Discover Cost-Effective Solutions with Packaging Machinery (2025)
Introduction: Navigating the Global Market for packaging machinery
In today’s fast-paced global marketplace, sourcing efficient packaging machinery can be a daunting challenge for B2B buyers, especially those operating in diverse regions like Africa, South America, the Middle East, and Europe. With the rise of e-commerce and heightened consumer expectations, the demand for innovative packaging solutions has surged. This guide aims to empower international buyers by providing a comprehensive overview of the various types of packaging machinery available, including bag sealers, flow wrappers, and custom systems tailored for specific industries such as food, pharmaceuticals, and e-commerce.
Navigating the complexities of supplier vetting is crucial, and this guide offers actionable insights on how to evaluate potential partners effectively. Key considerations such as cost analysis, maintenance programs, and technological advancements will be thoroughly explored. Additionally, we will delve into the latest trends in sustainable packaging, which is becoming increasingly important to consumers and businesses alike.
By leveraging the information contained in this guide, B2B buyers will be better equipped to make informed purchasing decisions that align with their operational needs and sustainability goals. Whether you are looking to enhance efficiency, reduce operational costs, or innovate your packaging processes, this resource is designed to support your journey in selecting the right packaging machinery for your business.
Understanding packaging machinery Types and Variations
Type Name | Key Distinguishing Features | Primary B2B Applications | Brief Pros & Cons for Buyers |
---|---|---|---|
Flow Wrappers | Continuous motion, servo-driven technology for high-speed packaging | Food, medical, consumer products | Pros: High efficiency, versatile; Cons: Higher initial cost. |
Bag Sealers | Various sealing methods (heat, vacuum, etc.) for different bag types | Food, e-commerce, industrial applications | Pros: Cost-effective, easy to operate; Cons: Limited to bagged products. |
Cartoners | Automates carton forming, filling, and sealing | Beverages, pharmaceuticals, cosmetics | Pros: Streamlines production; Cons: Space-intensive setup. |
Multipack Machinery | Configurable for various pack styles (clip, wrap, basket) | Beverage, food, household products | Pros: Customizable, efficient for bulk packing; Cons: Complex operation. |
Pick and Place Machines | Automated handling for precise placement and assembly | Electronics, food, consumer goods | Pros: Reduces labor costs, increases precision; Cons: Requires skilled setup and maintenance. |
What Are Flow Wrappers and Their B2B Suitability?
Flow wrappers are designed for high-speed packaging, particularly for products that require a continuous flow of packaging material. They utilize servo-driven technology to ensure precision and efficiency, making them ideal for food items, medical supplies, and consumer products. When considering flow wrappers, B2B buyers should evaluate the machine’s speed, ease of changeover for different products, and compatibility with existing production lines. While the initial investment may be higher, the long-term efficiency gains often justify the cost.
Why Choose Bag Sealers for Your Packaging Needs?
Bag sealers are essential for businesses looking to package products in bags efficiently. They come in various forms, including heat sealers and vacuum sealers, allowing for versatility across multiple industries such as food, e-commerce, and industrial applications. Buyers should consider the sealing method, bag material compatibility, and production volume requirements. While bag sealers are generally cost-effective and user-friendly, their limitation to bagged products may not suit all packaging needs.
How Do Cartoners Enhance Packaging Efficiency?
Cartoners automate the process of forming, filling, and sealing cartons, which is vital for industries like beverages, pharmaceuticals, and cosmetics. These machines can significantly streamline production lines by reducing manual labor and increasing output. B2B buyers should focus on the machine’s speed, ease of maintenance, and ability to handle various carton sizes. Although cartoners can require a substantial amount of space and upfront investment, their efficiency can lead to significant operational savings over time.
What Advantages Do Multipack Machinery Offer?
Multipack machinery is designed to create various packaging configurations, including clip-style, wrap-style, and basket-style packs. This flexibility is particularly beneficial for the beverage and food sectors, where bulk packaging is common. Buyers must assess the machine’s adaptability to different products, speed, and ease of operation. While the customization options provide significant advantages, the complexity of operation may require specialized training for staff.
Why Consider Pick and Place Machines for Precision Tasks?
Pick and place machines automate the handling of items for precise placement in packaging processes, making them ideal for industries such as electronics and food packaging. These machines enhance efficiency and accuracy, significantly reducing labor costs. When purchasing, B2B buyers should evaluate the machine’s speed, flexibility in handling different products, and maintenance requirements. Although they may require skilled operators and can be more expensive, the precision and efficiency gains often outweigh these challenges.
Key Industrial Applications of packaging machinery
Industry/Sector | Specific Application of Packaging Machinery | Value/Benefit for the Business | Key Sourcing Considerations for this Application |
---|---|---|---|
Food and Beverage | Automated Filling and Sealing Machines | Increases production speed, reduces labor costs, and ensures hygiene standards. | Compliance with food safety regulations, machine reliability, and ease of cleaning. |
Pharmaceuticals | Blister Packaging Machines | Protects product integrity, extends shelf life, and enhances branding. | Compatibility with various product sizes, regulatory compliance, and customization options. |
E-commerce and Fulfillment | Bagging and Shrink Wrapping Machines | Optimizes packaging for shipping, reduces material waste, and improves customer satisfaction. | Speed of operation, adaptability to different products, and sustainability features. |
Chemical Industry | Drum and Container Filling Equipment | Ensures accurate filling, reduces spillage, and improves safety during handling. | Material compatibility, automation capabilities, and adherence to safety standards. |
Personal Care Products | Labeling and Cartoning Machines | Enhances product presentation, improves efficiency, and reduces manual labor. | Versatility for various container shapes, ease of operation, and maintenance support. |
How is Packaging Machinery Used in the Food and Beverage Industry?
In the food and beverage sector, automated filling and sealing machines are pivotal. These machines streamline the packaging process, ensuring products are sealed hygienically and efficiently. They address challenges such as contamination and inconsistent fill levels, crucial for maintaining food safety standards. Buyers from regions like Africa and South America should consider sourcing equipment that complies with local food safety regulations and offers robust cleaning capabilities to manage diverse product lines.
What Role Does Packaging Machinery Play in Pharmaceuticals?
Blister packaging machines are essential in the pharmaceutical industry, offering protection against moisture and contamination while extending the shelf life of medications. They meet strict regulatory requirements, ensuring that products remain safe for consumption. For international buyers, particularly in the Middle East and Europe, it is vital to evaluate machinery that is adaptable to various product sizes and provides customization options to enhance branding and user experience.
