Discover 7 Essential Kinds of Locks for Your Business Needs (2025)
Introduction: Navigating the Global Market for kinds of locks
In the quest for securing properties, sourcing the right kinds of locks can pose a significant challenge for international B2B buyers, especially those operating in diverse markets across Africa, South America, the Middle East, and Europe. With an overwhelming array of options—from padlocks and deadbolts to lever handle locks—navigating this complex landscape requires a clear understanding of each lock’s functionality, security level, and best applications. This guide aims to demystify the various types of locks available, providing actionable insights into their applications and the critical factors to consider when making purchasing decisions.
Our comprehensive resource covers not only the different lock types but also delves into supplier vetting processes, cost considerations, and regional compliance standards. By equipping B2B buyers with essential knowledge about lock security features, installation requirements, and maintenance needs, we empower them to make informed decisions that align with their security goals and budget constraints. Whether you are operating in bustling urban centers or remote areas, understanding the nuances of lock types will help enhance your security strategy and protect your assets effectively.
For buyers from Spain to Nigeria, this guide serves as a vital tool in optimizing procurement processes, ensuring that the locks selected not only meet the highest security standards but also cater to the specific demands of their operational environments.
Understanding kinds of locks Types and Variations
Type Name | Key Distinguishing Features | Primary B2B Applications | Brief Pros & Cons for Buyers |
---|---|---|---|
Padlocks | Portable, available in combination or keyed varieties | Lockers, storage sheds, toolboxes | Pros: Versatile and easy to use. Cons: Limited security for high-value items. |
Deadbolts | Available in single, double, and lockable thumbturn configurations | External doors of commercial properties | Pros: High security, durable. Cons: Requires key access for both sides in some models. |
Knob Locks | Cylindrical design, typically installed on interior doors | Office interiors, residential bathrooms | Pros: Simple installation. Cons: Not suitable for exterior doors due to vulnerability. |
Lever Handle Locks | Push down handle, often ADA compliant | Internal doors in commercial settings | Pros: Easier to operate for those with disabilities. Cons: Vulnerable to forced entry. |
Cam Locks | Cylindrical base with a rotating cam, lightweight design | Filing cabinets, mailboxes, furniture | Pros: Cost-effective for low-security needs. Cons: Easily bypassed; not for high-security applications. |
What Are the Characteristics of Padlocks and Their B2B Suitability?
Padlocks are a versatile locking solution, ideal for securing items like lockers, toolboxes, and storage sheds. They come in both combination and keyed varieties, allowing for flexibility in usage. For B2B buyers, the primary consideration is the level of security needed; while they are excellent for low to moderate security needs, businesses should be cautious when using them for high-value items due to their vulnerability to tampering.
How Do Deadbolts Provide Enhanced Security for Businesses?
Deadbolts are known for their robust security features, making them a preferred choice for external doors in commercial properties. Available in single, double, and lockable thumbturn variations, they offer flexibility based on the security requirements of the business. Buyers should consider the ease of rekeying and the potential need for emergency access, particularly with double-cylinder models, which require a key for both sides.
Why Are Knob Locks Commonly Used and What Are Their Limitations?
Knob locks are frequently found on interior doors, such as those in offices and residential bathrooms, due to their simple installation and cost-effectiveness. However, they are not recommended for exterior doors because their design can be easily compromised. B2B buyers should evaluate the security needs of their premises and consider replacing knob locks with more secure options for external applications.
What Makes Lever Handle Locks a Good Choice for Commercial Settings?
Lever handle locks are designed for ease of use, making them ideal for internal doors in commercial settings, especially where ADA compliance is required. Their push-down mechanism is accessible for individuals with disabilities, enhancing usability in public spaces. However, businesses should be aware of their vulnerability to forced entry and consider supplemental security measures if used in high-risk areas.
How Do Cam Locks Fit into the Security Landscape for Businesses?
Cam locks are lightweight and commonly used for securing filing cabinets, mailboxes, and other low-security applications. They are an economical choice for businesses needing basic security for non-critical items. However, their simplicity can be a double-edged sword; buyers should recognize that cam locks are not suitable for high-security needs and should be used judiciously within a broader security strategy.
Key Industrial Applications of kinds of locks
Industry/Sector | Specific Application of kinds of locks | Value/Benefit for the Business | Key Sourcing Considerations for this Application |
---|---|---|---|
Manufacturing | Securing machinery and equipment | Protects valuable assets and reduces theft risk | Durability, resistance to environmental factors, and key control options. |
Logistics and Warehousing | Locking storage containers and trailers | Enhances inventory security and prevents unauthorized access | Portability, weather resistance, and ease of use for frequent access. |
Hospitality | Guest room locks and access control systems | Ensures guest safety and enhances overall experience | Compliance with local regulations, ease of installation, and key management systems. |
Education | Locking cabinets and storage rooms | Protects sensitive materials and equipment | Variety of lock types, ease of rekeying, and compatibility with existing systems. |
Retail | Securing display cases and stock rooms | Reduces shrinkage and enhances customer trust | Aesthetic appeal, security features, and ease of integration into store layouts. |
How Are Kinds of Locks Used in the Manufacturing Sector?
In the manufacturing industry, locks are essential for securing machinery and sensitive equipment. Heavy-duty padlocks and deadbolts prevent unauthorized access, thereby safeguarding valuable assets and reducing the risk of theft or vandalism. Buyers should prioritize durability and resistance to environmental factors, as many manufacturing facilities operate in harsh conditions. Additionally, key control options are crucial to manage access for various staff levels.
What Applications Do Kinds of Locks Have in Logistics and Warehousing?
In logistics and warehousing, locks are vital for securing storage containers and trailers. This application helps enhance inventory security and prevents unauthorized access, which can lead to significant losses. Buyers in this sector should consider the portability of the locks, weather resistance, and ease of use for frequent access. The ability to quickly secure or access items can streamline operations and improve overall efficiency.
How Are Kinds of Locks Utilized in the Hospitality Industry?
