Cut Costs with Polyethylene Tubing: The Ultimate Guide (2025)
Introduction: Navigating the Global Market for polyethylene tubing
Navigating the complexities of sourcing polyethylene tubing can be a daunting challenge for international B2B buyers, particularly those operating in diverse markets across Africa, South America, the Middle East, and Europe. As industries increasingly rely on this versatile material for applications ranging from agriculture to construction, understanding the nuances of product specifications, supplier reliability, and cost efficiency becomes critical. This comprehensive guide aims to demystify the global market for polyethylene tubing by covering essential topics such as types of polyethylene tubing, their various applications, effective strategies for supplier vetting, and cost considerations.
In this guide, buyers will find actionable insights tailored to their specific regional contexts. Whether you are a procurement officer in Kenya looking for high-density polyethylene (HDPE) for irrigation projects or a distributor in the UAE seeking flexible tubing for food and beverage applications, this resource empowers informed purchasing decisions. By understanding product characteristics and market dynamics, buyers can mitigate risks and enhance supply chain efficiencies.
With practical tips, industry best practices, and expert recommendations, this guide serves as a valuable tool for navigating the complexities of the polyethylene tubing market, ensuring that you can source the right products to meet your operational needs effectively.
Understanding polyethylene tubing Types and Variations
Type Name | Key Distinguishing Features | Primary B2B Applications | Brief Pros & Cons for Buyers |
---|---|---|---|
Low-Density Polyethylene (LDPE) | Flexible, lightweight, and resistant to impact | Food packaging, medical applications | Pros: Cost-effective, easy to handle. Cons: Lower tensile strength compared to HDPE. |
High-Density Polyethylene (HDPE) | Rigid, strong, and resistant to chemicals | Water supply, gas distribution, drainage systems | Pros: Durable, excellent chemical resistance. Cons: Less flexible, can be more expensive. |
Linear Low-Density Polyethylene (LLDPE) | Higher tensile strength and puncture resistance | Industrial applications, agricultural uses | Pros: Enhanced flexibility, good ESCR. Cons: Slightly higher cost than LDPE. |
Polyethylene Copolymer | Combines properties of both LDPE and HDPE | Specialty applications requiring specific traits | Pros: Versatile, tailored properties. Cons: May require custom orders, leading to higher costs. |
EVA-Lined Polyethylene | Incorporates ethylene-vinyl acetate for enhanced flexibility | Medical tubing, food processing | Pros: Excellent flexibility, FDA-approved. Cons: Limited temperature resistance. |
What Are the Characteristics of Low-Density Polyethylene (LDPE) Tubing?
Low-Density Polyethylene (LDPE) tubing is known for its flexibility and lightweight nature. It is commonly used in food packaging and medical applications due to its resistance to impact and moisture. B2B buyers should consider LDPE for applications where cost-effectiveness and ease of handling are priorities. However, its lower tensile strength compared to other types like HDPE may limit its use in high-pressure environments.
How Does High-Density Polyethylene (HDPE) Tubing Stand Out?
High-Density Polyethylene (HDPE) tubing is characterized by its rigidity and superior strength. It is resistant to a wide range of chemicals, making it ideal for water supply and gas distribution systems. B2B buyers focused on durability and chemical resistance will find HDPE a reliable choice. The trade-off is its lack of flexibility, which may pose challenges in installation and handling.
What Benefits Does Linear Low-Density Polyethylene (LLDPE) Tubing Offer?
Linear Low-Density Polyethylene (LLDPE) tubing provides enhanced tensile strength and puncture resistance compared to standard LDPE. It is well-suited for industrial applications and agricultural uses where flexibility is essential. B2B buyers should note that while LLDPE offers improved performance, it typically comes at a slightly higher cost than LDPE, which could impact budgeting for larger projects.
In What Scenarios Is Polyethylene Copolymer Tubing Beneficial?
Polyethylene Copolymer tubing combines the properties of both LDPE and HDPE, offering a versatile option for specialized applications. It can be tailored to meet specific requirements, making it suitable for projects where standard tubing types may not suffice. B2B buyers should be aware that custom orders can lead to higher costs and longer lead times, which may affect project timelines.
Why Choose EVA-Lined Polyethylene Tubing?
EVA-Lined Polyethylene tubing incorporates ethylene-vinyl acetate, enhancing its flexibility while maintaining FDA approval for food processing and medical applications. This type of tubing is particularly advantageous for projects requiring high flexibility and safety standards. However, buyers should consider its limited temperature resistance, which may restrict its use in high-heat environments.
Key Industrial Applications of polyethylene tubing
Industry/Sector | Specific Application of polyethylene tubing | Value/Benefit for the Business | Key Sourcing Considerations for this Application |
---|---|---|---|
Agriculture | Irrigation systems for crop watering | Efficient water usage and reduced labor costs | Consider durability, UV resistance, and local climate conditions. |
Oil and Gas | Transporting natural gas and liquids | Enhanced safety and reduced leakage risks | Ensure compliance with local regulations and standards. |
Food and Beverage | Food-grade tubing for liquid transfer | Maintains product integrity and safety | Verify FDA approval and resistance to temperature variations. |
Healthcare | Medical and pharmaceutical applications | Ensures safe transport of fluids and medications | Look for biocompatibility and sterilization options. |
Construction and Plumbing | Water supply and drainage systems | Reliable and long-lasting infrastructure solutions | Assess pressure ratings and compatibility with existing systems. |
How is Polyethylene Tubing Used in Agriculture for Irrigation Systems?
In agriculture, polyethylene tubing is extensively used for irrigation systems, enabling efficient water delivery to crops. This application helps to minimize water waste and labor costs while ensuring that plants receive adequate hydration. For international buyers, particularly in regions like Africa and South America, sourcing durable and UV-resistant tubing is crucial to withstand local climate conditions. Additionally, understanding the compatibility of the tubing with various irrigation technologies can enhance system effectiveness.
What Role Does Polyethylene Tubing Play in the Oil and Gas Industry?
Polyethylene tubing is vital in the oil and gas sector for transporting natural gas and other liquids. Its flexibility and resistance to corrosion make it ideal for underground installations, significantly reducing the risk of leaks and enhancing safety. For buyers in the Middle East and Europe, compliance with local regulations regarding material standards is essential when sourcing polyethylene tubing. Additionally, considering the tubing’s pressure ratings will ensure it meets the demands of specific applications.
How is Polyethylene Tubing Beneficial in Food and Beverage Applications?
In the food and beverage industry, polyethylene tubing is used for transferring liquids, ensuring that the product remains safe and uncontaminated. FDA-approved food-grade tubing is essential for maintaining product integrity, especially in regions with strict food safety regulations. International B2B buyers should prioritize sourcing tubing that is tasteless and odorless, as well as resistant to temperature fluctuations, to meet the diverse needs of food processing and distribution.
Why is Polyethylene Tubing Important in Healthcare?
