Discover Cost-Effective Sheets of Fibreglass Solutions (2025)
Introduction: Navigating the Global Market for sheets of fibreglass
Navigating the complexities of sourcing sheets of fiberglass can be a significant challenge for international B2B buyers, particularly those operating in diverse markets such as Africa, South America, the Middle East, and Europe. With a multitude of applications ranging from electrical insulation to structural components in various industries, understanding the nuances of fiberglass materials is crucial. This comprehensive guide delves into the different types of fiberglass sheets available, their specific applications, and essential factors for vetting suppliers.
By providing insights into cost considerations and best practices for procurement, this guide equips B2B buyers with the knowledge needed to make informed purchasing decisions. Whether you’re looking for G10/FR4 fiberglass sheets for industrial use or specialized options for unique applications, this resource will help streamline the sourcing process and mitigate risks associated with quality and supplier reliability.
As the global market for fiberglass continues to evolve, staying informed about the latest trends and technological advancements is vital. This guide not only highlights key product specifications and performance characteristics but also addresses the critical aspects of supplier relationships, ensuring that buyers can confidently navigate the marketplace and secure high-quality materials that meet their operational needs.
Understanding sheets of fibreglass Types and Variations
Type Name | Key Distinguishing Features | Primary B2B Applications | Brief Pros & Cons for Buyers |
---|---|---|---|
G10/FR4 Fiberglass Sheets | High strength, epoxy resin reinforcement, fire retardant | Aerospace, electronics, industrial applications | Pros: Excellent mechanical strength, good dielectric properties. Cons: Limited cosmetic use due to surface blemishes. |
Smooth Fiberglass Sheets | Smooth finish, available in various colors, light-weight | Construction, automotive, signage | Pros: Aesthetic appeal, customizable sizes. Cons: May require additional coatings for UV resistance. |
Honeycomb Fiberglass Panels | Lightweight, high strength-to-weight ratio, thermal insulation | Marine, automotive, aerospace | Pros: Space-saving design, excellent energy efficiency. Cons: More expensive than solid sheets. |
Porous Teflon Coated Fiberglass | Non-stick surface, chemical resistance, high durability | Food processing, medical devices | Pros: Easy to clean, withstands harsh chemicals. Cons: Higher cost compared to standard fiberglass sheets. |
Woven Fiberglass Fabric | Flexible, available in various weaves, high tensile strength | Sports equipment, industrial applications | Pros: Versatile, can be molded into complex shapes. Cons: Requires additional resin for structural applications. |
What Are G10/FR4 Fiberglass Sheets and Their Uses?
G10/FR4 fiberglass sheets are known for their high strength, typically reinforced with epoxy resin, making them ideal for demanding applications in aerospace, electronics, and industrial sectors. Their fire retardant properties enhance safety in electrical and mechanical environments. When purchasing, buyers should consider the thickness options, as they range from .005” to .030”, and the potential for surface blemishes, which may not affect performance but can influence aesthetic requirements.
How Do Smooth Fiberglass Sheets Differ from Other Types?
Smooth fiberglass sheets are characterized by their clean, smooth finish and are available in various colors. This type is particularly popular in construction, automotive, and signage applications due to its aesthetic versatility. B2B buyers should weigh the benefits of customization against the potential need for additional UV-resistant coatings, especially for outdoor applications, to ensure longevity and durability.
What Are the Benefits of Honeycomb Fiberglass Panels?
Honeycomb fiberglass panels are designed for lightweight strength and thermal insulation, making them suitable for marine, automotive, and aerospace industries. Their unique structure offers excellent energy efficiency, which can be a significant advantage in cost-sensitive projects. However, buyers should be aware that these panels can be more expensive than traditional solid sheets, so budget considerations are essential.
Why Choose Porous Teflon Coated Fiberglass?
Porous Teflon coated fiberglass sheets are noted for their non-stick properties and resistance to chemicals, making them ideal for food processing and medical device applications. They are easy to clean and can endure harsh conditions, which is a considerable advantage for industries where hygiene is paramount. However, the cost of these specialized sheets may be higher than standard fiberglass options, necessitating a careful evaluation of budget constraints.
What Makes Woven Fiberglass Fabric a Versatile Option?
Woven fiberglass fabric is flexible and available in various weaves, providing high tensile strength suitable for sports equipment and industrial applications. Its versatility allows it to be molded into complex shapes, making it a preferred choice for custom projects. Buyers should note that while it requires additional resin for structural applications, its adaptability can lead to innovative solutions in product design.
Key Industrial Applications of sheets of fibreglass
Industry/Sector | Specific Application of sheets of fibreglass | Value/Benefit for the Business | Key Sourcing Considerations for this Application |
---|---|---|---|
Aerospace | Aircraft interior components and structural parts | Lightweight yet durable, reducing fuel consumption | Certification standards, weight specifications, fire resistance |
Electrical & Electronics | Insulating panels and circuit board substrates | Excellent electrical insulation properties | Dielectric strength, thermal stability, custom thickness options |
Construction & Infrastructure | Wall panels and roofing materials | High resistance to moisture and chemicals | Local climate conditions, fire ratings, and weight restrictions |
Automotive | Body panels and structural components | Enhanced strength-to-weight ratio, cost-effectiveness | Compliance with automotive standards, surface finish requirements |
Marine | Boat hulls and interior components | Corrosion resistance and durability in harsh environments | Saltwater resistance, weight considerations, and custom fabrication options |
How are Fibreglass Sheets Used in Aerospace Applications?
In the aerospace sector, sheets of fiberglass are crucial for manufacturing lightweight yet robust components, such as interior panels and structural parts. These materials help in reducing the overall weight of the aircraft, thereby improving fuel efficiency and performance. International buyers in this industry must consider certification requirements, such as FAA regulations, as well as specific weight and fire resistance standards. Working with suppliers who can provide bespoke solutions that meet these rigorous standards is essential.
