Discover Cost-Saving Benefits of Spin Forming (2025)
Introduction: Navigating the Global Market for spin forming
In the competitive landscape of international manufacturing, sourcing reliable spin forming solutions can pose significant challenges for B2B buyers. As industries across Africa, South America, the Middle East, and Europe increasingly seek efficient and sustainable manufacturing methods, understanding the intricacies of spin forming becomes crucial. This guide serves as a comprehensive resource, covering various aspects of spin forming, including types of processes, applications across different sectors, supplier vetting strategies, and cost considerations.
The spin forming process is particularly valued for its ability to create complex geometries with minimal waste, making it an attractive option for companies aiming to enhance their production efficiency. With insights into the latest technologies, such as automated spin forming machines and advanced material capabilities, this guide empowers international B2B buyers to make informed purchasing decisions.
By exploring the strengths and applications of spin forming, buyers can better assess suppliers and their offerings, ensuring alignment with their specific needs and industry standards. Whether you are a manufacturer in Italy looking for high-quality aerospace components or a business in Kenya seeking sustainable metal solutions, this guide will equip you with the knowledge to navigate the global market effectively and achieve your manufacturing goals.
Understanding spin forming Types and Variations
Type Name | Key Distinguishing Features | Primary B2B Applications | Brief Pros & Cons for Buyers |
---|---|---|---|
Axis Symmetrical Spin Forming | Involves rotation around a single axis; ideal for uniform shapes. | Aerospace components, automotive parts, and industrial equipment. | Pros: High precision and reduced waste. Cons: Limited to simpler geometries. |
Axis Oval Spin Forming | Utilizes an oval mandrel to create non-circular shapes. | Custom tanks, pressure vessels, and decorative items. | Pros: Versatile for unique shapes. Cons: More complex setup may increase costs. |
Fully-Automated Spin Forming | Incorporates advanced robotics and automation for precision. | High-volume production in aerospace and defense. | Pros: Enhanced efficiency and consistency. Cons: Higher initial investment. |
Hydraulic Spin Forming | Uses hydraulic pressure to shape materials, suitable for thicker metals. | Heavy machinery components and structural parts. | Pros: Handles thicker materials effectively. Cons: Requires more maintenance due to hydraulic systems. |
CNC Spin Forming | Integrates CNC technology for precise control and repeatability. | Custom tooling, prototypes, and small batch runs. | Pros: Offers high precision and flexibility. Cons: Higher operational complexity and cost. |
What Are the Key Characteristics of Axis Symmetrical Spin Forming?
Axis symmetrical spin forming is characterized by its ability to produce components that are uniform and symmetrical around a central axis. This method is particularly suitable for creating cylindrical parts such as aerospace components and automotive parts, where precision and material efficiency are critical. For B2B buyers, the main considerations include the technology’s effectiveness in reducing material waste, which can significantly lower production costs, and its capability to achieve high tolerances, ensuring product quality.
How Does Axis Oval Spin Forming Differ from Other Methods?
Axis oval spin forming stands out by allowing the creation of non-circular geometries, utilizing an oval mandrel. This method is particularly useful for applications requiring custom shapes, such as tanks and decorative metalwork. B2B purchasers should consider the flexibility it offers in design, though they may face higher initial setup costs and longer lead times due to the complexity of the process.
Why Choose Fully-Automated Spin Forming for High-Volume Production?
Fully-automated spin forming employs robotics and advanced control systems to enhance precision and efficiency, making it ideal for high-volume production, especially in aerospace and defense sectors. Buyers should evaluate the trade-off between the higher initial investment and the long-term savings from increased production rates and reduced labor costs. The automation also minimizes human error, ensuring consistent quality across large batches.
What Are the Advantages of Hydraulic Spin Forming?
Hydraulic spin forming utilizes hydraulic pressure to shape thicker materials, making it particularly effective for heavy machinery components and structural parts. Buyers considering this method should weigh its ability to handle robust materials against the potential for increased maintenance needs associated with hydraulic systems. The capacity to form complex shapes while managing thicker materials can justify the investment for industries requiring durable components.
How Does CNC Spin Forming Enhance Precision in Manufacturing?
CNC spin forming integrates computer numerical control technology, allowing for precise shaping and repeatability in the manufacturing process. This method is highly beneficial for custom tooling and prototype development, catering to B2B buyers looking for flexibility and accuracy in small batch runs. While the operational complexity and cost may be higher compared to traditional methods, the benefits of precision and adaptability can be substantial for specialized applications.
Key Industrial Applications of spin forming
Industry/Sector | Specific Application of Spin Forming | Value/Benefit for the Business | Key Sourcing Considerations for this Application |
---|---|---|---|
Aerospace | Manufacturing of missile nose cones | High precision and reduced material waste | Compliance with aerospace standards and certification |
Defense | Production of pressurant tank hemispheres | Enhanced durability and strength | Availability of specialized materials and rapid prototyping |
Automotive | Creation of lightweight structural components | Improved fuel efficiency and performance | Cost-effectiveness and scalability of production |
Energy (Renewable) | Fabrication of wind turbine components | Increased efficiency and longevity | Supplier reliability and technological advancements |
Oil & Gas | Manufacturing of pressure vessels | Safety and compliance with industry regulations | Material certification and lead time for production |
How is Spin Forming Used in Aerospace Applications?
In the aerospace industry, spin forming is crucial for producing complex geometries like missile nose cones and components for aircraft fuselages. This technique allows manufacturers to achieve high precision while minimizing material waste, which is vital for maintaining cost-efficiency in high-stakes projects. International buyers, especially from regions like Europe and the Middle East, must ensure that suppliers adhere to rigorous aerospace standards and certifications to guarantee product reliability and performance.
What are the Benefits of Spin Forming in Defense Manufacturing?
Spin forming plays a significant role in the defense sector, particularly in the production of pressurant tank hemispheres. These components require high strength and durability to withstand extreme conditions. By using spin forming, manufacturers can create these tanks with fewer defects and enhanced structural integrity. Buyers from Africa and South America should focus on sourcing suppliers who offer rapid prototyping capabilities, enabling quicker turnaround times for critical defense projects.
Why is Spin Forming Important for Automotive Parts?