Polyethylene tubing finds significant applications in healthcare settings, particularly for the safe transport of fluids and medications. Its biocompatibility and ease of sterilization make it suitable for various medical applications, including IV lines and laboratory use. Buyers in this sector must ensure that the tubing meets stringent health regulations and standards, especially when sourcing from international suppliers. This guarantees the safety and efficacy of medical treatments.
How Does Polyethylene Tubing Support Construction and Plumbing Projects?
In construction and plumbing, polyethylene tubing is commonly used for water supply and drainage systems. Its durability and resistance to chemicals make it a reliable choice for long-lasting infrastructure solutions. For international buyers, particularly those in developing regions, it is essential to assess the tubing’s pressure ratings and compatibility with existing plumbing systems to ensure optimal performance and longevity. This consideration can lead to significant cost savings in maintenance and replacements.
3 Common User Pain Points for ‘polyethylene tubing’ & Their Solutions
Scenario 1: Inconsistent Quality of Polyethylene Tubing
The Problem: B2B buyers often face challenges related to inconsistent quality when sourcing polyethylene tubing. This inconsistency can lead to operational inefficiencies, such as leaks or ruptures in critical applications like gas or water transport. For instance, a manufacturing company in Kenya may find that different suppliers provide tubing that varies significantly in thickness or flexibility, resulting in unforeseen costs and delays in production due to the need for replacements or repairs.
The Solution: To ensure consistent quality, B2B buyers should prioritize sourcing from reputable suppliers who provide certifications and detailed product specifications. When evaluating potential suppliers, it’s essential to request samples and perform quality tests that align with industry standards. Establishing long-term relationships with manufacturers who use standardized production processes can mitigate the risks of quality fluctuations. Additionally, investing in third-party quality assurance services can help verify that the polyethylene tubing meets the required specifications, thus ensuring reliability in critical applications.
Scenario 2: Difficulty in Selecting the Right Specifications for Applications
The Problem: Another common pain point arises when buyers struggle to select the appropriate specifications of polyethylene tubing for their specific applications. For example, a construction firm in the UAE may be unsure whether to opt for low-density polyethylene (LDPE) or high-density polyethylene (HDPE) for water supply lines. The wrong choice can lead to serious issues, such as pipe failure or inadequate pressure handling, which can disrupt operations and increase costs.
The Solution: To overcome this challenge, buyers should conduct a thorough analysis of their application requirements, including pressure ratings, temperature ranges, and chemical exposure. Engaging with technical experts or using resources like product data sheets and chemical resistance charts can provide valuable insights into the best tubing material for their needs. Furthermore, buyers can benefit from consulting with their suppliers about the specific conditions of their applications, ensuring they receive tailored recommendations. Training sessions or workshops offered by suppliers can also enhance the buyer’s understanding of product specifications, fostering more informed decision-making.
Scenario 3: Challenges with Installation and Maintenance of Polyethylene Tubing
The Problem: Installation and maintenance of polyethylene tubing can pose significant challenges for B2B buyers, especially in regions with varying climates and environmental conditions. For instance, a farming operation in South America may encounter difficulties with tubing that becomes brittle in extreme temperatures, leading to premature failure and costly downtime during critical planting seasons.
The Solution: To address installation and maintenance challenges, buyers should ensure that their polyethylene tubing is suitable for the local climate and application. This can be achieved by selecting products that are specifically designed for temperature and UV resistance. It is also beneficial to provide proper training for installation teams to follow best practices, such as ensuring correct fittings and avoiding sharp bends that could stress the material. Regular maintenance checks can be scheduled to identify early signs of wear or damage, allowing for proactive replacements before significant failures occur. Engaging with suppliers who offer installation support and maintenance training can further enhance the longevity and performance of the tubing in varied conditions.
Strategic Material Selection Guide for polyethylene tubing
What Are the Key Properties of Common Polyethylene Tubing Materials?
When selecting polyethylene tubing for various applications, understanding the properties of different materials is crucial. The most common types of polyethylene tubing include Low-Density Polyethylene (LDPE), High-Density Polyethylene (HDPE), Linear Low-Density Polyethylene (LLDPE), and Cross-Linked Polyethylene (PEX). Each material has unique properties that influence performance, durability, and suitability for specific applications.
How Does Low-Density Polyethylene (LDPE) Perform in B2B Applications?
Key Properties: LDPE is known for its flexibility and resistance to impact. It typically operates effectively at temperatures up to 60°C (140°F) and has a lower pressure rating compared to other polyethylene types.
Pros & Cons: The primary advantage of LDPE is its excellent flexibility, making it suitable for applications requiring bending and shaping. However, it is less durable than HDPE and may not withstand high-pressure environments. Additionally, LDPE can be more susceptible to environmental stress cracking.
Impact on Application: LDPE is ideal for low-pressure applications such as irrigation and drainage systems. However, it may not be suitable for transporting aggressive chemicals or high-temperature fluids.
Considerations for International Buyers: LDPE must comply with various international standards, such as ASTM D1248. Buyers in regions like Africa and South America should also consider the availability of LDPE in local markets and its environmental impact, as recycling options may be limited.
What Are the Advantages of High-Density Polyethylene (HDPE)?
Key Properties: HDPE boasts a high strength-to-density ratio, making it suitable for high-pressure applications. It can withstand temperatures up to 80°C (176°F) and has excellent chemical resistance.
Pros & Cons: The key advantage of HDPE is its durability and resistance to corrosion, which makes it ideal for harsh environments. However, its rigidity may limit its use in applications requiring flexibility. The manufacturing process for HDPE can also be more complex, leading to higher costs.
Impact on Application: HDPE is commonly used for water supply systems, gas distribution, and industrial applications due to its robust nature. Its compatibility with a wide range of chemicals enhances its application versatility.
Considerations for International Buyers: Buyers in the Middle East and Europe should ensure compliance with standards such as DIN 8074 and JIS K 6762. The availability of HDPE may vary, so it’s essential to assess local suppliers for consistent quality.
Why Choose Linear Low-Density Polyethylene (LLDPE)?
Key Properties: LLDPE offers improved tensile strength and puncture resistance compared to LDPE. It operates effectively at temperatures up to 70°C (158°F) and has good chemical resistance.
Pros & Cons: The main advantage of LLDPE is its enhanced flexibility and strength, making it suitable for a broader range of applications. However, it can be more expensive than LDPE and may not be as widely available in all regions.
Impact on Application: LLDPE is often used in food and beverage applications due to its FDA compliance. It is also suitable for fluid transfer in various industries, including agriculture and construction.
Considerations for International Buyers: Buyers should verify FDA compliance and other certifications. In regions like Kenya, understanding local regulations regarding food-grade materials is essential.
What Are the Benefits of Cross-Linked Polyethylene (PEX)?
Key Properties: PEX is known for its high-temperature resistance (up to 95°C or 203°F) and flexibility. It is also resistant to corrosion and scaling.
