Are Common Trade Terms Related to Polyurethane Rollers?
Familiarity with industry jargon can help B2B buyers navigate purchasing and logistics more effectively. Below are some common terms associated with polyurethane rollers.
1. OEM (Original Equipment Manufacturer)
OEM refers to companies that produce parts or equipment that may be marketed by another manufacturer. For B2B buyers, understanding OEM relationships can be critical when sourcing rollers that need to fit specific machinery or equipment models.
2. MOQ (Minimum Order Quantity)
MOQ is the minimum number of units a supplier requires for an order. This is particularly important for B2B buyers as it can affect inventory costs and cash flow. Knowing the MOQ helps in planning purchases and ensures that the buyer can meet their operational demands without overcommitting financially.
3. RFQ (Request for Quotation)
An RFQ is a document that buyers send to suppliers requesting a price quote for specific quantities of goods. For B2B buyers, issuing an RFQ allows them to gather competitive pricing and terms from multiple suppliers, facilitating better decision-making.
4. Incoterms (International Commercial Terms)
Incoterms are standardized trade terms that define the responsibilities of buyers and sellers in international transactions. Understanding these terms is essential for B2B buyers engaged in cross-border trade to clarify shipping responsibilities, risk management, and cost allocation.
5. Lead Time
Lead time refers to the amount of time it takes from placing an order to receiving the goods. For B2B buyers, knowing the lead time is crucial for inventory management and ensuring that production schedules are met. Delays in lead time can impact business operations significantly.
By grasping these technical properties and trade terms, B2B buyers can make informed decisions when sourcing polyurethane rollers, ensuring that they select the right products for their specific needs.
Navigating Market Dynamics and Sourcing Trends in the polyurethane roller Sector
What Are the Key Market Dynamics and Sourcing Trends in the Polyurethane Roller Sector?
The polyurethane roller market is experiencing robust growth due to several global drivers. Increased demand for durable, high-performance materials across various industries—such as manufacturing, logistics, and food processing—is a primary factor. The rise of automation and advanced manufacturing technologies is also shaping sourcing strategies, with businesses seeking suppliers who offer innovative solutions that enhance operational efficiency. Notably, B2B buyers from regions like Africa, South America, the Middle East, and Europe should be aware of emerging trends such as the integration of IoT technology in supply chains, which enhances tracking and management of products, including polyurethane rollers.
Another significant trend is the growing emphasis on customization. International buyers are increasingly looking for suppliers who can provide tailored solutions that meet specific operational needs. This trend is particularly pronounced in industries with unique requirements, such as automotive and aerospace, where the performance of polyurethane rollers can directly impact production efficiency. Furthermore, the ongoing supply chain disruptions caused by geopolitical factors and the COVID-19 pandemic have prompted buyers to diversify their supplier base, favoring local suppliers to reduce lead times and enhance supply chain resilience.
How Does Sustainability and Ethical Sourcing Impact the Polyurethane Roller Industry?
Sustainability has become a critical consideration in the polyurethane roller sector. As businesses worldwide strive to reduce their environmental footprint, B2B buyers are increasingly prioritizing suppliers who demonstrate a commitment to sustainable practices. This includes using eco-friendly materials and processes in the manufacturing of polyurethane rollers. Buyers should look for certifications such as ISO 14001, which indicate a company’s adherence to environmental management standards.
Additionally, ethical sourcing is gaining traction, with buyers seeking suppliers who uphold fair labor practices and transparency in their supply chains. This shift not only mitigates reputational risks but also aligns with the values of a growing number of consumers who prefer environmentally and socially responsible products. In response, manufacturers are investing in ‘green’ certifications and materials that showcase their commitment to sustainability, such as water-based polyurethanes or recycled content in their products. By prioritizing suppliers with these credentials, international buyers can contribute to a more sustainable future while ensuring the quality and performance of polyurethane rollers.
What Is the Brief Evolution of the Polyurethane Roller Sector?
The evolution of the polyurethane roller sector can be traced back to the mid-20th century when the demand for durable, versatile materials began to rise. Initially, rubber rollers dominated the market; however, the introduction of polyurethane offered significant advantages, including enhanced wear resistance and load-bearing capabilities. Over the years, advancements in polyurethane formulations have led to the development of rollers that can withstand extreme temperatures and harsh chemicals, making them suitable for a wider range of applications.
As industries have evolved, so too have the manufacturing processes for polyurethane rollers. Techniques such as injection molding and urethane casting have improved production efficiency and allowed for greater customization. The current landscape reflects a blend of innovation and sustainability, with manufacturers continuously seeking ways to enhance product performance while minimizing environmental impact. This historical context highlights the importance of understanding both past trends and current dynamics for B2B buyers navigating the polyurethane roller market today.
Frequently Asked Questions (FAQs) for B2B Buyers of polyurethane roller
-
How do I choose the right polyurethane roller for my application?
