Unlock Efficiency: The Ultimate DC Power Supply Guide (2025)
Introduction: Navigating the Global Market for dc power supply
In today’s rapidly evolving global marketplace, sourcing the right DC power supply can be a daunting challenge for B2B buyers, especially those operating in regions such as Africa, South America, the Middle East, and Europe. With increasing demand for reliable and efficient power solutions across various industries—ranging from telecommunications to renewable energy—understanding the nuances of DC power supplies is essential for informed purchasing decisions.
This comprehensive guide explores the diverse types of DC power supplies available, their applications, and the critical factors to consider when vetting suppliers. From linear and switching power supplies to custom solutions tailored for specific needs, we provide insights into how to assess product specifications, certifications, and compatibility with existing systems. Additionally, we delve into pricing structures and cost-saving strategies, ensuring that buyers can navigate the complexities of international procurement effectively.
By equipping international B2B buyers with actionable insights and expert recommendations, this guide aims to empower you to make strategic purchasing decisions. Whether you are based in the UAE, Colombia, or any other market, understanding the dynamics of DC power supply sourcing will enhance your competitive edge and operational efficiency. Join us as we unravel the intricacies of this essential component in modern electrical systems.
Understanding dc power supply Types and Variations
Type Name | Key Distinguishing Features | Primary B2B Applications | Brief Pros & Cons for Buyers |
---|---|---|---|
Linear Power Supply | Simple design, low noise, stable output voltage | Laboratory equipment, audio devices | Pros: Reliable performance; Cons: Less efficient, larger size. |
Switching Power Supply | High efficiency, compact size, adjustable output | Telecommunications, industrial automation | Pros: Energy-efficient; Cons: Can produce noise, complex design. |
Programmable Power Supply | Adjustable voltage and current settings, digital control | Research & development, testing environments | Pros: Versatile; Cons: Higher cost, requires technical knowledge. |
Unregulated Power Supply | Simple, cost-effective, variable output | Basic electronic applications | Pros: Low cost; Cons: Output voltage varies with load. |
DC-DC Converter | Converts one DC voltage to another, compact design | Battery management systems, renewable energy | Pros: Space-saving; Cons: Limited to specific applications. |
What are the Characteristics of Linear Power Supplies?
Linear power supplies feature a straightforward design that provides a stable output voltage with minimal noise. They are commonly used in applications requiring high precision, such as laboratory equipment and audio devices. When considering a linear power supply, buyers should evaluate the load requirements and space availability, as these units can be bulkier and less efficient compared to switching alternatives.
How Do Switching Power Supplies Differ from Other Types?
Switching power supplies are known for their high efficiency and compact size, making them ideal for environments where space and energy consumption are critical. They adjust output voltage and current dynamically, catering to various industrial applications like telecommunications and automation. Buyers should consider the potential for electromagnetic interference and the complexity of installation when opting for this type.
Why Choose a Programmable Power Supply?
Programmable power supplies offer advanced features like adjustable voltage and current settings, often controlled digitally. They are particularly useful in research and testing environments where precise control is essential. While they provide versatility and adaptability, buyers need to account for the higher costs and the technical expertise required for operation.
What Should Buyers Know About Unregulated Power Supplies?
Unregulated power supplies are the simplest and most cost-effective option, providing variable output based on load conditions. These are suitable for basic electronic applications where precise voltage is not critical. However, buyers should be cautious of the fluctuating output voltage, which may not meet the requirements of sensitive devices.
How Are DC-DC Converters Utilized in Various Applications?
DC-DC converters are specialized devices that convert one DC voltage level to another, making them essential in battery management systems and renewable energy applications. Their compact design allows for easy integration into various systems. Buyers should evaluate the specific voltage requirements and efficiency levels to ensure compatibility with their applications.
Key Industrial Applications of dc power supply
Industry/Sector | Specific Application of dc power supply | Value/Benefit for the Business | Key Sourcing Considerations for this Application |
---|---|---|---|
Telecommunications | Powering telecom equipment and base stations | Ensures reliable communication and network uptime | Voltage stability, efficiency ratings, and regulatory compliance |
Manufacturing | Operating automated machinery and robotics | Enhances production efficiency and reduces downtime | Customization options, load requirements, and environmental conditions |
Renewable Energy | Supporting solar power systems and battery storage | Facilitates energy conversion and storage for sustainable use | Compatibility with existing systems and scalability options |
Automotive | Charging electric vehicles (EVs) and battery management | Promotes sustainable transport solutions and customer satisfaction | Fast charging capabilities, safety certifications, and durability |
Medical Equipment | Powering diagnostic and imaging devices | Ensures accuracy and reliability in critical healthcare settings | Compliance with medical standards, power quality, and redundancy features |
How is DC Power Supply Used in Telecommunications?
In the telecommunications sector, DC power supplies are crucial for powering telecom equipment, including base stations and routers. These systems require stable and continuous power to maintain communication networks. For international B2B buyers, particularly from regions like Africa and the Middle East, sourcing power supplies that offer high voltage stability and efficiency is essential. Additionally, regulatory compliance with local standards ensures safety and reliability, which are critical in maintaining network uptime.
What Role Does DC Power Supply Play in Manufacturing?
In manufacturing, DC power supplies are integral to operating automated machinery and robotics. These systems rely on precise voltage and current levels to function optimally, directly impacting production efficiency. Buyers in South America and Europe should consider customization options to meet specific load requirements and environmental conditions. Choosing power supplies that offer durability and high performance can significantly reduce downtime and enhance overall productivity in manufacturing processes.
How is DC Power Supply Beneficial for Renewable Energy Systems?
