Cut Costs with the Ultimate Baler Machine Guide (2025)
Introduction: Navigating the Global Market for baler machine
Navigating the global market for baler machines presents a unique set of challenges for international B2B buyers, especially those from regions such as Africa, South America, the Middle East, and Europe. One of the primary difficulties lies in sourcing the right baler machine that not only meets specific operational needs but also aligns with budget constraints and local regulations. This guide is designed to equip buyers with the essential knowledge to make informed decisions, covering a comprehensive range of topics including various types of balers, their applications in different industries, supplier vetting processes, and cost considerations.
In understanding the intricacies of baler machine procurement, buyers will discover the critical factors influencing their purchasing decisions, such as lead times, machine efficiency, and compatibility with existing waste management systems. The guide will delve into the nuances of selecting balers for recycling, agriculture, and waste management, ensuring that businesses can optimize their operations while minimizing environmental impact.
By leveraging the insights provided in this guide, B2B buyers will be empowered to navigate the complexities of the baler machine market confidently. Whether you are based in bustling urban centers or emerging markets, this resource aims to facilitate strategic sourcing, ultimately enhancing operational efficiency and sustainability in your organization.
Understanding baler machine Types and Variations
Type Name | Key Distinguishing Features | Primary B2B Applications | Brief Pros & Cons for Buyers |
---|---|---|---|
Horizontal Baler | Operates with a horizontal feed; high throughput; suitable for large volumes of material. | Recycling plants, large-scale manufacturing. | Pros: Efficient for high volumes, space-saving design. Cons: Higher initial investment. |
Vertical Baler | Operates vertically; compact footprint; suitable for smaller operations. | Retail, small warehouses, and agricultural uses. | Pros: Cost-effective, less space required. Cons: Lower throughput compared to horizontal balers. |
Round Baler | Produces round bales; ideal for hay and forage; often towed by tractors. | Agricultural sectors, livestock farms. | Pros: Suitable for uneven terrain, versatile for various crops. Cons: Limited to certain materials. |
Closed-End Baler | Designed for specific materials; features a closed-end design for compact bales. | Cardboard and plastic recycling. | Pros: Reduces dust and waste, enhances safety. Cons: Less flexible for different materials. |
Auto Tie Baler | Automates the tying process; improves efficiency; often used in high-volume settings. | Large recycling operations and distribution centers. | Pros: Reduces labor costs, increases productivity. Cons: Higher maintenance requirements. |
What Are the Characteristics of Horizontal Balers?
Horizontal balers are designed for high-volume operations, making them ideal for recycling plants and large-scale manufacturing. They feature a horizontal feed system that allows for continuous operation, efficiently processing materials such as cardboard, plastics, and metals. Buyers should consider the initial investment and the space required for installation, as these machines can be larger and more expensive compared to other types. However, their efficiency in handling large volumes can lead to significant cost savings in the long run.
How Do Vertical Balers Differ from Other Types?
Vertical balers are characterized by their compact design, making them suitable for smaller operations such as retail stores and warehouses. They operate with a vertical feed, which requires less floor space and can easily be placed in tight areas. These balers are perfect for businesses with lower waste volumes and can handle materials like cardboard and plastics. While they are generally more affordable, buyers should note that vertical balers offer lower throughput compared to horizontal models, which may not suffice for larger operations.
What Are the Advantages of Round Balers in Agriculture?
Round balers are specifically designed for agricultural applications, particularly for hay and forage. They produce cylindrical bales that are easier to handle and transport, making them suitable for livestock farms and agricultural settings. The ability to operate on uneven terrain is a significant advantage, allowing farmers to utilize more land effectively. However, round balers are limited to specific materials, and buyers should evaluate whether their operations align with these capabilities.
Why Choose a Closed-End Baler for Recycling?
Closed-end balers are tailored for specific materials, such as cardboard and plastics, and feature a design that minimizes dust and waste during the baling process. This design enhances safety and cleanliness in recycling operations. While these balers can be highly efficient for their intended materials, they may lack flexibility for businesses that handle a variety of recyclables. Buyers should assess their material types and volumes to determine if a closed-end baler meets their needs.
How Does an Auto Tie Baler Improve Efficiency?
Auto tie balers are equipped with automated systems that tie bales, significantly improving operational efficiency in high-volume settings. These machines are commonly used in large recycling operations and distribution centers, where labor costs can be reduced through automation. While they offer enhanced productivity, potential buyers should consider the increased maintenance requirements that come with more complex machinery. Evaluating the total cost of ownership, including maintenance and labor savings, is crucial for informed purchasing decisions.
Key Industrial Applications of baler machine
Industry/Sector | Specific Application of baler machine | Value/Benefit for the Business | Key Sourcing Considerations for this Application |
---|---|---|---|
Recycling and Waste Management | Compacting recyclable materials like cardboard and plastics | Reduces disposal costs, increases recycling efficiency, and minimizes landfill use | Consider machine capacity, material compatibility, and maintenance support |
Agriculture | Baling hay and straw for livestock feed | Enhances storage efficiency, reduces waste, and improves feed quality | Assess bale size and density, machine durability, and ease of transport |
Manufacturing | Compressing scrap metal and production waste | Lowers transportation costs, optimizes space, and promotes sustainability | Evaluate machine size, force, and adaptability to different waste types |
Retail and Distribution | Baling cardboard boxes from packaging | Streamlines waste management, improves site cleanliness, and reduces labor costs | Focus on compactness, ease of operation, and safety features |
Construction | Baling construction debris and waste | Minimizes site clutter, enhances recycling efforts, and reduces disposal fees | Look for machines that handle mixed materials and have high compaction force |
What are the Key Industrial Applications of Baler Machines in Recycling and Waste Management?
