Avoid Common Mistakes: USA Electrical Socket Guide (2025)
Introduction: Navigating the Global Market for usa electrical socket
Navigating the complexities of sourcing electrical sockets for the USA market can be a significant challenge for international B2B buyers, especially those from regions like Africa, South America, the Middle East, and Europe. Understanding the specific requirements for the USA electrical socket—including plug types, voltage specifications, and safety standards—is crucial for ensuring compatibility and safety when integrating electrical products into your operations. This guide offers a comprehensive overview of the types of sockets available, including the common types A and B, as well as the applications of each type in various industries.
International buyers will benefit from detailed insights into the process of vetting suppliers, assessing costs, and understanding regulatory compliance when purchasing electrical sockets for the USA. The guide is designed to empower businesses by providing actionable information that helps mitigate risks associated with electrical compatibility issues. It will also address common questions related to voltage converters and transformers, ensuring that you are well-equipped to make informed purchasing decisions.
By leveraging the knowledge presented in this guide, B2B buyers can streamline their sourcing strategies, enhance operational efficiency, and ultimately achieve greater success in the competitive landscape of international trade. Whether you are a distributor, manufacturer, or retailer, understanding the intricacies of USA electrical sockets will be pivotal in expanding your market reach and ensuring customer satisfaction.
Understanding usa electrical socket Types and Variations
Type Name | Key Distinguishing Features | Primary B2B Applications | Brief Pros & Cons for Buyers |
---|---|---|---|
Type A | Two flat parallel pins | Appliances without grounding requirements | Pros: Widely used, easy to find adapters. Cons: No grounding, may not support high-power devices. |
Type B | Two flat parallel pins and a grounding pin | Industrial equipment, higher power appliances | Pros: Grounded for safety, suitable for heavier loads. Cons: Requires specific adapters for non-grounded devices. |
Type C | Two round pins | Lesser common in the USA, but used in some devices | Pros: Common in Europe, can be used with adapters. Cons: Not standard in the USA, limited availability. |
Type D | Three round pins | Specialized equipment, certain older devices | Pros: Stable connection for specific applications. Cons: Rare in the USA, requires specific adapters. |
Universal | Multiple socket types | International business, travel adapters | Pros: Versatile, can accommodate various plug types. Cons: Bulkier than single-type adapters, may not support high wattage. |
What are the characteristics of Type A sockets?
Type A sockets feature two flat parallel pins and are commonly found in North America and parts of Asia. They are primarily used for devices that do not require a ground connection, making them suitable for low-power appliances. For B2B buyers, the convenience of finding travel adapters for Type A plugs is a significant advantage. However, it is essential to note that Type A sockets do not provide grounding, which can be a safety concern when using high-power equipment.
How do Type B sockets differ from Type A?
Type B sockets are an advancement over Type A, incorporating a third grounding pin alongside the two flat parallel pins. This grounding feature makes Type B sockets ideal for industrial and commercial applications, where safety is paramount. B2B buyers should consider the electrical requirements of their equipment when selecting Type B sockets, as they can safely accommodate higher power loads. While adapters for Type B are available, it is crucial to ensure that devices are compatible to avoid damage or safety hazards.
Are Type C sockets relevant for B2B buyers in the USA?
Type C sockets, characterized by their two round pins, are not standard in the USA but are prevalent in Europe and other regions. They can be used in the U.S. with the appropriate adapters, making them relevant for B2B buyers importing European equipment. However, the limited availability of Type C sockets in the U.S. means that businesses should evaluate the compatibility of their devices to avoid operational disruptions.
What is the application of Type D sockets in the USA?
Type D sockets feature three round pins and are typically used for specific older devices and specialized equipment. While they are rare in the U.S., B2B buyers dealing with legacy systems or certain industrial applications may encounter Type D plugs. It is vital to have the correct adapters on hand, as the lack of standardization can lead to compatibility issues. Businesses should assess their equipment needs and potential voltage differences when considering Type D devices.
How do universal adapters benefit international B2B buyers?
Universal adapters accommodate multiple socket types, including Types A, B, C, and D. These adapters are particularly beneficial for international B2B buyers who frequently travel or import equipment from various regions. While they offer versatility, buyers should be cautious about their wattage limits, as some universal adapters may not support high-power devices. Selecting a high-quality universal adapter can ensure seamless operations across different electrical systems, making them an essential tool for global business operations.
Key Industrial Applications of usa electrical socket
Industry/Sector | Specific Application of usa electrical socket | Value/Benefit for the Business | Key Sourcing Considerations for this Application |
---|---|---|---|
Hospitality | Powering guest room appliances | Enhances guest experience by providing accessible power outlets | Ensure compatibility with Type A and B sockets; consider voltage ratings. |
Manufacturing | Machinery and equipment operation | Reliable power supply for continuous operations | Assess wattage requirements; consider voltage converters for non-dual voltage equipment. |
Information Technology | Charging stations for devices | Supports employee productivity with readily available charging options | Look for dual voltage compatibility; ensure safety certifications. |
Retail | Point of Sale (POS) systems | Streamlines transactions and improves customer service | Evaluate power needs of POS systems; ensure reliable access to outlets. |
Education | Classroom technology integration | Facilitates the use of educational tools and devices | Confirm socket compatibility with various devices; assess power load capacity. |
How is the USA Electrical Socket Used in the Hospitality Industry?
In the hospitality sector, USA electrical sockets are crucial for powering guest room appliances such as lamps, televisions, and charging stations. Hotels and resorts benefit from providing easily accessible outlets, enhancing the guest experience and encouraging longer stays. International buyers from regions like Africa and South America should ensure their electrical appliances are compatible with Type A and B sockets, and consider the voltage requirements to avoid damage to devices.
What Role Does the USA Electrical Socket Play in Manufacturing?
Manufacturing facilities utilize USA electrical sockets to operate machinery and equipment efficiently. A reliable power supply is essential for continuous production processes. For international B2B buyers, it’s critical to assess the wattage and voltage requirements of the equipment being used. In cases where machinery is not dual voltage rated, sourcing voltage converters or transformers may be necessary to ensure safe operations without interruptions.
How is the USA Electrical Socket Integrated into Information Technology?
