Cut Costs with the Ultimate Packaging Machine Guide (2025)
Introduction: Navigating the Global Market for packaging machine
In an increasingly competitive global marketplace, sourcing the right packaging machines can be a daunting challenge for international B2B buyers. With diverse needs ranging from flexible packaging solutions to robust carton systems, understanding the vast array of options available is crucial. This guide serves as a comprehensive resource, exploring various types of packaging machines, their applications across industries, and essential criteria for supplier vetting. We delve into cost considerations, including financing options, to help businesses make informed purchasing decisions that align with their operational goals.
International buyers, particularly those from Africa, South America, the Middle East, and Europe, face unique market dynamics and logistical challenges. This guide empowers you to navigate these complexities by providing actionable insights tailored to your region’s specific needs. Whether you are seeking vertical form fill seal machines for food products or horizontal flow wrappers for non-food items, our detailed breakdown will equip you with the knowledge needed to select the best machinery for your operations.
By leveraging the information in this guide, you can streamline your procurement process, enhance your production efficiency, and ultimately improve your bottom line. Let us help you turn packaging challenges into opportunities for growth and innovation in your business.
Understanding packaging machine Types and Variations
Type Name | Key Distinguishing Features | Primary B2B Applications | Brief Pros & Cons for Buyers |
---|---|---|---|
Vertical Form Fill Seal (VFFS) | Automatically forms, fills, and seals bags from a roll of film | Food packaging, pharmaceuticals, chemicals | Pros: High speed, flexible bag sizes. Cons: Initial setup costs can be high. |
Horizontal Flow Wrapper | Wraps products in a continuous film, ideal for horizontal packaging | Snack foods, bakery items, pharmaceuticals | Pros: Efficient for irregular shapes. Cons: Limited to flat products. |
Premade Pouch Filling Machine | Uses pre-made pouches for filling and sealing | Sauces, snacks, pet food | Pros: Custom pouch designs, reduced material waste. Cons: Higher cost per pouch. |
Stick Pack Machine | Fills and seals products in stick packs, typically for single servings | Condiments, powdered drinks, snacks | Pros: Convenience for consumers, reduced material usage. Cons: Slower speed compared to bulk packing. |
Cartoning Machine | Forms, fills, and seals cartons for various products | Beverages, frozen foods, personal care products | Pros: Protects products during transport, customizable. Cons: Requires space and can be costly. |
What are the Characteristics of Vertical Form Fill Seal (VFFS) Machines?
Vertical Form Fill Seal (VFFS) machines are designed to create bags from a roll of film, fill them with product, and seal them in one continuous process. This type of machine is highly efficient, capable of producing a variety of bag sizes and styles, making it suitable for numerous industries, particularly food, pharmaceuticals, and chemicals. When considering a VFFS machine, buyers should evaluate the machine’s speed, the variety of bag styles it can produce, and the ease of maintenance, as these factors directly impact productivity and ROI.
How Do Horizontal Flow Wrappers Differ from Other Packaging Machines?
Horizontal flow wrappers are unique in that they wrap products in a continuous film, allowing for efficient packaging of flat or irregularly shaped items. They are commonly used in the snack food and bakery sectors, where speed and versatility are paramount. Buyers must consider the machine’s compatibility with their product shapes, the speed of operation, and the type of film used, as these elements will influence both packaging quality and operational efficiency.
What Advantages Do Premade Pouch Filling Machines Offer?
Premade pouch filling machines utilize ready-made pouches, which can be customized for branding and product protection. This type of machine is particularly advantageous for products like sauces and snacks that require a strong seal and attractive presentation. Buyers should assess the cost-effectiveness of using premade pouches versus roll stock, the machine’s flexibility in handling different pouch sizes, and the ease of integration into existing production lines.
Why Choose Stick Pack Machines for Single-Serve Products?
Stick pack machines are specifically designed for packing single servings, making them ideal for products like condiments and powdered drinks. Their compact design allows for efficient use of space, and they typically reduce material usage compared to traditional packaging. Buyers should consider the machine’s speed, the type of products it can handle, and the flexibility in stick pack design, as these factors will affect both consumer appeal and production efficiency.
What Should Buyers Know About Cartoning Machines?
Cartoning machines automate the process of forming, filling, and sealing cartons, which is essential for protecting products during shipping and storage. They are widely used in beverages and frozen food industries. When purchasing a cartoning machine, buyers should evaluate the machine’s speed, its ability to handle various carton sizes, and the required floor space, as these elements can significantly impact operational workflow and costs.
Key Industrial Applications of packaging machine
Industry/Sector | Specific Application of Packaging Machine | Value/Benefit for the Business | Key Sourcing Considerations for this Application |
---|---|---|---|
Food and Beverage | Vertical Form Fill Seal (VFFS) for snacks | Enhances speed and efficiency in packaging snacks, reducing labor costs. | Look for machines that offer flexibility in bag sizes and materials suitable for food safety regulations. |
Pharmaceuticals | Blister Packaging Machines for tablets | Provides tamper-evident packaging, ensuring product safety and compliance. | Ensure machines meet stringent health regulations and offer customization for various tablet sizes. |
Consumer Goods | Horizontal Flow Wrappers for personal care items | Increases shelf appeal and product protection, attracting consumers while reducing spoilage. | Consider machines that allow for quick changeovers to accommodate diverse product lines. |
Agriculture | Bagging Machines for grains and seeds | Streamlines packaging processes, improving inventory management and reducing waste. | Focus on durability and the ability to handle various bag styles, especially for bulk materials. |
E-commerce | Automated Pouching Systems for shipping | Increases packing speed and reduces shipping costs through optimized material usage. | Evaluate integration capabilities with existing fulfillment systems and the flexibility to handle different product dimensions. |
How are Packaging Machines Used in the Food and Beverage Industry?
In the food and beverage sector, Vertical Form Fill Seal (VFFS) machines are widely utilized for packaging snacks, powders, and liquids. These machines automate the process of creating bags from a roll of film, filling them with product, and sealing them, which significantly enhances packaging speed and efficiency. For international buyers, especially in regions like Africa and South America, sourcing VFFS machines that comply with local food safety regulations is crucial. Additionally, flexibility in bag sizes and materials can help businesses adapt to changing market demands.
What is the Role of Blister Packaging Machines in Pharmaceuticals?
