Your Ultimate Guide to Sourcing Ceramic Cnc Machining
Introduction: Navigating the Global Market for ceramic cnc machining
In the ever-evolving landscape of manufacturing, ceramic CNC machining stands out as a critical process that combines precision engineering with the unique properties of ceramics. Renowned for their exceptional hardness, thermal resistance, and chemical stability, ceramics are indispensable in industries ranging from aerospace to electronics and medical devices. However, the complexities involved in machining these brittle materials require specialized knowledge and advanced technology, making it essential for international B2B buyers to navigate this niche market effectively.
This comprehensive guide delves into the multifaceted world of ceramic CNC machining, providing insights into the various types of ceramics, their key properties, and the machining processes that yield high-quality components. It covers essential aspects such as manufacturing workflows, quality control standards, and supplier evaluation techniques, empowering procurement teams to identify reliable partners. Additionally, the guide addresses critical cost factors and market dynamics relevant to regions like Africa, South America, the Middle East, and Europe, ensuring that buyers can make informed decisions tailored to their unique needs.
By equipping B2B buyers with actionable insights and practical strategies, this resource aims to facilitate efficient sourcing and risk management, ultimately driving value and innovation in the global ceramic CNC machining market.
Understanding ceramic cnc machining Types and Variations
Type Name | Key Distinguishing Features | Primary B2B Applications | Brief Pros & Cons for Buyers |
---|---|---|---|
Alumina CNC Machining | High hardness, excellent wear resistance, and thermal stability. | Aerospace components, cutting tools, insulators. | Pros: Durable and cost-effective; Cons: Brittle, requires careful handling. |
Zirconia CNC Machining | Enhanced toughness, phase transformation toughening. | Dental implants, medical devices, wear parts. | Pros: High toughness; Cons: Higher cost, complex machining process. |
Silicon Carbide CNC Machining | Exceptional thermal conductivity and hardness. | Semiconductor applications, cutting tools. | Pros: High-performance in extreme conditions; Cons: Limited supplier availability. |
Boron Carbide CNC Machining | One of the hardest materials, exceptional wear resistance. | Body armor, abrasive tools, industrial applications. | Pros: Superior hardness; Cons: Very expensive, specialized machining required. |
Ceramic Composite CNC Machining | Combination of ceramics with other materials for enhanced properties. | Aerospace, automotive, electronics. | Pros: Tailored properties; Cons: Complexity in sourcing and production. |
Alumina CNC Machining
Alumina, or aluminum oxide, is a widely used ceramic in CNC machining due to its high hardness and wear resistance. It is particularly suitable for applications requiring durability, such as aerospace components and cutting tools. When sourcing alumina CNC machined parts, buyers should ensure that the supplier can meet stringent quality standards, especially regarding brittleness, which necessitates careful handling and specific machining techniques.
Zirconia CNC Machining
Zirconia is known for its remarkable toughness and resistance to crack propagation, making it a preferred choice for applications such as dental implants and medical devices. The phase transformation toughening mechanism of zirconia allows it to withstand high stress, but this complexity can lead to higher costs and more intricate machining processes. Buyers should consider the supplier’s expertise in handling zirconia to ensure quality and precision in the final product.
Silicon Carbide CNC Machining
Silicon carbide (SiC) is notable for its exceptional thermal conductivity and hardness, making it ideal for high-performance applications, particularly in the semiconductor industry and cutting tools. While SiC can maintain integrity under extreme conditions, buyers may find a limited number of suppliers capable of machining this material effectively. It is crucial to evaluate supplier capabilities and ensure they can meet the specific requirements for SiC components.
Boron Carbide CNC Machining
Boron carbide is one of the hardest known materials and is utilized in applications where extreme durability is necessary, such as body armor and abrasive tools. Its superior hardness comes at a cost, as it is one of the more expensive ceramic materials to machine. Buyers should weigh the benefits of its exceptional wear resistance against the higher price and ensure that suppliers have the specialized skills needed for machining boron carbide.
Ceramic Composite CNC Machining
Ceramic composites combine ceramics with other materials to enhance specific properties, such as toughness and thermal stability. These composites are increasingly used in advanced industries like aerospace and automotive, where tailored performance is crucial. However, sourcing these materials can be complex due to the variety of combinations available. Buyers should engage with suppliers who have experience in producing ceramic composites to ensure they receive products that meet their unique specifications.