Pros & Cons: PEX’s flexibility allows for easy installation in tight spaces, making it popular in plumbing applications. However, it can be more expensive than other polyethylene types, and its long-term exposure to UV light can degrade its properties.
Impact on Application: PEX is widely used in residential plumbing and heating systems due to its durability and flexibility. It is also suitable for hot and cold water distribution.
Considerations for International Buyers: Compliance with local plumbing codes and standards is crucial. Buyers in Europe should be aware of EN 15875 standards for PEX tubing.
Summary Table of Polyethylene Tubing Materials
Material | Typical Use Case for polyethylene tubing | Key Advantage | Key Disadvantage/Limitation | Relative Cost (Low/Med/High) |
---|---|---|---|---|
Low-Density Polyethylene (LDPE) | Irrigation and drainage systems | Excellent flexibility | Less durable, lower pressure rating | Low |
High-Density Polyethylene (HDPE) | Water supply and gas distribution | High strength and chemical resistance | Rigid, complex manufacturing | Medium |
Linear Low-Density Polyethylene (LLDPE) | Food and beverage applications | Enhanced strength and flexibility | More expensive than LDPE | Medium |
Cross-Linked Polyethylene (PEX) | Residential plumbing and heating | High-temperature resistance and flexibility | UV degradation potential | High |
This guide provides a comprehensive overview of common polyethylene tubing materials, enabling international B2B buyers to make informed decisions based on their specific application needs and regional considerations.
In-depth Look: Manufacturing Processes and Quality Assurance for polyethylene tubing
What Are the Key Stages in the Manufacturing Process of Polyethylene Tubing?
The manufacturing of polyethylene tubing involves several critical stages, each designed to ensure the final product meets industry standards for quality and performance. Understanding these stages can help B2B buyers make informed decisions when sourcing polyethylene tubing.
1. Material Preparation: What Materials Are Used?
The primary raw materials for polyethylene tubing are low-density polyethylene (LDPE) and high-density polyethylene (HDPE). These materials are chosen for their flexibility, chemical resistance, and durability. During the preparation stage, the raw materials are processed into pellets, which are then fed into an extruder. This step often includes the addition of colorants and stabilizers to enhance the tubing’s properties.
2. Forming: How Is Polyethylene Tubing Shaped?
The extrusion process is the heart of polyethylene tubing manufacturing. In this stage, the prepared pellets are heated and melted in the extruder. The molten polyethylene is then forced through a die, forming a continuous tube. The diameter and wall thickness can be adjusted by changing the die and the extrusion speed. This method allows for high-volume production with consistent quality.
3. Assembly: What Additional Components Are Integrated?
While many applications require only the tubing itself, some products may need additional components. This can include fittings, valves, or connectors, which are typically assembled post-extrusion. Automated systems may be used for this assembly process to ensure precision and efficiency.
4. Finishing: How Is the Tubing Processed for Final Use?
After extrusion, the tubing undergoes cooling, often using water baths or air cooling systems. This step solidifies the polyethylene and helps maintain its shape. Following cooling, the tubing may be cut to specified lengths and packaged for shipment. Some manufacturers also perform additional surface treatments or coatings to enhance performance characteristics.
What International Standards and Quality Control Measures Are Essential for Polyethylene Tubing?
Quality assurance is paramount in the production of polyethylene tubing, particularly for B2B buyers who require reliability and compliance with international standards. Understanding these standards and quality control measures can help buyers assess potential suppliers.
ISO 9001: What Does It Mean for Quality Management?
ISO 9001 is a globally recognized standard for quality management systems (QMS). Manufacturers of polyethylene tubing who are ISO 9001 certified have demonstrated their commitment to quality through rigorous processes that ensure consistent product performance. Buyers should inquire about a supplier’s ISO certification to validate their quality management practices.
CE Marking: Why Is It Important for Products in Europe?
For products sold in Europe, CE marking indicates compliance with health, safety, and environmental protection standards. Polyethylene tubing that carries the CE mark has undergone testing to ensure it meets EU regulations, which is crucial for buyers in Europe. Suppliers must provide documentation and testing results that support this certification.
API Standards: What Are They for Oil and Gas Applications?
For applications in the oil and gas industry, the American Petroleum Institute (API) has established standards that polyethylene tubing must meet. These standards ensure that the tubing can withstand harsh conditions and maintain integrity under pressure. B2B buyers in the energy sector should verify that their suppliers comply with relevant API standards.
How Are Quality Control Checkpoints Implemented in the Manufacturing Process?
Quality control (QC) is an integral part of the manufacturing process for polyethylene tubing. Effective QC measures include multiple checkpoints throughout production to ensure that the final product meets required specifications.
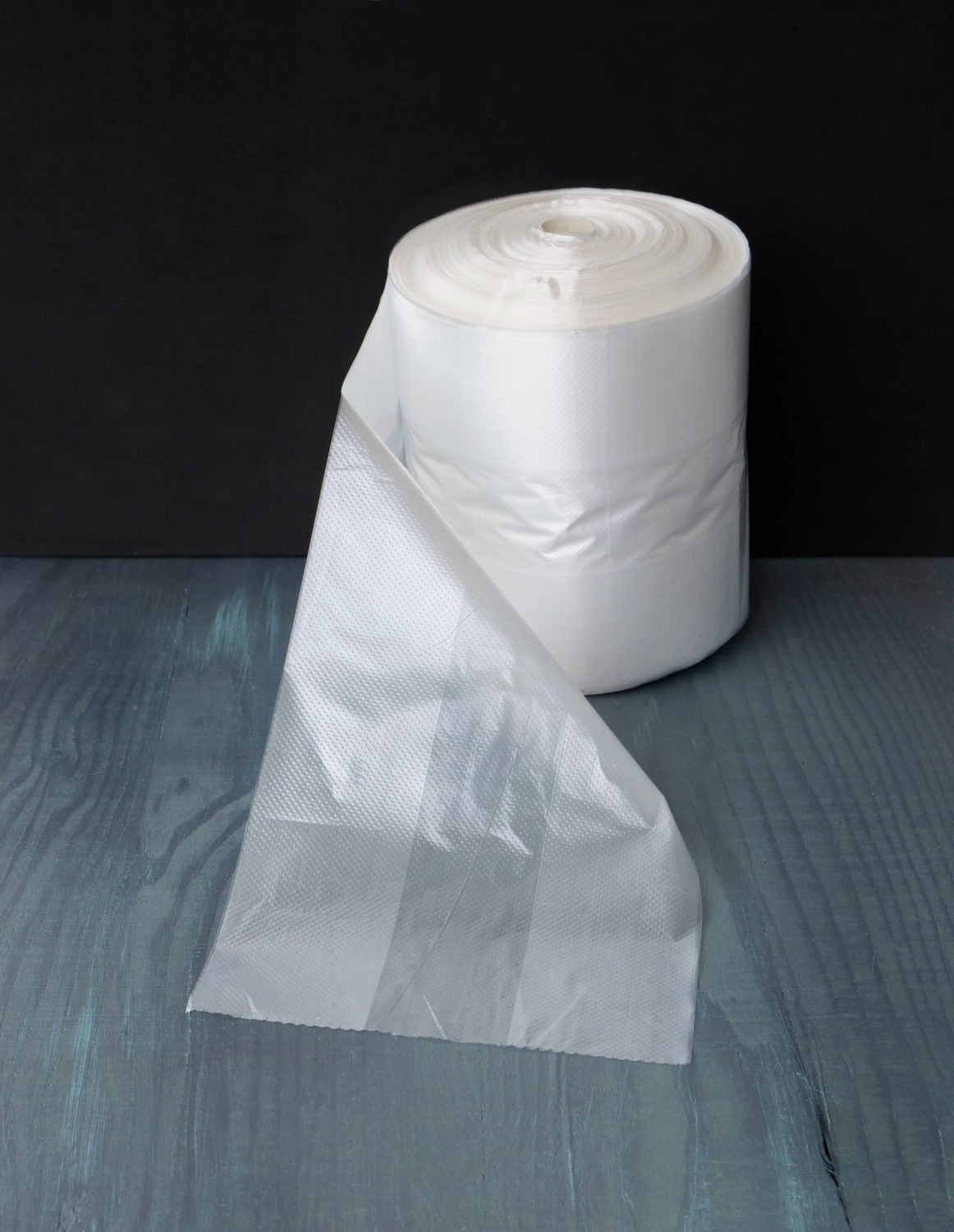
A stock image related to polyethylene tubing.