Blister packaging machines are vital in the pharmaceutical industry for packaging tablets and capsules. They provide a tamper-evident solution that ensures product safety and compliance with health regulations. For B2B buyers in the Middle East and Europe, it’s essential to source machines that can be customized for various tablet sizes and shapes. This adaptability, along with the ability to meet stringent health and safety standards, makes blister packaging machines a key investment for pharmaceutical companies looking to enhance product integrity.
How Do Horizontal Flow Wrappers Benefit Consumer Goods Packaging?
Horizontal flow wrappers are commonly used in the consumer goods sector for packaging personal care items and household products. These machines wrap products in a continuous flow, enhancing shelf appeal and protecting items from spoilage. For international buyers, particularly from Europe, sourcing flow wrappers that allow for quick changeovers is important to accommodate diverse product lines. The ability to customize packaging designs can also help businesses stand out in competitive markets.
What Advantages Do Bagging Machines Offer to the Agriculture Sector?
In agriculture, bagging machines are essential for efficiently packaging grains, seeds, and fertilizers. They streamline the packaging process, which helps improve inventory management and reduce waste. For buyers in regions such as Africa, where agricultural production is significant, focusing on the durability of these machines and their capacity to handle various bag styles is crucial. This ensures that businesses can maintain efficiency while adapting to different agricultural products.
How Do Automated Pouching Systems Enhance E-commerce Operations?
Automated pouching systems are increasingly used in e-commerce for packaging items for shipping. These machines optimize material usage and increase packing speed, which can significantly reduce shipping costs. For international B2B buyers, especially from South America and Europe, it is important to evaluate how these systems integrate with existing fulfillment operations. Flexibility in handling different product dimensions can also enhance operational efficiency, making these machines a valuable asset for e-commerce businesses.
3 Common User Pain Points for ‘packaging machine’ & Their Solutions
Scenario 1: High Downtime Due to Machine Malfunctions
The Problem: One of the most common challenges faced by B2B buyers of packaging machines is unexpected downtime caused by machine malfunctions. For instance, a food manufacturing company in South America might invest heavily in a state-of-the-art vertical form fill seal machine only to encounter frequent breakdowns. This not only disrupts production schedules but also leads to increased operational costs and potentially lost revenue. Downtime can be particularly detrimental in industries where timely delivery is crucial, such as food and beverage, where shelf life is a key concern.
The Solution: To mitigate downtime, buyers should prioritize purchasing machines from reputable manufacturers known for their reliability and customer support. Before finalizing a purchase, it’s advisable to inquire about warranty options, service agreements, and the availability of spare parts. Implementing a preventive maintenance program can also greatly enhance machine longevity and reliability. Regularly scheduled inspections and servicing can help identify potential issues before they escalate into major problems. Additionally, investing in training for operators on proper machine handling and troubleshooting can empower staff to address minor issues independently, reducing reliance on external support.
Scenario 2: Complexity of Machine Integration into Existing Lines
The Problem: Many companies, especially those in Europe and the Middle East, face the challenge of integrating new packaging machines into their existing production lines. This can be particularly problematic when upgrading from older, less sophisticated machines to more advanced technology. Buyers often struggle with compatibility issues, leading to inefficient workflows and wasted resources. The complexity of integration can deter companies from upgrading their equipment, resulting in outdated practices that could hinder productivity and growth.
The Solution: To ensure smooth integration, buyers should engage with manufacturers who offer comprehensive line integration services. It’s crucial to conduct a thorough assessment of the existing production environment to determine how new machines will fit into current workflows. Collaborating with engineering teams from the packaging machine supplier can provide insights into potential compatibility issues and facilitate custom solutions. Moreover, investing in modular machines that can be easily adapted or expanded upon can future-proof operations. Buyers should also consider training sessions that focus on the new systems, helping staff to adapt quickly and efficiently.
Scenario 3: Balancing Cost Efficiency with Quality Assurance
The Problem: Many B2B buyers, especially those in Africa and South America, grapple with the challenge of balancing cost efficiency and quality assurance when selecting packaging machines. In an effort to reduce operational costs, companies may be tempted to choose lower-priced machines that compromise on quality, leading to issues like product spoilage, poor packaging integrity, and ultimately dissatisfied customers. This dilemma is particularly pressing in competitive markets where both cost and quality are critical to success.
The Solution: To address this issue, buyers should adopt a value-based approach when evaluating packaging machines. This involves looking beyond the initial purchase price and considering the total cost of ownership, which includes maintenance, operational efficiency, and potential savings from reduced waste. It’s advisable to conduct a thorough market analysis to identify machines that offer the best balance of cost and quality. Engaging with suppliers who provide robust customer testimonials and case studies can also help buyers make informed decisions. Additionally, exploring financing options can allow companies to invest in higher-quality machines without immediate financial strain, ultimately leading to better long-term returns. By prioritizing quality while remaining cost-conscious, companies can enhance their packaging processes and customer satisfaction.
Strategic Material Selection Guide for packaging machine
What Are the Key Materials Used in Packaging Machines?
When selecting a packaging machine, the choice of materials plays a crucial role in determining the machine’s performance, durability, and suitability for specific applications. Here, we analyze four common materials used in packaging machines: stainless steel, aluminum, plastic composites, and carbon steel.
How Does Stainless Steel Benefit Packaging Machines?
Stainless steel is a widely preferred material in the packaging industry due to its excellent corrosion resistance and durability. It can withstand high temperatures and pressures, making it suitable for various applications, including food and pharmaceutical packaging. The non-reactive nature of stainless steel ensures that it does not contaminate the products being packaged.
Pros:
– High durability and resistance to corrosion.
– Easy to clean and maintain, which is essential for hygiene in food applications.
– Long lifespan, reducing the need for frequent replacements.
Cons:
– Higher initial cost compared to other materials.
– Requires specialized welding techniques during manufacturing, which can increase production complexity.
For international buyers, especially in regions like Africa and South America, compliance with health and safety standards (e.g., FDA or EU regulations) is critical. Stainless steel often meets these standards, making it a reliable choice.
What Advantages Do Aluminum Components Offer in Packaging Machines?
Aluminum is another common material used in packaging machines, particularly for components such as frames and casings. It is lightweight yet strong, making it easier to handle and install. Aluminum also has good thermal conductivity, which can be beneficial in processes requiring temperature control.
Pros:
– Lightweight, reducing shipping costs.
– Good corrosion resistance, especially when anodized.
– Cost-effective for mass production due to ease of machining.
Cons:
– Lower strength compared to stainless steel, which may limit its use in heavy-duty applications.
– Susceptible to scratching and denting, which may affect aesthetics and functionality.
