Discover Cost-Saving Benefits of Polyethylene Tube (2025)
Introduction: Navigating the Global Market for polyethylene tube
Navigating the global market for polyethylene tubes can be a daunting challenge for international B2B buyers, particularly those in regions like Africa, South America, the Middle East, and Europe. With a myriad of options available, from low-density polyethylene (LDPE) to high-density polyethylene (HDPE), sourcing the right polyethylene tube that meets specific application needs can feel overwhelming. This guide aims to simplify that process by providing a comprehensive overview of the various types of polyethylene tubes, their applications, and crucial factors to consider when vetting suppliers.
Throughout this guide, you will gain insights into the diverse applications of polyethylene tubes, such as for potable water systems, gas distribution, agricultural use, and industrial packaging. Additionally, we will discuss essential criteria for evaluating potential suppliers, including quality certifications, delivery capabilities, and pricing structures. By understanding these facets, B2B buyers can make informed decisions that not only meet their operational requirements but also contribute to cost efficiency and sustainability.
Empowering international buyers with actionable insights, this guide ensures that you can navigate the complexities of sourcing polyethylene tubes effectively. Whether you are based in Vietnam, Egypt, or elsewhere, the knowledge shared here will enhance your purchasing strategy, enabling you to secure high-quality products tailored to your specific needs.
Understanding polyethylene tube Types and Variations
Type Name | Key Distinguishing Features | Primary B2B Applications | Brief Pros & Cons for Buyers |
---|---|---|---|
Low-Density Polyethylene (LDPE) | Flexible, lightweight, and resistant to moisture | Packaging, shipping, and storage | Pros: Cost-effective, good chemical resistance. Cons: Less durable than HDPE. |
High-Density Polyethylene (HDPE) | Stiffer, more robust, and UV resistant | Water supply, gas distribution | Pros: Strong, long-lasting, suitable for outdoor use. Cons: Higher cost than LDPE. |
Polyethylene Tubing for Gas | Yellow color for gas applications, underground use | Natural gas and propane transport | Pros: Specifically designed for gas, robust. Cons: Limited to specific uses. |
Anti-Static Poly Tubing | Conductive properties to prevent static buildup | Electronics packaging | Pros: Protects sensitive electronics, versatile. Cons: Higher cost due to specialized features. |
Polyethylene Discharge Hose | Heavy-duty, designed for fluid transfer | Irrigation, drainage systems | Pros: Durable, high flow capacity. Cons: Bulky and less flexible than other types. |
What are the characteristics of Low-Density Polyethylene (LDPE) tubing?
Low-Density Polyethylene (LDPE) tubing is renowned for its flexibility and lightweight properties, making it ideal for various packaging and shipping applications. It offers excellent resistance to moisture, which is crucial for protecting products during storage and transit. B2B buyers should consider LDPE for projects requiring cost-effective solutions that do not compromise on chemical resistance. However, its lower durability compared to HDPE may be a drawback in more demanding environments.
How does High-Density Polyethylene (HDPE) tubing differ from LDPE?
High-Density Polyethylene (HDPE) tubing is characterized by its increased stiffness and robustness, providing superior strength and UV resistance. This makes it particularly suitable for applications in water supply and gas distribution. B2B buyers should prioritize HDPE when requiring long-lasting and outdoor-capable solutions, despite its higher cost compared to LDPE. Its durability ensures fewer replacements over time, ultimately providing a better return on investment.
Why is Polyethylene Tubing for Gas important in B2B applications?
Polyethylene tubing specifically designed for gas applications is typically colored yellow to signify its purpose for transporting natural gas and propane. This tubing is engineered for underground use, ensuring safety and compliance with industry standards. Buyers in the energy sector should consider this tubing for its robust design, which minimizes the risk of leaks. However, its specialized nature may limit its use to specific applications.
What are the benefits of using Anti-Static Poly Tubing in electronics?
Anti-Static Poly Tubing is designed with conductive properties to prevent static electricity buildup, which can damage sensitive electronic components. This type of tubing is essential for businesses involved in electronics packaging and shipping. While it offers significant protection for valuable products, buyers should be aware of the higher costs associated with its specialized features. Its versatility makes it a worthwhile investment for companies prioritizing product safety.
How does Polyethylene Discharge Hose serve irrigation and drainage systems?
Polyethylene Discharge Hose is a heavy-duty option designed specifically for fluid transfer in irrigation and drainage systems. Its durable construction allows for high flow capacity, making it ideal for agricultural and landscaping applications. B2B buyers should consider this type of tubing for its reliability and efficiency in managing water flow. However, its bulkiness may reduce flexibility, making installation more challenging in tight spaces.
Key Industrial Applications of polyethylene tube
Industry/Sector | Specific Application of polyethylene tube | Value/Benefit for the Business | Key Sourcing Considerations for this Application |
---|---|---|---|
Agriculture | Irrigation systems | Flexible and durable for efficient water delivery | UV resistance and compatibility with various fittings |
Construction | Water supply and drainage systems | Lightweight and easy to install, reducing labor costs | Compliance with local regulations and standards |
Oil & Gas | Gas distribution pipelines | High resistance to corrosion and pressure | Certifications for safety and compatibility with gas types |
Food & Beverage | Packaging for perishable goods | Protects products from moisture and contamination | Food-grade certifications and thickness options |
Medical | Medical tubing for fluid transfer | Ensures safety and sterility in medical applications | Compliance with health regulations and material safety |
How is Polyethylene Tube Used in Agriculture for Irrigation Systems?
In the agricultural sector, polyethylene tubes are widely used for irrigation systems, providing a flexible and durable solution for water delivery. They help solve the problem of inefficient water distribution, ensuring crops receive adequate moisture. Buyers in this sector should consider UV resistance to withstand sun exposure and compatibility with various fittings to facilitate easy installation and maintenance. For international buyers, sourcing from manufacturers who understand local agricultural practices can lead to better outcomes.
