Boost Efficiency: The Complete Bucket Conveyor Guide (2025)
Introduction: Navigating the Global Market for bucket conveyor
In today’s global market, sourcing an efficient bucket conveyor system is paramount for businesses aiming to streamline their bulk material handling processes. However, navigating the complexities of international suppliers, varying regulations, and diverse applications can pose significant challenges for B2B buyers. This guide is designed to demystify the world of bucket conveyors, providing a comprehensive overview of their types, applications, and the intricacies of supplier vetting. From exploring cost-effective solutions to understanding the latest technological advancements, we aim to equip international buyers—particularly those from Africa, South America, the Middle East, and Europe (such as Egypt and South Africa)—with actionable insights that foster informed purchasing decisions.
As you delve into this resource, you will uncover critical factors to consider when selecting a bucket conveyor, such as capacity requirements, environmental considerations, and the importance of modular designs for adaptability. Additionally, we will address essential questions regarding maintenance, durability, and compliance with local regulations, ensuring that your investment meets both operational needs and industry standards. Ultimately, this guide serves as a valuable tool for optimizing your supply chain and enhancing productivity, empowering you to make strategic decisions that propel your business forward in the competitive landscape of bulk material handling.
Understanding bucket conveyor Types and Variations
Type Name | Key Distinguishing Features | Primary B2B Applications | Brief Pros & Cons for Buyers |
---|---|---|---|
Bucket Elevators | Vertical transport, modular design, enclosed buckets | Food & Beverage, Agriculture, Manufacturing | Pros: High capacity, gentle handling; Cons: Higher initial cost, space requirements. |
Continuous Bucket Conveyors | Continuous flow, overlapping buckets, low spillage risk | Recycling, Bulk Material Handling | Pros: Efficient for bulk materials; Cons: Limited to specific materials, potential wear. |
Z-Type Bucket Conveyors | Z-shaped configuration, multiple inlets/outlets, flexible design | Packaging, Food Processing | Pros: Versatile layout, efficient space usage; Cons: Complex installation, maintenance challenges. |
C-Type Bucket Conveyors | C-shaped configuration, suitable for horizontal and vertical transport | Mining, Cement Industry | Pros: Effective for heavy materials; Cons: Requires more maintenance, potential for material degradation. |
Pneumatic Bucket Conveyors | Air-powered transport, enclosed system, suitable for powders | Pharmaceutical, Chemical Processing | Pros: Minimal contamination risk; Cons: High energy consumption, limited to lighter materials. |
What Are the Characteristics of Bucket Elevators?
Bucket elevators are designed for vertical transport of bulk materials, featuring a modular design that allows for easy customization. They are particularly suited for industries such as food and beverage, agriculture, and manufacturing due to their high capacity and gentle handling capabilities. When considering a bucket elevator, buyers should evaluate the initial investment against long-term operational efficiency and maintenance requirements. The enclosed design minimizes spillage, making them ideal for clean environments.
How Do Continuous Bucket Conveyors Work?
Continuous bucket conveyors maintain a steady flow of material using overlapping buckets, significantly reducing the risk of spillage. These systems are widely utilized in recycling and bulk material handling sectors, where efficiency is critical. Buyers should consider the types of materials being transported, as these conveyors are best suited for bulk materials. While they offer high efficiency, potential wear on components can lead to increased maintenance.
What Makes Z-Type Bucket Conveyors Versatile?
Z-type bucket conveyors feature a unique Z-shaped configuration that allows for multiple inlets and outlets, making them highly adaptable to various layouts. They are commonly used in packaging and food processing applications. When purchasing a Z-type conveyor, businesses should assess their space constraints and the complexity of installation. While these conveyors provide flexibility and efficiency, their installation can be more intricate, requiring specialized knowledge.
Why Choose C-Type Bucket Conveyors for Heavy Materials?
C-type bucket conveyors are designed for both horizontal and vertical transport, making them suitable for heavy materials commonly found in the mining and cement industries. They are effective in moving bulk materials but do require more frequent maintenance due to the heavier loads. Buyers should weigh the benefits of efficiency against the potential for increased wear and tear on the system.
What Are the Benefits of Pneumatic Bucket Conveyors?
Pneumatic bucket conveyors utilize air pressure to transport materials through enclosed systems, minimizing contamination risks, particularly in pharmaceutical and chemical processing applications. While they are excellent for handling powders, buyers should be aware of their high energy consumption and limited suitability for heavier materials. When considering pneumatic options, businesses should evaluate the operational costs versus the benefits of maintaining a clean processing environment.
Key Industrial Applications of bucket conveyor
Industry/Sector | Specific Application of Bucket Conveyor | Value/Benefit for the Business | Key Sourcing Considerations for this Application |
---|---|---|---|
Food & Beverage | Transporting grains, cereals, and packaged goods | Enhances efficiency, reduces spillage, and ensures hygiene | Compliance with food safety standards, material durability |
Agriculture | Elevating and transferring fertilizers and seeds | Streamlines operations, minimizes handling costs | Customization options for varying bulk densities |
Chemical Processing | Moving bulk chemicals and powders | Ensures safe and controlled material handling | Corrosion-resistant materials, ease of maintenance |
Mining | Transporting ores and minerals | Increases productivity and reduces manual labor | Heavy-duty construction, ability to handle abrasive materials |
Recycling | Sorting and moving recyclable materials | Improves sorting efficiency and reduces contamination risks | Modular designs for flexibility, ease of cleaning |
How Are Bucket Conveyors Used in the Food & Beverage Industry?