The automotive industry increasingly relies on spin forming for creating lightweight structural components that enhance vehicle performance and fuel efficiency. This manufacturing method allows for the production of complex shapes with consistent material properties, crucial for safety and performance standards. B2B buyers in regions like Italy should prioritize suppliers who can provide scalable solutions to meet varying production demands while ensuring cost-effectiveness.
How Does Spin Forming Enhance Renewable Energy Solutions?
In the renewable energy sector, spin forming is utilized for fabricating components such as wind turbine blades and housings. The precision and material efficiency of spin forming lead to increased performance and longevity of these components, making them more viable for long-term energy solutions. Buyers should consider suppliers with a strong track record in innovative manufacturing techniques to ensure that they receive high-quality products that meet industry standards.
What are the Key Considerations for Oil & Gas Applications?
In the oil and gas industry, spin forming is essential for manufacturing pressure vessels that must meet stringent safety regulations. The ability to create robust and reliable components through this method ensures compliance with industry standards while reducing the risk of failures. International buyers must focus on sourcing materials that are certified for their specific applications, alongside evaluating the lead times for production to align with project timelines.
3 Common User Pain Points for ‘spin forming’ & Their Solutions
Scenario 1: Difficulty in Achieving Precision in Complex Designs
The Problem: B2B buyers often face challenges when working with intricate designs that require high precision in spin forming. For example, manufacturers in the aerospace sector may need components like missile nose cones or complex tank geometries. The intricate nature of these designs can lead to issues such as dimensional inaccuracies, resulting in costly rework and delays in production schedules. Additionally, the selection of inappropriate materials can further complicate the process, leading to performance issues in end-use applications.
The Solution: To address precision challenges, it is crucial to collaborate with experienced spin forming manufacturers who specialize in complex geometries. Buyers should thoroughly communicate their design specifications and tolerances during the initial design consultation phase. Utilizing advanced technologies, such as CNC-controlled spinning lathes, can help achieve tighter tolerances and consistent shapes. Furthermore, implementing a robust prototyping phase can help identify potential design flaws before full-scale production, ultimately saving time and resources. For buyers in regions like Europe or the Middle East, partnering with local manufacturers familiar with regional material properties can enhance the quality and reliability of the final products.
Scenario 2: High Production Costs Due to Inefficient Processes
The Problem: B2B buyers, especially in emerging markets in Africa and South America, often grapple with high production costs linked to inefficient spin forming processes. This inefficiency can stem from outdated machinery, lack of automation, or suboptimal material usage, which can lead to increased scrap rates and prolonged lead times. Such challenges can significantly affect the competitiveness of businesses operating in cost-sensitive industries like automotive and consumer goods.
The Solution: To mitigate high production costs, buyers should consider investing in modern spin forming technologies that offer automation capabilities and higher efficiency. For example, selecting rotary spin forming machines with electric or hydraulic options can reduce maintenance costs and improve operational flexibility. Additionally, engaging in partnerships with manufacturers that provide integrated services—such as heat treatment and machining—can streamline processes and reduce the need for multiple vendors, thereby lowering overall costs. Regularly reviewing and optimizing material usage based on the latest industry practices can also minimize waste and enhance cost-effectiveness.
Scenario 3: Lack of Understanding About Material Selection and Its Impact
The Problem: Many B2B buyers struggle with understanding how different materials affect the spin forming process and the performance of the final products. This lack of knowledge can lead to inappropriate material choices, resulting in issues like poor product performance, increased manufacturing difficulties, and ultimately, customer dissatisfaction. For instance, in the defense sector, using substandard materials for critical components can jeopardize safety and reliability.
The Solution: Buyers must invest time in educating themselves about material properties and their implications for spin forming applications. Engaging with suppliers who offer in-depth guidance on material selection is essential. Buyers should consider hosting workshops or webinars with industry experts to gain insights into which materials are best suited for their specific applications, especially when dealing with high-strength alloys or exotic metals. Furthermore, implementing a collaborative approach with suppliers during the design phase can ensure that material choices align with production capabilities and end-use requirements. This proactive strategy not only enhances product quality but also strengthens supplier relationships, paving the way for future collaborations.
Strategic Material Selection Guide for spin forming
When selecting materials for spin forming, it is essential to consider the specific properties, advantages, and limitations of each material. This decision can significantly impact the performance, cost, and suitability of the final product. Below, we analyze four common materials used in spin forming, providing actionable insights for international B2B buyers.
What Are the Key Properties of Aluminum for Spin Forming?
Aluminum is one of the most widely used materials in spin forming due to its excellent properties. It has a low density, high strength-to-weight ratio, and good corrosion resistance. Aluminum can withstand moderate temperatures, making it suitable for various applications, including automotive and aerospace components.
Pros:
– Lightweight, which is advantageous for applications requiring reduced weight.
– Corrosion-resistant, enhancing the longevity of products exposed to harsh environments.
– Cost-effective for mass production due to its widespread availability.
Cons:
– Lower strength compared to some alloys, which may limit its use in high-stress applications.
– Requires careful handling during the forming process to avoid deformation.
Impact on Application: Aluminum is compatible with various media, including air and water, but may not be suitable for high-pressure applications without reinforcement.
Considerations for International Buyers: Buyers from regions like Africa and South America should ensure compliance with local standards, such as ASTM or ISO, particularly when sourcing aluminum from different suppliers.
How Does Stainless Steel Perform in Spin Forming Applications?
Stainless steel is renowned for its exceptional strength and corrosion resistance, making it ideal for demanding applications, including food processing and chemical industries. Its high-temperature resistance also allows it to perform well in environments where other materials might fail.
Pros:
– Superior durability and resistance to corrosion, suitable for harsh environments.
– Excellent mechanical properties, allowing for complex geometries.
Cons:
– Higher cost compared to aluminum, which can impact budget-sensitive projects.
– More challenging to form, requiring specialized tooling and processes.
Impact on Application: Stainless steel’s compatibility with aggressive media makes it a preferred choice for applications in the chemical and food sectors.
Considerations for International Buyers: Buyers in Europe and the Middle East should be aware of the relevant standards (e.g., EN and ASTM) and certifications required for food-grade stainless steel.
