Discover Cost-Saving Benefits of Die Cutting (2025)
Introduction: Navigating the Global Market for die cutting
In the dynamic world of manufacturing and packaging, sourcing the right die cutting solutions is crucial for businesses aiming to enhance their product appeal and streamline production processes. Die cutting, a versatile fabrication technique, allows companies to create custom shapes and designs that can significantly differentiate their products in the marketplace. However, international B2B buyers, particularly from regions like Africa, South America, the Middle East, and Europe, often face challenges in identifying reliable suppliers, understanding the various types of die cutting technologies, and evaluating costs associated with these solutions.
This comprehensive guide aims to equip B2B buyers with essential insights into the die cutting market. We will explore the different types of die cutting methods, their applications across various industries, and best practices for supplier vetting. Additionally, we will delve into cost considerations and provide actionable tips for negotiating favorable terms. By understanding these critical aspects, buyers can make informed decisions that not only meet their production needs but also enhance their competitive edge.
As you navigate through this guide, you’ll gain the knowledge needed to confidently source die cutting solutions that align with your business objectives, whether you’re operating in the bustling markets of Nairobi, the emerging economies of Brazil, or the established industries of Germany. Empower yourself with the tools to elevate your purchasing strategy and maximize your investment in die cutting technology.
Understanding die cutting Types and Variations
Type Name | Key Distinguishing Features | Primary B2B Applications | Brief Pros & Cons for Buyers |
---|---|---|---|
Flatbed Die Cutting | Uses a flat die and is versatile for various materials | Packaging, labels, and signage | Pros: High precision; suitable for large sheets. Cons: Slower production speed. |
Rotary Die Cutting | Employs a cylindrical die for continuous cutting | High-volume production, textiles | Pros: Fast and efficient; ideal for long runs. Cons: Higher initial setup costs. |
Laser Die Cutting | Utilizes laser technology for intricate designs | Custom packaging, prototypes | Pros: Extremely precise; no tooling required. Cons: Slower than mechanical methods for large volumes. |
Digital Die Cutting | Uses digital files to cut shapes | Short runs, personalized items | Pros: Quick turnaround; cost-effective for small batches. Cons: Limited material options. |
Steel Rule Die Cutting | Involves a steel rule die for flexible applications | Labels, boxes, and point-of-purchase displays | Pros: Economical for short to medium runs; versatile. Cons: Less durable than other methods. |
What Are the Characteristics of Flatbed Die Cutting?
Flatbed die cutting is a highly versatile method that utilizes a flat die to cut through various materials, including paper, cardboard, and plastics. This technique is particularly advantageous for creating custom packaging, labels, and signage. B2B buyers should consider this option for projects requiring high precision and flexibility in design. However, the trade-off is a slower production speed compared to other methods, making it more suitable for smaller batch runs or projects where detail is paramount.
How Does Rotary Die Cutting Benefit High-Volume Production?
Rotary die cutting employs a cylindrical die and is best known for its efficiency in high-volume production. This method is ideal for industries that require large quantities of products, such as textiles and packaging. Buyers looking to optimize their production lines should consider rotary die cutting for its speed and ability to handle continuous materials. While the initial setup costs can be higher, the long-term savings on labor and time make it a compelling choice for extensive manufacturing needs.
Why Choose Laser Die Cutting for Intricate Designs?
Laser die cutting is distinguished by its use of laser technology, which allows for intricate and precise designs that are often difficult to achieve with traditional methods. This approach is particularly useful for creating custom packaging and prototypes where detail is crucial. B2B buyers should weigh the benefits of precision against the slower production speed, especially for larger volumes. While laser cutting eliminates the need for physical dies, it may not be the most efficient for mass production.
What Are the Advantages of Digital Die Cutting?
Digital die cutting is a contemporary method that utilizes digital files to create shapes, making it ideal for short runs and personalized items. This technique offers a quick turnaround time and is cost-effective for projects that do not require large quantities. For B2B buyers, digital die cutting is an excellent choice for customized products or promotional materials. However, it is essential to note that material options may be limited compared to traditional methods.
When to Consider Steel Rule Die Cutting?
Steel rule die cutting involves a die made of steel rules, making it a flexible and economical option for short to medium runs. This method is widely used for labels, boxes, and point-of-purchase displays. Buyers should consider steel rule die cutting for its versatility and lower costs, particularly when producing smaller batches. However, it is less durable than other die cutting methods, which may impact long-term use in high-volume settings.
Key Industrial Applications of die cutting
Industry/Sector | Specific Application of Die Cutting | Value/Benefit for the Business | Key Sourcing Considerations for this Application |
---|---|---|---|
Packaging | Custom-shaped packaging and labels | Enhanced brand visibility and product appeal | Material compatibility, precision cutting capabilities, lead times |
Automotive | Gaskets and seals for engines and machinery | Improved durability and performance | Tolerance specifications, material properties, supplier reliability |
Electronics | Die-cut components for circuit boards | Streamlined assembly and reduced waste | Custom die design, prototyping capabilities, cost-effectiveness |
Textile & Apparel | Die-cut patterns for fabric and leather goods | Increased efficiency in production | Fabric type, cutting precision, waste minimization |
Medical Devices | Die-cut parts for surgical instruments and tools | Compliance with safety standards and regulations | Sterilization requirements, material certifications, precision |
How Is Die Cutting Used in Packaging and What Problems Does It Solve?
In the packaging industry, die cutting is employed to create custom-shaped packaging and labels that enhance brand visibility. This process allows businesses to design unique packaging that stands out on shelves, thus attracting more customers. For international buyers, especially in regions like Africa and South America, sourcing requires understanding local material compatibility and ensuring that the cutting process can handle various substrates. Additionally, precision in cutting is crucial to maintain product integrity during shipping.
What Are the Applications of Die Cutting in the Automotive Sector?