International buyers should consider local regulations regarding aluminum usage, particularly in food packaging, where food safety standards must be met.
Why Choose Plastic Composites for Flexible Packaging Solutions?
Plastic composites are increasingly popular in packaging machines due to their versatility and cost-effectiveness. They can be engineered to meet specific requirements, such as flexibility, strength, and resistance to chemicals. This makes them suitable for a wide range of applications, from food packaging to industrial products.
Pros:
– Highly customizable for various applications.
– Generally lower cost than metals, making them attractive for budget-conscious buyers.
– Lightweight, facilitating easier handling and transportation.
Cons:
– Limited temperature resistance compared to metals, which may restrict their use in high-heat applications.
– Environmental concerns regarding plastic waste and recyclability.
For buyers in Europe and the Middle East, understanding local recycling regulations and sustainability initiatives is essential when considering plastic composites.
What Role Does Carbon Steel Play in Packaging Machinery?
Carbon steel is often used in the construction of packaging machines due to its strength and durability. It is particularly advantageous for heavy-duty applications where high load-bearing capabilities are required. However, it is more susceptible to corrosion than stainless steel.
Pros:
– High strength and load-bearing capacity.
– Cost-effective for heavy-duty machinery.
– Readily available and easy to fabricate.
Cons:
– Prone to rusting and corrosion without proper treatment.
– Requires regular maintenance to ensure longevity.
International buyers should be aware of the need for protective coatings or treatments to enhance the corrosion resistance of carbon steel, especially in humid climates found in parts of Africa and South America.
Summary Table of Material Selection for Packaging Machines
Material | Typical Use Case for Packaging Machine | Key Advantage | Key Disadvantage/Limitation | Relative Cost (Low/Med/High) |
---|---|---|---|---|
Stainless Steel | Food and pharmaceutical packaging | High durability and corrosion resistance | Higher initial cost | High |
Aluminum | Frames and casings for machines | Lightweight and good thermal conductivity | Lower strength than stainless steel | Medium |
Plastic Composites | Flexible packaging solutions | Highly customizable and cost-effective | Limited temperature resistance | Low |
Carbon Steel | Heavy-duty packaging machinery | High strength and load-bearing capacity | Prone to rust without treatment | Medium |
This strategic material selection guide provides valuable insights for international B2B buyers, helping them make informed decisions based on their specific packaging needs and regional compliance requirements.
In-depth Look: Manufacturing Processes and Quality Assurance for packaging machine
What Are the Main Stages of Manufacturing Packaging Machines?
The manufacturing process of packaging machines involves several critical stages that ensure both functionality and quality. These stages typically include:
-
Material Preparation: This initial stage involves sourcing high-quality raw materials such as stainless steel, aluminum, and plastic components. The choice of materials is crucial, as they directly affect the durability and performance of the machines. Manufacturers often engage in rigorous supplier assessments to ensure that materials meet specified standards.
-
Forming: During the forming stage, raw materials are transformed into specific machine components. Techniques such as CNC machining, laser cutting, and injection molding are commonly used. Each method has its advantages; for instance, CNC machining allows for high precision, while injection molding is efficient for producing complex shapes in large quantities.
-
Assembly: After forming, components are assembled into the final machine. This stage may involve manual labor or automated assembly lines, depending on the complexity of the machine. Key techniques include robotic assembly for precision and human oversight for quality checks. Proper assembly is vital to ensure that all parts fit correctly and function as intended.
-
Finishing: The finishing stage includes processes such as surface treatment, painting, and the application of protective coatings. This not only enhances the machine’s aesthetic appeal but also protects against corrosion and wear, especially in industries like food packaging where hygiene is paramount.
How Is Quality Assurance Implemented in Packaging Machine Manufacturing?
Quality assurance (QA) in the manufacturing of packaging machines is paramount for ensuring that the final products meet international standards and customer expectations. Key elements of QA include:
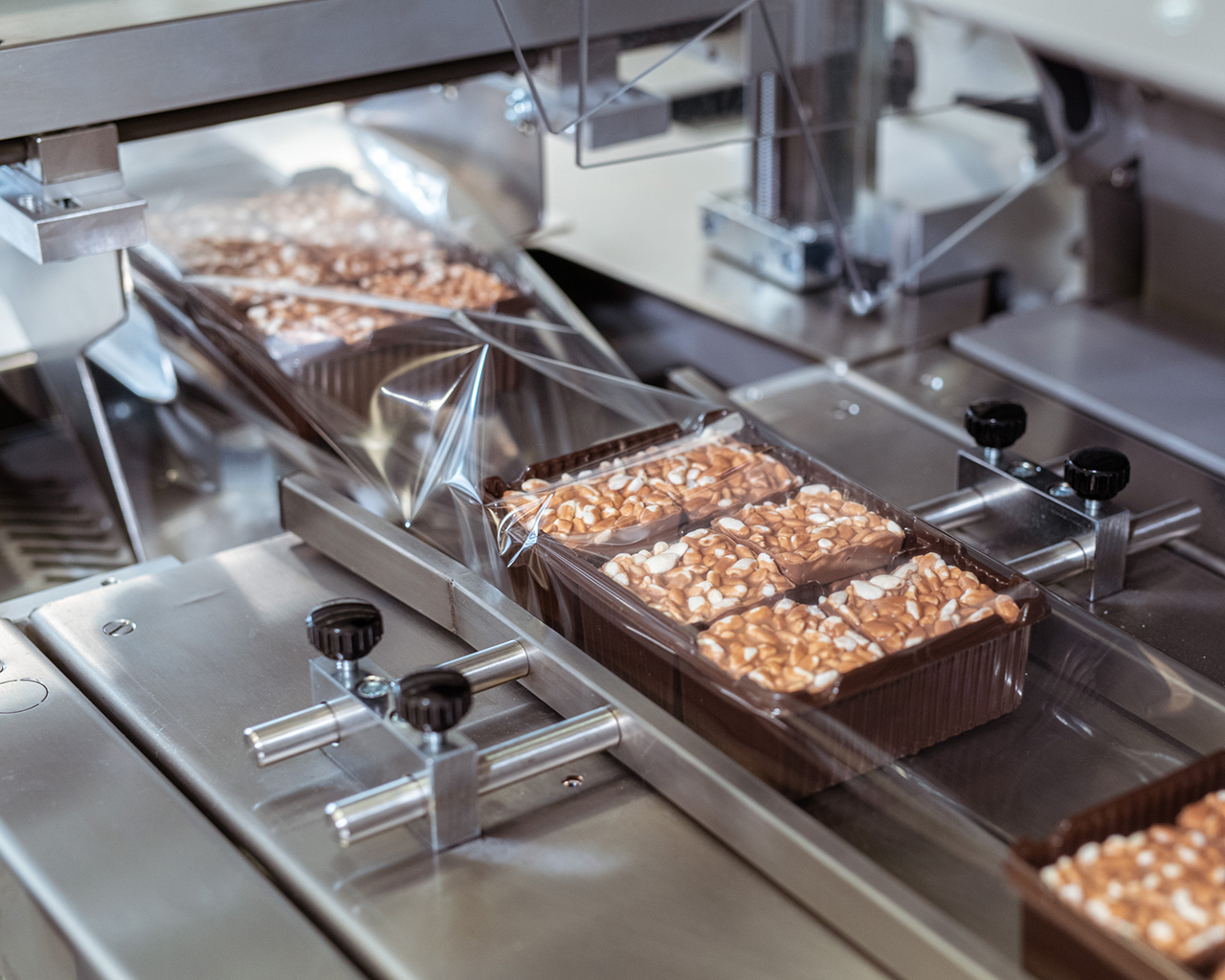
A stock image related to packaging machine.
