Discover Cost-Saving Benefits of Pneumatic Valve Solutions (2025)
Introduction: Navigating the Global Market for pneumatic valve
In today’s fast-paced industrial landscape, international B2B buyers face the challenge of sourcing the right pneumatic valves that meet their specific operational needs. Pneumatic valves are essential for regulating the flow of gases and liquids in various applications, from manufacturing and automation to HVAC systems and water treatment. With the growing demand for efficient and reliable control mechanisms, understanding the intricacies of pneumatic valves has never been more crucial.
This comprehensive guide delves into the diverse types of pneumatic valves available in the market, their applications across multiple industries, and the best practices for supplier vetting. It will also cover key considerations such as cost analysis and material compatibility, empowering buyers to make informed purchasing decisions. By addressing the unique requirements of buyers from regions like Africa, South America, the Middle East, and Europe—specifically countries like Nigeria and the UAE—this guide aims to simplify the procurement process.
With actionable insights and expert recommendations, you will gain the knowledge necessary to navigate the global market for pneumatic valves confidently. Whether you are involved in industrial automation, oil and gas, or food processing, this guide equips you with the tools to select the right pneumatic valves that enhance efficiency and ensure safety in your operations.
Understanding pneumatic valve Types and Variations
Type Name | Key Distinguishing Features | Primary B2B Applications | Brief Pros & Cons for Buyers |
---|---|---|---|
Directional Control | Controls the direction of airflow; available in 2-way, 3-way, and 5-way configurations. | Industrial automation, robotics, assembly lines | Pros: Versatile, precise control. Cons: Complexity may increase costs. |
Flow Control | Regulates the flow rate of air or fluid; typically features adjustable or fixed orifice. | HVAC systems, water treatment, pneumatic tools | Pros: Energy-efficient, customizable. Cons: Limited to flow regulation only. |
Safety Valves | Automatically shuts off air supply in case of pressure anomalies; essential for system safety. | Oil & gas, chemical processing, manufacturing | Pros: Enhances safety, reliable under pressure. Cons: May require regular maintenance. |
Solenoid Valves | Electrically operated valves that switch based on control signals; offers rapid actuation. | Automation systems, packaging, food processing | Pros: Quick response time, easy integration. Cons: Dependence on electrical supply. |
Double-Acting Valves | Utilizes compressed air for both extending and retracting motions; ideal for actuators. | Robotics, automated machinery, conveyor systems | Pros: Efficient operation, balanced force. Cons: More complex and potentially higher costs. |
What Are the Characteristics of Directional Control Valves?
Directional control valves are fundamental in pneumatic systems, allowing operators to manage the flow of air in multiple directions. They come in various configurations, including 2-way, 3-way, and 5-way options, making them adaptable for numerous applications such as industrial automation and assembly lines. When purchasing, buyers should consider the required configuration and the specific application to ensure optimal performance.
How Do Flow Control Valves Work and Where Are They Used?
Flow control valves are designed to regulate the flow rate of air or fluid within a system. They can be equipped with adjustable or fixed orifices, providing flexibility in managing fluid dynamics. Commonly utilized in HVAC systems and water treatment facilities, these valves contribute to energy efficiency. Buyers should evaluate the compatibility of the flow control valve with their existing systems and consider the specific flow requirements for their applications.
Why Are Safety Valves Essential in Pneumatic Systems?
Safety valves are crucial for maintaining the integrity of pneumatic systems, automatically shutting off the air supply in case of pressure anomalies. This feature is vital in high-risk environments like oil and gas or chemical processing industries. While they enhance safety and reliability, buyers must also consider the need for regular maintenance to ensure optimal operation and compliance with safety standards.
What Are the Advantages of Solenoid Valves in Automation?
Solenoid valves are electrically operated, enabling rapid actuation based on control signals. They are widely used in automation systems, packaging, and food processing due to their quick response times and ease of integration. For B2B buyers, the key considerations include the electrical supply requirements and compatibility with existing automation controls to ensure seamless operation.
How Do Double-Acting Valves Improve Efficiency?
Double-acting valves utilize compressed air for both extending and retracting motions, making them ideal for actuators in robotic systems and automated machinery. Their design allows for efficient operation and balanced force, which is beneficial in high-demand applications like conveyor systems. Buyers should assess the complexity and costs associated with double-acting valves, ensuring they align with their operational needs and budget constraints.
Key Industrial Applications of pneumatic valve
Industry/Sector | Specific Application of Pneumatic Valve | Value/Benefit for the Business | Key Sourcing Considerations for this Application |
---|---|---|---|
Industrial Automation | Regulating actuators in assembly lines | Enhances operational efficiency and speed | Compatibility with existing systems, response time |
HVAC Systems | Controlling airflow in commercial buildings | Improves energy efficiency and air quality | Material durability, pressure ratings |
Water and Wastewater Treatment | Managing chemical dosing in treatment plants | Ensures precise chemical usage and compliance | Corrosion resistance, size specifications |
Oil and Gas Industry | Flow control in extraction and refining processes | Increases safety and reliability in operations | High-pressure ratings, material compatibility |
Food Processing | Regulating ingredient flow during production | Maintains hygiene standards and process efficiency | Compliance with food safety regulations, easy cleaning |
How Are Pneumatic Valves Used in Industrial Automation?
In the industrial automation sector, pneumatic valves are crucial for regulating actuators that control mechanical components on assembly lines. By enabling precise control of the air supply to these actuators, pneumatic valves help improve the speed and efficiency of manufacturing processes. International buyers, especially from regions like Africa and South America, should focus on sourcing valves that are compatible with existing automation systems and offer rapid response times to enhance productivity.
What Role Do Pneumatic Valves Play in HVAC Systems?
In HVAC applications, pneumatic valves control the flow of air to maintain optimal temperature and humidity levels in commercial buildings. These valves contribute to energy efficiency and improve indoor air quality, which is essential for workplaces and public spaces. Buyers from the Middle East, where climate control is critical, should consider the durability of materials used in pneumatic valves to withstand high temperatures and ensure long-term reliability.
How Are Pneumatic Valves Utilized in Water and Wastewater Treatment?
