Discover Metal Washer Benefits: The Complete Sourcing Guide (2025)
Introduction: Navigating the Global Market for metal washer
Navigating the complexities of sourcing metal washers can be a daunting task for international B2B buyers, especially when balancing quality, cost, and supplier reliability. Metal washers, essential components in various industries, serve critical functions such as load distribution, vibration absorption, and surface protection in fastening systems. This guide aims to demystify the global market for metal washers, offering insights into different types, applications, and the best practices for supplier vetting and cost management.
In this comprehensive resource, we will explore the diverse range of metal washers—including flat, lock, and fender washers—along with their specific applications across industries from construction to automotive. Additionally, we will provide strategies for identifying reputable suppliers, ensuring quality control, and negotiating favorable pricing.
For B2B buyers from Africa, South America, the Middle East, and Europe, this guide is designed to empower informed purchasing decisions by equipping you with the knowledge needed to navigate the international landscape effectively. By addressing common challenges and providing actionable insights, we aim to simplify the sourcing process and help you secure the right metal washers for your operational needs, thereby enhancing the efficiency and reliability of your projects.
Understanding metal washer Types and Variations
Type Name | Key Distinguishing Features | Primary B2B Applications | Brief Pros & Cons for Buyers |
---|---|---|---|
Flat Washers | Thin, disc-shaped; used for load distribution | General fastening, machinery assembly | Pros: Cost-effective; versatile. Cons: Limited vibration resistance. |
Lock Washers | Split design creates tension; prevents loosening | Automotive, construction, aerospace | Pros: Excellent for vibration-prone applications. Cons: May require precise installation. |
Fender Washers | Larger outer diameter; distributes load over a wider area | Electrical enclosures, automotive bodywork | Pros: Enhanced load distribution; aesthetic appeal. Cons: Bulkier design may not fit all applications. |
Cup Washers | Concave shape; provides a finished look and prevents pull-through | Furniture, cabinetry, and decorative uses | Pros: Attractive finish; effective in soft materials. Cons: Limited applications in heavy-duty settings. |
Belleville Washers | Conical shape; allows for spring-like tension | Aerospace, heavy machinery | Pros: Maintains preload; compensates for thermal expansion. Cons: More expensive than standard washers. |
What Are Flat Washers and Their Applications in B2B?
Flat washers are the most commonly used type of washer in various industries. Their primary function is to distribute the load of a fastener, such as a bolt or screw, over a larger surface area, which helps to prevent damage to the material being fastened. Flat washers are ideal for general fastening applications, including machinery assembly and construction projects. When purchasing flat washers, consider the material type (e.g., stainless steel, galvanized) for corrosion resistance and the size to match the fastener requirements.
How Do Lock Washers Prevent Loosening?
Lock washers are designed with a split or bent shape that creates a spring-like effect, providing tension to the fastener. This feature is particularly beneficial in applications prone to vibration, such as automotive and aerospace industries. When selecting lock washers, buyers should ensure they match the fastener size and consider the material for durability and corrosion resistance. While they effectively prevent loosening, precise installation is crucial to maximize their effectiveness.
Why Choose Fender Washers for Load Distribution?
Fender washers have a larger outer diameter compared to standard flat washers, allowing them to distribute load more evenly across a wider area. This makes them suitable for applications in electrical enclosures and automotive bodywork, where aesthetics and functionality are both important. Buyers should consider the thickness and material of fender washers to ensure they meet specific load requirements. While they offer excellent load distribution, their bulkier design may limit their use in tight spaces.
What Are the Benefits of Using Cup Washers?
Cup washers feature a concave shape that provides a neat and finished appearance while preventing the screw head from pulling through soft materials. They are commonly used in furniture and cabinetry, where aesthetics matter. When purchasing cup washers, consider the diameter and depth to ensure compatibility with your application. While they add visual appeal, their use may be limited in heavy-duty applications where higher load-bearing capacity is required.
What Are Belleville Washers and Their Unique Features?
Belleville washers, or conical washers, are designed to provide a spring-like tension that maintains preload in bolted connections. They are particularly useful in aerospace and heavy machinery applications, where thermal expansion and contraction can affect joint integrity. Buyers should evaluate the load rating and size of Belleville washers to ensure they meet the specific needs of their projects. Although they are more expensive than standard washers, their ability to maintain tension can lead to longer-lasting connections and reduce maintenance costs.
Key Industrial Applications of metal washer
Industry/Sector | Specific Application of Metal Washer | Value/Benefit for the Business | Key Sourcing Considerations for this Application |
---|---|---|---|
Automotive | Vibration Dampening in Engine Assemblies | Enhances durability and performance of engine components | Material grade (stainless, carbon), size compatibility |
Construction | Load Distribution in Structural Connections | Increases stability and safety of buildings | Compliance with international standards, corrosion resistance |
Electronics | Grounding and Electrical Connections | Prevents electrical failures and enhances signal integrity | Electrical conductivity, size specifications |
Agriculture | Machinery and Equipment Assembly | Reduces wear and tear, prolongs equipment lifespan | Material suitability for outdoor conditions |
Renewable Energy | Wind Turbine and Solar Panel Installations | Improves efficiency and reliability of energy systems | Resistance to environmental factors, precise dimensions |
How are Metal Washers Used in the Automotive Industry?
In the automotive sector, metal washers play a critical role in vibration dampening within engine assemblies. They are strategically placed between fasteners and engine components to distribute loads evenly, reducing wear and tear. Buyers should prioritize sourcing high-quality materials, such as stainless steel, to ensure longevity and performance under high-stress conditions. Additionally, compatibility with various bolt sizes and adherence to automotive industry standards are essential for international buyers, especially in regions like Europe and South America.
What is the Role of Metal Washers in Construction?
Metal washers are essential in construction for load distribution in structural connections. They ensure that bolts and screws do not pull through softer materials, thereby enhancing the stability and safety of buildings. For international B2B buyers, sourcing washers that comply with local building codes and international standards is crucial. Corrosion resistance is another significant consideration, particularly in humid climates found in parts of Africa and South America.
How Do Metal Washers Contribute to Electronics?
In the electronics industry, metal washers are used primarily for grounding and securing electrical connections. They help prevent electrical failures by ensuring a stable connection between components, which is vital for signal integrity. Buyers in this sector must focus on sourcing washers made from conductive materials and ensure they meet specific size requirements for compatibility with electronic components. This is particularly important for international buyers in the Middle East and Europe, where regulatory standards may vary.
Why are Metal Washers Important in Agriculture?
