Discover 7 Key Conveyor Belt Types for Your Business Needs (2025)
Introduction: Navigating the Global Market for conveyor belt types
As businesses expand their operations globally, sourcing the right conveyor belt types becomes a critical challenge for B2B buyers. Selecting the most suitable conveyor system is essential not only for optimizing production efficiency but also for enhancing overall supply chain performance. This comprehensive guide delves into the various types of conveyor belts, such as flat belts, modular belts, and roller conveyors, detailing their unique applications across industries. We will also explore the intricacies of supplier vetting, cost considerations, and maintenance requirements, empowering you to make informed purchasing decisions.
International B2B buyers from regions like Africa, South America, the Middle East, and Europe face unique challenges, including navigating local regulations and understanding market dynamics. This guide aims to equip you with actionable insights tailored to your regional context, ensuring you choose the best conveyor solutions for your specific operational needs. By addressing the diverse applications and advantages of different conveyor belt types, we will help you streamline your procurement process and enhance productivity. Whether you are in manufacturing, logistics, or any sector that relies on efficient material handling, this guide serves as your essential resource for navigating the global market for conveyor belt systems.
Understanding conveyor belt types Types and Variations
Type Name | Key Distinguishing Features | Primary B2B Applications | Brief Pros & Cons for Buyers |
---|---|---|---|
Flat Belt Conveyors | Continuous flat surface, versatile material options | Assembly lines, packaging, food processing | Pros: Cost-effective, easy to maintain. Cons: Limited incline capabilities. |
Modular Belt Conveyors | Made of interlocked plastic segments, customizable layouts | Food handling, packaging, and manufacturing | Pros: Easy to clean and replace, suitable for complex paths. Cons: Higher initial cost. |
Cleated Belt Conveyors | Vertical cleats for material containment during transport | Bulk material handling, food processing | Pros: Prevents material slippage, ideal for inclines. Cons: Can be more expensive due to design complexity. |
Roller Bed Conveyors | Comprised of rollers that reduce friction for moving goods | Sorting, airport baggage handling, warehousing | Pros: Efficient for long distances, low friction. Cons: Requires more space and can be expensive to install. |
Metal Conveyor Belts | Constructed from metal, offering durability and strength | Heavy-duty applications, automotive, mining | Pros: Excellent for high-temperature materials, robust. Cons: Heavier and can be more costly to maintain. |
What are Flat Belt Conveyors and Their Key Features?
Flat belt conveyors are one of the most commonly used types in various industries, characterized by their continuous flat surface. They can be made from rubber, synthetic composites, or leather, making them suitable for transporting a wide range of products. Buyers should consider their operational environment, as flat belts work best in horizontal settings and may struggle with steep inclines. Their low profile and versatility make them an economical choice for assembly lines, packaging, and food processing applications.
How Do Modular Belt Conveyors Stand Out?
Modular belt conveyors utilize a series of interlocked plastic segments, allowing for easy customization and maintenance. This type is particularly advantageous in food handling and packaging due to its cleanability and ability to navigate complex pathways. When selecting a modular belt, businesses should assess the need for flexibility in their operations and the types of materials being conveyed. While the initial investment may be higher than traditional belts, the long-term savings in maintenance and downtime can offset these costs.
What Benefits Do Cleated Belt Conveyors Provide?
Cleated belt conveyors are designed with vertical cleats that secure materials during transport, making them ideal for moving bulk items up inclines or declines. This feature is particularly beneficial in industries such as agriculture and food processing, where material containment is crucial. Buyers should evaluate the specific cleat design needed for their applications, as different shapes cater to various material types. While they may come at a premium, the enhanced efficiency and reduced material loss can lead to significant operational savings.
Why Choose Roller Bed Conveyors?
Roller bed conveyors consist of a series of rollers that facilitate the movement of goods, significantly reducing friction. This makes them suitable for long-distance transport and applications such as sorting and airport baggage handling. When considering roller bed conveyors, businesses should assess space availability and loading methods, as they require more room than other types. Although installation costs can be higher, their efficiency in moving heavy items can justify the investment.
What Are the Advantages of Metal Conveyor Belts?
Metal conveyor belts are robust and durable, making them ideal for heavy-duty applications, including automotive and mining industries. Their ability to withstand high temperatures and harsh conditions is a key consideration for buyers in these sectors. However, the weight and maintenance costs associated with metal belts should also be factored into purchasing decisions. For businesses needing a reliable solution for challenging environments, metal conveyor belts offer a long-lasting and effective option.
Key Industrial Applications of conveyor belt types
Industry/Sector | Specific Application of Conveyor Belt Types | Value/Benefit for the Business | Key Sourcing Considerations for this Application |
---|---|---|---|
Food & Beverage | Modular Belt Conveyors for food handling | Enhanced hygiene and easy maintenance | Material safety certifications, ease of cleaning |
Mining & Minerals | Bucket Conveyors for bulk material transport | Efficient handling of heavy materials | Durability under extreme conditions, load capacity |
Automotive Manufacturing | Timing Belts in assembly lines | Precision in power transmission | Compatibility with existing machinery, tensile strength |
Logistics & Warehousing | Roller Bed Conveyors for package sorting | Increased throughput and reduced manual labor | Space requirements, load specifications |
Agriculture | Cleated Belt Conveyors for grain transport | Secure movement of loose materials on inclines | Cleat design suitability, material compatibility |
How Are Conveyor Belt Types Used in the Food & Beverage Industry?
In the food and beverage sector, modular belt conveyors are pivotal for transporting products safely through various stages of processing. Their design allows for easy cleaning, which is essential in maintaining hygiene standards. These conveyors can handle diverse shapes and sizes of food items while minimizing contamination risks. International buyers should ensure that the materials used comply with food safety regulations and that the belts can be easily disassembled for thorough cleaning.
What Role Do Conveyor Belt Types Play in Mining & Minerals?
In the mining industry, bucket conveyors are essential for transporting bulk materials like ores and minerals from one location to another. They efficiently handle heavy loads, reducing the need for manual labor and increasing operational efficiency. Buyers from regions with harsh mining conditions should focus on sourcing durable bucket conveyors that can withstand extreme wear and tear, as well as high-capacity models that align with their production needs.
How Are Timing Belts Utilized in Automotive Manufacturing?