In the recycling and waste management sector, baler machines are pivotal for compacting materials such as cardboard, plastics, and metals. They facilitate the efficient handling of recyclables by significantly reducing their volume, which leads to lower transportation costs and improved recycling rates. For international buyers, especially in regions like Africa and South America, selecting a baler that can handle diverse materials and has a robust maintenance plan is crucial to ensure operational longevity and efficiency.
How are Baler Machines Used in Agriculture?
In agriculture, balers are essential for compressing hay and straw into manageable bales for livestock feed. This process enhances storage efficiency, reduces spoilage, and improves feed quality. Buyers from the Middle East and Europe should consider the machine’s capacity to produce bales of the desired size and density, as well as its durability in varying weather conditions. Understanding local agricultural practices can also inform the choice of baler type, whether vertical or horizontal.
What Role Do Baler Machines Play in Manufacturing?
Manufacturers utilize baler machines to compress scrap metal and production waste, making it easier to manage and transport. This not only reduces the space required for waste storage but also promotes a more sustainable operation. When sourcing balers, businesses in Europe and Africa should evaluate the machine’s adaptability to different types of waste and its compaction force to ensure optimal efficiency.
How Do Baler Machines Benefit Retail and Distribution?
In the retail sector, balers are used to compact cardboard boxes generated from packaging. This application streamlines waste management, enhances site cleanliness, and can significantly reduce labor costs associated with waste handling. For international buyers, especially in emerging markets, it is important to focus on balers that are easy to operate and maintain, as well as those that meet local safety regulations.
What are the Advantages of Baler Machines in Construction?
In the construction industry, balers are effective for compressing debris and waste materials, helping to minimize site clutter and enhance recycling efforts. This leads to lower disposal fees and a more organized work environment. Buyers should look for machines capable of handling mixed materials and possessing a high compaction force to maximize efficiency and reduce transport frequency. Understanding the specific waste types prevalent in local construction projects can guide the selection of the appropriate baler.
3 Common User Pain Points for ‘baler machine’ & Their Solutions
Scenario 1: Inefficient Waste Management Processes
The Problem:
For many B2B buyers, particularly in sectors like manufacturing and retail, managing waste efficiently is a critical challenge. Businesses often struggle with excessive waste volume that leads to increased disposal costs and inefficient use of space. Companies in regions like Africa and South America, where waste management infrastructure may not be as developed, face additional hurdles in transporting and disposing of waste. As a result, they may be paying for multiple waste collection services or have overflowing bins that create environmental and aesthetic concerns.
The Solution:
Investing in a suitable baler machine can significantly streamline waste management processes. Buyers should first evaluate their waste types and volumes to select a baler that fits their specific needs. For instance, vertical balers can be ideal for smaller operations with limited floor space, while horizontal balers are better for larger facilities with high waste output. It’s essential to consider features like compaction force and bale size, which can directly impact cost savings.
Furthermore, sourcing from reputable manufacturers who offer machines designed for local waste types can enhance efficiency. Buyers should also explore options for leasing or renting balers to manage upfront costs while assessing their long-term needs. Training staff on the proper use and maintenance of the baler will maximize operational efficiency and prolong the machine’s lifespan, ensuring that the investment pays off in the long run.
Scenario 2: High Equipment Downtime and Maintenance Costs
The Problem:
B2B buyers often encounter the pain point of high downtime due to equipment failures or inefficient maintenance processes. In industries where continuous operation is essential, such as recycling or large-scale manufacturing, even minor delays can lead to significant financial losses. Buyers in the Middle East and Europe may find that parts for their balers are difficult to source, leading to prolonged downtime and increased maintenance costs.
The Solution:
To mitigate downtime, buyers should prioritize the selection of balers with a reputation for reliability and easy maintenance. Conducting thorough research on various brands and models can help identify machines that offer robust support and readily available spare parts. Additionally, establishing a proactive maintenance schedule can prevent breakdowns.
Investing in a comprehensive warranty or service contract with the manufacturer can provide peace of mind and reduce unexpected repair costs. Furthermore, buyers should consider training their maintenance teams on the specific requirements of their balers to facilitate quick troubleshooting and repairs. This proactive approach not only minimizes downtime but can also enhance the overall productivity of the operation.
Scenario 3: Limited Knowledge on Choosing the Right Baler Machine
The Problem:
Many international B2B buyers lack the expertise required to choose the right baler machine for their operations. This is particularly true for companies in emerging markets where advanced machinery is less common. Buyers may feel overwhelmed by the variety of options available and uncertain about which features are most beneficial for their specific needs, leading to potential misinvestments.
The Solution:
To address this issue, buyers should invest time in understanding their waste management requirements thoroughly before making a purchase. Conducting a waste audit can provide insights into the types and volumes of materials generated, which is critical in selecting the right baler.
Buyers are encouraged to engage with industry experts or consultants who specialize in waste management solutions. They can provide tailored recommendations based on the buyer’s specific circumstances. Additionally, attending trade shows or industry events can offer opportunities to see different machines in action and compare features directly.
Lastly, leveraging online resources, such as forums or product reviews, can help buyers gain insights from other users’ experiences. This informed approach will empower buyers to make confident purchasing decisions, ensuring they invest in equipment that aligns with their operational needs and budget.
Strategic Material Selection Guide for baler machine
What Materials are Commonly Used in Baler Machines?
When selecting a baler machine, the choice of materials plays a crucial role in determining its performance, durability, and operational efficiency. Here, we analyze four common materials used in baler machines, focusing on their properties, advantages, disadvantages, and specific considerations for international B2B buyers.
Steel: The Backbone of Baler Machines
Key Properties: Steel is known for its high tensile strength and durability, making it an ideal choice for the frame and structural components of baler machines. It can withstand high pressure and is resistant to deformation under heavy loads.
Pros & Cons: The primary advantage of steel is its robustness, which translates to a longer lifespan and reduced maintenance costs. However, steel is susceptible to corrosion unless treated, which can lead to increased costs over time, especially in humid or corrosive environments.
