Discover Cost-Saving Benefits of Aluminium Casting (2025)
Introduction: Navigating the Global Market for aluminium casting
In today’s fast-paced global market, sourcing high-quality aluminium casting solutions poses a significant challenge for international B2B buyers. With the growing demand for lightweight and durable components across various industries, understanding the nuances of aluminium casting becomes essential. This comprehensive guide delves into the different types of aluminium casting processes, including die casting, investment casting, and sand casting, while also exploring their specific applications in sectors such as automotive, aerospace, and construction.
Navigating the complexities of supplier vetting, cost considerations, and quality assurance can be daunting, especially for businesses located in Africa, South America, the Middle East, and Europe. This guide aims to empower B2B buyers by providing actionable insights into each aspect of the aluminium casting supply chain. From identifying reliable suppliers to understanding the factors that influence pricing, readers will gain the knowledge needed to make informed purchasing decisions that align with their operational needs and budget constraints.
By equipping international buyers with the tools to assess their options effectively, this guide not only enhances procurement strategies but also fosters long-term partnerships with reputable manufacturers. Whether you are in South Africa looking for innovative casting solutions or in Saudi Arabia seeking to optimize production processes, this resource is designed to streamline your journey in the global aluminium casting market.
Understanding aluminium casting Types and Variations
Type Name | Key Distinguishing Features | Primary B2B Applications | Brief Pros & Cons for Buyers |
---|---|---|---|
Die Casting | High precision; uses steel dies; suitable for large volumes | Automotive, aerospace, consumer goods | Pros: High accuracy, smooth surface finish. Cons: High initial tooling costs. |
Investment Casting | Uses a sacrificial model; ideal for complex shapes | Aerospace, medical devices, art pieces | Pros: Excellent detail and surface finish. Cons: Slower production rates. |
Sand Casting | Versatile; uses sand molds; suitable for low to medium volumes | Heavy machinery, automotive components | Pros: Cost-effective for low volumes. Cons: Lower precision and surface finish. |
Permanent Mold Casting | Reusable molds; good for medium production runs | Electrical housings, automotive parts | Pros: Good surface quality, faster than sand casting. Cons: Limited design complexity. |
Low-Pressure Casting | Uses lower pressure to fill molds; reduces porosity | Automotive and aerospace components | Pros: Reduced defects, better mechanical properties. Cons: Slower than die casting. |
What are the characteristics and suitability of Die Casting for B2B buyers?
Die casting is characterized by its use of hardened steel molds, which allow for high precision and repeatability in production. This method is particularly suitable for large-scale manufacturing, making it ideal for industries such as automotive and aerospace where component accuracy is critical. B2B buyers should consider the initial investment in tooling, as it can be significant, but the long-term benefits include reduced per-part costs and consistent quality.
How does Investment Casting stand out in terms of complexity and detail?
Investment casting involves creating a wax model of the desired part, which is then coated in a ceramic shell. This method is best suited for complex and intricate designs, making it popular in aerospace and medical device manufacturing. B2B buyers should weigh the advantages of exceptional detail and surface finish against the slower production rates and higher costs associated with this process.
Why is Sand Casting a versatile option for various industries?
Sand casting is known for its versatility and cost-effectiveness, particularly for low to medium production volumes. It employs sand molds, allowing for the easy creation of custom shapes. This method is frequently used in industries like heavy machinery and automotive components. Buyers should consider that while sand casting is economical, it may result in lower precision and surface finish compared to other methods.
What benefits does Permanent Mold Casting offer for medium production runs?
Permanent mold casting utilizes reusable molds, making it a favorable option for medium production runs. It provides good surface quality and faster cycle times compared to sand casting, making it suitable for applications like electrical housings and automotive parts. Buyers should assess the balance between mold costs and production efficiency, as this method allows for a more economical approach over time.
How does Low-Pressure Casting enhance mechanical properties for B2B applications?
Low-pressure casting is distinguished by its technique of filling molds at lower pressures, which minimizes gas entrapment and porosity. This results in superior mechanical properties, making it ideal for critical applications in the automotive and aerospace sectors. B2B buyers should evaluate the slower production speed of this method against the enhanced quality and durability of the final products, particularly for high-stakes applications.
Key Industrial Applications of aluminium casting
Industry/Sector | Specific Application of Aluminium Casting | Value/Benefit for the Business | Key Sourcing Considerations for this Application |
---|---|---|---|
Automotive | Engine Blocks and Cylinder Heads | Lightweight components improve fuel efficiency and reduce emissions. | Ensure high precision and low porosity in castings. |
Aerospace | Aircraft Structural Components | High strength-to-weight ratio enhances performance and fuel efficiency. | Compliance with stringent aerospace standards and certifications. |
Electrical and Electronics | Heat Sinks and Housings | Excellent thermal conductivity ensures efficient heat dissipation. | Consider sourcing alloys with specific thermal properties. |
Construction | Window Frames and Structural Supports | Durability and corrosion resistance enhance longevity and reduce maintenance costs. | Evaluate local suppliers for material availability and cost-effectiveness. |
Marine | Boat Hulls and Components | Lightweight yet strong materials improve speed and maneuverability. | Assess the impact of saltwater corrosion on material selection. |
How Is Aluminium Casting Used in the Automotive Industry?
In the automotive sector, aluminium casting is crucial for producing engine blocks and cylinder heads, which are essential for vehicle performance. These components benefit from aluminium’s lightweight nature, contributing to enhanced fuel efficiency and reduced emissions. International buyers must ensure that suppliers can deliver high-precision castings with minimal porosity, as defects can severely affect engine performance and longevity. Additionally, sourcing from regions with established automotive manufacturing capabilities, such as South Africa and Brazil, can offer logistical advantages.
What Are the Aerospace Applications of Aluminium Casting?
Aluminium casting plays a vital role in the aerospace industry, particularly in the fabrication of structural components for aircraft. The high strength-to-weight ratio of aluminium allows for lighter aircraft designs, improving fuel efficiency and overall performance. Buyers in this sector should prioritize suppliers who comply with stringent aerospace standards and certifications, ensuring the integrity and safety of components. Furthermore, sourcing from European manufacturers can provide access to advanced casting technologies and quality assurance processes that meet international aviation regulations.