In the IT sector, USA electrical sockets are vital for powering charging stations for laptops, tablets, and other electronic devices. This setup supports employee productivity by ensuring that devices are always charged and ready for use. Buyers must look for dual voltage compatibility in their devices to avoid the need for converters, and ensure that all electrical installations meet safety standards to prevent any electrical hazards.
What is the Importance of USA Electrical Sockets in Retail Environments?
In retail, USA electrical sockets power Point of Sale (POS) systems that facilitate transactions and enhance customer service. Reliable access to power helps reduce wait times and improves operational efficiency. When sourcing equipment for retail environments, businesses must evaluate the power needs of their POS systems and ensure that electrical installations are compliant with local standards to avoid any disruptions during peak hours.
How Do Educational Institutions Utilize USA Electrical Sockets?
Educational institutions leverage USA electrical sockets to integrate technology into classrooms, powering devices such as projectors, computers, and interactive whiteboards. This integration enhances learning experiences and promotes the use of modern educational tools. Buyers in the education sector should confirm the compatibility of their devices with USA socket types and assess the power load capacity of electrical installations to support multiple devices simultaneously.
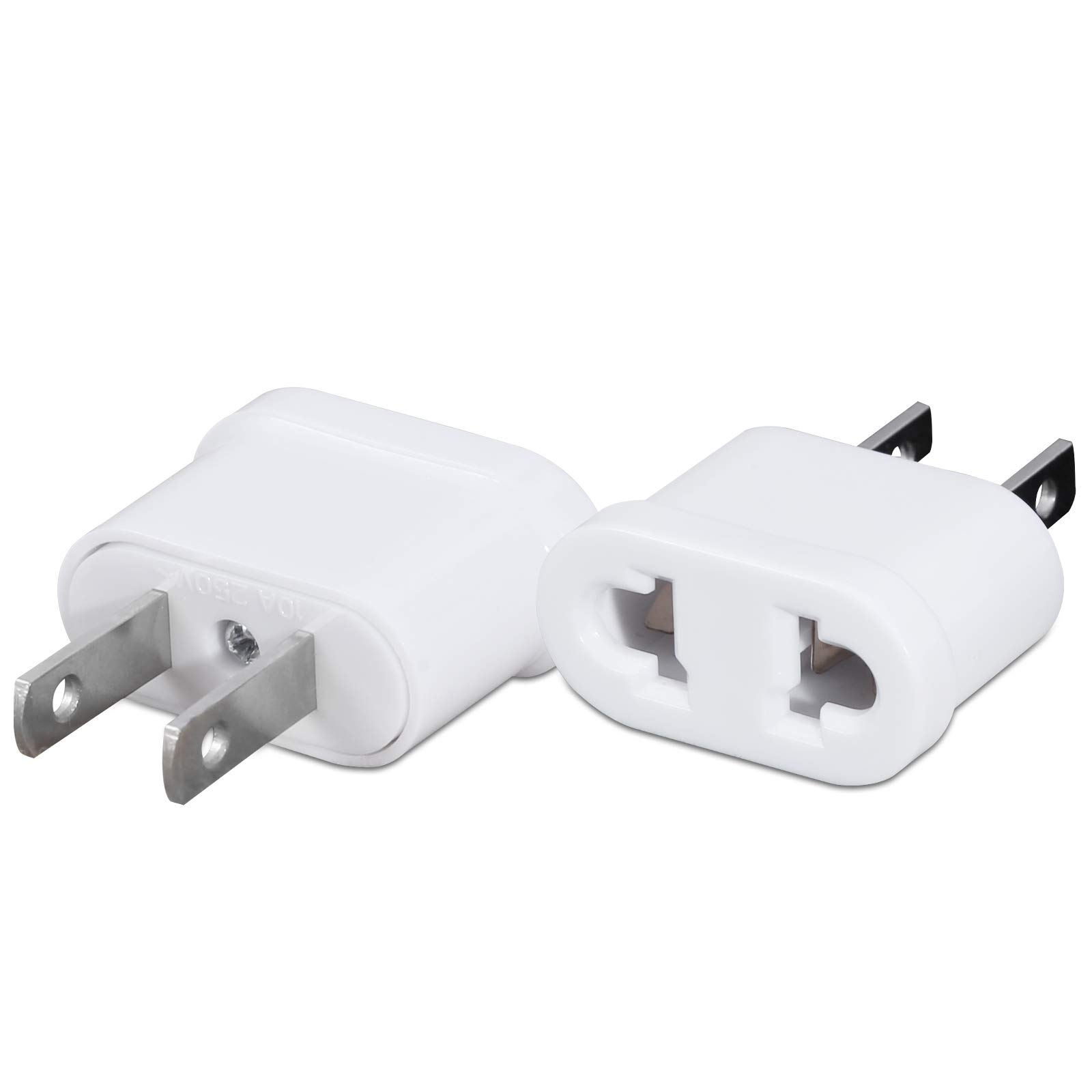
A stock image related to usa electrical socket.
3 Common User Pain Points for ‘usa electrical socket’ & Their Solutions
Scenario 1: Compatibility Issues with Electrical Appliances
The Problem:
International B2B buyers often face challenges when sourcing electrical appliances that are compatible with the USA’s socket types (A and B). Many appliances designed for markets in Africa, South America, and Europe operate on different voltages (typically 220-240V) and may not fit into the USA’s 120V system. This situation can lead to significant operational delays and increased costs, as buyers must either replace their equipment or invest in additional voltage converters or adapters.
The Solution:
To overcome compatibility issues, B2B buyers should prioritize sourcing dual-voltage appliances that specify an input range of 100-240V and support both 50Hz and 60Hz frequencies. This feature allows appliances to operate seamlessly in the USA without the need for a voltage converter. When purchasing, verify the specifications listed on the appliance rating plate or manufacturer’s documentation. Additionally, consider investing in universal travel adapters that can accommodate both type A and B plugs to ensure flexibility in various settings. Establishing relationships with suppliers that understand these requirements can streamline the procurement process and minimize operational disruptions.