Die cutting is widely used in the automotive industry for producing gaskets and seals essential for engines and machinery. These components must withstand extreme conditions, making durability a priority. For B2B buyers in the Middle East, where automotive parts must endure high temperatures, sourcing die-cut products involves careful consideration of material properties and tolerance specifications. Ensuring that suppliers can meet these requirements is critical for maintaining vehicle performance and reliability.
How Do Electronics Manufacturers Benefit from Die-Cut Components?
In the electronics sector, die cutting facilitates the creation of components for circuit boards, which streamlines assembly and reduces waste. This efficiency is vital for manufacturers looking to minimize costs and maximize production speed. Buyers in Europe, for instance, should focus on suppliers that offer custom die designs and prototyping capabilities, allowing them to test different configurations before full-scale production. Cost-effectiveness and the ability to meet tight deadlines are also key factors in supplier selection.
What Role Does Die Cutting Play in Textile and Apparel Production?
Die cutting is integral to the textile and apparel industry, where it is used to create precise patterns for fabric and leather goods. This method significantly increases production efficiency by reducing manual cutting time and minimizing fabric waste. For B2B buyers in Africa, understanding the specific fabric types and the required cutting precision is essential when selecting suppliers. Ensuring that the die-cutting process aligns with sustainable practices can also enhance brand reputation.
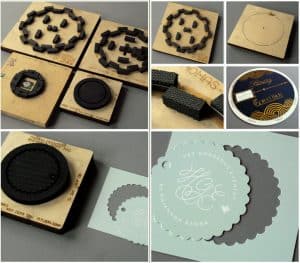
A stock image related to die cutting.
How Is Die Cutting Utilized in the Medical Device Industry?
In the medical device sector, die cutting is employed to produce parts for surgical instruments and tools, ensuring compliance with stringent safety standards. The precision required in this application is paramount, as any deviation can lead to severe consequences. Buyers from the Middle East and Europe must consider suppliers that meet sterilization requirements and possess the necessary material certifications. Additionally, the ability to produce components with high precision is essential for maintaining the integrity of medical devices.
3 Common User Pain Points for ‘die cutting’ & Their Solutions
Scenario 1: High Setup Costs for Custom Die Cutting Projects
The Problem:
Many B2B buyers, especially those in regions like Africa and South America, face significant challenges with the initial setup costs associated with custom die cutting projects. The expense of creating a unique die can be a barrier for small to medium-sized enterprises (SMEs) that wish to differentiate their packaging or products without incurring excessive costs. This scenario often leads to frustration, as buyers may feel compelled to settle for generic solutions that do not truly represent their brand’s identity.
The Solution:
To mitigate high setup costs, buyers should consider leveraging shared die cutting services or partnering with local manufacturers that offer die rental programs. This allows companies to access custom dies without the burden of creating one from scratch. Additionally, collaborating with suppliers that specialize in low-volume runs can provide the flexibility needed for prototypes and limited editions, ensuring that investments are made wisely. When specifying requirements, clear communication about budget constraints and desired outcomes can lead to tailored solutions that maximize cost-effectiveness.
Scenario 2: Inconsistent Quality of Die Cut Products
The Problem:
Inconsistent quality is a prevalent pain point for B2B buyers dealing with die cutting, particularly in the Middle East and Europe. Buyers may receive products that do not meet their specifications, leading to wasted materials, increased costs, and potential damage to their brand reputation. This inconsistency can stem from various factors, including poor die design, subpar materials, or inexperienced operators.
The Solution:
To ensure high-quality die cut products, buyers should prioritize working with reputable suppliers who have a proven track record of quality assurance. Before finalizing any contract, it’s crucial to request samples to evaluate the die cutting process and material quality. Additionally, establishing a clear set of quality standards and performance metrics will help maintain consistency throughout production. Regular communication and feedback loops between the buyer and supplier can also enhance product quality by addressing potential issues proactively before they escalate.
Scenario 3: Limited Design Flexibility with Die Cutting
The Problem:
B2B buyers often encounter limitations in design flexibility when utilizing die cutting for their projects. This is particularly evident in industries that require intricate designs or custom shapes, leading to frustration when suppliers cannot accommodate specific requests. For companies in Europe and the Middle East, where unique branding is crucial, the inability to achieve desired designs can hinder marketing efforts and product appeal.
The Solution:
To overcome design limitations, buyers should seek suppliers that offer advanced die cutting technologies, such as digital die cutting or laser cutting. These methods allow for greater precision and the ability to create complex designs without the constraints of traditional die cutting processes. Additionally, exploring partnerships with design firms that specialize in die cutting can provide innovative solutions tailored to specific branding needs. By providing detailed design briefs and collaborating closely with suppliers, buyers can unlock new creative possibilities that enhance their product offerings and market presence.
Strategic Material Selection Guide for die cutting
What Are the Common Materials Used in Die Cutting?