Key Industrial Applications of ceramic cnc machining
Industry/Sector | Specific Application of Ceramic CNC Machining | Value/Benefit for the Business | Key Sourcing Considerations for this Application |
---|---|---|---|
Aerospace | Engine components (e.g., turbine blades) | High-temperature stability and weight reduction | Supplier must demonstrate expertise in high-precision machining and material properties. |
Medical Devices | Dental implants and surgical instruments | Biocompatibility and durability | Compliance with medical standards and certifications is crucial. Verify quality control processes. |
Electronics | Insulators and substrates for circuit boards | Excellent electrical insulation and thermal resistance | Ensure sourcing from suppliers with capabilities in fine tolerances and surface finishes. |
Automotive | Cutting tools and wear-resistant components | Enhanced performance and longevity | Look for suppliers with experience in high-volume production and stringent quality assurance. |
Chemical Processing | Reaction vessels and components | Corrosion resistance and chemical stability | Evaluate suppliers on their ability to meet specific chemical resistance requirements. |
In the aerospace industry, ceramic CNC machining is integral for manufacturing high-performance engine components, such as turbine blades. These components benefit from ceramics’ excellent high-temperature stability, which is vital for maintaining performance in extreme conditions. B2B buyers should prioritize suppliers with proven experience in high-precision machining and a deep understanding of material properties to ensure reliability and safety in aerospace applications.
Within the medical devices sector, ceramic CNC machining is used to create dental implants and surgical instruments. The biocompatibility and durability of ceramics make them ideal for applications where human contact is critical. International buyers must ensure that suppliers comply with relevant medical standards and certifications, verifying their quality control processes to guarantee the safety and efficacy of the medical devices produced.
In the electronics sector, ceramics are machined into insulators and substrates for circuit boards. The ability of ceramics to provide excellent electrical insulation and thermal resistance allows for the development of more efficient electronic components. Buyers should seek suppliers capable of achieving fine tolerances and high-quality surface finishes, as these factors significantly impact the performance and reliability of electronic devices.
The automotive industry utilizes ceramic CNC machining for cutting tools and wear-resistant components, which enhance performance and longevity. The high hardness and wear resistance of ceramic materials allow for increased efficiency in machining operations. When sourcing, buyers should focus on suppliers experienced in high-volume production, ensuring they adhere to stringent quality assurance protocols to meet industry standards.
In chemical processing, ceramic CNC machining is employed to manufacture reaction vessels and other components that require corrosion resistance and chemical stability. The exceptional properties of ceramics make them suitable for handling aggressive chemicals, ensuring the integrity of processing equipment. Buyers should evaluate suppliers based on their ability to meet specific chemical resistance requirements, as well as their experience in producing custom solutions for the chemical industry.
Related Video: Insanely Fast CNC Machining Inconel 625 w/ Ceramic End Mills | Pushing UMC-750SS to the Limit
Strategic Material Selection Guide for ceramic cnc machining
When selecting materials for ceramic CNC machining, it is essential to consider the unique properties and applications of various ceramic types. Below, we analyze four common ceramic materials, focusing on their key properties, advantages and disadvantages, and implications for international B2B buyers.
1. Alumina (Al₂O₃)
Key Properties: Alumina is renowned for its high hardness (up to 20 GPa Vickers hardness) and excellent wear resistance. It can withstand temperatures exceeding 2050°C and is chemically stable against many corrosive substances.
Pros & Cons: The durability of alumina makes it ideal for applications requiring long-lasting components, such as cutting tool inserts. However, its brittleness can complicate machining processes, necessitating specialized tools and techniques. Additionally, the cost of alumina can be moderate to high, depending on purity and form.
Impact on Application: Alumina is widely used in industries like aerospace and electronics, where components must endure harsh environments. Its compatibility with various media makes it suitable for chemical processing applications.
Considerations for International Buyers: Buyers must ensure compliance with international standards such as ASTM and DIN for quality assurance. Understanding local sourcing options and logistics is crucial, especially in regions like Africa and South America, where supply chain complexities may arise.
2. Zirconia (ZrO₂)
Key Properties: Zirconia exhibits a unique phase transformation toughening mechanism, providing enhanced toughness compared to other ceramics. It can withstand high temperatures and is resistant to wear and corrosion.
Pros & Cons: The toughness of zirconia makes it suitable for demanding applications, such as dental implants and cutting tools. However, its higher cost compared to alumina can be a barrier for some buyers. Additionally, machining zirconia requires advanced techniques to avoid cracking.
Impact on Application: Zirconia is particularly valuable in medical applications where durability and biocompatibility are essential. Its resistance to thermal shock also makes it suitable for high-temperature environments.
Considerations for International Buyers: Buyers should verify that suppliers can meet specific quality standards and certifications, especially in the medical field. Understanding the regional market dynamics in Europe and the Middle East can help buyers identify reliable sources.