DC power supplies are vital in renewable energy applications, particularly in solar power systems and battery storage solutions. They facilitate the conversion of solar energy into usable electricity and manage energy storage effectively. For B2B buyers in Africa and South America, it’s essential to select power supplies that are compatible with existing systems and offer scalability options. This ensures that as energy demands grow, the power supply can adapt without requiring a complete overhaul.
How is DC Power Supply Used in the Automotive Industry?
In the automotive sector, DC power supplies are increasingly used for charging electric vehicles (EVs) and managing battery systems. They play a pivotal role in promoting sustainable transportation solutions, enhancing customer satisfaction through efficient charging capabilities. Buyers from Europe and the UAE should prioritize sourcing power supplies with fast charging features, safety certifications, and proven durability to meet the demands of modern EV technology.
What is the Importance of DC Power Supply in Medical Equipment?
DC power supplies are essential for powering diagnostic and imaging devices in healthcare settings. These devices require reliable and accurate power to ensure proper functionality and patient safety. For international B2B buyers, especially in Europe and the Middle East, compliance with medical standards and regulations is paramount. Additionally, selecting power supplies that offer redundancy features can safeguard against power failures, ensuring continuous operation in critical healthcare environments.
3 Common User Pain Points for ‘dc power supply’ & Their Solutions
Scenario 1: Inconsistent Power Supply for Critical Operations
The Problem: Many international B2B buyers, especially those in Africa and South America, face challenges with inconsistent power supply, which can severely impact operations reliant on DC power. For instance, a manufacturer in Colombia may rely on a DC power supply for their assembly line machinery. Frequent fluctuations in voltage can lead to equipment malfunction, increased downtime, and ultimately, loss of revenue. This unpredictability can be frustrating, as it affects productivity and the bottom line.
The Solution: To combat this issue, buyers should invest in high-quality DC power supplies equipped with voltage regulation features. Look for models that offer built-in overvoltage protection and constant voltage output to ensure steady performance. When sourcing these power supplies, consider suppliers who offer customization options to meet specific operational requirements, such as adjustable voltage and current settings. Furthermore, implementing a robust maintenance schedule can preemptively address potential issues, ensuring that the power supply remains functional and reliable.
Scenario 2: Complexity in Sizing and Specifications
The Problem: Sizing and specifying the right DC power supply can be a daunting task for B2B buyers, particularly in the Middle East and Europe, where application requirements can vary widely. For example, a telecommunications company in the UAE may require a DC power supply for a new network installation. Misjudging the specifications could lead to underpowered equipment or excess costs from over-specification. This complexity often leads to delays in project timelines and unexpected expenses.
The Solution: To simplify the selection process, buyers should conduct a thorough needs assessment that includes evaluating the total load requirements, peak usage, and any future scalability needs. Utilizing online tools and calculators provided by manufacturers can help in determining the precise specifications required. Additionally, consulting with technical support teams or industry experts during the purchasing process can clarify any uncertainties regarding power requirements. By choosing suppliers that provide detailed product documentation and customer support, buyers can ensure that they make informed decisions that align with their operational goals.
Scenario 3: Limited Availability of Suitable Products
The Problem: In regions such as Africa and parts of South America, B2B buyers often struggle with limited access to a diverse range of DC power supply products. This scarcity can hinder the ability to find reliable, certified, and high-performance power supplies that meet international safety standards. For instance, a startup in Africa aiming to develop renewable energy solutions may find it challenging to source suitable DC power supplies that comply with local regulations and certifications.
The Solution: To navigate this challenge, B2B buyers should consider establishing partnerships with reputable international suppliers who can provide a broader selection of products. Investigating suppliers that specialize in exporting DC power supplies can also yield more options. Additionally, buyers should prioritize suppliers that offer certification and compliance documentation, ensuring that the products meet both local and international standards. Participating in industry trade shows or online forums can also connect buyers with potential suppliers and innovations in DC power supply technology, enhancing product availability and knowledge within the region.
Strategic Material Selection Guide for dc power supply
What Are the Key Materials Used in DC Power Supply Manufacturing?
When selecting materials for DC power supplies, it is crucial to understand the properties and performance characteristics of the most commonly used materials. This knowledge helps international B2B buyers make informed decisions that align with their operational requirements and regional standards.
Copper: The Backbone of Electrical Conductivity
Key Properties: Copper is renowned for its excellent electrical conductivity, thermal conductivity, and malleability. It typically withstands temperatures up to 200°C and has a high resistance to corrosion, particularly when insulated.
Pros & Cons: The primary advantage of copper is its superior conductivity, which enables efficient power transfer. However, its cost can be a significant drawback, especially for large-scale applications. Manufacturing complexity is moderate, as copper can be easily shaped into wires and components.
Impact on Application: Copper is ideal for applications requiring high current and low resistance, such as in power distribution systems. Its compatibility with various media makes it a versatile choice for DC power supplies.
Considerations for International Buyers: Buyers from regions like the Middle East and Africa should be aware of the fluctuating copper prices and the need for compliance with international standards such as ASTM B75 for copper wire.
Aluminum: A Lightweight Alternative
Key Properties: Aluminum is lighter than copper and offers good conductivity, although it is less effective than copper. It can operate at temperatures up to 150°C and is resistant to corrosion due to the formation of a protective oxide layer.
Pros & Cons: The main advantage of aluminum is its lower cost and weight, making it suitable for portable power supplies. However, its lower conductivity can lead to increased energy losses, and it requires careful handling to avoid breakage during installation.
Impact on Application: Aluminum is often used in applications where weight is a critical factor, such as in aerospace or mobile equipment. Its compatibility with various environments makes it a popular choice.
Considerations for International Buyers: Buyers should consider regional standards for aluminum use, such as DIN 17660 in Europe, and ensure that their suppliers provide materials that meet these specifications.