In agriculture, metal washers are utilized in the assembly of machinery and equipment. They help reduce wear and tear on components, thereby prolonging the lifespan of expensive agricultural machinery. When sourcing washers, buyers should consider the material’s durability and resistance to outdoor conditions, such as moisture and temperature fluctuations. This is particularly relevant for buyers in Africa and South America, where agricultural equipment is often exposed to harsh environments.
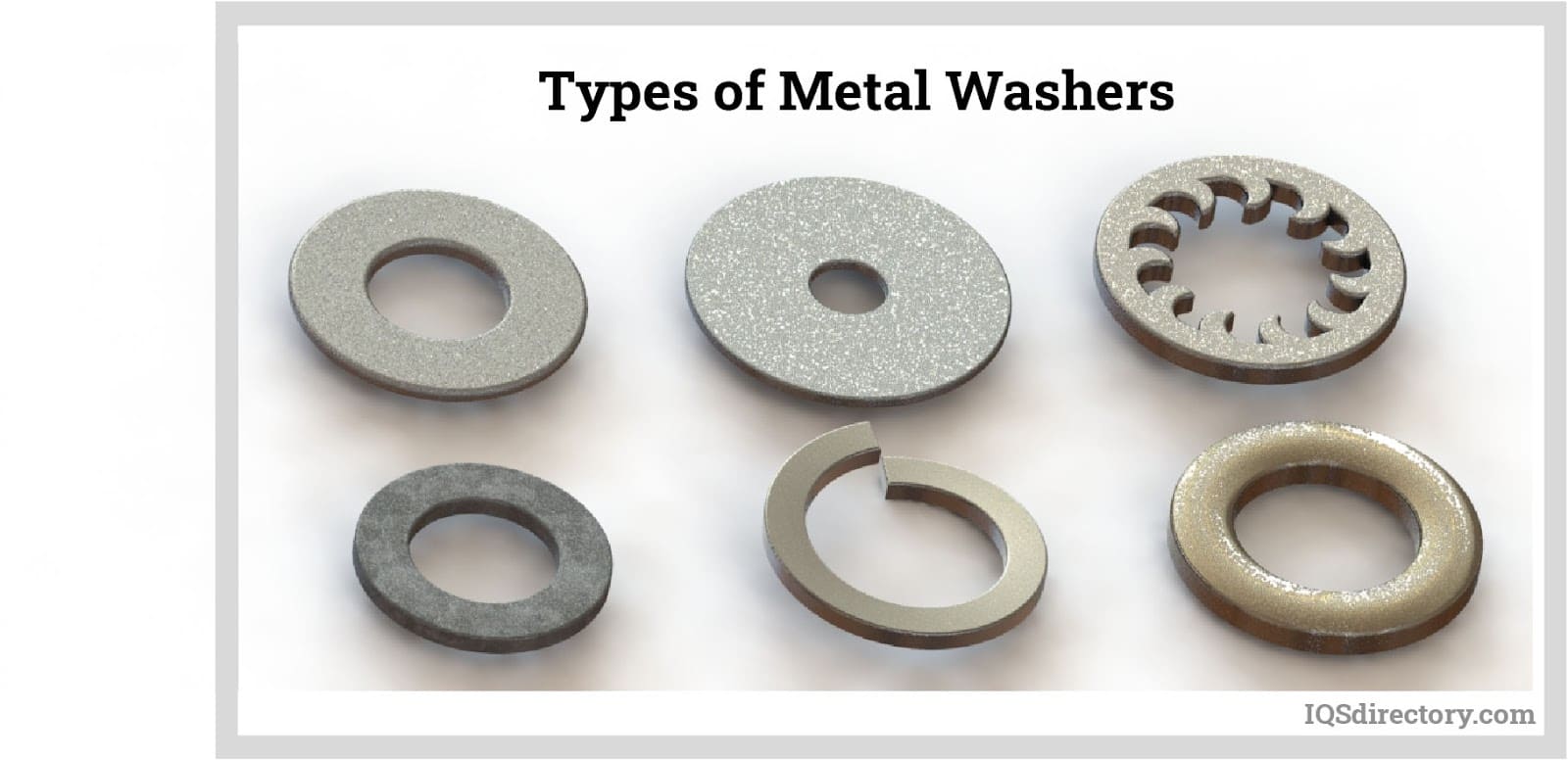
A stock image related to metal washer.
How Do Metal Washers Enhance Renewable Energy Systems?
Metal washers are integral to the assembly of renewable energy systems, such as wind turbines and solar panels. They improve the efficiency and reliability of these energy systems by providing secure fastening that can withstand environmental stressors. Buyers should prioritize sourcing washers that offer resistance to corrosion and other environmental factors. Precise dimensions are also critical to ensure compatibility with various installation requirements, especially for international buyers in Europe and the Middle East.
3 Common User Pain Points for ‘metal washer’ & Their Solutions
Scenario 1: Sourcing Quality Metal Washers for Diverse Applications
The Problem: International B2B buyers often struggle with sourcing high-quality metal washers that meet their specific application requirements. This is particularly challenging in regions like Africa and South America, where local suppliers may not offer a comprehensive range of washer types or materials. Buyers face the risk of receiving subpar products that fail to perform, leading to increased project costs and delays due to rework or equipment failure.
The Solution: To overcome this issue, buyers should establish relationships with trusted manufacturers or distributors that specialize in metal fasteners. Conducting thorough research on suppliers and checking their certifications, such as ISO 9001, can ensure quality. Additionally, buyers should request product samples to evaluate material strength and finish before committing to large orders. Utilizing online platforms that allow for direct communication with manufacturers can also facilitate better sourcing decisions. Consider engaging in trade shows or industry expos to connect with reputable suppliers who can offer customized solutions tailored to unique project needs.
Scenario 2: Understanding Washer Specifications and Standards
The Problem: Another common challenge is the confusion surrounding washer specifications and industry standards. B2B buyers may encounter various terms such as ASTM, ANSI, or metric versus imperial measurements, which can lead to misordering the wrong type or size of washers. This problem is exacerbated for buyers in Europe and the Middle East, where differing standards may apply compared to local regulations or practices.
The Solution: To mitigate this issue, it is essential for buyers to familiarize themselves with the relevant standards for metal washers applicable to their region and industry. Creating a specifications checklist that includes the type of washer (e.g., flat, lock, fender), material (e.g., stainless steel, carbon steel), and size (inner and outer diameter, thickness) can serve as a valuable reference during the ordering process. Additionally, buyers should consult with their engineering teams or technical experts to ensure they are making informed decisions. Leveraging online resources and industry forums can also provide clarity on standards and best practices.