In the food and beverage sector, bucket conveyors are extensively used for transporting grains, cereals, and packaged goods. These systems enhance operational efficiency by minimizing spillage and maintaining hygiene standards, crucial for compliance with food safety regulations. International buyers, particularly from regions like Africa and Europe, should consider sourcing conveyors that comply with FDA standards and are made from durable, food-grade materials to ensure long-term performance.
What Role Do Bucket Conveyors Play in Agriculture?
Bucket conveyors are pivotal in the agricultural industry for elevating and transferring fertilizers and seeds. They streamline operations by automating the movement of bulk materials, thus reducing manual handling costs and improving labor efficiency. Buyers in South America and Africa should seek customizable solutions that can accommodate varying bulk densities and facilitate easy integration into existing systems.
How Are Bucket Conveyors Applied in Chemical Processing?
In chemical processing, bucket conveyors are utilized for the safe transport of bulk chemicals and powders. These conveyors ensure controlled handling, which is essential for maintaining safety and preventing contamination. When sourcing, international buyers should prioritize corrosion-resistant materials and easy maintenance features to ensure the longevity and reliability of their systems, especially in harsh environments.
Why Are Bucket Conveyors Important in Mining?
In the mining industry, bucket conveyors are essential for transporting ores and minerals from extraction sites to processing facilities. They increase productivity by automating material movement, thereby reducing the need for manual labor. Buyers from regions with active mining operations, such as South Africa, should focus on heavy-duty constructions that can withstand abrasive materials and harsh conditions, ensuring operational efficiency.
What Benefits Do Bucket Conveyors Offer in Recycling Applications?
Bucket conveyors are increasingly used in recycling operations for sorting and moving recyclable materials. They improve sorting efficiency and reduce contamination risks, which are critical for maintaining the quality of recycled products. Buyers should consider modular designs that allow for flexibility in layout and ease of cleaning, facilitating quick adjustments to accommodate varying material types and volumes.
3 Common User Pain Points for ‘bucket conveyor’ & Their Solutions
Scenario 1: Overcoming Material Spillage During Transportation
The Problem: One of the most common issues faced by B2B buyers when using bucket conveyors is the spillage of materials during transportation. This often occurs when the buckets are not designed to overlap adequately or when there are gaps at the inlets and outlets. Spillage not only leads to material loss but also creates safety hazards in the workspace, requiring additional cleanup and potentially affecting the quality of the product being handled. Buyers from industries like food and beverage, manufacturing, or agriculture may find this particularly frustrating, as they need to maintain high standards for cleanliness and efficiency.
The Solution: To combat material spillage, it is crucial to select bucket conveyors with an enclosed and overlapping bucket design. Look for systems that feature pivoting buckets, which minimize gaps and prevent spillage during loading and unloading. Additionally, consider sourcing bucket conveyors with adjustable inlets and outlets that can be tailored to fit your specific material handling needs. Implementing regular maintenance checks to ensure that the conveyor is properly aligned and functioning can also significantly reduce the risk of spillage. Training staff on proper loading techniques will further optimize the system and minimize losses.
Scenario 2: Addressing High Maintenance Costs and Downtime
The Problem: Frequent breakdowns and high maintenance costs can plague businesses relying on bucket conveyors, particularly in regions with limited access to spare parts or technical support. This scenario is common among B2B buyers in Africa and South America, where supply chain issues may delay repairs and increase downtime. High operational costs can severely impact a company’s profitability, making it essential to find a solution that is both reliable and cost-effective.
The Solution: Invest in high-quality bucket conveyors designed for low maintenance and built with durable materials. Select models that feature easily removable inspection covers and accessible components, which simplify maintenance tasks and reduce the time spent on repairs. Opt for systems with automatic chain tensioning devices and overload protection to minimize wear and tear. Additionally, establishing a relationship with a local distributor for spare parts can reduce downtime in case of unexpected failures. Implementing a preventive maintenance schedule will further ensure that the system operates smoothly and efficiently, extending its lifespan and reducing overall costs.
Scenario 3: Navigating Customization Needs for Diverse Applications
The Problem: Many businesses require bucket conveyors that can handle a variety of materials and applications, from fragile food products to heavy industrial components. Buyers often struggle to find a one-size-fits-all solution that meets their unique needs, particularly in diverse markets like the Middle East and Europe. The inability to customize bucket conveyors can lead to inefficiencies and suboptimal performance, as the system may not be suited for specific material characteristics or handling requirements.
The Solution: When sourcing bucket conveyors, prioritize modular designs that offer customization options for different applications. Look for systems that allow for adjustable bucket sizes, multiple inlets and outlets, and selective tipping capabilities. Working with manufacturers that provide tailored solutions can ensure the conveyor meets your specific requirements. Engaging in a thorough needs assessment before purchasing can help identify the key features necessary for your operations. Additionally, consider partnering with a supplier that offers comprehensive support, including installation and training, to ensure optimal configuration and performance of your bucket conveyor system.
Strategic Material Selection Guide for bucket conveyor
When selecting materials for bucket conveyors, international B2B buyers must consider various factors that influence performance, durability, and compliance with industry standards. The choice of material directly impacts the operational efficiency and lifespan of the conveyor system. Below, we analyze four common materials used in bucket conveyor construction: carbon steel, stainless steel, plastic, and aluminum.
What Are the Key Properties of Carbon Steel for Bucket Conveyors?
