Cut Costs with the Ultimate Air Cooled Chiller Guide (2025)
Introduction: Navigating the Global Market for air cooled chiller
In today’s global marketplace, sourcing efficient air-cooled chillers presents a significant challenge for international B2B buyers, particularly those operating in regions such as Africa, South America, the Middle East, and Europe. With rising energy costs and increasing demands for sustainable cooling solutions, selecting the right chiller is crucial for maintaining competitive advantage while ensuring operational efficiency. This guide offers a comprehensive overview of air-cooled chillers, covering various types, their applications across industries, and practical insights for supplier vetting and cost considerations.
Whether you are involved in industrial refrigeration, data center cooling, or HVAC systems, understanding the nuances of air-cooled chillers can empower your purchasing decisions. The guide delves into the differences between scroll and screw chillers, their respective efficiencies, and the latest innovations in chiller technology. Additionally, it highlights the importance of selecting suppliers who align with your sustainability goals and operational requirements.
By equipping yourself with actionable insights and detailed comparisons, you will be better prepared to navigate the complexities of the air-cooled chiller market. This resource aims to foster informed decision-making, ensuring that your investments contribute to both immediate cooling needs and long-term sustainability objectives. With the right knowledge at your disposal, you can confidently choose air-cooled chillers that meet your specific business requirements.
Understanding air cooled chiller Types and Variations
Type Name | Key Distinguishing Features | Primary B2B Applications | Brief Pros & Cons for Buyers |
---|---|---|---|
Air-Cooled Scroll Chillers | Utilizes scroll compressors; compact design | Small to medium industrial processes | Pros: Easy installation, low maintenance. Cons: Limited cooling capacity. |
Air-Cooled Screw Chillers | Employs screw compressors; higher capacity options | Large commercial buildings, data centers | Pros: Greater efficiency, suitable for larger loads. Cons: More complex installation. |
Magnetic-Bearing Chillers | Zero-oil operation; high efficiency | District cooling, pharmaceuticals | Pros: Reduced maintenance, significant energy savings. Cons: Higher initial investment. |
Air-Cooled Heat Pump Chillers | Can provide both heating and cooling; versatile | HVAC systems, residential applications | Pros: Energy-efficient, dual functionality. Cons: May require more space. |
Integrated Free-Cooling Chillers | Combines cooling and free cooling options | Data centers, large commercial spaces | Pros: Cost-effective in cooler climates, energy-efficient. Cons: Limited effectiveness in hot climates. |
What Are Air-Cooled Scroll Chillers and Their Applications?
Air-cooled scroll chillers are designed for smaller to medium-sized industrial processes. They utilize scroll compressors, which allow for a compact design and easy installation. This type of chiller is ideal for applications where space is a constraint and where the cooling load is relatively low. Buyers should consider their limited cooling capacity, which makes them unsuitable for larger industrial requirements.
How Do Air-Cooled Screw Chillers Stand Out?
Air-cooled screw chillers are characterized by their use of screw compressors, offering a higher cooling capacity compared to scroll chillers. This makes them suitable for larger commercial buildings and data centers. They provide greater efficiency and can handle significant cooling loads, making them a solid investment for businesses requiring robust cooling solutions. However, the installation process is more complex, which may lead to higher upfront costs.
Why Choose Magnetic-Bearing Chillers?
Magnetic-bearing chillers are notable for their zero-oil operation, which enhances efficiency and reduces maintenance needs. They are particularly effective in district cooling systems and pharmaceutical applications due to their high cooling capacity and efficiency. While the initial investment may be higher, the long-term energy savings and reduced maintenance costs can justify the expense for businesses seeking sustainable cooling solutions.
What Are Air-Cooled Heat Pump Chillers?
Air-cooled heat pump chillers serve a dual purpose by providing both heating and cooling. This versatility makes them suitable for HVAC systems in residential and commercial applications. They are energy-efficient and can significantly reduce operating costs. However, buyers should be aware that they may require more installation space compared to traditional chillers, which could be a consideration in space-constrained environments.
How Do Integrated Free-Cooling Chillers Work?
Integrated free-cooling chillers combine traditional cooling methods with free cooling options, allowing for cost-effective operation in cooler climates. They are particularly advantageous for data centers and large commercial spaces, where energy efficiency is paramount. However, their effectiveness diminishes in hotter climates, making it essential for buyers to assess their local weather conditions before investing.
Key Industrial Applications of air cooled chiller
Industry/Sector | Specific Application of Air Cooled Chiller | Value/Benefit for the Business | Key Sourcing Considerations for this Application |
---|---|---|---|
Data Centers | Cooling systems for IT equipment | Maintains optimal operating temperatures, ensuring server reliability and uptime | Energy efficiency ratings, redundancy options, and noise levels |
Manufacturing | Process cooling in production lines | Enhances equipment performance and product quality by maintaining consistent temperatures | Capacity requirements, installation space, and maintenance needs |
Pharmaceuticals & Biotechnology | Temperature control for sensitive materials | Ensures product integrity and compliance with regulatory standards | Compliance with industry regulations, energy efficiency, and reliability |
Food & Beverage | Refrigeration for storage and processing | Extends shelf life of products and ensures food safety | Compliance with health regulations, efficiency, and scalability |
District Cooling | Centralized cooling for multiple buildings | Reduces energy consumption and operational costs across urban areas | Infrastructure compatibility, energy source, and environmental impact |
How Are Air Cooled Chillers Used in Data Centers?
In data centers, air cooled chillers are crucial for cooling IT equipment, which generates significant heat during operation. By maintaining optimal temperatures, these chillers help prevent overheating, ensuring that servers operate reliably and efficiently. For international buyers, especially in regions with varying climate conditions, it’s essential to consider energy efficiency ratings and noise levels, as these factors directly impact operational costs and compliance with local regulations.
What Role Do Air Cooled Chillers Play in Manufacturing?