-
International Standards Compliance: Many manufacturers adhere to international standards like ISO 9001, which outlines criteria for a quality management system. Compliance with ISO standards ensures that processes are efficient, and that products are consistently produced to meet quality specifications. Additionally, CE marking in Europe indicates compliance with health, safety, and environmental protection standards.
-
Quality Control Checkpoints: Various checkpoints are implemented throughout the manufacturing process to catch defects early. These checkpoints typically include:
– Incoming Quality Control (IQC): This involves inspecting raw materials upon arrival to ensure they meet predefined specifications.
– In-Process Quality Control (IPQC): Quality checks during the assembly process help identify issues before the machine is completed.
– Final Quality Control (FQC): Comprehensive testing is performed on the finished machine to verify its performance and safety. -
Common Testing Methods: Manufacturers often use a variety of testing methods to ensure quality, including:
– Functional Testing: Verifying that the machine operates according to design specifications.
– Durability Testing: Assessing the machine’s performance under stress to ensure long-term reliability.
– Safety Testing: Ensuring that the machine meets all safety regulations and does not pose risks to operators.
How Can B2B Buyers Verify Supplier Quality Control?
International B2B buyers must be proactive in verifying the quality control processes of potential suppliers. Here are several actionable steps:
-
Conduct Supplier Audits: Regular audits can provide insight into a supplier’s manufacturing processes, quality control measures, and compliance with international standards. This is especially important when sourcing from regions where standards may vary.
-
Request Quality Reports: Suppliers should provide documentation related to their quality management systems, including ISO certifications, quality control checklists, and records of past quality issues and resolutions. Reviewing these documents can give buyers confidence in the supplier’s commitment to quality.
-
Engage Third-Party Inspectors: Utilizing third-party inspection services can provide an unbiased evaluation of the supplier’s manufacturing processes and product quality. These inspectors can assess compliance with international standards and provide detailed reports.
What Are the Quality Control Nuances for International B2B Buyers?
When sourcing packaging machines internationally, particularly from regions such as Africa, South America, the Middle East, and Europe, buyers should be aware of several quality control nuances:
-
Cultural and Regulatory Differences: Different regions may have varying standards and practices regarding quality control. For instance, European manufacturers often have stricter regulations compared to some suppliers in Africa or South America. Understanding these differences can help buyers set realistic expectations.
-
Supply Chain Transparency: It’s crucial to establish transparency throughout the supply chain. Buyers should inquire about the sourcing of materials and the production process, as this can significantly impact the final product’s quality.
-
Post-Purchase Support: Quality assurance doesn’t end with the delivery of the machine. Buyers should evaluate the supplier’s after-sales support, including warranty terms, availability of replacement parts, and responsiveness to service requests. This ongoing support is essential for maintaining machine performance over time.
Conclusion: Enhancing Your Packaging Machine Procurement Process
For B2B buyers, particularly in emerging markets, understanding the manufacturing processes and quality assurance measures for packaging machines is critical. By actively engaging in supplier audits, requesting comprehensive quality reports, and leveraging third-party inspections, buyers can mitigate risks and ensure they are investing in reliable machinery. Furthermore, being aware of regional nuances in quality control practices will enhance the overall procurement process, ultimately leading to improved operational efficiency and product quality.
Practical Sourcing Guide: A Step-by-Step Checklist for ‘packaging machine’
The following guide serves as a practical checklist for international B2B buyers looking to procure packaging machines. This resource is tailored specifically for buyers from Africa, South America, the Middle East, and Europe, providing actionable insights to streamline the sourcing process.
Step 1: Define Your Technical Specifications
Before you begin your search, clearly outline your packaging needs. Determine the type of products you will be packaging (e.g., liquids, solids, or powders) and the desired packaging format (e.g., pouches, boxes, or bottles). This will help you identify machines that are tailored to your specific requirements, ensuring compatibility and efficiency.
- Consider bag styles: Identify whether you need premade pouches, vertical form fill seal bags, or horizontal flow wrappers.
- Assess speed requirements: Determine the production speed needed to meet your operational goals.
Step 2: Research Industry Trends and Innovations
Stay informed about the latest trends in packaging technology, including advancements in automation and eco-friendly materials. Understanding these trends can provide insight into which machines will offer the best ROI and align with sustainability goals.
- Explore flexible packaging options: These often reduce material costs and enhance shelf appeal.
- Investigate automation capabilities: Machines that integrate with existing production lines can significantly improve efficiency.
Step 3: Evaluate Potential Suppliers
Conduct thorough research on potential suppliers to ensure they can meet your needs. Request company profiles, case studies, and references from other buyers, especially those within your industry or region.
- Check for certifications: Ensure suppliers comply with international quality standards, such as ISO certifications.
- Analyze their product range: A supplier with a diverse offering can better accommodate future needs or changes in your product line.
Step 4: Request Quotes and Compare Pricing
Once you’ve identified potential suppliers, request detailed quotes. This should include not only the cost of the machinery but also any associated costs such as installation, training, and maintenance.
- Look for hidden costs: Be aware of additional fees for shipping, customs, or after-sales support.
- Evaluate financing options: Some suppliers may offer flexible payment plans that can alleviate upfront financial burdens.
Step 5: Assess After-Sales Support and Warranty
Review the after-sales support offered by each supplier. A robust support system can be invaluable, particularly if you encounter issues post-purchase.