Carbon steel is a popular choice for bucket conveyors due to its strength and durability. It typically has a high tensile strength, making it suitable for heavy-duty applications. Carbon steel can withstand significant mechanical stress and is generally resistant to wear and tear. However, it has a lower corrosion resistance compared to other materials, which can be a concern in humid or corrosive environments.
Pros:
– High strength and durability.
– Cost-effective for large-scale operations.
– Easily fabricated and welded.
Cons:
– Prone to rust and corrosion if not properly coated.
– Requires regular maintenance to prevent degradation.
Impact on Application: Carbon steel is ideal for transporting bulk materials in dry environments. However, in regions with high humidity, such as parts of Africa and South America, additional protective coatings may be necessary.
How Does Stainless Steel Compare for Bucket Conveyor Applications?
Stainless steel is renowned for its corrosion resistance and hygienic properties, making it an excellent choice for food and pharmaceutical applications. It can withstand a wide range of temperatures and is less prone to rusting than carbon steel. The material’s durability ensures a long lifespan, which is critical for continuous operations.
Pros:
– Exceptional corrosion resistance.
– Easy to clean and maintain.
– Suitable for high-temperature applications.
Cons:
– Higher initial cost compared to carbon steel.
– More complex to fabricate and weld.
Impact on Application: Stainless steel is particularly beneficial in industries where hygiene is paramount, such as food processing in Europe and the Middle East. Compliance with health standards (like FDA or EU regulations) is easier to achieve with this material.
What Are the Advantages of Using Plastic for Bucket Conveyors?
Plastic, specifically high-density polyethylene (HDPE) or polypropylene, is increasingly used in bucket conveyors due to its lightweight nature and resistance to corrosion. These materials are often used in applications where chemical resistance is essential, such as in the handling of fertilizers or chemicals.
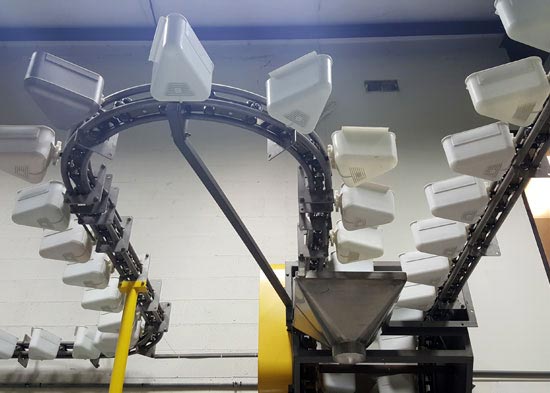
A stock image related to bucket conveyor.
Pros:
– Lightweight, reducing energy consumption.
– Resistant to a wide range of chemicals.
– Lower noise levels during operation.
Cons:
– Lower strength compared to metals, which may limit load capacity.
– Can be more susceptible to wear under heavy loads.
Impact on Application: Plastic buckets are ideal for transporting granular materials and are suitable for various industries, including agriculture and chemicals. Buyers in regions like South America and Africa may find plastic options advantageous due to their lower weight and ease of handling.
Why Consider Aluminum for Bucket Conveyors?
Aluminum is another viable option for bucket conveyors, known for its lightweight and excellent corrosion resistance. It is often used in applications where weight savings are crucial, such as in aerospace and automotive industries.
Pros:
– Lightweight, facilitating easier installation and operation.
– Good corrosion resistance, suitable for various environments.
– Aesthetic appeal for visible installations.
Cons:
– Generally more expensive than carbon steel.
– Lower tensile strength compared to steel options.
Impact on Application: Aluminum is suitable for applications requiring frequent movement or installation in corrosive environments. Buyers in the Middle East and Europe may prefer aluminum for its lightweight properties and aesthetic advantages.
Summary Table of Material Selection for Bucket Conveyors
Material | Typical Use Case for bucket conveyor | Key Advantage | Key Disadvantage/Limitation | Relative Cost (Low/Med/High) |
---|---|---|---|---|
Carbon Steel | Heavy-duty bulk material transport | High strength and durability | Prone to rust without protective coating | Medium |
Stainless Steel | Food and pharmaceutical applications | Exceptional corrosion resistance | Higher initial cost | High |
Plastic | Chemical handling | Lightweight and chemically resistant | Lower strength limits load capacity | Low |
Aluminum | Aerospace and automotive applications | Lightweight and corrosion-resistant | Generally more expensive | Medium |
By understanding the properties, advantages, and limitations of each material, B2B buyers can make informed decisions that align with their operational needs and compliance requirements.
In-depth Look: Manufacturing Processes and Quality Assurance for bucket conveyor
What Are the Main Stages of Manufacturing Bucket Conveyors?
The manufacturing of bucket conveyors involves several critical stages that ensure the final product meets both performance and quality standards. These stages include material preparation, forming, assembly, and finishing.
-
Material Preparation: The initial phase involves selecting high-quality materials suitable for the intended application. Common materials include carbon steel, stainless steel, and food-grade reinforced polyamide for the buckets. Suppliers often conduct material inspections to ensure compliance with specifications and standards such as ASTM or ISO 9001.
-
Forming: This stage involves shaping the materials into the required components. Techniques such as cutting, bending, and welding are commonly employed. For instance, bucket forming may involve injection molding for plastic components, while metal parts may be shaped using CNC machining for precision. Manufacturers often utilize advanced technologies like laser cutting for enhanced accuracy and efficiency.
-
Assembly: Once individual components are prepared, they are assembled into the complete conveyor system. This process may include the installation of buckets onto chains or belts, integration of motors, and alignment of components to ensure smooth operation. Quality checks at this stage are crucial to prevent issues during operation.
