Unlock the True Cost: How Much is a CNC Machine for B2B
Introduction: Navigating the Global Market for how much is a cnc machine
In today’s competitive manufacturing landscape, the decision to invest in a CNC (Computer Numerical Control) machine is pivotal for businesses aiming to enhance precision, efficiency, and scalability. Understanding how much a CNC machine costs is not just a matter of budget; it directly impacts your operational efficiency, production capacity, and ultimately, your bottom line. Prices can vary dramatically—from affordable entry-level models costing around $5,000 to high-end industrial systems exceeding $500,000—depending on machine type, capabilities, and regional market dynamics.
This comprehensive guide is designed to demystify CNC machine pricing for international B2B buyers, particularly those in Africa, South America, the Middle East, and Europe. We will cover essential topics, including:
- Comparative analysis of CNC machine types: routers, laser cutters, milling machines, and more.
- Material considerations tailored to various industries and applications.
- Manufacturing quality and certification standards critical for international procurement.
- Evaluating global suppliers to ensure alignment with your operational needs.
- Detailed cost breakdowns encompassing purchase, installation, and maintenance.
By equipping yourself with this knowledge, you can make informed sourcing decisions that minimize risk and maximize ROI. Whether you are looking to optimize your production capabilities or navigate the complexities of international trade, this guide provides actionable insights to empower your CNC machine acquisition strategy. Embrace the potential of CNC technology and position your business for sustained success in a rapidly evolving global market.
Understanding how much is a cnc machine Types and Variations
Type Name | Key Distinguishing Features | Primary B2B Applications | Brief Pros & Cons for Buyers |
---|---|---|---|
CNC Router | Versatile cutting, 3-axis or higher, large bed size | Woodworking, signage, plastics | Pros: Flexible, affordable entry-level. Cons: Less suitable for metals. |
CNC Milling Machine | Multi-axis, precision machining, metal cutting | Automotive, aerospace, precision parts | Pros: Very precise, robust. Cons: Higher cost and operational complexity. |
CNC Laser Cutter | Laser-driven, high-detail, non-contact process | Metalwork, signage, electronics | Pros: Clean, detailed cuts. Cons: High initial price, requires expertise. |
CNC Plasma Cutter | Ionized gas, high-speed metal cutting, conductive materials | Metal fabrication, construction | Pros: Fast, handles thick metals. Cons: Less precise, not for non-metals. |
CNC Waterjet Cutter | High-pressure abrasive water, cuts any material | Aerospace, stoneworking, specialized parts | Pros: Highly versatile, cold cutting. Cons: Expensive, higher maintenance. |
CNC Router
CNC routers are characterized by their versatility and capability to work with various materials, including wood, plastics, and composites. They are especially suitable for businesses in woodworking and signage production. For B2B buyers, the affordability of entry-level routers makes them an attractive option, particularly for startups or small manufacturers. When evaluating routers, consider bed size, material compatibility, and features like automation to enhance productivity.
CNC Milling Machine
CNC milling machines are designed for high-precision machining, making them ideal for sectors like automotive and aerospace. These machines can handle complex geometries and are robust enough for continuous industrial use. B2B buyers should focus on the machine’s build quality, the number of axes, and local service support to ensure operational efficiency. While they represent a higher investment, their accuracy and durability can lead to significant long-term savings and productivity gains.
CNC Laser Cutter
CNC laser cutters utilize focused laser beams to achieve clean, intricate cuts on a variety of materials. They are particularly valuable in industries requiring high detail, such as electronics and signage. Buyers must consider the initial investment, ongoing consumable costs, and the need for specialized training. Despite the higher upfront costs, the efficiency and precision of laser cutters can justify the expense, especially for businesses focused on high-value products.
CNC Plasma Cutter
CNC plasma cutters are known for their speed and efficiency in cutting through thick metals, making them suitable for metal fabrication and construction applications. They are generally more affordable than laser cutters and can quickly handle large volumes. B2B buyers should assess power supply requirements and cutting bed sizes when considering plasma cutters. While they excel in speed, precision may be a drawback for intricate designs, making them best suited for specific applications.
CNC Waterjet Cutter
CNC waterjet cutters are distinguished by their ability to cut through virtually any material using high-pressure water and abrasives. This versatility makes them ideal for specialized industries such as aerospace and stoneworking. However, they come with higher costs and maintenance needs. Buyers should evaluate their specific material requirements and operational costs when considering waterjet technology. Their cold cutting process minimizes thermal distortion, making them invaluable for sensitive materials.