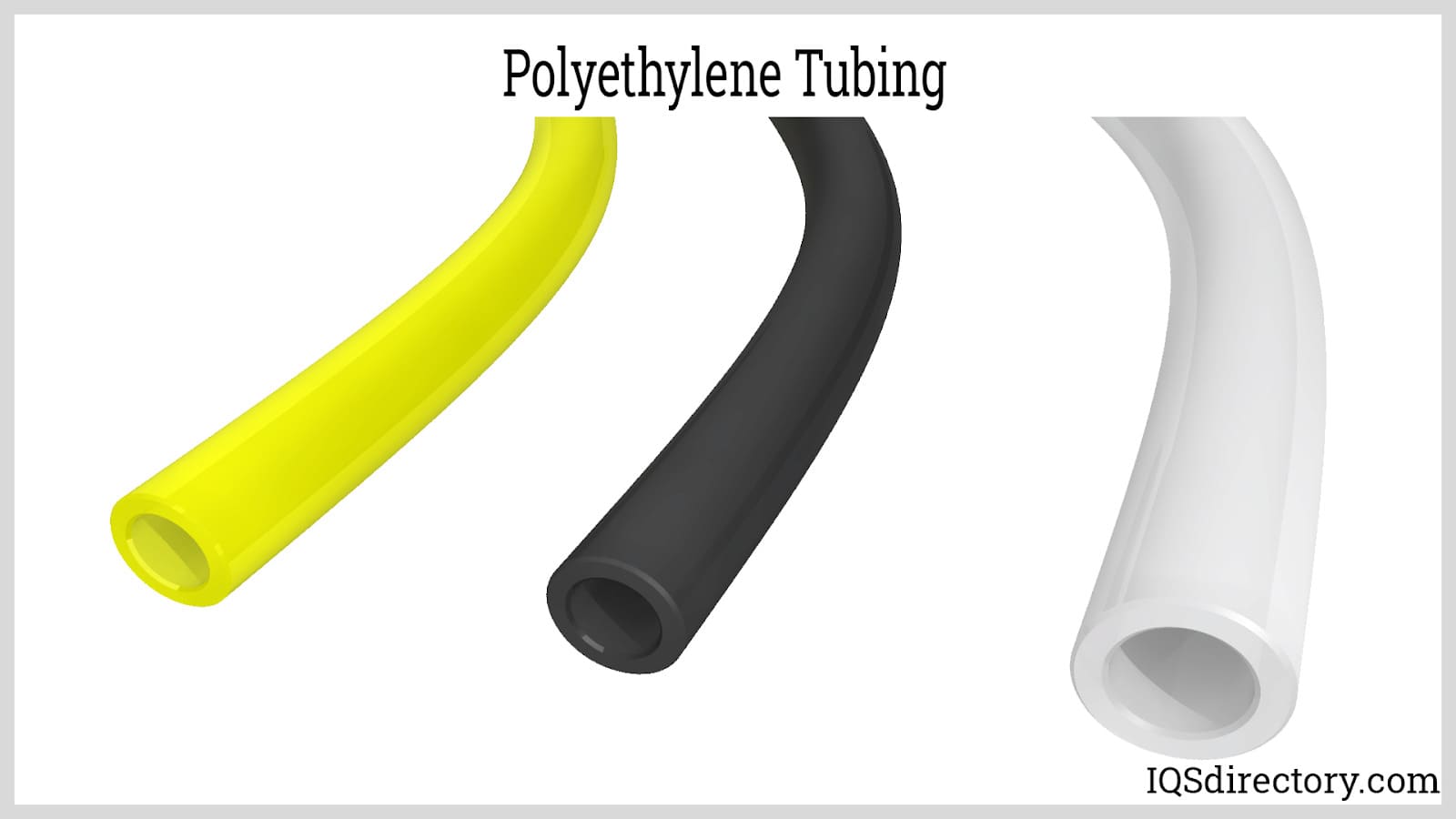
A stock image related to polyethylene tube.
What Role Does Polyethylene Tube Play in Construction for Water Supply and Drainage Systems?
In construction, polyethylene tubes are essential for water supply and drainage systems due to their lightweight nature and ease of installation. They reduce labor costs and time on-site while providing reliable performance. Buyers should ensure the products comply with local regulations and standards, as this can affect project approval and safety. Additionally, suppliers who offer a range of diameters and pressure ratings can better meet the diverse needs of construction projects across different regions.
How is Polyethylene Tube Utilized in the Oil & Gas Industry for Gas Distribution Pipelines?
The oil and gas industry relies on polyethylene tubes for gas distribution pipelines due to their high resistance to corrosion and ability to handle significant pressure. These tubes ensure safe and efficient transportation of natural gas and propane, addressing the critical need for reliable infrastructure. Buyers must prioritize sourcing from manufacturers with the necessary certifications to guarantee safety and compatibility with specific gas types. Understanding the local regulatory landscape is also crucial for compliance.
In What Ways Does Polyethylene Tube Benefit the Food & Beverage Industry for Packaging?
In the food and beverage sector, polyethylene tubes are used for packaging perishable goods, protecting products from moisture and contamination. This application is vital for maintaining product integrity and extending shelf life. Buyers should look for food-grade certifications and a variety of thickness options to suit different packaging needs. International buyers must consider local market preferences and regulations regarding food safety to ensure compliance and consumer trust.
How is Polyethylene Tube Essential in the Medical Sector for Fluid Transfer?
Polyethylene tubes play a critical role in the medical field, particularly for fluid transfer applications. They ensure safety and sterility, which are paramount in healthcare settings. Buyers in this sector should focus on sourcing materials that comply with health regulations and material safety standards. Additionally, understanding the specific requirements for medical applications can help international buyers navigate different regional regulations, ensuring the products meet local health and safety standards.
3 Common User Pain Points for ‘polyethylene tube’ & Their Solutions
Scenario 1: Sourcing Quality Polyethylene Tube for Diverse Applications
The Problem: International B2B buyers often struggle to source high-quality polyethylene tubes that meet specific requirements for diverse applications such as irrigation, gas distribution, and food packaging. Given the variation in manufacturing standards and the prevalence of counterfeit products, it can be challenging to ensure that the tubes will perform effectively in their intended environment. Buyers may also face difficulties in verifying the certifications and compliance of the products, which is critical for industries such as agriculture and food service.