How Is Aluminium Casting Beneficial in Electrical and Electronics?
In the electrical and electronics industry, aluminium casting is widely used for manufacturing heat sinks and housings. The excellent thermal conductivity of aluminium ensures efficient heat dissipation, which is critical for the performance and reliability of electronic devices. International B2B buyers should focus on sourcing alloys that possess specific thermal properties suitable for their applications. Additionally, considering suppliers with expertise in high-volume production can help reduce costs while maintaining quality standards, especially in fast-growing markets in the Middle East and South America.
What Role Does Aluminium Casting Play in Construction?
Aluminium casting is essential in the construction industry for producing window frames and structural supports. The durability and corrosion resistance of cast aluminium enhance the longevity of these components, ultimately reducing maintenance costs for builders and developers. Buyers should evaluate local suppliers for material availability and cost-effectiveness, particularly in regions like Africa, where construction is booming. Understanding the local market dynamics and potential supply chain challenges can also help buyers make informed decisions when sourcing aluminium castings.
How Is Aluminium Casting Utilized in Marine Applications?
In the marine sector, aluminium casting is employed to manufacture boat hulls and various components. The lightweight yet robust characteristics of aluminium enhance speed and maneuverability, making it a preferred material for marine applications. International buyers must assess the impact of saltwater corrosion on material selection, ensuring that the castings used are suitable for harsh marine environments. Moreover, sourcing from regions with established marine manufacturing industries, such as the Mediterranean countries, can provide valuable insights into best practices and material innovations.
3 Common User Pain Points for ‘aluminium casting’ & Their Solutions
Scenario 1: Overcoming Production Delays in Aluminum Casting
The Problem:
One of the most pressing challenges B2B buyers face in aluminum casting is production delays. This issue often arises due to several factors, including inadequate supplier capabilities, unexpected quality control failures, and long lead times for tooling and mold fabrication. For international buyers, particularly in regions like Africa and South America, these delays can severely disrupt supply chains, leading to missed deadlines and increased costs. Furthermore, when dealing with intricate designs or custom components, the risk of miscommunication between the buyer and supplier can exacerbate these delays, resulting in frustration and financial losses.
The Solution:
To mitigate production delays, it’s crucial for buyers to establish clear communication channels with suppliers from the outset. Detailed project specifications should be provided, including drawings, material requirements, and expected timelines. Additionally, conducting thorough due diligence on potential suppliers is essential. This includes evaluating their production capabilities, quality assurance processes, and past performance on similar projects.
Investing in a supplier who utilizes advanced technology—such as computer-aided design (CAD) and simulation software—can also enhance precision and reduce the likelihood of delays caused by design flaws. Lastly, establishing a contingency plan that includes alternative suppliers can provide a safety net against unexpected disruptions.
Scenario 2: Navigating Quality Issues in Aluminum Casting
The Problem:
Quality inconsistencies in aluminum castings are a common pain point for B2B buyers. Issues such as porosity, dimensional inaccuracies, and surface defects can lead to significant challenges in product performance and safety. This is particularly critical in sectors like automotive and aerospace, where the integrity of components is paramount. When castings do not meet stringent quality standards, it can result in costly recalls, reputational damage, and operational setbacks.
The Solution:
To ensure high-quality aluminum castings, buyers should prioritize working with suppliers who adhere to industry standards such as ISO 9001 for quality management. Requesting samples and conducting initial audits can provide valuable insights into a supplier’s quality control processes. Furthermore, employing non-destructive testing (NDT) methods during production can help identify potential defects early on.
Investing in advanced alloy materials that minimize common casting defects is another proactive approach. Collaborating closely with suppliers during the design phase can also lead to optimized casting techniques that enhance quality, such as using pressure die casting for complex geometries, which typically results in fewer defects compared to traditional sand casting methods.
Scenario 3: Managing Cost Overruns in Aluminum Casting Projects
The Problem:
Cost overruns are a pervasive issue in aluminum casting projects, often arising from unexpected material price fluctuations, inefficient production methods, and insufficient project planning. For buyers in regions with volatile economies, such as parts of the Middle East and South America, these financial uncertainties can significantly impact budgeting and profitability. Additionally, if buyers fail to account for additional costs related to tooling and post-casting processes, they may find themselves facing unanticipated expenses that strain resources.
The Solution:
To effectively manage costs, buyers should conduct a thorough market analysis to understand current pricing trends for aluminum and its alloys. Establishing fixed-price contracts with suppliers can help mitigate the risk of price increases. Additionally, incorporating value engineering principles during the design phase can lead to more cost-effective production methods without sacrificing quality.
Engaging in long-term partnerships with reliable suppliers can also lead to better pricing agreements and reduced material costs over time. Furthermore, buyers should consider investing in training for their teams on efficient project management practices to better predict costs and streamline production processes, ultimately reducing waste and ensuring that projects stay within budget.
Strategic Material Selection Guide for aluminium casting
What Are the Key Materials Used in Aluminium Casting?
When selecting materials for aluminium casting, it is crucial to understand the properties, advantages, and limitations of various alloys. This knowledge helps international B2B buyers make informed decisions that align with their specific application needs, production capabilities, and market standards.
Which Aluminium Alloys Are Commonly Used in Casting?
1. A356 Alloy
Key Properties:
A356 is known for its excellent corrosion resistance and good mechanical properties. It has a melting point of around 600°C and offers a tensile strength of approximately 310 MPa. This alloy is particularly suitable for applications requiring good weldability and thermal conductivity.
Pros & Cons:
The primary advantage of A356 is its excellent castability, making it ideal for complex shapes. However, it can be more expensive than other alloys, and its ductility is lower compared to some alternatives.
Impact on Application:
A356 is often used in automotive and aerospace applications where weight reduction is critical. Its corrosion resistance makes it suitable for marine environments, but it may not perform well under high-temperature conditions beyond its limits.