Pneumatic valves are employed in water and wastewater treatment plants to manage the flow of water and chemicals during various treatment stages. They ensure precise dosing of chemicals, which is crucial for compliance with environmental regulations. International buyers need to prioritize valves made from corrosion-resistant materials and those that meet specific size requirements for their systems, particularly in regions like Europe where regulatory standards are stringent.
What is the Importance of Pneumatic Valves in the Oil and Gas Industry?
In the oil and gas sector, pneumatic valves are vital for controlling the flow of crude oil, natural gas, and various chemicals used in extraction and refining processes. They enhance safety by providing reliable shut-off capabilities in case of emergencies, thereby reducing the risk of spills and accidents. Buyers in this industry should ensure that the valves can handle high-pressure environments and are compatible with the corrosive substances typically found in oil and gas operations.
How Do Pneumatic Valves Benefit Food Processing Operations?
Pneumatic valves are extensively used in food processing plants to regulate the flow of ingredients and control mixing processes. Their design helps maintain hygiene and safety standards, which are paramount in the food industry. B2B buyers, particularly from regions like Africa and Europe, should look for valves that comply with food safety regulations and are easy to clean, ensuring that they meet both operational efficiency and health standards.
3 Common User Pain Points for ‘pneumatic valve’ & Their Solutions
Scenario 1: Difficulty in Selecting the Right Pneumatic Valve for Specific Applications
The Problem: Many B2B buyers, especially those new to industrial automation, face the challenge of selecting the right pneumatic valve for their specific applications. With a wide variety of pneumatic valves available—differing in materials, sizes, and functionalities—buyers often struggle to identify the best match for their operational needs. This can lead to overspending on unnecessary features or, conversely, choosing a valve that cannot withstand the demands of their application, resulting in frequent failures and costly downtime.
The Solution: To overcome this challenge, buyers should conduct a thorough assessment of their operational requirements before sourcing pneumatic valves. Begin by gathering detailed information on the specific application, including the type of fluid being controlled, the required flow rates, pressure ranges, and environmental conditions (e.g., exposure to corrosive substances or extreme temperatures). Utilize a decision matrix to compare various valve types, considering factors such as compatibility with the working medium, expected lifespan, and maintenance requirements. Collaborating with experienced suppliers or manufacturers can provide valuable insights into the best materials and valve designs suited for your application. Additionally, requesting samples for testing can help ensure that the selected valve meets performance expectations.
Scenario 2: High Maintenance Costs and Downtime
The Problem: Another common pain point for B2B buyers is the high maintenance costs associated with pneumatic valves, particularly in environments where dust, moisture, or corrosive substances are prevalent. Buyers often find themselves facing unexpected downtime due to valve failures, which can disrupt production schedules and lead to significant financial losses. Over time, these issues can erode trust in the reliability of pneumatic systems.
The Solution: To mitigate maintenance costs and reduce downtime, it is crucial to prioritize regular maintenance schedules and invest in high-quality pneumatic valves designed for the specific environmental conditions of your facility. Buyers should consider valves with durable materials such as stainless steel or those equipped with protective coatings that enhance resistance to corrosion and wear. Furthermore, implementing predictive maintenance practices using IoT sensors can provide real-time data on valve performance, allowing for timely interventions before failures occur. Training staff on proper handling and maintenance procedures can also extend the lifespan of pneumatic valves, ensuring they function optimally and reducing the likelihood of unexpected breakdowns.
Scenario 3: Integration Challenges with Existing Systems
The Problem: As companies evolve, integrating new pneumatic valves into existing systems can present significant challenges. Buyers often encounter compatibility issues with legacy systems, leading to ineffective automation and increased costs associated with retrofitting or replacing equipment. These integration difficulties can hinder operational efficiency and slow down the adoption of new technologies.
The Solution: To streamline the integration process, buyers should work closely with manufacturers who offer pneumatic valves designed for easy compatibility with existing systems. Look for valves that support standard interface connections and can be seamlessly integrated into current setups. Before making a purchase, request detailed technical specifications and installation guidelines to identify potential challenges early on. Engaging in pre-purchase consultations with system integrators or automation specialists can provide valuable insights into how to effectively integrate new valves without significant overhauls. Additionally, opting for modular valve systems can facilitate easier updates and modifications, reducing the complexities associated with future integrations.
Strategic Material Selection Guide for pneumatic valve
What Are the Key Properties of Common Materials Used in Pneumatic Valves?
When selecting pneumatic valves, the choice of material is critical for ensuring optimal performance in various applications. Below, we analyze four common materials used in pneumatic valves: carbon steel, stainless steel, brass, and PVC. Each material has unique properties that affect its suitability for specific applications.
How Does Carbon Steel Perform in Pneumatic Valve Applications?
Key Properties: Carbon steel is known for its high strength and durability, with a temperature rating typically up to 400°F (204°C) and pressure ratings reaching 3,000 psi. However, it is prone to corrosion if not properly coated.
Pros & Cons: The primary advantage of carbon steel is its cost-effectiveness and strength, making it suitable for high-pressure applications. However, its susceptibility to rust and corrosion necessitates protective coatings, which can increase manufacturing complexity and costs.
Impact on Application: Carbon steel valves are ideal for applications involving non-corrosive gases and fluids. In regions like Africa and South America, where cost-efficiency is often prioritized, carbon steel valves can be a practical choice.
Considerations for International Buyers: Buyers should ensure compliance with local standards such as ASTM or DIN, especially in industries where safety and reliability are paramount.
What Are the Benefits of Using Stainless Steel for Pneumatic Valves?
Key Properties: Stainless steel offers excellent corrosion resistance, high-temperature tolerance (up to 1,500°F or 815°C), and pressure ratings similar to carbon steel.
Pros & Cons: The main advantage of stainless steel is its longevity and resistance to harsh environments, making it suitable for a wide range of applications, including food processing and chemical handling. However, it is generally more expensive than carbon steel and can be more challenging to machine.
Impact on Application: Stainless steel valves are ideal for applications involving corrosive substances or high hygiene standards, such as in the food and beverage industry. This is particularly relevant for buyers in the Middle East and Europe, where stringent regulations apply.
Considerations for International Buyers: Buyers should look for certifications that comply with international standards, such as JIS for Japanese markets or ISO for European markets, to ensure safety and quality.