How is Packaging Machinery Transforming E-commerce and Fulfillment?
In the rapidly growing e-commerce sector, bagging and shrink-wrapping machines optimize the packaging process for shipping. These machines not only reduce material waste but also enhance customer satisfaction through efficient packaging. B2B buyers from regions like South America and Africa should prioritize sourcing machines that can handle a variety of product shapes and sizes, while also offering sustainability features to align with global environmental standards.
Why is Packaging Machinery Important in the Chemical Industry?
Drum and container filling equipment plays a crucial role in the chemical industry by ensuring accurate filling and minimizing spillage. This machinery enhances safety during handling, an essential consideration given the potential hazards associated with chemicals. Buyers should focus on sourcing equipment that is compatible with various materials and adheres to stringent safety standards, particularly in regions with strict regulatory frameworks.
How Does Packaging Machinery Benefit Personal Care Product Manufacturers?
Labeling and cartoning machines are vital for personal care product manufacturers, enhancing product presentation while significantly improving operational efficiency. These machines reduce the need for manual labor, thereby cutting costs and minimizing errors. International buyers, especially from Europe and the Middle East, should look for versatile machines that can accommodate different container shapes and offer reliable maintenance support to ensure continuous operations.
3 Common User Pain Points for ‘packaging machinery’ & Their Solutions
Scenario 1: Inconsistent Packaging Quality Leading to Waste
The Problem:
Many B2B buyers in the packaging machinery sector encounter the issue of inconsistent packaging quality, which can lead to product damage, increased waste, and customer dissatisfaction. For example, a food manufacturer might find that their sealing machinery is not applying the correct pressure, resulting in faulty seals that compromise product integrity. This inconsistency not only affects the bottom line due to wasted materials and products but also damages the brand’s reputation in a competitive market.
The Solution:
To address this problem, buyers should invest in machinery equipped with advanced quality control features. Look for packaging machines that incorporate sensors and automated feedback systems to monitor the sealing process in real-time. These systems can adjust parameters like pressure and temperature automatically, ensuring a consistent seal every time. Additionally, establish a regular maintenance schedule to keep machinery in optimal condition. Engaging with suppliers who offer predictive maintenance programs can also prevent issues before they arise, ensuring machinery operates smoothly and efficiently.
Scenario 2: High Downtime and Maintenance Costs
The Problem:
Downtime due to machinery breakdown is a significant pain point for B2B buyers, particularly in industries such as food and beverage, where production schedules are tight. A packaging company may find its flow wrapping machine frequently breaks down, leading to delays in fulfilling orders and escalating maintenance costs. This situation not only strains resources but can also lead to lost sales opportunities and weakened customer trust.
The Solution:
To mitigate downtime, buyers should prioritize purchasing packaging machinery from manufacturers that offer robust support services, including training for in-house maintenance staff. Investing in machines with modular designs can also help; these allow for easier and quicker repairs or replacements of parts without halting entire production lines. Consider machinery that features predictive maintenance capabilities, which utilize IoT technology to analyze performance data and foresee potential issues. This proactive approach can significantly decrease unplanned downtime and maintenance costs.
Scenario 3: Difficulty in Adapting to Market Changes
The Problem:
The packaging landscape is rapidly evolving, with increased demand for sustainable solutions and the need for customization to meet varying consumer preferences. B2B buyers often struggle to adapt their machinery to accommodate new packaging materials or formats, leading to missed market opportunities. For instance, a beverage company may want to shift from plastic to paper-based packaging but finds its existing machinery is not compatible with the new materials.
The Solution:
To remain agile in a changing market, buyers should look for versatile packaging machines that can easily switch between different materials and formats. Engage with suppliers who offer customizable solutions and allow for quick changeovers. Consider investing in machinery with flexible automation features that can be reprogrammed for different product lines without extensive downtime. Furthermore, conduct market research to stay ahead of trends and proactively engage with suppliers who are innovating in sustainable packaging technologies. This forward-thinking approach will not only keep operations efficient but also position the company as a leader in sustainability.
Strategic Material Selection Guide for packaging machinery
When selecting materials for packaging machinery, international B2B buyers must consider various factors that directly influence the performance, cost, and suitability of the machinery for their specific applications. Below is an analysis of four common materials used in packaging machinery, focusing on their properties, advantages, disadvantages, and considerations for buyers from Africa, South America, the Middle East, and Europe.
What are the Key Properties of Stainless Steel in Packaging Machinery?
Stainless steel is a widely used material in packaging machinery due to its excellent mechanical properties and resistance to corrosion. It typically has a temperature rating of up to 1,500°F (815°C) and can withstand high pressure, making it suitable for a variety of applications, including food and beverage packaging.
Pros & Cons:
The durability of stainless steel is a significant advantage, as it can endure harsh environments and maintain integrity over time. However, the cost of stainless steel can be relatively high compared to other materials, and its manufacturing complexity may increase production lead times.
Impact on Application:
Stainless steel is compatible with a wide range of media, including acidic and alkaline substances, making it ideal for food and pharmaceutical applications.
Considerations for International Buyers:
Buyers should ensure compliance with international standards such as ASTM and DIN, especially in food safety regulations. In regions like Africa and South America, where local materials may be more cost-effective, the long-term benefits of stainless steel should be weighed against initial costs.
How Does Aluminum Compare as a Material for Packaging Machinery?
Aluminum is another popular choice for packaging machinery, particularly in applications requiring lightweight and corrosion-resistant materials. It has a temperature rating of up to 1,200°F (650°C) and is known for its excellent thermal conductivity.
Pros & Cons:
The lightweight nature of aluminum allows for faster machinery operation and easier handling. However, it may not be as durable as stainless steel, leading to potential wear and tear over time. Additionally, aluminum can be more expensive than some plastics.
Impact on Application:
Aluminum is compatible with various packaging applications, including those requiring heat sealing, and is particularly effective in food packaging due to its barrier properties.
Considerations for International Buyers:
Buyers should be aware of the specific alloys used in aluminum machinery, as they can vary in strength and corrosion resistance. Compliance with local regulations regarding food safety is crucial, especially in regions like the Middle East, where stringent standards may apply.
What Are the Benefits of Using Plastic in Packaging Machinery?