- Check warranty terms: Understand what is covered and the duration of the warranty.
- Evaluate training programs: Suppliers that provide comprehensive training can help your team operate the machines effectively from day one.
Step 6: Visit Manufacturing Facilities (if possible)
If feasible, arrange visits to the suppliers’ manufacturing facilities. This allows you to see the machines in action and assess the quality of workmanship firsthand.
- Inspect production processes: Evaluate how machines are assembled and tested for quality assurance.
- Engage with technical staff: Discuss your specific needs and gauge their expertise and willingness to support your business.
Step 7: Finalize the Purchase Agreement
Once you’ve selected a supplier, carefully review and negotiate the purchase agreement. Ensure that all terms, including delivery timelines, payment schedules, and support services, are clearly outlined.
- Include performance metrics: Specify expected performance levels to hold the supplier accountable.
- Clarify terms of cancellation or returns: Understand the process if the equipment does not meet your expectations.
By following this checklist, international B2B buyers can make informed decisions when sourcing packaging machines, ensuring their investment aligns with both current and future operational needs.
Comprehensive Cost and Pricing Analysis for packaging machine Sourcing
What Are the Key Cost Components in Packaging Machine Sourcing?
When sourcing packaging machines, understanding the cost structure is crucial for effective budgeting and financial planning. The main cost components include:
-
Materials: The choice of materials significantly influences the overall cost. High-quality components may increase initial expenses but can enhance durability and performance, leading to lower maintenance costs over time.
-
Labor: Labor costs encompass not only the workforce directly involved in manufacturing but also any skilled labor required for setup and maintenance. This can vary by region, with labor-intensive manufacturing being more expensive in developed countries compared to emerging markets.
-
Manufacturing Overhead: This includes indirect costs associated with production, such as utilities, rent, and equipment depreciation. These costs can fluctuate based on the location of the manufacturer and their operational efficiency.
-
Tooling: Custom tooling can add to the upfront costs but is essential for producing machines tailored to specific packaging needs. Investing in appropriate tooling can yield better production rates and quality.
-
Quality Control (QC): Ensuring that machines meet quality standards is vital. QC processes may add to costs but help prevent expensive errors and rework, ultimately contributing to a higher return on investment.
-
Logistics: Shipping and handling costs are often overlooked. For international buyers, these costs can escalate due to customs duties, tariffs, and freight expenses, particularly when sourcing from different continents.
-
Margin: Supplier profit margins can vary widely. Understanding the typical margins in your specific market can help you gauge whether a quoted price is fair.
How Do Price Influencers Affect Packaging Machine Costs?
Several factors can influence the pricing of packaging machines, particularly for international buyers:
-
Volume and Minimum Order Quantity (MOQ): Bulk purchasing often results in lower per-unit prices. Understanding the supplier’s MOQ can help negotiate better terms.
-
Specifications and Customization: Custom features can significantly affect pricing. Machines designed for specific applications may come with higher costs due to the added complexity and bespoke engineering.
-
Materials and Quality Certifications: Machines made from higher-grade materials or those that comply with international quality certifications (e.g., ISO, CE) may command premium prices. However, these certifications can assure buyers of reliability and safety.
-
Supplier Factors: The reputation and experience of the supplier can influence pricing. Established suppliers with a track record of performance may charge more but often provide better service and support.
-
Incoterms: Understanding Incoterms (International Commercial Terms) is essential for international transactions. These terms dictate who is responsible for shipping, insurance, and tariffs, impacting the overall cost.
What Are Essential Buyer Tips for Cost-Efficiency in Sourcing?
For B2B buyers, particularly from Africa, South America, the Middle East, and Europe, here are actionable tips to enhance cost-efficiency:
-
Negotiate Wisely: Engage in thorough discussions with suppliers. Leverage your knowledge of market rates and competitor pricing to negotiate better terms.
-
Consider Total Cost of Ownership (TCO): Look beyond the initial purchase price. Evaluate maintenance, operational efficiency, and potential downtime to understand the true cost over the machine’s lifespan.
-
Be Aware of Pricing Nuances: International buyers should account for fluctuations in currency exchange rates, as these can affect pricing. Additionally, be cautious of hidden costs such as import duties or taxes.
-
Research Market Trends: Stay updated on industry trends and technological advancements. This knowledge can help identify when to invest in new machinery versus upgrading existing systems.
-
Evaluate Supplier Relationships: Building strong relationships with suppliers can lead to better pricing and service. Consider long-term partnerships that can yield discounts on future purchases.
Conclusion and Disclaimer
The pricing landscape for packaging machines is complex and varies significantly based on multiple factors. Buyers should conduct thorough research and consider all cost components and price influencers before making purchasing decisions. While indicative prices may be available, they should be viewed as a general guide rather than a definitive cost. Always verify current pricing with suppliers to ensure accuracy.
Alternatives Analysis: Comparing packaging machine With Other Solutions
When considering the best packaging solutions, it’s essential to evaluate not only the traditional packaging machines but also alternative methods that may fit specific business needs. Understanding the capabilities and limitations of these alternatives can significantly influence an international B2B buyer’s decision-making process.
Comparison Aspect | Packaging Machine | Alternative 1: Manual Packaging | Alternative 2: Contract Packaging |
---|---|---|---|
Performance | High-speed, automated processes | Slower, labor-intensive methods | Varies based on service provider capabilities |
Cost | High initial investment, long-term savings | Low initial costs, higher labor costs | Variable costs based on project scope |
Ease of Implementation | Requires training and setup | Simple to implement but requires skilled labor | Quick setup, depends on contract terms |
Maintenance | Regular maintenance required | Minimal maintenance, labor-intensive | No maintenance responsibility for buyers |
Best Use Case | High-volume production | Small-scale or artisanal products | Businesses lacking in-house packaging capability |
What Are the Benefits and Drawbacks of Manual Packaging?
Manual packaging involves human labor for packing products. This method is often preferred by small businesses or those with lower production volumes. Pros include lower initial investment and flexibility in handling diverse products. However, the cons are evident in terms of slower output rates and higher long-term labor costs. For businesses operating in regions with high labor costs or limited access to skilled labor, manual packaging may not be sustainable.
How Does Contract Packaging Compare to Packaging Machines?
Contract packaging involves outsourcing the packaging process to third-party service providers. This option is advantageous for companies looking to focus on core competencies while leveraging the expertise of packaging specialists. The pros include reduced capital expenditure and a quick turnaround for packaging needs. However, the cons can include potential quality control issues and less control over the packaging process. This method is particularly effective for businesses in Africa and South America where establishing an in-house packaging operation may be cost-prohibitive.
