Discover Benefits of Electrical Coil: The Ultimate Guide (2025)
Introduction: Navigating the Global Market for electrical coil
Navigating the complex landscape of sourcing electrical coils can be a daunting challenge for international B2B buyers, especially those operating in diverse markets across Africa, South America, the Middle East, and Europe. With the demand for reliable components like electromagnetic coils, solenoid coils, and inductors surging, it is essential for businesses to understand the intricacies involved in selecting the right products. This guide is designed to provide a comprehensive overview of electrical coils, covering various types, applications, and key considerations for supplier vetting and cost assessment.
International buyers often face hurdles such as fluctuating prices, varying quality standards, and the need for compliance with local regulations. Understanding the nuances of different coil types—ranging from voice coils used in audio equipment to power transformers essential for energy distribution—can significantly impact operational efficiency and product reliability. This guide aims to empower B2B buyers by offering actionable insights that facilitate informed purchasing decisions.
By delving into critical factors such as material specifications, manufacturing processes, and industry best practices, this resource equips decision-makers with the knowledge necessary to navigate the global market effectively. Whether you’re sourcing components for industrial applications or consumer electronics, our guide will serve as a valuable tool in ensuring that you choose the right electrical coils for your specific needs.
Understanding electrical coil Types and Variations
Type Name | Key Distinguishing Features | Primary B2B Applications | Brief Pros & Cons for Buyers |
---|---|---|---|
Electromagnetic Coil | Generates electromagnetic fields when current flows | Used in transformers and inductors | Pros: Versatile; Cons: Sensitive to current fluctuations |
Inductor Coil | Stores energy in a magnetic field; passive component | Power supply circuits, filtering applications | Pros: Effective for energy management; Cons: Limited energy storage time |
Solenoid Coil | Wire wrapped around a core; creates linear motion | Actuators, relays, and valves | Pros: Reliable for linear movement; Cons: Requires precise current control |
Voice Coil | Copper or aluminum wire wound around a bobbin | Speakers and audio devices | Pros: High fidelity sound; Cons: Sensitive to overloading |
Toroidal Coil | Donut-shaped core; minimal electromagnetic interference | Power transformers, inductors, and filters | Pros: Efficient design; Cons: Can be more expensive than traditional coils |
What are Electromagnetic Coils and Their B2B Relevance?
Electromagnetic coils are essential components that create electromagnetic fields when electric current flows through them. They are widely used in transformers, where multiple coils work together to manage power transmission efficiently. For B2B buyers, selecting high-quality electromagnetic coils is crucial, as they play a significant role in energy conversion and management systems. Buyers should consider the coil’s wire gauge, core material, and the application’s specific current requirements when making their purchase.
How Do Inductor Coils Function in Power Applications?
Inductor coils are passive electrical components designed to store energy in a magnetic field. They are commonly used in power supply circuits and filtering applications, where they help maintain current flow and manage voltage spikes. For businesses, understanding the energy management capabilities of inductor coils is essential. Buyers should evaluate factors such as inductance value, size, and the type of core material, as these will affect performance in specific applications.
What Makes Solenoid Coils Important for B2B Buyers?
Solenoid coils consist of wire tightly wrapped around a core, generating linear motion when electric current passes through. They are widely used in actuators, relays, and valves, making them indispensable in industrial automation and control systems. B2B buyers should focus on the coil’s specifications, such as wire gauge and core material, to ensure reliability and efficiency in their applications. Additionally, understanding the power requirements for solenoid operation can aid in optimizing system performance.
Why are Voice Coils Crucial for Audio Equipment?
Voice coils are specialized coils made from copper or aluminum wire, typically used in speakers and audio devices. They convert electrical signals into sound by creating vibrations in the speaker cone. For B2B buyers in the audio industry, selecting high-quality voice coils is vital for achieving superior sound fidelity. Buyers should consider factors such as coil resistance, power handling capacity, and thermal management to ensure optimal performance in their audio products.
How Do Toroidal Coils Improve Power Efficiency?
Toroidal coils feature a donut-shaped core design that minimizes electromagnetic interference, making them ideal for power transformers and inductors. Their efficient design allows for reduced energy loss, which is particularly beneficial for businesses looking to enhance their power management systems. When purchasing toroidal coils, B2B buyers should assess core material, winding configurations, and application-specific requirements to ensure the best fit for their energy needs.
Key Industrial Applications of electrical coil
Industry/Sector | Specific Application of electrical coil | Value/Benefit for the Business | Key Sourcing Considerations for this Application |
---|---|---|---|
Power Generation | Transformers for voltage regulation | Ensures efficient power transmission and reduced losses | Quality of materials, compliance with international standards, and customization options. |
Manufacturing | Inductors in motor drives and control systems | Enhances operational efficiency and reliability | Durability of coils, thermal resistance, and availability of technical support. |
Telecommunications | Filters in signal processing circuits | Improves signal integrity and reduces electromagnetic interference | Frequency response, size constraints, and compliance with regional regulations. |
Automotive | Solenoid coils in ignition systems | Increases reliability and performance of ignition systems | Resistance to environmental factors, electrical specifications, and sourcing traceability. |
Consumer Electronics | Voice coils in audio devices | Enhances sound quality and user experience | Material quality, size compatibility, and production lead times. |
How Are Electrical Coils Used in Power Generation?
In the power generation industry, electrical coils are primarily utilized in transformers for voltage regulation. These transformers step up or step down voltage levels, ensuring that electricity can be transmitted efficiently over long distances. For international buyers, especially in regions like Africa and South America where infrastructure may be developing, sourcing high-quality transformers is crucial. Key considerations include the coil’s material quality and compliance with international standards to prevent energy loss and ensure safety.