3. Silicon Carbide (SiC)
Key Properties: Silicon carbide is known for its exceptional hardness and thermal conductivity, making it ideal for high-speed cutting applications. It can operate effectively at temperatures exceeding 1600°C.
Pros & Cons: The high thermal conductivity of SiC allows for effective heat dissipation, which is beneficial in machining operations. However, its brittleness and the complexity of machining processes can lead to higher manufacturing costs.
Impact on Application: SiC is commonly used in the semiconductor industry and for high-performance cutting tools. Its compatibility with high-temperature environments makes it suitable for aerospace and automotive applications.
Considerations for International Buyers: Buyers should be aware of the specific machining requirements for SiC to ensure quality outcomes. Compliance with international standards is critical, particularly for industries like aerospace, where safety regulations are stringent.
4. Boron Carbide (B₄C)
Key Properties: Boron carbide is one of the hardest materials available, second only to diamond, and offers excellent wear resistance and chemical stability.
Pros & Cons: Its extreme hardness makes boron carbide ideal for abrasive applications and body armor. However, the high cost and complexity of machining this material can limit its use in some applications.
Impact on Application: Boron carbide is primarily used in military and industrial applications where extreme wear resistance is crucial. Its chemical stability makes it suitable for harsh environments.
Considerations for International Buyers: Buyers should consider the availability of specialized suppliers capable of machining boron carbide. Understanding the procurement landscape in regions like Africa and South America can help mitigate risks associated with sourcing this high-cost material.
Summary Table
Material | Typical Use Case for ceramic cnc machining | Key Advantage | Key Disadvantage/Limitation | Relative Cost (Low/Med/High) |
---|---|---|---|---|
Alumina | Cutting tool inserts, aerospace components | High hardness and wear resistance | Brittle, requires specialized machining | Medium |
Zirconia | Dental implants, cutting tools | High toughness and thermal stability | Higher cost, complex machining | High |
Silicon Carbide | High-speed cutting tools, semiconductors | Excellent thermal conductivity | Brittle, higher manufacturing costs | High |
Boron Carbide | Body armor, abrasive tools | Extreme hardness and wear resistance | High cost, complex machining | High |
This strategic material selection guide provides B2B buyers with critical insights into the properties, advantages, and challenges associated with ceramic materials used in CNC machining. Understanding these factors can help buyers make informed decisions that align with their specific application needs and regional market conditions.
In-depth Look: Manufacturing Processes and Quality Assurance for ceramic cnc machining
Ceramic CNC machining is a meticulous process that involves several stages, from material preparation to final quality assurance. For international B2B buyers, especially those in Africa, South America, the Middle East, and Europe, understanding these processes and the corresponding quality assurance measures is essential for sourcing high-quality ceramic components.
Manufacturing Processes
1. Material Preparation
The first step in ceramic CNC machining is material preparation. The primary materials used include various types of ceramics such as alumina, zirconia, silicon carbide, and boron carbide. Each of these materials offers distinct properties that influence their machinability and application.
- Selection of Raw Material: Buyers must ensure that the selected ceramic material meets the required specifications for hardness, thermal stability, and chemical resistance.
- Powder Processing: The raw materials are often processed into fine powders to achieve a uniform particle size, which is crucial for consistency in the final product.
2. Forming
Once the material is prepared, the next step involves shaping the ceramic into the desired form.
- Pressing: Powdered ceramics are typically formed using uniaxial or isostatic pressing. This process compacts the powder into a mold, creating a green body that retains its shape until sintering.
- Injection Molding: For more complex geometries, injection molding may be used, allowing for greater design flexibility.
3. Sintering
After forming, the green body undergoes sintering, a critical step that enhances the material properties.
- High-Temperature Sintering: The formed ceramic is heated to high temperatures, causing particles to bond and eliminate porosity. This step is vital for achieving the desired hardness and strength of the ceramic.
- Controlled Atmosphere: The sintering process often occurs in a controlled atmosphere to prevent oxidation or contamination.
4. Machining
Once sintered, the ceramic component can be machined using CNC techniques.
- CNC Machining: Advanced CNC machines equipped with diamond tools are employed to achieve precise dimensions and tolerances. Multi-axis machining is commonly used for intricate designs.
- Cooling Techniques: To manage heat generation during machining, effective cooling techniques, such as mist cooling or air cooling, are utilized.
5. Finishing
The final stage involves surface finishing to meet specific requirements.
- Grinding and Polishing: Surface grinding and polishing ensure that the components achieve the required surface finish and dimensional accuracy. This step is crucial for applications in industries like aerospace and medical devices.
- Coating: In some cases, additional coatings may be applied to enhance properties like wear resistance or chemical stability.
