Discover Cost-Saving Strategies for Aircraft Cables (2025)
Introduction: Navigating the Global Market for aircraft cables
In the rapidly evolving aviation industry, sourcing high-quality aircraft cables presents a significant challenge for international B2B buyers. From ensuring safety and compliance with stringent regulations to navigating diverse supplier landscapes, the procurement process can be daunting. This comprehensive guide addresses the complexities of selecting the right aircraft cables, covering a wide array of topics such as types of cables, their applications in critical systems like flight controls and landing gear, and the nuances of supplier vetting.
Understanding the various specifications and materials used in aircraft cables—such as stainless steel, galvanized steel, and specialty alloys—is crucial for making informed purchasing decisions. This guide empowers B2B buyers, particularly from regions such as Africa, South America, the Middle East, and Europe (including key markets like Poland and Egypt), to navigate the global market with confidence. By providing actionable insights into cost considerations, quality standards, and supplier certifications, we aim to streamline the sourcing process.
Whether you’re seeking to enhance your supply chain reliability or ensure compliance with military specifications, this guide serves as a valuable resource to equip you with the knowledge necessary to make strategic procurement choices. Dive into our detailed analysis to discover how to effectively meet your aircraft cable needs while optimizing performance and safety standards in your operations.
Understanding aircraft cables Types and Variations
Type Name | Key Distinguishing Features | Primary B2B Applications | Brief Pros & Cons for Buyers |
---|---|---|---|
General Purpose Aircraft Cable | Commonly made from stainless or galvanized steel; available in 7×7 and 7×19 constructions. | Used in various applications including rigging and support systems. | Pros: Versatile and widely available. Cons: May not suit specialized needs. |
Rotation-Resistant Wire Rope | Designed to minimize twisting; typically larger diameter than standard cables. | Ideal for lifting and hoisting applications in aviation. | Pros: Enhanced stability under load. Cons: Heavier and more expensive than standard cables. |
Swaged & Compacted Wire Rope | Features tightly packed strands for improved strength; often used in critical applications. | Suitable for flight control systems and landing gear. | Pros: High strength-to-weight ratio. Cons: More complex installation process. |
Miniature Aircraft Cable | Small diameter cables suitable for tight spaces; often used in medical devices. | Applications in aerospace and medical equipment. | Pros: Excellent for precision applications. Cons: Limited load capacity. |
Specialty Alloy Cable | Made from unique materials like Monel or Tin Over Zinc for added corrosion resistance. | Used in harsh environments such as marine or chemical applications. | Pros: Superior durability in corrosive environments. Cons: Higher cost and specific sourcing requirements. |
What Are the Key Characteristics of General Purpose Aircraft Cable?
General Purpose Aircraft Cables are typically constructed from stainless steel or galvanized steel and are available in common configurations like 7×7 and 7×19. These cables serve a broad range of applications, including rigging, support systems, and general lifting tasks. B2B buyers should consider their specific application needs, as while these cables are versatile and widely available, they may not meet the requirements of more specialized tasks.
How Does Rotation-Resistant Wire Rope Enhance Performance?
Rotation-Resistant Wire Rope is engineered to minimize twisting and is usually found in larger diameters than standard cables. This type of wire rope is especially beneficial in lifting and hoisting applications within aviation, where stability under load is crucial. B2B buyers should weigh the benefits of enhanced stability against the potential drawbacks, such as increased weight and cost compared to standard cables.
Why Choose Swaged & Compacted Wire Rope for Critical Applications?
Swaged & Compacted Wire Rope features tightly packed strands that enhance strength and reduce the risk of failure. This type of cable is often used in critical applications, including flight control systems and landing gear. While it offers a high strength-to-weight ratio, buyers must be aware that the installation process can be more complex, requiring specialized knowledge and tools.
What Are the Applications of Miniature Aircraft Cable?
Miniature Aircraft Cables are designed for small diameter applications, making them ideal for use in tight spaces, such as in medical devices or aerospace components. While they excel in precision tasks, their load capacity is limited, which is a key consideration for B2B buyers. Understanding the specific load requirements of their applications is essential when selecting this type of cable.
How Do Specialty Alloy Cables Provide Added Value?
Specialty Alloy Cables, such as those made from Monel or Tin Over Zinc, offer enhanced corrosion resistance, making them suitable for harsh environments like marine or chemical applications. These cables are ideal for B2B buyers looking for durability in challenging conditions. However, they typically come at a higher cost and may require specific sourcing strategies, which should be factored into purchasing decisions.
Key Industrial Applications of aircraft cables
Industry/Sector | Specific Application of aircraft cables | Value/Benefit for the Business | Key Sourcing Considerations for this Application |
---|---|---|---|
Aerospace | Flight control systems (e.g., rudders, ailerons) | Ensures precise control and safety in aircraft operation | Compliance with MIL-SPEC standards and certifications |
Aviation Maintenance | Landing gear actuation systems | Enhances reliability and performance during takeoff and landing | Material durability (stainless vs. galvanized) and tensile strength |
Industrial Equipment | Hoisting and rigging applications | Provides strong support and safety for heavy lifting operations | Load ratings and corrosion resistance based on environment |
Marine Applications | Cable systems for deep-sea exploration equipment | Supports critical operations in challenging underwater conditions | Resistance to corrosion and fatigue under extreme conditions |
Telecommunications | Support structures for aerial communication cables | Facilitates stable and efficient communication infrastructure | Weight capacity and flexibility for installation requirements |
What Are the Key Applications of Aircraft Cables in the Aerospace Sector?
In the aerospace industry, aircraft cables are vital for flight control systems, such as rudders and ailerons. These cables ensure precise maneuverability and safety, which are paramount in aviation. Buyers must ensure that the cables comply with strict military specifications (MIL-SPEC) to guarantee performance under extreme conditions. Additionally, sourcing cables with high tensile strength and durability is crucial to prevent wear and tear over time, particularly in regions with diverse climates, like Africa and the Middle East.
How Are Aircraft Cables Used in Aviation Maintenance?
Aircraft cables play a crucial role in landing gear actuation systems. They facilitate the extension and retraction of landing gear, which is essential for safe takeoffs and landings. For B2B buyers, it is important to select cables made from materials that provide long-lasting performance, such as stainless steel for corrosion resistance or galvanized options for cost-effectiveness. The ability to withstand repeated stress and environmental factors is critical, especially in regions with high humidity or salt exposure, such as coastal areas in South America.