What Are the Advantages of Using Titanium in Spin Forming?
Titanium is a high-performance material known for its outstanding strength, low density, and excellent corrosion resistance. It is often used in aerospace and medical applications due to its biocompatibility and ability to withstand extreme conditions.
Pros:
– Exceptional strength-to-weight ratio, making it ideal for aerospace applications.
– High resistance to corrosion, suitable for marine and chemical environments.
Cons:
– Very high cost, which may not be feasible for all projects.
– More complex machining and forming processes are required.
Impact on Application: Titanium’s properties make it suitable for high-stress applications, but its cost can limit its use to critical components where performance is paramount.
Considerations for International Buyers: Buyers from regions like South America should assess the availability of titanium and consider the implications of sourcing high-cost materials.
What Makes Copper a Viable Option for Spin Forming?
Copper is another material that can be effectively used in spin forming, particularly for applications requiring excellent electrical and thermal conductivity. It is often used in electrical components and heat exchangers.
Pros:
– Excellent conductivity, making it ideal for electrical applications.
– Good malleability, allowing for complex shapes.
Cons:
– Prone to corrosion unless alloyed or treated, which may limit its use in certain environments.
– Heavier than aluminum, which can be a disadvantage in weight-sensitive applications.
Impact on Application: Copper is compatible with various media but may require protective coatings in corrosive environments.
Considerations for International Buyers: Buyers in Africa and Europe should ensure compliance with relevant standards for electrical applications, such as IEC or UL certifications.
Summary Table of Strategic Material Selection for Spin Forming
Material | Typical Use Case for Spin Forming | Key Advantage | Key Disadvantage/Limitation | Relative Cost (Low/Med/High) |
---|---|---|---|---|
Aluminum | Automotive components | Lightweight and cost-effective | Lower strength compared to alloys | Medium |
Stainless Steel | Food processing, chemical industries | Superior durability and corrosion resistance | Higher cost and forming complexity | High |
Titanium | Aerospace, medical applications | Exceptional strength-to-weight ratio | Very high cost and complex processing | High |
Copper | Electrical components, heat exchangers | Excellent conductivity | Prone to corrosion without treatment | Medium |
This strategic material selection guide provides a comprehensive overview for B2B buyers to make informed decisions regarding material choices in spin forming processes, taking into account their specific needs and regional standards.
In-depth Look: Manufacturing Processes and Quality Assurance for spin forming
What Are the Key Stages in the Spin Forming Manufacturing Process?
The spin forming manufacturing process is highly efficient and involves several critical stages: material preparation, forming, assembly, and finishing. Each stage plays a vital role in ensuring that the final product meets the required specifications and quality standards.
Material Preparation: How Is Material Selected and Prepared for Spin Forming?
The first step in the spin forming process is the selection of appropriate materials. Commonly used metals include aluminum, copper, and high-strength alloys due to their excellent formability and strength-to-weight ratios. The material is typically prepared by cutting it into blanks of specific dimensions, which are then subjected to a pre-treatment process, such as heat treatment or surface cleaning, to enhance their properties and ensure a smooth forming process.
Forming: What Techniques Are Employed in Spin Forming?
During the forming stage, the prepared metal blank is mounted on a lathe and spun at high speeds. As it rotates, tools are applied against the material to shape it around a mandrel, which defines the desired geometry. Key techniques include:
- Axis Symmetrical Forming: Ideal for creating cylindrical shapes.
- Axis Oval-Shaped Forming: Used for producing non-cylindrical parts, allowing for more complex geometries.
- CNC Controls: These ensure that the shapes produced are repeatable and consistent, which is crucial for maintaining quality in mass production.
This method is particularly advantageous because it minimizes material waste, making it cost-effective for large production runs.
How Is Quality Assurance Implemented in Spin Forming?
Quality assurance (QA) is critical in the spin forming process to ensure that products meet both international and industry-specific standards. Companies involved in metal spin forming must adhere to rigorous QA protocols throughout the manufacturing process.
What International Standards Should B2B Buyers Look For?
International standards, such as ISO 9001, provide a framework for quality management systems that ensure consistent quality in products and services. Additionally, industry-specific certifications, such as CE marking for compliance with European safety standards or API certifications for the petroleum and natural gas industries, are crucial for verifying that suppliers meet necessary regulations.
What Are the Key Quality Control Checkpoints in Spin Forming?
Quality control (QC) involves several checkpoints throughout the manufacturing process:
- Incoming Quality Control (IQC): Inspection of raw materials and components upon receipt to ensure they meet specified standards.
- In-Process Quality Control (IPQC): Continuous monitoring during the manufacturing process to catch defects early. This may include dimensional checks and visual inspections.
- Final Quality Control (FQC): A comprehensive inspection of the finished product to verify that it meets all specifications before shipment.
What Testing Methods Are Commonly Used in Spin Forming Quality Assurance?
Various testing methods are employed to verify the integrity and performance of spun products, including:
- Dimensional Inspection: Utilizing calipers and gauges to ensure that parts meet specified dimensions.
- Non-Destructive Testing (NDT): Techniques such as ultrasonic testing or dye penetrant testing to detect internal and surface flaws without damaging the product.
- Mechanical Testing: Evaluating properties like tensile strength and hardness to ensure that the material will perform as expected in its intended application.
How Can B2B Buyers Verify Supplier Quality Control?
For international B2B buyers, particularly those from Africa, South America, the Middle East, and Europe, verifying supplier QC is crucial to ensure product reliability.
What Are the Best Practices for Conducting Supplier Audits?
Conducting regular audits of suppliers can help B2B buyers confirm compliance with quality standards. Key steps include:
- On-Site Audits: Visiting the manufacturing facility to evaluate processes, equipment, and staff training.
- Reviewing QC Documentation: Requesting access to quality control reports, certifications, and past audit findings.
- Third-Party Inspections: Engaging independent inspection services to provide unbiased assessments of supplier capabilities and product quality.
What Are the Quality Control Nuances for International B2B Buyers?
International B2B buyers must navigate various challenges when ensuring quality control in spin forming. These include:
- Cultural Differences: Understanding the local business practices and quality standards in different regions, such as the emphasis on certifications in Europe versus more informal practices in some African countries.