What Role Do Fibreglass Sheets Play in Electrical and Electronics Industries?
Fibreglass sheets are widely used in electrical and electronics applications, particularly as insulating panels and substrates for circuit boards. Their excellent electrical insulation properties make them ideal for preventing short circuits and ensuring the reliability of electronic devices. B2B buyers from regions like Africa and South America should focus on sourcing sheets with high dielectric strength and thermal stability, as well as options for custom thickness to suit their specific applications.
How are Fibreglass Sheets Utilized in Construction and Infrastructure?
In construction, fibreglass sheets serve as effective wall panels and roofing materials due to their high resistance to moisture and chemical exposure. These properties make them suitable for both residential and commercial buildings, especially in humid or industrial environments. For international buyers, it is vital to consider local climate conditions and ensure that the selected fibreglass sheets comply with fire ratings and structural weight restrictions to guarantee safety and durability.
How Do Automotive Manufacturers Benefit from Fibreglass Sheets?
Automotive manufacturers leverage fibreglass sheets for body panels and structural components, capitalizing on their enhanced strength-to-weight ratio. This material not only contributes to vehicle performance but also offers cost-effectiveness in production. When sourcing fibreglass sheets, companies must ensure compliance with automotive industry standards, particularly regarding surface finish and durability, to meet consumer expectations and regulatory requirements.
Why are Fibreglass Sheets Important in Marine Applications?
In the marine industry, fibreglass sheets are essential for constructing boat hulls and interior components due to their superior corrosion resistance and durability in harsh aquatic environments. These properties help extend the lifespan of marine vessels while minimizing maintenance costs. Buyers from regions with active maritime industries should prioritize sourcing materials that are specifically designed for saltwater resistance, keeping in mind weight considerations and the need for custom fabrication options to meet specific design requirements.
3 Common User Pain Points for ‘sheets of fibreglass’ & Their Solutions
Scenario 1: Sourcing High-Quality Fiberglass Sheets for Specialized Applications
The Problem:
International B2B buyers often face the challenge of sourcing high-quality fiberglass sheets that meet specific application requirements. For instance, buyers from the aerospace or automotive industries need sheets that not only exhibit high mechanical strength but also comply with stringent safety and regulatory standards. Unfortunately, the market is saturated with low-quality products that can lead to project delays, increased costs, and compromised safety. This situation can be particularly frustrating for buyers in regions like Africa and South America, where access to reliable suppliers may be limited.
The Solution:
To overcome these sourcing challenges, buyers should focus on establishing partnerships with reputable manufacturers known for their quality assurance processes. Conduct thorough research to identify suppliers who provide detailed technical specifications and certifications for their products, such as ISO compliance or UL ratings. Additionally, consider using sample orders to evaluate the quality before committing to larger purchases. Engaging with suppliers who offer customization options can also help ensure that the sheets meet specific dimensions and properties required for your applications. This proactive approach not only mitigates risks but also builds long-term relationships that enhance supply chain reliability.
Scenario 2: Managing Costs While Ensuring Quality in Fiberglass Sheets
The Problem:
Cost management is a significant concern for B2B buyers, especially when dealing with materials like fiberglass sheets that can vary widely in price. Buyers often struggle to balance the need for high-quality products with budget constraints. This is especially true for businesses in developing regions where margins are tight, and the competition is fierce. The challenge lies in selecting a product that offers durability and performance without incurring excessive costs.
The Solution:
To effectively manage costs, buyers should adopt a value-based sourcing strategy. This involves analyzing not just the purchase price, but also the total cost of ownership, which includes factors like durability, maintenance, and potential downtime. Consider investing in higher-quality sheets that may have a higher upfront cost but provide better performance and longevity, reducing the need for frequent replacements. Additionally, negotiating long-term contracts with suppliers can lead to favorable pricing terms. Utilizing technology such as inventory management systems can help track usage and optimize ordering processes, ensuring that you are not overstocking or understocking materials.
Scenario 3: Ensuring Compliance with Regional Standards and Regulations
The Problem:
B2B buyers, particularly in Europe and the Middle East, must navigate a complex landscape of regional standards and regulations when sourcing fiberglass sheets. Each region may have specific fire safety, environmental, and performance standards that products must meet. Failing to comply can result in legal ramifications, project delays, and increased costs, which can severely impact business operations.
The Solution:
To address compliance issues, buyers should conduct a thorough assessment of the regulations applicable in their region before purchasing fiberglass sheets. Engage with local industry experts or consultants who can provide insights into the specific standards that must be adhered to. When selecting suppliers, prioritize those who are transparent about their compliance with relevant standards and provide necessary documentation. Regularly review and update your knowledge of regulatory changes to ensure ongoing compliance. Furthermore, consider joining industry associations or forums that focus on fiberglass applications to stay informed about best practices and changes in regulations. This proactive stance will safeguard your business against compliance risks and enhance your reputation in the market.
Strategic Material Selection Guide for sheets of fibreglass
When selecting fiberglass sheets for various applications, understanding the material properties and their implications is crucial for international B2B buyers. This guide analyzes four common materials used in fiberglass sheets, focusing on their key properties, advantages, disadvantages, and specific considerations for buyers from Africa, South America, the Middle East, and Europe.
What Are the Key Properties of G10/FR4 Fiberglass Sheets?
G10/FR4 fiberglass sheets are made from fiberglass prepreg reinforced with epoxy resin, providing high strength and excellent electrical insulating properties. These sheets can withstand temperatures up to 285°F and offer flame resistance rated at 94V-0. Their compressive strength is impressive, reaching up to 60,000 psi, making them suitable for demanding applications.