What Are the Industrial Applications of Aircraft Cables?
In industrial equipment, aircraft cables are extensively used for hoisting and rigging applications. They provide robust support for heavy lifting operations, ensuring safety and efficiency. Buyers should focus on load ratings and the cables’ resistance to corrosion, particularly in industries that operate in harsh environments. For instance, companies in Africa and Europe need to consider the cables’ performance under varying temperatures and humidity levels to maintain operational safety.
How Are Aircraft Cables Essential for Marine Applications?
Marine applications, particularly in deep-sea exploration, rely heavily on aircraft cables for their cable systems. These cables must withstand extreme underwater conditions, including high pressure and potential corrosion from saltwater. For buyers in the Middle East and South America, sourcing cables that offer superior resistance to fatigue and corrosion is essential for the longevity of their marine equipment. The choice between materials like stainless steel or specialized alloys can significantly impact operational efficiency and safety.
What Role Do Aircraft Cables Play in Telecommunications?
In telecommunications, aircraft cables are utilized for support structures in aerial communication systems. They provide the necessary strength and stability to ensure efficient communication infrastructure. B2B buyers should prioritize sourcing cables that meet specific weight capacities and flexibility requirements for installation. This is particularly relevant for regions in Europe, where regulatory standards for telecommunications infrastructure can be stringent, necessitating reliable and durable cable solutions.
3 Common User Pain Points for ‘aircraft cables’ & Their Solutions
Scenario 1: Challenges with Cable Specifications and Sourcing
The Problem: International B2B buyers often encounter difficulties when trying to specify and source the correct aircraft cables for their unique applications. Variations in construction, material, and strength ratings can lead to confusion, especially when dealing with multiple suppliers across different regions. For instance, a buyer in Egypt might struggle to understand the differences between 7×7 and 7×19 constructions, which can significantly impact the performance and safety of the aircraft. This uncertainty can lead to costly delays, project overruns, and potential safety risks if the wrong cable is used.
The Solution: To mitigate these issues, it is essential to establish clear specifications before initiating the purchasing process. Start by determining the specific load requirements, environmental conditions, and regulatory standards applicable to your project. Utilize a detailed checklist that includes the cable diameter, construction type, material (such as stainless steel or galvanized steel), and any industry-specific certifications (like MIL-SPEC). Engage with reputable suppliers who can provide technical datasheets and consultative support. For example, when contacting a supplier in Europe, ensure they can demonstrate compliance with European aviation standards. This proactive approach will not only streamline sourcing but also enhance overall project safety and efficiency.
Scenario 2: Maintenance and Longevity Concerns
The Problem: A common pain point for B2B buyers is the maintenance and longevity of aircraft cables. Many buyers, particularly in regions with harsh climates like South America and the Middle East, face challenges related to corrosion and wear over time. This can result in unexpected failures, leading to operational downtimes and increased maintenance costs. For example, a buyer may find that cables installed in a coastal area are corroding faster than anticipated, affecting the reliability of critical aircraft systems.
The Solution: To combat these issues, it is vital to select the right cable materials and implement a robust maintenance schedule. Opt for cables that offer enhanced corrosion resistance, such as those made from 316 stainless steel or specially coated options. Regular inspections should be scheduled to check for signs of wear, corrosion, or fraying. Establish a maintenance log that tracks the condition of cables over time, allowing for predictive maintenance before failures occur. Additionally, consider investing in wire rope lubricants to reduce friction and wear, especially in high-load applications. By adopting these practices, buyers can significantly extend the lifespan of their aircraft cables and reduce the likelihood of costly repairs.
Scenario 3: Understanding Load Ratings and Safety Compliance
The Problem: Buyers often struggle to understand load ratings and safety compliance requirements for aircraft cables, which is critical for ensuring the safety of flight operations. Misunderstanding these specifications can lead to the use of cables that do not meet the necessary strength requirements, posing serious risks during operation. For instance, a buyer in Poland may not fully grasp how to interpret the break strength of cables in relation to their specific application, resulting in potential safety hazards.
The Solution: To address this challenge, it is essential to educate yourself and your team on the critical aspects of load ratings and safety standards. Familiarize yourself with industry terminologies such as Working Load Limit (WLL) and Minimum Breaking Strength (MBS). Consult with experienced suppliers who can provide guidance and clarification on these terms. Additionally, utilize resources such as technical handbooks or online training courses focused on aircraft cable specifications and safety compliance. Implementing a checklist that includes verifying load ratings against specific application requirements will help ensure that the selected cables are suitable for their intended use. By prioritizing education and due diligence, buyers can confidently make informed decisions that enhance safety and compliance in their operations.
Strategic Material Selection Guide for aircraft cables
What are the Key Properties of Stainless Steel Aircraft Cables?
Stainless steel is a popular choice for aircraft cables due to its excellent mechanical properties and corrosion resistance. Typically made from alloys like 302, 304, or 316, these cables can withstand extreme temperatures and pressures, making them suitable for various aerospace applications. The corrosion resistance of stainless steel is particularly beneficial in environments where moisture and salt exposure are prevalent, such as coastal regions or humid climates.
Pros and Cons of Stainless Steel Cables
The primary advantage of stainless steel cables is their durability, which ensures a long service life even in challenging conditions. However, they can be more expensive than other materials, which may be a consideration for budget-sensitive projects. Manufacturing complexity can also be higher due to the need for specialized equipment to handle stainless steel.
Impact on Application
Stainless steel cables are ideal for critical applications such as flight control systems and landing gear mechanisms, where reliability is paramount. Their compatibility with various media, including hydraulic fluids, enhances their versatility in aircraft systems.
How Does Galvanized Steel Compare for Aircraft Cables?
Galvanized steel is another common material used in aircraft cables, characterized by a protective zinc coating that enhances its corrosion resistance. This type of cable is generally less expensive than stainless steel, making it an attractive option for budget-conscious buyers.
Pros and Cons of Galvanized Steel Cables
The main advantage of galvanized steel cables is their cost-effectiveness, combined with decent strength and corrosion resistance. However, the zinc coating can wear off over time, particularly in high-friction applications, which may lead to reduced performance and increased maintenance costs.
