Discover Cost-Saving Benefits of Air Filters for Your Business (2025)
Introduction: Navigating the Global Market for air filter
Navigating the global market for air filters can be a daunting challenge for international B2B buyers, particularly those operating in diverse environments such as Africa, South America, the Middle East, and Europe. With varying air quality standards and filtration needs, sourcing the right air filters tailored to specific applications is crucial. This guide serves as a comprehensive resource, detailing the different types of air filters available, their applications across various sectors, and the essential criteria for vetting suppliers.
As an international buyer, understanding the nuances of air filter specifications—including MERV ratings, filter sizes, and material compositions—is vital for making informed purchasing decisions. This guide also covers cost considerations, helping you to balance quality with budget constraints while ensuring compliance with local regulations and standards.
By equipping you with actionable insights and strategies, this resource empowers B2B buyers to confidently navigate the complexities of the air filter market. Whether you are in Brazil seeking energy-efficient solutions or in the Middle East looking for advanced filtration technologies, this guide is designed to enhance your sourcing process and optimize your air quality management. Embrace the opportunity to elevate your procurement strategy and ensure the health and safety of your indoor environments.
Understanding air filter Types and Variations
Type Name | Key Distinguishing Features | Primary B2B Applications | Brief Pros & Cons for Buyers |
---|---|---|---|
HEPA Filters | Captures 99.97% of particles ≥0.3 microns | Hospitals, laboratories, clean rooms | Pros: Excellent air quality, effective for allergens. Cons: Higher initial cost, requires regular replacement. |
Activated Carbon Filters | Contains activated carbon to absorb odors and gases | Food processing, chemical plants | Pros: Reduces odors and harmful gases. Cons: Limited particle filtration compared to HEPA. |
Electrostatic Filters | Uses static electricity to attract particles | Manufacturing, HVAC systems | Pros: Washable and reusable, low energy consumption. Cons: May require specialized maintenance. |
Pleated Filters | Increased surface area for improved airflow | Commercial buildings, offices | Pros: Cost-effective, higher dust-holding capacity. Cons: Can restrict airflow if not changed regularly. |
Media Filters | Thick filters with high dust-holding capacity | Industrial applications, HVAC systems | Pros: Long-lasting, effective for large particles. Cons: Bulkier, may require more space for installation. |
What are HEPA Filters and Their B2B Benefits?
HEPA (High-Efficiency Particulate Air) filters are designed to capture 99.97% of particles that are 0.3 microns or larger. This makes them ideal for environments requiring stringent air quality standards, such as hospitals and clean rooms. B2B buyers should consider the long-term cost of ownership, including the need for regular replacements and the initial investment, as HEPA filters can be more expensive than other types. However, the significant improvement in air quality can justify the cost, especially in sensitive applications.
How Do Activated Carbon Filters Work for Businesses?
Activated carbon filters are effective in absorbing odors and harmful gases, making them suitable for industries such as food processing and chemical manufacturing. These filters excel in environments where air quality is essential not just for comfort but for safety. Buyers should evaluate the specific needs of their operations, as these filters may not be as efficient in capturing particulate matter compared to HEPA filters. The balance between cost and the need for odor control is crucial in the purchasing decision.
What Advantages Do Electrostatic Filters Offer to B2B Buyers?
Electrostatic filters utilize static electricity to attract and capture particles, making them a unique option for businesses looking for a sustainable and cost-effective solution. They are often washable and reusable, which reduces long-term costs. Electrostatic filters are particularly beneficial in manufacturing and HVAC systems. However, buyers should be aware that these filters may require specialized maintenance to ensure optimal performance, which can affect operational efficiency.
Why Choose Pleated Filters for Commercial Use?
Pleated filters have a larger surface area compared to traditional flat filters, allowing for improved airflow and higher dust-holding capacity. They are commonly used in commercial buildings and offices, where they provide a balance between cost and performance. B2B buyers should consider the frequency of filter changes, as clogged pleated filters can restrict airflow and lead to increased energy costs. Their affordability and effectiveness make them a popular choice for many businesses.
What are Media Filters and Their Key Considerations for Buyers?
Media filters are thicker filters designed to hold a larger amount of dust and particles, making them suitable for industrial applications and HVAC systems. They provide long-lasting performance, which can reduce maintenance frequency and costs. However, their bulkiness may require additional space for installation. When considering media filters, B2B buyers should evaluate their specific space constraints and the required air quality levels to ensure they select the most appropriate filter type for their operations.
Key Industrial Applications of air filter
Industry/Sector | Specific Application of Air Filter | Value/Benefit for the Business | Key Sourcing Considerations for this Application |
---|---|---|---|
Manufacturing | HVAC systems in production facilities | Reduces airborne contaminants, improving product quality and worker health | MERV ratings, filter lifespan, compatibility with existing systems |
Food and Beverage | Air filtration in processing plants | Ensures compliance with health regulations and maintains product integrity | Food-grade certification, filter maintenance requirements, size specifications |
Pharmaceuticals | Cleanroom air filtration | Maintains sterile environments essential for drug production | HEPA filters, regulatory compliance, filter efficiency ratings |
Automotive | Paint booths and assembly line air filtration | Prevents dust and particles from affecting finish quality | Compatibility with specific machinery, filter replacement frequency, local regulations |
Data Centers | Air filters for cooling systems | Enhances equipment performance by maintaining optimal operating temperatures | Energy efficiency ratings, filter design for airflow, maintenance schedules |
How Are Air Filters Used in Manufacturing Facilities?
In manufacturing, air filters play a critical role in HVAC systems, ensuring that the air quality is maintained at optimal levels. This is crucial as airborne contaminants can adversely affect product quality and worker health. International B2B buyers should consider filters with appropriate MERV ratings to ensure they meet their specific needs. Additionally, understanding filter lifespan and compatibility with existing systems can lead to significant cost savings and operational efficiency.
What Role Do Air Filters Play in Food and Beverage Processing?
In the food and beverage industry, air filters are essential for maintaining compliance with health and safety regulations. They help to prevent contaminants from entering processing areas, thus safeguarding product integrity. Buyers in this sector must prioritize filters that are certified for food-grade applications, ensuring they meet stringent safety standards. It’s also important to consider the maintenance requirements and size specifications to avoid disruptions in production.