Plastics, particularly high-density polyethylene (HDPE) and polypropylene (PP), are commonly used in packaging machinery due to their versatility and cost-effectiveness. These materials can withstand temperatures up to 200°F (93°C) and offer good chemical resistance.
Pros & Cons:
Plastics are lightweight and can be produced at a lower cost than metals, making them attractive for budget-conscious buyers. However, they may not be suitable for high-temperature applications, and their durability can be a concern compared to metals.
Impact on Application:
Plastics are suitable for applications where flexibility and lightweight materials are required, such as in e-commerce packaging machinery.
Considerations for International Buyers:
Buyers should consider the environmental impact of plastic use and ensure compliance with recycling regulations in their respective regions. In Europe, for instance, there is a strong preference for sustainable materials, which may influence purchasing decisions.
Why Choose Composite Materials for Packaging Machinery?
Composite materials, which combine different materials to enhance properties, are increasingly being used in packaging machinery. These materials can offer high strength-to-weight ratios and excellent resistance to corrosion and chemicals.
Pros & Cons:
The primary advantage of composites is their ability to be tailored for specific applications, providing customized solutions. However, they can be more expensive and complex to manufacture, which may increase lead times.
Impact on Application:
Composites are suitable for specialized applications where traditional materials may not perform adequately, such as in high-speed packaging lines.
Considerations for International Buyers:
Buyers should assess the availability of composite materials in their region and consider the associated costs. Additionally, understanding the specific performance characteristics and compliance with international standards is essential for successful integration into existing systems.
Summary Table of Material Selection for Packaging Machinery
Material | Typical Use Case for packaging machinery | Key Advantage | Key Disadvantage/Limitation | Relative Cost (Low/Med/High) |
---|---|---|---|---|
Stainless Steel | Food and pharmaceutical packaging | High durability and corrosion resistance | Higher cost and manufacturing complexity | High |
Aluminum | Lightweight packaging applications | Lightweight with good thermal conductivity | Less durable than stainless steel | Medium |
Plastic | E-commerce and flexible packaging | Cost-effective and versatile | Limited high-temperature suitability | Low |
Composite | High-speed specialized applications | Tailored properties for specific needs | Higher cost and manufacturing complexity | High |
This strategic material selection guide provides international B2B buyers with essential insights into the common materials used in packaging machinery, helping them make informed decisions that align with their operational needs and regional compliance standards.
In-depth Look: Manufacturing Processes and Quality Assurance for packaging machinery
What Are the Main Stages in the Manufacturing Process of Packaging Machinery?
The manufacturing process of packaging machinery typically involves four main stages: material preparation, forming, assembly, and finishing. Each stage plays a crucial role in ensuring that the machinery meets the required specifications and quality standards.
-
Material Preparation: This initial stage involves sourcing high-quality raw materials, such as metals, plastics, and electronic components. Suppliers should be vetted for quality assurance to ensure compliance with international standards, particularly ISO certifications. The selection of materials directly impacts the durability and performance of the machinery.
-
Forming: In this stage, raw materials are transformed into the desired components using various techniques, including cutting, bending, and molding. Advanced technologies like CNC machining and laser cutting are often employed to achieve precision and efficiency. It’s essential for manufacturers to maintain strict tolerances during this phase to avoid issues in later stages.
-
Assembly: Once individual components are formed, they are assembled into the final machinery. This process may involve manual assembly or automated systems, depending on the complexity of the equipment. Effective assembly techniques, such as lean manufacturing principles, are crucial to minimize waste and optimize productivity.
-
Finishing: The final stage includes painting, coating, or applying other surface treatments to protect the machinery and enhance its aesthetic appeal. This stage often involves quality checks to ensure that the finishing meets industry standards and customer specifications.
How Is Quality Assurance Implemented in Packaging Machinery Manufacturing?
Quality assurance (QA) in the manufacturing of packaging machinery is paramount to ensure reliability and performance. Manufacturers adopt various international and industry-specific standards to maintain high-quality outputs.
-
International Standards: ISO 9001 is a widely recognized standard for quality management systems. Compliance with ISO 9001 ensures that manufacturers consistently meet customer and regulatory requirements. Additionally, CE marking indicates conformity with health, safety, and environmental protection standards for products sold within the European Economic Area.
-
Industry-Specific Certifications: Depending on the machinery’s application, additional certifications may be relevant. For instance, packaging machinery used in food production may require FDA compliance in the U.S. or specific standards in Europe, such as the Machinery Directive.
-
Quality Control Checkpoints: The quality control process typically involves several checkpoints:
– Incoming Quality Control (IQC): This initial inspection verifies that raw materials meet specified standards before production begins.
– In-Process Quality Control (IPQC): During the manufacturing process, ongoing inspections ensure that components are being produced according to specifications.
– Final Quality Control (FQC): Once the machinery is assembled, a comprehensive final inspection is conducted to ensure all systems function correctly and meet quality standards.
What Common Testing Methods Are Used in Packaging Machinery Quality Assurance?
Various testing methods are employed to assess the performance and reliability of packaging machinery. These include:
-
Functional Testing: This involves running the machinery under normal operating conditions to evaluate its performance. Tests may include speed, efficiency, and output quality assessments.
-
Durability Testing: Machinery is subjected to stress tests to determine its resilience under extreme conditions, ensuring it can withstand the rigors of continuous operation.
-
Safety Testing: Compliance with safety standards is critical. Safety tests evaluate emergency stop functions, electrical safety, and other critical safety features.
-
Performance Testing: This assesses the machinery’s efficiency in terms of speed, accuracy, and waste generation, which is crucial for B2B buyers looking to maximize productivity.
How Can B2B Buyers Verify Supplier Quality Control Processes?
International B2B buyers should take proactive steps to verify the quality control processes of suppliers to ensure they meet the necessary standards and requirements.
-
Supplier Audits: Conducting on-site audits can provide insights into the supplier’s manufacturing processes and quality control measures. Auditors should assess compliance with relevant standards and evaluate the effectiveness of QA practices.
-
Quality Reports: Requesting detailed quality reports from suppliers can help buyers understand their quality control mechanisms, including inspection results and compliance with international standards.
-
Third-Party Inspections: Engaging third-party inspection services provides an unbiased assessment of the machinery’s quality. These services can conduct thorough inspections and testing, ensuring that the machinery meets the required specifications before shipment.
