Cut Costs with the Ultimate Homogenizer Machine Guide (2025)
Introduction: Navigating the Global Market for homogenizer machine
In the competitive landscape of international trade, sourcing the right homogenizer machine can pose significant challenges for B2B buyers, particularly those operating in diverse markets across Africa, South America, the Middle East, and Europe. The process of homogenization—essential for industries ranging from food and beverage to pharmaceuticals—demands an understanding of various machine types, their applications, and the suppliers behind them. This guide is designed to navigate the complexities of the global homogenizer market, providing insights into high-pressure and mechanical homogenizers, their operational principles, and the specific needs they fulfill.
Buyers will benefit from a thorough exploration of key factors such as supplier vetting, pricing structures, and the unique considerations for different regional markets. For instance, understanding the nuances of local regulations and availability can significantly impact purchasing decisions. The guide will also delve into how to assess the compatibility of homogenizers with existing production lines and the importance of after-sales support.
By equipping B2B buyers with actionable insights and strategic knowledge, this comprehensive resource empowers informed purchasing decisions. Whether you are in Kenya, South Africa, or elsewhere, you will gain clarity on how to optimize your sourcing process and enhance operational efficiency through the right homogenization technology.
Understanding homogenizer machine Types and Variations
Type Name | Key Distinguishing Features | Primary B2B Applications | Brief Pros & Cons for Buyers |
---|---|---|---|
High-Pressure Homogenizers | Utilizes high pressure to achieve emulsification and particle size reduction. | Dairy, pharmaceuticals, cosmetics | Pros: Efficient for large volumes; versatile. Cons: Higher initial investment. |
High Shear Homogenizers | Features an impeller that creates high shear forces for mixing. | Food processing, sauces, emulsions | Pros: Effective for viscous materials; quick processing. Cons: May require frequent maintenance. |
Ultrasonic Homogenizers | Employs ultrasonic waves for particle dispersion and emulsification. | Biotechnology, pharmaceuticals | Pros: Excellent for small batches; precise control. Cons: Limited scale; more complex operation. |
Mechanical Homogenizers | Incorporates mechanical action for grinding and lysing. | Laboratory applications, tissue samples | Pros: Cost-effective; simple operation. Cons: Limited to small volumes; may not achieve fine emulsions. |
Bead Mill Homogenizers | Uses beads to disrupt cells and homogenize samples. | Research labs, food and beverage | Pros: Highly efficient for tough samples; versatile. Cons: Higher operational costs; requires cleaning between batches. |
What are High-Pressure Homogenizers and Their Applications?
High-pressure homogenizers are designed to apply intense pressure to liquids, forcing them through narrow openings. This process results in high shear forces and cavitation, which effectively reduces particle sizes and creates stable emulsions. They are particularly beneficial in industries such as dairy for milk homogenization, pharmaceuticals for emulsifying ointments, and cosmetics for creating creams. When considering a high-pressure homogenizer, B2B buyers should evaluate the required pressure levels, volume capacity, and maintenance needs, as these machines often come with a higher upfront cost.
How Do High Shear Homogenizers Work?
High shear homogenizers employ an impeller that generates significant shear forces to mix and emulsify products. This technology is especially useful in food processing for sauces and dressings, where a uniform texture is crucial. Buyers should consider the viscosity of their materials and the desired particle size when selecting a high shear homogenizer. While they offer quick processing times and effective mixing, these machines may require regular maintenance due to the wear on blades and other moving parts.
What Are the Benefits of Ultrasonic Homogenizers?
Ultrasonic homogenizers use high-frequency sound waves to disrupt particles and create emulsions. They are particularly well-suited for applications in biotechnology and pharmaceuticals, where precise control over particle size is essential. These machines are ideal for small batch processing, but their complexity and operational limits can be challenges for larger scale operations. B2B buyers should assess their production needs and the specific applications to determine if ultrasonic technology is the right fit for their processes.
What Makes Mechanical Homogenizers Suitable for Laboratories?
Mechanical homogenizers are powered devices that utilize mechanical action to grind, lyse, and homogenize biological samples. They are favored in laboratory settings for their cost-effectiveness and straightforward operation. However, their effectiveness is generally limited to smaller volumes, making them less suitable for large-scale production. When purchasing mechanical homogenizers, buyers should consider the types of samples they will process and whether they need additional features like variable speed settings or specific attachments.
How Do Bead Mill Homogenizers Enhance Sample Processing?
Bead mill homogenizers utilize beads to mechanically disrupt cells and homogenize samples, making them highly effective for tough materials. They are commonly used in research labs and the food and beverage industry for emulsification and particle size reduction. While they provide excellent efficiency and versatility, buyers should be aware of the higher operational costs associated with bead mills and the need for thorough cleaning between batches to prevent cross-contamination.
Key Industrial Applications of homogenizer machine
Industry/Sector | Specific Application of Homogenizer Machine | Value/Benefit for the Business | Key Sourcing Considerations for this Application |
---|---|---|---|
Food & Beverage | Emulsification of sauces and dressings | Improved texture and shelf-life of products | Compliance with food safety regulations and certifications |
Pharmaceuticals | Cell lysis for drug formulation | Enhanced drug efficacy and stability | Equipment validation and scalability for production |
Cosmetics & Personal Care | Formulation of creams and lotions | Consistent product quality and performance | Compatibility with various ingredients and formulations |
Chemical Manufacturing | Mixing of paints and coatings | Uniform color and texture, reducing waste | Robustness to handle viscous materials and continuous operation |
Biotechnology | Homogenization of biological samples for analysis | Accurate and reliable results in research and development | Customization for specific sample types and sizes |
How is a Homogenizer Machine Used in the Food & Beverage Industry?