Impact on Application
Galvanized cables are often used in non-critical applications, such as support structures and auxiliary systems, where extreme reliability is less critical. They are suitable for use in moderate environmental conditions but may not perform well in highly corrosive environments.
What Are the Benefits of Specialty Alloy Cables?
Specialty alloy cables, such as Monel or Tin Over Zinc, offer unique properties that can be beneficial for specific applications. These materials are designed to provide enhanced corrosion resistance and mechanical strength, making them suitable for specialized aerospace applications.
Pros and Cons of Specialty Alloy Cables
The key advantage of specialty alloy cables is their superior performance in harsh environments, including high-temperature and corrosive conditions. However, they tend to be more expensive and may require specialized manufacturing processes, which can complicate sourcing for international buyers.
Impact on Application
These cables are often used in mission-critical applications where failure is not an option. Their compatibility with a wide range of media makes them suitable for various aerospace systems, including fuel lines and hydraulic systems.
What Should International B2B Buyers Consider When Selecting Aircraft Cable Materials?
International B2B buyers, particularly from regions like Africa, South America, the Middle East, and Europe, should be aware of compliance with local and international standards such as ASTM, DIN, and JIS. Understanding these standards is crucial for ensuring that the selected materials meet safety and performance requirements. Additionally, preferences for specific materials may vary based on regional environmental conditions and economic factors.
Material | Typical Use Case for aircraft cables | Key Advantage | Key Disadvantage/Limitation | Relative Cost (Low/Med/High) |
---|---|---|---|---|
Stainless Steel | Flight control systems | Excellent corrosion resistance | Higher cost compared to other materials | High |
Galvanized Steel | Support structures | Cost-effective and decent strength | Zinc coating can wear off over time | Medium |
Specialty Alloys | Mission-critical applications | Superior performance in harsh environments | Higher cost and manufacturing complexity | High |
This strategic material selection guide provides a comprehensive overview of the key materials used in aircraft cables, highlighting their properties, advantages, and considerations for international B2B buyers. Understanding these factors will enable buyers to make informed decisions that align with their operational needs and compliance requirements.
In-depth Look: Manufacturing Processes and Quality Assurance for aircraft cables
What Are the Key Manufacturing Processes for Aircraft Cables?
The manufacturing of aircraft cables is a meticulous process that emphasizes precision and quality due to the critical applications in aviation. Understanding these processes can help international B2B buyers identify reliable suppliers.
Material Preparation: What Materials Are Used in Aircraft Cable Production?
The primary materials for aircraft cables include stainless steel, galvanized steel, and specialty alloys. The selection of materials is crucial, as they must meet stringent strength and corrosion resistance requirements. Buyers should ensure that suppliers use high-grade materials to guarantee the longevity and reliability of the cables.
- Metal Wire Sourcing: Manufacturers typically source raw wire from certified suppliers, ensuring it meets the necessary specifications.
- Wire Inspection: Incoming materials undergo rigorous inspections (Incoming Quality Control or IQC) to verify compliance with international standards.
How Are Aircraft Cables Formed and Assembled?
Once the materials are prepared, the next step involves forming and assembling the cables.
- Stranding: This process involves twisting multiple wires together to form strands. Different constructions, such as 7×7 or 7×19, are common, affecting the cable’s flexibility and strength.
- Swaging: In this step, the ends of the cables are fitted with terminals. The swaging process compresses the terminal onto the cable, ensuring a secure connection.
- Assembly of Cable Systems: Manufacturers may create complete cable assemblies, which include the cable, fittings, and terminals, pre-assembled for ease of installation.
What Finishing Techniques Are Used for Aircraft Cables?
The finishing process is essential for enhancing the performance and aesthetics of aircraft cables.
- Coating: Cables may receive protective coatings such as nylon, vinyl, or polyethylene to improve corrosion resistance and reduce wear.
- Quality Checks: After finishing, cables undergo a series of quality checks to ensure they meet design specifications.
Which International Standards Govern Aircraft Cable Quality Assurance?
Quality assurance in the manufacturing of aircraft cables is governed by various international and industry-specific standards.
- ISO 9001: This standard ensures that manufacturers maintain a quality management system that emphasizes customer satisfaction and continuous improvement.
- CE Marking: In Europe, CE marking signifies that products meet health, safety, and environmental protection standards.
- API Standards: For military and aerospace applications, manufacturers may also adhere to API standards, which provide guidelines for quality control in critical applications.
How Is Quality Control Implemented in Aircraft Cable Manufacturing?
Quality control (QC) is a multi-faceted process that involves several checkpoints throughout the manufacturing cycle.
- Incoming Quality Control (IQC): This initial inspection checks raw materials for compliance with specifications.
- In-Process Quality Control (IPQC): During production, ongoing inspections ensure that the manufacturing process adheres to quality standards. This includes checking the accuracy of stranding and swaging.
- Final Quality Control (FQC): After assembly, a comprehensive final inspection ensures that the finished product meets all specifications and standards.
What Common Testing Methods Are Used for Aircraft Cables?
To ensure safety and reliability, various testing methods are employed:
- Tensile Testing: This test measures the cable’s strength and elasticity by applying force until it breaks.
- Fatigue Testing: This assesses how the cable withstands repeated stress over time, simulating real-world conditions.
- Corrosion Resistance Testing: This test evaluates how well the cable withstands environmental factors that could lead to degradation.
How Can B2B Buyers Verify Supplier Quality Control?
For international B2B buyers, especially from regions like Africa, South America, the Middle East, and Europe, verifying a supplier’s quality control processes is crucial.
- Supplier Audits: Conducting on-site audits allows buyers to assess the manufacturing environment and quality control measures firsthand.
- Requesting Quality Reports: Buyers can ask suppliers for documentation detailing their QC processes, including results from testing and inspections.
- Third-party Inspections: Engaging independent inspectors to evaluate a supplier’s production process and quality standards can provide an unbiased perspective.
What Are the Quality Control Nuances for International Buyers?
When sourcing aircraft cables internationally, buyers should be aware of specific nuances:
- Regulatory Compliance: Different regions have varying regulations regarding aircraft components. Understanding local compliance is essential.