Scenario 3: Preventing Fastener Loosening in Vibration-Prone Environments
The Problem: Fastener loosening due to vibration is a significant concern in various industrial applications, particularly in sectors like construction and manufacturing. Buyers often find that without the proper washers, their assemblies can fail over time, leading to costly maintenance and safety issues. This is especially critical for buyers in high-vibration environments, such as those in the automotive or aerospace industries.
The Solution: To address this pain point, buyers should consider using specialized washers designed for vibration resistance, such as split lock washers or tooth lock washers. These types of washers are engineered to maintain tension and prevent loosening under dynamic loads. When specifying washers, it is vital to match the washer type with the fastener and application requirements. Conducting regular maintenance checks on assemblies can also help in identifying potential issues before they escalate. For added assurance, buyers can implement a quality assurance protocol that includes monitoring the performance of washers in their applications, allowing for timely replacements or adjustments as needed.
Strategic Material Selection Guide for metal washer
What Are the Key Properties of Common Materials Used for Metal Washers?
When selecting metal washers for various applications, understanding the properties of different materials is crucial. Here, we analyze four common materials: stainless steel, carbon steel, brass, and aluminum. Each material offers distinct characteristics that can significantly influence performance, durability, and cost.
How Does Stainless Steel Perform in Metal Washer Applications?
Key Properties: Stainless steel is known for its excellent corrosion resistance, making it suitable for applications exposed to moisture or chemicals. It can withstand high temperatures and pressures, which is essential in industries such as automotive and aerospace.
Pros & Cons: Stainless steel washers are durable and have a long lifespan, but they tend to be more expensive than other materials. Manufacturing complexity can also be higher due to the need for specialized tooling. However, their resistance to rust and staining often justifies the higher cost in environments where longevity is critical.
Impact on Application: Stainless steel washers are compatible with a wide range of media, including water, oil, and various chemicals. They are ideal for applications in humid environments or those requiring frequent cleaning, such as in the food and beverage industry.
Considerations for International Buyers: Compliance with standards like ASTM A240 and DIN 1.4301 is vital for international buyers. Buyers from regions like Europe and the Middle East should ensure that their suppliers can provide certifications for corrosion resistance and mechanical properties.
What Are the Advantages and Disadvantages of Carbon Steel Washers?
Key Properties: Carbon steel washers are strong and can handle significant loads. They are often treated with coatings to enhance corrosion resistance, though they are generally less resistant than stainless steel.
Pros & Cons: The primary advantage of carbon steel washers is their cost-effectiveness. They are widely available and suitable for many applications. However, their susceptibility to rust and corrosion makes them less suitable for environments with high moisture or chemical exposure.
Impact on Application: Carbon steel washers are commonly used in construction and automotive applications where cost is a primary concern. However, they should be avoided in applications involving exposure to corrosive substances unless adequately coated.
Considerations for International Buyers: Buyers should look for compliance with standards such as ASTM A307 and JIS B 117. In regions like Africa and South America, where environmental conditions can vary significantly, selecting the right coating is essential to prevent premature failure.
Why Choose Brass Washers for Specific Applications?
Key Properties: Brass washers offer good corrosion resistance and are non-magnetic, making them suitable for electrical applications. They also have a lower friction coefficient, which can be beneficial in certain mechanical applications.
Pros & Cons: While brass washers are durable and aesthetically pleasing, they can be more expensive than carbon steel options. Their softness may limit their use in high-load applications, as they can deform under pressure.
Impact on Application: Brass washers are often used in plumbing and electrical applications due to their resistance to corrosion and electrical conductivity. However, they may not be suitable for high-temperature environments.
Considerations for International Buyers: Compliance with standards like ASTM B16 is crucial for ensuring quality. Buyers in Europe and the Middle East should also consider the implications of using brass in environments with high humidity or exposure to salts.
What Are the Benefits of Using Aluminum Washers?
Key Properties: Aluminum washers are lightweight and resistant to corrosion, making them suitable for applications where weight is a critical factor. They also have good thermal and electrical conductivity.
Pros & Cons: The primary advantage of aluminum washers is their low weight and resistance to oxidation. However, they may not be as strong as steel options, which can limit their applications in high-stress environments.
Impact on Application: Aluminum washers are ideal for aerospace and automotive applications where reducing weight is essential. They are also used in marine environments due to their resistance to corrosion.
Considerations for International Buyers: Compliance with standards such as ASTM B221 and EN AW-6061 is important for ensuring product integrity. Buyers from regions like Africa and South America should be aware of the specific alloy grades available in their markets.
Summary Table of Material Selection for Metal Washers
Material | Typical Use Case for Metal Washer | Key Advantage | Key Disadvantage/Limitation | Relative Cost (Low/Med/High) |
---|---|---|---|---|
Stainless Steel | Food processing, automotive, aerospace | Excellent corrosion resistance | Higher cost and manufacturing complexity | High |
Carbon Steel | Construction, automotive | Cost-effective and strong | Susceptible to rust without coatings | Low |
Brass | Plumbing, electrical | Good corrosion resistance, non-magnetic | Softer, may deform under load | Medium |
Aluminum | Aerospace, marine | Lightweight and corrosion-resistant | Lower strength compared to steel | Medium |
This strategic material selection guide provides B2B buyers with essential insights into the properties, advantages, and limitations of various materials used for metal washers. Understanding these factors will aid in making informed purchasing decisions tailored to specific application needs.
In-depth Look: Manufacturing Processes and Quality Assurance for metal washer
What Are the Main Stages of Manufacturing Metal Washers?
Manufacturing metal washers involves several critical stages, each designed to ensure the highest quality and performance standards. Understanding these stages can help B2B buyers make informed decisions when sourcing washers from international suppliers.
Material Preparation: How Are Raw Materials Selected?
The first step in the manufacturing process is material preparation. Metal washers are typically made from materials such as stainless steel, carbon steel, and other alloys. The choice of material depends on the intended application, such as corrosion resistance for outdoor use or strength for heavy-load applications.
Key Techniques:
– Material Sourcing: Suppliers often use certified materials that comply with international standards, such as ASTM or ISO specifications. B2B buyers should verify the certification of raw materials used in the manufacturing process.
– Quality Checks: Before processing, incoming materials undergo inspection for defects and compliance with specifications, ensuring that only high-quality materials are used.
Forming: What Techniques Are Used to Shape Metal Washers?
