Discover Cost-Effective Hardware Brackets: A Complete Guide (2025)
Introduction: Navigating the Global Market for hardware brackets
In an increasingly interconnected world, sourcing hardware brackets can present unique challenges for international B2B buyers, especially those operating in diverse markets like Africa, South America, the Middle East, and Europe. From ensuring product quality to navigating import regulations, the complexity of procuring the right hardware brackets—be it mounting, corner, or mending types—can be daunting. This comprehensive guide aims to demystify the process by offering actionable insights into the various types of hardware brackets, their applications across different industries, and best practices for supplier vetting.
Our exploration will cover essential factors such as cost considerations, material specifications, and the importance of compliance with international standards. By understanding these elements, B2B buyers can make informed purchasing decisions that align with their operational needs and budget constraints. This guide is tailored to empower international buyers, providing them with the knowledge required to not only select the most suitable hardware brackets but also to establish long-term relationships with reliable suppliers.
As you navigate the global market for hardware brackets, our guide serves as a valuable resource to enhance your procurement strategies, ensuring that you can effectively meet project demands while minimizing risks associated with sourcing. Whether you are in Thailand, Germany, or elsewhere, the insights provided here will help streamline your purchasing process and optimize your supply chain.
Understanding hardware brackets Types and Variations
Type Name | Key Distinguishing Features | Primary B2B Applications | Brief Pros & Cons for Buyers |
---|---|---|---|
Angle Brackets | L-shaped, typically made of metal, used for right angles. | Structural support in construction. | Pros: Strong load-bearing capacity. Cons: Requires precise installation. |
Corner Braces | Triangular design, often used to reinforce corners. | Furniture assembly, cabinetry. | Pros: Enhances stability. Cons: Limited load capacity compared to other types. |
Mending Plates | Flat plates used to join two pieces of material together. | Repairing furniture, metalwork. | Pros: Easy to use and install. Cons: May not be aesthetically pleasing. |
Mounting Brackets | Designed to attach items to walls or other surfaces. | Shelving, signage, heavy equipment. | Pros: Versatile and widely available. Cons: Weight limits vary by design. |
Flat Braces | Flat strips used for reinforcement, often hidden from view. | Structural reinforcement. | Pros: Space-saving design. Cons: May require additional support for heavy loads. |
What Are Angle Brackets and Where Are They Used?
Angle brackets are L-shaped metal pieces that provide structural support by forming right angles. They are commonly used in construction and manufacturing to reinforce joints and frames. For B2B buyers, the key consideration is the material and gauge of the angle bracket, as these factors affect its load-bearing capacity. Galvanized steel options are particularly popular for outdoor applications due to their corrosion resistance.
How Do Corner Braces Enhance Stability?
Corner braces are triangular brackets that reinforce the corners of furniture and cabinetry. They are essential in applications where added stability is necessary, such as in shelving units or tables. B2B buyers should consider the thickness and finish of the brace, as these elements can affect both strength and aesthetics. The ease of installation is another important factor, especially for high-volume manufacturers.
What Are Mending Plates and Their Applications?
Mending plates are flat metal pieces used to join two materials together, making them ideal for repairs in furniture and metalwork. They are particularly useful in situations where a strong, permanent bond is required. Buyers should evaluate the plate’s dimensions and thickness to ensure compatibility with their projects. While they are easy to install, their appearance may not always be suitable for visible applications.
Why Choose Mounting Brackets for Versatile Applications?
Mounting brackets are designed to attach various items to walls or surfaces, making them highly versatile. They are widely used in shelving, signage, and mounting heavy equipment. When purchasing, buyers should consider the weight capacity and the type of installation required, as these factors can impact the bracket’s effectiveness. Additionally, the choice of material—whether metal or plastic—will influence durability and application.
What Are Flat Braces and Their Benefits?
Flat braces are strips of metal that provide support and reinforcement, often hidden from view. They are typically used in structural applications where aesthetics are less of a concern. B2B buyers should assess the brace’s length and thickness to determine its suitability for specific projects. While they save space and are easy to install, it’s crucial to ensure they are used in conjunction with other support systems for heavy loads.
Key Industrial Applications of hardware brackets
Industry/Sector | Specific Application of Hardware Brackets | Value/Benefit for the Business | Key Sourcing Considerations for this Application |
---|---|---|---|
Construction & Building | Structural support for beams and columns | Enhances stability and safety of structures | Material strength, corrosion resistance, and load capacity |
Furniture Manufacturing | Shelf and cabinetry support systems | Maximizes space utilization and aesthetic appeal | Design compatibility, weight capacity, and finish options |
Electrical & Electronics | Mounting brackets for electrical components | Ensures safety and accessibility of wiring systems | Compliance with local standards, material durability |
HVAC Systems | Support brackets for ductwork and piping | Improves efficiency and airflow in systems | Resistance to temperature fluctuations and corrosion |
Automotive & Transportation | Mounting solutions for vehicle components | Enhances performance and safety of vehicles | Vibration resistance, weight considerations, and durability |
How Are Hardware Brackets Used in the Construction & Building Industry?
In the construction and building sector, hardware brackets are essential for providing structural support to beams and columns. They are designed to bear significant loads, ensuring the stability and safety of buildings. International B2B buyers must consider the material strength and corrosion resistance of brackets, especially in regions prone to humidity or extreme weather. Meeting local building codes and standards is crucial to avoid legal complications and ensure safety.
What Role Do Hardware Brackets Play in Furniture Manufacturing?
In furniture manufacturing, hardware brackets are vital for creating robust shelf and cabinetry support systems. They help maximize space utilization while enhancing the aesthetic appeal of furniture pieces. Buyers in this sector should focus on design compatibility and weight capacity to ensure that the brackets can support the intended loads without compromising style. Additionally, various finishes may be required to match different furniture designs.
How Are Hardware Brackets Utilized in the Electrical & Electronics Sector?
For the electrical and electronics industry, mounting brackets are crucial for securing components such as circuit boards and wiring systems. Proper installation ensures safety and accessibility, minimizing the risk of electrical hazards. B2B buyers should prioritize compliance with local safety standards and durability of materials, especially in high-temperature environments. Additionally, sourcing brackets that provide easy access for maintenance can add significant value.