In the hospitality sector, locks are crucial for guest room security and access control systems. They ensure guest safety and enhance the overall experience, as guests feel secure in their accommodations. Buyers must focus on compliance with local regulations, ease of installation, and the integration of advanced key management systems. The ability to provide electronic locks that can be easily reprogrammed for different guests is also a growing trend in this industry.
What Role Do Kinds of Locks Play in Educational Institutions?
Educational institutions frequently use locks to secure cabinets and storage rooms, protecting sensitive materials and equipment from theft or unauthorized access. This application is particularly important in laboratories and libraries where valuable resources are stored. Buyers should look for a variety of lock types that are easy to rekey and compatible with existing systems. This flexibility ensures that security measures can adapt as the needs of the institution evolve.
How Are Kinds of Locks Important in Retail Environments?
In retail, locks are used to secure display cases and stock rooms, playing a critical role in reducing shrinkage and enhancing customer trust. Effective locking mechanisms deter theft while ensuring that customers can view products safely. Buyers should consider the aesthetic appeal of the locks, as they need to blend seamlessly with store layouts. Additionally, security features and ease of integration into existing systems are vital for maintaining a secure shopping environment.
3 Common User Pain Points for ‘kinds of locks’ & Their Solutions
Scenario 1: Inadequate Security for Commercial Properties
The Problem:
Many B2B buyers in commercial sectors face the challenge of securing their properties effectively. The increasing incidents of break-ins and theft, especially in urban areas of Africa and South America, have made it crucial for businesses to invest in reliable security solutions. A common pain point arises when businesses use inadequate locks, such as knob locks or basic padlocks, which can easily be bypassed or broken. This not only puts their assets at risk but can also lead to increased insurance premiums and loss of customer trust.
The Solution:
To address this issue, businesses should prioritize the installation of high-security deadbolts or electronic locks. Deadbolts, especially double-cylinder variants, provide enhanced security by requiring a key for entry from both sides, making it difficult for intruders to gain access through nearby windows. When selecting deadbolts, buyers should consider models that offer features like pick resistance and bump-proof technology. Additionally, electronic locks with keypads or biometric access can provide flexibility and an audit trail for enhanced security management. It’s advisable to partner with reputable suppliers who specialize in commercial-grade locks and can offer tailored security assessments based on the unique needs of the business location.
Scenario 2: Challenges in Lock Compatibility Across Locations
The Problem:
For B2B buyers managing multiple facilities across different regions, such as in the Middle East and Europe, ensuring uniform lock compatibility can be a significant challenge. Different facilities may require various types of locks based on local regulations, building codes, or security needs, leading to confusion and inefficiency in key management. This often results in operational delays and increased costs related to maintaining different sets of keys or lock systems.
The Solution:
To streamline lock management, businesses should adopt a master key system that can accommodate various types of locks while maintaining security. A master key system allows a single key to access multiple locks, reducing the number of keys needed and simplifying access for authorized personnel. When implementing this system, it’s important to choose locks from a single manufacturer to ensure compatibility and reliability. Additionally, buyers should consider high-security locks that offer rekeying capabilities, allowing for easy updates to the system as personnel changes occur or if keys are lost. Engaging with a locksmith experienced in designing master key systems can provide valuable insights and ensure a smooth implementation process.
Scenario 3: High Replacement Costs Due to Wear and Tear
The Problem:
B2B buyers in sectors with high foot traffic, such as retail or hospitality, often encounter the issue of rapid wear and tear on locks, leading to frequent replacements. This not only incurs high costs but can also disrupt business operations. Locks such as cam locks and standard knob locks may not withstand heavy use, resulting in malfunctioning mechanisms that can compromise security.
The Solution:
To mitigate replacement costs, businesses should invest in heavy-duty locks designed for high-traffic environments. For example, commercial-grade lever handle locks or mortise locks are specifically engineered to endure rigorous use and are less prone to failure. When sourcing these locks, buyers should look for options with a warranty or a service plan that covers repairs and replacements. Furthermore, implementing a regular maintenance schedule can extend the lifespan of existing locks. This can include lubricating mechanisms, checking for alignment issues, and promptly addressing minor repairs before they escalate. Collaborating with a lock supplier that offers maintenance services can provide an added layer of convenience and assurance for long-term security investment.
Strategic Material Selection Guide for kinds of locks
When selecting locks for various applications, the choice of material is crucial for ensuring security, durability, and functionality. Here, we analyze four common materials used in the manufacturing of locks: steel, brass, zinc alloy, and plastic. Each material has distinct properties, advantages, and limitations that international B2B buyers must consider based on their specific needs.
What Are the Key Properties of Steel for Lock Manufacturing?
Steel is one of the most widely used materials for locks due to its strength and durability. It typically has a high tensile strength, making it resistant to physical attacks such as cutting or prying. Steel locks can withstand high temperatures and are often treated for corrosion resistance, which is critical in humid or coastal environments.
Pros & Cons:
– Pros: Exceptional strength and durability, good corrosion resistance when treated, and suitable for high-security applications.
– Cons: Heavier than other materials, can be more expensive, and may require additional coatings to prevent rusting.
Impact on Application: Steel locks are ideal for heavy-duty applications such as industrial facilities, high-security areas, and outdoor use. However, they may not be suitable for environments with extreme corrosive conditions unless properly treated.
Considerations for International Buyers: Compliance with local standards such as ASTM or DIN is essential. Buyers from regions like Africa and South America should consider the availability of treated steel options to combat corrosion in humid climates.
How Does Brass Compare as a Material for Locks?
Brass is a popular choice for locks due to its aesthetic appeal and resistance to corrosion. It has a moderate tensile strength and is often used in residential and commercial applications where security is important but not the highest priority.
Pros & Cons:
– Pros: Excellent corrosion resistance, attractive appearance, and relatively easy to machine.
– Cons: Weaker than steel, can be more expensive than zinc alloys, and may not be suitable for high-security applications.
Impact on Application: Brass locks are commonly used in residential doors, furniture, and decorative applications. They perform well in indoor environments but may not be ideal for outdoor use without additional protective coatings.
Considerations for International Buyers: Buyers in Europe and the Middle East often prefer brass for its aesthetic qualities. Compliance with local standards is also crucial, especially for decorative locks.
What Advantages Does Zinc Alloy Offer for Lock Production?