The forming stage involves shaping the raw material into the desired washer form. This can be achieved through several techniques, including:
- Stamping: A high-speed stamping process is commonly used for mass production. Sheets of metal are fed into a stamping machine where they are cut and formed into washers.
- Laser Cutting: For more complex designs or smaller batch sizes, laser cutting offers precision and flexibility, allowing manufacturers to produce washers with intricate patterns or specific dimensions.
- CNC Machining: For custom washers or those requiring high precision, CNC machining is utilized. This technique allows for intricate designs and exact measurements.
Assembly: How Are Metal Washers Prepared for Delivery?
While metal washers are generally produced as standalone components, assembly may be required in certain applications, particularly for specialized washers that include additional features like locking mechanisms.
Techniques:
– Automated Assembly: In cases where washers are part of a larger assembly, automated systems can combine washers with other components, ensuring consistency and speed.
– Manual Inspection: Before packaging, washers are often manually inspected to ensure that they meet dimensional and aesthetic standards.
Finishing: What Surface Treatments Are Commonly Applied?
The finishing stage enhances the performance and durability of metal washers. Common finishing techniques include:
- Plating: Zinc plating, hot-dip galvanizing, or nickel plating can be applied to improve corrosion resistance. Buyers should consider the environment in which the washers will be used when selecting the appropriate finish.
- Coating: Specialty coatings may be applied for specific applications, such as non-slip surfaces or chemical resistance.
- Deburring: This process removes sharp edges and imperfections, improving safety and performance.
What Quality Assurance Measures Are Necessary for Metal Washers?
Quality assurance (QA) is a critical component of the manufacturing process for metal washers. B2B buyers should be aware of the various QA measures that suppliers employ to ensure product reliability.
Which International Standards Should B2B Buyers Look For?
Understanding the relevant international standards is crucial for ensuring the quality of metal washers. Some key standards include:
- ISO 9001: This standard outlines requirements for a quality management system and ensures that suppliers consistently meet customer and regulatory requirements.
- CE Marking: For products sold within the European Economic Area, CE marking indicates compliance with safety, health, and environmental protection standards.
- API Standards: For washers used in the oil and gas industry, the American Petroleum Institute (API) provides specific standards that must be met.
What Are the Key Quality Control Checkpoints?
Quality control (QC) involves several checkpoints throughout the manufacturing process to ensure that products meet specified standards:
- Incoming Quality Control (IQC): Raw materials are inspected upon arrival to ensure they meet quality standards before processing begins.
- In-Process Quality Control (IPQC): During the manufacturing process, various parameters are monitored to detect any deviations from quality standards.
- Final Quality Control (FQC): Finished products are subjected to rigorous testing and inspection before they are packaged and shipped. This includes dimensional checks, surface quality assessment, and functional testing.
What Common Testing Methods Are Used for Metal Washers?
Testing methods play a vital role in verifying the quality and performance of metal washers. Some common methods include:
- Dimensional Inspection: Using calipers and gauges to ensure that washers meet specified dimensions.
- Tensile Testing: This evaluates the strength and ductility of the material, ensuring it can withstand the required loads.
- Corrosion Testing: To determine the resistance of the washer’s surface treatment against various corrosive environments.
How Can B2B Buyers Verify Supplier Quality Control?
B2B buyers must take proactive steps to verify the quality control processes of their suppliers. Here are some actionable insights:
- Conduct Audits: Regular audits of suppliers can provide insights into their manufacturing processes and quality control measures. Buyers should consider both announced and unannounced audits for a comprehensive evaluation.
- Request Quality Reports: Suppliers should be willing to provide detailed quality reports, including results from IQC, IPQC, and FQC stages. This documentation can help verify compliance with industry standards.
- Utilize Third-Party Inspection Services: Engaging third-party inspection services can offer an unbiased assessment of product quality. This is especially important for international transactions, where buyers may be unable to visit suppliers in person.
What Are the Quality Control Nuances for International B2B Buyers?
When sourcing metal washers internationally, particularly from regions such as Africa, South America, the Middle East, and Europe, buyers should be aware of specific nuances:
- Cultural Considerations: Different regions may have varying approaches to quality assurance. Understanding these cultural differences can help in negotiating and establishing quality standards.
- Regulatory Compliance: Buyers should ensure that suppliers comply with both local and international regulations. This includes understanding import/export regulations that may impact product quality.
- Logistical Challenges: International shipping can introduce variables that affect product quality, such as temperature fluctuations and handling. Buyers should discuss packaging and shipping methods with suppliers to mitigate these risks.
By understanding the manufacturing processes and quality assurance measures for metal washers, B2B buyers can make more informed sourcing decisions, ensuring they receive high-quality products that meet their specific needs.
Practical Sourcing Guide: A Step-by-Step Checklist for ‘metal washer’
In the world of B2B procurement, sourcing metal washers requires careful consideration and a structured approach. This guide outlines a step-by-step checklist that will help international buyers, particularly from Africa, South America, the Middle East, and Europe, streamline their purchasing process for metal washers.
Step 1: Define Your Technical Specifications
Before reaching out to suppliers, it’s essential to clearly define your requirements. This includes specifying the type of metal washer needed—flat, lock, or fender—and the relevant dimensions such as inner diameter, outer diameter, and thickness. Understanding the application of the washer will guide you in choosing the right material and finish, ensuring compatibility with your project.
Step 2: Conduct Market Research
Engage in thorough market research to identify potential suppliers. Utilize online platforms, trade directories, and industry forums to gather a list of manufacturers and distributors. Pay attention to reviews and testimonials from other buyers in similar regions to gain insights into supplier reliability and product quality.
Step 3: Evaluate Potential Suppliers
Before committing to a supplier, it’s crucial to vet them thoroughly. Request company profiles, case studies, and references from buyers in a similar industry or region. Look for suppliers who have experience in exporting to your area, as they will be familiar with the regulations and requirements specific to your market.
Step 4: Verify Certifications and Standards
Ensure that the suppliers comply with relevant industry standards and certifications. This may include ISO certifications or compliance with local regulations regarding material safety and quality. Certifications provide assurance that the products meet international quality benchmarks, which is especially important when sourcing from different continents.
Step 5: Request Samples for Testing
Before finalizing your order, request samples of the metal washers. Testing samples allows you to assess the quality, material properties, and dimensions firsthand. Check for corrosion resistance, load distribution capabilities, and overall durability to ensure they meet your technical specifications.
Step 6: Negotiate Pricing and Terms
Once you’ve identified a suitable supplier, engage in negotiations regarding pricing, payment terms, and lead times. Be transparent about your budget and project timelines, and inquire about bulk order discounts or other pricing structures. Establish clear terms to avoid misunderstandings later in the procurement process.