The Solution: To overcome sourcing challenges, buyers should establish relationships with reputable manufacturers or suppliers known for their commitment to quality and compliance. Conduct thorough research by checking industry certifications such as ISO, NSF, and ASTM standards that validate product quality. Buyers should also request samples to test compatibility with their specific applications before placing larger orders. Engaging in direct communication with suppliers about material specifications and production processes can provide additional assurance of product integrity. Additionally, consider leveraging local distributors in your region who understand the market dynamics and can provide tailored solutions based on your unique requirements.
Scenario 2: Managing Costs and Budget Constraints with Polyethylene Tube Purchases
The Problem: Cost management is a significant concern for B2B buyers, especially when dealing with fluctuating prices of raw materials like polyethylene. Buyers from regions such as Africa and South America may face additional challenges related to import tariffs and shipping costs, which can escalate the overall expenditure on polyethylene tubes. This financial strain can limit their ability to procure the necessary quantities or quality of products needed for their projects.
The Solution: To effectively manage costs, B2B buyers should consider bulk purchasing agreements with suppliers to lock in prices and reduce per-unit costs. Establishing long-term relationships with manufacturers can also lead to better pricing and payment terms. It is essential to analyze the total cost of ownership (TCO) rather than just the initial purchase price; this includes transportation, storage, and potential downtime due to product failure. Buyers should also explore alternative materials or suppliers that offer competitive pricing without compromising on quality. Additionally, participating in industry associations can provide insights into market trends and opportunities for collective purchasing, further enhancing cost efficiency.
Scenario 3: Addressing Environmental Concerns with Polyethylene Tube Disposal
The Problem: Environmental sustainability is becoming increasingly important for businesses globally, and B2B buyers are often faced with the challenge of ensuring that their use of polyethylene tubes aligns with eco-friendly practices. Many buyers are concerned about the environmental impact of plastic waste, especially in regions where waste management systems are not robust. This concern can lead to hesitance in adopting polyethylene tubes, despite their advantages in terms of durability and versatility.
The Solution: To address environmental concerns, buyers should look for suppliers that provide options for recyclable or biodegradable polyethylene tubes. Engaging with manufacturers who have sustainable practices and offer take-back programs for used products can significantly mitigate the environmental impact. Buyers can also educate themselves about local recycling regulations and collaborate with waste management companies to create a responsible disposal strategy. Implementing a product lifecycle assessment can help identify areas for improvement in sourcing and disposal. Furthermore, consider investing in research and development for alternatives to traditional polyethylene, such as bio-based polymers, which can help position your business as a leader in sustainability within your industry.
Strategic Material Selection Guide for polyethylene tube
When selecting polyethylene tubes for various applications, it is essential to understand the properties and suitability of different materials. Below is an analysis of four common types of polyethylene materials used in tube manufacturing, focusing on their key properties, advantages, disadvantages, and considerations for international B2B buyers, particularly from regions such as Africa, South America, the Middle East, and Europe.
What are the Key Properties of Low-Density Polyethylene (LDPE) Tubes?
Low-Density Polyethylene (LDPE) is characterized by its flexibility and excellent chemical resistance. LDPE tubes can withstand temperatures up to 60°C (140°F) and are suitable for low-pressure applications. They are particularly resistant to moisture, making them ideal for packaging and storage purposes.
Pros: LDPE is lightweight, making it cost-effective for shipping and handling. Its flexibility allows for easy installation in various configurations.
Cons: However, LDPE has lower tensile strength compared to other polyethylene types, which may limit its use in high-pressure applications. Additionally, it can be less durable in extreme environmental conditions.
Impact on Application: LDPE is commonly used for applications involving non-potable water and certain chemicals. However, it is not recommended for high-temperature or high-pressure applications.
How Does High-Density Polyethylene (HDPE) Compare for Tube Applications?
High-Density Polyethylene (HDPE) offers superior strength and rigidity compared to LDPE. It can handle temperatures up to 80°C (176°F) and is resistant to a wide range of chemicals, making it suitable for various industrial applications, including water and gas distribution.
Pros: HDPE is known for its high impact resistance and durability, which makes it suitable for underground installations and applications requiring longevity.
Cons: The primary drawback is its higher cost compared to LDPE, which may impact budget-sensitive projects. Additionally, HDPE can be more challenging to work with due to its rigidity.
Impact on Application: HDPE tubes are ideal for transporting potable water, natural gas, and other pressurized fluids, making them a preferred choice in construction and municipal projects.
What are the Benefits and Limitations of Polypropylene Tubes?
Polypropylene (PP) tubes are known for their excellent chemical resistance and high-temperature tolerance, withstanding temperatures up to 100°C (212°F). They are lightweight and have a good balance of flexibility and rigidity.
Pros: Polypropylene is resistant to a wide range of solvents and is less prone to cracking under stress, making it suitable for various applications, including food and pharmaceutical industries.
Cons: However, polypropylene can be more expensive than both LDPE and HDPE. Additionally, it has a lower UV resistance, which may limit its outdoor applications without proper treatment.
Impact on Application: PP tubes are commonly used in applications requiring high purity and chemical resistance, such as in laboratories and food processing.
What Should International B2B Buyers Consider When Choosing Polyethylene Tubes?
International B2B buyers must consider several factors when selecting polyethylene tubes, including compliance with local standards such as ASTM, DIN, or JIS. Different regions may have specific regulations regarding the use of materials in potable water systems or food applications.
Additionally, understanding the local market preferences and availability of materials can significantly influence purchasing decisions. For instance, buyers in Africa and South America may prioritize cost-effectiveness, while those in Europe may focus on compliance and sustainability.
Summary Table of Material Selection
Material | Typical Use Case for polyethylene tube | Key Advantage | Key Disadvantage/Limitation | Relative Cost (Low/Med/High) |
---|---|---|---|---|
Low-Density Polyethylene (LDPE) | Packaging, non-potable water | Lightweight and flexible | Lower tensile strength | Low |
High-Density Polyethylene (HDPE) | Potable water, gas distribution | High durability and impact resistance | Higher cost and rigidity | Medium |
Polypropylene (PP) | Food processing, pharmaceuticals | Excellent chemical resistance | More expensive and lower UV resistance | Medium |
Low-Density Polyethylene (LDPE) | Packaging, non-potable water | Lightweight and flexible | Lower tensile strength | Low |
This analysis provides actionable insights for B2B buyers navigating the complexities of polyethylene tube selection, ensuring they make informed decisions that align with their operational needs and regional requirements.