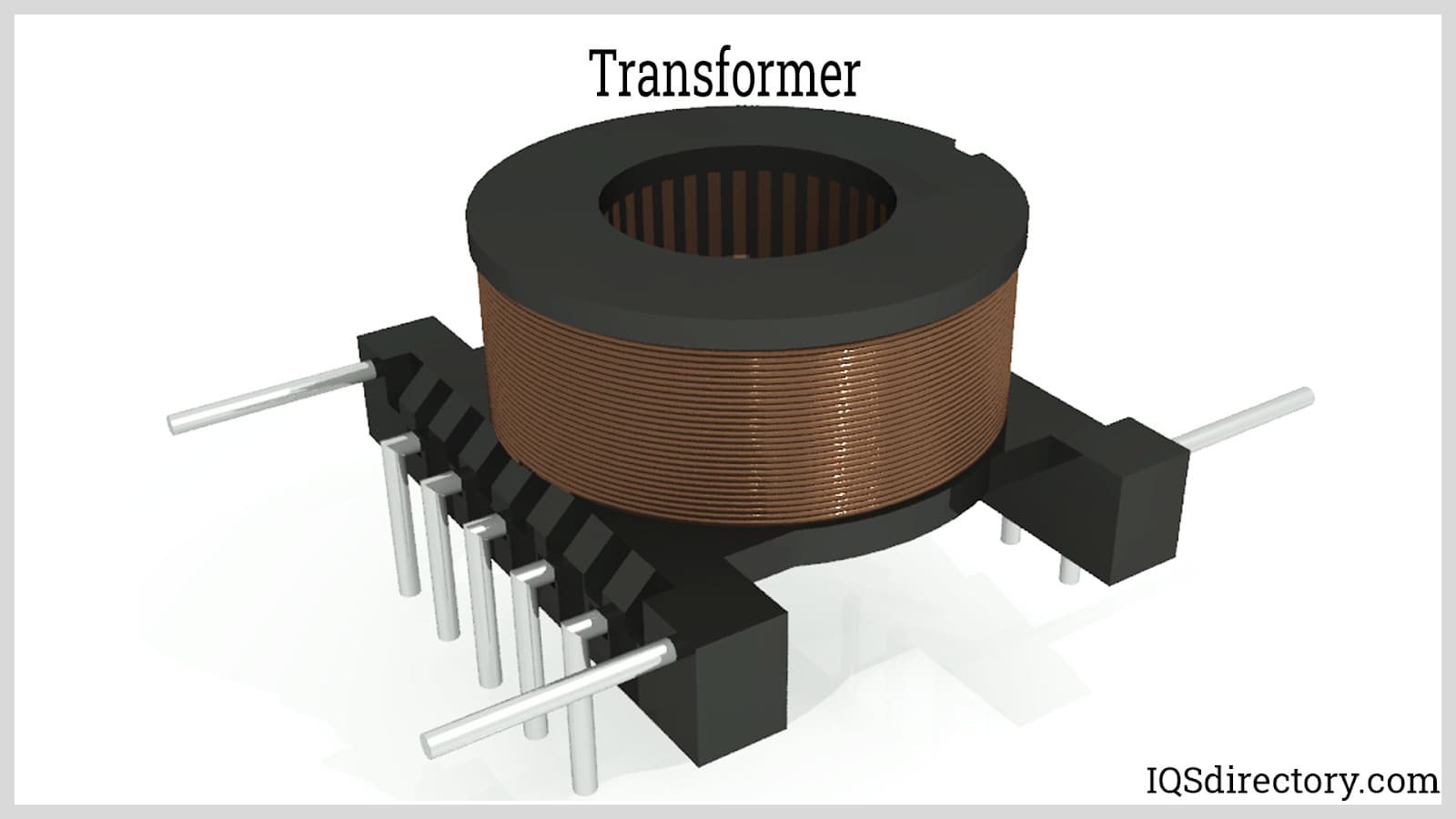
A stock image related to electrical coil.
What Role Do Electrical Coils Play in Manufacturing?
In manufacturing, inductors are integral to motor drives and control systems, where they help manage energy flow and enhance operational efficiency. By opposing sudden changes in current, inductors ensure smooth operation of machinery, which is vital for maintaining production schedules. Buyers from the Middle East and Europe should focus on the durability and thermal resistance of these coils, as they often operate in challenging environments. Availability of technical support for installation and maintenance is also a key factor in sourcing decisions.
How Are Electrical Coils Used in Telecommunications?
Telecommunications rely heavily on electrical coils as filters in signal processing circuits. These coils help maintain signal integrity by reducing electromagnetic interference, which is critical in ensuring clear communication. Buyers in this sector should consider the frequency response and size constraints of the coils, as they must fit within compact electronic devices. Compliance with regional regulations is also essential, particularly for companies operating across multiple countries.
What Is the Importance of Electrical Coils in Automotive Applications?
In the automotive industry, solenoid coils are essential components of ignition systems, where they generate the electromagnetic field necessary to ignite fuel. This enhances the reliability and performance of vehicles, particularly in regions with varying climate conditions like the Middle East. Buyers must ensure that the coils are resistant to environmental factors such as heat and moisture, and they should verify electrical specifications to ensure compatibility with vehicle systems. Sourcing traceability is also important for quality assurance.
How Do Electrical Coils Enhance Consumer Electronics?
Electrical coils, specifically voice coils, are crucial in audio devices, as they convert electrical energy into sound. This application directly impacts sound quality and user experience, making it a key focus for manufacturers in Europe and South America. Buyers should prioritize material quality to ensure durability and performance, as well as size compatibility with existing designs. Additionally, understanding production lead times is vital for maintaining competitive advantage in the fast-paced consumer electronics market.
3 Common User Pain Points for ‘electrical coil’ & Their Solutions
Scenario 1: Sourcing High-Quality Electrical Coils for Diverse Applications
The Problem:
B2B buyers often struggle to find reliable suppliers of electrical coils that meet the specific requirements of their applications. This is particularly true for industries such as telecommunications, automotive, and renewable energy, where the performance of the electrical coils directly impacts efficiency and safety. Buyers may face challenges related to inconsistent quality, lack of proper certifications, and difficulty in understanding the technical specifications of the coils needed for their projects.
The Solution:
To overcome this sourcing challenge, buyers should establish a well-defined supplier evaluation process. Start by identifying suppliers who specialize in the type of electrical coil required—be it solenoid coils for automated systems or inductors for energy storage. Request samples and conduct thorough quality assessments to ensure that the coils meet industry standards. It’s also beneficial to engage with suppliers who can provide detailed product specifications, including the coil’s material, wire gauge, number of turns, and core type. Consider building partnerships with multiple suppliers to diversify your risk and ensure a steady supply of high-quality products. Additionally, utilizing platforms that aggregate supplier information and customer reviews can help in identifying reputable manufacturers.