Step 7: Establish a Communication Plan
Effective communication is key to successful sourcing. Set up a structured plan to maintain contact with your supplier throughout the order process. Ensure that you have clear channels for addressing any issues that may arise, from production delays to quality concerns, fostering a collaborative relationship.
By following this checklist, international B2B buyers can enhance their sourcing strategy for metal washers, ensuring they make informed decisions that align with their operational needs and standards.
Comprehensive Cost and Pricing Analysis for metal washer Sourcing
What Are the Key Cost Components for Metal Washer Manufacturing?
Understanding the cost structure of metal washers is essential for international B2B buyers. The primary cost components include:
-
Materials: The choice of material significantly affects pricing. Common materials for metal washers include stainless steel, carbon steel, and brass. Stainless steel, particularly grades 304 and 316, are popular due to their corrosion resistance, but they come at a higher cost compared to carbon steel.
-
Labor: Labor costs vary by region and can impact the overall price of metal washers. In regions with lower labor costs, such as parts of Africa and South America, sourcing can be more economical.
-
Manufacturing Overhead: This includes expenses related to factory operations, utilities, and equipment maintenance. Efficient production processes can help reduce these costs.
-
Tooling: Initial costs for tooling can be high, especially for custom washers. However, these costs are amortized over larger production runs, making bulk orders more cost-effective.
-
Quality Control (QC): Ensuring that washers meet specific standards often incurs additional costs. Certifications and quality testing are essential for buyers in regulated industries.
-
Logistics: Shipping and handling costs can vary widely based on the distance from the supplier and the chosen shipping method. Incoterms can also influence logistics costs, so it’s crucial to clarify responsibilities for shipping and customs.
-
Margin: Suppliers typically add a margin to cover their costs and profit. This margin can vary based on the supplier’s market position and the competitiveness of their pricing.
How Do Pricing Influencers Affect Metal Washer Costs?
Several factors can influence the pricing of metal washers, including:
-
Volume and Minimum Order Quantity (MOQ): Larger orders often lead to lower per-unit costs due to economies of scale. Buyers should negotiate MOQs to align with their needs.
-
Specifications and Customization: Custom sizes, thicknesses, or materials can significantly increase costs. Buyers should evaluate whether standard options meet their needs to optimize pricing.
-
Material Quality and Certifications: Higher quality materials or certifications (e.g., ISO, ASTM) can drive up prices. Buyers in industries with stringent requirements should factor this into their sourcing decisions.
-
Supplier Factors: The supplier’s reputation, production capacity, and geographical location can influence pricing. It may be beneficial to establish long-term relationships with reliable suppliers for better pricing and service.
-
Incoterms: Understanding the chosen Incoterms (e.g., FOB, CIF) is crucial for budgeting. These terms determine who is responsible for shipping, insurance, and customs duties.
What Are the Best Buyer Tips for Cost-Efficient Metal Washer Sourcing?
For B2B buyers, especially from Africa, South America, the Middle East, and Europe, consider these actionable tips:
-
Negotiate Wisely: Always seek to negotiate prices, especially when placing large orders. Suppliers are often willing to provide discounts for bulk purchases.
-
Consider Total Cost of Ownership (TCO): TCO goes beyond the purchase price. Factor in shipping, potential tariffs, and any additional costs associated with quality control or compliance.
-
Understand Pricing Nuances for International Purchases: Fluctuating exchange rates and import duties can affect overall costs. Ensure you account for these variables when budgeting.
-
Engage Multiple Suppliers: Request quotes from multiple suppliers to compare prices and terms. This can provide leverage during negotiations and help identify the best value.
-
Leverage Technology: Utilize procurement software to track pricing trends and supplier performance. This can aid in making informed sourcing decisions.
Conclusion and Pricing Disclaimer
While indicative prices for metal washers can range from a few cents to several dollars per unit depending on the factors mentioned above, these prices can vary widely based on specific requirements and market conditions. Always conduct thorough market research and supplier assessments before finalizing any sourcing decisions.
Alternatives Analysis: Comparing metal washer With Other Solutions
In today’s global marketplace, B2B buyers often seek effective solutions to enhance their fastening needs. While metal washers are a standard choice for load distribution and stability, exploring alternatives can provide additional benefits tailored to specific applications. Below, we compare metal washers with two viable alternatives: plastic washers and lock washers.
Comparison Table of Metal Washers and Alternatives
Comparison Aspect | Metal Washer | Plastic Washer | Lock Washer |
---|---|---|---|
Performance | Excellent load distribution; suitable for high-stress applications. | Good for low-stress environments; lightweight. | Prevents loosening due to vibration; offers tension. |
Cost | Generally low to moderate cost; varies by material. | Typically lower cost than metal options. | Slightly higher than flat washers but cost-effective for high-performance needs. |
Ease of Implementation | Easy to install; requires no special tools. | Simple installation; compatible with standard fasteners. | Requires precise installation; may need specific torque settings. |
Maintenance | Durable and long-lasting; minimal maintenance required. | May degrade over time under UV or heat; not as durable as metal. | Low maintenance; effective as long as properly installed. |
Best Use Case | High-stress applications in construction and manufacturing. | Electrical insulation, lightweight applications, or environments prone to corrosion. | Vibration-prone applications, automotive, and machinery. |
What Are the Advantages and Disadvantages of Plastic Washers?