Related Video: How milling on a 4-axis CNC machine works
Key Industrial Applications of how much is a cnc machine
Industry/Sector | Specific Application of how much is a cnc machine | Value/Benefit for the Business | Key Sourcing Considerations for this Application |
---|---|---|---|
Automotive | Precision machining of engine components | Enhanced accuracy and reduced waste in production | Supplier certifications, local service support, and part compatibility |
Aerospace | Fabrication of complex parts for aircraft | High precision and reliability in critical applications | Material certifications, advanced machining capabilities, and compliance with industry standards |
Metal Fabrication | Custom metal parts and structural components | Increased production speed and flexibility in design | Cutting technology, machine size, and maintenance support |
Electronics Manufacturing | PCB manufacturing and housing fabrication | Improved efficiency and reduced production costs | Software compatibility, precision requirements, and supplier reputation |
Woodworking and Furniture | Production of custom furniture and cabinetry | Cost savings on materials and faster turnaround times | Bed size requirements, material compatibility, and automation features |
Automotive
In the automotive industry, CNC machines are essential for precision machining of engine components and other intricate parts. These machines enable manufacturers to achieve high accuracy, which reduces material waste and minimizes the risk of defects. For international buyers, especially in regions like South America and Africa, sourcing CNC machines that meet local standards and regulations is crucial. Additionally, ensuring robust after-sales support and availability of spare parts can significantly impact operational efficiency.
Aerospace
CNC technology plays a vital role in the aerospace sector, particularly in fabricating complex components like turbine blades and structural parts. The precision offered by CNC machines is critical, as even minor deviations can lead to catastrophic failures in aviation. International buyers must consider suppliers with a strong track record in aerospace manufacturing, ensuring that the machines adhere to stringent material certifications and industry compliance standards. Furthermore, understanding the specific machining capabilities required for various materials, such as titanium and composites, is essential for successful procurement.
Metal Fabrication
In metal fabrication, CNC machines are employed to create custom metal parts and structural components with high accuracy and speed. This capability allows businesses to respond quickly to market demands and customize products according to client specifications. For B2B buyers in regions like the Middle East, where construction and infrastructure projects are booming, selecting machines that offer advanced cutting technologies and larger bed sizes can enhance productivity. Buyers should also evaluate the maintenance support provided by suppliers to minimize downtime and ensure continuous operation.
Electronics Manufacturing
CNC machines are increasingly utilized in electronics manufacturing, particularly for producing printed circuit boards (PCBs) and enclosures. The precision and efficiency of CNC machining help reduce production costs and improve product quality. For international buyers, particularly in Europe, it is important to consider the compatibility of CNC software with existing systems and the precision requirements specific to electronics. Additionally, sourcing from reputable suppliers with experience in electronics can ensure adherence to quality standards and enhance overall supply chain reliability.
Woodworking and Furniture
CNC routers are widely used in the woodworking industry for producing custom furniture and cabinetry. They allow for intricate designs and high-volume production, significantly reducing material waste and labor costs. For B2B buyers in Africa and South America, understanding the machine’s bed size requirements and the types of materials it can handle is crucial. Furthermore, automation features such as tool changers can improve productivity and efficiency, making it essential to assess these capabilities when sourcing CNC machines for woodworking applications.
Related Video: CNC machining – What is it and How Does it Work? (Must Know Basics)
Strategic Material Selection Guide for how much is a cnc machine
When considering the acquisition of CNC machines, the choice of material for the components and products being manufactured plays a crucial role in determining performance, cost, and suitability for various applications. Below is an analysis of four common materials used in CNC machining, focusing on their properties, advantages, disadvantages, and implications for international B2B buyers.
Aluminum
Key Properties: Aluminum is lightweight, has excellent corrosion resistance, and offers good thermal and electrical conductivity. It typically withstands temperatures up to 600°F (315°C) without significant degradation.
Pros & Cons: Aluminum is durable and easy to machine, making it a popular choice for various applications, including aerospace and automotive components. However, it can be more expensive than other materials like steel, and its lower strength compared to steel may limit its use in heavy-load applications.
Impact on Application: Aluminum is compatible with a wide range of media, including air and water, making it suitable for both structural and aesthetic applications. Its lightweight nature enhances performance in applications requiring reduced weight.
Considerations for International Buyers: Buyers should ensure compliance with international standards such as ASTM for aluminum alloys. In regions like Africa and South America, sourcing aluminum may involve navigating import tariffs and shipping logistics, which can impact overall costs.