Scenario 2: Risk of Electrical Damage from Voltage Differences
The Problem:
Another significant pain point for B2B buyers is the risk of electrical damage to sensitive equipment due to voltage differences. Devices not rated for use at 120V can suffer irreversible damage if plugged directly into a USA socket. This is particularly concerning for businesses in sectors like telecommunications, medical equipment, and high-tech manufacturing, where equipment reliability is paramount.
The Solution:
To mitigate the risk of electrical damage, buyers should conduct thorough assessments of their electrical equipment before travel or importation. This includes checking if the devices are single or dual voltage rated. For devices that require a voltage transformer, select a high-quality transformer that matches the power rating of the equipment. Many suppliers provide transformers with built-in surge protection and overload features, offering additional safety. Engaging with electrical engineers or consultants can also provide insights into the best practices for using sensitive equipment in the USA, ensuring compliance with local electrical standards.
Scenario 3: Navigating Regulatory Compliance for Electrical Equipment
The Problem:
International buyers often struggle with understanding and complying with the regulatory standards for electrical equipment in the USA. The U.S. has specific regulations regarding safety, performance, and energy efficiency that must be met to avoid legal issues or fines. This can be particularly daunting for businesses from regions with less stringent standards, such as some parts of Africa and South America.
The Solution:
To navigate regulatory compliance, B2B buyers should familiarize themselves with the standards set by organizations like Underwriters Laboratories (UL) and the National Electrical Manufacturers Association (NEMA). It is advisable to work with suppliers that provide products already compliant with U.S. regulations. Buyers can also utilize resources like the U.S. Department of Energy’s guidelines for energy efficiency standards. Collaborating with local legal or compliance experts can help ensure that all products meet necessary safety certifications, thus reducing the risk of costly penalties and ensuring smooth market entry. Additionally, leveraging local distributors who understand the regulatory landscape can facilitate compliance and improve supply chain efficiency.
Strategic Material Selection Guide for usa electrical socket
When selecting materials for USA electrical sockets, understanding the properties, advantages, and limitations of common materials is essential for international B2B buyers. This guide analyzes four prevalent materials used in the manufacturing of electrical sockets, providing insights that can aid buyers from Africa, South America, the Middle East, and Europe.
What are the Key Properties of Thermoplastic Materials in Electrical Sockets?
Thermoplastic materials, such as polycarbonate or nylon, are widely used in electrical socket manufacturing due to their excellent insulating properties and mechanical strength. They typically have a high-temperature rating, often exceeding 100°C, and are resistant to impact and chemicals. This makes them suitable for various environments, including residential and commercial applications.
Pros & Cons:
– Advantages: Thermoplastics are lightweight, cost-effective, and easy to mold into complex shapes, which simplifies manufacturing processes. They also offer good electrical insulation and are resistant to UV light, making them suitable for outdoor applications.
– Disadvantages: While thermoplastics are durable, they may not withstand extreme temperatures as well as some other materials, which could limit their use in high-heat environments.
Impact on Application: Thermoplastics are compatible with most electrical media, making them versatile for different socket designs. However, buyers should ensure that the specific thermoplastic used complies with relevant safety standards, such as UL or IEC.
How Do Metal Components Enhance the Performance of Electrical Sockets?
Metal components, particularly copper and brass, are essential for electrical conductivity in sockets. Copper is known for its excellent electrical properties, while brass offers good corrosion resistance and strength.
Pros & Cons:
– Advantages: Metals like copper and brass provide superior conductivity and durability, ensuring long-lasting performance. They can handle higher current loads, making them ideal for heavy-duty applications.
– Disadvantages: Metals can be more expensive than plastics and may require additional coatings to prevent corrosion, particularly in humid or coastal environments.
Impact on Application: The choice of metal affects the socket’s ability to handle specific electrical loads and environmental conditions. Buyers should consider local climate conditions and ensure compliance with international standards, such as ASTM or DIN, to avoid failures.
What Role Do Composite Materials Play in Electrical Socket Manufacturing?
Composite materials, which combine thermoplastics with reinforcing fibers, offer enhanced mechanical properties and thermal stability. These materials are increasingly used in high-performance electrical sockets.
Pros & Cons:
– Advantages: Composites provide excellent strength-to-weight ratios and can withstand higher temperatures compared to standard thermoplastics. They are also resistant to chemicals and environmental degradation.
– Disadvantages: The manufacturing process for composites can be more complex and costly, which may increase the final product price.
Impact on Application: Composites are suitable for specialized applications where high strength and temperature resistance are required. International buyers should verify that these materials meet local compliance standards and are suitable for their specific applications.
Why Are Ceramics Considered in Electrical Socket Design?
Ceramics are utilized in electrical sockets primarily for their excellent insulating properties and high-temperature resistance. They are often used in applications requiring high durability and resistance to environmental factors.
Pros & Cons:
– Advantages: Ceramics are highly resistant to heat, chemicals, and wear, making them ideal for high-stress environments. They also provide excellent electrical insulation.
– Disadvantages: The brittleness of ceramics can lead to breakage during installation or use. Additionally, they are typically more expensive than other materials.
Impact on Application: Ceramics are particularly suited for high-voltage applications or environments with extreme conditions. Buyers must ensure that ceramic components comply with relevant safety standards and are appropriate for their intended use.
Summary Table of Material Selection for USA Electrical Sockets
Material | Typical Use Case for usa electrical socket | Key Advantage | Key Disadvantage/Limitation | Relative Cost (Low/Med/High) |
---|---|---|---|---|
Thermoplastic | General residential and commercial sockets | Lightweight and cost-effective | Limited high-temperature resistance | Low |
Metal | Heavy-duty applications | Superior conductivity and durability | Higher cost and potential corrosion | Medium |
Composite | High-performance sockets | Enhanced strength and thermal stability | Complex manufacturing process | High |
Ceramic | High-voltage and extreme environment sockets | Excellent insulation and heat resistance | Brittle and expensive | High |
This strategic material selection guide provides valuable insights for international B2B buyers, helping them make informed decisions when sourcing USA electrical sockets. Understanding the properties and applications of each material ensures compliance with local standards and suitability for specific needs.
In-depth Look: Manufacturing Processes and Quality Assurance for usa electrical socket
What Are the Main Stages in the Manufacturing Process of USA Electrical Sockets?