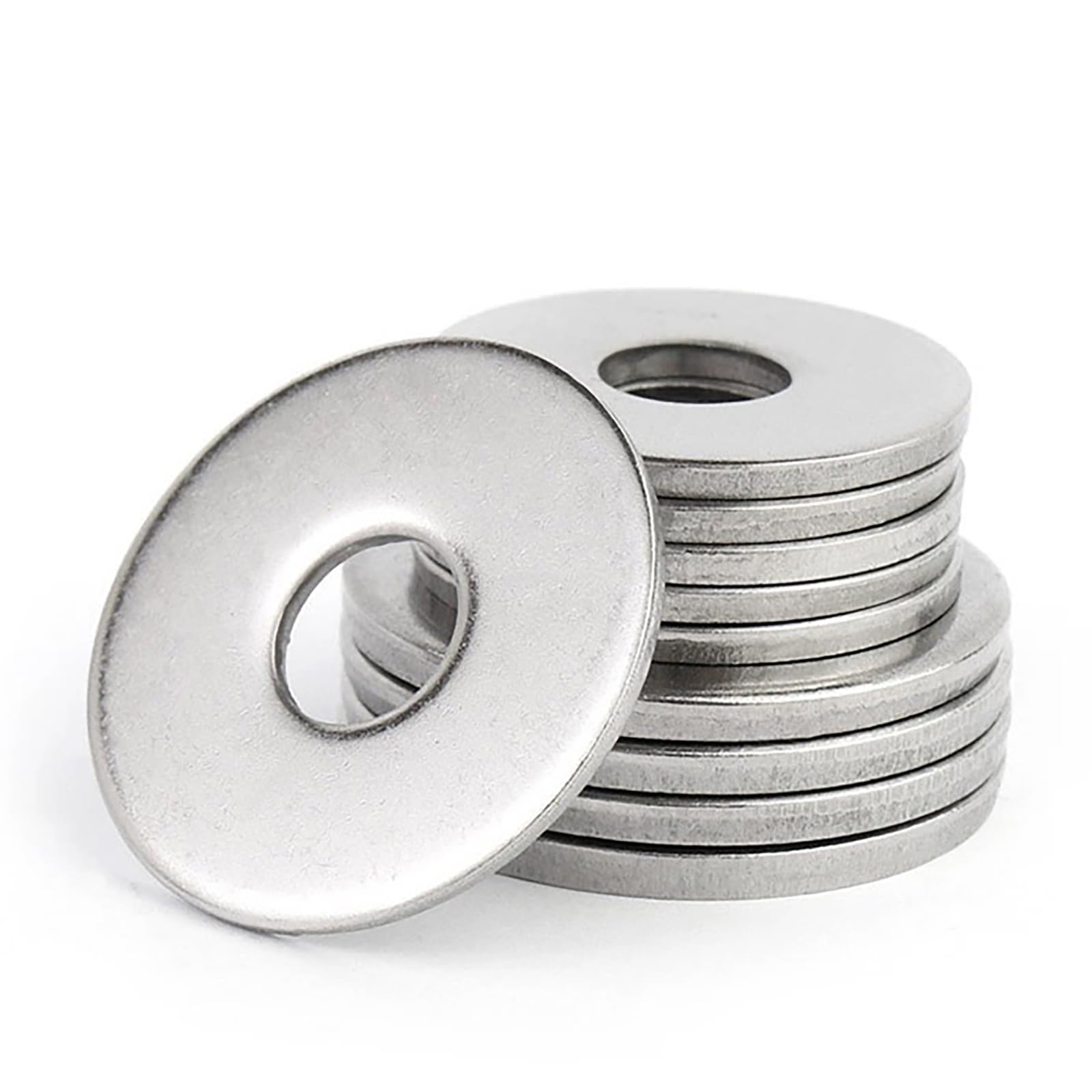
A stock image related to metal washer.
Plastic washers serve as a lightweight alternative to metal washers, making them ideal for applications where weight is a concern. They provide good load distribution but are best suited for low-stress environments. A significant advantage is their resistance to corrosion and electrical insulation properties, which can be beneficial in specific applications. However, they may not perform well under extreme temperatures or high mechanical stress, leading to potential failures in critical situations.
How Do Lock Washers Compare?
Lock washers are designed specifically to prevent fasteners from loosening due to vibration. They provide a spring-like tension that keeps the bolt tight, making them an excellent choice for applications where vibration is a concern, such as in automotive or industrial machinery. While they are slightly more complex to install than flat washers, they offer enhanced performance in maintaining bolt tension. The downside is that they can be more expensive than standard flat washers and may require careful torque management to ensure optimal effectiveness.
Conclusion: How Should B2B Buyers Choose the Right Solution?
When selecting between metal washers and alternatives like plastic or lock washers, B2B buyers must consider the specific requirements of their applications. For high-stress environments, metal washers remain the preferred option due to their durability and reliability. However, if weight reduction or electrical insulation is paramount, plastic washers may be more appropriate. In scenarios where vibration could lead to loosening, lock washers provide a robust solution. By assessing performance needs, cost constraints, and application contexts, buyers can make informed decisions that enhance their operations and product longevity.
Essential Technical Properties and Trade Terminology for metal washer
What Are the Key Technical Properties of Metal Washers?
When sourcing metal washers, understanding their technical specifications is crucial for ensuring compatibility and performance in your applications. Here are some critical properties to consider:
1. Material Grade
Metal washers are typically made from various materials, including stainless steel, carbon steel, and brass. Each material has specific properties that affect durability, corrosion resistance, and load-bearing capacity. For instance, 316 stainless steel is known for its excellent corrosion resistance, making it suitable for marine applications, while carbon steel is often used in less demanding environments due to its cost-effectiveness. Selecting the appropriate material grade can significantly impact the longevity and reliability of your assembly.
2. Inner and Outer Diameter
The inner diameter (ID) and outer diameter (OD) of a washer are critical dimensions that determine its fit with fasteners. An appropriate ID ensures a snug fit around the bolt or screw, while the OD provides the necessary surface area to distribute load effectively. For example, a washer with a larger OD can better disperse the load, reducing the risk of damage to the surface beneath the fastener. Accurate measurements are essential for achieving optimal performance.
3. Thickness
Washer thickness affects its load-bearing capabilities and overall strength. Thicker washers can handle more significant loads and provide better support, while thinner washers may be more suitable for lighter applications. Understanding the required thickness for your specific application ensures that the washer can withstand operational stresses without failure.
4. Tolerance
Tolerance refers to the permissible limit of variation in a washer’s dimensions. Tight tolerances are crucial for applications requiring precision, such as aerospace or automotive industries. In contrast, broader tolerances may suffice for general construction. Ensuring that washers meet the necessary tolerances is vital for maintaining assembly integrity and safety.
5. Finish Type
The surface finish of a washer can influence its performance and resistance to environmental factors. Common finishes include zinc plating, which enhances corrosion resistance, and black oxide, which provides a decorative appearance. Selecting the right finish can help ensure the washer performs well in its intended environment, especially in regions prone to moisture or chemical exposure.
What Are Common Trade Terms in the Metal Washer Industry?
Navigating the procurement process for metal washers involves familiarizing yourself with industry-specific terminology. Here are some essential terms:
1. OEM (Original Equipment Manufacturer)
OEM refers to companies that produce components that are used in the manufacturing of another company’s product. In the context of metal washers, an OEM may supply washers that meet specific standards required by the equipment manufacturer. Understanding OEM specifications ensures that you acquire parts that will fit seamlessly into your assembly.