Scenario 2: Understanding Electrical Coil Specifications for Optimal Performance
The Problem:
Many buyers find themselves overwhelmed by the technical specifications of electrical coils. This confusion can lead to misordering or utilizing coils that do not perform optimally within their applications. For example, selecting the wrong wire gauge or core material can result in reduced efficiency or even system failures, leading to costly downtime and repairs.
The Solution:
To navigate the complexity of electrical coil specifications, buyers should invest time in training their purchasing teams on the fundamental principles of electromagnetism and coil design. This knowledge will empower them to ask the right questions and make informed decisions. Collaborating closely with engineers during the specification phase is crucial; they can provide insights into the requirements based on the intended application. Additionally, utilizing simulation software to model the performance of different coil designs in your specific environment can help in making data-driven decisions. Lastly, maintaining an open line of communication with suppliers can facilitate better understanding and ensure that the selected coils align with operational goals.
Scenario 3: Dealing with Reliability Issues in Electrical Coils
The Problem:
Reliability is a critical concern for businesses that depend on electrical coils for their operations. Issues such as overheating, premature failure, or inconsistent performance can compromise the entire system, leading to significant operational disruptions. For buyers in regions with variable power quality, such as parts of Africa and South America, the risk of coil failure due to fluctuating voltage levels is particularly pronounced.
The Solution:
To enhance the reliability of electrical coils, buyers should prioritize sourcing coils that are designed to withstand specific environmental and operational conditions. Look for coils with features such as thermal insulation, robust core materials, and protective coatings that can mitigate the effects of temperature fluctuations and moisture. Implementing a preventive maintenance schedule can also help identify potential issues before they escalate. This includes regular inspections, testing the coils under operational conditions, and monitoring performance metrics. Additionally, consider investing in higher-quality power supplies and protection devices, such as surge protectors or voltage stabilizers, to provide a stable operating environment for the coils. Collaborating with suppliers who offer warranties and post-purchase support can further enhance reliability and provide peace of mind.
Strategic Material Selection Guide for electrical coil
When selecting materials for electrical coils, international B2B buyers must consider various factors that influence the performance, durability, and cost-effectiveness of the coils. Below, we analyze four common materials used in the manufacturing of electrical coils: copper, aluminum, ferrite, and steel. Each material has unique properties, advantages, and limitations that can significantly impact their application in different industries.
What Are the Key Properties of Copper for Electrical Coils?
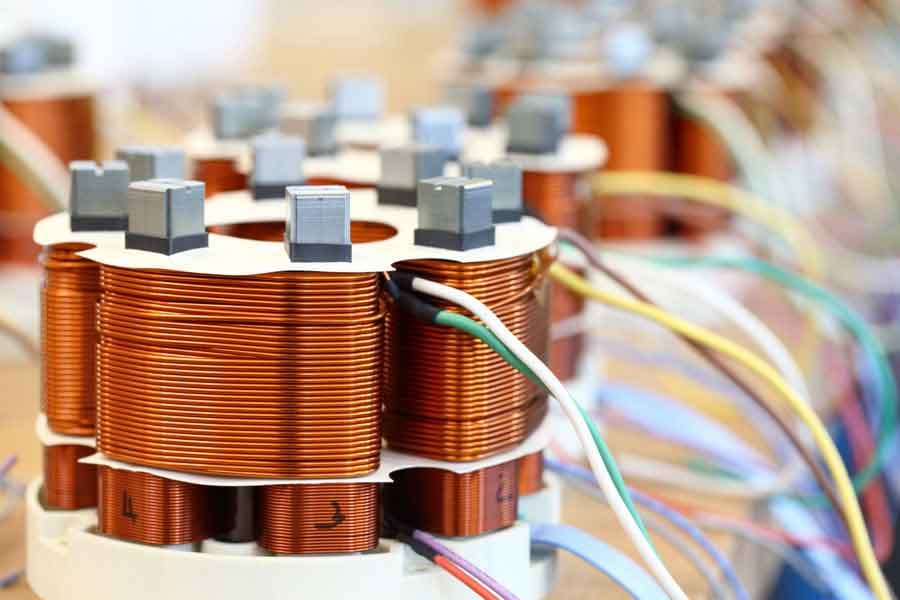
A stock image related to electrical coil.
Copper is widely recognized for its excellent electrical conductivity, making it a preferred choice for electrical coils. It has a high melting point of approximately 1,984°F (1,085°C) and offers good corrosion resistance, particularly when coated.
Pros: Copper coils are durable and can handle high temperatures, which is essential for applications in power transformers and inductors. They also provide superior performance in terms of energy efficiency due to their low electrical resistance.
Cons: The primary drawback of copper is its cost, which is generally higher than that of aluminum. Additionally, copper is heavier, which can complicate installation in certain applications.
Impact on Application: Copper coils are particularly suitable for high-frequency applications and environments where reliability is critical, such as in telecommunications and power generation.
Considerations for International Buyers: Buyers should ensure compliance with international standards such as ASTM B170 for copper wire. In regions like Europe and the Middle East, sourcing from certified suppliers can help meet local regulations.
How Does Aluminum Compare as a Material for Electrical Coils?
Aluminum is another common material used in electrical coils, known for its lightweight and good conductivity, albeit lower than copper.
Pros: The primary advantage of aluminum is its cost-effectiveness and lower weight, which can reduce shipping and handling costs. It is also resistant to corrosion, making it suitable for outdoor applications.
Cons: While aluminum is lighter, it has a lower thermal and electrical conductivity compared to copper, which may limit its use in high-performance applications. Additionally, aluminum coils can be more susceptible to mechanical stress.
Impact on Application: Aluminum coils are often used in applications where weight is a critical factor, such as in automotive and aerospace industries.
Considerations for International Buyers: Buyers should be aware of the specific grades of aluminum, like 1350 for electrical applications, and ensure compliance with standards such as ISO 9001 for quality management.
What Are the Advantages of Ferrite Materials in Electrical Coils?
Ferrite materials are ceramic compounds that exhibit magnetic properties, making them suitable for specific types of coils, especially in high-frequency applications.
Pros: Ferrite coils are excellent at reducing electromagnetic interference (EMI) and can operate effectively at high frequencies. They are also lightweight and can be manufactured in various shapes.
Cons: The brittleness of ferrite materials can be a limitation, as they can break under mechanical stress. Additionally, their cost can be higher due to the manufacturing complexity involved.