Why Are Hardware Brackets Important in HVAC Systems?
In HVAC systems, support brackets are used to secure ductwork and piping, ensuring efficient airflow and system performance. Properly installed brackets help prevent sagging and misalignment, which can lead to decreased efficiency and increased energy costs. Buyers should consider the resistance of materials to temperature fluctuations and corrosion, particularly in regions with extreme climates, to ensure longevity and reliability.
How Do Hardware Brackets Enhance Safety in Automotive & Transportation?
In the automotive and transportation industry, hardware brackets are used to mount various components, ensuring performance and safety. They play a critical role in securing parts that experience vibrations and dynamic loads. B2B buyers need to focus on vibration resistance and weight considerations when selecting brackets. Durability is also paramount, given the harsh conditions vehicles may encounter.
3 Common User Pain Points for ‘hardware brackets’ & Their Solutions
Scenario 1: Sourcing Reliable Hardware Brackets for Diverse Applications
The Problem: International B2B buyers often face the challenge of sourcing hardware brackets that meet specific project requirements across various industries. For instance, a construction company in South America may need heavy-duty brackets for steel framing, while a furniture manufacturer in Europe requires decorative brackets for wooden shelves. The inconsistency in quality and specifications from different suppliers can lead to project delays and increased costs, causing frustration for procurement teams.
The Solution: To effectively address this sourcing challenge, buyers should prioritize establishing relationships with reputable suppliers who specialize in the specific types of brackets needed. Conduct thorough research to identify manufacturers that offer detailed product specifications, including load ratings, material composition, and compliance with international standards. Utilize platforms such as trade shows, industry directories, and online marketplaces to connect with verified suppliers. Furthermore, consider bulk purchasing agreements to ensure consistent supply and negotiate favorable terms. This approach not only secures quality products but also streamlines procurement processes, reducing the risk of project interruptions.
Scenario 2: Ensuring Compatibility with Existing Structures
The Problem: A common issue B2B buyers encounter is ensuring that the hardware brackets they purchase are compatible with existing structures. For example, an engineering firm in Africa may need to retrofit an old building with new brackets for enhanced support. If the dimensions or mounting styles do not align, it could lead to costly modifications and extended project timelines.
The Solution: To prevent compatibility issues, buyers should conduct a comprehensive assessment of the existing structures before sourcing brackets. This includes taking precise measurements of the areas where the brackets will be installed and understanding the load-bearing requirements. It’s beneficial to consult with structural engineers or architects to determine the appropriate bracket types and sizes. When selecting brackets, ensure that suppliers provide detailed dimensional drawings and installation guidelines. Additionally, consider opting for adjustable or universal brackets, which can offer flexibility in accommodating various installation scenarios. This proactive approach helps avoid costly errors and ensures a smooth integration process.
Scenario 3: Managing Inventory and Reducing Waste
The Problem: Many B2B buyers struggle with managing their inventory of hardware brackets, leading to either excess stock or shortages that disrupt operations. For instance, a manufacturing company in the Middle East may overestimate its needs for a specific project, resulting in leftover brackets that contribute to waste and increased holding costs.
The Solution: Implementing a robust inventory management system can significantly mitigate this issue. Buyers should analyze historical project data to forecast demand accurately and adjust their purchasing strategies accordingly. Utilizing just-in-time (JIT) inventory practices can help maintain optimal stock levels, reducing the likelihood of overstocking. Additionally, consider collaborating with suppliers who offer flexible ordering options, allowing for smaller, more frequent shipments that align with project timelines. Training staff on effective inventory tracking and management techniques can also enhance efficiency and reduce waste. By adopting these strategies, companies can not only save costs but also contribute to more sustainable practices in their operations.
Strategic Material Selection Guide for hardware brackets
When selecting materials for hardware brackets, international B2B buyers must consider various factors such as performance properties, manufacturing complexities, and compliance with regional standards. Below, we analyze four common materials used in hardware brackets: steel, aluminum, plastic, and cast iron. Each material has unique characteristics that can significantly impact the performance and suitability of the brackets in different applications.
What Are the Key Properties of Steel for Hardware Brackets?
Steel is one of the most commonly used materials for hardware brackets due to its high strength and durability. Steel brackets can withstand high temperatures and pressures, making them suitable for heavy-duty applications. They also offer excellent corrosion resistance when galvanized or coated with protective finishes.
Pros and Cons: The primary advantage of steel is its strength-to-weight ratio, which allows for the design of robust brackets that can support significant loads. However, steel can be more expensive than other materials and may require additional treatments to enhance corrosion resistance, which can increase manufacturing complexity.
Impact on Application: Steel brackets are ideal for construction and industrial applications where structural integrity is paramount. However, buyers should be aware of potential rusting in humid environments, particularly in regions like Africa and the Middle East.
How Does Aluminum Compare as a Material for Hardware Brackets?
Aluminum is another popular choice for hardware brackets, especially in applications where weight is a concern. It is lightweight, resistant to corrosion, and can be anodized for additional protection.