Pros: The G10/FR4 sheets are durable, lightweight, and exhibit excellent dimensional stability. They are also resistant to moisture and various chemicals, ensuring longevity in harsh environments.
Cons: The manufacturing process can be complex and more expensive compared to other materials. Additionally, they are not suitable for cosmetic applications due to potential surface blemishes.
Impact on Application: G10/FR4 is ideal for electrical insulation and structural applications where high mechanical strength is required, such as in aerospace and industrial machinery.
Considerations for International Buyers: Compliance with standards like ASTM D578 is essential. Buyers should also ensure that suppliers can provide documentation for fire retardancy and electrical properties.
How Does Norplex-Micarta® Compare in Performance?
Norplex-Micarta® sheets are known for their high mechanical strength and excellent electrical insulation. They are often used in applications requiring durability and resistance to chemicals and moisture. These sheets can handle temperatures up to 300°F and have a compressive strength of around 50,000 psi.
Pros: The material offers a good balance of strength and weight, making it versatile for various applications, including automotive and industrial sectors.
Cons: The cost can be higher than standard fiberglass sheets, and the availability may vary by region, particularly in developing markets.
Impact on Application: Norplex-Micarta® is particularly suited for environments where exposure to chemicals and moisture is a concern, such as in manufacturing and processing industries.
Considerations for International Buyers: Buyers should verify compliance with international standards and consider the availability of the material in their region to avoid delays.
What Are the Benefits of Using Smooth Fiberglass (FRP) Sheets?
Smooth fiberglass (FRP) sheets are characterized by their smooth surface finish and are often used in applications requiring aesthetic appeal. They are resistant to corrosion and can withstand temperatures up to 200°F.
Pros: These sheets are lightweight, easy to clean, and provide a visually appealing finish, making them suitable for consumer-facing applications.
Cons: While they are durable, they may not offer the same mechanical strength as G10/FR4 or Norplex-Micarta®. Additionally, they can be more susceptible to UV degradation if not treated.
Impact on Application: Smooth fiberglass sheets are commonly used in construction and signage, where appearance is as important as functionality.
Considerations for International Buyers: Buyers should ensure that the sheets meet local building codes and standards, especially in regions with stringent regulations.
How Do Custom Fiberglass Sheets Enhance Performance?
Custom fiberglass sheets can be tailored to specific requirements, including thickness, resin type, and surface finish. This adaptability allows for enhanced performance in various applications.
Pros: Custom sheets can be designed to meet unique specifications, improving performance in targeted applications such as aerospace or specialized industrial uses.
Cons: The customization process can lead to higher costs and longer lead times, which may not be feasible for all projects.
Impact on Application: Custom fiberglass sheets are ideal for specialized applications where standard options do not meet the performance criteria.
Considerations for International Buyers: It’s essential to work with manufacturers who can provide certifications for custom materials and ensure compliance with international standards.
Summary Table of Fiberglass Sheet Materials
Material | Typical Use Case for sheets of fibreglass | Key Advantage | Key Disadvantage/Limitation | Relative Cost (Low/Med/High) |
---|---|---|---|---|
G10/FR4 | Electrical insulation, industrial machinery | High strength and durability | Higher manufacturing complexity | High |
Norplex-Micarta® | Automotive, industrial applications | Excellent chemical resistance | Higher cost and variable availability | High |
Smooth Fiberglass (FRP) | Construction, signage | Aesthetic appeal and easy maintenance | Lower mechanical strength | Medium |
Custom Fiberglass Sheets | Specialized industrial applications | Tailored performance to specific needs | Higher costs and longer lead times | High |
This strategic material selection guide provides valuable insights for B2B buyers seeking to make informed decisions regarding fiberglass sheets. Understanding the properties and implications of each material will aid in selecting the right solution for specific applications.
In-depth Look: Manufacturing Processes and Quality Assurance for sheets of fibreglass
What Are the Key Stages in the Manufacturing Process of Fiberglass Sheets?
The manufacturing process for fiberglass sheets typically involves several crucial stages: material preparation, forming, assembly, and finishing. Each stage plays a vital role in ensuring that the final product meets the required specifications and quality standards.
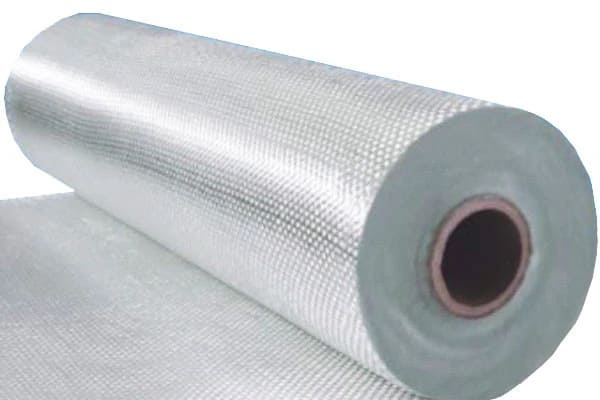
A stock image related to sheets of fibreglass.
-
Material Preparation
The primary materials used in fiberglass sheets include fiberglass fabric and epoxy resin. The preparation begins with the careful selection of high-quality fiberglass fibers, which are then layered and saturated with the resin. This process may involve the use of prepreg materials, which are pre-impregnated with resin to ensure consistent quality and reduced waste. -
Forming
In this stage, the prepared materials are shaped into sheets. Techniques such as autoclave curing are commonly employed to achieve a uniform thickness and remove any air bubbles that could compromise the structural integrity of the sheets. Autoclave curing involves heating the materials under pressure, ensuring that the resin cures properly and that the sheets are flat and lightweight. -
Assembly
For products requiring multiple layers or components, the assembly process is critical. This may involve laminating additional layers of fiberglass or integrating other materials for enhanced properties. The assembly stage must ensure that all components are aligned accurately to maintain the strength and functionality of the final product. -
Finishing
The finishing stage includes cutting the sheets to size, applying surface treatments, and ensuring smooth edges. Quality control checks are performed at this stage to ensure that all specifications are met, including thickness, flatness, and surface finish.