Quality Assurance
Quality assurance in ceramic CNC machining is paramount, particularly for international buyers who must adhere to various standards and regulations.
International Standards
B2B buyers should be familiar with relevant international quality standards, such as:
- ISO 9001: This standard specifies requirements for a quality management system (QMS) and is essential for ensuring consistent product quality.
- ISO 13485: For medical applications, this standard focuses on quality management systems specific to medical devices.
- CE Marking: In Europe, products must meet safety, health, and environmental protection requirements to obtain CE marking.
Quality Control Checkpoints
Quality control is typically divided into several checkpoints throughout the manufacturing process:
- Incoming Quality Control (IQC): At this stage, raw materials are inspected for compliance with specifications. This includes checking for consistency in size, shape, and composition.
- In-Process Quality Control (IPQC): During machining, regular checks are made to ensure that the processes remain within specified parameters. This may include monitoring machine performance and tool wear.
- Final Quality Control (FQC): After machining, the finished product undergoes thorough inspections, including dimensional checks, surface finish assessments, and functional testing.
Common Testing Methods
Several testing methods are employed to verify the quality of ceramic components:
- Mechanical Testing: This includes hardness tests, flexural strength tests, and wear resistance evaluations.
- Dimensional Inspection: Laser scanning and coordinate measuring machines (CMM) are used to ensure that components meet precise tolerances.
- Non-Destructive Testing (NDT): Techniques such as ultrasonic testing or X-ray inspection can identify internal defects without damaging the product.
Verifying Supplier Quality Control
For B2B buyers, verifying a supplier’s quality control processes is crucial to mitigate risks associated with international sourcing.
- Supplier Audits: Conducting on-site audits allows buyers to assess the supplier’s manufacturing capabilities, quality management systems, and adherence to international standards.
- Quality Reports: Requesting detailed quality reports and certifications can provide insights into the supplier’s compliance with relevant standards.
- Third-Party Inspections: Engaging third-party inspection agencies can offer an unbiased assessment of the supplier’s quality assurance processes and product quality.
Regional Considerations for B2B Buyers
When sourcing ceramic CNC machining services, international buyers should consider regional nuances:
- Cultural and Regulatory Differences: Understanding local regulations and cultural expectations can facilitate smoother transactions and build trust with suppliers.
- Logistics and Supply Chain: Buyers must assess logistics capabilities, including shipping times, customs regulations, and potential tariffs, which can affect lead times and costs.
In conclusion, the manufacturing processes and quality assurance measures in ceramic CNC machining are complex and require careful consideration by international B2B buyers. By understanding these processes and implementing rigorous quality checks, buyers can ensure they receive high-quality ceramic components that meet their specific needs.
Related Video: Ceramic tiles manufacturing process by Ceratec – How it’s made?
Comprehensive Cost and Pricing Analysis for ceramic cnc machining Sourcing
Ceramic CNC machining is a specialized process that involves intricate cost structures and pricing dynamics, essential for international B2B buyers. Understanding these elements can significantly enhance decision-making and sourcing strategies, especially for buyers in Africa, South America, the Middle East, and Europe.
Cost Components
The total cost of sourcing ceramic CNC machined parts can be broken down into several key components:
-
Materials: The choice of ceramic material, such as alumina or zirconia, directly impacts pricing. High-performance materials typically cost more due to their superior properties and processing requirements.
-
Labor: Skilled labor is essential for CNC machining, particularly when working with brittle ceramics. The labor cost can vary significantly based on the complexity of the machining operation and the expertise required.
-
Manufacturing Overhead: This includes costs associated with facility maintenance, utilities, and administrative expenses. Given the specialized nature of ceramic machining, overheads can be higher than for standard machining processes.
-
Tooling: Ceramic materials require specialized cutting tools that can withstand high wear rates. Tooling costs can be substantial, especially for custom or high-precision applications.
-
Quality Control (QC): Ensuring that ceramic components meet stringent quality standards incurs additional costs. This includes testing for tolerances, surface finishes, and material integrity.
-
Logistics: Shipping and handling costs must be considered, especially for international transactions. Factors such as distance, shipping methods, and customs duties can significantly affect overall expenses.
-
Margin: Suppliers will include a profit margin in their pricing, which can vary widely based on market conditions and the supplier’s positioning.
Price Influencers
Several factors can influence the pricing of ceramic CNC machined parts:
-
Volume/MOQ: Higher order volumes typically lead to lower per-unit costs due to economies of scale. Buyers should negotiate minimum order quantities (MOQ) to optimize pricing.
-
Specifications/Customization: Custom designs or specific tolerances can increase costs. Providing detailed specifications upfront can help mitigate unexpected price increases.