- Certification Verification: Ensure that suppliers possess the necessary certifications (e.g., ISO, CE) relevant to the buyer’s region and industry.
- Cultural Considerations: Familiarize yourself with the cultural context of the supplier’s region, as it may influence communication and business practices.
Conclusion: Ensuring Quality in Aircraft Cable Supply Chains
The manufacturing processes and quality assurance protocols for aircraft cables are integral to ensuring the safety and reliability of aviation systems. By understanding these processes, international B2B buyers can make informed decisions when selecting suppliers, ultimately enhancing their operational effectiveness and reducing risk. Investing time in verifying supplier quality control and compliance will lead to successful partnerships and high-quality products that meet the demands of the aviation industry.
Practical Sourcing Guide: A Step-by-Step Checklist for ‘aircraft cables’
The procurement of aircraft cables is a critical process for B2B buyers, particularly in the aerospace sector, where safety and reliability are paramount. This step-by-step sourcing checklist is designed to guide international buyers, especially those from Africa, South America, the Middle East, and Europe, through a systematic approach to selecting the right aircraft cables for their needs.
Step 1: Define Your Technical Specifications
Before initiating the sourcing process, clearly outline your technical requirements. This includes the cable’s diameter, construction type (e.g., 7×7 or 7×19), and material (stainless steel, galvanized steel, or specialty alloys). Defining these parameters ensures that you select cables that meet the specific performance and safety standards required for your applications, such as flight controls or landing gear.
Step 2: Research Regulatory Standards and Compliance
Understand the regulatory requirements governing aircraft cables in your region. Familiarize yourself with international standards such as ASTM, MIL-SPEC, and ISO certifications. Compliance with these standards is crucial to ensure that the cables you procure are safe and reliable for aviation use, thereby minimizing risks associated with non-compliance.
Step 3: ✅ Verify Supplier Certifications
It’s essential to vet potential suppliers thoroughly. Request documentation of their certifications, such as AS9100 for aerospace quality management systems or any relevant military approvals. This verification process helps you ensure that you are working with reputable suppliers who adhere to industry standards and can provide high-quality products.
Step 4: Evaluate Supplier Experience and Reputation
Assess the supplier’s experience in the aircraft cable market. Look for companies with a proven track record in manufacturing and supplying aircraft cables to reputable clients. Consider their references and case studies, especially from buyers in similar industries or regions. A supplier with extensive experience is more likely to provide reliable products and services.
Step 5: Request Samples and Perform Quality Testing
Before making a bulk purchase, request samples of the aircraft cables. Conduct quality tests to evaluate their strength, flexibility, and corrosion resistance. This step is vital to ensure that the cables will perform well under the specific conditions they will be subjected to in your operations.
Step 6: Negotiate Pricing and Terms
Once you have identified suitable suppliers, engage in price negotiations. Discuss not only the cost per unit but also terms related to delivery schedules, payment options, and warranty conditions. A clear understanding of these terms can help avoid potential disputes and ensure a smooth procurement process.
Step 7: Establish a Long-term Relationship
After selecting a supplier, aim to build a long-term relationship. Regular communication can lead to better pricing, priority service, and access to new products or innovations. A strong partnership can be beneficial as your needs evolve and you require ongoing support and expertise in sourcing aircraft cables.
By following this checklist, B2B buyers can navigate the complexities of sourcing aircraft cables more effectively, ensuring they make informed decisions that prioritize safety, compliance, and quality.
Comprehensive Cost and Pricing Analysis for aircraft cables Sourcing
What are the Key Cost Components in Aircraft Cables Sourcing?
When analyzing the cost structure of aircraft cables, several fundamental components contribute to the final price:
-
Materials: The choice of materials significantly affects pricing. Stainless steel and galvanized steel are common options, with stainless steel often commanding a higher price due to its corrosion resistance and strength. Specialty alloys may also incur additional costs.
-
Labor: Labor costs encompass the wages of skilled workers involved in manufacturing, assembly, and quality control. Labor rates can vary widely depending on the country of origin, which is particularly relevant for international buyers.
-
Manufacturing Overhead: This includes expenses related to factory operations, such as utilities, maintenance, and equipment depreciation. Overhead can be a hidden cost that varies based on the efficiency of the manufacturing process.
-
Tooling: Tooling costs relate to the equipment needed to produce specific cable types or custom designs. High-quality tooling can lead to better precision and reduced waste, impacting the overall cost.
-
Quality Control (QC): Implementing stringent QC measures ensures that the cables meet safety and performance standards. While this adds to the cost, it is essential for mission-critical applications in aviation.
-
Logistics: Transportation and warehousing costs are crucial, especially for international shipments. Factors like distance, mode of transport, and local customs regulations can significantly impact logistics expenses.
-
Margin: Suppliers typically add a profit margin to cover their operational costs and ensure business sustainability. This margin can vary based on supplier reputation and market demand.
How Do Price Influencers Impact Aircraft Cables?
Several factors influence the pricing of aircraft cables, which buyers should consider when sourcing:
-
Volume/MOQ: Larger orders often qualify for bulk discounts. Understanding the minimum order quantities (MOQ) can help buyers negotiate better pricing and achieve economies of scale.
-
Specifications and Customization: Customized cables tailored to specific applications may incur additional costs. Buyers should clearly define their specifications to avoid unexpected charges.
-
Materials: The choice between standard and specialty materials can lead to significant price differences. Buyers should assess their needs against the long-term benefits of investing in higher-quality materials.
-
Quality and Certifications: Cables that meet specific industry standards (e.g., MIL-SPEC) tend to be more expensive due to the rigorous testing and certification processes involved. Buyers should weigh the importance of certifications against their budget constraints.
-
Supplier Factors: The supplier’s reputation, location, and production capabilities can influence pricing. Suppliers with a strong track record in quality and reliability may charge a premium.
-
Incoterms: Understanding the chosen Incoterms (International Commercial Terms) is crucial. They define the responsibilities of buyers and sellers in international transactions, affecting costs related to shipping, insurance, and customs clearance.
What Tips Can Help Buyers Achieve Cost Efficiency in Aircraft Cables Sourcing?