Incoming Quality Control (IQC): What Does It Involve?
Incoming Quality Control (IQC) involves inspecting raw materials upon delivery. This step ensures that the materials meet specified criteria before they enter the production process. Buyers can ask for IQC reports to understand how suppliers maintain material quality.
In-Process Quality Control (IPQC): How Is It Conducted?
In-Process Quality Control (IPQC) occurs during the manufacturing process. This includes monitoring the extrusion parameters, such as temperature and pressure, to ensure consistency. Regular sampling and testing of the tubing during production help catch any defects early, reducing waste and ensuring quality.
Final Quality Control (FQC): What Tests Are Conducted?
Final Quality Control (FQC) involves comprehensive testing of the finished product. Common tests include pressure testing, dimensional checks, and physical property assessments. These tests help confirm that the tubing meets all specifications and is ready for shipment.
How Can B2B Buyers Verify Supplier Quality Control?
For international B2B buyers, verifying a supplier’s quality control processes is essential to ensure product reliability and compliance with relevant standards. Here are actionable steps buyers can take:
Conducting Supplier Audits: What Should Be Included?
Buyers should consider conducting supplier audits to assess manufacturing processes and quality control systems. An effective audit should review documentation, observe production practices, and assess compliance with international standards like ISO 9001 and CE marking.
Requesting Quality Assurance Reports: What Documentation Is Necessary?
Requesting quality assurance (QA) reports from suppliers can provide insights into their QC processes. These reports should detail testing results, certifications, and any corrective actions taken for non-conformance issues. Documentation should be clear and readily available for buyer review.
Utilizing Third-Party Inspection Services: How Can They Help?
Engaging third-party inspection services can provide an independent assessment of a supplier’s quality control processes. These services can conduct factory visits, product testing, and compliance checks, offering an objective view of the supplier’s capabilities.
What Are the Unique Considerations for International Buyers from Africa, South America, the Middle East, and Europe?
International B2B buyers must navigate various challenges when sourcing polyethylene tubing, particularly those from diverse regions such as Africa, South America, the Middle East, and Europe.
Understanding Regional Compliance: What Regulations Exist?
Buyers should familiarize themselves with local regulations and compliance standards that may differ from international norms. For example, certain countries may have unique environmental regulations or material safety standards that impact product specifications.
Logistics and Supply Chain Management: What Are the Challenges?
Logistics can pose significant challenges, particularly for buyers in remote or developing regions. Understanding shipping times, customs regulations, and potential tariffs is crucial for effective supply chain management. Buyers should collaborate with suppliers who have a robust logistics network to ensure timely delivery.
Building Long-Term Relationships: Why Is It Important?
Establishing long-term relationships with reliable suppliers can lead to better pricing, improved product availability, and enhanced support. Buyers should invest time in understanding their suppliers’ capabilities and fostering communication to build trust and collaboration.
In conclusion, a comprehensive understanding of the manufacturing processes, quality assurance measures, and regional considerations can empower B2B buyers to make informed sourcing decisions regarding polyethylene tubing. By focusing on quality and compliance, buyers can ensure they select suppliers who meet their specific needs and standards.
Practical Sourcing Guide: A Step-by-Step Checklist for ‘polyethylene tubing’
In the competitive landscape of B2B procurement, sourcing polyethylene tubing requires a methodical approach to ensure quality, compliance, and cost-effectiveness. This guide offers a step-by-step checklist tailored for international buyers, particularly those in Africa, South America, the Middle East, and Europe.
Step 1: Define Your Technical Specifications
Understanding your specific needs is crucial before reaching out to suppliers. Consider the following:
– Application Requirements: Identify if the tubing will be used for potable water, gas, or other applications.
– Material Type: Decide between low-density polyethylene (LDPE) and high-density polyethylene (HDPE) based on strength and flexibility needs.
– Size and Length: Specify the inner and outer diameters, as well as the required lengths.
Step 2: Research Potential Suppliers
Start by compiling a list of potential suppliers. Look for companies that specialize in polyethylene tubing and have a strong presence in your target market. Key aspects to consider include:
– Industry Experience: Suppliers with a proven track record in your industry can better understand your requirements.
– Customer Reviews: Analyze feedback from previous clients to gauge reliability and quality.
Step 3: Evaluate Supplier Certifications
It’s vital to ensure that your suppliers adhere to industry standards. Verify the following certifications:
– ISO Certification: Confirms that the supplier follows international quality management standards.
– FDA Approval: If applicable, ensure that the tubing is safe for food and beverage use.
– Environmental Compliance: Check for adherence to REACH and RoHS standards, especially if your operations are in the EU.
Step 4: Request Samples and Product Specifications
Before making a bulk purchase, always request product samples. This step allows you to:
– Test Quality and Performance: Evaluate the flexibility, tensile strength, and resistance to chemicals or environmental stress.
– Confirm Compliance: Ensure that the tubing meets your specifications in real-world conditions.
Step 5: Negotiate Terms and Pricing
Engage in discussions with your shortlisted suppliers to negotiate terms. Consider the following:
– Volume Discounts: Inquire if bulk orders can reduce costs.
– Payment Terms: Establish clear payment conditions that protect your cash flow.
– Lead Times: Ensure the supplier can meet your delivery deadlines, especially for urgent projects.
Step 6: Finalize Contractual Agreements
Once you have selected a supplier, it’s essential to formalize the agreement. Ensure that the contract includes:
– Detailed Specifications: Clearly outline product requirements, quality standards, and delivery schedules.