-
Materials: The type of ceramic selected not only affects performance but also the price. Non-oxide ceramics like silicon carbide can be more costly than traditional oxides.
-
Quality/Certifications: Suppliers with ISO certifications or other quality assurances may charge a premium, but this investment can pay off in reliability and performance.
-
Supplier Factors: The supplier’s location, reputation, and capacity to deliver on time can influence pricing. Buyers should assess the total value offered by potential suppliers.
-
Incoterms: Understanding Incoterms is crucial for international buyers. They define the responsibilities of buyers and sellers regarding shipping costs, risk, and insurance, which can significantly affect overall pricing.
Buyer Tips
For international B2B buyers, particularly from diverse regions like Africa and South America, here are some strategic insights:
-
Negotiation: Leverage your position as a buyer to negotiate better terms, especially on volume orders. Building long-term relationships with suppliers can also yield better pricing and service.
-
Cost-Efficiency: Focus on the Total Cost of Ownership (TCO) rather than just the upfront price. Consider factors such as durability, maintenance, and replacement costs when evaluating ceramic parts.
-
Pricing Nuances: Be aware of currency fluctuations and regional pricing disparities. Engaging with local suppliers may reduce logistics costs and simplify the purchasing process.
-
Market Research: Conduct thorough market research to identify trends and average pricing in your region. This knowledge can empower you during negotiations and supplier selection.
In conclusion, understanding the comprehensive cost structure and pricing dynamics of ceramic CNC machining is crucial for B2B buyers. By considering these factors and implementing strategic purchasing practices, buyers can enhance their sourcing outcomes and achieve significant value in their supply chains.
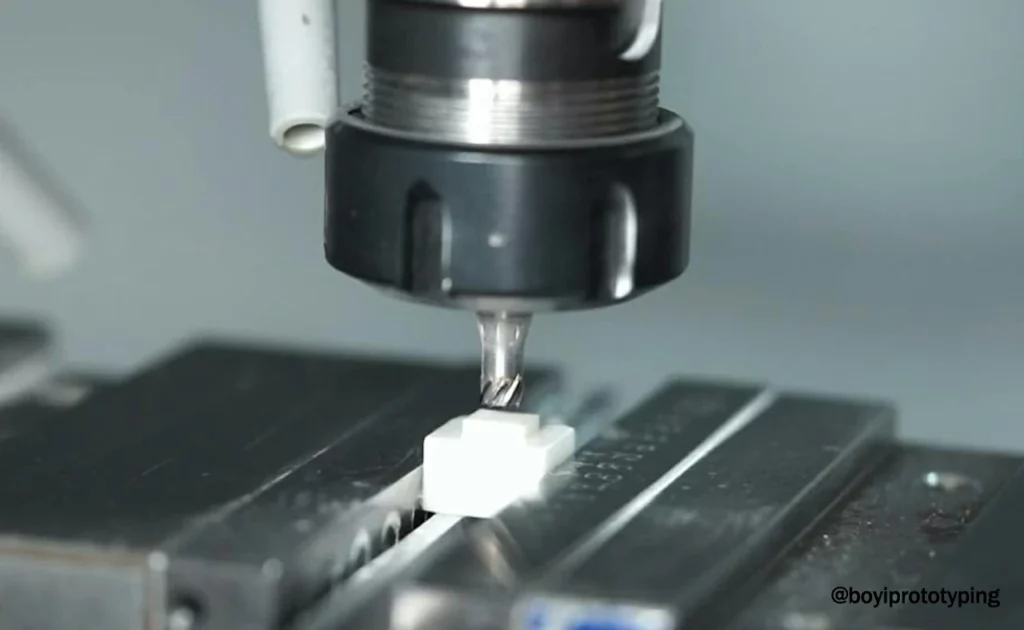
Illustrative Image (Source: Google Search)
- Disclaimer: Prices and costs mentioned in this analysis are indicative and may vary based on market conditions and specific project requirements.*
Spotlight on Potential ceramic cnc machining Manufacturers and Suppliers
This section looks at several manufacturers active in the ‘ceramic cnc machining’ market. This is a representative sample for illustrative purposes; B2B buyers must conduct extensive due diligence before any transaction. Information is synthesized from public sources and general industry knowledge.
Essential Technical Properties and Trade Terminology for ceramic cnc machining
Ceramic CNC machining is a complex process that demands a solid understanding of specific technical properties and trade terminology. For international B2B buyers, especially from Africa, South America, the Middle East, and Europe, grasping these concepts is crucial for informed purchasing decisions. Below is a detailed overview of the essential technical properties and industry terminology relevant to ceramic CNC machining.