How Is Quality Assurance Implemented in Fiberglass Sheet Manufacturing?
Quality assurance is essential in fiberglass sheet manufacturing to ensure that the products meet international standards and customer expectations. Here are key components of the quality assurance process:
-
Adherence to International Standards
Manufacturers often comply with international standards such as ISO 9001, which outlines requirements for a quality management system. Compliance with these standards demonstrates a commitment to quality and consistency, which is crucial for B2B buyers in different markets. -
Industry-Specific Certifications
Depending on the application of the fiberglass sheets, additional certifications may be required. For example, products intended for electrical applications may need CE certification, while those used in the oil and gas sector might require API certification. Understanding these certifications can help B2B buyers ensure that they are sourcing compliant materials. -
Quality Control Checkpoints
The quality control process typically includes several checkpoints:
– Incoming Quality Control (IQC): This step involves inspecting raw materials upon arrival to ensure they meet specified standards.
– In-Process Quality Control (IPQC): Throughout the manufacturing process, continuous monitoring is conducted to detect any deviations from quality standards.
– Final Quality Control (FQC): Before shipment, finished products undergo rigorous testing to confirm they meet all specified requirements.
What Common Testing Methods Are Used for Fiberglass Sheets?
Testing methods are critical in verifying the performance and safety of fiberglass sheets. Common tests include:
- Mechanical Testing: This involves assessing tensile strength, flexural strength, and impact resistance to ensure the sheets can withstand operational stresses.
- Electrical Testing: For sheets used in electrical applications, dielectric strength and insulation resistance tests are conducted to ensure safety and performance.
- Chemical Resistance Testing: This checks the sheets’ ability to withstand exposure to various chemicals, crucial for applications in industrial environments.
How Can B2B Buyers Verify Supplier Quality Control?
For international B2B buyers, particularly from regions like Africa, South America, the Middle East, and Europe, verifying supplier quality control is essential. Here are actionable steps to take:
-
Supplier Audits
Conducting audits of potential suppliers can provide insight into their manufacturing processes and quality control measures. An on-site visit allows buyers to assess the facilities, equipment, and practices in place. -
Requesting Quality Reports
Buyers should request detailed quality reports, including results from mechanical and chemical testing. This documentation should demonstrate compliance with relevant standards and certifications. -
Third-Party Inspections
Engaging third-party inspection services can provide an unbiased assessment of a supplier’s quality control practices. These inspections can be performed at various stages of production to ensure compliance with agreed specifications.
What Are the Nuances of Quality Control and Certification for International B2B Buyers?
Understanding the nuances of quality control and certification is crucial for international B2B buyers. Different regions may have varying standards and expectations regarding product quality. For instance:
- Regional Compliance Requirements: Buyers must be aware of specific regulations in their home markets. For example, products exported to the European Union must meet stringent CE marking requirements, while those in the Middle East may need to comply with local certification bodies.
- Documentation and Traceability: Buyers should ensure that suppliers provide thorough documentation, including material safety data sheets (MSDS), certificates of compliance, and production batch records. This traceability is vital for addressing any issues that may arise post-purchase.
- Cultural and Business Practices: Understanding the cultural and business practices in different regions can help buyers navigate negotiations and establish trust with suppliers. This is particularly important in regions such as Africa and South America, where local practices may differ significantly from those in Europe or the Middle East.
By focusing on these aspects, international B2B buyers can make informed decisions when sourcing fiberglass sheets, ensuring they partner with reliable manufacturers who prioritize quality and compliance.
Practical Sourcing Guide: A Step-by-Step Checklist for ‘sheets of fibreglass’
Introduction
Sourcing sheets of fiberglass for your business requires careful consideration and a structured approach. This guide provides a practical checklist designed to help international B2B buyers—particularly those from Africa, South America, the Middle East, and Europe—navigate the complexities of procurement. By following these steps, you can ensure that you select the right products and suppliers for your specific needs.
Step 1: Define Your Technical Specifications
Before initiating your search, clearly outline the technical specifications of the fiberglass sheets you require. This includes factors such as thickness, resin type (e.g., epoxy), and desired mechanical properties.
- Why It Matters: Having precise specifications helps streamline the sourcing process and ensures that suppliers understand your needs, reducing the likelihood of miscommunication.
- What to Look For: Consider the application of the sheets, whether for electrical insulation, structural support, or aesthetic purposes, as different specifications will suit different applications.
Step 2: Research Potential Suppliers
Conduct thorough research to identify potential suppliers. Look for manufacturers and distributors who specialize in fiberglass sheets and have a proven track record.
- Why It Matters: A well-researched supplier is more likely to meet your quality and delivery expectations.
- What to Look For: Check their online presence, customer reviews, and industry certifications. Engage with suppliers from regions you trust or those that have experience in your target market.
Step 3: Evaluate Supplier Certifications
Verify the certifications and compliance standards of potential suppliers. Look for certifications like ISO 9001, which indicates a commitment to quality management systems.
- Why It Matters: Certifications can be a strong indicator of a supplier’s reliability and the quality of their products.
- What to Look For: Ask for documentation proving their adherence to industry standards, especially if your application demands high safety or performance levels.
Step 4: Request Samples for Testing
Before making a bulk purchase, request samples of the fiberglass sheets. Testing samples allows you to assess their quality, performance, and suitability for your specific application.