In-depth Look: Manufacturing Processes and Quality Assurance for polyethylene tube
What Are the Key Stages in the Manufacturing Process of Polyethylene Tubes?
The manufacturing of polyethylene tubes involves several critical stages that ensure the final product meets the necessary specifications for strength, flexibility, and durability. Understanding these stages is essential for international B2B buyers seeking reliable suppliers.
1. Material Preparation
The process begins with the selection of the appropriate grade of polyethylene, typically low-density polyethylene (LDPE) or high-density polyethylene (HDPE). The chosen material is then subjected to quality control checks to ensure consistency in properties such as density and melt flow index. Material preparation also includes drying to remove moisture and additives that enhance the tube’s performance, such as UV stabilizers or colorants.
2. Forming
The forming stage involves extrusion, where the prepared polyethylene is heated and forced through a die to create a continuous tube. The extrusion process can be adjusted to achieve various diameters and wall thicknesses. This is a critical phase, as the extrusion speed, temperature, and pressure must be carefully controlled to prevent defects like sagging or uneven walls.
3. Assembly
For applications requiring specific fittings or configurations, the assembly stage may involve additional processes such as cutting the extruded tube to the desired length, welding sections together, or attaching fittings. This is particularly relevant for B2B buyers who require customized solutions for their projects.
4. Finishing
The finishing stage includes cooling, cutting, and potentially surface treatments, such as printing or applying protective coatings. Cooling is vital to ensure the tube retains its shape and dimensional integrity. Quality checks are performed at this stage to identify any visible defects or dimensional inaccuracies before packaging.
How Is Quality Assurance Implemented in Polyethylene Tube Manufacturing?
Quality assurance is paramount in ensuring that polyethylene tubes meet international standards and customer expectations. B2B buyers should be aware of the following key aspects of quality control.
Relevant International Standards for Polyethylene Tubes
International quality standards, such as ISO 9001, are widely adopted in the manufacturing of polyethylene tubes. This standard focuses on ensuring consistent quality through well-defined processes and continuous improvement. In addition, industry-specific certifications, such as CE marking for European markets and API standards for oil and gas applications, provide further assurance of product quality and safety.
What Are the QC Checkpoints in the Manufacturing Process?
Quality control in polyethylene tube manufacturing typically involves several checkpoints:
- Incoming Quality Control (IQC): This step involves inspecting raw materials before they enter the production process. Suppliers must provide documentation confirming material specifications.
- In-Process Quality Control (IPQC): During manufacturing, operators monitor parameters such as temperature, pressure, and speed. Regular sampling and testing help identify any deviations from quality standards.
- Final Quality Control (FQC): After production, finished products undergo rigorous testing for dimensional accuracy, pressure resistance, and overall integrity. This stage ensures that the tubes meet all specified requirements.
What Common Testing Methods Are Used for Polyethylene Tubes?
Several testing methods are employed to validate the quality of polyethylene tubes:
- Hydrostatic Pressure Testing: This method assesses the tube’s ability to withstand internal pressure without leaking or bursting.
- Dimensional Inspection: Using calipers and gauges, manufacturers verify that the tube dimensions adhere to specifications.
- Impact Resistance Testing: This assesses the tube’s durability and resilience, especially in applications subject to physical stress.
- Environmental Stress Crack Resistance (ESCR) Testing: This evaluates the tube’s resistance to cracking under environmental conditions, which is crucial for outdoor applications.
How Can B2B Buyers Verify Supplier Quality Control Processes?
B2B buyers should take proactive steps to ensure their suppliers maintain rigorous quality control standards. Here are some actionable insights:
Conduct Supplier Audits
Regular audits of potential suppliers can provide valuable insights into their manufacturing processes and quality control measures. Buyers should assess the supplier’s adherence to international standards, employee training programs, and maintenance of equipment.
Request Quality Control Reports
Buyers should request documentation of quality control procedures, including testing results, certifications, and any corrective actions taken in response to quality issues. This transparency allows buyers to gauge the supplier’s commitment to quality.
Utilize Third-Party Inspection Services
Engaging third-party inspection services can offer an unbiased assessment of the supplier’s operations. These inspections can verify compliance with specified quality standards and provide detailed reports on manufacturing practices.
What Are the QC and Certification Nuances for International B2B Buyers?
International B2B buyers, particularly those from Africa, South America, the Middle East, and Europe, should consider the following nuances:
- Understanding Regional Regulations: Different regions may have specific regulations regarding the use of polyethylene tubes, especially in applications like potable water or gas transportation. Buyers must ensure that suppliers comply with local laws and standards.
- Language and Documentation Barriers: Buyers should be prepared to navigate potential language barriers when reviewing quality documentation. Ensuring that all certifications and reports are available in a language that can be easily understood is crucial for effective communication.
- Supplier Relationships: Building strong relationships with suppliers can facilitate better communication regarding quality concerns. Regular engagement can lead to improved transparency and responsiveness from suppliers.
By comprehensively understanding the manufacturing processes and quality assurance measures for polyethylene tubes, international B2B buyers can make informed decisions, ensuring they partner with reliable suppliers that meet their specific needs.
Practical Sourcing Guide: A Step-by-Step Checklist for ‘polyethylene tube’
In the competitive landscape of sourcing polyethylene tubes, it’s essential for B2B buyers, especially from regions like Africa, South America, the Middle East, and Europe, to follow a structured approach. This practical sourcing guide outlines a comprehensive checklist to ensure you make informed purchasing decisions.
Step 1: Define Your Technical Specifications
Before initiating the sourcing process, clearly outline the technical specifications of the polyethylene tube you require. This includes dimensions, thickness, and any specific material properties such as low-density or high-density polyethylene. Understanding these parameters helps streamline your search and ensures compatibility with your applications, such as agricultural irrigation or industrial uses.