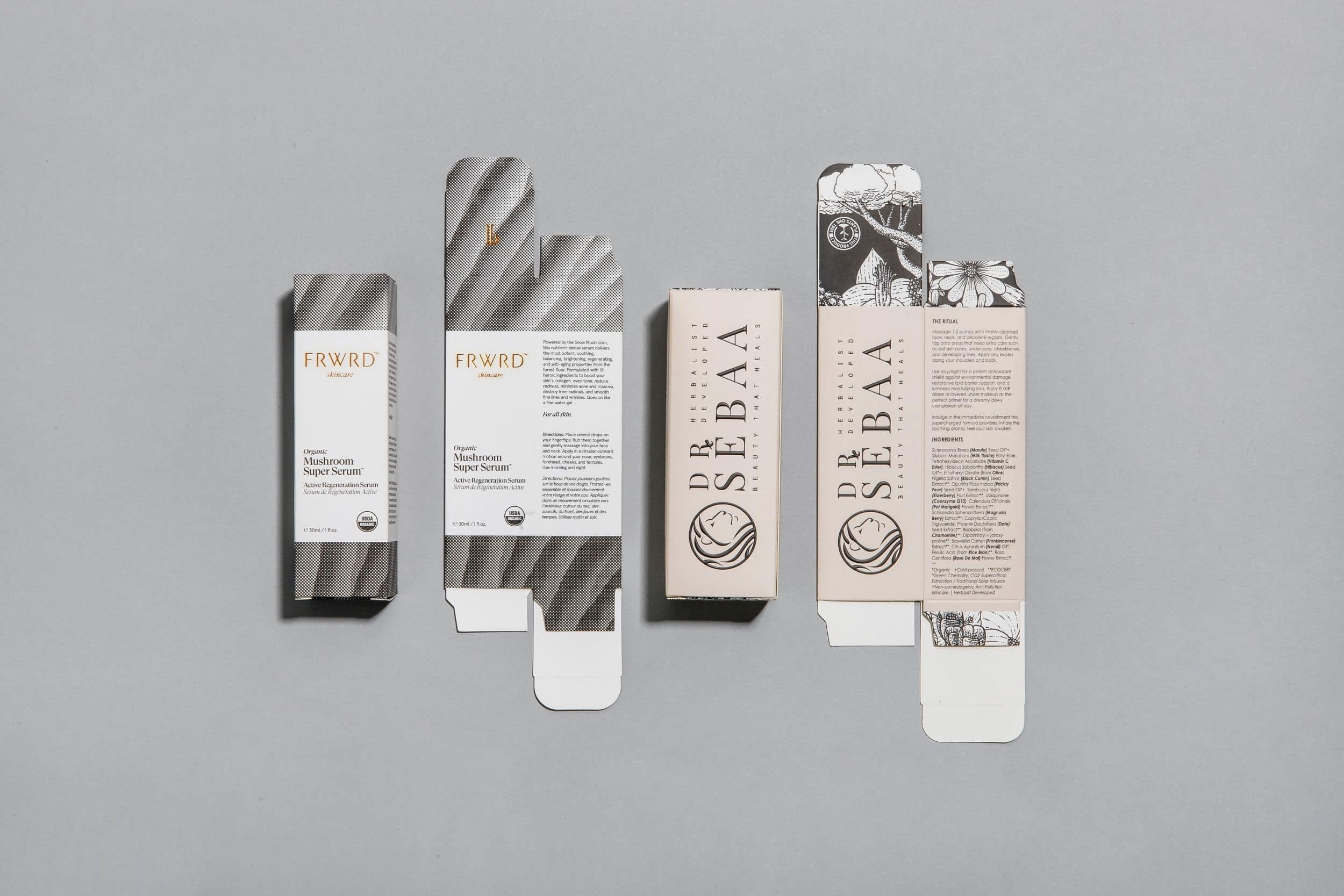
A stock image related to die cutting.
When selecting materials for die cutting, international B2B buyers must consider various factors, including the properties of the material, its suitability for specific applications, and compliance with regional standards. Below, we analyze four common materials used in die cutting, highlighting their key properties, advantages, disadvantages, and specific considerations for buyers in Africa, South America, the Middle East, and Europe.
What Are the Key Properties of Paperboard in Die Cutting?
Key Properties: Paperboard is a versatile material that offers good stiffness and is lightweight. It typically has a temperature rating of up to 120°C and can withstand moderate pressure during the die-cutting process.
Pros & Cons: The primary advantage of paperboard is its cost-effectiveness and ease of printing, making it suitable for packaging and promotional materials. However, it has limited durability compared to other materials and can be susceptible to moisture and bending, which may affect its performance in humid climates.
Impact on Application: Paperboard is ideal for creating packaging, labels, and displays. However, its compatibility with certain inks and coatings should be considered to ensure optimal adhesion and appearance.
Considerations for International Buyers: Buyers should ensure that the paperboard meets local compliance standards, such as those set by ISO or ASTM. In regions like Kenya and Saudi Arabia, understanding local preferences for recycled materials can also influence material selection.
How Does Plastic Perform in Die Cutting Applications?
Key Properties: Plastics, such as polypropylene and polyethylene, are known for their excellent chemical resistance and flexibility. They can handle temperatures ranging from -40°C to 80°C, depending on the specific type of plastic used.
Pros & Cons: The durability and water resistance of plastics make them suitable for a wide range of applications, including food packaging and industrial components. However, they can be more expensive than paperboard and may require specialized die-cutting equipment, increasing manufacturing complexity.
Impact on Application: Plastics are compatible with various printing techniques, making them a popular choice for labels and packaging that require vibrant graphics. However, their environmental impact and recyclability should be considered, especially in regions with strict sustainability regulations.
Considerations for International Buyers: Buyers should be aware of local regulations regarding plastic use and recycling, particularly in Europe, where stringent directives like the EU Plastics Strategy may apply.
What Advantages Do Metals Offer in Die Cutting?
Key Properties: Metals, such as aluminum and stainless steel, provide exceptional strength and durability. They can withstand high temperatures and pressures, making them suitable for heavy-duty applications.
Pros & Cons: The main advantage of using metals in die cutting is their longevity and ability to produce precise cuts. However, they are significantly more expensive than paper or plastic and may require specialized machinery for processing.
Impact on Application: Metals are ideal for industrial applications, including automotive and aerospace components. Their compatibility with various finishing processes, such as anodizing or plating, enhances their usability in demanding environments.
Considerations for International Buyers: Buyers must ensure compliance with international standards, such as ASTM or DIN, when sourcing metal materials. Additionally, understanding local supply chains and sourcing capabilities in regions like South America can help mitigate costs.
What Role Does Foam Play in Die Cutting?
Key Properties: Foam materials, such as EVA (ethylene-vinyl acetate) and polyurethane, are lightweight and flexible, with temperature ratings typically between -20°C and 70°C.