Key Technical Properties
- Material Grade
– The classification of ceramic materials based on their composition and properties. Common grades include alumina, zirconia, and silicon carbide.
– B2B Importance: Selecting the appropriate material grade is essential for ensuring that the final product meets the specific performance requirements of applications, such as wear resistance and thermal stability.
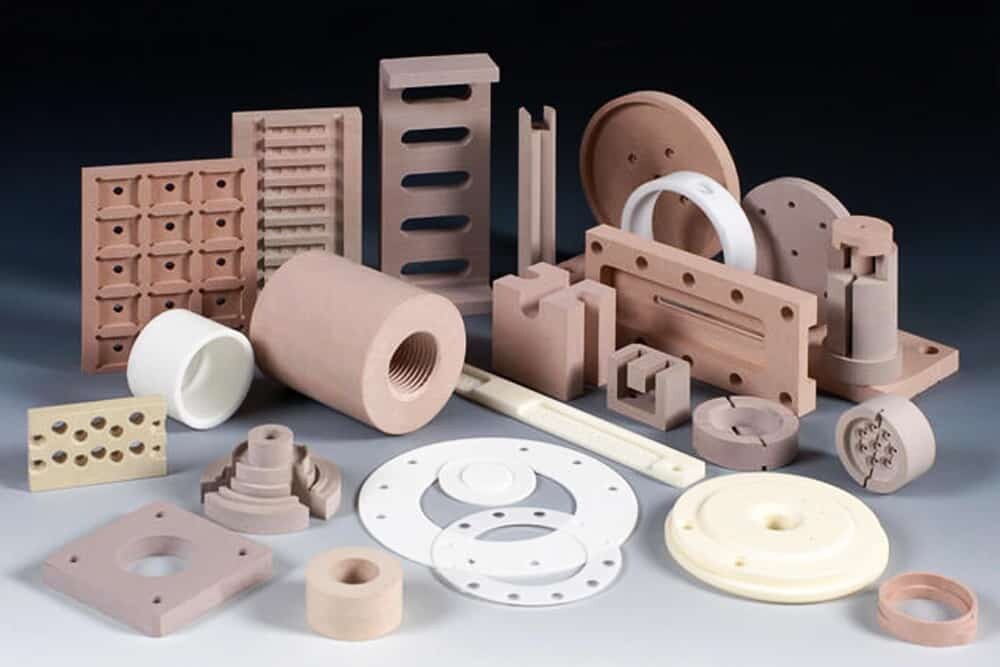
Illustrative Image (Source: Google Search)
-
Tolerance
– This refers to the permissible limit of variation in a physical dimension. In ceramic machining, tolerances can be very tight, often within ±0.01 mm.
– B2B Importance: High tolerance levels are critical for ensuring that components fit precisely in their intended applications, which is vital in industries like aerospace and medical devices where safety and functionality are paramount. -
Surface Finish
– The texture and smoothness of a machined surface, typically measured in microns. Common finishes include Ra (average roughness) values.
– B2B Importance: A superior surface finish can enhance the performance and longevity of ceramic components, especially in applications that experience friction or contact with other materials. -
Thermal Stability
– The ability of ceramic materials to withstand high temperatures without significant degradation. Many ceramics can perform effectively at temperatures exceeding 1000°C.
– B2B Importance: Understanding thermal stability is crucial for applications in industries like aerospace and automotive, where components are subjected to extreme thermal conditions. -
Brittleness
– A characteristic of ceramics that makes them prone to fracture under tensile stress.
– B2B Importance: Buyers must consider brittleness when designing components to avoid failure in high-stress applications, necessitating careful selection of machining techniques and tools. -
Chemical Resistance
– The ability of ceramics to resist degradation from corrosive substances, including acids and bases.
– B2B Importance: This property is vital for applications in chemical processing industries, ensuring that components maintain their integrity over time.
Common Trade Terminology
-
OEM (Original Equipment Manufacturer)
– A company that produces parts or equipment that may be marketed by another manufacturer. In the context of ceramics, an OEM might create components for various applications.
– Importance: Identifying OEMs can streamline sourcing processes, ensuring that quality standards are met consistently. -
MOQ (Minimum Order Quantity)
– The smallest quantity of a product that a supplier is willing to sell.
– Importance: Understanding MOQ is essential for budgeting and inventory management, especially for small to medium enterprises looking to minimize upfront costs. -
RFQ (Request for Quotation)
– A document sent to suppliers to solicit price quotes for specific goods or services.
– Importance: An effective RFQ process helps buyers obtain competitive pricing and assess supplier capabilities before making purchasing decisions. -
Incoterms (International Commercial Terms)
– A series of predefined commercial terms published by the International Chamber of Commerce, used in international contracts.