Timing belts are crucial in automotive manufacturing, particularly in assembly lines where precise power transmission is necessary for engine components. They interlock with camshafts and crankshafts to ensure synchronized movement, which is vital for engine performance. B2B buyers should prioritize sourcing timing belts that meet the specific tolerances and compatibility requirements of their machinery to ensure optimal performance and longevity.
What Advantages Do Roller Bed Conveyors Offer in Logistics & Warehousing?
Roller bed conveyors are widely used in logistics and warehousing for sorting and transporting packages. Their design allows for gravity-fed loading, reducing friction and facilitating the movement of heavy items over long distances. This results in increased throughput and a reduction in manual handling. When sourcing roller bed conveyors, businesses should consider the available space, load specifications, and the conveyor’s adaptability to different package sizes.
How Do Cleated Belt Conveyors Benefit the Agriculture Sector?
Cleated belt conveyors are particularly beneficial in the agriculture industry for transporting loose materials like grains. The vertical cleats prevent materials from sliding backward during transport, making them ideal for inclines. Buyers in this sector should focus on the design and material of the cleats to ensure they are suited for the types of grains being handled, as well as the conveyor’s overall durability and maintenance requirements.
3 Common User Pain Points for ‘conveyor belt types’ & Their Solutions
Scenario 1: Inefficiency in Material Handling Processes
The Problem: Many B2B buyers, particularly in sectors like manufacturing and logistics, often face challenges with inefficient material handling processes. This can manifest as bottlenecks in production lines or excessive downtime due to conveyor belt malfunctions. For example, a manufacturer might find that their flat belt conveyor frequently jams due to improper loading techniques or unsuitable belt material, leading to costly delays and reduced productivity. Such inefficiencies can directly impact a company’s bottom line and customer satisfaction.
The Solution: To mitigate these issues, it is crucial to choose the right type of conveyor belt for specific applications. Buyers should conduct a thorough analysis of their operational needs, including the types of materials being transported and the required speed and load capacity. When selecting a flat belt conveyor, consider investing in a model that features adjustable speed settings and a robust material composition to handle varying weights and sizes. Furthermore, implementing regular maintenance schedules and training staff on proper loading techniques can significantly reduce the risk of jams and enhance overall efficiency. Engaging with suppliers who offer comprehensive support and after-sales services can also ensure that your conveyor system remains in optimal condition.
Scenario 2: Difficulty in Selecting the Right Conveyor Belt Type
The Problem: B2B buyers often struggle to determine which type of conveyor belt is best suited for their specific application. With a plethora of options available—such as roller bed conveyors, modular belts, and cleated belt systems—making the right choice can be overwhelming. For instance, a buyer in the food industry may require a conveyor belt that not only transports goods effectively but is also easy to clean and compliant with food safety regulations. Inadequate research can lead to poor investment decisions that ultimately affect operational efficiency.
The Solution: To navigate this challenge, buyers should begin with a clear understanding of their operational requirements and constraints. Conducting a needs assessment that includes factors like load size, weight, material type, and environmental conditions is essential. Engage with experienced suppliers who can provide insights and recommendations based on industry standards and best practices. Additionally, consider utilizing simulation software or consulting with engineering experts to visualize how different conveyor types will perform in your specific environment. This proactive approach will help in making informed decisions, ensuring that the selected conveyor belt not only meets current needs but is also adaptable for future requirements.
Scenario 3: Maintenance Challenges Leading to Increased Downtime
The Problem: Maintenance issues are a significant pain point for B2B buyers of conveyor belt systems, particularly in regions with limited access to skilled technicians or replacement parts. Conveyor belts can experience wear and tear, leading to unexpected breakdowns and increased downtime, which can be especially detrimental for operations in sectors such as mining and agriculture. A buyer may find themselves facing high costs due to prolonged equipment failure and the subsequent need for emergency repairs, affecting overall productivity and profitability.
The Solution: To address maintenance challenges, buyers should prioritize the selection of conveyor belts that are known for durability and ease of maintenance. Opt for modular belt systems that allow for individual segment replacement rather than complete belt replacement, reducing downtime and repair costs. Establishing a regular maintenance program that includes routine inspections, cleaning, and lubrication can help catch potential issues before they escalate into major problems. Additionally, consider training in-house personnel on basic maintenance tasks to ensure quick response times. Partnering with suppliers who offer robust warranty options and readily available spare parts can also provide peace of mind and minimize operational disruptions.
Strategic Material Selection Guide for conveyor belt types
What Are the Key Properties of Rubber Conveyor Belts?
Rubber is one of the most commonly used materials for conveyor belts due to its excellent flexibility and durability. It offers a high temperature and pressure rating, making it suitable for various industrial applications. Rubber conveyor belts are resistant to wear and tear, providing a longer service life compared to other materials. Additionally, they exhibit good corrosion resistance, which is essential when transporting materials that may be abrasive or chemically reactive.
Pros and Cons of Rubber Conveyor Belts
The primary advantage of rubber conveyor belts is their durability, which translates to lower maintenance costs over time. They are also relatively cost-effective, especially for bulk applications. However, they can be prone to degradation when exposed to extreme temperatures or certain chemicals, which may limit their use in specific environments. Furthermore, manufacturing rubber belts can be complex, requiring specialized equipment and expertise.
Impact on Application
Rubber belts are particularly effective for transporting bulk materials, such as grains or aggregates. Their flexibility allows them to handle irregularly shaped items without damage. However, when selecting rubber belts, buyers must consider the specific media compatibility to ensure optimal performance.
How Do Metal Conveyor Belts Perform in Various Environments?
Metal conveyor belts are designed for high-strength applications and are often used in industries such as food processing, automotive, and mining. These belts can handle high temperatures and are resistant to corrosion, making them ideal for harsh environments. The use of metal also enhances the ability to handle heavy loads and provides excellent stability.
Pros and Cons of Metal Conveyor Belts
The key advantage of metal conveyor belts is their robustness and longevity, especially in high-load applications. They are easy to clean and maintain, which is crucial in industries where hygiene is a priority. However, metal belts tend to be more expensive than rubber or synthetic options, and their rigidity can limit their application in scenarios requiring flexibility.
Impact on Application
Metal belts are particularly suited for applications involving hot or heavy materials, such as in foundries or bakeries. Their ability to withstand extreme conditions makes them a preferred choice in environments where other materials might fail.