Why Are Air Filters Critical in Pharmaceuticals?
Pharmaceutical manufacturing relies heavily on cleanroom environments, where air filters are vital for maintaining sterility. HEPA filters are commonly used to achieve the necessary air quality standards. B2B buyers in this industry must ensure that their air filtration systems comply with regulatory requirements, as any lapse can result in costly production delays. Additionally, efficiency ratings of filters should be carefully evaluated to minimize operational costs while maintaining compliance.
How Do Air Filters Benefit Automotive Manufacturing?
In automotive manufacturing, air filters are used in paint booths and assembly lines to prevent dust and particulate matter from affecting the quality of finishes. This not only enhances the aesthetic appeal of vehicles but also protects the integrity of the manufacturing process. Buyers should consider the compatibility of filters with specific machinery and the frequency of replacements to ensure smooth operations. Local regulations regarding emissions and air quality should also be taken into account.
What Importance Do Air Filters Have in Data Centers?
Air filters in data centers are crucial for cooling systems, as they help maintain optimal operating temperatures for sensitive equipment. Effective air filtration enhances performance and longevity of servers and other electronic devices. Buyers should focus on energy efficiency ratings of air filters, as this can significantly impact operational costs. Moreover, understanding filter design for airflow and establishing a regular maintenance schedule is essential for preventing downtime and ensuring continuous operation.
3 Common User Pain Points for ‘air filter’ & Their Solutions
Scenario 1: Sourcing the Right Air Filter for Specific Applications
The Problem:
Many B2B buyers face the challenge of identifying the correct air filter type for their specific applications, especially in diverse industrial settings. In regions such as Africa and South America, where air quality varies significantly due to environmental factors, selecting a filter that meets both local regulations and operational needs can be daunting. Buyers often struggle with understanding the Minimum Efficiency Reporting Value (MERV) ratings, leading to potential over-purchasing of filters that may not be suitable for their HVAC systems or specific air quality requirements.
The Solution:
To overcome this challenge, buyers should conduct a thorough assessment of their air quality needs before sourcing air filters. Start by evaluating the specific pollutants present in the environment, including dust, pollen, or industrial contaminants. Utilize air quality monitoring systems to gather data on particulate matter and other pollutants. Based on this assessment, consult with filter manufacturers or suppliers who offer technical support to recommend the most suitable filter types and MERV ratings. Additionally, consider suppliers that provide a range of options, including custom filters tailored to specific sizes or filtration levels. This proactive approach ensures that the filters sourced will optimize air quality and efficiency, ultimately reducing costs associated with frequent replacements.
Scenario 2: Managing Inventory and Supply Chain Issues
The Problem:
International B2B buyers often encounter inventory management issues, particularly when dealing with air filters that have varying lead times due to supply chain disruptions. This problem is exacerbated by fluctuating demand, seasonal changes, and the need for specific filter sizes that may not be readily available in local markets. For businesses in the Middle East and Europe, unexpected delays can lead to operational downtime, affecting air quality and employee health.
The Solution:
Implementing a robust inventory management system is essential for mitigating these supply chain challenges. Begin by establishing a forecast model that takes into account historical usage data and anticipated demand fluctuations based on seasonal trends. Collaborate with multiple suppliers to create a diversified supply chain that reduces reliance on a single source. Moreover, consider using subscription services that allow for automatic reordering of air filters based on your inventory levels. This not only ensures a consistent supply but also allows buyers to take advantage of bulk purchasing discounts, ultimately streamlining operations and reducing costs. Regularly review and adjust your inventory strategy to adapt to changes in demand and supply chain dynamics.
Scenario 3: Understanding and Complying with Environmental Regulations
The Problem:
B2B buyers must navigate a complex landscape of environmental regulations related to air quality and filter usage. Different regions, particularly in Europe and the Middle East, have stringent guidelines governing the types of filters that can be used in commercial and industrial applications. Failure to comply with these regulations can result in hefty fines and reputational damage for businesses.
The Solution:
To ensure compliance with local regulations, B2B buyers should stay informed about the latest environmental standards related to air filtration. This can be achieved by subscribing to industry newsletters, attending workshops, and engaging with regulatory bodies. Partner with suppliers who are knowledgeable about compliance requirements and can provide filters that meet or exceed regulatory standards. Additionally, consider conducting regular audits of your air filtration systems to ensure they are operating within compliance limits. Documentation of compliance efforts, including filter specifications and maintenance records, is crucial for demonstrating adherence to regulations during inspections. This strategic approach not only safeguards your business against penalties but also enhances your reputation as a responsible corporate entity.
Strategic Material Selection Guide for air filter
What Are the Key Materials Used in Air Filters?
When selecting air filters for various applications, understanding the materials used is crucial for ensuring optimal performance and compliance with international standards. Here, we analyze four common materials used in air filters: fiberglass, pleated polyester, activated carbon, and HEPA media. Each material has distinct properties, advantages, and limitations that can significantly impact the effectiveness of air filtration systems.
How Does Fiberglass Perform as an Air Filter Material?
Fiberglass is a widely used material in air filters due to its affordability and effectiveness in capturing larger particles. Fiberglass filters typically have a MERV (Minimum Efficiency Reporting Value) rating between 1 and 4, making them suitable for residential and light commercial applications.
- Key Properties: Fiberglass filters can withstand high temperatures and have good moisture resistance, making them suitable for various environments.
- Pros: They are cost-effective and have a long lifespan, requiring less frequent replacement.
- Cons: However, they are less effective at capturing smaller particles, which may not meet the needs of industries requiring high air quality.
- Impact on Application: Fiberglass filters are ideal for basic filtration needs but may not be suitable for sensitive environments like hospitals or clean rooms.
- Considerations for International Buyers: Compliance with local standards such as ASTM or EN may be necessary, especially in regulated industries.
What Are the Advantages of Pleated Polyester Filters?
Pleated polyester filters offer a higher filtration efficiency compared to fiberglass, with MERV ratings typically ranging from 5 to 13. This material is known for its increased surface area, which enhances its ability to trap particles.
- Key Properties: Polyester filters are resistant to moisture and can operate effectively in a range of temperatures.