-
Certifications and Documentation: Buyers should request copies of relevant certifications (ISO, CE, etc.) and documentation that demonstrate compliance with quality standards. This information is crucial for ensuring that the machinery is suitable for their specific market requirements.
What Are the Quality Control Nuances for International B2B Buyers from Africa, South America, the Middle East, and Europe?
International B2B buyers face unique challenges when sourcing packaging machinery, particularly when navigating quality control nuances across different regions.
-
Regulatory Differences: Each region may have its own regulatory framework governing machinery safety and quality. Buyers should familiarize themselves with these regulations to ensure compliance, particularly when importing machinery.
-
Cultural Considerations: Understanding cultural differences in business practices can influence supplier relationships. Effective communication and relationship-building are essential for successful negotiations and long-term partnerships.
-
Supply Chain Logistics: Buyers should consider the implications of logistics on quality control. Ensuring proper handling during transportation can prevent damage to machinery, which may affect its performance and compliance with quality standards.
-
Local Support and Maintenance: Engaging suppliers with local support teams can enhance after-sales service and maintenance, ensuring that quality control is maintained throughout the machinery’s operational life.
By understanding these manufacturing processes and quality assurance practices, B2B buyers can make informed decisions, ensuring they select reliable suppliers that meet their specific packaging machinery needs.
Practical Sourcing Guide: A Step-by-Step Checklist for ‘packaging machinery’
The following guide provides a structured approach for B2B buyers seeking to procure packaging machinery. This checklist will help ensure that your sourcing process is thorough and aligned with your operational needs, particularly in diverse markets across Africa, South America, the Middle East, and Europe.
Step 1: Define Your Technical Specifications
Before initiating the procurement process, clearly outline your technical requirements. This includes the type of packaging machinery needed (e.g., bag sealers, flow wrappers, cartoners) and specifications such as speed, capacity, and compatibility with existing systems. Understanding these parameters is vital to ensure that the machinery meets your production demands and integrates seamlessly into your operations.
Step 2: Conduct Market Research
Investigate the current market landscape for packaging machinery. Identify leading suppliers and evaluate their product offerings, technological advancements, and customer feedback. This research phase is essential to understand price ranges, industry trends, and innovations that could enhance your packaging efficiency.
Step 3: Evaluate Potential Suppliers
Before committing, it’s crucial to vet suppliers thoroughly. Request company profiles, case studies, and references from buyers in a similar industry or region. Pay close attention to:
– Certifications: Verify any industry-specific certifications (e.g., ISO, CE) that demonstrate quality assurance.
– Track Record: Look for suppliers with proven experience in your specific packaging niche.
Step 4: Assess Machine Customization Options
Packaging needs can vary significantly based on the product and market. Inquire about the customization capabilities of the machinery. Suppliers should be able to offer tailored solutions that meet your specific requirements, such as unique sizes, shapes, or materials. This flexibility can lead to improved efficiency and cost savings in the long run.
Step 5: Evaluate After-Sales Support and Maintenance
Consider the level of after-sales support provided by the supplier. Reliable maintenance services and availability of spare parts are crucial for minimizing downtime. Look for suppliers who offer:
– Predictive Maintenance Programs: These can help prevent issues before they occur, ensuring smooth operations.
– Training Services: Ensure that your staff receives proper training on the machinery to maximize efficiency and minimize errors.
Step 6: Review Cost Structures and Financing Options
Understand the total cost of ownership, including purchase price, installation, and ongoing operational costs. Additionally, explore financing options that may be available, such as leasing or installment plans, to better manage your cash flow. Clear cost structures can prevent unexpected expenses down the line.
Step 7: Make an Informed Decision
After gathering all necessary information, compare the suppliers based on your criteria—technical specifications, customization options, support services, and costs. Conduct a final evaluation with your team to ensure alignment with your strategic goals. Making an informed decision will not only enhance your packaging operations but also contribute to your overall business success.
This comprehensive checklist is designed to guide you through the packaging machinery procurement process, ensuring that you make informed, strategic choices that align with your business needs.
Comprehensive Cost and Pricing Analysis for packaging machinery Sourcing
What Are the Key Cost Components in Packaging Machinery Sourcing?
When sourcing packaging machinery, understanding the various cost components is crucial for international B2B buyers. The primary cost elements include:
-
Materials: The choice of materials significantly impacts the overall cost. High-quality, durable materials may incur higher upfront costs but can lead to long-term savings through reduced maintenance and longer machinery lifespans.
-
Labor: Labor costs encompass both direct and indirect labor involved in the manufacturing process. Depending on the region, labor rates can vary considerably, impacting the final price of machinery.
-
Manufacturing Overhead: This includes costs related to factory utilities, administrative expenses, and equipment depreciation. Efficient manufacturing processes can help mitigate these costs.
-
Tooling: Custom tooling is often required for specialized machinery. This upfront investment can be substantial but is essential for producing equipment that meets specific operational needs.
-
Quality Control (QC): Implementing rigorous QC processes ensures machinery meets industry standards. While this can add to costs, it is critical for long-term reliability and compliance, especially for sectors like food and pharmaceuticals.
-
Logistics: Transportation costs, including shipping and handling, can vary based on the machinery’s size and weight. Incoterms also play a vital role in determining who bears these costs.
-
Margin: Supplier profit margins can differ widely based on market conditions, brand reputation, and service offerings. Understanding these margins can aid in negotiating better pricing.
How Do Price Influencers Affect Packaging Machinery Costs?
Several factors can influence the pricing of packaging machinery, particularly for international buyers:
-
Volume and Minimum Order Quantity (MOQ): Larger orders often lead to discounts due to economies of scale. Understanding the supplier’s MOQ can help buyers plan their purchases more effectively.
-
Specifications and Customization: Custom machinery tailored to specific applications typically incurs higher costs. Buyers should assess whether customization aligns with their operational needs and budget.
-
Materials and Quality Certifications: Machinery built with high-grade materials and certified for quality assurance may demand a premium price. Buyers should weigh the importance of certifications against potential cost savings.
-
Supplier Factors: The supplier’s reputation, experience, and service offerings can influence pricing. Established suppliers may charge more but often provide better support and reliability.
-
Incoterms: Familiarity with Incoterms is essential, as they define the responsibilities of buyers and sellers regarding shipping, insurance, and tariffs. This understanding can lead to more favorable pricing arrangements.