Impact on Application: Ferrite coils are commonly used in RF applications, such as in antennas and transformers, where minimizing signal loss is crucial.
Considerations for International Buyers: Buyers should verify that ferrite materials meet international standards like JIS C 2500, particularly in markets like Japan and South Korea.
Why Is Steel Used in Electrical Coils?
Steel, particularly silicon steel, is often used in magnetic cores of electrical coils due to its magnetic properties.
Pros: Steel coils can handle high magnetic flux densities, making them ideal for transformers and inductors. They are also relatively inexpensive compared to copper and aluminum.
Cons: Steel is heavier and less conductive than copper and aluminum, which can be a disadvantage in applications requiring high efficiency. Additionally, steel can be prone to corrosion if not properly coated.
Impact on Application: Steel is most commonly used in power transformers and electric motors, where magnetic properties are more critical than electrical conductivity.
Considerations for International Buyers: Buyers should ensure that the steel used complies with standards such as ASTM A1008 for cold-rolled steel and consider the environmental regulations regarding coatings and treatments.
Summary Table of Material Selection for Electrical Coils
Material | Typical Use Case for electrical coil | Key Advantage | Key Disadvantage/Limitation | Relative Cost (Low/Med/High) |
---|---|---|---|---|
Copper | Power transformers, inductors | Excellent electrical conductivity | Higher cost and weight | High |
Aluminum | Automotive and aerospace applications | Lightweight and cost-effective | Lower conductivity and mechanical stress susceptibility | Medium |
Ferrite | RF applications, antennas | Reduces electromagnetic interference | Brittle and higher manufacturing complexity | Medium to High |
Steel | Power transformers, electric motors | High magnetic flux density | Heavy and less conductive | Low |
This comprehensive analysis provides B2B buyers with actionable insights into material selection for electrical coils, ensuring informed decisions that align with their specific application requirements and regional compliance standards.
In-depth Look: Manufacturing Processes and Quality Assurance for electrical coil
What Are the Main Stages in the Manufacturing Process of Electrical Coils?
The manufacturing process of electrical coils is complex and involves several key stages: material preparation, forming, assembly, and finishing. Understanding each stage is crucial for international B2B buyers to ensure that the coils they procure meet their specific requirements.
Material Preparation: What Materials Are Used for Electrical Coils?
The first step in manufacturing electrical coils is selecting the appropriate materials. Common materials include copper or aluminum wire, which are chosen for their excellent conductivity. The core material can vary; ferromagnetic materials such as iron are often used to enhance the coil’s magnetic properties.
Before manufacturing begins, these materials undergo quality checks to ensure they meet specified standards. For instance, wire gauge and insulation thickness are critical parameters that can influence the coil’s performance. Suppliers often provide certifications for the materials used, which B2B buyers should review.
Forming: How Are Electrical Coils Formed?
Once materials are prepared, the forming stage begins. This typically involves winding the wire around a core. The winding process can be automated or manual, depending on the complexity and volume of production.
Key techniques used during this stage include:
- Automatic Winding Machines: These machines ensure precise and consistent winding, crucial for maintaining the inductance values of the coils.
- Lamination: For certain applications, laminated cores are used to reduce energy loss due to eddy currents. This is particularly important in high-frequency applications.
International B2B buyers should inquire about the machinery and techniques used, as they can impact the quality and consistency of the final product.
Assembly: What Components Are Assembled in Electrical Coils?
In the assembly stage, various components are brought together to create the final electrical coil. This may include integrating additional parts such as terminals or connectors, depending on the intended application of the coil.
Quality assurance during assembly is vital. Suppliers should have standardized processes to ensure that all components fit correctly and function as intended. B2B buyers should request information about the assembly process and whether it includes automated inspections to catch any defects early.
Finishing: What Finishing Techniques Are Used for Electrical Coils?
The finishing stage involves applying protective coatings or insulation to the coils. This is essential for ensuring durability and preventing short circuits. Common finishing techniques include:
- Varnishing: A protective layer is applied to prevent moisture ingress and corrosion.
- Insulation: Various types of insulation materials may be used, including enamel or thermoplastic coatings, depending on the application requirements.
B2B buyers should ensure that the finishing processes align with their operational conditions, such as exposure to environmental elements or electrical stress.
What International Standards and Quality Assurance Measures Should B2B Buyers Consider?
Quality assurance (QA) is a critical aspect of the electrical coil manufacturing process. International standards, such as ISO 9001, provide a framework for quality management systems, ensuring that manufacturers consistently meet customer and regulatory requirements.
What Are the Key Quality Control Checkpoints in Electrical Coil Manufacturing?
Quality control involves several checkpoints throughout the manufacturing process:
- Incoming Quality Control (IQC): This checkpoint assesses raw materials before they enter the production line. It ensures that only materials meeting quality standards are used.
- In-Process Quality Control (IPQC): Throughout the manufacturing process, random samples are taken to check for consistency and adherence to specifications.
- Final Quality Control (FQC): Before shipment, finished coils undergo rigorous testing to ensure they meet performance standards. This may include electrical testing and physical inspections.
B2B buyers should familiarize themselves with these checkpoints and request documentation from suppliers that demonstrate compliance.
How Can B2B Buyers Verify Supplier Quality Control Practices?
Verifying a supplier’s quality control practices is essential for ensuring product reliability. Here are effective methods for B2B buyers:
-
Supplier Audits: Conducting regular audits of the supplier’s manufacturing processes can provide insights into their quality management systems. This includes assessing adherence to international standards and internal QA protocols.
-
Quality Reports: Requesting detailed quality reports, including data on defect rates and corrective actions taken, can help buyers gauge a supplier’s commitment to quality.
-
Third-Party Inspections: Engaging third-party inspection services can provide an unbiased assessment of the supplier’s quality control processes. This is particularly beneficial for international buyers who may not have direct access to the supplier’s facilities.
What Are the QC and Certification Nuances for International B2B Buyers?
For B2B buyers from regions like Africa, South America, the Middle East, and Europe, understanding the nuances of quality control and certification is vital. Different markets may have varying regulatory requirements, which can affect product acceptance.
-
CE Certification: For buyers in Europe, ensuring that electrical coils meet CE marking requirements is crucial, as it signifies compliance with health, safety, and environmental protection standards.