Step 2: Research Potential Suppliers
Conduct thorough research to identify potential suppliers. Utilize online platforms, trade directories, and industry-specific forums to compile a list of candidates. Pay attention to their reputation, customer reviews, and any awards or recognitions they may have received. A well-established supplier is more likely to meet your quality and delivery expectations.
Step 3: Evaluate Supplier Certifications
âś… Verify Supplier Certifications
It’s crucial to ensure that your selected suppliers hold relevant certifications, such as ISO 9001 or industry-specific standards. Certifications validate that the supplier adheres to quality management principles and practices. Request copies of these certifications and check for compliance with local regulations, especially if you’re sourcing for critical applications like potable water systems.
Step 4: Request Samples for Quality Assessment
Before finalizing your order, request samples of the polyethylene tubes. This step allows you to physically assess the product quality, including flexibility, durability, and resistance to chemicals. Ensure the samples are representative of the supplier’s production capabilities and match your specified requirements.
Step 5: Compare Pricing and Terms
đź’° Analyze Pricing and Payment Terms
Once you have evaluated the quality of the samples, compare pricing among your shortlisted suppliers. Look beyond just the unit price; consider total cost implications including shipping, taxes, and potential tariffs. Additionally, review payment terms and conditions, ensuring they align with your budget and cash flow needs.
Step 6: Negotiate and Finalize Contracts
Engage in negotiations with your chosen supplier(s) to finalize pricing, delivery schedules, and terms of service. Clear communication during this phase is crucial to avoid misunderstandings later. Ensure that all agreements are documented in a formal contract, specifying quality guarantees, lead times, and penalties for non-compliance.
Step 7: Plan for Logistics and Delivery
📦 Coordinate Logistics and Delivery Options
After securing your contract, coordinate the logistics of shipping and delivery. Evaluate the supplier’s shipping capabilities and timelines, considering your operational needs. Plan for customs clearance, especially if you’re importing from overseas, and ensure you have the necessary documentation ready to facilitate a smooth process.
By following this structured checklist, international B2B buyers can effectively navigate the complexities of sourcing polyethylene tubes, ensuring they make informed decisions that align with their operational needs and business objectives.
Comprehensive Cost and Pricing Analysis for polyethylene tube Sourcing
What Are the Key Cost Components in Polyethylene Tube Sourcing?
When sourcing polyethylene tubes, understanding the cost structure is crucial for B2B buyers. The primary components include:
-
Materials: The type of polyethylene used (e.g., low-density polyethylene (LDPE) or high-density polyethylene (HDPE)) significantly affects costs. HDPE is generally more expensive due to its higher strength and durability. Fluctuations in the global oil market can also impact material costs.
-
Labor: Labor costs vary by region and can be influenced by local wage rates and skill levels. In emerging markets such as Africa and South America, labor costs may be lower, but it’s essential to consider the trade-off with quality and expertise.
-
Manufacturing Overhead: This includes costs associated with maintaining production facilities, utilities, and administrative expenses. Efficient manufacturing processes can help reduce these overheads.
-
Tooling: The initial setup costs for molds and machinery can be significant, especially for custom specifications. Buyers should evaluate whether the tooling costs are included in the quoted prices or if they will be additional.
-
Quality Control (QC): Ensuring that polyethylene tubes meet specific standards often requires investment in quality control processes. Compliance with international standards can add to the cost but is crucial for reliability, especially in regulated industries.
-
Logistics: Transportation costs can vary greatly depending on the supplier’s location and the chosen shipping method. Understanding local infrastructure and potential tariffs is vital for accurate cost assessment.
-
Margin: Suppliers typically build in a margin based on their operational costs and market conditions. Comparing multiple suppliers can help buyers gauge a reasonable margin.
How Do Price Influencers Affect Polyethylene Tube Costs?
Several factors can influence the pricing of polyethylene tubes:
-
Volume and Minimum Order Quantity (MOQ): Larger orders often result in lower per-unit costs. Buyers should consider their needs carefully to negotiate favorable terms, particularly if they can meet or exceed MOQs.
-
Specifications and Customization: Custom sizes, colors, or specifications can increase costs. Buyers should clearly communicate their requirements to obtain accurate quotes and avoid unexpected charges.
-
Material Quality and Certifications: Higher-quality materials or certifications (e.g., NSF for potable water) may come at a premium. Buyers should weigh the benefits of these certifications against their project requirements.
-
Supplier Factors: The supplier’s reputation, reliability, and geographic location can impact pricing. Established suppliers may charge higher prices but provide better service and quality assurance.
-
Incoterms: Understanding the terms of delivery (e.g., FOB, CIF) is essential for managing costs. Incoterms define the responsibilities of buyers and sellers in international shipping, which can affect the overall cost structure.
What Are Effective Buyer Tips for Cost-Efficiency in Sourcing?
To optimize sourcing costs, B2B buyers should consider the following strategies:
-
Negotiate Effectively: Always negotiate pricing based on your order size and potential long-term relationships. Suppliers may offer discounts for repeat business or larger orders.
-
Total Cost of Ownership (TCO): Evaluate not just the purchase price but also the long-term costs associated with sourcing polyethylene tubes, including maintenance, disposal, and logistics.
-
Understand Pricing Nuances for International Buyers: International sourcing can involve additional costs such as import duties, taxes, and currency fluctuations. It’s essential to factor these into the overall pricing strategy.
-
Research Local Suppliers: In regions like Africa and South America, sourcing from local suppliers can reduce shipping costs and lead times, enhancing overall supply chain efficiency.
-
Request Quotes from Multiple Suppliers: Obtain quotes from several suppliers to compare prices and services. This practice not only provides insight into market rates but also strengthens your negotiating position.
Disclaimer for Indicative Prices
Prices for polyethylene tubes can vary widely based on the factors discussed above. Buyers should always obtain current quotes and clarify all cost components before making purchasing decisions.
Alternatives Analysis: Comparing polyethylene tube With Other Solutions
Understanding Alternatives to Polyethylene Tubes
When selecting materials for various applications, B2B buyers often consider multiple alternatives to ensure they choose the most effective solution. Polyethylene tubes are widely used for their flexibility, durability, and cost-effectiveness. However, there are several other options available that may better suit specific needs depending on the application, budget, and environmental conditions. This analysis compares polyethylene tubes with two viable alternatives: PVC (Polyvinyl Chloride) tubing and rubber hoses.
