Discover Cost-Saving Benefits of Ceramic Insulator Solutions (2025)
Introduction: Navigating the Global Market for ceramic insulator
Navigating the global market for ceramic insulators presents a significant challenge for international B2B buyers, particularly in regions like Africa, South America, the Middle East, and Europe. With diverse applications ranging from electrical systems to industrial uses, sourcing the right ceramic insulator can be daunting. This guide aims to simplify the process by providing a comprehensive overview of various types of ceramic insulators, including alumina, zirconia, and steatite, along with their specific applications and benefits.
We will also delve into key considerations for supplier vetting, ensuring that buyers can identify reputable manufacturers who meet their quality and compliance standards. Additionally, understanding the cost factors associated with ceramic insulators will empower businesses to make informed purchasing decisions that align with their budgetary constraints and operational needs.
By leveraging the insights provided in this guide, B2B buyers will be equipped to navigate the complexities of sourcing ceramic insulators effectively, ensuring that they choose solutions that enhance their operational efficiency and reliability. Whether you are in South Africa looking to upgrade your electrical infrastructure or in Argentina seeking durable materials for industrial applications, this guide will serve as an invaluable resource in your procurement journey.
Understanding ceramic insulator Types and Variations
Type Name | Key Distinguishing Features | Primary B2B Applications | Brief Pros & Cons for Buyers |
---|---|---|---|
Alumina Ceramics | High hardness, excellent electrical resistance, low porosity | Electrical insulators, aerospace, medical | Pros: High durability, versatile; Cons: Higher cost compared to other materials. |
Zirconia Ceramics | Exceptional toughness and corrosion resistance | High-temperature applications, automotive | Pros: Superior strength, thermal stability; Cons: More expensive, limited availability. |
Steatite Ceramics | Economical, good thermal conductivity, low thermal expansion | General electrical applications | Pros: Cost-effective, suitable for moderate temperatures; Cons: Limited to lower performance under extreme conditions. |
Cordierite Ceramics | Excellent thermal shock resistance and low thermal conductivity | Kiln furniture, electrical insulators | Pros: High resistance to thermal stress; Cons: Less durable than alumina in harsh environments. |
Porcelain Insulators | Made from fine clay, higher firing temperature than ceramic | High-voltage transmission lines | Pros: Exceptional durability, withstands harsh weather; Cons: Higher production costs, heavier than ceramic. |
What Are the Characteristics of Alumina Ceramics?
Alumina ceramics are renowned for their exceptional hardness and strength, making them ideal for high-stress applications. With a low porosity of 0-0.05%, they exhibit excellent electrical resistance and thermal conductivity. This makes them suitable for various industries, including aerospace and medical devices. When purchasing alumina insulators, buyers should consider the specific temperature and environmental conditions of their applications, as well as the higher cost associated with these high-performance materials.
Why Choose Zirconia Ceramics for High-Temperature Applications?
Zirconia ceramics, or zirconium dioxide ceramics, are characterized by their remarkable toughness and corrosion resistance. These properties make them particularly suitable for high-temperature applications, such as in automotive and aerospace sectors. Buyers should note that while zirconia offers superior strength and thermal stability, it comes at a higher price point and may be less readily available than other ceramic types. Understanding the specific requirements of your application can help in making an informed purchasing decision.
What Are the Advantages of Steatite Ceramics?
Steatite ceramics are an economical option for various electrical applications due to their good thermal conductivity and moderate strength. They are capable of withstanding temperatures up to 2000°F and have low thermal expansion, making them suitable for general electrical insulators. However, buyers should be aware of their limitations in extreme environments. Cost-effectiveness is a key consideration for companies looking to optimize their budget while still achieving reliable performance.
How Do Cordierite Ceramics Handle Thermal Shock?
Cordierite ceramics are unique for their excellent thermal shock resistance, allowing them to endure rapid heating and cooling cycles. This makes them particularly useful in kiln furniture and electrical insulators. While they offer high resistance to thermal stress, buyers should consider that they may not be as durable as alumina ceramics in harsher environments. Evaluating the specific thermal requirements of your application is crucial when selecting cordierite products.
What Makes Porcelain Insulators a Reliable Choice?
Porcelain insulators are crafted from fine clay and are fired at higher temperatures than standard ceramic insulators, resulting in exceptional durability and resistance to harsh weather conditions. They are commonly used in high-voltage transmission lines. However, the production costs are higher, and they can be heavier than ceramic insulators. B2B buyers should weigh the long-term benefits of durability against the initial investment when considering porcelain insulators for their projects.
Key Industrial Applications of ceramic insulator
Industry/Sector | Specific Application of Ceramic Insulator | Value/Benefit for the Business | Key Sourcing Considerations for this Application |
---|---|---|---|
Power Generation | Insulation for high-voltage transmission lines | Enhances safety and efficiency of power distribution | Ensure high dielectric strength and thermal resistance |
Telecommunications | Insulators for antenna masts and towers | Increases signal reliability and reduces maintenance | Assess environmental durability and compatibility |
Rail and Transport | Insulators for electrical components in trains | Improves safety and performance of electrical systems | Evaluate temperature tolerance and mechanical strength |
Renewable Energy | Insulators for wind turbine electrical systems | Supports sustainable energy solutions | Focus on corrosion resistance and long-term reliability |
Agriculture | Electric fence insulators for livestock management | Reduces energy loss and enhances animal containment | Consider compatibility with various types of fence wire |
How Are Ceramic Insulators Used in Power Generation?
In the power generation sector, ceramic insulators are critical for high-voltage transmission lines. These insulators prevent electrical leakage and ensure safe power distribution, which is vital for operational efficiency. International B2B buyers should prioritize sourcing ceramic insulators with high dielectric strength and thermal resistance to withstand extreme conditions. This is particularly important in regions like Africa and the Middle East, where environmental factors can significantly impact electrical infrastructure.
What Role Do Ceramic Insulators Play in Telecommunications?
Ceramic insulators are extensively used in telecommunications, specifically for securing antennas on masts and towers. They help maintain signal integrity while minimizing maintenance costs due to their durability. For businesses in South America and Europe, sourcing insulators that can withstand harsh weather conditions is crucial. Buyers should assess the environmental durability of these insulators to ensure long-term performance and reliability.