In the food and beverage sector, homogenizer machines are essential for emulsifying sauces, dressings, and dairy products. By breaking down fat globules, these machines ensure that products maintain a uniform consistency and improved shelf-life. International B2B buyers, especially in regions like Africa and South America, must consider local food safety regulations and certifications when sourcing this equipment. The ability to efficiently process large batches while adhering to safety standards is crucial for maintaining product quality.
What Role Does a Homogenizer Machine Play in Pharmaceuticals?
In pharmaceuticals, homogenizers are vital for cell lysis, which aids in extracting active ingredients for drug formulation. The high shear forces generated during homogenization enhance drug efficacy and stability, leading to more effective therapeutics. Buyers from the Middle East and Europe should prioritize equipment validation and scalability to ensure compliance with stringent regulatory requirements. The ability to produce consistent results in various batch sizes is also a key consideration for pharmaceutical manufacturers.
How is a Homogenizer Machine Beneficial for Cosmetics & Personal Care?
For the cosmetics and personal care industry, homogenizers are used to create stable emulsions in creams and lotions. This process enhances the texture and performance of beauty products, ensuring a high-quality user experience. Buyers should look for machines that can handle diverse formulations, including those with natural ingredients, which are increasingly popular in markets across Europe and Africa. Compatibility with various ingredients is essential for maintaining product efficacy and meeting consumer demands.
How Do Homogenizers Improve Chemical Manufacturing Processes?
In chemical manufacturing, homogenizers facilitate the mixing of paints and coatings, ensuring uniform color and texture. This uniformity not only enhances product appeal but also reduces waste during production. B2B buyers from South America and Africa should consider sourcing robust machines that can handle viscous materials and operate continuously. The ability to maintain consistency in production while optimizing resource use is a significant advantage in this competitive sector.
What Applications Exist in Biotechnology for Homogenizers?
In biotechnology, homogenizers are crucial for the homogenization of biological samples prior to analysis. This process ensures accurate and reliable results in research and development, which is vital for advancing scientific knowledge and product development. International buyers, particularly from Europe and the Middle East, should focus on equipment customization options that cater to specific sample types and sizes. The capacity to adapt to various research needs can significantly enhance operational efficiency in laboratories.
3 Common User Pain Points for ‘homogenizer machine’ & Their Solutions
Scenario 1: Difficulty in Achieving Desired Particle Size Distribution
The Problem:
B2B buyers in industries such as food processing, pharmaceuticals, and cosmetics often face challenges with achieving the desired particle size distribution when using homogenizer machines. For instance, a manufacturer in South Africa might find that their high-pressure homogenizer is not adequately breaking down fat globules in milk, resulting in inconsistent texture and separation. This inconsistency not only affects product quality but can also lead to increased production costs and potential customer dissatisfaction.
The Solution:
To address this issue, it is crucial to properly calibrate and maintain the homogenizer machine. Start by examining the operating parameters, including pressure settings and flow rates. For high-pressure homogenizers, increasing the pressure can enhance the shear force, leading to finer particle sizes. Additionally, consider implementing a multi-pass homogenization process, which involves circulating the product through the machine multiple times to achieve the desired size distribution.
Investing in a homogenizer with adjustable parameters or advanced features, such as a digital control panel, can also provide greater precision. Regular maintenance checks, including cleaning and replacing worn-out parts, will ensure optimal performance. For businesses facing persistent challenges, consulting with equipment manufacturers for tailored solutions or upgrades may yield significant improvements.
Scenario 2: High Operational Costs and Inefficiencies
The Problem:
In the competitive B2B landscape, operational efficiency is paramount. A company in Kenya that utilizes homogenizer machines may struggle with high energy consumption and maintenance costs, leading to an unsustainable operational model. Frequent breakdowns and the need for specialized technicians can further exacerbate these issues, causing production delays and lost revenue.
The Solution:
To mitigate these costs, buyers should consider evaluating the total cost of ownership (TCO) of their homogenization equipment. Opting for energy-efficient models that utilize less power while maintaining high performance can significantly lower operational costs. Additionally, implementing predictive maintenance strategies—such as using sensors to monitor machine performance and detect potential failures before they occur—can reduce downtime and maintenance expenses.
Investing in training for staff on proper machine operation and maintenance can also enhance efficiency. By ensuring that operators are well-versed in the equipment’s capabilities and limitations, businesses can minimize errors that lead to costly repairs. Finally, consider sourcing homogenizers that come with comprehensive service agreements to ensure that any maintenance needs are promptly addressed, reducing the burden on in-house resources.
Scenario 3: Compatibility Issues with Various Materials
The Problem:
B2B buyers often face compatibility challenges when using homogenizer machines for different materials. For example, a cosmetic manufacturer in Brazil may find that their homogenizer is excellent for emulsifying creams but struggles with thicker formulations, leading to inconsistent results. This lack of versatility can hinder product development and limit the ability to expand product lines.
The Solution:
To overcome compatibility issues, buyers should carefully assess their homogenization needs and select equipment designed for versatility. Homogenizers that offer interchangeable parts or adjustable mixing speeds can accommodate a wider range of materials, including both high-viscosity substances and lighter liquids.
Additionally, conducting preliminary tests with various formulations can help determine the optimal settings and configurations for different materials. Collaborating with suppliers to obtain samples of homogenizers that have been proven effective for specific applications can also aid in making an informed purchasing decision. Finally, consider investing in modular homogenizers that allow for upgrades or changes as product lines evolve, ensuring that your equipment can adapt to future needs without requiring complete replacement.