Steel
Key Properties: Steel is known for its high tensile strength, durability, and resistance to deformation. It can withstand high temperatures and pressures, making it suitable for heavy-duty applications.
Pros & Cons: The main advantage of steel is its strength and versatility, allowing it to be used in a wide range of industries, from construction to automotive. However, it is heavier than aluminum and can be prone to corrosion if not properly treated, which may increase maintenance costs.
Impact on Application: Steel’s robustness makes it ideal for applications that require high strength and durability, such as machinery parts and structural components. Its compatibility with various coatings can enhance its corrosion resistance.
Considerations for International Buyers: Buyers should be aware of the specific grades of steel required for their applications and ensure compliance with standards like DIN or JIS. In regions with varying steel quality, it is crucial to verify the supplier’s certifications.
Plastic (e.g., ABS, Nylon)
Key Properties: Plastics like ABS and Nylon are lightweight, resistant to corrosion, and can be molded into complex shapes. They typically have lower temperature resistance, with a maximum service temperature around 200°F (93°C) for ABS.
Pros & Cons: Plastics are cost-effective and easy to machine, making them suitable for prototyping and low-stress applications. However, they may not be suitable for high-strength applications and can degrade under UV exposure or extreme temperatures.
Impact on Application: Plastics are ideal for applications requiring insulation or lightweight components, such as consumer products and electronic housings. Their compatibility with various chemicals enhances their use in specific environments.
Considerations for International Buyers: Buyers should consider the environmental regulations regarding plastic use in their regions, especially in Europe, where stringent recycling and material safety standards apply. Understanding local preferences for plastic types can also guide material selection.
Titanium
Key Properties: Titanium is known for its exceptional strength-to-weight ratio, corrosion resistance, and ability to withstand extreme temperatures. It can perform well in environments up to 1,000°F (538°C).
Pros & Cons: Titanium is highly durable and suitable for specialized applications, such as aerospace and medical devices. However, it is significantly more expensive than other materials and can be challenging to machine, requiring specialized tools.
Impact on Application: Titanium’s properties make it ideal for high-performance applications where strength and weight are critical. Its biocompatibility also makes it suitable for medical implants.
Considerations for International Buyers: Buyers must be aware of the high costs associated with titanium and ensure compliance with aerospace or medical standards, which can vary significantly by region. Sourcing titanium may also involve navigating complex supply chains.
Material | Typical Use Case for how much is a cnc machine | Key Advantage | Key Disadvantage/Limitation | Relative Cost (Low/Med/High) |
---|---|---|---|---|
Aluminum | Aerospace components, automotive parts | Lightweight and corrosion-resistant | Higher cost compared to steel | Medium |
Steel | Structural components, machinery parts | High strength and durability | Heavier and prone to corrosion | Medium |
Plastic (e.g., ABS, Nylon) | Consumer products, electronic housings | Cost-effective and easy to machine | Limited strength and temperature resistance | Low |
Titanium | Aerospace, medical implants | Exceptional strength-to-weight ratio | High cost and machining complexity | High |
This comprehensive analysis equips international B2B buyers with the necessary insights to make informed decisions regarding material selection for CNC machining, ensuring alignment with operational needs and market realities.
In-depth Look: Manufacturing Processes and Quality Assurance for how much is a cnc machine
CNC manufacturing processes are a vital aspect for B2B buyers, especially those navigating the complexities of international procurement. Understanding these processes, along with the quality assurance measures that accompany them, is crucial for making informed decisions that can impact operational efficiency and overall profitability.
Manufacturing Processes
Main Stages of CNC Manufacturing
-
Material Preparation
– Selection of Material: The first step involves choosing the appropriate material based on the desired product specifications. Common materials include metals (aluminum, steel), plastics, and composites.
– Cutting and Shaping: Raw materials are cut to manageable sizes using saws or shears. This is essential for ensuring they fit within the CNC machine’s working area. -
Forming
– CNC Machining: The core process involves using CNC machines to shape the material. Techniques include milling, turning, and drilling, which depend on the complexity and requirements of the final product.
– Tool Selection: Choosing the right tooling is critical. Specialized tools might be required for different materials or complex geometries, influencing both cost and production speed. -
Assembly
– Component Assembly: In cases where multiple parts are produced, assembly may be necessary. This can involve manual or automated processes to ensure precision and efficiency.