Impact on Application: Steel’s high strength makes it suitable for heavy-duty applications, such as baling industrial waste or agricultural products. However, its weight can be a drawback in mobile or smaller machines.
Considerations for International Buyers: Buyers should ensure compliance with local standards, such as ASTM or DIN, for structural integrity. In regions like Africa and South America, where corrosion can be a concern, selecting galvanized or coated steel may be essential.
Aluminum: Lightweight and Corrosion-Resistant
Key Properties: Aluminum is lightweight, corrosion-resistant, and has a good strength-to-weight ratio. It is often used in components where weight savings are critical.
Pros & Cons: The main advantage of aluminum is its resistance to rust and corrosion, making it suitable for various environments. However, it is generally more expensive than steel and may not provide the same level of strength for heavy-duty applications.
Impact on Application: Aluminum is ideal for portable balers or those used in environments with high moisture levels. However, its lower strength may limit its use in applications requiring high compaction forces.
Considerations for International Buyers: Buyers in Europe and the Middle East should be aware of the specific alloy grades required for their applications, as well as compliance with standards like JIS. The cost factor may also be a consideration, particularly in budget-sensitive markets.
Composite Materials: The Future of Baler Machines?
Key Properties: Composite materials, such as fiberglass or carbon fiber, offer high strength while being lightweight. They are also resistant to corrosion and can be molded into complex shapes.
Pros & Cons: The advantage of composites is their versatility and the potential for weight reduction in baler machines. However, they can be expensive to manufacture and may require specialized knowledge for repairs.
Impact on Application: Composites are suitable for specialized applications where weight and corrosion resistance are critical, such as in mobile balers or those used in harsh environments.
Considerations for International Buyers: Buyers should consider the availability of composite materials in their region and whether local manufacturers can provide support for maintenance and repairs. Compliance with international standards may also be a factor.
Rubber: Essential for Seals and Gaskets
Key Properties: Rubber provides excellent flexibility and resilience, making it ideal for seals, gaskets, and other components that require a tight fit.
Pros & Cons: The primary advantage of rubber is its ability to withstand wear and tear while maintaining a seal. However, it can degrade over time due to exposure to UV light and extreme temperatures.
Impact on Application: Rubber components are essential for ensuring the efficiency of baler machines by preventing leaks and ensuring smooth operation. However, their lifespan may be shorter compared to metal components.
Considerations for International Buyers: Buyers should ensure that the rubber used meets local compliance standards and is suitable for the specific environmental conditions in their region, such as temperature and humidity.
Summary Table of Material Selection for Baler Machines
Material | Typical Use Case for baler machine | Key Advantage | Key Disadvantage/Limitation | Relative Cost (Low/Med/High) |
---|---|---|---|---|
Steel | Frame and structural components | High strength and durability | Susceptible to corrosion | Medium |
Aluminum | Portable balers | Lightweight and corrosion-resistant | Higher cost than steel | High |
Composite | Specialized applications | Lightweight and versatile | Expensive and complex repairs | High |
Rubber | Seals and gaskets | Excellent flexibility | Degrades with UV exposure | Low |
This guide offers actionable insights for international B2B buyers, enabling them to make informed decisions regarding material selection in baler machines based on their specific needs and regional considerations.
In-depth Look: Manufacturing Processes and Quality Assurance for baler machine
What Are the Main Stages in the Manufacturing Process of Baler Machines?
The manufacturing process for baler machines involves several critical stages that ensure the final product meets quality and performance standards. Understanding these stages can help international B2B buyers make informed decisions when sourcing balers.
1. Material Preparation
The first step in manufacturing balers is material preparation. High-strength steel is the primary material used due to its durability and ability to withstand heavy loads. Suppliers typically source steel sheets and tubes that meet industry standards, ensuring they have the necessary strength and resistance to wear. This stage may also involve cutting and machining components to specific dimensions, which is crucial for the subsequent stages of production.
2. Forming
Once the materials are prepared, the forming stage begins. This involves processes such as bending, stamping, and welding. Advanced techniques like laser cutting and CNC machining are often employed to achieve precise shapes and sizes. For B2B buyers, understanding the forming techniques used can provide insights into the reliability and longevity of the baler. Machines with more advanced forming technologies typically offer better performance and durability.
3. Assembly
The assembly stage involves bringing together all the individual components, including the baling chamber, hydraulic systems, and control panels. This is a critical phase where skilled technicians ensure that all parts fit together correctly and function as intended. Buyers should inquire about the assembly processes used by manufacturers, as attention to detail during this stage can significantly affect the machine’s overall performance.
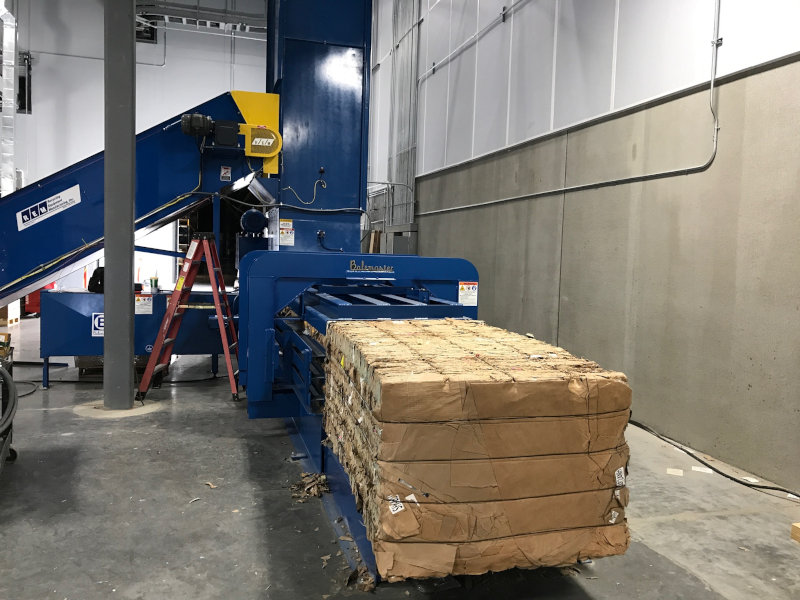
A stock image related to baler machine.
