Control Solenoid Valve: The Ultimate Buyer’s Guide (2025)
Introduction: Navigating the Global Market for control solenoid valve
In today’s rapidly evolving industrial landscape, sourcing the right control solenoid valve can be a daunting challenge for B2B buyers, especially in regions such as Africa, South America, the Middle East, and Europe. These essential components, which regulate the flow of liquids and gases, are critical to ensuring operational efficiency and reliability across various applications. With the increasing complexity of industrial systems and the demand for automation, understanding the different types of solenoid valves, their applications, and the best practices for supplier vetting has become paramount.
This comprehensive guide delves deep into the world of control solenoid valves, covering everything from the fundamental types—such as direct-acting and pilot-driven valves—to their specific applications in sectors like waterworks, manufacturing, and HVAC systems. Additionally, it addresses crucial considerations for international buyers, including cost factors, quality assurance, and compliance with local regulations.
By equipping B2B buyers with the knowledge to make informed purchasing decisions, this guide empowers organizations to select the most suitable solenoid valves tailored to their operational needs. Whether you are a procurement officer in South Africa looking to streamline processes or a manufacturing manager in Europe seeking to enhance efficiency, understanding the nuances of control solenoid valves will enable you to navigate the global market with confidence and precision.
Understanding control solenoid valve Types and Variations
Type Name | Key Distinguishing Features | Primary B2B Applications | Brief Pros & Cons for Buyers |
---|---|---|---|
Direct-Acting Solenoid Valve | Operates directly with minimal pressure; simple design. | Water control, HVAC systems | Pros: Quick response, compact design. Cons: Limited flow capacity. |
Pilot-Operated Solenoid Valve | Uses pilot pressure to control larger flow rates; more complex. | Industrial automation, large piping systems | Pros: High flow rates, energy efficient. Cons: More complex installation. |
3-Way Solenoid Valve | Can direct flow between two outlets; versatile configuration. | Fluid mixing, diverting flow | Pros: Flexible applications, space-saving. Cons: Potential for leaks if not maintained. |
Proportional Solenoid Valve | Adjusts flow based on input signal; supports precise control. | Process control, robotics | Pros: High precision, adaptable to various systems. Cons: Higher cost and complexity. |
Pneumatic Solenoid Valve | Controls air or gas flow; essential for pneumatic systems. | Manufacturing, packaging machinery | Pros: Fast operation, reliable in harsh conditions. Cons: Limited to pneumatic applications. |
What Are the Key Characteristics of Direct-Acting Solenoid Valves?
Direct-acting solenoid valves are designed for straightforward operation, functioning with minimal pressure to open and close. Their simple design allows for quick installation and maintenance, making them suitable for applications such as water control and HVAC systems. When purchasing, buyers should consider the valve’s size and the specific pressure requirements of their system, as these valves typically have a limited flow capacity.
How Do Pilot-Operated Solenoid Valves Work?
Pilot-operated solenoid valves utilize pilot pressure to manage larger flow rates, making them ideal for industrial automation and large piping systems. These valves are more complex than direct-acting types but offer significant advantages in terms of flow capacity and energy efficiency. Buyers should evaluate the installation requirements and the compatibility of pilot pressure with their existing systems, as well as the potential for higher upfront costs.
What Advantages Do 3-Way Solenoid Valves Offer?
3-way solenoid valves are versatile components that can switch flow between two outlet ports, facilitating fluid mixing and directing flow in various applications. Their flexibility allows for space-saving solutions in design. However, buyers need to be aware of the maintenance requirements, as improper upkeep can lead to leaks, which could affect operational efficiency.
Why Choose Proportional Solenoid Valves for Precision Control?
Proportional solenoid valves are engineered to adjust fluid flow based on an input signal, allowing for precise control in applications like process control and robotics. Their adaptability makes them suitable for various systems, though they come with a higher cost and complexity. Buyers should assess the integration capabilities with their control systems and the potential return on investment from improved accuracy.
In Which Situations Are Pneumatic Solenoid Valves Essential?
Pneumatic solenoid valves are crucial for controlling the flow of air or gas, particularly in manufacturing and packaging machinery. They are known for their fast operation and reliability, even in harsh conditions. When considering these valves, buyers should evaluate their specific pneumatic requirements, including pressure ratings and compatibility with existing equipment, to ensure optimal performance.
Key Industrial Applications of control solenoid valve
Industry/Sector | Specific Application of Control Solenoid Valve | Value/Benefit for the Business | Key Sourcing Considerations for this Application |
---|---|---|---|
Water Treatment | Automated control of water flow in purification systems | Ensures consistent water quality and compliance with regulations | Material compatibility with harsh chemicals, reliability, and maintenance requirements |
Agriculture | Irrigation control in precision farming | Optimizes water usage and boosts crop yield | Size and pressure specifications, environmental durability, and energy efficiency |
HVAC Systems | Temperature regulation in heating and cooling systems | Improves energy efficiency and system reliability | Voltage compatibility, responsiveness, and integration with smart controls |
Oil & Gas | Flow control in pipeline systems | Enhances safety and operational efficiency | Resistance to high pressure and corrosive environments, certifications |
Manufacturing | Automation in assembly lines for fluid transfer | Increases production speed and reduces manual labor costs | Compatibility with existing systems, response time, and ease of integration |
How Are Control Solenoid Valves Used in Water Treatment Systems?
In water treatment facilities, control solenoid valves are essential for automating the flow of water through purification systems. These valves regulate the flow rate, ensuring that water quality meets safety standards and environmental regulations. For international B2B buyers, particularly those in regions like Africa and South America, selecting valves that can withstand harsh chemicals and provide reliable performance is crucial. Additionally, maintenance requirements should be considered to minimize downtime and operational costs.