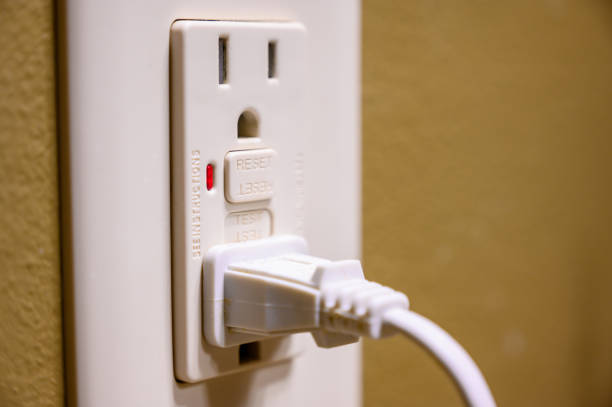
A stock image related to usa electrical socket.
The manufacturing of USA electrical sockets involves several critical stages, each designed to ensure the final product meets safety and performance standards. These stages typically include material preparation, forming, assembly, and finishing.
-
Material Preparation: The process begins with sourcing high-quality materials, primarily thermoplastics for the socket housing and copper for the electrical contacts. Manufacturers must ensure that the materials comply with relevant safety and durability standards. For B2B buyers, it is crucial to verify the specifications of materials used, as inferior materials can lead to product failure.
-
Forming: In this stage, the prepared materials are molded into the desired shapes. Injection molding is a common technique for creating the socket’s plastic housing, while stamping processes are often used for metal components. Advanced manufacturers may utilize CNC (Computer Numerical Control) machining for precision parts, which can enhance product consistency and quality.
-
Assembly: After forming, the components are assembled. This may involve inserting the metal contacts into the plastic housing and securing them with screws or other fasteners. Automated assembly lines are increasingly used to improve efficiency and reduce human error, which can be critical for maintaining quality in high-volume production.
-
Finishing: The final stage includes surface treatment, which may involve applying coatings to enhance durability and resistance to environmental factors. Quality checks during this stage ensure that all components fit properly and that the final product is visually appealing and functional.
How Does Quality Control (QC) Ensure the Safety and Reliability of USA Electrical Sockets?
Quality control is a vital component of the manufacturing process for USA electrical sockets. It ensures that the products meet international and industry-specific standards, which is particularly important for B2B buyers from regions such as Africa, South America, the Middle East, and Europe.
-
Relevant International Standards: Manufacturers often adhere to ISO 9001, which focuses on quality management systems, ensuring that products are consistently produced and controlled according to quality standards. Additionally, compliance with CE marking requirements is essential for products sold in Europe, signifying conformity with health, safety, and environmental protection standards.
-
Industry-Specific Standards: In the USA, electrical sockets must comply with standards set by organizations like Underwriters Laboratories (UL) and the American National Standards Institute (ANSI). These certifications indicate that the sockets have been tested for safety and performance.
-
QC Checkpoints: The QC process typically includes several checkpoints:
– Incoming Quality Control (IQC): This involves inspecting raw materials and components upon arrival to ensure they meet specified standards.
– In-Process Quality Control (IPQC): Continuous monitoring during the manufacturing process helps identify and rectify defects in real-time.
– Final Quality Control (FQC): The finished products undergo rigorous testing, including electrical performance tests and safety assessments, to ensure they meet all regulatory requirements.
What Common Testing Methods Are Used in the Quality Assurance of Electrical Sockets?
Testing methods play a crucial role in the quality assurance of electrical sockets. Common techniques include:
- Dielectric Strength Testing: This test evaluates the insulation of the socket to prevent electrical breakdown.
- Temperature Rise Testing: This method checks how much the socket heats up under load, which is critical for preventing overheating and potential fire hazards.
- Mechanical Durability Testing: Ensures that the physical structure can withstand repeated use and stress.
- Electrical Load Testing: Assesses how the socket performs under specified electrical loads, ensuring it can handle the typical usage scenarios.
How Can B2B Buyers Verify Supplier Quality Control Measures?
For international B2B buyers, particularly from regions like Africa, South America, and the Middle East, verifying the quality control measures of suppliers is essential to mitigate risks associated with product safety and compliance. Here are several actionable steps:
-
Conduct Supplier Audits: Regular audits help assess the supplier’s manufacturing processes and QC practices. This can include reviewing their documentation, quality management systems, and testing protocols.
-
Request Quality Reports: Suppliers should provide documentation demonstrating compliance with relevant standards (ISO, CE, UL). These reports can include test results, certification details, and records of any quality issues encountered and resolved.
-
Engage Third-Party Inspection Services: Utilizing third-party inspection agencies can provide an unbiased assessment of the manufacturer’s quality control measures. These agencies often conduct random inspections and testing of products before shipment, ensuring adherence to quality standards.
-
Review Customer Feedback and References: Engaging with other businesses that have sourced products from the supplier can provide insights into their reliability and quality performance.
What Are the Quality Control and Certification Nuances for International Buyers?
International buyers must navigate several nuances regarding quality control and certification when sourcing USA electrical sockets:
-
Understanding Regional Regulations: Different regions may have specific requirements regarding electrical safety and performance. For instance, sockets intended for the European market must meet CE standards, while those for the Middle East might require compliance with local electrical codes.
-
Language Barriers and Documentation: Ensure that all quality and compliance documentation is available in a language that can be understood by the purchasing team. This includes certificates, test reports, and user manuals.
-
Cultural Sensitivity in Communication: Recognize that business practices may vary by region. Building strong relationships with suppliers can facilitate smoother communication and negotiation regarding quality expectations.
-
Compliance with Import Regulations: Familiarize yourself with the import regulations in your country to avoid issues during customs clearance. This can include ensuring that all necessary certifications are in place before shipment.
By understanding these manufacturing processes and quality assurance practices, international B2B buyers can make informed decisions when sourcing USA electrical sockets, ensuring they choose suppliers that prioritize safety, reliability, and compliance.
Practical Sourcing Guide: A Step-by-Step Checklist for ‘usa electrical socket’
To effectively source USA electrical sockets, international B2B buyers must navigate technical requirements, supplier evaluations, and compliance standards. This guide provides a step-by-step checklist to streamline the procurement process, ensuring that you make informed decisions that align with your operational needs.