Why Choose Brass for Pneumatic Valves?
Key Properties: Brass is known for its good corrosion resistance and moderate temperature and pressure ratings (up to 200°F or 93°C and 1,500 psi).
Pros & Cons: The advantages of brass include its ease of machining and relatively low cost. However, it is less durable than stainless steel and can degrade in high-temperature applications.
Impact on Application: Brass valves are commonly used in low-pressure applications and where aesthetic appearance is important, such as in decorative fixtures. This makes them suitable for various industries, including HVAC and plumbing.
Considerations for International Buyers: Buyers should be aware of lead content regulations, especially in regions like Europe where lead-free brass is preferred for safety and compliance.
What Role Does PVC Play in Pneumatic Valve Selection?
Key Properties: PVC is lightweight, resistant to corrosion, and suitable for low-pressure applications. It typically handles temperatures up to 140°F (60°C) and pressures around 150 psi.
Pros & Cons: The primary advantage of PVC is its low cost and resistance to chemical corrosion, making it ideal for water and wastewater applications. However, it is not suitable for high-temperature or high-pressure environments.
Impact on Application: PVC valves are commonly used in agricultural and water treatment applications, particularly in regions with abundant water resources, such as parts of Africa and South America.
Considerations for International Buyers: When sourcing PVC valves, buyers should ensure that the material meets local environmental regulations, as well as standards like ASTM for product quality assurance.
Summary Table of Material Selection for Pneumatic Valves
Material | Typical Use Case for pneumatic valve | Key Advantage | Key Disadvantage/Limitation | Relative Cost (Low/Med/High) |
---|---|---|---|---|
Carbon Steel | High-pressure applications | Cost-effective and strong | Prone to corrosion | Low |
Stainless Steel | Food processing, chemical handling | Excellent corrosion resistance | Higher cost and machining complexity | High |
Brass | HVAC, plumbing | Easy to machine and low cost | Less durable in high temperatures | Medium |
PVC | Water treatment, agricultural | Lightweight and corrosion-resistant | Not suitable for high-pressure applications | Low |
This strategic material selection guide provides valuable insights for international B2B buyers, helping them make informed decisions based on their specific application needs and regional compliance requirements.
In-depth Look: Manufacturing Processes and Quality Assurance for pneumatic valve
What Are the Main Stages of Pneumatic Valve Manufacturing?
Pneumatic valves are complex mechanical devices that require meticulous manufacturing processes to ensure reliability and performance. The typical manufacturing stages include material preparation, forming, assembly, and finishing.
How Is Material Prepared for Pneumatic Valves?
The manufacturing process begins with the selection of appropriate materials, which can include carbon steel, stainless steel, brass, and PVC. Material selection is crucial as it affects durability, corrosion resistance, and overall performance. Before production, raw materials undergo quality checks to ensure they meet specific standards for thickness, tensile strength, and chemical composition.
Once materials are approved, they are cut to size using advanced cutting techniques, such as laser cutting or water jet cutting. This precise cutting is essential to maintain tolerances critical for valve functionality.
What Forming Techniques Are Used in Pneumatic Valve Production?
After material preparation, the forming process begins. This stage involves shaping the raw materials into the desired valve components, which typically include the valve body, actuator, and control mechanisms. Common techniques include:
- Casting: For complex shapes, materials are poured into molds to create valve bodies.
- Machining: CNC machines are used for precision shaping and drilling of valve components, ensuring tight tolerances.
- Forging: For high-strength applications, metals are heated and shaped under pressure, enhancing material properties.
These techniques are chosen based on the specific design requirements and the intended application of the pneumatic valves.
How Are Pneumatic Valves Assembled?
Once all components are formed, assembly takes place. This stage is critical for ensuring that all parts fit together correctly and function as intended. The assembly process typically includes:
- Component Inspection: Each part is inspected for defects before assembly.
- Assembly Techniques: Parts are joined using methods such as welding, screwing, or clamping, depending on the design.
- Integration of Actuators: Pneumatic valves often include actuators that need to be carefully integrated for optimal performance.
Quality control is paramount during this stage to prevent future operational failures.
What Finishing Processes Are Applied to Pneumatic Valves?
Finishing processes enhance the valve’s durability and aesthetic appeal. Common finishing techniques include:
- Surface Treatment: Processes such as anodizing, powder coating, or plating are employed to improve corrosion resistance.
- Cleaning: Components are cleaned to remove any contaminants that could affect performance.
- Testing: Before finalizing the product, valves undergo rigorous testing to ensure they meet operational standards.
What Quality Assurance Standards Are Relevant for Pneumatic Valves?
Quality assurance is critical in pneumatic valve manufacturing to ensure safety, reliability, and compliance with industry standards. International standards such as ISO 9001 are widely adopted, focusing on quality management systems and continuous improvement.
Which Industry-Specific Certifications Should Buyers Look For?
In addition to ISO 9001, various industry-specific certifications enhance the credibility of a manufacturer. These include:
- CE Marking: Indicates compliance with European health, safety, and environmental protection standards.
- API Standards: Important for valves used in the oil and gas industry, ensuring they meet performance and safety criteria.
For buyers from regions such as Africa, South America, the Middle East, and Europe, verifying these certifications is crucial for ensuring the quality and safety of pneumatic valves.
What Are the Key Quality Control Checkpoints During Manufacturing?
Quality control (QC) checkpoints are essential throughout the manufacturing process to catch defects early and ensure compliance with standards. Key QC checkpoints include:
- Incoming Quality Control (IQC): Inspection of raw materials upon arrival to confirm they meet specifications.
- In-Process Quality Control (IPQC): Continuous monitoring during manufacturing, including checks at each stage (forming, assembly, finishing).
- Final Quality Control (FQC): Comprehensive testing of finished products to verify they meet performance standards.
What Common Testing Methods Are Employed for Pneumatic Valves?
Various testing methods are employed to ensure pneumatic valves operate correctly under expected conditions. Common tests include:
- Pressure Testing: Valves are subjected to high pressures to ensure they can withstand operational demands without leaking.
- Functional Testing: Each valve is operated to verify its performance, including response time and actuation accuracy.