Zinc alloy is often used in lock manufacturing due to its lightweight nature and cost-effectiveness. It is less durable than steel or brass but can be designed to mimic their appearance through plating.
Pros & Cons:
– Pros: Lightweight, cost-effective, and can be produced in various shapes and finishes.
– Cons: Lower strength and durability compared to steel and brass, susceptible to corrosion if not coated.
Impact on Application: Zinc alloy locks are suitable for low-security applications such as cabinets, luggage, and temporary installations. They are not recommended for high-security environments.
Considerations for International Buyers: Given its affordability, zinc alloy is popular in developing markets. Buyers should ensure that the products meet local standards for safety and quality.
Why Is Plastic Used in Some Lock Applications?
Plastic locks are increasingly being utilized for specific applications due to their lightweight and non-corrosive properties. They are often used in combination with other materials to enhance security features.
Pros & Cons:
– Pros: Lightweight, resistant to corrosion, and can be produced in various colors and designs.
– Cons: Generally lower security compared to metal locks, can be easily broken or bypassed.
Impact on Application: Plastic locks are commonly used in indoor applications, such as securing lightweight items or for temporary use. They are not suitable for high-security needs.
Considerations for International Buyers: Buyers should assess the intended use carefully, especially in regions with high crime rates. Compliance with safety standards is essential, particularly in commercial applications.
Summary Table of Material Selection for Locks
Material | Typical Use Case for kinds of locks | Key Advantage | Key Disadvantage/Limitation | Relative Cost (Low/Med/High) |
---|---|---|---|---|
Steel | High-security industrial locks | Exceptional strength | Heavier and more expensive | High |
Brass | Residential and decorative locks | Excellent corrosion resistance | Weaker than steel | Medium |
Zinc Alloy | Low-security applications | Lightweight and cost-effective | Lower durability | Low |
Plastic | Indoor lightweight applications | Non-corrosive and versatile | Lower security | Low |
This strategic material selection guide provides B2B buyers with actionable insights into the advantages and limitations of various materials used in lock manufacturing. Understanding these factors will help ensure that the selected locks meet both security requirements and environmental conditions specific to their operational regions.
In-depth Look: Manufacturing Processes and Quality Assurance for kinds of locks
What Are the Main Stages of Lock Manufacturing Processes?
The manufacturing of locks involves several crucial stages, each designed to ensure that the final product meets both functional and security standards. The primary stages include material preparation, forming, assembly, and finishing.
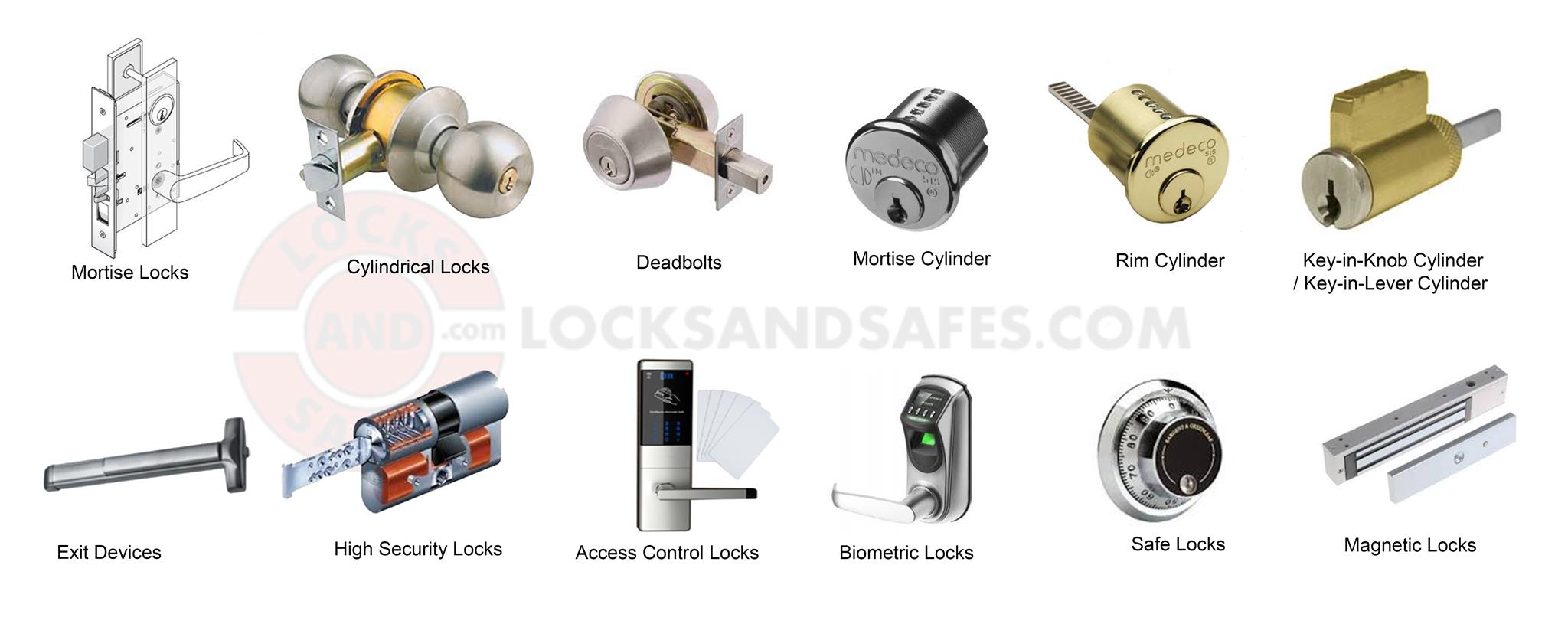
A stock image related to kinds of locks.
How Is Material Prepared for Lock Production?
The process begins with the selection of appropriate materials, which typically include various metals (e.g., brass, steel, zinc alloys) known for their durability and resistance to tampering. The materials are then cut, shaped, and treated to ensure they can withstand physical wear and environmental conditions.
For instance, steel components may undergo galvanization to prevent rust, while brass parts might be polished to enhance aesthetic appeal. B2B buyers should ensure their suppliers source high-quality materials, as the integrity of the lock is heavily dependent on the raw materials used.
