Cut Costs: The Ultimate Water Jet Cutter Buying Guide (2025)
Introduction: Navigating the Global Market for water jet cutter
Navigating the complexities of sourcing a water jet cutter can be daunting for international B2B buyers, particularly in regions such as Africa, South America, the Middle East, and Europe. The challenge often lies in selecting the right equipment that meets specific operational needs while ensuring cost-effectiveness and reliability. This guide aims to demystify the process by providing a comprehensive overview of water jet cutting technology, including various types of machines, their applications across industries, and essential factors to consider when vetting suppliers.
From aerospace to automotive manufacturing, water jet cutters offer versatile solutions for cutting a wide range of materials, including metals, plastics, and composites. By understanding the unique features of different models and the nuances of their operational capabilities, buyers can make informed decisions that enhance productivity and precision in their operations.
This guide empowers B2B buyers by breaking down critical aspects such as cost analysis, maintenance requirements, and the latest advancements in water jet technology. With actionable insights tailored to the specific needs of international markets, particularly in countries like Kenya and Spain, readers will be well-equipped to navigate the global market effectively, ensuring they invest in the right water jet cutter for their business needs.
Understanding water jet cutter Types and Variations
Type Name | Key Distinguishing Features | Primary B2B Applications | Brief Pros & Cons for Buyers |
---|---|---|---|
Abrasive Waterjet | Utilizes a mixture of water and abrasive materials | Aerospace, automotive, metal fabrication | Pros: Cuts through thick materials; versatile. Cons: Higher operating costs due to abrasives. |
Pure Waterjet | Uses only high-pressure water for cutting | Soft materials, food industry, textiles | Pros: Eco-friendly; low maintenance. Cons: Limited to softer materials. |
5-Axis Waterjet | Offers multi-directional cutting capabilities | Complex geometries in aerospace and automotive | Pros: High precision; suitable for intricate designs. Cons: Higher initial investment. |
Desktop Waterjet | Compact design for smaller workspaces | Prototyping, small businesses, education | Pros: Affordable; space-efficient. Cons: Limited cutting thickness and speed. |
CNC Waterjet | Computer-controlled for automated cutting | Manufacturing, sign-making, custom parts | Pros: High repeatability; consistent quality. Cons: Requires technical expertise to operate. |
What Are the Key Characteristics of Abrasive Waterjet Cutters?
Abrasive waterjet cutters are designed to handle tough materials by mixing high-pressure water with abrasives like garnet. They excel in applications requiring precision cutting of metals and composites, making them ideal for industries like aerospace and automotive. When considering an abrasive waterjet, buyers should evaluate the cost of abrasives and maintenance, as these can add to the overall operational expenses.
How Does Pure Waterjet Cutting Differ from Other Types?
Pure waterjet cutters utilize only high-pressure water, making them suitable for softer materials like rubber, foam, and food products. This eco-friendly option produces minimal waste and requires less maintenance compared to abrasive systems. However, they are not suitable for cutting hard materials, which limits their application scope. Buyers should consider their material requirements and environmental impact when choosing this type.
Why Choose a 5-Axis Waterjet Cutter for Complex Projects?
5-axis waterjet cutters provide advanced multi-directional cutting capabilities, making them perfect for intricate designs and complex geometries often found in aerospace and automotive applications. Their precision can significantly reduce the need for secondary operations. However, the initial investment is higher, and they require skilled operators to maximize their capabilities. B2B buyers should assess their project needs versus the potential return on investment.
What Are the Advantages of Desktop Waterjet Cutters?
Desktop waterjet cutters are compact and designed for smaller workshops, making them ideal for prototyping and educational purposes. They offer an affordable entry point for businesses looking to incorporate waterjet technology without significant space requirements. However, their cutting capabilities are limited in terms of thickness and speed compared to larger models. Buyers should consider their production volume and space constraints before opting for a desktop model.
How Do CNC Waterjet Cutters Enhance Manufacturing Efficiency?
CNC waterjet cutters utilize computer numerical control for automated, precise cutting, making them a popular choice in manufacturing and sign-making. They ensure high repeatability and consistent quality across production runs. While they require technical knowledge to operate effectively, the investment can pay off through increased efficiency and reduced labor costs. Buyers should evaluate their existing technical capabilities and training resources when considering CNC options.
Key Industrial Applications of water jet cutter
Industry/Sector | Specific Application of Water Jet Cutter | Value/Benefit for the Business | Key Sourcing Considerations for this Application |
---|---|---|---|
Aerospace | Rapid prototyping of complex parts | Accelerates design iterations and reduces time-to-market | Look for high precision and repeatability in cutting capabilities. |
Automotive | Custom parts fabrication for electric vehicles | Enables quick adaptations to changing design specifications | Ensure compatibility with various materials, including composites. |
Manufacturing | Production of intricate components | Reduces waste and increases efficiency in material usage | Evaluate machine size and power based on production volume needs. |
Glass Art | Detailed glass cutting for artistic designs | Allows for intricate designs without the risk of cracking glass | Consider the machine’s ability to handle varying thicknesses of glass. |
Signmaking | Custom signage production | Facilitates quick turnaround for bespoke signage needs | Assess software compatibility for design uploads and ease of use. |
How is Water Jet Cutting Used in Aerospace and What Problems Does It Solve?
In the aerospace industry, water jet cutters are utilized for rapid prototyping of complex parts. This technology allows engineers to create functional prototypes quickly, which significantly reduces the time required for design iterations. By eliminating traditional machining processes, businesses can address issues like material waste and long lead times. For international buyers, especially in regions like Africa and South America, sourcing machines that offer high precision and repeatability is crucial to meet stringent industry standards.
What Are the Applications of Water Jet Cutters in the Automotive Sector?