-
Negotiation: Effective negotiation can lead to better pricing. Buyers should research market prices and be prepared to discuss their needs with suppliers to secure favorable terms.
-
Total Cost of Ownership (TCO): Buyers should consider the total cost of ownership, which includes purchase price, maintenance, and operational costs. Investing in higher-quality cables may reduce long-term expenses related to repairs and replacements.
-
Pricing Nuances for International Buyers: International buyers, especially from regions such as Africa, South America, the Middle East, and Europe, should account for currency fluctuations, import duties, and shipping costs when evaluating prices.
-
Supplier Relationships: Building strong relationships with suppliers can lead to better pricing and service. Regular communication and feedback can also foster collaboration on future projects.
-
Market Research: Staying informed about market trends and price fluctuations can empower buyers to make informed purchasing decisions.
Disclaimer on Indicative Prices
Prices for aircraft cables can vary widely based on the aforementioned factors. It is advisable for buyers to conduct thorough research and obtain multiple quotes to ensure they are making cost-effective decisions tailored to their specific needs.
Alternatives Analysis: Comparing aircraft cables With Other Solutions
When evaluating options for applications requiring strength and durability, it’s essential to consider alternatives to aircraft cables. While aircraft cables are renowned for their performance in aerospace and other high-stress environments, there are alternative solutions that might suit specific needs better. This section provides a comparative analysis of aircraft cables against two viable alternatives: Synthetic Ropes and Wire Ropes.
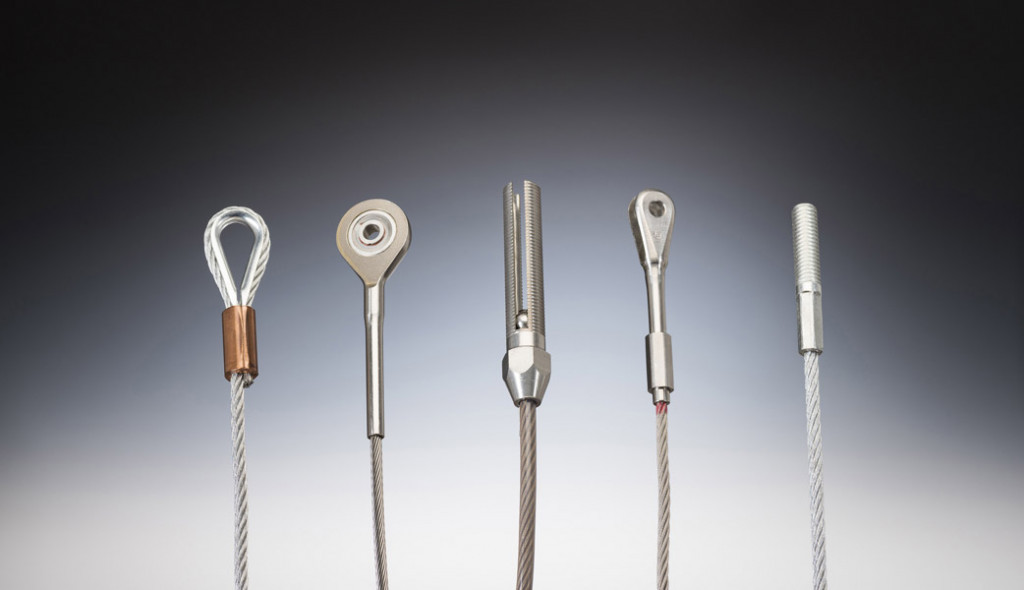
A stock image related to aircraft cables.
Comparison Table of Aircraft Cables and Alternatives
Comparison Aspect | Aircraft Cables | Synthetic Ropes | Wire Ropes |
---|---|---|---|
Performance | High tensile strength, fatigue-resistant; ideal for aerospace applications | Strong, lightweight; good for dynamic loads | High load-bearing capacity; durable |
Cost | Higher initial cost | Generally lower cost | Mid-range cost |
Ease of Implementation | Requires specialized fittings and installation | Easier to handle and splice | Moderate complexity in installation |
Maintenance | Requires regular inspection and lubrication | Low maintenance; resistant to UV and chemicals | Moderate maintenance; prone to corrosion |
Best Use Case | Critical flight systems, high-stress applications | Marine, climbing, and general rigging | Heavy lifting and industrial applications |
What Are the Advantages and Disadvantages of Synthetic Ropes?
Pros:
Synthetic ropes, such as those made from polyester or nylon, offer significant advantages in terms of weight and flexibility. They are easier to handle and can be spliced without specialized tools, making them a popular choice for marine and climbing applications. Additionally, synthetic materials resist UV degradation and chemicals, enhancing longevity in harsh environments.
Cons:
While synthetic ropes provide excellent flexibility and are lightweight, they generally do not match the tensile strength of aircraft cables. In high-stress environments, they may not perform as reliably as metal cables, especially in critical applications like aircraft control systems.
How Do Wire Ropes Compare to Aircraft Cables?
Pros:
Wire ropes are known for their high load-bearing capacity and durability, making them suitable for heavy lifting and industrial applications. They are available in various configurations and materials, including galvanized and stainless steel, which can enhance their corrosion resistance.
Cons:
Wire ropes can be heavier and more challenging to handle than aircraft cables. They also require more maintenance to prevent rust and wear, particularly in outdoor or corrosive environments. Furthermore, installation may involve specialized fittings, which could increase the overall time and cost.
How Can B2B Buyers Choose the Right Solution for Their Needs?
Selecting the right solution depends on several factors, including the specific application requirements, budget constraints, and environmental considerations. For critical aerospace applications, aircraft cables are often the best choice due to their proven performance and reliability. However, if weight and ease of handling are more critical, synthetic ropes may be preferable. For heavy-duty industrial use, wire ropes might offer the best compromise between strength and durability. By carefully assessing these factors, B2B buyers can make informed decisions that align with their operational needs and financial goals.
Essential Technical Properties and Trade Terminology for aircraft cables
What Are the Key Technical Properties of Aircraft Cables?
When sourcing aircraft cables, international B2B buyers must be familiar with critical technical specifications that ensure safety and performance. Understanding these properties can significantly impact procurement decisions, especially in industries requiring high reliability, such as aviation and aerospace.