– Integration: Assembled components may require integration with electronic systems or other mechanical parts, depending on the application. -
Finishing
– Surface Treatment: To enhance the appearance and functionality, surface treatments such as anodizing, painting, or polishing may be applied. This not only improves aesthetics but also increases durability.
– Quality Checks: Final inspections are performed to ensure that the finished product meets all specifications and standards before delivery.
Key Techniques in CNC Manufacturing
- 3D Modeling and Simulation: Advanced software allows for the creation of detailed models, enabling manufacturers to visualize the machining process and identify potential issues before production begins.
- Adaptive Machining: This technique adjusts the machining parameters in real-time based on feedback from the cutting process, optimizing tool life and product quality.
- Batch Production: CNC machines can be programmed to produce large quantities of parts consistently, which is beneficial for buyers looking to scale operations without sacrificing quality.
Quality Assurance
Quality assurance is paramount in CNC manufacturing, particularly when sourcing from international suppliers. Adherence to recognized standards ensures that products meet industry requirements and customer expectations.
Relevant International Standards
- ISO 9001: This quality management standard provides a framework for consistent quality in manufacturing. Compliance indicates a commitment to quality processes and customer satisfaction.
- CE Marking: For products sold in Europe, CE marking signifies conformity with health, safety, and environmental protection standards.
- API Standards: For industries such as oil and gas, compliance with American Petroleum Institute (API) standards is critical for safety and performance.
Quality Control Checkpoints
-
Incoming Quality Control (IQC)
– Inspection of raw materials upon receipt to ensure they meet specified standards before entering production. -
In-Process Quality Control (IPQC)
– Continuous monitoring during the machining process to catch defects early. This may include measuring dimensions, checking tolerances, and assessing tool wear. -
Final Quality Control (FQC)
– A comprehensive inspection of finished products to confirm they meet all design specifications and quality standards before shipment.
Common Testing Methods
- Dimensional Inspection: Using tools like calipers and micrometers to verify that parts meet specified dimensions.
- Material Testing: Conducting tensile tests or hardness tests to ensure material properties are within acceptable limits.
- Functional Testing: For complex assemblies, functional testing is crucial to ensure all components work together as intended.
Verifying Supplier Quality Control
For international B2B buyers, verifying supplier quality control processes is essential to mitigate risks associated with overseas procurement.
- Supplier Audits: Conducting regular audits of suppliers can provide insights into their quality management systems and adherence to industry standards.
- Quality Reports: Requesting documentation of quality control processes and results can help buyers assess the reliability of their suppliers.
- Third-Party Inspections: Engaging third-party inspection agencies can provide an unbiased assessment of a supplier’s quality practices and product conformity.
Quality Control Nuances for International Buyers
- Cultural Differences: Understanding cultural attitudes towards quality can influence supplier relationships. Buyers should be aware that expectations may vary significantly between regions.
- Regulatory Compliance: Different countries have varying regulations. B2B buyers must ensure that their suppliers meet local compliance requirements, which may include additional certifications.
- Logistics and Supply Chain: Coordinating logistics can impact quality. Buyers should ensure that transportation conditions do not compromise product integrity during shipment.
In conclusion, a thorough understanding of manufacturing processes and quality assurance practices is essential for B2B buyers, especially in regions with diverse market dynamics. By focusing on these elements, businesses can make informed decisions that enhance operational efficiency and drive long-term success in their CNC machine investments.
Related Video: SMART Quality Control for Manufacturing
Comprehensive Cost and Pricing Analysis for how much is a cnc machine Sourcing
Navigating the costs associated with sourcing CNC machines involves understanding a multifaceted cost structure and the various factors that can influence pricing. For international B2B buyers, particularly those in Africa, South America, the Middle East, and Europe, recognizing these elements can lead to more informed purchasing decisions and better alignment with operational needs.
Cost Components
-
Materials: The choice of materials significantly impacts the overall cost of CNC machines. Steel and aluminum are common in machinery construction, while specialized materials may incur additional expenses. Buyers should consider the long-term implications of material selection on machine durability and maintenance.
-
Labor: Labor costs encompass both the assembly of the machine and the operation once it is in place. Skilled machinists are required to operate complex CNC machines, and their salaries can vary widely by region. For buyers in emerging markets, training local staff can mitigate long-term operational costs.
-
Manufacturing Overhead: This includes indirect costs such as facility expenses, utilities, and administrative costs associated with production. Understanding the overhead of different suppliers can provide insights into their pricing structures.