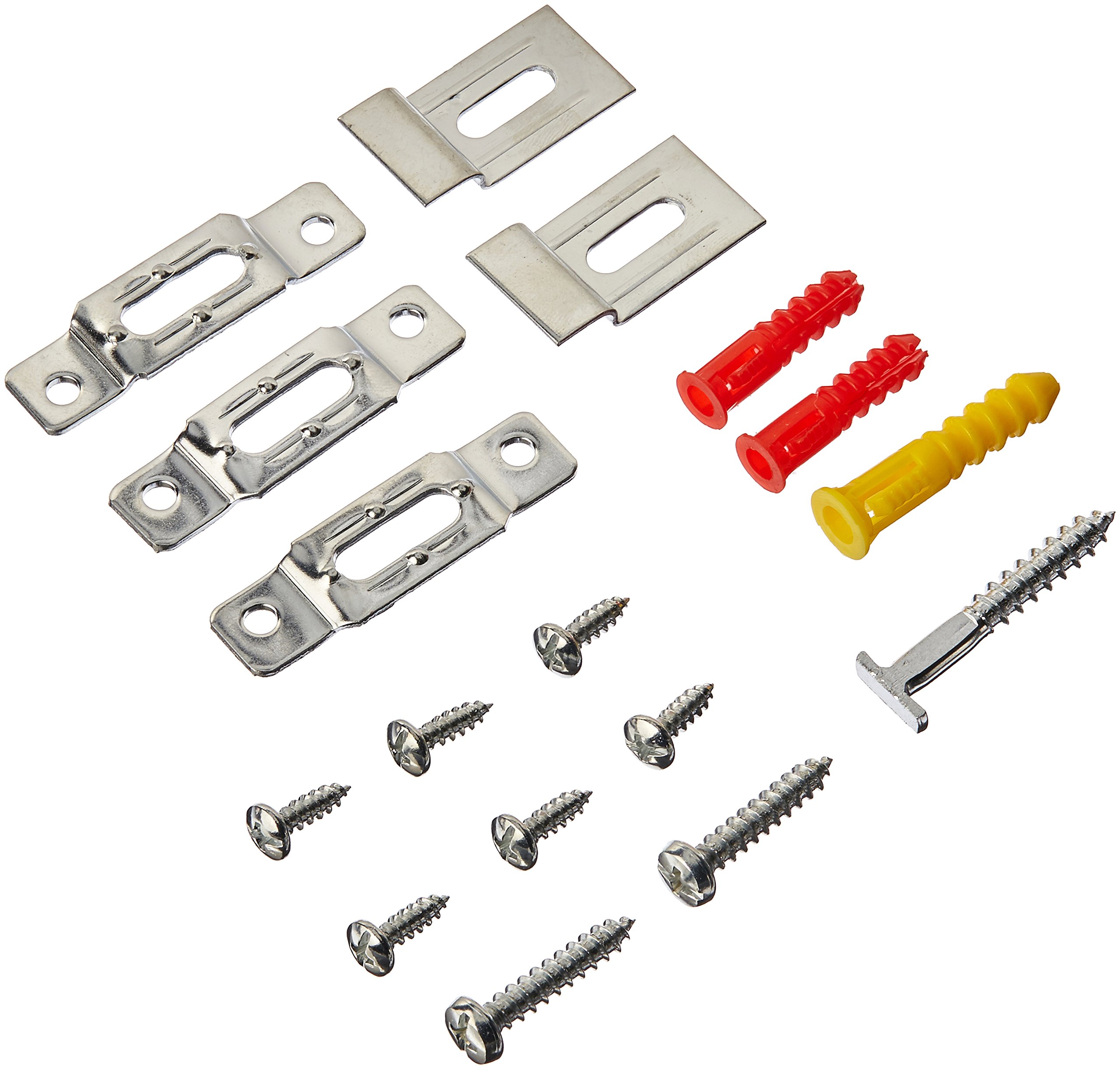
A stock image related to hardware brackets.
Pros and Cons: The main advantage of aluminum is its lightweight nature, making it easier to handle and install. However, it has a lower load-bearing capacity compared to steel, which may limit its use in heavy-duty applications. Additionally, aluminum can be more expensive than steel, particularly in regions where it is not locally sourced.
Impact on Application: Aluminum brackets are often used in the automotive and aerospace industries, as well as in applications requiring resistance to corrosion, such as coastal regions in South America and Europe. Compliance with standards like ASTM or DIN is essential for ensuring quality.
What Are the Advantages of Using Plastic for Hardware Brackets?
Plastic brackets are gaining popularity due to their versatility and resistance to corrosion. They are often used in applications where moisture exposure is a concern.
Pros and Cons: The advantages of plastic include low cost and ease of manufacturing. However, plastic brackets may not support heavy loads and can become brittle over time, especially under UV exposure.
Impact on Application: Plastic brackets are suitable for indoor applications or environments with minimal load requirements. Buyers in regions with high humidity, such as parts of Africa and South America, may find plastic brackets advantageous due to their moisture resistance.
Why Choose Cast Iron for Hardware Brackets?
Cast iron brackets are known for their strength and durability, making them suitable for decorative and structural applications. They can withstand high loads and provide stability in various environments.
Pros and Cons: The key advantage of cast iron is its high load-bearing capacity, making it ideal for heavy-duty applications. However, cast iron is heavier and more brittle than other materials, which can complicate installation and increase shipping costs.
Impact on Application: Cast iron is often used in architectural applications, such as in Europe, where aesthetic considerations are important. Compliance with local standards is crucial, especially in countries like Germany, where strict regulations govern construction materials.
Summary Table of Material Selection for Hardware Brackets
Material | Typical Use Case for hardware brackets | Key Advantage | Key Disadvantage/Limitation | Relative Cost (Low/Med/High) |
---|---|---|---|---|
Steel | Heavy-duty industrial applications | High strength and load-bearing capacity | Higher cost and corrosion treatment needed | High |
Aluminum | Automotive and aerospace applications | Lightweight and corrosion-resistant | Lower load capacity than steel | Medium |
Plastic | Indoor applications and moisture-prone areas | Low cost and moisture resistance | Limited load-bearing capacity | Low |
Cast Iron | Decorative and structural applications | High load-bearing capacity | Heavier and more brittle | Medium |
This strategic material selection guide provides actionable insights for international B2B buyers, helping them make informed decisions based on their specific application needs and regional considerations.
In-depth Look: Manufacturing Processes and Quality Assurance for hardware brackets
What Are the Key Manufacturing Processes for Hardware Brackets?
Manufacturing hardware brackets involves several critical stages that ensure the final product meets durability, functionality, and aesthetic standards. Understanding these processes is vital for B2B buyers to evaluate potential suppliers effectively.
1. Material Preparation: What Materials Are Commonly Used?
The first stage in manufacturing hardware brackets is material preparation. Common materials include:
- Steel: Often galvanized for corrosion resistance, steel is favored for its strength and load-bearing capabilities.
- Aluminum: Lightweight and resistant to corrosion, aluminum is used for brackets in environments where weight is a concern.