Manufacturing facilities utilize air cooled chillers for process cooling, which is vital for maintaining the performance of machinery and ensuring product quality. By regulating temperatures, chillers help minimize thermal stress on equipment, which can lead to breakdowns and production delays. Buyers should focus on capacity requirements and installation space, as well as the chiller’s maintenance needs, to ensure seamless integration into existing systems.
Why Are Air Cooled Chillers Important in Pharmaceuticals and Biotechnology?
In the pharmaceutical and biotechnology sectors, air cooled chillers are employed to maintain strict temperature controls for sensitive materials, including active ingredients and finished products. This is critical for ensuring product integrity and compliance with regulatory standards. Buyers in these sectors should prioritize chillers that meet industry regulations, offer high energy efficiency, and demonstrate reliability, as any failure can lead to significant financial losses.
How Do Air Cooled Chillers Benefit the Food and Beverage Industry?
The food and beverage industry relies on air cooled chillers for effective refrigeration during storage and processing. These systems help extend the shelf life of products while ensuring compliance with health and safety regulations. For international buyers, considerations should include compliance with local health regulations, energy efficiency to reduce operational costs, and scalability to accommodate fluctuating production demands.
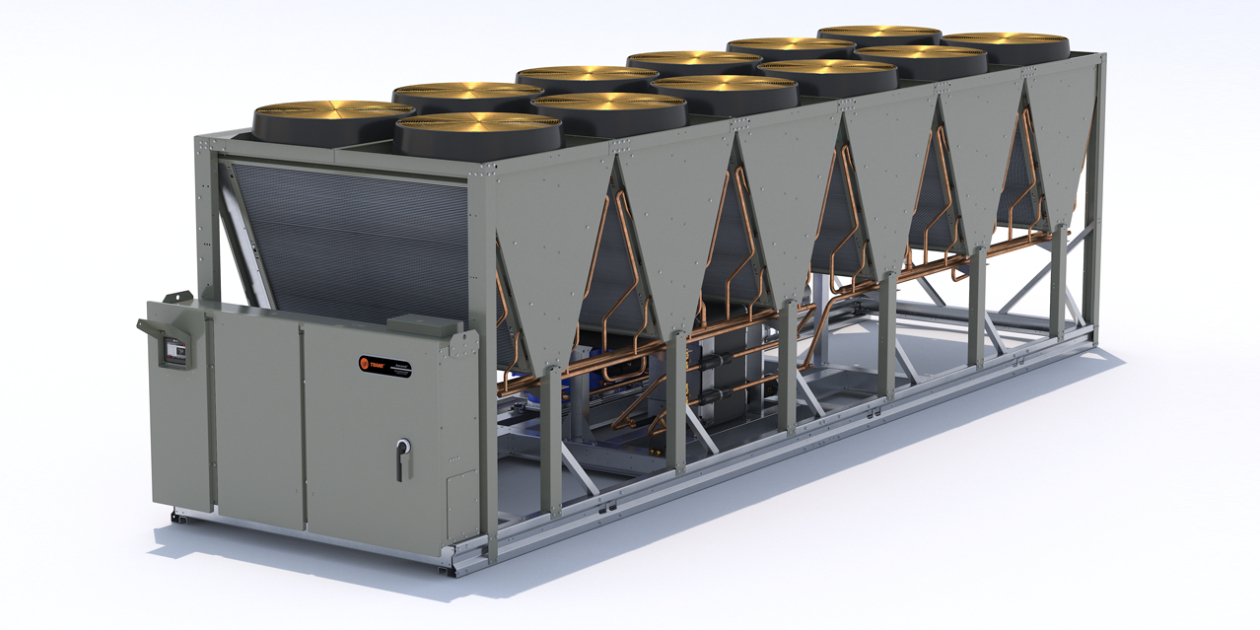
A stock image related to air cooled chiller.
What Are the Advantages of Using Air Cooled Chillers for District Cooling?
Air cooled chillers are increasingly utilized in district cooling applications, providing centralized cooling for multiple buildings within urban areas. This approach significantly reduces energy consumption and operational costs by optimizing the cooling process across several facilities. Buyers should assess infrastructure compatibility, available energy sources, and the environmental impact of their cooling solutions to ensure sustainable and efficient operations.
3 Common User Pain Points for ‘air cooled chiller’ & Their Solutions
Scenario 1: Difficulty in Selecting the Right Air-Cooled Chiller Capacity
The Problem:
International B2B buyers often face challenges in selecting the appropriate capacity of an air-cooled chiller for their specific application. This is particularly true for industries operating in hot climates such as those in Africa and the Middle East, where ambient temperatures can significantly affect cooling load requirements. Choosing a chiller that is either undersized or oversized can lead to inefficient operation, increased energy costs, and potential equipment failure, which can be detrimental to business operations.
The Solution:
To effectively determine the right chiller capacity, buyers should conduct a thorough analysis of their cooling load requirements. This includes considering factors such as the size of the facility, the type of equipment being cooled, and the local climate conditions. Utilizing software tools that simulate cooling loads can provide a more accurate estimation. Additionally, collaborating with manufacturers or experienced HVAC consultants can help in understanding the nuances of different chiller technologies, such as scroll versus screw compressors. Buyers should also consider future growth and scalability when selecting a chiller, opting for models that allow for modular expansion to accommodate increased cooling demands without the need for complete replacement.
Scenario 2: High Energy Consumption and Operational Costs
The Problem:
Many businesses are increasingly concerned about energy consumption and the associated operational costs of running air-cooled chillers, especially in regions like Europe and South America where energy prices can be high. Inefficient chiller systems can lead to skyrocketing utility bills, affecting overall profitability. Additionally, regulatory pressures regarding energy efficiency are prompting buyers to seek solutions that are not only cost-effective but also environmentally friendly.