– Importance: Familiarity with Incoterms is crucial for understanding shipping responsibilities, costs, and risks, facilitating smoother international transactions. -
CNC (Computer Numerical Control)
– Refers to the automated control of machining tools by means of a computer. CNC machining allows for precise and repeatable manufacturing of complex parts.
– Importance: Recognizing the capabilities of CNC technology helps buyers evaluate supplier offerings and ensure they meet technical specifications. -
Lead Time
– The total time it takes from placing an order to the delivery of the product.
– Importance: Understanding lead times is critical for planning production schedules and managing inventory effectively, especially in fast-paced industries.
By familiarizing themselves with these technical properties and trade terms, B2B buyers can navigate the complexities of ceramic CNC machining more effectively, ensuring that they make informed decisions that align with their operational needs and strategic goals.
Navigating Market Dynamics, Sourcing Trends, and Sustainability in the ceramic cnc machining Sector
Market Overview & Key Trends
The ceramic CNC machining sector is experiencing a transformative phase driven by several global trends that impact international B2B buyers. One of the primary drivers is the increasing demand for high-performance materials across diverse industries such as aerospace, automotive, and electronics. Ceramics, known for their hardness, thermal resistance, and chemical stability, are becoming essential components in advanced applications. Emerging technologies like automation and Industry 4.0 are reshaping sourcing strategies, allowing buyers to leverage digital platforms for enhanced supplier discovery, real-time tracking, and data analytics.
Furthermore, a notable trend is the shift towards customization and rapid prototyping. International buyers are seeking suppliers who can provide tailored solutions that meet specific requirements while maintaining high precision and quality standards. This demand for agility in manufacturing processes is compelling CNC machining companies to invest in advanced machinery and skilled labor.
In regions such as Africa and South America, local sourcing initiatives are gaining momentum, driven by a desire to reduce lead times and transportation costs. Meanwhile, buyers in Europe and the Middle East are increasingly focused on sourcing from suppliers that comply with rigorous quality certifications, ensuring that products meet international standards. Understanding these dynamics is crucial for procurement professionals aiming to optimize their supply chain and enhance competitiveness in the global market.
Sustainability & Ethical Sourcing in B2B
Sustainability is becoming a pivotal consideration in the ceramic CNC machining sector, with international buyers increasingly prioritizing environmentally responsible sourcing practices. The environmental impact of ceramic production, including energy consumption and waste generation, necessitates a focus on sustainable manufacturing processes. Buyers should seek suppliers that employ energy-efficient technologies and minimize waste through recycling and reuse of materials.
The importance of ethical supply chains cannot be overstated, as consumers and businesses alike demand transparency and responsibility from manufacturers. This trend is particularly evident in regions like Europe, where regulatory frameworks are pushing companies to disclose their sustainability practices. Suppliers offering “green” certifications, such as ISO 14001 for environmental management, can provide assurance to buyers about their commitment to sustainable practices.
Moreover, exploring alternative materials that are less harmful to the environment can further enhance a company’s sustainability profile. For example, the use of eco-friendly ceramics or composites that reduce the carbon footprint during production is gaining traction. By prioritizing sustainability and ethical sourcing, international B2B buyers can not only meet regulatory requirements but also enhance their brand reputation and appeal to environmentally-conscious customers.
Brief Evolution/History
The evolution of ceramic CNC machining has been marked by significant advancements in technology and material science. Initially, ceramics were primarily shaped through traditional methods such as pressing and sintering. However, the introduction of CNC machining techniques in the late 20th century revolutionized the sector, allowing for greater precision and complexity in ceramic component manufacturing.
Today, the integration of computer-aided design (CAD) and computer-aided manufacturing (CAM) software has further streamlined production processes. This evolution has enabled manufacturers to produce intricate designs and high-tolerance components that were previously unattainable. As the industry continues to evolve, innovations in ceramic materials and machining technologies are poised to drive further growth and efficiency, presenting new opportunities for international B2B buyers.
Related Video: Machining INCONEL 718 with Ceramics | DVF 5000 | DN Solutions
Frequently Asked Questions (FAQs) for B2B Buyers of ceramic cnc machining
-
What should I consider when vetting suppliers for ceramic CNC machining?
When vetting suppliers, assess their experience in ceramic CNC machining and their ability to meet your specific requirements. Look for certifications such as ISO 9001, which indicates a commitment to quality management. Review their portfolio for past projects and client testimonials to gauge reliability. Furthermore, inquire about their machining capabilities, equipment, and workforce expertise. A supplier’s ability to provide technical support and respond to challenges quickly can also influence the partnership’s success. -
Can I customize ceramic components, and what are the limitations?