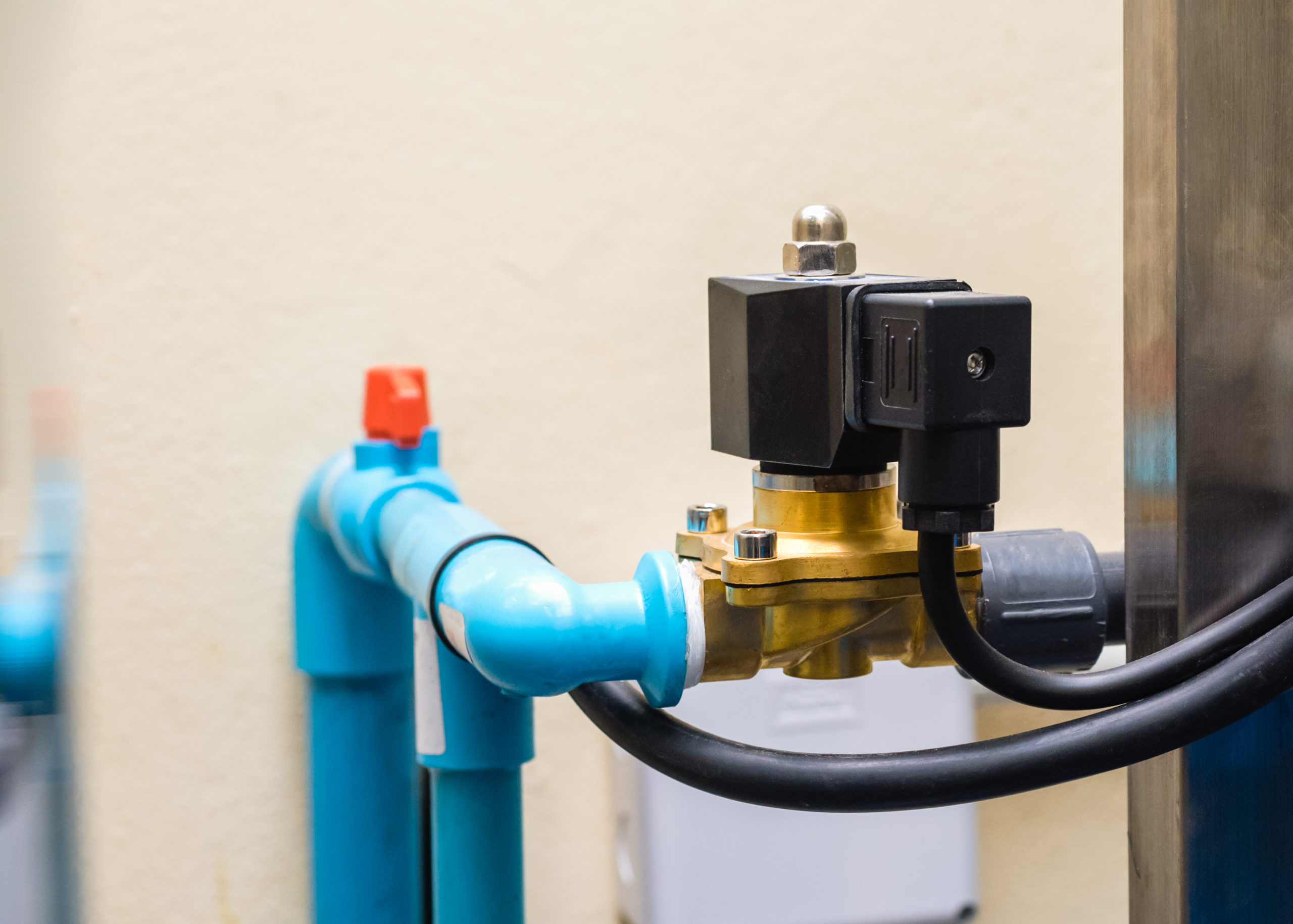
A stock image related to control solenoid valve.
What Role Do Control Solenoid Valves Play in Agriculture?
In the agricultural sector, control solenoid valves are used in irrigation systems to automate water delivery to crops. This application is particularly beneficial in precision farming, where optimizing water usage can significantly enhance crop yields. Buyers from the Middle East, where water scarcity is a concern, should focus on valves that offer durability against environmental conditions and energy-efficient operation. Understanding the specific size and pressure requirements for different irrigation systems is also critical for effective sourcing.
How Are Control Solenoid Valves Integrated into HVAC Systems?
Control solenoid valves are integral to HVAC systems, allowing for precise temperature regulation in both heating and cooling applications. By controlling the flow of refrigerants or water, these valves help improve energy efficiency and system reliability. European buyers, who often prioritize energy-efficient technologies, should consider voltage compatibility and the responsiveness of the valves to ensure seamless integration with existing systems. Additionally, the ability to interface with smart control systems can enhance operational efficiency.
What Is the Importance of Control Solenoid Valves in Oil & Gas Operations?
In the oil and gas industry, control solenoid valves are vital for managing flow in pipeline systems. They enhance safety by providing precise control over the flow of potentially hazardous materials, thus reducing the risk of leaks and spills. Buyers in this sector must prioritize valves that can withstand high pressures and corrosive substances. Certifications and compliance with industry standards are also essential considerations for ensuring safety and reliability in operations.
How Do Control Solenoid Valves Improve Manufacturing Processes?
Control solenoid valves are employed in manufacturing for automating fluid transfer in assembly lines. This automation increases production speed and reduces the need for manual labor, resulting in cost savings. For B2B buyers in various regions, including South Africa and Europe, compatibility with existing systems and quick response times are key factors to consider. Furthermore, ease of integration with other automation technologies can significantly enhance operational efficiency.
3 Common User Pain Points for ‘control solenoid valve’ & Their Solutions
Scenario 1: Difficulty in Sourcing Reliable Control Solenoid Valves
The Problem:
International B2B buyers often struggle to find reliable suppliers for control solenoid valves, especially in regions such as Africa and South America. This challenge can stem from a lack of local manufacturers, leading to long lead times and increased shipping costs. Furthermore, varying quality standards across different suppliers can result in inconsistencies in product performance. Buyers may also encounter language barriers and different regulatory requirements that complicate the procurement process.
The Solution:
To effectively source control solenoid valves, buyers should first conduct thorough research on potential suppliers. Look for manufacturers with a proven track record in the industry, positive customer reviews, and certifications that meet international standards. Joining B2B platforms that specialize in industrial products can facilitate connections with reputable suppliers. It’s also advisable to request samples before placing bulk orders to assess the quality firsthand. Establishing direct communication with suppliers can help clarify specifications and compliance with local regulations. Lastly, consider forming partnerships with local distributors who understand the regional market dynamics and can provide support in navigating the procurement process.
Scenario 2: Incompatibility with Existing Systems
The Problem:
Many businesses face the challenge of integrating new control solenoid valves into their existing systems. This is particularly prevalent in industries like manufacturing and oil & gas, where outdated equipment may not be compatible with modern solenoid technologies. The incompatibility can lead to increased downtime, costly modifications, and potential safety hazards if not addressed properly.