Water jet cutters play a vital role in the automotive sector by enabling the fabrication of custom parts, particularly for electric vehicles. The ability to cut through various materials—including metals and composites—allows manufacturers to adapt quickly to evolving design specifications. This flexibility can lead to reduced outsourcing costs and increased in-house production capabilities. Buyers in Europe, such as those in Spain, should focus on sourcing machines that can handle diverse materials and provide efficient cutting speeds.
How Do Water Jet Cutters Benefit the Manufacturing Industry?
In manufacturing, water jet cutters are essential for producing intricate components with high accuracy. They help reduce waste and enhance efficiency by utilizing a cold-cutting process that minimizes heat-affected zones. This is particularly beneficial for industries requiring tight tolerances. For B2B buyers in the Middle East, selecting a machine that can accommodate high production volumes while maintaining quality is essential for maximizing ROI.
What Advantages Do Water Jet Cutters Provide for Glass Art?
Water jet cutting technology is invaluable in the glass art industry, where it allows artists to create detailed designs without the risk of cracking. The precision of water jet cutting enables intricate patterns to be executed flawlessly, enhancing the artistic value of the pieces. For buyers in regions with a growing art market, such as parts of Africa, it is important to consider the machine’s capability to handle varying glass thicknesses and the availability of support for artistic applications.
How is Water Jet Cutting Used in Signmaking?
In the signmaking sector, water jet cutters facilitate the production of custom signage, allowing businesses to quickly turn around unique designs. This capability is particularly valuable in competitive markets where differentiation is key. B2B buyers should prioritize sourcing machines that offer user-friendly software for design uploads, ensuring a seamless workflow from design to production. This is especially pertinent for buyers in Europe, where trends in sign design are continually evolving.
3 Common User Pain Points for ‘water jet cutter’ & Their Solutions
Scenario 1: Difficulty in Achieving Precision Cuts for Complex Designs
The Problem: Many B2B buyers, particularly those in industries like aerospace and automotive, often struggle with achieving the level of precision required for complex designs. Traditional cutting methods can introduce inaccuracies, leading to costly material wastage and delays in production. The inability to cut intricate shapes or maintain tight tolerances can severely impact the overall quality of the final product, resulting in dissatisfaction from clients or loss of contracts.
The Solution: To overcome precision challenges, buyers should consider investing in advanced water jet cutting machines that offer high repeatability and precision. For example, water jets like those from Laguna Tools provide a repeatability of +/- 0.001 inches, which is crucial for detailed projects. Buyers should also evaluate machines with features such as a 5-axis cutting head, which allows for more complex shapes and angles. Additionally, integrating CAD software into the workflow can streamline the design process, ensuring that the cutting paths are optimized before sending them to the water jet cutter. Training staff on the software and machine operation is equally essential to maximize efficiency and precision.
Scenario 2: High Operating Costs and Maintenance Challenges
The Problem: International buyers often face the challenge of high operating costs associated with water jet cutters, including energy consumption, water usage, and maintenance. In regions like Africa and South America, where budgets can be tight, these ongoing costs can deter businesses from adopting this technology. Moreover, frequent breakdowns or maintenance needs can lead to unexpected downtimes, disrupting production schedules and affecting profitability.
The Solution: To mitigate high operating costs, buyers should focus on selecting water jet cutters that are known for energy efficiency and low maintenance requirements. For instance, machines like the WAZER Pro are designed to minimize water and energy consumption while delivering high performance. Implementing a regular maintenance schedule can also help prevent costly repairs. Buyers should consider partnering with local suppliers or manufacturers who can provide timely support and spare parts, reducing the need for expensive international shipping. Additionally, investing in staff training on machine upkeep can empower operators to identify potential issues before they escalate, further minimizing downtime.
Scenario 3: Limited Knowledge About Material Compatibility and Cutting Techniques
The Problem: A common pain point for B2B buyers is the lack of knowledge regarding the compatibility of various materials with water jet cutting technology. Buyers may hesitate to invest in a water jet cutter if they are unsure about which materials can be effectively cut and how to handle them. This uncertainty can lead to inefficient purchasing decisions, where buyers invest in equipment that doesn’t meet their specific needs, resulting in wasted resources and time.
The Solution: Buyers should conduct thorough research and consult with water jet cutter manufacturers to understand the range of materials their machines can handle. For example, WAZER machines can cut metals, plastics, glass, and composites, making them versatile options for various industries. Buyers should also consider investing in training programs that cover not only the operation of the machine but also the best practices for cutting different materials. This knowledge can empower buyers to make informed decisions about material selection, thereby enhancing production capabilities. Collaborating with manufacturers to gain insights into material performance can also lead to better outcomes in terms of efficiency and quality.
Strategic Material Selection Guide for water jet cutter
What Are the Key Properties of Metals for Water Jet Cutting?
Metals are among the most commonly cut materials with water jet technology. Their key properties include high strength, durability, and resistance to deformation under pressure. Common metals used in water jet cutting include aluminum, stainless steel, and carbon steel.
- Pros: Metals offer excellent durability and can withstand harsh environments, making them suitable for various applications, including aerospace and automotive industries. They can be cut to precise dimensions, which is critical for high-performance components.
- Cons: The cost of high-quality metals can be significant, and their manufacturing complexity may require advanced cutting techniques. Additionally, certain metals may require post-cutting treatments to achieve desired finishes.
- Impact on Application: The choice of metal affects the cutting speed and the type of abrasives used. For instance, stainless steel requires more powerful pumps to achieve optimal cutting speeds compared to aluminum.
- Considerations for International Buyers: Buyers in regions like Africa and South America should be aware of local standards such as ASTM for metals. Compliance with international quality standards is crucial for ensuring product reliability and safety.
How Do Composites Perform in Water Jet Cutting?
Composites, which consist of two or more constituent materials, are increasingly popular in industries such as aerospace, automotive, and construction due to their lightweight and high-strength characteristics.