What Are the Advantages of Modular Plastic Conveyor Belts?
Modular plastic conveyor belts consist of interlocking segments, allowing for easy customization and maintenance. They are lightweight and can be designed to handle various materials, including food products, due to their hygienic properties. Modular belts are also resistant to chemicals and can operate in a range of temperatures.
Pros and Cons of Modular Plastic Conveyor Belts
The primary advantage of modular plastic belts is their ease of maintenance; damaged segments can be replaced individually without needing to replace the entire belt. They are versatile and can be configured for different applications, including inclines and declines. However, the initial cost can be higher than traditional rubber belts, and their load capacity may be lower.
Impact on Application
These belts are particularly effective in food processing and packaging applications, where cleanliness and flexibility are paramount. Their design allows for fluid drainage, making them suitable for transporting wet or slippery items.
What Should International Buyers Consider When Selecting Conveyor Belt Materials?
When selecting conveyor belt materials, international buyers must consider compliance with local and international standards, such as ASTM, DIN, or JIS. This is crucial for ensuring safety and performance in their specific markets. Additionally, the choice of material may be influenced by regional preferences and the availability of local suppliers, which can affect lead times and costs.
Summary Table of Conveyor Belt Materials
Material | Typical Use Case for conveyor belt types | Key Advantage | Key Disadvantage/Limitation | Relative Cost (Low/Med/High) |
---|---|---|---|---|
Rubber | Bulk material transport (grains, aggregates) | Durable and cost-effective | Degradation in extreme conditions | Medium |
Metal | High-load applications (food processing, automotive) | Robust and easy to clean | Higher cost and rigidity | High |
Modular Plastic | Food processing and packaging | Easy maintenance and customization | Higher initial cost, lower load capacity | Medium |
In-depth Look: Manufacturing Processes and Quality Assurance for conveyor belt types
What Are the Main Stages of Manufacturing Conveyor Belt Types?
Manufacturing conveyor belts involves a series of well-defined processes that ensure the final product meets industry standards and customer requirements. The main stages include material preparation, forming, assembly, and finishing.
How Is Material Prepared for Conveyor Belt Manufacturing?
Material preparation is the first step in the manufacturing process. This involves sourcing high-quality raw materials, such as rubber, synthetic composites, or metal, depending on the type of conveyor belt being produced. Suppliers must ensure that the materials comply with relevant international standards such as ISO 9001 to guarantee quality and consistency.
Once the materials are sourced, they undergo testing for physical properties, durability, and resistance to wear and tear. This initial quality check is crucial for ensuring that the materials will withstand the demands of the specific applications for which the conveyor belts are intended.
What Techniques Are Used in the Forming Stage?
The forming stage involves shaping the prepared materials into the desired belt configuration. This process can vary based on the type of conveyor belt:
- Flat Belts: These are typically produced by layering and bonding multiple sheets of rubber or synthetic material using heat and pressure.
- Modular Belts: Composed of interlocking plastic pieces, these belts are formed through injection molding, allowing for precision and customization.
- Metal Conveyor Belts: These belts are usually created by weaving metal wires or sheets together, which requires specialized machinery to ensure durability and strength.
Each of these techniques not only defines the functionality of the conveyor belt but also influences its maintenance needs and lifespan.
How Is the Assembly of Conveyor Belts Conducted?
Assembly is the next critical stage, where the formed materials are put together to create a complete conveyor belt system. This stage often includes integrating additional components such as pulleys, bearings, and cleats.
Quality control measures during assembly include verifying that all components fit correctly and operate smoothly. Automated systems often assist in this process to enhance efficiency and accuracy. For international B2B buyers, understanding the assembly techniques used can help gauge the reliability of the end product.
What Finishing Techniques Are Applied to Conveyor Belts?
The finishing stage involves various treatments to enhance the performance and longevity of the conveyor belts. This may include:
- Surface Treatments: Coatings or treatments are applied to improve resistance to chemicals, oils, and abrasions.
- Quality Inspections: Visual and mechanical inspections are conducted to detect any defects before the product is packaged.
This step is essential for ensuring that the conveyor belts can perform optimally in their intended environments, whether in agriculture, manufacturing, or logistics.
What Quality Assurance Standards Are Relevant for Conveyor Belt Manufacturing?
Quality assurance is a critical aspect of conveyor belt manufacturing, ensuring that products meet international and industry-specific standards. For B2B buyers, familiarity with these standards can significantly influence procurement decisions.
Which International Standards Should Buyers Consider?
The most recognized international standard is ISO 9001, which focuses on quality management systems and continuous improvement. Compliance with ISO 9001 signifies that a manufacturer maintains high-quality processes that can lead to consistent product quality.
Additionally, other certifications may be relevant depending on the application:
- CE Marking: Indicates compliance with European safety standards, crucial for buyers in Europe.
- API Standards: Important for conveyor belts used in the oil and gas industries.
Understanding these standards helps buyers ensure they are sourcing from reputable manufacturers who adhere to best practices.
How Are Quality Control Checkpoints Implemented During Manufacturing?
Quality control (QC) checkpoints are integral to maintaining high standards throughout the manufacturing process. These checkpoints typically include:
- Incoming Quality Control (IQC): Assessing raw materials upon arrival to ensure they meet specified requirements.
- In-Process Quality Control (IPQC): Monitoring production processes to identify any deviations from the standard in real-time.
- Final Quality Control (FQC): Conducting thorough inspections of the finished product before shipment.
These checkpoints not only help in identifying and rectifying issues early in the production process but also enhance the reliability of the end product.
What Common Testing Methods Are Used to Ensure Conveyor Belt Quality?
To verify the quality of conveyor belts, various testing methods are employed:
- Tensile Strength Testing: Measures the force required to break the belt, ensuring it can withstand operational loads.
- Abrasion Resistance Testing: Evaluates how well the belt material holds up against wear over time.
- Chemical Resistance Testing: Determines the belt’s ability to resist degradation from exposure to various substances.
B2B buyers should inquire about these testing methods and request documentation to verify compliance with quality standards.
How Can B2B Buyers Verify Supplier Quality Control Processes?
For international buyers, especially in regions like Africa, South America, the Middle East, and Europe, verifying a supplier’s quality control processes is essential. Here are some actionable steps:
-
Conduct Supplier Audits: Regular audits can provide insights into the manufacturing processes and quality control measures employed by the supplier.