-
Tooling: The cost of tooling, which includes cutting tools and accessories, should not be overlooked. Specialty tools can be expensive and may need to be replaced regularly. Buyers should evaluate the lifetime cost of tooling as part of their total cost of ownership.
-
Quality Control (QC): Investing in robust QC processes can add to the initial costs but may save money in the long run by ensuring high-quality outputs and reducing rework. Certifications and compliance with international standards can also influence machine pricing.
-
Logistics: Transporting CNC machines can be a substantial expense, especially when dealing with international suppliers. Shipping costs, insurance, customs duties, and local delivery must all be factored into the total expenditure.
-
Margin: Supplier margins can vary based on brand reputation and market competition. Established brands may command higher prices due to perceived reliability and quality, while lesser-known brands might offer lower prices but with potential risks.
Price Influencers
-
Volume/MOQ: The volume of machines ordered can significantly affect pricing. Higher order quantities often lead to discounted rates, making it essential for buyers to assess their needs realistically.
-
Specifications/Customization: Custom features or specifications can lead to increased costs. Buyers should clearly define their requirements to avoid unnecessary expenses related to customization.
-
Quality/Certifications: Machines that meet specific quality standards or certifications may come at a premium. Buyers in regulated industries must consider these factors when sourcing machinery.
-
Supplier Factors: The reputation and reliability of the supplier can influence pricing. Established suppliers may offer better after-sales support and warranties, which can justify a higher upfront cost.
-
Incoterms: Understanding Incoterms is crucial for international buyers as they dictate the responsibilities of buyers and sellers in shipping and logistics. This knowledge can help avoid unexpected costs and delays.
Buyer Tips
-
Negotiation: Leverage multiple quotes from different suppliers to negotiate better pricing. Understanding the market rates and being informed about competitor offerings can strengthen your bargaining position.
-
Cost-Efficiency: Focus on the total cost of ownership rather than just the initial purchase price. This includes maintenance, operational costs, and the longevity of the machine.
-
Pricing Nuances: Be aware of regional pricing variations and the impact of currency fluctuations. Engaging with local suppliers in your region may provide cost advantages and reduce logistics expenses.
-
Long-term Relationships: Building strong relationships with suppliers can lead to better pricing and service over time. Consider establishing partnerships that can offer mutual benefits in the long run.
Disclaimer
The prices associated with CNC machines can vary widely based on numerous factors, including machine type, specifications, and regional market conditions. The figures provided in various sources should be viewed as indicative rather than definitive, and buyers should conduct thorough market research tailored to their specific needs and circumstances.
Spotlight on Potential how much is a cnc machine Manufacturers and Suppliers
This section looks at several manufacturers active in the ‘how much is a cnc machine’ market. This is a representative sample for illustrative purposes; B2B buyers must conduct extensive due diligence before any transaction. Information is synthesized from public sources and general industry knowledge.
Essential Technical Properties and Trade Terminology for how much is a cnc machine
Key Technical Properties for CNC Machines
Understanding the technical specifications of CNC machines is crucial for B2B buyers looking to make informed purchasing decisions. Here are some essential properties to consider:
-
Material Compatibility: This refers to the types of materials a CNC machine can process, such as metals, plastics, wood, and composites. B2B buyers must assess whether the machine can handle the specific materials relevant to their industry. Selecting a machine that supports the right materials can significantly enhance production efficiency and reduce waste.
-
Tolerance: Tolerance indicates the permissible limit of variation in a physical dimension. In CNC machining, tighter tolerances mean more precision in manufacturing parts. For industries such as aerospace or automotive, where safety and functionality depend on exact specifications, understanding tolerance levels is essential for ensuring product quality.
-
Axis Configuration: The number of axes a CNC machine operates on (e.g., 3-axis, 4-axis, 5-axis) determines its complexity and capability. More axes allow for intricate designs and more complex machining processes. Buyers should evaluate their specific machining needs and decide whether a simpler machine suffices or if a multi-axis machine is necessary for their operations.
-
Cutting Speed and Feed Rate: These parameters dictate how quickly a machine can cut through materials and how fast the material is fed into the cutting tool. Higher speeds can lead to increased productivity, but they may also affect the quality of the finished product. Understanding these specs helps buyers balance efficiency with quality.
-
Power Consumption: This refers to the energy required to operate the CNC machine. Machines with higher power ratings can handle tougher materials and larger workloads but may incur higher operational costs. Buyers should consider their budget for electricity and how it fits into overall operational expenses.