Steel: Strength and Durability
Key Properties: Steel is known for its strength and durability, capable of withstanding high pressures and temperatures, often exceeding 300°C. It is also resistant to mechanical wear and tear.
Pros & Cons: The strength of steel makes it ideal for structural components of DC power supplies, providing stability and protection. However, steel is heavier and more expensive than aluminum, and it can corrode if not properly treated.
Impact on Application: Steel is commonly used in enclosures and frames for power supplies, ensuring protection from environmental factors. Its robustness makes it suitable for heavy-duty applications.
Considerations for International Buyers: Compliance with standards such as ASTM A36 for structural steel is essential. Buyers in regions like South America should also consider local regulations regarding material sourcing and environmental impact.
Thermoplastics: Versatility in Insulation
Key Properties: Thermoplastics, such as polycarbonate and ABS, are lightweight and exhibit excellent electrical insulation properties. They can operate within a temperature range of -40°C to 85°C.
Pros & Cons: The primary advantage of thermoplastics is their versatility and cost-effectiveness. They can be molded into complex shapes, making them suitable for various applications. However, they may not withstand high temperatures as well as metals.
Impact on Application: Thermoplastics are often used for insulation and housing components in DC power supplies, providing safety and protection against electrical hazards.
Considerations for International Buyers: Buyers should ensure compliance with international safety standards, such as UL 94 for flammability, especially in regions with stringent safety regulations like Europe.
Summary of Material Selection for DC Power Supply
Material | Typical Use Case for dc power supply | Key Advantage | Key Disadvantage/Limitation | Relative Cost (Low/Med/High) |
---|---|---|---|---|
Copper | Conductors in power distribution | Superior electrical conductivity | High cost | High |
Aluminum | Lightweight applications | Lower cost and weight | Lower conductivity | Medium |
Steel | Structural components | High strength and durability | Heavier and prone to corrosion | Medium |
Thermoplastics | Insulation and housing | Versatile and cost-effective | Limited temperature resistance | Low |
This strategic material selection guide empowers international B2B buyers to choose the right materials for their DC power supply applications, ensuring compliance with regional standards and optimizing performance.
In-depth Look: Manufacturing Processes and Quality Assurance for dc power supply
What Are the Main Stages of Manufacturing DC Power Supplies?
The manufacturing process for DC power supplies consists of several critical stages, each designed to ensure the final product meets stringent performance and safety standards. Understanding these stages is essential for B2B buyers looking to procure high-quality power supplies.
Material Preparation
The first stage involves the careful selection and preparation of raw materials. Key components typically include transformers, capacitors, inductors, and circuit boards. Suppliers often source materials that comply with international standards, such as RoHS (Restriction of Hazardous Substances), to ensure environmental safety and compliance.
Before manufacturing begins, materials undergo inspection for quality and specifications. Buyers should verify that suppliers maintain a robust material management system to track the origin and quality of materials used in production.
Forming and Component Assembly
The next stage is forming, where raw materials are shaped into usable components. Techniques like PCB (Printed Circuit Board) fabrication play a crucial role here. Advanced manufacturing methods such as surface mount technology (SMT) and through-hole technology are commonly employed to assemble components onto PCBs.
Assembly is often a combination of manual labor and automated processes. Automated pick-and-place machines are used for high precision in component placement, while skilled technicians perform quality checks at each step. B2B buyers should inquire about the assembly techniques used by suppliers, as this can significantly impact the reliability of the final product.
Finishing Processes
Finishing includes several steps such as soldering, encapsulation, and protective coating. Soldering is critical for ensuring electrical connections are secure, while encapsulation protects sensitive components from moisture and contaminants. Quality assurance checks are conducted at this stage to catch defects early.
Buyers should ensure that suppliers utilize industry-standard practices for finishing processes. Techniques such as conformal coating can enhance durability, which is particularly beneficial for equipment used in harsh environments.
How Is Quality Assurance Integrated into the Manufacturing Process?
Quality assurance (QA) is integral to the manufacturing of DC power supplies, ensuring that each unit meets the required specifications and standards.
What International Standards Should Buyers Be Aware Of?
International standards such as ISO 9001 provide a framework for a quality management system that emphasizes continuous improvement and customer satisfaction. For DC power supplies, compliance with CE (Conformité Européenne) and FCC (Federal Communications Commission) certifications is also critical, as these indicate that products meet safety and environmental requirements.
Understanding these standards is crucial for international buyers, particularly in regions like Africa, South America, the Middle East, and Europe. Ensuring that suppliers adhere to these standards can mitigate risks associated with non-compliance.
What Are the Key Quality Control Checkpoints?
Quality control in manufacturing typically involves several checkpoints:
- Incoming Quality Control (IQC): Materials are inspected upon arrival to ensure they meet specifications.
- In-Process Quality Control (IPQC): Ongoing checks are performed during the manufacturing process to identify defects early.
- Final Quality Control (FQC): The completed products undergo rigorous testing to verify performance and safety standards.
B2B buyers should request details on the specific quality control methods used by suppliers to ensure comprehensive oversight throughout the manufacturing process.
What Testing Methods Are Commonly Used for DC Power Supplies?
Various testing methods are employed to validate the performance and reliability of DC power supplies. These include:
- Load Testing: Assessing the power supply’s performance under various load conditions to ensure it operates as expected.
- Thermal Testing: Evaluating how the unit performs under temperature variations to ensure safe operation in different environments.
- Electrical Testing: Checking for voltage, current, and ripple characteristics to ensure compliance with specifications.
Suppliers should provide documentation of test results to B2B buyers, which can serve as evidence of compliance with required standards.
How Can B2B Buyers Verify Supplier Quality Control?
Verifying the quality control practices of potential suppliers is crucial for B2B buyers. Here are several strategies to consider:
- Supplier Audits: Conducting on-site audits can provide insight into the supplier’s manufacturing processes, quality control measures, and adherence to standards.