1. Material Grade: What Should Buyers Know?
Aircraft cables are typically made from stainless steel or galvanized steel. Stainless steel offers superior corrosion resistance and is ideal for harsh environments, while galvanized steel provides a cost-effective solution with adequate durability. Selecting the appropriate material grade ensures that the cables will withstand operational stresses and environmental factors, reducing the risk of failure.
2. Construction Type: Why Does It Matter?
The construction of aircraft cables is classified into various configurations such as 7×7 or 7×19. These numbers indicate the number of strands and wires per strand. For instance, a 7×19 cable has 19 wires in each of its 7 strands, which offers increased flexibility and strength. Understanding the construction type helps buyers choose cables suitable for specific applications, such as flight controls or emergency systems.
3. Tensile Strength: How Is It Measured?
Tensile strength refers to the maximum amount of tensile (pulling) stress that a cable can withstand before failure. It is usually measured in pounds or kilograms. High tensile strength is crucial for applications that involve significant load-bearing capacities, making it vital for B2B buyers to verify this specification to ensure safety and compliance with industry standards.
4. Tolerance: What Is Its Role in Manufacturing?
Tolerance specifies the allowable deviation from a specified dimension, affecting cable performance and compatibility with fittings. Tight tolerances ensure a secure fit and enhance the reliability of the assembly. Buyers must consider tolerance requirements when selecting cables to avoid issues during installation and operation.
5. Break Strength: Why Is It Critical?
Break strength is the maximum load that a cable can handle before it breaks. It is usually higher than the working load limit (WLL), which is the maximum load the cable can safely support during normal use. Understanding break strength is essential for ensuring safety margins in applications where cables are subjected to dynamic loads.
What Are Common Trade Terms in the Aircraft Cable Industry?
Familiarity with industry jargon is essential for effective communication and negotiation in the B2B marketplace. Here are some key terms that buyers should know:
1. OEM (Original Equipment Manufacturer): What Does It Mean?
OEM refers to companies that produce parts or equipment that may be marketed by another manufacturer. In the context of aircraft cables, buyers often work with OEMs to ensure that the cables meet specific industry standards and specifications required for their applications.
2. MOQ (Minimum Order Quantity): Why Is It Important?
MOQ is the smallest quantity of a product that a supplier is willing to sell. This term is crucial for buyers to understand as it affects inventory costs and cash flow. Knowing the MOQ can help buyers negotiate better terms and manage their purchasing strategy effectively.
3. RFQ (Request for Quotation): How Should It Be Used?
An RFQ is a document issued by a buyer to solicit price quotes from suppliers. It details the specifications, quantities, and terms of purchase. Crafting a clear RFQ can lead to more accurate quotations and help buyers make informed decisions based on cost and quality.
4. Incoterms (International Commercial Terms): Why Are They Relevant?
Incoterms define the responsibilities of buyers and sellers for the delivery of goods under sales contracts. They clarify who is responsible for shipping, insurance, and tariffs. Understanding Incoterms is essential for international buyers to manage logistics and costs effectively.
5. Lead Time: What Should Buyers Consider?
Lead time is the duration from placing an order to receiving the product. It is critical for planning and inventory management. Buyers should inquire about lead times to align their procurement strategies with production schedules and project timelines.
By grasping these technical properties and trade terms, B2B buyers can make informed purchasing decisions, ensuring that they acquire the right aircraft cables for their operational needs.
Navigating Market Dynamics and Sourcing Trends in the aircraft cables Sector
What Are the Key Market Dynamics and Trends Affecting the Aircraft Cables Sector?
The global aircraft cables market is witnessing robust growth driven by the increasing demand for lightweight and high-strength materials in the aerospace sector. Key market drivers include the rising number of air travelers, which necessitates the expansion of airline fleets, and advancements in aircraft manufacturing technologies that prioritize safety and efficiency. Furthermore, regions such as Africa and South America are experiencing significant growth due to increased investments in aviation infrastructure, while the Middle East continues to emerge as a hub for aerospace innovation.
Emerging B2B technology trends include the integration of advanced materials such as composite cables that enhance durability and performance. Additionally, digital sourcing tools and platforms are becoming pivotal for international buyers seeking to streamline procurement processes. These technologies enable real-time tracking of supply chain dynamics and foster better communication between manufacturers and buyers, particularly in regions like Europe and the Middle East where regulations can be stringent.
International buyers must also navigate fluctuating raw material prices, influenced by geopolitical factors and supply chain disruptions. Understanding these dynamics is crucial for making informed purchasing decisions, especially in markets that are sensitive to economic changes, such as Poland and Egypt. It is advisable for buyers to diversify their supplier base and consider long-term contracts to mitigate risks associated with price volatility.
How Are Sustainability and Ethical Sourcing Impacting the Aircraft Cables Market?
Sustainability and ethical sourcing are becoming increasingly critical in the aircraft cables sector. The environmental impact of manufacturing processes, particularly in the extraction and processing of materials like steel and aluminum, has raised concerns among consumers and regulatory bodies alike. B2B buyers are now expected to prioritize suppliers who demonstrate commitment to reducing their carbon footprint through sustainable practices.
The importance of ethical supply chains cannot be overstated, as buyers are increasingly scrutinizing the sourcing of raw materials and the working conditions of laborers involved in production. Certifications such as ISO 14001 for environmental management and AS9100 for aerospace quality management are becoming essential for suppliers to prove their commitment to sustainability.
Moreover, the demand for ‘green’ materials is on the rise. Buyers should consider manufacturers that offer eco-friendly options, such as recycled materials or biodegradable lubricants, which can significantly reduce the environmental impact of aircraft cables. This trend not only supports corporate social responsibility goals but also aligns with the growing consumer preference for sustainable products.
What Is the Historical Context of Aircraft Cables in the B2B Sector?
The evolution of aircraft cables can be traced back to the early 20th century when aviation technology began to advance rapidly. Initially, cables were made from simple steel strands, primarily focusing on durability and strength. Over time, innovations in materials science led to the development of specialized alloys and composite materials that improved performance and reduced weight.
The introduction of military specifications (MIL-SPEC) during World War II set a new standard for quality and reliability in aircraft cables, emphasizing the importance of safety in aviation. In recent decades, manufacturers have increasingly adopted advanced manufacturing techniques and quality assurance processes, significantly enhancing the performance characteristics of aircraft cables.