What Are Effective Buyer Tips for Cost-Efficiency in Packaging Machinery?
For international B2B buyers, particularly from Africa, South America, the Middle East, and Europe, here are actionable tips to enhance cost-efficiency:
-
Negotiate Smartly: Engage in negotiations with a clear understanding of the costs involved. Leverage volume purchasing and long-term partnerships to secure better pricing.
-
Consider Total Cost of Ownership (TCO): While the initial purchase price is important, the TCO encompasses maintenance, operational costs, and potential downtime. Opt for machinery that offers long-term value rather than just the lowest upfront cost.
-
Research Pricing Nuances: Pricing can vary significantly based on regional market conditions. Conduct thorough market research to identify fair pricing benchmarks for the specific machinery required.
-
Explore Financing Options: Some suppliers offer financing plans that can ease cash flow constraints. This can be particularly beneficial for buyers in emerging markets.
-
Stay Informed on Industry Trends: Keeping abreast of technological advancements and market shifts can provide insights into potential savings and innovations that could enhance packaging operations.
Disclaimer on Indicative Prices
It is important to note that prices for packaging machinery can fluctuate based on market conditions, material costs, and supplier pricing strategies. Therefore, buyers should consider this variability when budgeting and negotiating purchases. Always obtain multiple quotes to ensure competitive pricing.
Alternatives Analysis: Comparing packaging machinery With Other Solutions
Understanding Alternatives to Packaging Machinery
In the dynamic landscape of packaging solutions, international B2B buyers must evaluate the most suitable technologies for their operational needs. While packaging machinery is a robust option for automating and streamlining packaging processes, alternative solutions exist that can also meet specific requirements. This section compares packaging machinery with manual packaging methods and semi-automated solutions, providing insights into their respective advantages and challenges.
Comparison Aspect | Packaging Machinery | Manual Packaging Methods | Semi-Automated Solutions |
---|---|---|---|
Performance | High speed and efficiency | Low speed, labor-intensive | Moderate speed, higher than manual |
Cost | High initial investment | Low initial cost | Moderate investment |
Ease of Implementation | Requires training and setup | Quick to implement | Requires some training |
Maintenance | Regular maintenance needed | Minimal maintenance | Moderate maintenance |
Best Use Case | High-volume production | Low volume, artisanal work | Mid-volume production |
What Are the Pros and Cons of Manual Packaging Methods?
Manual packaging methods involve human labor to package products without the assistance of machinery. This approach is cost-effective, especially for small businesses or startups that cannot afford high capital expenditures. The implementation is straightforward, requiring minimal setup and training. However, the performance is significantly slower compared to machinery, and it can lead to inconsistencies in packaging quality. Additionally, labor-intensive tasks can increase the risk of injuries and burnout among workers.
How Do Semi-Automated Solutions Compare?
Semi-automated solutions bridge the gap between manual methods and fully automated machinery. These systems often involve some level of machine assistance while still requiring human intervention. They offer a balanced approach, enhancing speed and efficiency over manual methods while being more affordable than full packaging machinery. However, they may still require training and can present maintenance challenges. Best suited for mid-volume production, semi-automated solutions allow for flexibility in operations but may not achieve the same level of efficiency as fully automated systems.
Conclusion: How Can B2B Buyers Choose the Right Packaging Solution?
Choosing the right packaging solution depends on several factors, including production volume, budget constraints, and operational capabilities. For businesses focused on high-volume production, investing in advanced packaging machinery is advantageous despite the initial costs due to its efficiency and reliability. Conversely, companies with lower production needs may benefit from manual methods or semi-automated solutions, which provide flexibility and reduced upfront investment. Ultimately, B2B buyers should assess their specific requirements, long-term goals, and the scalability of the chosen solution to ensure optimal performance and profitability.
Essential Technical Properties and Trade Terminology for packaging machinery
What Are the Essential Technical Properties of Packaging Machinery?
Understanding the technical properties of packaging machinery is crucial for B2B buyers, especially those looking to optimize their production processes. Here are several key specifications that should be considered:
1. Material Grade
The material grade of packaging machinery refers to the type of materials used in its construction, such as stainless steel, aluminum, or specific polymers. For B2B buyers, selecting the right material grade ensures durability, corrosion resistance, and compliance with industry standards (e.g., food safety). Higher-grade materials often result in longer machine life and reduced maintenance costs, which is essential for industries like food and pharmaceuticals.
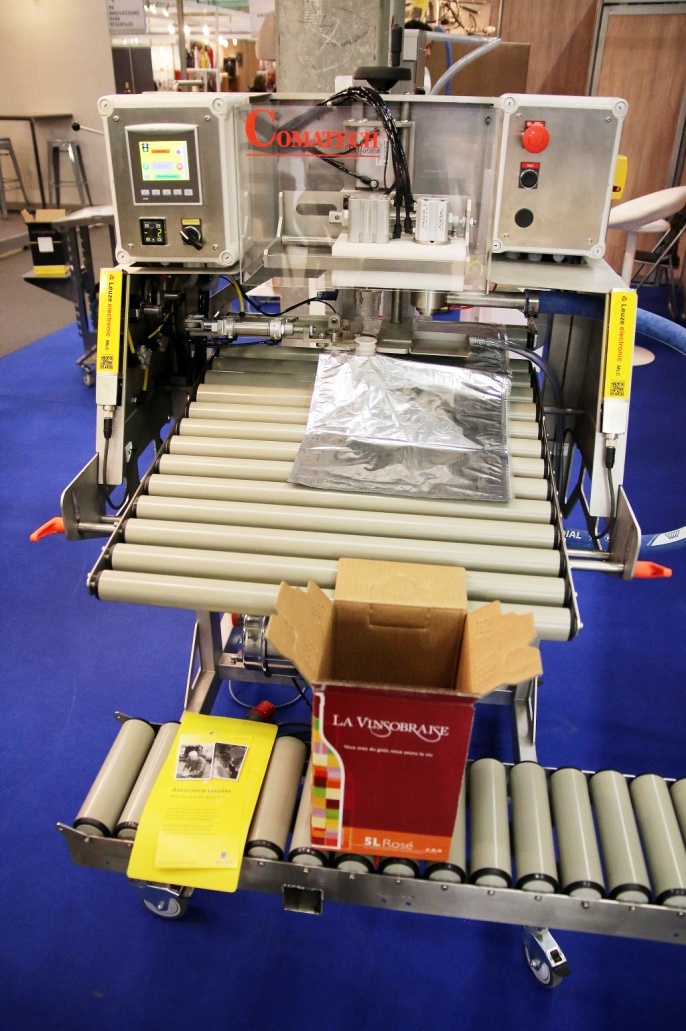
A stock image related to packaging machinery.