-
Request Quality Assurance Reports: Suppliers should provide documentation of their quality control processes, including details on certifications and testing results.
-
Engage Third-Party Inspectors: Utilizing independent inspection services can offer an unbiased assessment of the supplier’s quality assurance practices.
-
Review Customer Testimonials and Case Studies: Feedback from other B2B buyers can provide valuable insights into the reliability and quality of the supplier’s products.
What Nuances Should International Buyers Be Aware of Regarding Quality Control?
International B2B buyers must navigate various nuances related to quality control, including differing regional standards and practices. For instance, while ISO standards are globally recognized, local regulations may impose additional requirements that must be met.
Moreover, cultural differences in business practices can affect communication and expectation management. Therefore, establishing clear, consistent communication with suppliers and understanding their quality assurance processes will help mitigate risks and enhance the procurement experience.
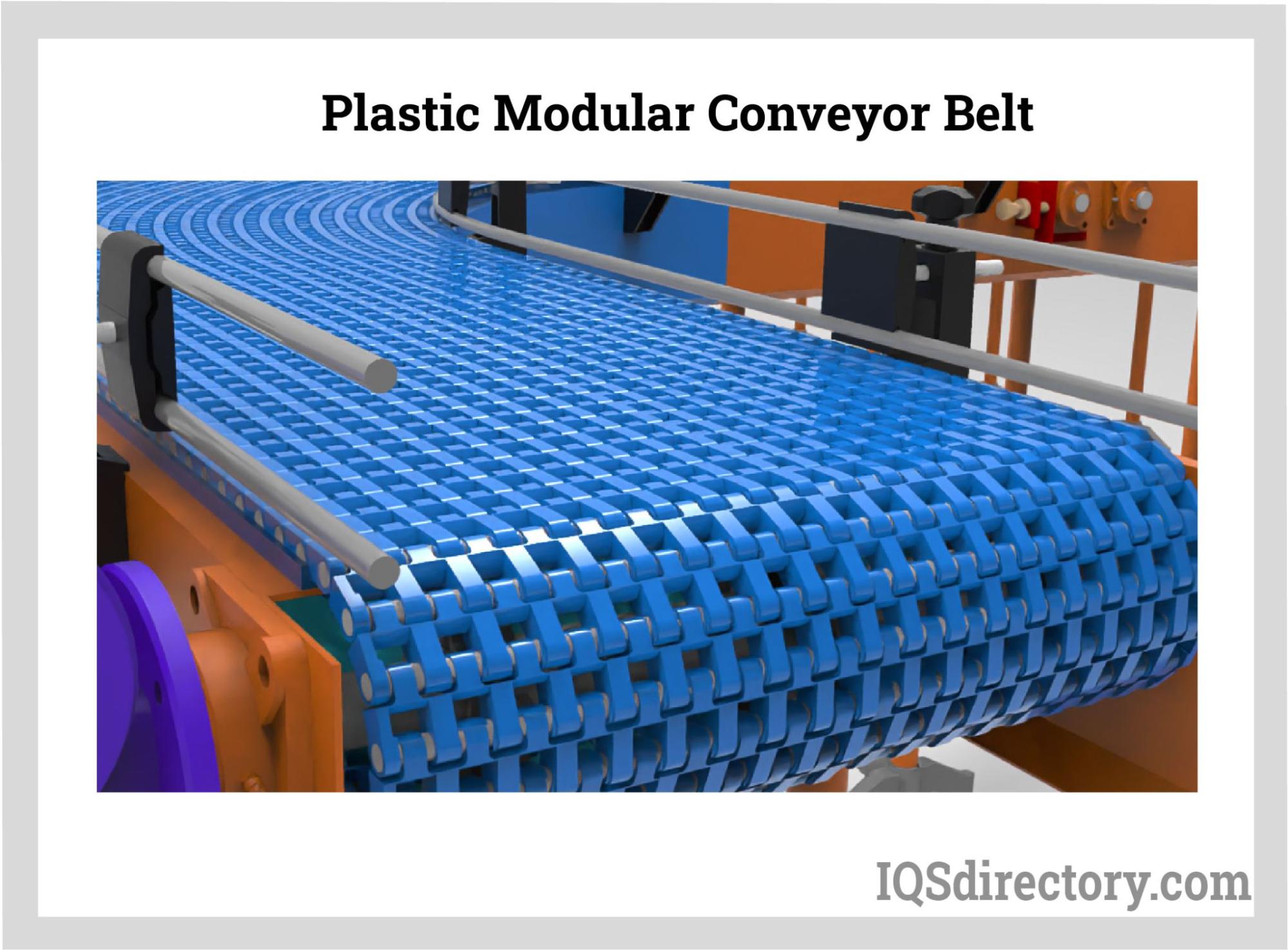
A stock image related to conveyor belt types.
By being informed about these manufacturing processes and quality assurance practices, B2B buyers can make better purchasing decisions, ensuring they acquire reliable, high-quality conveyor belts that meet their operational needs.
Practical Sourcing Guide: A Step-by-Step Checklist for ‘conveyor belt types’
The following guide serves as a practical checklist for international B2B buyers looking to procure various types of conveyor belts. This step-by-step approach will help ensure that you make informed and strategic sourcing decisions, aligning with your operational requirements and business goals.
Step 1: Define Your Technical Specifications
Begin by clearly identifying the technical specifications needed for your conveyor belt application. This includes the type of materials to be transported, load capacity, speed requirements, and environmental conditions (e.g., temperature, moisture). Establishing these criteria will streamline your selection process and help you communicate effectively with potential suppliers.
Step 2: Research Conveyor Belt Types and Their Applications
Understanding the different types of conveyor belts and their applications is crucial. For instance, flat belts are ideal for internal conveyance, while modular belts excel in handling food products due to their easy-to-clean features. Familiarize yourself with the specific benefits and limitations of each type to select the most suitable option for your operations.
Step 3: Evaluate Potential Suppliers
Before making a commitment, thoroughly vet potential suppliers. Request detailed company profiles, case studies, and references from businesses in similar industries or regions. Look for suppliers with proven track records in delivering the types of conveyor belts you require, and don’t hesitate to verify their experience and capabilities.