- Supply Chain Management: Ensuring that logistics and transportation do not compromise product quality during shipment.
- Communication Barriers: Establishing clear lines of communication with suppliers to address quality issues promptly.
Conclusion: Ensuring High-Quality Spin Forming Products
In summary, a thorough understanding of the spin forming manufacturing process and rigorous quality assurance practices is essential for B2B buyers. By focusing on material preparation, employing advanced forming techniques, and adhering to international quality standards, suppliers can deliver high-quality products. Buyers can protect their investments by conducting due diligence through audits, reviewing documentation, and utilizing third-party inspections. This proactive approach ensures that the products they source meet their expectations for quality, reliability, and performance.
Practical Sourcing Guide: A Step-by-Step Checklist for ‘spin forming’
To assist international B2B buyers in effectively sourcing spin forming services, this checklist outlines essential steps to ensure a successful procurement process. By following these guidelines, companies can secure high-quality spin forming solutions tailored to their specific needs.
Step 1: Define Your Technical Specifications
Understanding your project requirements is the foundation of successful sourcing. Clearly outline the dimensions, materials, and tolerances required for your spin-formed products. This will not only help potential suppliers provide accurate quotes but also ensure that the final products meet your operational needs.
- Key Considerations:
- Specify the type of metal (e.g., aluminum, steel) and thickness.
- Identify the desired shapes and geometries, including axis symmetrical or oval shapes.
Step 2: Research Potential Suppliers
Conduct thorough research to identify suppliers who specialize in spin forming. Look for companies with a proven track record in your industry and region, as they will be more familiar with the specific challenges and requirements you may face.
- What to Look For:
- Supplier experience in producing similar components.
- Reputation and reviews from previous clients, especially in Africa, South America, the Middle East, and Europe.
Step 3: Evaluate Supplier Certifications and Compliance
Ensuring that your suppliers meet industry standards is crucial for maintaining quality and safety. Verify any relevant certifications, such as ISO 9001, which indicate a commitment to quality management processes.
- Why This Matters:
- Certifications can provide confidence in the supplier’s capabilities.
- Compliance with regional regulations is essential, particularly in highly regulated industries like aerospace and defense.
Step 4: Request Detailed Proposals
Once you have shortlisted potential suppliers, request detailed proposals. This should include pricing, lead times, production capabilities, and any additional services such as secondary machining or heat treatment.
- What to Assess:
- Compare costs against the quality of services offered.
- Ensure that lead times align with your project schedule.
Step 5: Conduct Site Visits or Virtual Tours
If feasible, visiting the supplier’s facility can provide valuable insights into their operations. For international buyers, virtual tours can also serve as an effective alternative.
- Benefits of Site Visits:
- Observe equipment and technology in use, such as CNC controls and automated systems.
- Assess the working environment and safety protocols.
Step 6: Establish Communication Channels
Effective communication is key to a successful partnership. Ensure that the supplier is responsive and willing to engage in regular updates throughout the production process.
- Communication Strategies:
- Set up regular check-ins to monitor progress and address any issues.
- Utilize project management tools to facilitate collaboration.
Step 7: Finalize Contracts and Payment Terms
Before commencing production, ensure that all agreements are documented in a formal contract. This should outline payment terms, delivery schedules, and quality assurance measures.
- Important Contract Elements:
- Define penalties for late deliveries or quality failures.
- Include clauses for confidentiality and intellectual property protection if applicable.
By following this step-by-step sourcing guide, B2B buyers can streamline their procurement process for spin forming services, ensuring they select the right supplier to meet their technical requirements and business objectives.
Comprehensive Cost and Pricing Analysis for spin forming Sourcing
What Are the Key Cost Components in Spin Forming?
Understanding the cost structure of spin forming is essential for international B2B buyers aiming to optimize their sourcing strategies. The primary cost components include:
-
Materials: The choice of material significantly impacts cost. Commonly used metals in spin forming, such as aluminum, steel, and specialized alloys, vary in price based on market demand and availability. For instance, sourcing high-strength alloys for aerospace applications may incur higher costs compared to standard aluminum.
-
Labor: Labor costs can fluctuate based on geographic location and the skill level required. In regions such as Africa and South America, labor may be less expensive, but the expertise in advanced spin forming techniques could be limited. In contrast, European suppliers often have a higher labor cost but may provide superior craftsmanship.
-
Manufacturing Overhead: This encompasses the operational costs of running the manufacturing facility, including utilities, maintenance, and equipment depreciation. Efficient production processes, such as automated spin forming systems, can help reduce overhead costs.
-
Tooling: Custom tooling is often necessary for spin forming specific geometries. The cost of tooling can be substantial, especially for complex designs. Buyers should consider how tooling costs are amortized over production volume.
-
Quality Control (QC): Ensuring product quality through rigorous QC processes adds to costs but is crucial for compliance, particularly in industries like aerospace and defense. Certifications (e.g., ISO) can influence QC costs and pricing.
-
Logistics: Shipping costs, including packaging and handling, can vary widely depending on the destination and Incoterms used. Buyers should factor in these costs when evaluating total pricing.
-
Margin: Suppliers typically include a profit margin that varies based on market conditions, competition, and the perceived value of their offering.
How Do Price Influencers Affect Spin Forming Costs?
Several factors can influence pricing in spin forming, including:
-
Volume/MOQ: Larger orders generally lead to lower per-unit costs due to economies of scale. Buyers should negotiate minimum order quantities (MOQs) to maximize cost efficiency.
-
Specifications and Customization: Custom designs may incur additional costs. Clear communication of specifications can help prevent misunderstandings that lead to costly revisions.
-
Material Quality and Certifications: Higher quality materials and certifications can drive up costs but may be necessary for compliance in regulated industries. Buyers should weigh the benefits of premium materials against their budget constraints.
-
Supplier Factors: The reputation and reliability of suppliers can impact pricing. Established suppliers with proven track records may charge more but offer better support and quality assurance.
-
Incoterms: The choice of Incoterms affects the distribution of responsibilities and costs between the buyer and supplier. Understanding these terms is crucial for accurate pricing.
What Are the Best Buyer Tips for Negotiating Spin Forming Prices?