-
Finishing: The final stage involves applying protective coatings, such as powder coating or galvanization, to enhance durability and resistance to environmental factors. This is particularly important for systems operating in harsh conditions, such as those found in mining or food processing industries. Finishing processes may also include polishing or additional quality inspections.
How Is Quality Assurance Implemented in Bucket Conveyor Manufacturing?
Quality assurance (QA) in the manufacturing of bucket conveyors is vital for ensuring that products meet the required standards and function effectively in their intended environments.
-
Relevant International Standards: Many manufacturers adhere to international standards such as ISO 9001, which outlines quality management principles. Additionally, industry-specific certifications like CE for European markets or API for oil and gas applications may be required. These certifications ensure that products comply with safety, health, and environmental regulations.
-
Quality Control Checkpoints: Effective quality control (QC) involves multiple checkpoints throughout the manufacturing process:
– Incoming Quality Control (IQC): This involves inspecting raw materials upon receipt to ensure they meet specifications.
– In-Process Quality Control (IPQC): During the manufacturing process, regular inspections are conducted to identify any deviations from quality standards.
– Final Quality Control (FQC): Once the product is assembled, a final inspection is performed to verify that all components function correctly and meet design specifications. -
Common Testing Methods: Manufacturers typically employ various testing methods, including:
– Functional Testing: Ensures that the bucket conveyor operates as intended under load.
– Durability Testing: Assesses the wear and tear of components under simulated operational conditions.
– Safety Testing: Checks for compliance with safety standards, especially for conveyors used in food processing or pharmaceuticals.
How Can B2B Buyers Verify Supplier Quality Control?
For international B2B buyers, particularly those from regions such as Africa, South America, the Middle East, and Europe, ensuring the quality of bucket conveyors is paramount. Here are several strategies to verify supplier quality control:
-
Supplier Audits: Conducting on-site audits of potential suppliers allows buyers to assess their manufacturing processes, quality control measures, and adherence to international standards. Audits can reveal the supplier’s commitment to quality and any areas needing improvement.
-
Requesting Quality Reports: Buyers should request documentation that outlines the supplier’s quality management system, including ISO certifications, quality control processes, and results from previous quality audits. This documentation provides insight into the supplier’s operational standards.
-
Third-Party Inspections: Engaging third-party inspection agencies can offer an unbiased evaluation of the supplier’s manufacturing processes and product quality. These inspections can be particularly useful for buyers who are unable to visit the supplier’s facility.
-
Understanding QC Certification Nuances: Different regions may have varying certification requirements. For instance, CE marking is crucial for products sold in the European market, while other regions may require compliance with local standards. B2B buyers should familiarize themselves with these nuances to ensure compliance and avoid potential legal issues.
What Challenges Do B2B Buyers Face in Ensuring Quality Control?
International B2B buyers may encounter several challenges when ensuring quality control in bucket conveyor manufacturing:
-
Language Barriers: Communication issues can arise when dealing with suppliers from different regions. This can complicate negotiations and the understanding of quality requirements.
-
Cultural Differences: Varied business practices and cultural norms may impact quality assurance processes. Buyers should be aware of these differences and adapt their approach accordingly.
-
Logistical Issues: Transporting bucket conveyors across international borders can present challenges, including delays, damage during shipping, and customs regulations. Ensuring that quality is maintained throughout the supply chain is critical.
-
Supplier Reliability: Finding a reliable supplier who consistently meets quality standards can be difficult. Buyers may need to invest time in researching potential suppliers and establishing long-term relationships to ensure quality assurance.
Conclusion: The Importance of Quality in Bucket Conveyor Manufacturing
For B2B buyers, understanding the manufacturing processes and quality assurance measures involved in bucket conveyor production is essential for making informed purchasing decisions. By focusing on quality at every stage—from material preparation to final inspection—buyers can ensure they receive reliable and effective equipment tailored to their operational needs. Implementing robust verification strategies will further enhance the assurance that the chosen supplier adheres to international quality standards, ultimately contributing to the success of their operations.
Practical Sourcing Guide: A Step-by-Step Checklist for ‘bucket conveyor’
To assist international B2B buyers in making informed decisions when procuring bucket conveyors, this practical sourcing guide outlines essential steps and considerations. By following this checklist, you can ensure a streamlined procurement process that meets your operational needs.
Step 1: Define Your Technical Specifications
Begin by clearly articulating your technical requirements, including the type of materials to be handled, desired capacity, and specific dimensions. Consider the environment in which the bucket conveyor will operate, such as temperature ranges and exposure to moisture. This foundational step helps narrow down your options and ensures that suppliers can meet your unique needs.
Step 2: Research Market Options
Investigate various suppliers and manufacturers specializing in bucket conveyors. Look for companies with a strong reputation in your industry, particularly those experienced in serving markets in Africa, South America, the Middle East, and Europe. Pay attention to product catalogs and case studies that demonstrate their capabilities and past performance.
Step 3: Evaluate Supplier Certifications and Standards
Before engaging with a supplier, verify their compliance with relevant industry certifications and standards. This is crucial for ensuring product quality and safety, particularly in regulated sectors like food and pharmaceuticals. Check for certifications such as ISO 9001 and compliance with local regulations in your region.
Step 4: Request Detailed Quotations
Once you have identified potential suppliers, request detailed quotations that include pricing, lead times, and payment terms. Make sure to inquire about the warranty and after-sales support offered. Detailed quotes will help you make an apples-to-apples comparison among suppliers, facilitating a more informed decision.