-
API Standards: In certain industries, particularly oil and gas, adherence to API (American Petroleum Institute) standards may be necessary. Buyers should confirm that suppliers are compliant with relevant industry standards.
-
Local Regulations: Buyers must also consider local regulations that may impact product specifications. Engaging with local experts or legal consultants can aid in navigating these complexities.
Conclusion: Ensuring Quality in Electrical Coil Procurement
For international B2B buyers, particularly in diverse markets like Africa, South America, the Middle East, and Europe, understanding the manufacturing processes and quality assurance measures for electrical coils is essential. By focusing on the main stages of manufacturing, key quality control checkpoints, and verification methods, buyers can make informed decisions and ensure they procure high-quality products that meet their operational needs.
Practical Sourcing Guide: A Step-by-Step Checklist for ‘electrical coil’
The following guide is designed to assist B2B buyers in the international market, particularly those from Africa, South America, the Middle East, and Europe, in sourcing electrical coils effectively. This checklist will help streamline the procurement process, ensuring that buyers make informed decisions.
Step 1: Define Your Technical Specifications
Before initiating the sourcing process, it is essential to clearly outline the technical specifications of the electrical coils you require. This includes determining the type of coil needed—whether it’s an electromagnetic coil, solenoid coil, or inductor—as well as specifications regarding size, material, and application. Understanding these details will help you communicate your needs effectively to suppliers and ensure compatibility with your applications.
Step 2: Research Supplier Capabilities
Conduct thorough research on potential suppliers to understand their capabilities and product offerings. Look for suppliers that specialize in the type of electrical coil you need and have a track record of delivering quality products. Evaluate their manufacturing processes, technologies used, and capacity to meet your volume requirements. This information is vital to ensure that the supplier can meet your demands without compromising quality.
Step 3: Evaluate Supplier Certifications and Compliance
It’s crucial to verify that suppliers possess the necessary certifications and comply with international standards relevant to electrical components. Check for certifications such as ISO 9001 for quality management systems and any industry-specific standards that may apply. Compliance not only ensures product quality but also indicates that the supplier adheres to safety and environmental regulations, which is particularly important in regions with strict compliance requirements.
Step 4: Request Samples and Test Quality
Before placing a bulk order, request samples of the electrical coils to evaluate their quality. Testing the samples for performance, durability, and adherence to your specifications is vital. This step minimizes the risk of receiving subpar products and helps establish a baseline for quality that the supplier must meet for future orders.
Step 5: Compare Pricing and Payment Terms
Gather quotes from multiple suppliers to compare pricing structures. Consider not only the base price of the coils but also shipping costs, taxes, and potential tariffs, especially when sourcing internationally. Additionally, review payment terms to ensure they align with your budget and cash flow. Understanding the total cost of ownership will help you make a financially sound decision.
Step 6: Assess Lead Times and Logistics
Evaluate the lead times provided by suppliers and their logistics capabilities. Ensure that the supplier can deliver within your required time frame, especially if you are working on a tight schedule. Inquire about their shipping methods, reliability, and any partnerships with logistics companies that could facilitate timely deliveries.
Step 7: Establish Communication Channels
Finally, set up clear communication channels with your selected supplier. Effective communication is key to addressing any issues that may arise during the procurement process. Ensure that you have a dedicated contact person for inquiries and that the supplier is responsive to your needs. A strong relationship with your supplier can enhance collaboration and lead to better service and support over time.
By following these steps, B2B buyers can ensure a more efficient and effective sourcing process for electrical coils, ultimately leading to better product quality and supplier relationships.
Comprehensive Cost and Pricing Analysis for electrical coil Sourcing
What Are the Key Cost Components in Electrical Coil Sourcing?
When sourcing electrical coils, understanding the cost structure is crucial for B2B buyers. The main components include:
-
Materials: The choice of wire gauge, core material (e.g., iron, ferrite, or aluminum), and insulation significantly affects the cost. Higher quality materials often lead to better performance and longevity, but they also increase the price.
-
Labor: Labor costs vary by region and can include wages for skilled workers who manufacture the coils. In countries with lower labor costs, such as those in parts of Africa and South America, buyers may find more competitive pricing.
-
Manufacturing Overhead: This encompasses expenses related to facilities, utilities, and equipment used in production. Efficient manufacturing processes can help reduce overhead costs, which is beneficial for buyers.
-
Tooling: Investment in tooling can be substantial, particularly for custom coils. The initial setup costs for molds and dies can be amortized over large production runs, making it essential to consider volume when negotiating prices.
-
Quality Control (QC): Ensuring that coils meet specific standards and certifications can add to costs. Buyers should prioritize suppliers who have robust QC processes to minimize risks in the supply chain.
-
Logistics: Shipping costs, including customs duties and taxes, can significantly influence the total cost of ownership. International buyers must account for these expenses when sourcing from different regions.
-
Margin: Suppliers typically add a margin to cover their costs and profit. This margin can vary widely based on competition and market demand.
How Do Pricing Influencers Impact Electrical Coil Costs?
Several factors can influence the pricing of electrical coils, which B2B buyers should consider:
-
Volume/MOQ (Minimum Order Quantity): Ordering larger quantities can lead to significant discounts. Buyers should analyze their needs to take advantage of economies of scale.
-
Specifications and Customization: Custom coils tailored to specific applications often come at a premium. Clearly defining specifications can help suppliers provide accurate quotes.
-
Materials: The type and quality of materials used will directly affect the price. For instance, coils made with high-grade copper will be more expensive than those made with lower-quality materials.
-
Quality and Certifications: Coils that meet international standards (e.g., ISO, UL) typically command higher prices due to the assurance of quality and reliability.
-
Supplier Factors: Established suppliers with a track record of reliability may charge more, but their consistent quality and service can justify the higher cost.
-
Incoterms: The terms of trade can significantly affect the final price. Buyers should be clear about who bears the costs and risks associated with transportation and delivery.
What Are the Best Practices for Negotiating Electrical Coil Prices?
For international B2B buyers, particularly those from Africa, South America, the Middle East, and Europe, here are some actionable tips:
-
Conduct Market Research: Understanding prevailing market prices can provide leverage in negotiations. Reach out to multiple suppliers for quotes to gauge price ranges.
-
Leverage Total Cost of Ownership (TCO): When evaluating suppliers, consider not just the initial purchase price but also the long-term costs associated with reliability, maintenance, and potential failures.