- Requesting Reports: Suppliers should be willing to provide quality assurance reports and certifications that demonstrate compliance with international standards.
- Third-Party Inspections: Engaging third-party inspection agencies can add an additional layer of verification, ensuring that the products meet specified quality and performance criteria.
What Are the Nuances of Quality Control for International B2B Buyers?
For international buyers, particularly those from diverse regions like Africa, South America, the Middle East, and Europe, understanding the nuances of quality control is essential. Factors such as regional regulations, varying standards, and logistical challenges can impact the procurement process.
Buyers should be aware of the specific regulations in their region, as well as the certifications that may be required for importing electrical components. Additionally, establishing clear communication with suppliers regarding quality expectations and compliance can help mitigate risks associated with cross-border transactions.
By understanding the manufacturing processes and quality assurance measures associated with DC power supplies, international B2B buyers can make informed decisions that align with their operational needs and regulatory requirements. This comprehensive approach not only ensures product reliability but also fosters long-term partnerships with reputable suppliers.
Practical Sourcing Guide: A Step-by-Step Checklist for ‘dc power supply’
In the competitive landscape of B2B procurement, sourcing a reliable DC power supply is crucial for businesses across various industries. This guide provides a structured approach to help international buyers, particularly from Africa, South America, the Middle East, and Europe, effectively navigate the sourcing process.
Step 1: Define Your Technical Specifications
Before initiating the procurement process, it’s essential to clearly define your technical requirements. Specifications such as voltage output, amperage, and wattage are critical for ensuring compatibility with your existing systems. Consider the application—will it be used for industrial equipment, telecommunications, or consumer electronics?
- Voltage Output: Ensure it meets the needs of your equipment (e.g., 12V, 24V).
- Amperage and Wattage: Calculate the total power requirement to avoid underperformance or equipment damage.
Step 2: Research Potential Suppliers
Invest time in researching suppliers who specialize in DC power supplies. Look for companies with a strong reputation and experience in your specific industry. Utilize online directories, industry forums, and trade shows to gather a list of potential candidates.
- Industry Experience: Check if they have successfully supplied similar products to businesses in your region.
- Customer Reviews: Look for testimonials and case studies that reflect their reliability and product quality.
Step 3: Evaluate Supplier Certifications
Supplier certifications are a vital aspect of the sourcing process. Verify that the suppliers hold relevant certifications, such as CE, FCC, or ISO standards, which indicate compliance with international quality and safety norms.
- Quality Assurance: Certifications ensure that the products have undergone rigorous testing.
- Regulatory Compliance: This is particularly important for international shipping and usage in specific regions.
Step 4: Request Samples and Technical Support
Before making a bulk purchase, request samples of the DC power supply. This allows you to assess the quality and performance firsthand. Additionally, inquire about the technical support offered by the supplier.
- Quality Assessment: Test the samples in your operational environment to validate performance.
- Technical Assistance: Ensure the supplier provides adequate support for installation and troubleshooting.
Step 5: Compare Pricing and Payment Terms
Once you have shortlisted suppliers, compare pricing models and payment terms. Look beyond the initial cost; consider the total cost of ownership, which includes warranty, service, and shipping costs.
- Bulk Discounts: Ask about pricing structures for larger orders.
- Payment Flexibility: Understand payment terms and any financing options available.
Step 6: Negotiate Terms and Conditions
Engage in negotiations to secure favorable terms and conditions. Discuss aspects such as delivery timelines, return policies, and warranty coverage. A clear agreement will help mitigate risks associated with procurement.
- Delivery Schedules: Ensure timelines align with your project schedules.
- Warranty and Returns: Confirm the duration and coverage of the warranty to protect your investment.
Step 7: Finalize the Purchase Agreement
Once all terms are agreed upon, finalize the purchase agreement. Ensure that all specifications, pricing, and delivery terms are documented to avoid any misunderstandings later.
- Documentation: Keep records of all communications and agreements for future reference.
- Follow-Up: Establish a point of contact for any post-purchase inquiries or issues.
By following these steps, B2B buyers can streamline their sourcing process for DC power supplies, ensuring they select the best products for their needs while minimizing risks and optimizing costs.
Comprehensive Cost and Pricing Analysis for dc power supply Sourcing
What Are the Key Cost Components in DC Power Supply Manufacturing?
When sourcing DC power supplies, understanding the cost structure is crucial for making informed purchasing decisions. The primary cost components include:
-
Materials: This encompasses the raw materials required for manufacturing, such as semiconductors, capacitors, resistors, and printed circuit boards (PCBs). The quality and type of materials significantly impact the final product’s performance and durability.
-
Labor: Labor costs can vary based on the location of production. Regions with higher labor costs, such as parts of Europe, may result in higher overall prices. Conversely, sourcing from areas with lower labor costs can offer savings, but may come with trade-offs in quality and reliability.
-
Manufacturing Overhead: This includes expenses related to utilities, rent, and equipment maintenance. Efficient production processes can minimize overhead, positively affecting the pricing structure.
-
Tooling: Custom tooling is often required for specific designs or higher volumes. The initial investment in tooling can be significant, but it can be amortized over larger production runs, leading to lower per-unit costs.
-
Quality Control (QC): Implementing stringent QC processes ensures that products meet specified standards, which can add to the cost but reduces the risk of returns and warranty claims.
-
Logistics: Transportation and warehousing costs are essential components of the total cost. International buyers should consider the implications of shipping distances and methods on delivery timelines and expenses.
-
Margin: Suppliers will typically add a profit margin on top of their costs, which can vary significantly depending on the competitive landscape and demand.
How Do Price Influencers Affect DC Power Supply Sourcing?