- Plastic and Composite Materials: These are typically used for decorative brackets or where corrosion resistance is a priority.
Suppliers typically source materials from certified mills, ensuring that they meet international standards. B2B buyers should inquire about the material specifications, including grades and certifications, to ensure compliance with their project requirements.
2. Forming: How Are Brackets Shaped and Sized?
Forming is a crucial step where raw materials are shaped into bracket forms. Key techniques include:
- Cutting: Laser cutting or shearing is employed to create precise dimensions. Buyers should verify that suppliers use advanced technology to ensure accuracy.
- Bending: Methods such as press braking shape the material into the desired angle or form. This process must be controlled to maintain structural integrity.
- Stamping: High-volume production often utilizes stamping, which allows for quick and uniform production of brackets.
B2B buyers should ask for details about the machinery used and the capabilities of the supplier in producing custom sizes and designs.
3. Assembly: What Are the Common Assembly Techniques?
After forming, brackets may undergo assembly, especially if they consist of multiple components. Common assembly techniques include:
- Welding: For steel brackets, welding is a prevalent method to join parts securely. The quality of the weld is critical for strength.
- Riveting and Bolting: These methods are often used for aluminum brackets, allowing for disassembly if needed.
- Adhesive Bonding: Increasingly used in plastic and composite brackets, this technique provides a seamless finish.
B2B buyers should ensure that suppliers have skilled labor and appropriate machinery for assembly to maintain high-quality standards.
4. Finishing: How Are Brackets Coated and Protected?
Finishing processes enhance both the appearance and durability of hardware brackets. Common finishing methods include:
- Powder Coating: A popular choice for steel and aluminum brackets, powder coating provides a robust and weather-resistant finish.
- Galvanization: This process involves coating steel brackets with zinc to prevent rust, ideal for outdoor applications.
- Plating: Nickel or chrome plating is used for aesthetic purposes and corrosion resistance.
Buyers should inquire about the types of finishes available and their suitability for specific applications, especially in harsh environments.
What Quality Assurance Standards Should B2B Buyers Consider?
Quality assurance is crucial in ensuring that hardware brackets meet required specifications and standards. Buyers should familiarize themselves with both international and industry-specific standards.
1. What Are the Relevant International Standards?
- ISO 9001: This standard focuses on quality management systems and is applicable across various industries, including manufacturing. Suppliers certified under ISO 9001 have established processes for continuous improvement.
- CE Marking: Essential for products sold within the European Economic Area, CE marking indicates compliance with health, safety, and environmental protection standards.
B2B buyers should verify that their suppliers possess these certifications and understand their implications for product quality.
2. What Are the Industry-Specific Quality Certifications?
Depending on the application, additional certifications might be relevant:
- API (American Petroleum Institute): For brackets used in oil and gas applications, compliance with API standards ensures safety and reliability.
- ASTM (American Society for Testing and Materials): Many brackets must meet ASTM specifications for materials and performance.
Buyers should specify the required certifications based on their market and application needs.
What Are the Key Quality Control Checkpoints in Manufacturing?
Quality control (QC) is an integral part of the manufacturing process, ensuring that products meet the desired specifications. Key checkpoints include:
1. Incoming Quality Control (IQC)
IQC involves inspecting raw materials upon arrival. This includes verifying material certifications and conducting tests to ensure compliance with specifications. Buyers should inquire about the supplier’s IQC processes and the criteria used for material acceptance.
2. In-Process Quality Control (IPQC)
During the manufacturing process, IPQC checks are essential to monitor production techniques and ensure that tolerances are maintained. Regular audits and inspections should be conducted to identify any deviations early in the process.
3. Final Quality Control (FQC)
FQC occurs after manufacturing is complete, focusing on the final product’s adherence to specifications. This includes dimensional checks, functional testing, and visual inspections. B2B buyers should request samples of FQC reports to assess the supplier’s quality assurance practices.
How Can B2B Buyers Verify Supplier Quality Control?
Verifying a supplier’s quality control measures is essential for mitigating risk. Here are some actionable steps:
1. Conduct Supplier Audits
Regular audits of suppliers can provide insights into their manufacturing processes and QC practices. Buyers should consider establishing an audit schedule to maintain oversight.
2. Request Quality Reports
Buyers should ask for detailed quality reports, including IQC, IPQC, and FQC data. This documentation can help assess the supplier’s commitment to quality.
3. Utilize Third-Party Inspections
Engaging third-party inspection services can add an additional layer of assurance. These organizations can conduct independent assessments of both materials and finished products.
What Are the Quality Control Nuances for International B2B Buyers?
International buyers should be aware of certain nuances when it comes to quality control:
- Cultural Differences: Varying approaches to quality assurance may exist across regions. Understanding these differences can help buyers navigate supplier relationships effectively.
- Regulatory Compliance: Different countries have unique regulations regarding product safety and quality. Buyers should ensure that their suppliers are compliant with both local and international regulations.
By understanding the manufacturing processes and quality assurance practices associated with hardware brackets, B2B buyers can make informed decisions and foster successful supplier relationships.
Practical Sourcing Guide: A Step-by-Step Checklist for ‘hardware brackets’
To successfully source hardware brackets for your business, it’s essential to follow a structured approach that ensures quality and reliability. This checklist will guide international B2B buyers, particularly from Africa, South America, the Middle East, and Europe, through the sourcing process to make informed decisions.
Step 1: Define Your Technical Specifications
Before beginning your search for suppliers, clearly outline the technical specifications of the hardware brackets you need. This includes dimensions, materials (such as galvanized steel or aluminum), load-bearing capacities, and finishes. Understanding your requirements helps in communicating effectively with potential suppliers and ensures you receive products that meet your operational needs.
- Consider the application: Are these brackets for heavy-duty use or decorative purposes?
- Identify industry standards: Research if there are specific regulations or standards (like ISO or ASTM) that your brackets must comply with in your region.
Step 2: Research Potential Suppliers
Conduct thorough research to identify potential suppliers that specialize in hardware brackets. Look for manufacturers with a proven track record in your specific region, as they may better understand local market needs and regulations.
- Utilize online directories: Websites like Alibaba or ThomasNet can help you find verified suppliers.