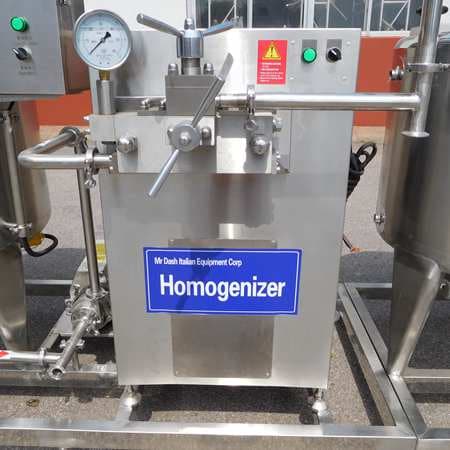
A stock image related to homogenizer machine.
Strategic Material Selection Guide for homogenizer machine
What Are the Key Materials Used in Homogenizer Machines?
When selecting a homogenizer machine, the choice of materials is crucial for ensuring optimal performance and longevity. Here, we analyze four common materials used in homogenizer construction: stainless steel, plastic, ceramic, and glass. Each material has distinct properties, advantages, and limitations that can significantly impact the machine’s functionality and suitability for various applications.
How Does Stainless Steel Impact Homogenizer Performance?
Key Properties: Stainless steel is renowned for its high corrosion resistance, mechanical strength, and ability to withstand high temperatures and pressures. Common grades include 304 and 316, with 316 offering superior resistance to chlorides, making it ideal for food and pharmaceutical applications.
Pros & Cons: The durability of stainless steel ensures a long lifespan, making it a cost-effective option in the long run. However, it is more expensive than other materials and can be complex to manufacture due to the need for precision machining.
Impact on Application: Stainless steel is compatible with a wide range of media, including acidic and alkaline substances. Its non-reactive nature makes it suitable for applications in the food and pharmaceutical industries, where contamination must be avoided.
Considerations for International Buyers: Buyers from regions like Africa and South America should ensure compliance with international standards such as ASTM and ISO. Additionally, the availability of stainless steel grades may vary, impacting procurement timelines.
What Role Does Plastic Play in Homogenizer Machines?
Key Properties: Plastics such as polypropylene and polycarbonate are lightweight, resistant to many chemicals, and can be molded into complex shapes.
Pros & Cons: The primary advantage of plastic is its lower cost and ease of manufacturing. However, plastics generally have lower temperature and pressure ratings compared to metals, limiting their use in high-stress applications.
Impact on Application: Plastic homogenizers are ideal for applications involving sensitive biological samples, as they minimize contamination risks. However, they may not be suitable for high-temperature or high-pressure processes.
Considerations for International Buyers: Buyers should verify that the plastic materials used comply with food safety standards, especially in the food and beverage sector. Regulatory compliance can vary significantly across regions.
How Do Ceramic Materials Enhance Homogenizer Efficiency?
Key Properties: Ceramics are characterized by their hardness, wear resistance, and ability to maintain structural integrity at high temperatures.
Pros & Cons: The durability and chemical resistance of ceramics make them suitable for abrasive materials. However, they can be brittle and more expensive than metals and plastics, which may deter some buyers.
Impact on Application: Ceramics are particularly effective in applications requiring the homogenization of tough materials, such as certain biological samples or industrial chemicals.
Considerations for International Buyers: Buyers should consider the availability of ceramic components and their compatibility with existing homogenizer systems. Compliance with local and international standards is also crucial.
What Advantages Does Glass Offer in Homogenizer Construction?
Key Properties: Glass is chemically inert, transparent, and can withstand a wide range of temperatures. It is often used for laboratory-grade homogenizers.
Pros & Cons: Glass homogenizers offer excellent resistance to chemical reactions and are easy to clean. However, they are fragile and can break easily, which may lead to higher maintenance costs.
Impact on Application: Glass is particularly suitable for applications in laboratory settings where sample visibility is essential. It is often used for small-scale homogenization tasks, especially in research.
Considerations for International Buyers: Buyers should assess the fragility of glass components and ensure that they meet the specific requirements of their applications. Additionally, transportation and handling logistics should be considered, particularly in regions with challenging infrastructure.
Summary Table of Material Selection for Homogenizer Machines
Material | Typical Use Case for homogenizer machine | Key Advantage | Key Disadvantage/Limitation | Relative Cost (Low/Med/High) |
---|---|---|---|---|
Stainless Steel | Food and pharmaceutical applications | High durability and corrosion resistance | Higher cost and manufacturing complexity | High |
Plastic | Biological sample homogenization | Lightweight and cost-effective | Limited temperature and pressure ratings | Low |
Ceramic | Abrasive material homogenization | Excellent wear and chemical resistance | Brittleness and higher cost | Medium |
Glass | Laboratory-grade homogenization | Chemically inert and easy to clean | Fragility and potential for breakage | Medium |
This strategic material selection guide provides essential insights for international B2B buyers, enabling them to make informed decisions based on their specific application needs and regional considerations.
In-depth Look: Manufacturing Processes and Quality Assurance for homogenizer machine
What Are the Key Manufacturing Processes for Homogenizer Machines?
The manufacturing of homogenizer machines involves a series of well-defined stages, each critical for ensuring the performance and reliability of the final product. Here’s a breakdown of the main stages in the manufacturing process:
1. Material Preparation: What Materials Are Used?
The first step in the manufacturing process is material preparation. Common materials include stainless steel, which is favored for its durability and resistance to corrosion, especially in food and pharmaceutical applications. Other materials may include high-grade plastics and specialized alloys depending on the specific application of the homogenizer.
In this stage, raw materials are sourced from verified suppliers, ensuring they meet relevant international standards. Buyers should inquire about the material specifications and certifications to ensure compliance with industry standards.
2. Forming: How Are Homogenizer Components Shaped?
The forming stage involves various techniques such as machining, welding, and casting. Advanced CNC (Computer Numerical Control) machines are typically employed to ensure precision in shaping components like valves, chambers, and impellers.