4. Finishing
The final stage in manufacturing is finishing, which includes painting and coating the baler to protect it from rust and wear. This step is essential for enhancing the machine’s aesthetic appeal and longevity. Manufacturers often use powder coating or galvanizing techniques to ensure a durable finish. B2B buyers should consider the type of finishing used, as it can impact maintenance requirements and the overall lifespan of the equipment.
How Is Quality Assurance Implemented in Baler Machine Manufacturing?
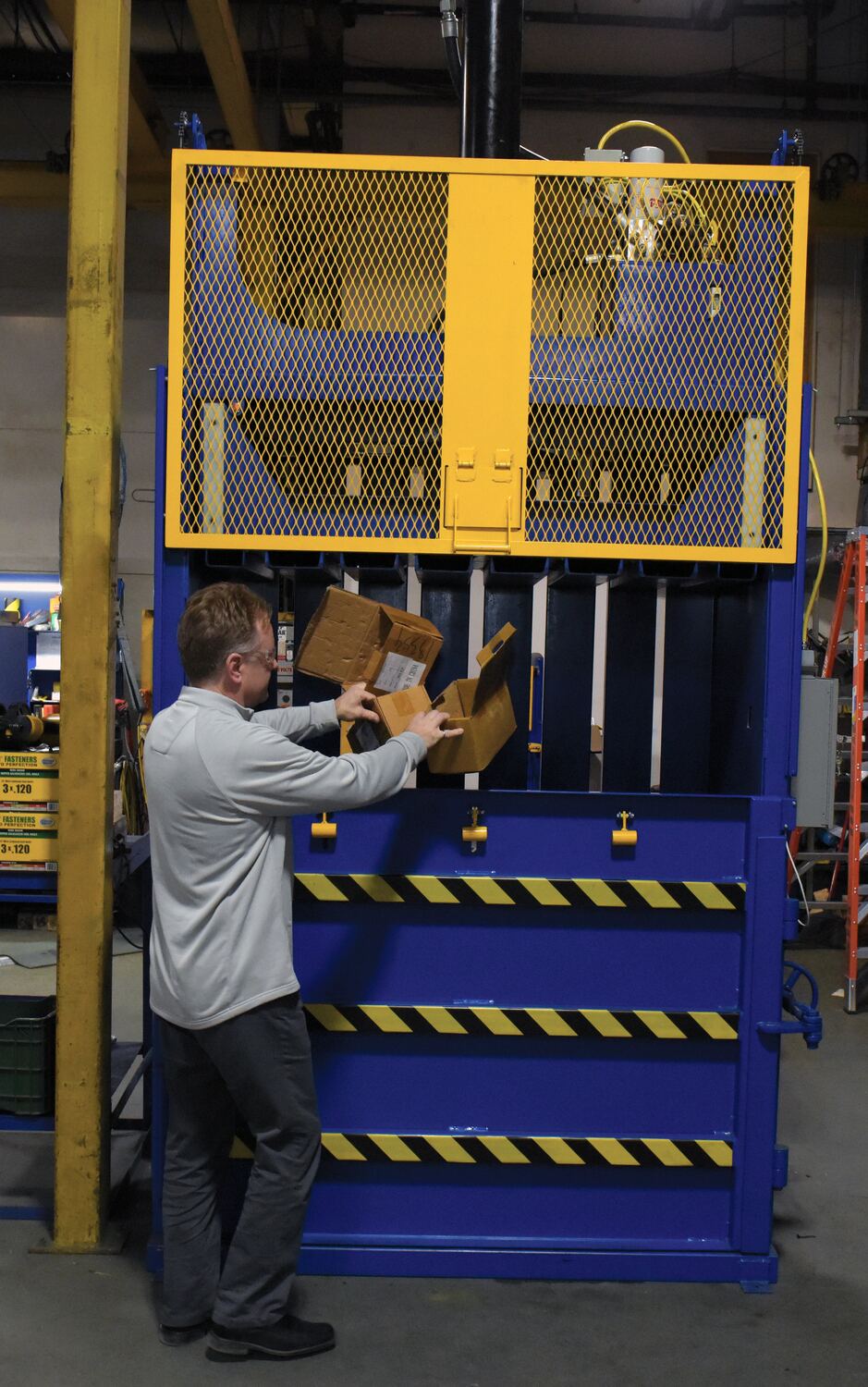
A stock image related to baler machine.
Quality assurance (QA) is a crucial aspect of manufacturing baler machines, ensuring that each unit meets international standards and customer expectations. Understanding the QA processes can help B2B buyers assess the reliability of potential suppliers.
Relevant International Standards for Baler Machine Manufacturing
Several international standards govern the quality assurance processes in baler manufacturing. The most notable include:
- ISO 9001: This standard outlines the requirements for a quality management system, focusing on continuous improvement and customer satisfaction.
- CE Certification: Required for products sold in the European market, CE marking indicates compliance with health, safety, and environmental protection standards.
- API Standards: While more common in the oil and gas industry, some balers designed for heavy-duty applications may also adhere to API standards for performance and safety.
What Are the Key Quality Control Checkpoints in Baler Manufacturing?
Quality control (QC) involves several checkpoints throughout the manufacturing process to ensure that the final product meets all specified requirements. B2B buyers should be aware of these checkpoints to evaluate a supplier’s commitment to quality.
1. Incoming Quality Control (IQC)
IQC focuses on inspecting raw materials upon arrival at the manufacturing facility. This stage ensures that all materials conform to specified standards before they enter the production line. Buyers should ask suppliers about their IQC processes to ensure they source high-quality materials.