How Are Ceramic Insulators Beneficial in Rail and Transport?
In the rail and transport industry, ceramic insulators are utilized in electrical components of trains. They enhance the safety and performance of electrical systems by providing effective insulation. Buyers should look for insulators that offer high mechanical strength and temperature tolerance, particularly in regions with extreme climates. This ensures that the insulators can operate effectively and reduce the risk of electrical failures.
Why Are Ceramic Insulators Important for Renewable Energy?
Ceramic insulators are essential in the renewable energy sector, particularly for wind turbine electrical systems. They support sustainable energy solutions by ensuring reliable electrical connections. Buyers should focus on sourcing insulators that exhibit excellent corrosion resistance and long-term reliability, especially in coastal areas where saltwater can accelerate wear and tear. This consideration is vital for international buyers looking to invest in renewable energy infrastructure.
How Do Ceramic Insulators Enhance Agricultural Practices?
In agriculture, ceramic insulators are used in electric fencing systems to manage livestock. They minimize energy loss and enhance the effectiveness of animal containment strategies. B2B buyers, particularly in regions like South Africa, should consider the compatibility of these insulators with various types of fence wire to ensure optimal performance. This will help improve livestock management and reduce operational costs.
3 Common User Pain Points for ‘ceramic insulator’ & Their Solutions
Scenario 1: Difficulty Sourcing Quality Ceramic Insulators
The Problem:
International B2B buyers, especially those from regions like Africa and South America, often struggle with sourcing high-quality ceramic insulators that meet their specific application requirements. This challenge can stem from limited access to reliable suppliers, variations in material quality, and inconsistent performance across different brands. Buyers may face critical production delays if the insulators they receive do not conform to technical specifications or are prone to failure under stress.
The Solution:
To overcome sourcing challenges, buyers should conduct thorough market research to identify reputable manufacturers that specialize in ceramic insulators. It is essential to request certifications and performance data, such as dielectric strength and thermal stability, for the specific products. Utilize platforms like trade shows or industry forums to connect with manufacturers that offer samples for testing. Establishing long-term relationships with suppliers who can provide consistent quality and technical support will also mitigate risks associated with sourcing. Additionally, consider leveraging local distributors who understand regional needs and can facilitate better supply chain logistics.
Scenario 2: Performance Issues in Extreme Conditions
The Problem:
B2B buyers operating in harsh environments, particularly in the Middle East where temperatures can soar, often encounter performance issues with ceramic insulators. Insulators can chip or crack under extreme thermal stress, leading to electrical failures and costly downtime. This is particularly concerning for industries like power generation or telecommunications, where reliability is paramount.
The Solution:
To ensure optimal performance, buyers must choose ceramic insulators specifically designed for high-temperature applications. Materials like alumina or zirconia ceramics, known for their high thermal stability and resistance to mechanical stress, should be prioritized. When selecting insulators, buyers should consider the manufacturer’s specifications regarding temperature ratings and mechanical strength. Implementing a regular maintenance schedule to inspect the insulators for any signs of wear or damage can also help in preemptively addressing potential failures. Furthermore, engaging with engineers to tailor solutions for specific applications will enhance the reliability of the insulators in extreme conditions.
Scenario 3: Misunderstanding Insulator Types and Applications
The Problem:
Many B2B buyers are often unclear about the differences between various types of ceramic insulators, such as those made from steatite versus alumina. This misunderstanding can lead to the selection of inappropriate insulators for specific applications, resulting in operational inefficiencies and increased costs due to failures or replacement needs.
The Solution:
Education is key to overcoming this knowledge gap. Buyers should invest time in understanding the properties and ideal applications of different ceramic insulators. For instance, steatite is more economical and suitable for moderate-temperature applications, while alumina offers superior performance in high-temperature scenarios. Buyers can benefit from consulting technical datasheets and engaging with suppliers for expert advice on product selection tailored to their needs. Furthermore, attending industry webinars or training sessions can provide valuable insights into the latest advancements in ceramic insulator technology. By gaining a deeper understanding of materials and their applications, buyers can make informed decisions that enhance performance and reduce costs.
Strategic Material Selection Guide for ceramic insulator
What are the Key Properties of Alumina Ceramics for Insulators?
Alumina ceramics, primarily composed of aluminum oxide, are renowned for their exceptional hardness and high-temperature performance, making them a popular choice for electrical insulators. They exhibit excellent electrical resistance and can withstand temperatures up to 1,600°C (2,912°F). Alumina also has a low porosity rate (0-0.05%), contributing to its durability and chemical resistance, which is crucial for applications exposed to harsh environments.
Pros and Cons of Alumina Ceramics
The primary advantage of alumina ceramics is their strength and durability, which translates into a longer lifespan for insulators. However, the manufacturing process can be complex and costly due to the need for precise machining and high-temperature sintering. While alumina insulators are suitable for various applications, their brittleness can be a disadvantage in environments prone to mechanical shock.
Impact on Applications
Alumina ceramics are ideal for high-voltage applications and environments where chemical exposure is a concern. They are commonly used in power generation and transmission systems, making them a preferred choice for B2B buyers in industries such as energy and telecommunications.
How Does Zirconia Ceramic Compare for Insulator Applications?
Zirconia ceramics, or zirconium dioxide ceramics, are recognized for their superior toughness and hardness, along with excellent corrosion resistance. They can withstand temperatures up to 2,200°C (3,992°F) and maintain their integrity under thermal stress, making them suitable for high-performance applications.