For high-pressure homogenizers, specialized forming techniques are utilized to create components that can withstand extreme pressures. It’s essential for buyers to understand the forming methods employed by their suppliers, as these directly impact the quality and longevity of the machines.
3. Assembly: How Are Homogenizer Machines Assembled?
Once individual components are formed, they move to the assembly stage. This process may be manual or automated, depending on the scale of production. Key components are assembled, including the motor, pressure valves, and control systems.
During assembly, manufacturers perform initial inspections to ensure all components fit correctly and function as intended. Buyers should ask about the assembly techniques used and the skill level of the personnel involved, as these factors contribute to the overall quality of the machine.
4. Finishing: What Final Touches Are Applied?
The finishing stage includes surface treatments such as polishing, coating, or anodizing to enhance the machine’s durability and aesthetic appeal. This stage may also involve rigorous cleaning processes to remove any contaminants that could affect performance.
Buyers should inquire about the finishing processes and any certifications associated with them, such as food safety standards, particularly for machines intended for food and beverage applications.
How Is Quality Assurance Managed in Homogenizer Manufacturing?
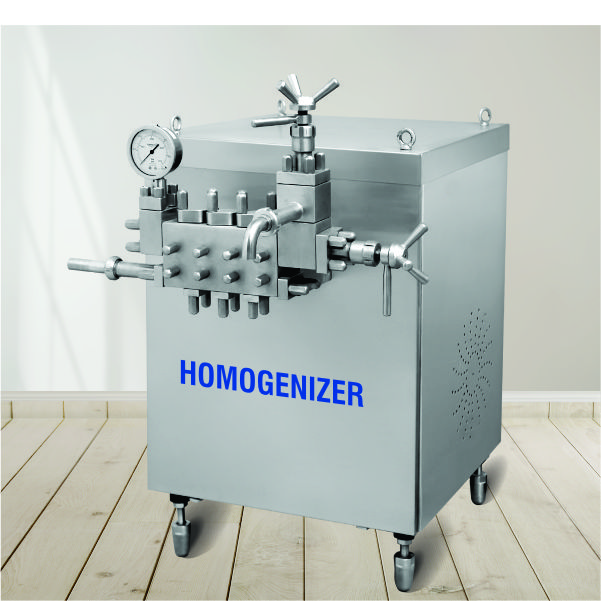
A stock image related to homogenizer machine.
Quality assurance (QA) is a crucial aspect of the manufacturing process, ensuring that homogenizer machines meet both performance and safety standards. Here’s how QA is typically structured:
International Standards: Which Standards Should Buyers Look For?
Most manufacturers adhere to international quality management standards, such as ISO 9001, which outlines requirements for a quality management system. Additionally, industry-specific certifications like CE (Conformité Européenne) for products sold in Europe and API (American Petroleum Institute) for applications in the oil and gas sector may also apply.
Buyers from Africa, South America, the Middle East, and Europe should ensure that their suppliers have these certifications, as they demonstrate compliance with globally recognized quality standards.
Quality Control Checkpoints: What Are the Key Stages?
Quality control (QC) typically involves several checkpoints during the manufacturing process:
-
Incoming Quality Control (IQC): This is the first line of defense where raw materials are inspected before production begins. Suppliers should provide documentation proving that materials meet specified standards.
-
In-Process Quality Control (IPQC): During manufacturing, ongoing inspections are conducted to monitor the production process. This ensures that any deviations from the standards are identified and rectified promptly.
-
Final Quality Control (FQC): After assembly, a thorough inspection and testing phase ensures the machine meets all specifications. This may include performance testing under simulated operating conditions.
Common Testing Methods: How Are Homogenizers Tested for Quality?
Testing methods may vary based on the type of homogenizer and its intended application. Common methods include:
-
Pressure Testing: For high-pressure homogenizers, ensuring that the machine can withstand operational pressures without leaks is critical.
-
Performance Testing: Evaluating the machine’s ability to achieve the desired particle size or emulsion stability is essential, often conducted using standardized testing protocols.
-
Durability Testing: Machines may undergo stress tests to simulate long-term usage and identify potential failure points.
How Can B2B Buyers Verify Supplier Quality Assurance?
For international B2B buyers, verifying a supplier’s quality assurance processes is essential to mitigate risks. Here are actionable steps:
Conducting Audits: What Should Buyers Look For?
Buyers should consider conducting on-site audits of potential suppliers. During these audits, focus on:
-
Production Processes: Observe the manufacturing environment and processes to ensure adherence to best practices.
-
Quality Management Systems: Review documentation related to quality control processes and certifications.
-
Employee Training: Evaluate the training programs for staff involved in manufacturing and quality assurance.
Requesting Reports: What Documentation Is Important?
Ask suppliers for detailed quality assurance reports, including:
-
Test Results: Documentation of performance testing results and compliance with international standards.
-
Certification Copies: Copies of relevant certifications (e.g., ISO 9001, CE) should be readily available.
-
Quality Control Records: Historical data on past QC processes and outcomes can provide insights into a supplier’s reliability.
Engaging Third-Party Inspectors: How Can Independent Verification Help?
Utilizing third-party inspection services can provide an unbiased evaluation of a supplier’s quality assurance practices. Independent inspectors can verify compliance with standards and assess whether the manufacturing processes meet the buyer’s requirements.
Conclusion: Ensuring Quality in Homogenizer Machine Sourcing
For international B2B buyers, particularly those from Africa, South America, the Middle East, and Europe, understanding the manufacturing processes and quality assurance practices of homogenizer machine suppliers is vital. By focusing on material preparation, forming, assembly, and finishing, alongside robust quality control measures, buyers can make informed decisions that ensure they procure reliable and high-quality equipment tailored to their specific needs.