- Leak Testing: Ensures no air or fluid escapes from the valve under pressure.
How Can B2B Buyers Verify Supplier Quality Control?
International B2B buyers should take several steps to verify the quality control measures of suppliers, particularly when sourcing pneumatic valves from different regions:
- Supplier Audits: Conducting on-site audits to assess manufacturing processes and quality control practices.
- Quality Reports: Requesting detailed quality reports that outline testing results, certifications, and compliance with standards.
- Third-Party Inspections: Engaging third-party inspection agencies to perform independent checks on product quality before shipment.
What Are the Quality Control Nuances for International B2B Buyers?
For B2B buyers from diverse regions, understanding the nuances of quality control is essential. Variations in manufacturing practices, regulatory requirements, and quality standards can significantly impact the reliability of pneumatic valves. Buyers should consider:
- Regional Standards: Familiarize themselves with local regulations that may affect product quality and safety.
- Cultural Differences: Acknowledge that communication and expectations may vary across cultures, which can influence quality assurance practices.
- Supply Chain Reliability: Assess the entire supply chain to ensure that quality control measures are maintained from raw material sourcing to final delivery.
In conclusion, understanding the manufacturing processes and quality assurance practices for pneumatic valves is vital for international B2B buyers. By focusing on material preparation, forming, assembly, finishing, and rigorous quality control measures, buyers can ensure they source reliable and high-quality pneumatic valves that meet their operational needs.
Practical Sourcing Guide: A Step-by-Step Checklist for ‘pneumatic valve’
To assist international B2B buyers in procuring pneumatic valves, this guide provides a structured checklist. These steps are designed to help you navigate the sourcing process effectively, ensuring you select a valve that meets your operational needs and quality standards.
Step 1: Define Your Technical Specifications
Establishing clear technical specifications is essential before starting your procurement process. This includes determining the pressure range, flow rate, size, and material compatibility with the fluids being handled. Knowing these specifications will guide your search for suitable pneumatic valves and help you communicate effectively with suppliers.
Step 2: Identify Your Application Needs
Understanding the specific application for which you require pneumatic valves is crucial. Consider factors such as the environment (e.g., industrial automation, HVAC systems, or food processing), the type of fluids involved, and the operational conditions (temperature, pressure, etc.). This step ensures you choose valves designed for your particular application, enhancing reliability and performance.
Step 3: Research and Shortlist Potential Suppliers
Conduct thorough research to identify and shortlist potential suppliers. Look for manufacturers or distributors with a strong reputation in your industry. Check for certifications such as ISO or CE, which indicate compliance with international quality standards. Additionally, consider suppliers who offer local support, as this can be beneficial for maintenance and troubleshooting.
Step 4: Evaluate Supplier Product Range and Quality
Assess the product range offered by your shortlisted suppliers. Ensure they provide a variety of pneumatic valves that meet your specifications, including options for different materials and sizes. Request product samples or detailed specifications to evaluate the quality and durability of the valves. This evaluation helps ensure that you invest in reliable products that will perform well in your applications.
Step 5: Request Quotes and Compare Pricing
Once you’ve narrowed down your options, request quotes from your shortlisted suppliers. Compare pricing not just on the valves themselves but also consider shipping costs, lead times, and any additional fees (e.g., for customization or warranty). This step is crucial for budgeting and ensuring you get the best value for your investment.
Step 6: Check for After-Sales Support and Warranty
Before finalizing your purchase, verify the after-sales support and warranty policies offered by the supplier. Ensure they provide technical assistance, maintenance services, and a reasonable warranty period. Reliable after-sales support can save you time and money in the long run, especially if you encounter issues with the valves after installation.
Step 7: Finalize the Order and Ensure Compliance
After selecting a supplier, finalize your order by confirming all details, including specifications, pricing, and delivery timelines. Ensure that the products comply with any relevant local regulations or industry standards applicable to your region. This diligence will help you avoid potential legal or operational issues down the line.
By following these steps, you can streamline your procurement process for pneumatic valves, ensuring you make informed decisions that meet your operational requirements.
Comprehensive Cost and Pricing Analysis for pneumatic valve Sourcing
What Are the Key Cost Components in Pneumatic Valve Sourcing?
When sourcing pneumatic valves, understanding the cost structure is crucial for making informed purchasing decisions. The main components that contribute to the overall cost include:
-
Materials: The choice of materials (e.g., stainless steel, brass, PVC) significantly impacts pricing. High-performance materials designed for corrosive environments or high-pressure applications typically cost more but can enhance durability and longevity.
-
Labor: Labor costs can vary based on the manufacturing location. Countries with lower labor costs may offer competitive pricing, but this can sometimes compromise quality.
-
Manufacturing Overhead: This includes costs associated with facilities, equipment maintenance, utilities, and administrative expenses. Efficient manufacturing processes can help minimize these costs.
-
Tooling: Custom tooling for specific valve designs can be a significant upfront investment. The complexity of the valve design will dictate tooling costs, with more complex designs generally incurring higher expenses.
-
Quality Control (QC): Implementing rigorous QC measures is essential for ensuring product reliability. While it adds to the cost, effective QC can prevent costly failures and enhance customer satisfaction.
-
Logistics: Shipping and handling costs can vary widely based on the location of the supplier and the destination. Factors such as Incoterms (International Commercial Terms) can influence logistics costs significantly.
-
Margin: Suppliers typically add a profit margin to their costs. This margin can vary based on the supplier’s market positioning and relationship with the buyer.
How Do Price Influencers Affect Pneumatic Valve Sourcing?
Several factors can influence the pricing of pneumatic valves, impacting overall procurement costs:
-
Volume/MOQ (Minimum Order Quantity): Suppliers often provide discounts for bulk orders. Understanding the optimal order quantity can lead to significant cost savings.
-
Specifications and Customization: Customized valves designed to meet specific application requirements can increase costs. Buyers should assess whether the benefits of customization outweigh the additional expense.
-
Material Selection: The material chosen for the valve affects both performance and cost. While high-end materials provide better resistance to wear and corrosion, they can significantly raise prices.
-
Quality Certifications: Valves that meet specific industry standards (e.g., ISO, API) may command higher prices due to the assurance of quality and reliability. Buyers should evaluate the importance of certifications for their application.