- Check Certifications: Ensure that the suppliers hold relevant certifications, such as ISO, that demonstrate their adherence to quality and safety standards.
- Assess Production Capabilities: Inquire about their manufacturing processes and capacity to meet your volume and lead time requirements.
Step 4: Request Samples and Conduct Trials
Once you’ve narrowed down your options, request samples of the conveyor belts you are considering. Conduct trials to assess their performance in real-world conditions. This hands-on evaluation will help you determine if the belt meets your technical specifications and operational needs.
Step 5: Negotiate Pricing and Terms
Engage in discussions with suppliers regarding pricing, payment terms, and warranty options. Consider the total cost of ownership, including installation, maintenance, and potential downtime. Be clear about your budget constraints while negotiating to ensure you get the best value for your investment.
Step 6: Understand After-Sales Support and Maintenance Services
Evaluate the after-sales support offered by the supplier, including training, maintenance services, and response times for repairs. Reliable after-sales support can significantly reduce downtime and enhance the longevity of your conveyor systems.
Step 7: Finalize the Purchase Agreement
After thorough evaluations and negotiations, finalize the purchase agreement. Ensure that all terms, conditions, and specifications are documented clearly. This will safeguard your interests and provide a reference point for both parties throughout the procurement process.
By following this comprehensive checklist, you can make a more informed decision when sourcing conveyor belts, ensuring they align with your operational requirements and contribute positively to your business efficiency.
Comprehensive Cost and Pricing Analysis for conveyor belt types Sourcing
What Are the Key Cost Components in Conveyor Belt Types Sourcing?
When sourcing conveyor belts, understanding the cost structure is essential for effective budgeting and decision-making. The primary cost components include:
-
Materials: The choice of materials significantly impacts costs. For instance, rubber and synthetic composites used in flat belts may have lower upfront costs but varying durability. Metal conveyor belts, while more expensive, offer superior longevity and performance in heavy-duty applications.
-
Labor: Labor costs encompass the workforce needed for manufacturing, assembly, and installation. Skilled labor can command higher wages, particularly in regions with a shortage of specialized technicians.
-
Manufacturing Overhead: This includes indirect costs associated with production, such as utilities, maintenance of equipment, and facility expenses. Efficient manufacturing processes can help reduce these overheads.
-
Tooling: Initial tooling costs can be substantial, especially for customized conveyor belt designs. Buyers should consider the tooling lifespan and potential amortization over multiple orders.
-
Quality Control (QC): Investing in robust QC processes ensures product reliability and compliance with industry standards, which can lead to higher initial costs but lower risks of failure and associated costs in the long run.
-
Logistics: Transportation costs vary widely depending on distance, shipping method, and Incoterms. Buyers should factor in local tariffs and import duties when calculating total logistics expenses.
-
Margin: Supplier margins can vary, often influenced by competition, demand, and the exclusivity of the product. Understanding market dynamics helps buyers negotiate better pricing.
How Do Price Influencers Affect Conveyor Belt Costs?
Several factors can influence pricing in the conveyor belt market:
-
Volume and Minimum Order Quantity (MOQ): Suppliers often provide discounts for larger orders. Negotiating MOQs can lead to significant savings, particularly for businesses with ongoing needs.
-
Specifications and Customization: Custom designs or specific material requirements can increase costs. Buyers should evaluate whether customization adds sufficient value to justify the additional expense.
-
Materials: The quality and type of materials selected directly affect costs. High-grade materials may come with a higher price tag but can reduce maintenance and replacement needs.
-
Quality and Certifications: Conveyor belts that meet international quality standards and certifications typically command higher prices. However, investing in certified products can mitigate risks and enhance operational efficiency.
-
Supplier Factors: Supplier reputation, reliability, and production capacity can also affect pricing. Established suppliers may charge a premium, but they often provide better service and product consistency.
-
Incoterms: The chosen Incoterms can influence total costs by defining responsibilities for shipping, insurance, and tariffs. Understanding these terms is crucial for budgeting effectively.
What Are the Best Buyer Tips for Cost-Efficient Conveyor Belt Sourcing?
For international B2B buyers, particularly those in Africa, South America, the Middle East, and Europe, implementing strategic purchasing practices can enhance cost-efficiency:
-
Negotiation: Build relationships with suppliers and negotiate terms that reflect your purchasing power. Leverage multiple quotes to ensure competitive pricing.
-
Total Cost of Ownership (TCO): Consider not just the purchase price but also maintenance, operational efficiency, and lifespan when evaluating conveyor belts. A lower upfront cost may lead to higher long-term expenses.
-
Pricing Nuances for International Buyers: Be aware of regional market trends and economic factors that can affect pricing, such as currency fluctuations and local demand. This knowledge can aid in timing purchases strategically.
-
Research Supplier Backgrounds: Investigate potential suppliers’ histories, product reviews, and case studies to ensure reliability and quality. This can prevent costly mistakes and ensure a smoother purchasing process.
-
Stay Informed on Market Trends: Understanding the latest trends in conveyor belt technology and materials can provide insights into potential cost savings and improved efficiencies.
Disclaimer on Indicative Prices
Prices for conveyor belts can vary widely based on the factors mentioned above. Buyers should seek detailed quotes tailored to their specific needs and circumstances. Always perform due diligence to ensure accurate pricing and supplier reliability before making purchasing decisions.
Alternatives Analysis: Comparing conveyor belt types With Other Solutions
In the realm of material handling and logistics, selecting the right solution for transporting goods is crucial for operational efficiency. While conveyor belts are a popular choice due to their versatility, several alternative technologies can also achieve similar objectives. This analysis compares various conveyor belt types against alternative methods, helping international B2B buyers make informed decisions tailored to their specific needs.
Comparison Aspect | Conveyor Belt Types | Automated Guided Vehicles (AGVs) | Pneumatic Conveying |
---|---|---|---|
Performance | High throughput; effective for continuous flow | Flexible routing; excellent for dynamic environments | Efficient for bulk materials |
Cost | Moderate initial investment; ongoing maintenance costs | Higher upfront costs; potential for reduced labor costs | Variable costs depending on material type and distance |
Ease of Implementation | Generally straightforward; requires space for setup | Requires infrastructure for navigation; training for staff needed | Installation complexity varies; depends on existing systems |
Maintenance | Regular maintenance required; wear on belts can be costly | Minimal maintenance; periodic software updates needed | Maintenance depends on system design; less frequent than belts |
Best Use Case | Ideal for assembly lines, packaging, and sorting | Best for warehouses and factories with variable routing needs | Suitable for transferring bulk powders, grains, and other materials |
What Are the Pros and Cons of Automated Guided Vehicles (AGVs)?