-
Negotiate Terms: Discuss payment terms, delivery timelines, and warranties. Flexible terms can sometimes be as valuable as a lower price.
-
Focus on Quality: While lower prices are appealing, prioritize quality and reliability to avoid costly failures in the future. Always ask for samples or references before committing to a supplier.
-
Establish Strong Relationships: Building relationships with suppliers can lead to better pricing and terms over time. Regular communication can help in negotiating future contracts.
Disclaimer on Indicative Prices
Prices for electrical coils can fluctuate based on market conditions, supplier availability, and other factors. It is advisable for buyers to obtain quotes directly from suppliers to get the most accurate and current pricing information.
Alternatives Analysis: Comparing electrical coil With Other Solutions
When exploring solutions for electrical applications, understanding the alternatives to electrical coils is crucial for B2B buyers. Various technologies can offer similar functions, and selecting the right one depends on specific operational needs and constraints. Below, we analyze electrical coils in comparison to other viable alternatives, focusing on their performance, cost, ease of implementation, maintenance, and best use cases.
Comparison Aspect | Electrical Coil | Inductor | Solenoid Coil |
---|---|---|---|
Performance | High efficiency in energy storage and conversion; suitable for various frequencies. | Excellent for filtering and energy storage; reacts well to varying currents. | Provides linear motion and control; suitable for applications requiring mechanical movement. |
Cost | Moderate cost, influenced by materials and design complexity. | Generally lower cost due to simpler design. | Higher cost due to complex assembly and core requirements. |
Ease of Implementation | Requires careful design and integration into circuits; moderate complexity. | Easy to integrate; often used in standard circuits. | More complex installation due to mechanical components. |
Maintenance | Low maintenance; typically long-lasting if properly designed. | Very low maintenance; passive component. | Requires occasional checks for mechanical wear and tear. |
Best Use Case | Power supply and transformer applications; energy storage. | Filtering and energy storage in circuits; used in radio frequencies. | Actuation in devices like valves and relays; applications requiring movement. |
What Are the Advantages and Disadvantages of Using Inductors as an Alternative?
Inductors serve as effective alternatives to electrical coils, particularly in applications requiring energy storage and filtering. Their design is often simpler, which leads to lower manufacturing costs and easier integration into electronic circuits. Inductors are particularly beneficial in power supplies and radio frequency applications, where they help manage current flow and signal integrity. However, their performance can be limited by frequency and may not provide the same level of energy storage as coils in high-demand scenarios.
How Do Solenoid Coils Compare to Electrical Coils?
Solenoid coils excel in applications where mechanical movement is required, such as in actuators and relays. They convert electrical energy into linear motion, making them invaluable in automated systems. While solenoids can be more expensive due to their construction and mechanical components, they offer unique advantages in control and automation. However, they may require more maintenance than electrical coils, as the moving parts can wear out over time.
Conclusion: How Can B2B Buyers Choose the Right Electrical Solution?
Selecting the appropriate technology—whether electrical coils, inductors, or solenoid coils—depends on the specific requirements of the application. B2B buyers should evaluate performance needs, cost constraints, ease of implementation, and maintenance capabilities. By understanding the unique advantages and limitations of each alternative, buyers can make informed decisions that align with their operational goals and budgetary considerations.
Essential Technical Properties and Trade Terminology for electrical coil
What Are the Key Technical Properties of Electrical Coils?
Understanding the technical properties of electrical coils is crucial for B2B buyers to ensure compatibility and performance in their applications. Here are some essential specifications to consider:
1. Material Grade
The material used in the construction of electrical coils significantly impacts their performance. Common materials include copper and aluminum for the wire, while the core may be made from iron, ferrite, or air. Copper, for instance, has high conductivity, making it ideal for applications requiring efficient power transmission. Buyers should assess the material grade to ensure it meets industry standards and is suitable for their specific needs.
2. Inductance
Inductance is a measure of a coil’s ability to store energy in a magnetic field. It’s expressed in henries (H) and is critical for applications in transformers and inductors. High inductance coils can store more energy, which is essential in power supply circuits. Understanding the inductance value helps buyers select coils that can handle their required electrical loads without saturation.
3. Tolerance
Tolerance refers to the allowable variation in the coil’s inductance, resistance, and other electrical parameters. It is crucial for ensuring that the coil performs reliably within the specified range. A tighter tolerance may be necessary for precision applications, while looser tolerances can be acceptable for general-purpose use. B2B buyers should evaluate tolerance levels to avoid issues related to performance and reliability.
4. DC Resistance
DC resistance (DCR) is the resistance of the coil when direct current flows through it, measured in ohms. It affects the efficiency and thermal performance of the coil, as higher resistance can lead to energy losses in the form of heat. Buyers should consider DCR when selecting coils for applications where power efficiency is critical.
5. Temperature Coefficient
This property indicates how the inductance of a coil changes with temperature. A lower temperature coefficient means that the inductance remains stable across a wider temperature range, which is crucial for applications exposed to varying environmental conditions. Buyers should assess the temperature coefficient to ensure consistent performance in their specific operating environments.
What Are Common Trade Terms Related to Electrical Coils?
Navigating the trade terminology in the electrical coil industry can help B2B buyers make informed purchasing decisions. Here are some essential terms:
1. OEM (Original Equipment Manufacturer)
An OEM is a company that produces components or products that are marketed by another company under its brand name. Understanding the OEM relationship is vital for buyers, as it helps them identify reputable manufacturers and ensures compatibility with their existing systems.
2. MOQ (Minimum Order Quantity)
MOQ refers to the minimum number of units that a supplier is willing to sell in a single order. This term is important for B2B buyers to understand as it affects pricing and inventory management. Buyers must evaluate their needs against the MOQ to optimize costs and avoid excess inventory.
3. RFQ (Request for Quotation)
An RFQ is a document sent to suppliers requesting a quote for specific products or services. It is an essential step in the procurement process, allowing buyers to compare pricing, terms, and conditions from multiple suppliers. A well-structured RFQ can lead to better pricing and terms for electrical coils.
4. Incoterms (International Commercial Terms)
Incoterms are a set of international rules that define the responsibilities of sellers and buyers in the delivery of goods. Familiarity with Incoterms such as FOB (Free On Board) or CIF (Cost, Insurance, and Freight) is crucial for B2B buyers engaged in international trade, as it clarifies shipping responsibilities and costs.