Step 5: Assess Customization Options
Consider whether the supplier can provide customizable solutions to fit your specific needs. Some operations may require unique configurations, such as multiple inlets and outlets or specialized bucket designs. Discuss potential modifications and assess the supplier’s flexibility in adapting their products to your requirements.
Step 6: Review Maintenance and Support Services
Evaluate the maintenance requirements and support services offered by each supplier. A reliable bucket conveyor should have low maintenance needs, but it’s important to understand what support is available in case of breakdowns. Inquire about training for your staff and the availability of spare parts to minimize downtime.
Step 7: Check References and Client Feedback
Finally, request references from previous clients, especially those in similar industries or geographical areas. This step provides insights into the supplier’s reliability and the performance of their bucket conveyors. Look for testimonials that highlight customer satisfaction and long-term operational success.
By following this step-by-step sourcing guide, you can confidently navigate the procurement process for bucket conveyors, ensuring that you select a solution that aligns with your operational goals and business needs.
Comprehensive Cost and Pricing Analysis for bucket conveyor Sourcing
What Are the Key Cost Components in Bucket Conveyor Sourcing?
When sourcing bucket conveyors, understanding the cost structure is crucial for international B2B buyers. The primary cost components include:
-
Materials: The type of materials used significantly impacts the cost. For instance, stainless steel may be more expensive than carbon steel, but it offers better corrosion resistance, which is vital for food or chemical applications.
-
Labor: Labor costs can vary based on the region and the complexity of the manufacturing process. Skilled labor is often necessary for the assembly and quality control of bucket conveyors, which can add to the overall cost.
-
Manufacturing Overhead: This includes indirect costs associated with production, such as utilities, rent, and administrative expenses. Efficient manufacturing processes can help reduce overhead, allowing suppliers to offer more competitive pricing.
-
Tooling: The initial investment in tooling can be significant, especially for customized or specialized conveyors. Buyers should inquire about the tooling costs when requesting quotes for custom solutions.
-
Quality Control (QC): Implementing robust quality control measures ensures the reliability and longevity of the conveyor system. However, these processes can also increase costs, particularly if third-party certifications are required.
-
Logistics: Shipping and handling costs vary based on the distance, weight, and size of the equipment. International buyers should consider the total logistics costs, including customs duties and taxes, when evaluating prices.
-
Margin: Suppliers typically incorporate a profit margin into their pricing. Understanding the industry standard margins can help buyers negotiate better deals.
How Do Price Influencers Affect Bucket Conveyor Costs?
Several factors influence the pricing of bucket conveyors:
-
Volume/MOQ: The minimum order quantity (MOQ) can affect pricing. Larger orders often lead to lower per-unit costs due to economies of scale, making it advantageous for buyers to consolidate orders.
-
Specifications and Customization: Custom specifications can significantly increase costs. Buyers should clearly define their requirements to avoid unnecessary expenses related to customization.
-
Materials and Quality Certifications: Higher quality materials and certifications (e.g., FDA compliance for food handling) typically come at a premium. Buyers should weigh the importance of these factors against their budget constraints.
-
Supplier Factors: Supplier reputation, location, and reliability can influence pricing. Established suppliers with a track record of quality may charge more but offer better assurance of performance.
-
Incoterms: Understanding Incoterms (International Commercial Terms) is essential as they define the responsibilities of buyers and sellers regarding shipping costs, insurance, and risk. Misunderstandings can lead to unexpected costs.
What Are Effective Buyer Tips for Negotiating Bucket Conveyor Prices?
B2B buyers can employ several strategies to enhance their purchasing power:
-
Negotiate Based on Total Cost of Ownership (TCO): Rather than focusing solely on the upfront price, consider the total cost of ownership, which includes maintenance, operation, and potential downtime costs. This perspective can help justify higher initial investments in more durable systems.
-
Explore Multiple Quotes: Obtaining multiple quotes from different suppliers allows buyers to compare prices and negotiate better terms. Ensure that quotes are based on the same specifications for accurate comparisons.
-
Leverage Long-term Relationships: Building long-term relationships with suppliers can lead to better pricing and terms. Suppliers are often more willing to negotiate with buyers they know will provide repeat business.
-
Consider Local Suppliers: For buyers in regions such as Africa or South America, sourcing from local manufacturers can reduce logistics costs and lead times. It also supports local economies.
-
Stay Informed About Market Trends: Understanding global market trends and potential supply chain disruptions can provide leverage in negotiations. Buyers can use this information to negotiate pricing or terms based on market conditions.
Conclusion: What Should International Buyers Keep in Mind?
While indicative prices for bucket conveyors can vary widely, understanding the detailed cost structure and price influencers enables informed decision-making. International B2B buyers, particularly from diverse regions like Africa, South America, the Middle East, and Europe, should approach sourcing strategically. By focusing on the total cost of ownership, negotiating effectively, and considering all relevant factors, buyers can secure the best value for their investment in bucket conveyor systems.