-
Supplier Factors: The reputation and reliability of the supplier can influence pricing. Established suppliers may charge a premium for their products but often provide better customer support and reliability.
-
Incoterms: Understanding Incoterms is essential for international buyers. These terms dictate who bears the shipping costs, insurance, and risk during transit, affecting the total landed cost of the valves.
What Are the Best Buyer Tips for Cost-Efficiency in Pneumatic Valve Sourcing?
For international B2B buyers, particularly those in Africa, South America, the Middle East, and Europe, the following strategies can enhance cost-efficiency in sourcing pneumatic valves:
-
Negotiate with Suppliers: Always negotiate pricing and terms. Building a relationship with suppliers can lead to better pricing and more favorable terms over time.
-
Consider Total Cost of Ownership (TCO): Look beyond the initial purchase price. Evaluate maintenance, operational efficiency, and lifespan to assess the true cost of ownership.
-
Research Local Suppliers: Local sourcing can reduce shipping costs and lead times. Additionally, working with local suppliers can simplify compliance with regional regulations.
-
Stay Informed About Market Trends: Understanding market dynamics, including raw material prices and global supply chain issues, can help in timing purchases for optimal pricing.
-
Leverage Technology: Utilize procurement software to analyze pricing data and supplier performance, allowing for more informed sourcing decisions.
Disclaimer on Indicative Prices
While this analysis provides a framework for understanding pneumatic valve costs and pricing factors, actual prices can vary significantly based on specific requirements, market conditions, and supplier negotiations. Always consult with multiple suppliers to obtain accurate and competitive pricing tailored to your needs.
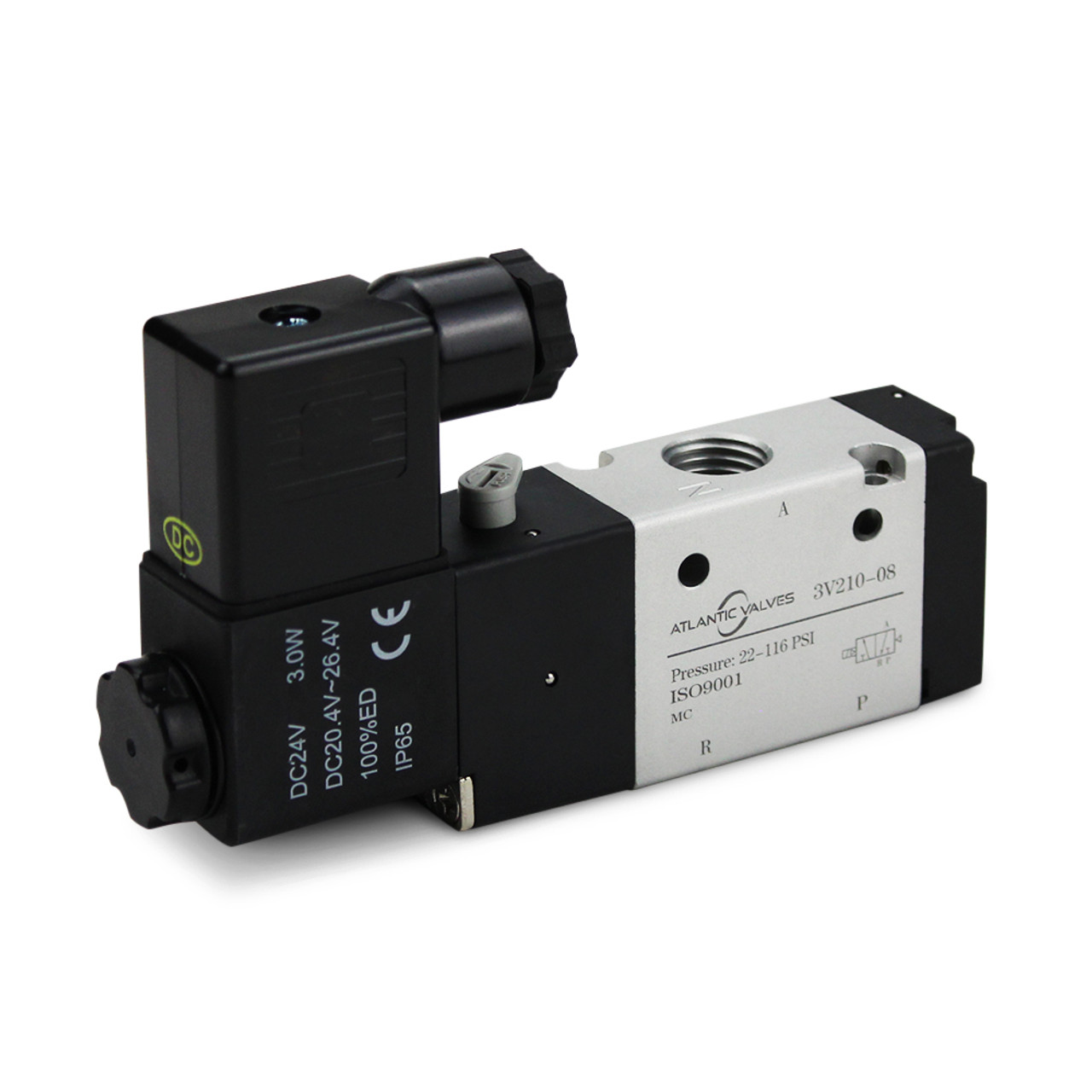
A stock image related to pneumatic valve.
Alternatives Analysis: Comparing pneumatic valve With Other Solutions
When considering the optimal solution for fluid control in industrial applications, it is crucial to evaluate the alternatives to pneumatic valves. The selection of the right technology can significantly impact performance, costs, and operational efficiency. Below, we will compare pneumatic valves with two viable alternatives: electric valves and hydraulic valves.