The Solution:
To prevent compatibility issues, buyers should perform a comprehensive assessment of their current systems before purchasing control solenoid valves. Engage with engineering teams to understand the specifications and operational requirements of existing equipment. When selecting new valves, opt for those that offer versatile compatibility features, such as adjustable pressure settings or multiple voltage options. Additionally, suppliers that provide technical support and installation services can be invaluable. Consider investing in modular valve systems that allow for easier upgrades and replacements, minimizing disruption to operations. It may also be beneficial to consult with system integrators who specialize in automation and can provide insights on the best solutions for seamless integration.
Scenario 3: Performance Reliability Under Harsh Conditions
The Problem:
Control solenoid valves are often subjected to challenging environments, such as extreme temperatures, corrosive substances, or high-pressure systems. Buyers in industries like agriculture and chemical processing frequently report issues with valve failures that stem from inadequate performance in these conditions. Such failures can lead to operational inefficiencies, increased maintenance costs, and even safety risks.
The Solution:
To ensure optimal performance under harsh conditions, B2B buyers should prioritize the selection of control solenoid valves designed specifically for such environments. Look for valves made from durable materials, like stainless steel or high-grade plastics, that resist corrosion and wear. It’s crucial to verify the valve’s specifications, including its pressure ratings and temperature tolerances, to ensure they meet the operational demands of your application. Additionally, implementing regular maintenance schedules can prevent unexpected failures. Buyers should also consider investing in smart solenoid valves equipped with monitoring technology that can provide real-time data on performance metrics, allowing for proactive adjustments before issues arise. Working closely with suppliers to understand the best practices for installation and operation in specific conditions can further enhance reliability and longevity.
Strategic Material Selection Guide for control solenoid valve
When selecting control solenoid valves, the choice of material is crucial for ensuring optimal performance and longevity in various applications. Here, we analyze four common materials used in the manufacturing of control solenoid valves, focusing on their properties, advantages, disadvantages, and implications for international B2B buyers.
What Are the Key Properties of Brass for Control Solenoid Valves?
Brass is an alloy primarily composed of copper and zinc, known for its excellent machinability and corrosion resistance. It typically operates effectively at temperatures up to 180°C (356°F) and can handle moderate pressure levels. Brass is particularly compatible with water, air, and low-pressure gas applications.
Pros:
– Brass is cost-effective and widely available, making it an attractive option for many manufacturers.
– It has good thermal conductivity, which helps in applications where heat dissipation is necessary.
Cons:
– While resistant to corrosion, brass can be susceptible to dezincification in certain environments, which may lead to premature failure.
– It may not be suitable for aggressive chemical environments.
Impact on Application:
Brass solenoid valves are commonly used in plumbing and HVAC systems. Buyers should ensure compatibility with the specific media to avoid corrosion issues.
How Does Stainless Steel Perform in Control Solenoid Valve Applications?
Stainless steel is renowned for its strength, durability, and excellent corrosion resistance, particularly in harsh environments. It can withstand high temperatures (up to 600°C or 1112°F) and pressures, making it ideal for demanding applications involving steam, chemicals, or corrosive fluids.
Pros:
– Stainless steel valves have a long service life due to their resistance to rust and corrosion.
– They are highly durable and can handle extreme conditions, making them suitable for industrial applications.
Cons:
– The cost of stainless steel is significantly higher than brass, which can impact overall project budgets.
– Manufacturing processes can be more complex, leading to longer lead times.
Impact on Application:
For international buyers, especially in industries like oil and gas or food processing, stainless steel valves are often a requirement due to stringent hygiene and safety standards.
What Advantages Do Plastic Materials Offer for Control Solenoid Valves?
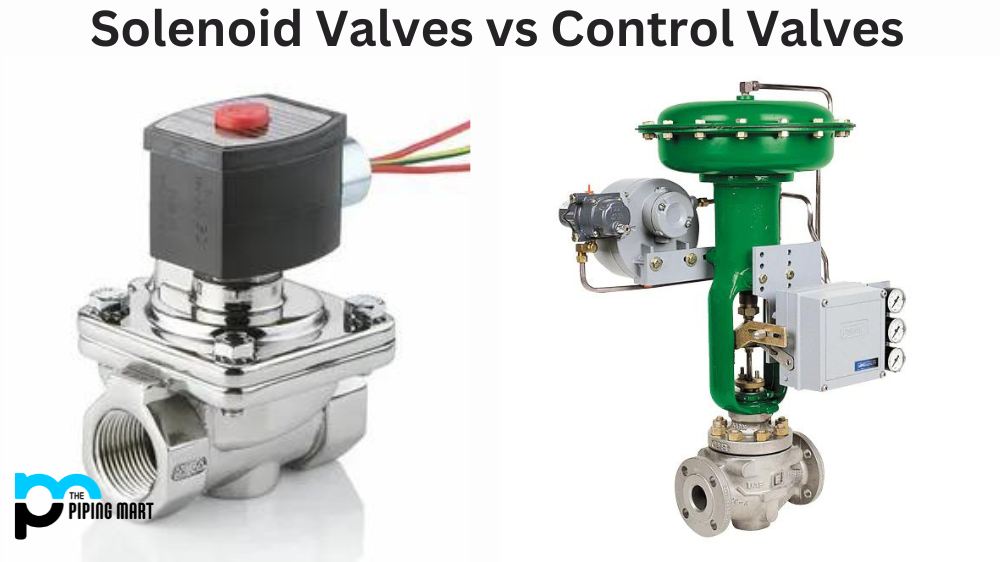
A stock image related to control solenoid valve.
Plastic solenoid valves, typically made from materials like PVC or polypropylene, are lightweight and resistant to corrosion. They are suitable for a range of temperatures, generally up to 60°C (140°F), and are often used in applications involving water and certain chemicals.
Pros:
– Plastic valves are generally more affordable and lighter than metal options, which can reduce shipping costs.
– They provide excellent chemical resistance, making them suitable for various industrial applications.
Cons:
– Plastic may not withstand high temperatures or pressures as effectively as metal, limiting their use in certain applications.
– They can be less durable than metal options, leading to potential wear and tear over time.
Impact on Application:
Plastic solenoid valves are popular in agricultural and water treatment applications. Buyers should verify chemical compatibility to ensure performance longevity.
How Do Aluminum Solenoid Valves Compare in Terms of Performance?
Aluminum is a lightweight metal that offers a good balance of strength and corrosion resistance, particularly when anodized. It can handle moderate temperatures (up to 150°C or 302°F) and pressures, making it versatile for various applications.