– Warranty and Return Policies: Understand the terms regarding defective products or returns.
– Confidentiality Agreements: Protect your business interests, especially when dealing with proprietary information.
Step 7: Monitor Supplier Performance
After procurement, maintain an ongoing relationship with your supplier. Regularly assess:
– Quality Control: Implement checks to ensure that the supplied tubing consistently meets your standards.
– Communication: Establish clear channels for feedback and support to address any issues promptly.
By following this checklist, B2B buyers can effectively navigate the sourcing process for polyethylene tubing, ensuring they select the right suppliers that meet their specific needs while adhering to industry standards.
Comprehensive Cost and Pricing Analysis for polyethylene tubing Sourcing
Understanding the cost structure and pricing dynamics of polyethylene tubing is crucial for international B2B buyers, particularly those from Africa, South America, the Middle East, and Europe. This analysis will delve into the key components affecting costs, the factors influencing pricing, and provide actionable insights to enhance sourcing strategies.
What Are the Key Components of Polyethylene Tubing Costs?
The cost structure of polyethylene tubing is comprised of several critical components:
-
Materials: The primary ingredient, polyethylene, can vary in price based on quality (e.g., low-density polyethylene (LDPE) vs. high-density polyethylene (HDPE)). Fluctuations in crude oil prices also directly impact material costs, so buyers should monitor market trends.
-
Labor: Labor costs are influenced by the location of manufacturing facilities. Regions with higher labor costs, such as parts of Europe, may see increased pricing compared to those in Africa or South America, where labor is generally less expensive.
-
Manufacturing Overhead: This includes utilities, maintenance, and facility costs. Efficient manufacturing processes can help reduce overhead, allowing suppliers to offer more competitive prices.
-
Tooling: The initial setup for production can be a significant cost, especially for custom sizes or specifications. Buyers should inquire about tooling costs when requesting quotes for custom products.
-
Quality Control (QC): Ensuring product quality can add to costs. Suppliers with stringent QC processes may charge more, but this can lead to fewer defects and lower long-term costs for buyers.
-
Logistics: Transportation costs can vary significantly based on the distance from the supplier to the buyer, as well as the chosen shipping method. Incoterms play a critical role here, determining who is responsible for shipping costs and risks.
-
Margin: Suppliers typically include a profit margin in their pricing. Understanding the standard margins within the industry can help buyers negotiate better.
What Factors Influence Polyethylene Tubing Pricing?
Several factors can affect the pricing of polyethylene tubing:
-
Volume/MOQ: Bulk purchases often lead to discounts. Buyers should consider their purchasing strategy—ordering larger quantities can lower the price per unit.
-
Specifications and Customization: Custom products with specific diameters, colors, or certifications (e.g., FDA approval for food-grade tubing) typically command higher prices. Clear communication of needs can help suppliers provide accurate quotes.
-
Material Quality and Certifications: Higher quality materials or those with specific certifications often lead to increased costs. Buyers should assess whether these certifications are necessary for their applications.
-
Supplier Factors: The reputation and reliability of the supplier can influence pricing. Established suppliers may charge a premium due to perceived quality and reliability.
-
Incoterms: Different Incoterms can significantly affect total costs. For instance, using EXW (Ex Works) means the buyer bears all transportation costs, while CIF (Cost, Insurance, and Freight) includes shipping costs, which can influence initial price perceptions.
How Can International Buyers Negotiate for Better Pricing?
Effective negotiation strategies can lead to substantial savings:
-
Understand Total Cost of Ownership (TCO): Beyond the initial purchase price, consider factors such as shipping, handling, and potential defects. A lower upfront cost may lead to higher long-term expenses.
-
Leverage Volume Discounts: Communicate your anticipated purchase volumes. Suppliers are often willing to negotiate better terms for guaranteed larger orders.
-
Build Long-Term Relationships: Establishing rapport with suppliers can lead to better pricing and priority service. Regular communication can also help in understanding market trends and pricing fluctuations.
-
Request Multiple Quotes: Engaging with several suppliers can provide a clearer picture of the market and enable better negotiation leverage.
What Pricing Nuances Should Buyers from Africa, South America, the Middle East, and Europe Be Aware Of?
International buyers must navigate various pricing nuances based on regional market dynamics:
-
Currency Fluctuations: Buyers should consider the impact of currency exchange rates on pricing, especially when dealing with suppliers in different regions.
-
Import Tariffs and Regulations: Understanding local import duties and regulations can help avoid unexpected costs.
-
Logistics Challenges: Buyers in remote areas may face higher shipping costs or longer lead times, impacting overall pricing strategies.
Conclusion
When sourcing polyethylene tubing, a thorough understanding of the cost components, pricing influencers, and effective negotiation strategies can empower international B2B buyers to make informed decisions. By actively engaging with suppliers and considering the total cost of ownership, businesses can optimize their procurement processes and achieve better pricing outcomes.
Alternatives Analysis: Comparing polyethylene tubing With Other Solutions
When evaluating solutions for fluid transfer and piping systems, it’s essential to consider various alternatives to polyethylene tubing. Each option has unique properties, advantages, and applications that can affect decision-making for international B2B buyers. This analysis focuses on comparing polyethylene tubing with two viable alternatives: PVC tubing and polyurethane tubing.
Comparison Table of Polyethylene Tubing and Alternatives
Comparison Aspect | Polyethylene Tubing | PVC Tubing | Polyurethane Tubing |
---|---|---|---|
Performance | Good flexibility; resistant to chemicals; suitable for various temperatures | Moderate flexibility; better for high-pressure applications; less chemical resistance | Excellent flexibility; superior abrasion resistance; ideal for dynamic applications |
Cost | Generally cost-effective; varies by grade | Low to moderate; often cheaper than polyethylene | Higher cost due to enhanced properties |
Ease of Implementation | Easy to install; lightweight and flexible | Simple to install; requires solvent cement for joints | Installation can be complex; may require special fittings |
Maintenance | Low maintenance; durable | Moderate maintenance; susceptible to UV degradation | Low maintenance; resistant to wear and tear |
Best Use Case | Agriculture, water supply, gas distribution | Plumbing, drainage, and electrical conduit | Robotics, pneumatic applications, and high-performance machinery |
What Are the Advantages and Disadvantages of PVC Tubing Compared to Polyethylene Tubing?
PVC (Polyvinyl Chloride) tubing is widely used due to its affordability and availability. It provides moderate flexibility and is better suited for high-pressure applications compared to polyethylene. However, it has limitations in chemical resistance, making it less ideal for environments with aggressive chemicals. PVC is often used in plumbing and drainage systems but may degrade when exposed to UV light over time.
How Does Polyurethane Tubing Compare to Polyethylene Tubing in Performance?