- Pros: They provide better filtration of allergens, dust, and pet dander, making them suitable for residential and commercial applications.
- Cons: The manufacturing process can be more complex, leading to higher costs compared to fiberglass.
- Impact on Application: These filters are a good choice for environments where air quality is a priority, such as schools and offices.
- Considerations for International Buyers: Buyers should ensure that the filters meet local environmental and health regulations, particularly in urban areas with high pollution levels.
How Effective Are Activated Carbon Filters?
Activated carbon filters are primarily used for odor and gas removal, making them essential in applications where air quality is critical, such as in restaurants or industrial settings.
- Key Properties: These filters are highly porous, providing a large surface area for adsorption of volatile organic compounds (VOCs) and odors.
- Pros: They excel at removing smells and harmful gases, which is vital for maintaining a pleasant indoor environment.
- Cons: Activated carbon filters are not as effective at capturing particulate matter and may require frequent replacement to maintain performance.
- Impact on Application: Best suited for applications focused on air quality rather than particulate filtration.
- Considerations for International Buyers: Buyers should look for certifications that verify the effectiveness of the carbon used, as standards can vary significantly across regions.
What Makes HEPA Media a Preferred Choice for Air Filters?
HEPA (High-Efficiency Particulate Air) filters are renowned for their ability to capture 99.97% of particles that are 0.3 microns or larger. These filters are essential in environments that require stringent air quality standards, such as hospitals and laboratories.
- Key Properties: HEPA filters can handle a range of temperatures and are resistant to moisture and chemical degradation.
- Pros: They provide superior filtration efficiency and are crucial for applications requiring clean air.
- Cons: The high manufacturing costs and complexity can make HEPA filters more expensive than other options.
- Impact on Application: Ideal for critical environments where air purity is paramount.
- Considerations for International Buyers: Compliance with international standards such as ISO 29463 or local regulations is critical, particularly in healthcare settings.
Summary Table of Air Filter Materials
Material | Typical Use Case for Air Filter | Key Advantage | Key Disadvantage/Limitation | Relative Cost (Low/Med/High) |
---|---|---|---|---|
Fiberglass | Residential and light commercial applications | Cost-effective and long lifespan | Low efficiency for smaller particles | Low |
Pleated Polyester | Schools, offices, and residential areas | Better filtration efficiency | Higher manufacturing complexity and cost | Medium |
Activated Carbon | Restaurants, industrial applications | Excellent for odor and gas removal | Less effective for particulate matter | Medium |
HEPA Media | Hospitals, laboratories | Superior filtration efficiency | High cost and complexity in manufacturing | High |
This strategic material selection guide provides B2B buyers with essential insights into the properties, advantages, and limitations of various air filter materials, enabling informed purchasing decisions tailored to specific applications and regional compliance requirements.
In-depth Look: Manufacturing Processes and Quality Assurance for air filter
What Are the Key Stages in the Manufacturing Process of Air Filters?
The manufacturing process for air filters involves several critical stages, each designed to ensure the highest quality and performance standards. Understanding these stages can help B2B buyers from Africa, South America, the Middle East, and Europe make informed decisions when selecting suppliers.
1. Material Preparation: What Materials Are Commonly Used?
The first stage of manufacturing air filters involves sourcing and preparing materials. Common materials include:
- Fiberglass: Known for its lightweight and effective filtration properties.
- Polyester: Offers durability and resistance to moisture and mold.
- Activated Carbon: Used for odors and volatile organic compounds (VOCs) removal.
- Synthetic Media: Often used in high-efficiency filters for better filtration.
These materials are assessed for quality and consistency before moving to the next stage. Buyers should inquire about the source and specifications of these materials to ensure they meet industry standards.
2. Forming: How Are Filter Media Constructed?
The forming stage involves shaping the prepared materials into filter media. This process can include:
- Pleating: Increasing the surface area to enhance filtration efficiency. Pleated filters are popular due to their higher dirt-holding capacity.
- Layering: Combining different materials to create a composite filter that addresses various contaminants.
Manufacturers often use automated machines to ensure precision and consistency during this stage. Buyers should check if suppliers utilize advanced technologies that minimize human error and variability.
3. Assembly: How Are Air Filters Assembled?
Once the filter media is formed, the next step is assembly. This typically involves:
- Frame Construction: The media is secured within a sturdy frame, often made from metal or plastic.
- Sealing: Ensuring that the media is tightly sealed to prevent air bypass, which can compromise efficiency.
Quality assembly is crucial for the longevity and performance of air filters. B2B buyers should inquire about the assembly techniques used and whether the manufacturer adheres to stringent quality control measures during this stage.
4. Finishing: What Final Touches Are Applied?
The finishing stage includes additional treatments to enhance the filter’s performance. This can involve:
- Coating: Applying a protective layer to improve durability or add properties like electrostatic charge for better particle capture.
- Labeling: Clearly marking specifications, MERV ratings, and other essential information for end-users.
Buyers should assess the finishing processes to ensure they align with their specific needs and standards.
What Quality Assurance Measures Are Essential in Air Filter Manufacturing?
Quality assurance (QA) is a critical aspect of air filter manufacturing, ensuring that products meet international standards and customer expectations. Understanding these QA measures can help B2B buyers make informed supplier choices.
International Standards: What Certifications Should Buyers Look For?
B2B buyers should be familiar with relevant international standards that pertain to air filter manufacturing. Key certifications include:
- ISO 9001: This standard focuses on quality management systems, ensuring that manufacturers consistently meet customer requirements and enhance satisfaction.
- CE Marking: Indicates compliance with European health, safety, and environmental protection standards.
- API Standards: Relevant for filters used in oil and gas industries, ensuring compatibility and safety.
Buyers should request documentation proving that suppliers hold these certifications, as they indicate a commitment to quality and reliability.
Key QC Checkpoints: What Are the Critical Control Points?
Quality control involves several checkpoints throughout the manufacturing process, including:
- Incoming Quality Control (IQC): Inspection of raw materials upon arrival at the facility to ensure they meet specified standards.
- In-Process Quality Control (IPQC): Ongoing checks during manufacturing to identify and rectify issues in real-time.
