Discover Cost-Saving Benefits of Force Sensors (2025)
Introduction: Navigating the Global Market for force sensor
In the rapidly evolving landscape of technology, sourcing the right force sensors can be a daunting challenge for international B2B buyers. These critical devices, which convert mechanical forces into electrical signals, are pivotal in applications ranging from robotics to structural monitoring. Understanding the various types of force sensors, their unique applications, and the intricacies of supplier vetting is essential for making informed purchasing decisions. This guide aims to equip buyers from Africa, South America, the Middle East, and Europe—such as those in Egypt and Spain—with the comprehensive insights necessary to navigate the global market effectively.
Throughout this guide, we will explore the diverse types of force sensors available, including strain gauge, piezoresistive, capacitive, and piezoelectric technologies. Each type serves distinct applications, from sensitive touch detection to robust industrial measurements. Additionally, we will discuss practical considerations like cost factors, quality standards, and how to assess supplier reliability. By synthesizing this information, we empower B2B buyers to not only select the most suitable force sensors for their specific needs but also to negotiate better terms and ensure long-term value from their investments. Whether you’re looking to enhance product design or optimize manufacturing processes, this guide will provide the essential knowledge to make informed and strategic choices in sourcing force sensors.
Understanding force sensor Types and Variations
Type Name | Key Distinguishing Features | Primary B2B Applications | Brief Pros & Cons for Buyers |
---|---|---|---|
Strain Gauge Sensors | High accuracy, versatile; measures tension/compression | Load testing, industrial automation | Pros: High precision, cost-effective; Cons: Sensitive to environmental factors. |
Piezoresistive Sensors | High sensitivity; uses silicon for small force detection | Medical devices, robotics | Pros: Excellent for miniaturization; Cons: Limited range for heavy-duty applications. |
Capacitive Sensors | Detects changes in capacitance; good for small forces | Touchscreens, pressure-sensitive applications | Pros: High sensitivity to light touch; Cons: Affected by environmental changes. |
Piezoelectric Sensors | Generates voltage under mechanical stress; good for dynamic forces | Vibration monitoring, impact detection | Pros: Fast response time; Cons: Not suitable for static force measurements. |
Optical Force Sensors | Utilizes light properties to measure force; high precision | Scientific research, advanced engineering | Pros: Very high accuracy; Cons: Complex setup and potentially higher cost. |
What are the characteristics of Strain Gauge Sensors and their suitability for B2B applications?
Strain gauge sensors are among the most widely used force sensors due to their high accuracy and versatility. They operate by measuring the deformation (strain) of a material when force is applied, which is then converted into an electrical signal. These sensors are particularly suitable for load testing and industrial automation applications, making them ideal for manufacturers and engineers looking to ensure product quality and performance. When considering a strain gauge sensor, buyers should evaluate factors such as environmental conditions, as these sensors can be sensitive to temperature and humidity fluctuations.
How do Piezoresistive Sensors work, and what are their key purchasing considerations?
Piezoresistive sensors utilize materials like silicon that change their electrical resistance when subjected to pressure or force. This property allows for high sensitivity, making these sensors perfect for applications in medical devices and robotics where precise measurements are critical. Buyers should consider the sensor’s range and sensitivity, as these sensors are best for small forces and may not perform well in heavy-duty scenarios. Additionally, compatibility with existing systems is crucial for seamless integration.
What advantages do Capacitive Sensors offer for specific applications?
Capacitive sensors operate by detecting changes in capacitance resulting from force application. They excel in applications requiring the detection of small forces, such as touchscreens and pressure-sensitive devices. Their high sensitivity allows for accurate readings with minimal force, making them suitable for consumer electronics and light industrial applications. However, buyers should be aware that capacitive sensors can be affected by environmental factors such as humidity and temperature, which may impact performance in certain conditions.
What are the unique features of Piezoelectric Sensors and their ideal applications?
Piezoelectric sensors generate an electrical voltage when mechanical stress is applied, making them ideal for dynamic force measurements like vibration monitoring and impact detection. Their fast response time allows them to capture rapid changes in force, which is essential in applications like automotive testing and machinery monitoring. Buyers should note that piezoelectric sensors are not suitable for static force measurements, so understanding the specific application requirements is vital when selecting this type of sensor.
Why are Optical Force Sensors considered advanced in precision measurement?
Optical force sensors utilize changes in light properties to measure force, offering exceptionally high precision. They are often used in scientific research and advanced engineering applications where accuracy is paramount. While they provide significant advantages in terms of measurement capabilities, buyers should consider the complexity of setup and potential costs associated with these systems. Additionally, the need for specialized knowledge to operate and maintain optical sensors can influence purchasing decisions for businesses looking for user-friendly solutions.
Key Industrial Applications of force sensor
Industry/Sector | Specific Application of Force Sensor | Value/Benefit for the Business | Key Sourcing Considerations for this Application |
---|---|---|---|
Manufacturing | Quality Control in Assembly Lines | Ensures product consistency, reducing waste and rework. | Accuracy, calibration, and compatibility with existing systems. |
Automotive | Load Testing of Components | Validates safety and performance, enhancing product reliability. | Sensor capacity, response time, and environmental resistance. |
Aerospace | Structural Integrity Testing | Identifies potential failures, ensuring safety and compliance. | High precision, range of force measurement, and certification standards. |
Robotics | Grasping and Manipulation | Improves interaction with objects, enhancing efficiency. | Sensitivity, size, and integration capabilities with robotic systems. |
Healthcare | Patient Monitoring Devices | Increases patient safety and comfort through accurate measurements. | Biocompatibility, reliability, and ease of integration into devices. |
How Are Force Sensors Used in Manufacturing for Quality Control?
In manufacturing, force sensors play a critical role in quality control on assembly lines. They measure the force exerted during the assembly process to ensure that components are fitted correctly and consistently. This application helps reduce waste and rework by identifying deviations in assembly force, thus maintaining product quality. For international B2B buyers, especially from regions like Africa and South America, sourcing sensors that offer high accuracy and compatibility with existing systems is essential to streamline operations and minimize costs.
What Role Do Force Sensors Play in Automotive Load Testing?