2. Tolerance
Tolerance indicates the allowable deviation from a specified dimension in the manufacturing process. In packaging machinery, tight tolerances are critical for ensuring that products are packaged accurately and consistently. For international buyers, understanding tolerance levels can help prevent costly errors during production, especially when dealing with automated systems that require precise alignment for optimal performance.
3. Speed and Throughput
Speed refers to the rate at which a packaging machine can operate, often measured in units per minute (UPM). Throughput is the total number of products processed over a specific time frame. For B2B buyers, knowing the speed and throughput capabilities of machinery is vital for aligning production capacity with demand. Higher speeds can lead to increased efficiency and lower operational costs, making it a key consideration for competitive markets.
4. Automation Level
The level of automation in packaging machinery can significantly impact operational efficiency. Machines can range from fully manual to fully automated systems. For international buyers, investing in higher automation can lead to reduced labor costs, enhanced consistency, and improved safety. Understanding the automation capabilities will help buyers choose machinery that meets their production needs and workforce capabilities.
5. Energy Consumption
Energy consumption measures the amount of energy required to operate the machinery. For B2B buyers, assessing energy efficiency can lead to significant cost savings over time, especially in regions where energy costs are high. Machines designed with energy efficiency in mind not only lower operational costs but also align with sustainability goals, which is increasingly important in global markets.
6. Maintenance Requirements
Maintenance requirements encompass the frequency and type of servicing needed to keep machinery running smoothly. A clear understanding of maintenance schedules and the availability of spare parts can prevent unexpected downtimes. For buyers, investing in machinery with lower maintenance needs can lead to higher productivity and reduced total cost of ownership.
What Are Common Trade Terms Used in Packaging Machinery?
Familiarizing yourself with industry-specific terminology can streamline communication and negotiation processes. Here are some essential terms to know:
1. OEM (Original Equipment Manufacturer)
An OEM is a company that produces parts or equipment that may be marketed by another manufacturer. For buyers, engaging with OEMs ensures that they receive high-quality, reliable components that are compatible with existing machinery, which is crucial for long-term operational success.
2. MOQ (Minimum Order Quantity)
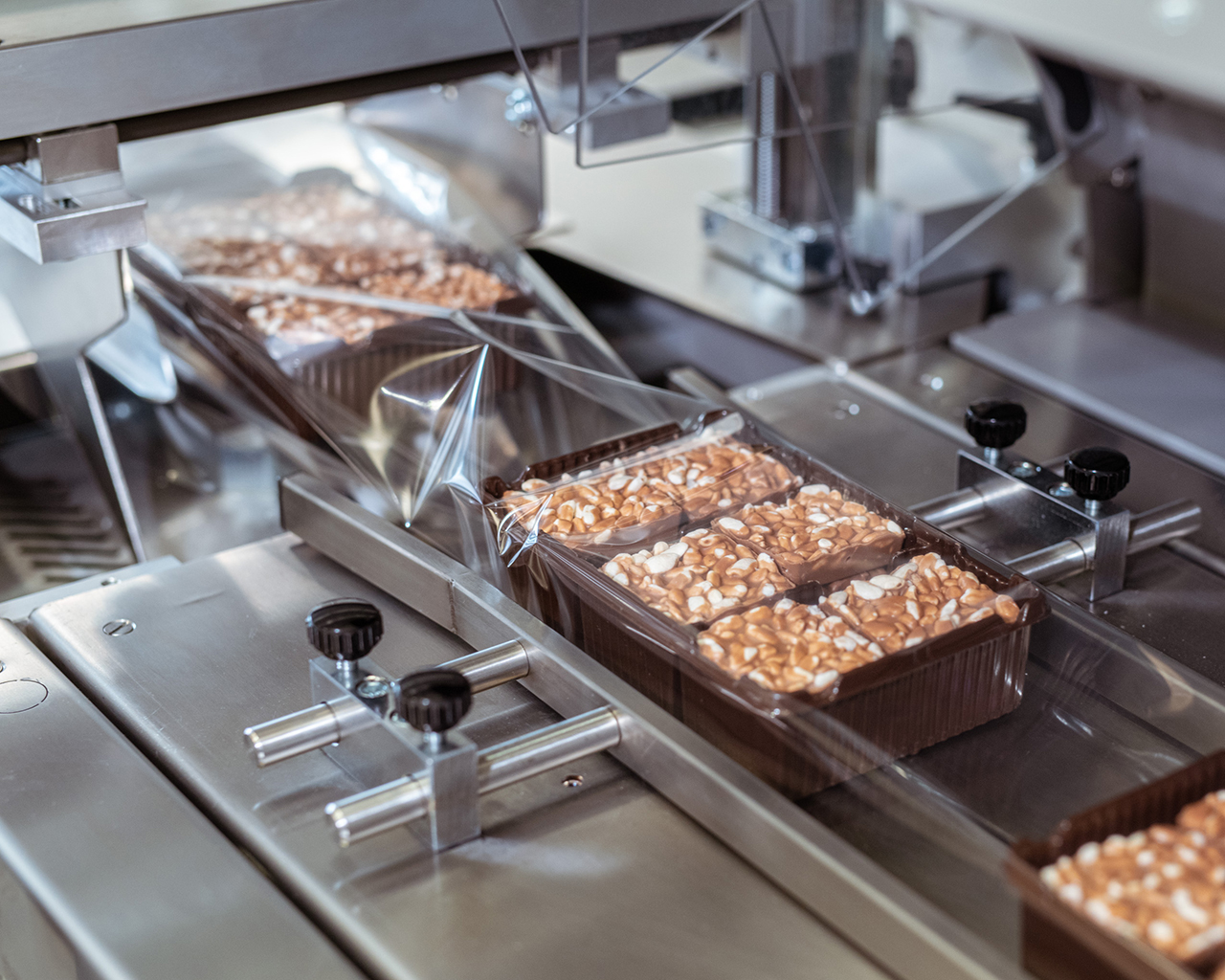
A stock image related to packaging machinery.