Considerations for International Buyers:
Buyers from regions like South Africa and Saudi Arabia should ensure compliance with international standards such as ASTM and DIN. The availability of A356 may vary, and local suppliers should be evaluated for their quality assurance processes.
2. A380 Alloy
Key Properties:
A380 is characterized by its excellent fluidity and high strength. It has a melting point of around 600-650°C and offers a tensile strength of about 310 MPa. This alloy is particularly known for its good wear resistance.
Pros & Cons:
The key advantage of A380 is its suitability for high-volume production due to its rapid solidification and low porosity. However, it is less resistant to corrosion compared to A356, making it less suitable for harsh environments.
Impact on Application:
A380 is widely used in the automotive industry for engine components and transmission housings. Its wear resistance makes it ideal for applications that experience friction but may be limited in corrosive environments.
Considerations for International Buyers:
B2B buyers in Europe and South America should consider the alloy’s compliance with local regulations and standards. The cost of A380 can vary significantly based on the supplier’s location and market conditions.
3. A413 Alloy
Key Properties:
A413 is known for its exceptional fluidity and is often used for intricate designs. It has a melting point of around 600°C and provides a tensile strength of approximately 240 MPa.
Pros & Cons:
The main advantage of A413 is its ability to produce thin-walled components, which reduces weight without sacrificing strength. However, it is less ductile than other alloys, which may limit its applications in high-stress environments.
Impact on Application:
This alloy is primarily used in the production of complex castings in the aerospace and electronics industries. Its fluidity allows for detailed designs, but its lower strength limits its use in structural applications.
Considerations for International Buyers:
For buyers in the Middle East and Africa, understanding the local supply chain for A413 is essential. Compliance with international standards like JIS may also be necessary for specific applications.
Summary Table of Common Aluminium Casting Materials
Material | Typical Use Case for Aluminium Casting | Key Advantage | Key Disadvantage/Limitation | Relative Cost (Low/Med/High) |
---|---|---|---|---|
A356 | Automotive and aerospace components | Excellent corrosion resistance | Higher cost compared to other alloys | Medium |
A380 | Engine components and transmission housings | High fluidity and low porosity | Less corrosion resistance | Medium |
A413 | Intricate castings in aerospace and electronics | Exceptional fluidity for detailed designs | Lower ductility limits applications | Medium |
By understanding these materials and their implications, international B2B buyers can make strategic choices that enhance their manufacturing processes and align with their market demands.
In-depth Look: Manufacturing Processes and Quality Assurance for aluminium casting
What Are the Main Stages of the Aluminum Casting Manufacturing Process?
Aluminum casting involves several critical stages, each essential for ensuring the final product meets quality and performance specifications. Understanding these stages can help B2B buyers from Africa, South America, the Middle East, and Europe make informed decisions about suppliers and processes.
How Is Material Prepared for Aluminum Casting?
The first step in aluminum casting is material preparation, which begins with the selection of aluminum alloys. The choice of alloy affects the final properties of the cast product, such as strength, ductility, and corrosion resistance. Common alloys include AlSi (Silicon) for casting and AlMg (Magnesium) for better corrosion resistance.
Once the appropriate alloy is selected, it undergoes melting in a furnace at temperatures typically ranging from 660°C to 750°C. This is followed by degassing, a crucial process to remove impurities such as hydrogen, which can lead to porosity in the final product. Proper material preparation ensures that the molten aluminum has the desired characteristics for casting.
What Techniques Are Used in the Forming Stage?
The forming stage involves pouring the molten aluminum into molds to create the desired shape. There are several techniques for this:
-
Die Casting: This method uses high pressure to force molten aluminum into a steel mold. Die casting is ideal for high-volume production and yields parts with excellent dimensional accuracy and surface finish.
-
Sand Casting: A more traditional method, sand casting involves packing sand around a pattern to form a mold. This technique is versatile and suitable for low to medium production volumes but may not achieve the same precision as die casting.
-
Investment Casting: This process uses a wax or polymer pattern that is melted away to create a cavity for molten aluminum. Investment casting is excellent for producing intricate designs and high-value components, albeit at a higher cost.
These forming techniques can significantly impact the characteristics of the finished product, influencing factors such as strength, weight, and finish quality.
How Is Assembly and Finishing Conducted in Aluminum Casting?
After the casting process, assembly and finishing are crucial for preparing the component for use. This may involve machining operations to achieve precise dimensions, surface treatments for enhanced corrosion resistance, and assembly of multiple cast parts into a final product.
Machining can include drilling, milling, and grinding, depending on the specifications of the end product. Surface treatments such as anodizing or painting enhance the aesthetic appeal and performance of aluminum parts, providing additional resistance to environmental factors.