International B2B buyers can employ several strategies to negotiate better pricing in spin forming:
-
Conduct Thorough Market Research: Understanding the current market landscape can empower buyers during negotiations. Gathering quotes from multiple suppliers can provide leverage.
-
Evaluate Total Cost of Ownership (TCO): Rather than focusing solely on upfront costs, consider the TCO, which includes maintenance, logistics, and potential downtime. This holistic view can lead to better decision-making.
-
Leverage Relationships: Building strong relationships with suppliers can lead to better pricing and terms. Regular communication and trust can facilitate negotiations.
-
Seek Long-Term Agreements: Committing to long-term contracts can often yield discounts. Suppliers value stability and may be willing to offer lower prices for guaranteed business.
-
Be Open to Alternative Materials: If budgets are tight, consider alternative materials that may offer similar performance at a lower cost. Discussing material flexibility with suppliers can uncover cost-saving opportunities.
Conclusion
Navigating the complexities of spin forming costs requires a strategic approach. By understanding the cost components, recognizing price influencers, and applying effective negotiation strategies, international B2B buyers can make informed decisions that enhance their sourcing success. While indicative prices can fluctuate based on market conditions, thorough research and a collaborative approach with suppliers can lead to mutually beneficial outcomes.
Alternatives Analysis: Comparing spin forming With Other Solutions
Introduction: Why Explore Alternatives to Spin Forming?
In the ever-evolving landscape of manufacturing, particularly within the B2B sector, it’s crucial for buyers to understand the various methods available for metal forming. While spin forming offers unique advantages, such as reduced material waste and the ability to create complex shapes, other technologies may also meet specific needs effectively. This section explores viable alternatives to spin forming, providing a comparative analysis that can assist international B2B buyers in making informed decisions.
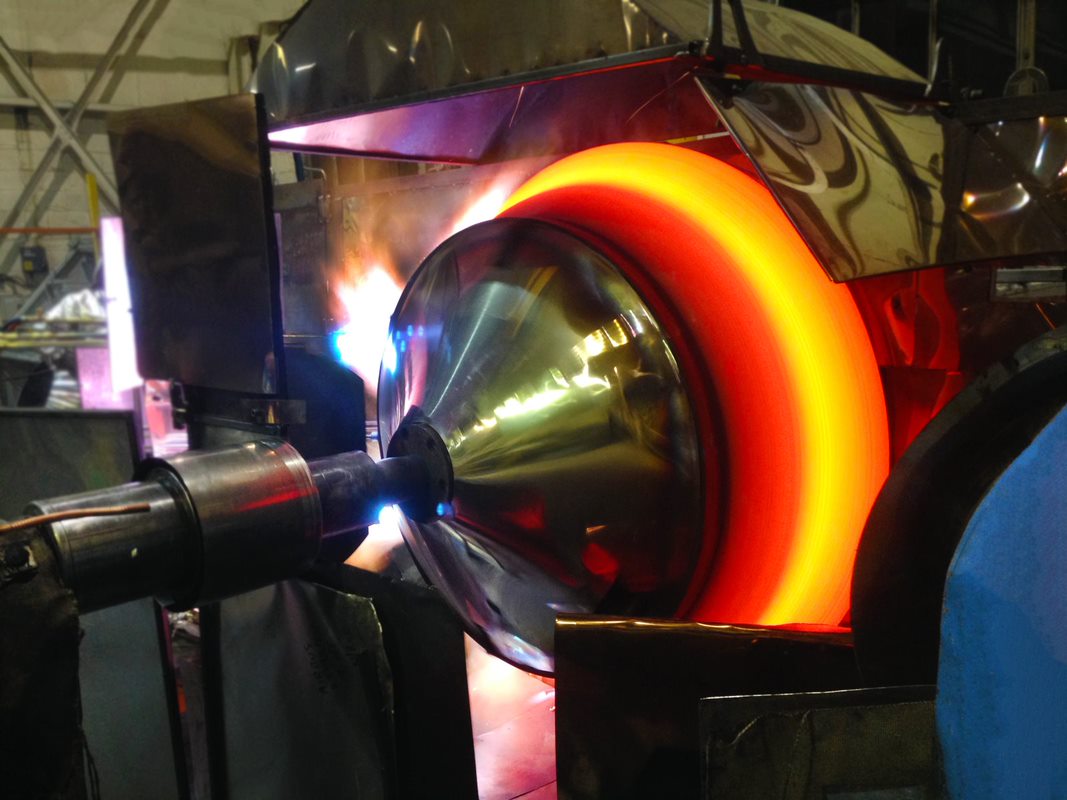
A stock image related to spin forming.
Comparison Table: Spin Forming vs. Alternative Methods
Comparison Aspect | Spin Forming | Hydroforming | Roll Forming |
---|---|---|---|
Performance | High precision and complex geometries | Excellent for thin-walled shapes | Ideal for continuous profiles |
Cost | Moderate initial investment | Higher due to equipment complexity | Lower due to continuous production |
Ease of Implementation | Requires skilled operators | Complex setup and training needed | Easier setup with less skilled labor |
Maintenance | Moderate; depends on tooling | High; requires regular checks | Low; fewer moving parts |
Best Use Case | Aerospace and defense applications | Automotive and pressure vessels | Construction and structural components |
In-Depth Analysis of Alternatives
Hydroforming: What Are Its Advantages and Disadvantages?
Hydroforming utilizes high-pressure fluid to shape materials, making it an effective method for creating complex, hollow parts with thin walls. This technique excels in automotive applications, where lightweight components are crucial. However, the cost of equipment and the need for specialized training can be prohibitive for some manufacturers. Additionally, the complexity of setup and potential for longer lead times may deter buyers looking for quick turnaround solutions.
Roll Forming: How Does It Compare to Spin Forming?
Roll forming is a continuous bending process that shapes metal sheets into uniform profiles. This method is particularly advantageous for high-volume production runs, offering lower per-unit costs due to its efficiency. However, roll forming is limited to simpler, uniform shapes and may not achieve the intricate designs possible with spin forming. Moreover, while the setup is relatively straightforward, the initial investment in machinery can still be significant.