Several factors can influence pricing when sourcing DC power supplies:
-
Volume and Minimum Order Quantity (MOQ): Suppliers often offer better pricing for larger orders. Understanding the MOQ can help buyers negotiate better rates and manage inventory more effectively.
-
Specifications and Customization: Customized solutions tailored to specific applications may incur additional costs. It’s essential to balance the need for tailored products with budget constraints.
-
Materials and Quality Certifications: Products with higher-quality materials or certifications (e.g., CE, FCC) typically command higher prices. Buyers should weigh the importance of these certifications against their requirements and budget.
-
Supplier Factors: The reputation and reliability of suppliers can significantly impact pricing. Established suppliers may charge a premium for their products due to their track record of quality and service.
-
Incoterms: Understanding Incoterms (International Commercial Terms) is vital for international transactions. They define the responsibilities of buyers and sellers regarding shipping, insurance, and tariffs, which can influence the final cost.
What Are the Best Negotiation Tips for International B2B Buyers?
Effective negotiation strategies can yield significant cost savings:
-
Research and Benchmarking: Collect data on pricing from multiple suppliers to establish a benchmark. This knowledge empowers buyers during negotiations.
-
Build Long-term Relationships: Establishing a partnership with suppliers can lead to better pricing, especially for repeat orders. Long-term relationships often foster trust and flexibility in negotiations.
-
Consider Total Cost of Ownership (TCO): Evaluate not only the initial purchase price but also ongoing costs, such as maintenance, energy efficiency, and potential downtime. A slightly higher upfront cost might result in lower TCO over time.
-
Leverage Volume Discounts: If possible, consolidate orders across multiple product lines to meet volume thresholds that unlock discounts.
-
Clarify Payment Terms: Negotiating favorable payment terms can improve cash flow and reduce upfront costs. Consider options like net 30 or net 60 terms.
What Pricing Nuances Should International Buyers Be Aware Of?
For international buyers, particularly from Africa, South America, the Middle East, and Europe, several nuances are crucial:
-
Currency Fluctuations: Be aware of exchange rates when sourcing from international suppliers. Currency volatility can significantly impact costs.
-
Import Tariffs and Duties: Understand the tariffs and duties applicable to imported goods in your country, as these can add substantial costs.
-
Cultural Differences in Negotiation: Different regions may have varying negotiation styles. Familiarizing yourself with local customs can facilitate smoother discussions.
Disclaimer on Indicative Prices
Prices for DC power supplies can fluctuate based on market conditions, supplier pricing strategies, and specific order requirements. Always request formal quotes and be prepared for negotiations to ensure the best possible deal.
Alternatives Analysis: Comparing dc power supply With Other Solutions
Exploring Alternatives to DC Power Supply Solutions
When considering power supply options for industrial applications, it’s crucial to evaluate the strengths and weaknesses of various technologies. While DC power supplies are widely used for their efficiency and reliability, several alternatives exist that may better suit specific operational needs. Below, we compare DC power supplies with two prominent alternatives: AC power supplies and battery systems.
Comparison Table of Power Supply Solutions
Comparison Aspect | DC Power Supply | AC Power Supply | Battery Systems |
---|---|---|---|
Performance | High efficiency; stable output | Versatile; can handle large loads | Portable; variable output |
Cost | Moderate initial investment; lower long-term costs | Typically lower upfront costs; higher operational costs | High initial costs; maintenance costs can vary |
Ease of Implementation | Requires specific installation | Easier to integrate into existing systems | Requires careful design for charging and discharging |
Maintenance | Low maintenance; long lifespan | Moderate; depends on technology used | Regular maintenance; lifespan dependent on usage |
Best Use Case | Electronics, telecommunication | Heavy machinery, lighting | Remote locations, backup power |
What Are the Advantages and Disadvantages of AC Power Supplies?
AC power supplies convert AC voltage into usable DC voltage for various applications. Their primary advantage lies in their ability to supply power over long distances without significant losses, making them ideal for industrial settings where large machinery operates. However, they generally require additional components to convert AC to DC, which can increase installation complexity and overall costs. Additionally, AC power supplies may not offer the same level of efficiency as dedicated DC supplies, particularly in low-voltage applications.
How Do Battery Systems Compare to DC Power Supplies?
Battery systems serve as a reliable alternative, especially in scenarios where portability and backup power are essential. They provide a steady DC output, similar to DC power supplies. The primary benefit of battery systems is their ability to operate independently of the grid, making them ideal for remote or off-grid applications. However, the initial investment can be substantial, and batteries require regular maintenance and eventual replacement, which can add to long-term operational costs. Moreover, the performance of battery systems can fluctuate based on charge cycles and environmental conditions.
Conclusion: How to Choose the Right Power Supply Solution for Your Needs
Selecting the right power supply solution for your business requires a careful analysis of your operational requirements and constraints. If your application demands high efficiency and stability, a DC power supply may be the best choice. On the other hand, if you are integrating into a system that primarily uses AC power, an AC supply could be more advantageous. For operations requiring mobility or backup capabilities, battery systems present a viable alternative, albeit with higher maintenance considerations. By evaluating these factors, international B2B buyers from regions like Africa, South America, the Middle East, and Europe can make informed decisions that align with their specific needs and operational goals.
Essential Technical Properties and Trade Terminology for dc power supply
What Are the Essential Technical Properties of DC Power Supplies?