Comparison Table of Pneumatic Valves and Alternatives
Comparison Aspect | Pneumatic Valve | Electric Valve | Hydraulic Valve |
---|---|---|---|
Performance | Quick response, reliable | High precision, slower actuation | High force, robust control |
Cost | Moderate initial investment | Higher upfront costs | Variable costs, often expensive due to complexity |
Ease of Implementation | Generally straightforward | Requires electrical setup | Complex installation, requires a hydraulic system |
Maintenance | Low, but periodic checks needed | Low, primarily electrical checks | High, frequent maintenance needed |
Best Use Case | Automated manufacturing, HVAC | Precision applications, robotics | Heavy machinery, construction |
What are the Pros and Cons of Electric Valves?
Electric valves utilize electrical signals for operation and are known for their precise control and adaptability. One of the primary advantages is their ability to integrate seamlessly with advanced automation systems, including PLCs and IoT devices. This makes them ideal for applications requiring precise flow control, such as in pharmaceuticals or food processing.
However, electric valves come with higher initial costs and often require more complex wiring and setup than pneumatic valves. They may also be less effective in environments with high humidity or explosive atmospheres, where pneumatic valves excel due to their inherent safety features.
What are the Pros and Cons of Hydraulic Valves?
Hydraulic valves operate using pressurized fluid, providing substantial force and enabling control over heavy machinery. They are particularly effective in applications like construction and mining, where high power is essential. The robustness of hydraulic systems allows them to handle significant loads, making them suitable for demanding environments.
On the downside, hydraulic systems are typically more complex and costly to maintain. They require regular checks for leaks and fluid levels, which can lead to higher operational costs over time. Moreover, the installation of hydraulic valves necessitates a comprehensive hydraulic system, complicating the setup process compared to pneumatic systems.
How Can B2B Buyers Choose the Right Solution?
Selecting the right valve technology hinges on various factors, including the specific application, budget constraints, and operational requirements. B2B buyers should start by assessing the nature of their processes—whether they prioritize speed and safety, precision control, or high force.
For environments where explosive hazards are a concern, pneumatic valves may be the best choice due to their safety features. Conversely, for applications requiring precise control and integration with modern automation systems, electric valves could be more suitable. Lastly, for heavy-duty applications, hydraulic valves might be the preferred option despite their maintenance demands.
By analyzing these aspects and understanding the strengths and weaknesses of each solution, buyers can make informed decisions that align with their operational goals and budget considerations.
Essential Technical Properties and Trade Terminology for pneumatic valve
What Are the Key Technical Properties of Pneumatic Valves?
Pneumatic valves are essential components in various industrial applications, and understanding their technical specifications is crucial for B2B buyers. Here are some critical specifications to consider:
1. Material Grade
The material used in pneumatic valves directly impacts their durability and performance. Common materials include stainless steel, carbon steel, and brass. Stainless steel is preferred for corrosive environments, while carbon steel is often used for general applications. Understanding the material grade helps buyers ensure compatibility with the fluids handled and resistance to wear and corrosion.
2. Pressure Rating
Pressure rating indicates the maximum pressure a valve can withstand. It is typically measured in pounds per square inch (PSI). Knowing the pressure requirements of your application is vital for selecting a valve that will operate reliably under expected conditions. A mismatch can lead to valve failure and costly downtime.
3. Port Configuration
Pneumatic valves come with various port configurations (2, 3, or 5 ports) that determine how air is directed through the valve. The choice of port configuration affects the valve’s functionality, including whether it can control single or double-acting actuators. Buyers should assess their system’s requirements to choose an appropriate configuration for optimal performance.
4. Actuation Type
Pneumatic valves can be actuated manually, pneumatically, or electrically. The actuation type influences the speed and precision of valve operation. Electric actuators, for example, offer faster response times and can be integrated with automated systems, making them ideal for high-efficiency environments. Understanding the actuation type helps buyers align their valve choice with operational needs.
5. Flow Rate
Flow rate measures how much fluid can pass through the valve over a specific period, usually in liters per minute (L/min). A valve with a high flow rate is essential for applications requiring quick fluid transfer, such as in manufacturing or HVAC systems. Buyers must analyze their system’s flow requirements to ensure proper valve selection.
6. Temperature Range
The temperature range indicates the operating temperatures the valve can handle without compromising functionality. Valves designed for high-temperature applications must be made from materials that can withstand heat without deforming or degrading. This property is crucial for industries like oil and gas or food processing, where temperature variations are common.
What Are the Common Trade Terms Associated with Pneumatic Valves?
Navigating the procurement process requires familiarity with specific trade terminology. Here are some essential terms to understand:
1. OEM (Original Equipment Manufacturer)
An OEM is a company that produces parts or equipment that may be marketed by another manufacturer. In the context of pneumatic valves, working with an OEM can ensure you receive high-quality, reliable products that meet specific industry standards.
2. MOQ (Minimum Order Quantity)
MOQ refers to the smallest quantity of a product that a supplier is willing to sell. Understanding MOQ is critical for buyers to manage inventory effectively and avoid overstocking or stockouts.
3. RFQ (Request for Quotation)
An RFQ is a document that a buyer sends to suppliers asking for a price quote on specific products. It is a crucial step in the procurement process, enabling buyers to compare prices and terms from multiple vendors before making a decision.
4. Incoterms (International Commercial Terms)
Incoterms are a set of international rules that define the responsibilities of buyers and sellers in international transactions. Familiarity with these terms helps buyers understand shipping responsibilities, risk allocation, and costs associated with transporting pneumatic valves across borders.
5. Lead Time
Lead time refers to the time taken from placing an order to the delivery of the product. Knowing the lead time is essential for planning production schedules and ensuring that operations are not disrupted due to delays.
6. Certification Standards
Certification standards, such as ISO or API, indicate that a product meets specific quality and safety benchmarks. Buyers should prioritize suppliers with recognized certifications to ensure the reliability and safety of pneumatic valves in their applications.
Understanding these technical properties and trade terms will empower B2B buyers from Africa, South America, the Middle East, and Europe to make informed decisions when sourcing pneumatic valves for their operations.
Navigating Market Dynamics and Sourcing Trends in the pneumatic valve Sector
What Are the Key Market Dynamics and Trends in the Pneumatic Valve Sector?
The pneumatic valve market is witnessing significant growth driven by the increasing demand for automation across various industries, including manufacturing, oil and gas, and food processing. As industrial processes become more sophisticated, the need for precise control of fluid dynamics has never been greater. International B2B buyers, particularly in regions like Africa, South America, the Middle East, and Europe, must stay informed about emerging trends that can affect their sourcing strategies.