- Check supplier reviews: Look for testimonials and case studies that showcase their reliability and quality.
Step 3: Evaluate Supplier Certifications
Before engaging in business, verify the certifications and standards that suppliers adhere to. This is crucial for ensuring product quality and compliance with safety regulations.
- Request documentation: Ask for ISO certifications, quality control processes, and material safety data sheets (MSDS).
- Investigate compliance: Ensure the supplier meets local regulations relevant to your industry.
Step 4: Request Samples for Quality Assessment
Once you have shortlisted suppliers, request samples of their hardware brackets. This step is vital in assessing the actual product quality, durability, and finish.
- Conduct tests: Test the samples under real-world conditions to ensure they meet your expectations for load capacity and longevity.
- Evaluate aesthetics: For decorative brackets, ensure the finish aligns with your design requirements.
Step 5: Compare Pricing and Payment Terms
Gather quotes from multiple suppliers to compare pricing effectively. Look beyond just the price; consider the total cost of ownership, including shipping, taxes, and potential tariffs.
- Negotiate payment terms: Discuss payment options that work for both parties, such as letters of credit or staggered payments based on order milestones.
- Consider bulk discounts: Inquire if there are discounts for larger orders, which can significantly reduce costs.
Step 6: Assess Customer Support and Communication
Evaluate the level of customer support provided by the supplier. Effective communication can be a significant factor in ensuring a smooth procurement process.
- Test responsiveness: Reach out with inquiries and assess how quickly and thoroughly they respond.
- Check after-sales support: Understand the processes for returns, refunds, or replacements in case of defects.
Step 7: Finalize the Contract and Place Your Order
Once you’ve selected a supplier, draft a clear contract that outlines all agreed-upon terms, including product specifications, delivery timelines, and payment terms.
- Include contingencies: Ensure the contract includes clauses for potential delays or quality issues.
- Confirm order details: Double-check the order details before finalizing to prevent any misunderstandings.
By following this practical sourcing guide, you can navigate the complexities of purchasing hardware brackets and ensure that your business acquires high-quality products that meet your operational needs.
Comprehensive Cost and Pricing Analysis for hardware brackets Sourcing
What Are the Key Cost Components for Hardware Brackets?
Understanding the cost structure of hardware brackets is essential for international B2B buyers, particularly those from diverse regions such as Africa, South America, the Middle East, and Europe. The primary cost components include:
-
Materials: The choice of material significantly impacts pricing. Common materials include galvanized steel, stainless steel, and aluminum. Higher-quality materials often result in increased costs but can offer better durability and performance.
-
Labor: Labor costs vary by region and can be influenced by local wage standards and labor availability. In countries with higher labor costs, it may be beneficial to consider sourcing from regions with lower wage rates, provided that quality is maintained.
-
Manufacturing Overhead: This includes costs related to facilities, utilities, and equipment maintenance. Efficient manufacturing processes can help reduce overhead costs, thereby lowering the overall price of brackets.
-
Tooling: Initial tooling costs for custom brackets can be significant. Buyers should consider these costs when evaluating quotes, especially for custom designs or specific dimensions.
-
Quality Control (QC): Implementing stringent QC measures can increase costs but is essential for ensuring product reliability and compliance with international standards. Buyers should weigh the benefits of enhanced QC against potential increases in price.
-
Logistics: Transportation costs can vary widely based on the origin of the brackets, shipping methods, and destination. Understanding local tariffs and shipping regulations is crucial for accurate cost estimation.
-
Margin: Suppliers typically include a profit margin in their pricing. This margin can vary significantly based on the supplier’s market position, brand reputation, and the competition in the region.
How Do Price Influencers Affect Hardware Bracket Costs?
Several factors influence the pricing of hardware brackets, which buyers should consider when sourcing:
-
Volume/MOQ (Minimum Order Quantity): Bulk orders often result in lower unit prices. Buyers should negotiate for better rates based on their purchasing volume.
-
Specifications and Customization: Custom brackets tailored to specific needs can increase costs. Buyers should clearly define their requirements to avoid unexpected expenses.
-
Materials: The material choice affects not just the cost but also the product’s end-use suitability. Buyers should assess the trade-off between cost and performance when selecting materials.
-
Quality and Certifications: Products that meet international quality standards or possess certifications may carry a premium price. However, investing in certified products can reduce long-term risks and liabilities.
-
Supplier Factors: The reputation and reliability of suppliers can influence pricing. Established suppliers might charge more due to their proven track record, but they often provide better service and quality assurance.
-
Incoterms: Understanding Incoterms is vital for cost management. They define the responsibilities of buyers and sellers regarding shipping costs, risks, and insurance, which can significantly affect total purchasing costs.
What Are Some Effective Buyer Tips for Sourcing Hardware Brackets?
International B2B buyers can enhance their sourcing strategies by applying the following tips:
-
Negotiation: Always negotiate pricing, especially for larger orders. Suppliers may have flexibility in their pricing structures, particularly if they want to secure a long-term relationship.
-
Cost-Efficiency: Evaluate the total cost of ownership (TCO), which includes purchase price, shipping, handling, and potential maintenance costs. Sometimes a higher initial price can lead to lower long-term costs.
-
Understanding Pricing Nuances: Be aware of regional pricing variations and market conditions. Factors such as currency fluctuations, local demand, and geopolitical factors can all impact prices.
-
Assessing Supplier Relationships: Building strong relationships with suppliers can lead to better pricing, priority service, and access to exclusive products or innovations.
-
Researching Market Trends: Staying informed about trends in hardware manufacturing and sourcing can provide insights into potential cost-saving opportunities and help in making informed purchasing decisions.
Disclaimer
The prices mentioned in this analysis are indicative and can vary based on market conditions, supplier pricing strategies, and specific buyer requirements. Always request quotes from multiple suppliers to ensure competitive pricing.
Alternatives Analysis: Comparing hardware brackets With Other Solutions
When considering hardware brackets for various applications, it’s essential to explore alternative solutions that can meet similar needs. This analysis will provide international B2B buyers, particularly from Africa, South America, the Middle East, and Europe, with a clear comparison of hardware brackets against other viable alternatives. By understanding the strengths and weaknesses of these options, businesses can make informed decisions that enhance their operational efficiency and cost-effectiveness.