When sourcing DC power supplies, understanding their technical properties is crucial for ensuring compatibility with your application. Here are some key specifications to consider:
-
Voltage Output (V)
Voltage output is the level of electrical potential that the power supply delivers. Common outputs range from 3V to 48V, with specialized units offering higher voltages. For B2B buyers, selecting the correct voltage output is essential to match the needs of your equipment. An improper voltage can lead to equipment failure or safety hazards. -
Amperage (A)
Amperage, or current output, indicates how much current the power supply can provide. This specification is often critical for applications requiring high power, such as industrial machinery or sensitive electronic devices. Buyers must ensure that the power supply’s amperage aligns with the operational requirements of their devices to avoid underperformance. -
Wattage (W)
Wattage is the product of voltage and amperage, representing the total power output. For example, a power supply rated at 12V and 5A can deliver up to 60W. Understanding wattage is vital for B2B buyers to ensure that the power supply can handle the total load without overheating or causing damage. -
Certifications and Compliance
Certifications such as CE, FCC, and UL indicate that the power supply has met specific safety and performance standards. For international buyers, these certifications can facilitate smoother trade and compliance with local regulations. It’s advisable to prioritize suppliers with reputable certifications to mitigate risks associated with safety and quality. -
Form Factor and Mounting Options
The physical design and mounting options (like rack mount, wall mount, or benchtop) can significantly affect installation and space management in facilities. Understanding the available form factors helps buyers select power supplies that fit seamlessly into existing setups without requiring extensive modifications.
What Are Common Trade Terms in the DC Power Supply Industry?
Familiarity with industry jargon can enhance communication and negotiation with suppliers. Here are some essential terms:
-
OEM (Original Equipment Manufacturer)
OEM refers to companies that produce components that are used in another company’s end product. For B2B buyers, partnering with OEMs can ensure high-quality components tailored to specific needs, leading to better performance and reliability. -
MOQ (Minimum Order Quantity)
MOQ is the smallest quantity of a product that a supplier is willing to sell. Understanding MOQ is crucial for buyers to manage inventory effectively. Negotiating MOQs can help reduce upfront costs, especially for smaller businesses or startups. -
RFQ (Request for Quotation)
An RFQ is a document that buyers send to suppliers to solicit price quotes for specific products. It often includes details about quantities and specifications. For international buyers, a well-structured RFQ can facilitate clearer communication and streamline the procurement process. -
Incoterms (International Commercial Terms)
Incoterms are standardized terms used in international trade to define the responsibilities of buyers and sellers regarding shipping, insurance, and tariffs. Understanding these terms helps buyers manage logistics and reduce potential disputes during the shipping process. -
Lead Time
Lead time refers to the time taken from placing an order to delivery. For B2B buyers, understanding lead times is essential for effective project planning and inventory management. Long lead times can affect production schedules, so it’s beneficial to discuss this upfront with suppliers. -
Warranty Period
The warranty period is the duration during which the manufacturer guarantees the product against defects. A solid warranty can provide peace of mind for buyers, ensuring support and possible replacement if issues arise.
By grasping these technical properties and trade terms, international B2B buyers can make informed decisions, enhance their purchasing strategies, and foster stronger relationships with suppliers in the DC power supply market.
Navigating Market Dynamics and Sourcing Trends in the dc power supply Sector
What Are the Current Market Dynamics and Key Trends in the DC Power Supply Sector?
The DC power supply sector is witnessing transformative changes driven by technological advancements and evolving market demands. Key global drivers include the rapid growth of renewable energy sources, particularly solar and wind, which necessitate efficient DC power solutions. Additionally, the increasing demand for electric vehicles (EVs) and energy storage systems is propelling the need for robust DC power supplies. B2B buyers, especially in emerging markets such as Africa, South America, and the Middle East, are focusing on acquiring reliable power solutions that can support these sustainable technologies.
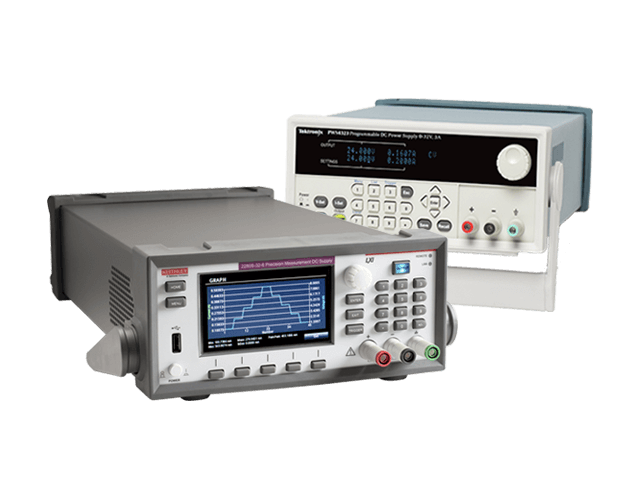
A stock image related to dc power supply.
Emerging trends in sourcing include a shift toward modular and customizable power supply solutions. This is particularly relevant for businesses that require specific configurations for unique applications, such as telecommunications, industrial automation, and medical devices. Buyers are increasingly favoring suppliers that offer advanced features such as programmable outputs and integrated power management systems. Furthermore, the rise of digital platforms for procurement is enabling buyers to easily compare products and suppliers, streamlining the sourcing process.