- Why It Matters: Physical samples help you verify claims made by suppliers and ensure that the product meets your expectations.
- What to Look For: Examine the samples for consistency in thickness, surface finish, and any defects that may affect performance.
Step 5: Compare Pricing and Terms
Once you have identified potential suppliers, compare their pricing structures and payment terms. Consider the total cost of ownership, including shipping, taxes, and any potential tariffs.
- Why It Matters: Understanding the full financial implications can help you make a more informed decision.
- What to Look For: Negotiate terms that align with your budget while ensuring you are not compromising on quality.
Step 6: Establish Communication Channels
Effective communication with your chosen supplier is crucial for a successful partnership. Establish clear channels for ongoing communication regarding order status, product updates, and any issues that may arise.
- Why It Matters: Clear communication helps build trust and ensures that any concerns are addressed promptly.
- What to Look For: Choose suppliers who are responsive and willing to engage in regular updates throughout the sourcing process.
Step 7: Finalize Your Order and Monitor Delivery
Once you have selected a supplier, finalize your order with a clear purchase agreement that outlines all terms, including delivery schedules.
- Why It Matters: A formal agreement protects both parties and ensures clarity on expectations.
- What to Look For: Monitor the delivery process and maintain contact with your supplier to ensure that your order is fulfilled as agreed.
Comprehensive Cost and Pricing Analysis for sheets of fibreglass Sourcing
What Are the Key Cost Components in Fiberglass Sheets Sourcing?
When sourcing fiberglass sheets, understanding the cost structure is crucial for international B2B buyers. The primary cost components include:
-
Materials: The core material for fiberglass sheets, such as G10/FR4 or other epoxy resin formulations, constitutes a significant portion of the total cost. Prices can vary based on quality and sourcing location. For instance, premium-grade materials may yield better performance but at a higher price point.
-
Labor: Labor costs are influenced by the region of production. Regions with lower labor costs, such as certain parts of Africa or South America, might offer competitive pricing but could compromise on quality if not managed effectively.
-
Manufacturing Overhead: This includes costs associated with factory operations, maintenance, and utilities. Efficient manufacturing processes can reduce overheads, allowing suppliers to pass on savings to buyers.
-
Tooling: Custom orders may require specialized tooling, which adds to the initial cost. For high-volume orders, these costs can be amortized over the production run, leading to lower per-unit pricing.
-
Quality Control (QC): Implementing robust QC processes ensures that the fiberglass sheets meet the required specifications and certifications. This may increase upfront costs but can significantly reduce long-term expenses related to returns or quality issues.
-
Logistics: Shipping and handling costs vary based on the distance between the supplier and the buyer, as well as the chosen Incoterms. International shipping can add considerable costs, particularly for bulky items like fiberglass sheets.
-
Margin: Suppliers typically add a margin to cover their costs and generate profit. This margin can vary widely based on market conditions and competitive pressures.
What Influences the Pricing of Fiberglass Sheets?
Pricing for fiberglass sheets is influenced by several factors:
-
Volume/MOQ (Minimum Order Quantity): Larger orders often attract discounts. Negotiating favorable terms based on projected volumes can lead to significant savings.
-
Specifications and Customization: Custom specifications such as thickness, finish, and material type can impact pricing. Standard products are generally more cost-effective than customized solutions.
-
Quality and Certifications: Higher quality standards and certifications (e.g., fire retardant ratings, chemical resistance) may come at a premium. Buyers should assess whether these certifications are essential for their applications.
-
Supplier Factors: The reputation and reliability of the supplier can also influence pricing. Established suppliers may offer higher prices but provide added value through superior service and product reliability.
-
Incoterms: Understanding the chosen Incoterms is vital for managing shipping costs and responsibilities. Terms like FOB (Free on Board) or CIF (Cost, Insurance, and Freight) can significantly affect the overall cost structure.
How Can B2B Buyers Negotiate Better Prices for Fiberglass Sheets?
Negotiating effectively is key to achieving cost efficiencies in fiberglass sheet procurement. Here are some actionable tips:
-
Understand Total Cost of Ownership (TCO): Evaluate not just the purchase price but also consider logistics, potential quality issues, and lifecycle costs. This comprehensive view can help justify higher upfront costs for superior products.
-
Leverage Volume Discounts: If your business can commit to larger orders, use this leverage in negotiations. Suppliers are often willing to offer better pricing for bulk purchases.
-
Build Long-Term Relationships: Establishing a long-term partnership with suppliers can lead to preferential pricing, better terms, and priority in production schedules.
-
Be Open to Alternative Suppliers: Don’t limit your search to local suppliers. Exploring options from different regions, such as Africa or South America, can uncover more competitive pricing and unique product offerings.
-
Clarify Specifications Upfront: Clearly outline your specifications and requirements to avoid misunderstandings that could lead to costly changes later in the production process.
Conclusion
Understanding the cost components and pricing influencers associated with fiberglass sheets is essential for international B2B buyers. By leveraging this knowledge and employing strategic negotiation techniques, buyers can secure favorable terms and ensure they are making informed purchasing decisions. Always remember to request indicative prices and be prepared for fluctuations based on market conditions and supplier capabilities.
Alternatives Analysis: Comparing sheets of fibreglass With Other Solutions
When evaluating materials for industrial applications, it is essential to consider various alternatives to sheets of fiberglass. This comparison not only highlights the strengths and weaknesses of fiberglass but also provides B2B buyers with a broader perspective on available options. In this analysis, we will compare sheets of fiberglass with two viable alternatives: composite aluminum panels and polycarbonate sheets.