In the automotive industry, force sensors are utilized for load testing various components, from brakes to suspension systems. They validate the safety and performance of parts under different force conditions, ensuring that vehicles meet regulatory standards and customer expectations. For buyers in Europe and the Middle East, it’s crucial to select sensors with the appropriate capacity and response time to handle the rigorous testing environments typical in automotive applications.
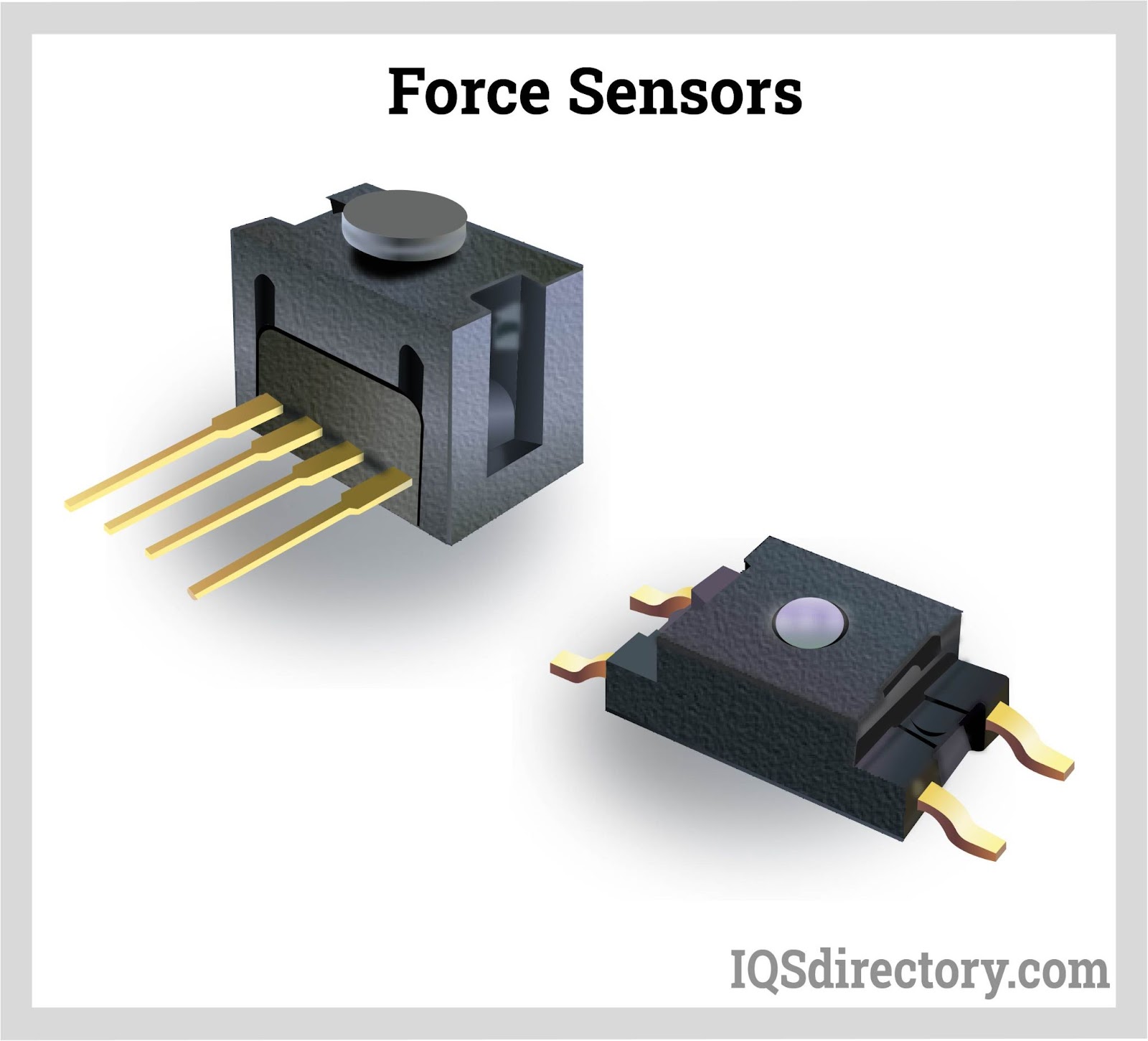
A stock image related to force sensor.
How Do Force Sensors Ensure Structural Integrity in Aerospace?
Force sensors are vital in aerospace for structural integrity testing of aircraft components. They help identify potential failures by measuring forces during stress tests, ensuring compliance with stringent safety regulations. Buyers, particularly from regions like Europe, must prioritize high precision and a wide range of force measurement capabilities when sourcing these sensors, as aerospace applications require rigorous standards and certifications.
Why Are Force Sensors Important for Robotics Grasping and Manipulation?
In robotics, force sensors enhance the ability of robots to interact with objects through precise grasping and manipulation. They provide feedback on the force being applied, allowing robots to adjust their grip, which is crucial for delicate tasks. Buyers from Africa and South America should focus on sourcing sensors that offer high sensitivity and compact designs to integrate seamlessly into robotic systems, maximizing operational efficiency.
How Do Force Sensors Improve Patient Monitoring in Healthcare?
In healthcare, force sensors are incorporated into patient monitoring devices to track various parameters, such as pressure and force applied to patients. This application significantly enhances patient safety and comfort by ensuring accurate measurements. For international B2B buyers, particularly in the Middle East and Europe, sourcing sensors that are biocompatible and reliable is essential for integrating them into medical devices, ensuring compliance with health regulations and standards.
3 Common User Pain Points for ‘force sensor’ & Their Solutions
Scenario 1: Inaccurate Measurements Leading to Production Delays
The Problem: Many B2B buyers face significant challenges when their force sensors provide inaccurate measurements. This issue can stem from improper calibration or selection of the wrong type of sensor for specific applications. For example, a manufacturer in Egypt utilizing a piezoelectric force sensor for delicate assembly tasks may experience inconsistent readings, leading to defective products and production delays. The financial implications are severe, as rework costs, lost time, and potential damage to client relationships can accumulate rapidly.
The Solution: To mitigate this issue, buyers should prioritize the selection of the right sensor technology for their specific application. It is essential to thoroughly assess the operating environment, including the range of forces to be measured, sensitivity requirements, and potential interference from surrounding equipment. Regular calibration should also be mandated as part of the maintenance schedule. Working with reputable suppliers who offer comprehensive support and training can ensure that the sensors are correctly configured and maintained, thus enhancing measurement accuracy and reliability. Furthermore, incorporating robust testing procedures before full-scale production can help identify any discrepancies early in the process, preventing costly delays.