Pros:
– Aluminum valves are lighter than stainless steel, making them easier to handle and install.
– They provide good corrosion resistance, particularly in non-aggressive environments.
Cons:
– Aluminum can be more susceptible to corrosion in harsh environments compared to stainless steel.
– The cost is generally higher than plastic but lower than stainless steel.
Impact on Application:
Aluminum solenoid valves are often used in pneumatic and low-pressure applications. Buyers should consider environmental factors that may affect the longevity of aluminum components.
Summary Table of Material Selection for Control Solenoid Valves
Material | Typical Use Case for Control Solenoid Valve | Key Advantage | Key Disadvantage/Limitation | Relative Cost (Low/Med/High) |
---|---|---|---|---|
Brass | Plumbing, HVAC systems | Cost-effective and widely available | Susceptible to dezincification | Low |
Stainless Steel | Oil and gas, food processing | Excellent corrosion resistance | Higher cost and complex manufacturing | High |
Plastic | Agricultural, water treatment | Lightweight and chemically resistant | Limited temperature and pressure tolerance | Low |
Aluminum | Pneumatic systems, low-pressure applications | Lightweight and good corrosion resistance | Susceptible to corrosion in harsh environments | Medium |
This material selection guide provides international B2B buyers with essential insights into the properties and suitability of various materials for control solenoid valves, aiding in informed purchasing decisions tailored to specific applications and environmental conditions.
In-depth Look: Manufacturing Processes and Quality Assurance for control solenoid valve
What Are the Key Stages in the Manufacturing Process of Control Solenoid Valves?
The manufacturing process of control solenoid valves is intricate and involves several critical stages. Each stage is essential for ensuring the final product meets the required performance specifications and quality standards. Below are the main stages involved in the manufacturing process:
Material Preparation
The first step in manufacturing control solenoid valves involves sourcing and preparing high-quality materials. Common materials used include stainless steel, brass, and plastic, which are selected based on the valve’s intended application and environmental conditions. The materials undergo rigorous testing to verify their mechanical properties and chemical resistance.
Forming Techniques
Once materials are prepared, they undergo various forming techniques, such as machining, casting, and stamping. Machining is often employed for precision components, ensuring tight tolerances are maintained. Casting may be utilized for more complex shapes, while stamping is effective for producing flat components. These techniques are crucial for creating the solenoid valve body, electromagnetic components, and other integral parts.
Assembly of Components
The assembly stage is where all individual components come together. This includes installing the solenoid coil, plunger, and valve body. The assembly process often employs automated machinery to enhance precision and efficiency. Manual assembly may also be necessary for components that require intricate handling. Ensuring proper alignment and integration of the components is vital for optimal valve functionality.
Finishing Processes
After assembly, finishing processes such as surface treatment, coating, and quality inspection take place. Surface treatments improve corrosion resistance, while coatings can enhance the valve’s durability and performance under various conditions. Final inspections are conducted to ensure that the valves meet design specifications and regulatory requirements.
How Is Quality Assurance Implemented in Control Solenoid Valve Manufacturing?
Quality assurance (QA) is integral to the manufacturing of control solenoid valves, ensuring that products meet industry standards and customer expectations. Here are the key components of a robust QA system for solenoid valves:
What International Standards Are Relevant for Control Solenoid Valves?
Manufacturers must adhere to various international standards, such as ISO 9001, which outlines quality management principles. Other relevant certifications include:
- CE Marking: Required for products sold in the European Economic Area, indicating compliance with health, safety, and environmental protection standards.
- API Standards: Particularly relevant for valves used in oil and gas applications, ensuring they meet industry-specific performance criteria.
Compliance with these standards is crucial for international B2B buyers, as it provides assurance of quality and safety.
What Are the Key Quality Control Checkpoints?
Quality control checkpoints are essential for monitoring the manufacturing process. The following checkpoints are typically implemented:
- Incoming Quality Control (IQC): This involves inspecting raw materials and components upon receipt to ensure they meet specified standards before processing.
- In-Process Quality Control (IPQC): Regular checks during the manufacturing process help identify defects early, reducing waste and rework.
- Final Quality Control (FQC): A comprehensive inspection of the finished product ensures it meets all design specifications and performance criteria.
What Common Testing Methods Are Used for Control Solenoid Valves?
Control solenoid valves undergo various testing methods to verify their performance and reliability:
- Functional Testing: Ensures the valve operates correctly under different conditions, including pressure and flow rates.
- Leak Testing: Identifies any leaks in the valve, which is critical for maintaining system integrity.
- Electrical Testing: Checks the electrical components for correct functionality, ensuring proper solenoid activation.
These tests provide B2B buyers with confidence in the product’s reliability and performance.
How Can B2B Buyers Verify Supplier Quality Control Processes?
For international B2B buyers, verifying a supplier’s quality control processes is essential for ensuring product quality. Here are actionable steps to conduct due diligence:
What Are the Best Practices for Conducting Supplier Audits?
Conducting supplier audits can provide insights into a manufacturer’s quality assurance practices. Key areas to focus on include:
- Production Processes: Review how the manufacturer manages their processes, including material sourcing, production techniques, and assembly methods.
- Quality Management Systems: Assess the implementation of international standards, such as ISO certifications, to gauge the effectiveness of their quality management systems.
What Documentation Should Be Requested?
Buyers should request documentation that demonstrates a supplier’s commitment to quality control, including:
- Quality Assurance Manuals: Outlining their QA processes and procedures.
- Certificates of Compliance: Validating adherence to international standards.
- Test Reports: Providing results from functional, leak, and electrical testing.
How Can Third-Party Inspections Enhance Quality Assurance?
Engaging third-party inspection services can further enhance the verification process. These independent entities can conduct audits and testing, providing an unbiased assessment of the supplier’s quality control processes. This adds an additional layer of assurance for B2B buyers, particularly those from regions such as Africa, South America, the Middle East, and Europe, where local regulations and standards may vary.
What Are the Quality Control Nuances for International B2B Buyers?
Navigating the quality control landscape can be complex for international buyers. Understanding specific nuances can aid in making informed purchasing decisions:
- Regulatory Compliance: Different regions have varying regulations that may affect product compliance. Buyers should be aware of the specific requirements in their target markets.
- Cultural and Operational Differences: Understanding the cultural context of suppliers can aid in fostering better communication and expectations regarding quality standards.
- Supply Chain Logistics: Buyers should consider the implications of shipping and logistics on product quality, particularly in terms of handling and transportation conditions.