Pros & Cons: The primary advantage of foam is its cushioning properties, making it suitable for protective packaging and insulation. However, foam can be less durable than other materials and may degrade over time, especially when exposed to UV light.
Impact on Application: Foam is commonly used in packaging applications where shock absorption is critical. Its compatibility with adhesives and coatings is also beneficial for customized solutions.
Considerations for International Buyers: Buyers should consider the sourcing of foam materials, particularly in regions with limited manufacturing capabilities. Understanding local preferences for eco-friendly materials can also influence the choice of foam.
Summary Table of Material Selection for Die Cutting
Material | Typical Use Case for die cutting | Key Advantage | Key Disadvantage/Limitation | Relative Cost (Low/Med/High) |
---|---|---|---|---|
Paperboard | Packaging, labels, displays | Cost-effective and easy to print | Limited durability and moisture sensitivity | Low |
Plastic | Food packaging, industrial labels | Excellent chemical resistance | Higher cost and manufacturing complexity | Medium |
Metals | Automotive, aerospace components | Exceptional strength and precision | High cost and specialized machinery required | High |
Foam | Protective packaging, insulation | Lightweight with cushioning properties | Less durable and UV sensitivity | Medium |
This guide provides a comprehensive overview of material selection for die cutting, helping international B2B buyers make informed decisions based on their specific needs and regional considerations.
In-depth Look: Manufacturing Processes and Quality Assurance for die cutting
What Are the Main Stages in Die Cutting Manufacturing Processes?
Die cutting is a specialized manufacturing process that requires precision and attention to detail at every stage. For international B2B buyers, understanding these stages can help in evaluating potential suppliers effectively.
Material Preparation: What Materials Are Used in Die Cutting?
The first stage in the die cutting process is material preparation. The choice of material significantly affects the quality of the final product. Common materials include paper, cardboard, plastics, and metals, depending on the application. Buyers should ensure that the supplier uses high-quality raw materials that meet industry standards, as this directly impacts the durability and performance of the die-cut products.
In preparation, materials are often rolled or stacked and then subjected to cutting, so it’s essential to check if the supplier has the capability to handle the specific types of materials required for your projects.
How Is the Forming Process Executed?
The forming stage involves using a die to cut out shapes from the prepared material. The die is a custom-made tool designed to achieve specific shapes, much like a cookie cutter.
There are several key techniques employed in die cutting:
-
Flatbed Die Cutting: This traditional method uses a flat die and is ideal for larger volumes. It provides high precision and is commonly used for packaging and labels.
-
Rotary Die Cutting: This technique employs a cylindrical die and is suitable for high-speed operations. It’s often used for continuous rolls of material, making it efficient for mass production.
-
Laser Die Cutting: This modern approach uses laser technology for intricate designs, allowing for complex shapes without the need for physical dies. It’s perfect for short runs or prototypes.
Understanding the capabilities of your supplier in these techniques is crucial for ensuring that your specific needs can be met.
What Happens During the Assembly and Finishing Stages?
Once the components are cut, the assembly stage involves bringing together various parts to create the final product. This could involve gluing, stitching, or other methods of joining materials. B2B buyers should inquire about the assembly techniques used and whether they align with the desired product specifications.
The finishing stage may include processes like laminating, coating, or applying adhesives. This not only enhances the appearance but also improves durability. Suppliers should provide information on the finishing options available to ensure that the final product meets your quality expectations.
What Quality Assurance Measures Are Important in Die Cutting?
Quality assurance (QA) is critical in the die cutting industry to ensure that products meet specified standards and are consistent in quality.
Which International Standards Should B2B Buyers Consider?
International standards, such as ISO 9001, are essential for maintaining quality management systems. Suppliers adhering to ISO standards demonstrate their commitment to quality, consistency, and continuous improvement. For specific industries, certifications such as CE (for European markets) or API (for oil and gas) may also be relevant.
B2B buyers from regions like Africa, South America, the Middle East, and Europe should prioritize suppliers who can provide proof of these certifications, as they reflect a commitment to quality that can reduce risks in the supply chain.
What Are the Key Quality Control Checkpoints?
Quality control (QC) is typically implemented at various checkpoints throughout the manufacturing process:
-
Incoming Quality Control (IQC): This involves inspecting raw materials upon arrival to ensure they meet specifications before production begins.
-
In-Process Quality Control (IPQC): During the manufacturing process, regular checks are performed to monitor critical parameters and ensure that the die cutting is executed correctly.
-
Final Quality Control (FQC): After production, a comprehensive inspection is carried out to verify the final product against the agreed specifications.
Understanding these checkpoints allows buyers to gauge how diligent a supplier is about maintaining quality throughout the manufacturing process.
What Testing Methods Are Commonly Used in Die Cutting?
Testing methods in die cutting can vary, but common practices include:
- Dimensional Inspection: Measuring the cut dimensions to ensure they conform to specifications.
- Material Testing: Assessing the strength and durability of the materials used, especially for packaging applications.
- Visual Inspection: Checking for any defects or inconsistencies in the final product.
Buyers should ask suppliers about their testing protocols and whether they provide documentation for these tests, as this can serve as evidence of quality assurance.
How Can B2B Buyers Verify Supplier Quality Control?
To ensure that suppliers maintain high-quality standards, B2B buyers can take several steps:
-
Conduct Audits: Regular audits of suppliers can help verify compliance with quality standards and operational practices.
-
Request QC Reports: Suppliers should be able to provide detailed reports on their quality control processes, including metrics and outcomes from inspections.
-
Engage Third-Party Inspectors: Hiring third-party inspectors can provide an unbiased evaluation of the supplier’s quality control measures and production practices.
What Are the Quality Control Nuances for International Buyers?
International buyers must navigate additional complexities in quality control. These may include:
-
Regulatory Compliance: Different regions have varying regulations regarding materials and safety standards. Buyers should ensure that suppliers are compliant with local regulations in their respective markets.