Conclusion: How to Choose the Right Packaging Solution?
Choosing the right packaging solution depends on several factors, including production volume, budget constraints, and operational capabilities. For businesses in Europe or the Middle East looking to scale, investing in a packaging machine may offer the best long-term value despite the higher upfront cost. Conversely, companies in Africa or South America with lower production volumes might find manual packaging or contract packaging more economical and flexible. Ultimately, understanding the specific needs and resources of your business will guide you in selecting the most suitable packaging method.
Essential Technical Properties and Trade Terminology for packaging machine
What Are the Key Technical Properties of Packaging Machines?
When evaluating packaging machines for international trade, especially in regions like Africa, South America, the Middle East, and Europe, several technical properties are crucial for ensuring that the equipment meets operational demands. Understanding these specifications can aid B2B buyers in making informed decisions.
1. Material Grade
Material grade refers to the quality and type of materials used in manufacturing the packaging machine. Common materials include stainless steel, aluminum, and high-density plastics. The choice of material affects the machine’s durability, corrosion resistance, and compliance with food safety standards. For B2B buyers, selecting machines made from high-grade materials can lead to lower maintenance costs and longer operational lifespans.
2. Tolerance
Tolerance indicates the permissible limit or limits of variation in a physical dimension. For packaging machines, maintaining tight tolerances is essential for achieving precise packaging, which directly impacts product quality and customer satisfaction. In B2B settings, machines with superior tolerances can enhance production efficiency and reduce waste, resulting in a better return on investment.
3. Speed and Output Capacity
Speed is a critical specification that reflects how many units a packaging machine can process within a given timeframe, typically measured in bags or packages per minute. Output capacity is equally vital, as it defines the maximum number of packages the machine can handle. Buyers should consider their production requirements and select machines that can meet or exceed these needs to maintain competitive advantages in their markets.
4. Automation Level
The level of automation in a packaging machine determines how much manual intervention is required during operation. Fully automated systems can significantly enhance efficiency and reduce labor costs. For B2B buyers, investing in higher automation levels can streamline operations and improve consistency, especially for large-scale production environments.
5. Energy Efficiency
Energy efficiency refers to how effectively a machine uses energy to perform its tasks. Machines with high energy efficiency not only lower operational costs but also contribute to sustainability efforts, which is increasingly important in global markets. For businesses focused on reducing their carbon footprint, selecting energy-efficient packaging machines can provide a dual benefit of cost savings and enhanced brand reputation.
What Are Common Trade Terminologies Related to Packaging Machines?
Familiarizing oneself with industry jargon is essential for effective communication and negotiation in the B2B packaging sector. Here are some common terms you should know:
1. OEM (Original Equipment Manufacturer)
An OEM refers to a company that produces parts or equipment that may be marketed by another manufacturer. In the context of packaging machines, understanding OEM relationships can help buyers identify reputable suppliers and ensure they receive high-quality components.
2. MOQ (Minimum Order Quantity)
MOQ is the smallest quantity of a product that a supplier is willing to sell. In packaging machinery, MOQs can affect purchasing decisions, particularly for smaller companies. Buyers need to assess their production needs against MOQs to avoid overcommitting resources.
3. RFQ (Request for Quotation)
An RFQ is a document issued by a buyer to invite suppliers to submit price offers for specific products or services. In the packaging industry, submitting an RFQ can help buyers compare prices and services from different manufacturers, aiding in informed decision-making.
4. Incoterms
Incoterms, short for International Commercial Terms, are standardized trade terms used in international transactions to clarify the responsibilities of buyers and sellers. Understanding Incoterms is crucial for B2B buyers as they define who is responsible for shipping costs, insurance, and risks, ultimately affecting the total cost of acquisition for packaging machines.
5. Turnkey Solutions
Turnkey solutions refer to complete packages that include all necessary components and services to make a machine operational. For B2B buyers, opting for turnkey solutions can simplify the purchasing process and reduce the time to market, as everything is pre-integrated and ready for use.
By grasping these essential technical properties and trade terminologies, B2B buyers can navigate the complex landscape of packaging machinery more effectively, ensuring they make choices that align with their operational needs and market demands.
Navigating Market Dynamics and Sourcing Trends in the packaging machine Sector
What Are the Key Drivers and Trends Influencing the Packaging Machine Market?
The global packaging machine market is experiencing dynamic growth, primarily driven by the increasing demand for automated solutions that enhance efficiency and reduce operational costs. In regions such as Africa, South America, the Middle East, and Europe, international B2B buyers are increasingly leaning towards advanced packaging technologies, including vertical form fill seal (VFFS) machines and horizontal flow wrappers. These technologies not only streamline packaging processes but also cater to diverse product types, from food items to consumer goods.
Emerging trends include the integration of Industry 4.0 technologies, which leverage IoT and AI for enhanced machine performance and predictive maintenance. This shift allows manufacturers to minimize downtime and improve product quality, thus appealing to cost-conscious buyers. Additionally, there is a growing interest in flexible packaging solutions, which are seen as more sustainable due to their lower carbon footprint and reduced material usage. As a result, buyers are prioritizing suppliers who offer innovative, adaptable, and efficient machinery that aligns with their operational needs.
Furthermore, the rise of e-commerce has intensified the demand for packaging machines that can handle varying product sizes and shapes, leading to the development of customizable equipment. B2B buyers are now seeking suppliers that not only provide machinery but also offer comprehensive service packages that include training, support, and spare parts, ensuring seamless operations and long-term partnerships.
How Is Sustainability Shaping Sourcing Decisions in the Packaging Machine Sector?
Sustainability has become a pivotal consideration for B2B buyers in the packaging machine sector. The environmental impact of packaging operations is under scrutiny, prompting companies to seek machines that minimize waste and utilize eco-friendly materials. The importance of ethical sourcing is also gaining traction, as buyers are increasingly aware of the social and environmental implications of their supply chains.