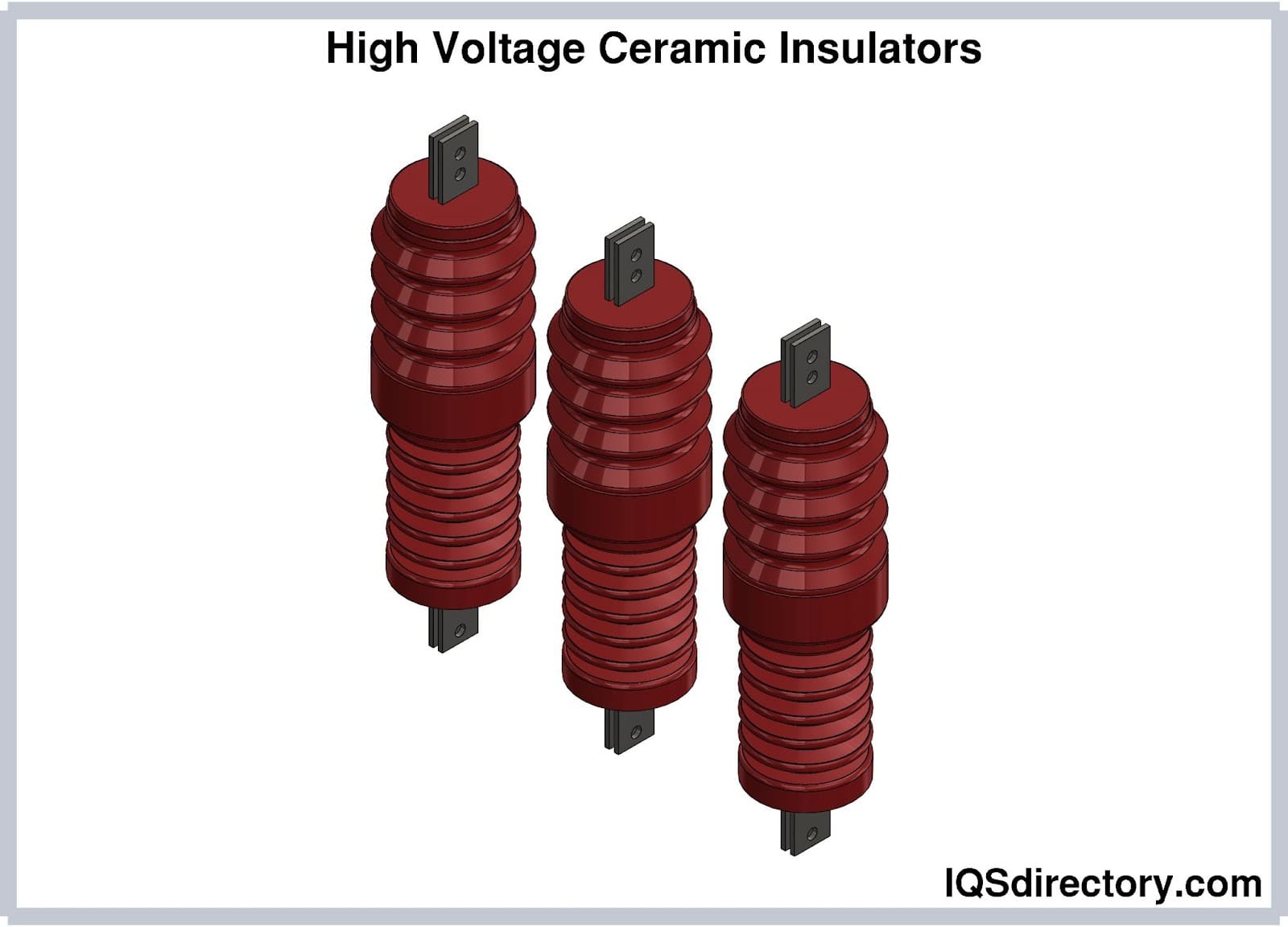
A stock image related to ceramic insulator.
Pros and Cons of Zirconia Ceramics
The key advantage of zirconia ceramics is their exceptional mechanical properties, which reduce the risk of failure under load. However, they are generally more expensive than alumina ceramics and may require specialized manufacturing processes, increasing overall costs. Their suitability for high-stress applications makes them a valuable option for industries requiring robust electrical insulators.
Impact on Applications
Zirconia ceramics are particularly beneficial in applications involving extreme temperatures and corrosive environments, such as in aerospace and automotive sectors. International buyers must consider the material’s compliance with standards such as ASTM and DIN, particularly in regions with stringent regulations.
What Role Does Steatite Play in Ceramic Insulators?
Steatite, a magnesium silicate ceramic, is often chosen for its cost-effectiveness and good electrical insulating properties. It can operate at temperatures up to 1,100°C (2,012°F) and has a low thermal expansion coefficient, making it resistant to thermal shock.
Pros and Cons of Steatite
Steatite’s affordability is a significant advantage for manufacturers, particularly for applications where high performance is not critical. However, it may not offer the same level of mechanical strength or thermal resistance as alumina or zirconia ceramics, limiting its use in high-stress environments.
Impact on Applications
Steatite is commonly used in less demanding electrical applications, such as in household appliances and low-voltage systems. Buyers from regions like Africa and South America may find steatite insulators appealing due to their lower cost and adequate performance for specific applications.
What are the Benefits of Cordierite in Ceramic Insulators?
Cordierite ceramics are known for their excellent thermal shock resistance and low thermal expansion, making them ideal for high-temperature applications. They can withstand temperatures up to 1,400°C (2,552°F) and are often used in environments where rapid temperature fluctuations occur.
Pros and Cons of Cordierite
The main advantage of cordierite is its ability to endure thermal cycling without cracking, which is crucial for applications in industrial furnaces and kilns. However, its mechanical strength is lower than that of alumina or zirconia, which may limit its use in high-stress applications.
Impact on Applications
Cordierite is well-suited for applications in ceramics and glass production, as well as in electrical insulators for heating elements. B2B buyers in Europe and the Middle East should consider the material’s thermal properties when selecting insulators for specific applications.
Summary Table of Ceramic Insulator Materials
Material | Typical Use Case for Ceramic Insulator | Key Advantage | Key Disadvantage/Limitation | Relative Cost (Low/Med/High) |
---|---|---|---|---|
Alumina | High-voltage electrical applications | High strength and durability | Brittle, complex manufacturing | Medium |
Zirconia | Aerospace and automotive applications | Exceptional toughness | Higher cost, specialized processes | High |
Steatite | Household appliances, low-voltage systems | Cost-effective | Lower thermal and mechanical strength | Low |
Cordierite | Industrial furnaces, heating elements | Excellent thermal shock resistance | Lower mechanical strength | Medium |
This guide provides international B2B buyers with essential insights into the strategic selection of ceramic materials for insulators, enabling informed decisions that align with their specific application needs and regional compliance requirements.