-
Cultural Differences: Understanding the cultural context of suppliers can aid in communication regarding quality expectations and standards.
-
Logistics Challenges: The logistics of transporting die-cut products across borders can introduce risks. Buyers should work with suppliers to establish clear quality expectations to mitigate potential issues.
By focusing on these areas, B2B buyers can ensure that they select suppliers who not only meet their die cutting needs but also uphold the highest standards of quality assurance.
Practical Sourcing Guide: A Step-by-Step Checklist for ‘die cutting’
When sourcing die cutting services or machinery, it’s essential to follow a structured approach to ensure you meet your specific needs and that the suppliers you engage with can deliver quality results. This checklist will guide you through the critical steps to make informed decisions as an international B2B buyer.
Step 1: Define Your Technical Specifications
Before reaching out to suppliers, clearly outline your technical requirements. This includes the type of material to be die-cut, dimensions, and the complexity of the designs.
- Material Considerations: Different materials (paper, plastic, metal) require specific cutting techniques.
- Design Complexity: Intricate designs may need advanced die cutting technology, impacting costs and lead times.
Step 2: Research Potential Suppliers
Conduct thorough research on potential suppliers to understand their capabilities and reputation. Look for companies with a strong presence in your target regions, such as Africa, South America, the Middle East, and Europe.
- Supplier Experience: Favor suppliers with extensive experience in your industry.
- Client Testimonials: Seek reviews or case studies from previous clients to gauge reliability and quality.
Step 3: Verify Certifications and Compliance
Ensure that the suppliers you consider have the necessary certifications and comply with international standards. This is especially crucial when sourcing from different continents.
- ISO Certifications: Look for ISO 9001 for quality management and ISO 14001 for environmental management.
- Local Regulations: Be aware of any local compliance requirements in your region or the supplier’s location.
Step 4: Request Samples
Before finalizing your order, request samples of previous work. This allows you to evaluate the quality and precision of their die cutting.
- Quality Check: Inspect the samples for accuracy, edge finish, and material compatibility.
- Design Validation: Ensure that the supplier can replicate your designs accurately.
Step 5: Discuss Pricing and Terms
Once you have narrowed down your options, engage in discussions about pricing and terms. Transparency is key to avoiding surprises later in the process.
- Cost Breakdown: Ask for a detailed quote that includes setup fees, production costs, and shipping.
- Payment Terms: Clarify payment methods and schedules to align with your financial processes.
Step 6: Assess Production Capacity and Lead Times
Understanding the supplier’s production capacity is critical, especially for large orders. Discuss lead times to ensure they align with your project timelines.
- Production Capabilities: Inquire about the maximum volume they can handle and whether they can scale if needed.
- Delivery Schedule: Confirm the expected delivery times to plan your supply chain effectively.
Step 7: Establish Clear Communication Channels
Effective communication is vital throughout the sourcing process. Establish clear channels to facilitate ongoing dialogue and updates.
- Point of Contact: Designate a specific contact person for all inquiries and updates.
- Feedback Mechanism: Implement a system for providing feedback on samples and production to ensure alignment.
By following these steps, B2B buyers can effectively navigate the die cutting sourcing process, ensuring they select the right suppliers that meet their specific needs and maintain high standards of quality.
Comprehensive Cost and Pricing Analysis for die cutting Sourcing
What Are the Key Cost Components in Die Cutting Sourcing?
When sourcing die cutting services, understanding the cost structure is vital for international B2B buyers. The primary cost components include:
-
Materials: The type of material chosen significantly impacts pricing. Common materials include paper, cardboard, plastics, and metals, each with varying costs based on thickness and quality.
-
Labor: Skilled labor is required for setup, operation, and quality control. Labor costs can vary widely depending on the region; for instance, labor costs may be lower in certain parts of Africa compared to Europe.
-
Manufacturing Overhead: This includes costs related to utilities, rent, and equipment maintenance. Efficient manufacturers often absorb some of these costs, which can lead to more competitive pricing.
-
Tooling: The creation of custom dies represents a significant upfront investment. Tooling costs can vary based on complexity and the number of dies required. For high-volume orders, these costs can be amortized over more units, reducing the per-unit cost.
-
Quality Control (QC): Ensuring that products meet specified standards can add to costs. Robust QC processes, while increasing upfront expenses, can prevent costly reworks and delays later.
-
Logistics: Transportation and shipping costs are crucial, especially for international buyers. The choice of Incoterms can greatly affect these costs, influencing who bears the responsibility for shipping and duties.
-
Margin: Suppliers will add a profit margin to cover risks and ensure sustainability. This margin can vary depending on the supplier’s market position and the competition level.
How Do Price Influencers Impact Die Cutting Costs?
Several factors influence the pricing of die cutting services, making it essential for buyers to consider these elements:
-
Volume and Minimum Order Quantity (MOQ): Larger orders typically lead to lower per-unit costs. Suppliers may offer discounts for bulk orders, so negotiating volume deals can be beneficial.
-
Specifications and Customization: Custom designs often incur additional costs. Buyers should clearly define their specifications to avoid unexpected charges later in the process.
-
Materials and Quality Certifications: Premium materials and certified quality standards (e.g., ISO certifications) can increase costs. However, investing in higher quality may yield better product performance and customer satisfaction.
-
Supplier Factors: The geographical location and reputation of the supplier can affect pricing. Suppliers in regions with lower operational costs may offer more competitive rates.
-
Incoterms: Understanding Incoterms is crucial for international transactions. They define the responsibilities of buyers and sellers regarding shipping, insurance, and tariffs, impacting the overall cost structure.
What Buyer Tips Can Help Optimize Costs in Die Cutting Sourcing?
International B2B buyers can adopt several strategies to enhance cost efficiency in die cutting sourcing:
-
Negotiate Effectively: Establish a clear understanding of all cost components and be prepared to negotiate terms. Building long-term relationships with suppliers may lead to better pricing and service.