The Solution:
Investing in high-efficiency air-cooled chillers equipped with advanced technologies, such as variable speed drives and low-GWP (Global Warming Potential) refrigerants, can significantly reduce energy consumption. Buyers should look for units with high Energy Efficiency Ratio (EER) ratings, as these will deliver better performance for less energy use. Moreover, implementing regular maintenance schedules can ensure optimal performance and longevity of the chiller, reducing the likelihood of costly repairs. Engaging with manufacturers that offer energy audits can also provide insights into potential upgrades or retrofits that can enhance energy efficiency. Additionally, considering options like integrated free cooling can leverage ambient air during cooler months, further decreasing reliance on energy-intensive cooling systems.
Scenario 3: Noise and Vibration Concerns in Sensitive Environments
The Problem:
In commercial settings such as hospitals, hotels, and office buildings, excessive noise and vibration from air-cooled chillers can disrupt operations and negatively impact the comfort of occupants. This is a particular concern in urban areas across Europe and South America, where noise regulations are stringent. B2B buyers need solutions that can provide effective cooling without compromising the acoustic environment.
The Solution:
Buyers should prioritize selecting air-cooled chillers specifically designed for low noise operation. Features such as sound-insulated enclosures, vibration isolation mounts, and fan speed modulation can significantly reduce noise levels. When sourcing chillers, it’s essential to review sound power level ratings and consult with manufacturers about their quiet operation models. Additionally, conducting site assessments to determine optimal placement for chillers can mitigate noise issues—situating the units away from sensitive areas or using acoustic barriers can further help. Engaging acoustical engineers during the planning phase can also provide tailored solutions that address both cooling efficiency and noise concerns, ensuring compliance with local regulations while maintaining occupant comfort.
Strategic Material Selection Guide for air cooled chiller
What Are the Key Materials Used in Air-Cooled Chillers?
When selecting an air-cooled chiller, the choice of materials significantly influences performance, durability, and cost-effectiveness. Here, we analyze four common materials used in the construction of air-cooled chillers: aluminum, stainless steel, copper, and plastic composites. Each material has unique properties and implications for international B2B buyers, particularly those in Africa, South America, the Middle East, and Europe.
How Does Aluminum Impact Air-Cooled Chiller Performance?
Aluminum is widely used in air-cooled chillers, especially for components such as heat exchangers and casings. Its key properties include a high strength-to-weight ratio and excellent thermal conductivity, which enhance heat transfer efficiency. Aluminum also has good corrosion resistance, particularly when anodized, making it suitable for various environments.
Pros: Aluminum is lightweight, facilitating easier installation and reduced shipping costs. It is also relatively inexpensive compared to other metals, making it a cost-effective choice for manufacturers.
Cons: While it offers decent corrosion resistance, aluminum can be susceptible to galvanic corrosion when in contact with other metals. Additionally, it may not withstand high-pressure applications as effectively as steel.
Impact on Application: Aluminum is compatible with various refrigerants and can handle typical operational pressures in air-cooled chillers. However, care must be taken in mixed-metal environments to prevent corrosion issues.
Considerations for International Buyers: Compliance with standards such as ASTM and DIN is essential. Buyers should also consider local environmental conditions, as regions with high humidity or saline air may require additional protective coatings.
What Role Does Stainless Steel Play in Chiller Applications?
Stainless steel is another popular material for air-cooled chillers, particularly in components exposed to harsh environments, such as condensers and evaporators. Its key properties include excellent corrosion resistance and high tensile strength, allowing it to withstand high pressures and temperatures.
Pros: Stainless steel’s durability makes it ideal for long-term use, reducing the need for frequent replacements. Its resistance to corrosion ensures that it maintains performance over time, especially in challenging environments.
Cons: The primary drawback of stainless steel is its higher cost compared to aluminum. Additionally, it is heavier, which can increase shipping and installation costs.
Impact on Application: Stainless steel is highly compatible with various refrigerants and can handle extreme temperature fluctuations, making it suitable for industrial applications.
Considerations for International Buyers: Buyers should ensure that the stainless steel grades used comply with international standards like ASTM A240. Understanding local sourcing options can also help mitigate costs.
How Does Copper Enhance Efficiency in Air-Cooled Chillers?
Copper is often utilized in the manufacturing of heat exchangers due to its superior thermal conductivity and ductility. It allows for efficient heat transfer, which is critical for the performance of air-cooled chillers.
Pros: Copper’s excellent thermal properties lead to improved energy efficiency, which can significantly reduce operational costs. It is also resistant to corrosion, particularly when treated or coated.
Cons: The primary disadvantage of copper is its cost, which is higher than aluminum and some plastics. Additionally, copper can be prone to corrosion in certain environments, necessitating protective measures.
Impact on Application: Copper is compatible with a wide range of refrigerants and is effective in high-temperature applications, making it a preferred choice for high-performance chillers.
Considerations for International Buyers: Buyers should be aware of the fluctuating market prices for copper and consider local regulations regarding the use of copper in HVAC systems, especially in regions with stringent environmental standards.
What Advantages Do Plastic Composites Offer in Chiller Design?
Plastic composites are increasingly used in air-cooled chillers, particularly for non-structural components. They are lightweight and resistant to corrosion, making them suitable for various applications.
Pros: The primary advantage of plastic composites is their resistance to corrosion and chemicals, which makes them ideal for humid or aggressive environments. They are also lightweight, reducing shipping and installation costs.
Cons: Plastic composites generally have lower thermal conductivity compared to metals, which can impact overall efficiency. Additionally, their mechanical properties may not be suitable for high-pressure applications.
Impact on Application: While plastic composites can be used in specific components, they are not typically suitable for critical heat exchange areas. Their use is best suited for non-load-bearing applications.
Considerations for International Buyers: Buyers should ensure that the plastics used meet international standards such as ISO and ASTM. Understanding the local climate and its effects on material performance is crucial for long-term reliability.