Scenario 2: High Costs Associated with Sensor Failure
The Problem: B2B buyers often encounter significant costs stemming from force sensor failures. A case from South America illustrates this point: a company invested heavily in advanced force sensors for a robotics application. However, frequent sensor malfunctions led to unexpected downtimes and increased maintenance costs. This situation not only strained the budget but also jeopardized project timelines and customer satisfaction.
The Solution: To counteract these challenges, buyers should conduct thorough due diligence when sourcing force sensors. Prioritize purchasing from manufacturers known for high reliability and robust product testing. It’s also beneficial to consider the total cost of ownership, including installation, maintenance, and potential downtime costs. Implementing a proactive maintenance strategy, including regular inspections and timely updates of sensor firmware, can extend the lifespan of the sensors and reduce the risk of unexpected failures. Moreover, investing in training for staff on proper handling and usage can minimize human errors that contribute to sensor damage.
Scenario 3: Limited Compatibility with Existing Systems
The Problem: A common challenge faced by buyers, particularly in the Middle East and Europe, is the limited compatibility of new force sensors with existing systems. For instance, a company in Spain may want to upgrade its force measurement capabilities but finds that new sensors cannot easily integrate with their current data acquisition systems. This incompatibility can lead to increased costs and extended project timelines as new software or hardware may need to be purchased.
The Solution: To address compatibility issues, buyers should conduct a comprehensive analysis of their existing systems before sourcing new force sensors. Engage with suppliers who provide detailed technical specifications and compatibility information. Choosing sensors that offer standardized communication protocols, such as I2C or SPI, can facilitate easier integration. Additionally, involving the IT department early in the process ensures that all technical requirements are met. Establishing a close working relationship with sensor manufacturers can also yield insights into integration solutions and customizations that may be necessary for seamless operation. This proactive approach not only saves time and money but also enhances operational efficiency in the long run.
Strategic Material Selection Guide for force sensor
When selecting materials for force sensors, international B2B buyers must consider various factors that influence performance, durability, and application suitability. Below is an analysis of four common materials used in force sensor manufacturing, detailing their properties, advantages, disadvantages, and specific considerations for buyers from regions like Africa, South America, the Middle East, and Europe.
What Are the Key Properties of Aluminum in Force Sensors?
Aluminum is a lightweight yet robust material often used in force sensors, particularly in applications requiring moderate strength and corrosion resistance. Its properties include:
- Temperature Rating: Aluminum can withstand temperatures up to 150°C.
- Corrosion Resistance: Naturally forms a protective oxide layer, making it suitable for various environments.
Pros: Aluminum is relatively inexpensive and easy to machine, allowing for efficient manufacturing processes. Its lightweight nature makes it ideal for portable applications.
Cons: While durable, aluminum can be less robust than steel under extreme stress. It may also require additional coatings for enhanced corrosion resistance in harsh environments.
Impact on Application: Aluminum force sensors are commonly used in automotive and aerospace applications where weight savings are critical.
Considerations for International Buyers: Buyers should ensure compliance with international standards like ASTM and DIN, particularly for aerospace and automotive applications.
How Does Stainless Steel Perform in Force Sensor Applications?
Stainless steel is a preferred material for force sensors due to its excellent mechanical properties and corrosion resistance. Key properties include:
- Temperature Rating: Can endure temperatures up to 300°C.
- Corrosion Resistance: Highly resistant to oxidation and corrosion, making it ideal for harsh environments.
Pros: Stainless steel offers high strength and durability, making it suitable for heavy-duty applications. Its resistance to corrosion enhances longevity.
Cons: The cost of stainless steel is higher than aluminum, and its manufacturing can be more complex due to its hardness.
Impact on Application: Stainless steel sensors are often used in industrial applications, including manufacturing and material testing, where reliability is paramount.
Considerations for International Buyers: Compliance with standards such as JIS for industrial applications is crucial, especially in regions with stringent quality requirements.
What Are the Benefits of Using Silicon in Force Sensors?
Silicon is widely used in piezoresistive force sensors due to its unique electrical properties. Key properties include:
- Temperature Rating: Typically operates effectively up to 125°C.
- Pressure Rating: Can handle pressures up to 1000 psi.
Pros: Silicon sensors are highly sensitive and can detect minute changes in force, making them suitable for delicate applications like robotics and consumer electronics.
Cons: Silicon is less durable compared to metals and can be sensitive to environmental conditions such as humidity and temperature fluctuations.
Impact on Application: Silicon-based sensors are ideal for applications in consumer electronics and medical devices, where precision is crucial.
Considerations for International Buyers: Buyers should consider the compatibility of silicon sensors with specific media, especially in medical applications, and ensure compliance with relevant health and safety standards.
Why Choose Polymer Materials for Force Sensors?
Polymers, particularly conductive polymers, are increasingly used in force sensors for their flexibility and lightweight properties. Key properties include:
- Temperature Rating: Generally suitable for temperatures up to 80°C.
- Corrosion Resistance: Excellent resistance to chemical corrosion.
Pros: Polymers are lightweight and can be manufactured in various shapes, making them versatile for different applications. They are also cost-effective.
Cons: Polymers may not withstand high temperatures or extreme mechanical stress, limiting their application in heavy-duty environments.
Impact on Application: Ideal for applications requiring flexibility, such as wearable technology and soft robotics.
Considerations for International Buyers: Ensure that polymer materials meet relevant standards for durability and safety, especially in consumer products.
Summary Table of Material Selection for Force Sensors
Material | Typical Use Case for Force Sensor | Key Advantage | Key Disadvantage/Limitation | Relative Cost (Low/Med/High) |
---|---|---|---|---|
Aluminum | Automotive, aerospace applications | Lightweight and cost-effective | Less robust under extreme stress | Low |
Stainless Steel | Industrial applications, material testing | High strength and corrosion resistance | Higher cost and complex manufacturing | High |
Silicon | Consumer electronics, medical devices | High sensitivity for minute changes | Less durable, sensitive to environment | Medium |
Polymer | Wearable technology, soft robotics | Lightweight and versatile | Limited temperature and stress tolerance | Low |
This strategic material selection guide provides actionable insights for international B2B buyers, helping them make informed decisions based on the specific requirements and standards of their respective markets.