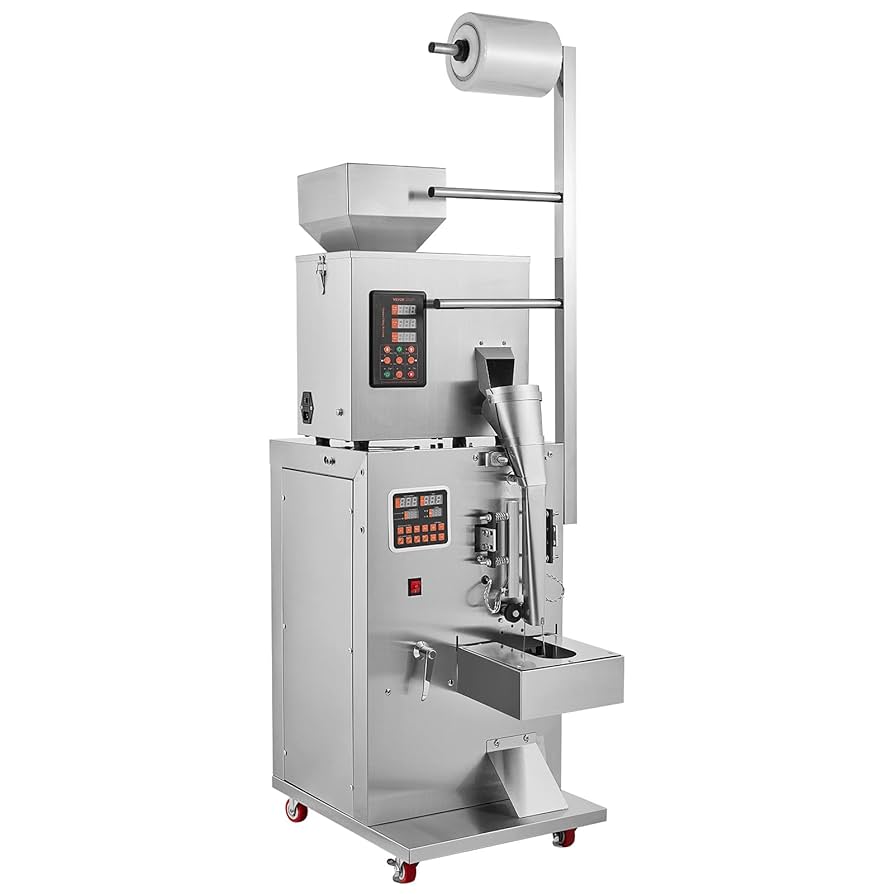
A stock image related to packaging machine.
To align with sustainable practices, many packaging machine manufacturers are adopting ‘green’ certifications and using recyclable or biodegradable materials in their production processes. Buyers from regions like Europe and South America are particularly influenced by stringent regulatory frameworks aimed at reducing plastic waste and promoting sustainable packaging solutions. Consequently, they favor suppliers who can demonstrate a commitment to sustainability through certifications such as ISO 14001 or FSC (Forest Stewardship Council) labels.
In addition, the trend toward circular economy practices encourages buyers to consider the entire lifecycle of their packaging solutions. This includes sourcing machines that facilitate easy recycling and reuse of packaging materials, thus enhancing brand reputation and consumer trust. As sustainability continues to shape market dynamics, B2B buyers must prioritize suppliers who not only meet their operational needs but also share their commitment to responsible sourcing and environmental stewardship.
What Has Been the Evolution of Packaging Machines Over the Years?
The packaging machine industry has undergone significant evolution, transitioning from manual to automated solutions. Early packaging methods were labor-intensive and limited in scope, often resulting in inefficiencies. The introduction of mechanical packaging machines in the mid-20th century marked a turning point, enabling faster production rates and improved accuracy.
With the advent of technology, the late 20th and early 21st centuries saw the integration of electronic controls and automation, enhancing operational capabilities. This shift allowed for more sophisticated machinery that could adapt to various product types and packaging formats. Today, the focus is on smart technologies and IoT integration, allowing for real-time monitoring and data-driven decision-making.
As the market continues to evolve, B2B buyers must stay informed about technological advancements and industry trends to ensure they select the best packaging machines that meet their current and future needs. This historical context underscores the importance of innovation and adaptability in the packaging machine sector, crucial for maintaining competitiveness in a rapidly changing global market.
Frequently Asked Questions (FAQs) for B2B Buyers of packaging machine
-
How do I choose the right packaging machine for my product?
Choosing the right packaging machine involves understanding your product specifications, production volume, and packaging requirements. Assess the type of product you’re packaging—solid, liquid, or powder—and its characteristics, such as size, shape, and fragility. Additionally, consider your production speed needs and whether you require flexibility for different bag styles. Engage with suppliers to discuss their offerings and seek advice based on your unique requirements. If possible, visit their facilities to see the machines in action or request samples of packaged products. -
What is the best packaging machine for small-scale production?
For small-scale production, consider semi-automatic or manual packaging machines. These options are generally more cost-effective and can accommodate lower production volumes without compromising quality. Machines like vertical form fill seal (VFFS) or tabletop baggers are ideal for small to medium-sized businesses. They are versatile and can handle various bag styles, making them suitable for different products. Additionally, ensure that the machine is easy to operate and maintain to minimize downtime and labor costs. -
What factors should I consider when vetting packaging machine suppliers?
When vetting suppliers, assess their experience in the industry, customer reviews, and case studies that demonstrate their capabilities. Check for certifications and compliance with international quality standards, as this reflects their commitment to quality. Additionally, inquire about their after-sales support, including training, spare parts availability, and warranty policies. Establish clear communication channels and ensure they understand your specific packaging needs, which can help in building a long-term partnership. -
What are the minimum order quantities (MOQ) for packaging machines?
Minimum order quantities (MOQ) can vary significantly among suppliers. Some manufacturers may offer flexibility with lower MOQs, particularly for standard machines, while custom machines might require higher quantities due to specific design and production costs. It’s essential to discuss your needs directly with suppliers to understand their MOQ policies and whether they can accommodate your requirements. This discussion can also include potential financing options if upfront costs are a concern. -
How can I ensure the quality of packaging machines I purchase?
To ensure quality, request detailed specifications, certifications, and compliance documents from the manufacturer. Conduct factory visits or request third-party inspections before shipment. Inquire about the materials used in construction and the technology employed in the machines. Additionally, consider purchasing from suppliers who offer warranties and maintenance packages, as these can provide peace of mind regarding long-term reliability and performance. -
What payment terms should I expect when purchasing packaging machines internationally?
Payment terms can vary by supplier and region. Common terms include a deposit upon order confirmation and the balance upon delivery or installation. Some suppliers may offer financing options or installment plans, which can alleviate upfront costs. Always clarify the payment methods accepted (such as letters of credit, wire transfers, or credit cards) and ensure that terms are documented in the purchase agreement to avoid misunderstandings. -
What are the logistics considerations for importing packaging machines?