Conclusion: Choosing the Right Solution for Your Needs
When evaluating spin forming and its alternatives, B2B buyers must consider their specific requirements, including production volume, complexity of designs, and budget constraints. Spin forming shines in applications requiring high precision and complex geometries, making it ideal for industries like aerospace and defense. In contrast, hydroforming is suitable for lightweight automotive components, while roll forming is best for continuous production of simpler shapes. By weighing these factors, buyers from regions such as Africa, South America, the Middle East, and Europe can make a well-informed decision that aligns with their operational goals and financial capabilities.
Essential Technical Properties and Trade Terminology for spin forming
What Are the Essential Technical Properties of Spin Forming?
Understanding the technical properties of spin forming is crucial for international B2B buyers. Here are some key specifications that influence production quality and cost-effectiveness:
1. Material Grade
Material grade refers to the specific type of metal used in the spin forming process, such as aluminum, steel, or titanium alloys. Each material has unique properties affecting its strength, ductility, and formability. Selecting the appropriate material grade is vital for ensuring that the final product meets performance standards and application requirements, particularly in sectors like aerospace and automotive.
2. Tolerance
Tolerance defines the allowable deviation from specified dimensions in the finished product. In spin forming, maintaining tight tolerances is critical, as it directly impacts the functionality of the component. B2B buyers must ensure that their suppliers can meet stringent tolerance requirements, especially for high-precision applications in industries like defense or medical equipment.
3. Wall Thickness
The wall thickness of the formed component can vary significantly based on the design and material used. This specification affects both the weight and strength of the final product. Buyers should consider how wall thickness influences performance and cost, as thicker materials may require more energy to spin and thus increase production costs.
4. Surface Finish
Surface finish pertains to the texture and quality of the surface of the formed part. A smooth surface finish can be crucial for components that require aesthetic appeal or reduced friction. Buyers should communicate their surface finish requirements clearly, as this will impact machining processes and overall production timelines.
5. Maximum Diameter and Length
The maximum diameter and length that can be achieved in spin forming are determined by the equipment capabilities. For instance, some lathes can form parts up to 16 inches in diameter or 262 inches in length. Buyers need to match their project specifications with the capabilities of their suppliers to avoid production delays and ensure feasibility.
Which Trade Terms Are Important for Spin Forming?
Familiarity with industry jargon can streamline negotiations and improve communication between buyers and suppliers. Here are some essential trade terms:
1. OEM (Original Equipment Manufacturer)
An OEM refers to a company that produces parts or equipment that may be marketed by another company. In the context of spin forming, buyers often deal with OEMs that supply components for larger assemblies. Understanding OEM relationships can help buyers navigate supply chains effectively.
2. MOQ (Minimum Order Quantity)
MOQ is the smallest quantity of a product that a supplier is willing to sell. This term is critical for buyers to understand, as it can affect inventory levels and cash flow. Knowing the MOQ helps in planning orders to ensure that production needs are met without overcommitting resources.
3. RFQ (Request for Quotation)
An RFQ is a document used by buyers to solicit price quotes from suppliers for specific products or services. For spin forming projects, an RFQ should detail specifications such as material grade, dimensions, and tolerances. A well-prepared RFQ can lead to better pricing and more accurate quotes.
4. Incoterms (International Commercial Terms)
Incoterms are standardized trade terms that define the responsibilities of buyers and sellers in international transactions. Understanding these terms is essential for managing logistics, costs, and risks associated with shipping products. Familiarity with Incoterms helps buyers clarify who is responsible for transportation, insurance, and customs duties.
5. Lead Time
Lead time refers to the time taken from placing an order to delivery of the product. For spin forming, lead times can vary based on material availability and production schedules. Buyers must account for lead times in their project planning to ensure timely delivery and avoid disruptions.
By grasping these essential properties and trade terms, international B2B buyers can make informed decisions when engaging with suppliers in the spin forming industry.
Navigating Market Dynamics and Sourcing Trends in the spin forming Sector
What Are the Current Market Dynamics and Key Trends in the Spin Forming Sector?
The global spin forming market is experiencing a robust transformation driven by advancements in technology and increasing demand for custom components across various industries, including aerospace, automotive, and defense. One significant trend is the rise of automation in spin forming processes. Fully-automated machines are enhancing precision, efficiency, and production speed, making them particularly appealing to international B2B buyers looking to streamline operations and reduce lead times. Companies such as Karman Space & Defense are pioneering these advancements, which allow for complex geometries and high-strength materials to be processed more reliably.
Another important factor is the growing emphasis on sustainability and resource efficiency. Spin forming, known for its minimal waste generation during production, aligns well with the increasing pressure on manufacturers to adopt greener practices. This trend is especially relevant in regions like Europe and South America, where regulatory frameworks are pushing businesses toward sustainable manufacturing methods. Moreover, with the advent of Industry 4.0, integrating IoT and data analytics into spin forming processes is becoming common, enabling real-time monitoring and predictive maintenance, thus enhancing operational efficiency.
For international B2B buyers, understanding regional market dynamics is crucial. In Africa, for example, the demand for localized manufacturing capabilities is increasing, driven by the need for job creation and skill development. Similarly, Middle Eastern markets are focusing on diversifying their economies, which opens up new avenues for sourcing spin formed components. European buyers are increasingly looking for suppliers that can provide high-quality, customizable solutions with a focus on sustainability.
How Can Sustainability and Ethical Sourcing Impact the Spin Forming Sector?
Sustainability is becoming a central concern in the spin forming sector, with environmental impacts influencing sourcing decisions among international B2B buyers. The production processes associated with spin forming are generally more resource-efficient than traditional methods, significantly reducing waste. However, buyers must also consider the sourcing of raw materials and the overall carbon footprint of their supply chains. This has led to an increased demand for suppliers who can demonstrate sustainable practices and transparency in their operations.
Ethical sourcing is not only about environmental responsibility but also encompasses social factors such as labor practices and community impact. Buyers are increasingly looking for suppliers who adhere to ethical standards, including fair labor practices and community engagement. Certifications such as ISO 14001 for environmental management and ISO 45001 for occupational health and safety are becoming critical in evaluating potential partners in the spin forming supply chain.