Common Trade Terminology
Familiarity with industry jargon is vital for effective communication and negotiation in the CNC machinery market. Here are some key terms that every B2B buyer should know:
-
OEM (Original Equipment Manufacturer): An OEM produces parts or equipment that may be marketed by another manufacturer. Buyers should understand whether they are purchasing directly from an OEM or a third-party distributor, as this can affect pricing, warranties, and after-sales support.
-
MOQ (Minimum Order Quantity): This term refers to the smallest number of units that a supplier is willing to sell. Understanding MOQ is crucial for budgeting, especially for smaller businesses or those testing new products. Negotiating MOQs can lead to better pricing and inventory management.
-
RFQ (Request for Quotation): An RFQ is a document sent to suppliers to request pricing for specific products or services. For B2B buyers, preparing a detailed RFQ can facilitate better comparisons across suppliers, helping them secure favorable terms and pricing.
-
Incoterms: These are international commercial terms that define the responsibilities of buyers and sellers in international transactions. Familiarity with Incoterms helps buyers understand shipping costs, insurance, and liability, ensuring that they factor these into their overall cost calculations.
-
Lead Time: This refers to the amount of time between placing an order and receiving the machine. Understanding lead times is crucial for planning production schedules and meeting customer demands. Buyers should factor lead times into their decision-making process, especially when sourcing from international suppliers.
By grasping these technical properties and trade terms, B2B buyers can navigate the complexities of CNC machine procurement more effectively, ensuring that their investments align with their operational needs and market conditions.
Navigating Market Dynamics, Sourcing Trends, and Sustainability in the how much is a cnc machine Sector
Market Overview & Key Trends
The CNC machine market is experiencing significant growth, driven by increasing demand for precision manufacturing across various industries, including automotive, aerospace, and electronics. For international B2B buyers in regions such as Africa, South America, the Middle East, and Europe, understanding the market dynamics is crucial. Key trends include the rise of automation, where advanced CNC machines are integrated with IoT technology for enhanced operational efficiency. This trend facilitates real-time monitoring and predictive maintenance, reducing downtime and operational costs.
Moreover, the shift towards custom and low-volume production is prompting buyers to invest in flexible CNC solutions that can adapt to diverse manufacturing needs. For instance, buyers in countries like Argentina and Kenya are leveraging CNC routers for woodworking and signage, while those in Mexico and the UAE focus on precision CNC milling for automotive components. Additionally, the growing emphasis on digital twins and simulation technology allows businesses to optimize their CNC machining processes before physical implementation, thus minimizing errors and waste.
International procurement is also influenced by geopolitical factors, trade agreements, and regional regulations, necessitating thorough market research to navigate import duties and compliance requirements effectively. Understanding these dynamics will empower B2B buyers to make informed decisions that align with their operational goals and budget constraints.
Sustainability & Ethical Sourcing in B2B
As sustainability becomes increasingly integral to business strategies, B2B buyers in the CNC machine sector must prioritize environmentally responsible sourcing practices. The environmental impact of CNC machining can be significant, from energy consumption to waste generation. Therefore, selecting machines that utilize energy-efficient technologies and materials is essential.
Buyers should look for suppliers that offer green certifications and adhere to ethical sourcing standards. Certifications such as ISO 14001 indicate a commitment to effective environmental management systems, while sourcing materials from sustainable suppliers minimizes the ecological footprint. Additionally, opting for machines that reduce waste through advanced cutting technologies can further enhance sustainability efforts.
Ethical supply chains are paramount as consumers and businesses alike demand transparency and accountability. By ensuring that CNC machines are produced under fair labor practices and with minimal environmental impact, buyers not only contribute to global sustainability efforts but also enhance their brand reputation. Investing in sustainable machinery can lead to long-term cost savings and greater operational resilience, making it a wise choice for forward-thinking businesses.