- Final Quality Control (FQC): Comprehensive testing of finished products to verify performance metrics and compliance with specifications.
Understanding these checkpoints can help buyers assess the reliability of their suppliers.
Common Testing Methods: How Is Quality Assured?
Various testing methods are employed to ensure the performance and safety of air filters. Common tests include:
- MERV Rating Tests: Assessing the filter’s efficiency in capturing particles of different sizes.
- Airflow Resistance Tests: Measuring the resistance the filter presents to airflow, which impacts system efficiency.
- Durability Tests: Evaluating the filter’s performance under different environmental conditions.
Buyers should ask suppliers about their testing protocols and the results of these tests to ensure they meet necessary performance standards.
How Can B2B Buyers Verify Supplier Quality Control?
To ensure that potential suppliers maintain high-quality standards, B2B buyers should consider the following verification methods:
Audits: What Should Be Included in Supplier Audits?
Conducting audits of potential suppliers can provide insights into their manufacturing processes and quality control measures. Key elements to review during an audit include:
- Facility Conditions: Assessing cleanliness, organization, and equipment maintenance.
- Quality Management Systems: Reviewing documentation related to quality policies and procedures.
- Employee Training: Ensuring that staff are adequately trained in manufacturing and quality control processes.
Regular audits can help identify any potential issues before they impact product quality.
Reports and Certifications: What Documentation Is Necessary?
Requesting reports and certifications from suppliers can help verify their commitment to quality. Essential documents include:
- Quality Assurance Manuals: Detailing the manufacturer’s quality control processes.
- Test Reports: Providing results from performance tests conducted on their products.
- Compliance Certificates: Proving adherence to international standards.
Having access to these documents allows buyers to make informed decisions based on verifiable data.
Third-Party Inspections: How Can They Enhance Trust?
Utilizing third-party inspection services can add an additional layer of assurance. These independent organizations can perform:
- Quality Inspections: Assessing products before shipment to ensure they meet specified requirements.
- Factory Audits: Evaluating manufacturing processes and quality control measures.
Engaging third-party inspectors can provide an unbiased assessment of a supplier’s capabilities, enhancing buyer confidence.
What Are the Unique QC Considerations for International Buyers?
For international B2B buyers, particularly from regions like Africa, South America, the Middle East, and Europe, several nuances exist regarding quality control:
- Understanding Regional Standards: Different regions may have varying regulatory requirements. Buyers should familiarize themselves with local standards that may affect product compliance.
- Supply Chain Transparency: Ensuring that suppliers provide clear information about their supply chain practices can mitigate risks associated with sourcing materials and components.
- Cultural Differences in Quality Expectations: Buyers should be aware that quality perceptions may vary by region, necessitating clear communication of expectations.
By considering these factors, international buyers can better navigate the complexities of sourcing air filters while ensuring high-quality standards are met.
Practical Sourcing Guide: A Step-by-Step Checklist for ‘air filter’
Introduction
Navigating the procurement of air filters can be a complex task, especially for international B2B buyers. This step-by-step checklist is designed to streamline your sourcing process, ensuring you select high-quality air filters that meet your operational needs while adhering to industry standards. Whether you’re in Africa, South America, the Middle East, or Europe, following these steps will help you make informed decisions.
Step 1: Define Your Technical Specifications
Before beginning the sourcing process, clearly define your technical specifications. Identify the size, type, and MERV (Minimum Efficiency Reporting Value) rating required for your application. This clarity will guide your supplier search and ensure you acquire filters that perform effectively in your specific environment.
– Key Considerations:
– Determine the airflow requirements and filter dimensions.
– Assess the contaminants you need to filter out, such as dust, allergens, or industrial pollutants.
Step 2: Research and Identify Potential Suppliers
Conduct thorough research to compile a list of potential suppliers. Use online marketplaces, industry directories, and trade shows to discover reputable manufacturers and distributors. Engaging with suppliers that have a strong presence in your target region can enhance reliability and reduce shipping times.
– Tip:
– Look for suppliers who specialize in the air filter market and have experience with international shipping to your specific region.
Step 3: Evaluate Supplier Certifications and Compliance
Ensure that potential suppliers comply with relevant industry standards and certifications, such as ISO 9001 for quality management systems. Compliance not only signifies product quality but also aligns with regulatory requirements in your region.
– What to Check:
– Request copies of certifications and ask about the supplier’s quality assurance processes.
– Verify compliance with local and international environmental regulations.
Step 4: Request Samples and Test Performance
Before making a bulk purchase, request samples of the air filters. Testing these samples allows you to evaluate their performance in real conditions and verify that they meet your specified requirements.
– Important Actions:
– Analyze the filters for durability, efficiency, and ease of installation.
– Conduct air quality tests to confirm their effectiveness in your specific environment.
Step 5: Assess Pricing and Payment Terms
Once you have shortlisted suppliers, compare their pricing structures and payment terms. Understand the total cost of ownership, which includes shipping, taxes, and any additional fees. Establishing favorable payment terms can improve cash flow and reduce financial risks.
– Considerations:
– Inquire about volume discounts for bulk orders and long-term contracts.
– Clarify payment methods and any financing options available.
Step 6: Negotiate and Finalize Contracts
After selecting a preferred supplier, engage in negotiations to finalize the contract. Focus on critical aspects such as delivery schedules, warranty conditions, and after-sales support. A well-defined contract protects both parties and sets clear expectations.
– Key Points:
– Ensure all terms are documented, including service level agreements (SLAs) for delivery and support.
– Discuss penalties for non-compliance or delays to safeguard your interests.
Step 7: Establish a Continuous Evaluation Process
Once your air filters are in use, establish a routine evaluation process to monitor their performance and supplier reliability. This ongoing assessment ensures that you maintain optimal air quality and can promptly address any issues that arise.
– Ongoing Actions:
– Regularly review filter performance data and gather feedback from maintenance staff.
– Maintain open communication with your supplier for continuous improvement and potential upgrades.
By following this comprehensive checklist, B2B buyers can effectively navigate the complexities of sourcing air filters, ensuring they meet both operational needs and regulatory requirements.
Comprehensive Cost and Pricing Analysis for air filter Sourcing
What Are the Key Cost Components in Air Filter Manufacturing?