Comparison Table of Fiberglass Sheets and Alternatives
Comparison Aspect | Sheets of Fiberglass | Composite Aluminum Panels | Polycarbonate Sheets |
---|---|---|---|
Performance | High mechanical strength, excellent chemical resistance | Moderate strength, good weather resistance | High impact resistance, lightweight |
Cost | $44.00 – $140.00 per sheet | $70.00 – $200.00 per panel | $30.00 – $120.00 per sheet |
Ease of Implementation | Requires specialized tools for cutting and installation | Easy to install, can be cut with standard tools | Can be easily cut and shaped, lightweight |
Maintenance | Low maintenance, resistant to moisture and chemicals | Moderate maintenance, may require occasional cleaning | Low maintenance, UV resistant |
Best Use Case | Electrical insulation, industrial applications | Facades, roofing, signage | Greenhouses, safety glazing, skylights |
What Are the Pros and Cons of Composite Aluminum Panels?
Composite aluminum panels consist of two thin layers of aluminum enclosing a non-aluminum core. They offer a unique combination of durability and aesthetics, making them suitable for building facades and signage.
Pros:
– Weather Resistance: These panels are resistant to corrosion and can withstand extreme weather conditions, making them ideal for outdoor applications.
– Aesthetic Flexibility: They can be coated in various colors and finishes, allowing for creative design possibilities.
Cons:
– Moderate Strength: While they are durable, they do not match the mechanical strength of fiberglass sheets, which could be a disadvantage in heavy-duty applications.
– Cost: They are generally more expensive than fiberglass, which may affect budget-conscious projects.
How Do Polycarbonate Sheets Compare?
Polycarbonate sheets are a transparent thermoplastic material known for their high impact resistance and lightweight nature. They are commonly used in applications where safety and visibility are paramount, such as in greenhouses and safety glazing.
Pros:
– Impact Resistance: Polycarbonate sheets are nearly unbreakable, offering superior safety features compared to fiberglass.
– Lightweight: Their low weight simplifies handling and installation, reducing labor costs.
Cons:
– UV Degradation: Although many polycarbonate sheets come with UV protection, prolonged exposure can lead to yellowing and loss of clarity over time.
– Lower Chemical Resistance: Compared to fiberglass, polycarbonate is less resistant to harsh chemicals, which may limit its use in certain industrial environments.
How Should B2B Buyers Choose the Right Solution?
When selecting the appropriate material for a project, B2B buyers should consider specific project requirements, including performance needs, budget constraints, and application environments. Fiberglass sheets provide excellent strength and chemical resistance, making them ideal for industrial applications. In contrast, if aesthetics and weather resistance are a priority, composite aluminum panels may be the better choice. Finally, for applications that require transparency and impact resistance, polycarbonate sheets could be the most effective solution.
In conclusion, a thorough understanding of the advantages and limitations of each material will help buyers make informed decisions that align with their project goals and operational needs.
Essential Technical Properties and Trade Terminology for sheets of fibreglass
What are the Key Technical Properties of Fiberglass Sheets?
When evaluating fiberglass sheets for procurement, understanding their essential technical properties is crucial for making informed purchasing decisions. Here are some of the most important specifications:
1. Material Grade (G10/FR4)
Material grades like G10 and FR4 indicate the type and quality of the fiberglass laminate. G10 is a high-pressure fiberglass laminate made with epoxy resin, providing excellent mechanical strength and thermal stability. FR4 is similar but specifically designed to be flame-retardant. For B2B buyers, selecting the correct grade is vital for applications requiring specific performance metrics, especially in industries like aerospace, automotive, and electronics.
2. Thickness Tolerance
Thickness tolerance is a critical specification that defines the acceptable variation in the thickness of the sheets. Common tolerances might range from +/- 0.002″ to +/- 0.006″. This specification is crucial for ensuring that the sheets fit seamlessly into existing assemblies or manufacturing processes. Inconsistent thickness can lead to complications in production, increased costs, and potential product failure.
3. Tensile and Compressive Strength
These properties measure how much force the fiberglass sheets can withstand before failing. For instance, a tensile strength of 40,000 psi (pounds per square inch) in lengthwise direction indicates high durability. Compressive strength values are equally important, especially in applications where the material will be subject to compressive loads. Understanding these strengths helps B2B buyers ensure that the selected sheets will meet performance requirements without risk of failure.
4. Coefficient of Thermal Expansion (CTE)
The coefficient of thermal expansion indicates how much a material expands or contracts with temperature changes. A lower CTE signifies less dimensional change under temperature fluctuations, which is essential for applications in industries like automotive or aerospace where thermal stability is crucial. B2B buyers must consider the CTE to prevent issues related to misalignment or structural failure in high-temperature environments.
5. Chemical Resistance
Fiberglass sheets’ resistance to various chemicals is a key property, especially in industries such as chemical processing and pharmaceuticals. Understanding the chemical resistance of the chosen fiberglass material will help buyers avoid premature degradation and ensure longevity in harsh environments.
What Common Trade Terms Should B2B Buyers Know?
Familiarity with industry jargon can streamline communication and ensure smoother transactions. Here are several key terms that B2B buyers should understand:
1. OEM (Original Equipment Manufacturer)
OEM refers to a company that produces parts or equipment that may be marketed by another manufacturer. Understanding OEM relationships can help buyers identify reliable suppliers and manufacturers that can provide high-quality fiberglass sheets that meet their specific needs.
2. MOQ (Minimum Order Quantity)
MOQ is the smallest quantity of a product that a supplier is willing to sell. Knowing the MOQ is essential for budgeting and inventory planning, especially for international buyers who may face shipping and customs challenges when ordering large quantities.