In-depth Look: Manufacturing Processes and Quality Assurance for force sensor
What Are the Key Stages in the Manufacturing Process of Force Sensors?
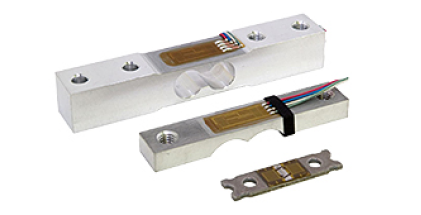
A stock image related to force sensor.
The manufacturing process of force sensors is intricate and involves several key stages to ensure the final product meets industry standards and customer expectations. Here’s a breakdown of the typical stages involved:
Material Preparation
The first step in manufacturing force sensors is the selection and preparation of materials. Common materials include metals like aluminum and stainless steel for structural components, as well as specialized materials such as silicon and piezoelectric crystals for sensing elements.
- Material Sourcing: It is crucial to source high-quality materials that comply with international standards. B2B buyers should look for suppliers that can provide certifications for their materials, ensuring they meet relevant quality benchmarks.
Forming and Fabrication Techniques
Once the materials are prepared, they undergo various forming techniques:
- Machining: This includes cutting, milling, and drilling to create the necessary shapes and sizes for sensor components.
- Welding and Joining: Techniques such as laser welding or adhesive bonding are often employed to assemble different parts securely.
- Molding: In some cases, particularly for encapsulated sensors, molding techniques are used to create protective casings.
Each of these methods must adhere to strict tolerances to ensure the sensors function accurately.
Assembly Process
After the components are fabricated, they are assembled into the final product. This stage typically involves:
- Integration of Sensing Elements: For example, strain gauges or piezoelectric crystals are integrated into the sensor body.
- Calibration: Sensors are calibrated to ensure accurate measurements. This process involves applying known forces and adjusting the output to match expected results.
- Encapsulation: Many force sensors are encapsulated to protect them from environmental factors such as moisture and dust, which could affect performance.
Finishing Touches
The final stage of manufacturing involves finishing processes that enhance durability and performance:
- Surface Treatment: Techniques like anodizing or coating are applied to improve corrosion resistance and wear.
- Quality Control Checkpoints: After assembly, each sensor typically undergoes a thorough inspection and testing phase to ensure it meets quality standards.
How Is Quality Assurance Implemented in Force Sensor Manufacturing?
Quality assurance (QA) is critical in the manufacturing of force sensors, ensuring that each unit meets the required specifications and performance standards. Here are some essential QA processes that B2B buyers should be aware of:
What International Standards Should B2B Buyers Look For?
Manufacturers often adhere to various international standards to ensure product quality and safety. Relevant standards include:
- ISO 9001: This standard focuses on quality management systems, ensuring that manufacturers consistently provide products that meet customer and regulatory requirements.
- CE Marking: In Europe, CE marking indicates that products meet EU safety, health, and environmental protection requirements.
- API Standards: For industries such as oil and gas, compliance with API standards ensures that the products are suitable for use in demanding environments.
B2B buyers should prioritize suppliers that can demonstrate compliance with these standards, as it reflects their commitment to quality.
What Are the Key Quality Control Checkpoints?
Quality control checkpoints are crucial in the manufacturing process of force sensors. Common checkpoints include:
- Incoming Quality Control (IQC): This involves inspecting raw materials upon arrival to ensure they meet specified standards.
- In-Process Quality Control (IPQC): During the manufacturing process, regular checks are conducted to monitor production quality and adherence to specifications.
- Final Quality Control (FQC): This final inspection ensures that each sensor is functioning correctly and meets all performance metrics before shipment.
What Testing Methods Are Commonly Used for Force Sensors?
Testing methods are vital for validating the performance and reliability of force sensors. Common testing methods include:
- Static and Dynamic Testing: These tests measure the sensor’s performance under various conditions, ensuring it can accurately measure both static and dynamic forces.
- Environmental Testing: This assesses how well sensors perform under different environmental conditions, such as extreme temperatures and humidity.
- Calibration Tests: These ensure that the sensor output aligns with known force values, validating the accuracy of the measurement.
How Can B2B Buyers Verify Supplier Quality Control Practices?
For international B2B buyers, especially those from Africa, South America, the Middle East, and Europe, verifying supplier quality control practices is essential. Here are actionable steps:
- Supplier Audits: Conducting supplier audits can provide insight into their manufacturing processes and quality assurance practices. This can help identify any gaps in compliance with international standards.
- Quality Reports: Requesting detailed quality reports and test results can help buyers assess the reliability of the sensors.
- Third-Party Inspections: Engaging third-party inspection agencies can provide an unbiased evaluation of the supplier’s quality control systems and product performance.
What Are the Unique Challenges for International B2B Buyers Regarding Quality Control?
International buyers may face unique challenges related to quality control, including:
- Regulatory Variances: Different regions may have varying regulatory requirements for force sensors. Buyers should familiarize themselves with the regulations specific to their region.
- Cultural Differences in Quality Expectations: Understanding cultural nuances in quality expectations can help in establishing clear communication with suppliers.
- Logistical Considerations: Shipping and customs regulations can complicate the procurement process, so buyers should ensure that suppliers are well-versed in international logistics.
By understanding these manufacturing processes and quality assurance practices, B2B buyers can make informed decisions when sourcing force sensors, ensuring they select reliable suppliers that meet their specific needs.
Practical Sourcing Guide: A Step-by-Step Checklist for ‘force sensor’
In this section, we provide a practical sourcing guide for B2B buyers interested in procuring force sensors. This checklist will help streamline your purchasing process, ensuring you make informed decisions that align with your operational needs.
Step 1: Define Your Technical Specifications
Start by clearly outlining the technical requirements for your force sensor. Consider factors such as the range of forces you need to measure, the environment in which the sensor will operate, and the required sensitivity. A well-defined specification helps in narrowing down options and ensures compatibility with your existing systems.
- Force Range: Determine the minimum and maximum forces the sensor must measure.
- Environmental Conditions: Assess if the sensor needs to withstand harsh conditions such as humidity, temperature extremes, or exposure to chemicals.