Polyurethane tubing is renowned for its exceptional flexibility and abrasion resistance, making it suitable for dynamic applications where movement and friction are common. It performs well under varying temperatures and pressures, but its higher cost may deter some buyers. Polyurethane is often used in robotics and pneumatic systems due to its durability, but installation can be more complex and may require specialized fittings, which can increase overall project costs.
How Should B2B Buyers Choose the Right Solution Among These Options?
When selecting the appropriate tubing solution, B2B buyers should assess their specific needs, including application requirements, budget constraints, and the environmental conditions the tubing will face. Polyethylene tubing is a solid choice for cost-sensitive projects where chemical resistance and flexibility are important. In contrast, PVC tubing is suitable for standard plumbing applications where cost is a primary concern. For high-performance environments that demand flexibility and durability, polyurethane tubing may be the best fit, despite its higher initial investment.
By carefully weighing the pros and cons of each option, buyers from regions like Africa, South America, the Middle East, and Europe can make informed decisions that align with their operational needs and financial considerations.
Essential Technical Properties and Trade Terminology for polyethylene tubing
What Are the Key Technical Properties of Polyethylene Tubing?
When considering polyethylene tubing for B2B applications, understanding its technical properties is crucial for making informed purchasing decisions. Here are some essential specifications:
1. Material Grade
Polyethylene tubing typically comes in two main grades: Low-Density Polyethylene (LDPE) and High-Density Polyethylene (HDPE). LDPE is flexible and has a lower tensile strength, making it suitable for applications such as food packaging and low-pressure environments. HDPE, on the other hand, offers higher tensile strength and is resistant to impact and environmental stress, making it ideal for high-pressure applications and underground installations. For B2B buyers, choosing the appropriate material grade can significantly affect the durability and application suitability of the tubing.
2. Tolerance
Tolerance refers to the allowable variation in the diameter and wall thickness of the tubing. It is crucial for ensuring compatibility with fittings and connectors. For instance, a tighter tolerance may be necessary in applications involving high precision, such as medical or laboratory environments. Understanding tolerance specifications helps buyers ensure that the tubing will fit seamlessly into their existing systems, reducing the risk of leaks or failures.
3. Pressure Rating
The pressure rating indicates the maximum pressure that the tubing can safely handle. This rating is vital for applications involving fluid or gas transfer, where exceeding the pressure limits could lead to catastrophic failures. B2B buyers must consider their specific operational pressures to select tubing that meets or exceeds these requirements, ensuring safety and reliability.
4. Flexibility and Bend Radius
Flexibility describes how easily the tubing can bend without kinking or collapsing. The bend radius is the minimum radius at which the tubing can be bent without damage. For applications requiring complex routing, such as in tight spaces or intricate systems, flexibility and a low bend radius are essential. Buyers should assess their installation environments to select tubing that can accommodate necessary bends without compromising performance.
5. Chemical Resistance
Polyethylene tubing’s resistance to various chemicals is a key consideration, especially in industries like agriculture, pharmaceuticals, and food processing. Different grades of polyethylene offer varying levels of resistance to acids, bases, and solvents. B2B buyers should evaluate the chemicals their applications involve and select tubing that can withstand these exposures, thus avoiding degradation and ensuring longevity.
What Are Common Trade Terms Related to Polyethylene Tubing?
Familiarity with industry jargon is essential for effective communication and negotiation in B2B transactions. Here are some common terms:
1. OEM (Original Equipment Manufacturer)
OEM refers to companies that produce parts or equipment that may be marketed by another manufacturer. In the context of polyethylene tubing, understanding OEM relationships can help buyers identify reliable sources for their required components, ensuring quality and compatibility.
2. MOQ (Minimum Order Quantity)
MOQ is the smallest quantity of product that a supplier is willing to sell. For B2B buyers, knowing the MOQ helps in budgeting and planning inventory. Suppliers often set MOQs to justify production and shipping costs, so it’s essential to negotiate if large-scale purchasing is not feasible.
3. RFQ (Request for Quotation)
An RFQ is a document sent to suppliers requesting pricing and terms for a specific quantity of products. For B2B buyers, issuing an RFQ can streamline the procurement process and help in comparing prices and terms across multiple suppliers, facilitating better decision-making.
4. Incoterms (International Commercial Terms)
Incoterms are internationally recognized rules that define the responsibilities of sellers and buyers in international transactions. These terms specify who pays for shipping, insurance, and tariffs, and they can significantly affect the total cost of goods. Understanding Incoterms is critical for B2B buyers engaged in international trade to avoid unexpected expenses.
5. Lead Time
Lead time refers to the time between placing an order and receiving the goods. For buyers, understanding lead times is crucial for inventory management and project planning. It allows businesses to align their supply chains and ensure that they have the necessary materials when needed.
By grasping these technical properties and trade terms, B2B buyers can make more informed decisions regarding polyethylene tubing, optimizing their procurement strategies for better operational efficiency and cost-effectiveness.
Navigating Market Dynamics and Sourcing Trends in the polyethylene tubing Sector
What Are the Current Market Trends Influencing Polyethylene Tubing Sourcing?
The polyethylene tubing market is currently experiencing significant growth, driven by increasing demand across various sectors, including agriculture, construction, and healthcare. Emerging markets in Africa, South America, the Middle East, and Europe are playing a crucial role in this expansion. Factors such as urbanization, infrastructure development, and the need for efficient fluid transfer systems are propelling the demand for polyethylene tubing. Notably, countries like Kenya and the UAE are investing in agricultural technologies and water management systems, which require high-quality tubing solutions.