Comparison Table of Hardware Brackets and Alternatives
Comparison Aspect | Hardware Brackets | Alternative 1: Structural Adhesives | Alternative 2: Welding |
---|---|---|---|
Performance | High load-bearing capacity | Strong bond for lightweight structures | Excellent strength for heavy-duty applications |
Cost | Moderate cost per unit | Generally lower than brackets | Higher initial cost due to labor and equipment |
Ease of Implementation | Requires pre-drilling and mounting | Easy application with no special tools | Requires skilled labor and equipment |
Maintenance | Low maintenance, durable materials | Potential for degradation over time | Very low maintenance, but repairs can be complex |
Best Use Case | Ideal for modular and adjustable structures | Best for seamless joins in lightweight assemblies | Suitable for permanent and heavy-duty connections |
What Are the Advantages and Disadvantages of Structural Adhesives?
Structural adhesives are a popular alternative to hardware brackets, especially in applications where aesthetics and seamless finishes are critical. The primary advantage of using structural adhesives is their ease of application, which does not require special tools or equipment. They are often less expensive than hardware brackets, making them a budget-friendly option for many projects. However, they are best suited for lighter loads, and their bond may degrade over time, especially in harsh environmental conditions.
How Does Welding Compare to Hardware Brackets?
Welding is another alternative that offers a robust solution for joining materials, particularly metals. The primary advantage of welding is its exceptional strength, making it ideal for heavy-duty applications where high load-bearing capabilities are required. However, welding demands skilled labor and specialized equipment, leading to higher initial costs. Additionally, while welds require minimal maintenance, any necessary repairs can be complicated and labor-intensive.
Conclusion: How to Choose the Right Solution for Your Needs?
When selecting between hardware brackets and alternative solutions like structural adhesives or welding, B2B buyers should consider the specific requirements of their projects. Factors such as load-bearing needs, budget constraints, and the desired permanence of the solution are critical in making the right choice. For modular applications where adjustments may be needed, hardware brackets are often preferable. In contrast, for permanent and heavy-duty installations, welding may provide the best results. Structural adhesives serve well for applications where aesthetics and ease of use are prioritized. By carefully evaluating these aspects, international buyers can select the solution that best aligns with their operational goals and project requirements.
Essential Technical Properties and Trade Terminology for hardware brackets
What Are the Key Technical Properties of Hardware Brackets?
When selecting hardware brackets for B2B applications, understanding their technical specifications is crucial. Here are some essential properties to consider:
1. Material Grade
Hardware brackets are typically made from materials like stainless steel, galvanized steel, and cast iron. The grade of the material affects its strength, corrosion resistance, and suitability for specific applications. For example, stainless steel brackets (e.g., 304 or 316 grades) are ideal for environments exposed to moisture, making them suitable for outdoor use in humid climates.
2. Load Capacity
The load capacity of a bracket indicates the maximum weight it can support without failure. This is critical for ensuring safety and functionality in applications ranging from shelving to structural support. B2B buyers should verify load ratings provided by manufacturers, often expressed in pounds or kilograms, to match the bracket to the intended application.
3. Tolerance
Tolerance refers to the allowable deviation from specified dimensions. In hardware brackets, this affects how well components fit together and how they perform under stress. High tolerance levels ensure that brackets will maintain their integrity and alignment, which is essential for long-term reliability.
4. Finish and Coating
The finish of a bracket, whether powder-coated, galvanized, or plain, impacts its aesthetic and functional properties. For instance, a powder-coated finish not only provides a decorative element but also adds a layer of protection against rust and wear, making it ideal for outdoor applications. Understanding these options allows buyers to select brackets that meet both aesthetic and durability needs.
5. Dimensions and Compatibility
Brackets come in various sizes and shapes, including corner braces, mounting brackets, and flat braces. Understanding the specific dimensions required for a project is crucial for ensuring compatibility with other components. Buyers should consider both the physical space available and the specific requirements of the application to choose the right size.
What Are Common Trade Terminologies Used in Hardware Brackets?
Familiarity with trade terminology is essential for effective communication in the B2B hardware market. Here are some commonly used terms:
1. OEM (Original Equipment Manufacturer)
An OEM is a company that produces parts or equipment that may be marketed by another manufacturer. In the context of hardware brackets, buyers may work directly with OEMs to ensure that the brackets meet their specific design and quality standards.
2. MOQ (Minimum Order Quantity)
MOQ refers to the smallest number of units that a supplier is willing to sell. Understanding MOQ is vital for buyers to manage inventory levels effectively and control costs, especially when sourcing hardware brackets from international suppliers.
3. RFQ (Request for Quotation)
An RFQ is a document that buyers send to suppliers to solicit pricing and terms for specific products, such as hardware brackets. This process helps businesses compare offers from multiple suppliers, ensuring they obtain the best possible deal.
4. Incoterms (International Commercial Terms)
Incoterms are a set of international rules that define the responsibilities of sellers and buyers in global trade. Familiarity with Incoterms helps B2B buyers understand shipping costs, risk management, and the obligations of both parties, which is crucial when sourcing hardware brackets from various regions, including Africa, South America, and Europe.
5. SKU (Stock Keeping Unit)
An SKU is a unique identifier for each distinct product and service that can be purchased. Understanding SKUs helps buyers manage inventory and streamline purchasing processes, particularly when dealing with large quantities of hardware brackets.
6. Lead Time
Lead time is the amount of time it takes for an order to be fulfilled once it has been placed. For B2B buyers, understanding lead times is essential for planning projects and ensuring that materials, like hardware brackets, are available when needed.
By grasping these technical properties and trade terminologies, B2B buyers can make more informed decisions when sourcing hardware brackets, ultimately leading to better project outcomes and cost management.
Navigating Market Dynamics and Sourcing Trends in the hardware brackets Sector
What Are the Current Market Dynamics and Sourcing Trends in the Hardware Brackets Sector?