What Techniques Are Used in the Forming Stage of Lock Manufacturing?
In the forming stage, manufacturers utilize techniques such as casting, machining, and stamping to shape lock components.
- Casting involves pouring molten metal into molds to create complex shapes, allowing for intricate designs that enhance security features.
- Machining is employed for precision parts, where tools are used to cut and shape the material into exact specifications.
- Stamping uses dies to press shapes into sheet metal, often used for simpler components like lock housings.
These methods ensure that each part fits together correctly, which is vital for the lock’s functionality and security.
How Is Assembly Conducted in Lock Manufacturing?
Once the components are formed, the assembly process begins. This typically involves:
- Fitting Together Components: Each part, such as the cylinder, bolt, and casing, is carefully assembled to ensure smooth operation.
- Incorporating Security Features: Advanced locks may include additional features like anti-drill plates or pick-resistant pins. This is where manufacturers often differentiate their products in the market.
B2B buyers should inquire about the assembly techniques used, as automated assembly lines can enhance precision and reduce human error.
What Are the Key Finishing Techniques in Lock Production?
The finishing stage is essential for both aesthetics and functionality. This stage may involve:
- Coating: Locks may be coated with paints, powder coatings, or plating to enhance corrosion resistance and durability.
- Polishing and Buffing: These processes improve the appearance of visible surfaces and can help reduce friction during use.
Quality finishes can also indicate the manufacturer’s commitment to quality, making it a crucial factor for B2B buyers when selecting suppliers.
Which International Standards Should B2B Buyers Consider for Quality Assurance?
Quality assurance in lock manufacturing is governed by various international standards, which help ensure that products are safe, reliable, and meet customer expectations. Key standards include:
- ISO 9001: This standard focuses on quality management systems and is applicable to any organization that wants to enhance customer satisfaction through effective quality management.
- CE Marking: In Europe, locks that meet specific safety, health, and environmental protection requirements must carry the CE mark.
- API Standards: For locks used in specific industries (e.g., oil and gas), the American Petroleum Institute (API) provides standards that must be adhered to.
B2B buyers should ensure that their suppliers comply with these standards, as they reflect the manufacturer’s commitment to quality.
What Are the Quality Control Checkpoints in Lock Manufacturing?
Quality control (QC) checkpoints are critical throughout the manufacturing process to ensure that each lock meets the required specifications. Common checkpoints include:
- Incoming Quality Control (IQC): This involves inspecting raw materials upon arrival to verify their quality and compliance with specifications.
- In-Process Quality Control (IPQC): During manufacturing, periodic checks are performed to ensure that the production process is within specified limits.
- Final Quality Control (FQC): After assembly, locks undergo rigorous testing to ensure they function correctly and meet durability standards.
B2B buyers should request details about their suppliers’ QC processes to ensure they are purchasing reliable products.
Which Testing Methods Are Commonly Used in Lock Quality Control?
Manufacturers employ various testing methods to validate the integrity and security of locks, including:
- Cycle Testing: Locks are opened and closed repeatedly to simulate long-term usage and ensure durability.
- Corrosion Testing: Products are exposed to corrosive environments to assess resistance to rust and degradation.
- Tamper Testing: Locks are subjected to forced entry attempts to evaluate their resistance to break-ins.
Understanding the testing methods used can help B2B buyers gauge the quality and reliability of locks.
How Can B2B Buyers Verify Supplier Quality Control?
To ensure that their suppliers maintain high-quality standards, B2B buyers should consider several verification strategies:
- Supplier Audits: Regular audits can help assess the supplier’s adherence to quality standards and manufacturing processes.
- Quality Reports: Requesting documented evidence of quality control procedures and test results can provide insights into the manufacturer’s commitment to quality.
- Third-Party Inspections: Engaging third-party inspection agencies can provide an unbiased assessment of the supplier’s quality control practices.
These strategies are particularly important for international buyers from regions like Africa, South America, the Middle East, and Europe, where verifying quality can mitigate risks associated with procurement.
What Are the Quality Control and Certification Nuances for International B2B Buyers?
When sourcing locks internationally, B2B buyers should be aware of specific nuances related to quality control and certification. For example:
- Regional Certifications: Different regions may have unique certification requirements (e.g., UL certification in the U.S. or EN standards in Europe). Buyers should verify that the products meet local regulations.
- Language Barriers: Documentation and certifications may be in different languages, which can lead to misunderstandings. It’s advisable to have translations or local representatives who can assist.
- Cultural Differences: Understanding the cultural context of your supplier can help navigate negotiations and build trust, essential for long-term partnerships.
By being informed about these nuances, B2B buyers can better navigate the complexities of international procurement in the lock industry.
Practical Sourcing Guide: A Step-by-Step Checklist for ‘kinds of locks’
When sourcing locks for your business, whether for commercial properties, industrial facilities, or retail outlets, it is essential to follow a structured approach. This guide provides a practical checklist designed to help B2B buyers navigate the complexities of lock procurement effectively.
Step 1: Identify Your Security Needs
Understanding the specific security requirements of your operation is the first step in selecting the right locks. Consider factors such as the type of property (commercial, residential, industrial), the potential threats (theft, vandalism), and the access control needs (who needs access and when). This assessment will guide your choice of lock types, such as deadbolts for external doors or lever locks for internal areas.
Step 2: Define Technical Specifications
Once you have assessed your security needs, it’s important to outline the technical specifications for the locks you require. This includes the lock types (e.g., deadbolts, padlocks, cam locks), materials (stainless steel, brass), and features (keyless entry, smart locks). Clearly defining these criteria will streamline the sourcing process and ensure that you receive products that meet your operational standards.
Step 3: Research and Shortlist Suppliers
Thorough research is crucial in identifying reliable suppliers. Look for manufacturers or distributors with a strong reputation in the market, particularly those who specialize in the types of locks you need. Pay attention to their experience, product range, and customer reviews. Shortlist at least three to five suppliers for further evaluation.