Step 1: Define Your Technical Specifications
Before initiating the sourcing process, clarify the technical requirements for the electrical sockets you need. This includes identifying the specific plug types (A and B) used in the USA, as well as the voltage and frequency specifications (120V, 60Hz). Knowing these details will help you avoid compatibility issues and ensure that the sockets meet your operational standards.
Step 2: Research Local Regulations and Standards
Understanding the regulations governing electrical installations in your target market is crucial. Each country may have different safety standards and certifications, such as UL or CE marks. Ensure that the products you procure comply with these regulations to avoid legal complications and ensure safety in usage.
Step 3: Evaluate Potential Suppliers
Conduct thorough evaluations of potential suppliers to ensure reliability and quality. Request documentation such as company profiles, case studies, and references from buyers within your industry. Pay close attention to their experience in supplying electrical components and their adherence to international quality standards.
- Considerations:
- Look for suppliers with a proven track record in your region, particularly in Africa, South America, the Middle East, or Europe.
- Investigate their production capabilities and whether they can scale to meet your demands.
Step 4: Request Samples for Testing
Before finalizing a bulk order, always request samples of the sockets. Testing these samples will allow you to verify their quality, durability, and compatibility with your existing systems. This step is essential to mitigate risks associated with bulk purchases.
- Testing Focus Areas:
- Ensure the plugs fit securely into the sockets.
- Verify that the sockets can handle the specified voltage and current without overheating.
Step 5: Verify Supplier Certifications
Confirm that your chosen suppliers possess the necessary certifications for their products. Certifications like ISO 9001 or relevant safety marks signify that the manufacturer adheres to international quality management standards. This verification is essential for establishing trust and ensuring product reliability.
Step 6: Negotiate Terms and Conditions
Once you have identified a suitable supplier, negotiate the terms of your purchase. Discuss pricing, payment terms, delivery schedules, and warranty provisions. Clear agreements will help prevent misunderstandings and ensure a smooth transaction process.
- Key Negotiation Points:
- Ensure clarity on lead times for delivery.
- Discuss options for after-sales support and handling of defective products.
Step 7: Plan for Logistics and Distribution
Finally, develop a logistics plan for transporting the sockets from the supplier to your location. Consider factors such as shipping methods, customs clearance, and local distribution channels. A well-structured logistics plan ensures that your products arrive on time and in good condition.
By following this checklist, international B2B buyers can confidently navigate the complexities of sourcing USA electrical sockets, ensuring both compliance and operational efficiency.
Comprehensive Cost and Pricing Analysis for usa electrical socket Sourcing
What Are the Key Cost Components in Sourcing USA Electrical Sockets?
When considering the sourcing of electrical sockets from the USA, it’s crucial to understand the various cost components involved. These include:
-
Materials: The primary materials used in electrical socket manufacturing typically include high-quality plastics, metals for contacts, and insulation materials. The cost of these materials can fluctuate based on market demand, availability, and supplier relationships.
-
Labor: Labor costs vary significantly depending on the region of manufacturing. In the USA, wages are generally higher than in many other countries, which can impact the overall cost of the product. However, investing in skilled labor can enhance the quality of the final product.
-
Manufacturing Overhead: This encompasses costs related to utilities, rent, and equipment maintenance. Overhead can vary by location, with urban areas often incurring higher costs.
-
Tooling: Initial tooling costs can be substantial, especially for custom designs or high-precision applications. Buyers should factor in these costs when calculating the total investment required for sourcing.
-
Quality Control (QC): Ensuring that products meet safety and regulatory standards is critical, particularly for electrical components. QC processes can add to the overall cost but are essential for maintaining reliability and compliance.
-
Logistics: Transportation and shipping costs can vary widely based on the shipping method, destination, and volume. Import duties and tariffs should also be considered, especially for international buyers.
-
Margin: Suppliers typically include a profit margin in their pricing. This margin can vary based on competition, market demand, and the supplier’s positioning.
How Do Price Influencers Impact USA Electrical Socket Sourcing?
Several factors can influence the pricing of USA electrical sockets:
-
Volume/MOQ: The minimum order quantity (MOQ) plays a significant role in pricing. Larger orders usually result in lower per-unit costs due to economies of scale. Buyers should negotiate MOQs to optimize their costs.
-
Specifications and Customization: Custom features or specific certifications can increase the price. Buyers should clearly define their requirements to avoid unnecessary costs.
-
Materials and Quality Certifications: Higher-quality materials or certifications (like UL or CE) can increase costs but are often necessary for safety and compliance, especially in regions with stringent regulations.
-
Supplier Factors: The supplier’s reputation, experience, and production capacity can influence pricing. Established suppliers may charge more due to their reliability and quality assurance.
-
Incoterms: Understanding the Incoterms (International Commercial Terms) is crucial as they define the responsibilities of buyers and sellers in shipping. Choosing the right Incoterm can help manage logistics costs effectively.
What Are the Best Buyer Tips for Cost-Efficient Sourcing of USA Electrical Sockets?
International buyers, particularly from Africa, South America, the Middle East, and Europe, can leverage several strategies for cost-efficient sourcing:
-
Negotiation: Engage in open discussions with suppliers about pricing, MOQs, and customization options. Building a good relationship can lead to better terms and pricing.
-
Consider Total Cost of Ownership (TCO): Evaluate not just the purchase price but also the long-term costs associated with maintenance, energy efficiency, and potential failure rates. A slightly higher upfront cost can lead to significant savings over time.
-
Explore Multiple Suppliers: Don’t settle for the first supplier. Gather quotes from multiple sources to compare prices and terms. This can also provide leverage in negotiations.
-
Stay Informed About Market Trends: Understanding market dynamics can help buyers anticipate price changes and plan their purchasing strategy accordingly.
-
Plan for Regulatory Compliance: Ensure that the electrical sockets meet the specific regulatory standards of your region. Non-compliance can lead to additional costs and delays.
What Should International Buyers Consider Regarding Indicative Prices?