Automated Guided Vehicles (AGVs) are driverless systems designed to transport materials across predefined paths. Their flexibility allows them to navigate complex environments and adapt to changing layouts, making them ideal for dynamic warehouse settings. However, the initial investment for AGVs can be significant, and they require a certain level of infrastructure and technology integration. Additionally, while they reduce labor costs over time, the upfront costs and training needs may be a barrier for some organizations.
How Does Pneumatic Conveying Work and What Are Its Benefits?
Pneumatic conveying systems utilize air pressure to transport bulk materials through tubes. This method is particularly effective for moving powders and granules over long distances, as it minimizes material handling and reduces contamination risks. The major advantage of pneumatic systems is their ability to convey materials without the need for physical contact, which is crucial in industries like food and pharmaceuticals. However, the complexity of installation and potential variability in costs based on the materials being transported can be drawbacks.
Conclusion: How Should B2B Buyers Choose the Right Solution?
When selecting between conveyor belt types and alternative solutions like AGVs or pneumatic conveying systems, B2B buyers should consider several factors. The specific application, material type, facility layout, and budget constraints play critical roles in determining the best option. For instance, businesses focused on high-volume, continuous operations may benefit more from conveyor belts, while those requiring flexibility and dynamic routing might prefer AGVs. Similarly, organizations handling bulk materials may find pneumatic conveying to be the most efficient choice. Ultimately, a thorough assessment of operational needs and long-term goals will guide buyers in making the most suitable investment.
Essential Technical Properties and Trade Terminology for conveyor belt types
What Are the Key Technical Properties of Conveyor Belts?
When selecting a conveyor belt, understanding its technical specifications is crucial for ensuring optimal performance in your operations. Here are several essential properties to consider:
1. Material Grade
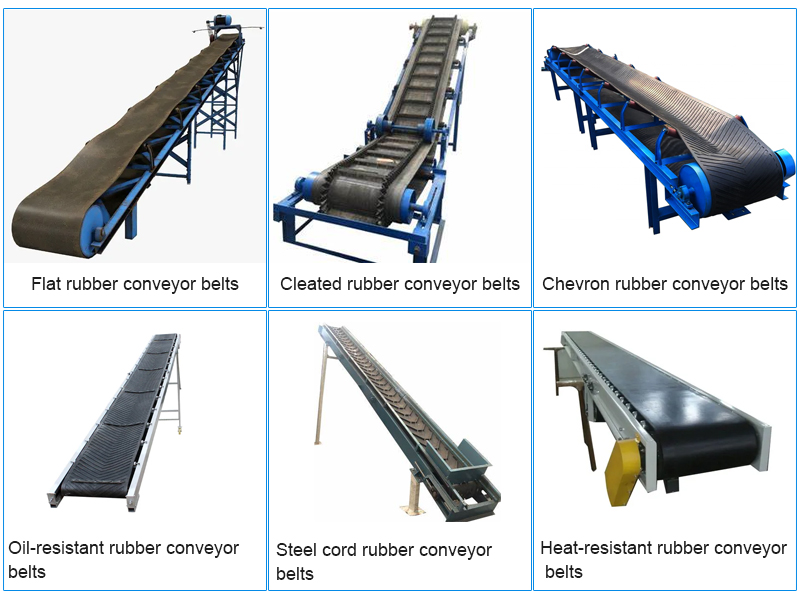
A stock image related to conveyor belt types.
The material grade of a conveyor belt determines its durability and suitability for specific applications. Common materials include rubber, PVC, and polyurethane. For instance, rubber belts are ideal for heavy-duty applications due to their resistance to wear and tear, while PVC belts are often used in food handling due to their non-toxic properties. Selecting the right material grade not only enhances the lifespan of the conveyor but also minimizes maintenance costs.
2. Tension Strength
Tension strength refers to the maximum load a conveyor belt can handle without breaking. It is typically measured in pounds or kilograms per inch of width. For B2B buyers, understanding tension strength is vital, as underestimating this property can lead to equipment failure, costly downtime, and safety hazards. Always ensure that the tension strength meets or exceeds your operational requirements.
3. Surface Texture
The surface texture of a conveyor belt affects its grip and material handling capabilities. Smooth surfaces are suitable for transporting lightweight items, while textured or cleated surfaces are better for moving bulk materials or items on inclines. Choosing the right surface texture can significantly improve operational efficiency and reduce the risk of product damage.
4. Width and Length Specifications
The width and length of a conveyor belt are tailored to fit specific machinery and operational layouts. It is essential to measure the space where the conveyor will be installed to avoid compatibility issues. Additionally, the length must accommodate the distance between loading and unloading points. Customizing these dimensions ensures optimal material flow and space utilization.
5. Temperature Resistance
For operations that involve extreme temperatures, selecting a conveyor belt with appropriate temperature resistance is critical. Different materials offer varying levels of heat and cold resistance, impacting their performance and lifespan. Understanding the temperature requirements of your application can prevent premature wear and operational disruptions.
What Are Common Trade Terms in the Conveyor Belt Industry?
Navigating the conveyor belt market requires familiarity with specific jargon and trade terms. Here are some key terms that B2B buyers should know:
1. OEM (Original Equipment Manufacturer)
OEM refers to companies that produce parts or equipment that are used in another company’s end product. In the conveyor belt industry, purchasing from an OEM ensures that you receive high-quality, compatible parts designed for your specific machinery. This is especially important for maintaining operational efficiency and reliability.
2. MOQ (Minimum Order Quantity)
MOQ indicates the smallest quantity of a product that a supplier is willing to sell. For international B2B buyers, understanding MOQ is essential for budgeting and inventory management. Suppliers often set MOQs based on production costs, and negotiating this figure can lead to significant savings.
3. RFQ (Request for Quotation)
An RFQ is a formal process where buyers request pricing and terms from suppliers for specific products. Crafting a detailed RFQ can help you receive accurate quotes and ensure that suppliers understand your requirements, leading to better pricing and service agreements.