Step 4: Verify Supplier Certifications and Compliance
Before making a commitment, ensure that your shortlisted suppliers have the necessary certifications and comply with international security standards. Look for ISO certifications, compliance with local regulations, and any industry-specific endorsements. This step is vital to ensure that the locks you procure meet quality and safety benchmarks.
Step 5: Request Samples for Testing
Request samples of the locks you are considering to evaluate their quality and functionality. Testing the locks in real-world scenarios allows you to assess their durability, ease of use, and effectiveness against unauthorized access. This hands-on experience is invaluable in making an informed purchasing decision.
Step 6: Negotiate Pricing and Terms
Once you have selected your preferred suppliers based on product testing, enter negotiations regarding pricing, payment terms, and delivery schedules. Be prepared to discuss bulk purchasing discounts, warranty conditions, and after-sales support. Effective negotiation can lead to cost savings and improved service agreements.
Step 7: Plan for Installation and Maintenance
After procurement, consider how the locks will be installed and maintained. If necessary, engage professional locksmith services for installation to ensure proper functionality and security. Additionally, establish a maintenance plan to regularly check and service the locks, thereby prolonging their lifespan and ensuring continued security.
By following these steps, B2B buyers can make informed decisions when sourcing locks, ultimately enhancing the security of their properties while optimizing procurement efficiency.
Comprehensive Cost and Pricing Analysis for kinds of locks Sourcing
What Are the Key Cost Components in Lock Manufacturing?
When sourcing locks for B2B applications, understanding the cost structure is essential. The primary cost components include:
-
Materials: The type of materials used significantly impacts the overall cost. High-security locks often utilize advanced materials like hardened steel or brass, which can increase expenses. Conversely, lower-grade materials can reduce costs but may compromise security.
-
Labor: Labor costs vary by region and can affect the final pricing of locks. In countries with higher labor costs, such as those in Europe, the manufacturing price may be higher compared to regions with lower labor costs, like parts of Africa or South America.
-
Manufacturing Overhead: This includes costs related to utilities, facility maintenance, and administrative expenses. Efficient manufacturers often have lower overhead, which can translate to competitive pricing.
-
Tooling: Initial setup and tooling costs for producing specific lock types can be substantial. Custom locks or high-precision locks require specialized tooling, impacting pricing.
-
Quality Control (QC): Ensuring locks meet safety standards and certifications is critical. Rigorous QC processes may add to the cost but are essential for compliance, especially in regulated markets.
-
Logistics: Shipping costs can vary widely based on the distance from the manufacturing site to the buyer. Additionally, incoterms will influence who bears the transportation costs, further affecting the total price.
-
Margin: Manufacturers typically add a profit margin to cover risks and ensure sustainability. This margin can fluctuate based on market demand and competition.
How Do Price Influencers Affect Lock Sourcing?
Several factors can influence the pricing of locks significantly:
-
Volume/MOQ (Minimum Order Quantity): Bulk purchasing often results in lower per-unit costs. Understanding the supplier’s MOQ can help buyers negotiate better pricing.
-
Specifications and Customization: Customized locks tailored to specific needs will incur additional costs. Buyers should evaluate whether the customization aligns with their security needs and budget.
-
Materials and Quality Certifications: Locks made from premium materials or those that meet specific international certifications (e.g., ISO) tend to be priced higher. Buyers should assess the importance of these features based on their application.
-
Supplier Factors: The reputation and reliability of suppliers can impact pricing. Established suppliers may charge more due to their proven track record but could offer superior quality and service.
-
Incoterms: Understanding shipping and delivery terms is crucial. Different incoterms can shift costs and responsibilities between buyers and suppliers, affecting the overall pricing structure.
What Are Effective Buyer Tips for Cost-Efficiency in Lock Sourcing?
B2B buyers can employ various strategies to enhance cost-efficiency when sourcing locks:
-
Negotiate Terms: Engaging in discussions with suppliers about pricing and payment terms can yield better deals. Leverage your purchasing power, especially if you’re placing large orders.
-
Consider Total Cost of Ownership (TCO): Evaluate not just the purchase price but also the long-term costs associated with maintenance, potential security breaches, and replacement. Higher upfront costs may lead to lower TCO if the locks are more durable.
-
Research Market Prices: Stay informed about prevailing market prices for different types of locks. This knowledge can empower buyers during negotiations and help avoid overpayment.
-
Assess Shipping Options: Evaluate different shipping methods and providers to find the most cost-effective logistics solutions. Consider local suppliers to reduce shipping costs and time.
-
Be Aware of Pricing Nuances for International Buyers: Understand that currency fluctuations, tariffs, and trade agreements can impact costs for international transactions. Buyers from Africa, South America, the Middle East, and Europe should stay informed about these factors to make informed purchasing decisions.
Conclusion
Sourcing locks involves a comprehensive understanding of costs and pricing factors. By analyzing the cost components, recognizing price influencers, and applying effective buyer strategies, international B2B buyers can make informed decisions that balance security needs with budget constraints. Always consider the broader context of the purchase, including long-term implications and market conditions, to ensure optimal sourcing outcomes.
Alternatives Analysis: Comparing kinds of locks With Other Solutions
Understanding Alternatives to Traditional Lock Solutions
As international B2B buyers explore security options, understanding alternatives to traditional locks is essential. While various types of locks, such as padlocks and deadbolts, provide basic security, advancements in technology have introduced alternative solutions that may offer enhanced security, convenience, and cost-effectiveness. Below, we compare traditional lock types with two viable alternatives: electronic access control systems and biometric security solutions.
Comparison Table of Lock Solutions
Comparison Aspect | Kinds of Locks | Electronic Access Control Systems | Biometric Security Solutions |
---|---|---|---|
Performance | Basic security, varying strength | High security, customizable access | High security, unique identification |
Cost | Generally low to moderate | Moderate to high initial investment | High initial investment, low maintenance |
Ease of Implementation | Simple installation | Requires professional installation | Requires professional installation |
Maintenance | Low maintenance | Regular software updates needed | Low maintenance, calibration may be needed |
Best Use Case | Residential and small business | Commercial buildings, restricted areas | High-security facilities, data centers |
Pros and Cons of Electronic Access Control Systems
Electronic access control systems replace traditional keys with card readers, keypads, or mobile apps. Pros include customizable access levels, audit trails for tracking who entered where and when, and remote management capabilities, making them ideal for businesses with multiple locations. However, the cons include higher initial costs and the need for ongoing software updates and maintenance to ensure security systems are functioning optimally. For B2B buyers in commercial sectors, this solution provides a robust alternative to traditional locking mechanisms, especially in environments that require frequent access changes.