2. In-Process Quality Control (IPQC)
During the manufacturing process, IPQC monitors the production stages to identify any defects or deviations from standards. This can involve regular inspections and testing of components as they are formed and assembled. Effective IPQC can prevent issues from escalating, resulting in fewer defects in the final product.
3. Final Quality Control (FQC)
FQC occurs after assembly and finishing, where the entire baler is tested for functionality, safety, and performance. This step may involve load testing, hydraulic pressure tests, and operational checks. B2B buyers should inquire about the FQC procedures to ensure that each baler is thoroughly tested before shipment.
How Can B2B Buyers Verify Supplier Quality Control?
Verifying a supplier’s quality control measures is essential for international buyers to ensure they receive reliable and compliant equipment. Here are several strategies to consider:
1. Conducting Supplier Audits
Audits provide an in-depth look at a supplier’s manufacturing processes and quality assurance practices. Buyers can assess compliance with international standards and evaluate the effectiveness of the supplier’s quality management system.
2. Requesting Quality Reports
Suppliers should be able to provide documentation related to their quality control processes, including test results, inspection reports, and certifications. Buyers should request these documents to ensure transparency and accountability.
3. Utilizing Third-Party Inspections
Employing third-party inspection services can provide an unbiased assessment of a supplier’s quality control practices. These inspections can occur at various stages of production, offering insights into the supplier’s adherence to quality standards.
What Are the Quality Control Nuances for International B2B Buyers?
B2B buyers from diverse regions, including Africa, South America, the Middle East, and Europe, face unique challenges related to quality control in baler machine procurement. Here are some nuances to consider:
1. Understanding Regional Regulations
Each region may have specific regulations and standards that impact the importation of balers. Familiarizing yourself with these requirements can help avoid compliance issues and ensure the equipment meets local standards.
2. Language and Communication Barriers
Effective communication is critical when discussing quality standards and specifications with suppliers. Buyers should ensure that they can clearly articulate their requirements and expectations to avoid misunderstandings.
3. Cultural Differences in Business Practices
Cultural differences can influence how quality is perceived and prioritized. Buyers should be aware of these differences and approach negotiations with an understanding of the supplier’s business culture.
By comprehensively understanding the manufacturing processes and quality assurance measures associated with baler machines, international B2B buyers can make more informed decisions, ensuring they invest in reliable and high-performing equipment.
Practical Sourcing Guide: A Step-by-Step Checklist for ‘baler machine’
When sourcing a baler machine, international B2B buyers must navigate various complexities, including technical specifications, supplier credibility, and operational needs. This step-by-step checklist aims to simplify the procurement process, ensuring that buyers from regions such as Africa, South America, the Middle East, and Europe can make informed decisions.
Step 1: Define Your Technical Specifications
Before initiating your search, it’s essential to outline the technical specifications that align with your operational requirements. Consider the types of materials you will be baling, such as cardboard, plastics, or agricultural waste, as different balers are designed for specific materials. Additionally, determine the expected volume of waste and desired bale size, as this will influence the capacity and model of the baler you need.
Step 2: Research Market Trends and Innovations
Stay updated on the latest market trends and technological advancements in baler machines. Innovations such as automated systems or energy-efficient models can significantly enhance productivity and reduce operating costs. Engaging with industry reports and attending trade shows can provide insights into emerging technologies that may benefit your operations.
Step 3: Evaluate Potential Suppliers
Conduct thorough evaluations of potential suppliers to ensure they meet your needs. Look for suppliers with a proven track record in your industry, and request company profiles, case studies, and references from clients in similar regions. This due diligence will help you gauge their reliability and the quality of their products.
- Check for certifications: Verify that suppliers have relevant certifications, such as ISO standards, which indicate adherence to quality management practices.
Step 4: Request Detailed Quotations
Once you have shortlisted potential suppliers, request detailed quotations that outline pricing, lead times, and after-sales support. A comprehensive quote should include all costs, such as shipping, installation, and training. This transparency helps you avoid hidden fees and allows for better comparison between suppliers.
Step 5: Assess After-Sales Support and Maintenance Services
A baler machine is a long-term investment, and the level of after-sales support can impact your operations significantly. Inquire about the availability of spare parts, maintenance services, and training for your staff. Suppliers that offer robust after-sales support can help minimize downtime and ensure the longevity of your equipment.
- Consider warranty options: Evaluate the warranty terms offered by suppliers to understand the coverage and support you can expect in case of malfunctions.
Step 6: Conduct Site Visits or Virtual Demos
Whenever possible, arrange site visits to the suppliers’ facilities or request virtual demonstrations of the baler machines. This firsthand experience allows you to evaluate the equipment’s performance and suitability for your operations. Observing the machinery in action can also provide insights into the efficiency and ease of use.
Step 7: Finalize the Purchase Agreement
Once you are satisfied with your choice, proceed to finalize the purchase agreement. Ensure that all terms, including delivery timelines, payment conditions, and service agreements, are clearly defined. A well-structured contract protects both parties and sets clear expectations.
By following this structured checklist, international B2B buyers can navigate the complexities of sourcing a baler machine effectively, ensuring that their investment meets operational needs and contributes to their business success.
Comprehensive Cost and Pricing Analysis for baler machine Sourcing
What Are the Key Cost Components for Baler Machines?
When sourcing baler machines, understanding the cost structure is crucial for international B2B buyers. The primary cost components include:
- Materials: The choice of materials significantly impacts the price. High-quality steel and components may increase initial costs but ensure durability and efficiency.
- Labor: Skilled labor is often required for assembly and quality control, particularly for custom or high-spec models. This labor cost can vary significantly depending on the manufacturing location.
- Manufacturing Overhead: This encompasses factory operation costs, utilities, and equipment maintenance, which can add a substantial amount to the overall pricing.
- Tooling: Specialized tools for production can be a one-time investment or ongoing expense, affecting the price based on the complexity of the baler design.
- Quality Control (QC): Rigorous testing and quality assurance processes ensure the reliability of balers, contributing to higher costs but offering peace of mind for buyers.