Step 2: Research Different Force Sensor Technologies
Familiarize yourself with the various force sensor technologies available, such as strain gauge, piezoresistive, capacitive, and piezoelectric. Each technology has its own strengths and applications, so understanding these can help you choose the right sensor for your needs.
- Application Suitability: Evaluate which technology best fits your application, whether it’s for delicate touch sensing or heavy load monitoring.
- Performance Characteristics: Look into sensitivity, accuracy, and response time associated with each technology.
Step 3: Evaluate Potential Suppliers
Before committing to a purchase, thoroughly vet potential suppliers. Request company profiles, case studies, and references from buyers in similar industries or regions. This step is crucial in ensuring that the supplier has a proven track record.
- Certifications: Check for industry-standard certifications such as ISO 9001, which can indicate quality management practices.
- Support Services: Investigate if the supplier offers post-sale support, including installation, maintenance, and technical assistance.
Step 4: Request Samples and Conduct Testing
Once you have shortlisted suppliers, request samples of the force sensors you are considering. Conduct hands-on testing to evaluate their performance under actual operating conditions. This practical evaluation is vital to ascertain if the sensors meet your specifications.
- Testing Parameters: Consider testing for accuracy, durability, and response time in real-world scenarios.
- User Feedback: Gather insights from your team about the usability and integration of the sensor with your systems.
Step 5: Compare Pricing and Total Cost of Ownership
While price is a significant factor, it’s essential to evaluate the total cost of ownership (TCO) of the force sensors. This includes not just the initial purchase price but also maintenance, calibration, and potential downtime costs.
- Long-term Value: Analyze whether a more expensive sensor could offer better durability and lower maintenance costs over time.
- Bulk Discounts: Inquire about pricing for bulk orders, as many suppliers offer discounts for larger purchases.
Step 6: Review Terms and Conditions
Before finalizing your purchase, closely review the supplier’s terms and conditions. Pay attention to warranty periods, return policies, and delivery timelines. This step can save you potential headaches down the line.
- Warranty Coverage: Understand what is covered under the warranty and the duration of coverage.
- Return Policy: Ensure there is a clear return policy in case the sensors do not meet your expectations upon delivery.
Step 7: Finalize the Purchase and Monitor Performance
Once you’ve completed all evaluations and are satisfied with your choice, proceed to finalize the purchase. After implementation, monitor the performance of the force sensors to ensure they meet your operational needs and provide feedback to the supplier for continuous improvement.
- Performance Tracking: Set up metrics to evaluate sensor performance over time.
- Supplier Communication: Maintain open lines of communication with your supplier for any future needs or issues.
By following this checklist, B2B buyers can navigate the complexities of sourcing force sensors, ensuring they select the right technology and supplier for their specific needs.
Comprehensive Cost and Pricing Analysis for force sensor Sourcing
What Are the Key Cost Components in Force Sensor Manufacturing?
When sourcing force sensors, understanding the various cost components is critical for B2B buyers. The primary cost elements include:
-
Materials: The choice of materials significantly influences the cost. Common materials like silicon for piezoresistive sensors or various alloys for strain gauges can vary widely in price based on quality and sourcing location.
-
Labor: Labor costs are affected by the region where manufacturing occurs. Countries with higher labor costs, such as those in Western Europe, may see increased prices compared to those in regions with lower labor costs like parts of Africa and South America.
-
Manufacturing Overhead: This includes utilities, rent, and equipment depreciation. Efficient production processes can lower these costs, which is crucial for competitive pricing.
-
Tooling: Initial setup costs for molds and specialized equipment can be significant, particularly for custom designs. These costs are amortized over the production run, impacting unit pricing.
-
Quality Control (QC): Rigorous testing and certification processes add to the cost but are essential for ensuring product reliability, particularly in high-stakes applications.
-
Logistics: Shipping costs vary based on the distance from the manufacturer to the buyer, as well as the chosen logistics provider. International shipping can introduce additional tariffs and duties.
-
Margin: Supplier margins can fluctuate based on market demand and competition. Established suppliers may command higher margins due to brand trust and quality assurance.
How Do Volume and Customization Affect Force Sensor Prices?
Pricing for force sensors is heavily influenced by order volume and customization:
-
Volume/MOQ: Higher order volumes typically lead to lower per-unit costs due to economies of scale. Buyers should negotiate minimum order quantities (MOQs) to maximize cost efficiency.
-
Specifications and Customization: Customized sensors tailored to specific applications can lead to increased costs. Buyers should clearly define their requirements to avoid unexpected charges during the production process.
-
Materials and Quality Certifications: Sensors made from higher-quality materials or those that meet specific certifications (e.g., ISO standards) will generally be more expensive. Buyers should balance the need for quality with their budget constraints.
What Buyer Tips Can Enhance Cost Efficiency in Force Sensor Sourcing?
International B2B buyers can adopt several strategies to optimize their sourcing process:
-
Negotiation: Engage suppliers in discussions about pricing structures and potential discounts for bulk orders. Building a long-term relationship can also lead to better terms.
-
Total Cost of Ownership (TCO): Consider not only the initial purchase price but also installation, maintenance, and operational costs over the sensor’s lifecycle. A slightly higher upfront cost might yield savings in the long run.
-
Pricing Nuances for International Buyers: Be aware of currency fluctuations, import duties, and local taxes that can affect the total cost. Understanding Incoterms can clarify responsibilities regarding shipping and delivery, helping to avoid unexpected expenses.
-
Supplier Factors: Research potential suppliers thoroughly. Assess their reliability, production capabilities, and customer service. This can significantly impact not only the initial cost but also the overall purchasing experience.
What Are Some Indicative Prices for Force Sensors?
While prices can vary based on the aforementioned factors, indicative prices for force sensors range widely. For example, basic strain gauge sensors may start at around $700, while more advanced piezoelectric sensors can exceed $1,800. Always consult with multiple suppliers to get a comprehensive view of the market pricing.
Conclusion
Understanding the cost structure and pricing dynamics of force sensors is essential for international B2B buyers. By focusing on key cost components, negotiating effectively, and considering the total cost of ownership, buyers can make informed decisions that align with their operational needs and budget constraints.