- Pros: Composites can be tailored to specific applications, offering excellent corrosion resistance and thermal stability. They also produce minimal waste during cutting, making them cost-effective.
- Cons: The complexity of composite materials can lead to challenges in cutting, such as delamination or fraying at the edges. They may also require specialized cutting heads.
- Impact on Application: The performance of composites in water jet cutting can vary based on the matrix and reinforcement materials used. Understanding the specific composite structure is essential for optimal cutting results.
- Considerations for International Buyers: Buyers should consider the availability of specific composite materials in their region and ensure compliance with local and international standards, such as ISO for composite materials.
What Are the Benefits of Cutting Glass with Water Jet Technology?
Glass is a delicate material that requires precision cutting to avoid breakage. Water jet cutting is particularly advantageous for glass due to its cold-cutting process, which prevents thermal stress.
- Pros: Water jet cutting of glass provides smooth edges and intricate designs without the risk of chipping, making it ideal for artistic and architectural applications.
- Cons: The cost of cutting glass can be higher due to the need for specialized equipment and the fragility of the material. Additionally, the cutting speed may be slower compared to metals.
- Impact on Application: The ability to cut complex shapes in glass opens up new design possibilities for artists and architects, enhancing the aesthetic appeal of their projects.
- Considerations for International Buyers: Buyers should ensure that the glass used meets local safety standards and regulations, particularly in construction applications. Compliance with standards such as EN for glass products is crucial.
Why Are Soft Materials Like Foam and Rubber Ideal for Water Jet Cutting?
Foam and rubber are soft materials that are often used in packaging, insulation, and cushioning applications. Water jet cutting is an effective method for these materials due to its ability to create intricate shapes without compression.
- Pros: Cutting foam and rubber with water jets minimizes material waste and allows for precise cuts, which is essential for custom applications. These materials are also generally more affordable than metals and composites.
- Cons: While soft materials are easier to cut, they may require more frequent blade changes and maintenance due to wear. Additionally, the cutting speed can be slower compared to harder materials.
- Impact on Application: The ability to cut various thicknesses and shapes makes water jet technology ideal for producing custom parts in industries such as automotive and packaging.
- Considerations for International Buyers: Buyers should consider the sourcing of quality foam and rubber materials, ensuring compliance with local regulations regarding material safety and environmental standards.
Summary Table of Material Properties for Water Jet Cutting
Material | Typical Use Case for Water Jet Cutter | Key Advantage | Key Disadvantage/Limitation | Relative Cost (Low/Med/High) |
---|---|---|---|---|
Metals | Aerospace, automotive components | High durability and strength | Higher cost and manufacturing complexity | High |
Composites | Aerospace, automotive, construction | Lightweight and tailored properties | Cutting challenges and specialized equipment needed | Medium |
Glass | Artistic installations, architecture | Smooth edges and intricate designs | Higher cutting cost and slower speed | Medium |
Foam/Rubber | Packaging, insulation, cushioning | Minimizes waste and precise cuts | Frequent blade changes and slower cutting speed | Low |
This strategic material selection guide provides essential insights for international B2B buyers in Africa, South America, the Middle East, and Europe, enabling informed decisions when investing in water jet cutting technology.
In-depth Look: Manufacturing Processes and Quality Assurance for water jet cutter
What Are the Main Stages of Manufacturing Water Jet Cutters?
The manufacturing process of water jet cutters involves several critical stages that ensure the final product meets stringent performance and quality standards. Understanding these stages is vital for B2B buyers to make informed purchasing decisions.
1. Material Preparation
The first step involves selecting high-quality raw materials, primarily steel, aluminum, and composite materials. Manufacturers often use advanced sourcing techniques to ensure the materials meet specific mechanical properties essential for durability and performance.
Once sourced, materials undergo a rigorous inspection process, often referred to as Incoming Quality Control (IQC). This involves verifying the specifications against international standards like ISO 9001, ensuring that the raw materials are suitable for the intended application.
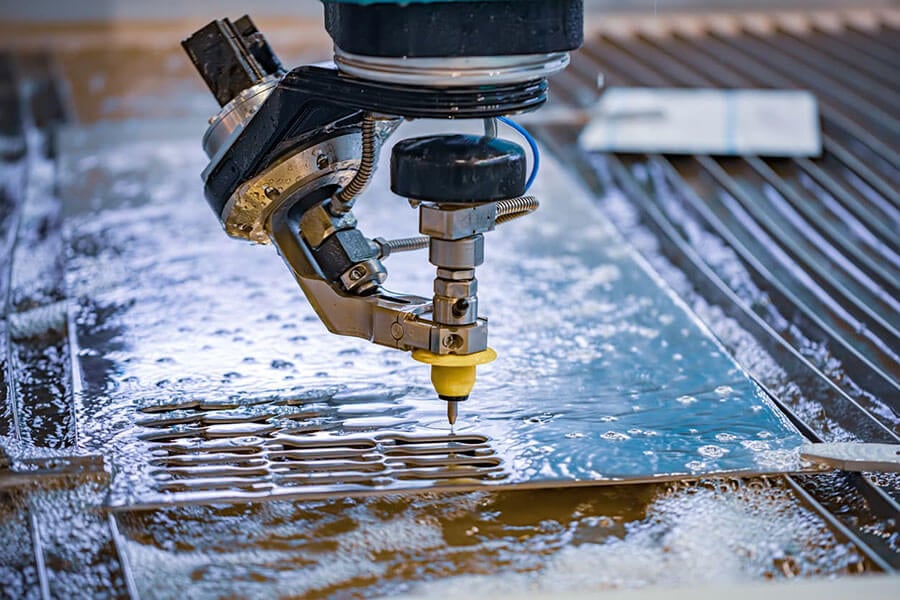
A stock image related to water jet cutter.