Summary Table of Material Properties for Air-Cooled Chillers
Material | Typical Use Case for Air-Cooled Chiller | Key Advantage | Key Disadvantage/Limitation | Relative Cost (Low/Med/High) |
---|---|---|---|---|
Aluminum | Heat exchangers, casings | Lightweight, cost-effective | Susceptible to galvanic corrosion | Low |
Stainless Steel | Condensers, evaporators | Excellent durability and corrosion resistance | Higher cost, heavier | High |
Copper | Heat exchangers | Superior thermal conductivity | Higher cost, prone to corrosion in certain environments | Med |
Plastic Composites | Non-structural components | Corrosion resistant, lightweight | Lower thermal conductivity, not suitable for high-pressure | Low |
This analysis provides a comprehensive overview of the materials commonly used in air-cooled chillers, offering international B2B buyers actionable insights for informed decision-making. By understanding the properties, advantages, and limitations of each material, buyers can choose the most suitable options for their specific applications and regional requirements.
In-depth Look: Manufacturing Processes and Quality Assurance for air cooled chiller
What Are the Key Stages in the Manufacturing Process of Air-Cooled Chillers?
The manufacturing of air-cooled chillers involves a series of critical stages that ensure both performance and reliability. Understanding these stages can help international B2B buyers make informed decisions when selecting suppliers.
Material Preparation: What Materials Are Used in Air-Cooled Chillers?
The first stage in manufacturing air-cooled chillers is material preparation. Manufacturers typically use high-quality metals such as aluminum and copper for heat exchangers due to their excellent thermal conductivity. Steel is often used for the chassis and frame to provide structural integrity. Additionally, manufacturers may incorporate environmentally friendly refrigerants, adhering to regulations like the European F-Gas Regulation, to minimize environmental impact.
How Is Forming Done in Air-Cooled Chiller Manufacturing?
Following material preparation, the forming process shapes components through techniques like stamping, bending, and welding. This stage is critical for creating the heat exchangers, compressor housings, and other vital parts. Advanced technologies, such as CNC machining, are often utilized for precision and efficiency. Quality control measures are integrated at this stage to ensure all components meet specified tolerances.
What Does the Assembly Process Look Like for Air-Cooled Chillers?
The assembly phase brings together the various components. Skilled technicians or automated systems carefully assemble the chillers, ensuring that each part is correctly positioned and secured. Key components, such as the compressor, evaporator, and condenser, are integrated, followed by the installation of electrical systems and control panels. It is during this phase that quality assurance checks are crucial to ensure that all parts are functioning as intended.
What Finishing Techniques Are Applied to Air-Cooled Chillers?
After assembly, the finishing stage involves applying protective coatings and conducting final inspections. Coatings may include anti-corrosive finishes that enhance durability, especially in regions with high humidity or saline environments. Final inspections at this stage often include pressure tests and leak detection to ensure the integrity of the entire system before it moves to the packaging stage.
How Is Quality Assurance Managed in Air-Cooled Chiller Manufacturing?
Quality assurance (QA) is essential in the manufacturing of air-cooled chillers to ensure reliability and compliance with international standards. Manufacturers typically implement a multi-tiered QA process, which includes:
What International Standards Should Buyers Be Aware Of?
International standards such as ISO 9001 focus on quality management systems, ensuring that manufacturers maintain consistent quality across their processes. Additionally, industry-specific certifications like CE for European markets or API standards for oil and gas applications are crucial indicators of compliance with safety and performance criteria.
What Are the Key Quality Control Checkpoints During Manufacturing?
Quality control checkpoints are integrated throughout the manufacturing process, including:
- Incoming Quality Control (IQC): This involves inspecting raw materials upon delivery to ensure they meet specified standards.
- In-Process Quality Control (IPQC): Continuous monitoring during manufacturing helps identify any defects or deviations from standards early in the process.
- Final Quality Control (FQC): This final inspection phase assesses the completed chillers for functionality, safety, and compliance with specifications.
Which Testing Methods Are Commonly Used in Air-Cooled Chiller Manufacturing?
Manufacturers employ various testing methods to ensure the quality and performance of air-cooled chillers. Common testing techniques include:
- Performance Testing: Evaluating the chiller’s cooling capacity and efficiency under different operating conditions.
- Leak Testing: Using methods such as pressure decay or helium leak testing to ensure no refrigerant escapes.
- Vibration Testing: Assessing operational stability and identifying potential mechanical issues.
How Can B2B Buyers Verify Supplier Quality Control Practices?
B2B buyers should take proactive steps to verify the quality control practices of their suppliers. This can include:
- Supplier Audits: Conducting on-site audits to review manufacturing processes, quality control measures, and compliance with international standards.
- Requesting Quality Reports: Suppliers should provide detailed reports on their quality management systems, including results from various tests conducted during manufacturing.
- Third-Party Inspections: Engaging independent inspection agencies can provide unbiased assessments of a supplier’s manufacturing quality and compliance with industry standards.
What Unique Quality Control Considerations Exist for International Buyers?
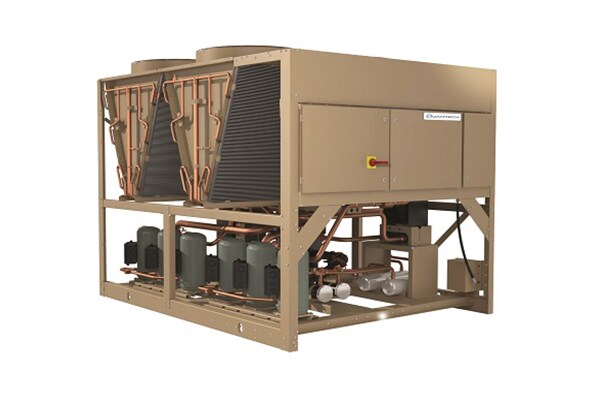
A stock image related to air cooled chiller.
International buyers, especially from regions like Africa, South America, the Middle East, and Europe, must consider unique quality control nuances. This includes understanding local regulations and certifications that may differ from those in their home countries. Furthermore, buyers should be aware of the logistics involved in shipping and receiving equipment, which can introduce additional risks. Ensuring that suppliers can provide robust documentation and support for international standards is vital.