5. Lead Time
Lead time refers to the amount of time it takes from placing an order to receiving the products. Understanding lead times is critical for supply chain management and project planning. Buyers should inquire about lead times to ensure that they can meet their production schedules without delays.
By grasping these technical properties and trade terminologies, international B2B buyers can enhance their procurement processes and ensure they select the right electrical coils for their applications.
Navigating Market Dynamics and Sourcing Trends in the electrical coil Sector
What Are the Key Market Dynamics and Trends Affecting the Electrical Coil Sector?
The electrical coil sector is experiencing dynamic changes driven by technological advancements and shifting global demands. Key factors such as the rise of renewable energy, smart technologies, and automation are reshaping the landscape. In particular, industries in Africa, South America, the Middle East, and Europe are witnessing increased investments in electric coils due to their critical roles in power distribution, energy storage, and electronic devices. For instance, the demand for inductors and solenoid coils is surging as they are integral to electric vehicles (EVs) and renewable energy systems like solar inverters.
Emerging trends include the integration of IoT (Internet of Things) technologies, which require more sophisticated coils for efficient energy management and connectivity. Additionally, the shift towards miniaturization in electronic devices is prompting manufacturers to innovate with smaller, more efficient coil designs. These developments are crucial for B2B buyers who need to stay ahead of market demands and secure reliable sources for high-performance components.
Furthermore, international B2B buyers are encouraged to leverage data analytics and AI for informed sourcing decisions. By analyzing market trends and supplier performance, businesses can optimize their procurement strategies, ensuring they acquire quality electrical coils that meet regulatory standards and performance expectations.
How Can Sustainability and Ethical Sourcing Influence B2B Buying Decisions?
As global awareness of environmental issues grows, sustainability is becoming a critical factor in the sourcing of electrical coils. B2B buyers must consider the environmental impact of their suppliers’ practices. This includes understanding the sourcing of raw materials, energy consumption during production, and the lifecycle of the products.
Ethical supply chains are increasingly important; companies that prioritize sustainable practices are more likely to attract environmentally conscious consumers and partners. Buyers should seek suppliers with certifications such as ISO 14001 (Environmental Management) and those using recycled or eco-friendly materials in their coil manufacturing processes.
Furthermore, many manufacturers are adopting green technologies to minimize waste and energy use in production. Investing in suppliers that demonstrate a commitment to sustainability can also enhance a company’s reputation and compliance with international regulations, particularly in regions like Europe where environmental standards are stringent.
How Has the Electrical Coil Sector Evolved Over Time?
The evolution of the electrical coil sector reflects broader technological advancements and changing market needs. Initially, coils were primarily used in basic electrical circuits for inductance and filtering. Over time, the introduction of electromagnetic coils, solenoids, and voice coils expanded their applications significantly.
The 20th century saw the rise of electronic devices, driving the demand for more sophisticated coils capable of handling higher frequencies and energy levels. Today, with the advent of smart technologies and renewable energy solutions, the role of electrical coils has expanded to include critical components in power transformers, energy storage systems, and electric vehicles.
This historical context is essential for B2B buyers who must understand how past innovations inform current market offerings and future developments in the electrical coil sector. By recognizing these trends, companies can better navigate their sourcing strategies to align with emerging technologies and consumer demands.
Frequently Asked Questions (FAQs) for B2B Buyers of electrical coil
-
How do I choose the right electrical coil for my application?
Choosing the right electrical coil involves understanding your specific requirements, such as the application type (transformers, relays, or filters), the electrical specifications (voltage, current, and frequency), and the physical dimensions. Consider the material of the wire and core, as these can significantly affect performance. It’s also essential to evaluate the coil’s inductance and resistance values to ensure compatibility with your circuit. Collaborating with suppliers who offer customization can help tailor coils to meet your unique needs. -
What are the benefits of using customized electrical coils?
Customized electrical coils can provide significant advantages, including enhanced performance tailored to specific applications, reduced energy losses, and improved efficiency. They allow for the integration of unique specifications such as size, shape, and material, which can be critical in specialized applications. Additionally, customized coils can better meet regulatory standards relevant to your industry or region, ensuring compliance and reliability in operation. -
What is the minimum order quantity (MOQ) for electrical coils?
The minimum order quantity (MOQ) for electrical coils varies widely among manufacturers. Typically, MOQs can range from a few dozen units to several hundred, depending on factors such as the complexity of the coil design and the manufacturer’s production capabilities. For international buyers, it’s advisable to discuss MOQs directly with suppliers during the sourcing process, as some may offer flexibility for first-time orders or smaller companies. -
How can I vet suppliers of electrical coils for international purchases?
Vetting suppliers involves several steps: first, research their reputation through reviews and testimonials. Verify their certifications and compliance with international standards such as ISO or CE. Request samples to assess product quality, and inquire about their production capabilities, lead times, and payment terms. Establishing communication and building relationships with potential suppliers can also provide insights into their reliability and customer service. -
What payment terms should I expect when sourcing electrical coils internationally?
Payment terms can vary by supplier and region, but common options include upfront payments, partial payments upon order confirmation, and payment upon delivery. International buyers should consider using secure payment methods like letters of credit or escrow services to mitigate risks. Discussing and negotiating payment terms upfront is crucial to ensure mutual understanding and to establish a trustworthy trading relationship. -
What are the common logistics considerations for shipping electrical coils?
Logistics for shipping electrical coils involve understanding shipping costs, delivery timelines, and customs regulations in both the exporting and importing countries. It’s essential to choose a reliable freight forwarder experienced in handling electrical components. Consider the packaging to protect coils during transit and check for any specific documentation required for customs clearance. Also, plan for potential delays or tariffs that may arise during international shipping. -
How do I ensure quality assurance for electrical coils during sourcing?
To ensure quality assurance, request detailed specifications and certifications from suppliers. Implement a quality control process that includes inspecting samples before bulk orders. Consider third-party inspections or audits of the manufacturing facility to verify production standards. Establish clear communication regarding quality expectations and have a return policy in place for defective products to safeguard your investment. -
What are the key factors affecting the price of electrical coils in international markets?