The use of green materials, such as recycled metals and eco-friendly coatings, is another trend gaining traction. B2B buyers from Europe and South America are particularly focused on incorporating such materials into their supply chains to comply with stringent environmental regulations. By prioritizing suppliers who offer sustainable products and processes, companies can enhance their brand reputation and align with the values of their customers, ultimately driving business growth.
What Is the Brief Evolution of Spin Forming in the B2B Context?
The evolution of spin forming can be traced back to ancient metalworking techniques, but its modern incarnation began in the mid-20th century with advancements in machinery and technology. Initially used primarily for creating simple shapes, the process has significantly evolved to accommodate complex geometries and high-performance materials, thanks to innovations in CNC controls and automation.
As industries began to demand higher precision and efficiency, spin forming emerged as a preferred method for producing components in sectors such as aerospace and automotive. The ability to create near-net shapes with minimal waste has positioned spin forming as a viable alternative to traditional manufacturing methods.
In recent years, the integration of advanced technologies such as robotics, IoT, and AI has further transformed the landscape, enabling manufacturers to optimize processes, reduce costs, and improve product quality. This ongoing evolution highlights the importance for B2B buyers to stay informed about technological advancements and market trends, ensuring they can make strategic sourcing decisions that align with their operational goals and sustainability commitments.
Frequently Asked Questions (FAQs) for B2B Buyers of spin forming
-
How do I solve issues related to lead times in spin forming?
To address lead time challenges, it is essential to establish clear communication with your spin forming supplier. Discuss your project timelines upfront and inquire about their production capacity and current workload. Opt for suppliers that employ advanced technologies, such as automated spin forming machines, which can significantly reduce production times. Additionally, consider building a strong relationship with your supplier for better prioritization of your orders. Lastly, plan for potential delays by incorporating buffer times into your project schedule to ensure timely delivery. -
What is the best material for spin forming applications?
The best material for spin forming largely depends on the specific application and desired properties. Commonly used materials include aluminum, copper, and various alloys, which offer excellent formability and strength. For applications requiring high durability, consider high-strength alloys or exotic metals. Always consult with your supplier about material options, as they can provide insights based on their capabilities and the intended use of the final product. Remember to consider factors such as cost, weight, and resistance to environmental conditions when making your choice. -
How do I vet potential spin forming suppliers?
Vetting suppliers involves several steps to ensure reliability and quality. Start by researching their industry reputation and customer reviews. Request case studies or references from previous clients to gauge their experience with similar projects. Evaluate their production capabilities, including technology used and quality control processes. Additionally, visit their facilities if possible, or conduct virtual meetings to assess their operations. Finally, ensure that they comply with international standards and certifications relevant to your industry, which will provide confidence in their commitment to quality. -
What customization options are typically available in spin forming?
Spin forming offers a high degree of customization, allowing buyers to specify dimensions, shapes, and material types based on their needs. Suppliers can work with you during the design phase to create parts that meet unique specifications, including complex geometries. Many suppliers also offer secondary operations, such as machining and finishing, which can further tailor the product to your requirements. It’s advisable to engage in early discussions about customization to align your expectations with the supplier’s capabilities. -
What are the minimum order quantities (MOQs) for spin forming services?
Minimum order quantities can vary significantly among spin forming suppliers, often influenced by factors such as material type, complexity of the part, and production processes. Generally, suppliers may set MOQs to justify setup costs and ensure economic feasibility. It’s beneficial to discuss your project needs openly with potential suppliers to understand their MOQ policies. Some suppliers may offer flexibility for first-time orders or prototypes, which can be advantageous for buyers looking to test a new product before committing to larger quantities. -
What payment terms should I expect when sourcing spin forming services?
Payment terms for spin forming services can vary widely depending on the supplier’s policies and the buyer’s relationship with them. Typically, terms may include upfront deposits, milestone payments during production, or full payment upon delivery. International buyers should also consider currency fluctuations and potential transaction fees. It’s crucial to negotiate clear terms that protect both parties’ interests while facilitating smooth transactions. Always ensure that these terms are documented in the contract to avoid any misunderstandings later on.
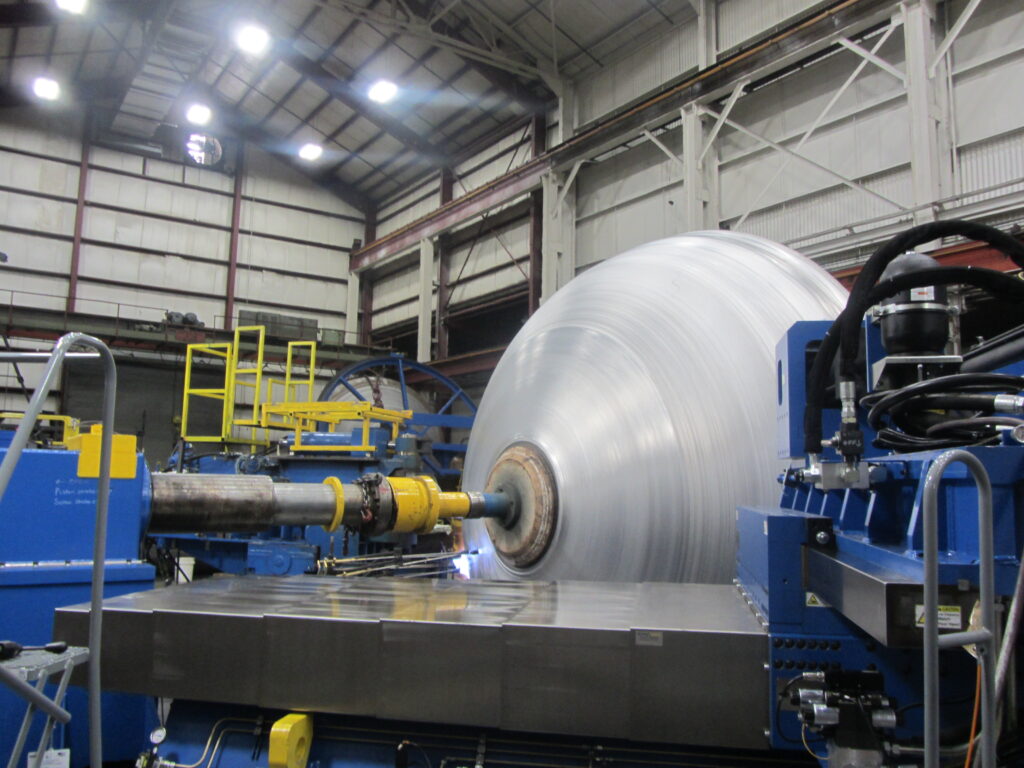
A stock image related to spin forming.