One of the most notable trends is the shift towards digitalization in pneumatic systems. Technologies such as Industry 4.0 and the Internet of Things (IoT) are facilitating real-time monitoring and control of pneumatic systems, leading to enhanced efficiency and reduced downtime. Buyers should consider suppliers who offer smart pneumatic valves that can be integrated into existing automation frameworks, providing data analytics capabilities for better decision-making.
Moreover, sustainability is becoming a focal point in sourcing practices. Buyers are increasingly looking for pneumatic valves that not only meet their operational needs but also align with their environmental goals. This includes sourcing from manufacturers that prioritize eco-friendly materials and production methods.
Additionally, the competitive landscape is shifting as manufacturers from emerging markets enhance their capabilities and offer cost-effective solutions. Buyers should evaluate their suppliers’ technological advancements and production capacities to ensure they are getting the best value for their investments.
How Can International Buyers Ensure Sustainability and Ethical Sourcing of Pneumatic Valves?
Sustainability and ethical sourcing are critical considerations for international B2B buyers in the pneumatic valve sector. The environmental impact of manufacturing processes, including resource consumption and waste generation, is under increasing scrutiny. Buyers should prioritize suppliers who demonstrate a commitment to sustainable practices, such as using recycled materials or implementing waste reduction strategies.
Moreover, certifications play a crucial role in identifying environmentally friendly products. Look for pneumatic valves that carry certifications such as ISO 14001 for environmental management, or those that utilize materials with low environmental impact. For example, valves made from lead-free brass or recyclable plastics can significantly reduce the ecological footprint of industrial operations.
Ethical supply chains are equally important. Buyers should conduct thorough due diligence on their suppliers to ensure fair labor practices and compliance with international standards. This not only mitigates reputational risks but also contributes to a more sustainable and responsible global supply chain.
By focusing on suppliers who prioritize sustainability and ethical practices, international B2B buyers can enhance their corporate social responsibility (CSR) efforts while ensuring compliance with regulatory requirements across different regions.
What Is the Brief Evolution and History of Pneumatic Valves?
Pneumatic valves have evolved significantly since their inception, transitioning from simple mechanical devices to advanced, automated systems. The early pneumatic valves were primarily operated manually, requiring direct human intervention to control fluid flow. However, with the advent of electrical and electronic controls in the late 20th century, the functionality of pneumatic valves expanded dramatically.
The introduction of valve islands—integrated systems that combine multiple valves into a compact unit—revolutionized the industry by reducing installation time and enhancing performance. As automation technologies advanced, pneumatic valves began to incorporate smart features, allowing for real-time monitoring and control through PLCs and IoT connectivity.
Today, pneumatic valves are integral components in various applications, from industrial automation to HVAC systems, reflecting a rich history of innovation that continues to shape the future of fluid control technologies. International buyers must recognize this evolution to make informed sourcing decisions that align with their operational needs and technological advancements.
Frequently Asked Questions (FAQs) for B2B Buyers of pneumatic valve
-
How do I choose the right pneumatic valve for my application?
Choosing the right pneumatic valve involves understanding your specific application requirements. Consider factors such as the type of fluid being controlled, the operating pressure range, temperature conditions, and the required flow rate. Additionally, evaluate the materials of construction to ensure compatibility with the fluid and environmental conditions. It’s also crucial to assess the valve’s actuation method (manual, pneumatic, or electric) based on your automation needs. Collaborating with a knowledgeable supplier can help streamline the selection process and ensure optimal performance. -
What are the key features to look for in a pneumatic valve supplier?
When sourcing a pneumatic valve supplier, prioritize their experience in your industry, their product range, and their ability to customize solutions. Look for suppliers with a robust quality assurance process and certifications such as ISO 9001. Additionally, assess their logistical capabilities, including shipping times and support for international trade compliance. Customer service responsiveness and technical support are also vital, as they can aid in resolving issues quickly and efficiently. -
Can pneumatic valves be customized for specific needs?
Yes, pneumatic valves can often be customized to meet specific operational requirements. Customization may include alterations in size, material, or design features such as port configuration and actuation type. Many suppliers offer tailored solutions for unique applications, which can enhance efficiency and effectiveness. When discussing customization, clearly communicate your specifications to ensure the supplier can deliver a product that meets your needs. -
What minimum order quantities (MOQs) should I expect when purchasing pneumatic valves?
Minimum order quantities for pneumatic valves can vary widely depending on the supplier and the specific product. Some manufacturers may have MOQs as low as 10 units for standard models, while custom or specialized valves may require larger orders. It’s essential to discuss MOQs upfront with your supplier to understand how they align with your purchasing needs and inventory management strategies. -
What payment terms are typically offered for international purchases of pneumatic valves?
Payment terms for international purchases can vary based on the supplier’s policies and the buyer’s creditworthiness. Common terms include advance payment, letters of credit, or net payment terms (e.g., net 30 or net 60 days). It’s crucial to negotiate payment terms that are favorable for your cash flow while ensuring that the supplier feels secure in the transaction. Be aware of any additional costs, such as taxes or tariffs, that may apply to international shipments.
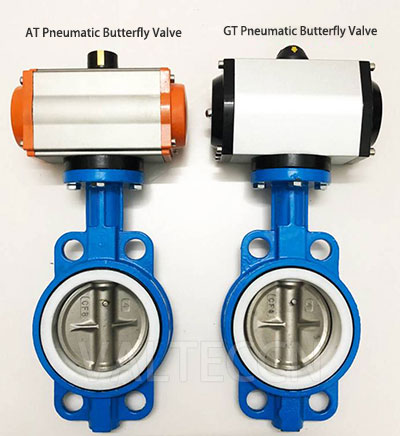
A stock image related to pneumatic valve.
-
How do I ensure quality assurance when sourcing pneumatic valves?
To ensure quality assurance when sourcing pneumatic valves, request documentation that verifies the supplier’s quality management system, such as ISO certifications. It’s also beneficial to ask for product samples or third-party test reports before placing a large order. Additionally, consider visiting the supplier’s manufacturing facility if feasible, as this can provide insights into their production processes and quality control measures. -
What are the logistics considerations for importing pneumatic valves?