Several factors influence the pricing of electrical coils, including raw material costs, labor expenses, and manufacturing processes. The complexity of the coil design and the volume of the order can also affect pricing, with larger quantities often leading to lower per-unit costs. Additionally, currency fluctuations and import tariffs in the buyer’s country can impact overall costs. It’s advisable to request quotes from multiple suppliers to compare pricing structures and negotiate better terms.
Important Disclaimer & Terms of Use
⚠️ Important Disclaimer
The information provided in this guide, including content regarding manufacturers, technical specifications, and market analysis, is for informational and educational purposes only. It does not constitute professional procurement advice, financial advice, or legal advice.
While we have made every effort to ensure the accuracy and timeliness of the information, we are not responsible for any errors, omissions, or outdated information. Market conditions, company details, and technical standards are subject to change.
B2B buyers must conduct their own independent and thorough due diligence before making any purchasing decisions. This includes contacting suppliers directly, verifying certifications, requesting samples, and seeking professional consultation. The risk of relying on any information in this guide is borne solely by the reader.
Strategic Sourcing Conclusion and Outlook for electrical coil
As international B2B buyers navigate the complexities of sourcing electrical coils, strategic sourcing emerges as a vital approach to ensure quality, cost-effectiveness, and supply chain resilience. Understanding the various types of electrical coils—such as inductors, solenoids, and transformers—along with their applications can greatly enhance procurement decisions. By assessing factors such as material composition, manufacturing capabilities, and market trends, buyers can identify reliable suppliers who meet specific industry needs.
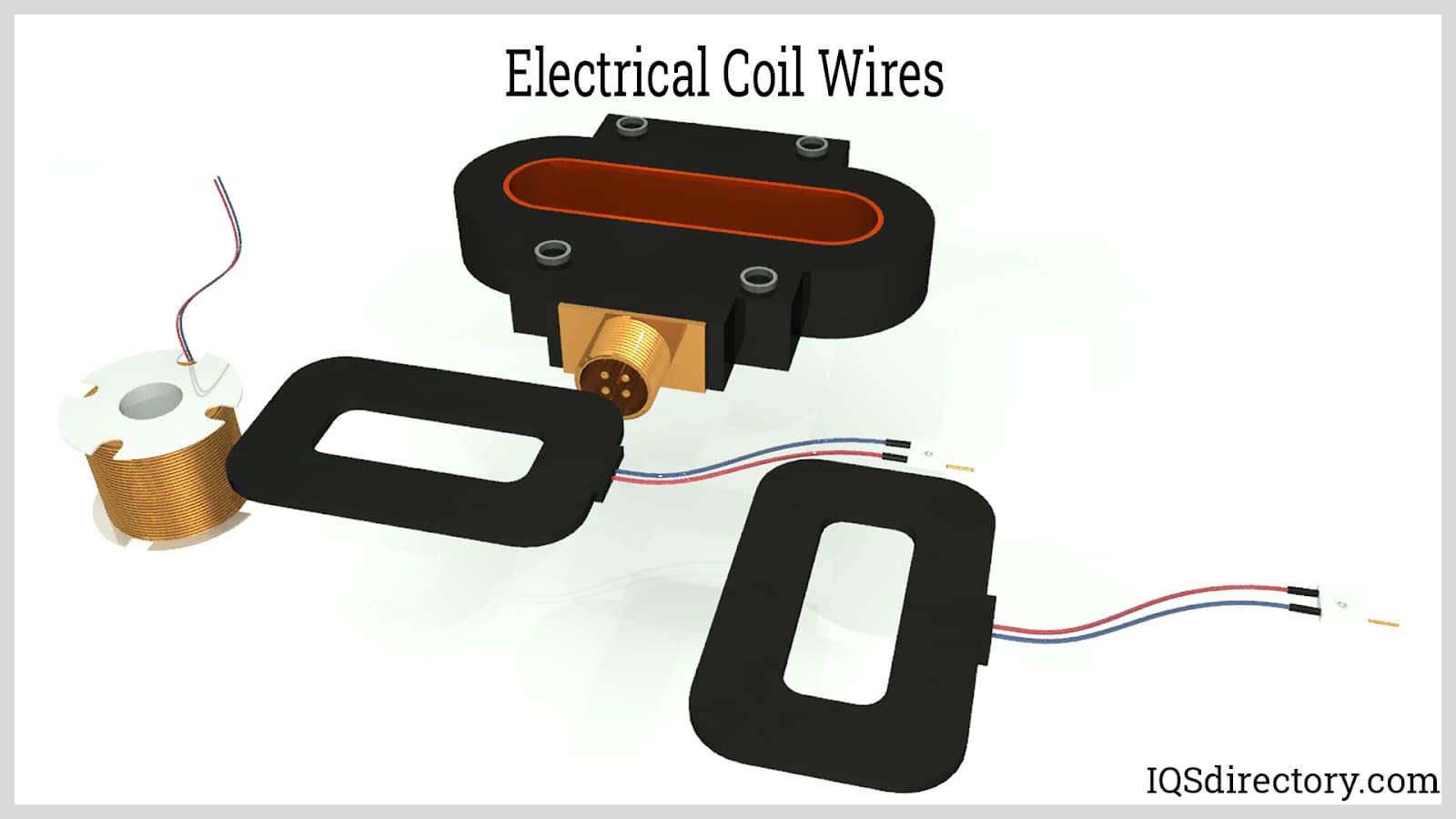
A stock image related to electrical coil.
What Are the Key Benefits of Strategic Sourcing for Electrical Coils?
The benefits of strategic sourcing include not only enhanced supplier relationships but also improved negotiation outcomes that can lead to better pricing and terms. Additionally, understanding regional market dynamics—especially in Africa, South America, the Middle East, and Europe—can provide insights into local supplier capabilities and innovation trends.
How Can Buyers Prepare for Future Trends in Electrical Coil Sourcing?
Looking ahead, the demand for electrical coils is likely to increase, driven by advancements in technology and the growing need for energy-efficient solutions. Buyers are encouraged to stay informed about emerging technologies and shifts in global supply chains that may impact availability and pricing. Engaging with suppliers who prioritize sustainability and innovation will be crucial for long-term success.
In conclusion, investing in strategic sourcing of electrical coils not only enhances operational efficiencies but also positions companies to capitalize on future growth opportunities. Take action today by exploring potential suppliers and integrating strategic sourcing principles into your procurement strategy.