Conclusion: Making Informed Decisions as an International B2B Buyer
Understanding the manufacturing processes and quality assurance measures for air-cooled chillers is crucial for international B2B buyers. By focusing on key stages such as material preparation, assembly, and quality control, buyers can ensure they select reliable suppliers who meet both local and international standards. This knowledge not only aids in making informed purchasing decisions but also helps establish long-term partnerships that drive efficiency and sustainability in their operations.
Practical Sourcing Guide: A Step-by-Step Checklist for ‘air cooled chiller’
Introduction
When sourcing an air-cooled chiller, it’s essential to follow a structured approach to ensure that you make an informed decision that aligns with your operational requirements and budget constraints. This checklist will guide international B2B buyers, particularly from Africa, South America, the Middle East, and Europe, through the critical steps necessary to procure an air-cooled chiller that meets their specific needs.
Step 1: Define Your Technical Specifications
Before you begin your search for an air-cooled chiller, clearly define your technical requirements. This includes understanding your cooling load, which is essential for determining the right size and capacity of the chiller.
- Cooling Load Assessment: Calculate the total heat load in your facility to ensure the chiller can meet demand.
- Type of Chiller: Decide between scroll, screw, or magnetic-bearing chillers based on your application and efficiency needs.
Step 2: Set Your Budget and Financing Options
Establishing a budget is critical to avoid overspending and to ensure financial feasibility. Consider both initial investment and long-term operational costs.
- Total Cost of Ownership (TCO): Include purchase price, installation, maintenance, and energy consumption in your budget.
- Financing Options: Explore leasing or financing arrangements that might ease cash flow constraints.
Step 3: Research and Shortlist Suppliers
Conduct thorough research to identify potential suppliers who specialize in air-cooled chillers. A well-informed shortlist can streamline your selection process.
- Supplier Reputation: Look for suppliers with a strong track record in your industry and region.
- Product Range: Ensure they offer a variety of models that meet your specifications.
Step 4: Evaluate Supplier Certifications and Compliance
Verify that your shortlisted suppliers comply with relevant industry standards and certifications. This step is crucial for ensuring product quality and safety.
- Certifications: Check for ISO certifications, energy efficiency ratings, and compliance with local environmental regulations.
- Sustainability Practices: Consider suppliers who prioritize eco-friendly refrigerants and technologies.
Step 5: Request Proposals and Compare Features
After narrowing down your list of suppliers, request detailed proposals. Comparing these can help you identify the best fit for your needs.
- Feature Comparison: Look for energy efficiency, noise levels, and advanced controls in the proposals.
- Warranty and Support: Evaluate the warranty terms and after-sales support services offered by each supplier.
Step 6: Visit Existing Installations or Request References
Where possible, visit installations of the chillers you are considering or request references from current users. This can provide invaluable insights into performance and reliability.
- On-Site Evaluation: Observe the chillers in operation to assess their performance and any potential issues.
- User Feedback: Speak with existing customers to understand their experiences, including maintenance challenges and energy consumption.
Step 7: Negotiate Terms and Finalize the Purchase
Once you’ve selected a supplier, negotiate the terms of purchase, including pricing, delivery schedules, and installation support.
- Contract Clarity: Ensure that all agreed terms are clearly outlined in the contract to avoid future disputes.
- Payment Terms: Discuss flexible payment options that align with your financial capabilities.
By following this step-by-step checklist, international B2B buyers can effectively navigate the complexities of sourcing air-cooled chillers, ensuring they choose a solution that meets their operational needs and budget constraints.
Comprehensive Cost and Pricing Analysis for air cooled chiller Sourcing
What Are the Key Cost Components for Air-Cooled Chillers?
When sourcing air-cooled chillers, understanding the cost structure is crucial for international B2B buyers. The primary components contributing to the overall cost include:
-
Materials: The choice of materials significantly influences pricing. High-quality metals and insulation materials increase durability and efficiency but also raise costs. Buyers should consider the long-term benefits of investing in superior materials.
-
Labor: Labor costs vary by region, impacting manufacturing expenses. In regions with higher labor costs, such as Europe, expect to pay more for production. However, skilled labor often results in better-quality products.
-
Manufacturing Overhead: This includes costs related to utilities, facilities, and equipment maintenance. Efficient manufacturing processes can reduce overhead and subsequently lower prices for buyers.
-
Tooling: Custom tooling for specific chiller designs can be a significant upfront cost. Buyers should evaluate whether the investment in custom tooling aligns with their volume needs.
-
Quality Control (QC): Implementing stringent QC measures ensures product reliability. While this adds to costs, it can prevent expensive failures and maintenance issues down the line.
-
Logistics: Shipping costs can fluctuate based on distance, mode of transport, and current fuel prices. Understanding logistics is vital, particularly for international buyers who may face additional tariffs and duties.
-
Margin: Supplier profit margins vary widely based on brand reputation, market demand, and product uniqueness. Established brands may command higher prices due to perceived reliability and performance.
How Do Price Influencers Affect Air-Cooled Chiller Costs?
Several factors can influence the price of air-cooled chillers, particularly for international buyers:
-
Volume and Minimum Order Quantity (MOQ): Larger orders typically result in better pricing due to economies of scale. Buyers should consider negotiating MOQs to achieve cost savings.
-
Specifications and Customization: Custom specifications can increase costs due to additional design and manufacturing requirements. Buyers should weigh the necessity of customization against budget constraints.
-
Materials and Quality Certifications: High-quality materials and certifications (e.g., ISO, ASHRAE) can elevate prices. However, they often correlate with better performance and lower Total Cost of Ownership (TCO).
-
Supplier Factors: The choice of supplier can impact pricing significantly. Established suppliers may offer higher prices but provide better support and warranty services. Newer suppliers might be more competitive but could lack reliability.
-
Incoterms: The agreed-upon Incoterms determine the responsibilities of buyers and sellers in shipping. Understanding these terms can help buyers estimate additional costs related to shipping, insurance, and customs.