Alternatives Analysis: Comparing bucket conveyor With Other Solutions
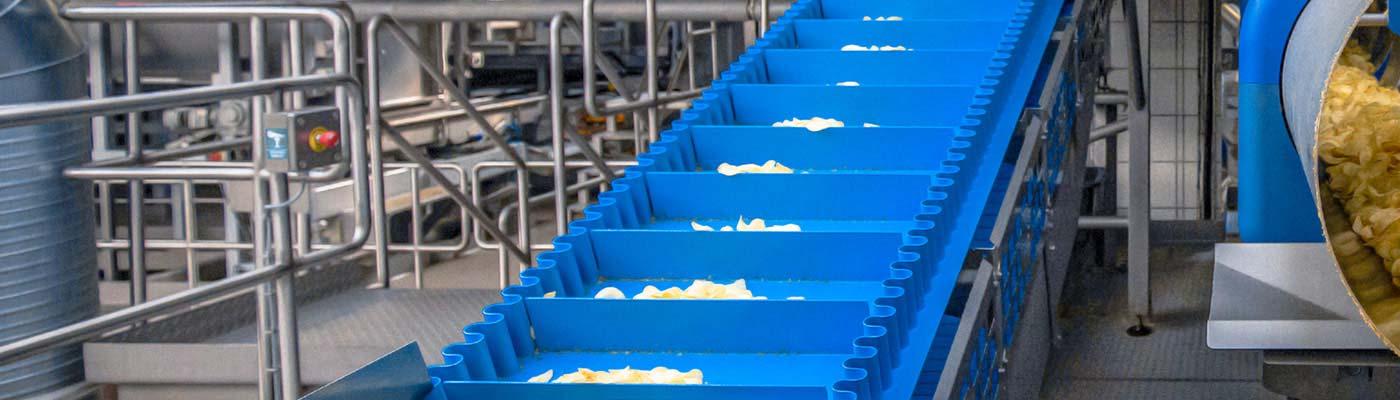
A stock image related to bucket conveyor.
The choice of material handling solutions in industrial settings is crucial for optimizing efficiency and reducing operational costs. This section will analyze bucket conveyors alongside other viable alternatives, providing B2B buyers with actionable insights to make informed decisions.
Comparison Aspect | Bucket Conveyor | Belt Conveyor | Screw Conveyor |
---|---|---|---|
Performance | High capacity; ideal for bulk materials | Versatile; good for various materials | Efficient for granular and powder materials |
Cost | Moderate initial investment; low operating costs | Low initial cost; medium maintenance costs | Moderate cost; higher maintenance compared to belt |
Ease of Implementation | Relatively simple; modular design allows customization | Easy to install; widely available components | Installation can be complex; requires precise alignment |
Maintenance | Low maintenance; easy access to components | Moderate; requires regular checks | Higher maintenance; components can wear out quickly |
Best Use Case | Food, agriculture, and chemical industries | General material handling; packaging | Bulk material handling; food and agriculture |
What Are the Advantages and Disadvantages of Belt Conveyors?
Belt conveyors are one of the most common alternatives to bucket conveyors. They offer a lower initial investment and are easy to implement due to their widespread availability. Their versatility allows them to handle various materials, from packaged goods to bulk items. However, they may not be as effective in situations requiring vertical lifting or gentle handling of fragile items. Regular maintenance is necessary to ensure that belts do not slip or wear out prematurely.
How Do Screw Conveyors Compare to Bucket Conveyors?
Screw conveyors are highly efficient for transporting granular and powder materials. They can be designed for horizontal, inclined, or vertical movement, making them versatile for different applications. However, screw conveyors require more maintenance due to the wear and tear on the screw and housing. Their installation can also be complex, requiring precise alignment to function effectively. While they are suitable for bulk materials, they may not handle fragile items as gently as bucket conveyors.
Conclusion: How to Choose the Right Material Handling Solution for Your Needs
When selecting between bucket conveyors and alternatives like belt or screw conveyors, B2B buyers should consider several factors, including the nature of the materials being handled, the required capacity, and maintenance capabilities. Bucket conveyors excel in applications requiring gentle handling and bulk movement, making them ideal for food and chemical industries. Conversely, belt conveyors offer a cost-effective solution for general material handling, while screw conveyors are suitable for specific bulk material applications. Evaluating these aspects against your operational needs will help ensure that you choose the most efficient and effective solution for your business.
Essential Technical Properties and Trade Terminology for bucket conveyor
What Are the Essential Technical Properties of Bucket Conveyors?
When considering the procurement of bucket conveyors, it is crucial to understand the technical specifications that can impact performance, durability, and maintenance costs. Here are some key properties:
1. Material Grade
Bucket conveyors are typically constructed from materials such as carbon steel, stainless steel, or reinforced polymers. The choice of material affects the conveyor’s resistance to corrosion, wear, and temperature extremes. For example, stainless steel is ideal for food processing applications due to its non-corrosive nature, while carbon steel might be more cost-effective for other industrial uses. Understanding the material grade helps B2B buyers select the right conveyor for their specific operational environment.
2. Capacity
The capacity of a bucket conveyor is measured in cubic feet per hour (CFH) and indicates how much bulk material it can transport within a given timeframe. Common capacities range from 300 CFH to 1,800 CFH. Choosing the right capacity is essential for ensuring that the conveyor meets production demands without causing bottlenecks, especially in high-volume operations.
3. Bucket Design and Size
The bucket design—whether overlapping or enclosed—affects material handling efficiency and minimizes spillage. Bucket sizes vary, typically ranging from 9 inches to 2 feet wide. The design should align with the type of material being transported and the operational requirements. For instance, larger buckets may be necessary for bulkier materials, while smaller buckets might be more suited for fine powders.
4. Drive Mechanism
The drive mechanism, often a variable frequency drive (VFD), controls the speed and efficiency of the conveyor. A well-designed drive mechanism can enhance energy efficiency and reduce operational costs. Understanding the drive type is vital for B2B buyers as it impacts the overall system’s performance and maintenance needs.