2. MOQ (Minimum Order Quantity)
MOQ is the minimum number of units a supplier is willing to sell in a single order. This term is significant for B2B buyers as it affects inventory management and purchasing strategies. Knowing the MOQ helps buyers plan their procurement effectively and avoid overstocking or stockouts.
3. RFQ (Request for Quote)
An RFQ is a document used to solicit price quotations from suppliers for specific products or services. When purchasing metal washers, submitting an RFQ allows you to compare prices, lead times, and terms from multiple suppliers, ensuring you make informed decisions.
4. Incoterms (International Commercial Terms)
Incoterms are standardized terms used in international trade to clarify the responsibilities of buyers and sellers regarding shipping, insurance, and tariffs. Familiarity with these terms helps B2B buyers understand their obligations and rights, ensuring smoother transactions and fewer misunderstandings during the shipping process.
5. Lead Time
Lead time refers to the period between placing an order and receiving the products. Understanding lead times is crucial for planning production schedules and inventory management. Buyers should consider lead times when sourcing metal washers to avoid delays in their projects.
By grasping these essential technical properties and trade terms, B2B buyers can make informed decisions when sourcing metal washers, ensuring quality, compatibility, and timely delivery.
Navigating Market Dynamics and Sourcing Trends in the metal washer Sector
What Are the Key Trends Influencing the Metal Washer Market?
The global metal washer market is witnessing significant growth, driven by advancements in manufacturing technologies and an increasing demand for fasteners across various industries. Key sectors such as automotive, construction, and electronics are propelling this demand, particularly in emerging markets in Africa, South America, and the Middle East. For international B2B buyers, understanding market dynamics is essential. The rise of e-commerce platforms has transformed sourcing, allowing buyers from regions like Spain and Mexico to access a wider range of suppliers and products.
Current trends include the adoption of automation and Industry 4.0 technologies, which enhance production efficiency and quality control in washer manufacturing. Additionally, there is a growing emphasis on customization, with manufacturers offering tailored solutions to meet specific application needs. Buyers are increasingly seeking suppliers that can provide a variety of washer types, including flat, lock, and fender washers, to accommodate diverse projects. Moreover, the focus on supply chain resilience has intensified, encouraging buyers to diversify their supplier base and consider regional sourcing options to mitigate risks associated with geopolitical instability and trade disruptions.
How Can Sustainability and Ethical Sourcing Impact the Metal Washer Supply Chain?
Sustainability is becoming a critical consideration for B2B buyers in the metal washer sector. The environmental impact of manufacturing processes, such as energy consumption and waste generation, has prompted many companies to seek greener alternatives. Buyers are encouraged to prioritize suppliers that utilize recycled materials and implement eco-friendly production practices. Certifications such as ISO 14001 (Environmental Management) and the use of sustainable materials can signal a supplier’s commitment to ethical sourcing.
Ethical supply chains are not only about environmental considerations; they also encompass labor practices and community impact. Buyers should conduct thorough due diligence on suppliers to ensure compliance with international labor standards and fair working conditions. Transparency in the supply chain is vital, and buyers can leverage technologies such as blockchain to trace the origins of materials used in metal washers. This approach not only enhances trust but also aligns with the growing consumer preference for ethically sourced products, ultimately benefiting brand reputation and customer loyalty.
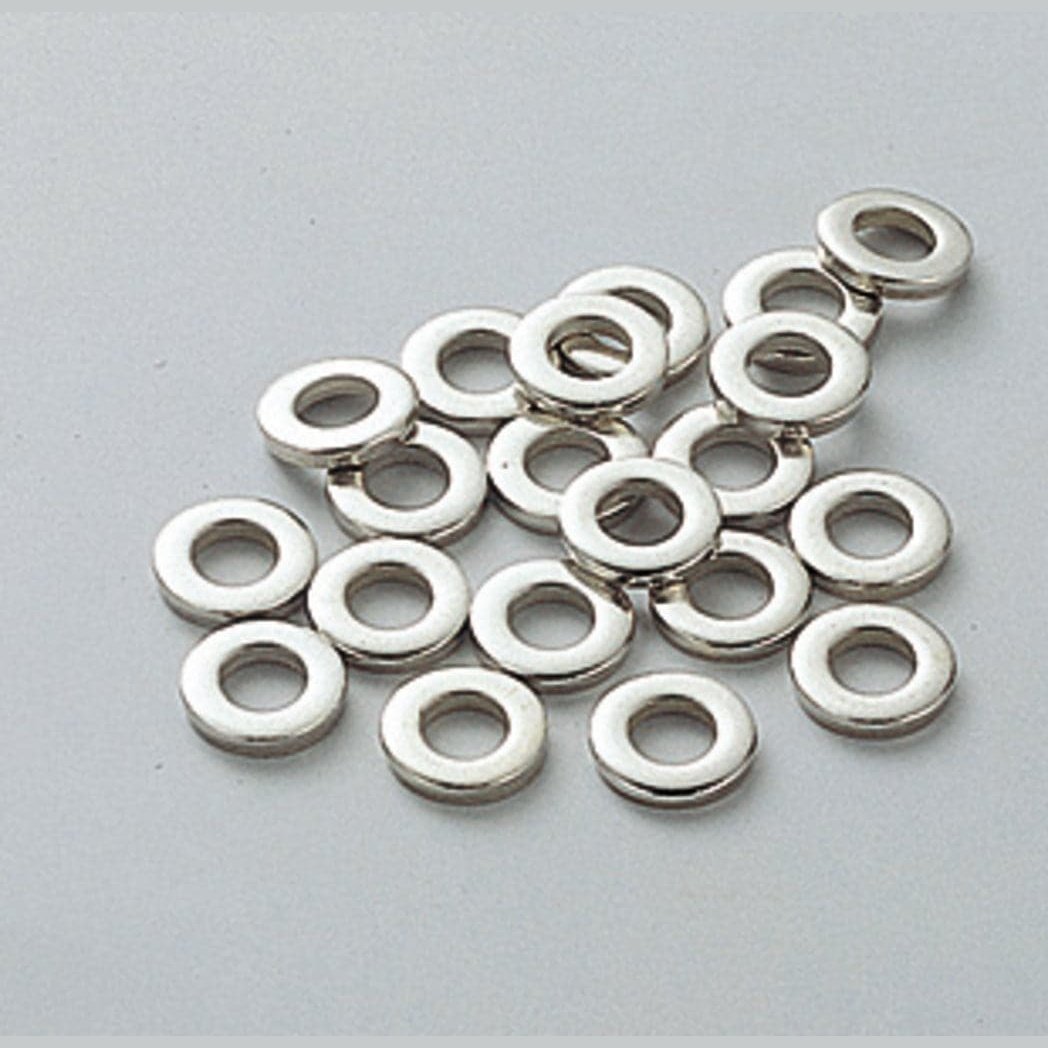
A stock image related to metal washer.