Comparison Aspect | Polyethylene Tube | PVC Tubing | Rubber Hose |
---|---|---|---|
Performance | Good flexibility and strength | Rigid; excellent chemical resistance | High elasticity; can handle high pressure |
Cost | Generally low | Moderate | Higher than polyethylene and PVC |
Ease of Implementation | Easy to install and work with | Requires specific fittings for installation | Simple to connect but may require clamps |
Maintenance | Low; resistant to corrosion | Low; can be damaged by UV light | Moderate; regular inspection required |
Best Use Case | Water supply, irrigation | Chemical transport, drainage | High-pressure applications, outdoor use |
What Are the Pros and Cons of PVC Tubing Compared to Polyethylene Tubes?
PVC tubing is known for its rigidity and excellent resistance to chemicals, making it an ideal choice for applications that involve hazardous materials. It is easy to clean and maintain, and its long lifespan often offsets the higher initial cost. However, PVC can be less flexible than polyethylene, which may pose installation challenges in tight spaces. Additionally, PVC can be susceptible to UV damage if exposed to sunlight for prolonged periods, limiting its outdoor applications.
How Does Rubber Hose Compare to Polyethylene Tubes?
Rubber hoses are highly flexible and can handle high-pressure scenarios, making them suitable for a variety of industrial applications. Their elasticity allows them to be used in environments where movement is frequent. However, rubber hoses tend to be more expensive than both polyethylene and PVC options. They require regular maintenance checks to ensure they remain in good condition, as they can be prone to wear and tear from external elements.
Conclusion: How Can B2B Buyers Choose the Right Solution for Their Needs?
When selecting between polyethylene tubes, PVC tubing, and rubber hoses, B2B buyers should carefully assess their specific application requirements, including the environment, pressure needs, and chemical exposure. For general water supply and irrigation, polyethylene tubes often provide the best combination of cost and performance. In contrast, if chemical resistance is paramount, PVC may be the superior choice. For high-pressure applications, rubber hoses could be the best fit despite their higher cost. Ultimately, understanding the unique advantages and limitations of each material will empower buyers to make informed purchasing decisions that align with their operational goals.
Essential Technical Properties and Trade Terminology for polyethylene tube
What Are the Key Technical Properties of Polyethylene Tubes?
When sourcing polyethylene tubes, understanding their technical properties is crucial for making informed purchasing decisions. Here are some of the key specifications to consider:
-
Material Grade
Polyethylene tubes are available in various grades, primarily Low-Density Polyethylene (LDPE) and High-Density Polyethylene (HDPE). LDPE is flexible and suitable for applications requiring bending, while HDPE offers higher strength and durability, making it ideal for pressure applications. Knowing the right material grade ensures that the product meets the specific demands of your project, whether it’s for gas transportation or agricultural irrigation. -
Nominal Diameter
The nominal diameter of a polyethylene tube is a critical specification that affects flow rates and compatibility with fittings. It is essential to match the nominal diameter with existing systems to ensure seamless integration. Different applications, such as potable water systems or drainage, may require specific diameters to function efficiently. -
Wall Thickness
The wall thickness of polyethylene tubes varies based on their intended use. Thicker walls provide greater pressure resistance and durability, particularly in underground applications. For B2B buyers, understanding the required wall thickness helps in selecting products that can withstand operational stresses without compromising safety. -
Pressure Rating
The pressure rating indicates the maximum pressure the tube can handle safely. It is measured in pounds per square inch (PSI) and is critical for applications involving liquids or gases. Selecting a tube with an appropriate pressure rating is essential to prevent leaks and ensure system reliability, especially in industrial and agricultural sectors. -
Chemical Resistance
Polyethylene tubes exhibit varying degrees of resistance to chemicals, which is crucial for applications in industries such as agriculture, construction, and manufacturing. Knowing the chemical compatibility of the tube material with the substances it will carry helps avoid premature failure and enhances product longevity. -
Temperature Range
Understanding the operational temperature range of polyethylene tubes is vital for ensuring their performance in different environments. Certain applications may expose tubes to extreme temperatures, which can affect flexibility and strength. Selecting tubes that can withstand the expected temperature conditions is essential for preventing damage and ensuring safety.
What Common Trade Terminology Should B2B Buyers Know?
In addition to technical specifications, familiarizing yourself with industry jargon can facilitate smoother transactions and communication with suppliers. Here are some common terms:
-
OEM (Original Equipment Manufacturer)
This term refers to companies that produce parts or equipment that may be marketed by another manufacturer. In the context of polyethylene tubes, knowing the OEM can help buyers assess the quality and reliability of the products they are sourcing. -
MOQ (Minimum Order Quantity)
MOQ indicates the smallest quantity of a product that a supplier is willing to sell. Understanding MOQ is essential for B2B buyers to manage inventory and costs effectively. Larger MOQs may lead to better pricing but can also result in excess inventory. -
RFQ (Request for Quotation)
An RFQ is a formal document sent to suppliers to request pricing and terms for a specific quantity of goods. This process is crucial for obtaining competitive quotes, allowing buyers to compare costs and make informed purchasing decisions. -
Incoterms (International Commercial Terms)
Incoterms are a set of predefined commercial terms used in international trade to clarify the responsibilities of buyers and sellers. Familiarity with these terms can prevent misunderstandings related to shipping, insurance, and liability, ensuring smooth international transactions. -
Lead Time
Lead time refers to the duration between placing an order and receiving the product. Understanding lead times is vital for planning and ensuring that projects stay on schedule, especially in industries with tight deadlines. -
Certification Standards
Certification standards, such as NSF (National Sanitation Foundation) or ASTM (American Society for Testing and Materials), indicate that the polyethylene tubes meet specific safety and quality benchmarks. Buyers should verify these certifications to ensure compliance with local regulations and industry standards.
By understanding these technical properties and trade terms, international B2B buyers can make more informed decisions when sourcing polyethylene tubes, ultimately leading to better project outcomes and cost management.