4. Incoterms (International Commercial Terms)
Incoterms are standardized trade terms used globally to define the responsibilities of buyers and sellers in international transactions. Familiarity with Incoterms can help you understand shipping costs, risks, and responsibilities, which is vital for effective supply chain management and cost control.
5. Lead Time
Lead time refers to the time taken from placing an order to receiving the product. In the conveyor belt industry, lead time can vary significantly based on the complexity of the order and the supplier’s production capacity. Understanding lead times can help in planning your operations and minimizing delays.
By grasping these technical properties and trade terms, international B2B buyers can make informed decisions that align with their operational needs and strategic goals.
Navigating Market Dynamics and Sourcing Trends in the conveyor belt types Sector
What Are the Key Market Dynamics and Trends Influencing Conveyor Belt Types?
The global conveyor belt market is experiencing significant growth, driven by the increasing demand for automation in various industries such as manufacturing, logistics, and food processing. Emerging economies in Africa and South America are investing heavily in industrial infrastructure, which is propelling the demand for various conveyor belt types. For international B2B buyers, understanding these dynamics is crucial for making informed sourcing decisions.
Current trends indicate a shift towards advanced technologies, including the integration of IoT and AI in conveyor systems. These technologies enable predictive maintenance, enhancing operational efficiency and reducing downtime. Furthermore, the rise of e-commerce is driving the need for efficient material handling systems, including automated guided vehicles (AGVs) and robotic palletizers, which are increasingly being integrated with traditional conveyor systems. Buyers should be aware of these innovations, as they can lead to improved supply chain efficiency and lower operational costs.
Additionally, suppliers are focusing on customization options to meet specific industry requirements. For example, modular belt conveyors are gaining traction due to their versatility and ease of maintenance. B2B buyers from regions like Europe and the Middle East should prioritize partnerships with manufacturers that offer tailored solutions, ensuring that their conveyor systems align with their operational needs.
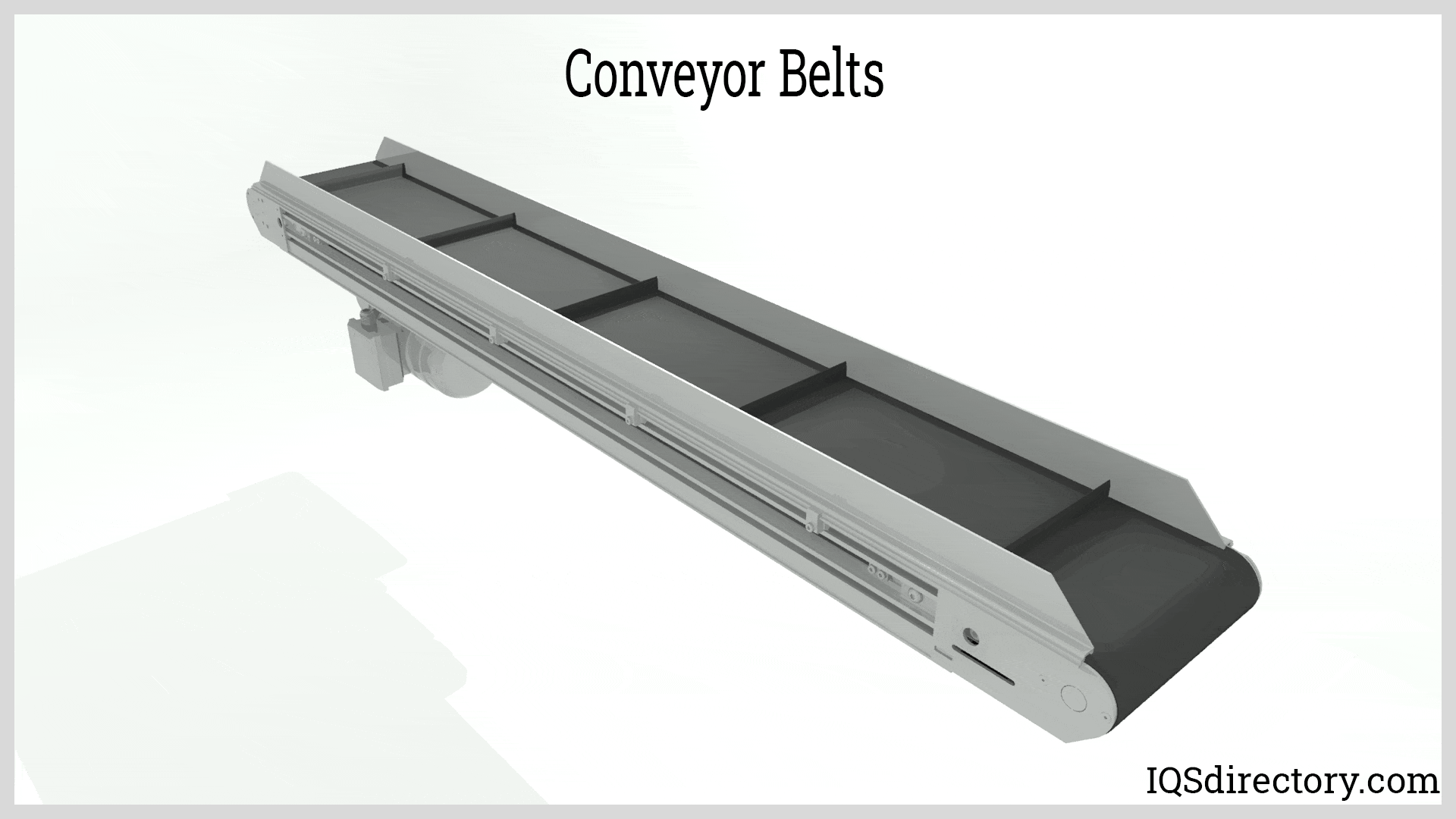
A stock image related to conveyor belt types.
How Is Sustainability and Ethical Sourcing Impacting Conveyor Belt Purchases?
Sustainability has become a pivotal factor in B2B sourcing decisions, especially for international buyers looking to align with global environmental standards. The conveyor belt industry is no exception, as manufacturers are increasingly adopting eco-friendly materials and practices. Buyers should consider suppliers that utilize recycled materials in their conveyor belt production, which can significantly reduce the environmental impact of their operations.