MOQ refers to the smallest quantity of a product that a supplier is willing to sell. Understanding MOQs is important for buyers as it can affect inventory levels and cash flow. Buyers should negotiate MOQs that align with their production needs while minimizing excess stock.
3. RFQ (Request for Quotation)
An RFQ is a document sent to suppliers to request pricing and terms for specific products or services. For B2B buyers, issuing an RFQ can facilitate comparison shopping and help secure the best pricing and terms, making it an essential tool for budgeting and procurement strategies.
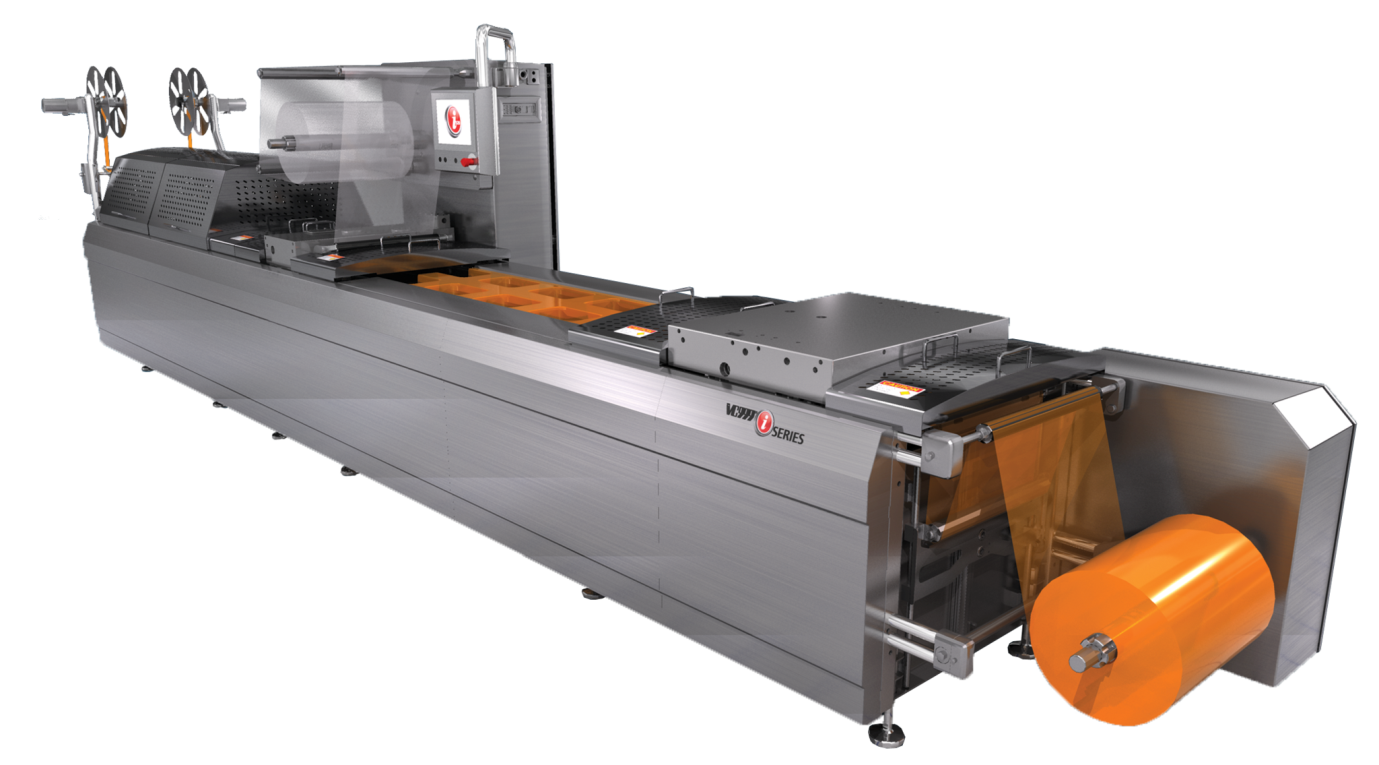
A stock image related to packaging machinery.
4. Incoterms (International Commercial Terms)
Incoterms define the responsibilities of buyers and sellers in international transactions, including shipping costs, insurance, and risk transfer. Understanding Incoterms is critical for international buyers to ensure clarity in contracts and to avoid disputes related to shipping and delivery responsibilities.
5. Lead Time
Lead time is the period between placing an order and receiving the product. For buyers, knowing the lead time for packaging machinery can assist in planning production schedules and managing customer expectations, especially in industries with tight delivery deadlines.
By grasping these essential technical properties and trade terminologies, B2B buyers can make informed decisions that enhance their operational efficiency and competitiveness in the global marketplace.
Navigating Market Dynamics and Sourcing Trends in the packaging machinery Sector
What Are the Current Market Dynamics and Key Trends in the Packaging Machinery Sector?
The global packaging machinery market is experiencing robust growth, driven by a surge in demand from various sectors, including food and beverage, pharmaceuticals, and consumer goods. As international B2B buyers from regions like Africa, South America, the Middle East, and Europe seek to enhance operational efficiency, they are increasingly looking for advanced machinery solutions that incorporate automation, artificial intelligence, and IoT technologies. These innovations not only streamline production processes but also improve product quality and reduce operational costs.
Emerging trends indicate a significant shift towards modular machinery that allows for easy upgrades and customization, catering to the unique requirements of diverse markets. For instance, the demand for multipack machinery is on the rise, as companies aim to optimize packaging for sustainability and consumer appeal. Additionally, predictive maintenance programs are becoming standard, enabling manufacturers to foresee potential failures and minimize downtime, which is crucial for maintaining competitive advantages in fast-paced markets.
International buyers must also consider the implications of geopolitical factors and global supply chain disruptions, which can impact sourcing strategies. Building relationships with local suppliers and diversifying sourcing options can mitigate risks associated with international logistics and tariffs, ensuring a more resilient supply chain.
How Can Sustainability and Ethical Sourcing Impact the Packaging Machinery Sector?
Sustainability is no longer just a trend; it has become a critical factor influencing purchasing decisions in the packaging machinery sector. International B2B buyers are increasingly prioritizing suppliers that demonstrate a commitment to environmentally friendly practices. This includes utilizing sustainable materials, reducing energy consumption, and minimizing waste throughout the production process.