What Are the Best Buyer Tips for Negotiating Air-Cooled Chiller Prices?
Navigating the procurement process for air-cooled chillers requires strategic negotiation and cost management:
-
Negotiate Terms: Always engage in discussions regarding pricing, payment terms, and delivery schedules. A flexible approach can lead to better deals.
-
Focus on Total Cost of Ownership (TCO): Rather than merely comparing upfront costs, consider the TCO, which includes energy efficiency, maintenance, and potential downtime. A higher initial investment may lead to lower operating costs.
-
Explore Pricing Nuances for International Buyers: Be aware of fluctuating exchange rates, tariffs, and local market conditions that can affect pricing. Understanding regional market trends can provide leverage in negotiations.
-
Conduct a Supplier Assessment: Evaluate potential suppliers based on reliability, service, and past performance. Building a relationship with a trustworthy supplier can lead to better pricing and service in the long run.
Disclaimer for Indicative Prices
Prices for air-cooled chillers can vary widely based on the factors mentioned above. It is essential for buyers to conduct thorough market research and supplier evaluations to obtain accurate and competitive pricing tailored to their specific needs.
Alternatives Analysis: Comparing air cooled chiller With Other Solutions
Exploring Alternatives to Air Cooled Chillers: What Are Your Options?
When considering cooling solutions for industrial or commercial applications, air cooled chillers are a popular choice. However, it’s crucial to evaluate viable alternatives that may better meet specific operational needs or budget constraints. This section compares air cooled chillers with water cooled chillers and magnetic-bearing chillers, providing valuable insights for international B2B buyers.
Comparison Aspect | Air Cooled Chiller | Water Cooled Chiller | Magnetic-Bearing Chiller |
---|---|---|---|
Performance | Moderate efficiency; suitable for small to medium loads | High efficiency; ideal for large loads | Exceptional efficiency; suitable for high-capacity needs |
Cost | Generally lower initial cost; affordable maintenance | Higher initial investment; potential savings over time | High initial cost; significant long-term savings |
Ease of Implementation | Simple installation; minimal site preparation | More complex installation; requires additional equipment | Complex installation; requires skilled technicians |
Maintenance | Low maintenance; accessible components | Moderate maintenance; cooling towers require upkeep | Minimal maintenance; oil-free operation reduces costs |
Best Use Case | Small to medium commercial applications | Large commercial buildings; district cooling | Data centers; industrial processes with high cooling demands |
In-Depth Analysis of Alternatives
What Are the Benefits of Water Cooled Chillers?
Water cooled chillers utilize water as a heat exchange medium, allowing for superior heat transfer capabilities compared to air cooled chillers. They are often more efficient, especially in larger installations, making them ideal for high-demand applications such as district cooling. However, the initial investment is higher, and they require a reliable water source, which can be a concern in regions facing water scarcity. Maintenance can also be more involved due to the need for regular upkeep of cooling towers.
Why Consider Magnetic-Bearing Chillers?
Magnetic-bearing chillers represent a cutting-edge technology that offers remarkable efficiency. By eliminating the need for oil lubrication, these chillers reduce energy losses and maintenance requirements significantly. They are particularly advantageous for data centers and industrial applications that require consistent and reliable cooling performance. The downside is the higher upfront cost, which may deter budget-sensitive buyers. However, the potential for long-term operational savings can justify the initial investment.
How to Choose the Right Cooling Solution for Your Business Needs
Selecting the appropriate cooling solution involves assessing several factors, including operational requirements, budget constraints, and environmental considerations. B2B buyers should conduct a comprehensive analysis of their cooling loads, available resources, and long-term operational goals. For those in regions like Africa or South America, where water scarcity is a concern, air cooled chillers may offer a more sustainable option. Conversely, European buyers in larger facilities might find that water cooled or magnetic-bearing chillers provide better efficiency and performance. Ultimately, the right choice will depend on balancing initial costs with long-term efficiency and reliability.
Essential Technical Properties and Trade Terminology for air cooled chiller
What Are the Essential Technical Properties of Air Cooled Chillers?
When sourcing air cooled chillers, understanding their technical specifications is crucial for making informed purchasing decisions. Below are key properties that international B2B buyers should consider:
1. Cooling Capacity
Cooling capacity, measured in tons, indicates the amount of heat a chiller can remove from a space per hour. Common ranges for air cooled chillers are between 10 to 500 tons. Selecting a chiller with the appropriate cooling capacity ensures optimal performance and energy efficiency, preventing over or under-sizing that could lead to higher operational costs.
2. Energy Efficiency Ratio (EER)
The EER is a measure of a chiller’s cooling output divided by its energy consumption, expressed in BTU/watt-hour. A higher EER signifies a more efficient unit, which translates to lower energy costs and a reduced environmental impact. Buyers should prioritize chillers with high EER ratings to align with sustainability goals and regulatory requirements, particularly in regions with stringent energy efficiency standards.
3. Refrigerant Type
Refrigerants are substances used in chillers to absorb and release heat. Current trends favor low Global Warming Potential (GWP) refrigerants, such as R-454B or R-513A, which are more environmentally friendly than traditional refrigerants like R-22. Understanding refrigerant types is vital for compliance with local regulations and for minimizing environmental impact, which is increasingly important to B2B buyers globally.
4. Compressor Type
Chillers typically use either scroll or screw compressors. Scroll compressors are generally quieter and more efficient for smaller applications, while screw compressors are better suited for larger cooling capacities. The choice of compressor affects not only the initial investment but also ongoing maintenance costs and energy consumption, making it a significant consideration for buyers.
5. Operating Temperature Range
The operating temperature range indicates the ambient conditions in which the chiller can function effectively. This property is particularly important for businesses in regions with extreme weather conditions, as it ensures the chiller operates reliably throughout the year. Buyers should verify that the chosen chiller’s operating range aligns with their specific environmental conditions.