3. RFQ (Request for Quotation)
An RFQ is a standard business process to invite suppliers to bid on specific products or services. It helps buyers obtain pricing and terms from multiple suppliers, facilitating better decision-making. For international buyers, issuing an RFQ can also clarify terms related to shipping, delivery timelines, and payment options.
4. Incoterms (International Commercial Terms)
Incoterms define the responsibilities of buyers and sellers in international transactions, such as shipping, insurance, and tariffs. Familiarity with these terms can help international B2B buyers navigate logistics effectively and avoid misunderstandings regarding shipping costs and responsibilities.
5. Custom Fabrication
Custom fabrication refers to the process of modifying fiberglass sheets to meet specific project requirements, such as cutting to size or adding surface treatments. Understanding this term is essential for buyers who need tailored solutions to fit unique applications or specifications.
By grasping these technical properties and trade terms, B2B buyers from Africa, South America, the Middle East, and Europe can enhance their procurement strategies for fiberglass sheets, ensuring they select the right products for their applications.
Navigating Market Dynamics and Sourcing Trends in the sheets of fibreglass Sector
What Are the Current Market Dynamics and Key Trends for Fibreglass Sheets?
The global market for fibreglass sheets is witnessing robust growth, driven by the increasing demand from various sectors such as automotive, construction, and aerospace. Key trends include the shift towards lightweight, high-strength materials that enhance energy efficiency and sustainability. The rise of advanced manufacturing technologies, like CNC machining and additive manufacturing, is enabling the customization of fibreglass sheets, allowing businesses to meet specific project requirements more effectively.
International B2B buyers from regions such as Africa, South America, the Middle East, and Europe are increasingly looking for suppliers that can provide tailored solutions. As these markets evolve, buyers are prioritizing suppliers who can demonstrate expertise in both product quality and rapid response times. Additionally, the integration of digital tools for supply chain management is becoming essential, facilitating real-time tracking and reducing lead times. This trend is particularly relevant for buyers in developing markets who seek to optimize their procurement processes.
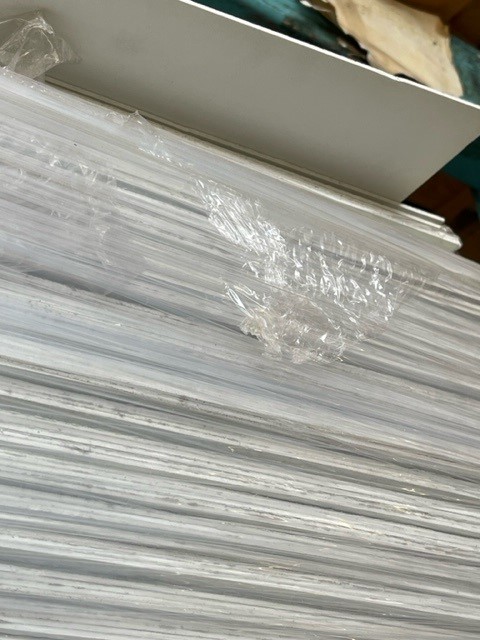
A stock image related to sheets of fibreglass.
Moreover, emerging markets are showing a growing interest in sourcing fibreglass sheets due to local infrastructure projects and industrial growth. Understanding regional differences in regulations and market needs is crucial for international buyers to navigate these dynamics successfully.
How Is Sustainability and Ethical Sourcing Shaping the Fibreglass Sheets Market?
Sustainability has emerged as a critical consideration for B2B buyers in the fibreglass sheets market. The environmental impact of materials used in manufacturing is under scrutiny, leading buyers to seek out suppliers who prioritize eco-friendly practices. This includes the use of recycled materials and processes that minimize waste and energy consumption.
Moreover, ethical sourcing is gaining traction, with businesses increasingly recognizing the importance of transparent supply chains. Buyers are looking for suppliers who can provide certifications that demonstrate adherence to environmental standards. Certifications such as ISO 14001 (Environmental Management) or specific ‘green’ labels for fibreglass materials can enhance a supplier’s credibility and appeal to conscientious buyers.
Incorporating sustainability into procurement strategies not only helps mitigate environmental risks but also aligns with the corporate social responsibility goals of many organizations. This shift is particularly important for buyers in Europe and North America, where regulatory pressures and consumer expectations are driving demand for sustainable products.
What Is the Historical Context of Fibreglass Sheets in B2B Markets?
The use of fibreglass in industrial applications dates back to the mid-20th century when it became popular for its strength-to-weight ratio and corrosion resistance. Initially, fibreglass sheets were primarily utilized in the automotive and aerospace industries. Over time, advancements in manufacturing techniques, such as autoclave curing, have improved the quality and consistency of fibreglass sheets, making them suitable for a broader range of applications.
As industries continue to evolve, the versatility of fibreglass sheets has led to their adoption in construction, marine, and even consumer goods. Today, the ongoing innovation in composite materials and manufacturing processes positions fibreglass sheets as a critical component in modern engineering solutions, further solidifying their role in the B2B marketplace.
This historical perspective provides valuable insights for international buyers, emphasizing the importance of selecting suppliers who understand the material’s evolution and can offer innovative solutions to meet current market demands.
Frequently Asked Questions (FAQs) for B2B Buyers of sheets of fibreglass
-
How do I choose the right type of fiberglass sheet for my application?
Choosing the right fiberglass sheet depends on several factors, including the intended application, environmental conditions, and required mechanical properties. For applications requiring high strength and thermal stability, G10/FR4 sheets are ideal due to their superior tensile strength and flame resistance. If moisture resistance is critical, opt for sheets with enhanced chemical resistance. Always consult technical datasheets and consider samples to evaluate performance under specific conditions. Engaging with suppliers for expert advice can also guide you in making the best choice. -
What are the key specifications to look for in fiberglass sheets?