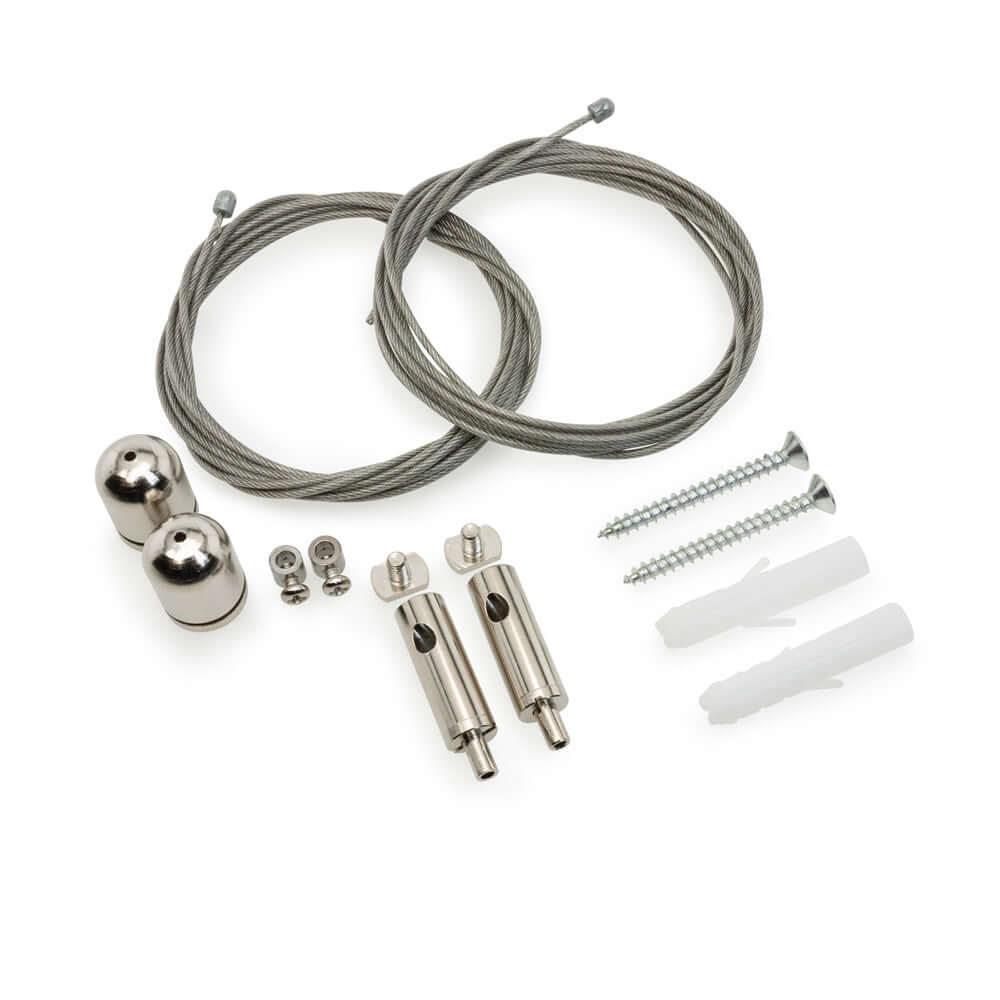
A stock image related to aircraft cables.
Today, the market is characterized by a diverse range of products, including stainless steel, galvanized steel, and specialty alloys designed for specific applications, such as flight controls and landing gear systems. This historical perspective underscores the importance of continuous innovation in meeting the evolving needs of the aerospace industry, providing B2B buyers with numerous options to suit their operational requirements.
Frequently Asked Questions (FAQs) for B2B Buyers of aircraft cables
-
How do I choose the right aircraft cable for my application?
Selecting the appropriate aircraft cable hinges on understanding your specific needs. Consider factors such as the cable’s diameter, material (stainless steel or galvanized), construction type (7×7 or 7×19), and its intended use, such as flight controls or landing gear systems. Consult technical specifications and industry standards to ensure compliance with safety regulations. Additionally, discuss your requirements with suppliers to gain insights on durability, tensile strength, and environmental resistance, which are crucial for mission-critical applications. -
What are the key differences between aircraft cable and wire rope?
Aircraft cables are typically smaller in diameter (3/8 inch and below) and constructed in configurations like 7×7 or 7×19, making them ideal for applications requiring flexibility and strength in confined spaces. Wire rope, on the other hand, is larger and offers various constructions, suitable for heavy-duty applications. When sourcing, ensure you understand these distinctions, as it will influence your choice based on load requirements, installation space, and functionality. -
What are the minimum order quantities (MOQ) for aircraft cables?
Minimum order quantities for aircraft cables can vary significantly among suppliers, influenced by factors like material type and production processes. Typically, MOQs may range from a few hundred meters to several kilometers. When negotiating with suppliers, clarify their MOQ policies to align with your project needs, especially if you are a smaller buyer or looking for customized solutions. This will help optimize your inventory management and cost-effectiveness. -
What should I consider when vetting international suppliers for aircraft cables?
When vetting international suppliers, prioritize their certifications, manufacturing capabilities, and compliance with industry standards (e.g., AS9100 for aerospace applications). Request samples and conduct thorough quality assurance checks to assess product reliability. Investigate their experience in international trade, including shipping logistics and customs handling, particularly for buyers in Africa, South America, the Middle East, and Europe. Additionally, look for customer reviews or case studies to gauge their reputation in the market. -
How can I customize aircraft cables to fit my specific requirements?
Customization of aircraft cables is often possible through discussions with manufacturers. Specify your needs regarding diameter, length, material, construction type, and any additional features such as coatings for corrosion resistance. Some suppliers offer bespoke solutions tailored to unique applications, but be prepared for potential lead times and minimum order quantities that may apply to custom products. Collaborating closely with your supplier will ensure your specifications are met accurately. -
What payment terms should I expect when sourcing aircraft cables internationally?
Payment terms for international transactions can vary widely based on the supplier’s policies and your relationship with them. Common terms include letters of credit, advance payments, or payment upon delivery. It is advisable to negotiate favorable terms that align with your cash flow and risk management strategies. Always ensure that payment methods are secure and that you understand the implications of currency fluctuations, especially when dealing with suppliers from different regions. -
What quality assurance processes should be in place for aircraft cables?