When sourcing air filters, understanding the cost structure is crucial for B2B buyers. The primary components include:
-
Materials: The quality and type of materials used, such as fiberglass, pleated paper, or synthetic fibers, significantly impact costs. Higher MERV-rated filters often require more advanced materials, which can increase the price.
-
Labor: Labor costs vary depending on the location of manufacturing. Regions with higher labor costs will reflect this in the pricing of air filters. Consider the skill level required for specialized production techniques, especially for custom filters.
-
Manufacturing Overhead: This includes costs related to the facility, utilities, equipment maintenance, and administrative expenses. Efficient production processes can help minimize overhead, affecting the final price.
-
Tooling: The initial investment in molds and tools for production can be substantial, particularly for custom or unique filter sizes. Buyers should inquire about tooling costs when discussing custom orders.
-
Quality Control (QC): Ensuring that filters meet regulatory standards and quality benchmarks requires investment in QC processes. Filters that are certified (e.g., HEPA, MERV ratings) will typically incur higher QC costs, which are passed on to the buyer.
-
Logistics: Shipping and handling costs can vary widely based on the origin of the product and the destination. International shipping, customs duties, and handling fees should be factored into the total cost.
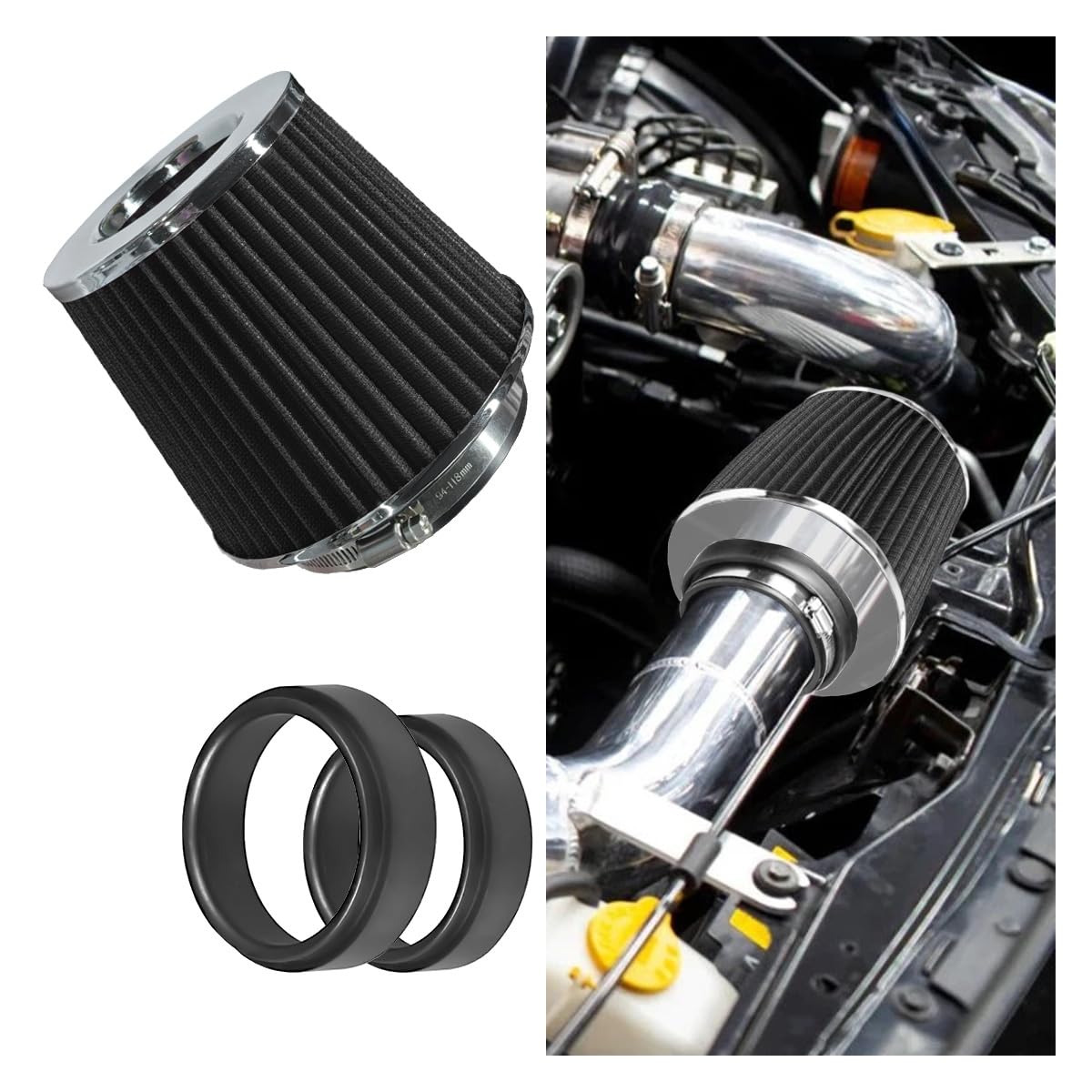
A stock image related to air filter.
- Margin: Suppliers will add a profit margin to cover their costs and ensure profitability. Understanding the typical margin in your specific market can help in negotiations.
How Do Price Influencers Affect Air Filter Costs?
Several factors can influence the pricing of air filters, particularly for international B2B buyers:
-
Volume and Minimum Order Quantity (MOQ): Larger orders often lead to bulk discounts. Buyers should negotiate MOQs to optimize pricing, especially when planning for long-term supply needs.
-
Specifications and Customization: Custom filters designed to meet specific needs (size, MERV rating, etc.) typically cost more than standard options. It’s essential to balance customization with budget constraints.
-
Materials and Quality Certifications: Filters with higher MERV ratings or specialized materials for specific applications (e.g., medical settings) will carry a premium. Buyers should assess whether the additional cost aligns with their air quality requirements.
-
Supplier Factors: The reputation and reliability of suppliers can impact pricing. Established suppliers may charge more due to perceived quality and service reliability, while newer entrants might offer competitive pricing to gain market share.
-
Incoterms: Understanding the delivery terms (e.g., FOB, CIF) can affect total costs. Different Incoterms dictate who bears responsibility for shipping and insurance, impacting overall pricing.