When sourcing fiberglass sheets, consider specifications such as thickness, tensile strength, flexural strength, and thermal resistance. For instance, tensile strength should ideally be above 40,000 psi for demanding applications. Additionally, check for flame resistance ratings (like 94V-0), as safety is paramount in many industries. Understanding the resin matrix used (e.g., epoxy) and the surface finish will also impact the performance and suitability of the sheets for your project requirements. -
What customization options are available for fiberglass sheets?
Many suppliers offer customization options for fiberglass sheets, including variations in thickness, size, and surface finish. You may also request specific fiber types or resin formulations tailored to your project needs. Custom machining services, such as CNC cutting and bonding, are often available to create pieces that fit precisely into your application. Engaging with manufacturers early in the design process can ensure that your unique requirements are met efficiently. -
What is the minimum order quantity (MOQ) for fiberglass sheets?
The minimum order quantity (MOQ) for fiberglass sheets varies by supplier and can depend on the type of sheet and customization options required. Generally, MOQs can range from a few sheets to several hundred, particularly for custom orders. When sourcing internationally, consider the impact of shipping costs and import duties on small orders. It may be beneficial to consolidate orders with other buyers or negotiate with suppliers for better terms based on your project scope. -
What payment terms should I expect when sourcing fiberglass sheets internationally?
Payment terms can vary significantly among suppliers, especially in international transactions. Common options include advance payment, letter of credit, or payment upon delivery. Always clarify these terms during negotiations to avoid misunderstandings. Be aware that international transactions may involve additional considerations such as currency exchange rates, transaction fees, and potential delays in processing. It’s advisable to establish a clear agreement in writing to ensure transparency and security for both parties.
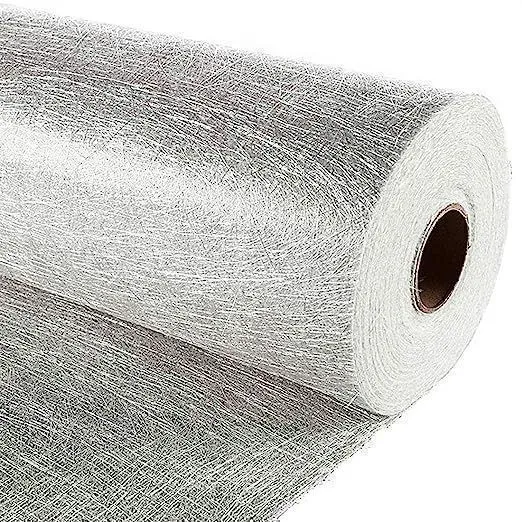
A stock image related to sheets of fibreglass.
-
How can I ensure quality assurance for fiberglass sheets?
To ensure quality assurance when sourcing fiberglass sheets, select suppliers who adhere to international quality standards, such as ISO certifications. Request detailed technical datasheets and sample products before placing bulk orders. Conducting factory audits or third-party inspections can also help verify manufacturing processes and material quality. Additionally, establishing a good communication channel with suppliers allows for addressing any quality concerns promptly, ensuring that the products meet your specifications. -
What are the best logistics practices for importing fiberglass sheets?
When importing fiberglass sheets, consider logistics practices that optimize cost and efficiency. Choose a reliable freight forwarder with experience in handling composite materials, as they can assist with customs clearance and documentation. Plan for proper packaging to protect sheets from damage during transit. Additionally, consider shipping methods based on urgency and budget, balancing between air freight for speed and ocean freight for cost-effectiveness. Tracking shipments and maintaining communication with suppliers can help mitigate delays. -
How do I vet suppliers for fiberglass sheets?
Vetting suppliers is crucial for ensuring reliable sourcing of fiberglass sheets. Start by researching potential suppliers’ reputations through reviews and testimonials from previous clients. Evaluate their certifications and compliance with industry standards. Request references and check their experience in your specific application area. Additionally, assess their production capabilities and lead times to ensure they can meet your project demands. Engaging in direct communication and discussing your requirements can also provide insights into their professionalism and reliability.
Important Disclaimer & Terms of Use
⚠️ Important Disclaimer
The information provided in this guide, including content regarding manufacturers, technical specifications, and market analysis, is for informational and educational purposes only. It does not constitute professional procurement advice, financial advice, or legal advice.
While we have made every effort to ensure the accuracy and timeliness of the information, we are not responsible for any errors, omissions, or outdated information. Market conditions, company details, and technical standards are subject to change.
B2B buyers must conduct their own independent and thorough due diligence before making any purchasing decisions. This includes contacting suppliers directly, verifying certifications, requesting samples, and seeking professional consultation. The risk of relying on any information in this guide is borne solely by the reader.
Strategic Sourcing Conclusion and Outlook for sheets of fibreglass
In the evolving landscape of fiberglass sheet sourcing, international B2B buyers from Africa, South America, the Middle East, and Europe must leverage strategic sourcing to maximize value and efficiency. The diverse applications of sheets, such as G10 and FR4 grades, highlight their versatility across industries, from automotive to construction. Understanding the technical specifications and manufacturing processes—like autoclave curing—ensures buyers select the right product for their specific needs, enhancing performance and durability.
Additionally, establishing strong relationships with suppliers who offer customization options, quick turnaround times, and comprehensive support can significantly improve supply chain resilience. As market dynamics shift, being proactive in sourcing can provide a competitive edge, especially in regions experiencing rapid industrial growth.
Looking ahead, it is crucial for buyers to stay informed about advancements in fiberglass technology and sustainability practices. By doing so, they can not only meet current demands but also anticipate future trends. Engage with reliable suppliers and explore innovative solutions to ensure your projects are equipped with the best materials available. The time to act is now—secure your supply chain and elevate your business outcomes in the fiberglass market.