While this analysis provides a comprehensive overview of the cost structure and pricing factors, it’s essential to acknowledge that prices can vary significantly based on market conditions and specific supplier negotiations. International buyers should seek quotations tailored to their requirements and remain flexible to adjustments in pricing due to fluctuating costs in materials and logistics.
Alternatives Analysis: Comparing usa electrical socket With Other Solutions
Understanding Alternatives to the USA Electrical Socket
When considering electrical solutions for international use, understanding the alternatives to the USA electrical socket is crucial for B2B buyers. Many businesses require adaptability in their electrical setups, particularly when dealing with international partners and customers. This section compares the USA electrical socket with two viable alternatives: the European (Type C) socket and the British (Type G) socket. Each option has unique characteristics that may better suit specific operational needs.
Comparison Table
Comparison Aspect | USA Electrical Socket | European Socket (Type C) | British Socket (Type G) |
---|---|---|---|
Performance | 120V, 60Hz | 230V, 50Hz | 230V, 50Hz |
Cost | Moderate | Low | High |
Ease of Implementation | Simple, common usage | Widely adopted in Europe | Requires special adapters |
Maintenance | Low | Low | Moderate |
Best Use Case | North America | Europe and parts of Asia | UK and former colonies |
In-Depth Analysis of Alternatives
What Are the Benefits and Drawbacks of the European Socket (Type C)?
The European socket (Type C) operates at 230V and 50Hz, making it suitable for most electrical appliances used across Europe and parts of Asia. One of its primary advantages is its widespread adoption, which allows for easy access to compatible devices and adapters. However, businesses that frequently operate in North America may find the voltage difference a challenge, as many appliances designed for lower voltage (120V) will not function correctly without a transformer or converter. This makes the Type C socket a less viable option for companies with dual market operations unless they invest in compatible equipment.
How Does the British Socket (Type G) Compare?
The British socket (Type G) offers a unique design with three rectangular pins and a built-in fuse for additional safety. Operating at 230V and 50Hz, it is a reliable option for high-power appliances. Its primary advantage lies in its safety features, which reduce the risk of electrical hazards. However, the higher cost of installation and maintenance can be a deterrent for some businesses. Additionally, the need for specific adapters when dealing with devices from other countries can complicate logistics, making it less appealing for companies with diverse international needs.
Conclusion: Which Electrical Socket Solution Should You Choose?
For B2B buyers, selecting the right electrical socket solution depends on multiple factors, including geographical operations, appliance compatibility, and budget constraints. If your business primarily operates in North America, the USA electrical socket is most suitable, given its widespread availability and compatibility with local devices. Conversely, if your operations extend into Europe or the UK, considering the European or British sockets may provide long-term benefits, despite potential upfront costs. Always assess your specific requirements and the electrical standards of your primary markets to ensure optimal performance and safety.
Essential Technical Properties and Trade Terminology for usa electrical socket
What Are the Key Technical Properties of USA Electrical Sockets?
Understanding the critical specifications of USA electrical sockets is essential for international B2B buyers. Here are some key properties to consider:
1. Voltage Rating (120V)
The standard voltage for USA electrical sockets is 120V. This specification is crucial for ensuring compatibility with electrical appliances. For B2B buyers, selecting products that operate within this voltage range minimizes the risk of equipment damage and ensures safe operation.
2. Frequency (60Hz)
The frequency of the electrical supply in the USA is 60Hz. This is particularly important for devices that rely on frequency for timing, such as clocks and some motorized equipment. Buyers should verify that their appliances can function correctly at this frequency to avoid operational issues.
3. Plug Types (Type A and Type B)
USA sockets accommodate two plug types: Type A, which has two flat parallel pins, and Type B, which includes an additional grounding pin. Buyers should ensure that their equipment is compatible with these plug types. Failing to do so may necessitate additional adapters or modifications, leading to increased costs and potential safety hazards.
4. Current Rating (15A)
Most USA electrical sockets are rated for a maximum current of 15 amps. Understanding this rating is vital for B2B buyers to ensure that their electrical devices do not exceed this limit, which could cause overheating and fire risks. It’s important to check the current requirements of all equipment intended for use.
5. Material Standards
The materials used in electrical sockets are often regulated to ensure safety and durability. Common materials include thermoplastics and metals that can withstand heat and electrical stress. Buyers should look for products that meet relevant safety certifications to ensure compliance with local and international standards.
6. Tolerance Levels
Tolerance levels refer to the allowable variation in dimensions and electrical properties of the socket. This is important for ensuring a snug fit and reliable electrical connections. Buyers should consider manufacturers that provide precise tolerances to guarantee compatibility with various devices.
What Are the Common Trade Terms Related to USA Electrical Sockets?
Familiarity with trade terminology is essential for effective communication and negotiation in the B2B sector. Here are some commonly used terms:
1. OEM (Original Equipment Manufacturer)
OEM refers to companies that produce parts or equipment that may be marketed by another manufacturer. In the context of electrical sockets, understanding OEM relationships can help buyers identify quality products and potential suppliers.
2. MOQ (Minimum Order Quantity)
MOQ is the smallest quantity of a product that a supplier is willing to sell. This term is critical for international buyers to understand as it can affect overall costs and inventory management. Buyers should negotiate MOQs that align with their needs to avoid excess inventory.
3. RFQ (Request for Quotation)
An RFQ is a document that a buyer sends to suppliers to request pricing and terms for specific products. For B2B buyers sourcing electrical sockets, issuing an RFQ helps compare offers and negotiate better deals.
4. Incoterms (International Commercial Terms)
Incoterms are a set of international trade terms that define the responsibilities of buyers and sellers regarding shipping, insurance, and tariffs. Understanding these terms is essential for B2B transactions to avoid disputes and ensure smooth logistics.
5. Compliance Standards
Compliance standards refer to the regulations that electrical products must meet to ensure safety and performance. Buyers should prioritize suppliers that adhere to recognized compliance standards to minimize liability and ensure product reliability.
6. Lead Time
Lead time is the time it takes from placing an order to receiving the goods. In the electrical socket industry, understanding lead times can help buyers plan their inventory and project timelines more effectively.
By grasping these technical properties and trade terms, international B2B buyers can make informed decisions when sourcing USA electrical sockets, ensuring compatibility and compliance while optimizing their supply chain.