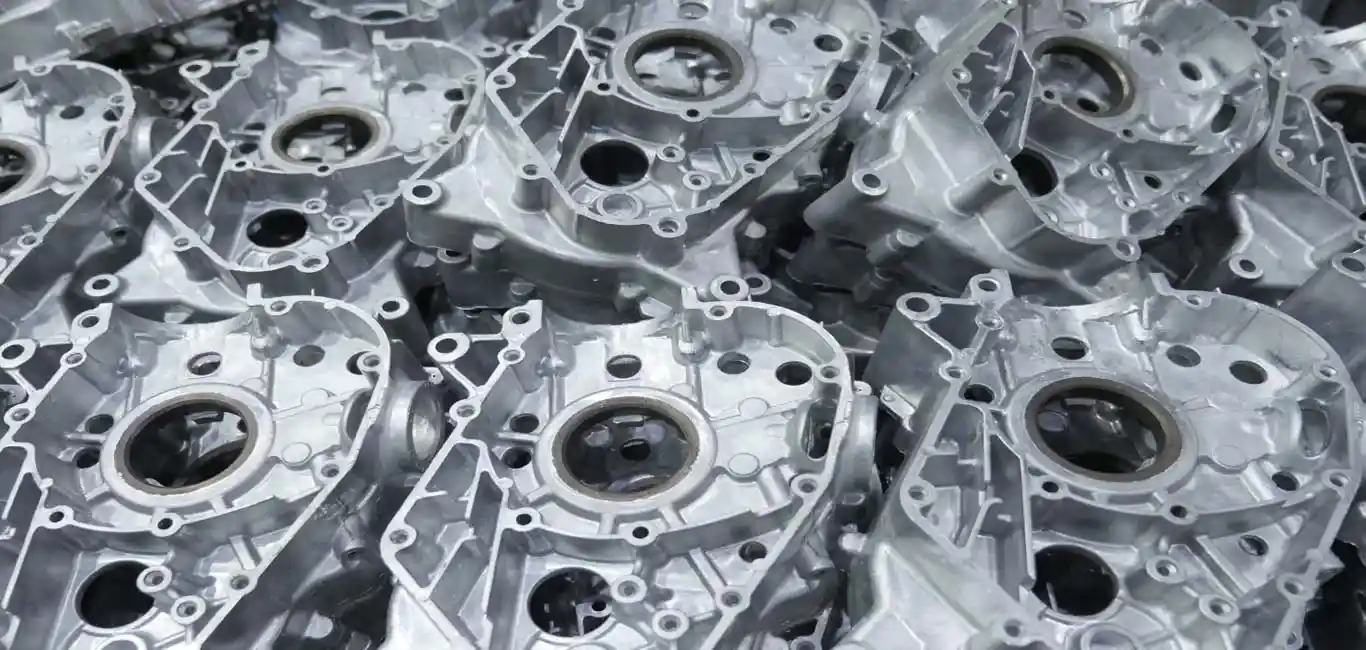
A stock image related to aluminium casting.
What International Standards Guide Quality Assurance in Aluminum Casting?
Quality assurance is paramount in aluminum casting, especially for international B2B buyers concerned about product reliability and compliance. Key international standards include:
-
ISO 9001: This standard outlines the requirements for a quality management system, ensuring consistent quality in products and services. Suppliers adhering to ISO 9001 demonstrate a commitment to quality and customer satisfaction.
-
CE Marking: For products sold within the European Economic Area, CE marking indicates conformity with health, safety, and environmental protection standards.
-
API Standards: In industries like oil and gas, API standards ensure that products meet rigorous quality and safety requirements.
These standards are essential benchmarks for B2B buyers to consider when evaluating potential suppliers.
What Are the Key Quality Control Checkpoints in Aluminum Casting?
Quality control (QC) in aluminum casting is implemented at various checkpoints throughout the manufacturing process. These include:
-
Incoming Quality Control (IQC): Before production begins, incoming materials are inspected to ensure they meet specifications. This includes verifying alloy composition and checking for defects.
-
In-Process Quality Control (IPQC): During the casting process, inspections are conducted to monitor parameters such as temperature, pressure, and flow rates. This helps identify issues early and ensures consistency throughout production.
-
Final Quality Control (FQC): After casting, finished parts undergo rigorous testing to ensure they meet design specifications. This may involve dimensional checks, visual inspections, and mechanical testing for strength and durability.
What Common Testing Methods Are Used in Aluminum Casting Quality Assurance?
Several testing methods are employed to ensure the quality and performance of aluminum castings:
-
Ultrasonic Testing (UT): This non-destructive testing method uses high-frequency sound waves to detect internal flaws and voids in the casting.
-
X-ray Inspection: Similar to UT, X-ray inspection identifies internal defects, such as inclusions or voids, that may compromise the integrity of the casting.
-
Tensile Testing: This mechanical test evaluates the strength and ductility of the aluminum casting, ensuring it meets specified performance criteria.
B2B buyers should request detailed reports of these tests from suppliers to verify the quality of the cast components.
How Can B2B Buyers Verify Supplier Quality Control Processes?
For international B2B buyers, verifying a supplier’s quality control processes is crucial. Here are actionable steps:
-
Conduct Audits: Regular audits of suppliers can provide insights into their manufacturing processes and adherence to quality standards. This can be done in-person or through third-party auditing services.
-
Request QC Reports: Suppliers should provide documentation of their quality control measures, including IQC, IPQC, and FQC results. These reports should detail the testing methods used and the outcomes of each stage.
-
Engage Third-Party Inspectors: Hiring independent inspectors to evaluate the manufacturing process and the final products can provide an unbiased assessment of quality.
What Are the Quality Control Nuances for International B2B Buyers?
International B2B buyers must consider the following nuances when assessing quality control in aluminum casting:
-
Cultural Differences: Different regions may have varying standards of quality and manufacturing practices. Buyers should be aware of these differences and ensure that suppliers meet their specific requirements.
-
Regulatory Compliance: Ensure that suppliers are compliant with the regulations specific to your region or industry, such as environmental standards or safety regulations.
-
Traceability: Requesting traceability documentation for materials and processes can help ensure that all components meet the required quality standards.
By understanding the manufacturing processes and quality assurance protocols in aluminum casting, B2B buyers can make informed decisions, ensuring they procure high-quality products that meet their operational needs.
Practical Sourcing Guide: A Step-by-Step Checklist for ‘aluminium casting’
The following practical sourcing guide provides B2B buyers with a clear checklist for procuring aluminum casting services and products. This step-by-step approach ensures that buyers can effectively evaluate their needs, identify suitable suppliers, and secure high-quality aluminum castings that meet their specific requirements.
Step 1: Define Your Technical Specifications
Establishing precise technical specifications is crucial for successful aluminum casting procurement. Clearly outline the dimensions, tolerances, and material properties required for your castings. This will help potential suppliers understand your needs and provide accurate quotes.
- Consider alloy types: Different aluminum alloys possess varying properties, such as strength and corrosion resistance. Identify which alloy best suits your application.
- Detail surface finishes: Specify whether you need standard finishes or custom treatments to enhance durability or aesthetics.
Step 2: Identify Your Production Volume Needs
Understanding your production volume requirements is essential for selecting the right supplier. Different casting methods, like die casting or sand casting, cater to varying production scales.
- Low vs. high volume: Determine if you need a few prototypes or thousands of units. Die casting is ideal for high-volume production, while sand casting suits lower volumes.