5. Maintenance Requirements
Bucket conveyors should be designed for low maintenance, featuring easily accessible inspection ports and removable covers. The frequency and complexity of maintenance tasks can significantly affect operational downtime and costs. B2B buyers should consider these factors when evaluating potential suppliers to ensure long-term operational efficiency.
What Common Trade Terms Should International B2B Buyers Know?
Familiarity with industry terminology is crucial for effective communication and negotiation in the procurement of bucket conveyors. Here are some essential trade terms:
1. OEM (Original Equipment Manufacturer)
This term refers to a company that produces parts or equipment that may be marketed by another manufacturer. In the context of bucket conveyors, knowing the OEM helps buyers understand the quality and reliability of the equipment being purchased.
2. MOQ (Minimum Order Quantity)
MOQ is the smallest quantity of a product that a supplier is willing to sell. Understanding the MOQ is vital for B2B buyers to ensure they can meet their operational needs without overcommitting financially.
3. RFQ (Request for Quotation)
An RFQ is a document that buyers send to suppliers requesting pricing and other details for specific products. Crafting an effective RFQ is essential for obtaining competitive bids and ensuring that all necessary specifications are included.
4. Incoterms
International Commercial Terms (Incoterms) define the responsibilities of buyers and sellers in the shipping process. Familiarity with these terms helps B2B buyers negotiate shipping costs and understand liability in case of damage or loss during transit.
5. Lead Time
Lead time refers to the amount of time it takes from placing an order to receiving the product. Understanding lead times is crucial for B2B buyers to plan their production schedules effectively and avoid delays.
Understanding these technical properties and trade terms equips international B2B buyers from regions like Africa, South America, the Middle East, and Europe with the knowledge needed to make informed purchasing decisions regarding bucket conveyors. By prioritizing these aspects, buyers can enhance operational efficiency and ensure a successful procurement process.
Navigating Market Dynamics and Sourcing Trends in the bucket conveyor Sector
What Are the Current Market Dynamics and Key Trends in the Bucket Conveyor Sector?
The bucket conveyor market is experiencing robust growth driven by increased industrial automation and the need for efficient bulk material handling solutions. Emerging technologies, such as IoT and AI, are enhancing operational efficiency by enabling predictive maintenance and real-time monitoring. For international B2B buyers, particularly from Africa, South America, the Middle East, and Europe, understanding these dynamics is crucial. Countries like South Africa and Egypt are witnessing a surge in infrastructure projects, creating demand for reliable bulk handling systems.
Moreover, the rise in e-commerce and food processing industries is propelling the need for advanced conveyor systems. Buyers should focus on modular designs that allow for customization, as these can adapt to varying operational requirements. The trend towards automation in manufacturing is also leading to the integration of bucket conveyors with other systems, such as robotics and automated storage solutions. This integration not only boosts productivity but also reduces labor costs, making it a compelling investment for businesses in emerging markets.
How Is Sustainability Impacting Sourcing Trends in the Bucket Conveyor Industry?
Sustainability has become a pivotal aspect of sourcing strategies in the bucket conveyor sector. International buyers are increasingly prioritizing suppliers that demonstrate commitment to environmental stewardship and ethical sourcing practices. This shift is particularly noticeable in regions like Europe, where stringent regulations on carbon emissions and waste management are in place.
Buyers are encouraged to seek manufacturers that utilize environmentally friendly materials, such as recyclable plastics and sustainable metals, in their bucket conveyor systems. Additionally, certifications like ISO 14001 for environmental management and LEED for sustainable building practices are essential indicators of a supplier’s commitment to sustainability. The adoption of energy-efficient technologies, such as variable frequency drives (VFDs), can also help reduce operational costs and carbon footprints. By aligning with sustainable suppliers, B2B buyers not only enhance their corporate social responsibility (CSR) profiles but also gain a competitive edge in their respective markets.
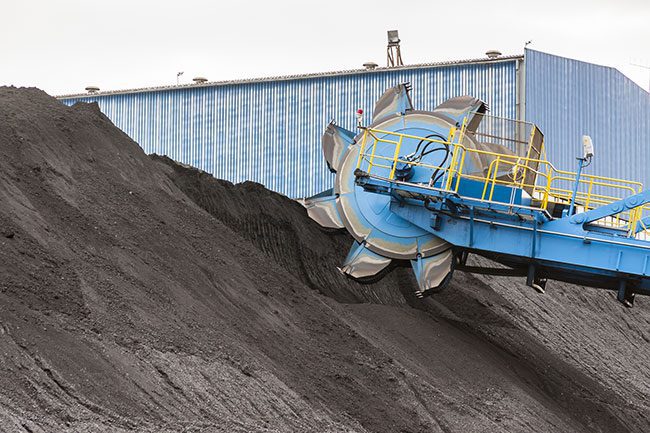
A stock image related to bucket conveyor.
What Is the Historical Evolution of Bucket Conveyors and Its Significance for B2B Buyers?
The bucket conveyor system has evolved significantly since its inception in the late 19th century. Originally developed for transporting bulk materials in mining, its applications have expanded across various industries, including food processing, pharmaceuticals, and recycling. The integration of advanced materials and technologies has transformed bucket conveyors into more efficient, durable, and versatile systems.
For B2B buyers, understanding this evolution is crucial as it highlights the importance of choosing modern, technologically advanced systems that can meet today’s operational demands. The advancements in design, such as modular configurations and automated tipping mechanisms, allow for greater flexibility and efficiency in material handling. By leveraging these innovations, buyers can optimize their supply chains and improve overall productivity, making a well-informed choice when sourcing bucket conveyor solutions.