In-depth Look: Manufacturing Processes and Quality Assurance for ceramic insulator
What Are the Key Stages in the Manufacturing Process of Ceramic Insulators?
Manufacturing ceramic insulators involves several critical stages, each designed to ensure the final product meets the required specifications for quality and performance. Understanding these stages is vital for international B2B buyers, particularly those in Africa, South America, the Middle East, and Europe, as it helps them assess supplier capabilities.
1. Material Preparation
The first step in manufacturing ceramic insulators is the preparation of raw materials. Common materials include alumina, zirconia, and steatite, chosen for their electrical and thermal insulating properties. The materials are typically sourced from reputable suppliers to ensure quality.
- Sourcing and Quality Control: It’s essential for buyers to verify that suppliers adhere to international standards for raw materials. This can include checking certifications and conducting audits to confirm the quality of bauxite, zirconium dioxide, or other materials used.
2. Forming Techniques: How Are Ceramic Insulators Shaped?
After materials are prepared, they undergo various forming techniques. The choice of technique often depends on the desired characteristics of the final product.
-
Injection Molding: This process allows for complex shapes and is suitable for high-volume production. It involves injecting a mixture of ceramic powder and a binder into a mold.
-
Die Pressing: This method is used for creating denser insulators. The ceramic powder is placed into a die and compressed to form a solid piece.
-
Isostatic Pressing: This technique applies pressure uniformly around the material, resulting in a higher density and improved mechanical properties.
-
Slip Casting: A slurry of ceramic materials is poured into a porous mold, allowing excess moisture to escape and forming a solid piece.
B2B buyers should inquire about the specific forming techniques used by suppliers, as these can impact the durability and performance of the insulators.
3. Assembly and Firing: What Happens Next?
Once the insulators are formed, they undergo assembly, particularly if they are part of a more complex system. Following assembly, the insulators are fired in a kiln.
-
Firing Process: The firing temperature can range from 2,100°F to 2,600°F, depending on the material. This process solidifies the insulator and enhances its mechanical strength and insulation properties.
-
Quality Considerations: Buyers should be aware of the firing conditions and the type of kiln used, as these factors can significantly influence the final product’s quality.
4. Finishing: How Are Ceramic Insulators Prepared for Market?
The final stage involves finishing processes that enhance the insulator’s performance and aesthetics. This can include glazing, which provides a protective layer against environmental factors and improves electrical insulation.
- Surface Treatments: Additional treatments may be applied to improve surface finish or enhance specific properties like chemical resistance.
B2B buyers should request detailed information about the finishing processes to ensure that the insulators meet their operational requirements.
What Quality Assurance Measures Are Essential for Ceramic Insulators?
Quality assurance (QA) is paramount in the manufacturing of ceramic insulators, ensuring that products meet international and industry-specific standards. For international buyers, understanding these measures can facilitate better sourcing decisions.
International Standards: What Should Buyers Know?
The manufacturing of ceramic insulators is often governed by international standards such as ISO 9001, which focuses on quality management systems. Compliance with these standards indicates that the manufacturer has established robust processes for maintaining product quality.
-
CE Marking: In Europe, products may also require CE marking, demonstrating compliance with EU safety, health, and environmental protection legislation.
-
API Standards: For insulators used in specific industries, such as oil and gas, adherence to American Petroleum Institute (API) standards may also be relevant.
B2B buyers should ensure that suppliers can provide documentation of compliance with these standards.
Key Quality Control Checkpoints: How Are Products Tested?
Quality control (QC) is integrated throughout the manufacturing process, with several checkpoints to ensure product integrity.
-
Incoming Quality Control (IQC): This initial checkpoint involves inspecting raw materials before production begins. Suppliers should maintain records of IQC results to provide transparency to buyers.
-
In-Process Quality Control (IPQC): During manufacturing, various tests are performed to monitor parameters such as density, dimensions, and mechanical strength. Buyers should inquire about the specific tests conducted during this phase.
-
Final Quality Control (FQC): After the insulators are produced, they undergo final testing to assess their electrical and thermal properties. Common tests include dielectric strength, thermal shock resistance, and mechanical strength assessments.
What Testing Methods Are Commonly Used?
Testing methods vary but typically include:
-
Dielectric Testing: Measures the insulator’s ability to withstand electrical stress without breaking down.
-
Thermal Shock Testing: Evaluates how well the insulator can handle sudden temperature changes.
-
Mechanical Strength Testing: Assesses the insulator’s durability under load.
B2B buyers should request detailed testing reports to verify that products meet their specific requirements.
How Can B2B Buyers Verify Supplier Quality Control?
Ensuring the reliability of suppliers is crucial for B2B buyers, particularly in international markets. Here are some actionable steps:
-
Conduct Supplier Audits: Regular audits can help assess compliance with quality standards and manufacturing processes. Buyers should establish criteria for these audits, focusing on both product quality and operational efficiency.
-
Request Quality Reports: Suppliers should provide detailed reports on IQC, IPQC, and FQC results. This documentation can offer insights into the supplier’s commitment to quality.
-
Engage Third-Party Inspectors: Utilizing independent inspection services can further validate the supplier’s quality claims. Third-party inspectors can provide objective evaluations of manufacturing processes and product quality.
What Are the QC/CERT Nuances for International B2B Buyers?
International B2B buyers must navigate various regulations and standards that can differ significantly by region.
-
Regional Standards: Buyers in Africa and South America may face different regulatory requirements compared to those in Europe or the Middle East. Understanding these nuances is essential for compliance and successful market entry.
-
Certification Nuances: Some regions may require additional certifications for specific applications, particularly in safety-sensitive industries. Buyers should clarify these requirements with their suppliers.
By comprehensively understanding the manufacturing processes and quality assurance measures for ceramic insulators, B2B buyers can make informed purchasing decisions, ensuring they acquire reliable products that meet their operational needs.
Practical Sourcing Guide: A Step-by-Step Checklist for ‘ceramic insulator’
In the global market for ceramic insulators, understanding the procurement process is crucial for B2B buyers. This step-by-step guide aims to assist international buyers, particularly from Africa, South America, the Middle East, and Europe, in sourcing high-quality ceramic insulators that meet their specific needs.