Pros and Cons of Biometric Security Solutions
Biometric security solutions utilize unique biological traits, such as fingerprints or facial recognition, to grant access. The pros of this technology include enhanced security since it is nearly impossible to duplicate a biometric feature, and it eliminates the need for keys or access cards. However, the cons include higher costs for installation and equipment, as well as potential privacy concerns regarding the storage and management of biometric data. For organizations prioritizing security, particularly in sensitive environments such as data centers or government facilities, biometric solutions can be an effective alternative to traditional locks.
Conclusion: Choosing the Right Security Solution for Your Needs
When considering alternatives to traditional locks, B2B buyers must evaluate their specific security needs, budget constraints, and operational requirements. While traditional locks may suffice for residential and low-risk environments, electronic access control systems and biometric solutions present compelling advantages for commercial applications and high-security settings. By carefully assessing the pros and cons of each option, businesses can select the most appropriate security measures to protect their assets and ensure efficient operations.
Essential Technical Properties and Trade Terminology for kinds of locks
What Are the Critical Technical Properties of Different Types of Locks?
When selecting locks for commercial applications, understanding their technical properties is crucial for ensuring security and functionality. Here are some key specifications that international B2B buyers should consider:
1. Material Grade: Why Does It Matter?
Locks are primarily made from materials such as brass, stainless steel, and zinc alloy. The material grade significantly affects durability, resistance to corrosion, and overall security. For example, stainless steel locks are ideal for outdoor applications due to their weather resistance, while brass locks may provide a more aesthetic appeal for indoor use. Buyers should assess the environment where the locks will be used to select the appropriate material.
2. Security Rating: What Does It Indicate?
Many locks come with security ratings that indicate their resistance to tampering and forced entry. Ratings often range from 1 to 3, with 1 being the most secure. This rating is essential for businesses that handle sensitive materials or high-value assets. Understanding these ratings can help buyers choose locks that meet their specific security needs, especially in regions with higher crime rates.
3. Tolerance: Why Is Precision Important?
Tolerance refers to the allowable variation in dimensions of the lock components. A tighter tolerance often results in better alignment and smoother operation, minimizing the chances of jamming or malfunction. For B2B buyers, especially those in manufacturing or construction, selecting locks with appropriate tolerances can prevent costly replacements and maintenance issues.
4. Key Control: How Does It Affect Security?
Key control is a specification that defines how keys are distributed and managed. Some locks offer restricted key systems, meaning only authorized personnel can obtain duplicate keys. This property is particularly important for businesses that require tight control over access, such as financial institutions or data centers. Understanding key control options can help buyers enhance their overall security posture.
5. Locking Mechanism: What Are the Options?
Different locking mechanisms, such as deadbolts, knob locks, and lever handle locks, serve various functions. Each type has its advantages and disadvantages based on application. For instance, deadbolts offer higher security for external doors, while cam locks are suitable for low-security applications like cabinets. Buyers should evaluate the specific needs of their premises to select the most appropriate locking mechanism.
What Are Common Trade Terms in the Lock Industry?
Familiarizing yourself with industry-specific terminology is essential for effective communication and negotiation in the B2B landscape. Here are some common terms that buyers should know:
1. OEM (Original Equipment Manufacturer): What Does It Mean?
OEM refers to companies that produce parts or equipment that may be marketed by another manufacturer. In the locks industry, understanding OEM specifications can ensure compatibility and quality in lock components. Buyers often seek OEM products for reliability and adherence to industry standards.
2. MOQ (Minimum Order Quantity): How Does It Impact Purchasing?
MOQ is the minimum number of units that a supplier is willing to sell in a single order. Knowing the MOQ is crucial for budgeting and inventory management. Buyers should negotiate MOQs to align with their project needs while considering storage and cash flow constraints.
3. RFQ (Request for Quotation): When Should You Use It?
An RFQ is a document sent to suppliers to request pricing and terms for specific products. It’s an essential tool for B2B buyers to ensure competitive pricing and gather information on various suppliers. Crafting a clear and detailed RFQ can lead to better responses and facilitate informed decision-making.
4. Incoterms: Why Are They Important for International Trade?
Incoterms (International Commercial Terms) are standardized trade terms that define the responsibilities of buyers and sellers in international transactions. They dictate who pays for shipping, insurance, and tariffs. Understanding Incoterms can help buyers mitigate risks and clarify obligations in cross-border purchases.
5. Lead Time: What Should You Expect?
Lead time is the duration between placing an order and receiving the goods. It can vary widely based on the supplier’s location, production capacity, and shipping method. For B2B buyers, understanding lead times is essential for planning and ensuring that security needs are met promptly.
By grasping these technical properties and trade terms, B2B buyers can make informed decisions when sourcing locks, ultimately enhancing their security measures and operational efficiency.
Navigating Market Dynamics and Sourcing Trends in the kinds of locks Sector
What Are the Key Market Dynamics and Trends in the Kinds of Locks Sector?
The global locks market is experiencing a paradigm shift driven by technological advancements, changing consumer preferences, and increased security awareness. International B2B buyers, particularly from regions like Africa, South America, the Middle East, and Europe, should note that the rise in urbanization and crime rates is prompting businesses to invest in high-security locking solutions. Key trends include the adoption of smart locks equipped with IoT technology, allowing for remote access control and enhanced security features. In addition, biometric locks are gaining traction, particularly in corporate and high-security environments, as they provide a higher level of authentication.