-
Evaluate Total Cost of Ownership (TCO): Look beyond the initial purchase price. Consider maintenance, potential wastage, and logistics costs to get a complete picture of the total expenditure.
-
Stay Informed About Pricing Nuances: Be aware of currency fluctuations, regional economic factors, and international trade agreements that may affect pricing. Buyers from Africa, South America, the Middle East, and Europe should stay updated on these variables.
-
Compare Multiple Suppliers: Solicit quotes from various suppliers to gauge market rates. This practice can help identify competitive pricing and service offerings.
-
Understand Local Regulations: Different regions may have specific regulations affecting material sourcing and production. Understanding these can help avoid compliance-related costs.
Conclusion
While sourcing die cutting services involves various cost components and price influencers, international B2B buyers can leverage strategies to optimize their purchasing decisions. By understanding the underlying factors affecting costs and employing effective negotiation tactics, buyers can secure better deals and enhance their overall sourcing strategy. Keep in mind that prices can vary widely based on numerous factors, and it’s advisable to conduct thorough market research before making commitments.
Alternatives Analysis: Comparing die cutting With Other Solutions
In the realm of manufacturing and product design, die cutting is a widely used method for producing precise shapes and designs from various materials. However, businesses must consider alternative methods that may better suit their specific needs, whether due to cost constraints, production volume, or material compatibility. Below, we will compare die cutting with two viable alternatives: laser cutting and CNC machining.
Comparison Table of Die Cutting and Alternatives
Comparison Aspect | Die Cutting | Laser Cutting | CNC Machining |
---|---|---|---|
Performance | High precision for large runs | Very high precision, versatile | High precision, complex shapes |
Cost | Moderate setup costs; low per unit | Higher initial costs; moderate per unit | High setup costs; varies by complexity |
Ease of Implementation | Requires die creation; longer lead time | Quick setup; no die required | Requires programming and setup |
Maintenance | Low maintenance, durable dies | Moderate maintenance; lens cleaning | High maintenance; tool wear |
Best Use Case | High volume, simple shapes | Complex designs, intricate details | Custom, complex parts; low volume |
What Are the Pros and Cons of Laser Cutting?
Laser cutting is a technology that uses focused laser beams to cut through materials. This method is highly versatile, capable of handling a variety of materials including metal, wood, and plastic.
Pros:
– Precision: Laser cutting offers exceptional accuracy, making it suitable for intricate designs.
– No Tooling Costs: Unlike die cutting, there’s no need for physical dies, reducing initial setup costs.
– Speed: Faster setup times compared to die cutting, especially for short runs.
Cons:
– Costly Equipment: Initial investment for laser cutting machines can be significant.
– Material Limitations: Some materials may not be suitable for laser cutting, such as certain types of plastics that release harmful fumes.
How Does CNC Machining Compare?
CNC (Computer Numerical Control) machining involves the use of computer-controlled tools to remove material from a workpiece. This method is particularly effective for creating complex shapes and parts that require high levels of precision.
Pros:
– Versatility: CNC machines can work with a wide range of materials and produce highly complex shapes.
– Consistency: Once programmed, CNC machining can replicate parts with high fidelity, making it ideal for manufacturing.
– Low Volume Efficiency: Economical for low-volume production runs of complex components.
Cons:
– High Initial Costs: The setup and programming of CNC machines can be expensive.
– Longer Lead Times: More complex setups can lead to longer production times compared to die cutting.
How Should B2B Buyers Choose the Right Solution?
When selecting between die cutting and its alternatives, B2B buyers should assess their unique production needs. If high-volume production of simple shapes is required, die cutting remains an efficient choice. However, for projects demanding intricate designs or flexibility with materials, laser cutting may be more suitable. CNC machining shines in scenarios where custom, complex parts are needed, particularly in lower volumes.
Ultimately, understanding the specific requirements of your project, including budget constraints, material types, and desired production speed, will guide you in selecting the most effective cutting solution for your business.
Essential Technical Properties and Trade Terminology for die cutting
What Are the Key Technical Properties of Die Cutting?
When considering die cutting for your business needs, understanding the essential technical properties can significantly impact your product quality and manufacturing efficiency. Here are some critical specifications to keep in mind:
1. Material Grade
The material grade refers to the type and quality of the stock used in die cutting. Common materials include paper, cardboard, plastic, and metal. Each material has different properties such as strength, flexibility, and weight, affecting the final product’s durability and appearance. Selecting the right material is crucial for aligning with your brand’s quality standards and customer expectations.
2. Tolerance
Tolerance in die cutting refers to the allowable deviation from a specified dimension. It is crucial for ensuring that parts fit together perfectly, especially in assembly processes. A tighter tolerance can lead to higher production costs, while looser tolerances may compromise product integrity. Understanding tolerance levels helps in making informed decisions about the precision required for your project.
3. Die Life
Die life indicates how many cuts a die can produce before it requires replacement or maintenance. A longer die life can reduce operational downtime and overall production costs, making it an important factor when choosing die cutting services. For businesses looking for long-term efficiency, evaluating die life is essential.
4. Cutting Speed
Cutting speed is the rate at which the die cutting machine operates. Higher speeds can lead to increased productivity but may also affect the quality of the cut. Balancing speed with quality is vital for meeting production deadlines without sacrificing product integrity.
5. Surface Finish
The surface finish refers to the texture and smoothness of the die-cut edges. A better finish can enhance the aesthetic appeal of the product and reduce the need for additional processing steps. Understanding surface finish requirements can help in selecting the right die cutting techniques and materials.
What Are Common Trade Terms in Die Cutting?
Familiarity with industry jargon is essential for effective communication and negotiations in die cutting. Here are some common terms you should know:
1. OEM (Original Equipment Manufacturer)
OEM refers to companies that manufacture products that are sold under another company’s brand name. In die cutting, understanding OEM relationships can help you identify potential partners for custom die-cut products that align with your branding.