Step 1: Define Your Technical Specifications
Before initiating the sourcing process, it’s essential to establish clear technical specifications for the ceramic insulators you require. Consider factors such as the type of ceramic material (e.g., alumina, zirconia, or steatite), temperature resistance, dielectric strength, and application environment. This clarity will help you communicate effectively with suppliers and ensure that the products you receive meet your operational needs.
Step 2: Research Market Trends and Supplier Options
Understanding market trends in the ceramic insulator industry can give you a competitive edge. Investigate the latest technologies, materials, and manufacturing processes used in ceramic insulators. Utilize online resources, industry publications, and trade shows to identify potential suppliers who are innovating in this space. Pay attention to suppliers that cater specifically to your region, as they may offer localized support and logistics advantages.
Step 3: Evaluate Potential Suppliers
Before committing to a supplier, conduct a thorough evaluation. Request company profiles, product catalogs, and references from buyers in similar industries or regions. Verify their manufacturing capabilities and quality control measures. Look for suppliers that have experience in producing ceramic insulators for your specific application, whether it’s electrical insulation or mechanical support.
- Key considerations:
- Check for ISO certification or other relevant industry standards.
- Assess their production capacity to ensure they can meet your volume requirements.
Step 4: Request Samples for Testing
Once you’ve narrowed down potential suppliers, request samples of their ceramic insulators for testing. This step allows you to evaluate the quality, performance, and suitability of the products in real-world conditions. Testing should focus on critical aspects such as thermal resistance, mechanical strength, and electrical insulation properties.
Step 5: Negotiate Pricing and Terms
After evaluating samples, engage in negotiations with your selected suppliers. Consider not only the unit price but also the total cost of ownership, including shipping, import duties, and any additional fees. Discuss payment terms, warranties, and return policies to ensure that they align with your business practices.
Step 6: Finalize Contracts and Place Orders
Once negotiations are complete, finalize contracts that clearly outline all terms and conditions, including delivery schedules and quality standards. Ensure both parties have a mutual understanding of the expectations to prevent any future disputes. Placing your order should be done with a clear timeline for delivery and a plan for receiving and inspecting the products upon arrival.
Step 7: Monitor Supplier Performance
After placing your order, establish a system for monitoring supplier performance. Keep track of delivery timelines, product quality, and communication efficiency. This ongoing assessment will help you build a strong relationship with your suppliers and make adjustments as necessary for future orders.
By following this structured checklist, B2B buyers can effectively navigate the sourcing process for ceramic insulators, ensuring they select the right products and suppliers to meet their operational requirements.
Comprehensive Cost and Pricing Analysis for ceramic insulator Sourcing
What Are the Key Cost Components in Ceramic Insulator Manufacturing?
When sourcing ceramic insulators, understanding the various cost components is essential for effective budget planning. The primary cost elements include:
-
Materials: The choice of material significantly impacts the price. Common materials for ceramic insulators include alumina, zirconia, and steatite. Alumina is known for its excellent electrical resistance and thermal conductivity, making it a popular choice despite being on the higher end of the cost spectrum.
-
Labor: Labor costs can vary depending on the manufacturing location. Countries with lower labor costs may provide a competitive advantage, but this can also affect quality. Skilled labor is often necessary for the precision machining of ceramic materials.
-
Manufacturing Overhead: This includes costs related to the operation of machinery, utilities, and facility maintenance. Overhead costs can vary significantly depending on the efficiency of the production process and the level of automation employed.
-
Tooling: The initial investment in tooling and molds can be substantial, especially for customized insulators. These costs are usually amortized over production runs, affecting the unit price.
-
Quality Control (QC): Ensuring that products meet international standards requires robust QC processes. This adds to the overall production cost but is essential for maintaining product reliability and safety.
-
Logistics: Shipping costs can vary based on distance, weight, and shipping method. For international buyers, understanding Incoterms can help clarify responsibilities related to shipping, insurance, and import duties.
-
Margin: Suppliers typically add a margin to cover their costs and ensure profitability. This margin can fluctuate based on market demand, competition, and supplier reputation.
How Do Volume and Customization Affect Pricing?
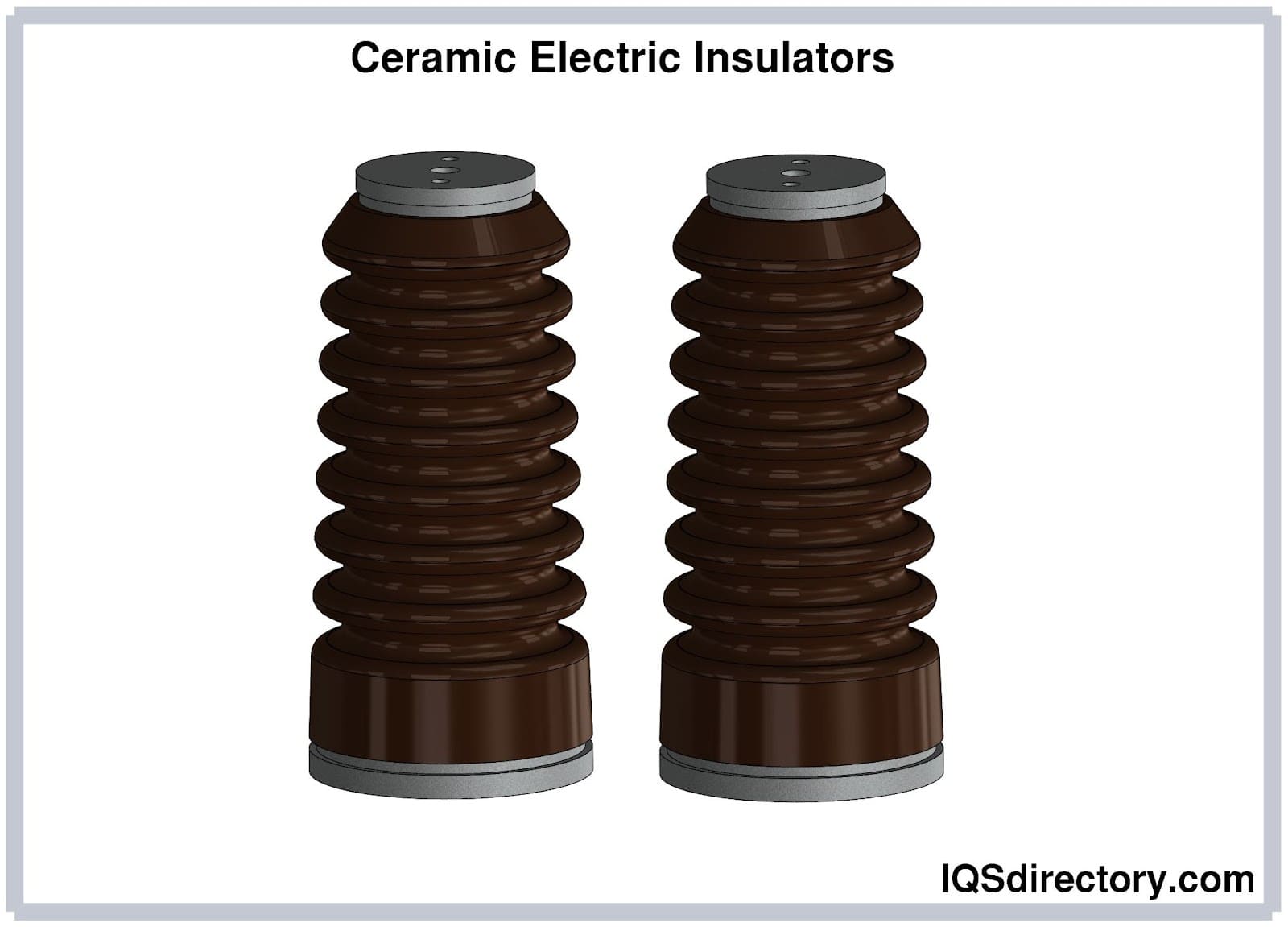