- Future scalability: Consider suppliers who can accommodate future increases in demand without compromising quality.
Step 3: Evaluate Potential Suppliers
Thoroughly vet potential suppliers to ensure they can meet your specific casting requirements. Request company profiles, case studies, and references from buyers in similar industries or regions.
- Check for industry experience: Look for suppliers with a proven track record in aluminum casting, especially in your sector.
- Assess production capabilities: Ensure the supplier has the necessary technology and equipment to produce high-quality castings.
Step 4: Verify Supplier Certifications
Certifications provide assurance that your supplier meets industry standards for quality and safety. Verify that potential suppliers possess relevant certifications, such as ISO 9001 or ISO/TS 16949.
- Quality control processes: Ask about the supplier’s quality management practices and how they ensure consistent production quality.
- Compliance with regulations: Ensure the supplier complies with local and international regulations, especially if you are sourcing from different regions.
Step 5: Request Samples and Prototypes
Before making a large commitment, request samples or prototypes of your desired aluminum casting. This allows you to assess the supplier’s capabilities and the quality of their work.
- Evaluate quality and precision: Inspect the samples for adherence to your specifications and overall craftsmanship.
- Test performance: If applicable, conduct performance testing to ensure the casting meets functional requirements.
Step 6: Discuss Lead Times and Delivery Logistics
Establish clear expectations regarding lead times and delivery logistics. Understanding these aspects will help you plan your production schedule effectively.
- Lead time transparency: Ask suppliers for estimated production times and any factors that may affect them.
- Shipping and handling: Discuss logistics, including shipping options and costs, to ensure timely delivery of your castings.
Step 7: Negotiate Pricing and Payment Terms
Finally, engage in discussions regarding pricing and payment terms. A transparent negotiation process helps establish a mutually beneficial relationship with your supplier.
- Compare quotes: Don’t settle for the first quote. Obtain multiple quotes to ensure competitive pricing.
- Payment flexibility: Discuss payment terms that suit your financial planning, such as upfront payments or milestone-based payments.
By following this comprehensive checklist, international B2B buyers can streamline their sourcing process for aluminum casting, ensuring they find the right supplier to meet their needs while maintaining quality and efficiency.
Comprehensive Cost and Pricing Analysis for aluminium casting Sourcing
What Are the Key Cost Components in Aluminium Casting Sourcing?
When sourcing aluminium casting, understanding the cost structure is essential for B2B buyers. The primary cost components include:
-
Materials: The cost of raw materials, particularly aluminium alloys, is a significant factor. Prices can fluctuate based on global demand, mining conditions, and geopolitical factors. Buyers should consider sourcing from regions with stable pricing and reliable supply chains.
-
Labor: Labor costs vary widely by region and can impact overall pricing. In countries with higher wages, such as those in Europe, the labor component may be more substantial compared to regions like Africa or South America. It’s vital to account for the skill level required for casting processes, which can also influence labor costs.
-
Manufacturing Overhead: This includes utilities, facility maintenance, and administrative expenses. Efficient production processes can help minimize overhead costs, but buyers should be aware that cheaper manufacturing may compromise quality.
-
Tooling: Tooling costs are often significant, especially for die casting, which requires precise, durable molds. The initial investment can be high, but it is amortized over the production run. Buyers should evaluate the tooling costs against the expected volume to ensure cost-effectiveness.
-
Quality Control (QC): Ensuring that the cast parts meet specific standards incurs additional costs. Quality assurance processes, certifications, and testing can add to the overall expense but are crucial for maintaining product integrity.
-
Logistics: Transportation costs, including shipping and customs duties, can significantly affect the final price. International buyers should consider the Incoterms that dictate responsibility for shipping costs and risks.
-
Margin: Suppliers will typically add a profit margin to cover their costs and risks. This margin can vary based on the supplier’s market positioning and the complexity of the casting requirements.
What Influences Pricing in Aluminium Casting?
Several factors can influence the pricing of aluminium casting, particularly for international buyers:
-
Volume and Minimum Order Quantity (MOQ): Pricing often decreases with higher volumes. Buyers should negotiate MOQs to ensure they receive favorable pricing without overcommitting to inventory.
-
Specifications and Customization: Custom parts typically incur higher costs due to the complexity involved in manufacturing. Buyers must weigh the benefits of customization against the potential for increased costs.
-
Materials and Quality Certifications: The choice of aluminium alloy can affect the price. Alloys with specific properties or certifications may be more expensive. Buyers should ensure that the material chosen meets their performance needs without unnecessary expenditure.
-
Supplier Factors: Supplier reliability, reputation, and production capacity can all impact pricing. Established suppliers may charge more but offer better quality assurance and service.
-
Incoterms: Understanding the terms of shipping and delivery can help buyers anticipate costs. Different Incoterms can shift responsibilities and risks, affecting the overall price.
What Tips Can Help Buyers Negotiate Better Prices for Aluminium Casting?
For B2B buyers, particularly from Africa, South America, the Middle East, and Europe, adopting strategic negotiation practices can lead to significant cost savings:
-
Negotiate Terms and Prices: Engage suppliers in discussions about pricing structures and potential discounts for larger orders or long-term contracts.
-
Focus on Total Cost of Ownership (TCO): Evaluate not only the initial purchase price but also the long-term costs associated with the casting, including maintenance and potential failures.
-
Be Informed About Market Trends: Stay updated on aluminium market conditions and pricing trends to leverage this knowledge in negotiations.
-
Assess Quality vs. Cost: While it may be tempting to opt for the lowest price, consider the long-term implications of quality. Lower-quality castings may lead to higher costs over time due to failures or replacements.
Disclaimer on Pricing
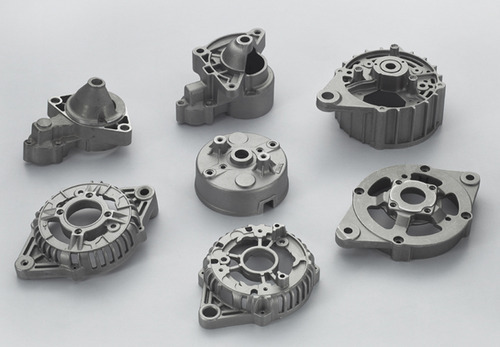
A stock image related to aluminium casting.