By focusing on these aspects, international B2B buyers can better navigate the complexities of sourcing control solenoid valves, ensuring they receive high-quality products that meet their operational needs.
Practical Sourcing Guide: A Step-by-Step Checklist for ‘control solenoid valve’
In the fast-paced world of industrial automation, sourcing the right control solenoid valves is crucial for operational efficiency and system reliability. This guide provides a practical checklist for international B2B buyers, especially from Africa, South America, the Middle East, and Europe, to ensure informed purchasing decisions.
Step 1: Define Your Technical Specifications
Start by clearly outlining the technical requirements for the control solenoid valves you need. Consider factors such as the type of fluid (liquid or gas), pressure levels, and temperature ranges they will operate under.
– Key Considerations: Identify whether you require direct-acting or pilot-operated valves, and specify connection types (e.g., NPT or flanged) based on your existing systems.
Step 2: Research Different Types of Control Solenoid Valves
Familiarize yourself with the various types of solenoid valves available on the market, including three-way, proportional, and pneumatic solenoid valves. Understanding these categories will help you select the valve that best suits your application needs.
– Examples of Use: For instance, proportional solenoid valves are ideal for applications requiring precise flow control, while pneumatic solenoid valves are essential for air or gas control.
Step 3: Evaluate Potential Suppliers
Conduct thorough research on potential suppliers before making a commitment. Look for manufacturers with a solid reputation in the industry and request company profiles, case studies, and references from buyers in similar sectors.
– Supplier Assessment: Ensure that suppliers have experience with your specific requirements and can provide evidence of past successful installations.
Step 4: Verify Supplier Certifications and Compliance
Confirm that the suppliers adhere to international quality standards and certifications relevant to your region, such as ISO 9001 or CE marking. Compliance with these standards indicates a commitment to quality and safety.
– Importance of Compliance: This step is essential to mitigate risks associated with substandard products that could lead to operational failures or legal issues.
Step 5: Request Samples and Technical Documentation
Before finalizing your order, ask for samples of the solenoid valves and any relevant technical documentation, including installation guides and operational manuals. This will allow you to evaluate the product quality and compatibility with your systems.
– Testing and Validation: Use the samples to conduct tests within your operational environment to ensure they meet your specifications.
Step 6: Negotiate Pricing and Terms
Once you have selected a supplier, engage in negotiations to secure favorable pricing and terms. Consider factors like bulk purchasing discounts, warranty periods, and after-sales support.
– Long-term Relationships: Establishing a good relationship with suppliers can lead to better deals and support in future procurement.
Step 7: Plan for Logistics and Delivery
Finally, coordinate logistics to ensure timely delivery of the solenoid valves to your operational site. Consider factors like shipping methods, customs regulations, and lead times.
– Logistical Considerations: Proper planning can prevent delays that could impact your operations and allow for seamless integration of the new valves into your systems.
By following these steps, international B2B buyers can effectively navigate the procurement process for control solenoid valves, ensuring they select the right products that meet their technical and operational needs.
Comprehensive Cost and Pricing Analysis for control solenoid valve Sourcing
What Are the Key Cost Components in Control Solenoid Valve Sourcing?
When sourcing control solenoid valves, it is crucial to understand the various cost components that contribute to the final pricing. These components typically include materials, labor, manufacturing overhead, tooling, quality control (QC), logistics, and the supplier’s margin.
-
Materials: The primary materials used in control solenoid valves include brass, stainless steel, and various plastics. The choice of materials affects durability and performance, which in turn influences pricing. For instance, stainless steel valves generally cost more due to their corrosion resistance, making them ideal for harsh environments.
-
Labor: Labor costs can vary significantly based on the manufacturing location. Countries with lower labor costs might offer more competitive pricing, but it is essential to consider the trade-off with quality and craftsmanship.
-
Manufacturing Overhead: This includes costs related to utilities, facility maintenance, and administrative expenses. Efficient manufacturing processes can help minimize these costs, leading to better pricing for buyers.
-
Tooling: Initial tooling costs can be significant, especially for customized or specialized valves. These costs are usually amortized over the production volume, impacting pricing for smaller orders.
-
Quality Control (QC): Ensuring that valves meet industry standards requires investment in QC processes. Certifications such as ISO or API compliance can add to the cost but are essential for reliability.
-
Logistics: Shipping and handling costs, especially for international transactions, can significantly affect the overall price. Factors like distance, shipping method, and customs duties play a crucial role.
-
Margin: Suppliers typically mark up their prices to cover operational costs and profit. The margin can vary based on the supplier’s reputation, market conditions, and demand.
How Do Price Influencers Affect Control Solenoid Valve Costs?
Several key factors can influence the pricing of control solenoid valves, making it essential for buyers to understand these nuances.
-
Volume/MOQ: Purchasing in bulk often leads to cost savings. Suppliers may offer lower prices for larger orders due to reduced per-unit manufacturing and logistics costs. Understanding the minimum order quantities (MOQs) is essential for optimizing procurement.
-
Specifications and Customization: Custom valves tailored to specific applications generally incur higher costs due to additional design and manufacturing requirements. It is vital to balance the need for customization with budget constraints.
-
Materials: As previously mentioned, the type of material impacts cost. Buyers should evaluate whether the benefits of higher-quality materials justify the price difference.
-
Quality and Certifications: Valves that meet specific industry standards and certifications typically command higher prices. However, they may also offer better reliability and lower maintenance costs in the long run.
-
Supplier Factors: Established suppliers with a good reputation may charge a premium for their products. However, this can be justified by their reliability and customer service.
-
Incoterms: Understanding international shipping terms can help buyers manage additional costs. Incoterms define the responsibilities of buyers and sellers regarding shipping, insurance, and tariffs, which can significantly affect total costs.
What Tips Can Help International B2B Buyers Optimize Costs?
International B2B buyers, especially from regions like Africa, South America, the Middle East, and Europe, can employ several strategies to optimize costs when sourcing control solenoid valves.
-
Negotiate Effectively: Leverage the competitive landscape to negotiate better prices. Building relationships with suppliers can lead to favorable terms and discounts.
-
Focus on Total Cost of Ownership (TCO): While initial pricing is important, consider the TCO, which includes maintenance, operational costs, and potential downtime. Investing in high-quality valves may result in lower TCO.
-
Stay Informed About Pricing Trends: Keep abreast of market trends and fluctuations in material costs. This knowledge can provide leverage during negotiations and help in budgeting.