Yes, customization of ceramic components is possible, but it is essential to communicate your specifications clearly. Discuss design elements such as dimensions, tolerances, and surface finishes with your supplier early in the process. Limitations may arise from the material properties of ceramics, such as brittleness and hardness, which could restrict complex geometries or specific machining techniques. Collaborating closely with the supplier can help identify viable custom solutions while adhering to your performance needs. -
What are typical minimum order quantities (MOQs) and lead times for ceramic CNC machining?
MOQs and lead times can vary significantly based on the supplier and the complexity of the components. Generally, MOQs for ceramic CNC machining can range from 50 to several hundred units, depending on the specific material and process. Lead times typically fall between 4 to 8 weeks, but this can be extended for more intricate designs or larger orders. Always discuss your project timelines with potential suppliers to ensure alignment with your production schedules. -
What payment options are available, and how do they affect international transactions?
Payment options for international transactions often include wire transfers, letters of credit, and online payment platforms. It’s advisable to negotiate payment terms that suit both parties, such as a deposit upfront and the balance upon delivery. Be aware of currency fluctuations and potential transaction fees, which could affect overall costs. Establishing a clear payment structure can minimize disputes and ensure smoother transactions. -
How do I ensure quality assurance and certification for my ceramic components?
To ensure quality assurance, request detailed information on the supplier’s quality control processes, including inspection methods and testing protocols. Suppliers should be able to provide documentation of certifications relevant to your industry, such as ISO standards or specific compliance certifications. Additionally, consider requesting pre-production samples to evaluate the quality and performance of the components before full-scale manufacturing begins. -
What logistics considerations should I keep in mind when sourcing ceramic components internationally?
Logistics for international sourcing include shipping methods, customs regulations, and delivery timelines. Choose a supplier with experience in exporting ceramic products to your region to facilitate smoother logistics. Discuss packaging options that protect fragile components during transit. Additionally, consider the total landed cost, including shipping, tariffs, and potential delays at customs, to accurately budget for your project. -
How can I handle disputes with suppliers effectively?
To manage disputes effectively, maintain open communication with your supplier throughout the project. Establish clear expectations in the contract regarding quality, delivery, and payment terms. If a dispute arises, address it promptly by discussing the issue directly with the supplier. Mediation or arbitration can be useful if an amicable resolution cannot be reached. Document all interactions and agreements to provide a clear record of the situation. -
What are the implications of using advanced ceramics in CNC machining?
Advanced ceramics offer enhanced properties such as increased strength, thermal resistance, and chemical stability, making them ideal for high-performance applications. However, these benefits can come with higher costs and more complex machining processes. It is crucial to evaluate whether the advantages of advanced ceramics align with your project requirements and budget. Collaborating with suppliers experienced in advanced ceramics can help you navigate these challenges effectively.
Important Disclaimer & Terms of Use
⚠️ Important Disclaimer
The information provided in this guide, including content regarding manufacturers, technical specifications, and market analysis, is for informational and educational purposes only. It does not constitute professional procurement advice, financial advice, or legal advice.
While we have made every effort to ensure the accuracy and timeliness of the information, we are not responsible for any errors, omissions, or outdated information. Market conditions, company details, and technical standards are subject to change.
B2B buyers must conduct their own independent and thorough due diligence before making any purchasing decisions. This includes contacting suppliers directly, verifying certifications, requesting samples, and seeking professional consultation. The risk of relying on any information in this guide is borne solely by the reader.
Strategic Sourcing Conclusion and Outlook for ceramic cnc machining
In conclusion, strategic sourcing of ceramic CNC machining components is crucial for international B2B buyers aiming to leverage the unique properties of ceramic materials in their applications. The combination of high hardness, thermal resistance, and chemical stability makes ceramics indispensable across industries such as aerospace, automotive, and medical devices. However, the challenges associated with machining these materials require careful consideration of supplier capabilities, machining techniques, and material selection.
To navigate this complex landscape effectively, buyers should prioritize relationships with suppliers who demonstrate expertise in ceramic machining and can meet stringent quality standards. Utilizing digital platforms for supplier evaluation and quoting can streamline procurement processes and enhance decision-making efficiency.
As global markets continue to evolve, the demand for innovative ceramic solutions will rise. B2B buyers in Africa, South America, the Middle East, and Europe are encouraged to embrace strategic sourcing practices that prioritize quality, compliance, and cost-effectiveness. By doing so, they can position themselves at the forefront of industry advancements and capitalize on emerging opportunities in ceramic CNC machining. Take action today to explore partnerships that will drive value and innovation in your supply chain.