2. Forming Processes
After material preparation, the next step is forming, which can involve various techniques such as:
- CNC Machining: Utilized for precise shaping and cutting of components.
- Water Jet Cutting: Some parts may be pre-cut using water jet technology itself to create intricate designs before assembly.
- Laser Cutting: Employed for high precision in thin materials.
These processes are critical as they directly influence the quality of the edges and overall dimensional accuracy of the water jet cutter.
3. Assembly
Following forming, the assembly stage begins. This is where various components, such as the high-pressure pump, cutting head, and control systems, come together.
Assembly is typically done in clean environments to minimize contamination. Manufacturers implement In-Process Quality Control (IPQC) during this stage, where each assembly step is monitored for accuracy. This includes checking alignments, electrical connections, and ensuring that no parts are missing.
4. Finishing Touches
Finally, the finishing stage involves surface treatments, painting, and quality checks. Finishing not only enhances the aesthetic appeal but also protects against corrosion and wear. Common finishing techniques include:
- Powder Coating: Provides a durable finish.
- Anodizing: Often used for aluminum parts to enhance corrosion resistance.
Each finished product undergoes Final Quality Control (FQC) to ensure it meets all specifications before shipment.
How is Quality Assurance Implemented in Water Jet Cutter Manufacturing?
Quality assurance is critical in the manufacturing of water jet cutters, ensuring that products meet international standards and customer expectations.
Relevant International Standards
Manufacturers often comply with several international standards, including:
- ISO 9001: This standard focuses on quality management systems and is essential for ensuring consistent quality in manufacturing processes.
- CE Marking: Particularly important for products sold in Europe, indicating compliance with safety, health, and environmental protection standards.
- API Standards: For applications within the petroleum and natural gas industries, adherence to American Petroleum Institute (API) standards is crucial.
These certifications not only enhance product reliability but also assure buyers of compliance with global safety and quality benchmarks.
Key Quality Control Checkpoints
Quality control in water jet cutter manufacturing involves various checkpoints:
- Incoming Quality Control (IQC): Ensures raw materials meet specifications.
- In-Process Quality Control (IPQC): Monitors the production process to catch defects early.
- Final Quality Control (FQC): Comprehensive testing of the final product to ensure it meets all design specifications.
These checkpoints are critical for maintaining high standards throughout the manufacturing process.
Common Testing Methods
Manufacturers employ various testing methods to ensure quality, including:
- Hydrostatic Testing: Used to check for leaks in the high-pressure systems.
- Performance Testing: Assesses the cutting speed and precision of the water jet cutter.
- Dimensional Inspection: Verifies the accuracy of the product against design specifications.
These tests provide objective data on the performance and reliability of the water jet cutters.
How Can B2B Buyers Verify Supplier Quality Assurance?
For international B2B buyers, particularly from regions like Africa, South America, the Middle East, and Europe, verifying the quality assurance of suppliers is essential. Here are several actionable strategies:
Conduct Supplier Audits
Before finalizing a purchase, consider conducting a supplier audit. This involves visiting the manufacturing facility to evaluate their processes, quality control measures, and compliance with international standards.
During the audit, focus on areas such as:
- The cleanliness and organization of the manufacturing floor.
- The presence of quality control checkpoints and documentation.
- Employee training and expertise in quality management practices.
Request Quality Assurance Reports
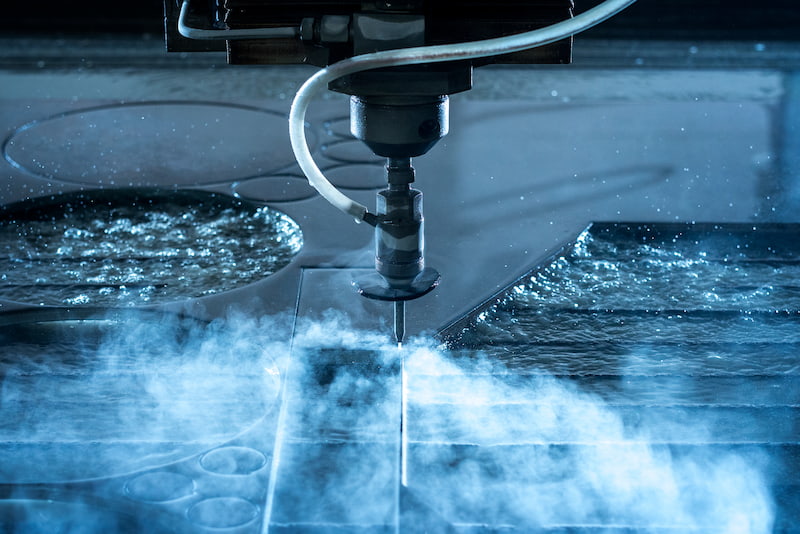
A stock image related to water jet cutter.
Ask suppliers for their quality assurance reports, including any certifications or compliance documents. This documentation should outline their quality control processes, testing results, and adherence to international standards.
Engage Third-Party Inspectors
For added assurance, consider hiring third-party inspectors to evaluate the manufacturing processes and final products. These inspectors can provide an unbiased review of the supplier’s quality assurance practices and product quality.
What Are the Quality Control Nuances for International Buyers?
When engaging with suppliers from different regions, it’s essential to understand the nuances in quality control that may affect your purchasing decisions.
Regional Standards Variability
Quality standards may vary significantly between regions. For instance, while ISO certifications are globally recognized, the specific requirements for CE marking may differ from those in Africa or South America.
Buyers should familiarize themselves with local regulations and standards relevant to their industries to ensure compliance.
Language and Communication Barriers
Language differences can pose challenges in understanding quality assurance documentation and processes. It’s advisable to work with suppliers who can provide documentation in a language you are comfortable with, ensuring clarity in quality expectations.
Cultural Differences in Quality Perception
Cultural attitudes towards quality can vary by region. In some cultures, there may be a more relaxed approach to quality assurance, while others may have stringent practices. Understanding these cultural differences can help buyers navigate expectations and negotiate effectively.