Navigating Market Dynamics and Sourcing Trends in the usa electrical socket Sector
What Are the Current Market Dynamics and Key Trends in the USA Electrical Socket Sector?
The USA electrical socket sector is experiencing significant shifts driven by technological advancements, changing consumer preferences, and regulatory developments. A major driver is the increased reliance on smart technology and Internet of Things (IoT) devices, which require more versatile and adaptive power solutions. As international B2B buyers from regions like Africa, South America, the Middle East, and Europe engage with the U.S. market, understanding the implications of these trends is critical.
Emerging sourcing trends include the rise of modular and customizable electrical socket solutions, allowing businesses to cater to specific market needs. Additionally, there is a growing focus on integrating safety features into electrical sockets, such as surge protection and child-proof designs, which are becoming essential selling points. International buyers should also be aware of the shift towards dual-voltage and multi-functional products, facilitating easier global trade and reducing logistical complexities.
Furthermore, sustainability is influencing purchasing decisions in the electrical socket sector. Buyers are increasingly looking for suppliers who prioritize eco-friendly manufacturing processes and materials. This trend aligns with broader global efforts to minimize carbon footprints and enhance energy efficiency, which resonates strongly with environmentally conscious consumers and businesses alike.
How Is Sustainability Influencing Sourcing Decisions in the USA Electrical Socket Market?
Sustainability has emerged as a pivotal factor for B2B buyers in the USA electrical socket sector, influencing sourcing strategies and supplier selection. The environmental impact of electrical components is coming under scrutiny, with an emphasis on reducing waste and promoting energy efficiency. Buyers are encouraged to seek suppliers who adhere to sustainable practices, such as using recycled materials or minimizing energy consumption during production.
Ethical sourcing is equally important, as businesses are increasingly held accountable for their supply chain practices. Certifications such as Energy Star, RoHS (Restriction of Hazardous Substances), and other green certifications are becoming essential for suppliers aiming to establish credibility and attract international buyers. By prioritizing suppliers with these certifications, companies can ensure that their sourcing strategies align with their corporate social responsibility goals.
Moreover, the demand for eco-friendly products is driving innovation within the electrical socket market. Manufacturers are exploring biodegradable materials and sustainable design principles to meet this demand. For international buyers, embracing these trends not only enhances their brand reputation but also positions them favorably in competitive markets that value sustainability.
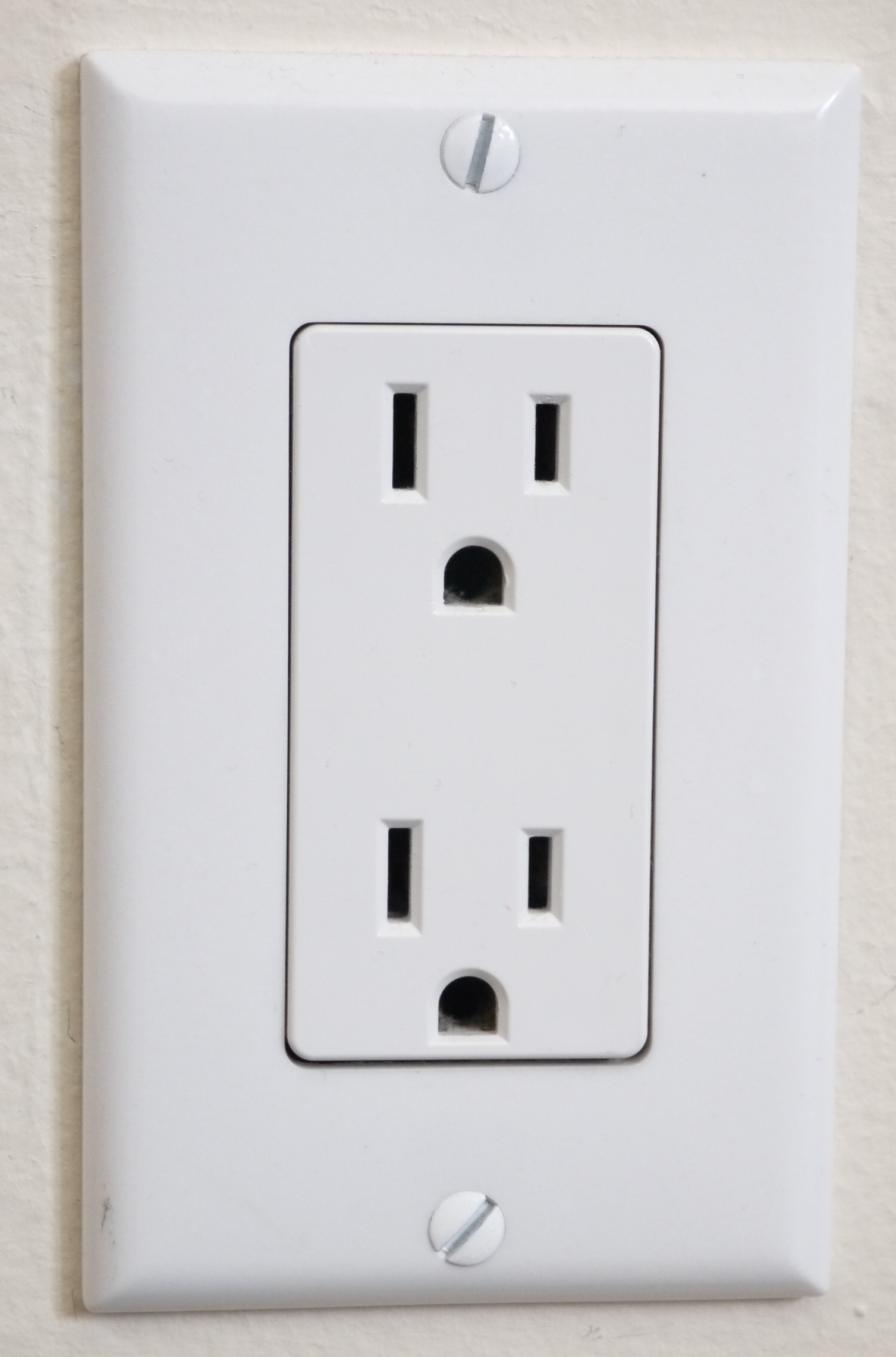
A stock image related to usa electrical socket.