-
How can I ensure quality assurance in spin forming products?
To ensure quality assurance in spin forming products, it’s vital to choose suppliers that implement stringent quality control measures. Inquire about their certification processes, such as ISO 9001, which indicates adherence to quality management systems. Discuss specific inspection methods they employ, such as dimensional checks and material testing, to confirm that products meet required specifications. Establishing a clear communication channel for quality feedback throughout the production process will also help address any issues proactively. -
What logistical considerations should I keep in mind when sourcing spin forming products internationally?
When sourcing spin forming products internationally, consider logistics factors such as shipping costs, customs regulations, and delivery times. Engage with suppliers to understand their shipping processes and the expected timelines for order fulfillment. Additionally, familiarize yourself with import/export regulations in your country and the supplier’s location to avoid unexpected delays. It may also be beneficial to work with logistics providers that specialize in international trade, ensuring that you navigate the complexities of cross-border shipping efficiently.
Important Disclaimer & Terms of Use
⚠️ Important Disclaimer
The information provided in this guide, including content regarding manufacturers, technical specifications, and market analysis, is for informational and educational purposes only. It does not constitute professional procurement advice, financial advice, or legal advice.
While we have made every effort to ensure the accuracy and timeliness of the information, we are not responsible for any errors, omissions, or outdated information. Market conditions, company details, and technical standards are subject to change.
B2B buyers must conduct their own independent and thorough due diligence before making any purchasing decisions. This includes contacting suppliers directly, verifying certifications, requesting samples, and seeking professional consultation. The risk of relying on any information in this guide is borne solely by the reader.
Strategic Sourcing Conclusion and Outlook for spin forming
How Can Strategic Sourcing Enhance Your Spin Forming Operations?
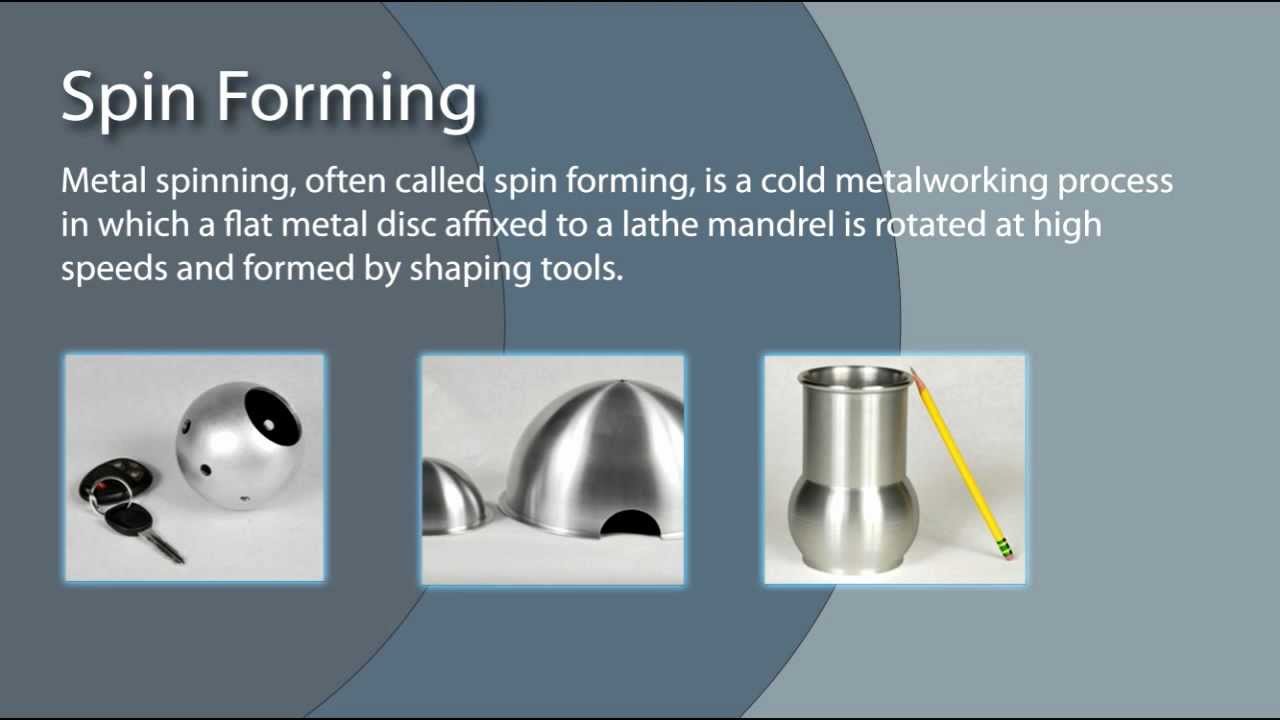
A stock image related to spin forming.
In conclusion, strategic sourcing is essential for optimizing spin forming operations in today’s competitive landscape. By partnering with suppliers who offer advanced metal spinning technologies, international B2B buyers can achieve significant cost savings, improved quality, and reduced lead times. The ability to form complex geometries with minimal waste not only enhances production efficiency but also supports sustainability goals.
Buyers from regions such as Africa, South America, the Middle East, and Europe, particularly countries like Italy and Kenya, should prioritize suppliers that provide vertically integrated processes—such as heat treatment and machining—alongside spin forming. This integrated approach streamlines manufacturing and allows for greater flexibility in meeting specific project requirements.
Looking ahead, the advancements in automation and material capabilities in spin forming will play a crucial role in meeting the demands of diverse industries, from aerospace to automotive. Engaging with innovative suppliers now will position your business for future growth and adaptability. Take action today by exploring partnerships that can elevate your manufacturing capabilities and drive competitive advantage in your market.