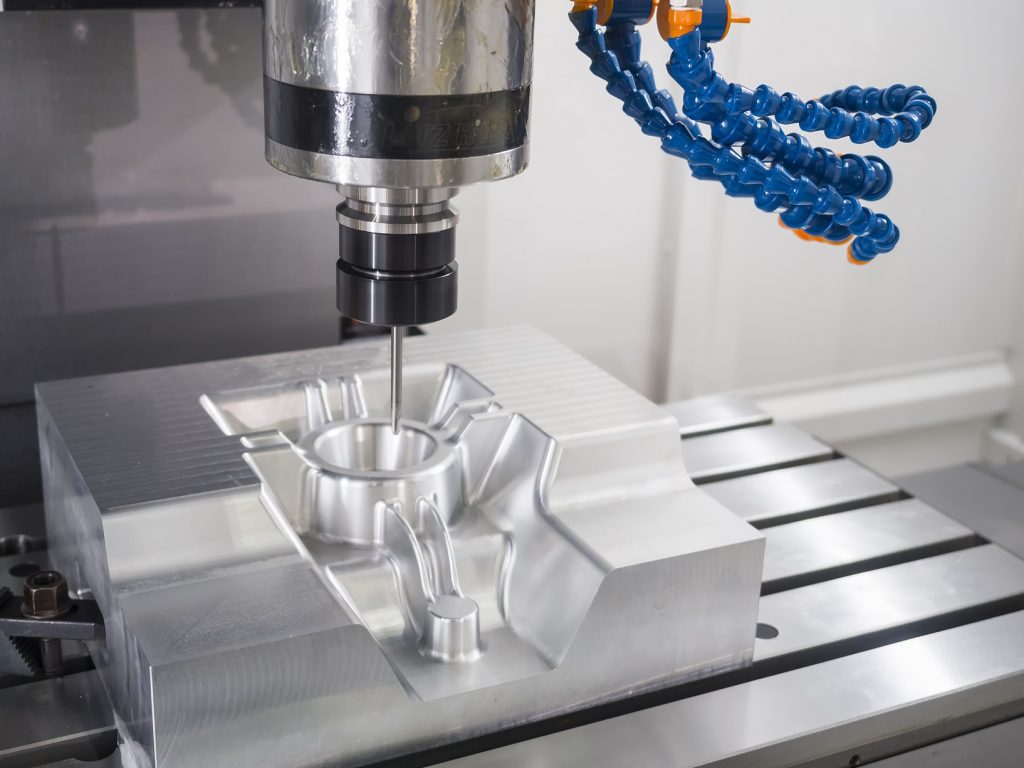
Illustrative Image (Source: Google Search)
Brief Evolution/History
The evolution of CNC technology dates back to the 1950s when numerical control (NC) was first introduced, revolutionizing manufacturing by allowing machines to be programmed for precise operations. With the advent of computers in the 1970s, CNC technology emerged, enabling even more sophisticated machining processes. Over the decades, advancements in software, automation, and materials have transformed CNC machines into essential tools for modern manufacturing.
Today, CNC machines come in various types and configurations, catering to diverse industries and applications. The historical progression from manual machining to fully automated CNC systems underscores the importance of these machines in enhancing productivity, precision, and flexibility in manufacturing. For B2B buyers, understanding this evolution is crucial for recognizing the capabilities and potential ROI of investing in CNC technology.
Related Video: Incoterms for beginners | Global Trade Explained
Frequently Asked Questions (FAQs) for B2B Buyers of how much is a cnc machine
-
What factors should I consider when vetting CNC machine suppliers?
When vetting CNC machine suppliers, prioritize their reputation, experience, and customer reviews. Check for certifications such as ISO 9001, which indicates a commitment to quality management. Additionally, assess their production capabilities and whether they specialize in the machine type you need. Request references from previous clients to gauge reliability and service quality. Understanding their after-sales support, including maintenance and training, is crucial for long-term success, especially in regions where technical support may be limited. -
Can I customize a CNC machine to fit my specific needs?
Yes, many manufacturers offer customization options for CNC machines to meet specific operational requirements. This may include modifications in size, capabilities, and additional features such as automated tool changers or advanced software integration. However, customization can impact lead times and costs. Clearly communicate your specifications to suppliers and inquire about their experience with similar custom projects. This ensures that the final product aligns with your production goals and minimizes potential compatibility issues. -
What are the typical minimum order quantities (MOQs) and lead times for CNC machines?
Minimum order quantities for CNC machines can vary significantly based on the supplier and machine type. Generally, for standard machines, MOQs may range from one to several units. Lead times can also fluctuate, often between 6 to 12 weeks, depending on the complexity of the machine and the supplier’s production capacity. It’s advisable to discuss your timeline requirements upfront and explore expedited options if your project is time-sensitive. Be aware that custom machines typically require longer lead times due to the design and manufacturing process. -
What payment options are available when purchasing a CNC machine internationally?