A stock image related to ceramic insulator.
Pricing for ceramic insulators is often influenced by order volume and the level of customization required. Larger orders typically benefit from economies of scale, reducing the per-unit cost. Conversely, custom designs may incur additional charges due to the need for specialized tooling and longer production times.
What Role Do Quality Certifications Play in Pricing?
Quality certifications can significantly impact the pricing of ceramic insulators. Products with certifications (like ISO or IEC standards) often command a higher price due to the assurance of quality and reliability. International buyers, particularly from Africa and South America, should prioritize suppliers who provide these certifications to ensure compliance with local regulations.
What Are the Key Buyer Tips for Negotiating Prices?
-
Negotiate Based on Volume: Leverage larger order quantities to negotiate better pricing. Establishing long-term relationships with suppliers can also lead to favorable terms.
-
Consider Total Cost of Ownership (TCO): Evaluate not just the purchase price but also the operational costs, including installation, maintenance, and potential downtime. A higher upfront cost may be justified by lower TCO in the long run.
-
Understand Pricing Nuances: Be aware of market trends and price fluctuations. Global supply chain issues, such as material shortages or increased shipping costs, can affect pricing.
-
Utilize Incoterms Wisely: Familiarize yourself with Incoterms to clarify the responsibilities of both buyer and seller regarding shipping, insurance, and risk transfer. This can prevent unexpected costs during transportation.
How Do Supplier Factors Influence Pricing?
The choice of supplier can greatly affect pricing. Established suppliers with a good reputation may charge more for their products due to perceived reliability and quality. On the other hand, newer suppliers might offer competitive pricing to gain market share but could pose risks in terms of quality and service. Always conduct thorough due diligence when selecting suppliers.
Disclaimer on Indicative Prices
Prices for ceramic insulators can vary widely based on the factors mentioned above. It’s essential for buyers to obtain quotes from multiple suppliers to get a comprehensive understanding of the market and to negotiate terms that align with their specific needs.
Alternatives Analysis: Comparing ceramic insulator With Other Solutions
When evaluating insulator options for various electrical applications, it’s crucial for B2B buyers to consider viable alternatives to ceramic insulators. Each alternative comes with its own set of advantages and challenges, depending on specific project requirements and operating conditions. This analysis aims to provide a clear comparison of ceramic insulators against two prominent alternatives: porcelain insulators and polymer insulators.
Comparison Aspect | Ceramic Insulator | Porcelain Insulator | Polymer Insulator |
---|---|---|---|
Performance | Excellent electrical resistance; good thermal stability. | Superior durability and withstands extreme weather conditions. | High flexibility, good dielectric strength, but may degrade over time. |
Cost | Generally lower production costs. | Higher initial investment; longer lifespan may offset costs. | Moderate cost; often cheaper than porcelain but more expensive than ceramic. |
Ease of Implementation | Relatively straightforward to install; compatible with various applications. | Requires careful handling due to fragility; installation can be cumbersome. | Lightweight and easy to install; flexible designs fit various applications. |
Maintenance | Low maintenance; can chip in cold weather. | Requires minimal maintenance; very durable against environmental factors. | May require more frequent inspections due to potential degradation. |
Best Use Case | Ideal for general electrical applications where cost is a factor. | Best for high-stress applications in extreme weather conditions. | Suitable for flexible or portable installations requiring lightweight solutions. |
What Are the Advantages and Disadvantages of Porcelain Insulators?
Porcelain insulators are known for their exceptional durability and resistance to harsh environmental conditions. They can withstand high temperatures and do not easily chip or break, making them suitable for high-stress applications such as transmission lines and substations. However, they come at a higher cost than ceramic insulators, which can be a significant factor for budget-conscious B2B buyers. The fragility of porcelain can also complicate transportation and installation, necessitating careful handling.
How Do Polymer Insulators Compare to Ceramic Insulators?
Polymer insulators are gaining popularity due to their lightweight nature and flexibility. They are particularly useful in applications where weight is a concern, such as on mobile electrical equipment or in areas with limited access. While they offer good dielectric strength, one downside is their susceptibility to degradation from UV exposure and environmental factors over time, potentially leading to more frequent replacements. This can increase long-term costs, which buyers should consider against the initial savings.
Conclusion: How Can B2B Buyers Choose the Right Insulator Solution?