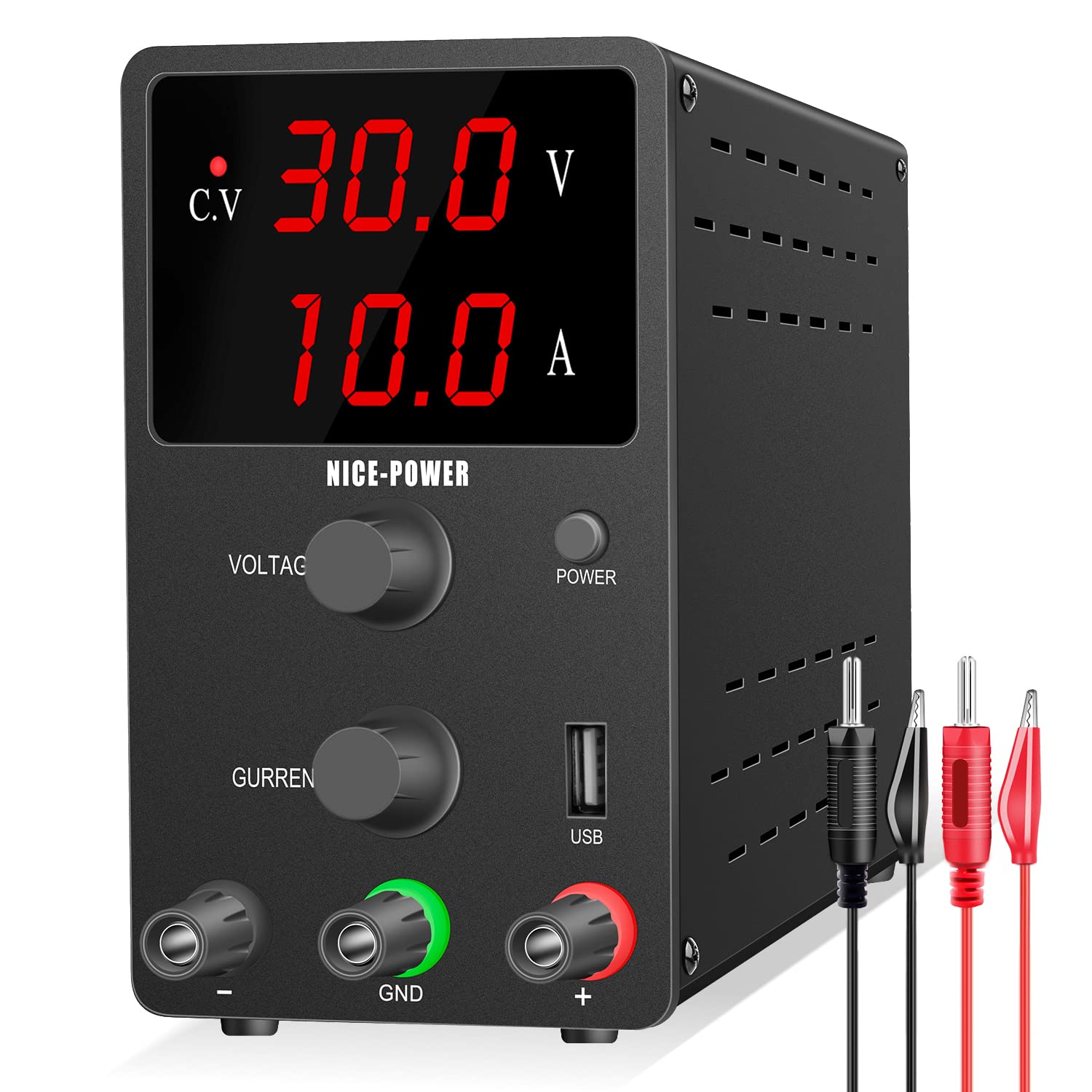
A stock image related to dc power supply.
Market dynamics are also influenced by regional factors. In Europe, stringent regulations around energy efficiency and sustainability are pushing manufacturers to innovate and provide more eco-friendly options. In contrast, markets in Africa and South America may prioritize affordability and availability, leading to different sourcing strategies. Understanding these regional nuances is crucial for international buyers looking to navigate the complexities of the DC power supply market.
How Is Sustainability Impacting Sourcing Trends in the DC Power Supply Sector?
Sustainability is becoming a paramount concern for B2B buyers in the DC power supply sector. The environmental impact of traditional power supply manufacturing processes is driving companies to seek out suppliers who prioritize ethical sourcing and sustainable practices. Buyers are increasingly demanding transparency in the supply chain, focusing on companies that can demonstrate adherence to environmental regulations and certifications.
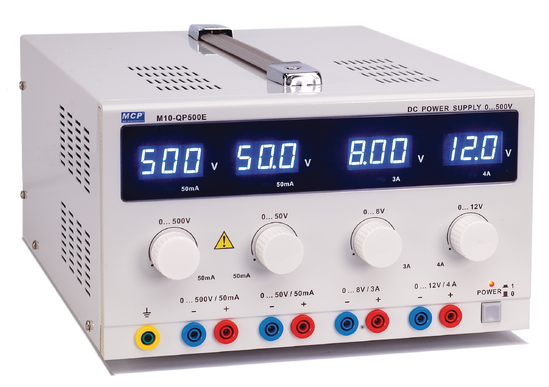
A stock image related to dc power supply.
Incorporating green certifications and materials is not just a trend; it is becoming a prerequisite for many international buyers. Certifications such as RoHS (Restriction of Hazardous Substances) and CE (Conformité Européenne) are indicators of a product’s compliance with environmental standards. Additionally, suppliers that utilize recycled materials or energy-efficient manufacturing processes are gaining a competitive edge in the marketplace.
The emphasis on ethical supply chains extends beyond just product sourcing; it includes the entire lifecycle of the product, from production to end-of-life disposal. This holistic approach is vital for companies aiming to enhance their corporate social responsibility (CSR) initiatives. Buyers are now more inclined to partner with suppliers who not only provide high-quality products but also align with their sustainability goals.
What Is the Evolution of the DC Power Supply Sector and Its Importance for B2B Buyers?
The DC power supply sector has evolved significantly from its early days of basic voltage regulation to the complex, high-efficiency systems we see today. Initially, DC power supplies were primarily used in laboratory and industrial applications. However, with advancements in technology, their applications have expanded into critical sectors such as telecommunications, medical equipment, and renewable energy systems.