6. Noise Levels
Noise levels, typically measured in decibels (dB), are an essential consideration, especially for chillers installed in noise-sensitive environments like residential areas or hospitals. Selecting a low-noise chiller can help maintain compliance with local noise regulations and enhance overall operational comfort.
What Are Common Trade Terms Related to Air Cooled Chillers?
Understanding industry jargon can help buyers navigate the procurement process more effectively. Below are some common trade terms related to air cooled chillers:
1. OEM (Original Equipment Manufacturer)
An OEM is a company that produces parts or equipment that may be marketed by another manufacturer. In the context of air cooled chillers, buyers often engage with OEMs for custom specifications or replacement parts, ensuring compatibility and quality.
2. MOQ (Minimum Order Quantity)
MOQ refers to the smallest quantity of a product that a supplier is willing to sell. For air cooled chillers, MOQs can vary significantly based on the manufacturer. Understanding MOQs is essential for budgeting and inventory planning, especially for companies in regions with specific cooling demands.
3. RFQ (Request for Quotation)
An RFQ is a document issued by a buyer to solicit price offers from suppliers. In the chiller market, an RFQ typically includes specifications such as capacity, efficiency, and installation requirements. Crafting a detailed RFQ helps ensure that buyers receive accurate and competitive pricing.
4. Incoterms (International Commercial Terms)
Incoterms are a series of predefined international sales terms that clarify the responsibilities of buyers and sellers in international transactions. Understanding Incoterms is crucial for B2B buyers to manage shipping costs, insurance, and customs clearance effectively.
5. Lead Time
Lead time refers to the period from placing an order until delivery. For air cooled chillers, lead times can vary based on the complexity of the order and the manufacturer’s production schedule. Buyers should consider lead times when planning project timelines to avoid delays.
6. Warranty Period
The warranty period is the time frame during which the manufacturer guarantees the product against defects. For air cooled chillers, warranties typically range from 1 to 5 years. Buyers should evaluate warranty terms to understand their potential long-term costs and service commitments.
By focusing on these technical properties and trade terms, international B2B buyers can make informed decisions when purchasing air cooled chillers, ultimately ensuring optimal performance and cost-effectiveness for their operations.
Navigating Market Dynamics and Sourcing Trends in the air cooled chiller Sector
What Are the Current Market Dynamics and Key Trends in the Air-Cooled Chiller Sector?
The air-cooled chiller market is experiencing significant transformation, driven by the growing demand for energy-efficient cooling solutions across various sectors, including industrial, commercial, and data centers. In regions such as Africa, South America, the Middle East, and Europe, the need for reliable and efficient cooling systems is on the rise due to increasing urbanization and industrialization. B2B buyers are particularly focused on solutions that not only meet their cooling requirements but also adhere to local regulations and energy efficiency standards.
Emerging technologies such as variable-speed compressors and advanced refrigerants are shaping the landscape. International buyers should look for chillers that offer superior performance metrics, such as lower Energy Efficiency Ratio (EER) ratings and compliance with global standards like ASHRAE. Additionally, the integration of IoT technology in chiller systems allows for real-time monitoring and predictive maintenance, enhancing operational efficiency and minimizing downtime.
Another critical trend is the shift towards modular and scalable systems, which provide flexibility for businesses to adapt their cooling capacity based on fluctuating demands. This is especially relevant for growing enterprises in developing regions where rapid changes in operational scale can occur. Buyers should prioritize vendors that offer customizable solutions to meet specific project needs, ensuring that both initial investments and long-term operational costs are optimized.
How Can Sustainability and Ethical Sourcing Influence B2B Decisions in the Air-Cooled Chiller Sector?
Sustainability is becoming a non-negotiable aspect of sourcing decisions for B2B buyers in the air-cooled chiller market. The environmental impact of cooling systems, particularly in regions facing climate change challenges, has led many businesses to seek ‘green’ certifications and sustainable materials. Air-cooled chillers that utilize low-global warming potential (GWP) refrigerants are increasingly preferred, as they align with global sustainability goals and local regulations aimed at reducing carbon footprints.
Ethical sourcing also plays a vital role in supply chain decisions. International buyers should evaluate suppliers based on their commitment to responsible manufacturing practices, labor rights, and environmental stewardship. Certifications such as ISO 14001 for environmental management and LEED for energy efficiency can provide assurance of a supplier’s dedication to sustainability. Additionally, engaging with manufacturers who prioritize local sourcing can enhance community relations and reduce transportation emissions, further contributing to an ethical supply chain.
B2B buyers are encouraged to conduct thorough due diligence when evaluating potential suppliers, ensuring that their choices reflect not only cost considerations but also long-term commitments to environmental and social responsibility. This strategic approach can enhance brand reputation and customer loyalty, particularly among eco-conscious consumers.
What Is the Brief Evolution of the Air-Cooled Chiller Market?
The evolution of the air-cooled chiller market can be traced back to the early 20th century when these systems were primarily employed in commercial buildings. Over the decades, advancements in refrigeration technology and increased awareness of energy efficiency have driven significant improvements in performance and reliability.
In the late 20th century, the introduction of scroll and screw compressor technologies revolutionized the sector, allowing for higher efficiencies and lower maintenance requirements. The 21st century has witnessed a further shift towards environmentally friendly refrigerants and smart technologies, aligning with global sustainability initiatives. Today, air-cooled chillers are integral to modern infrastructure, providing critical cooling solutions across diverse applications, from industrial manufacturing to data centers, while continuously adapting to meet evolving energy standards and consumer expectations.
As international B2B buyers navigate this dynamic market, understanding these historical trends can inform strategic sourcing decisions, ensuring they invest in solutions that are both reliable and future-proof.
Frequently Asked Questions (FAQs) for B2B Buyers of air cooled chiller
-
How do I select the right air-cooled chiller for my needs?