Moreover, the importance of ethical supply chains cannot be overstated. Sourcing from manufacturers with transparent supply chains not only enhances brand reputation but also mitigates risks associated with unethical labor practices. Certifications such as ISO 14001 for environmental management and Fair Trade can serve as indicators of a supplier’s commitment to sustainability and ethical sourcing.
Investing in ‘green’ conveyor belt materials can also yield long-term cost savings. For instance, belts made from biodegradable or recyclable materials can reduce waste and lower disposal costs. B2B buyers should actively seek suppliers that demonstrate a commitment to sustainability and ethical practices, as these factors are increasingly influencing consumer preferences and regulatory compliance.
What Is the Historical Context of Conveyor Belt Development Relevant to B2B Buyers?
The conveyor belt has a rich history that dates back to the late 18th century, initially designed for agricultural applications. Over time, the technology evolved significantly, particularly during the Industrial Revolution, when it became an essential component of manufacturing processes. Today, conveyor systems are integral to various sectors, including logistics, mining, and food processing, reflecting their versatility and adaptability.
B2B buyers should appreciate the advancements in conveyor belt technology, such as the development of modular and automated systems, which have revolutionized material handling. Understanding the historical context of these developments can provide insights into current market offerings and future trends, enabling buyers to make more strategic sourcing decisions. As the industry continues to innovate, staying informed about historical advancements can help buyers anticipate the future needs of their operations.
Frequently Asked Questions (FAQs) for B2B Buyers of conveyor belt types
-
How do I choose the right conveyor belt type for my industry?
Choosing the right conveyor belt type depends on several factors including the materials being transported, the environment of operation, and the specific application needs. For instance, flat belts are ideal for internal conveyance, while modular belts excel in food handling due to their easy cleaning features. Consider the load capacity, speed requirements, and whether your application involves inclines or declines. Always consult with suppliers who can provide insights based on your industry standards and operational challenges. -
What are the best conveyor belt types for food processing applications?
For food processing, modular belt conveyors and cleated belt conveyors are among the best choices. Modular belts are easily cleaned and resistant to bacteria, making them ideal for hygiene-sensitive environments. Cleated belts, equipped with vertical barriers, help secure loose items during transport, which is particularly useful for bulk materials. Always ensure the materials used are FDA-approved and comply with local food safety regulations. -
What customization options are available for conveyor belts?
Customization options for conveyor belts are vast and can include different materials, widths, lengths, cleat designs, and additional features such as sidewalls or guides. Many manufacturers offer bespoke solutions tailored to specific industry requirements. When seeking customization, it’s essential to communicate your exact needs, including load specifications and environmental conditions, to the supplier to ensure compatibility with your system. -
How do I vet suppliers for conveyor belts in international markets?
Vetting suppliers for conveyor belts involves assessing their industry experience, certifications, and customer reviews. Check if they comply with international quality standards such as ISO or ASTM. Additionally, request references from previous clients, and consider visiting their production facilities if feasible. Engaging in trade shows or industry conferences can also provide insights into reputable suppliers and their offerings. -
What are the minimum order quantities (MOQ) for conveyor belts?
Minimum order quantities (MOQ) for conveyor belts can vary significantly between suppliers and depend on factors such as the type of belt and customization requirements. Generally, MOQs can range from a few meters for standard products to larger quantities for custom orders. It’s advisable to discuss your needs upfront with suppliers to find a mutually beneficial arrangement, especially if you are a small or new business. -
What payment terms should I expect when sourcing conveyor belts internationally?
Payment terms for international transactions typically include options like upfront payments, letters of credit, or payment upon delivery. Many suppliers may require a deposit, often around 30%, with the remainder due before shipment. Always clarify the payment terms in advance and ensure they align with your financial capabilities. It’s also prudent to understand the currency exchange rates and any potential fees involved in international transactions. -
How can I ensure quality assurance for my conveyor belts?
To ensure quality assurance for conveyor belts, request detailed specifications and compliance certifications from suppliers. Many reputable manufacturers conduct rigorous testing on their products, such as tensile strength and material durability tests. Establishing a quality control process that includes receiving inspections and periodic checks during production can also safeguard against defects. Collaborating with suppliers who offer warranties and support can further enhance quality assurance. -
What logistics considerations should I keep in mind when importing conveyor belts?
When importing conveyor belts, consider logistics aspects such as shipping methods, lead times, and customs regulations. Depending on your location, sea freight may be the most economical option, but it could involve longer lead times. Ensure that you understand the customs duties and tariffs applicable to your products. Partnering with a reliable freight forwarder can streamline the logistics process and help you navigate any complexities involved in international shipping.
Important Disclaimer & Terms of Use
⚠️ Important Disclaimer
The information provided in this guide, including content regarding manufacturers, technical specifications, and market analysis, is for informational and educational purposes only. It does not constitute professional procurement advice, financial advice, or legal advice.
While we have made every effort to ensure the accuracy and timeliness of the information, we are not responsible for any errors, omissions, or outdated information. Market conditions, company details, and technical standards are subject to change.
B2B buyers must conduct their own independent and thorough due diligence before making any purchasing decisions. This includes contacting suppliers directly, verifying certifications, requesting samples, and seeking professional consultation. The risk of relying on any information in this guide is borne solely by the reader.
Strategic Sourcing Conclusion and Outlook for conveyor belt types
As businesses increasingly seek efficiency and cost-effectiveness, strategic sourcing of conveyor belts emerges as a critical factor for success. Understanding the various types of conveyor belts—such as flat belts, modular belts, and cleated belts—enables B2B buyers to make informed decisions that align with their operational needs. Each belt type offers distinct advantages, from the versatility of flat belts in internal conveyance to the robustness of metal conveyor belts for heavy-duty applications.
Investing in the right conveyor system not only streamlines production processes but also enhances overall productivity and profitability. For international buyers from Africa, South America, the Middle East, and Europe, leveraging strategic sourcing practices can yield significant competitive advantages. This includes evaluating suppliers based on quality, reliability, and technological innovation.
Looking ahead, the conveyor belt industry is poised for growth, driven by advancements in automation and material technology. To remain competitive, businesses should stay informed about emerging trends and innovations. Take the next step in optimizing your supply chain by assessing your current conveyor solutions and considering strategic partnerships that align with your long-term goals. Embrace the future of material handling—your business’s efficiency and success depend on it.