-
Understand Local Market Conditions: Buyers should be aware of economic conditions and currency fluctuations in their regions, as these factors can impact pricing and availability.
-
Consider Long-Term Partnerships: Establishing long-term relationships with suppliers can lead to better pricing and service agreements, improving overall procurement efficiency.
Disclaimer on Indicative Prices
Prices for control solenoid valves can vary widely based on the aforementioned factors. The indicative prices observed in the market may not reflect current rates or specific supplier offers. It is advisable for buyers to conduct thorough research and obtain quotes from multiple suppliers to ensure competitive pricing.
Alternatives Analysis: Comparing control solenoid valve With Other Solutions
Understanding Alternatives to Control Solenoid Valves
In the realm of fluid control systems, control solenoid valves are widely recognized for their efficiency and reliability. However, international B2B buyers should consider alternative solutions that may better suit specific operational needs, particularly in diverse markets such as Africa, South America, the Middle East, and Europe. This section provides a comparative analysis of control solenoid valves against other viable options, focusing on performance, cost, ease of implementation, maintenance, and best use cases.
Comparison Table of Control Solenoid Valve vs. Alternatives
Comparison Aspect | Control Solenoid Valve | Pneumatic Actuators | Manual Valves |
---|---|---|---|
Performance | High precision and rapid response | Good for high force applications | Moderate performance; operator-dependent |
Cost | Moderate initial cost | Higher initial investment | Low initial cost, but labor-intensive |
Ease of Implementation | Relatively easy to install with electrical connections | Requires pneumatic infrastructure | Simple to install, but requires manual operation |
Maintenance | Low maintenance, but needs electrical checks | Moderate; pneumatic systems need periodic checks | Low maintenance, but requires operator training |
Best Use Case | Automated systems needing precision | Heavy machinery and equipment | Simple on/off applications |
Detailed Breakdown of Alternatives
Pneumatic Actuators: Are They Worth the Investment?
Pneumatic actuators utilize compressed air to create motion, making them a strong alternative to control solenoid valves, especially in applications requiring high force. They excel in environments where heavy machinery is involved, offering robust performance. However, the initial setup cost can be significant, as they require a complete pneumatic system, including compressors and air lines. Maintenance can also be moderate, as pneumatic systems need regular checks to ensure optimal performance. For industries in Africa or South America where heavy equipment is prevalent, pneumatic actuators may be a suitable choice.
Manual Valves: When Simplicity is Key
Manual valves are straightforward devices that require human intervention to operate. They are cost-effective and easy to install, making them attractive for small-scale operations or applications where automation is unnecessary. However, the performance is heavily reliant on the operator’s skill and can lead to inefficiencies in larger systems. While they require minimal maintenance, the need for operator training can be a drawback. In regions with limited access to technology or where labor is abundant, manual valves may serve as a practical solution.
Conclusion: How to Choose the Right Solution for Your Needs
Selecting the appropriate fluid control solution involves careful consideration of various factors, including operational requirements, budget constraints, and maintenance capabilities. Control solenoid valves offer high precision and automation, making them ideal for complex systems. Pneumatic actuators may be more suitable for heavy-duty applications, while manual valves provide a low-cost, simple alternative for less critical processes. By thoroughly evaluating these options, B2B buyers can make informed decisions that align with their specific operational contexts, ensuring efficiency and cost-effectiveness in their fluid control systems.
Essential Technical Properties and Trade Terminology for control solenoid valve
What Are the Essential Technical Properties of Control Solenoid Valves?
When selecting control solenoid valves, it is crucial to understand their technical properties, as these specifications can significantly impact performance, reliability, and suitability for specific applications. Here are some essential properties to consider:
1. Material Grade
The material of the solenoid valve body can vary significantly, with common materials including brass, stainless steel, and plastic. Each material offers unique advantages; for instance, stainless steel is highly resistant to corrosion, making it suitable for harsh environments and aggressive fluids. In contrast, brass provides excellent durability and thermal conductivity. Understanding the material grade helps buyers select valves that align with their operational needs, especially in industries such as oil and gas, water treatment, and food processing.
2. Operating Pressure
Operating pressure defines the maximum pressure at which the valve can function effectively without failure. This specification is critical because it determines the valve’s compatibility with the fluid system it will be integrated into. Buyers must ensure that the operating pressure of the solenoid valve meets or exceeds the system’s pressure requirements to prevent leaks or catastrophic failures.
3. Voltage Rating
Control solenoid valves are available in various voltage ratings, such as 12V, 24V, and 110V AC. The voltage rating affects the valve’s power consumption and operational efficiency. Selecting the appropriate voltage is essential for ensuring compatibility with existing electrical systems, especially in automated setups that rely on precise control mechanisms.
4. Flow Rate
The flow rate indicates how much fluid can pass through the valve within a specific time frame, typically measured in liters per minute (LPM) or gallons per minute (GPM). This specification is vital for ensuring that the valve can handle the required flow for the application, whether it’s for irrigation, industrial automation, or HVAC systems. A mismatch in flow rate can lead to inefficiencies or operational disruptions.
5. Response Time
Response time refers to how quickly the solenoid valve can open or close after receiving an electric signal. Fast response times are essential in applications requiring immediate flow control, such as in chemical processing or emergency shut-off systems. Buyers should consider their operational needs and choose valves that offer suitable response times for their applications.
6. IP Rating (Ingress Protection)
The IP rating indicates the level of protection a valve has against dust and water ingress. A higher IP rating (e.g., IP67) means better protection in harsh environments. This is particularly important for applications exposed to moisture or dust, such as outdoor installations or in factories. Selecting a valve with an appropriate IP rating ensures longevity and reliability.
What Are Common Trade Terms Related to Control Solenoid Valves?
Understanding industry jargon is essential for effective communication and negotiations in the B2B marketplace. Here are some common terms related to control solenoid valves:
1. OEM (Original Equipment Manufacturer)
An OEM refers to a company that produces parts or equipment that may be marketed by another manufacturer. In the context of solenoid valves, it often denotes manufacturers who create valves for other brands, which can affect pricing and availability.
2. MOQ (Minimum Order Quantity)
MOQ is the minimum quantity of products that a supplier is willing to sell. For international buyers, understanding the MOQ is crucial for budgeting and inventory management. Suppliers may offer discounts for larger orders, making it beneficial to consolidate purchases.
3. RFQ (Request for Quotation)
An RFQ is a document that buyers send to suppliers to request pricing and availability for specific products. This process helps buyers compare costs and terms across different suppliers, facilitating informed purchasing decisions.