Choosing the right air-cooled chiller involves assessing your specific cooling requirements, including load capacity, efficiency, and application type. Start by calculating the cooling load for your facility to determine the appropriate tonnage. Consider factors such as energy efficiency ratings (EER), operational noise levels, and refrigerant types. Additionally, evaluate the installation space and local climate, as these can influence performance. Partnering with a reputable supplier can provide insights into customization options tailored to your unique needs. -
What are the advantages of air-cooled chillers compared to water-cooled chillers?
Air-cooled chillers offer several advantages, including lower installation costs, reduced water usage, and minimal maintenance requirements. They are ideal for applications where water availability is limited or where environmental concerns are paramount. Additionally, air-cooled chillers are easier to install and relocate, making them suitable for temporary or mobile cooling solutions. While they may be less efficient in large-scale operations compared to water-cooled options, advancements in technology have improved their performance significantly. -
What factors should I consider when vetting suppliers for air-cooled chillers?
When vetting suppliers, consider their experience, reputation, and the range of products offered. Look for suppliers with a track record in your specific industry and check references from previous clients. Ensure that they provide comprehensive support, including installation, maintenance, and after-sales service. Additionally, assess their certifications and compliance with international quality standards to ensure reliability and performance. Don’t hesitate to request detailed technical specifications and warranties for the equipment. -
What is the minimum order quantity (MOQ) for air-cooled chillers?
Minimum order quantities (MOQ) for air-cooled chillers can vary significantly based on the manufacturer and the specific model. Generally, MOQs might range from a single unit to several units for bulk orders. It’s crucial to clarify this with the supplier before placing an order. For smaller businesses or projects, some suppliers may offer flexible terms or allow for sample orders to facilitate trial runs. Always inquire about potential discounts for larger orders or long-term contracts. -
What payment terms are typically offered for international purchases of air-cooled chillers?
Payment terms for international purchases can vary widely, but common options include advance payments, letters of credit, or payment upon delivery. Many suppliers may offer a deposit system, where a percentage of the total cost is paid upfront, followed by the balance upon delivery or installation. Always negotiate favorable terms that align with your cash flow and project timelines. Ensure that payment methods are secure and consider any currency exchange implications when dealing with international suppliers. -
How can I ensure quality assurance (QA) for my air-cooled chiller purchase?
To ensure quality assurance, request detailed documentation from the supplier, including product specifications, test reports, and certifications. It’s advisable to conduct factory visits or inspections before shipment, especially for larger orders. Additionally, inquire about the supplier’s quality control processes and whether they adhere to international standards such as ISO 9001. Establishing a clear communication channel with the supplier can also facilitate timely updates on the production and delivery process. -
What logistics considerations should I keep in mind when importing air-cooled chillers?
Logistics considerations for importing air-cooled chillers include shipping methods, customs clearance, and transportation costs. Depending on the size and weight of the chillers, you may need to choose between air freight and ocean freight. Factor in lead times for both production and shipping, as well as any potential delays at customs. Engage with a logistics partner experienced in handling industrial equipment to streamline the process and ensure compliance with local regulations and import duties. -
Can air-cooled chillers be customized for specific applications?
Yes, many manufacturers offer customization options for air-cooled chillers to meet specific application needs. Customizations can include adjustments to capacity, energy efficiency ratings, refrigerant types, and noise levels. Additionally, features like integrated controls and monitoring systems can be tailored for particular operational requirements. Engage with your supplier early in the process to discuss your needs and explore available options that enhance the chiller’s performance for your unique applications.
Important Disclaimer & Terms of Use
⚠️ Important Disclaimer
The information provided in this guide, including content regarding manufacturers, technical specifications, and market analysis, is for informational and educational purposes only. It does not constitute professional procurement advice, financial advice, or legal advice.
While we have made every effort to ensure the accuracy and timeliness of the information, we are not responsible for any errors, omissions, or outdated information. Market conditions, company details, and technical standards are subject to change.
B2B buyers must conduct their own independent and thorough due diligence before making any purchasing decisions. This includes contacting suppliers directly, verifying certifications, requesting samples, and seeking professional consultation. The risk of relying on any information in this guide is borne solely by the reader.
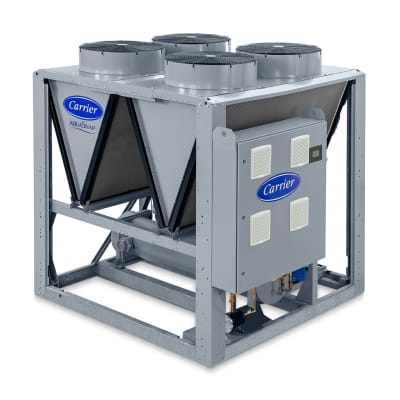
A stock image related to air cooled chiller.
Strategic Sourcing Conclusion and Outlook for air cooled chiller
As the global demand for efficient cooling solutions continues to rise, strategic sourcing of air-cooled chillers becomes paramount for international B2B buyers, especially from regions like Africa, South America, the Middle East, and Europe. By understanding the various types of chillers—such as scroll and screw chillers—and their specific applications in industries ranging from data centers to industrial refrigeration, buyers can make informed decisions that align with their operational needs.
Why is Strategic Sourcing Essential for Air-Cooled Chillers?
The value of strategic sourcing lies in its ability to ensure that companies select chillers that not only meet their immediate cooling requirements but also contribute to long-term energy efficiency and sustainability goals. With advances in technology, such as magnetic-bearing chillers and low-GWP refrigerants, buyers can leverage these innovations to reduce operational costs and enhance environmental performance.
How Can Buyers Prepare for Future Cooling Needs?
Looking ahead, international buyers should focus on establishing partnerships with reliable manufacturers and suppliers who offer customizable solutions tailored to specific project demands. This proactive approach will help mitigate risks associated with supply chain disruptions while ensuring access to cutting-edge technologies.
In conclusion, as the landscape of cooling solutions evolves, now is the time for B2B buyers to engage in strategic sourcing of air-cooled chillers. By prioritizing efficiency and sustainability, companies can position themselves for success in an increasingly competitive market.