Conclusion
For international B2B buyers, particularly those from Africa, South America, the Middle East, and Europe, comprehending the manufacturing processes and quality assurance practices of water jet cutters is essential. By focusing on the main manufacturing stages, understanding quality assurance standards, and implementing strategies for supplier verification, buyers can make informed decisions that align with their operational needs and quality expectations.
Practical Sourcing Guide: A Step-by-Step Checklist for ‘water jet cutter’
In this practical sourcing guide, we will outline essential steps for international B2B buyers looking to procure a water jet cutter. This checklist will help you make informed decisions and ensure that your investment meets your operational needs while aligning with industry standards.
Step 1: Define Your Technical Specifications
Before you start sourcing, it’s vital to clearly outline your technical requirements. Consider the types of materials you will be cutting (e.g., metals, plastics, glass) and the thickness of these materials. Additionally, think about the cutting precision and speed necessary for your applications, as these specifications will significantly influence your choice of machine.
- Material Types: Identify all materials you intend to work with and their respective thicknesses.
- Precision Needs: Determine the level of precision required for your projects, as some applications may require tighter tolerances.
Step 2: Research Available Water Jet Technologies
Understanding the different water jet cutting technologies available is crucial. There are primarily two types: pure water jet and abrasive water jet systems. Each has its own advantages depending on the materials and applications.
- Pure Water Jet: Ideal for softer materials, this method uses only high-pressure water.
- Abrasive Water Jet: Suitable for harder materials, this method incorporates abrasives to enhance cutting capability.
Step 3: Evaluate Potential Suppliers
Before making a purchase, thoroughly vet potential suppliers. Check their reputation in the market by requesting company profiles, case studies, and references from clients in similar industries or regions. A reputable supplier should provide clear evidence of their expertise and customer satisfaction.
- Certifications: Look for industry certifications that indicate compliance with international standards.
- Customer Reviews: Seek feedback from existing customers to gauge the supplier’s reliability and support.
Step 4: Assess Total Cost of Ownership
When evaluating water jet cutters, consider not just the initial purchase price but also the total cost of ownership. This includes maintenance costs, operational expenses, and potential downtime.
- Maintenance Requirements: Investigate the maintenance schedule and costs associated with the machine.
- Energy Consumption: Compare energy efficiency among different models to understand long-term operational costs.
Step 5: Request Demonstrations and Samples
Whenever possible, request live demonstrations or sample cuts from suppliers. This hands-on experience allows you to assess the machine’s performance and its suitability for your specific applications.
- Material Compatibility: Ensure the machine can handle the materials you will be working with.
- Quality of Cuts: Evaluate the edge quality and precision of the cuts made during the demonstration.
Step 6: Understand Warranty and Support Options
A solid warranty and reliable customer support are critical when investing in a water jet cutter. Clarify the terms of the warranty and understand what support options are available after purchase.
- Warranty Duration: Look for warranties that cover both parts and labor.
- Technical Support: Ensure that the supplier offers robust technical support, including training and troubleshooting services.
Step 7: Negotiate Payment Terms and Financing Options
Finally, explore payment terms and financing options that align with your budget and cash flow. Many suppliers offer flexible financing, which can make the investment more manageable.
- Monthly Payment Plans: Inquire about installment plans that allow you to spread out payments.
- Leasing Options: Consider leasing as an alternative to outright purchase, particularly if your needs may change in the near future.
By following this checklist, you can streamline the procurement process for a water jet cutter and ensure that your investment will enhance your operational capabilities effectively.
Comprehensive Cost and Pricing Analysis for water jet cutter Sourcing
What Are the Key Cost Components in Water Jet Cutter Sourcing?
When sourcing water jet cutters, understanding the cost structure is essential for B2B buyers. The primary cost components include:
-
Materials: The quality of materials used in manufacturing water jet cutters—such as high-pressure pumps, cutting heads, and frames—can significantly affect pricing. For instance, cutters made from premium-grade steel or equipped with advanced technology will generally command higher prices.
-
Labor: Labor costs vary by region and can impact overall pricing. In countries with higher wage standards, such as those in Europe, the labor component may contribute more to the final cost compared to regions with lower labor costs.
-
Manufacturing Overhead: This encompasses all indirect costs associated with production, including utilities, rent, and equipment depreciation. Efficient manufacturers often pass on lower overhead costs to their buyers, making it advantageous to source from streamlined operations.
-
Tooling: Custom tooling for specific applications can add to initial costs. Buyers should evaluate whether they need specialized tooling for their projects, as this can influence both the upfront investment and ongoing operational efficiency.
-
Quality Control (QC): Rigorous quality control processes ensure that the water jet cutters meet industry standards. Companies that invest in comprehensive QC may charge more, but this could lead to reduced maintenance costs and longer equipment lifespan.
-
Logistics: Shipping and handling can significantly affect total costs, especially for international buyers. Factors such as distance, mode of transport, and customs duties must be considered to avoid unexpected expenses.
-
Margin: The profit margin that manufacturers and distributors add to their costs can vary widely. Understanding typical margins in different regions can help buyers negotiate better prices.
How Do Price Influencers Affect Water Jet Cutter Sourcing?
Several factors can influence the pricing of water jet cutters, and being aware of these can aid in effective sourcing:
-
Volume and Minimum Order Quantity (MOQ): Suppliers often offer discounts for bulk purchases. Buyers should assess their production needs to negotiate favorable terms based on volume.
-
Specifications and Customization: Custom features or specifications often lead to increased costs. Buyers should clearly define their requirements to avoid unnecessary expenses while ensuring that the cutter meets their operational needs.
-
Materials: The choice of materials not only affects the price but also the performance and durability of the cutter. High-quality materials may incur a higher upfront cost but can result in lower maintenance and operational costs over time.