Selecting the appropriate insulator solution hinges on understanding the specific requirements of your application. If your project prioritizes cost and general performance, ceramic insulators may be the best fit. However, for environments that demand high durability and resistance to extreme conditions, porcelain insulators are likely the better choice despite their higher price point. Conversely, for applications where weight and flexibility are crucial, polymer insulators could provide the necessary advantages. Ultimately, evaluating the performance characteristics, costs, and specific use cases of each option will empower B2B buyers to make informed decisions that align with their operational needs and budget constraints.
Essential Technical Properties and Trade Terminology for ceramic insulator
What Are the Key Technical Properties of Ceramic Insulators?
When considering ceramic insulators for electrical applications, understanding their technical properties is crucial for ensuring optimal performance and durability. Here are some essential specifications that international B2B buyers should prioritize:
1. Material Grade
Ceramic insulators are typically made from materials like alumina, steatite, or zirconia. Alumina is favored for its high hardness and excellent electrical resistance, while steatite offers a more economical option with decent thermal stability. Buyers must assess the material grade to ensure it meets specific application requirements, particularly in high-temperature environments.
2. Dielectric Strength
This property indicates the insulator’s ability to withstand electrical stress without breaking down. It is measured in kilovolts per millimeter (kV/mm). Higher dielectric strength is essential for applications involving high voltage, as it ensures safety and reliability. A dielectric strength of 15-20 kV/mm is typically standard for high-performance ceramic insulators.
3. Thermal Conductivity
The ability of an insulator to conduct heat significantly affects its performance. Ceramic insulators usually have low thermal conductivity, which is beneficial for maintaining temperature stability in electrical applications. Buyers should look for materials with a thermal conductivity of less than 1 W/mK for effective insulation, especially in environments with fluctuating temperatures.
4. Porosity
Porosity refers to the void spaces within the ceramic material. Low porosity (ideally 0-0.05%) is vital for preventing moisture absorption, which can degrade insulating properties over time. Insulators with high porosity may lead to electrical failures, making it crucial for buyers to specify low-porosity materials.
5. Mechanical Strength
The mechanical strength of a ceramic insulator determines its resistance to physical stress and impact. This property is measured in megapascals (MPa). Insulators should have a tensile strength of at least 200 MPa to withstand operational stresses, especially in outdoor installations subject to environmental challenges.
What Are Common Trade Terms in the Ceramic Insulator Industry?
Familiarity with industry jargon can facilitate smoother transactions and communication between buyers and suppliers. Here are some essential terms:
1. OEM (Original Equipment Manufacturer)
An OEM is a company that produces parts or equipment that may be marketed by another manufacturer. Understanding the role of OEMs is important for buyers seeking customized insulator solutions tailored to specific applications.
2. MOQ (Minimum Order Quantity)
This term refers to the smallest quantity of a product that a supplier is willing to sell. For ceramic insulators, MOQs can vary significantly based on material type and manufacturing processes. Buyers should clarify MOQs upfront to ensure they can meet their project needs without overcommitting financially.
3. RFQ (Request for Quotation)
An RFQ is a document sent to suppliers requesting pricing for specific products or services. For B2B buyers, issuing an RFQ for ceramic insulators allows them to compare prices and negotiate terms effectively, ensuring they receive the best value for their investment.
4. Incoterms (International Commercial Terms)
Incoterms define the responsibilities of buyers and sellers in international transactions, including shipping and delivery. Familiarity with these terms helps buyers understand their obligations regarding shipping costs, insurance, and risk of loss during transportation.
5. Tolerance
Tolerance refers to the permissible limit of variation in a physical dimension or property of a product. In the context of ceramic insulators, tight tolerances are crucial for ensuring compatibility and performance in electrical systems. Buyers should specify tolerance requirements to ensure that the insulators fit correctly in their intended applications.
Understanding these properties and terms empowers B2B buyers to make informed decisions when sourcing ceramic insulators, ultimately enhancing the reliability and efficiency of their electrical systems.
Navigating Market Dynamics and Sourcing Trends in the ceramic insulator Sector
What Are the Current Market Dynamics and Key Trends in the Ceramic Insulator Sector?
The global ceramic insulator market is experiencing significant growth, driven by increasing demand for high-performance electrical insulation in various industries, including power generation, telecommunications, and transportation. Key trends influencing this market include the rising adoption of advanced manufacturing technologies, such as 3D printing and precision machining, which enhance the customization and efficiency of insulator production. Furthermore, the shift towards renewable energy sources, particularly in regions like Africa and South America, is propelling the need for reliable insulators that can withstand harsh environmental conditions.
For international B2B buyers, particularly in emerging markets, understanding local sourcing trends is crucial. Buyers are increasingly looking for suppliers who can offer flexible production capabilities and rapid prototyping services. Additionally, there is a growing preference for suppliers who can provide comprehensive technical support and after-sales services, which are vital in ensuring the optimal performance of ceramic insulators in specific applications. As competition intensifies, partnerships with local distributors and manufacturers can help facilitate better access to materials and reduce lead times.
How Does Sustainability and Ethical Sourcing Impact the Ceramic Insulator Industry?
Sustainability is becoming a focal point for B2B buyers in the ceramic insulator sector. The environmental impact of ceramic production, including energy consumption and emissions, is prompting companies to seek out eco-friendly manufacturing processes and materials. Ethical sourcing practices are also gaining traction, as buyers aim to ensure that their suppliers adhere to responsible labor practices and environmental regulations.
Many manufacturers are now pursuing ‘green’ certifications, such as ISO 14001, which demonstrates their commitment to environmental management. Additionally, the use of recycled materials in the production of ceramic insulators is on the rise, allowing companies to reduce their carbon footprint while maintaining product quality. For buyers in Africa, South America, the Middle East, and Europe, partnering with suppliers who prioritize sustainability not only enhances brand reputation but also aligns with the growing consumer demand for environmentally responsible products.
How Has the Ceramic Insulator Market Evolved Over Time?
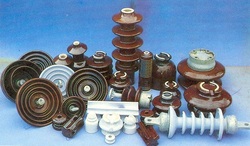
A stock image related to ceramic insulator.