Prices for aluminium casting can vary widely based on the factors mentioned above. This analysis provides a general overview, and buyers are encouraged to conduct thorough research and obtain multiple quotes to ensure competitive pricing tailored to their specific needs.
Alternatives Analysis: Comparing aluminium casting With Other Solutions
When exploring options for manufacturing processes, it’s crucial for international B2B buyers to evaluate alternatives to aluminum casting. This section provides a comparative analysis of aluminum casting against viable alternative solutions, namely steel fabrication and plastic injection molding. By understanding the strengths and weaknesses of each method, buyers can make informed decisions that align with their production requirements.
Comparison Aspect | Aluminium Casting | Steel Fabrication | Plastic Injection Molding |
---|---|---|---|
Performance | High precision, excellent stiffness-to-weight ratio. | Strong, durable, and suitable for heavy loads. | Fast production of complex shapes, good surface finish. |
Cost | Moderate initial costs; cost-effective for high volumes. | Generally higher due to material costs and labor. | Lower material costs but requires expensive molds. |
Ease of Implementation | Requires specialized knowledge and equipment; setup time can vary. | Straightforward but labor-intensive; skilled labor required. | High initial setup time and costs but streamlined once established. |
Maintenance | Low maintenance for finished products; care needed during casting. | Regular maintenance of tools and equipment required. | Minimal maintenance once molds are created. |
Best Use Case | Complex shapes, lightweight components in automotive and aerospace. | Structural components, heavy machinery, and construction. | High-volume production of consumer goods and automotive parts. |
What are the Pros and Cons of Steel Fabrication Compared to Aluminium Casting?
Steel fabrication involves shaping and assembling steel into desired forms, often through cutting, bending, and welding. The primary advantage of this method lies in the strength and durability of steel, making it ideal for heavy-duty applications such as construction and machinery. However, steel’s weight can be a drawback for applications requiring lightweight materials. Additionally, the cost of steel can be higher, especially with labor-intensive processes. B2B buyers in sectors like construction may favor steel for its robustness, while those in automotive or aerospace might lean towards aluminum for its lighter weight.
How Does Plastic Injection Molding Compare to Aluminium Casting?
Plastic injection molding is a manufacturing process that involves injecting molten plastic into a mold to create a wide variety of parts. This method excels in producing complex shapes quickly and at lower material costs compared to aluminum casting. However, the initial investment in molds can be significant, and the process may not be suitable for high-temperature applications. Moreover, while plastic components can be lightweight, they often lack the durability and heat resistance that aluminum offers. Buyers focused on high-volume production of non-structural components may find plastic injection molding to be a suitable alternative.
How Can B2B Buyers Choose the Right Solution for Their Needs?
Choosing the right manufacturing process depends on several factors, including the specific application, production volume, material properties, and budget constraints. Buyers should assess the performance requirements of their products, such as weight considerations and strength needs. Additionally, understanding the cost implications of each method, including initial setup and long-term maintenance, will aid in making a financially sound decision. Ultimately, evaluating the unique demands of their projects will guide B2B buyers toward the most suitable solution, whether that be aluminum casting, steel fabrication, or plastic injection molding.
Essential Technical Properties and Trade Terminology for aluminium casting
What Are the Key Technical Properties of Aluminium Casting?
Aluminium casting involves several critical specifications that international B2B buyers must understand to ensure they select the right materials and processes for their needs. Here are some essential properties:
1. Material Grade
Material grade refers to the specific classification of aluminium alloys based on their chemical composition and mechanical properties. Common grades for casting include A356 and A380, each offering distinct advantages such as enhanced corrosion resistance or improved strength. Understanding the material grade is vital for B2B buyers, as it directly impacts the performance and durability of the final product.
2. Ultimate Tensile Strength (UTS)
UTS measures the maximum stress a material can withstand while being stretched or pulled before breaking. For aluminium casting, UTS can vary significantly among different alloys. For example, A07130 has a UTS of 221 MPa, while pure aluminium has a much lower value of 90 MPa. Buyers should consider UTS when evaluating the suitability of aluminium parts for specific applications, particularly in high-stress environments.
3. Porosity Levels
Porosity refers to the presence of gas inclusions or voids within a casting, which can weaken the final product. Low porosity is crucial for achieving high strength and durability. B2B buyers should inquire about the casting process and quality control measures to ensure low porosity levels, especially for critical components in sectors such as automotive and aerospace.
4. Tolerances
Tolerances denote the acceptable limits of variation in a part’s dimensions. Tight tolerances are essential for precision applications, while looser tolerances may be acceptable for less critical uses. Understanding the required tolerances helps buyers communicate their needs clearly and ensures that suppliers can meet their specifications without costly rework.
5. Thermal Conductivity
Aluminium’s excellent thermal conductivity is a valuable property for applications requiring efficient heat dissipation, such as in electrical and electronic components. Buyers should assess the thermal conductivity specifications of aluminium castings to ensure compatibility with their end-use applications.
6. Corrosion Resistance
Corrosion resistance is the ability of a material to withstand deterioration due to environmental factors. Aluminium castings generally exhibit good corrosion resistance, making them suitable for outdoor and marine applications. Buyers should confirm corrosion resistance levels to enhance the longevity of their products.
What Are Common Trade Terms Used in Aluminium Casting?
Familiarity with trade terminology is crucial for effective communication and negotiation in the aluminium casting industry. Here are some common terms:
1. OEM (Original Equipment Manufacturer)
An OEM is a company that produces parts or equipment that may be marketed by another manufacturer. Understanding the role of OEMs is essential for buyers seeking high-quality components that meet specific standards.
2. MOQ (Minimum Order Quantity)
MOQ refers to the smallest quantity of a product that a supplier is willing to sell. Buyers should be aware of MOQs when planning purchases, as they can impact inventory costs and cash flow.