- Logistics: Shipping costs can vary depending on the size and weight of the baler, as well as the distance to the buyer’s location. Tariffs and import duties may also apply, particularly for buyers in Africa, South America, and the Middle East.
- Margin: Supplier profit margins can differ based on market dynamics and competition. Understanding these margins can help buyers gauge fair pricing.
What Factors Influence Baler Machine Pricing?
Several factors influence the pricing of baler machines, which international buyers should consider:
- Volume/MOQ: Bulk orders often lead to lower per-unit costs. Suppliers may offer discounts for larger quantities, making it beneficial to consolidate orders.
- Specifications and Customization: Custom-designed balers tailored to specific needs can significantly increase costs. Buyers should weigh the benefits of customization against budget constraints.
- Material Quality and Certifications: Machines made from higher-grade materials or those with industry certifications may come at a premium but offer enhanced performance and reliability.
- Supplier Factors: The reputation and reliability of the supplier can influence pricing. Established suppliers may charge more but provide better support and warranty services.
- Incoterms: The shipping terms agreed upon can affect total costs. Understanding Incoterms helps buyers anticipate who bears the costs and risks during transit.
How Can Buyers Negotiate for Better Pricing on Baler Machines?
Effective negotiation strategies can lead to better pricing and terms for baler machine purchases:
- Research Market Prices: Understanding the typical price range for specific baler models can empower buyers during negotiations. Use resources like industry reports and competitor pricing to inform your discussions.
- Leverage Relationships: Building strong relationships with suppliers can foster goodwill and potentially lead to better deals or more favorable terms.
- Discuss Total Cost of Ownership (TCO): Emphasizing the importance of TCO in negotiations can shift the focus from initial costs to long-term value. Highlighting savings from efficiency and reduced maintenance can justify a higher initial price.
- Be Flexible with Specifications: If a buyer can compromise on certain specifications or features, they may achieve a better price. Discussing alternative models can also yield significant savings.
What Are Pricing Nuances for International B2B Buyers?
International buyers, especially from regions like Africa, South America, and the Middle East, should be aware of specific pricing nuances:
- Currency Fluctuations: Variations in currency exchange rates can impact the final price. Buyers should consider locking in prices or negotiating in a stable currency to mitigate risks.
- Import Regulations and Tariffs: Understanding local import regulations and potential tariffs is crucial for calculating the total landed cost of a baler machine.
- Logistical Challenges: Buyers should account for potential delays and increased shipping costs due to logistical challenges in their region, which can affect the overall budget.
Conclusion
When sourcing baler machines, international B2B buyers must navigate a complex landscape of costs and pricing factors. By understanding the cost components, negotiating effectively, and considering regional nuances, buyers can optimize their purchasing strategies and achieve better outcomes. Always remember that indicative prices may vary based on market conditions, so continuous monitoring and engagement with suppliers are essential for successful sourcing.
Alternatives Analysis: Comparing baler machine With Other Solutions
Introduction: What Are the Alternatives to Baler Machines?
When considering waste management and recycling solutions, baler machines are a popular choice due to their efficiency in compressing waste materials. However, there are several alternative technologies and methods that can also achieve similar objectives. This section will compare baler machines with two viable alternatives: compactors and shredders. Each option has its unique advantages and disadvantages, which are essential for international B2B buyers to understand when making procurement decisions.
Comparison Table of Baler Machine and Alternatives
Comparison Aspect | Baler Machine | Compactor | Shredder |
---|---|---|---|
Performance | High compaction ratio; efficient for recycling | Reduces volume significantly; suitable for mixed waste | Effective in reducing material size; prepares waste for further processing |
Cost | High initial investment; variable operating costs | Moderate investment; lower operating costs | Generally lower cost; maintenance can add up |
Ease of Implementation | Requires specific installation space and power supply | Easier to integrate into existing systems | Minimal space requirements; user-friendly |
Maintenance | Regular maintenance needed; parts can be costly | Low maintenance; less frequent servicing | Moderate maintenance; blades require regular sharpening |
Best Use Case | Ideal for businesses with large volumes of recyclables | Suitable for general waste management in urban areas | Best for businesses needing to prepare materials for recycling or disposal |
Detailed Breakdown of Alternatives
Compactor: A Cost-Effective Waste Management Solution
Compactors provide a practical alternative to baler machines, particularly for businesses that manage mixed waste. They significantly reduce the volume of waste, allowing for fewer pickups and lower disposal costs. Compactors are generally easier to implement, requiring less specialized space and simpler setup. However, they may not achieve the same high compaction ratios as balers, which can be a drawback for companies focused on recycling initiatives. Overall, compactors are an excellent choice for urban environments with diverse waste streams.
Shredder: Ideal for Material Preparation
Shredders serve a different purpose than balers but can be a vital part of a waste management strategy. They effectively reduce the size of various materials, making them easier to transport and process. Shredders are generally more affordable than balers, making them appealing for smaller operations. They also require less maintenance than balers, although the blades do need regular sharpening to maintain efficiency. However, shredders may not provide the same volume reduction as balers or compactors, which could lead to increased disposal frequency.
Conclusion: How to Choose the Right Waste Management Solution
For international B2B buyers, selecting the right waste management solution depends on specific operational needs, budget constraints, and the types of materials being processed. Baler machines are ideal for high-volume recyclables, while compactors offer a versatile option for general waste management. Shredders are best suited for businesses focused on material preparation for recycling. Understanding the unique advantages and limitations of each solution will empower buyers to make informed decisions that align with their waste management goals.
Essential Technical Properties and Trade Terminology for baler machine
What Are the Essential Technical Properties of Baler Machines?