Alternatives Analysis: Comparing force sensor With Other Solutions
When evaluating solutions for measuring mechanical forces, it’s crucial to consider various alternatives to force sensors. Understanding these alternatives will help B2B buyers make informed decisions tailored to their specific needs, especially in diverse markets across Africa, South America, the Middle East, and Europe. Below, we compare force sensors against two viable alternatives: load cells and piezoelectric sensors.
Comparison Aspect | Force Sensor | Load Cell | Piezoelectric Sensor |
---|---|---|---|
Performance | High accuracy across various ranges | Excellent for static weight measurement | Ideal for dynamic force measurements |
Cost | Moderate to high (e.g., $700 – $1,840) | Moderate (e.g., $500 – $1,500) | Lower initial cost (e.g., $300 – $800) |
Ease of Implementation | Requires calibration and setup | Straightforward installation; often plug-and-play | Moderate; requires precise alignment |
Maintenance | Low, but calibration needed periodically | Low; minimal maintenance required | Moderate; can be affected by environmental factors |
Best Use Case | General force measurement in robotics and industrial applications | Weighing applications and static load monitoring | Impact testing and dynamic load applications |
What Are Load Cells and Their Advantages?
Load cells are widely used for measuring weight and force, particularly in industrial applications. They operate based on the principle of converting force into an electrical signal, typically using strain gauges.
Pros:
– Accuracy: Load cells provide precise measurements for static loads, making them suitable for applications like platform scales.
– Durability: They are built to withstand harsh environments, which is essential for industries in Africa and South America where conditions can be challenging.
Cons:
– Limited Dynamic Measurement: Load cells may not perform well in dynamic situations where forces change rapidly, such as in impact testing.
How Do Piezoelectric Sensors Work and What Are Their Benefits?
Piezoelectric sensors generate an electrical charge in response to applied mechanical stress. This property makes them particularly effective for measuring dynamic forces.
Pros:
– Sensitivity: Piezoelectric sensors are highly sensitive and can detect minute changes in force, making them ideal for applications like vibration monitoring.
– Quick Response: They are excellent for applications requiring real-time measurements, such as in automotive testing.
Cons:
– Calibration Requirements: These sensors can require regular calibration to maintain accuracy, and their performance can be influenced by environmental factors such as temperature and humidity.
Conclusion: How to Choose the Right Solution for Your Needs
When choosing between force sensors, load cells, and piezoelectric sensors, B2B buyers should consider their specific application requirements. If the primary need is for precise static measurements, load cells may be the best choice. For applications involving dynamic measurements, piezoelectric sensors can provide superior sensitivity. Force sensors, with their versatility, are ideal for a range of applications but may come with higher costs and more complex installation processes. By carefully assessing performance needs, budget constraints, and the operational environment, international buyers can select the most appropriate technology to achieve their measurement goals effectively.
Essential Technical Properties and Trade Terminology for force sensor
What Are the Essential Technical Properties of Force Sensors?
When selecting a force sensor for your application, understanding its technical properties is crucial. Here are some key specifications to consider:
1. Material Grade
The material of the force sensor can significantly impact its performance, durability, and suitability for specific environments. Common materials include stainless steel, aluminum, and specialized polymers. For instance, stainless steel is often chosen for its corrosion resistance, making it ideal for industrial applications in harsh environments. Understanding material grade helps buyers ensure the sensor can withstand operational conditions, reducing maintenance costs and prolonging equipment life.
2. Measurement Range
The measurement range defines the minimum and maximum forces that a sensor can accurately measure. It is essential to choose a sensor with a range that aligns with the expected forces in your application. A sensor with too narrow a range may not provide accurate data, while one with an excessively high range could be more expensive than necessary. This parameter is critical for ensuring the sensor meets the operational demands of your business.
3. Sensitivity
Sensitivity refers to the sensor’s ability to detect small changes in force. Higher sensitivity is vital for applications that require precision, such as in laboratory settings or delicate manufacturing processes. For B2B buyers, knowing the sensitivity helps in selecting a sensor that aligns with the specific needs of their application, ensuring accurate measurements without overspending on unnecessary features.
4. Tolerance
Tolerance indicates the allowable deviation from the specified measurement. It is a critical property as it defines the sensor’s accuracy and reliability. A lower tolerance means higher precision, which is essential in applications where force measurements impact quality control or safety. Buyers should consider the tolerance level required for their applications to avoid costly errors.
5. Output Signal Type
Force sensors can produce different types of output signals, such as analog voltage, digital signals, or current outputs. The choice of output type should align with the existing systems and data acquisition methods within your operation. Understanding the output signal type is crucial for integration into your existing technology stack, ensuring seamless operation and data analysis.
What Are Common Trade Terms Related to Force Sensors?
Navigating the procurement of force sensors involves understanding specific industry terminology. Here are some essential terms that B2B buyers should be familiar with:
1. OEM (Original Equipment Manufacturer)
An OEM is a company that produces components that are used in another company’s end product. In the context of force sensors, buyers often work with OEMs to integrate sensors into larger systems or machinery. Understanding OEM relationships can help buyers negotiate better pricing and ensure compatibility with existing equipment.
2. MOQ (Minimum Order Quantity)
MOQ refers to the smallest number of units that a supplier is willing to sell. This term is significant for B2B buyers as it impacts inventory costs and purchasing strategies. Knowing the MOQ can help businesses plan their orders effectively, especially when considering budget constraints and storage capabilities.
3. RFQ (Request for Quotation)
An RFQ is a document sent to suppliers to solicit pricing and terms for specific products or services. For buyers in need of force sensors, issuing an RFQ can facilitate competitive pricing and better understand supplier offerings. This process is essential for making informed purchasing decisions.
4. Incoterms
Incoterms are international commercial terms that define the responsibilities of buyers and sellers in the shipping process. Understanding Incoterms is crucial for B2B buyers, as they impact shipping costs, risks, and insurance. Familiarity with these terms helps businesses manage their logistics more effectively, especially when dealing with international suppliers.
5. Calibration
Calibration is the process of adjusting and setting a sensor to ensure it measures accurately. For force sensors, proper calibration is vital to maintain measurement integrity over time. B2B buyers should ensure that suppliers provide calibration services or guidelines to uphold the accuracy of their sensors in operational environments.
By understanding these technical properties and trade terms, B2B buyers can make informed decisions when sourcing force sensors, ultimately enhancing operational efficiency and product quality.