Logistics considerations include shipping methods, customs clearance, and delivery timelines. Choose a reliable freight forwarder experienced in handling machinery shipments. Ensure you understand the customs regulations and tariffs applicable to your country to avoid unexpected costs. Additionally, factor in lead times for production, shipping, and installation, as these can vary significantly based on the supplier’s location and your destination. -
How can I customize my packaging machine to meet specific needs?
Customization options depend on the manufacturer’s capabilities. Discuss your specific requirements, such as bag size, sealing methods, or automation levels, with the supplier. Many manufacturers offer modular designs that allow for upgrades or modifications over time. Be prepared to provide detailed information about your product and packaging goals, which can assist the supplier in developing a tailored solution that enhances efficiency and meets your production standards.
Important Disclaimer & Terms of Use
⚠️ Important Disclaimer
The information provided in this guide, including content regarding manufacturers, technical specifications, and market analysis, is for informational and educational purposes only. It does not constitute professional procurement advice, financial advice, or legal advice.
While we have made every effort to ensure the accuracy and timeliness of the information, we are not responsible for any errors, omissions, or outdated information. Market conditions, company details, and technical standards are subject to change.
B2B buyers must conduct their own independent and thorough due diligence before making any purchasing decisions. This includes contacting suppliers directly, verifying certifications, requesting samples, and seeking professional consultation. The risk of relying on any information in this guide is borne solely by the reader.
Strategic Sourcing Conclusion and Outlook for packaging machine
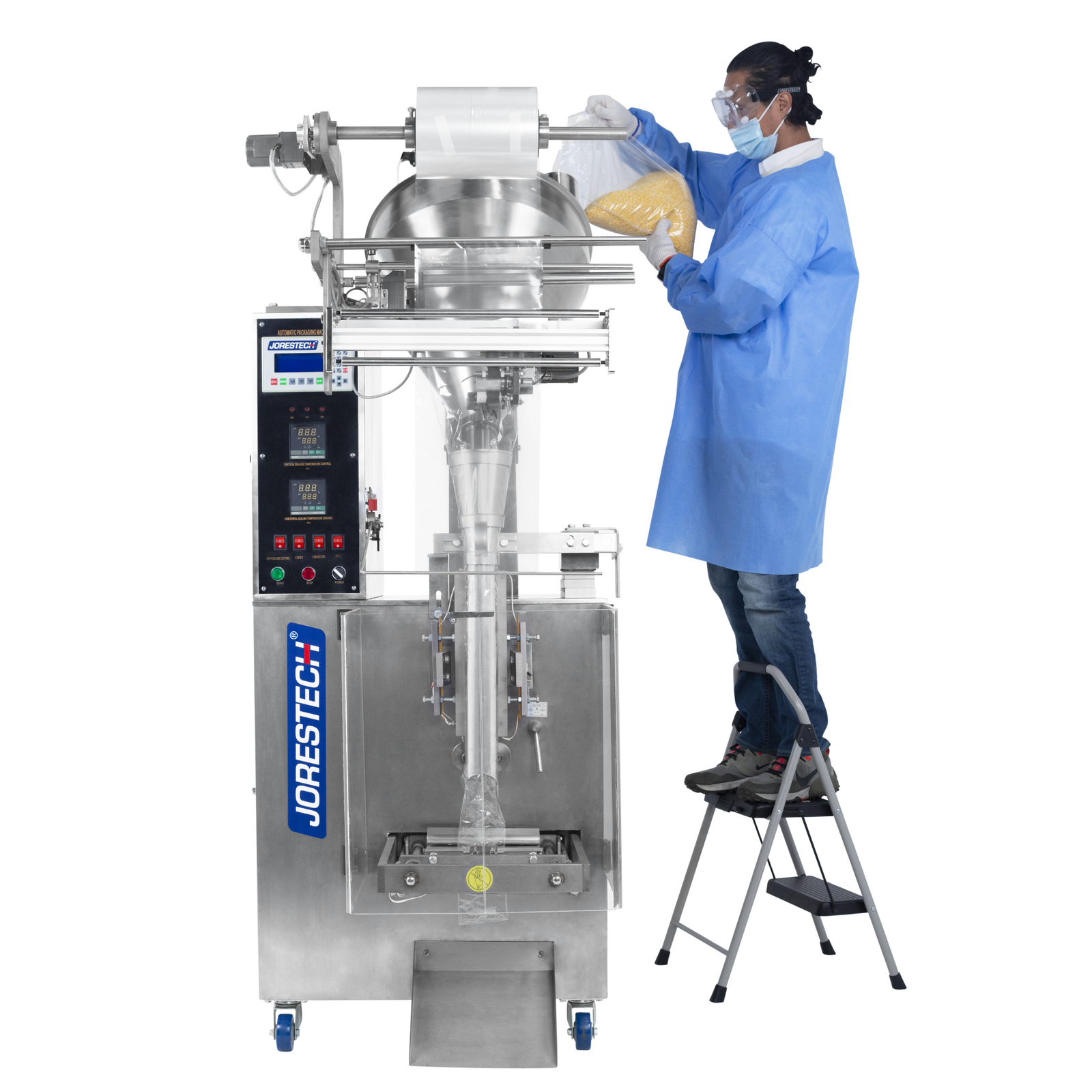
A stock image related to packaging machine.
What Are the Key Takeaways for International B2B Buyers in Packaging Machines?
In conclusion, strategic sourcing of packaging machines is crucial for optimizing production efficiency and reducing operational costs. By understanding the diverse options available—from flexible packaging solutions to advanced automation technologies—buyers can tailor their choices to meet specific industry demands. For international B2B buyers, particularly from Africa, South America, the Middle East, and Europe, the ability to source the right machinery can significantly enhance competitive advantage.
How Can Buyers Leverage Strategic Sourcing for Future Success?
Investing in high-quality packaging equipment not only improves product quality but also supports sustainability initiatives by minimizing waste and energy consumption. Additionally, considering factors such as machine adaptability, ease of integration, and after-sales support can lead to long-term operational efficiencies.
What’s Next for B2B Buyers in the Packaging Machine Market?
As the packaging industry continues to evolve, staying informed about the latest technologies and trends will empower buyers to make strategic decisions that align with their growth objectives. We encourage you to engage with suppliers, explore financing options, and leverage industry insights to ensure your sourcing strategies are not just reactive but proactively designed for future demands. Your journey towards streamlined operations and enhanced profitability starts now—take the next step in evaluating your packaging machine needs today.