When considering the purchase of a baler machine, understanding its technical specifications is crucial for making informed decisions. Here are some of the key properties to evaluate:
1. Compaction Force
Compaction force refers to the pressure applied by the baler to compress materials into bales. This is typically measured in tons and can range from 3 tons in smaller balers to over 60 tons in industrial models. A higher compaction force translates into denser bales, which can reduce transportation costs and maximize storage efficiency. For B2B buyers, selecting a baler with the appropriate force is essential based on the types of materials being processed.
2. Bale Size and Weight
Bale size and weight specifications determine the dimensions and mass of the bales produced. Standard sizes include small bales (30-50 kg) and larger bales (up to 100 kg or more). Understanding the required bale size is critical for logistics and storage; larger bales may reduce handling frequency but require more space. Buyers must consider their operational needs and the volume of materials when selecting a baler.
3. Throughput Capacity
Throughput capacity indicates how much material a baler can process within a specified time frame, often expressed in tons per hour. This metric is vital for businesses with high-volume waste or recycling operations. Buyers should assess their operational demands and ensure that the baler’s throughput aligns with their processing needs to avoid bottlenecks.
4. Material Compatibility
Different balers are designed for specific materials, such as cardboard, plastics, or metals. Understanding the material compatibility is critical to ensure effective operation. For instance, a baler designed for cardboard may not efficiently handle plastics. B2B buyers should clearly define the materials they will be baling to select the right machine.
5. Energy Consumption
Energy consumption is a significant operating cost. Balers vary widely in their energy efficiency, often measured in kilowatt-hours (kWh) per ton of material processed. Evaluating energy consumption can lead to substantial cost savings, especially for operations running multiple shifts. Buyers should consider machines that offer energy-efficient features to minimize long-term expenses.
What Are Common Trade Terms Related to Baler Machines?
Familiarity with trade terminology can streamline the purchasing process. Here are some essential terms relevant to baler machines:
1. OEM (Original Equipment Manufacturer)
An OEM is a company that produces parts and equipment that may be marketed by another manufacturer. For baler machines, understanding whether you are dealing directly with the OEM or a reseller can impact warranty, service, and parts availability. B2B buyers should prioritize OEMs for reliable support.
2. MOQ (Minimum Order Quantity)
MOQ refers to the smallest quantity of a product that a supplier is willing to sell. This term is significant for international buyers who might be looking to import balers. Understanding the MOQ helps in planning purchases and managing inventory effectively.
3. RFQ (Request for Quotation)
An RFQ is a document sent to suppliers requesting pricing and terms for specific products. When sourcing baler machines, submitting an RFQ can help buyers compare offers from multiple manufacturers, ensuring they get the best deal possible.
4. Incoterms (International Commercial Terms)
Incoterms are a set of rules that define the responsibilities of buyers and sellers in international transactions. They clarify who is responsible for shipping, insurance, and tariffs. Understanding Incoterms is essential for B2B buyers from regions like Africa and South America, where international shipping logistics can be complex.
5. Lead Time
Lead time is the duration from placing an order to receiving the product. This can vary significantly between manufacturers and can impact operational planning. Buyers should always inquire about lead times when sourcing balers to align their purchase with operational timelines.
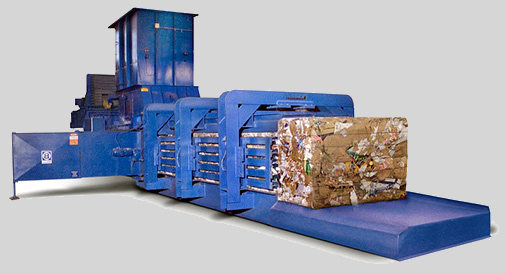
A stock image related to baler machine.
6. Warranty and Service Agreements
These terms outline the manufacturer’s responsibilities regarding repairs and maintenance of the baler machine. A solid warranty and comprehensive service agreement can provide peace of mind for B2B buyers, ensuring support and reducing downtime. Understanding these agreements can influence purchasing decisions significantly.
By grasping these essential technical properties and trade terms, B2B buyers can navigate the complexities of purchasing baler machines more effectively, ensuring that their operations run smoothly and efficiently.
Navigating Market Dynamics and Sourcing Trends in the baler machine Sector
What Are the Current Market Dynamics and Key Trends in the Baler Machine Sector?
The global baler machine market is currently experiencing transformative dynamics driven by technological advancements and increasing demand for waste management solutions. With a rising focus on sustainability, international B2B buyers from regions like Africa, South America, the Middle East, and Europe are prioritizing the acquisition of baler machines that enhance recycling capabilities and reduce waste disposal costs. The market is characterized by a surge in automated and semi-automated balers, which improve efficiency and reduce labor costs. Moreover, buyers are increasingly gravitating towards machines capable of handling diverse materials such as plastics, paper, and textiles, reflecting a broader trend towards multi-functionality in waste processing.
Emerging technologies such as IoT (Internet of Things) integration and real-time monitoring systems are revolutionizing how businesses manage their waste processes. For instance, IoT-enabled balers can provide data analytics on material volumes and operational efficiency, allowing companies to optimize their waste management strategies. Buyers should also consider lead times and availability when sourcing balers, as global supply chain disruptions can impact delivery schedules. Understanding regional market nuances and sourcing from reliable suppliers can help mitigate these risks.
How Does Sustainability Influence Sourcing Trends in the Baler Machine Sector?
Sustainability is not just a trend; it has become a core business principle in the baler machine sector. The environmental impact of waste management practices is prompting international buyers to seek machines that are energy-efficient and capable of maximizing material recovery. The use of eco-friendly materials in manufacturing balers is gaining traction, as buyers demand equipment that aligns with their corporate social responsibility goals.
Furthermore, ethical sourcing practices are becoming increasingly important. Companies are now looking for suppliers that can demonstrate transparency in their supply chains, ensuring that materials are sourced responsibly and sustainably. Certifications such as ISO 14001 (Environmental Management) and adherence to ‘green’ standards can significantly enhance a supplier’s credibility. By prioritizing sustainability, buyers not only improve their environmental footprint but also enhance their brand reputation and competitiveness in the marketplace.