The evolution of the ceramic insulator market can be traced back to the early 20th century when traditional materials like wood and metal were predominantly used for electrical insulation. The introduction of ceramics offered superior electrical resistance and durability, leading to widespread adoption in various applications. Over the decades, advancements in material science have led to the development of high-performance ceramics, such as alumina and zirconia, which provide enhanced mechanical strength and thermal resistance.
As industries continue to innovate, the ceramic insulator market is expected to evolve further, embracing new technologies and sustainable practices that meet the demands of modern electrical systems. For international B2B buyers, staying informed about these trends is essential for making strategic sourcing decisions that align with both current market needs and future industry developments.
Frequently Asked Questions (FAQs) for B2B Buyers of ceramic insulator
-
How do I choose the right ceramic insulator for my application?
Selecting the appropriate ceramic insulator depends on several factors, including the electrical and thermal requirements, environmental conditions, and mechanical stress levels. For high-voltage applications, materials like alumina and zirconia are recommended due to their exceptional dielectric strength and thermal resistance. Additionally, consider the specific usage scenario—insulators for electric fencing may differ significantly from those used in power generation. Always consult with manufacturers to ensure compliance with local standards and specifications, particularly if sourcing from international suppliers. -
What are the advantages of using ceramic insulators over porcelain insulators?
Ceramic insulators are generally less expensive to produce than porcelain insulators, making them a cost-effective choice for various applications. They offer excellent insulation quality and are suitable for moderate temperature ranges. While ceramics can chip under extreme cold, they are still preferred for many applications due to their lower cost and adequate performance. In contrast, porcelain insulators withstand harsher weather conditions and higher temperatures, making them suitable for more demanding environments. Assess your operational needs to make an informed decision. -
What factors should I consider when vetting international suppliers of ceramic insulators?
When vetting suppliers, prioritize their experience in the ceramic industry, production capacity, and quality assurance processes. Check for certifications that comply with international standards, such as ISO 9001, which indicates a commitment to quality management. Additionally, request samples to evaluate product quality and performance. Research their reputation through customer reviews and industry references, and consider their ability to provide after-sales support and warranty options. -
Can I customize ceramic insulators to meet specific requirements?
Yes, many manufacturers offer customization options for ceramic insulators. You can specify dimensions, shapes, and material compositions based on your unique application needs. When discussing customization, provide detailed specifications and performance requirements to ensure the manufacturer understands your expectations. However, be mindful that custom orders may have higher minimum order quantities (MOQs) and longer lead times. -
What are the typical minimum order quantities (MOQs) for ceramic insulators?
MOQs for ceramic insulators can vary significantly based on the manufacturer and the type of insulator. Generally, MOQs may range from a few hundred to several thousand units, depending on the complexity of the design and the materials used. It’s essential to discuss your requirements with suppliers upfront to understand their MOQ policies and explore options for smaller orders, especially if you are just testing the market or need insulators for a pilot project. -
What payment terms should I expect when purchasing ceramic insulators internationally?
Payment terms can vary widely depending on the supplier and the country of origin. Common arrangements include upfront payments, partial payments upon order confirmation, and remaining balances due before shipment. Be prepared to negotiate terms that fit your cash flow needs while ensuring security. Additionally, consider using secure payment methods like letters of credit or escrow services, particularly for large transactions or new suppliers, to mitigate financial risk. -
How can I ensure quality assurance when sourcing ceramic insulators?
To ensure quality assurance, request detailed product specifications and certifications from suppliers. Many reputable manufacturers will provide test reports, compliance documentation, and samples for evaluation. Establish a clear agreement on quality expectations and inspection processes before placing an order. You may also consider third-party inspections or audits to verify the manufacturing processes and material quality, especially for large orders or ongoing contracts. -
What logistics considerations should I keep in mind when importing ceramic insulators?
Logistics play a crucial role in international sourcing. Evaluate shipping options based on cost, time, and reliability, and consider using freight forwarders who specialize in your product type. Be aware of customs regulations and import duties that may apply to ceramic materials in your country. Ensure that your supplier provides the necessary documentation for smooth customs clearance. Additionally, plan for potential delays in transit and have contingency plans in place to minimize disruptions to your supply chain.
Important Disclaimer & Terms of Use
⚠️ Important Disclaimer
The information provided in this guide, including content regarding manufacturers, technical specifications, and market analysis, is for informational and educational purposes only. It does not constitute professional procurement advice, financial advice, or legal advice.
While we have made every effort to ensure the accuracy and timeliness of the information, we are not responsible for any errors, omissions, or outdated information. Market conditions, company details, and technical standards are subject to change.
B2B buyers must conduct their own independent and thorough due diligence before making any purchasing decisions. This includes contacting suppliers directly, verifying certifications, requesting samples, and seeking professional consultation. The risk of relying on any information in this guide is borne solely by the reader.
Strategic Sourcing Conclusion and Outlook for ceramic insulator
What Are the Key Takeaways for B2B Buyers of Ceramic Insulators?
In conclusion, strategic sourcing of ceramic insulators presents a significant opportunity for international B2B buyers, particularly in emerging markets across Africa, South America, the Middle East, and Europe. Understanding the different types of ceramic materials—such as alumina and zirconia—along with their unique properties and applications, can enhance decision-making and optimize procurement processes. The durability, cost-effectiveness, and superior insulation capabilities of ceramic insulators make them an essential component in various industries, from electrical to construction.
How Can Buyers Leverage Strategic Sourcing for Competitive Advantage?
By adopting a strategic sourcing approach, buyers can not only reduce costs but also ensure quality and reliability in their supply chain. Engaging with reputable manufacturers and suppliers who understand local market conditions will further enhance procurement efficiency. Additionally, staying informed about technological advancements and market trends will enable buyers to anticipate changes and adapt accordingly.
What’s Next for International B2B Buyers in the Ceramic Insulator Market?
As the global demand for sustainable and high-performance materials continues to rise, the ceramic insulator market is poised for growth. Buyers are encouraged to explore partnerships with innovative suppliers and invest in research to identify new applications and enhancements in ceramic technology. Embrace the future of sourcing by integrating these insights into your procurement strategy, ensuring your business remains competitive in a rapidly evolving landscape.