Practical Sourcing Guide: A Step-by-Step Checklist for ‘homogenizer machine’
In the competitive landscape of international B2B procurement, sourcing a homogenizer machine requires careful consideration of various factors. This guide provides a practical checklist to help buyers streamline their sourcing process, ensuring they make informed decisions that align with their operational needs.
Step 1: Define Your Technical Specifications
Before reaching out to suppliers, clearly outline the technical specifications required for your homogenizer machine. Consider factors such as:
– Type of homogenization needed: Will you be processing liquids, solids, or both?
– Desired capacity: Determine the volume you need to process, as this will influence the size and power of the machine.
– Material compatibility: Ensure the machine is suitable for the specific materials you intend to homogenize, especially if they are abrasive or corrosive.
Step 2: Research Different Types of Homogenizers
Understand the various types of homogenizers available in the market. Common types include:
– High-pressure homogenizers: Ideal for emulsions and cell lysis, suitable for larger volumes.
– High-shear mixers: Effective for mixing dissimilar liquids and solids.
– Ultrasonic homogenizers: Utilize sound energy for particle size reduction.
Knowing the pros and cons of each type will help you select the right equipment for your needs.
Step 3: Evaluate Potential Suppliers
It’s crucial to vet suppliers thoroughly before making a commitment. Look for:
– Company reputation: Check online reviews and industry ratings.
– Experience in your sector: Suppliers familiar with your industry will better understand your needs.
– References: Ask for case studies or testimonials from other clients, particularly those in similar geographical regions like Africa, South America, or Europe.
Step 4: Verify Supplier Certifications
Ensure that potential suppliers hold relevant certifications that demonstrate their compliance with industry standards. Important certifications may include:
– ISO certifications: Indicate quality management systems.
– CE marking: Required for products sold in the European Economic Area.
– Local regulatory compliance: Particularly important in regions like Africa and the Middle East where regulations may vary.
Step 5: Request Quotes and Compare Costs
Once you have shortlisted suppliers, request detailed quotes. Ensure the quotes include:
– Total cost of ownership: Look beyond initial purchase price and consider maintenance, operation, and potential downtime.
– Warranty and service terms: Understand the support available post-purchase.
– Delivery timelines: Confirm how quickly you can receive the machine, as delays can impact your operations.
Step 6: Assess After-Sales Support and Training
Consider the level of after-sales support offered by the supplier. Key aspects to look for include:
– Technical support availability: Ensure there is accessible support for troubleshooting.
– Training programs: Suppliers should provide training for your staff to ensure safe and effective operation of the homogenizer.
Step 7: Conduct a Final Review Before Purchase
Before finalizing your purchase, conduct a comprehensive review that includes:
– Cross-checking specifications against your initial requirements: Ensure that the selected model meets all your operational needs.
– Final discussions with the supplier: Address any last-minute questions or concerns regarding the machine or contract terms.
By following this checklist, international B2B buyers can make informed decisions when sourcing a homogenizer machine, ensuring they select the right equipment that meets their specific needs and operational goals.
Comprehensive Cost and Pricing Analysis for homogenizer machine Sourcing
Understanding the cost and pricing structure for sourcing homogenizer machines is critical for international B2B buyers, especially those operating in regions like Africa, South America, the Middle East, and Europe. This analysis will break down cost components, identify pricing influencers, and provide actionable buyer tips for negotiating better deals.
What Are the Key Cost Components for Homogenizer Machines?
-
Materials: The cost of raw materials significantly impacts the overall pricing of homogenizer machines. High-quality stainless steel and specialized alloys used in manufacturing can increase costs. Additionally, the choice between standard and customized components will affect material expenses.
-
Labor: Labor costs vary by region and the complexity of the homogenizer design. Skilled labor is required for assembly, particularly for high-pressure and ultrasonic models, which may command higher wages. Countries with lower labor costs can offer competitive pricing, but this may also impact quality.
-
Manufacturing Overhead: This includes costs associated with factory operations such as utilities, maintenance, and administrative expenses. Manufacturers with advanced facilities may have higher overheads, which can translate to higher prices.
-
Tooling: The cost of tools and machinery used in the production process is a significant factor. Specialized tooling for high-precision homogenizers can be expensive, particularly if the equipment is designed for specific applications.
-
Quality Control (QC): Implementing rigorous QC processes ensures that machines meet specified standards, but this adds to the overall cost. Certifications such as ISO can further enhance the price due to the associated compliance costs.
-
Logistics: Shipping and handling costs can vary widely based on the destination and the weight/size of the homogenizer. For international buyers, understanding Incoterms is crucial to managing these costs effectively.
-
Margin: Manufacturer margins vary based on market positioning and competition. Established brands may have higher margins due to perceived quality and reliability.
How Do Volume and Customization Affect Pricing?
Volume/MOQ: Ordering in bulk can significantly reduce the price per unit. Manufacturers often provide tiered pricing, where larger orders receive discounts. Buyers should consider their long-term needs to optimize purchasing quantities.
Specifications and Customization: Custom features or specifications can lead to increased costs. Buyers should clearly define their requirements upfront to avoid unexpected expenses. Collaborating with manufacturers to identify standard options that meet their needs can help mitigate costs.
What Influences Pricing for International Buyers?
Materials and Quality Certifications: The materials used and the certifications held by the manufacturer can influence pricing. Machines made from superior materials with recognized certifications typically command higher prices but may offer better performance and longevity.
Supplier Factors: The reputation and reliability of the supplier play a critical role in pricing. Well-established suppliers may charge more due to their proven track record, while emerging suppliers might offer lower prices to gain market share.