2. MOQ (Minimum Order Quantity)
MOQ is the minimum number of units a supplier is willing to produce. Knowing the MOQ is crucial for budgeting and inventory management. For international buyers, understanding MOQs can help you negotiate better terms and avoid excess stock.
3. RFQ (Request for Quotation)
An RFQ is a document sent to suppliers requesting price estimates for specific products or services. When sourcing die cutting services, providing a detailed RFQ can lead to more accurate quotes and help you compare offers effectively.
4. Incoterms
Incoterms (International Commercial Terms) define the responsibilities of buyers and sellers in international transactions. They specify who is responsible for shipping, insurance, and tariffs. Understanding Incoterms is critical for international buyers from regions like Africa and South America to avoid misunderstandings and additional costs.
5. Matrix
In die cutting, the matrix refers to the excess material left over after the desired shape has been cut out. Understanding how matrix affects costs and waste management is important for environmentally-conscious businesses looking to minimize their footprint.
Conclusion
Grasping these essential technical properties and trade terminology can empower international B2B buyers, particularly in regions like Africa, South America, the Middle East, and Europe, to make informed decisions in die cutting processes. Whether you are looking for custom products or negotiating terms, this knowledge will enhance your purchasing strategy and operational efficiency.
Navigating Market Dynamics and Sourcing Trends in the die cutting Sector
What Are the Current Market Dynamics and Key Trends in the Die Cutting Sector?
The die cutting industry is experiencing a transformative phase driven by advancements in technology and shifts in consumer preferences. Globally, the demand for customized packaging solutions has surged, primarily due to the rise of e-commerce and the need for brands to differentiate themselves in a crowded marketplace. This trend is particularly relevant for international B2B buyers from regions like Africa, South America, the Middle East, and Europe, where unique product presentation can significantly enhance market appeal.
Emerging technologies such as digital die cutting and automation are reshaping sourcing strategies. Digital die cutting machines offer precision and flexibility, allowing businesses to respond quickly to market changes with minimal waste. For B2B buyers, investing in such technology can streamline production processes and reduce lead times. Moreover, the integration of artificial intelligence in design and production is beginning to optimize operations, enabling tailored solutions that meet specific client needs.
Another noteworthy trend is the increasing focus on cost-efficiency and sustainability. Buyers are seeking suppliers who can offer not only competitive pricing but also innovative solutions that minimize environmental impact. As a result, companies that adopt eco-friendly practices and materials are likely to gain a competitive edge in the marketplace.
How Can Sustainability and Ethical Sourcing Impact Your Die Cutting Operations?
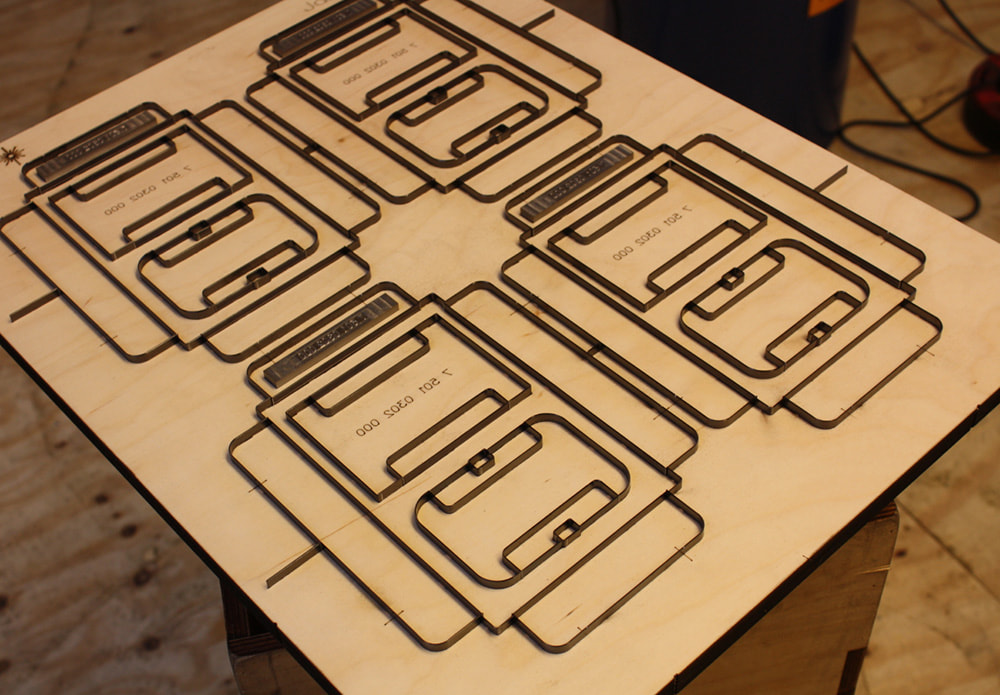
A stock image related to die cutting.
Sustainability is no longer just a buzzword; it has become a critical factor in B2B purchasing decisions. The die cutting sector contributes to environmental challenges, primarily through waste generation and resource consumption. Therefore, buyers are increasingly prioritizing suppliers who demonstrate commitment to ethical sourcing and sustainable practices.
Implementing sustainable practices in die cutting can involve using recycled materials, minimizing waste during the production process, and opting for energy-efficient machinery. Certifications such as FSC (Forest Stewardship Council) for paper products and ISO 14001 for environmental management can assure buyers of a supplier’s commitment to sustainability.
Moreover, ethical supply chains that prioritize fair labor practices and transparency are becoming essential. Buyers from Africa, South America, the Middle East, and Europe are especially keen on partnering with suppliers who can demonstrate responsible sourcing. This not only enhances brand reputation but also aligns with the growing consumer demand for sustainable and ethically produced products.
What Is the Evolution of Die Cutting and Its Relevance to Today’s B2B Landscape?