The transition from linear to switching power supplies marked a significant turning point, offering higher efficiency and reduced size, which is crucial for modern applications. As a result, B2B buyers now have access to a wider range of products that cater to specific needs, such as compact designs for space-constrained environments or high-power solutions for industrial applications.
Understanding this evolution is essential for international buyers looking to make informed purchasing decisions. As the market continues to innovate, staying abreast of technological advancements and market trends will empower buyers to select the most suitable DC power supply solutions for their businesses.
Frequently Asked Questions (FAQs) for B2B Buyers of dc power supply
-
How do I choose the right DC power supply for my application?
Choosing the right DC power supply involves understanding your specific requirements, including voltage, current, and power ratings. Start by assessing the voltage range your application needs, then determine the maximum current draw. Consider factors such as the type of load (constant voltage vs. constant current), efficiency ratings, and whether you need features like adjustable outputs or programmability. Additionally, consider the environment where the power supply will be used, ensuring it meets any necessary certifications for safety and compliance relevant to your region. -
What is the best DC power supply for industrial applications?
For industrial applications, look for DC power supplies that offer robust performance, high efficiency, and reliability. Switching power supplies are often preferred due to their compact size and efficiency, especially in high-power applications. Key features to consider include overload protection, thermal shutdown, and wide input voltage ranges. Brands with a proven track record and certifications such as CE, UL, or RoHS compliance are recommended to ensure quality and safety. Additionally, consider the availability of technical support and warranty options. -
What are the typical minimum order quantities (MOQs) for DC power supplies?
Minimum order quantities (MOQs) for DC power supplies can vary significantly based on the manufacturer and the type of supply. Standard models may have lower MOQs, often ranging from 10 to 100 units, while custom solutions may require higher MOQs due to the complexities involved in production. When sourcing from suppliers in regions such as Africa, South America, or the Middle East, it’s essential to communicate your needs clearly and negotiate terms that are favorable for your business, especially if you are a smaller buyer. -
How can I vet suppliers for DC power supplies in international markets?
Vetting suppliers for DC power supplies involves several steps. Start by researching their reputation and customer reviews online. Request references from other clients to gauge reliability and quality. Verify their certifications and compliance with international standards. Additionally, consider visiting their manufacturing facilities if possible, or using third-party inspection services. It’s also advisable to assess their responsiveness and customer service capabilities, as these can be indicative of their overall professionalism and reliability. -
What payment terms should I negotiate when sourcing DC power supplies?
When sourcing DC power supplies, common payment terms include advance payment, letter of credit, or net 30/60 days after delivery. Depending on your relationship with the supplier and the size of the order, you may negotiate a deposit upfront with the balance due upon delivery. Ensure that payment methods are secure and that you understand any fees associated with international transactions. Establishing clear payment terms can help mitigate risks and foster a more trustworthy relationship with your supplier. -
How can I ensure quality assurance for DC power supplies?
To ensure quality assurance for DC power supplies, request detailed specifications and compliance certifications from your suppliers. Establish quality control protocols, including pre-shipment inspections, to verify product specifications against your requirements. You may also consider implementing a warranty clause that covers defects and performance issues. Regular communication with the supplier regarding quality standards and expectations can help maintain product integrity and foster a collaborative relationship. -
What logistics considerations should I keep in mind when importing DC power supplies?
Logistics considerations for importing DC power supplies include understanding shipping methods, customs regulations, and potential tariffs. Choose a reliable freight forwarder with experience in handling electronic components. Ensure that the supplier provides all necessary documentation, including invoices, packing lists, and certificates of origin. Familiarize yourself with import regulations in your country to avoid delays. Additionally, consider warehousing options if you anticipate high inventory turnover or need to manage stock levels effectively. -
Are there customization options available for DC power supplies?
Many suppliers offer customization options for DC power supplies to meet specific application requirements. Customization can include adjusting output voltage and current, adding additional features such as programmable settings, or modifying the physical design for specific installations. When discussing customization, provide detailed specifications and communicate your needs clearly to the supplier. Be aware that custom solutions may have longer lead times and higher costs, so plan accordingly in your procurement process.
Important Disclaimer & Terms of Use
⚠️ Important Disclaimer
The information provided in this guide, including content regarding manufacturers, technical specifications, and market analysis, is for informational and educational purposes only. It does not constitute professional procurement advice, financial advice, or legal advice.
While we have made every effort to ensure the accuracy and timeliness of the information, we are not responsible for any errors, omissions, or outdated information. Market conditions, company details, and technical standards are subject to change.
B2B buyers must conduct their own independent and thorough due diligence before making any purchasing decisions. This includes contacting suppliers directly, verifying certifications, requesting samples, and seeking professional consultation. The risk of relying on any information in this guide is borne solely by the reader.
Strategic Sourcing Conclusion and Outlook for dc power supply
In the evolving landscape of DC power supply sourcing, international B2B buyers must prioritize strategic sourcing to secure high-quality, cost-effective solutions. By leveraging global suppliers from regions such as Africa, South America, the Middle East, and Europe, businesses can tap into diverse product offerings that meet their specific operational needs. Understanding the technical specifications, certifications, and application suitability of various power supply models is crucial. This knowledge not only aids in making informed purchasing decisions but also enhances the reliability and efficiency of electrical systems.
As the demand for energy-efficient solutions grows, strategic partnerships with manufacturers who emphasize innovation and sustainability become increasingly valuable. Buyers should explore custom power supply options that cater to unique requirements, ensuring flexibility and adaptability in their operations.
Looking ahead, the focus on renewable energy sources and advanced technologies will shape the future of DC power supply solutions. B2B buyers are encouraged to stay ahead of industry trends, engage with suppliers who prioritize innovation, and consider how emerging technologies can enhance their operations. By doing so, they will not only enhance their competitive advantage but also contribute to a more sustainable energy future.