Incoterms: Understanding Incoterms is essential for international buyers. They dictate who bears the costs and risks during transportation, which can significantly affect the total cost of ownership.
What Are Effective Negotiation Tips for B2B Buyers?
-
Research Market Prices: Familiarize yourself with the average market prices for different types of homogenizers to inform your negotiations.
-
Leverage Volume Discounts: If you anticipate ongoing needs, negotiate based on volume to secure better pricing.
-
Request Transparent Pricing: Ask suppliers to break down costs, allowing you to identify areas for potential savings.
-
Consider Total Cost of Ownership (TCO): Evaluate not just the purchase price, but also maintenance, operational costs, and longevity of the equipment when making decisions.
-
Build Relationships: Establishing long-term relationships with suppliers can lead to better pricing and service over time.
Conclusion
Understanding the comprehensive cost structure and pricing influences of homogenizer machines is vital for international B2B buyers. By considering materials, labor, logistics, and other factors, and leveraging effective negotiation strategies, buyers can make informed decisions that enhance their operational efficiency and cost-effectiveness. Always remember that prices can vary significantly based on specifications, volume, and supplier reputation, so thorough due diligence is essential in the sourcing process.
Alternatives Analysis: Comparing homogenizer machine With Other Solutions
When considering the optimal method for achieving homogenization in various industrial applications, it is essential to evaluate alternatives to the traditional homogenizer machine. Each method has unique characteristics that can affect performance, cost, and operational efficiency. Below, we compare homogenizer machines against two viable alternatives: high shear mixers and ultrasonic homogenizers.
Comparison Table of Homogenizer Machine and Alternatives
Comparison Aspect | Homogenizer Machine | High Shear Mixer | Ultrasonic Homogenizer |
---|---|---|---|
Performance | High efficiency for emulsions and cell lysis | Effective for mixing dissimilar liquids | Excellent for breaking down particles and cells |
Cost | $21,557 – $50,400 USD | $10,000 – $30,000 USD | $5,000 – $15,000 USD |
Ease of Implementation | Moderate; requires setup and calibration | Simple; often plug-and-play | Moderate; requires technical knowledge |
Maintenance | Regular maintenance needed | Low maintenance | Moderate; requires care to avoid overheating |
Best Use Case | Large-scale emulsions and homogenization | Food processing and cosmetics | Laboratory applications and small-scale production |
What are the Benefits and Drawbacks of High Shear Mixers?
High shear mixers utilize a rapidly rotating impeller to create a high-speed flow that effectively breaks down and mixes materials. They are particularly advantageous in industries such as food processing, where they can quickly blend thick mixtures like sauces or creams. The simplicity of their design often allows for easy implementation, making them a popular choice for many manufacturers. However, while they are effective for certain applications, they may not achieve the same level of particle size reduction as homogenizer machines, which can be critical in specific formulations.
How Do Ultrasonic Homogenizers Work and What Are Their Pros and Cons?
Ultrasonic homogenizers employ sound waves to induce cavitation in liquids, leading to the disruption of particles. This technology is particularly suitable for applications requiring precise control over particle size, such as in pharmaceuticals and biotechnology. They are compact and generally less expensive than high-pressure homogenizers, making them accessible for smaller laboratories. However, their performance can be limited when processing large volumes, and they may require more technical knowledge to operate effectively, especially in maintaining optimal temperature and pressure conditions.
Conclusion: How Should B2B Buyers Choose the Right Solution?
For international B2B buyers, selecting the right homogenization method depends on several factors, including application requirements, budget constraints, and operational capacities. Homogenizer machines are ideal for large-scale operations needing consistent emulsification and particle size reduction. High shear mixers serve well for straightforward mixing tasks in the food and cosmetic industries, while ultrasonic homogenizers offer precision for laboratory applications. Assessing the specific needs of your operation, including volume, desired particle size, and budget, will guide you in choosing the most suitable solution for your homogenization needs.
Essential Technical Properties and Trade Terminology for homogenizer machine
What Are the Essential Technical Properties of Homogenizer Machines?
When evaluating homogenizer machines for purchase, international B2B buyers should consider several critical technical specifications. These properties not only affect the performance of the machine but also influence operational efficiency and product quality.
1. Material Grade: Why Is It Important?
The material grade of a homogenizer significantly impacts its durability and resistance to corrosion, especially in industries like food and pharmaceuticals where hygiene is paramount. Stainless steel is the most common material due to its strength and ease of cleaning. Buyers should ensure that the homogenizer’s materials comply with industry standards like FDA or GMP, which assures that products processed meet safety regulations.
2. Pressure Rating: How Does It Affect Performance?
The pressure rating of a homogenizer indicates the maximum pressure it can handle during operation. High-pressure homogenizers can achieve pressures up to 30,000 psi, which is essential for applications requiring emulsification or particle size reduction. Understanding the required pressure for specific applications allows buyers to select machines that optimize performance and ensure product consistency.
3. Flow Rate: What Should Buyers Look For?
Flow rate, measured in liters per hour (L/h), determines how much material a homogenizer can process over a given time. A higher flow rate is advantageous for large-scale operations, allowing for increased productivity and reduced processing time. Buyers need to match the flow rate with their production demands to avoid bottlenecks in the manufacturing process.
4. Tolerance Levels: Why Do They Matter?
Tolerance levels refer to the precision with which the homogenizer can achieve the desired particle size or emulsion stability. Tighter tolerances ensure that the end product meets specific quality standards, which is crucial in competitive markets. Buyers should evaluate the machine’s tolerance capabilities to ensure compliance with their quality assurance protocols.
5. Power Consumption: How Does It Impact Operational Costs?
Power consumption is an often-overlooked specification that can affect the total cost of ownership. Homogenizers with higher power requirements may lead to increased energy costs, particularly in high-volume operations. Buyers should consider energy-efficient models that reduce operational expenses while maintaining performance.