The hardware brackets sector is experiencing significant growth driven by the expanding construction and manufacturing industries globally. Key markets in Africa, South America, the Middle East, and Europe are increasingly investing in infrastructure development, which fuels demand for robust and reliable hardware solutions. In particular, the rise of modular construction techniques has led to a greater focus on the versatility of brackets, necessitating a broader range of designs, materials, and load capacities.
Emerging technologies such as 3D printing and automation are reshaping sourcing trends, allowing manufacturers to produce custom brackets more efficiently and at lower costs. This trend is particularly relevant for international B2B buyers looking to streamline their procurement processes. Additionally, the increasing use of e-commerce platforms is transforming how buyers source hardware brackets, offering improved accessibility to global suppliers and facilitating real-time price comparisons.
International buyers must also navigate fluctuating raw material prices, particularly steel and aluminum, which can significantly impact production costs. Understanding regional market dynamics, including tariff implications and local regulations, is crucial for making informed purchasing decisions.
How Is Sustainability Influencing Sourcing Decisions for Hardware Brackets?
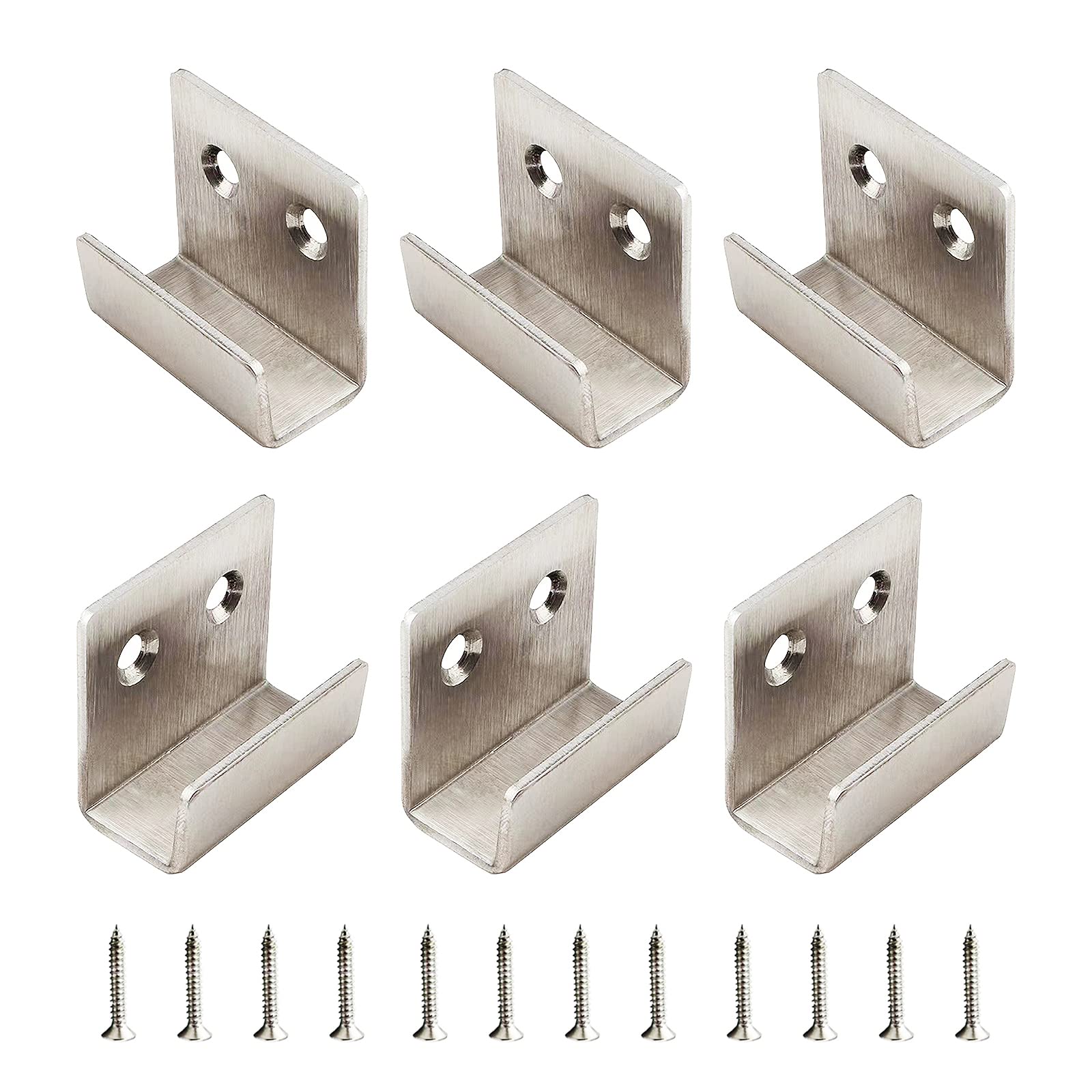
A stock image related to hardware brackets.
Sustainability is becoming a central consideration in the hardware brackets sector, reflecting a broader shift towards environmentally conscious sourcing practices. International B2B buyers are increasingly prioritizing suppliers that adhere to sustainable practices, which not only mitigates environmental impacts but also enhances brand reputation.
The environmental footprint of hardware manufacturing can be significant, particularly in terms of carbon emissions and waste. Buyers are encouraged to seek out suppliers who utilize recycled materials or offer ‘green’ certifications, such as LEED (Leadership in Energy and Environmental Design) or ISO 14001, which signify adherence to rigorous environmental management standards.
Moreover, the trend towards sustainable sourcing is further amplified by consumer demand for ethically produced products. B2B buyers can leverage this trend by ensuring their supply chains are transparent and ethical, fostering trust with end consumers and differentiating their offerings in competitive markets.
What Is the Historical Context of Hardware Brackets in B2B Markets?
The evolution of hardware brackets can be traced back to the industrial revolution, when the need for structural support in buildings and machinery became paramount. Initially made from wood, brackets transitioned to metal as manufacturing processes advanced, allowing for stronger and more durable designs.