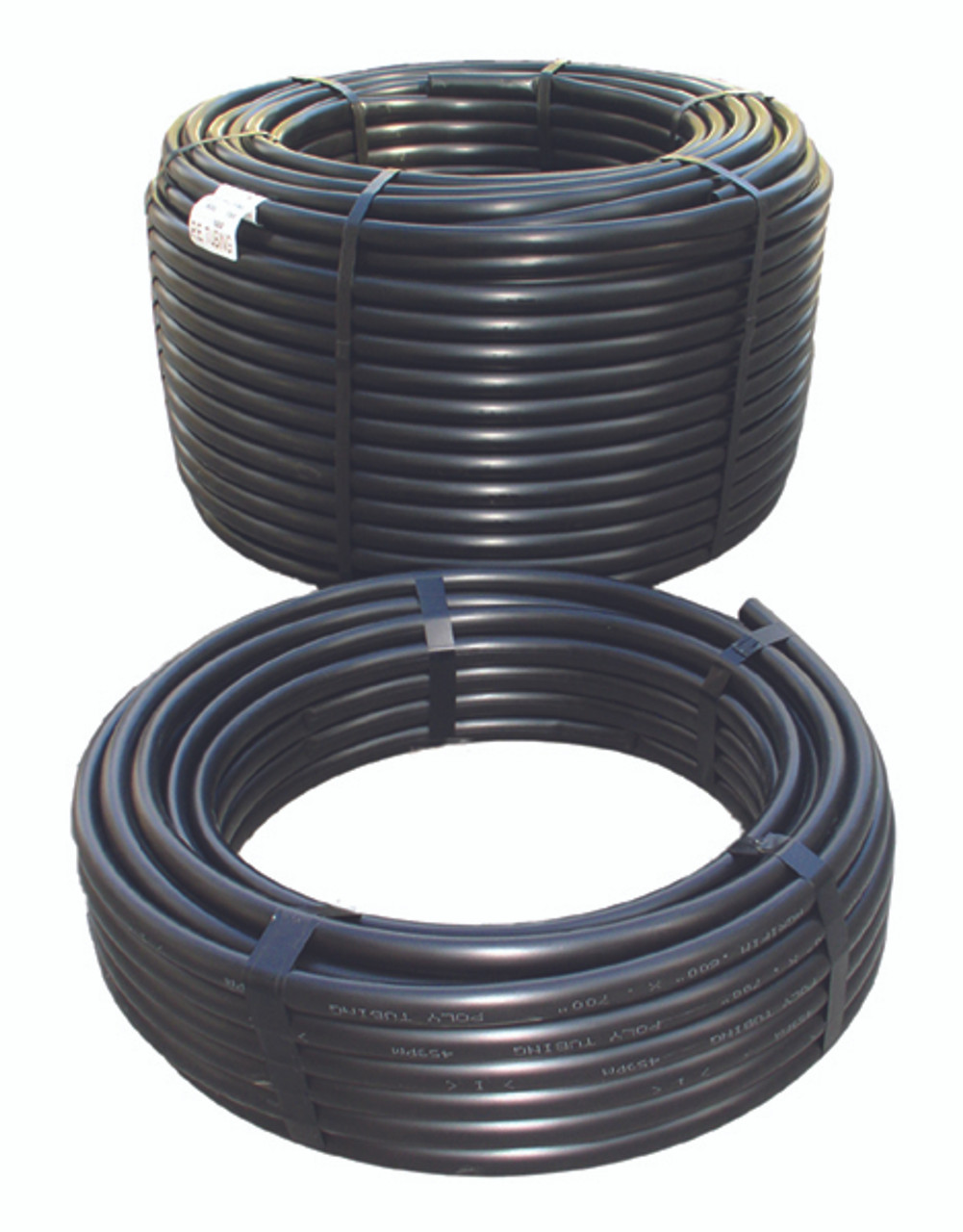
A stock image related to polyethylene tubing.
Technological advancements are also reshaping the sourcing landscape. The rise of smart manufacturing technologies, such as IoT and automation, has streamlined production processes, leading to cost efficiencies and improved product quality. Moreover, online sourcing platforms are becoming popular among B2B buyers, enabling them to compare prices and specifications easily. As businesses increasingly focus on just-in-time inventory management, suppliers who can offer flexible, rapid shipping options are gaining a competitive edge.
In addition, the ongoing global push towards digital transformation is changing how businesses engage with suppliers. Enhanced data analytics tools allow buyers to make informed decisions based on market trends and supplier performance metrics, ensuring they source the right products at the right time.
How Is Sustainability Impacting the Sourcing of Polyethylene Tubing?
Sustainability has become a paramount concern for international B2B buyers, significantly impacting sourcing strategies in the polyethylene tubing sector. The environmental impact of plastic production and waste management has led to increased scrutiny of supply chains. Buyers are now prioritizing suppliers who demonstrate commitment to sustainable practices, such as using recycled materials or implementing eco-friendly production processes.
Ethical sourcing is equally important, with many companies seeking to ensure that their supply chains are free from unethical labor practices. Certifications such as ISO 14001 for environmental management and RoHS for hazardous materials are gaining traction. These certifications not only validate a supplier’s commitment to sustainability but also enhance a buyer’s brand reputation in increasingly eco-conscious markets.
Furthermore, the development of biodegradable and compostable polyethylene alternatives is on the rise, providing sustainable options for businesses committed to reducing their environmental footprint. B2B buyers should actively seek suppliers who offer such innovative materials, as they align with global sustainability goals and consumer preferences.
What Is the Historical Context of Polyethylene Tubing in B2B Markets?
The history of polyethylene tubing can be traced back to the mid-20th century when polyethylene was first synthesized. Initially used for its lightweight and corrosion-resistant properties, the material quickly gained popularity in various applications, including plumbing, irrigation, and chemical transfer. Over the decades, advances in polymer technology have led to the development of different polyethylene grades, such as Low-Density Polyethylene (LDPE) and High-Density Polyethylene (HDPE), each catering to specific industry needs.
In the B2B context, the evolution of polyethylene tubing has been characterized by growing customization options, allowing manufacturers to meet diverse customer requirements. The introduction of FDA-approved food-grade polyethylene has opened new markets in the food and beverage sector, further solidifying polyethylene’s role as a versatile material in international trade.
Understanding the historical evolution of polyethylene tubing helps B2B buyers appreciate its current applications and market dynamics, enabling them to make informed sourcing decisions that align with industry trends and sustainability goals.
Frequently Asked Questions (FAQs) for B2B Buyers of polyethylene tubing
-
How do I choose the right polyethylene tubing for my application?
Selecting the appropriate polyethylene tubing involves considering the specific requirements of your application. Factors such as temperature, pressure, and the type of fluids being transported are crucial. For instance, Linear Low-Density Polyethylene (LLDPE) is ideal for flexibility and puncture resistance, while High-Density Polyethylene (HDPE) offers superior strength. Additionally, ensure the tubing complies with industry standards relevant to your region, such as FDA approval for food applications. -
What is the best type of polyethylene tubing for agricultural applications?
For agricultural applications, the best choice is typically Low-Density Polyethylene (LDPE) or LLDPE tubing due to their flexibility and resistance to environmental stress. These materials can withstand UV exposure and harsh weather conditions, making them suitable for irrigation systems. When sourcing, consider tubing that has been specifically designed for agricultural use to ensure durability and reliability in field conditions. -
How can I ensure the quality of polyethylene tubing from international suppliers?
To ensure quality, perform thorough vetting of potential suppliers. Request samples for testing and check for certifications that align with international standards, such as ISO or ASTM. Additionally, consider suppliers with a transparent quality assurance process, including regular inspections and testing of their products. Engaging in direct communication with suppliers can also provide insights into their manufacturing practices and commitment to quality. -
What are the minimum order quantities (MOQs) for polyethylene tubing?
Minimum order quantities for polyethylene tubing can vary significantly depending on the supplier and the specific product. Generally, MOQs can range from a few hundred meters to several thousand meters. It’s advisable to discuss your requirements directly with suppliers to negotiate MOQs that suit your purchasing capabilities. Many suppliers also offer flexibility for bulk orders or long-term contracts, which may further reduce costs. -
What payment terms should I expect when sourcing polyethylene tubing internationally?