Selecting the appropriate polyurethane roller involves considering several factors, including load capacity, roller diameter, and the specific application requirements. Assess the weight and type of materials the roller will handle, as well as the surface it will operate on. For environments prone to high temperatures or chemicals, opt for high-performance polyurethane that can withstand these conditions. Additionally, consult with suppliers to ensure compatibility with your equipment and inquire about custom sizes or configurations if standard options do not meet your needs. -
What are the key advantages of using polyurethane rollers in industrial applications?
Polyurethane rollers offer numerous benefits, including excellent wear resistance, high load-bearing capacity, and minimal noise during operation. Their elasticity allows them to absorb shocks and vibrations, protecting both the roller and the surface underneath. Polyurethane is also resistant to chemicals and moisture, making these rollers suitable for a wide range of environments, from manufacturing plants to food processing facilities. Additionally, they provide a non-marking surface, which is particularly valuable in settings where aesthetics matter, such as retail spaces. -
What is the typical lead time for ordering polyurethane rollers from international suppliers?
Lead times for polyurethane rollers can vary significantly based on factors such as supplier location, customization requirements, and order volume. Generally, expect a lead time of 2-6 weeks for standard orders, while custom rollers may take longer, potentially up to 12 weeks. It’s advisable to communicate directly with suppliers to obtain specific timelines and consider placing orders well in advance to avoid production delays, especially when sourcing from overseas manufacturers in regions like Asia or Europe. -
What should I consider when vetting suppliers of polyurethane rollers?
When evaluating potential suppliers, prioritize factors such as their industry experience, production capabilities, and customer reviews. Request samples to assess the quality of their products and verify if they adhere to international quality standards, such as ISO certifications. Additionally, inquire about their supply chain reliability, including sourcing of raw materials and logistics practices. Building a relationship with suppliers who have a proven track record in your target market (Africa, South America, the Middle East, Europe) can also enhance trust and communication. -
What are the common minimum order quantities (MOQs) for polyurethane rollers?
Minimum order quantities for polyurethane rollers can range from a few units to several hundred, depending on the supplier and the specific product. Many manufacturers set MOQs to ensure cost-effectiveness in production and shipping. If you are a smaller business or startup, it’s advisable to discuss your needs with suppliers, as some may offer flexibility or tiered pricing based on order size. Always confirm the MOQ before placing an order to avoid unexpected costs or delays. -
What payment terms should I expect when sourcing polyurethane rollers internationally?
Payment terms can vary widely among suppliers, but common practices include upfront payment, partial payment upon order confirmation, or net 30/60 days after delivery. For large orders, consider negotiating terms that provide some level of financial security, such as letters of credit or escrow services. It’s crucial to establish clear payment conditions in your purchase agreement to avoid misunderstandings later. Additionally, be aware of currency exchange rates and international transaction fees that may affect overall costs.
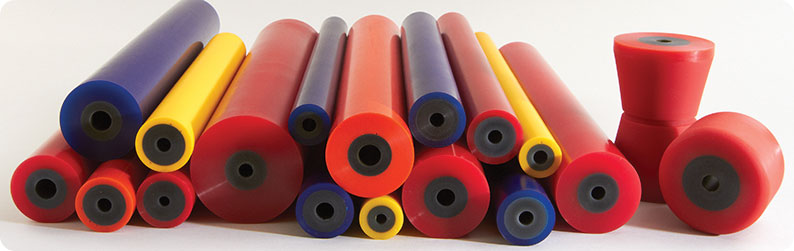
A stock image related to polyurethane roller.
-
How can I ensure quality assurance (QA) for polyurethane rollers purchased overseas?
To maintain quality assurance for polyurethane rollers sourced internationally, request detailed product specifications and certifications from your suppliers. Implement a quality control process that includes pre-shipment inspections and third-party audits if necessary. Establish clear acceptance criteria for the rollers, focusing on dimensions, weight capacity, and material quality. Engaging a local representative or partner in the supplier’s country can also facilitate better oversight and ensure compliance with agreed standards. -
What logistical considerations should I keep in mind when importing polyurethane rollers?
When importing polyurethane rollers, consider shipping options, customs regulations, and potential tariffs that may apply. Assess the most efficient shipping methods based on your timeline and budget, whether by air or sea freight. Ensure you have all necessary documentation, such as invoices, packing lists, and certificates of origin, to avoid customs delays. Engaging a freight forwarder familiar with your specific region can streamline the process and help navigate any logistical challenges that may arise.
Important Disclaimer & Terms of Use
⚠️ Important Disclaimer
The information provided in this guide, including content regarding manufacturers, technical specifications, and market analysis, is for informational and educational purposes only. It does not constitute professional procurement advice, financial advice, or legal advice.
While we have made every effort to ensure the accuracy and timeliness of the information, we are not responsible for any errors, omissions, or outdated information. Market conditions, company details, and technical standards are subject to change.
B2B buyers must conduct their own independent and thorough due diligence before making any purchasing decisions. This includes contacting suppliers directly, verifying certifications, requesting samples, and seeking professional consultation. The risk of relying on any information in this guide is borne solely by the reader.