4. Incoterms (International Commercial Terms)
Incoterms are international trade terms that define the responsibilities of buyers and sellers regarding the delivery of goods. Familiarity with these terms helps B2B buyers understand shipping costs, risks, and responsibilities, which is especially important for international transactions.
5. Lead Time
Lead time refers to the amount of time it takes for a supplier to deliver goods after an order is placed. Understanding lead times is essential for planning and ensuring that production schedules are met, particularly in industries with tight timelines.
By grasping these technical properties and trade terminologies, B2B buyers can make informed decisions when sourcing control solenoid valves, ensuring compatibility and efficiency within their operations.
Navigating Market Dynamics and Sourcing Trends in the control solenoid valve Sector
What Are the Key Market Dynamics and Trends in the Control Solenoid Valve Sector?
The control solenoid valve sector is currently witnessing robust growth driven by increasing automation across industries such as manufacturing, water management, and HVAC systems. Global drivers include the rise in smart manufacturing practices and the integration of the Internet of Things (IoT) in control systems. These technologies enhance operational efficiency, enabling real-time monitoring and control, which is particularly beneficial for B2B buyers looking for reliable and efficient solutions.
Emerging trends in sourcing include a shift towards smart solenoid valves that can be controlled remotely via applications or integrated into SCADA (Supervisory Control and Data Acquisition) systems. These innovations not only streamline operations but also reduce the need for manual oversight, which is crucial for industries in Africa and South America, where labor costs can be significant. Additionally, buyers are increasingly seeking suppliers who offer customized solutions tailored to specific applications, such as pneumatic or proportional control, enhancing operational efficiency in diverse settings from agriculture to industrial manufacturing.
Moreover, international buyers from Europe and the Middle East are prioritizing suppliers that can demonstrate compliance with regional standards and certifications. The push for automation and the need for energy-efficient solutions are central to purchasing decisions, making it essential for suppliers to adapt their offerings in response to these market dynamics.
How Is Sustainability Shaping the Sourcing of Control Solenoid Valves?
Sustainability is a growing concern for B2B buyers, influencing procurement strategies within the control solenoid valve sector. The environmental impact of manufacturing processes is under scrutiny, prompting companies to seek suppliers who prioritize eco-friendly practices. This includes the use of sustainable materials and energy-efficient manufacturing methods, which not only reduce the carbon footprint but also align with corporate social responsibility goals.
Ethical sourcing is becoming a critical criterion for international buyers, particularly those from Europe and the Middle East, where regulatory pressures are intensifying. Buyers are increasingly interested in suppliers who can provide transparency in their supply chains, ensuring that materials are sourced responsibly. Certifications such as ISO 14001 for environmental management systems and the use of recyclable materials in product design are becoming essential for demonstrating commitment to sustainability.
Furthermore, the demand for “green” products is prompting manufacturers to innovate in the development of solenoid valves that minimize energy consumption and have longer life cycles. Such products not only help businesses meet sustainability targets but also offer long-term cost savings, making them attractive to B2B buyers across various industries.
What Is the Evolution of Control Solenoid Valves and Its Relevance to Today’s B2B Buyers?
The evolution of control solenoid valves has been marked by significant technological advancements that have transformed their functionality and application. Initially, solenoid valves were primarily mechanical devices, but the integration of electronic components has allowed for more sophisticated control mechanisms. This evolution has facilitated the development of smart solenoid valves, which are now capable of providing real-time data and remote control capabilities.
For B2B buyers, understanding this evolution is crucial, as it highlights the shift from basic on/off control to more complex, automated solutions that enhance operational efficiency. The ability to integrate these valves into modern automation systems is particularly relevant for industries seeking to optimize processes and reduce operational costs.
As the market continues to evolve, staying informed about technological advancements and emerging trends will empower buyers to make informed decisions that align with their business needs and sustainability goals. This historical perspective not only underscores the importance of innovation in the control solenoid valve sector but also emphasizes the necessity for suppliers to adapt to the changing demands of international B2B buyers.
Frequently Asked Questions (FAQs) for B2B Buyers of control solenoid valve
-
How do I choose the right control solenoid valve for my application?
Selecting the appropriate control solenoid valve involves understanding the specific requirements of your application, such as the type of fluid (liquid or gas), pressure, temperature, and flow rate. Consider whether you need a direct-acting or pilot-operated valve, as this can impact performance. Additionally, assess the material compatibility with the media being controlled, especially in harsh environments. Consulting with suppliers can provide tailored solutions based on your operational needs and compliance with regional standards. -
What are the key features to look for in a control solenoid valve?
When sourcing control solenoid valves, focus on key features such as response time, durability, and energy consumption. Look for valves with robust sealing materials to enhance longevity, especially in challenging environments. Additional features like manual override, built-in pressure regulation, and compatibility with control systems (e.g., SCADA) can also be advantageous. It’s beneficial to request technical specifications and performance data from suppliers to ensure the valves meet your operational requirements. -
What are the common applications of control solenoid valves in industry?
Control solenoid valves are widely used in various industries, including water treatment, HVAC systems, and automation processes. They play crucial roles in controlling fluid flow, regulating pressure, and managing temperature in applications ranging from irrigation systems to industrial machinery. Understanding the specific demands of your industry can help you identify the most suitable solenoid valve types, such as 2-way or 3-way configurations, for your operations. -
What should I consider regarding minimum order quantities (MOQ) for solenoid valves?
Minimum order quantities can vary significantly between suppliers, influenced by factors like production capacity and material availability. For international B2B buyers, it’s essential to clarify MOQs upfront to ensure they align with your procurement strategy. If your needs are lower than the MOQ, discuss the possibility of bulk purchasing or co-op buying with other businesses. This approach can help you manage costs while still meeting your operational requirements.