-
Quality Certifications: Equipment that meets international quality standards (ISO, CE, etc.) may be priced higher. However, certifications can be crucial for ensuring reliability, particularly in regulated industries.
-
Supplier Factors: The reputation and reliability of the supplier can influence pricing. Established suppliers with a strong track record may charge more but offer better customer support and warranty options.
-
Incoterms: Understanding the terms of trade (Incoterms) is vital for international buyers. They dictate who bears the cost and risk at various points in the shipping process, affecting the total cost of ownership.
What Tips Can Help B2B Buyers Optimize Costs?
For international B2B buyers, particularly those in Africa, South America, the Middle East, and Europe, here are actionable tips to optimize costs when sourcing water jet cutters:
-
Negotiate Terms: Engage in discussions with suppliers about pricing, payment terms, and warranties. Building a relationship can often lead to better deals.
-
Consider Total Cost of Ownership (TCO): Look beyond the initial purchase price. Assess ongoing operational costs, maintenance, and potential downtime to get a clearer picture of the investment.
-
Evaluate Local Suppliers: Depending on your location, sourcing from local manufacturers may reduce shipping costs and lead times. This can be particularly beneficial in regions like Africa and South America, where logistics can be challenging.
-
Leverage Technology: Utilize web-based design and cutting software that can enhance productivity and reduce operational costs, especially for smaller businesses.
-
Stay Informed on Market Trends: Keeping abreast of industry developments can help you anticipate price changes and make informed purchasing decisions.
Disclaimer
The prices mentioned in this analysis are indicative and subject to change based on market conditions, supplier negotiations, and specific buyer requirements. Always consult multiple suppliers for the most accurate pricing tailored to your needs.
Alternatives Analysis: Comparing water jet cutter With Other Solutions
When evaluating cutting technologies, it’s essential for B2B buyers to understand the various alternatives available to water jet cutters. Each solution has its unique features, benefits, and ideal use cases, which can significantly impact operational efficiency and cost-effectiveness. Below, we compare water jet cutters with two viable alternatives: laser cutting machines and plasma cutting systems.
Comparison Aspect | Water Jet Cutter | Laser Cutting Machine | Plasma Cutting System |
---|---|---|---|
Performance | High precision, no heat-affected zones | Fast cutting speed, less precision on thicker materials | Quick cuts on metals, less precision on intricate designs |
Cost | $9,999 to $225,995 | $10,000 to $300,000 | $5,000 to $50,000 |
Ease of Implementation | Requires water source and drainage | Requires proper ventilation and safety systems | Portable, but requires electrical supply and air compressor |
Maintenance | Low, minimal wear on parts | Medium, optics and mirrors need regular cleaning | Medium to high, consumables like electrodes need frequent replacement |
Best Use Case | Cutting soft and hard materials, ideal for intricate designs | Ideal for metal sheets, signage, and thin materials | Suitable for heavy-duty metal fabrication and construction |
What Are the Advantages and Disadvantages of Laser Cutting Machines?
Laser cutting machines are renowned for their speed and efficiency. They excel in cutting thin materials and are often used in applications such as signage, metal fabrication, and automotive parts. However, they can struggle with thicker materials, leading to a loss of precision. Additionally, the heat generated during the cutting process can warp or affect the properties of the material, which is a significant drawback for industries requiring high precision. The initial investment can also be high, especially for advanced systems with high wattage.
How Does Plasma Cutting Compare to Water Jet Cutting?
Plasma cutting systems are favored for their speed and ability to cut through thick metals quickly, making them a common choice in heavy-duty industries like shipbuilding and construction. They can cut through materials that are several inches thick, which is advantageous for specific applications. However, plasma cutting generates significant heat, which can lead to distortion of the material and rough edges that may require additional finishing. The overall cost of plasma systems can be lower than laser cutting, but ongoing maintenance and consumables can add to the long-term costs.
Conclusion: How Should B2B Buyers Choose Between Water Jet Cutters and Alternatives?
Choosing the right cutting technology depends on several factors, including the types of materials being cut, the required precision, and budget constraints. Water jet cutters offer unique advantages for intricate designs and heat-sensitive materials, making them a strong contender for industries like aerospace and automotive. In contrast, laser cutting may be preferred for faster operations on thinner materials, while plasma cutting serves well in heavy-duty applications. B2B buyers should assess their specific operational needs, budget, and the materials they work with to make an informed decision that aligns with their business objectives.
Essential Technical Properties and Trade Terminology for water jet cutter
What Are the Key Technical Properties of Water Jet Cutters?
When considering a water jet cutter for your business, understanding its technical specifications is crucial for making an informed purchasing decision. Here are some essential properties to consider:
1. Material Compatibility
Water jet cutters can handle a wide variety of materials, including metals, glass, plastics, and composites. The ability to cut multiple materials allows businesses to diversify their offerings and meet various client demands without the need for multiple machines. For B2B buyers, evaluating the range of materials a cutter can process is vital, as it directly impacts operational flexibility and potential market opportunities.
2. Cutting Thickness
The cutting thickness capability varies across different machines. For instance, some models can cut through materials up to 1 inch thick, while others may only handle thinner sheets. This specification is critical as it determines the types of projects your business can undertake. Understanding the maximum cutting thickness helps in assessing whether the machine meets your production needs.
3. Precision and Tolerance
Precision is a significant factor in water jet cutting, often measured in tolerances of +/- 0.001 inches. High precision is essential for industries like aerospace and automotive, where even minor deviations can result in significant issues. For B2B buyers, knowing the precision specifications is important for ensuring that the final product meets quality standards and customer expectations.
4. Pump Pressure
The pump pressure of a water jet cutter affects its cutting efficiency and speed. Machines typically operate at pressures ranging from 30,000 to 90,000 psi. Higher pressure allows for quicker cuts and the ability to tackle tougher materials. B2B buyers should consider how pump pressure correlates with production speed and overall project turnaround times.