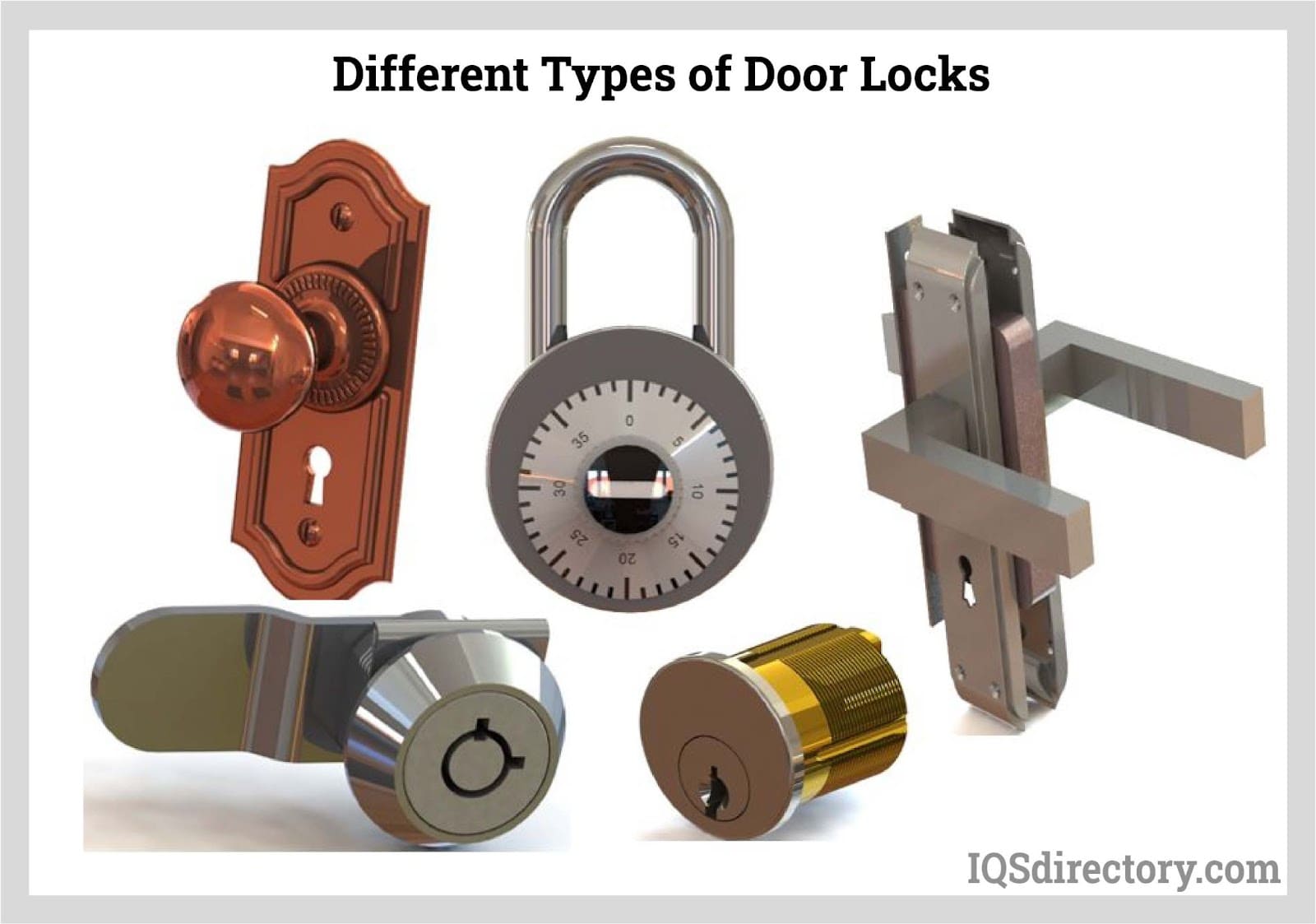
A stock image related to kinds of locks.
Moreover, the sourcing landscape is evolving with a focus on regional suppliers who can offer both cost-effective solutions and faster delivery times. This trend is particularly relevant for buyers in Africa and South America, where logistics can be a challenge. Leveraging local manufacturers can not only reduce lead times but also foster stronger business relationships. Additionally, suppliers that can provide customization options are increasingly sought after, as businesses look to tailor security solutions to their specific needs.
How Can Sustainability and Ethical Sourcing Impact the Kinds of Locks Market?
Sustainability is becoming a critical consideration for B2B buyers in the locks sector. The environmental impact of manufacturing processes and materials used in locks is under scrutiny, prompting companies to seek ‘green’ certifications and sustainable materials. For instance, locks made from recycled metals or sustainably sourced materials are gaining popularity. Buyers should prioritize suppliers who demonstrate a commitment to sustainability through eco-friendly practices and certifications like ISO 14001, which pertains to effective environmental management systems.
Ethical sourcing is equally important, especially in regions where labor practices may vary significantly. Ensuring that suppliers adhere to fair labor practices not only enhances brand reputation but also mitigates risks associated with supply chain disruptions. Buyers should conduct due diligence on their suppliers to confirm compliance with international labor standards. By fostering ethical supply chains, businesses can contribute positively to their communities and improve their market standing.
What Is the Historical Context Behind the Evolution of Locks?
The evolution of locks can be traced back thousands of years, with the earliest known locks made of wood and used by the ancient Egyptians. Over the centuries, materials and technologies have advanced significantly, leading to the creation of more sophisticated locking mechanisms. The introduction of the pin tumbler lock in the 19th century revolutionized security, making locks more difficult to pick and thereby enhancing their effectiveness.
In recent years, the focus has shifted towards electronic and smart locks, reflecting the broader technological advancements in security systems. These modern locks not only provide enhanced security features but also integrate with other smart home technologies, appealing to a tech-savvy clientele. For B2B buyers, understanding this historical evolution can inform purchasing decisions, as it highlights the importance of investing in reliable and innovative locking solutions that meet contemporary security needs.
Frequently Asked Questions (FAQs) for B2B Buyers of kinds of locks
-
How do I choose the right type of lock for my business needs?
Selecting the appropriate lock depends on several factors, including the level of security required, the type of door or compartment, and environmental conditions. For high-security needs, deadbolts and padlocks are often recommended, while cam locks may suffice for lighter applications, like office cabinets. Consider the lock’s durability, resistance to tampering, and whether it meets local regulations. Additionally, consult with security experts or suppliers who can provide tailored recommendations based on your specific industry and application. -
What is the best deadbolt lock for commercial properties?