3. RFQ (Request for Quotation)
An RFQ is a document issued by a buyer to solicit pricing and terms from suppliers. It is a critical step in the procurement process, enabling buyers to compare offers and select the best value for their needs.
4. Incoterms (International Commercial Terms)
Incoterms are a set of predefined international trade terms that clarify the responsibilities of buyers and sellers. Familiarity with these terms, such as FOB (Free On Board) and CIF (Cost, Insurance, and Freight), is essential for international B2B transactions to avoid misunderstandings.
5. Lead Time
Lead time refers to the time taken from placing an order to receiving the goods. Understanding lead times helps buyers manage production schedules and inventory levels effectively.
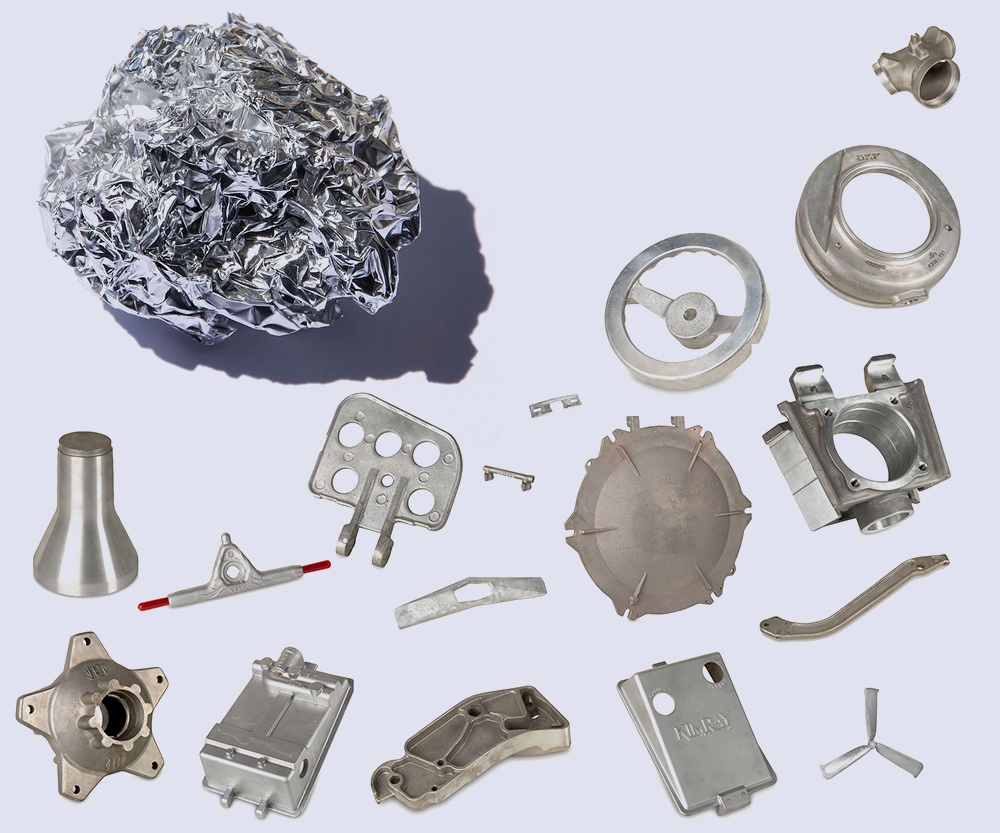
A stock image related to aluminium casting.
6. Casting Yield
Casting yield is the ratio of usable product to the total material used in the casting process. A higher casting yield indicates a more efficient process, which can lead to cost savings for buyers.
By understanding these technical properties and trade terms, international B2B buyers can make informed decisions in the aluminium casting market, ensuring they select the right materials and suppliers for their projects.
Navigating Market Dynamics and Sourcing Trends in the aluminium casting Sector
What Are the Current Market Dynamics and Key Trends in Aluminium Casting?
The aluminium casting market is witnessing significant growth driven by the increasing demand from various sectors, including automotive, aerospace, and consumer goods. The global shift towards lightweight materials for improved fuel efficiency and performance is propelling aluminium casting to the forefront. In regions like Africa and South America, burgeoning industries are increasingly adopting aluminium components due to their strength-to-weight ratio and corrosion resistance. For instance, in South Africa, the automotive sector is seeing a rise in demand for high-precision cast parts, which are critical for meeting regulatory standards and enhancing vehicle performance.
Emerging technologies are reshaping sourcing strategies in the aluminium casting sector. The integration of Industry 4.0 technologies such as IoT, AI, and big data analytics is facilitating smarter supply chain management. B2B buyers can leverage these technologies to optimize inventory levels, forecast demand, and enhance operational efficiency. Furthermore, automation in casting processes, including advancements in die casting and 3D printing, is leading to faster production cycles and reduced lead times. Buyers should seek suppliers that are adopting these technologies to ensure they remain competitive in a fast-evolving market.
How Is Sustainability Impacting Sourcing Trends in Aluminium Casting?
Sustainability is becoming a cornerstone of sourcing strategies in the aluminium casting industry. The environmental impact of aluminium production, particularly in terms of energy consumption and greenhouse gas emissions, necessitates a shift towards more sustainable practices. Buyers are increasingly prioritizing suppliers that adopt eco-friendly methods, such as recycling scrap aluminium, which can reduce the carbon footprint by up to 95% compared to primary aluminium production.
Moreover, the importance of ethical supply chains cannot be overstated. B2B buyers should ensure their suppliers comply with international environmental standards and possess certifications such as ISO 14001. These certifications indicate a commitment to environmental management and sustainability practices. The use of ‘green’ materials, such as low-carbon aluminium and recycled alloys, is becoming a differentiating factor in procurement decisions. As consumers and regulatory bodies place greater emphasis on sustainability, aligning sourcing strategies with these values is essential for long-term success.
What Is the Brief Evolution and History of Aluminium Casting?