Ethical sourcing is equally vital, as businesses strive to ensure that their supply chains reflect responsible practices. Certifications such as FSC (Forest Stewardship Council) for paper products and ISO 14001 for environmental management systems are essential indicators of a supplier’s commitment to sustainability. Buyers should inquire about the sourcing of raw materials and the environmental impact of the machinery they intend to purchase.
Moreover, the trend towards “green” packaging solutions is driving innovations in machinery design. Many manufacturers are now offering machines that can easily switch between traditional and sustainable materials, such as paper and biodegradable plastics, allowing businesses to adapt to changing consumer preferences without significant capital investment.
What Is the Historical Context Behind Current Packaging Machinery Innovations?
The evolution of packaging machinery can be traced back to the industrial revolution, where the introduction of mechanization significantly increased production capabilities. Over the decades, advancements in technology have transformed packaging processes, leading to the development of automated systems that enhance efficiency and reduce labor costs.
In the late 20th century, the introduction of computer-controlled machinery revolutionized the sector, allowing for precision and flexibility that was previously unattainable. Today, the integration of smart technologies such as AI and IoT is setting new benchmarks for operational excellence. These innovations not only address the immediate needs of manufacturers but also pave the way for future advancements, positioning packaging machinery as a cornerstone of modern manufacturing.
By understanding these market dynamics, sustainability imperatives, and historical context, international B2B buyers can make informed decisions that align with their operational goals and ethical standards, ensuring long-term success in the packaging machinery sector.
Frequently Asked Questions (FAQs) for B2B Buyers of packaging machinery
-
How do I choose the right packaging machinery for my business needs?
Choosing the right packaging machinery involves assessing your production requirements, including the type of products, packaging styles, and volume. Conduct a thorough analysis of your workflow to identify bottlenecks and areas for improvement. Additionally, consider machinery versatility, maintenance needs, and the availability of spare parts. Engaging with suppliers who offer customized solutions can also help you find the best fit for your specific application. -
What factors should I consider when sourcing packaging machinery internationally?
When sourcing packaging machinery internationally, consider factors such as supplier reliability, compliance with local regulations, and after-sales support. Conduct due diligence by checking references, certifications, and customer reviews. Evaluate the supplier’s experience in your industry and their ability to provide local service. Additionally, be mindful of import tariffs, shipping costs, and delivery timelines to avoid unexpected expenses. -
What is the minimum order quantity (MOQ) for packaging machinery?
Minimum order quantities (MOQ) for packaging machinery can vary significantly between suppliers and product types. While some manufacturers may accept single-unit orders, others might require bulk purchases to optimize production costs. It’s essential to discuss your needs with potential suppliers to understand their MOQ policies and negotiate terms that align with your business capabilities. -
What payment terms are commonly offered by packaging machinery suppliers?
Payment terms can vary widely among suppliers, but common practices include upfront deposits, progress payments, and net payment terms. Many suppliers may request a deposit (usually 30-50%) upon order confirmation, with the balance due before shipment or upon delivery. It’s advisable to clarify payment terms early in negotiations to ensure transparency and protect your financial interests. -
How can I ensure quality assurance (QA) for my packaging machinery?
To ensure quality assurance (QA) for your packaging machinery, request detailed specifications, and certifications from suppliers. Inquire about their quality control processes and any third-party inspections they undergo. It’s beneficial to conduct factory visits or virtual audits to observe the manufacturing process. Additionally, consider negotiating a warranty that covers defects and performance issues for a specified period post-purchase. -
What are the logistics considerations when importing packaging machinery?
Logistics considerations for importing packaging machinery include selecting reliable freight forwarders, understanding shipping regulations, and ensuring proper documentation. Be aware of customs clearance processes in your country, as well as potential duties and taxes. Plan for the machinery’s delivery and installation, considering any specialized handling required due to size or sensitivity. Communicating with your supplier about logistics can help streamline the process. -
Can I customize packaging machinery for my specific products?
Yes, many packaging machinery suppliers offer customization options to meet specific product requirements. Customization can include modifications in size, design, and functionality to suit unique packaging needs. Discuss your specifications with potential suppliers early in the procurement process to understand the possibilities and limitations of their equipment. Custom solutions can enhance efficiency and improve packaging quality. -
What are the benefits of attending packaging trade shows for B2B buyers?
Attending packaging trade shows offers numerous benefits for B2B buyers, including networking opportunities with industry professionals and suppliers. It provides a platform to see the latest machinery innovations firsthand, allowing you to assess performance and capabilities. Trade shows often feature workshops and seminars, offering insights into industry trends and best practices. Additionally, face-to-face interactions can foster stronger supplier relationships and potentially lead to better negotiation terms.
Important Disclaimer & Terms of Use
⚠️ Important Disclaimer
The information provided in this guide, including content regarding manufacturers, technical specifications, and market analysis, is for informational and educational purposes only. It does not constitute professional procurement advice, financial advice, or legal advice.
While we have made every effort to ensure the accuracy and timeliness of the information, we are not responsible for any errors, omissions, or outdated information. Market conditions, company details, and technical standards are subject to change.
B2B buyers must conduct their own independent and thorough due diligence before making any purchasing decisions. This includes contacting suppliers directly, verifying certifications, requesting samples, and seeking professional consultation. The risk of relying on any information in this guide is borne solely by the reader.
Strategic Sourcing Conclusion and Outlook for packaging machinery
In today’s competitive landscape, strategic sourcing of packaging machinery is essential for businesses aiming to optimize their operations and enhance product delivery. Key takeaways from this guide emphasize the importance of aligning machinery selection with specific operational needs, considering factors such as efficiency, maintenance, and sustainability. As international B2B buyers from regions like Africa, South America, the Middle East, and Europe navigate the complexities of sourcing, leveraging advanced technologies and predictive maintenance programs can significantly reduce downtime and improve overall productivity.
How can international buyers leverage strategic sourcing for packaging machinery? By adopting a proactive approach to procurement, companies can not only ensure timely delivery of high-quality machinery but also foster long-term partnerships with suppliers. This collaboration can lead to innovative solutions tailored to meet evolving market demands.
Looking ahead, the packaging machinery sector is poised for growth, driven by technological advancements and increasing consumer expectations for sustainability. Now is the time for international buyers to engage with leading suppliers, explore innovative packaging solutions, and secure their competitive edge in the global marketplace. Embrace the future of packaging by making informed sourcing decisions today.