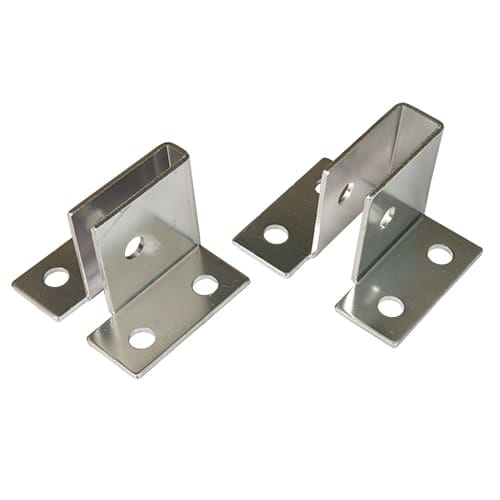
A stock image related to hardware brackets.
Over the decades, the hardware brackets sector has diversified, with innovations leading to a wide range of materials—such as stainless steel, galvanized steel, and aluminum—each offering unique benefits. This historical context underscores the sector’s adaptability and responsiveness to both technological advancements and market demands, which remains crucial for B2B buyers aiming to source reliable and innovative hardware solutions today.
By understanding these dynamics, international buyers can better navigate the complexities of the hardware brackets market, aligning their sourcing strategies with current trends and future opportunities.
Frequently Asked Questions (FAQs) for B2B Buyers of hardware brackets
-
How do I solve issues with sourcing high-quality hardware brackets?
To address sourcing challenges, start by identifying reliable suppliers with proven track records. Utilize online platforms such as Alibaba, Global Sources, or trade directories specific to your region. Request samples to evaluate quality, and consider suppliers that adhere to international standards like ISO certifications. Additionally, attending trade shows or industry expos can connect you with manufacturers and distributors, allowing for direct communication and negotiation. -
What is the best material for hardware brackets in different applications?
The best material for hardware brackets depends on the intended use. For heavy-duty applications, galvanized steel or stainless steel offers high strength and corrosion resistance, making them ideal for outdoor or industrial use. For decorative purposes, cast iron or aluminum can provide aesthetic appeal while still maintaining functionality. Always consider the environment in which the brackets will be used to ensure longevity and performance. -
How can I customize hardware brackets for my specific needs?
Most manufacturers offer customization options for hardware brackets, including size, finish, and load capacity. When discussing customization, provide detailed specifications and requirements to your supplier. Consider factors such as the intended load, installation type, and environmental conditions. Engaging a supplier with experience in custom fabrication can yield better results and ensure that the brackets meet your exact needs. -
What are the typical minimum order quantities (MOQ) for hardware brackets?
Minimum order quantities can vary significantly based on the supplier and the type of brackets. Generally, for standard products, MOQs may range from 100 to 500 units, while custom brackets might require larger orders. Always clarify MOQ with your supplier upfront, as some may be flexible depending on your relationship or potential for future orders. This is particularly important for international transactions where shipping costs can impact overall expenses. -
What payment terms should I expect when purchasing hardware brackets internationally?
Payment terms can vary widely among suppliers, but common practices include upfront deposits (often 30-50%) with the balance due upon shipment or delivery. Some suppliers may offer letters of credit or payment through escrow services for larger orders, ensuring both parties’ security. Always negotiate terms that protect your interests, particularly for international transactions where additional risks may be involved. -
How do I ensure quality assurance for hardware brackets?
Quality assurance can be managed through several strategies. Request certifications from suppliers that demonstrate compliance with international quality standards. Conduct factory audits or quality inspections before shipment, which can be arranged through third-party inspection services. Additionally, consider implementing a quality control protocol that includes periodic checks upon receipt of goods to ensure they meet your specifications. -
What logistics considerations should I keep in mind for importing hardware brackets?
When importing hardware brackets, consider shipping methods, lead times, and customs regulations. Engage a freight forwarder familiar with your destination country to navigate logistics efficiently. Ensure that all documentation is prepared, including invoices, packing lists, and certificates of origin, to avoid customs delays. Additionally, factor in potential tariffs or duties that may apply, as these can significantly affect your overall costs. -
How can I vet suppliers for hardware brackets to ensure reliability?
To vet suppliers, research their reputation through online reviews and ratings, and seek references from other clients. Verify their business licenses, certifications, and production capabilities. Engage in direct communication to assess responsiveness and professionalism. If possible, visit the supplier’s facility or request a video tour to observe their operations firsthand. Establishing a relationship based on transparency and trust is crucial for long-term partnerships.
Important Disclaimer & Terms of Use
⚠️ Important Disclaimer
The information provided in this guide, including content regarding manufacturers, technical specifications, and market analysis, is for informational and educational purposes only. It does not constitute professional procurement advice, financial advice, or legal advice.
While we have made every effort to ensure the accuracy and timeliness of the information, we are not responsible for any errors, omissions, or outdated information. Market conditions, company details, and technical standards are subject to change.
B2B buyers must conduct their own independent and thorough due diligence before making any purchasing decisions. This includes contacting suppliers directly, verifying certifications, requesting samples, and seeking professional consultation. The risk of relying on any information in this guide is borne solely by the reader.
Strategic Sourcing Conclusion and Outlook for hardware brackets
In today’s global marketplace, the strategic sourcing of hardware brackets is essential for B2B buyers aiming to optimize their supply chains and enhance project efficiency. By evaluating suppliers based on material quality, pricing structures, and delivery capabilities, businesses can secure high-performance products that meet their specific needs. For buyers in Africa, South America, the Middle East, and Europe, leveraging local manufacturers can not only reduce costs but also foster sustainable partnerships that benefit both parties.
What are the key factors to consider in sourcing hardware brackets? When making purchasing decisions, it’s crucial to assess the versatility of bracket designs, the availability of bulk pricing, and the supplier’s commitment to quality assurance. Additionally, understanding regional regulations and market trends can provide a competitive edge.
Looking ahead, the demand for innovative hardware solutions will only increase. International buyers should embrace technological advancements and explore digital platforms to enhance their sourcing strategies. By staying informed and proactive, businesses can navigate the evolving landscape of hardware procurement with confidence. Engage with reliable suppliers and invest in strategic relationships to ensure your projects are supported by the best hardware solutions available.