Aluminium casting has a rich history that dates back to the late 19th century when the first commercial applications of aluminium were explored. Initially overshadowed by more readily available metals like iron and steel, aluminium gained traction as its unique properties became better understood. The development of efficient extraction methods, such as the Bayer and Hall-Héroult processes, enabled the large-scale production of aluminium, making it a viable material for casting.
Over the decades, advancements in casting techniques, including die casting and sand casting, have significantly improved the precision and quality of aluminium parts. Today, these methods are complemented by cutting-edge technologies such as 3D printing, which allows for the rapid prototyping and production of complex geometries. This evolution not only highlights aluminium’s versatility but also underscores its critical role in modern manufacturing, particularly for international B2B buyers seeking innovative solutions.
Frequently Asked Questions (FAQs) for B2B Buyers of aluminium casting
-
How do I choose the right aluminum casting supplier for my business needs?
When selecting an aluminum casting supplier, consider their experience and reputation in the industry. Look for suppliers with a proven track record of quality and reliability, especially those who specialize in your specific requirements. Assess their manufacturing capabilities, including the types of casting methods they employ (e.g., die casting, sand casting). Request samples and certifications to ensure compliance with international standards. Additionally, evaluate their communication responsiveness and ability to meet your timelines, as these factors are crucial for establishing a successful partnership. -
What are the key factors to consider when sourcing aluminum casting internationally?
International sourcing of aluminum casting requires careful consideration of several factors. First, evaluate the supplier’s location and the associated shipping costs, as these can significantly impact your total expenditure. Understand the regulatory compliance and quality standards required in your region, and ensure the supplier can meet them. Additionally, assess the supplier’s ability to handle customs and logistics, as delays in international shipping can affect production timelines. Lastly, consider currency exchange rates and payment terms to mitigate financial risks. -
What is the typical minimum order quantity (MOQ) for aluminum castings?
The minimum order quantity (MOQ) for aluminum castings can vary widely based on the supplier and the complexity of the parts being produced. Generally, MOQs can range from a few hundred to several thousand units. For custom designs, suppliers may have higher MOQs due to the setup costs involved. It’s essential to discuss your specific requirements with the supplier, as many are willing to negotiate MOQs based on the project’s scale and the potential for long-term partnerships. -
What are the common payment terms for international aluminum casting orders?
Payment terms for international aluminum casting orders often include options such as advance payment, letter of credit, or payment upon delivery. Many suppliers may request a deposit (e.g., 30-50%) before commencing production, with the balance due upon completion or shipment. It’s crucial to establish clear payment terms upfront to avoid misunderstandings. Additionally, consider using secure payment methods that protect both parties, and discuss the possibility of payment milestones tied to production stages for larger orders. -
How can I ensure quality assurance in aluminum casting products?
To ensure quality assurance in aluminum casting products, request detailed quality control processes from your supplier. This should include material certifications, in-process inspections, and final product testing. Look for suppliers who adhere to international standards like ISO 9001, as this indicates a commitment to quality management. Additionally, consider arranging for third-party inspections or audits, especially for large orders, to verify that the products meet your specifications and industry standards before shipment. -
What customization options are available for aluminum casting parts?
Customization options for aluminum casting parts are extensive and can include variations in size, shape, and alloy type. Most suppliers can accommodate specific design requirements, such as intricate geometries or surface finishes. You can also choose different casting methods based on your needs—die casting for high-volume production or sand casting for more complex designs. Discuss your specific requirements with the supplier early in the process to ensure they can meet your customization needs effectively. -
What are the advantages of using aluminum casting in manufacturing?
Aluminum casting offers several advantages for manufacturing, including a high strength-to-weight ratio, excellent corrosion resistance, and good thermal and electrical conductivity. This makes aluminum castings ideal for various applications in industries such as automotive, aerospace, and electronics. Additionally, aluminum’s low melting point and ease of casting allow for intricate designs and efficient production processes, reducing waste and lead times. By leveraging these benefits, manufacturers can create lightweight, durable components that enhance product performance. -
How do logistics and shipping affect the sourcing of aluminum castings?
Logistics and shipping play a critical role in sourcing aluminum castings, impacting both cost and delivery timelines. When sourcing internationally, consider the logistics involved in transporting heavy metal products, including shipping methods (air, sea, or land), potential tariffs, and customs clearance procedures. Collaborate closely with your supplier to develop a logistics plan that minimizes delays and maximizes efficiency. Additionally, factor in lead times for production and shipping to ensure that your supply chain remains uninterrupted and meets your production schedules.
Important Disclaimer & Terms of Use
⚠️ Important Disclaimer
The information provided in this guide, including content regarding manufacturers, technical specifications, and market analysis, is for informational and educational purposes only. It does not constitute professional procurement advice, financial advice, or legal advice.
While we have made every effort to ensure the accuracy and timeliness of the information, we are not responsible for any errors, omissions, or outdated information. Market conditions, company details, and technical standards are subject to change.
B2B buyers must conduct their own independent and thorough due diligence before making any purchasing decisions. This includes contacting suppliers directly, verifying certifications, requesting samples, and seeking professional consultation. The risk of relying on any information in this guide is borne solely by the reader.
Strategic Sourcing Conclusion and Outlook for aluminium casting
The strategic sourcing of aluminum casting is essential for businesses looking to enhance their manufacturing capabilities and product quality. By focusing on key aspects such as the selection of appropriate alloys, understanding casting methods like die casting and sand casting, and considering the unique needs of diverse markets, international B2B buyers can significantly improve their supply chain efficiency.
Investing in high-quality aluminum castings not only ensures better performance and durability but also contributes to cost savings in the long run. As industries in Africa, South America, the Middle East, and Europe continue to evolve, leveraging advanced aluminum casting technologies can provide a competitive edge, particularly in sectors such as automotive and aerospace.
Looking ahead, the demand for sustainable and lightweight materials will drive innovation in aluminum casting processes. B2B buyers should actively seek partnerships with reliable suppliers that prioritize sustainability and technological advancement. By doing so, companies can position themselves favorably in a rapidly changing market. Engage with trusted suppliers today to unlock the full potential of aluminum casting for your business and stay ahead of the competition.