What Is the Brief Evolution of the USA Electrical Socket Sector?
The evolution of the USA electrical socket sector can be traced back to the early 20th century when standardized plug types emerged to address the growing need for electrical appliances. The introduction of Type A and Type B plugs in the 1920s established a foundation for electrical safety and compatibility. Over the decades, advancements in technology have led to the incorporation of safety features, such as grounding pins and circuit breakers, enhancing user protection.
In recent years, the market has shifted towards smart electrical solutions, integrating connectivity and automation into traditional socket designs. This evolution reflects broader trends in consumer electronics and the increasing demand for multifunctional devices. For international B2B buyers, understanding this historical context is crucial for navigating the current landscape and making informed sourcing decisions in the USA electrical socket market.
Frequently Asked Questions (FAQs) for B2B Buyers of usa electrical socket
-
How do I solve compatibility issues with USA electrical sockets for my devices?
To solve compatibility issues with USA electrical sockets, first, check the plug type of your devices. The USA primarily uses Type A and Type B plugs, with Type A having two flat parallel pins and Type B having an additional grounding pin. If your devices do not fit these types, you will need a travel adapter. Additionally, ensure your devices can handle the USA’s standard voltage of 120V and frequency of 60Hz. If your appliances are single voltage rated and operate at a different voltage, consider using a voltage converter. -
What is the best travel adapter for USA electrical sockets?
The best travel adapter for USA electrical sockets is one that supports both Type A and Type B plugs. Look for a universal travel adapter that accommodates various plug types if you frequently travel. Ensure it has built-in safety features like surge protection. Additionally, check the maximum power rating to confirm it can handle your devices. Adapters with USB ports are also a convenient choice for charging multiple devices simultaneously. -
What are the typical minimum order quantities (MOQs) for USA electrical sockets?
Minimum order quantities (MOQs) for USA electrical sockets can vary significantly by supplier and product type. Generally, MOQs range from 500 to 5,000 units, depending on whether you’re sourcing standard or customized products. It’s advisable to communicate directly with manufacturers or suppliers to negotiate MOQs based on your purchasing needs. Some suppliers may offer flexibility for first-time buyers or smaller businesses. -
How can I vet suppliers for USA electrical sockets effectively?
To vet suppliers for USA electrical sockets, start by checking their certifications and compliance with safety standards such as UL or CE. Review their manufacturing capabilities and request product samples to assess quality. Utilize platforms like Alibaba or Global Sources, and read customer reviews. Additionally, consider visiting factories if possible, or use third-party inspection services to ensure that the supplier meets your quality expectations before placing a large order. -
What payment terms should I negotiate when sourcing USA electrical sockets?
When sourcing USA electrical sockets, common payment terms include a 30% deposit upfront and 70% upon delivery or before shipment. Depending on the supplier’s credibility, you might negotiate for more favorable terms, such as a letter of credit (LC) or payment through escrow services. Ensure that the payment method is secure and provides you with protection against potential disputes. Always clarify terms related to late payments or cancellations to avoid misunderstandings. -
What quality assurance (QA) processes should I expect from suppliers?
Quality assurance (QA) processes from suppliers of USA electrical sockets should include initial production inspections, in-process quality checks, and final product evaluations. Suppliers should be able to provide documentation of testing procedures and certifications. Inquire about their adherence to international quality standards such as ISO 9001. Establish clear communication channels for addressing any quality issues that may arise during production or post-delivery. -
How do logistics and shipping affect the cost of sourcing USA electrical sockets?
Logistics and shipping significantly impact the overall cost of sourcing USA electrical sockets. Factors such as shipping method (air vs. sea), distance, and weight of the shipment will determine freight costs. Additionally, customs duties and taxes can add to your expenses. To optimize costs, consider consolidating shipments or negotiating shipping rates with logistics providers. It’s also wise to factor in lead times when planning your inventory to avoid stock shortages. -
What customization options are available for USA electrical sockets?
Many suppliers offer customization options for USA electrical sockets, including size, color, and branding. You can request specific features like surge protection or smart technology integration. However, customization may affect MOQs and lead times, so discuss these factors with your supplier early in the negotiation process. Ensure that all specifications are documented in your agreement to avoid misunderstandings during production.
Important Disclaimer & Terms of Use
⚠️ Important Disclaimer
The information provided in this guide, including content regarding manufacturers, technical specifications, and market analysis, is for informational and educational purposes only. It does not constitute professional procurement advice, financial advice, or legal advice.
While we have made every effort to ensure the accuracy and timeliness of the information, we are not responsible for any errors, omissions, or outdated information. Market conditions, company details, and technical standards are subject to change.
B2B buyers must conduct their own independent and thorough due diligence before making any purchasing decisions. This includes contacting suppliers directly, verifying certifications, requesting samples, and seeking professional consultation. The risk of relying on any information in this guide is borne solely by the reader.
Strategic Sourcing Conclusion and Outlook for usa electrical socket
As international B2B buyers navigate the complexities of sourcing electrical sockets for the U.S. market, understanding the specifications and requirements of Type A and Type B plugs is paramount. This knowledge not only ensures compliance with U.S. electrical standards but also enhances the safety and efficiency of electrical usage.
Why is Strategic Sourcing Essential for Electrical Components in the USA?
Strategic sourcing allows companies to identify reliable suppliers who meet the necessary certifications for quality and safety, crucial in the electrical components sector. For businesses in Africa, South America, the Middle East, and Europe, leveraging strong supplier relationships can lead to cost savings and improved supply chain resilience.
How Can International Buyers Prepare for the U.S. Market?
Buyers should consider the voltage requirements (120V, 60Hz) and the need for potential voltage converters or transformers when sourcing products. Additionally, confirming the dual voltage compatibility of appliances will facilitate smoother operations.
What’s Next for Global Buyers?
As the demand for electrical components continues to grow, staying informed about evolving standards and innovations in the U.S. market will be vital. Engage with local industry experts and suppliers to optimize your sourcing strategies. By doing so, you position your business for success in a competitive landscape, ensuring you meet customer needs while driving profitability.