Navigating Market Dynamics and Sourcing Trends in the force sensor Sector
What Are the Key Market Dynamics and Trends in the Force Sensor Sector?
The global force sensor market is experiencing significant growth, driven by advancements in technology and increasing demand across various industries, including automotive, aerospace, healthcare, and consumer electronics. Key trends influencing the market include the integration of Internet of Things (IoT) capabilities, which enhances data collection and analysis, and the growing emphasis on automation in manufacturing processes. For international B2B buyers, particularly from regions like Africa, South America, the Middle East, and Europe, understanding these dynamics is crucial for making informed sourcing decisions.
In recent years, the demand for miniaturized and highly sensitive force sensors has surged, particularly in applications such as robotics and medical devices. Buyers are increasingly seeking sensors that offer high precision and reliability, which can be critical for maintaining quality control and enhancing operational efficiency. Moreover, the trend towards smart manufacturing and Industry 4.0 is pushing companies to invest in advanced sensor technologies that facilitate real-time monitoring and predictive maintenance.
Another noteworthy trend is the rise of customized solutions tailored to specific industry needs. This trend enables businesses to optimize performance and reduce costs. International buyers should focus on suppliers that demonstrate flexibility and the capability to deliver tailored sensor solutions. Additionally, emerging markets in Africa and South America are gradually adopting advanced sensor technologies, presenting opportunities for suppliers looking to expand their footprint in these regions.
How Is Sustainability Impacting Sourcing Decisions in the Force Sensor Industry?
Sustainability has become a critical consideration for B2B buyers in the force sensor sector. The environmental impact of manufacturing processes, from resource extraction to production waste, is under increasing scrutiny. Buyers are now prioritizing suppliers that adopt sustainable practices and demonstrate a commitment to reducing their carbon footprint.
Ethical sourcing is equally important, as businesses aim to ensure that their supply chains are free from exploitation and adhere to fair labor practices. Buyers should seek suppliers who provide transparency regarding their sourcing methods and labor conditions. Certifications such as ISO 14001 for environmental management and Fair Trade can serve as indicators of a supplier’s commitment to sustainability and ethical practices.
In the force sensor market, the use of eco-friendly materials is gaining traction. Suppliers that offer ‘green’ certifications for their products or utilize recyclable materials can provide a competitive advantage. By prioritizing sustainability, B2B buyers not only enhance their corporate social responsibility but also appeal to a growing consumer base that values environmentally conscious products.
How Has the Force Sensor Sector Evolved Over Time?
The evolution of force sensors has been marked by significant technological advancements and increasing application diversity. Initially, the industry relied heavily on strain gauge technology, which remains a staple due to its simplicity and effectiveness. Over time, other technologies such as piezoelectric, capacitive, and optical sensors have emerged, broadening the range of applications and enhancing measurement accuracy.
The integration of digital technologies has also transformed the sector, enabling sensors to communicate seamlessly with other devices and systems. This evolution has opened up new possibilities for data analysis and real-time monitoring, particularly in smart manufacturing environments. As industries continue to seek greater efficiency and automation, the demand for advanced force sensors is expected to grow, reflecting the sector’s dynamic nature and its critical role in various technological advancements.
In conclusion, understanding these market dynamics, sustainability considerations, and the historical context of force sensors equips international B2B buyers with the insights needed to make informed sourcing decisions and remain competitive in an evolving landscape.
Frequently Asked Questions (FAQs) for B2B Buyers of force sensor
-
How do I choose the right force sensor for my application?
Choosing the right force sensor involves understanding your specific requirements, including the type of force you need to measure (tension, compression, etc.), the expected force range, and the sensor’s sensitivity. Consider the environment in which the sensor will operate, as factors like temperature, humidity, and potential exposure to chemicals can affect performance. Additionally, evaluate the sensor’s compatibility with your existing systems and whether it requires special mounting or integration. Seeking expert guidance from suppliers can also help clarify your options. -
What are the different types of force sensors available for B2B applications?
Force sensors come in various types, including strain gauge sensors, piezoresistive sensors, capacitive sensors, and piezoelectric sensors. Each type has its unique advantages; for instance, strain gauges are widely used due to their durability and accuracy, while piezoelectric sensors are ideal for dynamic measurements. Understanding the specific requirements of your application—such as precision, response time, and environmental conditions—will help you select the most suitable type for your needs. -
How can I ensure the quality of force sensors from international suppliers?
To ensure quality when sourcing force sensors from international suppliers, conduct thorough research on potential vendors, including their reputation, certifications (ISO, CE), and customer reviews. Request samples and conduct performance tests to evaluate the sensors against your specifications. Additionally, consider suppliers that offer warranties and customer support. Engaging in direct communication can also provide insights into their quality assurance processes, manufacturing capabilities, and adherence to industry standards. -
What are the typical payment terms for purchasing force sensors internationally?
Payment terms can vary widely depending on the supplier and the region. Common options include upfront payment, partial payment upon order confirmation, and balance upon delivery. For larger orders, it may be possible to negotiate credit terms or letters of credit. Always clarify payment methods accepted (such as wire transfers, credit cards, or escrow services) and ensure all terms are documented in a formal purchase agreement to avoid misunderstandings. -
What is the minimum order quantity (MOQ) for force sensors?
Minimum order quantities (MOQ) for force sensors can differ significantly based on the manufacturer and the specific sensor model. Some suppliers may offer low MOQs for standard models, while customized sensors often have higher MOQs due to production costs. When negotiating, inquire about MOQs and express your needs; some suppliers may be flexible, especially for first-time orders or long-term partnerships. -
How long does it typically take to receive force sensors after placing an order?
Delivery times for force sensors can vary based on factors such as supplier location, manufacturing lead times, and shipping methods. Generally, orders can take anywhere from a few days to several weeks. For international shipments, customs clearance can also add to the timeline. It is advisable to confirm estimated delivery dates with the supplier and consider potential delays, particularly if sourcing from regions with longer lead times. -
Are customization options available for force sensors?
Many suppliers offer customization options for force sensors to meet specific application needs. Customizations may include adjusting sensor size, modifying measurement ranges, or integrating additional features such as wireless connectivity. Discuss your requirements with potential suppliers early in the negotiation process to understand the possibilities, associated costs, and lead times for customized solutions. -
What are the best practices for shipping force sensors internationally?