Payment options for international CNC machine purchases commonly include wire transfers, letters of credit, and escrow services. Wire transfers are straightforward but require trust in the supplier. Letters of credit offer more security, as they ensure that payment is only released upon meeting specified conditions. Escrow services provide a neutral ground where funds are held until both parties fulfill their obligations. Discuss payment terms with your supplier and consider negotiating favorable conditions, especially for larger investments. -
How can I ensure quality assurance and certifications for my CNC machine?
To ensure quality assurance, request copies of relevant certifications, such as CE marking for compliance with European safety standards or ISO certifications that indicate adherence to quality management systems. Ask suppliers about their quality control processes, including testing and inspection protocols. It’s also beneficial to inquire about warranties and service agreements, which can provide additional assurance of the machine’s reliability and performance. Conducting a factory visit, if feasible, can further validate the supplier’s commitment to quality. -
What logistics considerations should I keep in mind when importing a CNC machine?
When importing a CNC machine, consider shipping costs, customs duties, and the logistics of transporting large machinery. Work with freight forwarders experienced in handling industrial equipment to navigate complex international regulations. Ensure that the supplier provides all necessary documentation for customs clearance, including invoices, packing lists, and certificates of origin. Additionally, factor in local logistics, such as transportation to your facility and installation requirements, to avoid unexpected delays and costs. -
How should I handle disputes with my CNC machine supplier?
To handle disputes effectively, first, maintain clear and open communication with your supplier. Document all agreements, correspondence, and any issues that arise. If a problem occurs, attempt to resolve it amicably through discussion. If that fails, refer to the terms of your contract, which should outline dispute resolution procedures, such as mediation or arbitration. Engaging legal counsel familiar with international trade laws can also be beneficial in navigating complex disputes and protecting your interests. -
What are the ongoing operational costs associated with CNC machines?
Ongoing operational costs for CNC machines include maintenance, tooling, software updates, and training. Regular maintenance is essential to prevent breakdowns and prolong machine life, while tooling costs can add up quickly as cutting tools wear out or need replacement. Additionally, software licenses for operating the CNC machine may incur annual fees, and staff training is crucial for safe and efficient operation. Budgeting for these costs is vital for ensuring that your CNC investment remains productive and cost-effective over time.
Important Disclaimer & Terms of Use
⚠️ Important Disclaimer
The information provided in this guide, including content regarding manufacturers, technical specifications, and market analysis, is for informational and educational purposes only. It does not constitute professional procurement advice, financial advice, or legal advice.
While we have made every effort to ensure the accuracy and timeliness of the information, we are not responsible for any errors, omissions, or outdated information. Market conditions, company details, and technical standards are subject to change.
B2B buyers must conduct their own independent and thorough due diligence before making any purchasing decisions. This includes contacting suppliers directly, verifying certifications, requesting samples, and seeking professional consultation. The risk of relying on any information in this guide is borne solely by the reader.
Strategic Sourcing Conclusion and Outlook for how much is a cnc machine
Navigating the complexities of CNC machine pricing and sourcing is critical for international B2B buyers aiming to enhance their operational capabilities. Key takeaways from this guide emphasize the importance of understanding the diverse types of CNC machines, the factors influencing their costs, and the implications of strategic sourcing decisions.
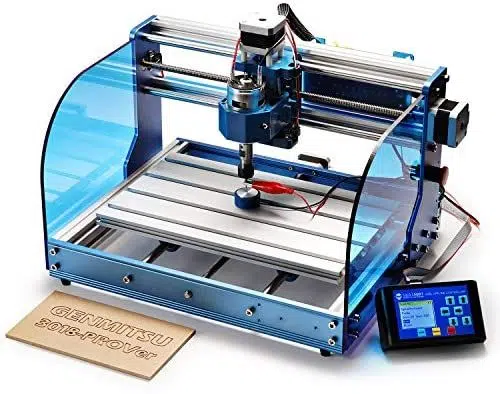
Illustrative Image (Source: Google Search)
Investing wisely in CNC technology can significantly impact your production efficiency, allowing for faster turnarounds and reduced waste. Whether considering entry-level machines or high-end industrial-grade systems, aligning your choice with your specific operational needs is essential. Furthermore, comprehensive evaluations of suppliers, including their service capabilities and reputation, can mitigate risks associated with international procurement.
As the demand for precision manufacturing continues to rise globally, particularly in regions like Africa, South America, the Middle East, and Europe, now is the time to invest in CNC machinery that aligns with your long-term business goals. Embrace strategic sourcing as a pathway to not only enhance productivity but also to gain a competitive edge in your market. Take the next step by assessing your current capabilities and exploring how CNC machines can transform your operations for the future.