5. Software Compatibility
Modern water jet cutters often come with software that aids in design and cutting processes. The ability to integrate with existing design software can streamline operations and improve efficiency. For businesses, understanding software compatibility is crucial for ensuring a smooth transition and minimizing downtime.
6. Maintenance Requirements
Regular maintenance is necessary to keep water jet cutters in optimal working condition. Machines with lower maintenance requirements can lead to reduced operational costs and less downtime. B2B buyers should inquire about maintenance schedules and costs to accurately assess the total cost of ownership.
What Are Common Trade Terminology and Jargon Related to Water Jet Cutters?
Understanding industry terminology can facilitate smoother negotiations and communications. Here are some essential trade terms every B2B buyer should know:
1. OEM (Original Equipment Manufacturer)
OEM refers to a company that produces parts and equipment that may be marketed by another manufacturer. In the context of water jet cutters, understanding the OEM can help buyers gauge the quality and reliability of the machine.
2. MOQ (Minimum Order Quantity)
MOQ is the smallest amount of product that a supplier is willing to sell. Knowing the MOQ is essential for B2B buyers when planning purchases, especially for materials or spare parts associated with water jet cutters.
3. RFQ (Request for Quotation)
An RFQ is a document sent to suppliers to solicit price quotations for specific products or services. B2B buyers should prepare detailed RFQs to ensure they receive accurate and competitive pricing for water jet cutters and related services.
4. Incoterms (International Commercial Terms)
Incoterms are a set of international rules that define the responsibilities of buyers and sellers in international transactions. Familiarity with Incoterms is vital for B2B buyers to understand shipping costs, insurance, and risk management related to water jet cutter procurement.
5. CNC (Computer Numerical Control)
CNC refers to the automated control of machining tools by means of a computer. Water jet cutters with CNC capabilities allow for higher precision and automation, making them more efficient and user-friendly.
6. Abrasive vs. Water-Only Cutting
This distinction refers to the type of cutting mechanism used. Abrasive cutting incorporates materials like garnet to enhance cutting capabilities, while water-only cutting uses just high-pressure water. Understanding these differences can help buyers select the right machine based on their specific cutting needs.
By grasping these technical properties and industry terms, B2B buyers can make more informed decisions when investing in water jet cutters, ensuring they select the best equipment for their operational requirements.
Navigating Market Dynamics and Sourcing Trends in the water jet cutter Sector
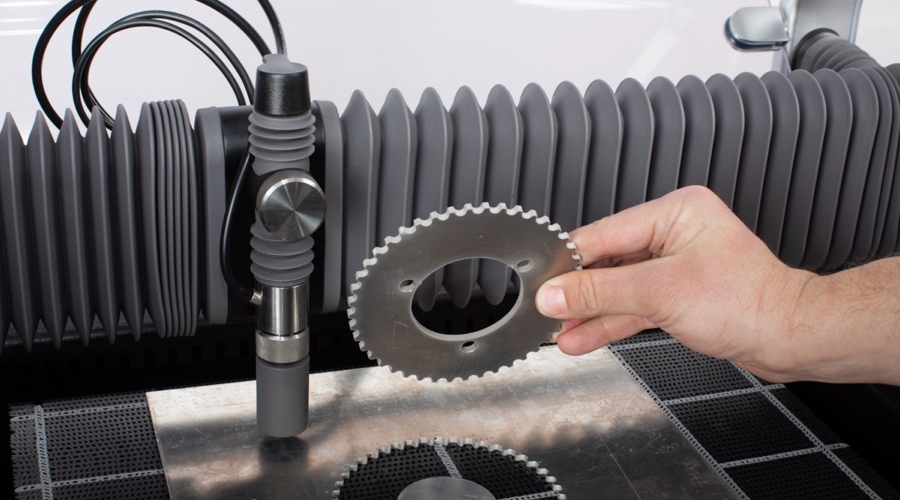
A stock image related to water jet cutter.
What Are the Current Market Dynamics in the Water Jet Cutter Sector?
The water jet cutter market is experiencing significant growth driven by the increasing demand for precision cutting across various industries such as aerospace, automotive, and manufacturing. International B2B buyers, particularly from regions like Africa, South America, the Middle East, and Europe, are seeking advanced technology that combines efficiency with high-quality output. The advent of compact, affordable machines, like the WAZER Pro, is making this technology accessible to smaller businesses and educational institutions, thus expanding the market reach.
Emerging trends include the integration of automation and smart technologies in water jet cutting systems. These innovations enhance operational efficiency and reduce labor costs, making them attractive to businesses looking to optimize production processes. Additionally, the demand for customizable cutting solutions is on the rise, as companies look for tailored machinery that can handle diverse materials, from metals to composites. This trend is particularly notable in regions like Kenya, where local manufacturers seek to innovate and compete on a global scale.
How Is Sustainability Impacting Water Jet Cutter Sourcing Decisions?
Sustainability is becoming a critical consideration for B2B buyers in the water jet cutter sector. The environmental impact of manufacturing processes is under scrutiny, prompting businesses to seek machines that minimize waste and energy consumption. Water jet cutting is inherently more sustainable than traditional cutting methods, as it generates less heat and waste, preserving material integrity and reducing the need for secondary finishing processes.
Buyers are increasingly favoring suppliers who demonstrate a commitment to ethical sourcing and sustainable practices. This includes the use of certified materials and components, as well as adherence to environmental regulations. Certifications such as ISO 14001 can serve as indicators of a supplier’s dedication to sustainability. As international markets evolve, B2B buyers from Europe and the Middle East are leading the charge in demanding greener solutions, setting a standard that is likely to influence sourcing decisions globally.
How Has the Water Jet Cutter Technology Evolved Over Time?