What Are Common Trade Terminologies Used in the Homogenizer Industry?
Understanding industry jargon is essential for effective communication during the purchasing process. Here are several key terms that international B2B buyers should familiarize themselves with:
1. OEM (Original Equipment Manufacturer): What Does It Mean?
OEM refers to companies that manufacture products that are sold under another company’s brand. In the context of homogenizers, buyers may encounter OEM parts that ensure compatibility and reliability. Understanding OEM relationships can help buyers secure quality components and service.
2. MOQ (Minimum Order Quantity): Why Is It Relevant?
MOQ indicates the smallest number of units a supplier is willing to sell. This term is crucial for B2B buyers, as it affects inventory management and cash flow. Knowing the MOQ helps in planning purchases and avoiding overstocking or stockouts.
3. RFQ (Request for Quotation): How Should It Be Used?
An RFQ is a formal request to suppliers for pricing and terms on specified products. For homogenizer machines, submitting an RFQ allows buyers to compare different suppliers’ offerings and negotiate better deals. This process is vital for making informed purchasing decisions.
4. Incoterms (International Commercial Terms): Why Are They Important?
Incoterms define the responsibilities of buyers and sellers in international shipping. Familiarity with terms like FOB (Free on Board) or CIF (Cost, Insurance, and Freight) helps buyers understand their obligations regarding shipping costs, insurance, and delivery points, which can significantly impact total landed costs.
5. Lead Time: What Should Buyers Expect?
Lead time refers to the time it takes from placing an order to receiving the product. Understanding lead times helps buyers plan their production schedules and manage inventory effectively. This is particularly important for businesses that rely on timely delivery to meet customer demands.
By grasping these technical properties and industry terminologies, international B2B buyers can make informed decisions when investing in homogenizer machines, ensuring they select the right equipment for their operational needs.
Navigating Market Dynamics and Sourcing Trends in the homogenizer machine Sector
What Are the Current Trends Influencing the Homogenizer Machine Market?
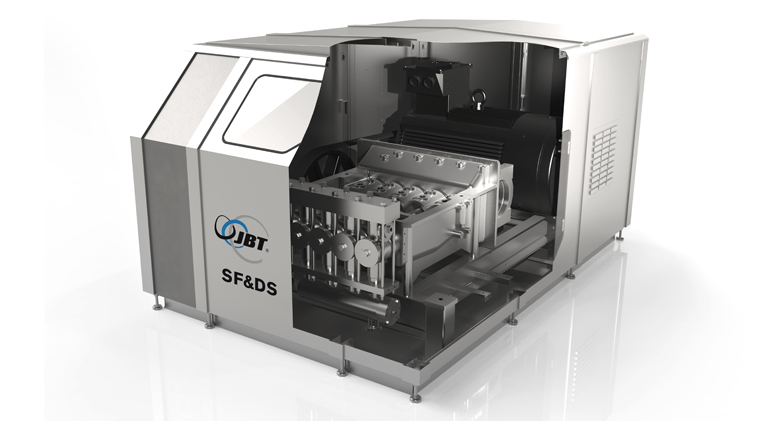
A stock image related to homogenizer machine.
The homogenizer machine sector is witnessing significant growth driven by several global factors. One of the primary drivers is the increasing demand for high-quality emulsions and suspensions in food and beverage, pharmaceuticals, and cosmetics industries. As international standards for product quality continue to rise, manufacturers are compelled to invest in advanced homogenization technology to meet these requirements.
Emerging technologies such as high-pressure homogenizers and ultrasonic homogenizers are becoming increasingly popular due to their ability to achieve superior particle size reduction and improved product consistency. Additionally, the rise of automation and Industry 4.0 technologies is shaping sourcing trends, with many manufacturers looking for machines that integrate seamlessly with digital systems for enhanced operational efficiency.
International B2B buyers, particularly from regions like Africa, South America, the Middle East, and Europe, should also be aware of the growing trend towards customization in homogenizer machines. Buyers are increasingly seeking equipment tailored to their specific processing needs, which calls for close collaboration with suppliers. Moreover, the market dynamics are influenced by fluctuating raw material costs and supply chain disruptions, necessitating strategic sourcing practices to mitigate risks.
How Is Sustainability Shaping the Sourcing of Homogenizer Machines?
In today’s market, sustainability has emerged as a crucial consideration for B2B buyers in the homogenizer machine sector. Companies are increasingly focused on the environmental impact of their operations, and this extends to the equipment they purchase. High-energy consumption and waste generation associated with traditional homogenizers are prompting buyers to seek energy-efficient and environmentally friendly alternatives.
Ethical sourcing is also gaining traction, with buyers prioritizing suppliers who adhere to sustainable practices and provide transparency in their supply chains. This includes the use of recyclable materials, energy-efficient manufacturing processes, and adherence to international environmental standards. Certifications such as ISO 14001 and Green Seal are becoming vital indicators of a supplier’s commitment to sustainability.
Moreover, many manufacturers are now offering ‘green’ homogenizer models designed to minimize environmental impact without compromising performance. International buyers should assess potential suppliers based on their sustainability practices and the certifications they hold, ensuring that their sourcing decisions align with their corporate social responsibility goals.
How Has the Homogenizer Machine Evolved Over Time?
The evolution of homogenizer machines is marked by significant technological advancements that have transformed their functionality and efficiency. Initially, homogenizers were primarily mechanical devices designed for simple mixing and emulsification tasks. However, as industries grew more complex, the need for precision and consistency led to the development of high-pressure and high-shear homogenizers.