What Tips Can Help International Buyers Optimize Air Filter Sourcing Costs?
For international B2B buyers, particularly from Africa, South America, the Middle East, and Europe, the following strategies can enhance cost-efficiency:
-
Negotiate Terms and Prices: Engage in open discussions with suppliers about pricing structures and payment terms. Leverage volume commitments to negotiate better rates.
-
Consider Total Cost of Ownership (TCO): Evaluate not just the purchase price but also factors like shipping, maintenance, and disposal costs. A cheaper filter might lead to higher operational costs if it requires more frequent replacements.
-
Research Local Suppliers: Sourcing from local manufacturers can reduce shipping costs and lead times. Additionally, local suppliers may offer better insights into regional regulations and standards.
-
Stay Informed on Market Trends: Keep abreast of global supply chain issues, material shortages, and economic conditions that could affect pricing. This knowledge can be a valuable tool in negotiations.
-
Evaluate Quality vs. Cost: While it may be tempting to opt for the lowest price, consider the long-term implications of quality. Investing in higher-quality filters can lead to improved air quality and lower overall costs over time.
Conclusion: Understanding Pricing Nuances
Prices for air filters can vary widely based on multiple factors. It’s essential for B2B buyers to conduct thorough analyses of both cost components and price influencers to make informed purchasing decisions. By employing strategic sourcing techniques, buyers can optimize their investments in air filters, ensuring they meet their air quality needs while remaining within budget.
- Disclaimer: The prices mentioned are indicative and can fluctuate based on market conditions, supplier negotiations, and specific buyer requirements.*
Alternatives Analysis: Comparing air filter With Other Solutions
The search for effective air quality solutions often leads buyers to explore various alternatives to traditional air filters. Each option presents unique advantages and potential drawbacks, making it essential for B2B buyers to evaluate their specific needs against these alternatives.
Comparison Aspect | Air Filter | UV-C Light Systems | Electrostatic Precipitators |
---|---|---|---|
Performance | High (MERV ratings) | Very High (99%+) | Moderate to High (90%+) |
Cost | Moderate initial cost | Higher upfront cost | Higher initial investment |
Ease of Implementation | Easy to install | Requires professional setup | Moderate complexity |
Maintenance | Regular replacement | Low (annual service) | Medium (periodic cleaning) |
Best Use Case | Residential & commercial HVAC systems | Hospitals, labs, and high-traffic areas | Industrial settings, large facilities |
What Are the Advantages and Disadvantages of UV-C Light Systems?
UV-C light systems utilize ultraviolet light to eliminate airborne pathogens and allergens. This technology has gained popularity in environments requiring stringent air quality standards, such as hospitals and laboratories.
Pros:
– High effectiveness against a broad spectrum of microorganisms, including bacteria and viruses.
– Low maintenance needs, typically requiring only annual service.
Cons:
– Higher initial costs can be a barrier for smaller businesses.
– Installation complexity may necessitate professional help, increasing overall expenses.
How Do Electrostatic Precipitators Compare?
Electrostatic precipitators (ESPs) employ electrical fields to remove particles from the air, providing a non-filtering solution that can handle larger volumes of air.
Pros:
– Effective for large-scale applications, especially in industrial settings.
– Low ongoing costs since they can be cleaned and reused.
Cons:
– Higher initial investment compared to conventional air filters.
– Maintenance is required to ensure optimal performance, which can be more labor-intensive than simply changing filters.
Conclusion: How Should B2B Buyers Choose the Right Air Quality Solution?
When deciding among air filters, UV-C light systems, and electrostatic precipitators, B2B buyers should consider their specific operational needs and environmental conditions. For general applications, air filters offer a balanced solution with ease of maintenance and installation. Conversely, if the focus is on high-risk environments needing stringent air quality control, UV-C systems may provide the necessary level of protection. For larger industrial applications, electrostatic precipitators can be cost-effective over time, despite their higher upfront costs. Evaluating these factors will help buyers select the most suitable solution for their air quality management needs.
Essential Technical Properties and Trade Terminology for air filter
What Are the Essential Technical Properties of Air Filters for B2B Buyers?
Understanding the technical specifications of air filters is crucial for B2B buyers to ensure they select the right products for their applications. Below are some critical specifications that buyers should consider:
1. MERV Rating: What Does It Indicate?
The Minimum Efficiency Reporting Value (MERV) rating measures the effectiveness of air filters in trapping airborne particles. Ranging from 1 to 20, a higher MERV rating signifies better filtration efficiency. For example, filters with a MERV rating of 8 to 13 are suitable for residential use, while those rated above 13 are preferred for commercial and industrial applications. Buyers should choose filters with appropriate MERV ratings based on their specific air quality needs.
2. Filter Material: Which Options Are Best?
Air filters can be made from various materials, including fiberglass, polyester, and pleated media. Fiberglass filters are cost-effective but provide lower filtration efficiency. In contrast, pleated filters, often made from synthetic materials, offer higher surface area and better filtration capabilities. Selecting the right material is essential for balancing cost and performance, especially for businesses operating in environments requiring stringent air quality standards.
3. Filter Size: Why Is It Important?
Air filters come in numerous sizes, and selecting the correct dimensions is vital for ensuring optimal airflow and filtration efficiency. Common dimensions include 16x25x1 inches and 20x25x4 inches, but custom sizes are also available. Buyers should measure existing filters or consult HVAC professionals to avoid compatibility issues that could lead to inefficiencies or increased operational costs.
4. Airflow Resistance: What Should You Know?
Airflow resistance refers to the pressure drop across a filter when air passes through it. Filters with high airflow resistance can impede system efficiency and increase energy costs. Buyers should assess airflow resistance ratings to ensure they select filters that maintain system performance while providing adequate filtration.
5. Filter Lifespan: How Often Should They Be Changed?
The lifespan of an air filter can vary based on the type, usage, and environmental conditions. Typically, disposable filters need replacement every 1-3 months, while reusable filters may last up to a year. Understanding the expected lifespan helps businesses plan maintenance schedules and budget for replacements, minimizing downtime.
What Are the Common Trade Terminology and Jargon in the Air Filter Industry?