What Is the Historical Context of Metal Washers in B2B Transactions?
The evolution of metal washers can be traced back to their initial use as simple devices for load distribution in fastening systems. Over the decades, their design and functionality have advanced significantly, driven by the demands of various industries. In the early 20th century, washers were primarily made of steel and used in basic mechanical applications. However, as industries expanded and technology advanced, the introduction of materials such as stainless steel and specialized alloys enhanced their performance and durability.
Today, metal washers are integral components in complex machinery and construction projects, reflecting the need for reliability and efficiency in fastening solutions. The historical context of metal washers illustrates their transformation from basic fasteners to critical elements in modern engineering and manufacturing processes. For B2B buyers, understanding this evolution can inform sourcing decisions, particularly regarding material specifications and application suitability.
Conclusion
Navigating the market dynamics and sourcing trends in the metal washer sector requires an understanding of the driving forces behind industry growth, the importance of sustainability, and the historical context that shapes current practices. By focusing on these areas, international B2B buyers can make informed decisions that align with both operational needs and ethical standards, ensuring a competitive edge in their respective markets.
Frequently Asked Questions (FAQs) for B2B Buyers of metal washer
-
How do I determine the right type of metal washer for my application?
To choose the appropriate metal washer, consider the specific application requirements, including load distribution, material compatibility, and environmental factors. For example, flat washers are ideal for load dispersion, while lock washers are suited for vibration-prone applications. Assess the size of the fasteners and the surfaces they will contact, ensuring the washer’s inner diameter matches the bolt or screw size. Additionally, consider factors like corrosion resistance; stainless steel washers are preferred in humid or corrosive environments. -
What is the best material for metal washers in varying environments?
The ideal material for metal washers largely depends on the environment in which they will be used. Stainless steel washers offer excellent corrosion resistance, making them suitable for outdoor applications or humid areas. Zinc-plated steel washers are cost-effective for indoor use but may corrode if exposed to moisture. For high-temperature applications, consider using materials like carbon steel or specialized alloys. Always consult with your supplier to ensure the selected material meets the specific needs of your project. -
What are the minimum order quantities (MOQ) for metal washers when sourcing internationally?
Minimum order quantities (MOQ) for metal washers can vary significantly among suppliers and regions. Typically, MOQs range from 100 to 1,000 pieces, depending on the material, size, and manufacturing process. When sourcing from international suppliers, inquire about MOQs early in the negotiation process. Some suppliers may offer flexibility in MOQs for larger orders or long-term contracts, which can be beneficial for B2B buyers looking to optimize costs and inventory management. -
What payment terms should I expect when sourcing metal washers internationally?
Payment terms can vary by supplier and region, but common options include upfront payment, letter of credit, and payment upon delivery. When dealing with international suppliers, be prepared for terms that may require a deposit (usually 30-50%) before production, with the balance due upon shipment. It’s essential to negotiate favorable terms that protect your interests while ensuring the supplier’s confidence. Always verify payment methods and consider using secure platforms to mitigate risks associated with international transactions. -
How can I ensure the quality of metal washers from international suppliers?
To guarantee the quality of metal washers, conduct thorough supplier vetting before placing an order. Request certifications such as ISO 9001 or relevant industry standards that demonstrate their commitment to quality management. Additionally, consider ordering samples for inspection prior to bulk purchases. Implement a quality assurance process that includes third-party inspections or audits, especially for large orders. Establish clear specifications and expectations in your contracts to minimize discrepancies. -
What logistics considerations should I keep in mind when importing metal washers?
When importing metal washers, evaluate shipping options, lead times, and customs regulations. Choose a reliable freight forwarder familiar with the import process in your country. Understand the total landed cost, which includes shipping, tariffs, and taxes, to avoid unexpected expenses. Ensure all documentation is in order, including commercial invoices and packing lists, to facilitate smooth customs clearance. Additionally, factor in potential delays and plan your inventory needs accordingly. -
Can I customize metal washers to meet my specific requirements?
Yes, many manufacturers offer customization options for metal washers, including size, thickness, material, and finishes. When seeking customized washers, provide detailed specifications, including dimensions, tolerances, and intended applications. Discuss your requirements with potential suppliers to determine their capabilities and any associated costs. Customization may involve longer lead times, so it’s advisable to plan accordingly to avoid project delays. -
What are the common applications for metal washers in various industries?
Metal washers are widely used across numerous industries, including automotive, construction, and electronics. In automotive applications, they serve as spacers and load distributors to enhance assembly integrity. In construction, washers prevent bolt loosening and protect surfaces from damage. In electronics, they can be used to secure components and reduce vibration. Understanding the specific needs of your industry will help you select the right type of washer for your applications.
Important Disclaimer & Terms of Use
⚠️ Important Disclaimer
The information provided in this guide, including content regarding manufacturers, technical specifications, and market analysis, is for informational and educational purposes only. It does not constitute professional procurement advice, financial advice, or legal advice.
While we have made every effort to ensure the accuracy and timeliness of the information, we are not responsible for any errors, omissions, or outdated information. Market conditions, company details, and technical standards are subject to change.
B2B buyers must conduct their own independent and thorough due diligence before making any purchasing decisions. This includes contacting suppliers directly, verifying certifications, requesting samples, and seeking professional consultation. The risk of relying on any information in this guide is borne solely by the reader.
Strategic Sourcing Conclusion and Outlook for metal washer
In conclusion, strategic sourcing of metal washers is essential for optimizing procurement processes and ensuring product quality. International B2B buyers, particularly from Africa, South America, the Middle East, and Europe, should prioritize suppliers that offer a diverse range of washer types—such as flat, lock, and fender washers—tailored to specific applications. Understanding the material properties and performance characteristics of washers can lead to enhanced durability and reliability in your projects.
Moreover, leveraging strong relationships with manufacturers and distributors can yield better pricing, timely deliveries, and access to innovative products. As global supply chains continue to evolve, staying informed about market trends and potential disruptions will empower buyers to make educated decisions.
Looking ahead, the demand for high-quality metal washers is expected to rise, driven by advancements in industries such as construction, automotive, and electronics. Now is the time for buyers to reevaluate their sourcing strategies and align with partners who can adapt to changing market conditions. Actively engage with suppliers to explore customized solutions that meet your specific needs, ensuring your operations remain competitive in the global marketplace.