When importing pneumatic valves, consider factors such as shipping methods, lead times, and customs clearance processes. Ensure that your supplier provides all necessary documentation for import, including invoices, packing lists, and certificates of origin. Familiarize yourself with the import regulations specific to your country to avoid delays or additional costs. Collaborating with a reliable freight forwarder can help streamline the logistics process and ensure timely delivery. -
How do pneumatic valves perform in extreme environments?
Pneumatic valves can be designed to operate effectively in extreme environments, such as high temperatures or corrosive conditions. Selecting valves made from robust materials, such as stainless steel or specialized coatings, can enhance their durability in harsh settings. Ensure that the valve’s specifications align with the environmental conditions it will face, including pressure fluctuations and exposure to chemicals. Consulting with your supplier can help identify suitable options for extreme applications.
Important Disclaimer & Terms of Use
⚠️ Important Disclaimer
The information provided in this guide, including content regarding manufacturers, technical specifications, and market analysis, is for informational and educational purposes only. It does not constitute professional procurement advice, financial advice, or legal advice.
While we have made every effort to ensure the accuracy and timeliness of the information, we are not responsible for any errors, omissions, or outdated information. Market conditions, company details, and technical standards are subject to change.
B2B buyers must conduct their own independent and thorough due diligence before making any purchasing decisions. This includes contacting suppliers directly, verifying certifications, requesting samples, and seeking professional consultation. The risk of relying on any information in this guide is borne solely by the reader.
Strategic Sourcing Conclusion and Outlook for pneumatic valve
What Are the Key Takeaways for B2B Buyers in Pneumatic Valve Sourcing?
In conclusion, strategic sourcing of pneumatic valves is crucial for optimizing industrial processes across various sectors, including manufacturing, oil and gas, and food processing. B2B buyers must prioritize reliability, efficiency, and cost-effectiveness when selecting suppliers. Understanding the unique applications and specifications—such as material compatibility and pressure requirements—ensures that your pneumatic systems function smoothly and safely.
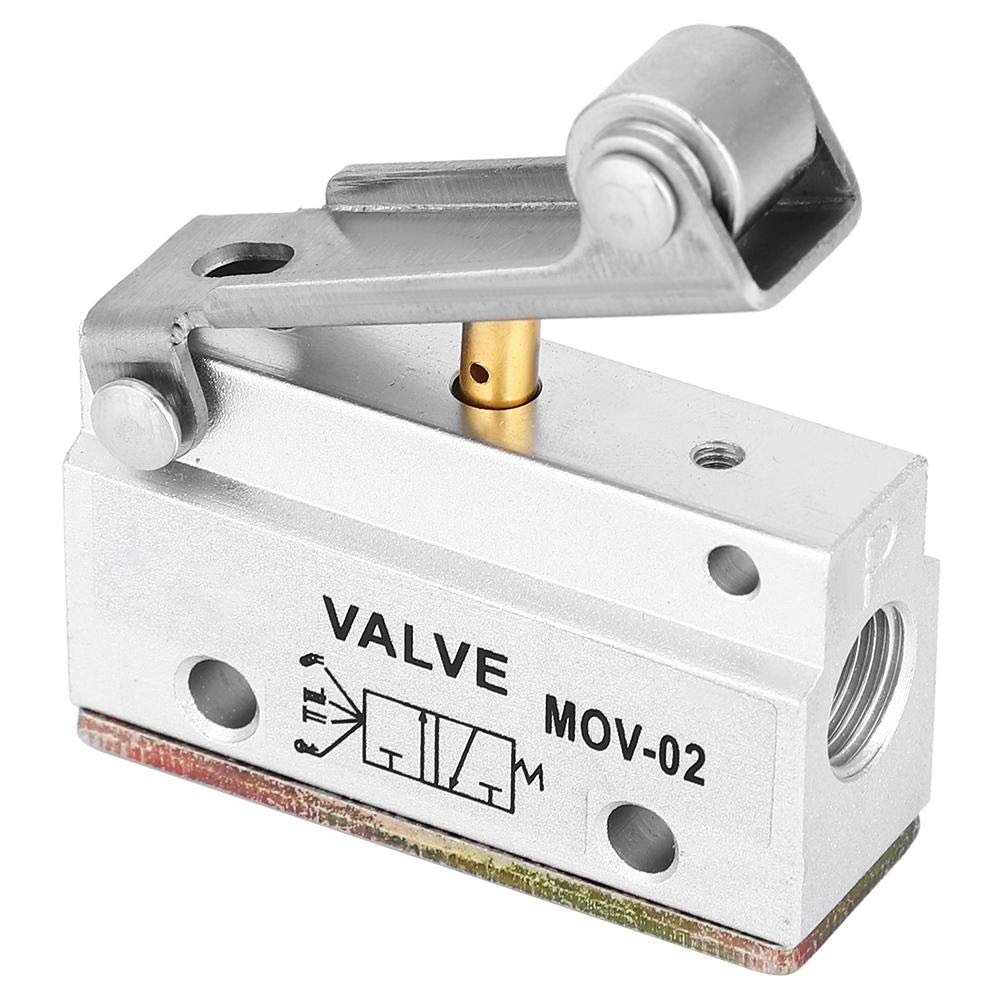
A stock image related to pneumatic valve.
Why Is Strategic Sourcing Essential for International Buyers?
For international buyers, particularly from regions like Africa, South America, the Middle East, and Europe, strategic sourcing goes beyond just procurement; it involves establishing long-term partnerships with manufacturers who understand local market dynamics. Leveraging the advantages of pneumatic valves, such as their quick response times and safety features, can lead to significant operational efficiencies and reduced downtime.
What Does the Future Hold for Pneumatic Valve Technology?
Looking ahead, advancements in pneumatic valve technology, including smart automation and integration with digital systems, will reshape how industries approach fluid control. B2B buyers should remain proactive in exploring these innovations to enhance their operations. By engaging with reliable suppliers and investing in cutting-edge solutions, you can position your business at the forefront of industrial automation. Take action today to streamline your sourcing strategy and unlock the full potential of pneumatic valve applications in your operations.