When shipping force sensors internationally, ensure that they are well-packaged to prevent damage during transit. Choose reliable shipping methods that suit the urgency and budget of your order. Be aware of customs regulations in both the sending and receiving countries, as well as any applicable tariffs. Collaborating with a logistics partner experienced in international shipping can help streamline the process and ensure compliance with regulations, reducing the risk of delays.
Important Disclaimer & Terms of Use
⚠️ Important Disclaimer
The information provided in this guide, including content regarding manufacturers, technical specifications, and market analysis, is for informational and educational purposes only. It does not constitute professional procurement advice, financial advice, or legal advice.
While we have made every effort to ensure the accuracy and timeliness of the information, we are not responsible for any errors, omissions, or outdated information. Market conditions, company details, and technical standards are subject to change.
B2B buyers must conduct their own independent and thorough due diligence before making any purchasing decisions. This includes contacting suppliers directly, verifying certifications, requesting samples, and seeking professional consultation. The risk of relying on any information in this guide is borne solely by the reader.
Strategic Sourcing Conclusion and Outlook for force sensor
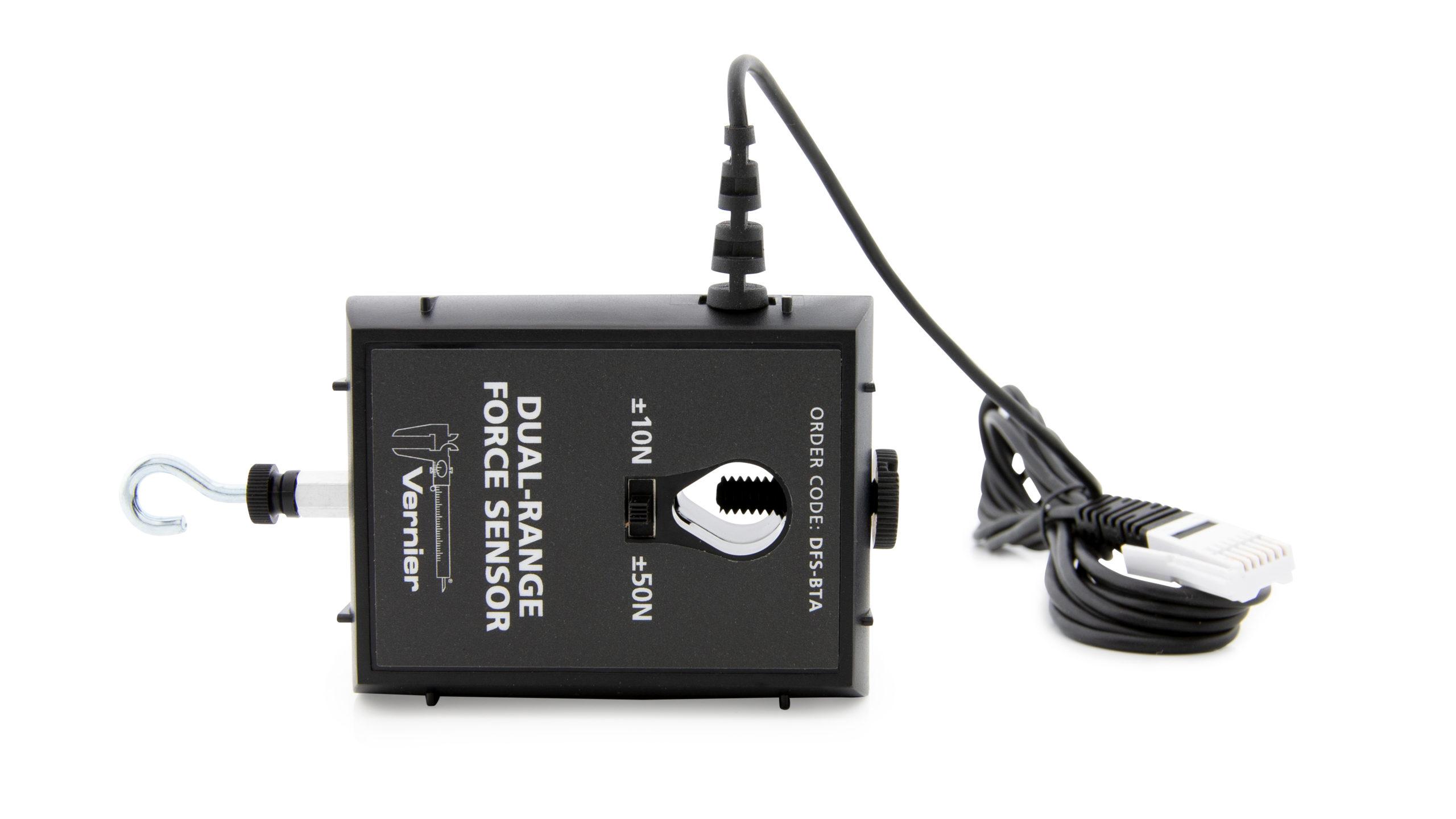
A stock image related to force sensor.
What Are the Key Takeaways for B2B Buyers in Force Sensors?
In the evolving landscape of force sensors, strategic sourcing remains paramount for international B2B buyers. Understanding the various technologies—such as strain gauge, piezoresistive, and capacitive—allows buyers to select the optimal sensor for their specific applications. Additionally, considering factors like force capacity, sensitivity, and environmental conditions can significantly enhance the efficiency and reliability of operations.
How Can Strategic Sourcing Enhance Your Business Operations?
By leveraging strategic sourcing practices, buyers can not only secure quality products but also foster long-term partnerships with suppliers. This approach enables organizations to navigate the complexities of global supply chains effectively, ensuring timely delivery and competitive pricing. Moreover, engaging with reputable manufacturers from diverse regions—such as Europe, Africa, and South America—can provide unique insights into emerging technologies and trends in force sensing.
What Lies Ahead for Force Sensor Technology?
Looking forward, the demand for advanced force sensors will continue to grow, driven by innovations in automation, robotics, and smart technologies. As industries seek to enhance precision and efficiency, now is the ideal time for B2B buyers to evaluate their sourcing strategies. Invest in high-quality force sensors to stay ahead of the curve and ensure your operations remain competitive in a rapidly changing market. Engage with suppliers today to explore the latest advancements and secure the best solutions for your business needs.