The die cutting process has evolved significantly since its inception, transitioning from manual techniques to highly sophisticated automated systems. Initially used in small-scale crafts, die cutting has expanded into various sectors, including packaging, textiles, and automotive industries. This evolution is crucial for B2B buyers as it reflects the industry’s adaptability and responsiveness to market demands.
Today, digital die cutting technologies enable rapid prototyping and customization, allowing businesses to innovate quickly. The historical shift from traditional to digital methods has made die cutting more accessible and efficient for international B2B buyers. As the industry continues to evolve, understanding this history can provide valuable context for making informed sourcing decisions that align with current market dynamics and trends.
In summary, the die cutting sector presents numerous opportunities for international B2B buyers, particularly in navigating market dynamics, embracing sustainability, and leveraging the evolution of technology for competitive advantage.
Frequently Asked Questions (FAQs) for B2B Buyers of die cutting
1. How do I choose the right die cutting machine for my business?
Selecting the appropriate die cutting machine hinges on your production needs and material types. Assess the volume of production and the intricacy of the designs you intend to create. For high-volume operations, consider a hydraulic or automatic machine, while manual or semi-automatic machines are suitable for smaller tasks. Additionally, ensure the machine supports the specific materials you plan to use, such as paper, plastic, or metal. Research various brands, read customer reviews, and if possible, test the machines to find the best fit for your operations.
2. What are the key factors to consider when sourcing die cutting suppliers internationally?
When sourcing die cutting suppliers, consider their manufacturing capabilities, quality assurance processes, and experience in your specific industry. Verify their certifications and compliance with international standards. It’s crucial to request samples to assess the quality of their work and ensure they can meet your design specifications. Additionally, evaluate their lead times and shipping options to align with your production schedules. Building a strong relationship through clear communication can also enhance collaboration and reliability.
3. What customization options are typically available for die cutting?
Most die cutting suppliers offer extensive customization options, including shape, size, and material. You can request custom dies to create unique shapes that fit your branding needs. Additionally, inquire about options for embossing, debossing, or printing on the die-cut products. Some suppliers may also offer design assistance to help refine your concepts. Be sure to provide detailed specifications and artwork to ensure the final product aligns with your vision.
4. What are the typical minimum order quantities (MOQs) for die cutting services?
Minimum order quantities for die cutting services can vary significantly based on the supplier and the complexity of the project. Typically, MOQs range from 100 to 1,000 units. However, some suppliers may accommodate smaller orders, particularly for custom designs or prototypes. When negotiating terms, discuss your specific needs and explore the possibility of lower MOQs, especially if you plan to establish a long-term partnership.
5. What payment terms should I expect when sourcing die cutting services?
Payment terms for die cutting services can differ based on the supplier’s policies and your relationship with them. Common arrangements include a deposit of 30-50% upfront, with the remaining balance due upon completion or before shipment. Always clarify payment methods accepted, such as bank transfers or letters of credit. If you are a first-time buyer, suppliers may require more stringent payment terms. Building a trustworthy relationship can lead to more favorable terms over time.
6. How can I ensure quality assurance in die cutting products?
To ensure quality assurance in die cutting products, establish clear specifications and standards before production begins. Request detailed samples and prototypes to assess the quality of materials and craftsmanship. Many suppliers implement quality control measures at various stages of production; inquire about their QA processes. Additionally, consider performing third-party inspections, especially for large orders, to verify that the final products meet your quality expectations before shipment.
7. What logistics considerations should I keep in mind when importing die-cut products?
When importing die-cut products, consider the logistics of shipping costs, customs duties, and delivery timelines. Work with suppliers who have experience in international shipping to navigate these complexities. Ensure your chosen shipping method aligns with your delivery requirements—air freight is faster but more expensive, while sea freight is more economical but takes longer. Prepare all necessary documentation, such as invoices and packing lists, to facilitate a smooth customs clearance process.
8. How do I handle communication barriers when dealing with international die cutting suppliers?
To mitigate communication barriers with international suppliers, establish clear and concise communication channels. Utilize email, instant messaging, or video calls for more effective interactions. If language differences are significant, consider hiring a translator or using translation tools. Always confirm understanding by summarizing key points and decisions after discussions. Regular updates on project status can also enhance transparency and ensure that both parties are aligned throughout the process.
Important Disclaimer & Terms of Use
⚠️ Important Disclaimer
The information provided in this guide, including content regarding manufacturers, technical specifications, and market analysis, is for informational and educational purposes only. It does not constitute professional procurement advice, financial advice, or legal advice.
While we have made every effort to ensure the accuracy and timeliness of the information, we are not responsible for any errors, omissions, or outdated information. Market conditions, company details, and technical standards are subject to change.
B2B buyers must conduct their own independent and thorough due diligence before making any purchasing decisions. This includes contacting suppliers directly, verifying certifications, requesting samples, and seeking professional consultation. The risk of relying on any information in this guide is borne solely by the reader.
Strategic Sourcing Conclusion and Outlook for die cutting
Die cutting has emerged as a crucial process in various industries, particularly for businesses looking to differentiate their products in competitive markets. For international B2B buyers from regions like Africa, South America, the Middle East, and Europe, strategic sourcing of die-cut products can lead to enhanced brand visibility and operational efficiency. By leveraging die cutting, companies can create custom shapes and designs that resonate with their target audience, ultimately driving sales and customer engagement.
To maximize the benefits of die cutting, it is essential to partner with reliable suppliers who understand the nuances of this process. Considerations such as material quality, production capabilities, and delivery timelines are vital in ensuring that your sourcing strategy aligns with your business goals.
Looking ahead, the die cutting market is poised for growth, fueled by advancements in technology and increasing demand for customized solutions. International buyers should stay informed about emerging trends and innovations in die cutting to capitalize on new opportunities. Embrace this transformative approach to manufacturing and take proactive steps in your sourcing strategy—your next successful product launch could depend on it.