Navigating Market Dynamics and Sourcing Trends in the polyethylene tube Sector
What Are the Current Market Dynamics and Key Trends in the Polyethylene Tube Sector?
The polyethylene tube market is experiencing robust growth, driven by increased demand across various industries including agriculture, construction, and healthcare. Key trends shaping this market include the adoption of advanced manufacturing technologies such as automation and IoT, which enhance production efficiency and quality control. Additionally, the rise of e-commerce has transformed sourcing strategies, allowing international B2B buyers from regions like Africa, South America, the Middle East, and Europe to access a wider range of suppliers and products online.
In emerging markets, particularly in Africa and South America, there is a growing focus on infrastructure development, which is fueling demand for polyethylene tubes. In Europe and the Middle East, regulatory frameworks promoting sustainability are influencing sourcing decisions, pushing suppliers to innovate and provide eco-friendly solutions. As a result, buyers are increasingly seeking suppliers who can offer not only competitive pricing but also the ability to meet stringent quality and sustainability standards.
Moreover, with the global shift towards digital platforms, B2B buyers now have access to real-time data and analytics. This empowers them to make informed decisions regarding price negotiations, supplier reliability, and product quality. As the polyethylene tube sector continues to evolve, understanding these market dynamics and leveraging technology will be crucial for international buyers to remain competitive.
How Is Sustainability Influencing Sourcing Decisions in the Polyethylene Tube Sector?
Sustainability has become a critical consideration for B2B buyers in the polyethylene tube sector, reflecting a broader shift towards environmental responsibility. The production and disposal of traditional polyethylene materials pose significant environmental challenges, including pollution and waste. As such, buyers are increasingly prioritizing suppliers who demonstrate a commitment to ethical sourcing and sustainable practices.
One significant trend is the adoption of recycled polyethylene (rPE) materials, which not only reduce waste but also lower the carbon footprint associated with production. Suppliers that offer ‘green’ certifications, such as those from the Forest Stewardship Council (FSC) or ISO 14001 for environmental management, are gaining a competitive edge. These certifications provide assurance to buyers that the products meet stringent environmental standards.
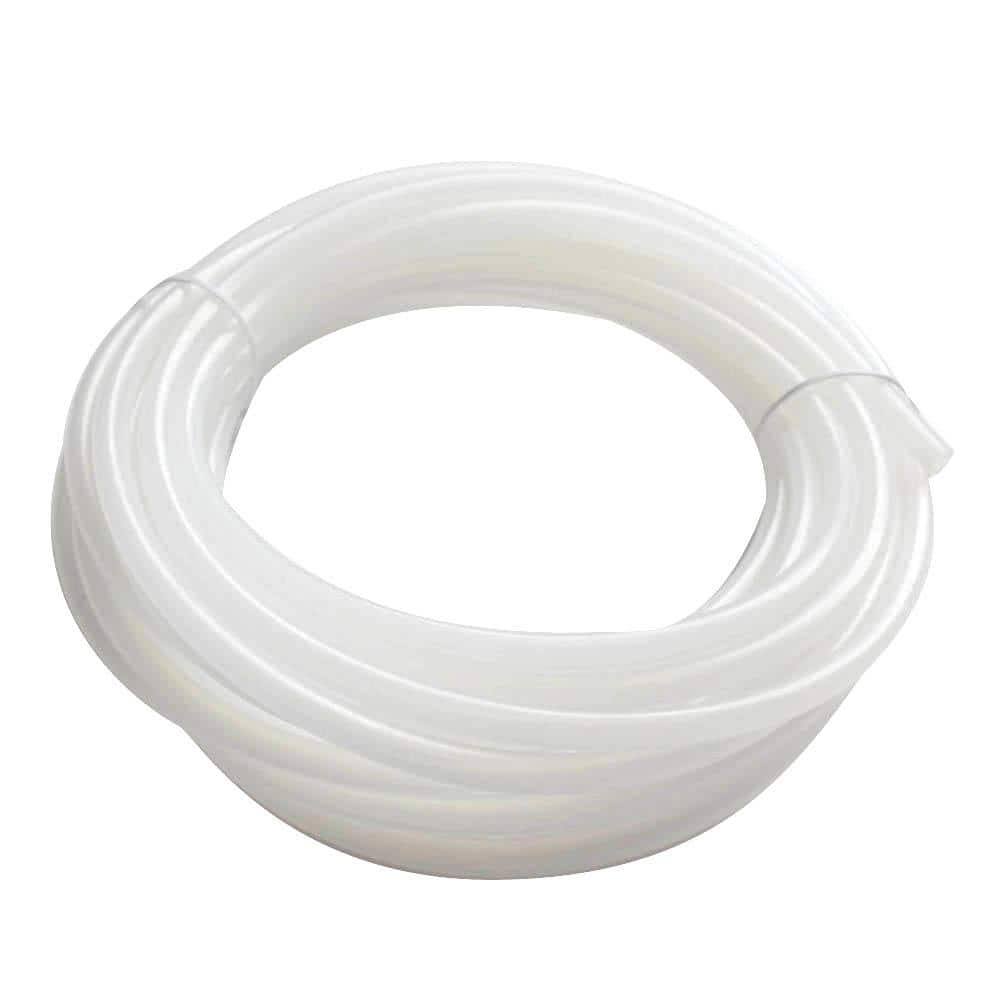
A stock image related to polyethylene tube.
Additionally, ethical supply chains are becoming a focal point for many international buyers. This involves scrutinizing suppliers for their labor practices, sourcing transparency, and overall corporate social responsibility. By choosing suppliers with strong sustainability credentials, businesses can enhance their brand reputation while contributing to global sustainability goals.
What Is the Evolution of the Polyethylene Tube Industry and Its Relevance to B2B Buyers?
The polyethylene tube industry has evolved significantly since its inception in the mid-20th century, transitioning from a niche product to a vital component across multiple sectors. Initially, polyethylene tubes were primarily utilized in agricultural applications for irrigation and drainage. However, advancements in polymer technology have led to the development of high-density polyethylene (HDPE) and low-density polyethylene (LDPE) tubes that offer superior durability and flexibility.