Over the decades, innovations such as ultrasonic homogenization and advanced control systems have enabled manufacturers to achieve finer particle sizes and improved product quality. The integration of digital technologies has further revolutionized the sector, allowing for real-time monitoring and adjustments to the homogenization process.
Today, the homogenizer machine market continues to advance, with an increasing focus on automation, energy efficiency, and sustainable practices, making it a dynamic field for international B2B buyers to explore. Understanding this evolution can help buyers make informed decisions when sourcing equipment that meets their operational needs while aligning with modern standards of sustainability and efficiency.
Frequently Asked Questions (FAQs) for B2B Buyers of homogenizer machine
-
How do I choose the right homogenizer machine for my specific application?
Choosing the right homogenizer depends on the materials you are working with and the desired outcome. For emulsions or cell lysis, high-pressure homogenizers are recommended, while high-shear mixers are suitable for applications requiring particle size reduction. Consider the volume you need to process; bench-top models work well for smaller batches, whereas industrial units are necessary for larger operations. Consulting with suppliers about your specific application can also provide tailored recommendations. -
What is the best homogenizer machine for emulsification processes?
High-pressure homogenizers are typically the best choice for emulsification processes. They create a high shear environment that allows for the effective mixing of immiscible liquids, such as oil and water, resulting in stable emulsions. Models like the ShearJet HL60 or the Micro DeBEE High Pressure Homogenizer are highly regarded in the industry for their efficiency and ability to produce consistent results. It’s crucial to evaluate the specifications of each model to ensure it meets your production needs. -
What are the typical lead times for ordering homogenizer machines internationally?
Lead times can vary significantly based on the supplier’s location, manufacturing capabilities, and shipping options. Generally, expect anywhere from 2-6 weeks for standard models. Custom orders may take longer, so it’s advisable to discuss timelines upfront with your supplier. For urgent needs, some suppliers offer stock units that can ship within 48 hours. Ensure you factor in potential customs delays when planning your purchase. -
What are the minimum order quantities (MOQs) for homogenizer machines?
Minimum order quantities can vary by supplier and model. Many manufacturers will have a MOQ for bulk orders, especially for customized machines. However, some suppliers may offer single units for trial purposes, particularly for laboratory-grade equipment. Always clarify MOQs with the supplier before placing an order to avoid unexpected costs or delays. -
How can I verify the quality of a homogenizer machine before purchasing?
To ensure quality, consider requesting samples of products processed with the homogenizer you intend to buy. Reviewing certifications such as ISO or CE compliance can also provide assurance of quality standards. Additionally, ask for references or testimonials from other clients in your industry. Visiting the supplier’s facility or attending trade shows can also offer insights into their quality assurance processes. -
What payment terms should I negotiate when buying homogenizer machines?
Payment terms can vary widely, but it’s common to negotiate terms such as a deposit followed by the balance upon delivery. Some suppliers may offer financing options or extended payment plans, especially for larger orders. It’s essential to clarify terms related to currency, payment methods (e.g., wire transfer, letter of credit), and any potential penalties for late payments. Always ensure the terms are documented in the purchase agreement. -
What logistics considerations should I be aware of when importing homogenizer machines?
When importing homogenizer machines, consider shipping methods, customs duties, and import regulations specific to your country. Air freight is faster but more expensive, while sea freight is economical for larger units but takes longer. Work with a reliable freight forwarder familiar with machinery imports to navigate customs clearance efficiently. Also, ensure that the supplier provides proper documentation, including invoices and packing lists, to facilitate smooth customs processing. -
How can I ensure after-sales support and maintenance for my homogenizer machine?
Before purchasing, inquire about the supplier’s after-sales support services, including warranty terms, spare parts availability, and technical support. Some suppliers offer maintenance contracts to ensure your equipment remains operational. It’s beneficial to choose suppliers with a local presence or those who can provide remote assistance. Establishing a good relationship with your supplier can also enhance the support you receive post-purchase, ensuring your operations run smoothly.
Important Disclaimer & Terms of Use
⚠️ Important Disclaimer
The information provided in this guide, including content regarding manufacturers, technical specifications, and market analysis, is for informational and educational purposes only. It does not constitute professional procurement advice, financial advice, or legal advice.
While we have made every effort to ensure the accuracy and timeliness of the information, we are not responsible for any errors, omissions, or outdated information. Market conditions, company details, and technical standards are subject to change.
B2B buyers must conduct their own independent and thorough due diligence before making any purchasing decisions. This includes contacting suppliers directly, verifying certifications, requesting samples, and seeking professional consultation. The risk of relying on any information in this guide is borne solely by the reader.
Strategic Sourcing Conclusion and Outlook for homogenizer machine
In conclusion, effective strategic sourcing of homogenizer machines is essential for international B2B buyers aiming to enhance their production capabilities. The diverse range of homogenizers—high-pressure, high-shear, and ultrasonic—offers unique advantages tailored to specific applications across industries such as food and beverage, pharmaceuticals, and biotechnology. By understanding the intricacies of each type, buyers can make informed decisions that align with their operational needs and budget constraints.
What key factors should international buyers consider when sourcing homogenizer machines? Price, compatibility with existing systems, and supplier reliability are critical elements that influence the overall value. Engaging with reputable suppliers who provide comprehensive support and service can also mitigate risks associated with equipment downtime and maintenance.
Looking ahead, the demand for advanced homogenization technology is poised to grow, particularly in emerging markets across Africa, South America, the Middle East, and Europe. Buyers are encouraged to leverage this momentum by exploring innovative solutions that enhance productivity and product quality. By investing in the right homogenizer, businesses can not only streamline their processes but also position themselves competitively in the global marketplace. Consider reaching out to trusted suppliers today to discuss your specific needs and unlock new opportunities for growth.