The best deadbolt for commercial properties typically includes a double cylinder deadbolt, which requires a key for both entry and exit. This design is beneficial for external doors where windows are nearby, as it prevents unauthorized access from inside. Look for deadbolts that are ANSI Grade 1 rated for maximum security. Additionally, consider features such as rekeyability and weather resistance, especially for businesses in regions with extreme climates. -
What are the key factors to consider when vetting lock suppliers internationally?
When vetting international lock suppliers, focus on their reputation, certifications, and compliance with international standards. Check their manufacturing processes, quality assurance measures, and customer reviews. It’s also important to assess their ability to communicate effectively and respond to inquiries. Request samples to evaluate product quality before placing large orders. Lastly, ensure they have robust logistics capabilities to handle shipping and customs processes in your region. -
How can I customize locks for my specific security needs?
Many manufacturers offer customization options such as specific keying systems, sizes, and finishes. To customize locks, clearly outline your requirements, including the type of materials and design features you need. Engage in discussions with suppliers about their capabilities and minimum order quantities for custom products. Custom locks can enhance security tailored to your business environment, ensuring that you have unique solutions that meet your operational needs. -
What are the minimum order quantities (MOQs) for locks when sourcing internationally?
Minimum order quantities vary by supplier and the type of locks ordered. Typically, MOQs for standard locks can range from 50 to several hundred units, while customized locks may have higher MOQs due to the costs associated with manufacturing. Always clarify MOQs before finalizing orders, as this can significantly affect your budget and inventory management. Consider negotiating with suppliers for lower MOQs, especially if you are establishing a new relationship. -
What payment terms should I expect when sourcing locks from international suppliers?
Payment terms can vary widely, but common practices include advance payments, letters of credit, or payment upon delivery. Many suppliers may require a deposit (usually 30%) before production, with the balance due upon completion or shipment. It’s crucial to discuss and agree on payment terms upfront to avoid misunderstandings. Additionally, consider using secure payment methods that protect both parties during the transaction process. -
How do I ensure quality assurance when importing locks?
To ensure quality assurance, request detailed product specifications and certifications from your supplier. Conduct factory audits if possible, or hire third-party inspection services to assess products before shipment. Establish clear quality benchmarks and acceptance criteria, and include these in your contract. Regular communication with your supplier during the production phase can also help mitigate issues and ensure that the final products meet your standards. -
What logistics considerations should I keep in mind when importing locks?
When importing locks, consider the logistics of shipping, including the choice of freight forwarder, shipping methods, and customs clearance processes. Evaluate the costs associated with shipping, insurance, and potential tariffs or duties. Ensure that your supplier can provide necessary documentation for customs, such as invoices and certificates of origin. Additionally, plan for lead times and potential delays, especially in regions with complex customs regulations.
Important Disclaimer & Terms of Use
⚠️ Important Disclaimer
The information provided in this guide, including content regarding manufacturers, technical specifications, and market analysis, is for informational and educational purposes only. It does not constitute professional procurement advice, financial advice, or legal advice.
While we have made every effort to ensure the accuracy and timeliness of the information, we are not responsible for any errors, omissions, or outdated information. Market conditions, company details, and technical standards are subject to change.
B2B buyers must conduct their own independent and thorough due diligence before making any purchasing decisions. This includes contacting suppliers directly, verifying certifications, requesting samples, and seeking professional consultation. The risk of relying on any information in this guide is borne solely by the reader.
Strategic Sourcing Conclusion and Outlook for kinds of locks
How Can Strategic Sourcing Enhance Your Lock Procurement Process?
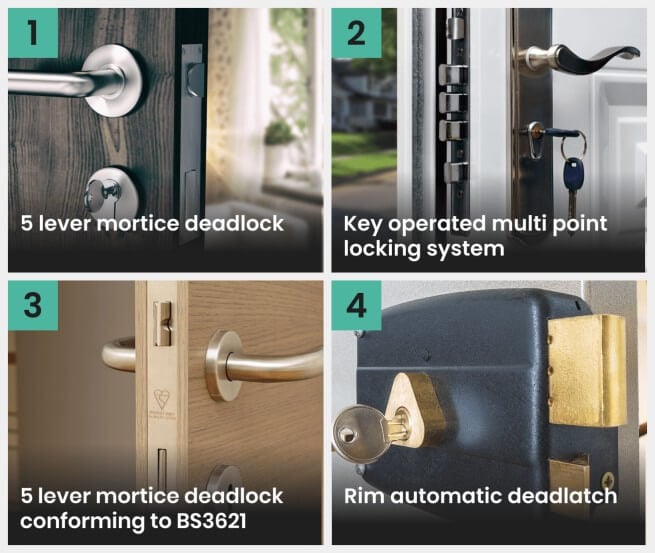
A stock image related to kinds of locks.
In today’s competitive marketplace, strategic sourcing for locks is essential for international B2B buyers seeking optimal security solutions. Understanding the diverse types of locks—such as padlocks, deadbolts, knob locks, and lever handle locks—enables businesses to make informed purchasing decisions tailored to their specific security needs. By prioritizing quality, durability, and functionality, buyers can ensure that their investments provide long-term protection for their assets.
Moreover, engaging with reputable suppliers who understand the unique security challenges faced in regions like Africa, South America, the Middle East, and Europe can further streamline the sourcing process. Buyers should consider not only price but also the supplier’s reputation, product certifications, and after-sales support. This comprehensive approach to sourcing not only enhances security but also fosters long-term partnerships that can lead to better pricing and exclusive access to innovative products.
What’s Next for B2B Buyers in the Lock Industry?
As we look to the future, the demand for advanced locking mechanisms will continue to rise, driven by increased security concerns globally. International buyers are encouraged to stay informed about emerging technologies, such as smart locks and biometric systems, which are reshaping the landscape of security solutions. By adopting a proactive stance in sourcing and investing in the latest technologies, businesses can safeguard their operations and build a resilient security framework. Take the next step in your strategic sourcing journey—evaluate your current security measures and explore new partnerships to enhance your locking solutions today.