Frequently Asked Questions (FAQs) for B2B Buyers of bucket conveyor
-
How do I choose the right bucket conveyor for my business needs?
Choosing the right bucket conveyor involves assessing your specific material handling requirements, such as the type of materials you are moving, the desired capacity, and the layout of your facility. Consider factors such as the height and distance the materials need to be transported, the speed of operation, and the need for multiple inlets or outlets. Additionally, evaluate the construction material of the conveyor, especially if you operate in a wet or corrosive environment. Consulting with suppliers who can provide tailored solutions based on your operational needs is highly recommended. -
What are the key advantages of using bucket conveyors over other systems?
Bucket conveyors offer several advantages, including their ability to handle bulk materials gently without spillage, which is crucial for industries like food and pharmaceuticals. Their modular design allows for easy customization and installation, making them versatile for different applications. Unlike traditional belt conveyors, bucket conveyors can transport materials vertically and horizontally, optimizing space. Moreover, they require minimal maintenance due to their robust construction, which can lead to cost savings in the long run. -
What customization options are available for bucket conveyors?
Customization options for bucket conveyors include varying bucket sizes, materials, and configurations to suit specific applications. Buyers can opt for features such as selective tipping capabilities, multiple inlets and outlets, and varying heights and angles of incline. Additionally, you can choose between different construction materials, such as stainless steel or carbon steel, based on your operational environment. Discussing your specific needs with manufacturers can lead to tailored solutions that enhance efficiency and productivity. -
What is the typical minimum order quantity (MOQ) for bucket conveyors?
Minimum order quantities (MOQ) for bucket conveyors can vary significantly depending on the manufacturer and the complexity of the conveyor system. Generally, MOQs can range from a single unit for standard models to larger quantities for custom or specialized designs. It is advisable to directly contact suppliers to inquire about their MOQ policies and explore options that may accommodate smaller businesses or trial orders. -
What payment terms should I expect when sourcing bucket conveyors internationally?
Payment terms for international purchases of bucket conveyors typically include options such as advance payment, letters of credit, or payment upon delivery. Terms can vary based on the supplier’s policies, the buyer’s creditworthiness, and the total order value. It is essential to negotiate terms that align with your cash flow requirements and to ensure clarity on any additional costs, such as shipping and customs duties, to avoid unexpected expenses. -
How do I ensure quality assurance for bucket conveyors sourced from international suppliers?
To ensure quality assurance when sourcing bucket conveyors internationally, it is crucial to conduct thorough due diligence on potential suppliers. This includes reviewing their certifications, quality control processes, and customer testimonials. Requesting product samples or visiting manufacturing facilities can provide insights into their production standards. Additionally, consider implementing a third-party inspection service before shipment to verify that the conveyors meet your specifications and industry standards. -
What logistics considerations should I keep in mind when importing bucket conveyors?
When importing bucket conveyors, logistics considerations include selecting the right shipping method based on urgency and cost, understanding customs regulations in your country, and ensuring proper documentation is in place. It’s important to plan for potential delays at customs and to work with freight forwarders who have experience with heavy machinery. Additionally, consider the cost of insurance for high-value items during transit and ensure that your delivery schedule aligns with your operational needs. -
How can I assess the reliability of a bucket conveyor supplier?
Assessing the reliability of a bucket conveyor supplier involves researching their reputation in the industry, checking for customer reviews and case studies, and evaluating their experience and expertise in your specific sector. Look for suppliers who provide transparent communication, responsive customer service, and comprehensive support, including installation and maintenance services. Participating in industry trade shows or networking events can also help you connect with reputable suppliers and gather firsthand insights from other buyers.
Important Disclaimer & Terms of Use
⚠️ Important Disclaimer
The information provided in this guide, including content regarding manufacturers, technical specifications, and market analysis, is for informational and educational purposes only. It does not constitute professional procurement advice, financial advice, or legal advice.
While we have made every effort to ensure the accuracy and timeliness of the information, we are not responsible for any errors, omissions, or outdated information. Market conditions, company details, and technical standards are subject to change.
B2B buyers must conduct their own independent and thorough due diligence before making any purchasing decisions. This includes contacting suppliers directly, verifying certifications, requesting samples, and seeking professional consultation. The risk of relying on any information in this guide is borne solely by the reader.
Strategic Sourcing Conclusion and Outlook for bucket conveyor
What Are the Key Takeaways for Strategic Sourcing of Bucket Conveyors?
In today’s competitive landscape, strategic sourcing of bucket conveyors is essential for optimizing operational efficiency and ensuring the longevity of material handling systems. Key considerations include selecting equipment that offers durable construction, minimal maintenance, and adaptability to specific industry needs. The modular design of modern bucket conveyors allows for customization, making them suitable for diverse applications, from food processing to heavy-duty industrial use.
How Can International Buyers Benefit from Strategic Sourcing?
For international B2B buyers, particularly in Africa, South America, the Middle East, and Europe, investing in high-quality bucket conveyors can significantly enhance productivity. Leveraging suppliers that provide robust solutions with advanced features—such as gentle handling, multiple inlets and outlets, and compliant materials—can lead to reduced operational costs and improved product safety.
What’s Next for International B2B Buyers?
As the market evolves, staying informed about technological advancements and supplier capabilities is crucial. Engaging with manufacturers who prioritize innovation and sustainability will position your business for future success. We encourage you to explore strategic partnerships and consider the long-term benefits of investing in reliable bucket conveyor systems. Your commitment to quality sourcing today will pave the way for operational excellence tomorrow.