In the 1980s and 1990s, the industry began to diversify, with polyethylene tubes finding applications in construction, telecommunications, and healthcare. This diversification opened new markets and opportunities for international B2B buyers. Today, the polyethylene tube market is characterized by a wide range of products tailored to specific applications, including potable water delivery, gas distribution, and medical tubing.
Understanding the evolution of this sector is crucial for B2B buyers, as it highlights the importance of innovation and adaptation in sourcing strategies. As the market continues to evolve, staying informed about technological advancements and market trends will empower buyers to make strategic sourcing decisions that align with their business objectives.
Frequently Asked Questions (FAQs) for B2B Buyers of polyethylene tube
-
How do I choose the right polyethylene tube for my application?
When selecting polyethylene tubes, consider the specific application requirements, such as pressure ratings, chemical compatibility, and temperature range. Different grades of polyethylene, like Low-Density Polyethylene (LDPE) and High-Density Polyethylene (HDPE), offer distinct characteristics suitable for various uses. For example, LDPE is more flexible, making it ideal for packaging, while HDPE is better suited for high-pressure applications. Always consult product specifications and, if needed, engage with suppliers for recommendations based on your operational needs. -
What are the advantages of using polyethylene tubing over other materials?
Polyethylene tubing is lightweight, durable, and resistant to chemicals, moisture, and abrasion, making it a popular choice in various industries. It offers flexibility, which allows for easy installation and handling. Additionally, polyethylene is cost-effective compared to alternatives like metal or PVC tubing, especially for large-scale applications. Its corrosion resistance and low friction properties also enhance its longevity and efficiency in fluid transfer systems. -
What are the minimum order quantities (MOQs) for polyethylene tubes?
Minimum order quantities for polyethylene tubes can vary significantly between suppliers, often depending on the tube specifications and customization requirements. Many suppliers may have a standard MOQ ranging from 100 to 1,000 feet or more. For international buyers, negotiating MOQs might be possible, particularly for bulk orders or if you’re establishing a long-term partnership. Always clarify MOQs upfront to avoid unexpected costs. -
How can I ensure the quality of polyethylene tubing from international suppliers?
To ensure quality, request samples before committing to large orders. Verify if the supplier adheres to international quality standards such as ISO 9001. Look for certifications relevant to your industry, such as NSF for potable water applications. Additionally, consider conducting factory audits or third-party inspections, especially when sourcing from regions with varying manufacturing standards. Establishing a clear quality assurance agreement can also help mitigate risks. -
What payment terms should I expect when purchasing polyethylene tubing internationally?
Payment terms can vary widely among suppliers, but common practices include options like advance payment, letter of credit, or payment upon delivery. For larger transactions, consider negotiating terms that provide both parties with security, such as partial payment upfront and the balance upon delivery. Always ensure that the payment method is secure and offers protection against fraud, particularly when dealing with new suppliers. -
What are the logistics considerations when importing polyethylene tubes?
Logistics for importing polyethylene tubes involve understanding shipping methods, customs regulations, and potential tariffs. Consider the mode of transport (air vs. sea) based on cost and urgency. Ensure that your supplier provides accurate shipping documentation, including invoices and packing lists. Familiarize yourself with the import regulations of your country to avoid delays at customs. Working with a reliable freight forwarder can streamline the process and help navigate complex logistics. -
Can I customize polyethylene tubing for my specific needs?
Yes, many suppliers offer customization options for polyethylene tubing, including variations in thickness, color, and length. You may also request specific formulations to enhance properties like UV resistance or anti-static features. When considering customization, be prepared to discuss your requirements in detail with the supplier to ensure they can meet your needs. Keep in mind that custom orders may have longer lead times and higher costs. -
How do I handle potential supply chain disruptions when sourcing polyethylene tubes?
To mitigate supply chain disruptions, diversify your supplier base across different regions. Establishing relationships with multiple suppliers can provide alternatives in case of delays or shortages. Stay informed about geopolitical developments and market trends that may impact supply chains. Additionally, consider building buffer stock to accommodate fluctuations in demand or unexpected delays, ensuring your operations remain uninterrupted. Regular communication with suppliers can also help anticipate and address potential issues proactively.
Important Disclaimer & Terms of Use
⚠️ Important Disclaimer
The information provided in this guide, including content regarding manufacturers, technical specifications, and market analysis, is for informational and educational purposes only. It does not constitute professional procurement advice, financial advice, or legal advice.
While we have made every effort to ensure the accuracy and timeliness of the information, we are not responsible for any errors, omissions, or outdated information. Market conditions, company details, and technical standards are subject to change.
B2B buyers must conduct their own independent and thorough due diligence before making any purchasing decisions. This includes contacting suppliers directly, verifying certifications, requesting samples, and seeking professional consultation. The risk of relying on any information in this guide is borne solely by the reader.
Strategic Sourcing Conclusion and Outlook for polyethylene tube
In the rapidly evolving landscape of polyethylene tube sourcing, strategic partnerships are essential for B2B buyers aiming to optimize their supply chains. With diverse applications spanning agriculture, construction, and plumbing, polyethylene tubes offer unparalleled flexibility, durability, and resistance to various environmental factors. Buyers should prioritize suppliers that provide a range of product specifications, including varying diameters and thicknesses, to meet specific project needs effectively.
Why is Strategic Sourcing Essential for Polyethylene Tube Purchases?
Strategic sourcing not only enhances cost-effectiveness but also ensures the quality and reliability of materials. By engaging with multiple suppliers across different regions—especially in Africa, South America, the Middle East, and Europe—buyers can mitigate risks associated with price fluctuations and supply chain disruptions. Establishing long-term relationships with reputable manufacturers can lead to better terms and quicker response times, which are crucial for maintaining operational efficiency.
What Does the Future Hold for Polyethylene Tube Buyers?
Looking ahead, the demand for sustainable and versatile materials will continue to rise. International buyers are encouraged to explore innovative solutions such as recycled polyethylene options to meet both regulatory requirements and consumer expectations. By leveraging strategic sourcing practices, businesses can position themselves competitively in the market. Now is the time to assess your current supply strategies and align them with future trends to maximize your procurement effectiveness.