Familiarity with industry-specific terminology is essential for effective communication and negotiation. Here are some common terms that B2B buyers should know:
1. OEM (Original Equipment Manufacturer): What Does It Mean?
An OEM refers to a company that produces components that are used in another company’s products. In the air filter industry, OEM filters are designed to fit specific HVAC systems. Buyers often prefer OEM filters for guaranteed compatibility and performance.
2. MOQ (Minimum Order Quantity): Why Is It Relevant?
MOQ is the smallest quantity of a product that a supplier is willing to sell. This term is crucial for B2B buyers as it affects purchasing decisions, inventory management, and cash flow. Understanding the MOQ helps businesses negotiate better terms and assess supplier viability.
3. RFQ (Request for Quotation): How to Use It?
An RFQ is a document sent to suppliers to solicit pricing and terms for specific products or services. For air filter purchases, an RFQ helps buyers compare options from different suppliers, ensuring they secure the best value for their investment.
4. Incoterms: What Are They and Why Do They Matter?
Incoterms (International Commercial Terms) define the responsibilities of buyers and sellers in international transactions. Understanding these terms is essential for B2B buyers engaged in cross-border purchases of air filters, as they clarify shipping costs, insurance, and risk allocation.
5. Lead Time: What Should Buyers Expect?
Lead time refers to the period from placing an order to receiving the product. In the air filter industry, lead times can vary based on stock availability, production schedules, and shipping methods. Understanding lead times is crucial for effective supply chain management and maintaining operational efficiency.
By grasping these technical properties and trade terminologies, B2B buyers can make informed decisions, optimize their procurement processes, and ensure compliance with air quality standards.
Navigating Market Dynamics and Sourcing Trends in the air filter Sector
What Are the Key Trends Influencing the Global Air Filter Market?
The air filter market is experiencing dynamic shifts driven by various global factors, particularly relevant for international B2B buyers from Africa, South America, the Middle East, and Europe. Increasing awareness of air quality and its impact on health has heightened demand for high-efficiency particulate air (HEPA) filters and those with advanced MERV ratings. This trend is especially pronounced in regions with growing industrial activities and urbanization, where pollution levels are rising.
Technological advancements are also reshaping the market landscape. Innovations such as smart air filters equipped with IoT capabilities enable real-time monitoring of air quality and filter performance. These features are increasingly appealing to businesses looking to enhance operational efficiency and maintain compliance with health regulations. Additionally, the rise of e-commerce platforms simplifies the sourcing process for B2B buyers, allowing them to access a wider range of products and suppliers globally.
Emerging markets are witnessing a surge in investment from both local and international players aiming to establish manufacturing bases to cater to regional demands. Buyers in Africa and South America, for instance, can benefit from localized production, reducing lead times and shipping costs. This trend towards regional sourcing is also driven by the need for customized solutions tailored to specific market conditions.
How Important Is Sustainability and Ethical Sourcing in the Air Filter Sector?
Sustainability has become a central pillar in the air filter sector, influencing sourcing decisions among international B2B buyers. The environmental impact of manufacturing processes and the materials used in air filters is under increasing scrutiny. Buyers are now prioritizing suppliers that demonstrate a commitment to sustainable practices, such as using recycled materials or eco-friendly manufacturing processes.
Ethical sourcing is equally critical, as businesses strive to ensure that their supply chains are transparent and responsible. Certifications such as ENERGY STAR and Green Seal are becoming key indicators for buyers looking to validate the sustainability of their purchases. These certifications not only signify compliance with environmental standards but also enhance a company’s reputation and appeal to a growing segment of eco-conscious consumers.
Moreover, buyers should consider the lifecycle of air filter products, including end-of-life disposal and recyclability. Engaging with suppliers who offer take-back programs or biodegradable materials can significantly reduce environmental footprints and align with corporate sustainability goals. This shift towards green procurement strategies is not just beneficial for the planet; it can also lead to cost savings through improved energy efficiency and reduced waste.
What Is the Historical Context of Air Filter Development for B2B Buyers?
The evolution of the air filter industry has been shaped by technological advancements and changing consumer preferences. Initially, air filters were primarily simple mechanical devices designed to trap dust and particulates. However, as air quality concerns grew, particularly in industrialized nations, the development of more sophisticated filtration systems became necessary. HEPA filters emerged in the mid-20th century, revolutionizing air purification by capturing up to 99.97% of airborne particles.
In recent decades, the focus has expanded beyond mere filtration to include aspects such as energy efficiency and environmental impact. The introduction of smart technology into air filters is a testament to the industry’s responsiveness to market demands, enabling real-time data collection and analysis. This historical context highlights the importance of innovation and adaptability, which are crucial for B2B buyers seeking to make informed sourcing decisions in a rapidly evolving marketplace.
Frequently Asked Questions (FAQs) for B2B Buyers of air filter
-
How do I choose the right air filter for my business needs?
Choosing the right air filter involves assessing your specific requirements, such as the type of contaminants you want to filter out, the size of your HVAC system, and your budget. Look for filters with a suitable MERV (Minimum Efficiency Reporting Value) rating; a higher rating indicates better filtration. Additionally, consider the filter’s size and depth to ensure compatibility with your system. Consulting with a filtration expert can provide tailored recommendations based on your operational environment. -
What is the best air filter type for industrial applications?
For industrial applications, HEPA filters are often the best choice due to their high efficiency in capturing airborne particles, including dust, allergens, and pathogens. Depending on your specific needs, you may also consider filters with activated carbon to absorb odors and volatile organic compounds (VOCs). Evaluate your facility’s air quality requirements, as well as local regulations, to determine the most effective filter type for your operations. -
How can I verify the quality of air filters from suppliers?
To verify the quality of air filters, request certification documents from suppliers that demonstrate compliance with industry standards, such as ASHRAE or ISO. Additionally, check customer reviews and testimonials to gauge satisfaction levels. You can also conduct independent testing of samples to assess their performance in your specific environment. Establishing a quality assurance protocol within your procurement process will help ensure you consistently receive high-quality products. -
What are the typical minimum order quantities (MOQ) for air filters?