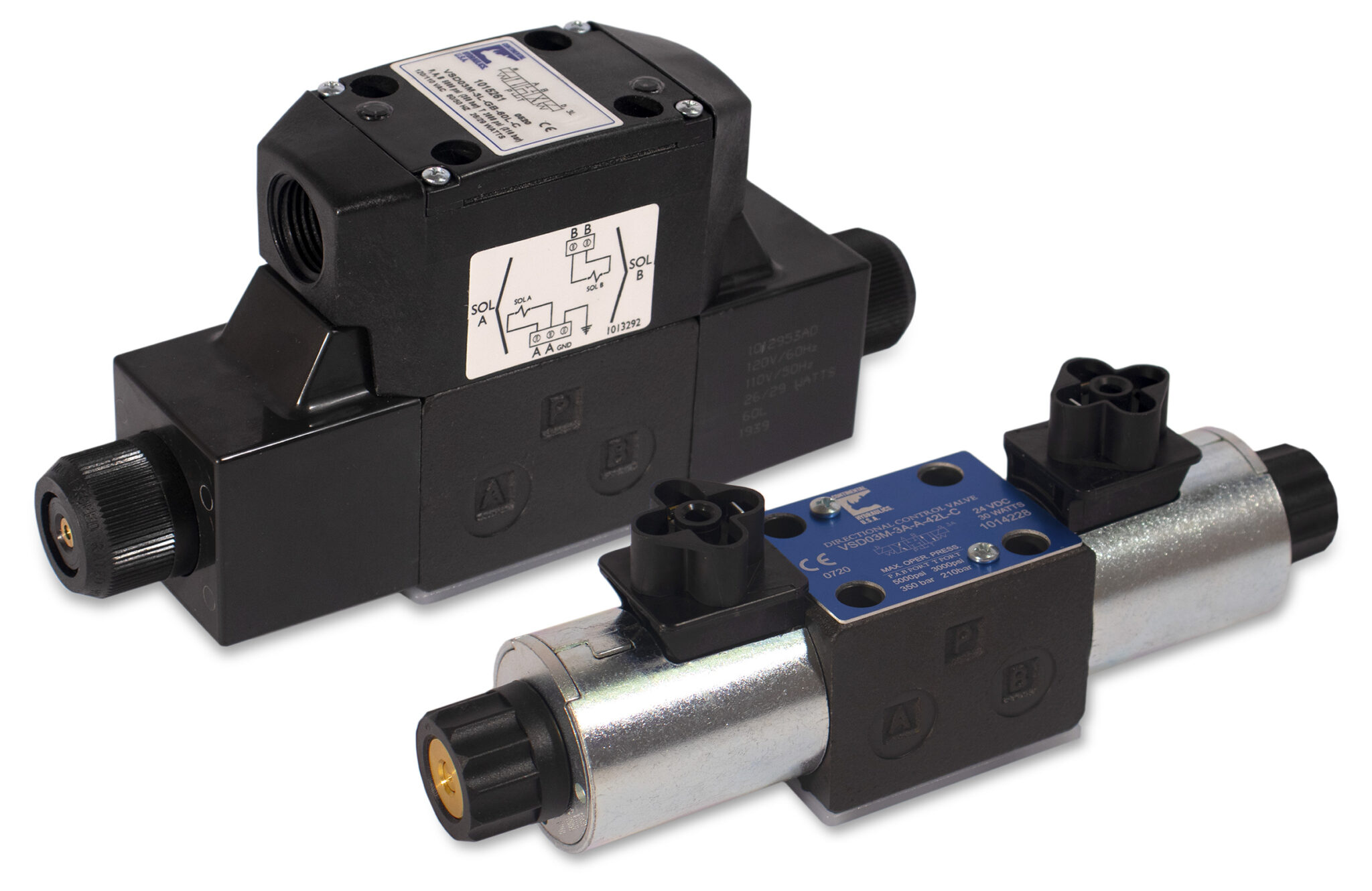
A stock image related to control solenoid valve.
-
How can I ensure the quality of control solenoid valves from suppliers?
To ensure quality, request certifications and compliance documentation from suppliers, such as ISO certifications and product testing reports. Conduct due diligence by reviewing supplier reputation and customer feedback, which can often be found on industry forums or through references. Additionally, consider ordering sample valves for preliminary testing in your application before committing to a larger order. This step helps verify performance and durability under your specific operating conditions. -
What payment terms should I negotiate when purchasing solenoid valves internationally?
When negotiating payment terms, consider factors like your cash flow, supplier reputation, and order size. Common payment methods include letters of credit, advance payments, and open account terms. Ensure that payment terms are mutually beneficial and clearly outlined in the contract to avoid misunderstandings. Additionally, inquire about any potential discounts for early payments or bulk orders, as these can enhance overall cost-effectiveness. -
What logistics considerations should I keep in mind when importing control solenoid valves?
Logistics considerations are critical for timely delivery and cost management. Evaluate shipping options based on delivery speed and cost, considering factors like freight forwarding and customs clearance processes. Be aware of local regulations regarding the import of industrial components, including any tariffs or duties that may apply. Establishing a reliable logistics partner can streamline the process and mitigate risks associated with international shipping. -
Can I customize control solenoid valves for specific operational needs?
Many manufacturers offer customization options for control solenoid valves to better suit your operational requirements. Customization may include alterations in size, material, or electrical specifications. When discussing customization, provide detailed specifications and operational conditions to suppliers. This collaborative approach can lead to more effective solutions tailored to your specific applications, enhancing performance and reliability in your processes.
Important Disclaimer & Terms of Use
⚠️ Important Disclaimer
The information provided in this guide, including content regarding manufacturers, technical specifications, and market analysis, is for informational and educational purposes only. It does not constitute professional procurement advice, financial advice, or legal advice.
While we have made every effort to ensure the accuracy and timeliness of the information, we are not responsible for any errors, omissions, or outdated information. Market conditions, company details, and technical standards are subject to change.
B2B buyers must conduct their own independent and thorough due diligence before making any purchasing decisions. This includes contacting suppliers directly, verifying certifications, requesting samples, and seeking professional consultation. The risk of relying on any information in this guide is borne solely by the reader.
Strategic Sourcing Conclusion and Outlook for control solenoid valve
In the evolving landscape of industrial automation, the strategic sourcing of control solenoid valves is crucial for enhancing operational efficiency and reliability. Buyers from Africa, South America, the Middle East, and Europe must consider the specific applications and requirements of their industries when selecting solenoid valves. Key factors such as valve type (direct-acting or pilot-controlled), material compatibility, and integration with existing systems should guide their purchasing decisions.
Moreover, the ability to leverage technology, such as SCADA systems and smart control options, can significantly improve process management and data collection, leading to informed decision-making. As industries increasingly prioritize automation and sustainability, sourcing high-quality solenoid valves that meet international standards will not only optimize performance but also ensure compliance with regulatory requirements.
Looking ahead, B2B buyers are encouraged to engage with suppliers who offer comprehensive support and expertise in solenoid valve applications. By fostering strategic partnerships and investing in advanced technologies, businesses can position themselves competitively in their respective markets. Embrace the future of fluid control solutions and take the next step in your sourcing strategy today.