The evolution of water jet cutting technology has been marked by significant advancements in precision and efficiency. Initially developed for industrial applications, water jet cutters have transformed over the decades, becoming more versatile and accessible. Early machines were often bulky and costly, limiting their use to larger enterprises. However, recent innovations have introduced compact and affordable models that cater to small and medium-sized businesses.
Today, water jet cutters leverage advanced software and automation, enabling users to produce intricate designs with unmatched accuracy. The ability to cut a wide range of materials, including metals, glass, and composites, has expanded their application across various sectors. This evolution is crucial for B2B buyers as it opens up new opportunities for customization and production efficiency, meeting the diverse needs of modern manufacturing environments.
Frequently Asked Questions (FAQs) for B2B Buyers of water jet cutter
-
How do I choose the right water jet cutter for my business needs?
Selecting the appropriate water jet cutter depends on several factors, including the materials you plan to cut, the thickness of those materials, and the precision required for your applications. Consider whether you need a machine that can handle metals, glass, or composites, and assess the cutting capabilities such as the number of axes (3-axis vs. 5-axis). Additionally, evaluate the software compatibility for design uploads and your budget constraints. Consulting with suppliers to discuss your specific needs can provide tailored recommendations. -
What are the advantages of using water jet cutting technology over traditional methods?
Water jet cutting technology offers several advantages, including the ability to cut a wide range of materials without introducing heat, which prevents thermal distortion. This cold-cutting process ensures high precision and a clean edge, reducing the need for secondary finishing. Moreover, water jet cutters can handle intricate designs and thicker materials, making them versatile for various industries such as aerospace, automotive, and manufacturing. The efficiency and reduced waste associated with this method can also lead to cost savings. -
What customization options are available for water jet cutters?
Customization options for water jet cutters can vary significantly by manufacturer. Common customizations include adjusting the cutting table size, selecting between abrasive and water-only cutting heads, and incorporating specific software features for design processing. Some suppliers may also offer tailored maintenance packages or financing options based on your operational needs. Engaging directly with manufacturers can help identify the best customization options for your specific applications and budget. -
What are the typical payment terms for purchasing a water jet cutter internationally?
Payment terms for international purchases of water jet cutters often include a deposit upon order placement, with the remaining balance due prior to shipment or upon delivery. Terms can vary based on the supplier’s policies and your relationship with them. It’s crucial to discuss payment methods, such as wire transfers or letters of credit, and to clarify any additional costs, including shipping and customs duties. Establishing clear communication regarding terms can prevent misunderstandings. -
How can I vet suppliers for water jet cutters effectively?
Vetting suppliers involves researching their reputation, experience, and customer reviews. Look for certifications such as ISO or other industry-specific accreditations that indicate quality and reliability. Request references from existing clients and inquire about their after-sales service and support. Additionally, visiting their facility or attending trade shows can provide insights into their manufacturing capabilities. Engaging with local distributors can also facilitate better communication and support for international buyers. -
What is the minimum order quantity (MOQ) for water jet cutters?
The minimum order quantity for water jet cutters can vary widely among suppliers. While some manufacturers may offer single units, others may require bulk orders to meet production efficiencies. Discussing your needs upfront can help clarify if a supplier can accommodate smaller orders. If you’re considering additional equipment or accessories, bundling purchases may also allow for more favorable terms regarding MOQs. -
What logistics considerations should I keep in mind when importing a water jet cutter?
When importing a water jet cutter, consider logistics factors such as shipping methods, lead times, and customs clearance processes. Ensure that the supplier provides necessary documentation, including invoices, packing lists, and certificates of origin. Collaborating with a reliable freight forwarder can streamline the import process and help navigate customs regulations specific to your country. Additionally, factor in delivery and installation logistics, as these may require specialized handling. -
How do I ensure quality assurance (QA) for my water jet cutter?
To ensure quality assurance for your water jet cutter, it’s advisable to establish clear specifications and standards prior to purchase. Request detailed product documentation, including technical specifications and testing certifications. Many suppliers offer warranty and service agreements that outline maintenance schedules and performance guarantees. Regular maintenance and calibration checks are essential for sustaining operational efficiency and ensuring the machine meets your cutting requirements over time.
Important Disclaimer & Terms of Use
⚠️ Important Disclaimer
The information provided in this guide, including content regarding manufacturers, technical specifications, and market analysis, is for informational and educational purposes only. It does not constitute professional procurement advice, financial advice, or legal advice.
While we have made every effort to ensure the accuracy and timeliness of the information, we are not responsible for any errors, omissions, or outdated information. Market conditions, company details, and technical standards are subject to change.
B2B buyers must conduct their own independent and thorough due diligence before making any purchasing decisions. This includes contacting suppliers directly, verifying certifications, requesting samples, and seeking professional consultation. The risk of relying on any information in this guide is borne solely by the reader.
Strategic Sourcing Conclusion and Outlook for water jet cutter
As international B2B buyers navigate the complexities of sourcing water jet cutters, understanding the strategic advantages of these machines is crucial. Water jet cutting technology stands out for its versatility, precision, and ability to handle a wide range of materials, from metals to composites. This adaptability makes it an invaluable asset across various industries, including aerospace, automotive, and manufacturing.
Incorporating water jet cutters into your operations not only enhances production capabilities but also reduces outsourcing costs, allowing for on-demand manufacturing and rapid prototyping. This strategic sourcing approach ensures that businesses remain competitive in a global market, particularly in regions like Africa, South America, the Middle East, and Europe.
Looking ahead, the demand for efficient and precise cutting solutions will continue to grow. Buyers should leverage technological advancements and financing options to invest in high-quality water jet systems that meet their specific needs. By prioritizing strategic sourcing and adopting the latest innovations, companies can position themselves for success in an evolving marketplace. Embrace this opportunity to enhance your operational efficiency and drive growth in your business.