Payment terms for international orders can vary widely, but common practices include upfront payments, net 30, or net 60 days after delivery. Some suppliers may also offer letters of credit or escrow services for larger transactions to provide security for both parties. Always clarify payment terms before placing an order, and consider negotiating terms that align with your cash flow and financial practices. -
How do I handle logistics and shipping for polyethylene tubing from overseas suppliers?
When dealing with international logistics, consider partnering with a freight forwarder who understands the nuances of shipping polyethylene tubing. They can help navigate customs regulations and ensure compliance with import/export requirements. Evaluate shipping options such as sea freight for cost-efficiency or air freight for quicker delivery. Additionally, account for potential delays due to customs clearance and plan accordingly. -
What customization options are available for polyethylene tubing?
Many suppliers offer customization options, including variations in diameter, length, color, and material properties. You can also request specific additives to enhance features like UV resistance or anti-static properties. Discuss your unique requirements with suppliers to explore available customization options that meet your application needs. Custom solutions can significantly improve performance and compatibility in specialized applications. -
How do I assess the environmental impact of polyethylene tubing?
To assess the environmental impact, inquire about the materials and manufacturing processes used by suppliers. Look for products made from recycled materials or those that adhere to eco-friendly practices. Certifications such as RoHS or REACH can indicate compliance with environmental standards. Additionally, consider the end-of-life options for polyethylene tubing, such as recycling programs, to further mitigate environmental impact.
Important Disclaimer & Terms of Use
⚠️ Important Disclaimer
The information provided in this guide, including content regarding manufacturers, technical specifications, and market analysis, is for informational and educational purposes only. It does not constitute professional procurement advice, financial advice, or legal advice.
While we have made every effort to ensure the accuracy and timeliness of the information, we are not responsible for any errors, omissions, or outdated information. Market conditions, company details, and technical standards are subject to change.
B2B buyers must conduct their own independent and thorough due diligence before making any purchasing decisions. This includes contacting suppliers directly, verifying certifications, requesting samples, and seeking professional consultation. The risk of relying on any information in this guide is borne solely by the reader.
Strategic Sourcing Conclusion and Outlook for polyethylene tubing
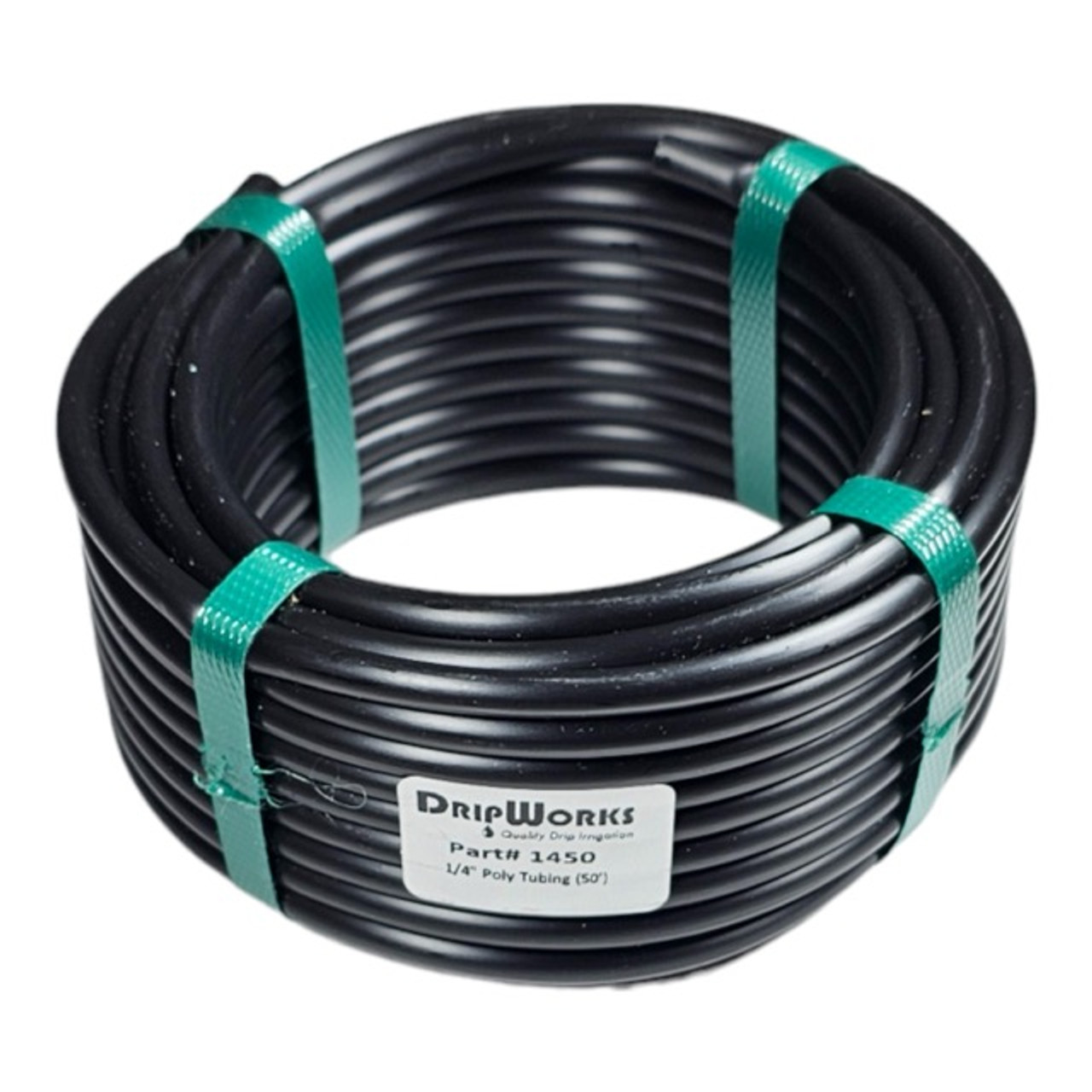
A stock image related to polyethylene tubing.
In the evolving landscape of polyethylene tubing, strategic sourcing emerges as a pivotal factor for international B2B buyers, especially those from Africa, South America, the Middle East, and Europe. By prioritizing quality suppliers who offer diverse product options—such as LLDPE, EVA lined, and FDA-approved tubing—businesses can ensure compliance with safety standards while optimizing their supply chain. This approach not only mitigates risks associated with supply disruptions but also enhances operational efficiency and cost-effectiveness.
Understanding the specific applications of polyethylene tubing, whether for potable water systems, gas transport, or food-grade requirements, allows buyers to make informed decisions that align with their operational needs. As demand for sustainable and versatile solutions continues to rise, investing in high-quality polyethylene products becomes increasingly essential.
Looking ahead, international buyers are encouraged to foster partnerships with reputable manufacturers and suppliers who can provide innovative solutions tailored to their market demands. By embracing strategic sourcing practices, businesses can position themselves for growth, ensuring they remain competitive in a dynamic global market. Take the next step in your sourcing strategy today—explore the possibilities within the polyethylene tubing sector to drive your business forward.