Quality assurance is critical in sourcing aircraft cables due to their application in safety-sensitive environments. Suppliers should adhere to rigorous testing protocols, including tensile strength tests, corrosion resistance evaluations, and compliance with industry standards. Request documentation of these tests and ensure that the supplier has a quality management system in place, such as ISO certifications. Regular audits and inspections can also help maintain high standards throughout the production process. -
What logistics considerations should I keep in mind when importing aircraft cables?
Logistics play a crucial role in the timely delivery of aircraft cables. Ensure that your supplier can provide reliable shipping options and has experience with customs regulations in your region. Consider factors such as shipping times, costs, and the potential for delays at ports. Additionally, work with freight forwarders who specialize in your type of cargo to facilitate smooth transportation. Understanding these logistics will help you mitigate risks and ensure that your project timelines are met.
Important Disclaimer & Terms of Use
⚠️ Important Disclaimer
The information provided in this guide, including content regarding manufacturers, technical specifications, and market analysis, is for informational and educational purposes only. It does not constitute professional procurement advice, financial advice, or legal advice.
While we have made every effort to ensure the accuracy and timeliness of the information, we are not responsible for any errors, omissions, or outdated information. Market conditions, company details, and technical standards are subject to change.
B2B buyers must conduct their own independent and thorough due diligence before making any purchasing decisions. This includes contacting suppliers directly, verifying certifications, requesting samples, and seeking professional consultation. The risk of relying on any information in this guide is borne solely by the reader.
Strategic Sourcing Conclusion and Outlook for aircraft cables
As international B2B buyers navigate the complex landscape of aircraft cable sourcing, understanding the nuances of product specifications and supplier capabilities is crucial. The strategic sourcing of aircraft cables not only ensures compliance with industry standards but also enhances operational efficiency and safety. Buyers should prioritize suppliers with robust certifications, such as AS9100 and MIL-Spec approvals, to guarantee reliability in mission-critical applications.
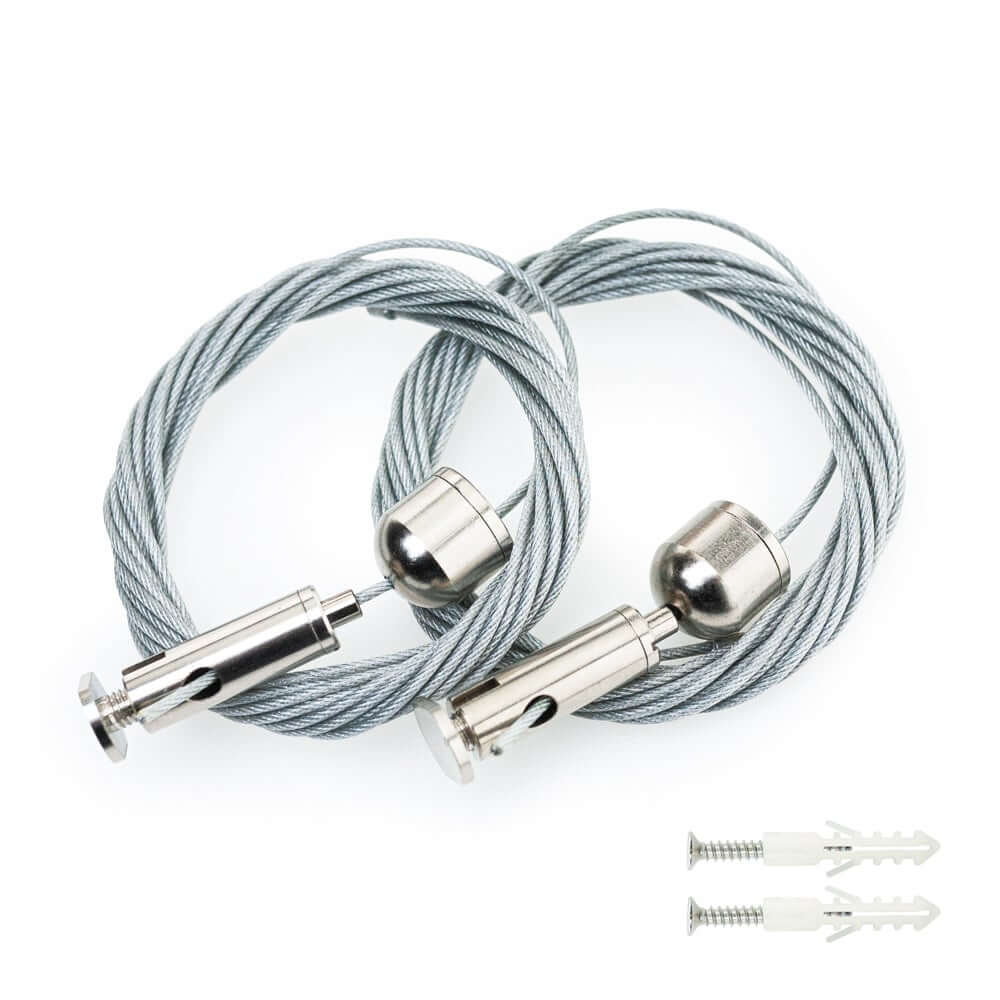
A stock image related to aircraft cables.
How Can International Buyers Enhance Their Sourcing Strategy for Aircraft Cables?
To optimize sourcing strategies, buyers from Africa, South America, the Middle East, and Europe must engage with manufacturers that offer a diverse range of materials—like stainless steel and galvanized options—tailored to specific operational needs. Leveraging local suppliers can also reduce lead times and shipping costs, fostering better relationships and understanding of regional market dynamics.
What Does the Future Hold for Aircraft Cable Sourcing?
Looking ahead, the demand for high-performance aircraft cables is expected to rise, driven by advancements in aviation technology and an increasing focus on safety. As international markets grow, buyers are encouraged to adopt a proactive approach, continuously seeking innovative solutions and establishing long-term partnerships with reputable suppliers. By doing so, they can ensure not only compliance but also contribute to the overall safety and efficiency of their operations in the aviation industry.