What Is the Brief Evolution of Baler Machines and Their Significance for B2B Buyers?
The evolution of baler machines dates back to the early 20th century, when the first manual balers were developed for agricultural use. Over the decades, technological advancements have transformed these machines into sophisticated pieces of equipment capable of handling various materials efficiently. The introduction of hydraulic systems and automation has significantly improved performance, making balers essential for modern waste management and recycling operations.
For B2B buyers, understanding this evolution is crucial, as it highlights the ongoing innovation in the sector. The shift from manual to automated systems not only enhances productivity but also reflects the industry’s response to increasing environmental regulations and the need for sustainable practices. Buyers who recognize the historical context of baler machines can make more informed decisions when investing in equipment that meets their operational needs while aligning with sustainability goals.
In summary, navigating the baler machine sector requires an awareness of current market dynamics, a commitment to sustainability, and an understanding of the equipment’s evolution. These factors collectively empower international B2B buyers to make informed, strategic sourcing decisions that benefit their businesses and the environment.
Frequently Asked Questions (FAQs) for B2B Buyers of baler machine
-
How do I choose the right baler machine for my business needs?
Selecting the appropriate baler machine involves assessing your operational requirements, including the types of materials you will be baling (e.g., cardboard, plastics, or metals), the volume of waste generated, and the desired bale size and weight. Additionally, consider the machine’s throughput capacity and whether it can handle your expected production rates. It’s also essential to evaluate the space available for installation and operation, as some balers require more room than others. Partnering with a supplier that understands your industry can provide valuable insights and recommendations tailored to your needs. -
What are the key features to look for in a baler machine?
When sourcing a baler machine, focus on features such as compaction force, bale size options, and ease of operation. Automatic tie systems can significantly enhance efficiency, while safety features like emergency stops and clear access points are crucial. Additionally, consider the machine’s energy efficiency, maintenance requirements, and the availability of parts and service support. Lastly, look for options that allow for customization, as this can ensure the machine fits seamlessly into your existing operations. -
What is the typical lead time for ordering a baler machine?
Lead times for baler machines can vary significantly based on the model and manufacturer. Generally, standard machines may have lead times ranging from 2 to 26 weeks. Custom orders or specialized models could take longer, so it’s advisable to discuss timelines with your supplier upfront. Keep in mind that factors such as shipping logistics and customs clearance can also impact delivery schedules, especially for international orders. -
What are the minimum order quantities (MOQ) for baler machines?
Minimum order quantities for baler machines can vary by supplier and the specific model. Typically, manufacturers may set MOQs for bulk orders or customized machines, while standard models may not have strict MOQs. For international buyers, it’s crucial to clarify these terms with your supplier early in the negotiation process to align your purchasing strategy with their requirements. -
What payment terms are commonly offered by baler machine suppliers?
Payment terms can vary widely among suppliers, but common options include upfront payments, deposits with the balance due upon delivery, or payment plans over a specified period. Some suppliers may also offer financing options. It is important to negotiate terms that align with your cash flow situation and to ensure all agreements are documented clearly to avoid misunderstandings. -
How can I verify the credibility of a baler machine supplier?
To vet a baler machine supplier, conduct thorough research by checking their reputation in the industry, reading customer reviews, and requesting references from past clients. Additionally, assess their experience in the market and any certifications or affiliations with industry organizations. A visit to their facility, if feasible, can also provide insight into their manufacturing processes and quality control measures. -
What quality assurance (QA) measures should I expect from baler machine manufacturers?
Reputable baler machine manufacturers typically implement stringent quality assurance measures, including rigorous testing of machines before shipment, adherence to international standards, and certifications like ISO 9001. Request documentation of QA processes, such as inspection reports and warranty details. Understanding the manufacturer’s commitment to quality will help you gauge the reliability and longevity of the equipment. -
What are the logistics considerations for shipping baler machines internationally?
When shipping baler machines internationally, consider factors such as shipping methods, customs regulations, and potential tariffs or duties. Work with suppliers who have experience in exporting heavy machinery to ensure compliance with local regulations in your country. It’s also wise to discuss shipping insurance to protect your investment during transit. Clear communication with your supplier about delivery expectations and logistics support can streamline the process significantly.
Important Disclaimer & Terms of Use
⚠️ Important Disclaimer
The information provided in this guide, including content regarding manufacturers, technical specifications, and market analysis, is for informational and educational purposes only. It does not constitute professional procurement advice, financial advice, or legal advice.
While we have made every effort to ensure the accuracy and timeliness of the information, we are not responsible for any errors, omissions, or outdated information. Market conditions, company details, and technical standards are subject to change.
B2B buyers must conduct their own independent and thorough due diligence before making any purchasing decisions. This includes contacting suppliers directly, verifying certifications, requesting samples, and seeking professional consultation. The risk of relying on any information in this guide is borne solely by the reader.
Strategic Sourcing Conclusion and Outlook for baler machine
As the demand for baler machines grows across various industries, international B2B buyers must prioritize strategic sourcing to maximize value and efficiency. By assessing lead times, pricing structures, and the specific needs of their operations, buyers can ensure they select the right baler type—be it vertical, horizontal, or specialized for recycling purposes. Engaging with reliable suppliers and understanding regional market dynamics is crucial for securing competitive pricing and reducing operational downtime.
How can strategic sourcing enhance your procurement process for baler machines? By leveraging global supply chains, businesses can access advanced technologies and cost-effective solutions tailored to their unique requirements. This approach not only optimizes waste management but also contributes to sustainability goals by facilitating recycling and reducing landfill contributions.
Looking ahead, the baler machine market is poised for innovation, driven by technological advancements and increasing environmental regulations. International buyers from Africa, South America, the Middle East, and Europe should take proactive steps to integrate these machines into their operations, ensuring they remain competitive and compliant. Embrace strategic sourcing today to transform your waste management processes and unlock long-term benefits for your business.