Minimum order quantities (MOQ) for air filters can vary widely based on the supplier and the type of filter. Generally, MOQs range from 50 to several hundred units. When sourcing from international suppliers, it’s essential to discuss MOQs upfront to understand potential volume discounts and shipping considerations. If you require smaller quantities, consider suppliers that offer custom or made-to-order options. -
What payment terms should I expect when sourcing air filters internationally?
Payment terms for international orders typically include options such as advance payment, letters of credit, or net payment terms (e.g., net 30 or net 60 days). Discuss these terms with potential suppliers to find a mutually agreeable arrangement. Be aware of any additional costs related to currency conversion and international banking fees, and ensure you understand the implications of your chosen payment method on cash flow and risk management. -
How do I handle logistics and shipping when importing air filters?
When importing air filters, coordinate closely with your suppliers and logistics providers to ensure smooth shipping processes. Evaluate shipping options, including air freight for faster delivery and sea freight for cost savings. Consider customs regulations in your country to avoid delays and additional fees. Establishing a reliable supply chain with clear communication will help mitigate risks and ensure timely delivery. -
What customization options are available for air filters?
Many suppliers offer customization options for air filters, including size, MERV rating, and filter media. Custom filters can be tailored to meet specific air quality needs or fit unique HVAC systems. When discussing customization with suppliers, provide detailed specifications and inquire about lead times and additional costs associated with custom orders. This ensures that you receive a product that meets your precise requirements. -
How often should I replace air filters in my facility?
The frequency of air filter replacement depends on several factors, including the type of filter used, the level of contaminants in the environment, and the specific HVAC system. Generally, filters should be checked monthly and replaced every 1-3 months for standard use. In high-traffic or industrial environments, more frequent changes may be necessary. Implementing a regular maintenance schedule can improve air quality and system efficiency, ultimately reducing operational costs.
Important Disclaimer & Terms of Use
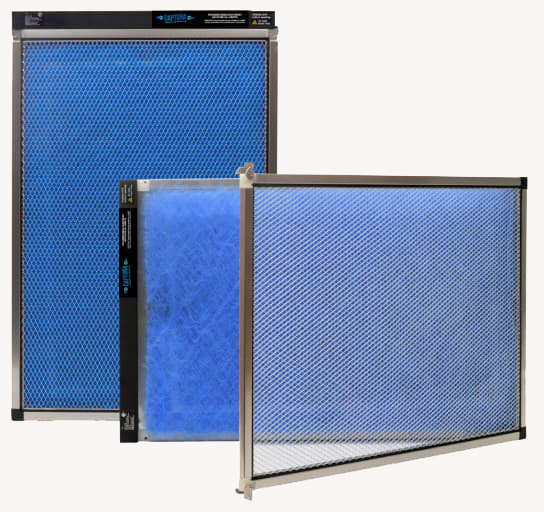
A stock image related to air filter.
⚠️ Important Disclaimer
The information provided in this guide, including content regarding manufacturers, technical specifications, and market analysis, is for informational and educational purposes only. It does not constitute professional procurement advice, financial advice, or legal advice.
While we have made every effort to ensure the accuracy and timeliness of the information, we are not responsible for any errors, omissions, or outdated information. Market conditions, company details, and technical standards are subject to change.
B2B buyers must conduct their own independent and thorough due diligence before making any purchasing decisions. This includes contacting suppliers directly, verifying certifications, requesting samples, and seeking professional consultation. The risk of relying on any information in this guide is borne solely by the reader.
Strategic Sourcing Conclusion and Outlook for air filter
What Are the Key Takeaways for B2B Buyers in Air Filter Sourcing?
As international B2B buyers navigate the complexities of sourcing air filters, several strategic insights emerge. Firstly, understanding the diverse MERV ratings is crucial; selecting the appropriate rating can significantly impact indoor air quality and operational efficiency. Buyers should also consider the availability of custom sizes to meet specific needs, particularly in markets with unique HVAC systems.
Additionally, leveraging subscriptions for regular filter deliveries can enhance supply chain efficiency, ensuring that replacements are timely and preventing operational disruptions. Establishing relationships with multiple suppliers across Africa, South America, the Middle East, and Europe can also provide flexibility and resilience against potential market fluctuations.
How Can International Buyers Prepare for Future Air Filter Trends?
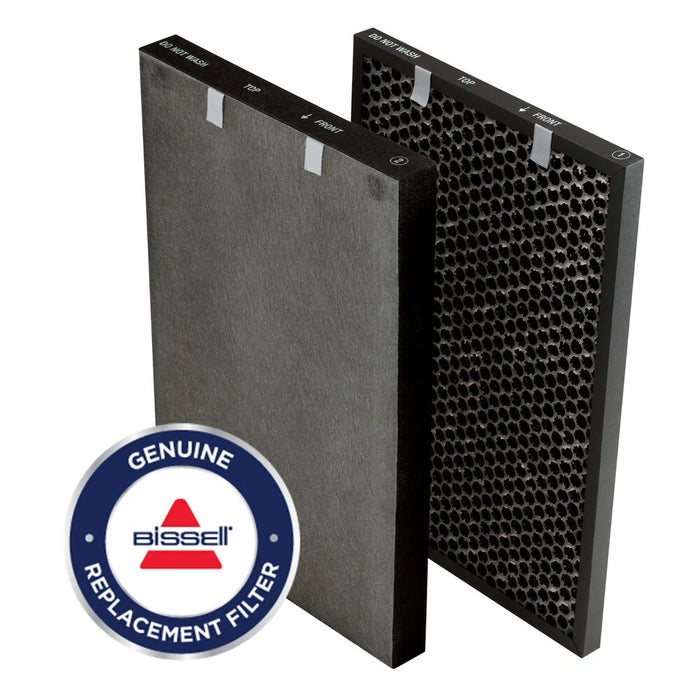
A stock image related to air filter.
Looking ahead, the demand for sustainable and energy-efficient air filtration solutions is set to rise. Buyers should proactively seek suppliers who prioritize eco-friendly materials and manufacturing processes. Engaging in strategic sourcing will not only help in securing high-quality products but also align with global sustainability goals.
In conclusion, it is imperative for B2B buyers to remain informed about market trends and supplier innovations. By adopting a strategic sourcing approach, companies can enhance their operational efficiency and contribute to a healthier environment. Start exploring your options today to secure the best air filtration solutions for your needs.